Abstract
The recent developments in manufacturing organizations recognize sustainability as an important value addition for survival in the competitive scenario. The design engineers are in search of approaches for creating environmental conscious products. The purpose of this paper is to report a research carried out for ensuring sustainable product design by the integration of Design for Environment (DFE) and Design for Manufacture and Assembly (DFMA) methodologies. In this context, this paper reports a case study carried out in an automotive component. The candidate product is the charge alternator pulley. The existing pulley has been created using Computer Aided Design. Then sustainability analysis was conducted on the existing component for determining environmental impact. This is followed by the engineering analysis of the component using ANSYS. Then conceptual design changes were developed in the proposed product using DFMA concept. Then the environmental impact has been evaluated in terms of carbon footprint, energy consumption and air/water impacts on proposed product. It has been found that the optimized pulley design possesses minimal environmental impact. The result of the case study indicated that the integration of DFE and DFMA concept could initiate new developments in sustainable designs with minimal impact to the environment and it also reduces the product cost.
1. Introduction
The technological advancement and improvement in industries improves the demand for new products. To fulfill this demand, the speed and capacity of production by a company must be enhanced with eco-friendliness. In this regard, sustainability is recognized as an important concept for survival in the competitive business environment (Bevilacqua, Ciarapica, and Giacchetta, Citation2007). In general, the contemporary designers prefer tools that automate and simplify material decisions due to ever increasing cost and regulatory issues. Sustainable design is a complete and holistic approach for creating products and systems that are environmentally safe, harmless, socially equitable and economically viable. It makes clear that the design should be such that it offers measurable environmental benefits; it caters to the needs of everyone involved in its production, use, disposal or reuse. Sustainable organizations reduce production cost and prevent environmental problems for maintaining clean and green atmosphere (Senthilkumaran et al. Citation2001). Sustainable development influenced developed countries, major organizations and automotive industry to adopt environmental conscious practices. Automobile manufacturers have clearly committed themselves to supply the market with safer and more environment friendly products, which are continuously investing enormously in research & development aimed at further improvements of the product. The practical aspects of sustainable product design involve minimal material usage, improved material choices, design for ease of disassembly, product reuse, minimal energy consumption, manufacture without producing hazardous wastes and usage of clean technologies. Moreover, Design for Manufacture and Assembly (DFMA) assists Design for Environment (DFE) in its application, especially in the recycling and recovery stages of a product’s life cycle. In addition to assisting DFE, DFMA reduces costs and product development time by reducing the number of design corrections at the manufacturing stage, through early application in the design process and simplification of the design (Boothroyd, Dewhurst, and Knight, Citation1994).
In this context, this paper reports the study of ensuring sustainable design of the alternator pulley using Computer Aided Design (CAD), engineering analysis using ANSYS and DFMA methodologies. This case study begins with CAD modelling of pulley followed by sustainability analysis to determine environmental impact in terms of carbon footprint, energy consumption, etc. on existing and proposed models. Then the alternator pulley design has been optimized using DFMA methodology. This is followed by the measurement of environmental impact. The results of the case study indicated that the utilization of CAD and DFMA concepts could lead to the development of sustainable products. The uniqueness and novelty of the study is that it is an attempt to integrate DFE and DFMA for ensuring sustainability in the early design stage of pulley and thereby environmental impact has been minimized. Nevertheless, the integration of DFE and DFMA provides greater potential for advanced manufacturing practices because redesign of product to suit manufacturability and further design studies tries to minimize environmental impact, product development time and cost.
2. Literature review
The literature has been reviewed from the perspective of DFE, Sustainability and DFMA.
2.1. Literature review on DFE and sustainability
Bras (Citation1997) have presented various issues and options of incorporating environmental issues in product design and realization. The author has presented a brief overview and classification of a number of approaches for reducing the environmental impact as well as their organizational impact. Gungor and Gupta (Citation1999) have presented environmentally conscious manufacturing and product recovery, which involves integration of environmental thinking into new product development including design, material selection, manufacturing processes and delivery of the product to the consumers, plus the end-of-life management of the product after its useful life. Senthilkumaran et al. (Citation2001) have presented life cycle environmental cost analysis model to include eco-cost into the total cost of the products. The model identifies the feasible alternative for cost-effective, eco-friendly parts/products. Kaebernick, Kara, and Sun (Citation2003) have presented the integration of environmental requirements throughout the entire lifetime of a product. They presented throughout, the concept of an approach to product development based on paradigm for sustainable manufacturing. Four examples of methodologies and decision tools are discussed, representing the most important sources of environmental impacts of a product. The emphasis lies on the integrating concept rather than on the details of the methodologies. Masui et al. (Citation2003) have presented a methodology called quality function deployment for environment (QFDE) intended to be used in the early stages of product design. The proposed methodology by the authors incorporates the environmental aspects into QFDE to handle both traditional and environmental quality requirements. Maxwell and Vorst (Citation2003) have developed the concept of sustainable products as well as service development (SPSD) throughout the entire lifecycle of a product and/or service. It can be used to identify, assess and implement the options for optimum sustainability in the design and development of a product and/or service. Ijomah et al. (Citation2007) have presented a process of bringing used products to a ‘like-new’ functional state with warranty to match, which is being regarded as vital strategy in waste management and environmentally conscious management. The author has presented an outline of the elements of the remanufacturing concept to improve the robustness of design-for-remanufacturing. Bevilacqua, Ciarapica, and Giacchetta (Citation2007) have presented a methodology for integrating design for environment and Life Cycle Assessment (LCA) techniques, both into new product development and into the process of redesigning a set of existing product. The proposed methodology benefits the use of LCA data both during new product development and when modifying old products, with the aim of continuously reducing the overall environmental impact of products during their life cycle. Furthermore, Bovea and Wang (Citation2007) proposed a novel redesign approach that integrates QFD, LCA, Life Cycle Cost (LCC) and Contingent Valuation (CV). This approach identifies environmental improvement options and at the same time compares the increase that the incorporation of these options produces on the life cycle cost of the product, to the additional money that the customer is willing to pay for perceiving environmental benefits. A case study of office furniture redesign shows that redesigning products with a significant improvement in their sustainability without compromising other customer requirements is possible. To estimate customer willingness to pay (WTP) is crucial in product eco-design. Ljungberg (Citation2007) has reviewed current as well as present models in developing sustainable products. The author has reviewed LCA, environmental impact, eco-efficiency, eco-management and audit scheme. Rusinko (Citation2007) has presented an exploratory study of the relationship between specific environmentally sustainable manufacturing practices and specific competitive outcomes in a US commercial carpet industry. Chen and Wang (Citation2008) have presented CIMSMINER that combines data mining with Computer Integrated Manufacturing Systems (CIMS) and instructs its objectives, model, physical architecture and methods. Considering the characteristics of remanufacturing of automotive products, the CIMSMINER has been used to derive information concourse together and obtain data mining results to enable the improvement of products. Gehin, Zwolinski, and Brissaud (Citation2008) have presented a strategy called End of Life (EoL) to assess product EoL process, which would be profitable for an enterprise given the business model is in place. They integrated constraints from EoL strategies into early phases of design, which is one important aspect that needs to be improved by combining this idea with principles from concurrent engineering, to develop design aids which permits designers to compare their products to remanufacturable product profiles. Benedetto and Klemes (Citation2009) have presented an ‘Environmental Performance Strategy Map’ for LCA to analyse environmental impacts on a wide perspective with reference to a product system and the related environmental and economic impacts. This graphical map allows combing the main environmental indicators with the sustainable Environmental Performance Indicator as a single measure for sustainability of a given option so that comparison of different options for strategic decision-making purposes can be enhanced and facilitated with the use of this indicator. Sakao (Citation2009) proposed the application of quality engineering in the early phase of environmentally conscious design (Eco-design). The author has presented a framework for classification of environmental characteristics of products/services in two dimensions. The integration of the classification and the strategies are applied to three environmental characteristics against Japanese markets. Jayal et al. (Citation2010) reported many aspects of sustainability in the context of manufacturing and they have been investigated, particularly in recent years. For instance, modelling and optimization of challenges for sustainable manufacturing have been examined, considering the product, process and system levels. Ilgin and Gupta (Citation2010) have presented a state of art review of environmentally conscious product design, reverse and closed-loop supply chains, remanufacturing and disassembly. They have suggested that Environmentally Conscious Manufacturing (ECM) deals with green principles that are concerned with developing methods for manufacturing products from conceptual design to final delivery to consumers, and ultimately to the End of Life (EOL) disposal, that satisfies environmental standards and requirements. Vinodh (Citation2011) reports a case study in a manufacturing company in India. Sustainability analysis based on a CAD tool is conducted on the existing design of a sprocket for determining its environmental impacts in terms of carbon footprint, energy consumption and air/water usage. The analysis reveals critical design features with greater environmental impacts. Design optimization is then performed to produce design variants with lower impacts, validated by interviewing manufacturing executives in industry. This empirical study demonstrates the effectiveness of redesign for developing environment friendly products. Chu, Su, and Chen (Citation2011) presented an integrated framework for product designers to make environmental friendly decisions in consideration of the product design, manufacturing and the supply chain simultaneously. It incorporates a number of factors into the system design stage that ecologically influence product development activities. These factors, including component selection, assembly sequencing, assembly method, component merge and supplier selection, allow automatic variation of manufacturing BOM’s. The variation result is guaranteed to provide all product functions and to be interference-free during assembly. A computational framework was proposed to search for better BOM’s with minimized CO2 emission. A sample of bicycle design was tested to demonstrate the capability of the proposed framework. The test results show that the system design stage offers feasible means that can significantly improve impact of product development. Yung et al. (Citation2012) presented a case study to show how an LCA of a personal electronic product is conducted subject to the requirements of the EuP Directive. A commercial software tool, GaBi, was employed to determine the lifecycle inventory of a heart rate monitoring sensor. They reported that the bill of material (BOM) usually provides high-level information only and is not sufficient for a detailed LCA. There is a gap between the information that can be retrieved from the BOM or received from the manufacturer and the input interface to the software. Substantial effort was into filling this gap by transforming the information, gathered from factory visits and face-to-face meetings, into useful input from the software perspective. In this case study, material selection process, which occurs at the very beginning of the product, development cycle, is a dominant phase in reducing environmental impact. Several managerial insights are provided for implementing a proper eco-design strategy in a company. Cross-functional cooperation is of vital importance in success of eco-design product development, due to the complexity of the LCA in terms of its data collection and modelling. LCA modelling can, in fact, and should be reused so that the modelling effort is dramatically reduced when considering similar products. Top management also plays an important role in supporting the eco-design strategy as part of the company’s business strategy. Similar studies must be extended to other product types so that the derived insights could be made more generic.
2.2. Literature review on DFMA concept
Womack, Jones, and Roos (Citation1990) mentioned that because of competition in global markets for a large range of products, an ever increasing emphasis on shortening product development cycles has been seen as strategically and technologically imperative. In this context, the idea of concurrent engineering has gained popularity. Boothroyd and Dewhurst (Citation1991) narrated that DFM is a systematic methodology that will reduce manufacturing cost through reduction of overall parts of the product and redesign the parts, so that the product will be easy to handle and assemble. Boothroyd, Dewhurst, and Knight (Citation1994) mentioned that with the ever shrinking time available for developing new products and bringing them to global markets, companies have sought to ensure that their products could be easily manufactured and assembled. One of the development approaches broadly applied involves design for manufacturing/assembly (DFM/DFA) methods where products are systematically designed and evaluated to minimize setups during production operations, component counts and overall product complexity. By simplifying a product’s design to enhance component manufacturing and product assembly, production costs are reduced and unit quality improved. The benefits of applying DFMA are introduced by Ashley (Citation1995), who reports cases in which significant reduction in cost and lead time are accomplished by the use of this tool. Meeker and Rousmaniere (Citation1996) referred that DFMA has its roots in work that was started at the University of Massachusetts funded by the National Science Foundation (NSF) in 1977. DFMA has evolved over time to become a philosophy of optimizing the total product from the standpoint of assembly, part design and total life cycle cost. DFMA is a well established technique for accomplishing significant improvement of products through the application of a set of generic guidelines: Minimize part count, Encourage modular design, Design for top-down assembly, Minimize separate fasteners, Specify standard parts, Facilitate parts handling, Minimize reorientation at assembly, Minimize cables, Minimize final adjustments after assembly, Use self fastening parts, Use self locating parts, Accommodate process/part variation. By implementing DFMA in the concept design phase, significant cost reductions can be realized since again, 60–80% of the products cost will be fixed in this phase. The reduction in the number of parts simplifies the product. The majority of products can easily be further simplified. Kuo, Huang, and Zhang (Citation2001) discussed the importance of DFMA in product development by means of reduction of development and manufacturing costs and time-to-market. They also indicated the growing trend to include DFE in product development. In addition, the authors concluded that the best way to implement DFX, after encountering managerial resistance and interdisciplinary team conflict is through an intelligent expert system with an easy-to-use human interface. Kalpakjian and Schmid (Citation2001) mentioned that DFM is a systematic procedure to maximize the use of manufacturing processes in the design of components and DFA is a systematic procedure to maximize the use of components in the design of product. The aim of DFMA is to maximize the use of manufacturing processes and minimize the number of components in an assembly or product. Design decisions are responsible for up to 20% of the product cost (Boothroyd, Dewhurst, and Knight, Citation1994) and 80% of environmental damage (Otto and Wood Citation2001). Xie (Citation2003) mentioned that in order to survive and develop in the market, enterprises have to present their new product to the public rapidly and continuously with low price and high quality. Hundal (Citation2002) reported in a chapter on design methodologies for the environment and highlighted that designers must use their creativity in several different ways to come up with efficient “green” product designs for further generations. Fortunately, the designers have several tools (such as CAD/CAM and DFMA software) at their disposal. He also suggested that whenever possible the designers could attempt to incorporate a concurrent engineering philosophy (i.e. Just in time, DFMA, Design for disassembly, etc.) to aid the overall DFE effort.
Mendoza, Ahuett, and Molina (Citation2003) summarized the experiences gained during the application of Quality Function Deployment (QFD), Value Engineering (VE) and DFMA to five design case studies. The exercise was motivated by the need to establish a methodology that produces designs that are easy to assemble and manufacture, and that perform as needed. The focus of this work is that a process that integrates QFD, VE and DFMA can be use to optimize the product design by streamlining information and by providing a roadmap that guarantees the quality of proposed design. Kovalchuk and Junior (Citation2006) demonstrated the applicability of the concepts of DFMA and Concurrent Engineering in the development of product parts for the White Goods industry (major appliances as refrigerators, cookers and washing machines), indicating one case regarding the development and release of a product. Finally, it is demonstrated in a short term how a solution was developed that could provide cost savings and time reduction to product delivery using those techniques. The main goal of current DFMA approaches is to obtain a product with a high level of manufacturability. The present problem of global warming is a challenging one for the manufacturing industries. Estorilio and Simiao (Citation2006) presented a study of manufacture and assembly costs reduction in a diesel engine model manufactured in an industry situated in Curitiba that intends to make the engine economically feasible and also the study presented a brief literature review on product development and technological resources to support product design, emphasizing a review on DFMA method. Paramasivam and Senthil (Citation2009) say that DFM and DFA are most of the time considered simultaneously as DFMA. But they have conflict nature between them. DFMA is important for design because it has three beneficial impacts. First and foremost, it reduces part count and also reduces cost and time. Chowdary and Harris (Citation2009) have reported that the integration of DFMA and DFE methodologies can be beneficial to organizations involved in the design and development of products and presented a case study. This paper presents the integration of DFMA and DFE with product design and development tools such as research analysis and QFD. The case study involved is a desktop organizer designed to increase workspace available on a desk. Solidworks was used to generate CAD models which were further analysed using Simapro 7 Demo software for DFE and Excel for DFMA principles. Besides, the concept that was developed with the DFMA and DFE methodologies showed significant reductions in cost, material assembly time, eco-indicator 99 values and the number of parts.
The research gap observed based on the literature review is that though many researchers have contributed sustainable product development, DFE and DFMA approaches, very few researchers attempted to the best of our knowledge from the viewpoint of utilizing CAD and DFMA for sustainable product development. Moreover, when the sustainability analysis is conducted in the CAD environment at the early design stage, it enables the determination of the environmental impact of a product in an effective manner. Thus, the integration of DFE and DFMA leads to varied benefits ranging from improvement in product design and development, reduction of cost and product development time, generation of robust products, minimizing the environmental impact, etc. In this context, this research project has been carried out.
3. Research methodology
The methodology followed during this project is shown in Figure . The project starts with the review on DFE, sustainability and DFMA principles. Then the candidate product has been chosen as the alternator pulley. Then, the CAD modelling of existing model and proposed model has been performed. The conceptual design changes developed on the proposed product by implementing the DFMA concept, the proposed product designs have reduced manufacturing cost and ease of assembly with reduction in weight. This is followed by the conduct of sustainability analysis of existing model and proposed model. The environmental impact of pulley has been measured and compared.
4. Case study
This section presents the details about the candidate product, CAD modelling, stress analysis and sustainability analysis of pulley model.
4.1. About the case component and background details
The case study has been carried out in an automotive component. For a successful operation of automobiles, there are several parts behind it like cylinder, piston, piston ring, valves, crank shaft, connecting rod, alternator, alternator pulley, cooling system, battery, etc... In this research project, an alternator pulley is selected as a candidate product.
An alternator is a device that converts mechanical energy into electrical energy. A pulley is a wheel on an axle that is designed to support movement of a cable or belt along its circumference. Pulleys are used in a variety of ways to lift loads, apply forces and to transmit power. A pulley is also called a sheave or drums and may have a groove between two flanges around its circumferences. In this way an alternator pulley is used in modern cars. The location of the charge alternator pulley is shown in Figure . Generally an alternator produces more amperage when it spins faster to its maximum capacity. Most of them need the best output at low speed. If the alternator pulley has the longer diameter, then the alternator will not produce as much power because it is turning slow during idling time of engine. So we have to boost the output at lower RPM. Based on this aspect, the candidate product geometry modified using DFMA concepts and sustainability of the product has been improved. There existed a need for the organization to minimize environmental impact in the design and development of alternator pulley. In this context, this study has been initiated.
4.2. CAD and stress analysis
After collecting the two-dimensional drawing of the pulley from automotive company, the solid model of the existing pulley has been created using Pro/Engineer software package. Such developed existing pulley model is shown in Figure .
After modelling the existing pulley, stress analysis of existing pulley has been done using ANSYS software package and shown in Figures and , respectively. After engineering analysis of existing pulley design, the geometrical modification is carried on the proposed pulley for the purpose of ease in manufacturing and ease of assembly using DFMA methodologies. Then the proposed model was developed to reduce the weight of the pulley and their production cost using DFMA concept. This solid model of the proposed pulley has been created using Pro/Engineer software package. Such developed proposed pulley model is shown in 3D in Figure . Later, Stress analysis of proposed pulley has been done using ANSYS software package and shown in Figures and . After engineering analysis of proposed pulley design, design optimization has been performed to determine the optimized design parameters using DFMA methodologies.
4.2.1. Stress analysis of existing alternator pulley model (D1)
Stress analysis such as total deformation and equivalent stress has been done on the existing pulley model (D1) and the output is shown in Figures and .
4.2.2. Stress analysis of proposed alternator pulley model (D2)
Stress analysis of proposed pulley (D2) such as total deformation and equivalent stress has been done and the output is shown in Figures and .
4.3. Sustainability analysis
The sustainability analysis has been carried out using sustainability module of Solid Works software package. The package is embedded with algorithms that screen the CAD models of products to generate the various environmental impact parameters. The inputs to the package include design in the form of CAD model, material, manufacturing process, locations of manufacture and distribution. The output is the environmental impact that has been measured in terms of carbon footprint, air acidification, total energy consumed and water eutrophification. The existing material of pulley has been specified as cast alloy steel. The volume, surface area and weight are computed. The proposed pulley material is aluminium. The manufacturing process has been specified as CNC machining. Figure shows the results of sustainability analysis of existing design (D1) using the cast alloy steel material and Figure shows the results of the sustainability analysis for the proposed design (D2) using aluminium alloy material. Four important environmental parameters considered in this study are carbon footprint, air acidification, total energy consumed and water eutrophication.
Figure 9. Results of sustainability analysis of existing charge alternator pulley using cast alloy steel (D1).
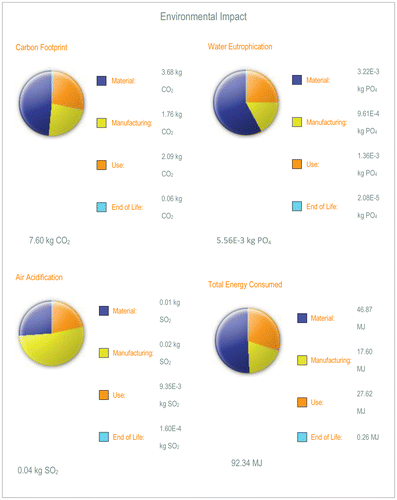
Figure 10. Results of sustainability analysis of proposed charge alternator pulley using aluminium alloy (D2).
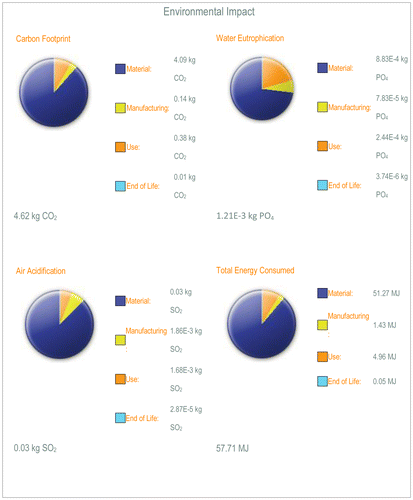
The results of the sustainability analysis indicated that the proposed models (D2) possess minimal environmental impact compared to existing model (D1).
5. Results and discussion
Sustainability analysis measures the environmental impact over the life cycle of pulley in terms of carbon footprint, air acidification, total energy consumed and water eutrophication.
The comparison of results of environmental impact of baseline and proposed pulley model are highlighted in Table in terms of carbon footprint, water eutrophication, air acidification and total energy consumed and corresponding values of environmental impact minimization percentages are 39.21, 78.24, 25 and 37.50. Moreover, the total environmental impact minimization percentage of product as minimized to 45% with this approach. From Table , it has been found that the proposed models are found to possess minimal environmental impact.
Table 1. Comparison of the results of environmental impact of baseline and proposed pulley model.
Figure depicts the carbon footprint, water eutrophication, air acidification and total energy consumed for different phases of life cycle such as material procurement, product manufacturing, product use and End of Life. The reduction in environmental impact parameters across various lifecycle phases is shown in Table . Moreover, from Table , the total life cycle phases percentages based on the environmental impact are calculated as -36.98, 91.61, 81.98 and 82.04. As shown, the carbon footprint, water eutrophication, air acidification and total energy consumed have been reduced in the proposed design when compared to the baseline design. Figure shows a comparative graph depicting the environmental impact reduction percentage of existing and proposed product designs.
Figure 11. Comparison of environmental impact among the baseline and new design of charge alternator pulley across the life cycle.
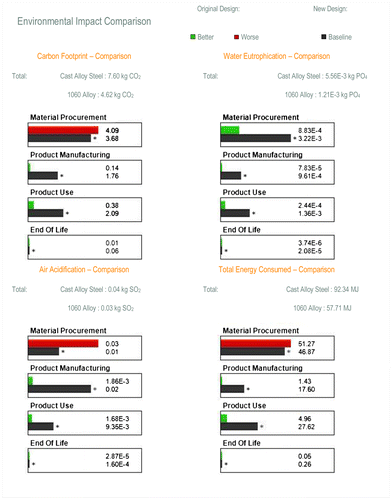
Table 2. Environmental impact comparison for the existing and redesigned designs of pulley across various lifecycle phases.
Based on the conduct of study, it can be inferred that the integration of DFE, sustainability and DFMA concepts enable the development of sustainable alternator pulley. The conduct of sustainability analysis in a virtual CAD environment facilitated the redesign of the product, making the product more eco-friendly. By this method and appropriate design modifications, the environmental impact has been reduced. This method making the design was found to be sustainable.
5.1. Industrial implications
This method facilitates to evaluate the environmental impact of the product at the early design stage. The case study has been conducted with the objective of ensuring sustainable product design by the integration of DFE, sustainability and DFMA concepts using CAD and ANSYS. Various variables considered in the study include ergonomics, functionality and environmental impact. This study has resulted in the remarkable minimization of environmental impact. The redesigned product has been further subjected to design studies. Thus, this study has addressed the three perspectives namely environmental, social and economic sustainability improvements. Besides, such type of solutions are already available in the market, this integrated approach helps the designer to derive effective solution to develop environmentally conscious design quickly and can achieve business benefits such as reduced cost and time to improve business profitability. Moreover, Winston Knight and Boothroyd Dewhurst addressed (DFMA Citation2009) about DFMA software that
Manufacturers are increasingly aware that addressing the environmental impact of their products will soon be a requirement for entry into major markets. Designers can now select best materials for greener products, even as they innovate with DFMA to build more performance into efficient, leaner designs.
6. Conclusions
The new trends in manufacturing organizations are focused on developing environment friendly products. The alternator pulley has been modeled using CAD model and sustainability analysis has been carried out. Sustainability analysis measures the environmental impact over the life cycle of handle in terms of carbon footprint, air acidification, total energy consumed and water eutrophication. This is followed by the geometrical modification carried on the proposed pulley for the purpose of ease in manufacturing and assembly using DFMA concept. After incorporating the dimensional changes in the proposed pulley, the environmental impact on proposed pulley design has been reduced which leads to the inference that CAD and ANSYS would enable the attainment of sustainability in product design. The results of the sustainability analysis indicated that the proposed alternator pulley is found to possess minimal environmental impact. The results of the case study indicated that there is an improvement in product development using this integrated approach. In this design, DFE, DFMA and sustainability were integrated using the CAD and ANSYS to create a sustainable product.
6.1. Limitations and future research direction
The sustainability analysis has been carried out for a single product and for a single manufacturing organization. In this paper, integration of DFE, sustainability and DFMA concepts alone have been carried out for the development of single product. In future, a large number of case studies should be conducted for several products across a range of manufacturing organizations. The proposed model could also be subjected to design and shape optimization in future.
Acknowledgements
The work reported in this paper was supported by Sustainable Product Design Laboratory, Department of Production Engineering, National Institute of Technology, Tiruchirappalli, Tamilnadu, India towards the execution of sustainability analysis on existing and proposed products.
Disclosure statement
No potential conflict of interest was reported by the authors.
References
- Ashley, S. 1995. “Cutting Costs and Time with DFMA.” Mechanical Engineering 117 (3): 74–77. Accessed 29 August 2015. http://web.mit.edu/meeker/Public/CuttingtimeandcostwithDFMA.pdf
- Benedetto, L. D., and J. Klemes. 2009. “The Environmental Performance Strategy, Map: An Integrated LCA Approach to Support the Strategic Decision-Making Process.” Journal of Cleaner Production 17 (10): 900–906. doi:10.1016/j.jclepro.2009.02.012.
- Bevilacqua, M., F. E. Ciarapica, and G. Giacchetta. 2007. “Development of a Sustainable Product Lifecycle in Manufacturing Firms: A Case Study.” International Journal on Production Research 45 (18–19): 4073–4098. doi:10.1080/00207540701439941.
- Boothroyd, G., and P. Dewhurst. 1991. Product Design for Assembly. 1st ed. Wakerfield, USA: Boothroyd Dewhurst.
- Boothroyd, G., P. Dewhurst, and W. Knight. 1994. Product Design for Manufacture and Assembly. New York: Marcel Dekker.
- Bovea, M. D., and B. Wang. 2007. “Redesign Methodology for Developing Environmentally Conscious Products.” Journal of Production Research 45 (18–19): 4057–4072. doi:10.1080/00207540701472678.
- Bras, B. 1997. “Incorporating Environmental Issues in Product Design and Realization.” Industry and Environment, 20 (1–2): 1–19. http://www.srl.gatech.edu/education/ME4171/UNEP-IE-paper.pdf
- Chen, K., and J. Wang. 2008. “The Data Mining Technology Based on CIMS and Its Application on Automotive Remanufacturing.” International Workshop on Knowledge Discovery and Data Mining 2008: 48–52. doi:10.1109/WKDD.2008.125.
- Chowdary, B. V., and A. Harris. 2009. “Integration of DFMA and DFE for Development of a Product Concept: A Case Study.” Proceedings of Seventh Latin American and Caribbean Conference for Engineering and Technology, June 2–5, San Cristobal, Venezuela. http://www.laccei.org/LACCEI2009-Venezuela/p65.pdf
- Chu, C. H., J. C. P. Su, and Y. T. Chen. 2011. “An Integrated Approach to Sustainable Product Development at the System Design Stage.” Proceedings of CIRP Design Conference, 1–8
- DFMA, 2009. “New DFMA 2009 Software from Boothroyd Dewhurst Targets Environmental Compliance.” Accessed August 29, 2015. http://www.dfma.com/news/dfma2009.htm
- Estorilio, C., and M. C. Simiao 2006. “Cost Reduction of a Diesel Engine Using the DFMA Method.” Product: Management & Development, 4 (2): 95–103. http://pmd.hostcentral.com.br/revistas/vol_04/nr_2/v4n2a4205.pdf
- Gehin, A., P. Zwolinski, and D. Brissaud. 2008. “A Tool to Implement Sustainable End-of-Life Strategies in the Product Development Phase.” Journal of Cleaner Production 16 (5): 566–576. doi:10.1016/j.jclepro.2007.02.012.
- Gungor, A., and S. M. Gupta. 1999. “Issues in Environmentally Conscious Manufacturing and Product Recovery: A Survey.” Computers & Industrial Engineering 36: 811–853. doi:10.1016/S0360-8352(99)00167-9.
- Hundal, M. S. 2002. Mechanical Life Cycle Handbook: Good Environmental Design and Manufacturing. New York: Marcel Dekker. ISBN: 0-8247-0572-6.
- Ijomah, W. L., C. A. McMahon, G. P. Hammond, and S. T. Newman. 2007. “Development of Robust Design-for-Remanufacturing Guidelines to Further the Aims of Sustainable Development.” International Journal of Production Research 45 (18–19): 4513–4536. doi:10.1080/00207540701450138.
- Ilgin, M. A., and S. M. Gupta. 2010. “Environmentally Conscious Manufacturing and Product Recovery (ECMPRO): a Review of the State of the Art.” Journal of Environmental Management 91: 563–591. doi:10.1016/j.jenvman.2009.09.037.
- Jayal, A. D., F. Badurdeen, O. W. Dillon Jr, and I. S. Jawahir. 2010. “Sustainable Manufacturing: Modeling and Optimization Challenges at the Product, Process and System Levels.” CIRP Journal of Manufacturing Science and Technology 2: 144–152. doi:10.1016/j.cirpj.2010.03.006.
- Kaebernick, H., S. Kara, and M. Sun. 2003. “Sustainable Product Development and Manufacturing by Considering Environmental Requirements.” Robotics and Computer Integrated Manufacturing 19: 461–468. doi:10.1016/S0736-5845(03)00056-5.
- Kalpakjian, S., and S. R. Schmid. 2001. Manufacturing Engineering and Technology. 4th ed. Upper Saddle River, New Jersey: Prentice Hall.
- Kovalchuk, J. P. B., and O. C. Junior 2006. “DFMA Application on the Development of Parts for the White Goods Industry – A Case Study.” Third International Conference on Production Research, America’s Region 2006 (ICPR-AM06).
- Kuo, T.-C., S. H. Huang, and H. C. Zhang. 2001. “Design for Manufacture and Design for ‘X’: Concepts, Applications, and Perspectives.” Computers & Industrial Engineering 41 (3): 241–260. doi:10.1016/S0360-8352(01)00045-6.
- Ljungberg, L. Y. 2007. “Materials Selection and Design for Development of Sustainable Products.” Materials and Design 28 (2): 466–479. doi:10.1016/j.matdes.2005.09.006.
- Masui, K., T. Sakao, M. Kobayashi, and A. Inaba. 2003. “Applying Quality Function Deployment to Environmentally Conscious Design.” International Journal of Quality and Reliability Management 20 (1): 90–106. doi:10.1108/02656710310453836.
- Maxwell, D., and R. van der Vorst. 2003. “Developing Sustainable Products and Services.” Journal of Cleaner Production 11 (8): 883–895. doi:10.1016/S0959-6526(02)00164-6.
- Meeker, D. G. and A. Rousmaniere. 1996. “DFMA and Its Role in the Integrated Product Development Process.” Accessed 29 August 2015. http://web.mit.edu/meeker/Public/DFMAandIPDP.pdf
- Mendoza, N., H. Ahuett, and A. Molina. 2003. “Case Studies in the Integration of QFD, VE and DFMA during the Product Design Stage” Proceedings of the 9th International Conference of Concurrent Enterprising, Espoo, Finland, 16–18, June 2003.
- Otto, K., and K. Wood. 2001. Product Design: Techniques in Reverse Engineering and New Product Development. Upper Saddle River, New Jersey: Prentice Hall.
- Paramasivam, V., and V. Senthil. 2009. “Analysis and Evaluation of Product Design through Design Aspects Using Digraph and Matrix Approach.” International Journal on Interactive Design and Manufacturing 3: 13–23. doi:10.1007/s12008-009-0057-9.
- Rusinko, C. A. 2007. “Green Manufacturing: An Evaluation of Environmentally Sustainable Manufacturing Practices and Their Impact on Competitive Outcomes.” IEEE Transactions on Engineering Management 54 (3): 445–454. doi:10.1109/TEM.2007.900806.
- Sakao, T. 2009. “Quality Engineering for Early Stage of Environmentally Conscious Design.” The TQM Journal 21 (2): 182–193. doi:10.1108/17542730910938164.
- Senthilkumaran, D., S. K. Ong, B. H. Tan, and A. Y. C. Nee. 2001. “Environmental Life Cycle Cost Analysis of Products.” Environmental Management and Health 12 (3): 260–276. doi:10.1108/09566160110392335.
- Vinodh, S. 2011. “Sustainable Design of Sprocket Using CAD and Design Optimization.” Environment, Development and Sustainability 13 (5): 939–951. doi:10.1007/s10668-011-9299-3.
- Womack, J.P., D.T. Jones, and D Roos. 1990. The Machine That Changed the World. New York, NY: Rawson Associates.
- Xie, X. 2003. “Design for Manufacture and Assembly” Department. of Mechanical Engineering, University of Utah. http://home.utah.edu/~u0324774/pdf/DFMA.pdf
- Yung, W. K. C., H. K. Chan, D. W. C. Wong, J. H. T. So, A. C. K. Choi, and T. M. Yue. 2012. “Eco-Redesign of a Electronic Product Subject to the Energy-Using Product Directive.” International Journal of Production Research 50 (5): 1411–1423. doi:10.1080/00207543.2011.571941.