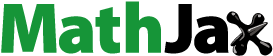
Abstract
The interest in obtaining alternative fuels from waste sources and at the same time diminishing the impact of waste disposal has drawn attention to scrap tyres' carbon recovery. In order to thermally degrade used tyre rubber, a laboratory pyrolysis system was developed in this work. The installation devised focused on the production of liquid pyrolysates, where shredded rubber was supplied as the feedstock and nitrogen used as the carrier gas to provide an oxygen-free atmosphere. The variables affecting the performance of the process were investigated, including target temperature, heating rate and total residence time. Characterization of the volatile matter released was conducted by means of mass spectrometry to determine the composition of products, and particulate matter analysis to ascertain the aerosol content in the gas stream. The reproducibility of experiments, the influence of the temperature and time, and differences between the vapours before condensation and the exhaust gases are discussed. This work identified that the larger hydrocarbon fragments condense to constitute the oils, whereas the lighter molecules remain as non-condensable gases. This work also identified that the total number of nano-scale particles carried by the exhaust stream varies with temperature; significant changes in the composition of products and particle content were reported at approximately 400°C. The high number of nano-scale solid particulate matter present in the exhaust gases suggests that a thorough treatment for that stream would be required to avoid human health hazards.
Keywords::
Abbreviations: | ||
BTX | = | benzene–toluene–xylene' |
GMD | = | geometric mean diameter |
MS | = | mass spectrometry/spectrometer |
N/cc | = | number of particles per cubic centimetre |
PA | = | particle analysis/analyser |
PAH | = | polycyclic aromatic hydrocarbons |
THT | = | total heating time |
TRT | = | temperature rise time |
1. Introduction
There has been increasing concern about the consequences of human activity in the transport sector. One of the most preoccupying concerns is the depletion of fossil fuel sources. The search for alternative fuels has developed a great interest within the scientific community, prompting research towards imaginative solutions that allow the use of current engines in the immediate future. On the other hand, as raw materials are consumed, the rate of generation of waste rises, which poses major problems at the time of discarding, reusing or recycling vehicles' components. Both of these worries are related to the management of post-consumer tyres, since they constitute disposable waste, however, profitable if rendered to useful materials (Vermeulen et al. Citation2011). It is estimated that 2.5 million tonnes of tyres are rejected per year in the European Union (López et al. Citation2010), and as traffic trends indicate, these estimates are surely set to increase, enhanced by safety measures that require more frequent replacement. Even though tyres represent only 2% of all the generated waste, their disposal has aroused a lot of attention since they usually end up stockpiled or illegally dumped, and tyre piles are at risk of causing noxious emissions in the event of fire and constitute a breeding home for vermin and disease-transmitting mosquitoes. Their inert nature makes them especially hard to redirect to other uses. Indeed, statistics have shown that only 30% of used tyres currently go to recovery, 28% for recycling, 12% are retreaded, 18% still end up landfilled, 6% are exported and 6% are reused (EC Citation2005).
Besides getting rid of non-biodegradable waste, making profit of their carbon content is fundamental not only for avoiding environmental damage, but, at the same time, for obtaining value-added products. Taking into account that tyre valorization methods are generally subsidized (Houghton et al. Citation2004), many efforts are being employed towards gasification and pyrolysis. Both lead to the production of profitable substances that, once on a stable market, could make the process self-sustainable. The social acceptance of incineration is decaying since it does not allow the recovery of the chemical potential of scrap tyres, in addition to the emission of hazardous pollutants. The nature and economical value of the products obtained drive the process selection, in which pyrolysis – the decomposition of compounds at high temperatures in the absence of oxygen – has been considered interesting since it yields three valuable fractions: gas, oils and solids (char). Potentially, all the resulting products may be utilized for fuelling purposes, although valuable chemicals can also be extracted from the gases and liquids, and carbon black or activated carbon is economically more efficient if upgraded from the solids. Pyrolysis stands preferable against gasification (induced cracking at very high temperatures in a reducing atmosphere yielding short-chain hydrocarbons) because it occurs at lower temperatures, value-added products are directly obtained (separation needed but no further synthesis) and the yield of oils is higher.
Building-up a viable methodology to transform used tyres into valid fluid fuel would establish a turning point in the way of dealing with the two above-mentioned problems. Vehicles' waste would be employed as vehicles' feed, thus decreasing the overall environmental impact of the automotive sector. This solution would also find support by the petrochemical industry since, as fossil sources are scarcer, the blending of tyre-derived fuel would prolong the time span of conventional engines for transport purposes.
A brief review of the parameters that affect the pyrolytic process follows, including the technology employed for fuel production from scrap tyres, the heating source selected and the temperature rise time (TRT, °C/min), the steady-state temperature attained and the total heating time (THT). These variables are usually manipulated to optimize the process towards securing the maximum yield and quality for the target product. As for the technology employed, different systems have been attempted according to the energy source. Ultrasonic devulcanization was investigated by Isayev, Chen, and Tukachinsky (Citation1995) using sonic energy to break the disulphur bonds in the rubber under high pressure, obtaining a viscous product only apt as remoulding material. Supercritical water depolymerization (Park and Gloyna Citation1997) decomposes the rubber compounds into their monomers, however, expensively and thus an impractical method for large-scale purposes. Appleton et al. (Citation2005) applied microwave pyrolysis, whose heating is volumetrically uniform, although the appearance of hotspots represents a major problem. Catalysts have been sought that increase the reproducibility of a certain chemical (Boxiong, Chunfei, Cai, et al. Citation2007). These are usually zeolites specifically developed for industrial commercializing, normally under patent (Aguado Zarraga et al. Citation2008) or at high prices. Both vacuum pyrolysis (Roy, Chaala, and Darmstadt Citation1999) and inert gas pyrolysis (Cunliffe and Williams Citation1998; Barbooti et al. Citation2004) have been successfully applied. They limit the secondary reactions of the gases, thus leading to higher yields of oils.
Pyrolysis temperature has a critical effect in the process performance. Higher temperatures lead to higher conversion rates, different product distributions and final composition. Most researches have described three different regions in the thermogravimetrical analysis of tyre rubber samples: Murillo et al. (Citation2006) divided the zones in the ranges 150–310, 310–430 and 350–490°C, whereas Díez et al. (Citation2004) recognized stages at 200–350, 350–450 and 450–550°C, and Betancour et al. (Citation2009) defined the domains 100–270, 270–350 and 350–450°C. The latter found a main weight loss at about 430°C.
All these papers attribute these phenomena to: (1) the drying of the molecules and the degradation of the tyres' additives, (2) decomposing of the present natural rubber and (3) the breakdown of styrene–butadiene and butadiene polymers.
The yield towards oils has also been widely studied in terms of an optimum steady-state temperature. Increasing the temperature increases the production of lighter molecules at the expense of solids. Leung et al. (Citation2002) suggested that this is due to the stronger level of cracking attained as the temperature rises, leading to that inverse relationship. More stable concentrations are found at about 500°C, whereas from 600°C onwards, gases are increasingly obtained. Very high temperatures above 760°C can promote the interaction of some species with the remaining solid phase (González et al. Citation2001). Secondary oxidation reactions may be enhanced, especially in hotter spots near the walls of the reactor. Nitrogen flow is recommended to carry away the newly created oils and to prevent further cracking. As it can be observed in Table , major production of oils by pyrolysis is achieved at about 500°C since working at higher temperatures does not produce any more benefits while increasing the amount of energy spent in the process, with slight variations depending on other process parameters employed by different researchers.
Table 1 Appropriate final temperature for the maximum yield of oils by author.
The heating rate, or the TRT (°C/min), is another of the parameters that have been widely studied in tyre pyrolysis, since the heating source selected limits the speed with which the maximum temperature can be reached. Some authors have tried variable heating rates throughout the process (González et al. Citation2001; Díez et al. Citation2004), while others have preferred to keep them constant (de Marco et al. Citation2001; Murillo et al. Citation2006; Murugan, Ramaswamy, and Nagarajan Citation2008). The most common values for electrical external heating through coils are approximately 1–15°C/min. Unapumnuk et al. (Citation2008) reported that the yield of oils remains practically unaffected by the heating rate when the maximum temperature is similar. In contrast, the TRT seems to affect the composition of products within the oils: at each heating rate, as the target temperature is increased, the greater the proportion of aromatics, the lesser the aliphatic portion. The sulphur content in the liquid fraction is diminished as the heating rate and the temperature are increased (California Integrated Waste Management Board Citation1995).
The introduction of a gas flow during pyrolysis is reckoned to increase the yield towards oily products (Yongrong, Jizhong, and Guibin Citation2000). Nitrogen and helium are the most common inert carrier gases used in tyre pyrolysis. The nature of the gas does not influence the quantity or quality of the products; however, a wide range of gas flow rates has been found in the literature. A helium current is employed for flash pyrolysis when the residence time is shortened (Zabaniotou and Stavropoulos Citation2003). As for small pyrolytic reactors or relatively small samples, gas flows of nitrogen have been reported to fall in the region of 10− 2–10− 3 l/min order of magnitude (Napoli et al. Citation1997; González et al. Citation2001; Murillo et al. Citation2006; Qu et al. Citation2006). Bulkier samples seem to require higher gas flow rates (Cunliffe and Williams Citation1998; Laresgoiti et al. Citation2004), however, depending on the initial sample size: a relationship with the sample size was encountered by Barbooti et al. (Citation2004), concluding that smaller particles yielded more oils throughout the range of gas flows.
The THT is another fundamental variable, of as much importance as the final temperature attained. Enough time has to be allowed for the pyrolysis to be completed and the cracking of the long chains into the desired length range accomplished. Rofiqul Islam, Haniu, and Rafiqul Alam Beg (Citation2008) eventually concluded that the higher the time that gaseous products are kept in the reactor, the lower the yield towards liquids, since the possibility of secondary reactions increases. Berrueco et al. (Citation2005) carried out experiments of several hours' duration and determined that the greater changes occurred in the first 15–30 min, and then a slower conversion took place. At moderate heating rates, 15°C/min, the THT can be reduced to 30 min, as utilized by de Marco et al. (Citation2001) and Laresgoiti et al. (Citation2004). Murillo et al. (Citation2006) investigated the reaction time influence on performance, which happened to be dependent on the gas flow rate, target temperature and heating rate as well.
In terms of composition and properties, most authors have agreed on the general composition of the pyrolytic products (Cunliffe and Williams Citation1998; Kaminsky and Mennerich Citation2001; Berenguer Citation2007; Boxiong, Chunfei, Cai, et al. Citation2007), comprising alkanes, alkenes, cyclic derivatives and vinylalkenes, and also aromatics such as benzene, toluene, xylene (BTX), styrene, limonene and polycyclic aromatic hydrocarbons (PAH) such as naphthalene, fluorene and phenanthrene. Benzothiazol also appears in oils due to the common inclusion of this compound as the vulcanization accelerator in the rubber industry. The presence of PAH poses some problems in the use of tyre-derived oils as fuels. They have been recognized to be carcinogenic and mutagenic, so in case they are not completely burned, health hazards would be involved. Another main issue is their tendency to particle generation and the increased soot formation caused by their combustion (Williams, Besler, and Taylor Citation1990). It is known that PAH start appearing with increasing pyrolysis temperature, in the range of 700–800°C (Yongrong, Jizhong, and Guibin Citation2000), so primarily their content would be much lower if the temperature is maintained under that threshold.
Regarding the particle content carried by the gases (Wu, Sua, and Baeyens Citation1997) or remnant in the oils, very little has been found so far by explicitly analysing their abundance or size. Although the influence of the dimension of the tyre crumbs initially fed has been widely investigated (Islam, Khan, and Alam Citation2003; Al-Salem, Lettieri, and Baeyens Citation2009), and also the combustion behaviour of pyro-oils and their emitted particles (Williams, Besler, and Taylor Citation1990), particulate matter analysis of the vapours produced during tyre pyrolysis is a novelty introduced in this work. This might bring light to the management of gaseous residues and liquid streams in future production plants, constituting a major subject for quality control, human safety and environmental impact. The development of this work is based on the beneficial impact that the production of good-quality tyre oils may cause in the fuel industry.
Considering the batch regime intended and the available resources, inert gas pyrolysis has been selected as the suitable production method, using electrical resistances as the heating source and nitrogen as the carrier gas. Mass spectrometry (MS) of the vapours coming out of pyrolysis has been performed before and after the condensation stage for retrieving the liquids. The main scope of this work is confined to investigating the total number, size range and geometric mean diameter (GMD) of nano-scale particulate matter originating from the tyre pyrolyis process that could be emitted into the atmosphere through the untreated exhaust stream, using a small-scale experimental set-up.
2. Experimental methodology
The reactor was a hermetic stainless-steel vessel, specifically built for this purpose (110 mm height, 100 mm diameter, 8 mm thickness), provided with an RS 206-3750 digital thermocouple (Digitron Instruments Ltd, Devon, UK) in order to measure the in-vessel temperature. The system was purged with nitrogen (2 bar) in order to displace oxygen from the pipelines and provide a pressure slightly higher than the atmospheric pressure, which prevents oxygen leaks from the surrounding air during the operation. The heating was supplied by an electric 1500 W hot plate (Ningbo Guanhao Electric Appliance Co. Ltd, Cixi Zhenjiang, China), in addition to an electric wrapping heater Typ-TD05 (Isopad GmbH, Heidelberg, Germany). The two methods were installed for a more uniform heating rate control. Once the vapours started forming, they were led to a condensation bath consisting of a plastic water container and submerged stainless-steel coils. The separated non-condensable phase came out as exhaust, whereas the liquids were collected in adequate glass recipients. Vapour and gas samples were extracted, respectively, at two points, before and after the condensation stage. Their composition was determined by means of MS (Vacuum ThermoStar™, Pfeiffer, Asslar, Germany provided with MS software Quadsar 422; NIST MSSearch database available for spectrum analysis) (Pfeiffer-Vacuum 2009) and its particle content was measured by a fast particle spectrometer (DMS500, Cambustion Ltd, Cambridge, UK, provided with software version UIv2.08). The set-up was installed inside a ventilated cell. The regime of production was discontinuous, i.e. by batches. The operational conditions varied for different sets of experiments, although the procedure was kept unchanged, as depicted in Figure . A SartΦrius I8100P scale (precision ± 0.01 g) was used to determine the initial weight of the samples. In each batch, 100 g of tyre rubber was introduced into the reaction chamber. For the sake of repeatability, at least three experiments were performed at the same operational conditions. Time and temperature were noted down at regular intervals so that the TRT and THT were strictly monitored. Whereas only a qualitative analysis of the compounds present in the products was performed by means of MS, the particle analyser (PA) detected the specific number of particles per volume (N/cc) and their size as the GMD. Once the characterization of the vapours was completed, the sampling lines were closed and pyrolysis was focused on oil collection.
2.1 Nano-scale particulate matter measurement
The particulate number count and size distributions were measured using a DMS500 fast particle spectrometer. The measurements were based on the particle's electrical mobility. Electrical mobility is a measure of the ease with which a charged particle will be deflected by an electric field, and is a function of both the charge on the particle and its aerodynamic drag. Both of these parameters are in turn functions of the particle diameter; so by knowing a particle's electrical mobility, its size can be determined (Cambustion Citation2006). A schematic diagram of the particle classification column of DMS500 is shown in Figure .
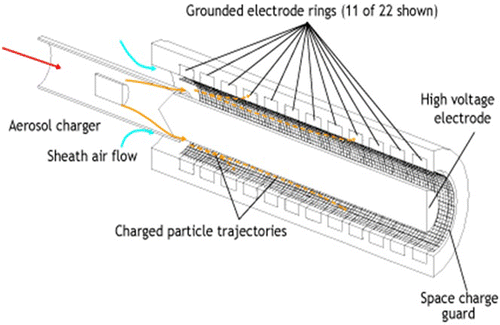
Particles that enter the particle spectrometer are diffusion charged, made to collide with air ions to charge them and then carried down the central column, as shown in Figure . The electrode in the middle repels the particles, which are deflected according to their electrical mobility. Particles with a high electrical mobility will be repelled sooner than those with a lower electrical mobility. A total of 22 electron rings run around the outside of the columns, which detect the particles landing on them, and a size density spectrum is built up accordingly. The minimum diameter that the instrument can detect is 5 nm.
2.2 Mass spectrometry
A quadrupole MS [28] used in this study consists of an ionization chamber, an analyser tube, an ion detector and an amplifier. The sample gas enters the ionization chamber through a small orifice, where its molecules are bombarded by electrons generated by the hot cathode filament. The electrons generated at the cathode are then attracted to the anode, and pass through the sample. The electrons collide with the sample molecules, removing the electrons from them to create positively charged ions. These are then repelled towards the analyser tube. The ionized sample travels along the analyser tube, and is deflected by a magnetic field. The amount of deflection is proportional to the mass/charge (m/e) ratio of the sample. The ion detector measures the current generated by the sample, and the distance deflected (m/e ratio). The signal is then amplified and recorded. The m/e ratio and the ion current are then built up to generate the mass spectrum.
The aim of this analysis was purely qualitative: the identification of relevant species in the vapour stream from tyre rubber pyrolysis in order to check whether the composition was similar to previous studies. This work does not attempt to decipher the tyre's composition. Even though race tyres differ significantly from passenger car tyres, the expected main pyrolysis products come from the same rubber compounds. The available MS performed screenings from 0 to 100 m/z at 10− 6 mbar vacuum. The position of a peak has a precision of ± 1 amu.
2.3 Tyre pre-treatment
A used racing rain tyre, Goodyear D2691 20.0x7.0-13 R065, was cleaned and all other elements, but rubber, removed. Rubber cut pieces from the tyre sidewall and tread were manually chipped to regular size, water washed and allowed to dry in-between blotting paper sheets. Prior to each batch of production, 100 g of chopped rubber were oven-dried at 110°C for a few hours until constant weight. The removal of moisture is beneficial to avoid an excess of water molecules if an inert atmosphere is to be really attained.
3. Results and discussion
3.1 Heating rate, temperature and reaction time
The TRT is one of the variables that most affects the tyre pyrolysis. A fine control over this parameter was achieved by combined systems of electrical heating. The curve that represents the variation in temperature with time can be observed in Figure (a). The gradual increment in temperature is very similar for all the cases. The slope of that curve indicates the instantaneous rate, which acquires disperse values, but close to 5°C/min, as advised in the literature. As the temperature increases, the rate diminishes considerably, although all the results show the same logarithmic trend (Figure (b)), thus proving that the system is able to reproduce those conditions.
The maximum temperature reached depended slightly on the atmospheric conditions in the laboratory present at the moment of pyrolysis, varying from 450 to 500°C (Table ). However, for characterization purposes, temperatures within 10°C were considered constant. Pyrolysis occurred, as evidenced through the mass spectra registered, which means that those temperatures were high enough to cause the cracking of rubber compounds.
Table 2 Maximum temperatures and THT for different experiments.
As for the reaction time, the THT and TRT are related. The THT depended on the time required to attain the maximum temperature, and on the period it stayed at that temperature, as shown in Table . The isothermal stage was maintained until the vapours were consumed, when pyrolysis was declared finished. Mass spectroscopy was employed to determine whether there were reactions still occurring and whether there was composition variation during that lapse.
3.1.1 Temperature
Changes in composition at different temperatures are shown in Figure . At lower temperatures, just above 200°C, the intensity of the peaks is lower, although compounds other than those present in the reference air appear, which means that cracking has already started. As the temperature is increased, the peaks gain in intensity. From 300°C onwards, the abundance of impacts decays very slightly, probably due to the fewer vapours generated as the volatile matter of the rubber is consumed. At temperatures over 400°C, defined peaks are still clearly observed, meaning that pyrolysis is still in full swing. As for the changes that are supposed to occur once the maximum temperature is established and kept constant, they are visualized in Figure . The spectrum registered just after reaching the maximum temperature presents higher peaks than those observed after a while. In the high mass region, there is almost a disappearance of products, whereas lighter compounds still are being produced, although at a lower intensity. This is again attributed to the scarcer vapours generated near the THT.
3.1.2 Condensation
The characterization undertaken so far compares samples of the vapours from the reactor, i.e. prior to condensation. These vapours carry both the condensable and non-condensable fractions. The difference in the intensity or position of the peaks between the samples extracted before (vapour phase) and after the condensation stage (gas phase) yields considerable information, as shown in Figure . At lower masses, most of the peaks in the gas stream are comparable with the reference current, whereas the vapours seem to be richer in those fragments. In the high mass region, the composition does not greatly vary (correspondent peaks), although the concentration of the larger fragments (intensity) is clearly lower in the exhaust gases; this is probably because larger molecules are prone to condense.
3.1.3 Composition
Focusing on the mass fragments, the actual identification of compounds that were collected is shown in Table and Figure . As expected from the literature, short molecules (hydrogen) and olefins are present to a great extent. These are the monomers conforming rubber polymers (styrene, isoprene and butadiene) or coming from rupture processes (ethane and propene) (Grieco, Bernardi, and Baldi Citation2008). According to Laresgoiti et al. (Citation2004), also longer chains (>C20) should be encountered, although the limit of the MS in 100 amu restricted the capability to detect them. Cyclic compounds are very common as well, whether single rings of five or six carbon atoms, or coupled rings. Unsaturations are known to be favoured under heating conditions. BTX and compounds based on benzene chemistry were already predicted. In this case, they coincide with research by Kaminski and Mennerich (Citation2001). PAH were difficult to identify given the low concentrations of the peaks in the high mass region. Nevertheless, traces of naphthalene were recognized in the vapours.
Table 3 Tentative assignment of composition.
This represents a superficial analysis of which molecules carry the vapours. Our aim was not to determine the former composition of the racing tyre, but to ascertain to some extent whether the exhaust gases or condensed liquids contained the expected compounds, and to detect high levels of health hazardous substances generated by this production methodology.
3.2 Particulate matter analysis
The determination of particle content in the vapours from tyre pyrolysis is considered a vital measurement of the quality of the exhaust gases and the condensed oils. The absence of the literature in this respect makes this section especially important. A fast particle spectrometer, DMS500, was employed to characterize the nano-scale particles carried away by the gas stream. The differential analyser available provides a number and size of spectra for the particles between 5 nm and 1 μm. This instrument uses a classifier column operating at a sub-atmospheric pressure. A cyclone separator first removes the particles larger than 1000 nm, and then the sample passes through a corona discharge charger. The instrument response time is 300 ms. The amplified signal is converted to the total number of particles per cubic centimetre, N/cc, and the GMD. These two parameters will grant significant conclusions.
3.2.1 Total number of particles
Three experiments are selected to be compared for the sake of clarity. The repeatability of results and their variation with temperature throughout pyrolysis can be simultaneously represented in a three-dimensional plot. Figure shows the total number of particles carried away by the gas stream. The total number of particles endures an overall increase as the temperature rises irrespective of minor variations. Nevertheless, there seems to be a plateau at approximately 400°C, a temperature at which major changes have been observed, both in composition and in particle size as it will be unfolded later on.
Experiment 2 presents recordings that are asymmetrically biased towards a higher number of particles compared with the other two experiments, whose measurements are much more coherent. In this case, however, the dependency with temperature shows that the number of solids increases as the temperature is raised up to 400°C, from which it diminishes again. Also, aggregation phenomena could be taking place, condensing small nuclei into larger particles that are separated by the cyclone. The size study will further deal with these suppositions in the following section.
3.2.2 Geometric mean diameter
It is important to highlight that not only the number of particles remaining in the resultant products is relevant, but also their size is crucial to characterize the quality of pyrogases and pyro-oils. The GMD is used as a measure of the equivalent average diameter of the 5–1000 nm particle size range investigated. The GMD of a range of particle diameters is the nth root of the product of n diameters. Once the liquids were subtracted, the analysis of the solids present in the gaseous exhaust resulted in Figure . As can be perceived, the particle size is much lower for this fraction. The diameters for experiment 3 seem to be displaced towards higher figures, although the results can be positively designated as repeatable. In these samples, the influence of the temperature does not seem to cause major changes in the mean size of the particles. Whether their number may be higher or fewer, their size in most cases is below 40 nm. Regarding the treatment of these exhaust gases, these findings recommend that they be carefully disposed, and safety measures be undertaken, since they cannot be collected by simple electrostatic precipitation. Solids in the nano meter range can be inhaled and promote various diseases as well as pollution. On the other hand, this feature is desirable if the gases and, especially, oils are destined to be used as fuels: small particles would not be problematic during combustion, neither damaging the engines nor generating soot.
3.2.3 Size spectral density
The particle sizes' actual distribution, instead of a mean diameter, contributes to adding the information of variations undergone in the period of sampling for each temperature recorded for a given experiment. The plots representing the size density, i.e. the number of particles of each size per volume , resemble Gaussian curves with different widths, often askew or showing shoulders (Figure ). At approximately 400°C, a surge of larger molecules, in the region of 100 nm, is observed. From then onwards, although the average diameter remains low, there is a sudden increase in the specific number of total particles. The width of the curves indicates the deviation, which is considerable at low temperatures but diminishes as the curves become more pointed. The spectral density shows that the number density of smaller particles increases with temperature.
In order to emphasize the changes that seem to occur at 400°C, the size density and the mass spectrum are plotted together (Figure ). At this temperature, the differences before and after the condensation stage are evident, indicating that larger particles are influenced by the liquid condensing current, and carried away. However, particles of less than 50 nm remain suspended in the gas stream.
The atomic mass peaks present at this temperature may indicate a relation between the particle content and composition. A higher peak than normal appears at 90 amu, referring to high-molecular-weight compounds (multiple ring and multiple radical chains), and at about 78 amu, recognizing the presence of benzene and derivates. The generation of these types of compounds might induce the expelling of solid particles of higher size or promote aggregation. As their production diminishes, so does the equivalent diameter of particles.
3.2.4 Oil production
After completing the set of experiments due for characterization of tyre pyrolysis products, we proceeded to the collection of oils. In order to determine the volatile matter contained in the tyre rubber, the mass introduced in the reactor for each experiment was noted down, and compared with the mass of solids recovered at the end. The pyrolysis unit was able to reproduce the process quite accurately (Table ). Vapours conformed around 50% of the initial rubber, which is an optimistic percentage, indicating that half of the material can be directly converted to combustibles. However, the condensable liquids' contribution to that percentage could not be calculated. Even though liquids were indeed collected, a great portion was lost in the pipelines due to several reasons. First of all, it was noticed that the vapour flow was pulsating, not homogeneously exiting the reaction chamber, and this affected to a great extent the condensation efficiency of the system. In addition, some of the vapours remained in the closed ends of the piping (dead volumes) instead of being directed to the cooling bath. This could be avoided if the production capacity was higher, so it represents a problem only at the laboratory scale. Moreover, the compounds have different heating capacities, so their cooling requirements are dissimilar. It meant that they started condensing at different pipe lengths. Therefore, various samples were collected at subsequent points of the installation: at the short, mid and full length of the available refrigeration coil. The gathered liquids had different appearance: thin, light yellowish and heavy, thick brownish fractions, respectively. The lighter fraction, obtained at a short length, is supposed to contain the lightest fragments, whereas the heavy fraction must include larger molecules. When the oils make contact with water, an emulsion is established according to their organic nature. The accurate composition of each fraction collected could be ascertained by means of high-performance liquid chromatography, which will constitute part of future studies initiated by this work.
Table 4 Yields of products in weight percentage.
3.2.5 Reproducibility
The experiments carried out to characterize the nano-scale particle carried away by the gas stream after the condensation unit showed that the experiments are repeatable as long as the temperature of the reactor is maintained constant. The present study analysed the mass spectra of the vapour stream (sample taken before the condensation unit) and the gas stream (sample taken before the condensation unit) and the particles from the gas phase. It was assumed that the condensation bath is sufficient to condense the vapour into liquid and only the gas and suspended solid are present in the gas stream. It is not possible to ascertain that consumption fully since vapour removal canisters are used in the gas stream rather than relying on the condenser unit to remove all vapours from the pyrolysis products. However, this study shows the importance of the need for the after-treatment system if an industrial process is established for tyre pyrolysis.
4. Conclusions
The present study used a small-scale experimental set-up to measure the nano-scale particulate matter in the exhaust stream of the tyre pyrolysis process. It identified that:
The total number of particles detected increased as the temperature was raised and a portion of those particles proved to be carried away in the liquids. They cover a non-negligible range of 107 to 108 particles per cc. In fact, at 400°C, there was an inflexion point, and the number of particles started decreasing in the exhaust again to the 107 order.
After the condensation of pyrolysis products, the solid particles did not vary in size with temperature.
The size spectral density confirms that considerable changes take place at 400°C: larger particles appear but in fewer number, which may be attributed to an aggregation phenomenon. This also might explain the increased number of small particles present in the gases, since the condensed particles would be carried away by the liquid fraction.
The productivity of the system in terms of the yield of volatile matter is good, producing 50%w of the vapours.
The high number of nano-scale solids present in the exhaust gases suggests that a thorough treatment for that stream would be required to avoid human health hazards. However, it also represents that no significant problems would arise from the combustion of either gases or pyro-oils.
Acknowledgement
This work was developed under the framework of Cajastur-Fernando Alonso scholarship at the School of Technology, Oxford Brookes University.
Notes
1. Email: [email protected]
References
- Aguado Zarraga, R., B. Elorriaga Javier, J. L. Martinez Camus, and M. Aurrecoechea Olazar . 2008. “Method for Treating Tyres and Pyrolysis Reactor for Carrying Out Said Method.” European Patent Application, publication number: WO2008126042; filed: Spain, 11 April.
- Al-Salem, S. M. , P. Lettieri , and J. Baeyens . 2009. “Kinetics and Product Distribution of End of Life Tyres (ELTs) Pyrolysis: A Novel Approach in Polyisoprene and SBR Thermal Cracking.” Journal of Hazardous Materials 172 (2–3): 1690–1694. 10.1016/j.jhazmat.2009.07.127.
- Appleton, T. J. , R. I. Colder , S. W. Kingman , and I. J. Lowndes . 2005. “Microwave Technology for Energy-Efficient Processing of Waste.” Applied Energy 81 (1): 85–113. 10.1016/j.apenergy.2004.07.002.
- Barbooti, M. M. , T. J. Mohamed , A. A. Hussain , and F. O. Abas . 2004. “Optimization of Pyrolysis Conditions of Scrap Tires Under Inert Gas Atmosphere.” Journal of Analytical and Applied Pyrolysis 72 (1): 165–170. 10.1016/j.jaap.2004.05.001.
- Berenguer, A. 2007. “Oferta tecnológica: Reciclado de neumáticos por pirólisis y combustión.” [Technological Offer: Recycled tires for pyrolysis and combustion.] Alicante. Spain: Universitat d'Alacant. www.sgitt-otri.ua.es/es/empresa/documentos/reciclado-neumaticos.pdf .
- Berrueco, C. , E. Esperanza , F. J. Mastral , J. Ceamanos , and P. García-Bacaicoa . 2005. “Pyrolysis of Waste Tyres in an Atmospheric Static-Bed Batch Reactor: Analysis of the Gases Obtained.” Journal of Analytical and Applied Pyrolysis 74 (1–2): 245–253. 10.1016/j.jaap.2004.10.007.
- Betancur, M. , J. D. Martínez , and R. Murillo . 2009. “Production of Activated Carbon by Waste Tire Thermochemical Degradation with CO2 .” Journal of Hazardous Materials 168 (2–3): 882–887. 10.1016/j.jhazmat.2009.02.167.
- Boxiong, S. , W. Chunfei , G. Binbin , W. Rui , and L. Cai . 2007. “Pyrolysis of Waste Tyres with Zeolite USY and ZSM-5 Catalysts.” Applied Catalysis B: Environmental 73 (1–2): 150–157. 10.1016/j.apcatb.2006.07.006.
- Boxiong, S. , W. Chunfei , L. Cai , G. Binbin , and W. Rui . 2007. “Pyrolysis of Waste Tyres: The Influence of USY Catalyst/Tyre Ratio on Products. 2007.” Journal of Analytical and Applied Pyrolysis 78 (2): 243–249. 10.1016/j.jaap.2006.07.004.
- California Integrated Waste Management Board, Sacramento . 1995. “Environmental Factors of Waste Tire Pyrolysis, Gasification, and Liquefaction.” CalRecovery Report No. 1364.
- Cambustion . 2006. DMS500 Fast Particulate Spectrometer; User Manual. Cambridge, UK: Cambustion.
- Cunliffe, A. M. , and P. T. Williams . 1998. “Composition of Oils Derived from the Batch Pyrolysis of Tyres.” Journal of Analytical and Applied Pyrolysis 44: 131–152. 10.1016/S0165-2370(97)00085-5.
- de Marco, I. , M. F. Laresgoiti , M. A. Cabrero , A. Torres , M. J. Chomon , and B. Caballero . 2001. “Pyrolysis of Scrap Tyres.” Fuel Processing Technology 72 (1): 9–22. 10.1016/S0378-3820(01)00174-6.
- Díez, C. , O. Martínez , L. F. Calvo , J. Cara , and A. Morán . 2004. “Pyrolysis of Tyres. Influence of the Final Temperature of the Process on Emissions and the Calorific Value of the Products Recovered.” Waste Management 24 (5): 463–469. 10.1016/j.wasman.2003.11.006.
- EC (European Commission) . 2005. “Implementation of the Landfill Directive in the 15 Member States of the European Union.” REF ENV.A.2/ETU/2004/0016. Accessed October 2005. www.ec.europa.eu/environment/waste/landfill_index.htm .
- González, J. F. , J. M. Encinar , J. L. Canito , and J. J. Rodríguez . 2001. “Pyrolysis of Automobile Tyre Waste. Influence of Operating Variables and Kinetics Study.” Journal of Analytical and Applied Pyrolysis 58–59: 667–683. 10.1016/S0165-2370(00)00201-1.
- Grieco, E. , M. Bernardi , and G. Baldi . 2008. “Styrene–Butadiene Rubber Pyrolysis: Products, Kinetics, Modelling.” Journal of Analytical and Applied Pyrolysis 82 (2): 304–311. 10.1016/j.jaap.2008.05.004.
- Houghton, N. , K. Preski , N. Rockliffe , and D. Tsolakis . 2004. Final Report: Economics of Tyre Recycling. Australia: Department of Environment and Heritage. RC3765.
- Isayev, A. I. , J. Chen , and A. Tukachinsky . 1995. “Novel Ultrasound Technology for Devulcanisation of Waste Rubbers.” Rubber Chemistry and Technology 68 (2): 267–280. www.dx.doi.org/10.5254/1.3538741.
- Islam, M. N., M. F. R. Khan, and M. Z. Alam . 2003. “Production and Characterization of Scrap Tyre Pyrolysis Oil and Its Blend.” In Proceedings of the International Conference on Mechanical Engineering (ICME2003), Dhaka, Bangladesh, December 26–28, 1–4.
- Kaminsky, W. , and C. Mennerich . 2001. “Pyrolysis of Synthetic Tire Rubber in a Fluidised-Bed Reactor to Yield 1,3-Butadiene, Styrene and Carbon Black.” Journal of Analytical and Applied Pyrolysis 58–59: 803–811. 10.1016/S0165-2370(00)00129-7.
- Laresgoiti, M. F. , B. M. Caballero , I. de Marco , A. Torres , M. A. Cabrero , and M. J. Chomón . 2004. “Characterization of the Liquid Products Obtained in Tyre Pyrolysis.” Journal of Analytical and Applied Pyrolysis 71 (2): 917–934. 10.1016/j.jaap.2003.12.003.
- Leung, D. Y. C. , X. L. Yin , Z. L. Zhao , B. Y. Xu , and Y. Chen . 2002. “Pyrolysis of Tire Powder: Influence of Operation Variables on the Composition and Yields of Gaseous Product.” Fuel Processing Technology 79 (2): 141–155. 10.1016/S0378-3820(02)00109-1.
- López, G. , M. Olazar , R. Aguado , and J. Bilbao . 2010. “Continuous Pyrolysis of Waste Tyres in a Conical Spouted Bed Reactor.” Fuel 89: 1946–1952. 10.1016/j.fuel.2010.03.029.
- Murillo, R. , E. Aylón , M. V. Navarro , M. S. Callén , A. Aranda , and A. M. Mastral . 2006. “The Application of Thermal Processes to Valorise Waste Tyre.” Fuel Processing Technology 87 (2): 143–147. 10.1016/j.fuproc.2005.07.005.
- Murugan, S. , M. C. Ramaswamy , and G. Nagarajan . 2008. “A Comparative Study on the Performance, Emission and Combustion Studies of a DI Diesel Engine Using Distilled Tyre Pyrolysis Oil–Diesel Blends.” Fuel 87 (10–11): 2111–2121. 10.1016/j.fuel.2008.01.008.
- Napoli, A. , Y. Soudais , D. Lecomte , and S. Castillo . 1997. “Scrap Tyre Pyrolysis: Are the Effluents Valuable Products?” Journal of Analytical and Applied Pyrolysis 40–41: 373–382. 10.1016/S0165-2370(97)00011-9.
- Park, S. , and E. F. Gloyna . 1997. “Statistical Study of the Liquefaction of Used Rubber Tyre in Supercritical Water.” Fuel 76 (11): 999–1003. 10.1016/S0016-2361(97)00088-4.
- Pfeiffer-Vacuum . 2009. ThermoStar Operating Manual. Asslar: Pfeiffer Vacuum GmbH.
- Qu, W. , Q. Zhou , Y.-Z. Wang , J. Zhang , W.-W. Lan , Y.-H. Wu , J.-W. Yang , and D.-Z. Wang . 2006. “Pyrolysis of Waste Tire on ZSM-5 Zeolite with Enhanced Catalytic Activities.” Polymer Degradation and Stability 91 (10): 2389–2395. 10.1016/j.polymdegradstab.2006.03.014.
- Rofiqul Islam, M. , H. Haniub , and M. Rafiqul Alam Beg . 2008. “Liquid Fuels and chemicals from Pyrolysis of Motorcycle Tire Waste: Product Yields, Compositions and Related Properties.” Fuel 87 (13–14): 3112–3122. 10.1016/j.fuel.2008.04.036.
- Roy, C. , A. Chaala , and H. Darmstadt . 1999. “The Vacuum Pyrolysis of Used Tires: End-Uses for Oil and Carbon Black Products.” Journal of Analytical and Applied Pyrolysis 51 (1–2): 201–221. 10.1016/S0165-2370(99)00017-0.
- Unapumnuk, K. , T. C. Keener , M. Lu , and F. Liang . 2008. “Investigation into the Removal of Sulfur from Tire Derived Fuel by Pyrolysis.” Fuel 87 (6): 951–956. 10.1016/j.fuel.2007.05.036.
- Vermeulen, I. , J. Van Canegham , C. Block , J. Baeyens , and C. Vandecasteele . 2011. “Automotive Shredder Residue (ASR): Reviewing its Production from End-of-Life Vehicles (ELVs) and Its Recycling, Energy or Chemicals' Valorisation.” Journal of Hazardous Materials 190 (1–3): 8–27. 10.1016/j.jhazmat.2011.02.088.
- Williams, P. T. , S. Besler , and D. T. Taylor . 1990. “The Pyrolysis of Scrap Automotive Tyres: The Influence of Temperature and Heating Rate on Product Composition.” Fuel 69 (12): 1474–1482. 10.1016/0016-2361(90)90193-T.
- Wu, S. Y. , M.-F. Sua , and J. Baeyens . 1997. “The Fluidized bed Pyrolysis of Shredded Tyres: The Influence of Carbonparticles, Humidity, and Temperature on the Hydrodynamics.” Powder Technology 93 (3): 283–290. 10.1016/S0032-5910(97)03268-3.
- Yongrong, Y., C. Jizhong, and Z. Guibin . 2000. “Technical Advance on the Pyrolysis of Used Tyres in China.” China–Japan International Academic Symposium Environmental Problem in Chinese Iron-Steelmaking Industries and Effective Technology Transfer Sendai, Japan, March 6.
- Zabaniotou, A. A. , and G. Stavropoulos . 2003. “Pyrolysis of Used Automobile Tires and Residual Char Utilization.” Journal of Analytical and Applied Pyrolysis 70 (2): 711–722. 10.1016/S0165-2370(03)00042-1.