Abstract
Increasing petroleum prices, increasing threat to the environment from exhaust emissions and global warming have generated intense international interest in developing renewable and alternative non-petroleum fuels for engines. Evolving technology and a recurring energy crisis necessitates a continuous investigation into the search for sustainable and clean-burning renewable fuels. In this paper, cottonseed oil methyl ester (COME) was used in a four-stroke, single-cylinder variable compression ratio diesel engine. Tests were carried out to study the effects of fuel injection timing, fuel injector opening pressure (IOP) and injector nozzle geometry on the performance and combustion of COME biodiesel fuel used in a compression ignition engine with a single fuel mode. Fuel injection timing varied from 19° to 27° before top dead centre (bTDC) in incremental steps of 4° bTDC; fuel IOP varied from 210 to 240 bar in incremental steps of 10 bar. Fuel nozzle injectors with three, four and five holes, each of 0.3 mm size, were selected for the study. The results suggested that with retarded injection timing of 19° bTDC, increased IOP of 230 bar and a four-hole nozzle injector of 0.3 mm size resulted in overall better engine performance with an increased brake thermal efficiency and reduced HC, CO and smoke emission levels.
1. Introduction
All nations in the world are confronted with the problem of energy. There is an ever-increasing demand for energy in the industrial, transport and domestic sectors. Sustainable source of energy is essential for economic and social development. The existing sources of energy from fossil fuels may not be adequate to meet the ever-increasing energy demand. The diminishing and continuously increasing cost of petroleum resources along with their alarming pollution levels emitted from diesel engines has led to an intense interest in finding renewable, alternative and sustainable fuels to diesel fuel. India's share in global oil reserves is about 0.5%, whereas its share in global consumption is about 3%. India ranks among the top 10 largest oil-consuming countries importing about 70% of its oil needs. The total oil consumption in India is about 2.5–2.8 million barrels per day. The demand for fossil fuels will rise higher and higher with every passing decade and is expected to reach an amount of nearly 250 million tons by the year 2024. Consequently, to reduce the huge amount of import bills of crude oil and to become a self-reliant country in the energy sector, India has initiated the use of renewable energy over the last three decades (Agarwal Citation2006).
Renewable fuels have advantages in terms of renewability, biodegradability, energy security, environmental concerns, foreign exchange savings and socio-economic issues compared with fossil fuels. The use of renewable energy from non-edible oils reduces greenhouse gas emissions, gives better food and energy security to the nation and ensures sustainable development (Banapurmath et al. Citation2005; Banapurmath and Tewari Citation2010; Murugesan et al. Citation2009).
Therefore, renewable fuels such as biofuels can be used predominantly for both transportation and power generation sectors (Atadashi, Aroua, and Abdul Aziz Citation2010; Basha, Raja Gopal, and Jebaraj Citation2009; Murugesan et al. 2009).
A number of vegetable oils have been used for biodiesel production and are also being used in diesel engine applications. These include biodiesel fuels produced from jatropha, honge (karanja), honne, palm, rubber seed, rapeseed, mahua and neem seed oils (Banapurmath, Tewari, and Hosmath Citation2008, Citation2009; Bari, Lim, and Yu Citation2002; Gajendra Babu, Kumar, and Das Citation2006; Karnwal et al. Citation2010; Morshed et al. Citation2011; Onga et al. Citation2011; Ramadhas, Muraleedharan, and Jayaraj Citation2005; Ramadhas, Jayaraj, and Muraleedharan Citation2005; Raheman and Phadatare Citation2004; Sahoo et al. Citation2007, Citation2009; Venkanna and Venkataramana Reddy Citation2011; Yang et al. Citation2011). Biodiesel is a clean-burning alternative fuel produced from domestic renewable resources. It is simple to use, biodegradable, non-toxic and essentially free of sulphur and aromatics. Biodiesel improves lubricity and reduces premature wearing of fuel pumps.
In this paper, cottonseed oil methyl ester (COME) is used as a fuel in a diesel engine. In India, cottonseed oil is categorised as vanaspati oil. Also, India has been ranked as the second largest producer of cotton seeds and cottonseed oil in the world followed by China as the top producer (Ministry of Agriculture, India and U.S. Department of Agriculture). The estimated values of 1190 and 10,600 MT for cottonseed oil and cotton seed production in 2012 reveal that India is self-reliable for consumption of cottonseed oil. Consequently, in the last 3 years, there has been a rise in the capital growth of cotton seed production in India. The values for cottonseed oil production have been estimated to be 1045, 1150 and 1210 MT, which accounted for capital growth rates of 1.46, 10.05 and 5.22% in 2009, 2010 and 2011, respectively. Therefore, it can be concluded that India has a vital option of utilising cottonseed oil as a marginal substitute for the conventional petroleum diesel fuel to meet its energy demand. However, the Indian government should come up with strong and well-furnished polices for oil seed production.
Many investigators have studied the feasibility of COME and their blends in diesel engine applications. They have reported lower CO, CO2, NOx and smoke emission levels for COME fuel. Lower brake thermal efficiency (BTE) with COME and their blends operation is mainly due to their lower heating value compared with neat diesel fuels (Karabektas, Ergen, and Hosoz Citation2008; Nurun Nabi, Mustafizur Rahman, and Shamim Akhter Citation2009; Naga Sarada et al. Citation2010; Xiaohu et al. Citation2008; Yucesu and Ilkilic Citation2006). Lower and medium percentages of COME fuel can be partially substituted for diesel fuel without any major modifications in the diesel engine (Huseyin and Bayindir Citation2010; Martin and Edwin Citation2011). The effects of using neat cottonseed oil or its neat methyl ester (ME) biodiesel on the combustion behavior of a standard, high-speed, direct injection (HSDI) hydra diesel engine has been reported in literature (Rakopoulos et al. Citation2010). A heat release analysis of an experimentally obtained cylinder pressure diagram has been developed and used. The maximum cylinder pressure remained the same for raw cottonseed oil and slightly increased for the biodiesel with cottonseed oil (Rakopoulos et al. Citation2010). Approximately 20–40% of cottonseed oil can be substituted for diesel as fuel without any major modifications in the engine required.
Several researchers have conducted engine tests on a compression ignition (CI) engine with different vegetable oils and their esters at different injection pressures and injection timings (Gajendra Babu Citation2007). Varied fuel injection timings change the position and magnitude of the cylinder pressures and temperatures. The retarded injection timings showed a significant reduction in diesel and biodiesel NOx emission levels (Hountalas et al. Citation2001; Tao et al. Citation2005). Cylinder pressures and temperatures gradually decrease when injection timings are retarded (Roy Citation2009). The results on the effect of fuel injection timings for waste cooking oil as a fuel used in a direct injection diesel engine with an advanced injection timing of 4° bTDC has shown better efficiency, reduced CO and higher NOx emission levels (Bari, Yu, and Lim Citation2004).
Furthermore, other investigators have performed experiments on a CI engine with different vegetable oils and their esters at different injection pressures. The engine showed better performance and higher peak cylinder pressures and temperatures were obtained (Bari, Yu, and Lim Citation2004; Puhan Sukumar Jegan, Balasubbramanian, and Nagarajan Citation2009; Rosli, Semin, and Ismail Citation2008; Roy Citation2009).
From the literature survey, it follows that only limited work has been carried out to investigate the effects of injection timings, injector opening pressure (IOP) and nozzle geometry on the performance, combustion and emission characteristics of a COME-fuelled diesel engine.
The present study reports the effects of fuel injection timings, fuel IOP and injector nozzle geometry on the performance and combustion characteristics of a CI engine fuelled with COME.
2. Experimental set-up
Table lists the properties of cotton seed oil and COME used in the study. A schematic diagram of the engine test rig used in the present study is shown in Figure . The engine tests were conducted on a four stroke, single-cylinder, water-cooled direct injection CI engine provided with a displacement volume of 662 cc, compression ratio of 17.5:1 and a rated power of 3.7 kW running at 1500 rpm. The engine was always operated at a rated speed of 1500 rpm and had a conventional fuel injection system. The IOP and the static injection timing were 205 bar and 23° bTDC, respectively, as specified by the manufacturer. The engine was provided with a governor that maintains a constant engine speed at all load levels. It was also used to control the speed of the engine. The engine comprised a hemispherical combustion chamber with overhead valves that were operated through push rods. The engine was cooled by circulating the water through the jackets in the engine block and cylinder head. A piezoelectric pressure transducer was mounted onto the cylinder head surface to measure the cylinder pressure. Table outlines the specification of the engine used for the present study. Figure shows fuel injectors with three different holes having an orifice diameter of 0.3 mm. The exhaust gas analyser and smoke meter employed for the measurement of exhaust gas emission levels are shown in Figures and , respectively. Their specifications are given in Tables and , respectively.
Table 1 Properties of the fuels used.
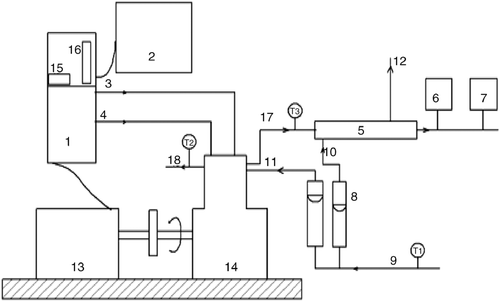
Table 2 Specifications of a CI engine.
Table 3 Specifications of the exhaust gas analyser.
Table 4 Specifications of the smoke meter.
3. Results and discussion
The effects of injection timings, IOP and nozzle geometry on the performance of a diesel engine fuelled with COME are discussed in the following sections.
3.1 Effect of injection timings
Tests on engine performance were conducted at three injection timings of 19°, 23° and 27° bTDC. Compression ratio of 17.5:1 and an IOP of 205 bar (20.5 MPa) were maintained during the test period. A fuel injector with three holes each having an orifice diameter of 0.3 mm was selected for the experimental test.
3.1.1 Brake thermal efficiency
The effect of injection timings on the BTE of the CI engine fuelled with COME at the three injection timings is shown in Figure . For 80% load, highest BTE of 25.57% was obtained at a static injection timing of 23° bTDC in the diesel engine. The optimum injection timing for a standard diesel was found to be 23° bTDC, which also matched with the manufacturer's specification. However, BTE of the engine when fuelled with COME for the injection timing of 23° bTDC was found to be 21.50%. BTEs were lower for COME biodiesel fuel than for the standard diesel fuel at all the three injection timings tested. The decreased BTE for COME biodiesel might be attributed to its lower energy content and higher fuel consumption for the same power generation. Due to the high viscosity of COME, the formation of its mixture with air and subsequent combustion were poorer compared to diesel fuel operation. However, the retarding injection timing by a crank angle (CA) of 4° exhibited an improved BTE. The BTE at the injection timing of 19° bTDC was 23.01%. Based on the BTE values, the optimum injection timings for the standard diesel fuel and COME biodiesel fuel were 23° and 19° bTDC, respectively.
3.1.2 HC and CO emissions
Figures and show the effect of the injection timings on HC and CO emission levels, respectively, for the standard diesel fuel and COME biodiesel fuel. HC emission from diesel engines is mainly caused due to lean mixture formation during the delay period and under-mixing of fuel leaving the fuel injector nozzle with a lower velocity. A general trend of increased HC and CO emission levels for COME biodiesel fuel was observed when compared with the standard diesel fuel at all the three injection timings tested. This trend may be attributed to the poor spray characteristics of COME and its poor mixing with air and results in poor combustion efficiency. At the 80% load, HC emission levels were found to be 64, 79 and 94 ppm at the injection timings of 19°, 23° and 27° bTDC, respectively. The lowest HC emission levels were found at the optimum injection timing of 23° bTDC for the standard diesel fuel. However, for COME biodiesel fuel, the lowest levels were found to be at the injection timing of 19° bTDC.
Carbon monoxide is a toxic by-product and is a clear indication of incomplete combustion of the pre-mixed mixture. The levels of CO emission decreased at part loads and increased at higher loads at all the injection timings. The levels of CO emission at the 80% load were 0.25, 0.33 and 0.45% at the injection timings of 19°, 23° and 27° bTDC, respectively. The lowest CO emission levels were found at the optimum injection timing of 23° bTDC for the standard diesel fuel. It may be concluded that at the injection timing of 19° bTDC, improved combustion and increased cylinder pressures and temperatures resulted in lower HC and CO emission levels when compared with the other injection timings for COME biodiesel fuel.
3.1.3 NOx emissions
The effect of the injection timings on NOx emission levels for the standard diesel fuel and COME biodiesel fuel is shown in Figure . In general, the retarded injection timings result in a substantial reduction in NOx emission levels. When the injection timing is retarded, the combustion process also becomes retarded. NOx emission levels were lower when the peak temperature was lower. On the other hand, NOx emission levels were higher at the injection timings of 23° and 27° bTDC, thereby leading to a sharp pre-mixed heat release due to a higher ignition delay (Figure ).
NOx emission levels were slightly lower for COME biodiesel fuel than for the standard diesel fuel. From these results, the best injection timing was taken as 19° bTDC for COME biodiesel fuel.
3.1.4 Combustion analysis
Figures and show the effect of the injection timings on pressure variations and heat release rate for engine operation at a full load, respectively.
The delay period increased with an increase in the injection advance angle, as shown in Figure . This is because the pressures and temperatures are lower at the beginning of the injection. When the injection advance angles are small, the delay period reduces and the operation of the engine becomes smoother. The optimum angle of injection advance would cause the peak pressure to occur at a temperature range of 10–15°C after top dead centre.
For advanced injection timing, the ignition delay period also increases and heat release rate decreases during the pre-mixed combustion phase, with a minor effect being observed on the mixing-controlled combustion phase. From Figure , it is clear that this observed effect is more pronounced at the advanced injection timing of 27° bTDC.
3.2 Effect of IOP
An IOP of 205 bar for the diesel engine was recommended by the supplier. However, IOP was varied from 210 to 240 (21.0–24.0 MPa) in incremental steps of 10 bar to study its effect on the performance of COME. Also, nozzle with three, four and five-holes were considered for these ranges of IOP to study its effect on the engine performance. The part-load (80%) and full-load tests were conducted fort these ranges of IOP and the engine operated at a rated speed of 1500 rpm. At these loads, airflow rates, COME flow rates, exhaust gas temperatures and HC, CO and NOx emission levels were recorded. Based on the results, the optimum injection pressures and nozzle geometries were identified and fixed for COME oil. Subsequently, the performance, emission and combustion parameters of COME biodiesel fuel were compared with the standard diesel fuel.
3.2.1 Standard diesel operation
The engine was operated at an IOP of 205 bar, injection timing of 23° bTDC and compression ratio of 17.5:1, as per the manufacturer’s specifications. It was observed that for 80% load, maximum BTE was found to be 25.57%, and was complying with the standard engine specifications provided.
3.2.2 Operation on COME
Performance parameters
The effects of IOP and varying nozzle geometry at the static injection timing of 19° bTDC and the maximum compression ratio of 17.5:1 are presented.
The effects of brake power on BTE at different IOPs and different nozzle geometries with three holes, four holes and five holes are shown in Figures , respectively. Among all the IOPs tested, the highest BTE occurred at an IOP of 230 bar for the nozzle geometry with four holes, each having an orifice diameter of 0.3 mm. This is because at higher injection pressures, atomisation, spray characteristics and mixing with air are better, resulting in improved combustion. A higher IOP (240 bar) will lead to a delayed injection period negating the gain.
The BTE was found to be 24.95% at the 80% load, and its maximum value was obtained for a four-hole nozzle geometry at an IOP of 230 bar. The BTE reported for the three-hole and five-hole nozzles were 24.50 and 24.25% at an IOP of 230 bar, respectively.
In view of this, the results revealed that among all the IOP and nozzle geometries studied, a higher BTE was found for a four-hole nozzle geometry at an IOP of 230 bar. The optimum IOPs for the other two nozzles (three holes and five holes) were also found at 230 bar, respectively.
The increased number of nozzle holes did not affect the ignition delay period much, but provided increased fuel–air mixing rate.
Emission parameters
HC emissions: Figures show the effect of brake power on HC emission levels at different IOPs and different nozzle geometries for COME biodiesel fuel. A significant decline in HC emission levels was observed for a four-hole nozzle geometry at an IOP of 230 bar due to better combustion. Enhanced atomisation will also lead to a lower ignition delay period. This will enhance the performance of the engine fuelled with biodiesels, which normally have a higher ignition delay due to their higher viscosity. An improvement in spray characteristics will lead to a lower ignition delay period. HC emission levels decreased from 90 to 80 ppm after the IOP increased from 210 to 230 bar at a full load. The highest IOP of 240 bar led to an increased HC emission levels to 85 ppm, and was probably attributed to the reduced BTE. In addition, a very high IOP will lead to a considerable portion of the combustion occurring in the diffusion phase and is due to the small ignition delay period. A higher IOP (240 bar) will lead to a delayed injection period negating the gain.
HC emission levels were found to be lower for the four-hole compared with the three- and five-hole nozzle geometries at an IOP of 230 bar, respectively. It can be concluded that unburnt hydrocarbons are less during the operation of the engine with a four-hole nozzle at an IOP of 230 bar, which is due to improved atomisation and proper combustion of COME biodiesel fuel.
CO emissions: Figures show the effect of brake power on CO emission levels. The observed trend for CO emission levels was similar to that for HC emission levels, with lower CO emission levels occurring for a four-hole injector at an IOP of 230 bar IOP.
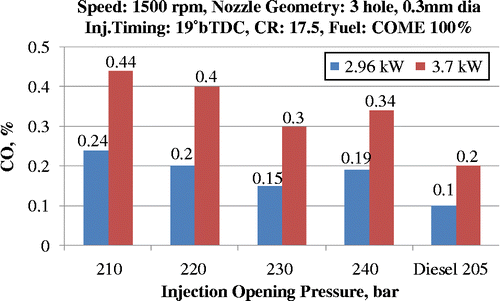
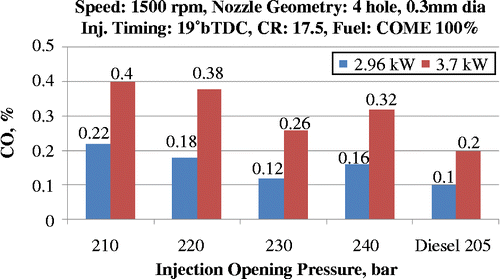
NOx emissions: NOx emission levels increased with the increase in IOP due to faster combustion and higher temperatures reached in the cycle, as shown in Figures .
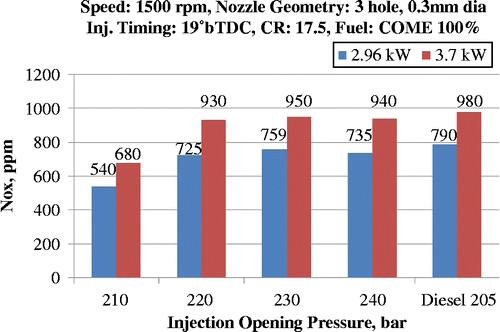
Combustion analysis
Figures and show the effect of injection pressures on pressure variations and heat release rates with CA during full-load engine operation.
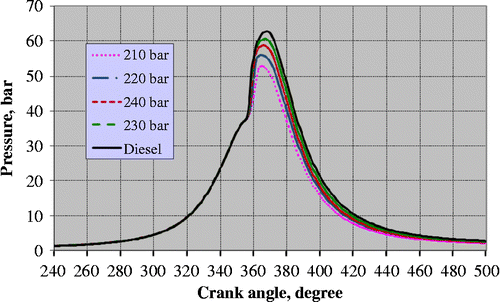
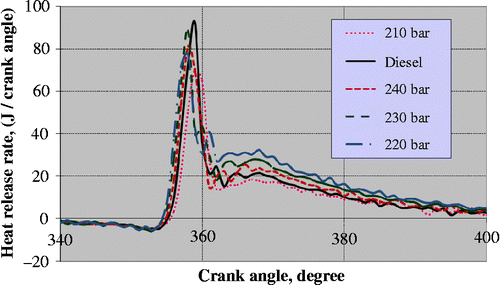
Figure shows that the peak pressure for COME biodiesel fuel throughout the combustion process increased with increased fuel injection rates as the fuel injection pressures increased from 210 to 230 bar. Figure shows that heat release rates with COME throughout the combustion process increased with increased fuel injection rates when fuel injection pressures were increased from 210 to 230 bar. Heat release rates were lower at injection opening pressures of 210 and 220 bar than at 230 and 240 bar, respectively. Heat release rates were the highest at an IOP of 230 bar followed by IOPs of 240 and 220 bar, respectively. The rates were the lowest at an IOP of 210 bar where the BTE was also lower when compared with the other IOPs.
4. Conclusions
From this exhaustive study on the feasibility of a COME-fuelled diesel engine, it can be found that its performance is lower when compared with the standard diesel fuel. However, by suitably adjusting the engine parameters such as injection timings, IOPs and nozzle geometries, it can be found that the performance of the diesel engine fuelled with COME can be improved. Therefore, COME oil can be used as an alternative fuel in diesel engines.
The retardation of injection timings from 23° to 19° bTDC showed encouraging results for COME fuel. Increasing the injection pressures from 210 to 230 bar for COME fuel favoured the performance of the engine with reduced emission levels. Increasing the number of nozzle holes in the fuel injector from three to four improved the performance of the COME-fuelled engine with reduced emission levels. However, further increasing the number of nozzle holes reduced the performance of the engine.
Finally, it can be concluded that operating the existing diesel engine with slightly higher injection pressures, increased number of holes in the fuel injector and retarded injection timings improved the performance of the COME fuelled diesel engine considerably.
REFERENCES
- Agarwal, A. K.2006. “Biofuels (Alcohols and Biodiesel) Applications as Fuels for Internal Combustion Engines.” Progress in Energy and Combustion Science33: 233–271.
- Atadashi, I. M., M. K.Aroua, and A.Abdul Aziz. 2010. “High Quality Biodiesel and Its Diesel Engine Application: A Review.” Renewable and Sustainable Energy Reviews14 (7): 1999–2008.
- Banapurmath, N. R., and P. G.Tewari. 2010. “Performance Combustion and Emissions Characteristics of a Single Cylinder Compression Ignition Engine Operated on Ethanol – Biodiesel Blended Fuels.” Proceedings of the Institution of Mechanical Engineers, Part A: Journal of Power and Energy533: 533–543.
- Banapurmath, N. R., P. G.Tewari, Y. H.Basavarajappa, and V. S.Yaliwal. 2005. Performance of Honge (Pongamia pinnata) Oil Blends in a Diesel Engine, XIX NCICEC, Annamalai University Chidambaram, India.
- Banapurmath, N. R., P. G.Tewari, and R. S.Hosmath. 2008. “Combustion and Emission Characteristics of a Direct Injection, Compression–Ignition Operated on Honge Oil, HOME and Blends of HOME and Diesel.” International Journal of Sustainable Engineering1 (2): 80–93.
- Banapurmath, N. R., P. G.Tewari, and R. S.Hosmath. 2009. “Effect of Biodiesel Derived from Honge Oil and Its Blends with Diesel When Directly Injected at Different Injection Pressures and Injection Timings in Single-Cylinder Water-Cooled Compression Ignition Engine.” Proceedings of the Institution of Mechanical Engineers, Part A: Journal of Power and Energy223 (1): 31–40.
- Bari, S., T. H.Lim, and C. W.Yu. 2002. “Effect of Preheating of Crude Palm Oil (CPO) on Injection System, Performance and Emission of a Diesel Engine.” Renewable Energy27: 339–351.
- Bari, S., C. W.Yu, and T. H.Lim. 2004. “Effect of Fuel Injection Timing with Waste Cooking Oil as a Fuel in Direct Injection Diesel Engine.” Proceedings of the Institution of Mechanical Engineers, Part D: Journal of Automobile Engineering218: 93–104.
- Basha, Syed Ameer, K.Raja Gopal, and S.Jebaraj. 2009. “A Review on Biodiesel Production, Combustion, Emissions and Performance.” Renewable and Sustainable Energy Reviews13: 1628–1634.
- Fan, Xiaohu, XiWang, ChenFeng, Daniel P.Geller, and Peter J.Wan. 2008. “Engine Performance Test of Cottonseed Oil Biodiesel.” The Open Energy and Fuels Journal1: 40–45.
- Gajendra Babu, M. K.2007. “Studies on Performance and Exhaust Emissions of a CI Engine Operating on Diesel and Diesel Biodiesel Blends at Different Injection Pressures and Injection Timings.” Paper No. 2007-01-0613. Society of Automotive Engineers, USA.
- Gajendra Babu, M. K., Chandan Kumar, and L. M. Das. 2006. “Experimental Investigations on a Karanja Oil Methyl Ester Fuelled DI Diesel Engine.” Paper No. 2006-01-0238. Society of Automotive Engineers, USA.
- Hountalas, D. T., D. A. Kouremenos, K. B. Binder, A. Raab, and M. H. Schnabel. 2001. “Using Advanced Injection Timing and EGR to Improve DI Engine Efficiency at Acceptable NO and Soot levels.” Paper No. 2001-01-0199. Society of Automotive Engineers.
- Huseyin, Aydin, and HasanBayindir. 2011. “Performance and Emission Analysis of Cottonseed Oil Methyl Ester in a Diesel Engine.” Renewable Energy35: 588–592.
- Karabektas, M., G.Ergen, and M.Hosoz. 2008. “The Effects of Preheated Cottonseed Oil Methyl Ester on the Performance and Exhaust Emissions of a Diesel Engine.” Applied Thermal Engineering28: 2136–2143.
- Karnwal, A., NaveenKumar, M. M.Hasan, RajeevChaudhary, ArshadNoor Siddiquee, and Z. A.Khan. 2010. “Production of Biodiesel from Thumba Oil: Optimization of Process Parameters, Iranica.” Journal of Energy & Environment1 (4): 352–358.
- Martin, Leenus Jesu M., and GeoEdwin. 2011. “Effect of Diesel Addition on the Performance of Cottonseed Oil Fuelled DI Diesel Engine.” International Journal of Energy and Environment2 (2): 321–330.
- Morshed, Mahbub, KanizFerdous, Maksudur R.Khan, M. S. I.Mazumder, M. A.Islam, and Md. T.Uddin. 2011. “Rubber Seed Oil as a Potential Source for Biodiesel Production in Bangladesh.” Fuel90: 2981–2986.
- Murugesan, A., C.Umarani, R.Subramanian, and N.Nedunchezhian. 2009. “Bio-diesel as an Alternative Fuel for Diesel Engines – A Review.” Renewable and Sustainable Energy Reviews13 (3): 653–662.
- Naga Sarada, S., M.Shailaja, A. V.Sita Rama Raju, and K.Kalyani Radha. 2010. “Optimization of Injection Pressure for a Compression Ignition Engine with Cotton Seed Oil as an Alternate Fuel.” International Journal of Engineering, Science and Technology2 (6): 142–149.
- Nurun Nabi, Md., Md.Mustafizur Rahman, and Md.Shamim Akhter. 2009. “Biodiesel from Cotton Seed Oil and Its Effect on Engine Performance and Exhaust Emissions.” Applied Thermal Engineering29: 2265–2270.
- Onga, H. C., T. M. I.Mahlia, H. H.Masjukia, and R. S.Norhasyimab. 2011. “Comparison of Palm Oil, Jatropha curcas and Calophyllum Inophyllum for Biodiesel.” Renewable and Sustainable Energy Reviews15: 3501–3515.
- Puhan Sukumar Jegan, R., K.Balasubbramanian, and G.Nagarajan. 2009. “Effect of Injection Pressure on Performance, Emission and Combustion Characteristics of High Linolenic Linseed Oil Methyl Ester in a DI Diesel Engine.” Renewable Energy34: 1227–1233.
- Raheman, H., and A. G.Phadatare. 2004. “Diesel Engine Emissions and Performance from Blends of Karanja Methyl Ester and Diesel.” Biomass and Bioenergy27: 393–397.
- Rakopoulos,, C. D., D. C.Rakopoulos, E. G.Giakoumis, and A. M.Dimaratos. 2010. “Investigation of the Combustion of Neat Cottonseed Oil or Its Neat Bio-diesel in a HSDI Diesel Engine by Experimental Heat Release and Statistical Analyses.” Fuel89 (12): 3814–3826.
- Ramadhas, A. S., S.Jayaraj, and C.Muraleedharan. 2005. “Characterization and Effect of using Rubber Seed Oil as Fuel in the Compression Ignition Engines.” Renewable Energy30: 795–803.
- Ramadhas, A. S., C.Muraleedharan, and S.Jayaraj. 2005. “Performance and Emission Evaluation of a Diesel Engine Fueled with Methyl Esters of Rubber Seed Oil.” Renewable Energy30: 1789–1800.
- Rosli, Abu Bakar, Semin, and Abdul RahimIsmail. 2008. “Fuel Injection Pressure Effect on Performance of Direct Injection Diesel Engines Based on Experiment.” American Journal of Applied Sciences5 (3): 197–202.
- Roy, M. M.2009. “Effect of Fuel Injection Timing and Injection Pressure on Combustion and Odorous Emissions in DI Diesel Engine.” Journal of Energy Resources Technology, ASME Transactions131: 1–8.
- Sahoo, P. K., L. M.Das, M. K. G.Babu, P.Arora, V. P.Singh, N. R.Kumar, and T. S.Varyani. 2009. “Comparative Evaluation of Performance and Emission Characteristics of Jatropha, Karanja and Polanga Based Biodiesel as Fuel in a Tractor Engine.” Fuel88 (9): 1698–1707.
- Sahoo, P. K., L. M.Das, M. K. J.Babu, and S. N.Naik. 2007. “Biodiesel Development from High Acid Value Polanga Seed Oil and Performance Evaluation in a CI Engine.” Fuel86: 448–454.
- Tao, F., Y. Liu, B. H. Rempel Ewert, D. E. Foster, R. D. Reitz, D. Choi, and P. C. Miles. 2005. “Modelling the Effect of EGR and Retarded Injection on Soot Formation in a High Speed Diesel Injection (HSDI) Diesel Engine using a Multi Step Phenomenological Soot Model.” Paper No. 2005-01-0121. Society of Automotive Engineers, USA.
- Venkanna, B. K., and C.Venkataramana Reddy. 2011. “Performance, Emission and Combustion Characteristics of Direct Injection Diesel Engine Running on Calophyllum Inophyllum Linn Oil (Honne Oil).” International Journal of Agricultural & Biological Engineering4 (1): 26–34.
- Yang, Ru, MengxingSu, JianchunZhang, FuqiangJin, ChunhongZha, MinLi, and XinminHao. 2011. “Biodiesel Production from Rubber Seed Oil Using Poly (Sodium Acrylate) Supporting NaOH as a Water-Resistant Catalyst.” Bioresource Technology102: 2665–2671.
- Yucesu, H. S., and C.Ilkilic. 2006. “Effect of Cotton Seed Oil Methyl Ester on the Performance and Exhaust Emission of a Diesel Engine.” Energy Sources Part A28: 389–398.