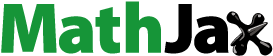
Abstract
The flowability of biomass is an indicator of how amenable biomass is to handling. The flowability measurements are often determined with empirical or tertiary experiments. This status quo impedes employing engineering principles to advance the design and operation of biomass handling systems. It is imperative to establish an experimental protocol minimizing empirical aspects of flowability characterization to account for the variability of biomass. This study demonstrates the operational principles of the large chamber cubical triaxial tester and the procedure of triaxial tests to quantify bulk flow behaviors of two milled biomass feedstocks, namely corn stover 2 mm (CS) and Douglas fir 1 mm (DF). The Mohr-Coulomb (MC), Drucker-Prager (DP) and modified Cam-Clay (mCC) models are calibrated for both biomasses. Analysis indicates that CS will exhibit a cohesive flow with a larger cohesion coefficient of MC (3.8 ± 3.5 kPa) than DF (0.42 ± 0.9 kPa) and a larger d value of DP (6.9 kPa) than DF (0.0 kPa), respectively. CS exhibits a higher spring-back index of mCC (0.39 ± 0.05) than DF (0.27 ± 0.05) also suggesting handling issues, which agrees with the experiences in the industry. This study demonstrates the capability of a CTT in a quantitative investigation of biomass handling characteristics.
Introduction
Unreliable handling of biomass is prevalent in plants using milled biomass. Such inconsistency in handling raises issues in logistics and reduces the on-stream time of downstream unit operations. Therefore, avoiding biomass handling issues is critical in achieving reliable operations of plants using biomass feedstock in facilities such as integrated biomass refineries.
Milled biomass is a bulk particulate material (bulk solid) that exhibits unique mechanical responses that differ from solids, liquids, or gases. The flow behavior of bulk particulate material manifests mechanical interactions between the particulate material and handling equipment [Citation1,Citation2]. The mechanical properties of milled biomass are much more complex than most powders and crushed minerals due to the effects of moisture and temperature on the rheological behavior of individual particles [Citation3].
Combined effects of material properties and handling equipment should be considered in the characterization protocol of the flow behavior of milled biomass. In other words, the mechanical properties of milled biomass should be determined with minimal confounding effects of the characterization instrument. The status quo requires empirical approaches in the design and operation of biomass handling equipment to overcome confounded characterization data.
For example, with a shear-cell type instrument, biomass mechanical properties of bulk biomass are determined with a sample chamber with a rigid wall. The rigidity of the lateral wall interacts with the test specimen during the consolidation and shearing. As a result, the determined bulk mechanical properties include such interaction and thus confounding the data. The resulting bulk biomass property will be directly applicable only to the region of a handling system with a similar die-wall interaction. On the other hand, applying the measured properties to handling systems with different die-wall interactions will lead to a design or an operation parameter that will not ensure the intended handling behavior.
Further, bulk biomass is prone to a larger deformation than other types of bulk particulate material. During a shear test, the imposed lateral shear deformation induces misalignment of the direction in which the normal consolidation stress of bulk biomass is applied. This misalignment is often negligible, but it can become too large to ignore for bulk biomass. These interferences may result in an inaccurate determination of material strength [Citation4].
The inadequate characterization of biomass flow properties should be resolved first by investigating the applicability and implications of analytical biomass flow models. For example, ‘yield’ and ‘flow/failure’ of bulk material are not representing the same mechanical implication. Jenike's flow factor [Citation5] uses the unconfined yield stress of bulk material as a basis of flow condition, which is the yield strength of a bulk solid at an exposed and traction-free surface. More formally, this is defined as major principal stress at which an unconfined bulk material yields in shear. Following this conjecture, the determination of the unconfined yield stress of biomass is a critical step in characterization protocols. However, because of the mismatch between the definition of the yield and failure, the determined value may or may not indicate the conditions indicating biomass flow. Furthermore, because of the effect of a rigid wall in shear cells, the determined yield stress at lower consolidation stress may deviate from the accurate unconfined yield stress. Considering that the consolidation of biomass by self-weight represents low-pressure consolidation, this is a significant challenge to address in biomass storage and handling.
Measurement of true properties will lead to more accurate predictions of biomass behavior in biomass storage and handling by enabling engineering practices based on the first principle. The first-principle-based engineering becomes possible when the fundamental bulk biomass properties can be determined without interferences from the biomass and wall interactions. Therefore, it is imperative to develop protocols that can characterize the mechanical properties of biomass with minimal confounding effects.
In addition, mechanical properties representing the flow characteristics of milled biomass are defined by the parameters of a particular biomass flow model. In turn, the theoretical framework of the biomass flow model determines the calibration procedures of the set of mechanical properties to be determined. In addition to the accuracy and repeatability, the validity of an experimental protocol and the instrument reflecting the correct conceptual and theoretical backgrounds play a critical part in the calibration of a biomass flow model [Citation4,Citation6]. Because the widely used Jenike's approach [Citation5,Citation7] is based on the Mohr-Coulomb model, which is a simpler model of the kind, the biomass flow characterization using a type of shear-cell prevents the application of other constitutive models. Furthermore, the lack of an appropriate characterization instrument limits the possibility of using other constitutive models because of an inadequate characterization protocol to determine model parameters.
Overall, the current issue of unreliable biomass handling is equally contributed by the limitation of the characterization method and inappropriate analytical biomass flow models. Observed inconsistent biomass flow suggests that the current engineering approach underestimates the strength gain of stored biomass, overestimates shear stress developing during handling, or combines both incorrect predictions. The interference of the characterization instrument with the measured responses of bulk biomass exacerbates issues in storage and handling due to the unaccounted variability and environmental factors. Therefore, there exists an urgent need to characterize the mechanical behavior of biomass free from such confounding effects of a characterization instrument.
This study aims to address this challenge by demonstrating the advantage of using a true triaxial tester in characterizing bulk biomass flow behavior. We developed a cubical triaxial tester (CTT) with a sample chamber appropriately large for bulk biomass using flexible pressure application membranes. The use of a flexible membrane minimizes the constraints of a rigid wall during tests. In addition, because of the cubical shape of the test specimen, the application of stress and measurement of strain is maintained in the principal directions. This configuration enables an unambiguous procedure to determine the material parameters of biomass flow models based on the first principles [Citation6,Citation7]. Utilizing a CTT makes calibration of governing models for mechanical behavior of bulk biomass possible, including the Drucker-Prager model or critical-state theory.
This study demonstrates how the large chamber CTT is used to characterize compressive and shear responses of milled biomass samples. The experimental data are used in determining the parameters of three elasto-plasticity models, i.e. Mohr-Coulomb, Drucker-Prager and modified Cam-Clay models. This paper discusses the advantage of using the large chamber CTT in characterizing bulk biomass flow responses and determining parameters of bulk biomass flow models. Investigating multiple governing models of biomass flow provides valuable insights into the nature of handling characteristics of biomass.
Methods and materials
Materials
For this study, corn stover and Douglas fir samples are considered. Corn stover is a crop residue that has been actively studied as a potential source of alternative biorenewable material. Corn stover is estimated to constitute more than three-fourths of primary crop residues profitable to collect [Citation8,Citation9]. However, the difficulty in handling corn stover is one of the obstacles in establishing corn stover as profitable and reliable biomass. Douglas fir is a common softwood in the Northwest United States, selected as woody biomass known to have better handling characteristics than corn stover.
Dry bales of corn stover from Poweshiek County, Iowa, were procured, debaled by hand, milled and screened with Forest Concept's Crumbler® precision processing equipment resulting in nominal mean particle size (Xgm) of 2 mm. As received, the baled stover is sufficiently dry, and no subsequent drying is needed. Similarly, Douglas fir fuel-grade chips were procured, then milled, screened and dried with Forest Concept's Crumbler® precision processing equipment, resulting in nominal mean particle size (Xgm) of 1 mm. Particle size distributions of milled biomass samples are shown in , which shows distinct particle size distributions between corn stover 2 mm (CS C2mm) and Douglas fir 1 mm (DF C1mm) and little variances within respective sample sets.
The particle density was determined with a Gas pycnometer using dried air as the medium. The particle density values of corn stover 2 mm and Douglas fir 1 mm are 1370 ± 160 kg/m3 and 1550 ± 130 kg/m3, respectively (error represents the standard deviation). The loose bulk density values of corn stover 2 mm and Douglas fir 1 mm are 137 ± 3 kg/m3 and 191 ± 3 kg/m3, respectively (ISO Small container [Citation10], n = 4, and error represents the standard deviation). For the moisture contents of corn stover 2 mm and Douglas fir 1 mm are 7.3 ± 0.3% and 10.3 ± 0.5%, respectively (n = 9 for each material).
Cubical triaxial tester
In this study, a set of triaxial tests is conducted to characterize milled biomass flowability using a CTT. A CTT is a true triaxial tester using a flexible pressure membrane, minimizing the confounding interference of bulk mechanical behavior of a test specimen [Citation11–15]. Because a CTT uses flexible membranes for the sample holding and applying the pressure, a CTT can minimize confounding effects from the die-wall friction constraints. Using a flexible pressure application membrane helps a CTT determine truer fundamental mechanical properties of bulk biomass compared to measurements from other types of triaxial testers or shear testers.
As the name of the apparatus implies, a CTT has a cubical cavity at the center to install the test specimen. A cubical test specimen is subjected to three orthogonal pressures simulating three principal stresses during the tests. The cubical shape of a test specimen maintains the directions of stress application and corresponding strain responses in the principal directions. As a result, a CTT can apply engineering shear, whose direction coincides with principal directions. Maintained principal stress application and strain measurement allow a CTT to avoid misalignment between the force-displacement measurement directions and a theoretical framework of a constitutive model common in a shear-cell type instrument [Citation4,Citation16]. In addition, a CTT allows the characterization of compressive yield responses, which is critical in calibrating Cap-plasticity models. In the long run, using a CTT will help overcome the limits of conventional elasto-plasticity biomass flow models by including the consideration of anisotropy in three dimensions.
A CTT scaled for fine particulates was developed at Penn State and has been successfully used to characterize fundamental mechanical properties for the last three decades [Citation8,Citation16–21]. The Penn State CTT uses a cubical test specimen of edges of 50 mm. Although this sample size suffices for investigating typical particulate materials, milled biomass tends to have particles larger than one-sixth [Citation12,Citation22–25] of the sample chamber for well-graded material or one-tenth for other particulate materials [Citation12], which are the suggested limits of particle size without interferences of the sample size with the bulk behavior.
To determine a minimal appropriate sample chamber size, bulk densities of different biomass feedstock samples are determined with containers of varying sizes (). Bulk density values of biomass feedstock samples were measured with containers of different volumes. This observed difference of the bulk density values is contributed to the container dimension, as shown in Figure 3.
Therefore, a new CTT with a larger sample size (a cube with an edge of 250 mm, ) was developed by Forest Concepts LLC and Penn State. The new biomass-scale CTT can accommodate and characterize commonly used processed biomass feedstock by any biorefinery facility with the minimal confounding effect of bulk sample size. It should be noted that the initial bulk density of CTT samples differs from the loose bulk density determined with an ISO small container [Citation10]. When initial bulk density was determined using the dimension and weight of cubical samples prepared for triaxial tests, the initial bulk density values of corn stover 2 mm and Douglas fir 1 mm CTT samples are 164 ± 7 kg/m3 and 188 ± 9 kg/m3, respectively (n = 9 for each material and error represents the standard deviation). The initial bulk density of the CTT sample is thought to be closer to the bulk density of the bulk biomass in the real world.
Figure 2. Biomass-scale cubical triaxial tester developed by Forest Concepts, LLC and Pennsylvania State University.
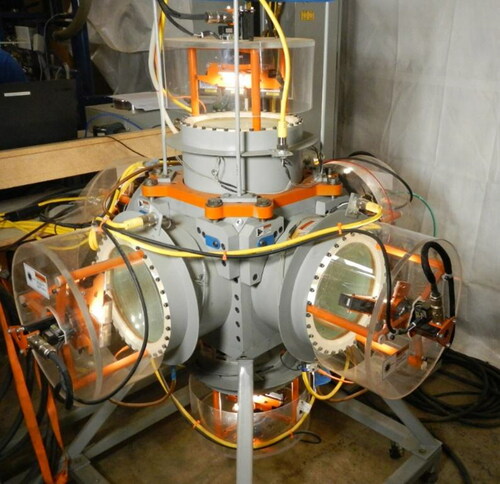
Figure 3. Bulk density values of biomass feedstock samples measured with containers of different volumes. ISO small and ISO large container volumes are 0.0046 m3 and 0.0326 m3, respectively. Containers (200, 250, 300 and 400 mm) are cubes represented by the length of edges, and the volumes of these containers are 0.008 m3, 0.016 m3, 0.027 m3 and 0.064 m3, respectively.
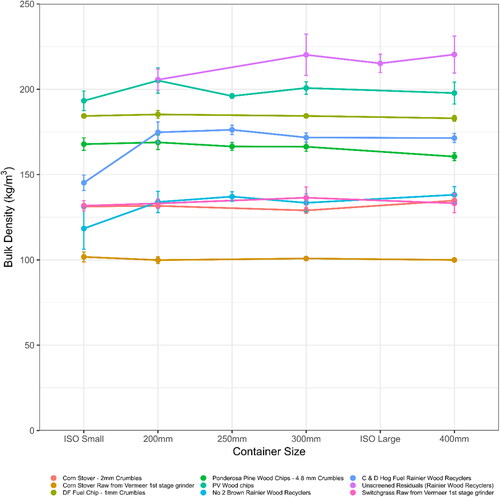
The CTT unit used in this study is specifically designed to address low to medium pressure biomass handling devices such as gravity hoppers and augurs, i.e. pressure levels lower than 125 kPa. It also can test dry material at temperatures up to 120 °C and wet materials up to 75 °C to represent the flowability parameters of materials in the vicinity of dryers and other feedstock preparation equipment.
Triaxial tests
The advantages and versatility of the CTT lie in its reproducibility of the test results and ability to perform triaxial tests employing any proportional stress paths. In this study, two types of triaxial tests are conducted to determine analytical biomass flow model parameters: the hydrostatic triaxial compression (HTC) test and the conventional triaxial compression (CTC) test.
Hydrostatic triaxial compression (HTC) test
The purpose of an HTC test is to measure a compressive response of bulk biomass under isotropic stress conditions, i.e. hydrostatic pressure. The application of isotropic stress in the principal directions is achieved by imposing the same amount of pressure to a cubical test sample is subjected in all three axes directions (). The pure hydrostatic compression state is maintained by controlling the pressure increments to be the same in all three directions. A cubical test sample remains in the hydrostatic condition without shear stress. Thus, the test specimen will not fail throughout a test procedure. The criterion of 'failure' is defined later in the results and discussion section.
Figure 4. Hydrostatic triaxial compression (HTC) test (a) depicts the schematic of isotropic stress condition where and
represent stress in x, y and z directions, respectively, and
and
represent stress increment in x, y and z directions, respectively. (b) The HTC stress paths with three unloading-reloading isotropic stress paths ending with the final unloading. Volumetric strain response to an unloading-reloading isotropic stress path allows the determination of bulk mechanical properties relevant to the hydrostatic compression.
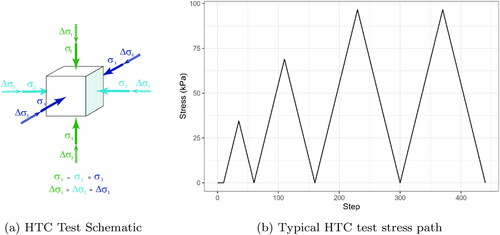
If the bulk biomass is perfectly elastic, the isotropic stress and volumetric strain relationship must exhibit a linear relationship. However, as a particulate system, bulk biomass is not strictly elastic, and the slope of the compression response is continuously changing. Therefore, to measure the bulk modulus of consolidated bulk biomass at a specific pressure level, unloading and reloading are added to the stress paths (), representing consolidation conditions of stored biomass, including the self-weight. In this study, the hydrostatic compression stress is applied at 82.8 kPa/min to measure the quasi-static responses of samples. In addition, from the volumetric recovery under a stress release, the volumetric expansion can be quantified, which is critical in predicting volume change during handling.
Conventional triaxial compression (CTC) test
The CTC test measures the shear and failure response of the test specimen, which are directly related to the flow behavior of bulk biomass. CTC tests induce incremental deviatoric (shear) stress in the test specimen consolidated by a pre-determined isotropic stress (hydrostatic compression) condition. In this study, 34.5, 48.3 and 69.0 kPa were applied as the confining pressure levels reflecting a typical depth of gravity hopper. After the consolidation, the pressure in one axis, usually the vertical direction representing the z axis, increases while horizontal pressures are maintained at the set confining pressure (). The increment of deviatoric stress is maintained until the deviatoric strain exhibits pre-determined failure criteria. In this study, the hydrostatic consolidation stress and deviatoric stress are applied compression stress are applied at 82.8 kPa/min to measure the quasi-static responses of samples.
Figure 5. Conventional Triaxial compression (CTC) test (a) depicts the schematic of isotropic consolidation followed by deviatoric stress in the vertical direction. Here, and
represent stress in x, y and z directions, respectively, and
and
represent stress increment in x, y and z directions, respectively. (b) The CTC stress paths with the consolidation stress of 34.5 kPa (5 psi) followed by two unloading-reloading deviatoric stress paths ending with the final unloading. Deviatoric strain response to an unloading-reloading deviatoric stress path allows the determination of bulk mechanical properties relevant to the shear.
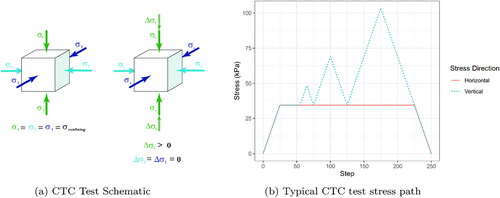
The incremental shear (deviatoric) stress in the vertical direction induces the corresponding shear deformation of the test specimen. Because bulk biomass exhibits a non-linear shear response, it is not feasible to determine shear modulus (G) from the slope of induced shear stress versus strain response. Therefore, unloading-loading deviatoric stress paths () are added, producing closed shear-stress versus shear-strain loops. The overall slope of an unloading-reloading deviatoric stress-strain response represents two times a shear modulus of bulk biomass consolidated at a given hydrostatic pressure.
Results and discussion
Failure criterion relevant to biomass flow
In this study, a set of HTC and CTC tests are used in determining parameters of widely used elasto-plasticity models, namely the Mohr-Coulomb model, Drucker-Prager model and modified Cam-clay model. It should be noted that the conventional definition of ‘yield’ and ‘flow’ of elasto-plasticity theories is not necessarily consistent with the incipient bulk biomass flow. While an incipient flow of bulk biomass indicates an onset of a large deformation followed by a continuous movement of bulk biomass, a ‘yield’ of elasto-plastic bulk biomass defines the level of stress or strain that accompanies irrecoverable deformation. The deformation beyond the yield limit of a material is plastic and called plastic flow [Citation11,Citation26]. The customary use of ‘plastic flow’ is not consistent with the intended meaning of the flow of bulk biomass.
Instead, a failure of the bulk biomass sample, indicated by a sudden and discontinuous increase in the shear strain, is a more appropriate indicator of the stress-strain state representing the incipient state of a continuous movement of bulk biomass. However, from CTC tests with corn stover 2 mm and Douglas fir 1 mm, no distinct failure is observed () with the consolidation of bulk biomass comparable to the consolidation by self-weight. Therefore, an axial strain of 7% was used as the criterion of the incipient flow of bulk biomass samples following ASTM Standard D7181 [25] and Kamath and Puri [Citation27]. The choice of the axial strain of 7% is made based on the observations that the failure of bulk particulate specimen ranges from 5% to 12% [Citation13,Citation17,Citation18]. It should be noted that the 7% of axial strain corresponds to the deformation of 1.75 mm of a 250 mm-cubical triaxial test specimen.
Rather than a discrete failure, shear hardening is observed in many cases, especially at a larger deviatoric strain range (). The shear hardening is more distinct in corn stover 2 mm, which indicates that a higher level of additional shear stress is required to maintain the consistent increase in shear strain. Shear hardening is an indicator of handling issues such as jamming or arching of the gravity flow because such biomass handling equipment relies on shear stress development by self-weight.
Determined failure shear stresses of corn stover 2 mm and Douglas fir 1 mm show increasing trends when the confining pressure increases (). The increase of failure stress of Douglas fir 1 mm exhibits a linear trend, whereas the increase of failure stress of corn stover 2 mm appears to follow a logarithmic curve. The non-linear behavior of corn stover 2 mm suggests that the mechanical behavior may not conform to fundamental assumptions of the Mohr-Coulomb or Drucker-Prager model.
Figure 7. Failure shear stress trend of corn stover 2 mm (CS C2mm) and Douglas fir 1 mm (DF C1mm) at air-dried moisture content. A box and whiskers represent the first, second, third, and fourth quantiles with a mean value shown as a solid point. Data points outside the first or fourth quantile represent outlier.
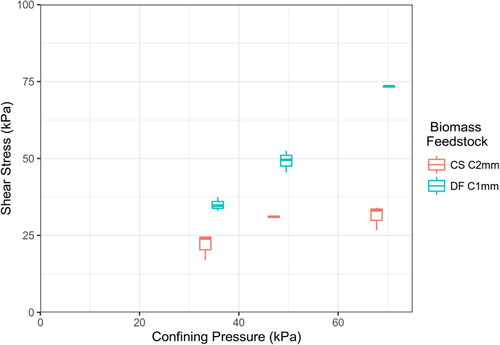
Biomass flow model: Mohr-Coulomb model
Mohr-Coulomb model is the basis of widely used Jenike's approach in predicting a hopper flow [Citation5,Citation28,Citation29]. The Mohr-Coulomb model assumes that bulk material flows when the shear stress exceeds the Mohr-Coulomb failure envelope representing the plane of failure.
In the Mohr-Coulomb model (1), a flow of bulk material is defined by a straight line in the normal stress () and shear stress (
) plane with a slope of
which is an internal angle of friction, and the shear stress intercept of
which is cohesion coefficient.
(1)
(1)
Conventionally, a Mohr-Coulomb failure envelope is determined by estimating a common tangent line of multiple Mohr circles determined from shear test results. From the results of CTC tests with different consolidation stress levels, multiple Mohr circles can be obtained. A common tangential line representing a Mohr-Coulomb failure envelope can be determined using a pair of Mohr circles of two tests with different consolidation pressures. shows obtained Mohr-Coulomb failure envelopes of corn stover 2 mm and Douglas fir 1 mm.
Figure 8. Mohr-Coulomb failure envelopes of air-dried corn stover 2 mm and Douglas fir 1 mm with consolidation stress levels (represented as normal stress) of 34.5, 48.3 and 69.0 kPa, respectively. Red lines demonstrate Mohr-Coulomb failure envelopes that are common tangential lines of two Mohr circles.
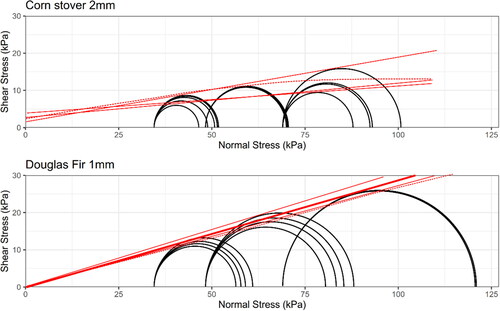
As shown in , the experimental variation can be accounted for by constructing multiple common tangential lines of all combinations of two Mohr circles from different consolidation conditions. The cohesion coefficient () from the intercept of
axis and the angle of internal friction from the slope values of corn stover 2 mm and Douglas fir 1 mm show considerable variation (). From the positive angles of internal friction of corn stover 2 mm and Douglas fir 1 mm, it is confirmed that the strength of bulk particulate increases proportionally to the degree of compression, which is a fundamental assumption of the Mohr-Coulomb model. However, applying the Mohr-Coulomb model to the bulk biomass does not appear to always conform with the linearity assumption as evidenced by corn stover 2 mm. On the other hand, the non-linear strengthening of corn stover 2 mm can be accounted for by considering the variability of the determined Mohr-Coulomb model parameters.
Figure 9. Mohr-Coulomb model parameters of air-dried corn stover 2 mm (CS C2mm) and Douglas fir 1 mm (DF C1mm) as box plots. A box and whiskers represent the first, second, third and fourth quantiles with a mean value shown as a solid point. Data points outside the first or fourth quantile represent outlier. The smaller angle of internal friction value of corn stover 2 mm suggests that corn stover 2 mm gains less strength than Douglas fir 1 mm. However, the larger variation of corn stover 2 mm suggests potential issues in handling. On the other hand, the close to zero cohesion coefficient of Douglas fir 1 mm indicates a good handling characteristic.
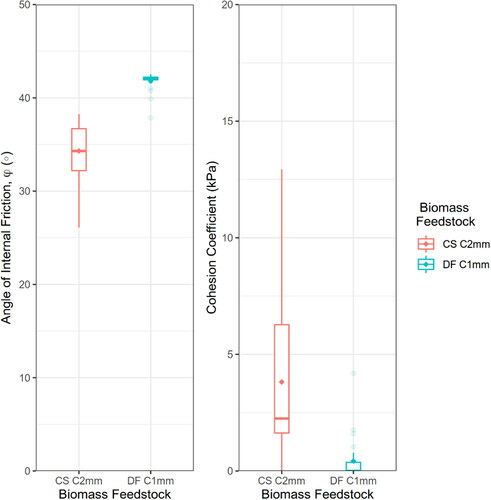
Although Coulomb had not extended his theory to the tensile failure [Citation30], the Mohr-Coulomb model assumes that the compressive and tensile strength are equivalent in magnitude when a material fails due to shear. This assumption should be further substantiated. Finally, because Jenike's approach relies on the determination of unconfined yield stress, the change in the angle of internal friction near the zero-consolidation state is critical information to determine. Although no noticeable change in the angle of internal friction is observed in , this should be further validated with CTC tests with zero consolidation.
Biomass flow model: modified Drucker-Prager model
The failure envelope of the Drucker-Prager model is defined on a plane with the hydrostatic stress axis and deviatoric stress axis [Citation11,Citation26,Citation31,Citation32]. As a result, the Drucker-Prager model comprises a straight failure envelope similar to the Mohr-Coulomb model. In a CTC test, the hydrostatic stress corresponds to the consolidation stress, and the additional stress in one axis corresponds to the deviatoric stress.
In a shear-cell type tester, the axis along which a consolidation actuator moves differs from transverse axes, along which the test specimen is passively constrained and lateral movement is imposed. Similarly, a conventional cylindrical triaxial tester, such as those commonly used in soils analysis, cannot fully isolate the principal stresses and strains. One of the advantages of the CTT over shear-cell and cylindrical triaxial type testers is that the consolidation stress is maintained at the exact same level for all three principal axes throughout the test, and the transverse deformations of the test specimen are constantly measured. This configuration of CTT makes it possible to control stresses, measure strains in principal directions, and thus quantify complete three-dimensional stress-strain responses. The complete principal stress-strain relationship makes it straightforward to determine Drucker-Prager model parameters from the CTT test data.
The linear Drucker-Prager envelope is determined from failure stresses corresponding to hydrostatic stresses, the pre-determined consolidation pressure levels. The straight Drucker-Prager envelope is expressed as an extended von Mises yield criterion as follows:
(2)
(2)
where
is the second invariant of a deviatoric tensor and
is the first invariant of a Cauchy stress tensor,
is the slope of a failure envelope and
is the intercept of a failure envelope. Considering that the
represents the failure of biomass, i.e. the onset of flow,
and
is analogous to the angle of internal friction (
) and the coefficient of cohesion (
) of the Mohr-Coulomb failure envelope.
From the results of CTC tests with different consolidation stress levels, the and
at failure can be directly estimated using principal stresses, which are shown in . Supposedly, these consolidation pressure levels represent the expected pressure developing at the bottom of stored bulk biomass due to the self-weight.
Figure 10. Failure deviatoric stress and hydrostatic stress of corn stover 2 mm (CS C2mm) and Douglas fir 1 mm (DF C1mm) at air-dried moisture content. A box and whiskers represent the first, second, third and fourth quantiles with a mean value shown as a solid point.
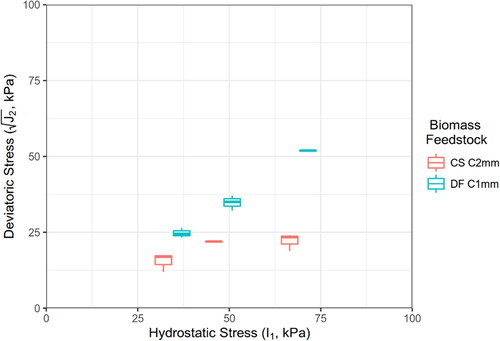
From a linear relationship between and
at failure,
and
can be obtained as parameters of the Drucker-Prager yield envelope from a linear regression analysis. illustrates the obtained Drucker-Prager envelopes of corn stover 2 mm (
and Douglas fir 1 mm (
).
Figure 11. Drucker-Prager model parameters of air-dried corn stover 2 mm (CS C2mm) and Douglas fir 1 mm (DF C1mm). The smaller β of corn stover 2 mm suggests that corn stover 2 mm gains less strength than Douglas fir 1 mm. However, the smaller R2 value of corn stover 2 mm suggests potential issues in handling. On the other hand, the close to zero d value of Douglas fir 1 mm indicates a good handling characteristic. These observations are consistent with the Mohr-Coulomb parameters.
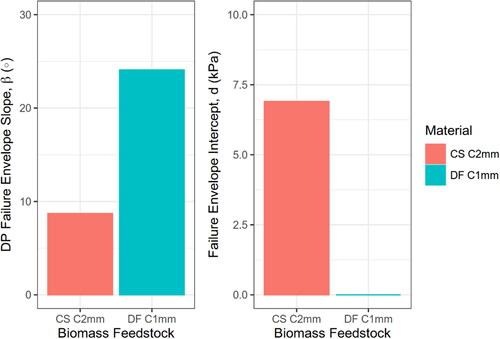
The Drucker-Prager model is considered more rigorous than the Mohr-Coulomb model in terms of how a failure stress state is described under a three-dimensional stress state. On the other hand, the Drucker-Prager model postulates that the relationship between the compression and material strength is linear, similar to the Mohr-Coulomb model.
As shown in and by a higher value, bulk Douglas fir 1 mm appears to conform to the linear relationship between consolidation pressure and strength. However, the observed trend of failure stress and the moderate
value suggest that bulk corn stover 2 mm may have a non-linear relationship between the consolidation pressure and strength, consistent with the Mohr-Coulomb model.
In terms of the predicted bulk flow behavior from the Drucker-Prager model parameters, Douglas fir 1 mm is found to have larger β (24.1°) than corn stover 2 mm (β = 8.7°). A larger β value suggests that the Douglas fir 1 mm will gain more strength than corn stover 2 mm under the same amount of hydrostatic compression condition. This observation is consistent with the Mohr-Coulomb model. Similarly, the d value of Douglas fir 1 mm is 0.0 kPa, which indicates a cohesionless flow behavior. On the other hand, the d value of corn stover 2 mm is 6.9 kPa, which suggests a cohesive flow behavior prone to handling issues. Overall, The Drucker-Prager model and Mohr-Coulomb model indicate similar flow behavior for both materials. However, the Drucker-Prager model can describe a more complex three-dimensional stress state that is advantageous in modeling and simulating handling behaviors in realistic biomass handling equipment.
Biomass flow model: modified Cam-Clay/cap model
Modified Cam-Clay model [Citation11,Citation26,Citation33,Citation34] is based on the critical-state theory [Citation34,Citation35], assuming that bulk particulate under shearing reaches a critical state at the failure. The critical state is described as a constant volume of a test specimen while it is being sheared. The modified Cam-Clay model assumes a non-linear response of the shear-volume relationship until it reaches the critical state. The modified Cam-Clay model uses a void ratio instead of the volumetric strain. Because the void ratio does not involve the directionality of deformation, the presumed anisotropic behavior of biomass does not interfere with the failure envelope determination.
The modified Cam-Clay model comprises a straight critical-state line on the plane defined with the hydrostatic stress () axis and shear stress (deviatoric stress
) axis. In the modified Cam-Clay model, the yield locus representing the critical-state line
(3)
(3)
where the slope of the critical-state line (M) is determined from failure stress in deviatoric stress (q) corresponding to hydrostatic stress (p), and hydrostatic stress corresponding to the intersection of the yield loci with the p axis (
). Because the cubical triaxial test results are recorded in the principal stresses and corresponding principal strains, EquationEquation (3)
(3)
(3) can be directly used in the determination of the critical-state line (M). represents the CTC test results shown in the deviatoric stress (q) versus q/p plane for this purpose.
Figure 12. Conventional Triaxial Compression (CTC) test results in volumetric strain versus q/p (ratio between deviatoric stress, q, and hydrostatic stress, p) of air-dried corn stover 2 mm (CS C2mm) and Douglas fir 1 mm (DF C1mm).
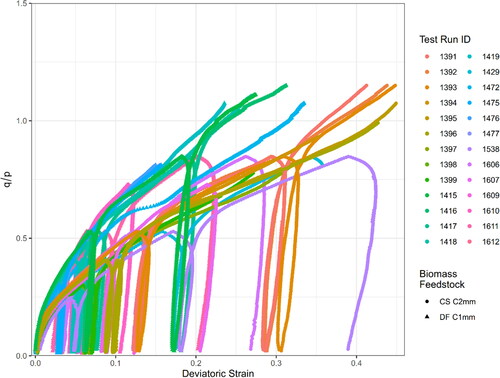
In , neither corn stover 2 mm nor Douglas fir 1 mm reaches a critical state. On the contrary, both biomass samples show a continued increase in q/p, whereas shear hardening is observed, suggesting issues in handling. Consistent with the Mohr-Coulomb and Drucker-Prager model parameters, the deviatoric strain of 7% was used as the failure criterion to determine modified Cam-Clay model parameters.
The slope of the critical-state line () can be obtained from CTC test results, using the regression analysis with the data from consolidation pressure (
and deviatoric stress
at failure (). From this relationship, the M of corn stover 2 mm is 22.4° (
) and Douglas fir 1 mm is 51.8° (
) (). This trend is consistent with the angle of internal friction of the Mohr-Coulomb model and β of the Drucker-Prager model.
The modified Cam-Clay model includes a compressive yield that accounts for biomass plastic deformation before reaching the yield strength. The compressive yield is described by the cap, which is defined by incremental volumetric strain on the yield cap.
(4)
(4)
where
is the initial void ratio,
is the compression index and
is the spring-back index.
In terms of determining the yield cap of the modified Cam-Clay model, the compression index () and spring-back index (
) can be determined from HTC test results representing the relationship between the void ratio (e) and the isotropic stress (
). The compression index (
) is determined from the slope of the hydrostatic consolidation line of the
plane. The spring-back index (
) is determined from the slope of the hydrostatic swelling line of the
plane. shows the change in the void ratio due to the hydrostatic compression illustrating the log-normal relationship for both corn stover 2 mm and Douglas fir 1 mm.
Figure 13. Hydrostatic Triaxial Compression test results in void ratio versus (Isotropic Stress (kPa)) versus the void ratio of air-dried corn stover 2 mm and Douglas fir 1 mm.
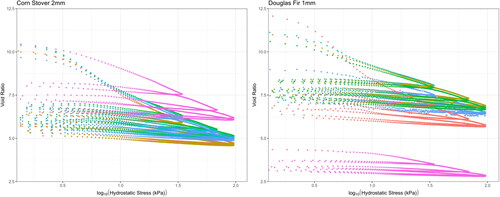
The compression index () of corn stover 2 mm (2.57 ± 0.81) is larger than Douglass Fir 1 mm (1.74 ± 0.57). The spring-back index (κ) of corn stover 2 mm (0.39 ± 0.05) is larger than Douglass fir 1 mm (0.27 ± 0.05) (). Considering that compression and spring-back indices are determined with the void ratio (e), larger compression and spring-back indices of corn stover 2 mm predict more compression and expansion over the same amount of hydrostatic pressure change. This trend means that corn stover 2 mm will exhibit a larger volume change under varying hydrostatic pressure. This observation corroborates the bulk modulus values of K (), indicating that bulk corn stover 2 mm is more volumetrically compliant than bulk Douglas fir 1 mm. An extensive volume fluctuation indicates potential handling issues, e.g. the expansion of volume due to the onset of gravity discharge will be prone to arching and hinder the establishment of the flow.
Figure 14. Modified Cam-Clay parameters of air-dried corn stover 2 mm and Douglas fir 1 mm: (a) Slope of the critical-state line, which represents the failure envelope, (b) bulk modulus (K), (c) compression index (l) and (d) spring-back index (k).
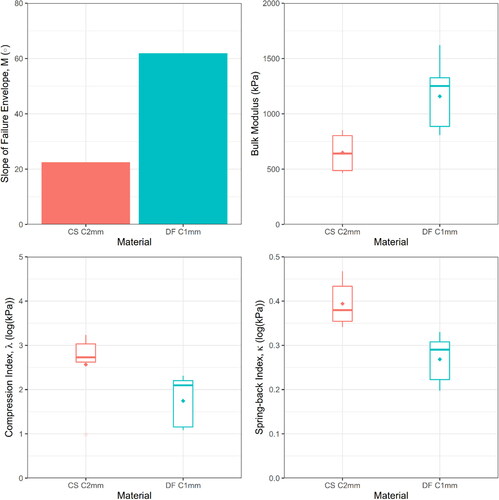
The yield cap will expand as the isotropic stress on the bulk biomass sample increases. The location where the critical-state line and the expansive cap meets and the shape of the cap is defined with the void ratio () at the unit pressure, the shear modulus (
), and the void ratio at the interaction of cyclic loading-unloading during the hydrostatic compression test. The shear modulus (
) can be determined from cyclic loading during CTC tests, which provide direct shear-strain responses to the applied shear stress (
).
Overall, all three models commonly suggest that the corn stover 2 mm is more prone to handling issues than Douglas fir 1 mm. This result coincides with the observations in the industry, i.e. corn stover is a more difficult material to handle, and issues like rat-holing are common. On the other hand, Douglas fir 1 mm is easy to handle reactor-ready biomass feedstock.
More specifically, higher cohesion values of corn stover 1 mm related coefficients appear to indicate the handling issue in the Mohr-Coulomb and Drucker-Prager model. The modified Cam-Clay model provides an additional origin of handling issues from the perspective of the volume fluctuation during handling. In other words, corn stover 2 mm exhibits larger volumetric compression and expansion than Douglas fir 1 mm, which predicts a potential blockage of a flow path at the onset of flow, which will interfere with the space needed to be cleared for the successive flow of corn stover.
To validate the performance of those constitutive biomass flow models quantitatively, it is necessary to compare the predictions of the biomass flow out of handling equipment with experimental results. Such comparisons can be achieved by modeling and simulating biomass handling with a computation modeling such as the finite element analysis. The material parameters determined with the biomass-scale CTT are expected to perform well because of the limited confounding effects in the experimental calibration procedure and unambiguous representations of volumetric stress-strain responses in the principal directions. Future finite element analysis of a specific biomass handling device will discuss the performance and advantage of fundamental mechanical parameters determined with the biomass-scale CTT.
Conclusion
In this study, the biomass-scale CTT is used in characterizing the mechanical behavior of bulk biomass, including corn stover and Douglas fir. From two types of triaxial tests, i.e. HTC test and CTC test, parameters of elasto-plasticity models relevant to biomass flow are determined.
Using the three-dimensional stress and strain measurements in principal directions obtained from HTC and CTC tests, parameters of the Mohr-Coulomb model, Drucker-Prager model and modified Cam-Clay model are determined. Because of the true three-dimensionality of the test results and coincidence with the theoretical framework of analytical models, the parameter determination procedure is unambiguous. Owing to the minimized die-wall effect in the test results, the obtained bulk biomass mechanical properties are believed to reflect truer biomass flow behavior.
All three biomass flow model parameters indicate that Douglas fir 1 mm will be amenable to reliable handling whereas corn stover 2 mm will be prone to a cohesive flow, which is known to induce core flow, development of a rat-hole and blocked flow. Such handling issues of corn stover are expected to hinder the efforts of adopting milled corn stover as a biomass feedstock. Considering that the corn stover is one of major agricultural residual sought after as a renewable biomass feedstock, this is an urgent challenge to overcome. This quantitative observation coincides with the anecdotal experiences. Therefore, it is expected that biomass flow model parameters determined with a CTT will overcome the existing gap in engineering practices of biomass handling and highlight shortcomings of theoretical limitations of biomass flow models.
In addition, it has been hypothesized that the anisotropic mechanical behavior of biomass contributes to the issues in biomass handling. Widely used Mohr-Coulomb model and Drucker postulate an isotropic material behavior. The assumed isotropy of bulk biomass may skew the calibrated failure plane of bulk biomass from conventional shear-cell. This simplification may exacerbate the potential error in mechanical properties of bulk biomass already influenced by the confounding effect of the measurement protocol. Because CTT data provides the complete three principal stress-strain responses, such as anisotropy can be accounted for with an appropriate failure criterion.
Acknowledgments
This material is based upon work supported by the U.S. Department of Energy's Office of Energy Efficiency and Renewable Energy (EERE) under the Bioenergy Technologies Office, Integrated Biorefinery Optimization award number DE-EE0008254 and partially supported by USDA NIFA Agricultural Experiment Station project PEN-4601. This report was prepared as an account of work sponsored by an agency of the United States Government. Neither the United States Government nor any agency thereof, nor any of its employees, makes any warranty, express or implied, or assumes any legal liability or responsibility for the accuracy, completeness, or usefulness of any information, apparatus, product, or process disclosed, or represents that its use would not infringe privately owned rights. Reference herein to any specific commercial product, process, or service by trade name, trademark, manufacturer, or otherwise does not necessarily constitute or imply its endorsement, recommendation, or favoring by the United States Government or any agency thereof. The views and opinions of authors expressed herein do not necessarily state or reflect those of the United States Government or any agency thereof.
Disclosure statement
No potential conflict of interest was reported by the authors.
Additional information
Funding
References
- Prescott JK, Barnum RA. On powder flowability. Pharmaceut. Technol. 2000;24:60–82.
- Ennis BJ, Green J, Davies R. The legacy of neglect in the United-States. Chem Eng Prog. 1994;90:32–43.
- Stasiak M, Molenda M, Bańda M, et al. Mechanical properties of sawdust and woodchips. Fuel. 2015;159:900–908.
- Schwedes J. Review on testers for measuring flow properties of bulk solids. Granular Matter. 2003;5(1):1–43.
- Jenike AW. Gravity flow of bulk solids. Bulletin No. 108, Bulletin of the University of Utah. 1961;52:322.
- Kamath S, Puri VM. Measurement of powder flow constitutive model parameters using a cubical triaxial tester. Powder Technol. 1997;90(1):59–70.
- Karamchandani A, Yi H, Puri VM. Measurement and comparison of mechanical properties of ground corn stover, switchgrass, and willow and their pellet qualities. St. Joseph, MI: American Society of Agricultural and Biological Engineers; 2014. p. 1–5. DOI:
- Perlack RD, Eaton LM, Turhollow AF, Jr, et al. US billion-ton update: biomass supply for a bioenergy and bioproducts industry; 2011. https://works.bepress.com/douglas_karlen/47/ (accessed July 3, 2016).
- Perlack RD, Wright LL, Turhollow AF, et al. Biomass as feedstock for a bioenergy and bioproducts industry: the technical feasibility of a billion-ton annual supply, DTIC Document; 2005. http://oai.dtic.mil/oai/oai?verb=getRecord&metadataPrefix=html&identifier=ADA436753 (accessed July 3, 2016).
- ISO Standard 17828, Solid biofuels – determination of bulk density. Geneva, Switzerland: International Standard Organization; 2015.
- Desai CS, Siriwardane HJ. Constitutive laws for engineering materials, with emphasis on geologic materials. Englewood Cliffs, NJ: Prentice-Hall; 1984.
- Donaghe RT, Chaney, RC, Silver ML, ASTM Committee D-18 on Soil and Rock, editors. Advanced triaxial testing of soil and rock. West Conshohocken, PA: ASTM International; 1988.
- Kamath S. Constitutive parameter determination for food powders using cubical triaxial tester and finite element analysis of incipient flow from hopper bins Ph.D. The Pennsylvania State University; 1996. http://search.proquest.com/pqdt/docview/304304536/abstract/D4B8BF4458F5474DPQ/1 (accessed January 23, 2020).
- Selig ET, Lade PV. Cubical triaxial apparatus for soil testing. Geotech Test J. 1978;1(2):93–101.
- Li F, Puri VM. Measurement of anisotropic behavior of dry cohesive and cohesionless powders using a cubical triaxial tester. Powder Technol. 1996;89(3):197–207.
- Kolymbas D. ed., Constitutive modelling of granular materials. Berlin, Heidelberg: Springer; 2000.
- Puri VM, Tripodi MA, Manbeck HB, et al. Constitutive model for dry cohesive powders with application to powder compaction. KONA Powder Particle J. 1995;13(0):135–150.
- Tripodi MA, Puri VM, Manbeck HB, et al. Triaxial testing of dry, cohesive powder and its application to a modified cam-clay constitutive model. Powder Technol. 1994;80(1):35–43.
- Tripodi MA, Puri VM, Manbeck HB, et al. Constitutive models for cohesive particulate materials. J Agric Eng Res. 1992;53:1–21.
- Yi H, Mittal B, Puri VM, et al. Measurement of bulk mechanical properties and modeling the load response of rootzone sands. Part 3: Effect of organics and moisture content on continuous sand mixtures. Part Sci Technol. 2002;20(2):125–157.
- Yi H, Mittal B, Puri VM, et al. Measurement of bulk mechanical properties and modeling the load-response of rootzone sands. Part 1: Round and angular monosize and binary mixtures. Part Sci Technol. 2001;19(2):145–173.
- ASTM Standard D2850, D18 Committee, Test method for Unconsolidated-Undrained triaxial compression test on cohesive soils. West Conshohocken, PA: ASTM International; 2015. http://enterprise.astm.org/SUBSCRIPTION/filtrexx40.cgi?REDLINE_PAGES/D2850.htm (accessed October 2, 2014).
- ASTM Standard D4767, D18 Committee. Test method for consolidated undrained triaxial compression test for cohesive soils. West Conshohocken, PA: ASTM International, 2011. http://enterprise.astm.org/SUBSCRIPTION/filtrexx40.cgi?REDLINE_PAGES/D4767.htm (accessed October 2, 2014).
- ASTM Standard D5311, D18 Committee. Test method for load controlled cyclic triaxial strength of soil. West Conshohocken, PA: ASTM International. http://enterprise.astm.org/SUBSCRIPTION/filtrexx40.cgi?REDLINE_PAGES/D5311D5311M.htm (accessed October 2, 2014).
- ASTM Standard D7181. Test method for consolidated drained triaxial compression test for soils. West Conshohocken, PA: ASTM International; 2020. http://enterprise.astm.org/SUBSCRIPTION/filtrexx40.cgi?REDLINE_PAGES/D7181.htm (accessed October 2, 2014).
- Chen W-F. Constitutive equations for engineering materials volume 2: Plasticity and modeling. Rev. ed. Amsterdam: Elsevier; 1994.
- Kamath S, Puri VM. Finite element model development and validation for incipient flow analysis of cohesive powders from hopper bins. Powder Technol. 1999;102(2):184–193.
- Jenike AW. Storage and flow of solids. Bulletin No. 123, Bulletin of the University of Utah. 1964;53:198.
- Jenike AW. Steady gravity flow of Frictional-Cohesive solids in converging channels. J Appl Mech. 1964;31(1):5–11.
- Heyman J. Coulomb’s memoir on statics: an essay in the history of civil engineering. London, UK: University of Cambridge; 1997.
- Dimaggio FL, Sandler IS. Material model for granular soils. J Eng Mech. 1971; 97(EM3): 930–950.
- Drucker DC, Prager W. Soil mechanics and plastic analysis or limit design. Quart Appl Math. 1952;10(2):157–165.
- Roscoe KH, Burland JB. On the generalized Stress-Strain behavior of wet clay. Cambridge, UK: Engineering Plasticity; 1968. p. 535–609.
- Schofield A, Wroth P. Critical state soil mechanics. London: McGraw-Hill; 1968.
- Szalwinski CM. On critical states, rupture states and interlocking strength of granular materials. Materials. 2017;10(8):865.