Abstract
A prediction for product gases of Jatropha curcas Linn (JCL) oil cake gasified in the entrained flow reactor is studied in this paper. ASPEN PLUS commercial software is used to carry out the simulation using Gibbs free energy minimisation with equilibrium phase. A series of simulations and analyses have been carried out to investigate the composition of product gases in JCL oil cake with reactor temperature ranging from 1000 to 1400°C. In the first prediction step, the gas composition of sawdust and rice husk are validated. After this, the simulation model is used to predict JCL oil cake gas composition. Mean error analysis is carried out to identify the maximum and minimum error of the simulation. The results show that with increasing reactor temperature, the amount of carbon monoxide (CO) and hydrogen (H2) increases while the amount of carbon dioxide (CO2) and methane (CH4) decreases. The results of the gas composition of JCL oil cake show that the CO content at a temperature of 1000°C ranges from 41.35% to 53.36%. Composition of other gases such as hydrogen (H2), carbon dioxide (CO2), methane (CH4) is 24.65–32.7%, 4.4–22.99% and 0.94%–19.62%, respectively.
Nomenclature
a | = |
Attraction parameter |
b | = |
Van der Waals co-volume |
| = |
Standard specific heat at constant pressure |
f i | = |
Fugacity species i |
| = |
Standard fugacity species i |
f(L) | = |
Lagrange function |
g | = |
Atom balance |
h_B | = |
Enthalpy of biomass |
h_G | = |
Enthalpy of the product gas |
h_R | = |
Enthalpy of reaction |
G t | = |
Total Gibbs free energy (kJ) |
G 0 | = |
Gibbs free energy (kJ/kmol) |
N | = |
Total number of data points |
n | = |
Number of mol |
P | = |
Pressure (bar) |
P i | = |
Pressure in species i (atm) |
| = |
Standard pressure in species i (atm) |
R | = |
gas constant (8314 kJ/kmol K) |
RSS | = |
Residual sum of squares |
T | = |
Absolute temperature (K) |
v | = |
Molar volume |
x i | = |
Mol fraction of species i |
x i,e | = |
Mol fraction of species i on experiment |
x i,sim | = |
Mol fraction of species i on simulation |
y i | = |
Mol fraction of species i |
μ | = |
Chemical potential |
Subscript | = | |
λ | = |
Lagrange multipliers |
− | = |
Endothermic |
+ | = |
Exothermic |
e | = |
Experiment |
sim | = |
Simulation |
1. Introduction
During the last decades, the world energy consumption has increased significantly. This is mainly because of population growth and industrialisation. Furthermore, the conventional fossil fuels such as oil, coal and natural gas have been favoured by countries. The world population growth has led to an increase in energy consumption from 3.8 billion toe in 1965 to 11.3 billion toe in 2008 (Jess Citation2010). This condition has been contradicted with the fact that the world's energy resource has been depleted. Saxena et al. (Citation2009) showed that the world's crude oil reserves are estimated to get depleted by 2050. Furthermore, the use of conventional fuels produces greenhouse gas emissions. These gases contaminate the atmosphere and cause global warming effects. According to Onishi (Citation2007), the amount of carbon dioxide (CO2) released to the atmosphere globally was about 25,811.54 metric tons carbon equivalent (MCTE) in 2000 and will be increased to about 51,809 MCTE in 2020.
To prevent the negative impact on the environment, biomass can be used as an alternative fuel, which is a sustainable energy resource. Biomass is an organic material derived from plant or living matter. In fact, using biomass for energy production also releases CO2 to the atmosphere, but this CO2 will be absorbed during photosynthesis. Hence, biomass can be considered as carbon-neutral referring to the carbon cycle in the atmosphere. The world's future biomass potential is predicted to be in the range of 33–1130, consisting of biomass production on surplus agricultural land, biomass production on degraded lands, agricultural residues, forest residues, animal manure (dung), tertiary residue (organic waste) as well as biomaterials (Hoogwijk et al. Citation2003). Biomass contributes to 239 TWh of world's electricity supply currently and has the potential to exceed 4800 gigawatts (GW) by 2030 (IEA Citation2010).
In the last decades, one of the most widely developed plants for energy production is Jatropha curcas Linn (JCL). Several countries from Asia and Africa as well as South America such as Indonesia (Hambali et al. Citation2007), Thailand (Prueksakorna et al. Citation2010), India (Shah et al. Citation2005) and Nicaragua (Foidl et al. Citation1996) have developed biodiesel from its seed. The advantage of using JCL species as a future energy plant lies in its ability to grow in marginal soil and reach reasonable production output (Jongschaap et al. Citation2007). This means that the JCL does not compete with food plant, which has become an issue in world food security. The conversion process of JCL into crude Jatropha oil (CJO) is shown in Figure .
As reported by Openshaw (Citation2000) and Banerji et al. (Citation1985), the content of cake seeds of JCL reaches 61–67% per unit weight. Meanwhile, the content of CJO is around 33–39%. This means that there is a high possibility to convert JCL waste to energy from both shell and oil cake.
Currently, the gasification process is undergoing significant development. This is because due to gasification, the quality of the produced gas can be standardised, and the gas is also more versatile to use (McKendry Citation2002). The gasification of biomass has been studied by many authors (Mansaray et al. Citation1999, Jayah et al. Citation2003, Na et al. Citation2003, Li et al. Citation2004, Lv et al. Citation2004, McLendon et al. Citation2004, Lv et al. Citation2007, Vyas and Singh Citation2007, Dai et al. Citation2008, Doherty et al. Citation2009, Zhou et al. Citation2009, Sheth and Babu Citation2010). Some of these studies are concerned with process simulation (Jayah et al. Citation2003, Mehrdokht et al. 2008, Doherty et al. Citation2009). Lv et al. (Citation2004) carried out high-pressure co-gasification at a pressure of 30 bars with a mixed biomass feedstock and coal. Gases extraction using JCL waste is a new area in the gasification research. D.K. Vyas and R.N. Singh studied the gasification of JCL seed husk in an open core reactor (Vyas and Singh Citation2007). According to these studies increasing the feedstock flow rates from 4.5 to 5.5 m3h− 1 decreases hydrogen (H2) in the product gas composition while the composition of other product gases increase. Neither experimental nor simulation research on gasification of JCL oil cake has been published. The gasification of JCL oil cake in this research is the new idea to utilise this waste to produce syngas. The objective of this study was to predict the composition of JCL oil cake gases in the gasification process. Simulation compositions are validated by using sawdust and rice husk in an entrained flow reactor. The composition is predicted by the use of ASPEN PLUS process simulator (http://aspentech.com). The flowsheet will predict steady-state performance of entrained flow reactor with pure oxygen as the gasification agent. The syngas product is estimated by Gibbs free energy minimisation at equilibrium phase. Restricted equilibrium is used to set the product gas.
2. Methodology
2.1 Process description
The gasification process consists of a feeding system, a gasification reactor, a cleaning system and a cooling system. The substance flows sequentially from a feeding system to a cooling system. The feedstock enters the gasifier through the upper or sidewall. An automatic feeding system having a double piston is applied to prevent the gas from flowing out of the reactor. Highly complex reactions occur inside the reactor. Depending on the reactor type, these reactions occur in varying sequences.
In the gasifier, four processes occur: drying, pyrolysis, oxidation and reduction. The drying process is the mass transfer in the material, which reduces the amount of moisture. It is then converted by heat from liquid to gas phase. The gas phase of moisture then reacts with other gases in the next reaction. The pyrolysis process occurs when the material decomposes into some of the substances without oxygen. The temperature ranges around 300–800°C and releases the substances such as CO, CO2, CH4, H2, H2O and C. These substances react in oxidation as well as in reduction reaction. The steps of chemical reaction including the amount of enthalpy amount are provided in Table .
Table 1 Chemical reactions in the gasifier.
The chemical reactions of gasification are partly endothermic and partly exothermic, but the overall gasification reaction is endothermic. The drying and pyrolysis product will react in oxidation and reduction with the additional gasification agents such as steam, air or pure oxygen. Inside the gasification reactor, the temperature varies between 500 and 1500°C. Pressure can vary from atmospheric to high pressure.
Gasification reactors currently available are fixed bed reactors, which consist of updraft and downdraft flow. The differences in these reactors are the feedstock flow and gasification agents. The feedstock and gasification agent in the updraft gasifier flow in opposite directions. The feedstock enters from the upper side while the gasification agents enter from the lower side. The reaction occurring from upper to lower side consists of drying, pyrolysis, reduction and oxidation. The oxidation reaction takes place at the bottom side. The product gases flow upward and leave the gasifier from the upper side. The product gas releases heat while it is flowing. This heat is absorbed by other reactions. The downdraft type improves the reactor performance concerning tar concentration. The feedstock enters through the upper side while the gasification agent enters from the sidewall. The formation of reactions in the downdraft reactor differs when compared with that of the updraft reactor.
In the fluidized bed reactor, sand (SiO2) is commonly used as the solid agent to improve heat transfer inside the reactor (Li et al. Citation2004, Sheth and Babu Citation2010). The temperature ranges from 500 to 1000°C. The disadvantage of using this reactor is the agglomeration and sintering of ash, which causes a problem during the process (Mansaray et al. Citation1999). The suitable feedstock for this reactor is feedstock which has low ash content. The entrained flow reactor improves the performance gasification regarding sintering and agglomeration. It uses high temperatures reaching 1400°C. Several researchers have studied this gasifier (Lee et al. 1996, Mansaray et al. Citation1999, Zhou et al. Citation2009). Zhou et al. (Citation2009) used a pre-heater device to increase the oxygen temperature to 400°C. Lee et al. (1996) used oxygen temperature of 250°C.
2.2 Simulation description
The objective of the simulation process is to estimate the composition of the product gas by calculating mass and energy balance as well as chemical equilibrium of the process. The software gives information of thermodynamics data, operational condition as well as builds the appropriate model. ASPEN PLUS has databases that include pure components as well as phase equilibrium data for conventional chemicals, electrolytes, solids and polymers. Additional data, such as the molecular weight, normal boiling point, specific gravity at 60 F (288 K) and standard enthalpy as well as Gibbs energy formation, can be given by the user. Non-conventional component is used for the coal and biomass stream because of the complexity of chemical structure. Working with this component includes proximate, ultimate and sulphur analyses. This is used to calculate the enthalpy in the property methods.
In ASPEN PLUS, blocks are placed into the flowsheet window. Streams connect these blocks to each other. The streams include material, heat and work, while the block models include mixer, separator, heat exchanger, column, reactor, pressure changers, manipulators, solid and user models.
3. Modelling
3.1 Model assumption
In modelling work, assumptions need to be set. The purpose is to create a model that is as realistic as possible. The assumptions for this model are as follows:
• | The process is the steady state. | ||||
• | The reactor is assumed in uniform bed temperature. | ||||
• | Char contains carbon and ash. | ||||
• | Drying and pyrolysis occur simultaneously in block RYIELD. | ||||
• | Oxidation and reduction reactions occur in block RGIBBS. | ||||
• | The pyrolysis product is assumed by the equivalent elemental component. | ||||
• | The separation system is assumed to have a cyclone having 100% separation efficiency. | ||||
• | The nitrogen stream is assumed flowing together with the biomass stream. |
3.2 Model description
In the gasification process, drying and pyrolysis occur in block RYIELD, while the oxidation and reduction occur in block RGIBBS as shown in Figure . In reality, the reaction occurs simultaneously in one reactor and no separated block RYIELD and RGIBBS. The gasification agent also flows into the reactor simultaneously with biomass feedstock. Block SEP is used to separate product gases from solids. The solid component consists of two substances, carbon (C) and ash, while the gas components consist of many substances. Stream FEED is biomass material, and it is the fuel to the gasifier. Biomass is handled in ASPEN PLUS as a non-conventional component, so no data can be found for it in the databanks. The HCOALGEN model is used to calculate the heating value, heat capacity, heat of formation and heat of combustion.
3.2.1 Biomass decomposition
Block RYIELD is used to decompose the non-conventional component FEED to conventional components such as C, H, O and N. This process includes drying, which releases moisture (H2O). In the pyrolysis process, the FEED will break down into steam (H2O), carbon (C), hydrogen (H2), nitrogen (N2), oxygen (O2), sulphur (S) and ash. The breakdown system is used because the block RGIBBS cannot perform the complex structure in the non-conventional component like biomass. After the decomposition of FEED, the product yield (stream 1) is mixed with oxygen and nitrogen in this process.
3.2.2 Oxidation and reduction reactions
Block RGIBBS simulates both oxidation and reduction reactions. This also includes the option for restricted chemical equilibrium, which can be specified with either restricted temperature approach or restricted reactions. The purpose of using restriction chemical equilibrium is to set the final product of the reactor. This model is successfully used by Doherty et al. (Citation2009) in biomass gasification in a circulating fluidised bed reactor. In this work, the restriction equilibrium is applied using temperature approach.
The block RGIBBS applies Gibbs free energy minimisation in the system. ASPEN PLUS calculates Gibbs free energy as follows:
The potential chemical (μ
i
) can be written as a function of pressure (P) as shown in Equation (Equation3). In this case, the fugacity coefficient must be provided (θ):
The complete Gibbs free energy minimisation can be rewritten as follows:
Now, the equations above will be applied with Lagrange multiplier function. This method applies the elemental balance for each atom.
The partial derivatives of the Lagrange function (f(L)) with respect to each component must approach zero as shown in Equation (Equation8). The final product of Gibbs reactor is created using the set equations above.
3.2.3 Separation
SEP block is used to separate gas from solid. The solid consists of two substances, carbon (C) and ash, while the gases consist of many substances. In fact, the block of SEP is represented by cyclone with 100% efficiency. Varying efficiencies could be simulated with block SEP.
3.2.4 Property method
The appropriate property method carries the correct composition of product in the thermodynamics calculation. ASPEN PLUS uses the data of enthalpy, density, temperature and heat duty to calculate the thermodynamic reaction using the specific property method. In this work, the simulation uses Peng–Robinson property method because it is appropriate for high temperature reactor models (e.g. entrained flow reactor).
3.3 Validation of the model
3.3.1 Experimental validation
The model used in this study has been validated against the experimental data of Jinsong et al. (2009). The experiment uses entrained flow reactor at a temperature range of 1000–1400°C. Rice husk and sawdust are used as feedstock in the model validation. Proximate and ultimate analyses data are given in Table .
Table 2 The ultimate and proximate analyses of feedstock.
The data of experimental set-up are given in Table . These parameters are applied in the simulation.
Table 3 The set-up data are used by simulation.
3.3.2 Mean error calculation
The simulation result is then compared with the experimental data by using the mean error. The method proposed by Mansaray et al. (Citation2000) is used to estimate the accuracy of the simulation results.
Residual sum of squares (RSS) creates the square value of the experimental data and simulation results in accordance with the number of data points taken. This is then divided by the number of data points. It creates the mean value that is shown in Equation (Equation11).
3.3.3 JCL oil cake prediction
Composition of the product gases of gasified JCL oil cake is predicted with the same simulation model. The calculation of enthalpy is done by HCOALGEN. The feedstock can be changed by changing the ultimate analysis of the stream. The simulation result of product gases of JCL oil cake is associated with the mean error calculation.
4. Result and discussion
Table shows energy balance information obtained from the simulation. The heat capacity of standard () JCL oil cake is obtained using the difference in ambient temperature. It shows that JCL oil cake has the highest heat capacity (1.84 kJ/kg·°C). However, the enthalpy of the product gas during reaction is quite low compared with that of sawdust. The heat of reaction is obtained by the difference between the RYIELD and the RGIBBS. The heat of reaction of this simulation is 3.75 kW for JCL oil cake.
Table 4 Energy balance of biomass.
Table shows the experimental results as reported by Zhou et al. (Citation2009) and the model simulation using input data from Tables and .
Table 5 Comparison of product gas compositions obtained with experiments and simulations at 1000°C.
There is no information available on this experiment research related to the heat of reaction, but based on the simulation the heat of reaction can be obtained by the RYIELD and RGIBBS block. The RYIELD reactor is an endothermic process for drying and pyrolysis, while the RGIBBS reactor is exothermic for the reduction and oxidation.
Sensitivity analysis is used to evaluate the changes in operating and design variables of the process. In this study, the temperature is used as a design variable to determine the product gas composition. As in the experimental study (Lee et al. 1996), the temperature parameter plays an important role in the composition of product gases because it is the agent of reaction. Increase in temperature will influence the composition of products gases.
4.1 Rice husk and sawdust product gases
Figures and show the rice husk and sawdust gasification results obtained both with experiments and with simulation. Reactor temperature is set in the range of 1000–1400°C. The product gases obtained with simulations are in good agreement with those in the experiments. Increasing the temperature of reactor increases the composition of CO. In accordance with Le Chatelier's principle, higher temperatures of reaction favour the reactants in exothermic reactions and favour the gases in endothermic reactions. As Table indicates, CO is created in exothermic conditions such as reactions (Equation5) and (Equation6
). However, it can also be created in exothermic conditions such as the partial combustion reaction in reaction (Equation2
) and water–gas shift reaction in reaction (Equation7
) (Figure ).
Figure 3 Experiments and simulation results of product gas with rice husk gasification as a function of temperature.
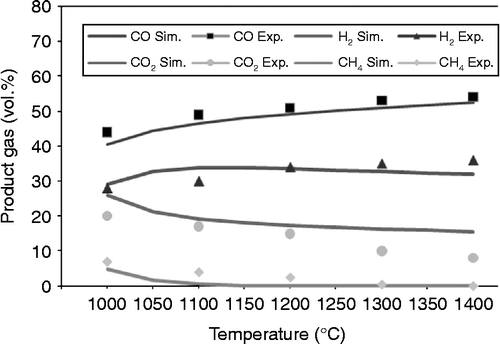
Figure 4 Experiment and simulation results of product gases with sawdust gasification as a function of temperature.
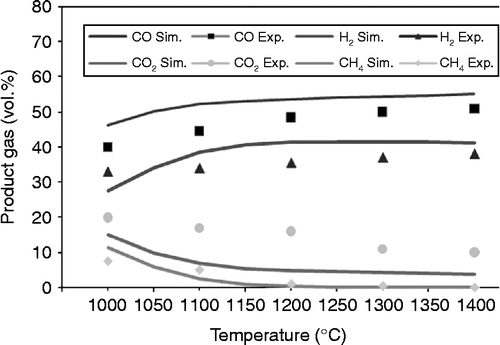
This exothermic part of the reaction is not enough to make the overall reaction exothermic because of the domination of the endothermic conditions. With endothermic reactions it is also possible to obtain H2 gas. However, CO2 and CH4 occur only in exothermic reactions.
4.2 Mean error calculations
Table provides the results of data analysis using the sum squared deviation method described in Equations (Equation9-(11). The results of the analysis show that CH4 has the highest mean error for rice husk and sawdust. Meanwhile, CO has the lowest mean error. The mean error is associated with the temperature approach in restriction equilibrium in the RGIBBS reactor that is used in this model. The temperature approach is searched based on the accuracy of each substance. The simulation results are in good agreement with the experimental results.
Table 6 Mean error analyses.
4.3 JCL oil cake prediction
Figure shows the comparison of simulation results of JCL oil cake with the results of rice husk and sawdust. This simulation uses the same simulation flowsheet that was used with sawdust and rice husk. The results show a uniform pattern which is shown in Figure . Increasing the temperatures increases the gas composition of CO and H2 and decreases the gas composition of CO2 and CH4. Figures (c) and 5(d) show that the highest volumetric compositions values of CO2 and CH4 in JCL oil cake are 26% (vol.) and 12.78% (vol.), respectively. This is caused by the carbon content of 59% in JCL oil cake.
4.4 Maximum and minimum error prediction
Figure shows the variation in the product gases of JCL oil cake by the mean error calculation. The analysis of the mean error obtained from Table provides information of the error value of each substance, and then the biggest error value is applied to each substance of JCL oil cake. The results provide maximum and minimum error values. Figure shows a stock chart application that provides information of the composition range of JCL oil cake. In Figure (a), the amounts of CO at temperatures of 1000°C ranges from 41.35% to 53.36% and the amounts of H2, CO2 and CH4 range from 24.65 to 32.7%, from 4.4 to 22.99% and from 0.94 to 19.62%, respectively.
5. Conclusion
Entrained flow gasification reactor model was created using ASPEN PLUS software. In the model description, block RYIELD represented the drying and pyrolysis process. Meanwhile, the oxidation and reduction processes occur in block RGIBBS. Block SEP is used to separate product gases from solids. This simulation study is used to estimate the composition of product gases from JCL oil cake.
Temperature is the observed parameter that affects product gas composition. Increasing the temperature of the reactor increases the composition of carbon monoxide. According to Le Chatelier's principle, higher temperatures of reaction favour the reactants in exothermic reactions and favour the products in endothermic reactions. Product gases in the simulation process are in close agreement with experimental data. This is shown by mean error analysis, which is based on the mole fraction of substance. CH4 has the highest mean errors with both rice husk and sawdust with values 0.8776 and 0.6115, respectively. CO has the lowest mean error. The mean error is associated with the temperature approach in restriction equilibrium in the RGIBBS reactor that is used in this model. The temperature approach is searched based on the accuracy of each substance.
The variation in the product gases of JCL oil cake is shown by applying the mean error analysis. According to the prediction, the amount of carbon monoxide at temperatures 1000°C ranges from 41.35% to 53.36%. Amounts of H2, CO2 and CH4 range from 24.65 to 32.7%, from 4.4 to 22.99% and from 0.94 to 19.62%, respectively.
Data variation of the above will converge when the reference data of biomass increase. If the experimental data for gasification of JCL oil cake were available, the validity of the simulation would be better with a low error level. However, as long as such information is not available, the predictions presented provide the characteristics of JCL oil cake in entrained flow reactors. Further work will be focused on the energy and exergy analysis of gasification of JCL in relation to the biodiesel plant.
Acknowledgements
The authors are grateful to Center for International Mobility (CIMO) for their financial assistance during research in Finland. Use of the facilities of laboratory energy engineering and environmental protection, Aalto University, is also greatly acknowledged.
References
- Banerji , R. 1985 . Jatropha seed oils for energy . Biomass , 8 ( 4 ) : 277 – 282 .
- Dai , Z. 2008 . Pilot-trial and modeling of a new type of pressurized entrained-flow pulverized coal gasification technology . Fuel , 87 ( 10–11 ) : 2304 – 2313 .
- Doherty , W. , Reynolds , A. and Kennedy , D. 2009 . The effect of air preheating in a biomass CFB gasifier using ASPEN PLUS simulation . Biomass and Bioenergy , 33 ( 9 ) : 1158 – 1167 .
- Foidl , N. 1996 . Jatropha curcas L. As a source for the production of biofuel in Nicaragua . Bioresource Technology , 58 ( 1 ) : 77 – 82 .
- Hambali , E. 2007 . Teknologi bioenergi , Jakarta : Agromedia .
- Hernández , J.J. , Aranda-Almansa , G. and Bula , A. 2010 . Gasification of biomass wastes in an entrained flow gasifier: effect of the particle size and the residence time . Fuel Processing Technology , 91 ( 6 ) : 681 – 692 .
- Hoogwijk , M. 2003 . Exploration of the ranges of the global potential of biomass for energy . Biomass and Bioenergy , 25 ( 2 ) : 119 – 133 .
- International Energy Agency (IEA) . 2010 . World energy outlook executive summary http://www.iea.org/texlbase/npsumweo2009sum.pdf
- Jayah , T.H. 2003 . Computer simulation of a downdraft wood gasifier for a tea drying . Biomass and Bioenergy , 25 ( 4 ) : 459 – 469 .
- Jess , A. 2010 . What might be the energy demand and energy mix to reconcile the world's pursuit of welfare and happiness with the necessity to preserve the integrity of the biosphere? . Energy Policy , 38 ( 8 ) : 4663 – 4678 .
- Jinsong , Z. 2009 . Biomass-oxygen gasification in a high-temperature entrained-flow gasifier . Biotechnology Advances , 27 ( 5 ) : 606 – 611 .
- Jongschaap , R.E.E. 2007 . Claim and facts on Jatropha curcas L., global Jatropha curcas evaluation, breeding and propagation programme , Wageningen : Plant Research International B.V .
- Li , X.T. 2004 . Biomass gasification in a circulating uidized bed . Biomass and Bioenergy , 26 ( 2 ) : 171 – 193 .
- Lv , P. 2007 . Hydrogen-rich gas production from biomass air and oxygen/steam gasification in a downdraft gasifier . Renewable Energy , 32 ( 13 ) : 2173 – 2185 .
- Lv , P.M. 2004 . An experimental study on biomass air-steam gasification in a fluidized bed . Bioresource Technology , 95 ( 1 ) : 95 – 101 .
- Mansaray , K.G. 1999 . Air gasification of rice husk in a dual distributor type fluidized bed gasifier . Biomass and Bioenergy , 17 ( 4 ) : 315 – 332 .
- Mansaray , K.G. 2000 . Mathematical modeling of a fluidized bed rice husk gasifier: Part I – model development . Energy Sources , 22 ( 1 ) : 281 – 296 .
- McKendry , P. 2002 . Energy production from biomass (part 3): gasification technologies . Bioresource Technology , 83 ( 1 ) : 55 – 63 .
- McLendon , T.R. 2004 . High-pressure co-gasification of coal and biomass in a fluidized bed . Biomass and Bioenergy , 26 ( 4 ) : 377 – 388 .
- Na , J.I. 2003 . Characteristic of oxygen-blown gasification for combustible waste in a fixed-bed gasifier . Applied energy , 75 ( 3–4 ) : 275 – 285 .
- Onishi , A. 2007 . The impact of CO2 emissions on the world economy . Journal of Policy Modeling , 29 ( 6 ) : 797 – 819 .
- Openshaw , K. 2000 . A review of Jatropha curcas: An oil plant of unfulfilled promise . Biomass and Bioenerg , 19 ( 1 ) : 1 – 15 .
- Prueksakorna , K. 2010 . Energy analysis of Jatropha plantation systems for biodiesel production in Thailand . Energy for Sustainable Development , 14 ( 1 ) : 1 – 5 .
- Saxena , R.C. , Adhikari , D.K. and Goyal , H.B. 2009 . Biomass-based energy fuel through biochemical routes: a review . Renewable and Sustainable Energy Reviews , 13 ( 1 ) : 167 – 178 .
- Sheth , P.N. and Babu , B.V. 2010 . Production of hydrogen energy through biomass (waste wood) gasification . International Journal of Hydrogen Energy , 35 ( 19 ) : 1 – 8 .
- Shah , S. , Sharma , A. and Gupta , M.N. 2005 . Extraction of oil from Jatropha curcas L. seed kernels by combination of ultrasonication and aqueous enzymatic oil extraction . Bioresource Technology , 96 ( 1 ) : 121 – 123 .
- Vyas , D.K. and Singh , R.N. 2007 . Feasibility study of Jatropha seed husk as an open core gasifier feedstock . Renewable energy , 32 ( 3 ) : 512 – 517 .
- Zhou , J. 2009 . Biomass-oxygen gasification in a high-temperature entrained-flow gasifier . Biotechnology Advances , 27 ( 5 ) : 606 – 611 .