Abstract
This paper presents a feasibility study of Marotti oil biodiesel as an alternative to diesel fuel for a compression ignition engine. Marotti oil is inedible and available mainly in the state of Kerala. The oil is extracted from Marotti seeds. However, the high viscosity, poor volatility and cold flow characteristics of many vegetable oils in general, and Marotti oil in particular, can cause problems such as injector coking, severe engine deposits, filter gumming, piston ring sticking and thickening of lubrication from long-term use in diesel engines. These problems can be eliminated or minimised by transesterification of the vegetable oils to form monoesters. Although transesterification improves the fuel properties of vegetable oil, the viscosity and volatility of biodiesel are still worse than for petroleum diesel fuel. Subsequently, Marotti oil was converted into its methyl ester by the process of transesterification. The methyl ester was blended with diesel in various proportions to obtain different blends of Marotti oil with diesel. The performance, emission and combustion characteristics of Marotti methyl ester and its blends with diesel were studied and the results were compared with the base line data generated for diesel operation. Experiments were conducted using an injection timing of 23° before top dead centre (BTDC) and an injection pressure of 205 bar at various power outputs and at a constant rated speed of 1500 rpm. The engine manufacturer specifies an injection timing of 23° BTDC and injection pressure of 205 bar for the standard diesel fuel operation. The heat release rates, maximum rate of pressure rise, ignition delay and combustion duration for these fuel combinations were obtained.
From the results obtained, it was observed that the biodiesel produced from Marotti oil and its blends with diesel have slightly reduced brake thermal efficiency and increased smoke, hydrocarbon, carbon monoxide and reduced NO x emissions compared with diesel-only operation. The investigation showed that the B20 biodiesel blend of Marotti oil with diesel produced better performance in terms of higher brake thermal efficiency, lower specific fuel consumption and comparatively lower emissions compared to the other blend ratios considered.
1. Introduction
Decentralised energy production is at times vital for the development of rural societies. Apart from the use of pure biodiesels in engines, their blends with diesel can also be advantageous in several aspects. Notwithstanding the present adversaries of economics, academic interest to study our own home-made diesel fuel prompts us to make a comparative study of different vegetable oils available in the state of Kerala. Hence research is focused on the use of vegetable oils as an alternative fuel, as they are renewable, as non-toxic, biodegradable and have low-emission profiles (Altin et al. Citation2000, Pramanik Citation2003, Demirbas Citation2005, Ramadhas et al. Citation2005a, Labeckas and Slavinskas Citation2006, Agarwal and Agarwal Citation2007, Pereira et al. Citation2007). Though much research work is done within and outside the country, biodiesel production and its use are not so popular in Kerala. The most important oil crop in Kerala is coconut but it is edible and so the focus of research was shifted to the testing of Marotti oil (Hydnocarpus laurifolia), an inedible oil. Many researchers have already investigated rubber seed oil, which is also available in Kerala (Nwafor Citation2003, Ramadhas et al. Citation2005b), and this paper reports an investigation of the as yet unexplored Marotti oil.
Marotti oil is extracted from the seeds using steam distillation. The Marotti trees are of Indian origin; grow to about 15–20 m in height, with a thick trunk. Their drooping branches are covered with long leaves. The small flowers, greenish white, form sparse clusters; male and female flowers appear on different trees. The brown round fruit, 6–7 cm in diameter, contains many long seeds of 2 cm diameter that are rich in oil (roughly 60%). Marotti belongs to the Hydnocarpus family, which is a common plant family in southern Asia. Marotti oil is pale yellow in colour, useful in the treatment of skin diseases, scrofula, rheumatism, eczema, and as a counter-irritant for bruises, sprains, etc., and it is sometimes applied to open wounds and sores. The essential oil contains chaulmoogric acid and palmitic acid, and the fatty oil has been found to yield glycerol, a very small quantity of phytosterol and a mixture of fatty acids. It is heavy and viscous, has a mild, woody aroma and is non-toxic. Neat vegetable oils pose some problems when subjected to prolonged use in compression ignition (CI) engines. These problems are attributed to the high viscosity, low volatility and polyunsaturated character of neat vegetable oils (Demirbas Citation2005, Labeckas and Slavinskas Citation2006, Agarwal and Agarwal Citation2007). The high viscosity of vegetable oils causes some problems during atomisation in injector systems and combustion in diesel engine cylinders. Some of the common problems in the long run are poor atomisation, carbon deposits, trumpet formation on the injectors, oil ring sticking, and thickening and gelling of lubricating oil as a result of contamination by the vegetable oils (Labeckas and Slavinskas Citation2006). There are different methods of reducing viscosity of vegetable oils such as preheating, blending and transesterification (Barsic and Humke Citation1981, Nwafor Citation2003, Meher et al. Citation2004, Muralidharan et al. Citation2004, Vivek and Gupta Citation2004, Ramadhas et al. Citation2005c).
One possible method for viscosity reduction is transesterification of vegetable oils to produce esters (commonly known as biodiesel) of the respective oils. In the transesterification process, a triglyceride reacts with three molecules of alcohol in the presence of a catalyst, producing a mixture of fatty acids, alkyl esters and glycerol (Barsic and Humke Citation1981, Meher et al. Citation2004, Muralidharan et al. Citation2004). Conversion of vegetable oil to biodiesel is affected by different parameters namely time of the reaction, reactant ratio (molar ratio of alcohol to vegetable oil), type of catalyst, amount of catalyst, temperature of the reaction; and these parameters were optimised to obtain higher yields of Marotti which is explained in Section 2 of the experiments (Lancaster et al. Citation1975, Vivek and Gupta Citation2004, Ramadhas et al. Citation2005c).
In the present investigation, inedible Marotti oil was selected as an alternative fuel to diesel. Subsequently, Marotti oil was transesterified to obtain its biodiesel Marotti oil methyl ester (MOME). Finally, it was blended with diesel fuel to obtain blends of MAR10 (B10), MAR15 (B15) and MAR20 (B20), respectively. The performance, combustion and emission characteristics of these fuel combinations considered for the study were studied on a four-stroke, direct injection and water cooled CI engine to check their feasibility as CI engine fuels.
2. Experiments
2.1 Transesterification of Marotti oil
This section outlines the process for making biodiesel fuel from Marotti oil. This fuel can be made in a blender or in a larger, home-built mixer. The materials needed are Marotti oil, methanol and a base or acid catalyst. Since each batch of Marotti oil is different, the amount of catalyst + methanol in each batch of biodiesel will be different. To ensure that the correct amount is used, a small test batch of biodiesel is made before attempting a reaction in a large mixing tank. For the test batch, a sample consisting of 100 ml Marotti oil, 20 ml methanol, 5 g of sodium hydroxide pellets and distilled water was prepared. Next, the amount of catalyst to be used was determined. By a trial and error method, it was determined that for 1000 ml of Marotti oil mixed with 200 ml of methanol an addition of 10 g of NaOH catalyst (1% by mass of vegetable oil) was necessary to obtain about 96% yield of Marotti oil biodiesel. The optimised values of the parameters that resulted in the highest biodiesel yield of 96% were: 1% NaOH catalyst; 5:1 molar ratio of methyl alcohol; 60 min; and 65°C, respectively.
Preparation of biodiesel from Marotti oil.
Requirements for the transesterification of Marotti oil process are as follows: 100 ml Marotti oil, 20 ml methanol, 5 g sodium hydroxide pellets and warm distilled water (100 ml).
Procedure:
-
Methanol was poured into a 250 ml measuring flask.
-
Sodium hydroxide pellets were added slowly to the methanol and vigorously stirred to prepare a solution.
-
Marotti oil was than poured into a beaker and heated to remove any moisture remaining in the oil, after which it was slowly cooled.
-
To the cooled Marotti oil kept on the heater, the mixture of methanol and sodium hydroxide was slowly added. The mixture was stirred continuously for 2–3 min until two layers were formed on settling.
-
The mixture was poured into a separating funnel and allowed to settle for 1 h.
-
The run-off lower layer contained glycerol that was released during the reaction.
-
The lower layer was discarded. Later, 40 ml of 1% sulphuric acid was added (any mineral acid could be used) with 100 ml of distilled water to the crude product and mixed well (shaking is not advisable since an emulsion can form which will take a long time to separate). The mixture was allowed to settle for 1 h.
-
The lower layer was run-off and discarded (the washing procedure was repeated until the product was clear).
-
The washed biodiesel was heated to remove any moisture.
-
The biodiesel was decanted and then stored in a storage bottle.
2.2 Fuel properties
The properties of raw Marotti oil, its methyl ester and blends of MOME with diesel were determined as per the Bureau of Indian standards and are summarised in Table .
Table 1 Properties of diesel, Marotti oil and blends of MOME.
2.2.1 Free fatty acid and the chemical content of Marotti oil
The botanical name of the Marotti oil is Hydnocarpus Laurifolia. The essential Marotti oil contains chaulmoogric acid and palmitic acid, and the fatty oil has been found to yield glycerol, a very small quantity of phytosterol and a mixture of fatty acids. It is heavy and viscous, has a mild, woody aroma and is non-toxic. Chaulmogra has a mild, woody aroma.
2.3 Experimental heat release rate estimation
The heat release rate of the fuel causes a variation of gas pressure and temperature within the engine cylinder. It strongly affects the fuel economy, power output and the engine emissions (Aman Citation1985, Hayes et al. Citation1986, Heywood Citation1988, Rocco Citation1993, Homsy and Arvind Citation1997, Brunt and Platts Citation1999, Banapurmath et al. Citation2005, CitationBrown). A program was developed to obtain the ensemble averaged pressure crank angle data of 100 cycles. Heat release analysis was conducted within the framework of the first law of thermodynamics. Here, in a one-zone model, the cylinder contents were assumed to be uniform. The net heat release rate was determined by using a one-zone heat release model (Agrawal and Rajmanoharan Citation2009).
2.4 Experimental set-up
The test was aimed at optimising the concentration of ester in the biodiesel blends to be used for long-term operation. For this, several blends of various concentrations were prepared ranging from 0% (diesel oil only) to10% (B10), 15% (B15), 20% (B20) and 100% biodiesel. These blends were than subjected to performance and emission tests on the engine. The data were then analysed from the graphs of performance, emission and combustion characteristics of the biodiesel blends. The optimum blend was determined from the graphs based on maximum brake thermal efficiency and emission considerations.
Figure shows the schematic diagram of the experimental set-up. A photographic view of the experimental set-up is shown in Figure . The engine tests were conducted on a four-stroke, single cylinder, direct injection, water cooled CI engine. The specifications of the engine are given in Table . The engine was operated at a rated speed of 1500 rev/min. The engine had a conventional fuel injection system. The injection nozzle had three holes of 0.3 mm diameter with a spray angle of 120°. The injector opening pressure and the static injection timing, as specified by the engine manufacturer, were 205 bar and 23° BTDC, respectively. There was no special arrangement to control the engine speed; the regular governor of the engine was used to control the engine speed. The engine was provided with a hemispherical combustion chamber with overhead valves operated through push rods. Cooling of the engine was accomplished by circulating water through the jackets of the engine block and cylinder head. Experiments were conducted under steady thermal state conditions for the engine with an inlet cooling water temperature of 60°C. A piezoelectric pressure transducer was mounted flush with the cylinder head surface to measure the cylinder pressure.
Figure 1 Schematic diagram of the experimental set-up. T 1, T 3, inlet water temperature; T 2, outlet engine jacket water temperature; T 4, outlet calorimeter water temperature; T 5, EGT before calorimeter; T 6, EGT after calorimeter; F 1, fuel flow differential pressure (DP) unit; F 2, air intake DP unit; PT, pressure transducer, N-RPM decoder EGA-DELTA 1600S-Exhaust 5 Gas Analyser, SM-Hartridge smoke meter.
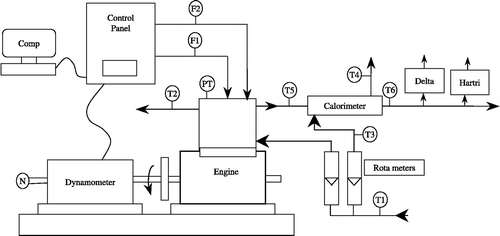
Table 2 Specifications of the engine.
Exhaust gas opacity was measured using a Hartridge smoke opacity meter. The exhaust gas composition was measured using an exhaust gas analyser (Make: MRU, Model: Delta 1600S). The measured emissions included CO2, CO, HC, NO x and O2. The basic principle for measurement of CO2, CO, HC, NO emissions is non-dispersive infrared technology with electrochemical methods used for the NO x and oxygen measurement.
3. Results and discussion
In this section, experiments were conducted using Marotti oil and MOME.
3.1 Performance characteristics
The effect of power output on brake thermal efficiency for MOME and its blends with diesel is shown in Figure . There is a steady increase in brake thermal efficiency as the load increases for diesel, MOME and its blends with diesel, but after 80% load it decreases. The trend of the thermal efficiency curves was generally improved by mixing biodiesel with mineral diesel oil. The thermal efficiency of the engine was found to improve by increasing the concentration of biodiesel in the blend. The possible reasons for this may be a more complete combustion and the additional lubricity of biodiesel; i.e. with an increasing amount of biodiesel, the frictional horsepower losses in the engine are reduced. The energy saved by the decrease in frictional horsepower made additional contributions towards useful energy, cooling losses and exhaust losses.
Figure 3 Effect of brake power on brake thermal efficiency with MOME and its blends with diesel at optimum parameters.
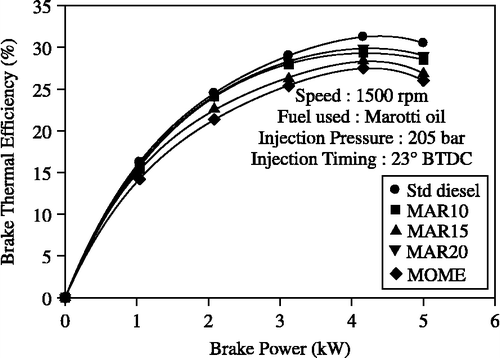
The brake thermal efficiency with B20 blend operation was closer to diesel operation followed by the B10 blend. Operation with B100 resulted in the lowest efficiency due to the reduced calorific value of the fuel. The maximum brake thermal efficiency with MOME operation was 28.38% at 80% power output whereas it was 31.25% with diesel-only operation. However, the thermal efficiency with the B20 at 80% power output was 29.9%, which is close to diesel operation and this was followed in efficiency by the B10 blend operation.
The effect of brake power on exhaust gas temperature (EGT) for diesel and MOME and its blends with diesel is shown in Figure . It was observed that the EGT increased with an increase in brake power for all the injected fuels tested. Compared to diesel-only operation, all the fuels demonstrated increased EGT and this could be attributed to the lower calorific value of MOME and its blends with diesel and the incomplete combustion process that prevails in the engine. It is evident from the graphs that the EGT is also increasing along with thermal efficiency as a function of blend concentration. With the B20 biodiesel blend, a lower EGT was observed when compared to the other blend ratios. The poor volatility and high viscosity of the MOME blends lead to a more dominant diffusion combustion phase than diesel, which is responsible for this. Also, the late burning of injected ester blends results in slower combustion and hence results in higher EGT. The maximum temperature of exhaust gas at 80% power output was 434°C with the B20 and 450°C with methyl ester of Marotti oil. These temperatures are slightly higher in comparison to diesel-only operation. The peak EGT for diesel-only operation was observed to be 390°C.
3.2 Emission characteristics
Figure shows the variation of smoke opacity of Marotti methyl ester and its blends with power output. Smoke opacity increased with an increase in brake power for all the fuels tested. Furthermore, smoke opacity of MOME and its blends with diesel is higher than for diesel-only operation. At higher loads, the smoke opacity of the blends increases due to the heavier molecular structure and higher viscosity of the blends resulting in poor combustion. The smoke opacity increases with increase in MOME concentration in blends particularly at higher loads. Smoke opacity for biodiesel blends is also observed to be generally higher than that for diesel oil. The reasons could be that the higher thermal efficiency produces better and more complete combustion and a reduced amount of unburned hydrocarbons in the engine exhaust, thereby improving the smoke opacity values. For the B20 blend, the smoke opacity decreased at higher loads due to better combustion. The smoke level at 80% power output was 68 HSU (Hartridge Smoke Units) for the MOME and 58 HSU for the B20 blend which is 10–28% higher when compared to diesel-only operation. The smoke level with diesel-only operation was 53 HSU.
Figure 5 Effect of brake power on smoke opacity with MOME and its blends with diesel at optimum parameters.
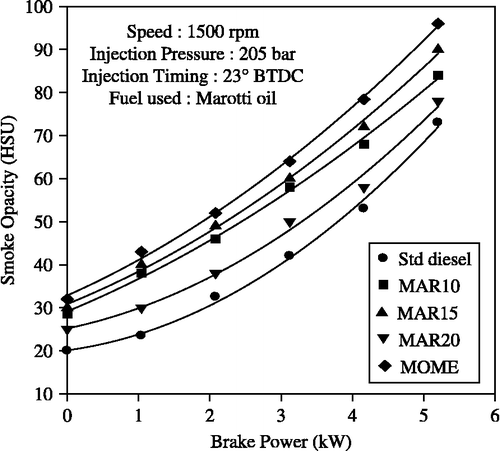
The effect of brake power output on HC and CO emissions with methyl ester of Marotti oil and its blends with diesel is shown in Figures and , respectively. The biodiesel blends generally exhibit lower HC emissions at lower engine loads and higher HC emissions at higher engine loads compared to diesel oil. This is because relatively less oxygen is available for the reaction when more fuel is injected into the engine cylinder at high engine load. HC and CO emissions were higher with MOME and MOME-blends when compared to diesel-only operation. Higher HC emissions in the exhaust of the blended fuel may be attributed to the inefficient mixing of the oil with air leading to incomplete combustion. The reasons mentioned for lower thermal efficiency of these oils are also responsible for this trend. The HC level is 45 ppm with the B20 and 48 ppm with the methyl ester of Marotti oil which is marginally higher compared to 41 ppm for the diesel-only operation.
It can be seen from Figure that lower CO emissions were observed as the blend ratio increased and the 20% blend produced the lowest CO emissions of the different blends selected for study. Owing to the high viscosity, the air-fuel mixing process is affected by the difficulty in atomisation and vaporisation of all the biodiesel blends tested. The resulting locally rich mixtures cause more incomplete combustion products of CO and HC. At lower loads, no significant change was observed in CO emissions for MOME and its blends when compared to diesel-only operation. The measured values of CO were 0.132, 0.145 and 0.1125% for B20, MOME and diesel-only operation, respectively.
Figure shows the effect of brake power on NO emission for diesel-only and MOME and its blends with diesel. Nitric oxide emission increased with an increase in load for all the fuel combinations. MOME and its blends showed lower NO emission when compared to standard diesel operation. The emission of NO was found to be significantly lower for the biodiesel blends. The most important factor for the formation of NO is the combustion temperature in the engine cylinder and the availability of oxygen. The vegetable oils have higher viscosity; therefore, the fuel droplet size in the engine is expected to be larger than for the diesel oil. Larger droplets have longer combustion duration and they demonstrate significant energy release during the late burning phase. This suggests that the peak combustion chamber temperature is possibly lower for the biodiesel and its blends compared to diesel, leading to lower formation and emission of NO. This reduction in NO emission is mainly associated with the reduced premixed burning rate following the delay period. The NO x emissions for B10, B15, B20 and MOME fuels were measured as 1070, 1066, 1150 and 1070 ppm, respectively, in comparison to 1250 ppm for diesel-only operation.
3.3 Combustion characteristics
The variation of ignition delay is shown in Figure . Ignition delay was calculated based on the static injection timing. MOME and its blends showed longer ignition delays when compared to diesel. However, the B20 blend showed a shorter ignition delay than the other blends of MOMEs.
Figure 9 Effect of brake power on ignition delay with MOME and its blends with diesel at optimum parameters.
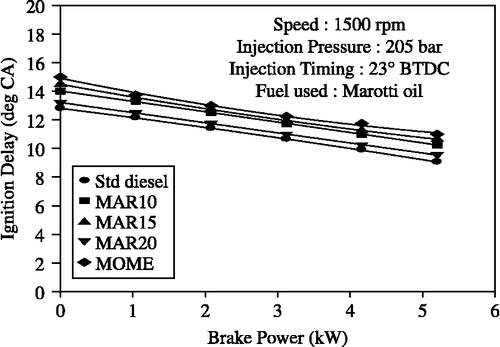
Peak pressure and maximum rate of pressure rise were highest for diesel followed by the MOME blends as shown in Figures and . The peak pressures with B10, B15, B20 and MOME were measured to be: 75, 71, 78.5, 69.25 bar, respectively; whereas for diesel-only operation it was 81.75 bar at full load. The trends in the maximum rate of pressure rise were also similar. In a compression-ignition engine, peak pressure depends on the combustion rate in the initial stages, which in turn is influenced by the amount of fuel taking part in the uncontrolled combustion phase. The premixed or uncontrolled combustion phase is governed by the ignition delay period and by the mixture preparation during the delay period. Thus, the higher viscosity and lower volatility of the MOME blends, which lead to poor atomisation and mixture preparation with air during the ignition delay period, are the reasons for this trend of peak pressure and maximum rate of pressure rise.
Figure 10 Effect of brake power on peak pressure with MOME and its blends with diesel at optimum parameters.
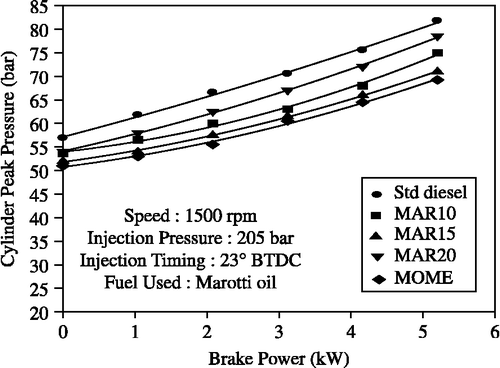
The combustion duration shown in Figure was calculated based on the duration between the start of combustion and the point of 90% cumulative heat release. It was observed that combustion duration increased with an increase in the power output with all the fuels tested. This was due to an increase in the quantity of fuel injected. Higher combustion durations were observed with MOME blends than for diesel-only operation due to the longer diffusion combustion phase. With the B20 blend, the combustion duration reduced.
Figure 12 Effect of brake power on combustion duration with MOME and its blends with diesel at optimum parameters.
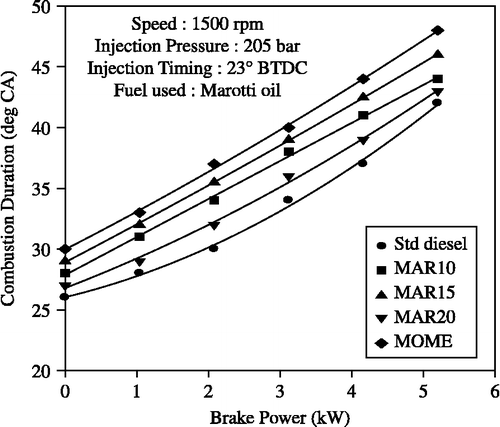
Figure shows the variation of heat release rate with crank angle for diesel MOME, its blends with diesel at 80% load. The premixed burning phase associated with a higher heat release rate is significant with diesel operation. This is the reason for the higher thermal efficiency with diesel. The diffusion-burning phase indicated under the second peak is greater for B20 compared to diesel operation. This is consistent with the expected effects of vegetable oil viscosity on the fuel spray and reduction of air entrainment and fuel air mixing rates. This leads to less fuel being prepared for rapid combustion with Marotti oil and its blends after the ignition delay. Therefore, more burning occurs in the diffusion phase rather than in the premixed phase with Marotti oil. The significantly higher combustion rates during the later stages with MOME blends lead to higher EGTs and lower brake thermal efficiency. However, the B20 blend showed an improvement in heat release rate in comparison with the other blends and neat MOME operation.
4. Conclusions
The main objective of this investigation was to obtain biodiesel from Marotti oil by the process of transesterification. This was necessary to reduce the viscosity of Marotti oil and bring its value closer to that of conventional diesel in order to check its feasibility as a CI engine fuel. The following conclusions were drawn from the study.
Transesterification of Marotti oils
-
The quantity of catalyst and methyl alcohol used is crucial for a successful reaction. Washing is necessary to remove undesired contaminants in the biodiesel. The biodiesel should be heated to remove excess moisture.
-
The optimum values of the parameters that result in highest biodiesel yield (96%) are 1% NaOH catalyst, 5:1 molar ratio of methyl alcohol, 60 min and 65°C, respectively. The properties of MOME and its ester blends were comparable to those of standard diesel.
-
Operation using MOME and its blends with diesel suggests that no major modifications were required for the existing diesel engine.
-
MOME and its blends with diesel produced slightly reduced brake thermal efficiency when compared with diesel-only operation along with increased smoke, HC and CO levels.
-
NO emission was lower for MOME blends due to slower combustion.
-
The heat release rate for all the blends indicated that there was a short premixed heat release portion despite the increase in ignition delay.
-
Brake thermal efficiency values for B20 are comparable to diesel-only operation.
A blend of Marotti oil with diesel, i.e. the B20 blend, could be used in CI engines in rural areas for agriculture, irrigation and electricity generation. On the whole, it was observed that engine operation was smooth with MOME and its blends.
References
- Agarwal , D. and Agarwal , A.K. 2007 . Performance and emission characteristics of jatropha oil (preheated and blends) in a direct injection compression ignition engine . Applied Thermal Engineering , 27 : 2314 – 2323 .
- Agrawal , A.K. and Rajmanoharan , K. 2009 . Experimental investigations of performance and emissions of Karanja oil and its blends in a single cylinder agricultural diesel engine . Applied Energy , 86 : 106 – 112 .
- Altin , R. , Cetinkaya , S. and Yucesu , H.S. 2000 . The potential of using vegetable oil fuels as fuel for diesel engines . Energy Conversion and Management , 42 : 529 – 538 .
- Aman, C.A., 1985. Cylinder pressure measurement and its use in engine research. Society of Automotive Engineers, Paper No. 852067 USA
- Banapurmath, N.R., Tewari, P.G., Basavarajappa, Y.H., and Yaliwal, V.S., 2005. Performance of Honge (Pongamia pinnata) oil blends in a diesel engine. XIX NCICEC, December 21–23, 2005 Annamalai University, Chidambaram
- Barsic, N.J. and Humke, A.C., 1981. Performance and emission characteristics of a naturally aspirated diesel engine with vegetable oil fuels. Society of Automotive Engineers, Paper No. 810262, 95–109, USA
- Brown, B.R., Combustion Data Acquisition and Analysis – Final Year Project M.Eng. Automotive Engineering, Department of Aeronautical Loughborough University
- Brunt, M.F.J. and Platts, K., 1999. Calculation of heat release rate in direct injection diesel engines. Society of Automotive Engineers, 1999 Paper No. 1999-01-0187
- Demirbas , A. 2005 . Biodiesel production from vegetable oils via catalytic and non-catalytic supercritical methanol transesterification methods . Progress in Energy and Combustion Science , 31 : 466 – 487 .
- Hayes, T.K., Savage, L.D., and Soreson, S.C., 1986. Cylinder pressure data acquisition and heat release analysis on a personal computer. Society of Automotive Engineers, Paper No. 860029, USA
- Heywood , J.B. 1988 . Internal combustion engine fundamentals , Singapore : McGraw-Hill Book Co .
- Homsy, S.C. and Arvind, A., 1997. An experimental heat release rate analysis of a diesel engine operating under steady state conditions. Society of Automotive Engineers, Paper No. 970889, USA
- Labeckas , G. and Slavinskas , S. 2006 . Performance of direct injection off road diesel engine on rapeseed oil . Renewable Energy , 31 : 849 – 863 .
- Lancaster, D.R., Krieger, R.B., and Lienesh, J.H., 1975. Measurement and analysis of engine pressure data. Society of Automotive Engineers, Paper No. 750026, USA
- Meher , L.C. , Naik , S.N. and Das , L.M. 2004 . Methanolysis of Pongamia pinnata (Karanja) oil for production of biodiesel . Journal of Scientific and Industrial Research , 63 : 913 – 918 .
- Muralidharan, M., Thariyan, M.P., Roy, S., Subrahmanyam, J.P., and Subbarao, P.M.V., 2004. Use of pongamia biodiesel in CI engines for rural application. Society of Automotive Engineers, Paper No. 28-0030, USA
- Nwafor , M.I. 2003 . The effect of elevated fuel inlet temperature on performance of diesel engine running on neat vegetable oil at constant speed conditions . Renewable Energy , 28 : 171 – 181 .
- Pereira , R.G. , Oliveira , C.D. , Oliveira , J.L. , Oliveira , P.C.P. , Fellos , C.E. and Piamba , O.E. 2007 . Exhaust emissions and electric energy generation in a stationary engine using blends of diesel and soyabean biodiesel . Renewable Energy , 32 : 2453 – 2460 .
- Pramanik , K. 2003 . Properties and use of jatropha curcas oil and diesel fuel blends in compression ignition engine . Renewable Energy , 28 : 239 – 248 .
- Ramadhas , A.S. , Muraleedharan , C. and Jayaraj , S. 2005a . Biodiesel production from high FFA rubber seed oil . Fuel , 84 : 335 – 340 .
- Ramadhas , A.S. , Muraleedharan , C. and Jayaraj , S. 2005b . Performance and emission evaluation of a diesel engine fueled with methyl esters of rubber seed oil . Renewable Energy , 30 : 1789 – 1800 .
- Ramadhas , A.S. , Muraleedharan , C. and Jayaraj , S. 2005c . Characterization and effect of using rubber seed oil as fuel in compression ignition engines . Renewable Energy , 30 : 795 – 803 .
- Rocco, V., 1993. Di diesel engine in cylinder pressure data analysis under TDC setting error. Society of Automotive Engineers, Paper No. 930595, USA
- Vivek and Gupta , A.K. 2004 . Biodiesel production from Karanja oil . Journal of Scientific and Industrial Research , 63 : 39 – 47 .