ABSTRACT
Sustainable hydraulic cements based on alkali aluminosilicate chemistry were developed with market-limited wastes acting as the primary aluminosilicate precursors. Two sets of formulations were developed with waste brick or impounded coal ash used at relatively large volume as aluminosilicate precursors. Supplementary materials were used to produce raw materials of viable chemistry. Blends of raw materials were transformed into hydraulic cements by input of mechanical energy without resorting to elevated temperatures. The resultant hydraulic cements exhibited viable strength development characteristics. FTIR, SEM, EDS and NMR analyses were conducted in order to gain insight into the structure of the hydraulic cements and their hydration products. The results pointed at the prevalence of calcium aluminosilicate hydrates among the products of hydration which thoroughly bound the non-hydrated cores of cement particles.
Introduction
Climate change and waste management are among the environmental problems threatening sustainable development (Smith et al. Citation2001). Cement industry has played a vital role in the development of infrastructure systems which support diverse societal functions ranging from sewage management to transportation. Production of Portland cement, however, is a major source of CO2 emissions; production of one ton of Portland cement releases approximately 0.8 ton of CO2 to the atmosphere (Davidovits Citation1994). There are also growing concerns with the longevity of infrastructure systems that is correlated with the barrier qualities of Portland cement concrete and its durability under the aggressive exposures encountered in diverse applications such as sanitary sewer pipes and bridge structures (Parande et al. Citation2006). These environmental and performance considerations are encouraging development of alternative hydraulic cements with reduced carbon footprint and energy content, which also offer enhanced barrier and durability characteristics. Today’s Portland cement concrete incorporates some industrial by-products, primarily coal fly ash, as a partial replacement for cement (Papadakis and Tsimas Citation2002). The chemistry of Portland cement, however, limits the extent of coal ash use, and is not compatible with the evolving chemistry of coal fly ash (and other industrial by-products) which are influenced by the growing demands for control of toxic and environmentally harmful emissions (Carlson and Adriano Citation1993; Galiano, Pereira, and Vale Citation2011). The work reported herein focused on the development of a new class of hydraulic cement which make value-added use of large volumes of waste brick and impounded/landfilled coal ash.
Waste brick is an important constituent of the construction and demolition (C&D) waste stream; defective bricks generated during production constitute another source of waste brick. Clay, a major source of aluminosilicates, is the primary raw material used for production of brick. During high-temperature firing of brick, a liquid phase develops, which subsequently forms an amorphous glassy phase upon cooling. It is this glassy phase that binds the crystalline and other phases that make up the brick (Khatib and Wild Citation1996). The relatively large landfilled quantities of waste brick rationalise efforts to develop markets for this constituent of the construction and demolition (C&D) waste stream (Kinuthia and Nidzam Citation2011). Ground waste brick has been evaluated as a pozzolan in production of Portland cement concrete (Gonçalves et al. Citation2009). The potential use of brick waste as a partial replacement for Portland cement in production of mortar has also been investigated. The mechanical properties of mortar were found to benefit from replacement of about 10 wt.% of cement with ground brick (Anseau et al. Citation2005).
Impounded/landfilled coal ash has accumulated in tremendous quantities (estimated at billions of tons) (Rostami and Brendley Citation2003); there are growing concerns with its adverse environmental and health impacts (Veranth et al. Citation1998). These ashes are by-products of coal combustion in power plants. The fact that they have not found applications could be a result of their less favourable composition. In addition, their quality is subject to change during ageing in ponds and landfills. This project views the tremendous quantities of available impounded/landfilled ash as sustainable resources in production of a new class of hydraulic cement with robust chemistry. This approach views impounded/landfilled ash as a rich source of amorphous aluminosilicates, to be produced in production of hydraulic cements which rely upon alkali aluminosilicate hydrates (in lieu of calcium silicate hydrates in Portland cement) to render binding effects. The cement chemistry based primarily on alkali aluminosilicates enables use of coal ashes which are not of value to the conventional Portland cement chemistry, and is also particularly effective in stabilization/solidification of any hazardous constituents of impounded/landfilled coal ash (Shi and Fernandez-Jimenez Citation2006).
Efforts were made to synthesise alkali activated cement by calcining low-quality bentonite with dolomite and Na2CO3. The highest 28-day compressive strength achieved was 38 MPa after heat curing at 80 °C (Peng et al. Citation2017). Other work investigated the potential use of granite quarry dust as raw material for geopolymer synthesis. The granite dust fused in presence of sodium hydroxide at temperature 550 °C. The resultant fused material was then used to synthesise geopolymers at room temperature using sodium silicate as activator. Most room temperature-cured specimens provided 28-day compressive strengths in the 10–25 MPa range (Tchadjié et al. Citation2016). Production of geopolymer binder from ground concrete waste powder blended with coal fly ash has also been reported (Ahmari et al. Citation2012). This work used the traditional two-part geopolymer synthesised by the addition of alkalis in solution form to the blended waste powder. The resulting 7-day compressive strength ranged from 10 to 35 MPa depending on the Ca/Si and Si/Al ratios.
The work reported herein focused on synthesis of high-recycled-content hydraulic cements based primarily on alkali aluminosilicate chemistry using waste brick or impounded/landfilled coal ash as the primary aluminosilicate precursors. Emphasis was also made to take advantage of other supplementary wastes as raw materials in production of these hydraulic cements. An energy-efficient and environmentally friendly approach, relying upon mechanochemical phenomena, was employed in production of these high-recycled-content hydraulic cements. The hydraulic cement formulations considered in this investigation do not contain any Portland cement.
Materials and processing of hydraulic cements
Materials and their characteristics
The focus of this project was on market-limited wastes, relying upon the robust chemistry of aluminosilicate-based hydraulic cements to make effective use of them. The primary raw materials used in the project were the brick constituent of the construction and demolition (C&D) waste, and impounded/landfilled coal ash. The brick constituent of C&D waste was obtained from Hammond (Dewitt, Michigan). It was crushed using a Willey Mill (Standard Model 3) to produce millimetre-sized particles. Impounded coal ash was collected from a landfill containing the ash generated by a DTE power plant in Detroit, Michigan. This impounded ash was received in moist condition because it was exposed to weather in the landfill; the ash was dried in an oven at 110 °C to reach a constant mass. Other waste materials were also used in relatively small concentrations. Waste glass was obtained from Granger (Lansing, Michigan) and washed, dried and crushed/milled prior to use for production of hydraulic cement. Milled C&D gypsum waste was obtained from Builders Ready mix (Lansing, Michigan).
presents the chemical composition of the waste brick, waste glass and the impounded ash used in this study. Silicon and aluminium oxides constitute about 74% of the total mass of the waste brick. The waste glass comprises largely of SiO2 (61.6 wt.%). The presence of high calcium content in the waste glass (20.7%) could be important to the stability and long-term performance of alkali-activated binders (Lloyd, Provis, and Van Deventer Citation2010; Van Deventer, Provis, and Duxson Citation2012). also indicates that waste brick and glass have notable alkali metal content (5.88 wt.% in brick and 6.92 wt.% in glass). Availability of these alkalis would benefit formation of alkali aluminosilicate-based hydraulic cements. The impounded ash comprises primarily of SiO2, Al2O3 and Fe2O3 at 36.4, 18.2 and 30.6 wt.%, respectively. It also contains a relatively low CaO content, which qualifies it as a Class F coal ash. The impounded ash has a relatively high LOI of 18.4%, pointing at its high carbon content. The high LOI could also reflect the presence of carbonates like CaCO3.
Table 1. Chemical composition of waste brick, glass and impounded ash raw materials (wt.%).
The XRD spectra for waste brick, waste glass and the impounded ash are presented in . Waste brick observed to have a relatively high degree of crystallinity (69%), governed by the presence of quartz. Waste glass, as expected, is highly (>80%) amorphous. The major crystalline constituents of impounded ash include calcite (CaCO3) and quartz (SiO2). Thernadite (Na2SO4) and maghemite (Fe2O3) were also identified in smaller quantities. The presence of calcite could explain the relatively high LOI of the impounded ash.
shows SEM images of the as-received waste brick and the impounded ash used in this investigation. Waste brick was observed relatively dense and homogenous structure, which results from high-temperature processing of clay for production of brick (Karaman, Ersahin, and Gunal Citation2006). The impounded coal ash seems to be encrusted, etched and corroded, unlike coal fly ash particles that are normally have smooth outer surfaces (due to the formation under non-crowded free-fall conditions and rapid cooling (Mamane, Miller, and Dzubay Citation1986; Seames Citation2003). These morphological changes could be a result of leaching (Seames Citation2003) and formation of secondary mineral phases such as calcite (as noted in XRD spectra) on the surfaces of particles during storage (Yeheyis, Shang, and Yanful Citation2009).
To supplement the chemistry of waste raw materials, sodium carbonate, calcium oxide, magnesium oxide, Aluminium hydroxide and sodium hydroxide were used as sources of alkali/alkaline earth metal cations. These materials were purchased in powder form with 97–98% purity from Sigma Aldrich. Crushed granite with 12.5 mm maximum size was used as coarse aggregate, and natural sand with 4.75 mm maximum size was used as fine aggregate. The fineness modulus of the blend of coarse and fine aggregates was 4.3.
Processing of hydraulic cement
Blends of raw materials (wastes, alkali activators and additives) were mechanochemically processed through either ball-milling in a ceramic milling jar or grinding with a high speed mechanical grinder (24,000 RPM). In ball-milling, steel balls of 10–250 mm size were used, with solid-to-steel ball ratio of 1: 8. The speed of rotation was chosen to be in the range where milling media experiences ‘cascade’ action, that is, the balls gain enough energy to get up to a certain height and fall down, hitting other balls and the particles of powder at an angle of 45–60 degrees above the horizontal. The critical speed (rpm) was calculated as: n
C
= 42.29/, where d is the internal diameter of the milling jar (in metres) (Deniz Citation2004). The ball milling was performed at about 75% of the critical speed. The mill was filled with balls and materials to 40–60% of its volume. Ball-milling (BM) was carried out over a 2-h period, and high-speed grinding (HSG) over a 4-min period. These processes transferred the mechanical energy required for transforming the high-recycled-content blends of raw materials into hydraulic cements. The duration of milling was selected to produce hydraulic cements with specific surface area (ASTM C204 Blaine fineness) and mean particle size of about 3000 cm2/g and 15 μm, respectively.
Cement formulations
The formulations considered here produce chemical compositions comprising SiO2 (30–45%), Al2O3 (15–20%), MgO (0–3.6%) CaO (2–10%), Fe2O3 (10–20%), and Na2O (10–20%). ASTM C150 specifies a chemical composition for Type I Portland cement comprising CaO (60–65%), SiO2 (15–25%), Al2O3 (max 6%), Fe2O3 (max 6%) and MgO (max 6%), and equivalent alkalis (max of 0.6%). The hydraulic cements developed here are based on alkali aluminosilicate chemistry. Their Na2O, Al2O3 and Fe2O3 contents are higher than those for Portland cement, and their CaO content is lower than that of Portland cement.
Sodium carbonate was used as the primary source of alkali metal cations to destabilise/ disorder the aluminosilicate structure of the waste brick and impounded ash during mechanochemical processing (Feng, Provis, and Deventer Citation2012). The formulations of raw materials were devised to produce a desired chemical balance defined by the following molar ratios (M refers to Na or K): M2O/SiO2 of 0.2–0.48, SiO2/Al2O3 of 3.3–4.5, and M2O/Al2O3 of 0.8–1.6 (Komnitsas and Zaharaki Citation2007).
The alkalis used for activation of waste brick were sodium carbonate and magnesium oxide. The formulations derived based on trial-and-adjustment studies for production of hydraulic cements with relatively large volumes of waste brick are presented in . The presence of gypsum improves the solubility of the alumina that is present in waste brick (Provis Citation2009). Glass contributes amorphous silica and calcium for enhancement of long-term strength development. The presence of MgO in the raw materials of aluminosilicate-based hydraulic cements can benefit its rate of strength gain and ultimate strength by inducing the formation of hydrotalcite-like phases integrated into the base alkali aluminosilicate hydrate structure. The extent of strength gain depends upon the (alkaline) activator chemistry (Ben Haha et al. Citation2011).
Table 2. Brick-based cement formulations, wt.%.
Calcium oxide and sodium carbonate were used for activation of the impounded coal ash. Waste glass was also used at low concentration as a source of reactive silica, and potentially calcium oxide and sodium oxide. The formulations of raw materials used for processing into hydraulic cements are presented in . These formations were derived based on the chemical criteria outlined below, and after preliminary trial-and-adjustment investigations. Calcium oxide was used to enhance the aluminosilicate-based hydrates by forming calcium aluminosilicate hydrate gel (Lancellotti et al. Citation2013) . The presence of CaO lowers microstructural porosity, and thus improves the structure and properties of the resultant binder. It also benefits silicate and polysialate network formation, stimulating uniform hardening throughout the matrix and achieving higher early age strengths (Temuujin, Van Riessen, and Williams Citation2009). The addition of high contents of soluble aluminium compounds, such as Al(OH)3, lowers the Si/Al molar ratio, and thus raises the degree of crosslinking and moisture resistance of the resultant aluminosilicate hydrates (Fletcher et al. Citation2005; Rattanasak, Chindaprasirt, and Suwanvitaya Citation2010).
Table 3. Formulations (wt.%) of raw materials for production of hydraulic cements with impounded ash.
Concrete mix design
The resulting hydraulic cements were evaluated by testing concrete materials incorporating them. The base concrete mix design considered in this experimental work is presented in . The water content of concrete mixtures was adjusted to achieve comparable fresh mix workability with different (high-recycled-content) hydraulic cements. The 28-day strength targeted here was about 25 MPa which is the lower limit for normal-strength concrete.
Table 4. Concrete mix proportions.
A 20 Quart planetary mixer (Hobart A-200) was used to prepare the concrete mixtures. The hydraulic cement was added first to the mixer followed by water, and mixed for about 1 min at medium speed. Fine and coarse aggregates were added subsequently, followed by 3 min of mixing to produce a homogeneous fresh concrete mixture. The resulting fresh mix was cast into moulds for preparing 50 mm cubes, and consolidated via external vibration at medium speed for 3 min. The moulded specimens were kept in sealed condition, and were demoulded after 24 h. They were then subjected to room-temperature curing by simply sealing the specimens and storing them at room temperature until different test ages. Three replicated specimens were tested for each mix, and the mean values are reported under test results
Test methods
Compressive strength tests were performed, as a primary means of determining the quality of hydraulic cements, on cube specimens following the ASTM C109 procedures. Compression tests were performed at different ages on concrete materials prepared with various hydraulic cement formulations. Elemental analysis was performed using the X-ray fluorescence (XRF) technique. A Bruker S2 Ranger XRF spectrometer was used for this purpose. The mineralogy of raw materials was assessed via X-ray diffraction (XRD) using a Bruker D8 daVinci diffractometer equipped with Cu X-ray radiation operating at 40 kV and 40 mA. NMR Spectroscopy was used to identify different chemical environments associated with the coordinated state of Al. 27Al multiple-quantum MAS NMR (MQMAS) spectroscopy was used in this investigation. ATR-FTIR spectroscopy was used to assess the presence of bonds associated with chemically reacted species in raw materials, cements and cement paste. A JASCO FTIR-4100 system was used for performance of FTIR tests. Scanning electron microscopy was performed using a JEOL JSM-6610LV scanning electron microscope. Specimens were coated with a 20-nm thick platinum layer in an Emscope Sputter Coater model Sc 500 (Ashford, Kent, England) purged with Argon gas.
Results and discussion
Hydraulic cement formulated with waste brick
compares the cube concrete specimens prepared with the brick-based hydraulic cement subjected to mechanochemical processing via ball-milling and high-speed grinding. The hydrated concrete is observed to have the red colour of brick. This points at a common feature of alkali aluminosilicate cements where a lower degree of hydration than Portland cement is adequate for providing binding effects. With ball-milling ((a)), a uniform surface efflorescence was noted. This was not the case with high-speed grinding ((b)). Surface efflorescence with alkali aluminosilicate cements has been attributed to the migration of sodium cations to the surface where they carbonate and form sodium carbonate. This phenomenon points at the relative mobility (and abundance) of sodium cations within hydration products, which has been encountered in alkali activated binders irrespective of their production method (Škvára et al. Citation2009). This phenomenon relates to the specific chemistry of the hydration products, and tends to be more pronounced with room-temperature curing.
Figure 3. Visual appearances of concrete cube specimens prepared with hydraulic cement of Formulation 3 processed via ball milling (a), and high-speed grinding (b).
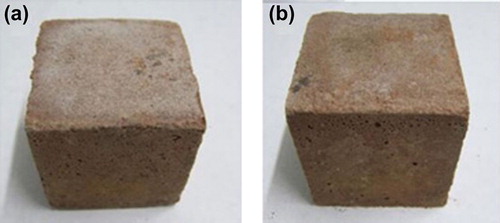
The mean values and 95% confidence intervals of the concrete compressive strength test results for the waste brick cement formulations subjected to different mechanochemical processing methods are presented in . Formulation 3 is observed to provide the highest compressive strengths of 22.1, 25.4 and 26.1 MPa after 3, 7 and 28 days, respectively, for room-temperature curing in sealed condition with high-speed grinding. These compressive strength levels (up to 27 MPa at 28 days of age) are comparable to those produced using Portland cement (Ahmadi and Shekarchi Citation2010) or blends of Portland cement and coal fly ash (Siddique Citation2004) with similar aggregate types and proportions. This preferred formulation incorporates gypsum at a relatively small dosage, which has probably raised the solubility of aluminium compounds, thus enhancing the networking and stability of the alkali aluminosilicate hydrate structure. When a small concentration of glass was used (Formulation 2), however, compressive strength was reduced in the case of ball-milled cements, which could be explained by the slow reactivity of amorphous silicate in waste glass. High-speed grinding of the cement formulation with glass raised the compressive strength of the resultant concrete, especially after 28 days of curing. At this age, introduction of waste glass into the formulation produced 12% gain in compressive strength. This can be attributed to the relatively low solubility of waste glass, which makes it more effective after longer-term curing (Schwarz and Neithalath Citation2008). This finding is consistent with the outcomes of a recent work which pointed at the favourable effects of dissolving waste glass in sodium silicates for geopolymer production (Redden and Neithalath Citation2014).
Figure 4. Compressive strength test results (means & 95% confidence intervals) for the brick-based hydraulic cement concrete materials.
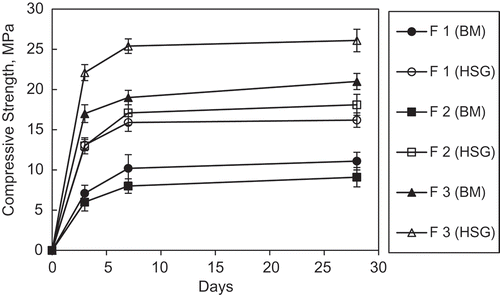
The compressive strength test results presented in indicate that high-speed grinding is more effective than ball-milling in mechanochemical processing of the raw materials into a hydraulic cement; this was despite the higher specific surface area of the resultant hydraulic cement processed via ball-milling (3877 cm2/g) versus high-speed grinding (2835 cm2/g). This finding points at the distinctions between the size reduction and mechanochemical effects of the milling action. Size reduction alone cannot be used as a measure of the strength development qualities of the hydraulic cement. Milling can also cause chemical and structural changes with effects that can overshadow those of size reduction. The compressive strengths of concrete materials made with ball-milled cements were about one-third of those made with cements subjected to high-speed grinding. This finding points at the need for intense input of mechanical energy to render thorough mechanochemical effects.
compares the FTIR spectra of as-received waste brick, brick-based (mechanochemically processed) cement, and the paste resulting from hydration of this cement. As-received brick has a major peak near 1060 cm−1, which can be attributed to asymmetric stretching of Si-O-T (T = Si or Al). When brick was mechanochemically processed into hydraulic cement, this Si-O peak shifted to a higher wavenumber (1060–1140 cm−1), indicating that mechanochemical effects alter the brick structure. This observation suggests that non-bridging oxygen atoms increased under mechanochemical effects, rendering the material more reactive (highly disordered, in high-energy state). This shift may also be caused by the formation of different structural units within the same silicate structure (Lee and van Deventer Citation2003). Also, Si-O bands for amorphous silica occur at approximately 1100 cm−1 (Handke and Mozgawa Citation1993), suggesting that mechanochemical activation increases the amorphous content. The shift is more pronounced with high-speed grinding (versus ball-milling), which correlates with the higher compressive strength achieved with the use of high-speed grinding. Upon hydration, the Si-O-T peaks were shifted to lower numbers, indicating that the peaks at 990 cm−1 are due to Si-O-Si or Si-O-Al bonds (corresponding to geopolymer binders). The band at around 1096 cm−1 is associated with the Si-OH bond of hydrates (Dimas, Giannopoulou, and Panias Citation2009), and that at 1060 cm−1 is due to Si-O (non-bonded oxygen) (Q3) (Serra et al. Citation2003). The bands at 1470 cm−1 are attributed to the stretching vibration of O-C-O bonds of , reflecting the possibility of carbonation reactions occurring during or after hydration. The signal identified at ~860 cm−1 corresponds to the asymmetric stretching vibration of the tetrahedrally coordinated Al present in the formed gel, which corroborates the presence of (geopolymer) structures comprising tetrahedral SiO4 and AlO4, distributed in different configurations (Granizo, Blanco-Varela, and Martínez-Ramírez Citation2007).
Figure 5. FTIR spectra of as-received brick, brick-based hydraulic cement, and the paste resulting from hydration of this cement.
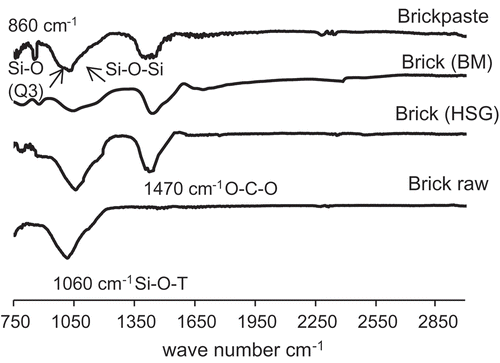
The effects of mechanochemical processing on transformation of brick waste (and other raw materials) into hydraulic cement were further investigated via solid-state 27Al NMR spectroscopy (). The single pulse data (not shown) are broad, and very hard to interpret directly (due to the presence of high iron content in brick and quadrupolar coupling of aluminium nuclei). However, using a 2D method called MQMAS, we could separate out signals from 4- and 6-coordinate Al species. Comparing the two data-sets, a strong sideband pattern for the 4-coordinated Al in the hydraulic cement subjected to high-speed grinding, and a corresponding shift in peak position lowering of the intensity of the additional 4-coordinated Al peak were observed. This points at the possibility of forming new 6-coordinated aluminium species due to the incorporation of alkalis into the aluminosilicate structure via the grinding action and size reduction.
Figure 6. 27Al MQ/MAS NMR Data ((a): waste brick and (b): mechanochemically processed brick-based hydraulic cement).
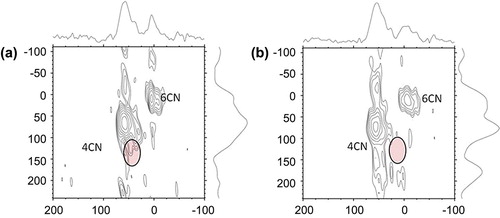
presents an SEM image and EDS mapping covering two different regions of the SEM image the paste component of concrete materials made with hydraulic cements formulated with waste brick (Formulation 3). The microstructure comprises micrometre-scale granules which are bonded together by hydration products. This observation has been made with other alkali activated systems where hydration via dissolution and through-solution reactions occurs mostly at the surfaces of hydraulic cement particles, leaving the cores of particles as well-bonded fillers within hydration products. This microstructure has also been observed in the case of conventional geopolymer binders produced via alkali activation of aluminosilicate precursors (Van Jaarsveld, Van Deventer, and Lukey Citation2003; Duxson et al. Citation2007). The EDS spectra for Regions 1 and 2 exhibit Si/Al molar ratios of 2.9 and 1.85, respectively, which are close to the recommended Si/Al molar ratio of about 2 for geopolymer binders (Davidovits Citation1989; Xu and van Deventer Citation2003). This can be used to explain the high strength of the waste brick-based hydraulic cement concrete. It is interesting to note that the region with high Ca content also had a high Na content (Region1).
Hydraulic cement formulated with impounded coal ash
The mean values of compressive strength for concrete materials prepared with hydraulic cement formulations developed with high impounded ash contents are presented in . Viable levels of compressive strength were obtained with the impounded coal ash-based hydraulic cements. The basic formulation (Formulation 4) provided the highest compressive strengths at all ages (15.4, 19.2 and 23.4 MPa at 3, 7 and 28 days, respectively). Using 10% Al(OH)3 (Formulation 5) reduces the compressive strength at all ages.
Figure 8. Compressive strength test results (means & 95% confidence intervals) for the impounded ash-based hydraulic cement concrete materials.
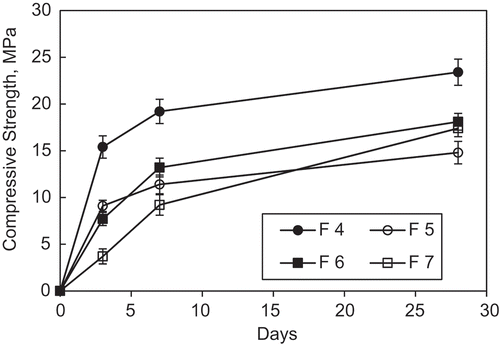
Formulation 5 produced relatively low compressive strengths when compared with Formulation 4. Replacement of 5 wt.% of impounded ash with waste glass in Formulation 5, which yielded Formulation 6, raised the compressive strength by more than 15 and 18% after 7 and 28 days, respectively. Introduction of waste glass lowered the water requirement for achieving a desired fresh mix workability (with water/cement ratio dropping from 0.47 to 0.44, which could be due to the low sorption rate of glass powder when compared with ash particles). The low reactivity of glass could lower the initial concentration of silicon cations in solution, enabling incorporation of higher alumina contents into alkali aluminosilicate hydrates. This would raise the degree of cross-linking of hydrates, thus benefiting the structure and properties of the resulting binders and concrete materials. Using 10 wt.% CaO in Formulation 7 produced a significant rise in compressive strength. Formulation 7 provided a relatively low compressive strength after 3 days (~3.5 MPa). Its rate of strength gain accelerated after 7 days, achieving a compressive strength of 17.4 MPa after 28 days.
An SEM image and EDS analysis of the impounded ash-based hydraulic cement paste (Formulation 7) is shown in . This typical image points at the achievement of an advanced stage of hydration, with products of hydration covering the non-hydrated cores of cement particles. Similar to the hydrated paste of waste brick-based cements, the hydrates of impounded ash-based cement exhibited a microstructure comprising micrometre-scale granules which integrated (bonded) by hydration products. This is typical of alkali activated materials where hydration products bond the unreacted cores of original particles to form a solid binder (Fernández-Jiménez, Palomo, and Criado Citation2005). The hydration products in Region 1 of the SEM image exhibit high concentrations of calcium, sodium, aluminium and silica. Region 1 has a Ca/Si molar ratio of 2.3 with a relatively low Si/Al molar ratio of 1.2. This Ca/Si molar ratio detected via EDS is very close to those in the C-A-S-H gel of geopolymer binders (Garcia-Lodeiro et al. Citation2011; García-Lodeiro, Fernández-Jiménez, and Palomo Citation2013). This could point at the formation of calcium aluminosilicate hydrates. Region 2 of the SEM image has a high Si concentration with very low Al and Ca contents.
The compressive strengths achieved in this study (Brick-Formulation 3 HSG, and Impounded ash (Formulation 7) were in the 19–24 MPa rage at 7 days and 24–27 MPa range at 28 days. For Portland cement concrete, the compressive strengths achieved with similar aggregates and mix designs were 23 and 28 MPa at 7 and 28 days, respectively (Ahmadi and Shekarchi Citation2010). Other investigations on similar mixed, which concerned partial replacement of Portland cement with fly ash, indicated that Portland cement: coal fly ash at 55: 45 weight ratios produced compressive strengths of 15.3 and 24.7 MPa at 7 and 28 days, respectively (Siddique Citation2004). Hence, the compressive strengths achieved with some of the hydraulic cement formulations developed in this project are competitive when compared with Portland cement or blends of Portland cement and coal fly ash.
Conclusions
A sustainable class of hydraulic cements based on alkali aluminosilicate chemistry was developed. The robust chemistry of this cement allows for large-volume use of market-limited wastes as primary raw materials. The energy-efficient mechanochemical approach devised to processing of this cement further benefits its sustainability. Waste brick and impounded ash were evaluated as aluminosilicate precursors in processing of hydraulic cements. Relatively small concentrations of compounds incorporating alkali/alkaline earth metal cations were required to produce a viable chemistry of raw materials. The mechanochemical process transformed the blend of raw materials into a hydraulic cement comprising disordered aluminosilicate framework embodying alkali/alkaline earth metal cations. Evaluation of the resultant hydraulic cements yielded the following conclusions.
The aluminosilicate precursors used in the project (waste brick and impounded ash) provided viable SiO2/Al2O3 ratios for production of alkali aluminosilicate-based hydraulic cements. The degree of crystallinity of waste brick, however, was found to be relatively high. In spite of this, mechanochemical processing of raw materials formulations with brick as the primary aluminosilicate precursor produced, after mechanochemical processing, a desirable disordered structure marked by shifting of the Si-O bond FTIR spectral peak. More intense milling actions benefited these structural changes in waste brick in the presence of other raw materials. The waste brick-based hydraulic cement formulation comprising waste brick: waste glass: Na2CO3: C&D gypsum waste at 68: 3.5: 25: 3.5 weight ratios, processed via high-speed grinding, produced 28-day compressive strengths approaching 26 MPa.
Impounded ash was also found to be a viable aluminosilicate precursor for production of alkali activated hydraulic cements. The formulation comprising impounded ash: Na2CO3 at 70: 30 weight ratios, processed mechanochemically via ball-milling, produced 28-day compressive strengths approaching 24 MPa.
The compressive strength test data pointed at the promise of the approach to transform market-limited wastes that are abundantly available into technically viable and sustainable hydraulic cements for concrete production.
The microstructure of hydrated cement pastes comprised aluminosilicate gel structures which thoroughly covered and bound the non-hydrated cores of cement particles. There was a prevalence of Al, Si and Ca within the products of cement hydration. The chemistry of cement hydrates points at the presence of calcium aluminosilicate hydrate as a prevalent binding gel.
The work reported herein has established the merits of some abundant market-limited wastes for production of alkali aluminosilicate-based hydraulic cements. The findings of this research warrant further development and characterisation of these hydraulic cements. Weathering resistance, and dimensional and chemical stability of some important aspects of the cement hydrates that need to be investigated.
Disclosure statement
The authors declare that they have no conflict of interest.
Funding
This work was supported by the U.S. Environmental Protection Agency [grant number EPD-D-15-036].
Notes on contributors
Faris Matalkah received his PhD in Civil Engineering from Michigan State University, Unites States. He is currently an assistant professor of Civil Engineering at Yarmouk University, Jordan. His research interests include development of sustainable, energy-efficient and low-cost cementitious materials. His previous publications have appeared in Construction and Building Materials, Concrete International, Advances in Cement Research and others.
Mohamed Mahmoud received his MS in Civil Engineering from Michigan State University, Unites States. His research interest is toward development of sustainable hydraulic cements using locally available materials.
A.G.N.D Darsanasiri received his MSc in Chemistry and MPhil in Biotechnology and Nanochemistry, he is a research scientist at Metna Company. His research and professional experience is focused on material characterization and formulation development in material science, and biotechnology and nanotechnology. He has presented papers at conferences and, published articles and papers in various journals.
Nastaran Abdol received his BS in Chemistry, she is a laboratory specialist at Metna Company. Her research interest includes material characterization, processing and fabrication of advanced materials. Her previous publications have appeared in Carbon, JOJ Material Science, and Industrial and Engineering Chemistry Research and others.
Parviz Soroushian, PE, FACI, FASCE , received his PhD from Cornell University, is a professor of Civil and Environmental Engineering at Michigan State University. His research focuses on advanced structural and environmental friendly, materials. His research interests include materials science and engineering, and sustainable construction materials and systems. His background includes research and development of technologies concerning structural applications of nanocomposites, reinforcing fibers for composites and smart materials and structural systems. He currently serves as the president of Metna Company.
Anagi M. Balachandra received her PhD in Analytical chemistry from Michigan State University and MS in Analytical Chemistry from Eastern Michigan University, and BS in Chemistry Hons., she is currently serving as the senior research scientist at Metna Company. Her research focuses on polymer chemistry and materials that integrates fundamental studies for the development of nanostructured and advanced materials. Her professional experience covers 10+ years of industrial research, development and commercialization in the field of materials science and engineering. Her recent publications appeared in Macromolecules, Carbon, Journal of Material Science, Construction and Building Materials and others. Also one of her co-authored article was recently selected for “2017 Best Paper Award” in Cogent Engineering.
References
- Ahmadi, Babak, and Mohammad Shekarchi. 2010. “Use of Natural Zeolite as a Supplementary Cementitious Material.” Cement and Concrete Composites 32 (2): 134–141.10.1016/j.cemconcomp.2009.10.006
- Ahmari, Saeed, Xin Ren, Vahab Toufigh, and Lianyang Zhang. 2012. “Production of Geopolymeric Binder from Blended Waste Concrete Powder and Fly Ash.” Construction and Building Materials 35: 718–729.10.1016/j.conbuildmat.2012.04.044
- Anseau, Michel R., Jennifer P. Leung, Nita Sahai, and Thomas W. Swaddle. 2005. “Interactions of Silicate Ions with Zinc(II) and Aluminum(III) in Alkaline Aqueous Solution.” Inorganic Chemistry 44 (22): 8023–8032.10.1021/ic050594c
- Ben Haha, M., B. Lothenbach, G. Le Saout, and F. Winnefeld. 2011. “Influence of Slag Chemistry on the Hydration of Alkali-activated Blast-furnace Slag – Part I: Effect of MgO.” Cement and Concrete Research 41 (9): 955–963. doi:10.1016/j.cemconres.2011.05.002.
- Carlson, Claire L., and Domy C. Adriano. 1993. “Environmental Impacts of Coal Combustion Residues.” Journal of Environment Quality 22 (2): 227–247.10.2134/jeq1993.00472425002200020002x
- Davidovits, Joseph. 1989. “Geopolymers and Geopolymeric Materials.” Journal of Thermal Analysis 35 (2): 429–441.10.1007/BF01904446
- Davidovits, Joseph. 1994. “Global Warming Impact on the Cement and Aggregates Industries.” World Resource Review 6 (2): 263–278.
- Deniz, V. 2004. “The Effect of Mill Speed on Kinetic Breakage Parameters of Clinker and Limestone.” Cement and Concrete Research 34 (8): 1365–1371.10.1016/j.cemconres.2003.12.025
- Dimas, D., I. Giannopoulou, and D. Panias. 2009. “Polymerization in Sodium Silicate Solutions: A Fundamental Process in Geopolymerization Technology.” Journal of Materials Science 44 (14): 3719–3730.10.1007/s10853-009-3497-5
- Duxson, Peter, Ana Fernández-Jiménez, John L. Provis, Grant C. Lukey, Angel Palomo, and J. S. J. Van Deventer. 2007. “Geopolymer Technology: The Current State of the Art.” Journal of Materials Science 42 (9): 2917–2933.10.1007/s10853-006-0637-z
- Feng, Dingwu, John L. Provis, and Jannie S. J. Deventer. 2012. “Thermal Activation of Albite for the Synthesis of One-part Mix Geopolymers.” Journal of the American Ceramic Society 95 (2): 565–572.10.1111/jace.2012.95.issue-2
- Fernández-Jiménez, Ana, A. Palomo, and M. Criado. 2005. “Microstructure Development of Alkali-activated Fly Ash Cement: A Descriptive Model.” Cement and Concrete Research 35 (6): 1204–1209.10.1016/j.cemconres.2004.08.021
- Fletcher, R. A., K. J. D. MacKenzie, C. L. Nicholson, and S. Shimada. 2005. “The Composition Range of Aluminosilicate Geopolymers.” Journal of the European Ceramic Society 25 (9): 1471–1477. doi:10.1016/j.jeurceramsoc.2004.06.001.
- Galiano, Y. Luna, C. Fernández Pereira, and J. Vale. 2011. “Stabilization/Solidification of a Municipal Solid Waste Incineration Residue Using Fly Ash-based Geopolymers.” Journal of Hazardous Materials 185 (1): 373–381.10.1016/j.jhazmat.2010.08.127
- García-Lodeiro, I., A. Fernández-Jiménez, and A. Palomo. 2013. “Variation in Hybrid Cements Over Time. Alkaline Activation of Fly Ash–portland Cement Blends.” Cement and Concrete Research 52: 112–122.10.1016/j.cemconres.2013.03.022
- Garcia-Lodeiro, I., A. Palomo, Ana Fernández-Jiménez, and D. E. Macphee. 2011. “Compatibility studies between N-A-S-H and C-A-S-H Gels. Study in the Ternary Diagram Na2O–CaO–Al2O3–SiO2–H2O.” Cement and Concrete Research 41 (9): 923–931.10.1016/j.cemconres.2011.05.006
- Gonçalves, J. P., L. M. Tavares, R. D. Toledo Filho, and E. M. R. Fairbairn. 2009. “Performance Evaluation of Cement Mortars Modified with Metakaolin or Ground Brick.” Construction and Building Materials 23 (5): 1971–1979.10.1016/j.conbuildmat.2008.08.027
- Granizo, M. Luz, María Teresa Blanco-Varela, and Sagrario Martínez-Ramírez. 2007. “Alkali Activation of Metakaolins: Parameters Affecting Mechanical, Structural and Microstructural Properties.” Journal of Materials Science 42 (9): 2934–2943.10.1007/s10853-006-0565-y
- Handke, Mirosław, and Włodzimierz Mozgawa. 1993. “Vibrational Spectroscopy of the Amorphous Silicates.” Vibrational Spectroscopy 5 (1): 75–84.10.1016/0924-2031(93)87057-Z
- Karaman, Sedat, Sabit Ersahin, and Hikmet Gunal. 2006. “Firing Temperature and Firing Time Influence on Mechanical and Physical Properties of Clay Bricks.” Journal of Scientific and Industrial Research 65 (2): 153–159.
- Khatib, J. M., and S. Wild. 1996. “Pore size Distribution of Metakaolin Paste.” Cement and Concrete Research 26 (10): 1545–1553.10.1016/0008-8846(96)00147-0
- Kinuthia, J. M., and R. M. Nidzam. 2011. “Towards Zero Industrial Waste: Utilisation of Brick Dust Waste in Sustainable Construction.” Waste Management 31 (8): 1867–1878.10.1016/j.wasman.2011.03.020
- Komnitsas, Kostas, and Dimitra Zaharaki. 2007. “Geopolymerisation: A Review and Prospects for the Minerals Industry.” Minerals Engineering 20 (14): 1261–1277. doi:10.1016/j.mineng.2007.07.011.
- Lancellotti, I., M. Catauro, C. Ponzoni, F. Bollino, and C. Leonelli. 2013. “Inorganic Polymers from Alkali Activation of Metakaolin: Effect of Setting and Curing on Structure.” Journal of Solid State Chemistry 200: 341–348. doi:10.1016/j.jssc.2013.02.003.
- Lee, W. K. W., and J. S. J. van Deventer. 2003. “Use of Infrared Spectroscopy to Study Geopolymerization of Heterogeneous Amorphous Aluminosilicates.” Langmuir 19 (21): 8726–8734. doi:10.1021/la026127e.
- Lloyd, Redmond R., John L. Provis, and Jannie S. J. Van Deventer. 2010. “Pore Solution Composition and Alkali Diffusion in Inorganic Polymer Cement.” Cement and Concrete Research 40 (9): 1386–1392.10.1016/j.cemconres.2010.04.008
- Mamane, Y., J. L. Miller, and T. G. Dzubay. 1986. “Characterization of Individual Fly Ash Particles Emitted from Coal-and Oil-fired Power Plants.” Atmospheric Environment (1967) 20 (11): 2125–2135.10.1016/0004-6981(86)90306-9
- Papadakis, V. G., and S. Tsimas. 2002. “Supplementary Cementing Materials in Concrete.” Cement and Concrete Research 32 (10): 1525–1532.10.1016/S0008-8846(02)00827-X
- Parande, A. K., P. L. Ramsamy, S. Ethirajan, C. R. K. Rao, and N. Palanisamy. 2006. “Deterioration of Reinforced Concrete in Sewer Environments.” Proceedings of the Institution of Civil Engineers-municipal Engineer 159 (MEI): 11–20.
- Peng, Mei Xun, Zheng Hong Wang, Qiu Guo Xiao, Fei Song, Wen Xie, Liang Cai Yu, Hao Wen Huang, and Shou Jun Yi. 2017. “Effects of Alkali on One-part Alkali-activated Cement Synthesized by Calcining Bentonite with Dolomite and Na2CO3.” Applied Clay Science 139: 64–71.10.1016/j.clay.2017.01.020
- Provis, J. L. 2009. “Activating Solution Chemistry for Geopolymers.” Geopolymers: Structures, Processing, Properties and Industrial Applications. 50–71: Woodhead Publishing10.1533/9781845696382.1.50
- Rattanasak, Ubolluk, Prinya Chindaprasirt, and Prasert Suwanvitaya. 2010. “Development of High Volume Rice Husk Ash Alumino Silicate Composites.” International Journal of Minerals, Metallurgy, and Materials 17 (5): 654–659.10.1007/s12613-010-0370-0
- Redden, Rachel, and Narayanan Neithalath. 2014. “Microstructure, Strength, and Moisture Stability of Alkali Activated Glass Powder-based Binders.” Cement and Concrete Composites 45: 46–56.10.1016/j.cemconcomp.2013.09.011
- Rostami, Hossein, and William Brendley. 2003. “Alkali Ash Material: A Novel Fly Ash-based Cement.” Environmental Science & Technology 37 (15): 3454–3457. doi:10.1021/es026317b.
- Schwarz, Nathan, and Narayanan Neithalath. 2008. “Influence of a Fine Glass Powder on Cement Hydration: Comparison to Fly Ash and Modeling the Degree of Hydration.” Cement and Concrete Research 38 (4): 429–436.10.1016/j.cemconres.2007.12.001
- Seames, Wayne S. 2003. “An Initial Study of the Fine Fragmentation Fly Ash Particle Mode Generated during Pulverized Coal Combustion.” Fuel Processing Technology 81 (2): 109–125.10.1016/S0378-3820(03)00006-7
- Serra, J., P. González, S. Liste, C. Serra, S. Chiussi, B. León, M. Pérez-Amor, H. O. Ylänen, and M. Hupa. 2003. “FTIR and XPS Studies of Bioactive Silica Based Glasses.” Journal of Non-crystalline Solids 332 (1–3): 20–27.10.1016/j.jnoncrysol.2003.09.013
- Shi, Caijun, and A. Fernandez-Jimenez. 2006. “Stabilization/Solidification of Hazardous and Radioactive Wastes with Alkali-activated Cements.” Journal of Hazardous Materials 137 (3): 1656–1663.10.1016/j.jhazmat.2006.05.008
- Siddique, Rafat. 2004. “Performance Characteristics of High-volume Class F Fly Ash Concrete.” Cement and Concrete Research 34 (3): 487–493.10.1016/j.cemconres.2003.09.002
- Škvára, František, Lubomír Kopecký, V. Lenka Myšková, Lucie Alberovska Šmilauer, and Lenka Vinšová. 2009. “Aluminosilicate Polymers–Influence of Elevated Temperatures, Efflorescence.” Ceramics-Silikáty 53 (4): 276–282.
- Smith, Alison, Keith Brown, Steve Ogilvie, Kathryn Rushton, and Judith Bates. 2001. “Waste Management Options and Climate Change: Final Report to the European Commission.” In Waste Management Options and Climate Change: Final Report to the European Commission. DG Enviornment: European Commission.
- Tchadjié, L. N., J. N. Y. Djobo, N. Ranjbar, H. K. Tchakouté, B. B. D. Kenne, A. Elimbi, and D. Njopwouo. 2016. “Potential of Using Granite Waste as Raw Material for Geopolymer Synthesis.” Ceramics International 42 (2): 3046–3055.10.1016/j.ceramint.2015.10.091
- Temuujin, J., A. Van Riessen, and R. Williams. 2009. “Influence of Calcium Compounds on the Mechanical Properties of Fly Ash Geopolymer Pastes.” Journal of Hazardous Materials 167 (1–3): 82–88.10.1016/j.jhazmat.2008.12.121
- Van Deventer, Jannie S. J., John L. Provis, and Peter Duxson. 2012. “Technical and Commercial Progress in the Adoption of Geopolymer Cement.” Minerals Engineering 29: 89–104.10.1016/j.mineng.2011.09.009
- Van Jaarsveld, J. G. S., J. S. J. Van Deventer, and G. C. Lukey. 2003. “The Characterisation of Source Materials in Fly Ash-based Geopolymers.” Materials Letters 57 (7): 1272–1280.10.1016/S0167-577X(02)00971-0
- Veranth, John M., David W. Pershing, Adel F. Sarofim, and Jeffrey E. Shield. 1998. “Sources of Unburned Carbon in the Fly Ash Produced from Low-NO x Pulverized Coal Combustion.” Symposium (International) on Combustion 27 (2): 1737–1744.
- Xu, Hua, and Jannie S. J. van Deventer. 2003. “Effect of Source Materials on Geopolymerization.” Industrial & Engineering Chemistry Research 42 (8): 1698–1706. doi:10.1021/ie0206958.
- Yeheyis, Muluken B., Julie Q. Shang, and Ernest K. Yanful. 2009. “Chemical and Mineralogical Transformations of Coal Fly Ash after Landfilling.” World of Coal Ash Conference, Lexington, Kentucky.