Abstract
Increased petroleum prices, increased threat to the environment from exhaust emissions and global warming have generated intense international interest in developing renewable and alternative non-petroleum fuels for internal combustion engines. Evolving suitable technology for addressing energy crisis creates a continued investigation into the search for sustainable and clean-burning renewable fuels. This work investigates suitability of different non-edible-derived biodiesels such as cotton seed oil methyl ester (COME), Honne oil methyl ester (HnOME) and Rubber seed oil methyl ester (RuOME) to four stroke, single cylinder compression ignition (CI) engine. Engine tests were conducted to study the effect of fuel blending, thermal barrier coating (TBC) or Low Heat Rejection (LHR) and injector nozzle geometry on the performance, combustion and emission characteristics of COME, HnOME and RuOME in the modified CI engine. Blends of biodiesels with diesel were varied from 20 to 80% in steps of 20%. Two thermal barrier coatings of partially stabilized zirconium (PSZ) and aluminium oxide (Al2O3) were provided on the engine to make it fully adiabatic. Nozzle injectors of 3, 4 and 5 holes, with size of orifice varied from 0.2 to 0.3 mm size were selected for the study. It was concluded that B20 biodiesel blend, PSZ-coated engine and four hole nozzle injector of 0.2 mm size resulted in overall better engine performance with increased brake thermal efficiency (BTE) and reduced HC, CO, smoke emissions for the fuel combinations tested. Combustion analysis to study the effect of biodiesel blends, LHR coatings, injector nozzle geometry on the performance of the biodiesel-fuelled engine has been presented to give more insight into the behaviour of operation.
1. Introduction
All nations in the world are confronted with the problem of energy shortage. There is an ever increasing demand for energy in the industrial, transport and domestic sectors. Sustainable source of energy is essential for economic and social development. The existing energy sources of energy from fossil fuels may not be adequate to meet the ever increasing energy demands. The diminishing and continuous increasing cost of petroleum resources associated with their alarming pollution levels from diesel engines has caused an interest in finding renewable, alternative and sustainable fuels to fossil diesel. India’s share in global oil reserves is about 0.5%, whereas its share in global consumption is about 3%. India ranks amongst the top 10 largest oil-consuming countries importing about 70% of its oil needs. The total oil consumption of our country is about 2.5 to 2.8 million barrels per day. The demand for fossil fuel will rise higher and higher with every passing decade and is expected to reach an amount of nearly 250 million ton by the year 2024. In view of this, to reduce the huge amount of import bill of crude oil and become a self reliance in energy sector, India has initiated renewable energy sources like solar, vegetable oil, firewood and so on for quite long use (Agarwal and Agarwal Citation2007).
Renewable fuels have advantages in terms of their renewability, biodegradability, energy security, environmental concerns, foreign exchange savings and socio-economic issues compared to fossil fuels. The use of renewable energy from non-edible oils reduces the green house gas emissions and gives better food and energy security to the nation and ensures sustainable development. Therefore, renewable fuels such as biofuels can be used predominantly as fuel for both transportation and power generation sectors (Atadashi, Aroua, and Abdul Aziz Citation2010; Basha, Raja Gopal, and Jebaraj Citation2009).
A number of vegetable oils have been used for biodiesel production and their use in diesel engine applications. These include biodiesels derived from jatropha, honge (karanja), honne, palm, rubber seed, rape seed, mahua and neem seed oils (Banapurmath et al. Citation2008a; Karnwal et al. Citation2010; Morshed et al. Citation2011; Onga et al. Citation2011; Ramadhas, Jayaraj, and Muraleedharan Citation2005; Sahoo et al. Citation2007; Yang et al. Citation2011). Biodiesel is a clean burning alternative fuel, produced from domestic, renewable resources. Biodiesel is simple to use, biodegradable, non-toxic and essentially free of sulphur and aromatics. Biodiesel improves lubricity and reduces premature wearing of fuel pumps. Vegetable oil blends can be used in the existing diesel engines without modifications. Blending vegetable oils with diesel is a simple process and results in significant improvement in their physical properties. The properties such as viscosity and density are considerably reduced and volatility is also improved. Many researchers have tried varying proportions of vegetable oils in diesel (Banapurmath et al. Citation2008; Martin and Geo Citation2011; Sahoo et al. Citation2009). Results obtained from the experiments on a direct Injection diesel engine using a blend of vegetable oil and diesel showed improved brake thermal efficiency and reduced exhaust smoke emissions than neat vegetable oils.
Feasibility of COME and their blends in diesel engine applications has been reported by several researchers. Lower CO, CO2, NOx, smoke emissions and lower brake thermal efficiency with COME and their blends operation compared to diesel fuel operation has been reported (Nabi, Rahman, and Akhter Citation2009; Naga et al. Citation2010). Lower and medium percentages of COME can partially be substituted to the diesel fuel without any modifications in diesel engine (Aydin and Bayindir 2010; Martin and Geo Citation2011). The effects of using neat cottonseed oil or its neat ME (methyl ester) bio-diesel, on the combustion behaviour of a standard, high speed, direct injection (HSDI) has been reported (Rakopoulos et al. Citation2010). It is reported that ignition delay was not much affected, the fuel injection pressure diagrams were very slightly advanced accompanied with higher injection pressures, maximum cylinder pressures remained the same with the vegetable oil and slightly increased with the biodiesel, and the cyclic irregularity was not affected with the biofuels remaining at the acceptable levels (Rakopoulos et al. Citation2010). With HOME or Karanja biodiesel and their blends operation higher CO, NOx, smoke emissions and lower brake thermal efficiency compared to diesel fuel operation has been reported (Banapurmath et al. Citation2008). The major drawback of biodiesel usage is its higher viscosity (nearly twice its counterpart diesel fuel) and lower volatility. Use of adiabatic engines is one solution to effectively combust the biodiesels in the diesel engines. Many studies using adiabatic or low heat rejection (LHR) concept in standard diesel engines using biodiesel has been reported in the literature (Agarwal and Agarwal Citation2007; Ahmaniemi et al. Citation2004; Amman Citation1988; Banapurmath et al. Citation2008; Ekrem, Tahsin, and Muhammet Citation2006; Jaichandar and Tamilporai Citation2003). Various thermal barrier coatings of silicon carbide, silicon nitride, aluminium titanate, aluminium magnesium silicate and ceramic such as aluminium oxide, partially stablilized zerconia (PSZ) have been used. PSZ has been found to be quite desirable for adiabatic engine applications. This is because of its excellent insulating characteristics, strength and thermal expansion characteristics. They are coated on piston, cylinder head, cylinder liner and inlet and exhaust valves. The coating thickness varies from 1 to 2 mm. Some important advantages of coated LHR engines are their improved fuel economy, reduced engine noise and multi-fuel capability using low cetane fuels of biodiesels (Agarwal and Agarwal Citation2007; Ahmaniemi et al. Citation2004; Banapurmath et al. Citation2008). A large number of studies on the performance, structure and durability of the LHR engine have also been carried out. The results of the investigations have been contradictory in nature. Most of them have concluded that insulation reduces heat transfer, improves thermal efficiency and reduces exhaust emissions. However, some experimental studies have indicated almost no improvement in thermal efficiency and claim that exhaust emissions deteriorate when compared with conventional diesel engines.
In the present work, the engine combustion chamber elements such as piston, cylinder head and valve faces are provided with two types of thermal barrier coatings such as PSZ and Al2O3. Engine performance and emission characteristics were then studied with these two coatings as well as with normal uncoated engine when fuelled with biodiesels derived from cotton seed, honne and rubber seed oils. Many researchers have performed the tests on compression ignition (CI) engine with different vegetable oils at different injection pressures and injection timings (Gajendra Babu Citation2007). Changes in injection timings change the position of the piston and cylinder pressure and temperature at the injection. Retarded injection timings showed significant reduction in diesel NOx and biodiesel NOx (Hountalas et al. Citation2001; Tao et al. Citation2005). Cylinder pressures and temperatures gradually decrease when injection timings are retarded (Roy Citation2009). The effect of fuel injection timing with waste cooking oil as fuel in direct injection diesel engine with advanced injection timing by 40 BTDC better efficiency, reduced CO and higher NO emissions has reported (Bari, Yu, and Lim Citation2004). Some investigators have performed experiments on CI engine with different vegetable oils at different injection pressures (Bakar and Ismail Citation2008; Puhan et al. Citation2009). Better performance, higher peak cylinder pressure and temperature were observed at increased injection pressure (Bakar and Ismail Citation2008; Roy Citation2009) Effect of number of injector holes on the performance of diesel engine operated on different biodiesels has been reported by the same authors (Suresh, Kamath, and Banapurmath et al. Citation2014).
2. Properties of test fuels
Honne and rubber seed oils of non-edible nature and cotton seed oil (both edible and non-edible nature) were selected for the study. These oils were transesterified to obtain their respective biodiesel. The properties of diesel, non-edible oils and their respective biodiesel were measured and are shown in Table .
Table 1. Properties of fuels used.
3. Heat release rate calculation
The heat release rate at each crank angle was calculated using a first law analysis of the average pressure versus crank angle variation obtained from 100 cycles using the following expression given below:(1)
where Qapp,-apparent heat release rate (J); γ,-ratio of specific heats Cp/(Cp – ); R, gas constant in (J/kmol – K); Cp-specific heat at constant pressure (J/kmol – K); V, instantaneous volume of the cylinder (m3); P, cylinder pressure (bar), Qwall, heat transfer to the wall (J)
4. Experimenta set-up
Overall view of the experimental set-up is shown in Figure . The engine tests were conducted on a four stroke single cylinder direct injection water-cooled compression ignition (CI) engine. The specifications of the engine are given in Table . The engine was operated at a rated speed of 1500 rev/min. The engine was having a conventional fuel injection system. As per manufacturers specification the injection nozzle used for diesel have three holes of 0.3 mm diameter with a spray angle of 120° apart following an injector opening pressure of 205 bar along with static injection timing 23° before top dead centre (BTDC). The nozzle used for biodiesel have four holes of 0.3 mm diameter with spray angle of 90° apart following an injector opening pressure of 230 bar along with static injection timing of 19° BTDC . There was no special arrangement to control the engine speed; the regular governor of the engine was used to control the engine speed. The engine had been provided with a hemispherical combustion chamber with overhead valves operated through push rods. Cooling of the engine was accomplished by circulating water through the jackets of the engine block and cylinder head. Experiments were conducted under a thermal steady-state condition of the engine with an inlet cooling water temperature of 80 °C. A piezoelectric pressure transducer was mounted flush with the cylinder head surface to measure the cylinder pressure.
Figure 1. Overall view of the experimental set-up with EGR arrangement. 1 – control panel, 2 – computer system, 3 – diesel flow line, 4 – air flow line, 5 – calorimeter, 6 – exhaust gas analyzer, 7 – smoke meter, 8 – rotameter, 9, 11– inlet water temperature, 10 – calorimeter inlet water temperature,12 – calorimeter outlet water temperature, 13 – dynamometer, 14 – CI engine, 15 – speed measurement,16 – burette for fuel measurement, 17 – exhaust gas outlet, 18 – outlet water temperature, T1– inlet water temperature, T2 – outlet water temperature, T3 – exhaust gas temperature.
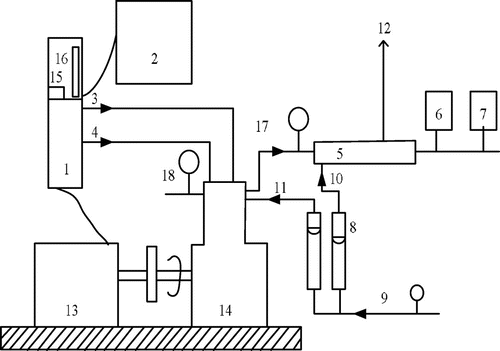
Table 2. Specifications of the engine.
The exhaust gas emissions were measured using an exhaust gas analyser. Figures and show the piston and cylinder head coated with PSZ and Al2O3 to obtain an LHR engine.
All measurements were done when engine was attained steady state. For each load, five readings were generated to ensure accuracy of the data recorded and careful experimental arrangements were made to make it possible to obtain consistent and repeatable measurements. In order to reduce the error in the measurement of emissions, five readings were recorded and only their averages are presented in the graphs. The uncertainty of the measured parameters was estimated with confidence limits of ±2σ (95.45% of the measured data lie within the limits of ±2σ around the mean). The percentage uncertainty of the measured parameters was estimated using the following relation:
5. Results and discussions
Experiments were conducted on direct injection compression ignition engine in three different phases. The first phase involves fuel modification of three selected non-edible oils in the form of their respective biodiesel production and subsequent blending with diesel in different proportions. In next phase, engine is provided with PSZ and Al2O3 ceramic coatings. Base line readings were also generated with existing uncoated diesel engine for the comparative study. The engine was fuelled with COME, HnOME and RuOME in both versions of coated and normal diesel engine operation. In the final phase, different injectors with varying number of holes have been considered for studying their effect on the biodiesel-fuelled engines.
5.1. Effect of blend on performance of the engine
This section describes the effect of blending three non-edible derived biodiesels with diesel in different proportions on the performance, emission and combustion characteristics of the diesel engine. The engine is operated on biodiesels of COME, HnOME and ROME and their blends of diesel under variable load conditions and compared with diesel engine performance. Injection timing of 23° BTDC, compression ratio of 17.5 and injection pressure of 205 bar has been selected for the engine operation. B100 operation refers to optimized engine conditions with IOP of 230 bar, IT of 19° BTDC and injector with four holes. While all other blends run with diesel engine conditions of IOP of 205 bar, IT of 23° BTDC and injector with three holes.
5.1.1. Performance parameters
The effect of brake power on brake thermal efficiency for respective biodiesel and their blends with diesel is shown in Figure . There is a steady increase in efficiency as load increases. The brake thermal efficiency with B20 blend operation of three biodiesels is closer to diesel operation. Further increase in proportion of respective biodiesels in the blend, brake thermal efficiency decreased. This drop in thermal efficiency with increase in proportion of biodiesels or esters can be attributed to the poor combustion characteristics of the blends considered. Their relatively high viscosity and poor volatility characteristics overcomes the excess oxygen present in the biodiesel. The B20 blend of HnOME (BHnOME20) showed better performance when compared to that of COME (BCOME20) and RuOME (BRuOME20). Diesel being common the properties of the respective biodiesel are obviously responsible for this behaviour. The maximum brake thermal efficiency value observed with BHnOME20, BCOME20 and BRuOME20 operation was 26.55, 26 and 25.00% at 80% load compared to 27.57% with diesel.
5.1.2. Emissions
The effect of brake power on smoke emission for respective biodiesel and their blends with diesel is shown in Figure . It is seen that the smoke opacity increases with increase in brake power for diesel, for respective biodiesel and their blends with diesel. As the percentage of biodiesel increases in the blend with diesel the smoke opacity increases. The increased smoke emission with biodiesel blends could be attributed to increased viscosity of the blends that result in poor spray pattern thereby leading to poor combustion. The reduction in smoke emissions with biodiesel blends could be due to increase in excess air ratio because of the oxygen present in the fuel itself. The B20 blend of HnOME (BHnOME20) showed lower smoke opacity when compared to that of COME (BCOME20) and RuOME (BRuOME20). Diesel being common the properties of the respective biodiesel are obviously responsible for this behaviour. The smoke level with BHnOME20, BCOME20 and BRuOME20 operation was 59, 65 and 68 ppm at 80% load compared to 53 ppm with diesel.
Figure shows the effect of brake power on nitric oxide (NOx) emission for respective biodiesel and their blends with diesel. It is observed from figure that the NOx emission increases with the increase in load for all the fuel combinations. Further it follows that biodiesel and their blends show lower NOx emission compared to standard diesel operation. This reduction in NOx emission is mainly associated with reduced premixed burning rate following the delay period. It may be noted that the rate of heat release during the premixed burning phase is lower with biodiesel and their blends as compared to diesel even though the ignition delay was higher as seen in Figure . As the blend ratio increases lower heat release rates are observed.
The B20 blend of HnOME (BHnOME20) showed higher NOX emissions when compared to that of COME (BCOME20) and RuOME (BRuOME20). Diesel being common the properties of the respective biodiesel are obviously responsible for this behaviour.
The NO emissions with BHnOME20, BCOME20 and BRuOME20 operation were 784, 772 and 770 ppm at 80% load compared to 790 ppm with diesel.
5.2. Effect of LHR on the performance of the engine
Figure shows the effect of thermal barrier coatings (TBC) of PSZ on BTE with brake power for the three different biodiesels. The biodiesel performance improved due to the reduced heat transfer rate with coated engine compared to normal engine operation. However, coating being common, type of biodiesel plays an important role in the behaviour and accordingly HnOME resulted in higher brake thermal efficiency compared to COME and RuOME. The brake thermal efficiency with PSZ coating were 26.55, 26.0 and 25.5%, respectively, for HnOME, COME and RuOME compared to 27.57% diesel operation at 80% load.
5.2.1. Smoke opacity
Effect of TBC of PSZ on smoke opacity with brake power for different biodiesels is shown in Figure . Coating of the ceramic elements on the combustion chamber increases in-cylinder soot oxidation due to higher surface temperature resulting in improved combustion efficiency. PSZ being a common ceramic material, type of biodiesel injected resulted in the behaviour shown. Accordingly, RuOME resulted in lower efficiency compared to COME and HnOME. The smoke levels were 60, 65 and 70 HSU for HnOME + LHR (PSZ), COME + LHR (PSZ) and RuOME + LHR (PSZ) compared to 53 HSU diesel operations, respectively, at 80% load.
5.2.2. Nitric oxide emission
Effect of TBC of PSZ on NOx with brake power for the three biodiesels used is shown in Figure . Lower NOX emissions were observed in normal engine compared to TBC engine. Increased after combustion temperature causes an increase in NOX emission compared to uncoated engine. Factors facilitating and accelerating the reaction between oxygen and nitrogen, increases the NOX formation. PSZ being a common ceramic material, type of biodiesel injected results in the behaviour shown. Accordingly, HnOME results in higher NOX emission compared to COME and RuOME.
The NOx levels were 1240, 1080 and 890 ppm for HnOME + LHR (PSZ), COME + LHR (PSZ) and RuOME + LHR (PSZ), respectively, compared to 1310 ppm diesel operation, respectively, at 80% load.
5.3. Effect of nozzle injector geometry on the performance of the engine
The injector opening pressures were varied from 205 bar and 210–240 bar (21.0–24.0 MPa) in steps of 10 bar. Two hundred and thirty bar was found to be optimum for all the biodiesels tested. Initially different nozzles with 3, 4 and 5 holes each having 0.3 mm diameter were selected to study the effect of number of holes on the performance of biodiesel fuelled engines. The Part load (80% load) tests were conducted at these injection pressures for different pressure, operating the engine at 1500 rev/min. At these loads, air flow rate, biodiesel flow rates, exhaust gas temperatures, HC, CO and nitric oxide emissions were recorded. Based on the results, the optimum injection pressures and nozzle geometry was identified and fixed for COME, HnOME and RuOME biodiesels. Subsequently performance, emission and combustion parameters with the standard diesel were compared.
5.3.1. Performance parameters
In the initial stage, engine was operated with diesel only at manufacturer specified injector opening pressure (IOP) of 205 bar, optimum start of injection (SOI) 23 BTDC and maximum compression ratio 17.5. It was observed that maximum brake thermal efficiency at full load comply with BTE as specified in standards and was found to be 27.57%.
The effect of brake power on brake thermal efficiency at different injector opening pressures (IOP) and different nozzle geometry such as 3, 4, 5 hole are shown in for the three biodiesels in Figure . Amongst all the IOPs tested, the highest brake thermal efficiency occurred at 230 bar for a nozzle geometry of 4 hole with a orifice diameter of 0.3 mm each for all the biodiesels. This is because at higher injection pressures atomization, spray characteristics and mixing with air are better, which result in improved combustion. Too high at IOP 240 bar will lead to delayed injection neglecting the gain due to higher IOP.
Figure 10. Variation of brake thermal efficiency for three biodiesels with different injector orifices.
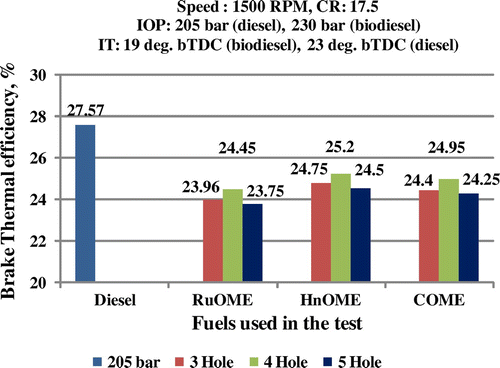
For HnOME operation maximum BTE of 25.2% was obtained with 4-hole nozzle at an IOP of 230 bar. The BTE reported for COME and RuOME were 24.95 and 24%, respectively, with 4-hole nozzle at 230 bar, respectively.
In view of this, the results revealed that, BTE was found to be more with 4-hole nozzle geometry and IOP of 230 bars amongst all IOP and nozzle geometry studied. The IOP for other two nozzles (4-hole and 5-hole) were also found to be optimum at 230 bar, respectively.
Increase in number of holes has no much effect on ignition delay, but the fuel–air mixing rate increased. Also heat release rates during premixed combustion and mixing controlled combustion phases increases with the increase in number of holes on the injector.
5.3.2. Emission parameters
5.3.2.1. NO emission
Nitric oxide emissions increases with the increase in IOP due to faster combustion and higher temperatures reached in the cycle as shown in Figure . However, at 240 bar the NOx emissions reduced due to lowered combustion efficiency at this pressure.
Higher NOx with all biodiesels is observed with increased number of holes. Four hole injector provides better air and fuel mixing and hence higher premixed combustion occurs leading to higher NOx. For HnOME operation higher NOX of 769 ppm was obtained with 4-hole nozzle at an IOP of 230 bar. The NOX reported for COME and RuOME were 740 and 750 ppm, respectively, with 4-hole nozzle at 230 bar, respectively.
6. Conclusions
Different techniques for improving the performance of diesel engine fuelled with non-edible derived biodiesels such as COME, HnOME and RuOME has been undertaken. Merits and demerits of each method has been carefully analysed and the following conclusions can be made from the observations recorded.
(1) | Blending of biodiesel (B20) with diesel is an attractive option as it improves engine performance significantly in terms of increased brake thermal efficiency and reduced emissions. Besides it also substitutes 20% of the fossil fuel, i.e. diesel thereby reducing the import cost of crude petroleum fuel. This option with increased blending percentage becomes more viable if the cost of biodiesel production is lowered and its oxidation stability is ensured. | ||||
(2) | With suitable thermal barrier coatings the engine performance is enhanced. The performance though is comparable to blending option it has several disadvantages in its use as a sustainable option. Providing LHR coating is limited to a certain thickness and does not ensure a permanent layer on piston, cylinder walls and valves. Moreover, after a long duration of engine operation the coating wears out. This option is acceptable if it can act as a permanent coating with economical viability while applying this layer. | ||||
(3) | Finally providing suitable injection strategies in terms of injection timing, injector opening pressure and nozzle geometry ensures sustained and improved diesel engine performance when fuelled with non-edible derived biodiesels. However, the herculean task that is necessary is to optimize these for different biodiesel engine operation. Most biodiesels perform better when injector opening pressure is maintained between 230 and 240 bar. Some biodiesels require retarded injection timing while some other advanced injection timing for improved engine performance. Increased number of holes on a given injector improves biodiesel operation. However, finding the optimum number of holes for biodiesels of different origin needs more experimentation. Another interesting area is to change the size of orifices on the given injector nozzle. This option needs thorough investigation as each biodiesel is unique and may behave differently when used in diesel engines. |
On the closure it can be concluded that B20 blended biodiesel with appropriate LHR coating along with optimized injector nozzle combination can significantly enhance the biodiesel fuelled engine operation and the performance will then be comparable to diesel engine.
Disclosure statement
No potential conflict of interest was reported by the authors.
References
- Agarwal, D., and A. K. Agarwal. 2007. “Performance and Emissions Characteristics of Jatropha Oil (Preheated and Blends) in a Direct Injection Compression Ignition Engine.” Applied Thermal Engineering 27: 2314–2323.10.1016/j.applthermaleng.2007.01.009
- Ahmaniemi, S., J. Tuominen, M. Vippola, P. Vuoristo, T. Mäntylä, F. Cernuschi, C. Gualco, A. Bonadei, and R. Di Maggio. 2004. “Characterization of Modified Thick Thermal Barrier Coatings.” Journal of Thermal Spray Technology 13 (3): 361–369.10.1361/10599630420371
- Amann, C. A. 1988. “Promises and Challenges of the Low-Heat-Rejection Diesel.” Journal of Engineering for Gas Turbines and Power 110: 475–481.10.1115/1.3240145
- Atadashi, I. M., M. K. Aroua, and A. Abdul Aziz. 2010. “High Quality Biodiesel and Its Diesel Engine Application: A Review.” Renewable and Sustainable Energy Reviews 14 (7): 1999–2008.10.1016/j.rser.2010.03.020
- Bakar, Rosli Abu, and Semin Abdul Rahim Ismail. 2008. “Fuel Injection Pressure Effect on Performance of Direct Injection Diesel Engines Based on Experiment.” American Journal of Applied Science 5 (3): 197–202.
- Banapurmath, N. R., P. G. Tewari, and R. S. Hosmath. 2008a. “Combustion and Emission Characteristics of a Direct Injection, Compression‐Ignition Engine When Operated on Honge Oil, HOME and Blends of HOME and Diesel.” International Journal of Sustainable Engineering 1 (2): 80–93.10.1080/19397030802221265
- Banapurmath, N. R., P. G. Tewari, and R. S. Hosmath. 2008b. “Experimental Investigations of a Four-Stroke Single Cylinder Direct Injection Diesel Engine Operated on Dual Fuel Mode with Producer Gas as Inducted Fuel and Honge Oil and Its Methyl Ester (HOME) as Injected Fuels”.” Renewable Energy 33: 2007–2018.10.1016/j.renene.2007.11.017
- Bari, S., C. W. Yu, and T. H. Lim. 2004. “Effect of Fuel Injection Timing with Waste Cooking Oil as a Fuel in a Direct Injection Diesel Engine.” Proceedings of the Institution of Mechanical Engineers, Part D: Journal of Automobile Engineering 218: 93–104.10.1243/095440704322829209
- Basha, Syed Ameer, K. Raja Gopal, and S. Jebaraj. 2009. “A Review on Biodiesel Production, Combustion, Emissions and Performance.” Renewable and Sustainable Energy Reviews 13: 1628–1634.
- Ekrem, B., E. Tahsin, and C. Muhammet. 2006. “Effects of Thermal Barrier Coating on Gas Emissions and Performance of a LHR Engine with Different Injection Timings and Valve Adjustments.” Energy Conversion and Management 47: 1298–1310.
- Gajendra Babu, M. K. 2007. “Studies on Performance and Exhaust Emissions of a CI Engine Operating on Diesel and Diesel Biodiesel Blends at Different Injection Pressures and Injection Timings.” Society of Automotive Engineers, Paper No.: 2007-01-0613, 2007.
- Hountalas, D. T., D.A. Kouremenos, K. B. Binder, A. Raab, and M. H. Schnabel. 2001. “Using Advanced Injection Timing and EGR to Improve DI Engine Efficiency at Acceptable NO and Soot Levels.” Society of Automotive Engineers, Paper No.: 2001-01-0199. SAE (Society of Automotive Engineers).
- Jaichandar, S., and P. Tamilporai. 2003. “Low Heat Rejection Engines – An Overview”. Society of Automotive Engineers, Paper No.: 2003-01-0405, SAE (Society of Automotive Engineers), USA.
- Karnwal, Ashish, M. M. Naveen Kumar, Rajeev Chaudhary Hasan, Arshad Noor Siddiquee, and Zahid A. Khan. 2010. “Production of Biodiesel from Thumba Oil: Optimization of Process Parameters.” Journal of Energy & Environment. 1 (4): 352–358.
- Martin, M. Leenus Jesu, and Edwin Geo. 2011. “Effect of Diesel Addition on the Performance of Cottonseed Oil Fuelled DI Diesel Engine.” International Journal of Energy and Environment 2 (2): 321–330.
- Morshed, Mahbub, Kaniz Ferdous, Maksudur R. Khan, M. S. I. Mazumder, M. A. Islam, and Md T. Uddin. 2011. “Rubber Seed Oil as a Potential Source for Biodiesel Production in Bangladesh.” Fuel 90: 2981–2986.10.1016/j.fuel.2011.05.020
- Nabi, Md Nurun, Md. Mustafizur Rahman, and M. Shamim Akhter. 2009. “Biodiesel from Cotton Seed Oil and Its Effect on Engine Performance and Exhaust Emissions.” Applied Thermal Engineering 29: 2265–2270.10.1016/j.applthermaleng.2008.11.009
- Naga, Sarada S., M. Shailaja, A. V. Sita Rama Raju, and K. Kalyani Radha. 2010. “Optimization of Injection Pressure for a Compression Ignition Engine with Cotton Seed Oil as an Alternate Fuel.” International Journal of Engineering, Science and Technology 2 (6): 142–149.
- Ong, H. C., T. M. I. Mahlia, H. H. Masjuki, and R. S. Norhasyima. 2011. “Comparison of Palm Oil, Jatropha curcas and Calophyllum inophyllum for Biodiesel: A Review.” Renewable and Sustainable Energy Reviews 15: 3501–3515.10.1016/j.rser.2011.05.005
- Puhan, Sukumar, R. Jegan, K. Balasubbramanian, and G Nagarajan. 2009. “Effect of Injection Pressure on Performance, Emission and Combustion Characteristics of High Linolenic Linseed Oil Methyl Ester in a DI Diesel Engine.” Renewable Energy 34: 1227–1233.10.1016/j.renene.2008.10.001
- Rakopoulos, C. D., D. C. Rakopoulos, E. G. Giakoumis, and A. M. Dimaratos. 2010. “Investigation of the Combustion of Neat Cottonseed Oil or Its Neat Bio-Diesel in a HSDI Diesel Engine by Experimental Heat Release and Statistical Analyses.” Fuel 89 (12): 3814–3826.10.1016/j.fuel.2010.07.012
- Ramadhas, A. S., S. Jayaraj, and C. Muraleedharan. 2005. “Characterization and Effect of Using Rubber Seed Oil as Fuel in the Compression Ignition Engines.” Renewable Energy 30: 795–803.10.1016/j.renene.2004.07.002
- Roy, M. M. 2009. “Effect of Fuel Injection Timing and Injection Pressure on Combustion and Odorous Emissions in DI Diesel Engine.” Journal of Energy Resources Technology, ASME Transactions 131: 1–8.
- Sahoo, P. K., L. M. Das, M. K. J. Babu, and S. N. Naik. 2007. “Biodiesel Development from High Acid Value Polanga SeedOil and Performance Evaluation in a CI Engine.” Fuel 86: 448–454.
- Suresh, G., H. C. Kamath, and N. R. Banapurmath. 2014. “Effect of injection timing, injector opening pressure and nozzle geometry on the performance of cotton seed oil methyl ester fuelled diesel engine. International Journal of Sustainable Engineering.” Taylor and Francis Publications 7 (1): 82–92.10.1016/j.fuel.2006.07.025
- Tao F., Y. Liu, B. H. Rempel Ewert, D. E. Foster, R. D. Reitz, D. Choi, and P. C. Miles. 2005. “Modelling the Effect of EGR and Retarded Injection on Soot Formation in a High Speed Diesel Injection (HSDI) Diesel Engine Using a Multi Step Phenomenological Soot Model.” Society of Automotive Engineers, Paper No.: 2005 -01-0121. Society of Automotive Engineers (SAE).
- Yang, Ru, Mengxing Su, Jianchun Zhang, Fuqiang Jin, Chunhong Zha, Min Li, and Xinmin Hao. 2011. “Biodiesel Production from Rubber Seed Oil Using Poly (Sodium Acrylate) Supporting NaOH as a Water-Resistant Catalyst.” Bioresource Technology 102: 2665–2671.10.1016/j.biortech.2010.10.131