Abstract
Rutting is a common type of shear failure-related deformation in asphalt (hot mix asphalt, HMA) pavements. It occurs over time as a result of slow, repeated heavy loads from vehicles moving along the wheel path. This problem is most noticeable when the pavement is at a high temperature and its stiffness is the lowest. Previous investigations have concluded that flowing water in pipes embedded in the pavement leads to a reduction in surface temperature, and consequently rutting. However, the thermophysical properties of HMA limit the cooling effect to a small region immediately around the pipe. It is proposed that the area of cooling be enhanced by adding a highly conductive spreader layer below the pavement in conjunction with the pipe. A theoretical design optimisation has been carried out by exploring different aspects of the spreader layer–pipe spacing (W), depth of the pipe–spreader (D), spreader thickness (t s), thermal conductivity (k s) and variation in the boundary conditions. Finite element modelling predicts that a properly designed, highly conductive spreader layer will lead to a significant reduction in surface temperature with a minimal piping network leading to an extended functional life of the HMA pavement.
Introduction
Prolonged daytime exposure to sunlight coupled with poor thermal conductivity and high heat capacity leads to a rapid rise in surface temperature of hot mix asphalt (HMA) pavements (Wahhab and Balghunaim Citation1994). The problem is exacerbated in warm climates with the pavement temperature reaching as high as 70°C in places like Houston, TX (NCHRP Citation2004). Being a viscoelastic material, HMA exhibits lower stiffness at higher temperature and at longer times of loading (slow speed; Monismith et al. Citation1994, Lu and Wright Citation2000). Consequently, investigations have shown that the amount of damage by rutting, a form of shear failure-related deformation in HMA pavements, is directly related to the temperature (Brown and Cross Citation1992, Bonaquist and Mogawer Citation1997, Pomerantz et al. Citation2000, White et al. Citation2002). It follows that, compared with a pavement with low temperature, a pavement with a higher temperature will require more maintenance and/or have a shorter life (in terms of rutting failure). One study (Mallick et al. Citation2009) found that the service life of a pavement with a maximum temperature of 53°C is more than double that of a pavement with a maximum temperature of 70°C; 20 years compared to 8 years using a mechanistic empirical pavement design guide/software (NCHRP Citation2004). Estimated costs for milling and resurfacing a rural road vary between $120,000 (FLDoT Citation2001) and $415,000 (MODoT Citation2010) per mile. Therefore, it would be beneficial to lower HMA pavement temperature in hot conditions, particularly in areas of heavy use.
Various strategies have been adopted to reduce the pavement surface temperature. Reflective coating has been a popular approach. Synnefa et al. (Citation2009) showed that lighter pavement colours were able to reduce average surface temperature by 5°C compared with black asphalt. Wan and Ping (Citation2009) tested road paint in Singapore designed to reflect infrared rays. Their experiment showed a reduction in pavement temperature from 65 to 38°C, a change of 27°C. However, this approach has the downside of reflecting the energy on adjoining buildings that may exacerbate urban heat island effects. In addition, changing the reflectivity and colour of the pavement surface can lead to problematic issues to driver vision. Paint coatings may also negatively affect pavement surface mix stiffness which can lead to surface cracks, wearing properties and skid resistance.
Kubo and Kido (Citation2006) extended the study by comparing the surface temperature characteristics and rutting capabilities of various types of asphalt: water-retaining, porous and porous with reflective paint in Tokyo. Although their study concluded that there was no clear advantage for rutting resistance, they found that the water-retaining pavement achieved a surface temperature of up to 16°C less than conventional pavements, while the temperature of the ambient air dropped by roughly 1°C. Extracting heat from asphalt pavements by convection using flowing water through pipes has been developed by Ooms Avenhorn (the Road Energy System®). This has been used as a means of reducing pavement temperature during the summer (reducing rutting), then storing liquid in large underground systems and re-circulating during the winter to de-ice the road surface (Loomans et al. Citation2003, Srivastava Citation2009). Structural integrity of the pavement and lowering of stress concentration were achieved by modification of the asphalt binder and adding grids to hold pipes in place. Large-scale testing on roads has been implemented in parking lots, using the low-grade extracted heat with heat pumps for heating and cooling nearby buildings (van Bijsterveld Citation2000, van Bijsterveld and de Bondt Citation2002). Earlier studies carried out at Worcester Polytechnic Institute have shown the ability of water flowing through pipes below HMA pavements to reduce surface temperature by 13°C. However, poor thermal conductivity of the pavement required close pipe spacing or serpentine piping for lowering the surface temperature uniformly (Chen Citation2008, Chen et al. Citation2009).
Objective
Since the poor pavement thermal conductivity requires pipes to be closely spaced to cool a large pavement surface area uniformly, a theoretical alternative is explored in this study. A thermally conductive spreader layer (that would be placed in the same way as a geotextile layer) coupled to pipes with flowing water will increase the effective area of the pipes so that the pipes need not be placed directly below the wheel path. This study theoretically investigates the geometric and thermophysical property variations of the spreader and the placement of the pipe–spreader combination that allows for a practical solution with maximum pavement surface cooling.
Modelling and analysis
The basic concept of the pipe–spreader heat exchanger is shown in Figure . The goal is to place the spreader along the wheel path below the pavement to conduct the heat away from the most vulnerable region of the pavement (ruttingwise) to the pipes where the heat is removed convectively by a flowing fluid. The pipes would ideally be placed in the shoulder region to minimise stress concentration in the pavement. However, under certain conditions, the pipes may be placed in the median region of the pavement, or in other regions where the loading is less severe. Under all circumstances, the pipes would not fall directly below the wheel path.
Figure 1 Sketch of asphalt solar collector embedded in highway lane. Note: Pipes spaced away from the wheel path.
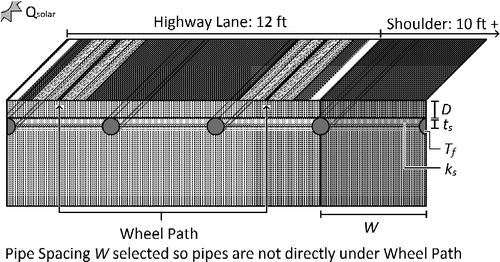
The design variables and their ranges are given in Table . They include pipe spacing (W) and depth (D); spreader properties such as thickness (t s), conductivity (k s) and spreader shape. In addition, the range of the two variable boundary conditions, solar flux absorbed (Q s) and fluid temperature (T f), are also specified. Table includes the default material properties used. The pipe was assumed to be made of copper having a diameter of 6 mm.
Table 1 Design variables and their respective ranges.
Table 2 Default material properties used, unless otherwise noted.
Modelling was carried out using finite element technique, with the help of COMSOL™ (COMSOL Citation2009) software (general heat transfer module). The governing equations used by this software for this application are listed in Table . Each model was meshed using COMSOL's ‘extremely fine’ mesh setting (triangle elements) having a maximum element edge length of 0.0015 m. The grid size corresponds to the dimensions of the model; for example W = 40 cm represents a grid size of roughly 160 × 100. COMSOL's PARDISO time-dependent solver was used to simulate 8 h of heating, using adaptive time-stepping with a maximum increment of 25 s.
Table 3 Governing equations and boundary conditions used (unless otherwise noted).
Results
First, the effects of pipe and pipe–spreader combination in lowering the surface temperature are presented, followed by a detailed exploration of the geometric and thermophysical properties. In this section, temperature plots are first shown for the top surface and the cross-section of the pavement to describe the temperature distribution in a pavement under a design constraint. The plots are followed by graphs showing the maximum temperature (T max – obtained somewhere on the surface) as a function of a particular parameter. Finally, the roles of various boundary conditions in modulating the pavement surface temperature are explored. Unless otherwise stated, all simulations are reported after 8 h of continuous heating, reflecting the worst-case scenario.
Comparison of temperature distribution between a conventional pavement, a pavement with a pipe and a pavement with pipe and spreader
Figure clearly demonstrates the role of a pipe alone (2(b)) and a pipe–spreader combination (2(c)) when compared with a pavement alone (2(a)). A pipe is able to reduce the surface temperature significantly by over 20°C; however, that effect is confined to the vicinity of the pipe for about 5–10 cm (entire width of each section is 20 cm). The effect of cooling can be enhanced spatially in all directions by the addition of a spreader layer. The spreader layer also allows further lowering of the temperature. Figure , therefore, establishes the comparative benefit of a pipe alone and a pipe and spreader, respectively.
Effect of pipe spacing (no spreader)
First, the temperature distribution of the pavement was plotted as a function of pipe spacing in Figure . In general, the contour plots demonstrate that the maximum cooling is obtained around the pipe and the effect of cooling rapidly dissipates within 10 cm. Therefore, for larger spacing, a substantial part of the road remains hot. A spacing of 0.5 m (1.6 ft) and higher leads to minimal surface cooling and substantial hot spots. The maximum temperature on the pavement and within starts to drop only after the pipes are brought closer.
As summarised in Figure , the maximum surface temperature drops by 10°C or higher at W ≤ 0.5 m. The exponential part of the curve indicating significant lowering of maximum pavement temperature is prominent at W ≤ 0.5 m. Therefore, without a spreader, a significant cooling of pavement will require pipes to be spaced within 0.5 m.
Effect of pipe and spreader depth (D)
The simulations given in the previous sections were carried out for a constant pipe depth (D) of 25 mm (1 in.). However, it may be prudent to put the pipes deeper inside the pavement to avoid maintenance issues. Figure shows the effect of increasing D with the spreader. As D increases, the pavement surface retains a higher temperature. At 75 mm (3 in.), the effect of the pipe–spreader system is largely diminished to an insignificant one. Furthermore, the spatial temperature distribution that one observes with cooler conditions near the pipe and warmer conditions further away also seems to be less. The maximum surface temperature increases over 20°C with an increase in D from 25 to 75 mm.
Figure 5 Top and side temperature distribution of pavement with spreader layer depth (a) D = 25 mm, (b) D = 50 mm, (c) D = 75 mm. Note: W = 40 cm, t = 8 h.

These effects are further summarised in Figure . As shown clearly, a pipe alone has no effect on the surface temperature when it is placed 25 mm or further below. This is because the effect of the pipe placement alone is minimal. The maximum temperature becomes sensitive to the placement depth only when the spreader layer is included. As one installs the pipe–spreader system deeper, the influence of cooling of the system diminishes at the surface of the pavement. For example, to maintain the maximum surface temperature below 40°C, the system should be placed not below 50 mm from the surface of the pavement.
Effect of spreader layer thickness (ts)
Figure shows the spatial variation of temperature with varying spreader layer thickness (t s). A very thin spreader layer does not have the desired effect, as seen in part (a) with a noticeable hot spot. It does not effectively draw heat towards the pipe due to the limited conductive benefit that it provides. This has been confirmed experimentally (Chen Citation2008). The purpose of the spreader layer is to conduct heat towards the pipe; with too little material to achieve this purpose, the conduction flux becomes ‘bottlenecked’ and results in an increased temperature gradient across the spreader. A thicker layer of material does not encounter the same bottleneck. Therefore, the thickest spreader layer offers the best possible cooling effect, in terms of lowest temperature and largest area of coverage.
Figure 7 Top and side temperature distribution of pavement with spreader layer thickness, (a) t s = 1.6 mm, (b) t s = 3.2 mm, (c) t s = 6.4 mm. Note: W = 40 cm, t = 8 h.
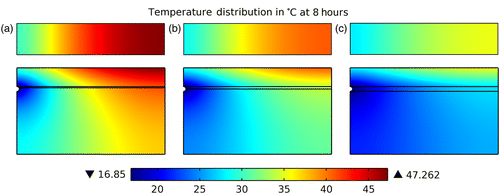
As a design optimisation, for various pipe spacing (W) and spreader layer thickness (t s), the maximum temperature was predicted. Figure represents the results of the simulation using an isothermal pipe of 17°C. At closer pipe spacing below 0.5 m, with or without the spreader layer, the temperature curves begin to converge. However, for pipe spacing >0.5 m the curve rises exponentially with increasing W. The effect of increased spreader thickness (t s) is to lower the maximum surface temperature. This effect is more prominent above a W of 0.5 m. In addition, as the spreader becomes thicker, the maximum temperature curve becomes flatter. For widely spaced pipes, (W>1.5 m), t s values need to be >12.8 mm (0.5 in.) to obtain substantial results. Therefore, an optimisation of pipe spacing and spreader thickness is required depending on the allowable temperature maxima of the pavement.
Sloped and lipped spreader geometries
Although it is clear that increasing t s will lead to further lowering of surface temperature and improvement in rutting resistance, it is impractical and unwieldy to put thick spreaders (exceeding an inch) below the pavement. However, if the pipes are placed near the edge of the road and in shoulder regions, it is possible to make the spreader thicker at the points immediately surrounding the pipe. Two designs, as shown in Figure , (a) a sloped design and (b) a lipped design, were investigated. The first design introduces a gentle slope that was varied from 6.4 to 9.6 mm. The lipped design allows a further curvature near the pipe for better heat transfer.
The rationale for using sloped or lipped spreaders is demonstrated in Figure . Part (a) shows the bottlenecking that occurs with a 6.4 mm (1/4 in.) spreader layer. The maximum heat flux is at the pipe–spreader interface. Various factors come into play: the thickness and the conductivity of the spreader layer, as well as the pipe spacing, contribute significantly to the formation of the bottleneck. The cumulative effect of the surface heat flux causes a flux concentration near the pipe. The larger amount of heat passing through the spreader layer as it nears the pipe induces a temperature gradient across a shorter length (causing the area further from the pipe to heat up much faster). Part (b) correspondingly shows that a modest variation in spreader layer shape can easily reduce the effect of this flux bottleneck.
Figure 10 Heat flux distribution of pavement with spreader layer shape: (a) flat, t s = 6.4 mm, (b) sloped, (c) lipped. Note: W = 40 cm, t = 8 h.
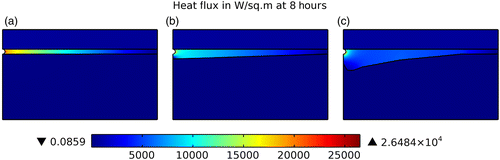
Figure shows the effect of the sloped (c) and lipped (d) designs on temperature distribution and compares them to flat spreader layers (a) and (b), again using a pipe spacing of 40 cm. The sloped and lipped shapes do not drastically change the temperature variations along the length. The ‘Sloped’ design shows a reduction in maximum temperature by roughly 2.9°C whereas the ‘Lipped’ design shows a reduction of 4.1°C compared with the 6.4 mm spreader (Figure (a)), signifying that the modified designs have a benefit if varied geometry is a possibility.
Variation in thermal conductivity of spreader layer (ks)
The thermal conductivity of the spreader layer (k s) will affect the temperature distribution within the pavement. Since the spreader material will be made of a conductive geotextile, the sensitivity of temperature distribution was assessed while varying k s. In this way, it would become easier to assess theoretically a range of materials as candidate for the conductive spreader material. As shown in Figure , increasing k s by one order of magnitude from the pavement conductivity (part (a)) allowed a noticeable lowering of surface temperature, but the effect did not spread across the entire width as seen by the reddish hot spots away from the pipe. However, as shown in part (b), changes of two orders of magnitude in k s (160 W/m K) clearly led to more uniform cooling of the pavement surface. Further enhancement of k s led to minimal improvement in surface temperature distribution.
Figure 12 Top and side temperature distribution of pavement with spreader layer conductivity k s = (a) 10 W/m K, (b) 160 W/m K, (c) 500 W/m K. Note: W = 40 cm, t = 8 h, t s = 6.4 mm.
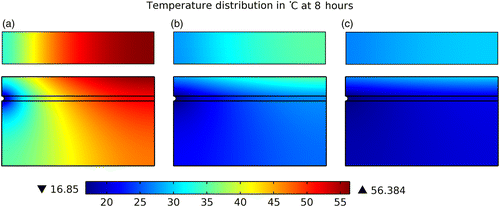
These effects are summarised in Figure which plots T max as a function of varying conductive spreader layer conductivity. In addition, k sx and k sy were varied to determine whether there was a directional dominance of conductivity in the system. Results indicate that the maximum surface temperature dropped exponentially with increasing k s. Increasing k s beyond 200 W/m K provided diminishing returns of temperature reduction, indicating that spreader conductivity ∼200 W/m K can give the most improved performance (given W and t s). When the spreader conductivity was directionally analysed (as k sx and k sy ), it was found that the vertical conductivity (k sy ) of the spreader layer is insignificant compared with the horizontal component (k sx ) in regard to temperature reduction.
Effect of boundary conditions
Although the design of the pipe–spreader system (W, D, t s, k s) is the most crucial aspect in reducing the maximum pavement surface temperature and, therefore, preventing the rutting potential, boundary constraints play a practical role in modulating the temperature distribution in the pavement. So far, a constant solar flux Q s = 700 W/m2 and cooling fluid temperature T f = 16.8°C have been assumed. Next, Q s was varied from 500 to 1100 W/m2 and T f from 12 to 30°C.
Figure shows the variation in T max for W = 40 cm and various incoming solar radiation. Results are shown for no spreader (t s = 0) and various t s. The maximum pavement temperature expectantly increases with increasing Q s. The temperature is highest with no spreader and decreases with increasing t s. With increasing t s, the increase in maximum pavement temperature was damped as illustrated by a progressively shallower slope of each curve.
Figure 14 Effects of absorbed solar flux (Q s) on maximum surface temperature (T max), varying spreader thickness (t s). Note: W = 40 cm, t = 8 h.
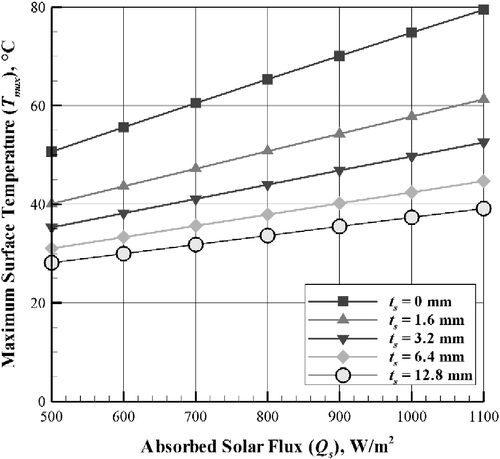
Figure shows the variation in T max for W = 40 cm and various T f. As the incoming T f increases, the heat extracted from the pavement decreases and, therefore, the pavement surface temperature increases. Increasing t s helps in lowering the maximum pavement temperature, but increases the sensitivity to T f as indicated by the steeper slope of the curve for progressively increasing t s.
Daily cycles
Finally, a more practical model was constructed to include sinusoidal variations in solar flux and ambient temperature, more accurately representing the conditions occurring on the road surface. Both the solar flux and ambient temperature were assumed to behave as a half sine wave with a half-period of 14 h. The values started at an initial value at the beginning of the day (Q s = 0 W/m2 and T amb = 26.8°C, respectively), rising to some peak value (Q s = 1000 W/m2 and T amb = 36.8°C, respectively) halfway through the day and returning to the initial value at sunset. During this time, the fluid in the pipe was assumed to be flowing sufficiently to provide an isothermal pipe wall condition of 16.8°C. This ‘daytime’ period of 14 h was followed by a ‘nighttime’ period of 10 h in which the solar flux and ambient temperature were held constant (Q s = 0 W/m2 and T amb = 26.8°C, respectively) and the fluid flow in the pipe was assumed to be off. Therefore, an insulated pipe wall condition was used. This simulation process was repeated over a total of 7 days.
A pipe half-spacing of W = 61 cm was chosen. This was selected as it is one-third of the width of a US interstate traffic lane (12 ft), such that the pipes can be placed away from the wheel path as shown in Figure . An unmodified control simulation, featuring pavement material only, was created. Another simulation was done with a pipe (D = 25.4 mm) below the surface to present the effects of the pipe itself. Finally, a model was created with a spreader layer (t s = 6.4 mm, k s = 1000 W/m K) and pipe (D = 25.4 mm) below the surface to show its full effect in comparison.
Figure shows the variations in maximum surface temperature over the course of 7 days. Unmodified pavement clearly shows the highest maximum temperature, which increases over the first 3 days, representing the cumulative effects of energy storage in the material. The sample with the pipe shows a very small reduction in the maximum temperature of the pavement. Although the pipe itself provides a means of removing the energy from the pavement, the poor conductivity of the pavement material limits the effective pipe area. Regions near the pipe are kept cool, whereas the area far away from the pipe is barely affected and reaches a consistent high maximum temperature. The sample with the spreader layer shows a dramatic reduction in temperature. The high conductivity of the spreader layer bolsters heat conduction through the pavement, allowing energy to be transported into the pipe and out of the pavement, therefore, preventing a significant temperature rise.
Figure 16 Maximum temperature (T max) of samples subjected to sinusoidal solar flux and varied ambient temperature over 7 days. Note: W = 61 cm.
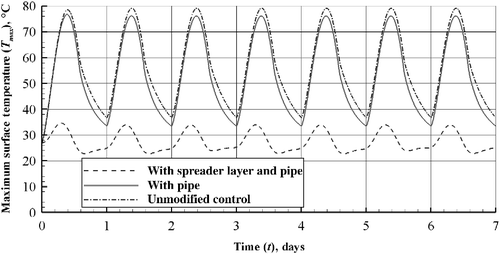
The boundary conditions from the previous simulation were applied to a 3D extension of the model. T f was varied linearly along the direction of the pipe from 16.8 to 26.8°C to account for the rise in fluid temperature (representing a constant heat flux case – the worst case scenario). Figure shows the temperature distribution of the aforementioned configuration with the spreader layer. With this configuration, the maximum temperature around the wheel path is lowered by 35–40°C. This is a substantial improvement over the case without a spreader. In summary, the temperature of the pavement surface is reduced, increasing the stiffness of the asphalt mixture and its resistance to permanent deformation.
Discussion
Rutting is a serious problem in HMA pavements in many regions of the world (Brown and Cross Citation1992, Bonaquist and Mogawer Citation1997, Pomerantz et al. Citation2000, White et al. Citation2002). The subtropical and tropical regions of the globe are densely populated; in these regions roads are generally trafficked by heavily loaded (quite often overloaded) vehicles. A combination of high temperature and load leads to severe rutting damage that causes over ten million dollars in maintenance expenditure in the USA alone. Rutting can be reduced by either modifying the asphalt to make it stiffer at higher temperature or reducing the pavement temperature. Polymer-modified binders have been used to increase stiffness of pavements at higher temperatures, but their cost is double that of asphalt (Srivastava Citation2009). The approach of lowering the pavement temperature using reflective coating does not provide the optimal solution (Pomerantz et al. Citation2000, Kubo and Kido Citation2006, Synnefa et al. Citation2009, Wan and Ping Citation2009). Therefore, alternatives must be explored as a means of reducing rutting-related damage.
The proposed approach is a modification of the approach developed by the Dutch group for energy extraction from HMA pavements (Loomans et al. Citation2003, Srivastava Citation2009). Their design used a closely spaced piping network below the pavement with flowing water that extracted the heat. Since it would be impractical to have such closely spaced pipes below active roads, we proposed a modified design. This design incorporates a conductive spreader layer below the wheel path at depths of 25 mm or greater connected to the embedded pipes that are located away from the wheel paths (Figure ). The road below the wheel path is the region prone to rutting failure and, therefore, cooling that region is a priority. Numerical analysis of the design is able to establish temperatures below 45°C along the wheel path with only two pipes placed within the active road and the rest in the median/shoulder region (Figure ). This is a substantial improvement in lowering the temperature from a peak of 75°C on hot sunny days as obtained from simulations (Figure ). Therefore, there is a substantial practical advantage of using a spreader layer in conjunction with pipes below the pavement.
The reduction in rutting will increase the service life of a given roadway, allowing for a much longer interval between resurfacing. However, resurfacing may be inevitable during the existence of the road. In order to prevent damages to the piping system, other than developing a new system for resurfacing, milling should be limited to the pavement layer above the pipes. During major rehabilitation work (which has a significantly higher interval than maintenance work), a re-laying of the system can be done.
The success of this design is dependent on the spreader material. As seen in this study, a 6.4 or 12.8 mm thick spreader (0.25 or 0.5 in.) with a k s value above 100 W/m K will be a good spreader material (Figure ). Although several metallic sheets such as copper and aluminium are available with these specifications, they are cost prohibitive and will most likely lead to shear failure due to low adhesion to asphalt. Geosynthetics are a durable and flexible man-made material that has adequate friction with asphalt mix layer; therefore, they are compatible for long-term maintenance and are the material of choice for use as a heat spreader. Geosynthetics already serve a multitude of tasks in pavement structures such as drainage, separation and reinforcement (Joint Departments of the Army and Air Force Citation1995, Koerner Citation1998, Button and Lytton Citation2007). They have also been used as reinforcement to prevent rutting. However, they are made of polypropylene or polyethylene terephthalate, which are normally poor conductors and would be inadequate spreaders. The option is to use carbon fibres that have high conductivity and can be woven in the form of mats. Already, polyacrylonitrile based woven composite fibres exist which can be used as spreader material. One of the features of the current design is that a high k sx is adequate for the spreader material. This allows composite laminate sheets that have high lateral conductivity (k x ) but poor transversal conductivity (k y ) to be used for spreader material. The use of flexible sheets that can be easily replaced and coupled to the pipes without difficulty during repaving of pavement surfaces makes composite laminate sheets an attractive option as a spreader layer.
Although the current study theoretically investigated the feasibility of putting a spreader–pipe network below the pavement, the study was limited to a thermal analysis only. Structural analysis is required on the pavement–pipe–spreader system before large-scale implementation is possible. Previous studies have conducted stress analysis on pavements with embedded pipes only (van Bijsterveld Citation2000, van Bijsterveld and de Bondt Citation2002). They have shown that although stress concentration takes place at the pipe–pavement interface, they are below the critical failure point. Some of the stress concentration (for pipes located directly under or close to wheel path) can be mitigated by having the pipes deeper in the pavement.Since the proposed system has pipes that are further away from the wheel path, this problem can be minimised. Similar stress analysis under cyclic compressive loading needs to be conducted. A comprehensive analysis that incorporates modulus values of piping–spreader materials is required.
Finally, the current design presents new opportunities that have not been fully explored for HMA pavements. The pipes have the potential of delivering a circulating water/fluid at temperatures above 55°C on a regular basis in warm climates. The hot water/fluid can be used for various applications. In addition to serving hot water to a community, the water may be used in absorption chiller or refrigeration systems, air conditioning systems or as a heat source to an organic Rankine cycle for power generation or simply as process heat for industrial operations (Goswami et al. Citation2000). Preliminary economic analysis provides favourable payback in regions of high solar insolation (Mallick et al. Citation2011). Although further design analysis and optimisation will be required for scaling up the system, the current design provides the first step towards sustainable HMA pavements.
Conclusion
In the current study a theoretical thermal analysis has been conducted to determine the major factors affecting the surface temperature distribution of a HMA pavement. A pipe with fluid circulating within it is coupled to a conducting spreader layer and the entire system has been embedded under the pavement. Sensitivity analysis of the temperature distribution as well as Tmax was conducted as a function of pipe spacing (W), depth of the pipe–spreader system (D), thickness (ts) of spreader layer (and other variable thickness) and thermal conductivity of the spreader (ks). It was found that pipes alone cannot cool a very large area because of poor pavement conductivity, and spreaders are effective in cooling a larger area of the pavement. Increasing ts and ks allows effective spreader with lowering of Tmax, but material and structural limitations will determine the final properties. One option is to place the pipe–spreader deeper (D = 50 mm) inside the pavement and use higher ts values. Deeper placement of the system will also allow design flexibility of lipped or sloped spreader layers which allows one to cool the pavement further. It may shield the system from stress concentrations. A sensitivity analysis to the two major boundary conditions (Qs and Tf) shows the slopes of increasing Tmax with higher flux and fluid temperature. Finally, a realistic simulation clearly indicates that Tmax can be lowered by more than 30°C – thus significantly improving the rutting resistance of HMA pavements.
References
- Bonaquist , R.J. and Mogawer , W.S. 1997 . Analysis of pavement rutting data from FHWA pavement testing facility superpave validation study , Transportation Research Record, 1590 Washington, DC
- Brown, E.R., and Cross, S.A., 1992. A national study of rutting in hot mix asphalt (HMA) pavements. NCAT Report 92-5
- Button , J.W. and Lytton , R.L. 2007 . “ Guidelines for using geosynthetics with hot mix asphalt overlays to reduce reflective cracking ” . In 86th annual meeting of the TRB , 21–25 January 2007 Vol. 1 , 111 – 119 . Washington, DC
- Chen, B.-L., 2008. Capture solar energy and reduce heat-island effect from asphalt pavement. Thesis (PhD). Worcester Polytechnic Institute
- Chen , B.L. , Bhowmick , S. and Mallick , R. 2009 . A laboratory study on reduction of heat island effect of pavements . Journal of Association of Asphalt Paving Technologists (AAPT) , 78 : 209 – 248 .
- COMSOL, 2009. Heat transfer module user's guide. COMSOL Multiphysics 3.5a
- Florida Department of Transportation (FLDoT), 2011. Generic cost per mile models. [online] Available from: http://ftp.dot.state.fl.us/LTS/CO/Estimates/CPM/summary.pdf. [Accessed 8 August 2011]
- Goswami , Y.D. , Kreith , F. and Kreider , J.F. 2000 . Principles of solar engineering , 2nd ed. , New York : Wiley and Sons .
- Joint Departments of the Army and Air Force . 1995 . Engineering use of geoxtextiles , Washington, DC : Headquarters, Departments of the Army and Air Force .
- Koerner , R.M. 1998 . Designing with geosynthetics , 4th ed. , Upper Saddle River, NJ : Prentice Hall .
- Kubo , K. and Kido , H. 2006 . “ Study on pavement technologies to mitigate the heat island effect and their effectiveness ” . In Proceedings of the 10th international conference of asphalt pavements , 12–17 August 2006 Vol. 3 , 223 – 232 . Quebec City, Canada
- Loomans , M. 2003 . “ Tool for the thermal energy potential of asphalt pavements ” . In Eighth international IBPSA conference , 11–14 November 2003 Eindhoven, Netherlands
- Lu , Y. and Wright , P.J. 2000 . Temperature related visco-elastoplastic properties of asphalt mixtures . Journal of Transportation Engineering , 126 : 1
- Mallick , R.B. , Chen , B.-L. and Bhowmick , S. 2009 . Harvesting energy from asphalt pavements and reducing the heat island effect . International Journal of Sustainable Engineering , 2 ( 3 ) : 214 – 228 .
- Mallick , R.B. 2011 . Evaluation of the potential of harvesting heat energy from asphalt pavements . International Journal of Sustainable Engineering , 4 ( 2 ) : 164 – 171 .
- Missouri Department of Transportation (MODoT), 2010. Better roads, brighter future – engineering policy guide. [online]. Available from: http://epg.modot.org/index.php?title = Category:Better_Roads%2C_Brighter_Future [Accessed 8 August 2011]
- Monismith , C.L. 1994 . Permanent deformation response of asphalt aggregate mixes , Strategic Highway Research Program, A-415 Washington, DC
- National Cooperative Highway Research Program (NCHRP), 2004. Design guide: mechanistic-empirical design of new & rehabilitated pavement structures. [online] Available from: www.trb.org/mepdg [Accessed 8 August 2011]
- Pomerantz, M., Akbari, H., and Harvey, J.T., 2000. The benefits of cooler pavements on durability and visibility. Lawrence Berkeley National Laboratory Report, LBNL-43443
- Srivastava, A., 2009. Pavements: the thermal energy potential of asphalt and the advantages of polymer modified bitumen. [Online]. Available from: http://www.irfnet.ch/files-upload/knowledges/Ooms_Paperedit%_6_.pdf [Accessed August 8, 2011]
- Synnefa , A. 2009 . “ Measurement of optical properties and thermal performance of coloured thin layer asphalt samples and evaluation of their impact on the urban environment ” . In 2nd international conference on countermeasures to urban heat islands , 21–23 September 2009 Berkley, CA
- van Bijsterveld, W.T., 2000. Energy from asphalt – analysis of structural and thermal aspects. Thesis. Delft University of Technology
- van Bijsterveld , W.T. and de Bondt , A.H. 2002 . “ Structural aspects of pavement heating and cooling systems ” . In 3rd international symposium on finite elements , 2–5 April 2002 Amsterdam, The Netherlands
- Wahhab , H.I.A. and Balghunaim , F.A. 1994 . Asphalt pavement temperature-related to arid Saudi environment . Journal of Materials in Civil Engineering, ASCE , 6 ( 1 ) : 1 – 14 .
- Wan , W. and Ping , T. 2009 . “ A study on the effectiveness of heat mitigating pavement coatings in Singapore ” . In 2nd international conference on countermeasures to urban heat islands , 21–23 September 2009 Berkley, CA
- White, T.D., et al., 2002. Contributions of pavement structural layers to rutting in hot mix asphalt pavements. National Cooperative Highway Research Program Report, 468