Abstract
In this paper, experiments have been performed in order to determine the quantity of water produced from the atmospheric air using different desiccant materials named Silica gel, Activated alumina and Molecular sieve 13 X. On the bases of experimental results, a correlation is derived among the different temperatures and water production using Central Composite Design (CCD) of Response Surface Methodology. A newly designed solar glass desiccant box type system (SGDBS), three in number, has been used. Design parameters for the production of water has been taken as depth of material from the glass is 0.22 m, inclination in angle as 30°, effective thickness of glass as 3 mm and number of glazing as single. It has been found experimentally that the maximum quantity of water produced by Silica gel, Activated alumina and Molecular sieve 13 X is 160, 20 and 35 ml/kg/day, respectively. Whereas theoretically, value of water produced by the Silica gel, Activated alumina and Molecular sieve 13 X is 600, 28 and 60 ml/kg/day, respectively.
1. Introduction
There is a very important relationship between energy and water. Water is required by all the resources of energy in their production, for example, cooling requirement in thermal processes, cleaning processes, cultivation of biofuel crops and power turbine (including electricity), whereas energy is required to make the water resources available to the human being for its daily requirements through transport, treatment, pumping and desalination. This is a well-known fact that conventional water resources are depleting day-by-day and thus strives for the alternate ways for the water production. Alayli, Hadji, and Leblond (Citation1987), Aristov et al. (Citation1999), Gordeeva et al. (Citation2002) performed experiments for the production of water from atmospheric air using different composite materials, i.e. by modifying the isotherms of the material, by selective water sorbent (SWS) and using thick corrugated layers. Abualhamayel and Gandhidasan (Citation1997) studied analytically the method of production of fresh water using a liquid desiccant. It was proposed that at a given set of operating condition, it was possible to obtain 1.90 kg of water per m2. Hamed (Citation1999) used two host materials, namely mesoporous silica gel and alumina with the two composites SWS-1L and SWS-1A which was formed by impregnating two host matrices with CaCl2 in order to study the kinematics of water vapour sorption. Gad, Hamed, and Sharkawy (Citation2001) manufactured two samples of selective water solvent SWS-2C and SWS-2EG using mesoporous synthetic carbon subunit and macroporous-expanded graphite impregnated with lithium bromide in order to study the water sorption capacity of novel composite desiccant. Dawoud and Aristov (Citation2002) experimentally investigated the integrated desiccant collector system for the production of water from air using a thick corrugated layer of cloth and CaCl2. It was found that the system provided 1.5 L of fresh water per square metre per day. Sultan (Citation2004) studied a non conventional method of water production from atmospheric air using calcium chloride (CaCl2) as desiccant material. It was observed that the system efficiency increased with the initial concentration and decreased with the increase in regeneration air velocity and absorption temperature. Hamed (Citation2002) experimentally investigated the adsorption of water vapour on the horizontal surface of a sandy layer impregnated with calcium chloride (CaCl2). It was found that rate of absorption decreased with a decrease in mixing ratio and mass transfer coefficient is highly affected by the desiccant concentration in the bed. Bar (Citation2004) studied the extraction of water from air-patented technology based on extraction of air humidity into water streams. This technology absorbs air humidity on a solid desiccant, desorbs water to vapour and condense vapours into water using the solar energy or waste heat. For the production of water, low-grade energy was required to be 100–150 kcal/l. Kabeel (Citation2006) experimental work had been done on the glass pyramid shape with a multi-shelf solar system to extract water from the atmospheric air. Two pyramids with bed made up of cloth and saw wood, saturated with 30% CaCl2 solution were used. It was found that 2.5 L/day/m2 of fresh water can be produced by this experiment. Ji, Wang, and Li (Citation2006) and Hamed, Aly, and Zeidan (Citation2011) experimentally investigated the recovery of water from atmospheric air using the composite material MCM-41and a sandy bed impregnated with calcium chloride. It was found that 1.2 kg and 1.0 L/m2 water can be produced.
Some of the researchers have used adsorption and regeneration properties of desiccant materials in the applications like production of dry air or desiccant cooling system. Few researchers have done work in the production of water from atmospheric air using different desiccant material. An attempt has been made for the production of water using the different desiccant materials experimentally and theoretically. Experiments have been performed in the Indian climatic condition at NIT Kurukshetra, India [29°58′ (latitude) North and 76°53′ (longitude) East] in the month of August 2014.
2. Experimental set-up, measurement and method
2.1. Experimental set-up
The photograph of the experimental set-up is shown in Figure . It consists of solar glass desiccant box type system (SGDBS). The solar glass desiccant box type system (SGDBS) consists of following main parts:
(1) | FRP container | ||||
(2) | Glazing | ||||
(3) | Wire mesh tray | ||||
(4) | Water measuring cylinder | ||||
(5) | Connecting pipe | ||||
(6) | Desiccant material | ||||
(1) | FRP container: Three containers of fibre-reinforced plastic (FRP), because of good strength and long life, of size 0.6 m × 0.6 m × 0.3 m have been used as shown in Figures and (b). Two windows of size 0.3 m × 0.3 m have been provided for the process of adsorption in the night time. This function is an advantage over the other set-up designs, in which, for the adsorption process, glass has to be removed and for regeneration again glass has to be fixed. A water collecting tray with slight slope has been provided on the front side for the collection of drops coming along the glass after condensation. | ||||
(2) | Glazing: A glass of 3 mm thickness is used for the purpose of glazing which also acts as a condenser for the regeneration process. Glass allows to pass sun rays of shorter wavelength inside the SGDBS and traps the ray of longer wavelength, which comes after heating the solid desiccant material. It is used to create the greenhouse effect inside the SGDBS. | ||||
(3) | Wire mesh tray: A wire mesh of steel wire is used inside the SGDBS for holding the solid desiccant material. The dimension of the wire mesh is 3 mm × 3 mm. Wire mesh is screwed on the frame which is made up of plastic. | ||||
(4) | Connecting pipe: Connecting pipe is attached between water collecting tray and bottle in order to provide a path for the flow of condensed water droplets. | ||||
(5) | Water measuring cylinder: A water measuring cylinder is used outside the SGDBS for the collection of water. The water is coming directly from the water collection tray through the connecting pipe to the bottle. There is provision of measuring marks outside the cylinder which indicates the collecting quantity of the water. The minimum quantity of water that can be measured is 5 ml. | ||||
(6) | Desiccant material: Silica gel, activated alumina and molecular sieve 13 X has been used as desiccant material. The properties of these desiccant materials are listed in Tables as provided by SORBEAD INDIA Pvt. Ltd., INDIA. When the silica gel is not used for the water production, it is stored in a cool, dry and air-tight closed container. Since the material is insoluble and non-toxic, so after its processing, it must be land-filled according to the local state and federal regulations. |
Figure 1. Schematic diagram for Solar Glass Desiccant based System (SGDBS), Kumar and Yadav (Citation2015).
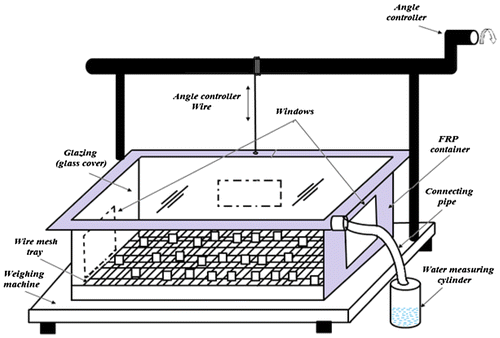
Figure 2. Photograph of the experimental set-up (a) during adsorption process (b) during regeneration process.
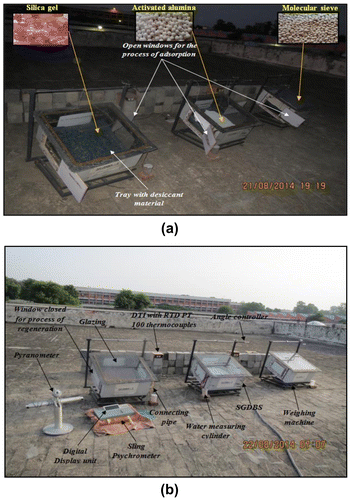
Table 1. Properties of silica gel used as a desiccant material.
Table 2. Properties of activated alumina used as a desiccant material.
Table 3. Properties of Molecular sieve 13 X used as a desiccant material.
2.2. Measuring devices and instruments
Different parameters were measured during experiments as follows:
• | Temperature of material, inner side of glass, outer side of glass and inside space temperature of SGDBS. | ||||
• | Ambient temperature. | ||||
• | Solar radiation intensity. | ||||
• | Weighing machine. |
Temperature of material, inner side of the glass, outer side of glass and inside temperature of SGDBS were measured with the help of RTD PT100 thermocouples which was connected with a digital temperature indicator that showed the temperature with a resolution of 0.1.
Dry-bulb temperature of ambient air was measured with the help of sling Psychrometer.
The solar radiation intensity was measured during the day time with a Pyranometer Model CM11, of Kipp and Zonen, Holland.
Adsorption of moisture during the experiment was measured with the help of a digital weighing machine of maximum capacity 50 kg, 1 g minimum capacity and resolution of 0.001 kg. Weighing machine was the maker of ‘THOMSON Electronic weighing scales’.
2.3. System operation
For the working of the experimental set-up, the solid desiccant material, i.e. silica gel, activated alumina and molecular sieve 13 X, are placed on the wire mesh tray. For the adsorption process, the side windows of SGDBS are opened at 7:00 pm in the evening. The adsorption process starts because the vapour pressure on the surface of desiccant material (adsorbent) is lower than the atmospheric air. This process is continued up to late night till the equilibrium conditions, i.e. when the vapour pressure on the adsorbent surface is same as that of atmospheric air, attained. In the morning at 6’o clock, the side windows are closed and set-up is exposed to the sun rays for the regeneration process. As the temperature of the desiccant material raises, the vapour pressure difference between the surface of the desiccant material and the air of the internal space of the box increases. Therefore, adsorbed moisture is transferred to the air of the internal space and increases the vapour pressure. As the solar intensity increases, mass transfer of vapour from material to the air of internal space increases and reaches saturation condition. The water vapour condenses on the inner side of the glass and after coalition forms the small drops. The small drops slide along the surface of the glass and get collected in the water collection tray. Due to the slope in water collecting tray, water goes to the water measuring container through a connecting pipe. The amount of collected water is measured after a regular interval of 30 min.
3. Analysis of experimental data
The adsorption rate of quantity of desiccant is the amount of water content absorbed by the desiccant per unit time and is given by Pramuang and Exell (Citation2007)(1)
The generalized equation of the quadratic response model is given by [15](2)
4. Result and discussion
4.1. Case – 1: central composite design and observed values of response for Silica gel
A Central Composite Design (CCD) design matrix has been chosen for optimizing the level of variables. On the basis of experimental data, first, the significant variables that affect the response were identified. Design expert of 7.0 has been used for optimizing variables. A four-level, four factors CCRD namely material temperature, internal space temperature, inner glass temperature and the outer glass temperature were opted in this work to optimize the factors that affect the response. These parameters with their range are shown in Table . The experiments have been performed on the basis of central composite second order, which are shown in Table .
Table 4. Levels and coded variables chosen for CCD.
Table 5. CCD values with experimental values of water production.
The model F-value of 160.81 implies that the model is significant as shown in Table . There is only a 0.01% chance that a ‘Model F-value’ this large could occur due to noise. A value of ‘prob > F’ less than 0.0500 indicates model terms are significant. In this case, A, B, C, D, AB, BC, BD, CD, A2, B2, C2 are significant model terms. A value greater than 0.1000 indicates the model terms are not significant. If there are many insignificant model terms (not counting those required to support hierarchy), model reduction may improve the model. The predicated R2 of 0.8617 is reasonably close to the adjusted R2 of 0.9872. ‘Adeq Precision’ measures the signal-to-noise ratio. A ratio greater than four is desirable. A ratio of 34.938 indicates an adequate signal. The model can be used to navigate the design space.
Table 6. ANOVA for response surface quadratic model of water production.
Table also shows that for the water production, i.e. in case of the regeneration process, the required parameter are material temperature (A), internal space temperature (B), inner glass temperature (C) and outer glass temperature (D) which are shown as significant terms. Whereas if other combination are considered as shown by ‘star’ (*), even then water can be produced.
Based on the experimental data, multiple regression analysis is given by the second-order polynomial equation:
Final equation in term of actual factors:(3)
where T1- material temperature; T2- inner space temperature; T3- internal glass temperature; and T4- outer glass temperature.
Equation 3 predicts that T2 is the most significant term for water production followed by T4, T32 and T1 × T2, whereas T3 is least significant (Figure ).
Figure 3. Variation of water production with (a) material temperature, (b) internal space temperature and (c) inner glass temperature.
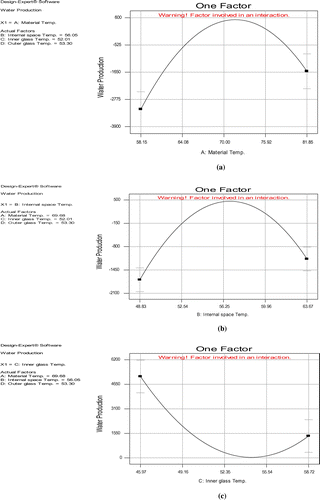
Figure (a) shows that with in increase in material temperature up to the optimum range of 72 °C and by keeping the other parameter constant, i.e. internal space temperature, inner glass temperature and outer glass temperature as 56.06, 52.01 and 53.30 °, respectively, the water production rate can be increased up to 600 ml/kg/day and beyond this range the water production will start to decrease. Figure (b) shows that water production will be maximum up to 500 ml/kg/day if the internal space temperature is around 56.25 °C and by keeping other parameters constant, i.e. material temperature, inner glass temperature and outer glass temperature as 69.68, 52.01 and 53.30 °C, respectively. Figure (c) shows that as the temperature of the inner glass is low, the water production is maximized and as the temperature of the inner glass starts to increase, water production starts to decrease. This is because the water vapours move towards the side where the temperature is less and as the inner glass temperature is less so it will result in maximum amount of water production. As the temperature of the inner glass starts to rise, the rate of condensation will decrease considerably.
4.2. Case – 2: CCD and observed values of response for activated alumina
A CCD design matrix has been chosen for optimizing the level of variables. On the basis of experimental data, first the significant variables that affect the response were identified. Design expert of 7.0 has been used for optimizing variables. A four-level, four factors CCRD namely material temperature (T1), internal space temperature (T2), inner glass temperature (T3) and outer glass temperature (T4) were opted in this work to optimize the factors that affect the response. These parameters with their range are shown in Table . The experiments have been performed on the basis of central composite second order, which are shown in Table .
Table 7. Levels and coded variables chosen for CCD.
Table 8. CCD values with experimental values of water production.
The model F-value of 159.18 implies that the model is significant as shown in Table . There is only a 0.01% chance that a ‘Model F-value’ this large could occur due to noise. A value of ‘prob > F’ less than 0.0500 indicates model terms are significant. In this case A, B and C are significant model terms. A value greater than 0.1000 indicates the model terms are not significant. If there are many insignificant model terms (not counting those required to support hierarchy), model reduction may improve the model. The predicated R2 of 0.9657 is in reasonable agreement with the ‘adjusted R2’ of 0.9820. ‘Adeq Precision’ measures the signal-to-noise ratio. A ratio greater than four is desirable. A ratio of 33.716 indicates an adequate signal. The model can be used to navigate the design space.
Table 9. ANOVA for response surface 2FI model of water production.
Table also shows that for the water production, i.e. in case of the regeneration process, the required parameter are material temperature (A), internal space temperature (B) and inner glass temperature (C) which are shown by ‘star’ (*).
Final equation in term of actual factors:(4)
where T1- material temperature; T2- inner space temperature; T3- internal glass temperature; T4- outer glass temperature.
Equation 4 predicts that T2 is the most significant term for water production whereas T3 is the least significant term.
The model graph of water production is shown in Figure . It is shown from the graph that by keeping the inner glass temperature as 51.95 °C, outer glass temperature as 52.00 °C and varying internal space temperature and material temperature, water production can reach up to 28 ml/kg/day, which is experimentally found to be 20 ml/kg/day.
4.3. Case-3: CCD and observed values of response for molecular sieve
A CCD design matrix has been chosen for optimizing the level of variables. On the basis of experimental data, first the significant variables that affect the response were identified. Design expert of 7.0 has been used for optimizing variables. A four-level, four factors CCRD namely material temperature (T1), internal space temperature (T2), inner glass temperature (T3) and outer glass temperature (T4) were opted in this work to optimize the factors that affect the response. These parameters with their range are shown in Table . The experiments have been performed on the basis of central composite second order, which are shown in Table .
Table 10. Levels and coded variables chosen for CCD.
Table 11. CCD values with experimental values of water production.
The model F-value of 2152.34 implies that the model is significant as shown in Table . There is only a 0.01% chance that a ‘Model F-value’ this large could occur due to noise. A value of ‘prob > F’ less than 0.0500 indicates model terms are significant. In this case, A, B, AB, AC, AD, BC, BD, A2, B2 are significant model terms. A value greater than 0.1000 indicates the model terms are not significant. If there are many insignificant model terms (not counting those required to support hierarchy), model reduction may improve the model. The predicated R2 of 0.8851 is reasonably close to the adjusted R2 of 0.9990. ‘Adeq Precision’ measures the signal to noise ratio. A ratio greater than four is desirable. A ratio of 107.580 indicates an adequate signal. The model can be used to navigate the design space.
Table 12. ANOVA for response surface quadratic model of water production.
Final equation in term of actual factors:(5)
where T1 - material temperature; T2 - inner space temperature; T3 - internal glass temperature; T4 - outer glass temperature.
Equation 5 predicts that T1 is the most significant term for water production whereas T4 is the least significant term.
The model graph of water production is shown in Figure . It is shown from the graph that by keeping inner glass temperature as 59 °C, outer glass temperature as 53.25 °C and varying internal space temperature and material temperature, water production can reach up to 60 ml/kg/day, which is experimentally found to be 35 ml/kg/day.
5. Experimental error
The measured values during the experiment are not accurate. These are affected by the deviations caused by the various errors. There are two types of errors, namely systematic error and random error. Systematic errors are because of the instrument error and environmental errors. Random errors arise due to random and unpredictable fluctuation in the experimental conditions, for example, unpredictable fluctuation in temperature, voltage supply, mechanical vibrations in experimental set-up etc., and personal errors by the observer taking readings.
The error is calculated for the measuring instruments during the experiments
% error in measuring intensity = 2%
% error in measuring temperatures = 0.3%
% error in measuring water quantity = 0.025%
Total % error for the SGDBS = 1 × 2 + 4 × 0.3 + 1 × 0.025 = 3.225%
% of error in weighing machine = 0.1%.
6. Testing of water sample
A number of tests have been carried out in order to check the quality of the water sample collected from the desiccant material silica gel. The sample collected from the silica gel has been selected because it has a maximum water production among the other desiccant materials. The tests have been performed at CSSRI lab, Karnal, Haryana, India on 23 August 2014. The results of physical and chemical tests are shown in Table .
Table 13. Analysis report of water sample produced by the silica gel.
7. Cost analysis of solar glass desiccant based system (SGDBS)
The use of SGDBS depends upon the cost effectiveness. Investment is made on the SGDBS in order to reduce the dependency on the conventional system for the production of water, as the demand for the water is increasing day-by-day.
A comprehensive study of cost analysis is presented by Govind and Tiwari (Citation1984).
If P is the initial investment of SGDBS, r% as annual rate of interest, n as number of useful years to which system will perform and S as salvage value of the SGDBS then,(6)
Final annual cost of the system = (CRF) P(7)
(8)
(9)
7.1. For SGDBS
The cost break-up for the SGDBS has been given in Table
Table 14. Cost analysis for SGDBS.
P = Rs. 3000
S = Rs. 250
Assuming n = 15 years, r = 12% and maintenance cost = 10% of the total cost,
The cost calculation can be done as follows:
CRF = 0.1467
SFF = 0.0268
Final annual cost of the system = CRF × p = 0.1467 × 3000 = Rs. 440.26
Annual salvage value = SFF × S = 0.0268 × 250 = Rs. 6.70
Annual maintenance cost = 10% = 0.10 × 440.26 = Rs. 44
Annual cost = 440.26 + 44 – 6.70 = Rs. 477.56
Annual yield by silica gel = 0.160 × 365 = 58.4 liter/year
Annual yield by molecular sieve = 0.035 × 365 = 12.775 liter/year
Annual yield by activated alumina = 0.020 × 365 = 7.3 liter/year
8. Conclusions
The following conclusion emerges from the experimental and theoretical results:
(1) | Experimental results of SGDBS have shown that water can be produced from the atmospheric air using different desiccant materials. | ||||
(2) | Experimental results from the water production shows that the maximum quantity of water produced by silica gel is 4.57 times of molecular sieve 13 X and 8 times that of activated alumina. | ||||
(3) | Theoretical results for the water production shows that the maximum quantity of water produced by silica gel is 10 times of molecular sieve 13 X and 21.42 times that of activated alumina, subjected to fixed temperature conditions for material temperature, internal space temperature, inner glass temperature and outer glass temperature. | ||||
(4) | Experimentally maximum quantity of water produced by the silica gel is 160 ml/kg/day and theoretically it is 600 ml/kg/day. |
8.1. Future work
In the existing experimental set-up, research work can be done on the condensation side along with making the system more leak proof. Also, calcium oxide, calcium chloride, charcoal, composite desiccant materials and liquid desiccant materials can be used as an adsorbent for the production of water from atmospheric air. This can reduce the gap between the predicted and experimental results of water production from atmospheric air. For using the experimental system as per the regional conditions, the design parameters have to be investigated by covering a wide range of climatic conditions.
Nomenclature | ||
CRF | = | capital recovery factor |
GA | = | adsorption rate (kg/hr) |
L | = | latent heat of water at average bed temperature (J/kg) |
Msol. | = | mass of solution (kg) |
Ms | = | mass of salt (kg) |
Mw | = | mass of water (kg) |
mws | = | weight of desiccant on wet basis (kg) |
n | = | number of useful years |
P | = | initial investment |
r% | = | annual rate of interest |
S | = | salvage value |
SFF | = | sinking fund factor |
w | = | moisture content in desiccant (kgwater vapor/kgdesiccant) |
X | = | concentration of solution |
References
- Alayli, Y., N. E. Hadji, and J. Leblond. 1987. “A New Process for Extraction of Water from Air.” Desalination 67: 227–229.10.1016/0011-9164(87)85020-8
- Aristov, Yu I, M. M. Tokarev, L. G. Gordeeva, V. N. Snytnikov, and V. N. Parmon. 1999. “New Composite Sorbents for Solar-driven Technology of Fresh Water Production from the Atmosphere.” Solar Energy 66: 165–168.10.1016/S0038-092X(98)00110-8
- Abualhamayel, H. I., and P. Gandhidasan. 1997. “A Method of Obtaining Fresh Water from Humid Atmosphere.” Desalination 113: 51–63.10.1016/S0011-9164(97)00114-8
- Bar, Etan. 2004. “Extraction of Water from Air – An Alternative Solution for Water Supply.” Desalination 165: 335.10.1016/S0011-9164(04)00268-1
- Dawoud, Belal, and Yuri Aristov. 2002. “Experimental Study of Water Vapor Sorption on Selective Water Sorbents, Silica Gel and Alumina under Typical Operating Conditions of Sorption Heat Pump.” International Journal of Heat and Mass Transfer 46: 273–281.
- Gordeeva, L. G., G. Restuccia, A. Ferni, and Yu I. Aristov. 2002. “Water Sorption on Composites LiBr in a Porous Carbon.” Fuel Processing Technology 79: 225–231.10.1016/S0378-3820(02)00186-8
- Gad, H. E., A. M. Hamed, and I. I. Sharkawy. 2001. “Application of Solar Desiccant/Collector System for Water Recovery from Atmospheric Air.” Renewable Energy 22: 541–556.10.1016/S0960-1481(00)00112-9
- Govind, and G. N. Tiwari. 1984. “Economic Analysis of Some Solar Energy Systems.” Energy Conversion and Management 24: 131–135.10.1016/0196-8904(84)90024-4
- Hamed, M. Ahmed 1999. “Absorption-regeneration Cycle for Production of Water from Air-theoretical Approach.” Renewable Energy 19: 625–635.
- Hamed, A. M. 2002. “Experimental Investigation on the Natural Absorption on the Surface of Sandy Layer Impregnated with Liquid Desiccant.” Renewable Energy 28: 1587–1596.
- Hamed, Ahmed M., Ayman A. Aly, and El-Shafei B. Zeidan. 2011. “Application of Solar Energy for Recovery of Water from Atmospheric Air in Climatic Zones of Saudi Arabia.” Natural Resources 2: 8–17.10.4236/nr.2011.21002
- Ji, J. G., R. Z. Wang, and L. X. Li. 2006. “New Composite Absorbent for Solar-driven Fresh Water Production from the Atmosphere.” Desalination 212: 176–182.
- Kabeel, A. E. 2006. “Water Production from Air Using Multi-shelves Solar Glass Pyramid System.” Renewable Energy 32: 157–172.
- Kumar, Manoj, and Avadhesh Yadav. 2015. “Experimental Investigation of Design Parameters of Solar Glass Desiccant Box Type System for Water Production from Atmospheric Air.” Journal of Renewable Sustainable Energy 7: 033122.10.1063/1.4922142
- Pramuang, S., and R. H. B. Exell. 2007. “The Regeneration of Silica Gel Desiccant by Air from a Solar Heater with a Compound Parabolic Concentrator.” Renewable Energy 32: 173–182.10.1016/j.renene.2006.02.009
- Sultan, Ahmed. 2004. “Absorption/Regeneration Non-conventional System for Water Extraction from Atmospheric Air.” Renewable Energy 29: 1515–1535.10.1016/S0960-1481(03)00020-X