ABSTRACT
The secondary reaction of toluene is difficult to be suppressed in benzene alkylation with methanol over conventional acidic zeolite catalysts. Moreover, the formation of coke yet remains a challenging problem. In this study, Na-Y zeolites were modified with ammonium carbonate (AC), citric acid (CA) and caesium nitrate(CN) to evaluate the alkylation of benzene with methanol, which was also characterized by XRD, SEM, FT-IR, N2 adsorption and Py-IR. For the Na-Y treated with AC-CA-CN, not only the catalytic selectivity for the alkylation of benzene with methanol was improved (the total selectivity of toluene and xylene was 97.9% and toluene selectivity was 86.4%), but also the quantity of coke was greatly decreased.
GRAPHICAL ABSTRACT
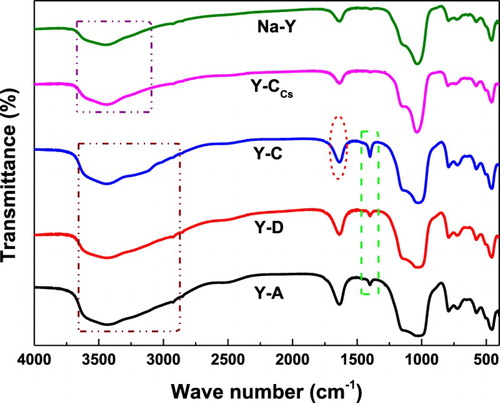
1. Introduction
Toluene is viewed as a bridge for synthesis of important chemical products, namely important chemical intermediates, such as fuels, solvents, polyurethane products, medicine, dyestuff, explosives, agricultural chemicals and other pillar industries (Citation1–6). So the high yield of toluene, especially the preparation of a special catalyst for toluene, is urgently needed. Meanwhile, The status quo of Chinese resources is the excessive production of benzene in the petrochemical industry and the production overcapacity of methanol in coal chemical industry. Hence, currently, the alkylation of benzene with methanol to produce toluene has attracted a lot of attention due to the decline in crude oil resources and coal resources being rich relatively. In brief, it is imperative that the technology of methanol-to-benzene reaction to toluene is systematically researched to further implement the coupling cycle development strategy of the coal chemical industry and the petrochemical industry.
According to the literature, methylation reactions catalyzed by acidic zeolites are highly important in several transformation processes of hydrocarbons, such as ZSM-5 (Citation7–13), mordenite (Citation8), zeolite Beta (Citation14, Citation15), zeolite X (Citation16), SAPO-5/SAPO-11 (Citation17), NU-87/SSZ-33 (Citation18), MCM-41 (Citation19) and MCM-22 (Citation17, Citation20), as well as Pt (Citation7), Zn, Mg (Citation21), P (Citation11), La, Ce, B-modified (Citation22) zeolite catalysts. As a result, there were great differences in the catalytic activity and selectivity among these zeolites. Summary learning, the production of a mixture of toluene and xylene was generally researched over the above catalysts, but toluene as the ultimate product is a relatively difficult point. Moreover, coke yet remains a challenging problem. Therefore, seeking a breakthrough, the observed high selectivity of toluene can be attributed to a combination of differences in (1) Acidity (Citation14, Citation22): the catalytic selectivity and activity of zeolites for the aromatics’ alkylation mainly depend on the acidity of the catalyst, and the zeolites with less Brönsted acidity could help to minimize the side reaction of methanol; (2) Pore modification (Citation17): the last few decades have brought many reports concerning pore modification of ZSM-5 to enhance para-selectivity adsorption behavior; (3) Diffusivity (Citation23): The presence of two diffusion pathways for aromatic molecules in ZSM-5 has been established. This was possible through rigorous exclusion of potential artifacts resulting from the presence of discrete particle size distributions or heat effects; (4) Si/Al ratio (Citation7): The results indicated that directly adjusting the Si/Al ratio of the catalyst can successfully suppress ethylbenzene formation by suppressing the side reaction of methanol to olefins; (5) Effect of Water (Citation15): most of these alkylation reactions are typically studied in the absence of water, etc. Based on the above, new zeolites with different acidities and structures have been continuously synthesized, and some of them may be more suitable for toluene alkylation with methanol than ZSM-5 zeolites in recent years.
In this paper, we studied the catalytic performance of AC-CA-CN-modified Na-Y zeolites in the alkylation of benzene with methanol using different techniques (i.e. BET, XRD, SEM, FT-IR, Py-IR). The effect of AC and CA on the structure of the catalyst, carbon deposition and the selectivity of toluene product was also investigated. We observed that Cs2O-modified catalysts could indeed significantly suppress the formation of coke.
1.1. Experimental
1.1.1. Materials
Commercial Na-Y and H-Y were purchased from the Catalyst Plant of Lanzhou. Ammonium carbonate (AC), citric acid (CA), caesium nitrate (CN), benzene and methanol were purchased from Lanzhou Chemical Reagents Co. and used without further purification.
1.1.2. Catalyst preparation
Commercial H-Y, Na-Y were retreated by high-temperature (823 K) processing for 4 h. The obtained samples were labeled H-Y, Na-Y.
Na-Y was treated with a solution of a suitable concentration of AC at normal temperature for 1.5 h under stirring. The turbid solution was then filtered and washed with distilled water. The modified solid sample was dried at 453 K overnight and calcined at 823 K for 4 h under ambient conditions. The final product was labeled Y-A.
The obtained Na-Y samples were modified with CA (1.5 h), AC and CA added in turn (1.5 h), and AC and CA added in turn (>1.5 h). The modified catalysts were named Y-B, Y-C, Y-D, respectively.
Beyond that, Y-C was treated with a solution of a suitable concentration of CN at normal temperature for 20 min under glass rod stirring and then was impregnated overnight at normal temperature. The modified Y-C sample was dried at 453 K. The sample was calcined in air at 823 K for 4 h (heating rate of 10oC/min). The final product was labeled Y-CCs (5% Cs).
1.1.3. Catalyst characterization
XRD patterns of catalysts were obtained with a D/MAX-2400 X-ray diffractometer equipped with atmosphere and temperature control stages and using Cu-Kα radiation (λ = 1.542 Å) operated at 40 kV and 50 mA. In these experiments, XRD patterns were recorded every 50°C with a ramp rate of 10oC/min up to 700°C under 5% H2/N2. BET surface areas of reduced catalysts were measured by N2 adsorption/desorption at 77 K using Micromeritics ASAP 2010 instruments. Before measurement, the samples were degassed under vacuum at 130°C overnight. The Fourier transform infrared absorption spectra (FT-IR) of the materials were acquired on a Nicolet Nexus 670 FT-IR spectrometer (Thermo Nicolet, U.S.A.) at room temperature in KBr pellets over the range of 7400∼350 cm−1 under atmospheric conditions. Pyridine adsorption measurements were performed by infrared spectroscopy aiming to determine the nature of acidic sites (Brönsted and Lewis). Pyridine chemisorption samples were obtained by passing pyridine vapor over the catalysts at 373 K for 1 h in the flow system. After the pyridine adsorption, the samples were stabilized in an N2 flow for 30 min, then allowed to cool to room temperature and subsequently used for IR analysis.
1.1.4. Catalytic activity tests
Catalytic activity of the samples was measured in a continuous-flow jet bubbling reactor with a glass tube (8 mm i.d.) at atmospheric pressure. The catalyst (0.5 g) was heat-treated in situ from ambient temperature to 400°C at 10°C/min and maintained at 400°C for 15 min in N2 flow before reaction. Then the benzene and methanol mixture (B/M molar ratio = 1:1) was fed into the reactor (WHSV = 2.0 h−1); the collected products from the reactor were analyzed online by gas chromatography (Fuli GC9790) with a DB-1 capillary column (30 m × 0.25 mm × 1.00 μm) and a flame ionization detector. In order to ensure all of the products were in the gas phase, the temperature of the effluent line was maintained at 200°C by a heating belt.
The conversion of benzene (CB) and the selectivity of toluene (ST) are defined by the following equations.
2. Results and discussion
2.1. Catalyst characterizations
The powder XRD patterns () of all the samples exhibited well-resolved diffraction peaks, which are characteristic of the Y type (H-Y, Na-Y, Y-A, Y-B, Y-C, Y-CCs and Y-D) framework structure. All the samples exhibited the typical characteristic patterns with peaks observed at 2θ in sections between 10.0° and 39.0° which corresponded to the structure of faujasite (FAU) topology. Moreover, similar diffraction peaks of the samples indicated that the adjustment of the acid sites in the synthesis process did not have a significant influence on the framework of Y zeolites (Citation24).
shows the SEM images of Na-Y(a), Y-A(b), Y-B(c), Y-D(d), Y-C(e) and Y-CCs(f) catalysts. The conglomeration results in the shape of the sample crystal being roughly faujasite cage (a size of about approximately 1 μm with smooth and angular surfaces). Notably, the difference is: as showed in (b–d) the crystals of Y-A, Y-B and Y-D exhibited more disorderly shape with rough surfaces and even the phenomenon of agglomeration. This morphology arose from the modified agent treatment to achieve partial desilication or dealumination, which led to collapse of the catalyst tunnel, even agglomerate. Nevertheless, in (e,f) the crystals of Y-C and Y-CCs clearly showed the crystal is roughly faujasite cage.
shows the N2 adsorption/desorption isotherms and the pore size distribution corresponding to the modified Y-C catalyst. The isotherm belongs to a transition between type II and type IV, according to IUPAC classifications. The large slope at a relative pressure between 0.02 and 0.5 indicates that multilayer adsorption dominates for Y-C, which is pertinent to the FAU model. The large slope is consistent with the extraordinarily large FAU surface area (698 m2 g−1) observed for this sample. Moreover, sizes of mesopores were about 3 nm according to the pore size distribution ((b)).
The textural properties of samples are listed in , which compares the surface area, average pore diameter and pore volume of H-Y, Na-Y, Y-A, Y-B, Y-C, Y-CCs and Y-D samples. The order of average pore diameter for the catalysts is as follows: Y-B> Y-A> Y-D > Na-Y > Y-C > Y-CCs > H-Y. Compared with the Na-Y, the Y-C and Y- CCs samples show a slight decrease in the average pore diameter. The BET surface area of Y-C and Y-CCs increased substantially, because natriumion is displaced in the channels of Na-Y. In contrast, the BET surface area of Y-A, Y-B and Y-D decreased substantially, because of the modified agent treatment to achieve partial desilication or dealumination, which led to collapse of the catalyst tunnel, even agglomerate. Experimental results (in and ) show that the surface area and the pore volume have an effect on selectivity of toluene in the alkylation of benzene with ethanol. Furthermore, the order of average pore diameter for the catalysts coincided well with experimental results according to which the order of coking speed for the catalysts is as follows: Y-D > Y-C >> Y-CCs. The size of the average pore diameter is also one of the main causes of carbon deposition (Citation25).
Table 1. Surface area and pore structure analyses from N2 physisorption.
Table 2. Products’ content of benzene alkylation with methanol over the different catalysts.
shows the FT-IR spectra of Na-Y, Y-A, Y-C, Y-CCs and Y-D. For all samples, in the FT-IR spectra of the framework absorption region (1600∼400 cm−1), absorption bands were observed at 1250∼1050 cm−1 (external or internal asymmetric stretch), 800 cm−1 (external symmetric stretch) (Citation26, Citation27) and 730 cm−1 (internal symmetric stretch) (Citation28). In the FT-IR spectra of the absorption region (3000∼3670 cm−1), the bands at 3645 cm−1 are assigned to the terminal silanol (Si-OH) active sites, and the bridging hydroxyl (OH) active sites of Si and Al ions located in the super-cage of zeolite Y, respectively. Bands at 3670 and 3528 cm−1 are attributed to the extra-framework aluminum hydroxyl [Al(OH)2+] (Citation29). FT-IR spectra demonstrated that the addition of AC, CA and Cs2O did not affect the skeleton framework of the Y zeolite. Notably, the bands at 1630 cm−1 of Y-A, Y-C and Y-D become stronger obviously while the band at 1630 cm−1 of Y-CCs has no obvious change in comparison with Na-Y. The absorption region (3000∼3670 cm−1) becomes wider, assigned to asymmetric stretching of the OH group. Correspondingly, bands of 1407 cm−1 are observed, indicating that the protonation reaction of the AC-CA molecules occurs. This result fully indicates that the OH active sites of the Si and Al ions are located in the super-cage of the Y type zeolite. For the Y-CCs catalyst, the bands at 1407 cm−1 cannot be observed.
shows the Py-IR spectra of these catalysts at a specific temperature. The spectra of these samples exhibit four bands at frequencies 1620, 1540, 1490 and 1450 cm−1. Bands at 1620 and 1450 cm−1 indicate the presence of coordinated pyridine of the Lewis acid sites of the catalyst. The IR band appearing at 1490 cm−1 is associated with the vibration of the pyridine ring on Brönsted and Lewis acid sites. In addition, the IR band at nearly 1540 cm−1 is due to the adsorption of pyridine coordinated on Brönsted acid sites (Citation30–32). In , the number of acid sites increases in the order of Na-Y < H-Y << Y-CCs < Y-C <Y-D. It should be noted that the order of the L/B ratio is as follows: Y-CCs (1.84)> Y-C (1.62)> Y-D (1). This observation is in good agreement with the results of acid active sites. This phenomenon was proved by experiments; at the same time, the color of Y-CCs after the reaction is gray-white and the color of others after the reaction is black.
2.2. Comparison of benzene alkylation with methanol over different zeolites
The results in show the benzene conversion and desired product selectivity during alkylation with different catalysts at 673 K, 2.0 h−1 WHSV and a benzene–methanol molar ratio of 1/1 using continuous nitrogen flow at atmospheric pressure. Toluene selectivity was in the order Y-B < Y-A < Y-D < Y-CCs <Y-C.
The catalytic performance of the H-Y sample was even worse. The conversion of benzene was nearly 0.1 times that of the Y-C catalyst. The reason may be that the activity of the H-Y catalyst was activated at 823 K (Citation28). The Na-Y catalyst has no activity attributed to any acid site in . Fortunately, over Y-C, the total selectivity of toluene and xylene reached 96.9%, the selectivity of toluene was 87.7% and the benzene conversion also reached 43.9%. The total selectivity of toluene and xylene, the selectivity of toluene and benzene conversion over Y-CCs were just 97.9%, 86.4% and 42.6%, respectively. Hence, experimental results clearly indicate that AC and CA treatment improved the unique framework. This helps to increase benzene conversion and selectivity of toluene. AC and CA ion exchange in the zeolites has a significant role in activating the catalysts, which together with the acidic sites of Y produce the best acidic environment. Overall, the results showed that most of Cs2O entered the channels in Y and covered some of the acid sites. Because Cs2O has high basicity, it is preferentially attracted to strong acid sites, thus preventing further alkylation. In addition, metal oxide can narrow the channels, which prevents further alkylation and can suppress the quantity of coke, which extends the service life of the catalyst. All the changes to Na-Y helped to improve the selectivity of toluene considerably. Therefore, the modified Y-CCs showed good catalytic performance.
3. Conclusions
We investigated benzene alkylation with methanol as an alkylating agent over Y-CCs for the selective formation of toluene and xylene, particularly toluene. We can draw the following conclusions from our results. The activity of Y-C with Cs2O at concentrations of 5% was effective for the alkylation of benzene with methanol by changing the number of acid sites and the pore structure. The total selectivity of toluene and xylene, the selectivity of toluene and benzene conversion were just 97.9%, 86.4% and 42.6%, respectively. Meanwhile, Cs2O also improved the stability of the catalyst significantly. The drawback is the stability of the Y-CCs catalyst improved but the selectivity of toluene slightly reduced in comparison with Y-C.
Disclosure statement
No potential conflict of interest was reported by the authors.
Notes on contributors
Peng Dong a doctoral candidate in chemical engineering from Lanzhou University of Technology. He has carried out research projects in catalytic hydrogenation. He has 4 years of teaching experience as a lecturer. He has 10 research papers in various international journals. He is currently working as lecturer of Lanzhou petrochemical college of vocational technology.
Zeyu Li is an undergraduate in Organic chemistry from Lanzhou University.
Xiaorui Wang graduated with master's degree in chemical engineering from Lanzhou University of Technology. She has 5 years of teaching experience as a lecturer. She has 5 research papers in various international journals. She is currently working as lecturer of Lanzhou petrochemical college of vocational technology.
Hongfei Yun a doctoral candidate in chemical engineering from Lanzhou University of Technology. He has 3 research papers in various international journals.
Guixian Li graduated with Ph.D. degree from Lanzhou Institute of Chemical Physics. He has carried out research projects in catalytic hydrogenation, green catalysis, Heteropoly acid, et al. Current Lanzhou University of Technology department director, chemical industry leader in Lanzhou. He is currently working as professor of Lanzhou University of Technology.
Additional information
Funding
References
- Bruijnincx, P.C.A.; Weckhuysen, B.M. Angew. Chem. Int. Ed. 2013, 52, 11980–11987. doi: 10.1002/anie.201305058
- Lin, Z.; Nikolakis, V.; Ierapetritou, M. Ind. Eng. Chem. Res. 2014, 53, 10688–10699. doi: 10.1021/ie402469j
- Zhang, Q.; Tan, J.; Wang, T.; Zhang, Q.; Ma, L.; Qiu, S.; Weng, Y. Fuel. 2016, 165, 152–158. doi: 10.1016/j.fuel.2015.10.071
- Wang, L.; Lei, H.; Bu, Q.; Ren, S.; Wei, Y.; Zhu, L.; Zhang, X.; Liu, Y.; Yadavalli, G.; Lee, J.; Chen, S.; Tang, J. Fuel. 2014, 129, 78–85. doi: 10.1016/j.fuel.2014.03.052
- Collias, D.I.; Harris, A.M.; Nagpal, V.; Cottrell, I.W.; Schultheis, M.W. Ind. Biotechnol. 2014, 10, 91–105. doi: 10.1089/ind.2014.0002
- Green, S.K.; Patet, R.E.; Nikbin, N.; Williams, C.L.; Chang, C.C.; Yu, J.; Gorte, R.J.; Caratzoulas, S.; Fan, W.; Vlachos, D.G.; Dauenhauer, P.J. Appl Catal. B. 2016, 180, 487–96. doi: 10.1016/j.apcatb.2015.06.044
- Hu, H.L.; Zhang, Q.F.; Cen, J.; Li, X.N. Catal. Lett. 2015, 145, 715–722. doi: 10.1007/s10562-014-1458-3
- K.Saxena, Sandeep; Viswanadham, Nagabhatla. Enhanced catalytic properties of mesoporous mordenite for benzylation of benzene with benzyl alcohol. Applied Surface Science. 2017, 392, 384–390. doi: 10.1016/j.apsusc.2016.09.062
- Kaeding, W.W. J. Catal. 1988, 114, 271–276. doi: 10.1016/0021-9517(88)90030-9
- Adebajo, M.O.; Long, M.A. Catal. Commun. 2003, 4, 71–76. doi: 10.1016/S1566-7367(02)00259-5
- Tan, W.; Liu, M.; Zhao, Y.; Hou, K.; Wu, H.; Zhang, A.; Liu, H.; Wang, Y.; Song, C.; Guo, X. Microporous Mesoporous Mater. 2014, 196, 18–30. doi: 10.1016/j.micromeso.2014.04.050
- Ding, W.; Cui, Y.Y.; Li, J.J.; Yang, Y.Q.; Fang, W.P. RSC Adv. 2014, 4, 50123–50129. doi: 10.1039/C4RA07918C
- Zhang, Y.Y.; Li, Y.F.; Chen, L.; Au, C.T.; Yin, S.F. Catal. Commun. 2014, 54, 6–10. doi: 10.1016/j.catcom.2014.05.013
- der Mynsbrugge, J.V.; Visur, M.; Olsbye, U.; Beato, P.; Bjørgen, M.; Van Speybroeck, V.; Svelle, S. J. Catal. 2012, 292, 201–212. doi: 10.1016/j.jcat.2012.05.015
- Xu, W.Y.; Miller, S.J.; Agrawal, P.K.; Jones, C.W. Catal. Lett. 2014, 144, 434–438. doi: 10.1007/s10562-013-1167-3
- Palomares, A.E.; Eder-Mirth, G.; Lercher, J.A. J. Catal. 1997, 168, 442–449. doi: 10.1006/jcat.1997.1685
- Zhu, Z.R.; Chen, Q.L.; Xie, Z.K.; Yang, W.; Li, C. Microporous Mesoporous Mater. 2006, 88, 16–21. doi: 10.1016/j.micromeso.2005.08.021
- Llopis, F.J.; Sastre, G.; Corma, A. J. Catal. 2004, 227, 227–241. doi: 10.1016/j.jcat.2004.07.014
- Zheng, S.; Heydenrych, H.R.; Jentys, A.; Lercher, J.A. J. Phys. Chem. B. 2002, 106, 9552–9558. doi: 10.1021/jp014091d
- Choi, M.; Cho, H.S.; Srivastava, R.; Venkatesan, C.; Choi, D.H.; Ryoo, R. Nat. Mater. 2006, 5, 718–723. doi: 10.1038/nmat1705
- Chen, N.Y.; Kaeding, W.W.; Dwyer, F.G. J. Am. Chem. Soc. 1979, 101, 6783. doi: 10.1021/ja00516a065
- Takeuchi, M.; Hidaka, M.; Anpo, M. J. Hazard. Mater. 2012, 237–238, 133–139. doi: 10.1016/j.jhazmat.2012.08.011
- Gobin, O.C.; Reitmeier, S.J.; Jentys, A.; Lercher, J.A. Microporous Mesoporous Mater. 2009, 125, 3–10. doi: 10.1016/j.micromeso.2009.01.025
- Li, G.X.; Dong, P.; Ji, D.; Xu, Y.; Li, Y.; Mu, R. Solid State Sciences. 2013, 23, 13-16. doi: 10.1016/j.solidstatesciences.2013.06.003
- Wang, G.R. Catalyst and Catalysis (M), Dalian University of Technology Press: Dalian, 2015; pp 95–96.
- Kirschhock, C.E.; Ravishankar, R.; Verspeurt, F.; Grobet, P.J.; Jacobs, P.A.; Martens, J.A. J. Phys. Chem. B. 1999, 103, 4965–4971. doi: 10.1021/jp990297r
- Barthos, R.; Bánsági, T.; Zakar, T.S.; Solymosi, F. J. Catal. 2007, 247, 368–378. doi: 10.1016/j.jcat.2007.02.017
- Venuto, P.B.; Landis, P.S. Organic Catalysis over Crystalline Aluminosilieates, Petroleum Chemical Press: New York and London, 1968; Vol. 40.
- Zu, Y.; Qin, Y.C.; Gao, X.H.; Liu, H.; Zhang, X.; Zhang, J.; Song, L. Applied Catalysis B: Environmental. 2017, 203, 96–107. doi: 10.1016/j.apcatb.2016.10.008
- Wang, F.; Xu, X.L.; Sun, K.P. React. Kinet. Catal. Lett. 2008, 93, 135–140. doi: 10.1007/s11144-008-5218-5
- Jaehong, L.; Seong, L.S.; Jackie, Y.Y. Chem. Commun. 2010, 46, 806–808. doi: 10.1039/B917986K
- Hu, H.L.; Lyu, J.H.; Wang, Q.T.; Zhang, Q.F.; Cen, J.; Li, X. N. RSC Adv. 2015, 5, 32679–32684. doi: 10.1039/C5RA03048J