Abstract
Thermo-mechanical, optical and physical properties of polypropylene (PP)/lignocellulosic fibre-filled/maleated PP composites were studied as a function of extrusion screw speeds. All materials were extruded at four screw speeds and injection moulded as dogbone specimens. The density, yellowness index (YI) and Fourier-transform infrared spectra were determined for the processed specimens. Tensile properties and coefficient of linear thermal expansion (CLTE) were also determined. The densities of the composites remained constant within the same composition. YI and absorbances of carbonyl, vinylidene and hydroxyl groups, which are indicators of thermo-oxidation, decreased with a shorter extruder residence time. The CLTE and tensile properties showed peak properties at intermediate screw speeds. The analysis suggested optimising the residence time assisting in achieving a balance of properties.
1. Introduction
Natural fibre-reinforced thermoplastic composites are major competitors in markets such as automotive body parts and commodity goods (Mohanty et al. Citation2005). Often referred to as a bio-based composite since a renewable fibre constituent is added, these composite materials offer the advantage of comparable mechanical performance compared to the base polymer, at a lowered cost (Scott and Wiles Citation2001, Fuqua and Ulven Citation2008) and several other functionalities. Bio-based polymers (biopolymers) that promise a higher utilisation of renewable resources are still in a relatively developmental phase. Today, the bio-based composites with a commodity synthetic polymers are the choice for gaining an edge in overall cost, and more environmentally friendly processing (Scott and Wiles Citation2001).
Currently, the newly developed bio-based composite technologies encounter a number of challenges in penetrating potential markets and undergoing further commercialisation because of the unclear understanding of several aspects in processing and resulting properties. Building confidence through implementing improvements in processing and optimisations is the driving force for these biocomposite applications.
Specifically, processing-related effects for bio-based composites, such as colour change, odour and surface texture, all limit their selection when designing a potential application. Mechanical properties remain the most critical aspect in the selection and design with these biocomposites in meeting the performance requirements. Moreover, the selection of polymer matrices is limited (Rowell et al. Citation1997) when using natural fibres, e.g., polypropylene (PP) (Fuqua and Ulven Citation2008), acrylonitrile butadiene styrene (Chevali et al. Citation2010b, Citation2010c), poly(vinyl chloride) (Bledzki et al. Citation1998), etc., because of the low (>200°C) degradation temperature of the lignocellulosic natural fibre constituents.
For short/filler-type fibres, the most economically beneficial sources are waste streams of agricultural produce or co-products of oil/fuel (e.g., ethanol) extraction. However, the downsides of the usage of these natural fillers are the concerns (Reddy and Yang Citation2005) in the areas of seasonal fluctuations, such as in supply, harvesting methods, and in the specific methods of handling and processing of these fibres.
Bio-based composites with PP have been studied extensively in the literature. Often developed for semi-structural applications, the successful biocomposite grades have an optimal matrix/filler bond with the matrix as the controller with respect to load transfer. A fibre surface treatment is applied for achieving the desired interfacial strength to increase the surface energy and concomitantly, the compatibility of the hydrophilic natural fibre with the hydrophobic polyolefin matrix. The most common treatments (Li et al. Citation2007) include the usage of maleated coupling agents such as maleic anhydride-grafted PP (MAPP) and silane coupling agents. Of these surface treatments, the MAPP treatment causes both an increased compatibility between the natural filler surface and the matrix and an increased interfacial bond strength. An increased interfacial compatibility in PP-based composites causes improvements in mechanical properties, e.g., dynamic modulus (Gassan and Bledzki Citation2000), elastic modulus (Doan et al. Citation2006), tensile strength (Doan et al. Citation2006, Yang et al. Citation2007), and interlaminar shear strength (van de Velde and Kiekens Citation2002). However, a marginal change in impact toughness is often observed by the addition of these compatibilising agents (Doan et al. Citation2006, Yang et al. Citation2007). The addition of MAPP is also governed by a critical weight fraction over which the advantage of the coupling agent is no longer realised. This critical fraction is dependent on the matrix/fibre system, and the most common range is about 2.0–3.0 wt%. In addition, the method of application, i.e., matrix modification or natural filler surface treatment also controls the properties. Nevertheless, processing parameters also possess a pivotal role in obtaining the optimum design requirements.
During the processing of thermoplastic polyolefins, high shear forces are applied to the polymer melt (Voigt and Todesco Citation2002) subjecting a portion of polymer chains to homolytic scission at –C–C– bonds. This scission produces peroxide radicals that undergo an unimolecular decomposition to yield alkyl radicals (Grassie and Scott Citation1985, Achimsky et al. Citation1997). These high-activity alkyl radicals often initiate radical chain reactions. With the presence of oxygen, these reactions are accelerated. To a certain degree, these radicals recombine, and with an abundant supply of oxygen, the radicals induce permanent chain breakages (Grassie and Scott Citation1985). In polyolefins such as PP, the formation of a hydroperoxide (–OOH) intermediate is the potential source for the ensuing susceptibility to oxidation in the finished product. The concentration of these peroxide radicals increases with an increasing processing time. Hence, the processing method is expected to influence the thermo-oxidative mechanisms of the material.
The thermal stability of the composite, however, is a complex combination of the matrix oxidation, the effect of the natural fibre and the maleated coupling agent. The addition of lignocellulosic fibre that starts to degrade around 200°C (Schniewind Citation1989) presents additional challenges in maintaining the thermal stability of the composite. Moreover, the thermal degradation of the composite is controlled by the co-dependent influences of natural fibre and the polyolefin matrix (Renneckar et al. Citation2004). Thermal degradation often shows a slight increase with the addition of a compatibiliser such as MAPP (Salemane and Luyt Citation2006, Tajvidi and Takemura Citation2010), whereas a system with no maleated agent and a natural filler shows marginal decreases (Salemane and Luyt Citation2006). Thus, all constituents of the composite are expected to affect the overall thermal stability of the composite in a variable degree.
The effect of processing-induced oxidation on the thermo-mechanical and mechanical properties in lignocellulosic particulate fibres is a challenge. This study investigated the thermal degradation in PP reinforced with lignocellulosic fibre as a function of variable screw speeds (extruder dwell time). The extruded/injection-moulded parts were characterised using Fourier-transform infrared (FTIR) spectroscopy to identify functional groups. Colorimetry was performed to detect the degree of yellowness of the material. The moulded specimens were tested (a) in tension and (b) in controlled force mode in dynamic mechanical analysis (DMA) to determine the coefficient of linear thermal expansion (CLTE). The mechanical properties, compositional FTIR information and optical (colorimetry) properties were correlated.
2. Processing-related auto-oxidation and degradation
In the processing of PP by extrusion, macroalkyl radicals are produced by near-melt temperatures and by the action of screw/polymer, polymer/wall shear interaction (Scheirs Citation2000). The formation of these radicals is dependent on screw rpm, extruder clearances, screw-design and shear rate sensitivity of the polymer (Scheirs Citation2000). The radical concentration increases with the increase in mechanical shear that is encountered in the processing equipment.
The high-activity alkyl radicals (Grassie and Scott Citation1985, Scheirs Citation2000, Voigt and Todesco Citation2002, Sarrabi et al.
Citation2008) react with available oxygen to form peroxyl radicals [Equation (Equation1)]. Following hydrogen abstraction, hydroperoxides (R–OOH) are formed [Equation (Equation2
)], along with the formation of an alkyl radical (R√).
The hydroperoxide intermediate formed in the propagation step further undergoes homolytic cleavage (Grassie and Scott Citation1985, Sarrabi et al.
Citation2008) under extruder heat to produce alkoxyl, peroxyl and hydroxyl radicals [Equations (Equation3) and (Equation4
)]
Chain termination (Scheirs Citation2000) occurs according to either of these probable routes [Equations (Equation5) and (Equation6
)] in polyolefins
The chain termination scheme according to Equation (Equation6) is likely in case of an abundant oxygen supply.
Vinylidene group is produced in polyolefins from the thermo-oxidative reactions in an environment that contains oxygen (Gugumus Citation2006). The formation of vinylidene can occur through (a) intramolecular decomposition of hydroperoxide groups, (b) intramolecular decomposition of special hydroperoxide groups, (c) direct decomposition of peroxy radicals, or (d) bimolecular hydroperoxide decomposition.
3. Materials and processing
3.1 Polymer and chemical modifier
PP used in this study was obtained as PP 3825 grade (Anon 2009b) from Total Petrochemicals, Inc. (Houston, TX, USA) with minimal amount of additives. MAPP was used as a chemical modifier to improve the interfacial adhesion between the natural fibres and the matrix. MAPP was obtained from Clariant, Inc. (Charlotte, NC, USA) as Licomont AR 504 (Anon 2009a). The properties of these materials are listed in Table .
Table 1 Nominal properties of the materials used in this study.
3.2 Fibre
Sunflower is grown in abundance locally in the Northern Great Plains geographical location of the USA, with little known use for the residual hulls after oil/seed extraction. A chemical analysis of the constituents of this hull structure showed a 44 wt% of cellulose, critical for structural strength (Mohanty et al. Citation2005) and 22 wt% of lignin, which dictates the thermal behaviour (Mohanty et al. Citation2005). Proteins and polysaccharides constitute the remainder of the sunflower hull (SFH). The SFH received from Red River Commodities, Inc. (Fargo, ND, USA) was ground as a particulate using a Retsch centrifugal mill with a 0.25 mm mesh. A quantitative microscopic analysis (Chevali et al. Citation2010a) showed the final aspect ratio of the fibres of l/d = 2.095 ± 0.021.
3.3 Extrusion and injection moulding
A twin-screw co-rotating extruder (Leistritz Micro 18 GL-40 D) was used to compound the dry mixture of the PP, SFH and MAPP in varying concentrations. These grades are listed in Table . The temperatures from feed zone to the extruder exit ranged from 176 to 190°C in incremental succession. A Brabender® gravimetric feeder was used to feed the material. The mean residence times for 50 rpm (5.2 rad/s), 150 rpm (15.7 rad/s), 250 rpm (26.2 rad/s), 350 rpm (36.7 rad/s) and 450 rpm (47.1 rad/s) were measured by recording the time for the material to travel from the feed zone to the die exit with an initial empty barrel. These times are shown in Figure . The residence times, as expected, do not decrease linearly because of the extruding action of the twin screws. The extrudate strands were water cooled, chopped and dried for 12 h at 80°C prior to injection moulding.
Table 2 Nomenclature and description of grades processed in this study.
Figure 1 A plot of mean residence time calculated from feed to exit on an empty barrel using PP00F00M.
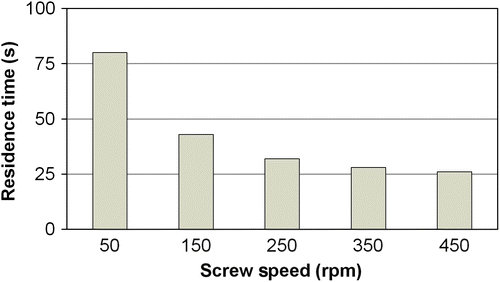
A single screw, Technoplas 5080 injection moulding machine was used to process the material into ASTM D638 Type-I tensile test specimens. The barrel temperature profile ranged from 170°C at the feed zone to 210°C at the exit nozzle. This profile was kept constant for all the specimens processed for this work.
4. Experimental procedure
4.1 Fourier-transform infrared spectroscopy
The changes in the structural groups and developing thermo-oxidation products were assessed by monitoring their corresponding FTIR absorbances. A Thermo-Nicolet FTIR 6700 was used in the attenuated total reflectance (ATR) mode in the 650–4000 cm− 1 (mid infrared) range at a resolution of 4 cm− 1, and 32 scans per each run. An ATR correction built in the vendor software was applied to the spectra.
4.2 Colorimetry
A bench-top colorimeter (Macbeth ColorEye Model # 7000) was used to monitor the colour change (ΔX, ΔY, ΔZ) or yellowness in the processed panels. Yellowness is an optical property of a polymer representing the chromatic deviation from whiteness in wavelengths ranging from 570 to 580 nm (ASTM International Citation2003). A ΔX ΔYΔZ scale was used for calculating yellowness index (YI), according to ASTM E 313-05 using
The YI was calculated as an average of a three-specimen sample.
4.3 Coefficient of linear thermal expansion
CLTE was measured using a DMA Q800 (TA Instruments, Inc., New Castle, DE, USA) (Anon 2009c), in the controlled force mode. The specimen was held in the clamp using a minimal preload force (∼0.1 N), and was subjected to a temperature ramp of 5°C/min from room temperature (23°C) to 150°C. The specimen displacement was plotted as a function of temperature, and the slope was determined in the initial linear region. The slope was then translated to a CLTE (α) value using
4.4 Tensile testing
The tensile behaviour of the materials was determined using the injection moulded Type-I dogbone specimens as specified in ASTM D 638, at room temperature. A minimum of four specimens were used for each material. The ultimate tensile strength (σT), Young's modulus (E T), percentage extension to failure and strain at maximum stress were recorded.
5. Results and discussion
5.1 Materials characterisation
The processed material in the form of dogbone specimens was characterised for (a) density, (b) change in yellowness (colour) and (c) to monitor changes in the functional groups, using FTIR spectroscopy.
The densities measured using the immersion density apparatus are shown in Figure . As expected, density increased with the addition of the SFH fibre. The density of the neat polymer was seen constant at about 0.810 g/cm3. The variation of screw speed also showed a weak effect as the density remained relatively constant at about 0.865 g/cm3. The published density of the specific neat PP used for this study (PP 3825, Total Petrochemicals, Inc.) is approximately 0.905 g/cm3. A decrease of about 10% in density from the as-received polymer can be attributed to a decrease in molecular weight with multiple extrusion operations (Rust et al. Citation2006). In this study, all materials were subjected through two extrusion cycles, i.e. twin-screw extrusion and plastication within the injection moulding operation.
5.1.1 Yellowness index
The average YI of the materials is shown in Figure . Overall, the YI showed a decrease with increase in screw speed (i.e. decrease in dwell time) in the extruder. The evolution of colour in the biocomposites used in this study is a function of both the agricultural fillers and is because of thermo-oxidation occurring at the processing temperatures (∼180°C), with a ready presence of oxygen within the equipment. An increase in yellowness or deviation from whiteness is an indicator of the formation of oxidation products. Overall, the visual appearance of the specimens after processing varied from a darker shade if processed at lower screw speed to a lighter shade at higher screw speeds. YI, thus, was a quantitative measure of the ongoing colour change with respect to underlying photo-oxidation.
Figure 3 The average change in YI calculated using ASTM E-313 shown as a function of varying screw speeds.
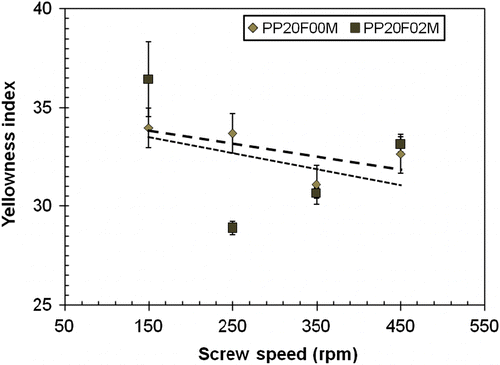
The YI of the composites as measured using colorimetry is shown in Figure . Overall, a decreasing trend was seen with an increasing screw speed. A higher standard deviation in YI at lower screw speeds was observed. This increase in variation in YI can be attributed to the formation of a larger number of oxidation products through a relatively random and large selection of oxidation pathways involving the alkyl radicals because of a higher dwell time (Grassie and Scott Citation1985). This effect is decreased by decreasing the dwell time by increasing the screw speeds. Individually, the addition of MAPP showed a higher YI indicating a darker appearance of the finished product. The addition of MAPP causes a marginal change in the rate of colour change as compared to the composite.
5.1.2 Fourier-transform infrared spectroscopy
The FTIR absorbances of the neat polymer (not shown here) exhibited no changes with the increasing screw speeds. The FTIR spectra for the vinylidene group absorbance of PP20F00M are shown in Figure (a). The increasing vinylidene absorbance is an indicator of the ongoing thermo-oxidative degradation in the material. As seen from this plot, the absorbance decreased with an increase in the screw speed or an increase in the residence time in the extruder. This induction of thermo-oxidative mechanism is nearly linear, as a decrease in the absorbance is seen gradually. Similarly, the vinylidene group absorbance for the PP20F02M material is shown in Figure (b). As seen, a major change in the 900 cm− 1 absorbance is realised only at 450 rpm, which implies that MAPP introduces nonlinearity to the oxidative mechanism, and the intermediate (propagation) step encountering a steering effect because of the faster initiation step. The comparison of the absorbances over the four screw speeds (Figure (c)) shows the vinylidene group affected in the PP20F02M, nearly similar to the trend followed by the PP20F00M composite. This effect clearly indicates different oxidation routes adopted by these materials. The differences, which are not quantified here, are most likely the selection of one of the four possible criteria for the formation of vinylidene radicals from either the intermediate or the special hydroperoxides (Gugumus Citation2006).
Figure 4 The absorbance of vinylidene groups at the screw speeds investigated for (a) PP20F00M, (b) PP20F02M and (c) comparison of absorbances.
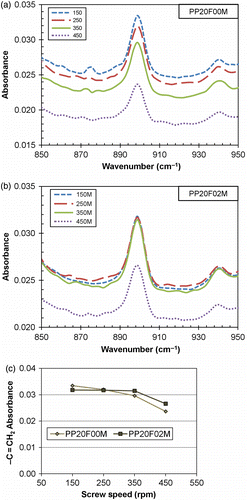
Figure (a) shows the hydroxyl region of the PP20F00M grade. An increase in –OH group is expected because of the formation of (a) hydroxyl species in propagation, and (b) from combination of hydroperoxide (–OOH) species in the termination step causing the production of an –OH. A higher absorbance of –OH is seen with lower screw speed. A decrease of about 80% peak absorbance is seen at around 3410 cm− 1. Also, necking/branching of the –OH group peak is seen at 3150 cm− 1, indicating the formation of an additional oxidation product with a higher extruder residence time.
Figure 5 The FTIR spectra showing the hydroxyl (–OH) absorbances for the materials (a) PP20F00M, (b) PP20F02M and (c) comparison of absorbances.
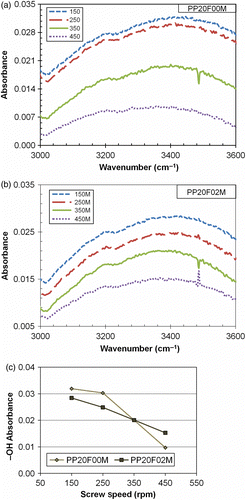
Similarly, Figure (b) shows the hydroxyl absorbance for the PP20F02M material. In this case, also, the absorbance showed a decrease with an increase in screw speed. As opposed to the vinylidene absorbance, a near linear trend in decrease was realised. In addition, all materials showed the additional neck as seen in the lower screw speeds in PP20F02M composite. The spike at 3500 cm− 1 is likely from the lignin component of the natural fibre.
The change in the hydroxyl group absorbance with the screw speeds is shown in Figure (c). Both materials showed a decrease with a decreasing extruder dwell time. The percentage change, however, is higher in PP20F00M (∼70%) than in PP20F02M, which shows about a 50% decrease in the –OH group absorbance.
Figure (a) shows the change in the carbonyl index of the PP20F00M composite. The carbonyl index decreased with a decrease in the extruder dwell, and the concomitant mechanical shearing and the resultant hydroperoxide formation and oxidation products with a –C = O group (Grassie and Scott Citation1985). The change in the carbonyl index for PP20F02M is shown in Figure (b). The decrease in PP20F02M is relatively nonlinear as compared to that in PP20F00M. The decreasing trends in these materials are shown in Figure (c). Both materials exhibited a clear decrease with a decrease in the extruder dwell time. In this case, relatively linear decrease and higher degree of change in –C = O absorbance were observed in PP20F00M composite, whereas PP20F02M showed a possible incubation period in the first three sampling intervals. This observation suggests higher activation energy for PP20F02M, along with an inhibiting mechanism that assists in the retardation of the auto-oxidation.
5.1.3 Crystallinity
Crystallinity was measured assuming proportionality with the macrotacticity of PP, i.e. the ratio of absorbances at 997 and 972 cm− 1. The crystallinity showed a very minor change with increase in screw speed, and remained constant at X c = (87.3 ± 0.5)% for PP20F00M, and X c = (86.8 ± 0.1)% for PP20F02M.
The crystallinity changes in lignocellulosic natural fibres can be attributed to PP crystallite growth as a function of available nucleation sites on the fibre surface for crystallisation (Amash and Zugenmaier Citation2000, Grozdanov et al. Citation2007). The addition of lignocellulosic fibres in PP has been known to increase crystallisation temperature, enthalpy of crystallisation and the percentage of crystallinity. This effect is stronger in the case of chemically treated fibres, which intensify the formation of a trans-crystalline layer at the fibre/polymer interface. In the current set of materials, the crystallinity remained in the same range because (a) polymeric segments and the fibre aspect ratio that is required for initiating crystallisation are likely absent, and (b) the fibres are not chemically treated, and thus not possess reactive end groups. In the case of MAPP compatibilised PP20F02M also, most reactive end groups are unavailable as they are linked either to the cellulosic –OH or are grafted as side chains to the polymer matrix.
5.1.4 Linear thermal expansion
Figure shows the comparison of CLTE values that were calculated from a controlled-forced DMA experiment for the four screw speed cases. The neat polymer showed about 20% decrease from 150 to 450 rpm, whereas PP20F00M composite CLTE remained similar at an average of 1.2 (μm/μm)/°C. The MAPP coupled composite also retained the CLTE until 350 rpm, but decreased at 450 rpm by about 20%. For both composites, an average of about 33% decrease in CLTE was obtained, as compared to PP00F00M.
Figure 7 The variation in the CLTE as calculated using a controlled-force DMA experiment for the three materials.
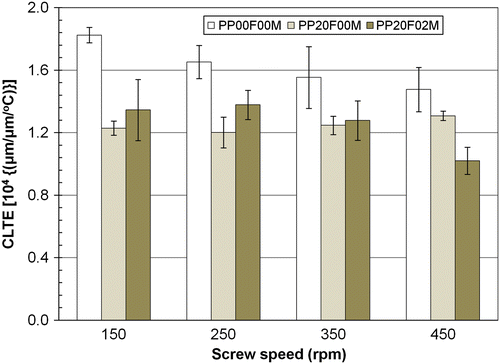
The CLTE is dependent on the resistance offered by the polymeric chains in a thermally activated process, and the presence of lignocellulosic fibres decreases the CLTE (Klyosov Citation2007). The average CLTE values of the PP00F00M decrease with a lower dwell period, which can be attributed to the lower rate of formation of –C = O and –OH radicals. The CLTEs of PP20F00M are lower than those of PP00F00M because of the stiffening action of the natural fibres. Within the four screw speeds, the CLTE values remain within one standard deviation, but show an increase at 450 rpm, which suggests a lower degree of consolidation as opposed to the 150–350 rpm cases. PP20F02M shows comparable values as PP00F00M, also within one standard deviation. However, the CLTE value at 450 rpm shows a lower value, which can be attributed to the preferable orientation of the fibres along the axial direction with a faster extrusion speed (Klyosov Citation2007). The same is true with injection moulding, where a longitudinal runner injects the particulate fibres along the axis of the dogbone specimens.
The CLTE is an indirect measure of mould shrinkage. As apparent from these observations, the CLTE of the neat resin is a strong function of changes in the processing parameters, whereas the filled/compatibilised materials show less variation, strengthening their rationale of usage and application.
5.2 Tensile properties
The elastic modulus obtained from the tensile test for all cases is shown in Figure (a). As shown, within each screw speed case, an increase in modulus was observed with the addition of the natural filler. On an average over all cases, about 25% increase was seen in PP20F00M composite, and about 40% increase was observed in the PP20F02M composite. Individually, over 350 rpm, only a minor change in the MAPP coupled composite was seen.
Figure 8 The variation in the (a) elastic modulus and (b) tensile strength of the three composite grades.
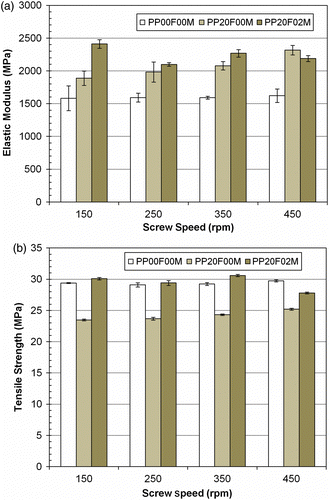
Figure (b) shows the tensile strength obtained from a tensile test. In the literature, often a decrease in tensile strength is reported with the addition of natural filler, whereas a partial improvement is reported with the addition of a compatibiliser, such as MAPP. In this study, a similar trend was observed for these composite, in all cases. The average decrease in tensile strength with the addition of MAPP alone is about 20%, whereas the average increase with the addition of MAPP coupling agent is about 22%. This observation is valid except in the 450-rpm case, where a decrease is seen in the tensile strength, consistent with the observations in CLTE behaviour.
The tensile properties of natural fibre-reinforced PP are a function of two effects. The modulus or stiffness increases with the addition of particulate natural fibres as they interrupt the long polymeric chains, thus increasing the brittleness (Mohanty et al. Citation2005). The tensile strength, however, takes a setback with natural fibre addition because of the same reason. Since the brittleness increases, the energy required to break the polymeric chains is discrete. Hence, although the initial resistance to deformation is higher over the neat polymer, the subsequent resistance to such deformational forces diminishes because of the presence of these fibres. Moreover, the addition of a compatibilisation agent such as MAPP to the PP matrix and the fibre acts to increase the degree of linkage between these two constituents (Bledzki et al. Citation1998, Fuqua and Ulven Citation2008).
The benefit of adding MAPP is greater towards the strength improvements rather than the modulus. As seen, PP200F02M shows an increase in strengths, with a peak at about 350 rpm. Further decrease in dwell time would cause a lower degree of melt mixing/consolidation. The improvements with MAPP addition in both modulus and strength show a similar strength, wherein the 350 rpm case shows benefits in both areas.
6. Summary and conclusions
A thermo-mechanical property analysis of the effect of extrusion screw speed on PP-based biocomposites was conducted. Three grades, i.e. (1) neat PP, (2) PP with natural fibre and (3) PP with natural fibre and a compatibiliser, were investigated at four screw speeds from 150 to 450 rpm in a 100-rpm increment. The materials were extruded and injection moulded and characterised using FTIR. Thermal expansion and tensile mechanical properties were determined.
The following conclusions were drawn from this study:
• | YI, which is an indicator of oxidation, decreased with decreasing extruder residence time; | ||||
• | FTIR analyses supported the thermo-oxidative degradation mechanisms arising from thermo-mechanical stresses and the presence of oxygen in the extruder; | ||||
• | Thermo-oxidative degradation and concomitant increases in carbonyl, hydroxyl and vinylidene absorbances increased with an increasing extruder residence time. The trends in these increases varied with the addition of MAPP compatibiliser and; | ||||
• | Overall, the greatest improvements in properties within the materials processed at the four extrusion speeds were found to be at an extruder residence time that corresponded to the balance of the optimum compounding and preclusion of sustained thermo-oxidation. For the PP/SFH/MAPP combination of this study, this optimal residence time was about 27–30 s. |
Acknowledgements
The authors would like to acknowledge financial assistance from the North Dakota Centre of Excellence – SUNRISE Bioproducts. The authors would also like to thank NDSU Research Specialists, Dr Darrin Haagenson and Dr Heidi Docktor for their technical assistance.
Additional information
Notes on contributors
Chad A. Ulven
1Notes
1. Email: [email protected]
References
- Achimsky , L. , Audouin , L. and Verdu , J. 1997 . Kinetic study of the thermal oxidation of polypropylene . Polymer Degradation and Stability , 57 ( 3 ) : 231 – 240 .
- Amash , A. and Zugenmaier , P. 2000 . Morphology and properties of isotropic and oriented samples of cellulose fibre-polypropylene composites . Polymer , 41 ( 4 ) : 1589 – 1596 .
- Anon, 2009a. [online]. Available from: http://pa.clariant.com/pa/e2wtools.nsf/lookupdownloads/k330gb_licomont_ar_504.pdf/$file/k330gb_licomont_ar_504.pdf [Accessed 21 June 2009]
- Anon, 2009b. [online]. Available from: http://www.ides.com/grades/ds/E4964.htm [Accessed 15 September 2009]
- Anon, 2009c. [online]. Available from: http://www.tainstruments.com/product.aspx?id = 25&n = 1&siteid = 11 [Accessed 15 September 2009]
- Bledzki , A. , Gassan , J. and Theis , S. 1998 . Wood-filled thermoplastic composites . Mechanics of Composite Materials , 34 ( 6 ) : 563 – 568 .
- Chevali , V. 2010a . “ Design and evaluation of biocomposite materials for an injection molded lawn tractor grab handle ” . In Global plastics environmental conference , Orlando, FL : Society of Plastics Engineers .
- Chevali , V.S. 2010b . Utilization of agricultural by-products as fillers and reinforcements in ABS . SAE International Journal of Materials and Manufacturing , 3 ( 1 ) : 221 – 229 .
- Chevali , V.S. 2010c . Utilization of agricultural by-products as fillers and reinforcements in ABS , ed. SAE World Congress 2010 Detroit, MI : Society of Automotive Engineers .
- Doan , T.-T.-L. , Gao , S.-L. and Mäder , E. 2006 . Jute/polypropylene composites I. Effect of matrix modification . Composites Science and Technology , 66 ( 7–8 ) : 952 – 963 .
- Fuqua , M.A. and Ulven , C.A. 2008 . Characterization of polypropylene/Corn fiber composites with maleic anhydride grafted polypropylene . Journal of Biobased Materials and Bioenergy , 2 ( 3 ) : 258 – 263 .
- Gassan , J. and Bledzki , A.K. 2000 . Possibilities to improve the properties of natural fiber reinforced plastics by fiber modification “jute polypropylene composites” . Applied Composite Materials , 7 ( 5 ) : 373 – 385 .
- Grassie , N. and Scott , G. 1985 . Polymer degradation and stabilisation , Cambridge : Cambridge University Press .
- Grozdanov , A. 2007 . Nonisothermal crystallization kinetics of kenaf fiber/polypropylene composites . Polymer Engineering and Science , 47 ( 5 ) : 745 – 749 .
- Gugumus , F. 2006 . Physico-chemical aspects of polyethylene processing in an open mixer. Part 19: Mechanisms and kinetics of vinyl and vinylidene group formation . Polymer Degradation and Stability , 91 ( 6 ) : 1333 – 1345 .
- International ASM . 2003 . Characterization and failure analysis of plastics , Materials Park, OH : ASM International .
- Klyosov , A.A. 2007 . Wood-plastic composites , Chichester : Wiley .
- Li , X. , Tabil , L. and Panigrahi , S. 2007 . Chemical treatments of natural fiber for use in natural fiber-reinforced composites: a review . Journal of Polymers and the Environment , 15 ( 1 ) : 25 – 33 .
- Mohanty , A.K. , Misra , M. and Drzal , L.T. 2005 . Natural fibers, biopolymers, and biocomposites , Boca Raton, FL : Taylor and Francis .
- Reddy , N. and Yang , Y. 2005 . Biofibers from agricultural byproducts for industrial applications . Trends in Biotechnology , 23 ( 1 ) : 22 – 27 .
- Renneckar , S. 2004 . Compositional analysis of thermoplastic wood composites by TGA . Journal of Applied Polymer Science , 93 ( 3 ) : 1484 – 1492 .
- Rowell , R. 1997 . Utilization of natural fibers in plastic composites: problems and opportunities , Lignocellulosic-Plastic Composites, São Paulo, USP & UNESP 23 – 51 .
- Rust , N. , Ferg , E.E. and Masalova , I. 2006 . A degradation study of isotactic virgin and recycled polypropylene used in lead acid battery casings . Polymer Testing , 25 ( 1 ) : 130 – 139 .
- Salemane , M.G. and Luyt , A.S. 2006 . Thermal and mechanical properties of polypropylene-wood powder composites . Journal of Applied Polymer Science , 100 ( 5 ) : 4173 – 4180 .
- Sarrabi , S. , Colin , X. and Tcharkhtchi , A. 2008 . Isothermal oxidation kinetics of unstabilized polypropylene in the molten state . Journal of Applied Polymer Science , 110 ( 4 ) : 2030 – 2040 .
- Scheirs , J. 2000 . Practical polymer analysis: techniques and strategies for the compositional and failure analysis of polymers, elastomers and composites , New York : Wiley .
- Schniewind , A.P. 1989 . Concise encyclopedia of wood & wood-based materials , Cambridge, MA : Pergamon Press .
- Scott , G. and Wiles , D.M. 2001 . Programmed-life plastics from polyolefins: a new look at sustainability . Biomacromolecules , 2 ( 3 ) : 615 – 622 .
- Tajvidi , M. and Takemura , A. 2010 . Thermal degradation of natural fiber-reinforced polypropylene composites . Journal of Thermoplastic Composite Materials , 23 ( 3 ) : 281 – 298 .
- van de Velde , K. and Kiekens , P. 2002 . Development of a flax/polypropylene composite with optimal mechanical characteristics by fiber and matrix modification . Journal of Thermoplastic Composite Materials , 15 ( 4 ) : 281 – 300 .
- Voigt , W. and Todesco , R. 2002 . New approaches to the melt stabilization of polyolefins . Polymer Degradation and Stability , 77 ( 3 ) : 397 – 402 .
- Yang , H.-S. 2007 . Effect of different compatibilizing agents on the mechanical properties of lignocellulosic material filled polyethylene bio-composites . Composite Structures , 79 ( 3 ) : 369 – 375 .