Abstract
This paper investigated the effect of combining rubber crumbs with recycled aggregates and fly ash on the mechanical properties and environmental impact of concrete. Increasing the amount of rubber crumbs linearly reduced strength and Young's modulus regardless of aggregate or binder type, but the effect of recycled aggregate on strength decreased as the amount of rubber crumbs increased. Air permeability also increased with the amount of rubber crumbs but the effect of recycled aggregates varied, as it was constant in the case of non-fly ash but completely reduced with fly ash. The mechanical–environmental efficiency was calculated by weighting the strength by the volume of raw materials, and recycled aggregates were found to have the highest efficiency whereas rubber crumbs were inefficient. When setting a specific strength level, the weighted strength could be used to select the most efficient combination of waste materials.
Introduction
Sustainable development was famously defined as the development which ‘meets the needs of the present without compromising the ability of future generations to meet their own needs’ by the Brundtland Commission (Citation1987). However, although this definition is widely accepted, the diversity of perspectives on what qualifies as ‘sustainable’ and the broad scope of sustainable development – including human, ecological, biological and other systems – make it difficult to practically adopt a single definition. This difficulty is illustrated in a large variety of meanings given to sustainability, with more than 100 different definitions from the literature presented by Pearce and Walrath (Citation2008).
For future human development, one important aspect of sustainability is the consumption of natural resources, the availability of which may have a significant impact on the development of future societies. Natural resources are necessarily consumed as building and construction materials when developing infrastructure for improving the quality of human life, and thus the sustainability of construction materials, including not only the cost and strength aspects but also the durability and environmental issues, need to be more strongly considered (Khatib Citation2009). In particular, concrete and reinforced concrete construction are globally utilised as the fundamental building blocks towards infrastructure development. Concrete is the second-most used resource after water (Sakai Citation2009), and the concrete industry is estimated to be one of the world's largest consumers of natural resources, with concrete production consuming roughly 10–11 billion tons of sand, gravel and crushed rock per year, in addition to over 1 trillion litres of water (Mehta Citation2001). At the other end of the life cycle, in 1998, worldwide generation of concrete and masonry rubble from construction demolition was estimated at roughly 1 billion metric tons (Lauritzen Citation1998); over the subsequent decade, however, this number has grown much larger due to increases in population and infrastructure development, particularly in Asia. Conversely, in Japan, the amount of construction waste discharge was observed to decrease from 1995 to 2005 from 99 million tons to 77 million tons due to reduced construction activities (Noguchi Citation2009).
The generation of construction waste, however, presents one means for the concrete industry to advance sustainable practice – through the recycling of its own demolition waste. A wide variety of research work has been conducted on the usage of recycled concrete demolition waste as a replacement for raw coarse aggregates in new concrete, and applications of and standards for construction and demolition waste can already be seen in many countries around the world (Hendriks et al. Citation2005). In Japan, where land available for disposal is limited, the recycling rate of concrete was up to 96% in 2000; however, the majority of this material was ‘down-cycled’ and used as backfill and sub-grade for road construction (MLIT Citation2009). This is partially due to issues related to Japanese acceptance standards (Kawano Citation2002), and partially due to the reduced quality of concrete utilising recycled aggregates, which is generally weaker and less durable than normal-aggregate concrete due to the interface and bond between the recycled aggregate and the new cement mortar matrix (Otsuki et al. Citation2003, Poon et al. Citation2004, Kou et al. Citation2007, Lo et al. Citation2008). However, satisfactory performance has been achieved through careful mix proportioning, specific mixing procedures and quality control.
Application of recycled coarse aggregates, however, only reduces the usage of raw coarse aggregates; therefore, to further reduce resource consumption, other waste materials need to be combined in concrete. The use of fly ash as a replacement for cement in concrete has been extensively investigated, with researchers reporting that its usage is generally beneficial when considering cost and fresh and hardened concrete properties (Mehta Citation1989). As fly ash is a by-product of the coal industry, this provides an opportunity for the concrete industry to practice industrial ecology by utilising the waste of other industries as a raw material in the concrete production process. Furthermore, the addition of fly ash to recycled aggregate concrete has been found to improve the concrete's properties, particularly durability, due to improvement of the pore structure and bonding (Corinaldesi et al. Citation2001, Ann et al. Citation2008, Reiner et al. Citation2010). Combining these two waste materials can contribute to reducing the consumption of both cement and coarse aggregates in new concrete; however, natural sand is still necessary for fine aggregates.
The recycling rate of the waste rubber tires in Japan is also high – roughly 89% in 2009 – but this material is generally not used as raw material in concrete [Japan Automobile Tyre Manufacturers Association (JATMA) Citation2009]. The usage of recycled rubber crumbs as a replacement for sand has, however, been investigated to some extent, with results showing that, while rubberised concrete has high-energy absorption capacity, it may not be attractive as a structural material due to its significantly reduced strength and its adverse effects on fresh and hardened properties (Eldin and Senouci Citation1994, Topçu Citation1995, Toutanji Citation1996). On the other hand, rubberised high-strength concrete (HSC) may be applicable when combined with mineral admixtures and extended curing (Wong and Ting Citation2009).
Considering these research results and setting the reduction of raw materials as a target, this research investigated the effect of replacing sand with recycled rubber crumbs in concrete containing both recycled aggregates and fly ash. HSC was set as the base concrete mix, and the effect of each combination of waste material on the hardened properties and on the environmental impact – evaluated as the volume of raw materials – was investigated. As it can be expected that such a combination will reduce the mechanical performance, the mechanical–environmental efficiency was also calculated by weighting the mechanical performance by the environmental impact and normalising it against a control material used to represent the general-use concrete.
Experimental programme
Materials
Concrete was prepared using tap water (W), type-I portland cement (C), Japan Industrial Standard (JIS) type-II fly ash (FA), river sand (S), recycled rubber crumbs (GC), normal coarse aggregates (NA), low-grade recycled coarse aggregates (RA), and air-entraining (AE) and super plasticiser (SP) admixtures. The density and fineness were 3.15 g/cm3 and 3300 cm2/g for cement and 2.19 g/cm3 and 4040 cm2/g for fly ash and met the specifications of JIS A 6201 [Japan Industrial Standard (JIS) Citation1999]. The specific properties of the utilised JIS type-II fly ash are also shown in Table . The recycled aggregate, shown in Figure , was obtained from crushed demolition waste processed and classified by the recycled aggregate supplier as low-grade following JIS A 5023 (JIS Citation2006a) specifications summarised in Table . Wastes mixed with the recycled aggregates such as wood, glass and so on were removed prior to mixing. The density and absorption were measured according to JIS A 1110 (JIS Citation2006b) and are given in Table along with the properties for sand, rubber crumbs and normal coarse aggregates. Based upon the measured results, the low-grade recycled aggregates were submerged in water for 2 days prior to casting and then surface dried using cloth in order to obtain saturated surface dry conditions. Rubber crumbs with a maximum size of 3 mm, as shown in Figure , were processed from waste tires, and no steel wires or other materials were included.
Table 1 Properties of utilised JIS type-II fly ash.
Table 2 JIS recycled aggregate specifications.
Table 3 Properties of sand, rubber crumbs and coarse aggregates.
Mix proportions
Concrete mix proportions and fresh concrete properties are given in Table . The water–binder ratio was set at 0.3, and two recycled aggregate replacement ratios (0 and 100% by volume), two binder combinations (C100% and C50%–FA50% by mass) and three rubber crumb replacement ratios (0, 25 and 50% replacement of sand by volume) were selected for this experimental investigation. A control concrete with a water–binder ratio of 0.5 and no waste or recycled materials was also prepared to serve as a reference for the normal-use concrete.
Table 4 Mix proportions and fresh properties.
Specimens and curing
Cylinder (10Ø × 20 cm) specimens were cast for each concrete mix. After casting, moulded specimens were covered in plastic wrap and cured in the moulds for 24 h, after which they were removed from the moulds and placed in water curing at 20–21°C.
Testing and environmental impact assessment
Compressive strength was measured according to JIS A 1108 (JIS Citation2006c) and conducted at 7, 28 and 91 days. Young's modulus was measured according to JIS A 1149 (JIS Citation2010) at 28 days using stress values calculated from the compressive strength load data and strain values obtained from strain gauges installed on the cylinder under compressive testing. The reported values are the average of three specimens.
The air permeability coefficient, an indicator of durability, was also measured at 28 days as follows. Air permeability specimens were taken from cylinders by cutting a 40 mm-thick section from the centre of the cylinder. Specimens were then placed in an oven and dried for 1 week at 40°C. After dry conditions were met, the specimens were set into the air permeability machine and the volume of air flow was measured under the steady-state conditions. The air permeability coefficient was calculated from the loading pressure, specimen thickness, volume of air flow and sectional area, and the reported values are the average of three specimens.
The environmental impact was assessed using the volume of raw materials, which was calculated from the per cent volume of cement, water, sand and normal aggregates per cubic metre of concrete. Therefore, if the volume of raw materials in a given mix decreases, then this is assumed to represent a reduction in the natural-resource consumption and thus a reduced environmental impact. CO2 emissions and input energy – which may conversely increase in the case of waste and recycled materials due to processing – were not considered in this investigation due to a lack of inventory data on the rubber crumbs.
Results
Compressive strength
Compressive strength development from 7 to 91 days is shown in Figure for the concrete mixes with 0, 25 and 50% rubber crumb replacement ratios. At 0% rubber crumbs, the strength development of concretes with normal aggregate (both 100% cement and 50% cement–50% fly ash) and concrete with recycled aggregate and fly ash follows a similar trend, with the largest difference occurring from casting up to 7 days. In the case of concrete with recycled aggregate and no fly ash, very little strength gain was observed from 28 to 91 days; this may indicate that the bond between the high-strength mortar and the low-grade recycled aggregate is limiting the strength gain, as the mix with normal aggregates and 50% fly ash exceeds this mix's strength by 91 days. The strength development of the mix combining recycled aggregates and 50% fly ash is close to the behaviour of the control mix up to 91 days.
Figure 3 Compressive strength development from 7 to 91 days for 0% (top), 25% (middle) and 50% (bottom) rubber crumb replacement ratios.
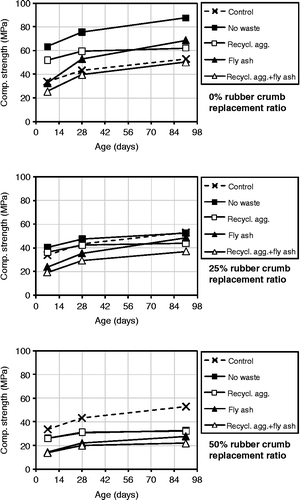
At 25% replacement of sand with rubber crumbs, the overall strength levels are much lower than for 0% rubber crumbs and are either comparable to or lower than the control series, and there is less strength development observed from 28 to 91 days. Furthermore, the difference between the normal and recycled aggregates is smaller, but again little strength gain is observed for the mix with recycled aggregate and no fly ash from 28 to 91 days. Finally, at 50% rubber crumbs, the strength levels of all series are much lower than the control series and little to no strength development can be seen after 28 days, except in the case of the concrete with normal aggregates and 50% fly ash.
The effect of the rubber crumb replacement ratio on the 28-day compressive strength is shown in Figure . Increasing the amount of rubber crumbs linearly reduces the compressive strength, regardless of binder composition or coarse aggregate type. The concretes with normal aggregates lose the greatest percentage of strength (59.1 and 58.6% for 100% cement and 50% cement–50% fly ash, respectively) when increasing the rubber chip replacement ratio from 0 to 50%; in contrast, the concretes with recycled aggregate lose only 47.8 and 49.8% for normal cement and 50% fly ash, respectively. The effect of recycled aggregates and fly ash is also reduced as the amount of rubber crumbs increases, but by 50% rubber crumb replacement ratio only the effect of fly ash can be seen. Increasing the amount of rubber crumbs to 25% reduces strength below the level of the control mix for the fly ash concretes, and at 50% rubber crumb replacement ratio all mixes have lower strength than the control.
Young's modulus
Figure shows the effect of rubber crumb replacement ratio on the 28-day Young's modulus. Similar to the 28-day compressive strength, increasing the replacement ratio linearly reduces the Young's modulus. Unlike the compressive strength, however, the effect of recycled aggregate and fly ash remains fairly constant at all replacement ratios. It can also be seen that Young's modulus for concretes with just fly ash and concretes with just-recycled aggregate is nearly the same, regardless of the amount of rubber crumbs. Young's modulus of the control series is higher than that of all series, except for the concrete containing no waste materials.
The relationship between 28-day compressive strength and Young's modulus is shown in Figure . In this figure, the Japan Society of Civil Engineers (JSCE Citation2002) standard curve is used as a reference. The standard curve generally overestimates Young's modulus for most of the concrete mixes, with the exceptions being the control mix and the two mixes containing 25% rubber crumbs without recycled aggregates. Other mixes without recycled aggregates also fall near to the standard curve, but mixes with recycled aggregates generally fall further below the curve, regardless of the amount of rubber crumbs.
Compressive failure mode
Differing failure modes under compressive loading could also be observed, as shown in Figure . Mixes without rubber crumbs, particularly those with high strength such as the non-fly ash concretes with normal and recycled aggregates, underwent brittle failure with specimens suddenly exploding into small pieces at the peak load. On the other hand, usage of 25% rubber crumbs significantly affected this failure mode, with specimens failing in a much less brittle fashion. The strength of these specimens, however, is much lower than that of the high-strength specimens but comparable to the strength of the normal concrete mix, and Figure shows that even at this strength level normal concrete also undergoes brittle failure under compressive loading, so the effect of rubber crumbs on failure mode can be clearly seen.
Air permeability
The air permeability coefficient measurement results are given in Figure . The effect of rubber crumbs is markedly different depending on the binder composition. For non-fly ash concrete, increasing the amount of rubber crumbs increases the air permeability consistently, with a smaller increase from 25 to 50% than from 0 to 25%. A large difference can also be seen between the normal and recycled aggregates for the non-fly ash concretes, with this difference remaining fairly constant regardless of rubber crumb replacement ratio. For the fly ash concretes, however, increasing the amount of rubber crumbs from 0 to 25% has little effect on the air permeability, but increasing from 25 to 50% produces a large increase. In addition, the type of aggregate does not have as large an effect in the fly ash concretes as it does in the non-fly ash concretes.
Environmental impact
The calculation results for volume of raw materials are shown in Figure . Increasing the rubber crumb replacement ratio linearly decreases the volume of raw materials roughly 6% for each 25% increase in amount of rubber crumbs. Replacement of 50% cement with fly ash reduces the volume of raw materials roughly 12%, whereas the usage of 100% recycled aggregates reduces the volume of raw materials to roughly 37%. The combination of both fly ash and recycled aggregates can achieve roughly a 47% reduction, with the combination of all three waste and recycled materials reaching a maximum reduction of 52.8 and 58.5% for 25 and 50% rubber crumb replacement ratio, respectively.
Relationship between mechanical and environmental
To examine the relationship between environmental impact and mechanical performance, the volume of raw materials and 28-day compressive strength is plotted together in Figure . As both these properties varied linearly with the amount of rubber crumbs, the relationship between them is also linear with compressive strength increasing as the volume of raw materials increases. The data points fall into two main groups depending on the type of aggregate, with recycled aggregate mixes having the lowest volume of raw materials but lower strength than the normal-aggregate mixes. The results of the mixes combining fly ash and recycled aggregates and the mixes with just-recycled aggregates also follow a linear trend, with the strength and volume of raw materials of the mixes combining fly ash, recycled aggregates, and 0 and 25% rubber crumbs falling near to the strength and volume of raw materials of the mixes combining recycled aggregate with 25 and 50% rubber crumbs. The difference between fly ash and non-fly ash mixes is slightly larger in the case of the normal-aggregate concretes.
Mechanical–environmental efficiency
While Figure clearly shows that decreasing the volume of raw materials reduces strength, it is difficult to determine which mix has the best balance of strength and raw materials – that is, the most efficient combination of mechanical and environmental performance. The following equation was proposed to evaluate the mechanical–environmental efficiency by creating a weighted strength index which considers both the compressive strength as well as the usage of raw materials. This concept is similar to the ‘environmental performance indicator’ as proposed by Nielsen (Citation2009), which focused on CO2 emissions,
The calculation results are shown in Figure , where the effect of rubber crumb replacement ratio on the weighted strength can be seen. Relative to the normal compressive strength results, the weighted strength of the mixes with only rubber crumbs increased only slightly, as did the mixes combining fly ash and rubber crumbs. Mixes combining fly ash and recycled aggregates with rubber crumbs have the second highest weighted strength. Furthermore, at 0% rubber crumb replacement ratio the weighted strengths of the mix combining fly ash and recycled aggregates and the mix with no waste materials are roughly the same; however, increasing the amount of rubber crumbs reduces the weighted strength faster in the case of the concrete with no waste, indicating that combining all three waste materials together is more efficient than utilising rubber crumbs on their own. Finally, the mixes with recycled aggregates and rubber crumbs have the highest weighted strengths.
The efficiency of the normal-use concrete is represented by the weighted strength of the control mix, so to understand the efficiency of the concretes using waste materials relative to this baseline, the weighted strengths were normalised by the control mix. The results, given in Figure , show that almost all combinations of waste materials are more efficient than the control mix. The only exceptions to this result are the mixes using 50% rubber crumbs only or with fly ash. Concretes combining recycled aggregates with fly ash, with no waste materials and combining 25% rubber crumbs with recycled aggregates all have comparable efficiency and are the second highest behind the concrete with only recycled aggregates.
Discussion
The test results showed that the usage of rubber crumbs clearly reduces the mechanical performance; however, combining rubber crumbs with other waste materials reduces mechanical performance even further, as the best compressive strength and Young's modulus (and reasonable air permeability) were all obtained in the case of HSC containing only rubber crumbs. The bonding between rubber and hardened paste has been cited as a weakness in rubberised HSC (Wong and Ting Citation2009), and the results shown here demonstrate that this may also be the case even when using fly ash, as the amount of strength development between 28 and 91 days decreased as the amount of rubber crumbs increased. One exception to this is the combination of fly ash and rubber crumbs, which generally had a higher strength development in this time period compared with the other rubberised concrete mixes. The usage of fly ash also showed some benefit regarding air permeability, as the air permeability coefficient of concrete combining rubber crumbs and fly ash was generally lower than when fly ash was not used, although there was some unclear behaviour when the amount of rubber crumbs was increased to 50%. The improvement of air permeability without an improvement in strength shows that, while fly ash may not necessarily improve the bonding of the cement matrix with the rubber crumbs, it can contribute to reducing mass transport properties to some extent. In addition, it was also observed that as the rubber crumb replacement ratio increased, the effect of recycled aggregate was greatly reduced in the case of compressive strength, but this trend was different for air permeability, where the behaviour varied depending on whether fly ash was included. In non-fly ash concrete, the effect of recycled aggregate on air permeability remained fairly constant even when 50% rubber crumbs were included, but for fly ash concrete the effect of recycled aggregate was almost entirely reduced when rubber crumbs were included. Therefore, fly ash does not serve to improve the bonding with recycled aggregates (as similar differences in strength between normal and recycled aggregates were observed for both non-fly ash and fly ash concretes), but it can improve air permeability when combined with both recycled aggregate and rubber crumbs.
Weighting the compressive strength by the volume of raw materials was conducted as a way to consider the environmental impact along with the mechanical performance. Considering this calculation, most combinations of waste materials may be considered more ‘efficient’ than the control mix, as was shown when the weighted strengths were normalised by the control mix. However, when considering the actual specification of concrete materials, the foremost requirement is that the concrete meets a certain performance requirement, and the weighted strength does not explicitly consider this as it is a function of both strength and volume of raw materials. However, the normalised weighted strength may be useful when comparing mixes with similar strength levels. The control mix, used to represent a ‘normal concrete’, had a 28-day strength of 43.5 MPa. Other mixes with compressive strengths around this level include recycled aggregates and fly ash at 39.7 MPa, 25% rubber at 47.6 MPa, recycled aggregates and 25% rubber at 42.2 MPa, and fly ash and 25% rubber at 35.4 MPa; the normalised weighted strengths for these four mixes are 1.73, 1.16, 1.71 and 0.99, respectively. From this comparison, it can be said that at this strength level the combination of recycled aggregates and fly ash has the best balance of mechanical and environmental performance while meeting the strength requirement. Performing a similar exercise with a target strength level of around 30 MPa would yield recycled aggregates, fly ash and 25% rubber (28-day strength: 29.1 MPa) as the most efficient combination of waste materials. This methodology of weighting mechanical by environmental to identify the efficiency of different combinations of waste materials could also be extended to other properties as well as to other mix proportions or wastes.
Conclusion
The following conclusions were made based on the results of this experimental investigation:
• | Increasing the amount of rubber crumbs from 0 to 50% linearly reduced the compressive strength, regardless of the aggregate or binder type, and also reduced the rate of strength development from 28 to 91 days. Combination of rubber crumbs with recycled aggregates, with fly ash and with both recycled aggregates and fly ash reduced strength in that order. As the amount of rubber crumbs increased, the effect of recycled aggregates on strength was reduced until only the effect of fly ash could be seen at 50% rubber crumb replacement ratio. The usage of fly ash did not appear to improve bonding between the rubber crumbs and the cement matrix nor between the recycled aggregates and the cement matrix. | ||||
• | Increasing the amount of rubber crumbs also linearly reduced Young's modulus, and the effect was the same regardless of aggregate or binder type. The effect of fly ash and recycled aggregate could be seen even when increasing the amount of rubber crumbs to 50%. The JSCE standard curve was found to overestimate Young's modulus of nearly all the experimental series. | ||||
• | The usage of 25% rubber crumbs could drastically reduce brittle failure under compression loading and prevent explosive destruction of the high-strength specimens. This was observed to occur both when the water–binder ratio was held constant, as well as between mixes with comparable compressive strength, and also for both normal and recycled aggregates. | ||||
• | The effect of rubber crumbs on the air permeability coefficient depended primarily on the binder type. In the case of non-fly ash concretes, air permeability increased steadily as the amount of rubber crumbs increased, and the effect of recycled aggregates was marked and constant. For fly ash concretes, increasing the rubber crumbs to 25% produced only a small change, but increasing to 50% drastically increased the air permeability. The effect of recycled aggregates was small regardless of the rubber crumb replacement ratio, and the effectiveness of fly ash for improving the air permeability of both rubber crumb and recycled aggregate concretes could be seen. | ||||
• | The mechanical–environmental efficiency of the mixes was calculated using an index which weighted the compressive strength by the volume of raw materials in each experimental mix. Overall, the usage of only 100% recycled aggregates had the highest efficiency, followed by the mixes with no waste materials, combining recycled aggregate with 25% rubber crumbs, and combining recycled aggregates with fly ash. Rubber crumbs were found to be an inefficient means for reducing environmental impact when using the weighted strength as an evaluation index. When comparing the weighted strengths of concretes at a target strength level, the combination of recycled aggregates and fly ash was most efficient at the 40 MPa level and the combination of recycled aggregates, fly ash and 25% rubber crumbs was most efficient at the 30 MPa level. | ||||
• | While the mechanical–environmental efficiency calculated here was based on the reduction of raw materials (the target of this research), other mechanical properties or environmental impacts may also be used, for example, Nielsen (Citation2009) proposed weighting the strength by the CO2 emissions to create an ‘environmental performance indicator’. The usage of fly ash, in particular, contributes not only in reducing the consumption of resources used in cement production but also significantly reducing the CO2 footprint in concrete when replacing cement. Although this factor was not considered in this research due to the lack of inventory data on the rubber crumbs, future works should consider the balance between different environmental impacts in addition to the mechanical–environmental efficiency. |
References
- Ann , K.Y. 2008 . Durability of recycled aggregate concrete using pozzolanic materials . Waste Management , 28 : 993 – 999 .
- Brundtland , G. 1987 . Our common future, report of the World Commission on Environment and Development , Oxford : Oxford University Press .
- Corinaldesi , V. 2001 . “ Feasibility and performance of recycled aggregate in concrete containing fly ash for sustainable buildings ” . In ACI SP-202 sustainable development of cement and concrete , Edited by: Malhotra , V.M. 161 – 180 . Farmington Hills : ACI .
- Eldin , N.N. and Senouci , A.B. 1994 . Measurement and prediction of the strength of rubberized concrete . Cement and Concrete Composites , 16 : 287 – 298 .
- Hendriks , C.F. , Janssen , G.M.T. and Vázquez , E. , eds. 2005 . RILEM report 30: use of recycled materials , Bagneux : RILEM Publications S.A.R.L .
- Japan Automobile Tyre Manufacturers Association . 2009 . Tyre industry of Japan , Tokyo : JATMA . (in Japanese)
- Japan Industrial Standard . 1999 . Fly ash for use in concrete, JIS A 6201:1999 , Tokyo : JIS . (in Japanese)
- Japan Industrial Standard . 2006a . Recycled concrete using recycled aggregate class L, JIS A 5023:2006 , Tokyo : JIS . (in Japanese)
- Japan Industrial Standard . 2006b . Methods of test for density and water absorption of coarse aggregates, JIS A 1110:2006 , Tokyo : JIS . (In Japanese)
- Japan Industrial Standard . 2006c . Method of test for compressive strength of concrete, JIS A 1108:2006 , Tokyo : JIS .
- Japan Industrial Standard . 2010 . Method of test for static modulus of elasticity of concrete, JIS A 1149:2010 , Tokyo : JIS . (in Japanese)
- Japan Society of Civil Engineers . 2002 . Standard specifications for concrete structures – 2002 “materials and construction” , Tokyo : JSCE .
- Kawano , H. 2002 . “ The state of using by-products in concrete in Japan and outline of JIS/TR on “recycled concrete using recycled aggregate” . In Proceedings of the 1st fib Congress , 1 – 10 . Tokyo : Japan Concrete Institute .
- Khatib , J. 2009 . Sustainability of construction materials , Cambridge : Woodhead Publishing Limited .
- Kou , S.C. , Poon , C.S. and Chan , D. 2007 . Influence of fly ash as cement replacement on the properties of recycled aggregate concrete . Journal of Materials in Civil Engineering , 19 ( 9 ) : 709 – 717 .
- Lauritzen , E.K. 1998 . “ The global challenge for recycled concrete ” . In Symposium on sustainable construction: the use of recycled concrete aggregate , 505 – 519 . London : Thomas Telford .
- Lo , C.Y. 2008 . “ Comparison of recycled and natural aggregate properties ” . In Third ACF International Conference , 450 – 454 . Hanoi : Vietnam Institute for Building Materials .
- Mehta , P.K. 1989 . “ Pozzolanic and cementitious by-products in concrete – another look ” . In ACI SP-114 Fly ash, silica fume, slag and natural pozzolans in concrete , Edited by: Malhotra , V.M. 1 – 43 . Farmington Hills, MI : ACI .
- Mehta , P.K. 2001 . Reducing the environmental impact of concrete . Concrete International , 23 ( 10 ) : 61 – 66 .
- Ministry of Land, Infrastructure, and Transportation . 2009 . MLIT annual report , Tokyo : MLIT . (in Japanese)
- Nielsen , C.V. 2009 . “ Towards sustainable concrete structures ” . In Sustainability in concrete and concrete structures , 1 – 17 . Tokyo : The University of Tokyo .
- Noguchi , T. 2009 . “ Outline of recommendations for environmentally conscious practice of RC buildings published by AIJ ” . In Proceedings of the International fib Symposium, Concrete: 21st Century Superhero , Camberly, Surrey : The Concrete Society .
- Otsuki , N. , Miyazato , S. and Yodsudjai , W. 2003 . Influence of recycled aggregate on interfacial transition zone, strength, chloride penetration and carbonation of concrete . Journal of Materials in Civil Engineering , 15 ( 5 ) : 443 – 451 .
- Pearce , A. and Walrath , L. 2008 . “ Definitions of sustainability from the literature ” . In Sustainable facilities and infrastructure , Atlanta, GA : Georgia Tech Research Institute .
- Poon , C.S. , Shui , Z.H. and Lam , L. 2004 . Effect of microstructure of ITZ on compressive strength of concrete prepared with recycled aggregates . Construction and Building Materials , 18 : 461 – 468 .
- Reiner , M. , Durham , S.A. and Rens , K.L. 2010 . Development and analysis of high-performance green concrete in the urban infrastructure . International Journal of Sustainable Engineering , 3 ( 3 ) : 198 – 210 .
- Sakai , K. 2009 . “ Towards environmental revolution in concrete technologies ” . In Proceedings of the International fib Symposium, Concrete: 21st Century Superhero , Camberly, Surrey : The Concrete Society .
- Topçu , İ.B. 1995 . The properties of rubberized concretes . Cement and Concrete Research , 25 ( 2 ) : 304 – 310 .
- Toutanji , H.A. 1996 . The use of rubber tire particles in concrete to replace mineral admixtures . Cement and Concrete Composites , 18 : 135 – 139 .
- Wong , S.F. and Ting , S.K. 2009 . Use of recycled rubber tires in normal- and high-strength concretes . ACI Materials Journal , 106 ( 4 ) : 325 – 332 .