ABSTRACT
The influence of reaction temperature and time on the hydrothermal dissolution-precipitation synthesis of hydrotalcite was investigated. Untreated MgO, Al(OH)3 and NaHCO3 were used. An industrially beneficial, economically favourable, environmentally friendly, zero effluent synthesis procedure was devised based on green chemistry principles, in which the salt-rich effluent typically produced was eliminated by regenerating the sodium bicarbonate in a full recycle process. It was found that the formation of hydromagnesite dominates at low temperatures independent of reaction time. With an increase in reaction time and temperature, hydromagnesite decomposes to form magnesite. At low temperatures, the formation of hydrotalcite is limited by the solubility of the Al(OH)3. To achieve a hydrotalcite yield of 96%, a reaction temperature of 160°C for 5 h is required. A yield higher than 99% was achieved at 180°C and 5 h reaction time, producing an layered double hydroxide with high crystallinity and homogeneity.
GRAPHICAL ABSTRACT

1. Introduction
Layered double hydroxides (LDHs) are layered anionic clays with the general formula with [
] describing the composition of the LDH layers consisting of trivalent (MIII) and divalent (MII) metal cations, and [
] representing the composition of the anionic interlayer (
Citation1, 1021). Hydrotalcite is a naturally occurring LDH form with the formula Mg6Al2(OH)16CO3·4H2O (
Citation2). In its synthetic form, hydrotalcite can exist in Mg:Al ratios ranging from 1:1 to 3:1 (
Citation1, 1024). Hydrotalcite has a wide range of applications which include the use as polymer stabilizers, flame-retardants for polymers and anion scavengers (
Citation3;
Citation4;
Citation5;
Citation6) as well as a wide range of environmental applications which are comprehensively discussed in the Handbook of Clay Science (
Citation7) and include applications as basic catalysts and water purification agents.
Various synthesis methods for hydrotalcite have been developed, the most widely used being co-precipitation, urea hydrolysis and sol–gel ( Citation8). Although these methods can yield high-quality material, they also present major drawbacks:
Hydrotalcite produced by these synthesis methods usually requires post-synthesis treatment such as hydrothermal aging to increase the crystallinity (Citation9);
Metals salts used for the synthesis are expensive;
Metal salts used as reactants in these methods invariably result in the production of salt-rich effluent streams that are harmful to the environment;
and
Expensive effluent treatment prior to disposal is required.
In order to eliminate some of these drawbacks, alternative synthesis methods have been developed – one of which is a hydrothermal synthesis route which offers an alternative to existing synthesis methods ( Citation7). In the hydrothermal synthesis route, metal oxides/hydroxides are used as reactants and a dissolution-precipitation mechanism is typically employed to form the LDH phase ( Citation10). Hydrothermal synthesis offers a greener production approach by eliminating the additional processes required to treat harsh salt-containing effluent produced during co-precipitation and urea hydrolysis. The hydrothermal synthesis route does, however, present one major drawback: the metal oxides/hydroxides required have a very low solubility. This necessitates the establishment of the correct synthesis conditions for the formation of LDH at the desired quality.
Dyer et al. ( Citation11) discussed the parameters that influence the solubility (and therefore the dissolution/precipitation reactions) of metal oxides/hydroxides/carbonates; these include: particle size, crystallinity, reaction temperature, pH and time. Castet et al. ( Citation12) indicated that the hydrolysis of boehmite (AlO(OH)) is favored with an increase in temperature. A possible shift of boehmite solubility with an increase in temperature and pH was observed. These results were confirmed by Bénézeth et al. ( Citation13). Therefore, it can be concluded that an alkaline aqueous environment would favor the solubility of some metal species such as Al(OH)3 at higher temperatures which in turn is favorable for LDH formation. A pH above 10 is preferable for the precipitation of MgAl-CO3 LDH ( Citation8).
In previous investigations concerning the hydrothermal synthesis of hydrotalcite, great care was taken to enhance the reactivity of reactants prior to synthesis. In general, the pre-treatment entailed calcination of magnesium- and aluminum salts to produce a fine-powdered oxide mixture ( Citation14). Xu and Lu ( Citation10) investigated the formation mechanism of hydrotalcite. They stated that magnesium nitrate and aluminum hydroxide should be calcined to produce magnesium oxide and alumina (Al2O3) with a high surface area to yield highly reactive reactants. These were then reacted hydrothermally for long periods (5– 10 days) at temperatures near boiling. Hydrotalcite with slight brucite contamination was formed.
Mitchell et al. ( Citation15) investigated the production of specific poly-types of hydrotalcite with hydroxide anions in the interlayer. Budhysutanto et al. ( Citation9) used reactant grade magnesium oxide and partially amorphous transition alumina prepared by flash calcination of gibbsite in hydrothermal synthesis between 100°C and 240°C for up to 1 h, reaching high conversions after approximately 30 min with slight brucite impurities. They found that other pre-treatment methods include blending, ultrasonic treatment and wet grinding to increase surface area and subsequently enhance reactivity. These pre-treatments – especially calcination – are generally energy intensive due to the high temperatures required ( Citation9).
It is evident that most synthesis techniques are cost- and time intensive, require extensive pre- or post-treatment and produce undesirable effluent streams. The objective of this study, therefore, was to find an environmentally friendly synthesis route capable of producing a high-quality hydrotalcite without the use of expensive reactants. To improve the economic viability and comply with green synthesis principles, processing steps, such as pre-treatment of reactants and product post-treatment, should be eliminated. In addition, the production of treatment-intensive effluent streams should be avoided. Finally, the optimum reaction conditions using this environmentally friendly synthesis route should be found.
2. Experimental
2.1. Materials
Chemically pure (CP) grade reactants were used throughout. Magnesium oxide light 96% (CAS nr. 1309-48-4), aluminum hydroxide 99% (CAS nr. 21645-51-2) and sodium hydrogen carbonate 99% (CAS nr. 144-55-8) were all obtained from Merck KGaA – South Africa. Alcamizer 1 used for comparative purposes was obtained from Kisuma Chemicals.
2.2. Synthesis
A laboratory scale version of the green synthesis route by Labuschagné et al. ( Citation16; Citation17) was followed to produce hydrotalcite samples with a Mg:Al molar ratio of 2:1. This method is based on hydrothermal dissolution-precipitation. The procedure was designed to comply with green-synthesis principles as discussed in the introduction. A schematic of the devised synthesis procedure is shown in .
Figure 1. Block diagram of effluent free hydrotalcite production showing recycle routes and processing steps required.
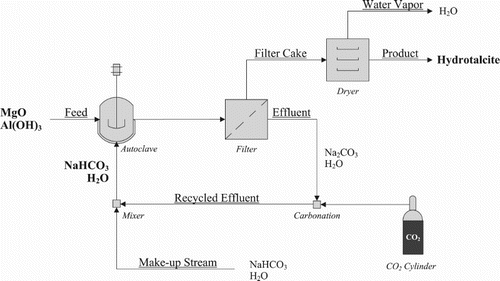
All reactants were used without pre-treatment. The untreated metal oxide/hydroxide solution for each experiment was prepared by stoichiometrically weighing off the required chemicals according to Equation (Equation2) and adding them to separate beakers containing distilled water under constant stirring. A 20%wt total solids loading was used.
The mixture was stirred for 5 min before addition to a 450 ml Series 4560 Parr autoclave reactor fitted with a pressure gauge and a fixed tungsten-iron thermocouple. Temperature was controlled with a Parr 4843 controller. The samples were reacted at temperatures ranging between 120°C and 180°C for 1– 5 h. After each run, the reactor was allowed to cool down by natural convection and was drained as soon as the temperature reached 50°C. Each sample was washed with distilled water until a filtrate pH of 8 was reached. The filter cake was dried in a convection oven at 70°C for 8 h. All filtrate was collected. The sodium bicarbonate (NaHCO3) was regenerated by bubbling CO2 through the sodium carbonate (Na2CO3) filtrate solution from a previous run – thus eliminating the need for expensive salt effluent treatment and only needing small amounts of sodium carbonate as part of a make-up stream if required.
Possible side reactions of magnesium were investigated by reacting magnesium oxide and the carbonate source according to Equation (Equation2) in the absence of aluminum hydroxide over a temperature range of 120–180 °C for the upper time limit of 5 h.
2.3. Characterization
Wide angle X-ray scattering (WAXS) measurements were performed with the X'pert-Pro diffractometer system from PANalytical with a continuous scanning using a step size of 0.001° between the ranges 5.01° and 89.99° 2θ. Co-Kα radiation was generated with a wavelength of 0.1789 nm at 50 mA and 35 kV by a diffractometer. The irradiated length was kept at 15 mm with a specimen length of 10 mm. The distance focus-diverge slit was kept at 100 mm and the measuring time was kept at s for each point.
A SPECTRO ARCOS model Inductively Coupled Plasma Optical Emission Spectrometer (ICP-OES) was used for the determination of the LDH aluminum and magnesium ratio. For analysis, 1 g of each LDH sample was dissolved in 20 ml of 37% hydrochloric acid solution and diluted with distilled water in a 1:10 ratio. A multi-element standard ICP grade from Merck was used for comparison. The analysis was performed using argon gas plasma. ICP analysis was done in triplicate.
Scanning electron microscopy (SEM) was used to confirm the morphological characteristics expected for the hydrotalcite phase. The samples were coated with graphite (three coats) using a Polaron h/v coater. The coated samples were then analysed using Ultrahigh Resolution Field Emission SEM (JEOL 6000F) at 3 kV. A Gatan Digital Micrograph imaging system was used.
Thermogravimetric analysis (TGA) was used to confirm the expected two-step decomposition of hydrotalcite. A Mettler Toledo A851 simultaneous TGA/DTA setup was used for differential thermal analysis and TGA. A small amount of the powder sample (ca. 10 mg) was placed in an open 70 μl alumina pan and heated from 25°C to 1000°C at a rate of 25°C/min in air flow (50 ml min−1).
3. Results and discussions
It is believed that the formation of hydrotalcite via the reaction of insoluble or low solubility metal oxides, hydroxides or carbonates occurs through a dissociation–deposition–diffusion mechanism ( Citation10). In order to commence the reaction, the metal oxides/hydroxides must dissolve to at least to some extent. Magnesium oxide loaded into the reactor must dissolve and react with water to precipitate as brucite (magnesium hydroxide) which is the base layer of the LDH material. Aluminum hydroxide must dissolve to make aluminum ions available for isomorphic replacement of some of the magnesium ions in the brucite layers to form the positively charged layers required as part of the desired hydrotalcite structure. The anion intercalated into the structure balances the positively charged layers and causes hydrotalcite to precipitate; crystal water is trapped in the interlayer during this process ( Citation10). If hydrotalcite is the least soluble species at the system temperature and pressure, it precipitates and removes the relevant ions from solution, causing more metal ions from metal oxides/hydroxides fed to the reaction to dissolve following Le Chatelier's Principle.
Of course, given the right conditions, other species can also form. For example, according to Hartmann-Petersen et al. ( Citation18), magnesite (MgCO3) is a highly stable carbonate form of magnesium that is produced by bubbling CO2 through a magnesium hydroxide slurry; the precipitation occurs relatively rapidly.
Furthermore, when an excess of CO2 is bubbled through a magnesite solution, carbonic acid is formed causing the solution to become more acidic. This aids in the solubility of the magnesite and forms hydrated magnesium carbonates (such as hydromagnesite 4MgCO3·Mg(OH)2·2(H2O)), a more soluble form of magnesium ( Citation19). The formation of hydrated magnesium carbonates generally occurs at low temperatures in an excess carbonate environment and is referred to as “the magnesite problem” ( Citation20).
Although no CO2 was bubbled through the reaction mixture per se, CO2 released from the aqueous bicarbonate environment as a result of temperature, pressure and pH decomposition of carbonic acid would have led to the formation of hydromagnesite as observable in Figures and . These figures show experimental results for the experiments conducted. All reflections on the XRD patterns were identified. Quantitative results based on Rietveld refinement for all the experiments conducted are shown in . The experimental results will now be discussed further.
Figure 2. XRD results for experiments used to determine the formation of side products at four different temperatures (120°C, 140°C, 160°C and 180°C) when reacting MgO and NaHCO3 for 5 h in water. All characteristic reflections are indicated.
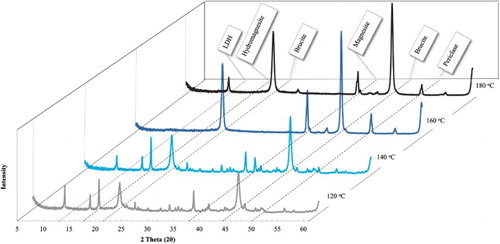
Figure 3. XRD results for experiments conducted for the synthesis of hydrotalcite at temperatures varying between 120°C and 180°C and reaction times varying between 1 h and 5 h. All characteristic reflections are indicated.
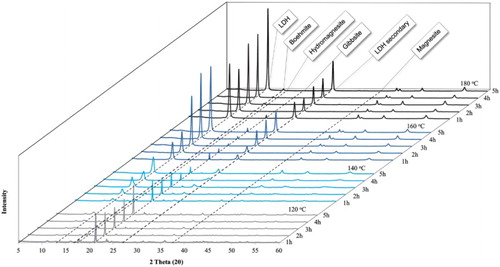
Table 1. Rietveld refinement for the synthesized MgAl-CO3 LDHs. All values are given as %wt of the compound present in the sample. 3σ errors indicated in italics.
3.1. Reactions without an aluminum source
As previously mentioned, the purpose of these experiments (results shown in ) was to observe the formation of side products at the reaction conditions tested.
3.1.1. Formation of Al-based products
The formation of hydrotalcite was observed at 180°C, as can be seen from , and is indicated in bold in . This is impossible as no aluminum source was added to the reactor intentionally. Unintended contamination must, therefore, have occurred.
3.1.2. Formation of Mg-based complexes
Trace amounts of MgO (less than 1%) were detected in the samples prepared at temperatures greater or equal to 140°C. Typically, it is expected that all caustic MgO added to the reactor reacts with water to form Mg(OH)2 at all reaction temperatures. The results were, therefore, surprising and it was concluded that a possible explanation for this observation could be the presence of a highly crystalline and unreactive form of MgO impurity in the feed material. Nevertheless, the XRD and Rietveld refinement data confirmed the presence of large quantities of brucite in all the samples besides this MgO impurity.
Due to the known “magnesite problem,' it was also of interest which reaction path is followed when adding a NaHCO3 to the mixture and in which form the magnesium precipitates at a given temperature: magnesite or hydromagnesite. Magnesite, which is a frequently found precipitate when adding carbonate to a solution of brucite and water, was not detected for the synthesis performed at 120°C; hydromagnesite was found. When using intermediate reaction conditions – a temperature of 140°C and 5 h reaction time – both hydromagnesite and magnesite were formed. When increasing the reaction temperature further to 160°C and 180°C, no hydromagnesite was detected but magnesite was found.
As described in the literature (Citation20), it is evident from and that the formation of magnesite is favored at higher temperatures, while hydromagnesite formation is favored at lower temperatures. Their formation was found not to be completely driven by the carbonate concentration.
3.2. Reactions with an aluminum source
The discussion will now refocus on the formation of the LDH phase when adding an aluminum source to the reaction.
3.2.1. Products formed at 120°C
When looking at the experimental series conducted at 120°C () several things can be observed. Firstly, a large reflection situated at a 2θ value of 21° which corresponds to the primary reflection of crystalline, unreacted gibbsite left in the samples, can be noted, indicating an incomplete reaction. However, although the reaction was incomplete, the desired MgAl-CO3 LDH phase (primary reflection at 13° 2θ) was formed in every experiment. From and it is also observable that an increase in the formation of this phase occurred with an increase in reaction time. However, the LDH secondary reflection which normally occurs around a 2θ angle of 27° is barely noticeable, indicating a low yield and/or low crystallinity LDH. The formation of the investigated hydromagnesite phase was visible in all reactions at 120°C as expected (Citation21) (primary reflection around 18° 2θ, secondary reflection around 16° 2θ).
shows several interesting correlations between reactant depletion and product formation; confirmations of which were found through Rietveld refinement (results shown in ). A gradual decrease in gibbsite can be seen with an increase in reaction time coupled with an increase in LDH yield. This indicates that the reaction times were not long enough (at the low reaction temperature of 120°C) to solubilize the aluminum hydroxide. For all reaction times at this reaction temperature, around 50 %wt of the products were hydromagnesite, indicating that the magnesium oxide dissolved completely, reacted with water and the carbonate species to form a magnesium basic carbonate. Due to its extreme low solubility, gibbsite is the limiting reactant for the formation of the LDH and therefore its dissolution the rate limiting step.
3.2.2. Products formed at 140°C
A significant difference was noted when comparing the XRD and Rietveld quantitative results of 140°C with those obtained for 120°C. The primary LDH reflection at the 2θ position of 13° showed a clear increase in reflection intensity as the reaction time was increased. Confirmation of an increase in the amount of the LDH phase and not only an increase in the sample crystallinity was obtained through Rietveld refinement. An LDH yield of 79.52% after just 1 h and 91.49% after 5 h could be obtained. The significant decrease in the gibbsite reflection is also evident. The presence of gibbsite decreased from 15.38% after 1 h to 7.34% after 5 h at 140°C, indicating that an increased reaction time is needed for an increased gibbsite solubility.
The XRD patterns show no presence of hydromagnesite for any of the reaction times used. However, the presence of magnesite with a primary reflection at 38° 2θ was detected. The reason for this being unclear when considering the results obtained investigating the side reactions of magnesium oxide with a carbonate source and without an aluminum source. This observation was, however, believed to be made due to the low concentration of magnesium ions in solution, favoring the formation of a low magnesium to carbonate ratio compound (compared to the high magnesium to carbonate ratio hydromagnesite formed at 120°C).
3.2.3. Products formed at 160°C and 180°C
For the experimental series at 160°C and 180°C, it can easily be observed from that all characteristic reflections of LDH (including those at a 2θ positions 41°, 46° and 55°) are well defined with high intensity and small broadening at the base, indicating the formation of a product with good crystallinity for all reaction times. Some unreacted gibbsite was found to still be present, evident from the reflection at 21° 2θ, but the amount decreased with reaction time. From the Rietveld analysis, LDH formation was found to be the dominant reaction (compared to magnesite and hydromagnesite at the lower reaction temperatures). The amount of gibbsite in the sample decreased and remained fairly constant between 3% and 4% up until 180°C and 5 h reaction time. The XRD patterns for 180°C indicate that after 5 h, unreacted gibbsite dissolved completely and re-precipitated as boehmite (another crystal form of aluminum hydroxide) with the primary reflection at 17° 2θ. Furthermore, all magnesium was converted to LDH and no hydromagnesite or magnesite was found at any reaction time for the reactions occurring at 180°C.
The results were confirmed by quantitative data from Rietveld refinement, showing an LDH yield of >96%wt. at 1 h and >99%wt. (with the balance being unreacted aluminum hydroxide) at 5 h. It is also believed that aging and an increase in crystallinity occur at high temperatures during the final hour of the reaction where the small LDH crystals dissolve and re-precipitate to form a much more crystalline product through the process of Ostwald ripening (Citation22).
3.2.4. Summative discussion
No magnesium hydroxide, magnesium oxide or magnesite was detected for the synthesis carried out at 120°C. The XRD and Rietveld refinement data confirmed the presence of large quantities of hydromagnesite, which is a metastable hydrated magnesium carbonate mineral (Citation23). As the reaction time was increased, the decrease in the hydromagnesite reflections and concentration could be seen with the corresponding increase in the primary and secondary LDH reflections and concentration. During the synthesis at 140°C, large quantities of magnesite were formed, while no magnesium hydroxide or magnesium oxide was detected.
As with the reaction at 120°C, the LDH primary reflection and concentration increased with the reduction in the amount of the magnesium carbonate based material. Most noticeable was the increase in the amount of LDH formed with an increase in gibbsite solubility (and decreased Al(OH)3 found in the product). Reactions at high temperatures were, therefore, found to favor the formation of the LDH phase due to larger amounts of brucite reacting with more aluminum in solution. This effect was ascribed to an increasing solubility of gibbsite with increasing temperature. Furthermore, the presence of the magnesium carbonate compounds had no part in the reaction; they were formed as sink for the carbonate in solution since little LDH can form due to the low gibbsite solubility at low temperatures. Finally, the formation of magnesite is favored at higher temperatures and hydromagnesite at lower temperatures (Citation20).
3.3. Mg:Al ratio of precipitated MgAl-CO3 LDHs
is a visual representation of the difference in the Mg:Al ratio as a function of temperature and time, as determined by the ICP analysis. The reactants were added to form synthetic hydrotalcite with an intended divalent to trivalent metal ratio of 2:1. Successful formation of the desired product could be observed for the samples produced at 180°C with a metal ratio very close to 2:1. At 120°C and for reaction times above 5 h, a drop in metal ratio could be observed corresponding to the formation of hydromagnesite which increased the solubility of the Mg, thereby indicating that some of the Mg could have been washed out during filtration as soluble ions.
Figure 4. Ratios of Mg:Al obtained by ICP analysis for hydrotalcite synthesised at temperatures between 120°C and 180°C and reaction times of 1 h to 5 h.
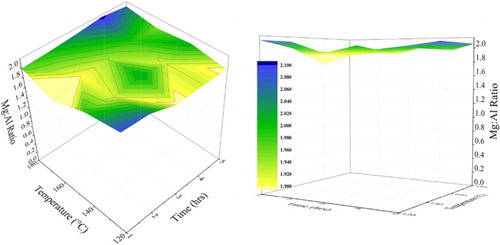
For all the other samples, the Mg:Al ratio remained just below or above a value of 2:1, which indicates that very little (if any) of the metal ions were dissolved and lost as ions during the reactions. The lowest Mg:Al ratio of 1.76:1 was observed at a reaction time of 1 h and 160°C. This is unexpected and can indicate the loss of some of the magnesium ions due to the conversion of other soluble magnesium species to hydrotalcite. The exact mechanism behind this is not yet fully understood and is being investigated.
3.4. Environmental considerations
The proposed synthesis procedure could successfully be used to produce high-quality hydrotalcite while reducing the environmental impact of the synthesis and minimizing production costs; the main advantage being the possibility to run the synthesis as a zero effluent process as previously shown in . The effluent stream (filtrate) containing sodium carbonate formed during the reaction was recycled and regenerated through carbonation; thereby converting the sodium carbonate back to sodium bicarbonate that can be re-used as the carbonate source for a following batch. The advantages of running the synthesis in this zero effluent manner are a reduced water usage, no salt by-product being formed, and lower reactant costs as a result of the recycle system and metal oxides/hydroxides used. Furthermore, pre- and post-treatments were eliminated (in comparison to (Citation9; Citation10; Citation14; Citation15)) and reaction times shortened (Citation10). Overall the green synthesis route was found to drastically simplify hydrotalcite formation and increase the process economics.
3.5. Product quality
XRD, SEM and TGA analysis confirmed the successful formation of hydrotalcite of exceptional quality using the devised green, zero effluent synthesis method at the identified optimum reaction conditions of 180°C and 5 h. The XRD patterns obtained for the synthesised material have been discussed in length and are shown in . clearly indicates the typical two-step decomposition expected for an LDH phase. Furthermore, indicates the typical expected hexagonal platelet structure. Morphological homogeneity of the sample could be observed. Hence, it could be concluded that the material formed is hydrotalcite. High crystallinity, large platelet size and morphological homogeneity furthermore indicate the formation of a good quality product. For further proof of hydrotalcite quality using the green synthesis method devised in this paper, a comparison was drawn to Alcamizer 1 (an industrially produced product). It is clearly visible in that the product produced is of higher crystallinity and similar platelet size and homogeneity.
4. Conclusions
A very pure form of MgAl-CO3 LDH (>99% purity) could be synthesized using a green synthesis method: hydrothermal dissolution-precipitation. The main advantages of the utilized green synthesis method are that it requires only inexpensive, run-of-mine metal oxides / hydroxides and excludes the production of harsh salt containing effluent when run as a zero effluent process by recycling and carbonating the filtrate stream. Furthermore, the reactants do not have to be treated prior to synthesis (calcined) which lowers the total energy requirements of synthesis. All these factors contribute to the system being a more environmentally friendly and greener synthesis method.
Figure 7. Comparative plot of XRD graphs and SEM micrographs for hydrotalcite prepared via the green, zero effluent dissolution-precipitation synthesis route at 180°C and 5 h and Alcamizer 1.
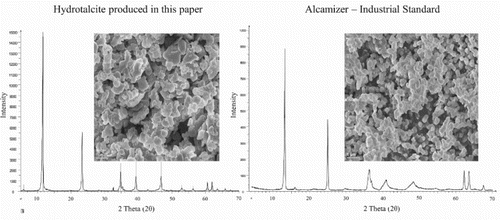
It was found, that the formation of hydromagnesite is the dominant reaction at low temperatures. With an increase in reaction time and temperature, hydromagnesite decomposes and forms magnesite. At low temperatures the formation of MgAl-CO3 LDH is limited by the solubility of gibbsite. A MgAl-CO3 LDH yield of 80% was obtained at 140°C after 5 h with low crystallinity. To achieve an MgAl-CO3 LDH conversion greater than 96%, a reaction temperature of 160°C for a minimum of 5 h reaction time is required; this is also achieved within 1 h at 180°C. A 99.37% conversion was achieved at reaction at 180°C for 5 h yielding an MgAl-CO3 LDH of very high crystallinity and homogeneity.
Disclosure statement
No potential conflict of interest was reported by the authors.
Notes on contributors
F. J. W. J. Labuschagné Prof Labuschagné obtained his Bachelor's degree in Chemical Engineering in 1998 at the University of Pretoria. He started research in the polymer field during his post graduate studies under Prof Walter Focke in the field of organo-metallic based intumescent flame retardants. After obtaining his PhD in 2003 at the University of Pretoria, South Africa, he left the academia to do research in industry on a joint industrially and South Africa Government funded project as project leader. He and his team developed and patented a novel process to beneficiation mined raw materials into high value polymer additives such as synthetic hydrotalcite – an anionic clay. Funding has been obtained to erect a full scale commercial plant in collaboration with the CSIR. During this time in industry he kept in close contact with Prof Focke and supplied hydrotalcite samples for modification and intercalation studies and evaluation in other polymers and applications. In 2009 he rejoined the University of Pretoria on hydrotalcite related research; where he is focusing on broadening the patented process to include other LDH materials, LDH modification and new applications. He currently lectures 3 undergraduate courses and one post graduate course in Chemical Engineering at the University of Pretoria. He has published 15 pier reviewed articles in accredited journals, 3 South African patents, 3 provisional patents and several national and international conference presentations in his academic career.
A. Wiid studied Chemical Engineering at the University of Pretoria and obtained her Bachelor's Degree in 2013. She obtained her Honours Degree in Chemical Engineering in 2014 Cum Laude and her Master's Degree in 2016. She spent 6 months in Germany at the Leibniz-Institut für Polymerforschung Dresden e. V. in 2015 researching the synthesis of LDH materials. She is currently working at McCain Foods Limited South Africa as Engineer.
H. P. Venter obtained his Chemical Engineering Bachelor's degree in 2010 from the University of Pretoria. He obtained his Honour's degree in 2011 and his Master's degree in 2014 (with distinction). As part of his Master's work he spent 9 months at the Leibniz-Institut für Polymerforschung Dresden e. V., Gemany working on the synthesis of different LDH materials. He also spent most of 2014 at the CSIR, South Africa helping with the design and initial erection of a pilot facility to synthesise new LDH materials for the local polymer industry. He is currently working as Engineer at Process Design and Automation Pty Ltd.
B. R. Gevers completed her BEng Chemical Engineering degree with distinction at the University of Pretoria in 2016. During her final year research project she investigated the formation of hydrocalumite in an economically viable process. She then started her BEng Hons degree in Chemical Engineering at the same university in 2017 and will be continuing on with a Masters in 2018. During her Honours year, her primary research focus shifted from synthesis of hydrocalumite and hydrotalcite to the development of photoelectrochemically active catalysts for the generation of hydrogen from water and sunlight, and for use in artificial photosynthesis to generate renewable fuels from CO2 and sunlight. She spent 1.5 months at the Leibniz-Institut für Polymerforschung Dresden e. V. in 2017 researching the synthesis of LDH materials.
Dr A. Leuteritz studied chemistry at the Friedrich-Alexander-University Erlangen-Nuremberg. He completed his Diploma thesis at Siemens AG, his topic being “Chloride-free synthesis of alkali-soluble polymers”. He completed his dissertation at the Dresden University of Technology, Institute of Industriual Chemistry, his topic being “Polymer immobilization of ethylenediamine nickel complexes for the electrochemical dehalogenation of organohalogen compounds”. He has been a research associate at the Leibniz Institute for Polymer Research since 2000. His main work comprises of the development of novel nanocomposite materials through integration of natural and artificial minerals for targeted design of the particle-matrix interaction. The findings of these investigations form the basis for the development of multifunctional materials. He is also involved in the investigation and evaluation of the long-term stability of multifunctional materials in various fields of application. Dr Andreas Leuteritz was awarded the Innovation Prize of the Leibniz-Institut für Polymerforschung for the development of nanocomposites together with Doris Pospiech and Bernd Kretzschmar in 2008, and for contributions to a process for the electron-induced reactive treatment of polymers together with Uwe Gohs, Udo Wagenknecht, Sven Wießner and Michael Wilms 2015.
ORCID
F.J.W.J. Labuschagné http://orcid.org/0000-0002-4820-4585
H.P. Venter http://orcid.org/0000-0002-2010-3782
B. R. Gevers http://orcid.org/0000-0003-2756-1484
Additional information
Funding
References
- Forano, C.; Hibino, T.; Leroux, F.; Taviot-Guého, C. Chapter 13.1 Layered Double Hydroxides. In Developments in Clay Science: Faïza, B., Gerhard, L., Eds.; Vol. 1, Elsevier: Amsterdam: 2006; pp 1021–1095.
- Miyata, S.; Kumura, T. Chem. Lett. 1973, (8), 843–848. doi: 10.1246/cl.1973.843
- Finta, Z.; Hell, Z.; Balán, D.; Cwik, A.; Kemény, S.; Figueras, F. J. Mol. Catal. A 2000, 161 (1), 149–155. doi: 10.1016/S1381-1169(00)00341-1
- Costa, F.R.; Leuteritz, A.; Wagenknecht, U.; Jehnichen, D.; Häußler, L.; Heinrich, G. Appl. Clay Sci. 2008, 38 (3–4), 153–164. doi: 10.1016/j.clay.2007.03.006
- Tronto, J.; Crepaldi, E.L.; Pavan, P.C.; Cipriano De Paula, C.; Valim, J.B. Mol. Cryst. Liq. Cryst. Sci. Technol. Sect. A 2001, 356 (1), 227–237. doi: 10.1080/10587250108023703
- Folarin, O.; Sadiku, E. Int. J. Phys. Sci. 2011, 6 (18), 4323–4330.
- Bergaya, F.; Lagaly, G. Chapter 1 - General Introduction: Clays, Clay Minerals, and Clay Science. In Developments in Clay Science: Faïza, B., Gerhard, L., Eds.; Vol. 5, Elsevier: Amsterdam: 2013; pp 1–19.
- Forano, C.; Costantino, U.; Prévot, V.; Gueho, C.T. Chapter 14.1 - Layered Double Hydroxides (LDH). In Developments in Clay Science: Faïza, B., Gerhard, L., Eds.; Vol. 5, Elsevier: Amsterdam: 2013; pp 745–782.
- Budhysutanto, W.N.; Kramer, H.J.M.; van Agterveld, D.; Talma, A.G.; Jansens, P.J. Chem. Eng. Res. Des. 2010, 88 (11), 1445–1449. doi: 10.1016/j.cherd.2009.10.010
- Xu, Z.P.; Lu, G.Q. Chem. Mater. 2005, 17 (5), 1055–1062. doi: 10.1021/cm048085g
- Dyer, J.A.; Scrivner, N.C.; Dentel, S.K. Environ. Prog. 1998, 17 (1), 1–8. doi: 10.1002/ep.670170112
- Castet, S.; Dandurand, J.-L.; Schott, J.; Gout, R. Geochim. Cosmochim. Acta 1993, 57 (20), 4869–4884. doi: 10.1016/0016-7037(93)90126-H
- Bénézeth, P.; Palmer, D.A.; Wesolowski, D.J. Geochim. Cosmochim. Acta 2001, 65 (13), 2097–2111. doi: 10.1016/S0016-7037(01)00585-3
- Roy, D. M.; Roy, R.; Osborn, E. F. Am. J. Sci. 1953, 251 (5), 337–361. doi: 10.2475/ajs.251.5.337
- Mitchell, S.; Biswick, T.; Jones, W.; Williams, G.; O'Hare, D. Green Chem. 2007, 9 (4), 373–378. doi: 10.1039/b613795d
- Labuschagné, F.J.W.J.; Giesekke, E.W.; Van Schalkwyk, J.D. Production of Hydrotalcite. PCT WO 2006/123284 A2, 2006.
- Labuschagné, F.J.W.J.; Giesekke, E.W.; Van Schalkwyk, J.D. Production of Hydrotalcite. RSA Patent 2007/09947, 2007.
- Hartmann-Petersen, P.; Gerrans, G.C.; Hartman-Petersen, R.; Eds. SASOL Encyclopedia of Science and Technology, 2nd ed.;Claremont: South Africa, 2007.
- Singal, A. The Pearson Guide to Inorganic Chemistry for the IIT JEE, Dorling Kindersley: London, 2010.
- Deelman, J. Low-Temperature Formation of Dolomite and Magnesite, Compact Disk Publications: Eindhoven, 2003.
- Focke, W.W.; Molefe, D.; Labuschagne, F.; Ramjee, S. J. Mater. Sci. 2009, 44 (22), 6100–6109. doi: 10.1007/s10853-009-3844-6
- Yao, J.H.; Elder, K.R.; Guo, H.; Grant, M. Phys. Rev. B 1993, 47 (21), 14110. doi: 10.1103/PhysRevB.47.14110
- Vágvölgyi, V.; Frost, R.L.; Hales, M.; Locke, A.; Kristóf, J.; Horváth, E. J. Therm. Anal. Calorim. 2008, 92 (3), 893–897. doi: 10.1007/s10973-007-8845-6