ABSTRACT
Waste materials are often used in brick manufacturing to develop a sustainable building material and reduce the consumption of natural clay resources. In this study, palm oil fuel ash (POFA), a waste generated from the palm oil industry, was used in brick production as clay replacement at dosages of 5, 10, 15 and 20% by weight. The brick specimens were produced in a local factory to study the feasibility of manufacturing bricks containing POFA under real industrial production conditions and their properties were compared with conventional bricks (0% POFA). The results show that a lighter brick is produced when mixed with POFA but the flexural and compressive strength decreased. Water absorption and initial rate of absorption increased when clay is mixed with POFA due to the presence of a more porous structure than conventional bricks. Further, brick specimens containing POFA had a higher resistance to the formation of efflorescence than conventional bricks; however, their resistance was poor when subjected to sulphate attack. The findings of this study suggest that up to 5% POFA can be used as clay replacement for bricks produced in a local brick kiln industry to meet the current international standards for conventional bricks.
1. Introduction
Bricks are commonly used as the construction material for walls in buildings and their use continues to increase year on year. However, the depletion of clay deposits due to the increasing production of bricks has become an environmental issue. Approximately 3.13 billion m3 of clay soil is required each year for brick manufacturing, and this demand is predicted to increase in the future (Mohajerani et al. Citation2019). This situation demands alternative new materials that can be used to replace clay in brick production. At the same time, the huge amount of waste material generated from palm oil industry including palm oil fuel ash (POFA) can be used as an alternative material in the manufacturing of bricks. In this study, an attempt is made to utilise this waste for brick production.
Indonesia is the largest palm-oil-producing country in the world, accounting for approximately 48% of global production in 2011 (Gatto, Wollni, and Qaim Citation2015). The biomass solid waste generated after the palm oil extraction process, such as palm kernel shells, mesocarp fibre, and empty fruit brunches, is mainly used as fuel in palm oil mills or power plants to produce electricity when combusted at temperatures of 800–1000°C (Mushtaq et al. Citation2015; Umar, Jennings, and Urmee Citation2013). After combustion, approximately 5% of the solid waste material is POFA (Sata, Jaturapitakkul, and Kiattikomol Citation2004). As a result of its low nutritional value, POFA is mostly disposed in open fields, which creates environmental problems and health issues including lung disease (Tay and Show Citation1995). The disposal of POFA is, therefore, a significant challenge for the palm oil industry. Recognising this, POFA has great potential to be used as a locally produced raw material in brick manufacturing to reduce environmental impact and reduce brick production costs.
2. Literature review
2.1. Existing studies
The property of bricks is mainly influenced by the manufacturing process and the characteristics of the raw materials (Abbas et al. Citation2017). Attempts have been made to find alternative materials that can be used to replace clay in brick production, such as industrial and agricultural waste materials. For instance, the production of bricks by mixing fly ash and clay has been suggested (Abbas et al. Citation2017; Leiva et al. Citation2016; Lingling et al. Citation2005). Leiva et al. (Citation2016) reported that the compressive strength of fly ash-clay bricks depends on the firing temperature; increases in compressive strength were observed at a firing temperature of 1000 °C and this decreased with higher proportions of fly ash content and at lower firing temperatures. A lighter brick can be produced with fly ash, which reduces transportation and labour costs, offers easier handling, and reduces the overall weight of structures (Abbas et al. Citation2017).
The use of waste glass in brick manufacturing has been shown to enhance strength and increase resistance against sulphate attack, freeze–thaw, and efflorescence-driven degradation (Kazmi et al. Citation2017; Djangang et al. Citation2014). The replacement of 15% of the clay content with brick kiln dust produced bricks that satisfy the compressive strength requirements of second-class bricks when used for ordinary masonry construction, and provides higher resistance against efflorescence (Riaz, Khitab, and Ahmed Citation2019). The replacement of 40% of the clay content with ceramic sludge and firing at 850 °C produced bricks with a 32% improvement in compressive strength compared with conventional bricks categorised as having moderate weathering resistance and better thermal performance (Subashi De Silva and Hansamali Citation2019). Furthermore, incorporating 40–60% quarry residues in clay bricks has been shown to increase the compressive strength by a factor or 1.5 relative to normal clay bricks at firing temperatures of 1000–1100 °C (Rukijkanpanich and Thongchai Citation2019).
Agricultural waste materials such as rice husk, rice husk ash (RHA), and sugarcane bagasse ash (SBA) have also been used to replace clay in brick production. The replacement of clay with rice husk ash in relatively low proportions (i.e., 4% by weight) was shown to provide better structural, thermal, and acoustic properties than conventional clay bricks (Subashi De Silva and Perera Citation2018). Similarly, incorporating RHA produces lighter bricks with improved resistance against efflorescence (Kazmi et al. Citation2016a). However, brick porosity increases with > 5% RHA content by weight of clay, leading to increases in water absorption (Kazmi et al. Citation2016a; Andreloa et al. Citation2018). Furthermore, incorporating SBA at proportions of up to 5% by weight of clay produced bricks that satisfy the international standard for burnt clay bricks (Kazmi et al. Citation2016a; Faria, Gurgel, and Holanda Citation2012).
Agricultural solid waste materials including rice husk and palm oil shell can be used as additive in brick production. Lighter bricks were obtained with the addition of rice husk owing to increase in the porosity of the bricks; thus, it reduced the compressive strength of the bricks (Gorhan and Simsek Citation2013; Sutas, Mana, and Pitak Citation2012). However, the addition of 5% and 10% rice husk yielded a compressive strength of 7–10 MPa, which can be used for indoor structural walling materials with a lower thermal conductivity (Gorhan and Simsek Citation2013). Similarly, the addition of 3% palm fibre and palm kernel shell into clay bricks increased the porosity followed by a decrease in density, thermal conductivity, and compressive strength (Kadir, Zahari, and Mardi Citation2013).
POFA has been used as a replacement for clay to reduce its environmental impact and brick production costs. In their study, Kadir and Sarani (Citation2020) produced bricks with different proportions of POFA, that is 0, 1, 5, 10, 20 and 30% by clay weight, and firing in a furnace at a temperature of 1050 °C. Their study found that the addition of POFA decreased the compressive strength of bricks but produced lightweight bricks owing to the higher porosity, and up to 5% POFA was considered as optimum replacement for producing non-load bearing bricks. Another study by Elhusna and Wahyuni (Citation2016) also found similar results in which the addition of POFA decreased the compressive strength and increased the absorption capacity of bricks.
Since the properties of bricks are mainly influenced by the manufacturing process including the preparation and firing method, the feasibility of POFA as clay replacement under real industrial production conditions in a larger scale should be investigated. The method of manufacturing bricks in the laboratory and in a real industrial condition may differ, which significantly affects the properties. Furthermore, existing research on the durability properties of POFA-containing bricks (initial rate absorption, efflorescence, and sulphate resistance) is very rare. In the present study, POFA was used as a replacement for clay at dosages of 5, 10, 15 and 20% by weight of clay for manufacturing bricks in local industrial kilns on a large scale, and their mechanical and durability properties were compared with those of conventional bricks without POFA.
2.2. Research significance
The use of clay for producing bricks on a large scale can reduce the use of natural clay deposits, which has a negative impact on the environment. Natural clay, which is non-renewable, is at risk of being depleted, and urgent measures are required to ensure its preservation. On the other hand, the environmental burden due to the generated industrial waste as a result of inefficient waste management systems increases every year.
This study investigates the feasibility of using POFA as clay replacement for bricks production in a large scale. In a real industrial condition, conventional bricks are produced on a large scale in a brick kiln, unlike the approach in previous studies (Kadir and Sarani Citation2020; Elhusna and Wahyuni Citation2016) in which a controlled firing temperature was used in the laboratory. Different production methods can affect the brick properties. The primary objective of this study therefore, is to investigate the mechanical and durability properties of POFA-containing bricks manufactured under full-scale production conditions compared with those of conventional bricks. This study aims to fill the research gap in this subject area, as well as promote a sustainable approach to the utilisation of POFA as clay replacement in the brick industry.
In addition, as the highest palm-oil-producing country in the world, Indonesia produces a huge amount of POFA annually, which causes significant environmental impact. Therefore, the use of POFA as a locally produced raw material for brick manufacturing can reduce the negative environmental impact of the material and brick production costs.
3. Materials and methods
3.1. Materials
Clay materials were obtained from local kiln bricks in Makassar, Indonesia, and POFA materials were obtained from the local palm oil industry. The chemical properties of the clay and POFA materials were determined using X-Ray fluorescence (XRF), the results of which are presented in . The clay is composed of 56.62% SiO2 along with 13.55, 9.97, 7.83 and 5.80% of Al2O3, CaO, Fe2O3 and K2O, respectively. Other oxides including TiO2, MnO, and SrO are also present in small quantities. Clay containing 50–60% SiO2 is commonly used in local brick factories (Velasco et al. Citation2014). Here, the SiO2 content of the clay met this specified range, and having a CaO content of more than 6%, the clay is classified as calcareous with low refractory properties (Netinger et al. Citation2014; Musthafa, Janaki, and Velraj Citation2010). The POFA contains a high amount of SiO2 (67.74%) and, to a lesser extent, K2O (7.51%), Fe2O3 (6.13%), P2O5 (5.84%), Al2O3 (5.67%) and CaO (5.64%). The high K2O content is as a result of the uptake of K2O from the soil by the palm oil trees during the cultivation period (Thomas, Kumar, and Arel Citation2017). The loss on ignition (LOI) of the POFA is higher than that of the clay, which is attributed to the presence of organic matter in the ash. In addition, the specific gravity of the POFA (2.12) is lower than that of the clay (2.24). Therefore, the use of POFA as a replacement for clay should result in lighter bricks.
Table 1. Chemical properties of clay and POFA
The X-Ray diffraction (XRD) patterns of the clay and POFA are shown in . The clay shows the presence of the following crystalline phases: quartz (SiO2), calcite (CaCO3), haematite (Fe2O3), and alumina (Al2O3), with quartz (SiO2) being dominant. On the other hand, the POFA is comprised of quartz (SiO2), potassium aluminium phosphate (K3Al2 (PO4)3), calcite (CaCO3), and haematite (Fe2O3), also with a significant quantity of quartz (SiO2). These results are consistent with the XRF data.
shows the particle size distribution curve of the clay and POFA. The POFA is finer than the clay; the clay consists of 97.12% and 2.88% sand and silt, respectively, whereas the POFA contains 77.46% and 22.54% sand and silt, respectively. The gradation of such raw materials is another important parameter affecting the porosity of bricks (Murari et al. Citation2015).
Scanning electron microscope (SEM) images of the clay and POFA are shown in . The clay has irregularly shaped particles, whereas the POFA particles are more angular and irregular in form, with a porous surface texture. Both the clay and the POFA contain different particles sizes, which agree with the particle size analysis result.
3.2. Preparation and testing of bricks
Bricks were produced by mixing the clay with various percentages of POFA, specifically 0 (control), 5, 10, 15 and 20% by weight of clay (). The amount of water added to the mixture was adjusted to achieve a casting consistency according to factory standards. The mixtures were then cast into brick moulds (220 mm x 100 mm x 50 mm) without applying pressure, which is common for local brick production. The brick specimens were dried for 8 days in sunlight before being transferred to a brick kiln. The bricks were fired at 750–850 °C for 96 h using wood and rice husk as fuel. After the burning process, the specimens were cooled for an additional 14 days before being transported to the laboratory for further testing.
Table 2. Mixture proportions of the test bricks
Laboratory tests were conducted to determine the density, flexural strength, compressive strength, water absorption, initial rate of absorption (IRA), efflorescence, sulphate resistance, and microstructural characterisation. Five specimens of each mixture () were tested in each case.
The density was determined by dividing the weight by the volume of the samples. The mechanical properties (flexural and compressive) were measured in accordance with the American Standard Testing and Material (ASTM) C67 (ASTM Standard C67 Citation2003). The water absorption test was conducted in accordance with the ASTM C67 (ASTM Standard C67 Citation2003). The brick specimens were first dried in an oven at 105°C for 24 h to obtain their dry weights (W1). The specimens were then immersed in water for further 24 h and re-weighted to obtain the saturated weights (W2). Water absorption (Wa) was determined using the following equation:
Wa = ((W2 – W1)/W1) x 100%(1)
The IRA was determined by immersing the specimens in a 5-mm depth of water for 1 min. The samples were then removed and weighted in accordance with the ASTM C67 (ASTM Standard C67 Citation2003). The efflorescence was measured by immersing one end of each brick in water at a constant depth of 25 mm for 7 days. After 7 days, the presence of soluble salts on brick specimens were inspected after drying in an oven for 24 h. In the sulphate resistance tests, the bricks were fully immersed in a 5% sodium sulphate solution for 30 days as specified in the ASTM C1012 (ASTM Standard C1012 Citation2018). After 30 days of immersion, the weight change and the residual compressive strength of the brick specimens were measured after drying in an oven at 105°C. The development of porosity of the selected brick specimens were also further investigated using SEM.
4. Results and discussion
4.1. Physical properties
4.1.1 Density
shows the density of the bricks produced using different proportions of POFA. Notably, the density of the bricks decreased with an increase in the POFA content, leading to lighter bricks as the POFA was increased. The density reductions corresponding to 5, 10, 15 and 20% replacements of clay were 2.32, 3.64, 7.03 and 10.43%, respectively. This is attributed to the increase in the porosity of bricks due to the presence of POFA. A similar result was reported in previous studies (Faria, Gurgel, and Holanda Citation2012; Kazmi et al. Citation2016b; Kadir and Sarani Citation2020), where the replacement of clay by agricultural waste ash reduced the density of bricks. Furthermore, the density values are still in the range of 1200–2200 kg/m3 as prescribed by the German Institute for Standardisation (DIN) 105–100 (DIN Standard 105–100, Citation2012) for a good quality brick.
4.1.2. Water absorption
shows the results of the water absorption tests. The amount of water absorbed increased with an increase in the POFA content. The water absorption of the 5, 10, 15 and 20% POFA bricks increases by 9.26, 30.63, 49.97 and 59.23%, respectively compared with that of the control bricks. This likely reflects the porous nature of POFA given that the trend in water absorption showed good agreement with the density measurements; a higher density indicates less internal pore space and capillaries that can hold water (Leiva et al. Citation2016). Bricks with water absorption of less than 17% are categorised as having resistance to severe weathering as stipulated in the ASTM C62 (ASTM Standard C62 Citation2013), whereas those with less than 22% have moderate resistance. Thus, incorporating 5% POFA as a clay replacement gives a water absorption value (21.47%) within the moderate weathering resistance category.
4.1.3. Initial rate of absorption
The IRA of bricks greatly influences bonding between the bricks and mortar. Bricks with higher IRA result in quick absorption of moisture from mortar to pair the brick, which leads to weak bonding between the two materials. In contrast, a very low IRA also adversely affects the bonding strength (Christy and Tensing Citation2011).
shows the IRA measurements for bricks containing POFA; the IRA values were all higher than those of the control bricks and increased proportionally with the increase in the POFA content. For instance, the average IRA value of the 0% POFA brick was 0.28 g/min/cm2, increasing to 0.82 g/min/cm2 for the 20% POFA brick. This is attributed to the higher porosities of the bricks containing more POFA. Similar results have also been previously reported (Eliche-Quesada et al. Citation2017). Bricks with IRA values of more than 0.15 g/min/cm2 should be wetted before laying in accordance with the ASTM C62 (ASTM Standard C62 Citation2013) to avoid dehydration of the mortar. Therefore, it can be concluded that both the control and POFA bricks should be wetted before laying.
4.2. Mechanical properties
4.2.1. Flexural strength
The results of the flexural strength tests are shown in . The flexural strength decreased with an increase in the POFA content. For instance, the flexural strength reduced from 1.39 N/mm2 for the control bricks to 0.79 N/mm2 for bricks containing 15% POFA. This agrees with results reported in previous studies (Kazmi et al. Citation2016a, Citation2016b; Ugwu and Dickson Citation2014) in which the flexural strength of brick decreased with the addition of agricultural waste ash. The replacement of clay with up to 15% POFA satisfies the minimum flexural strength requirements of building brick as specified in the ASTM C67 (ASTM Standard C67 Citation2003). However, a 20% POFA content yielded a flexural strength below the value recommended in this standard. Generally, the flexural strength of brick is related to its microstructural characteristics, and in this case, the addition of POFA led to an increase in the porosity and, hence, a lower flexural strength (Riaz, Khitab, and Ahmed Citation2019; Bilgin et al. Citation2012).
4.2.2. Compressive strength
shows the compressive strength of bricks with various POFA contents. Similar to the flexural strength, the compressive strength of bricks containing POFA was lower than those of the control bricks. For instance, the compressive strength was 13.26% lower with the addition of 5% POFA compared with that of the control mix. These reductions are attributed to the enhanced porous structure of bricks when clay is replaced with POFA. The decomposition of organic matter and high amount of silica in POFA can result in higher porosities and may induce flaws during the firing process. Similar results have been reported in previous studies for bricks containing other porous material as a replacement for clay (Leiva et al. Citation2016; Kazmi et al. Citation2016a; Aouba et al. Citation2016).
Although the compressive strength decreased as more clay was replaced with POFA, the 5% POFA mix still satisfied the minimum compressive strength requirements for conventional bricks according to the European Standard (EN) 771–2 (EN Standard 771–2, Citation2011) and the British Standard (BS) 3921:1985 (British Standard BS3921 Citation1985), that is, 5 N/mm2 and 5.2 N/mm2, respectively. Therefore, incorporating up to 5% POFA as a replacement for clay can produce more sustainable bricks that meet strength standards.
4.3. Durability properties
4.3.1 Efflorescence
Efflorescence is a grey or white deposit of salts that forms on the surface of bricks, which can cause aesthetic problems on masonry structures. Efflorescence is considered as ‘slight’ if the white deposits cover less than 10% of the surface, ‘moderate’ when covering approximately 50% of the surface, and ‘heavy’ when covering more than 50% of the surface (Leiva et al. Citation2016).
A slight efflorescence (7% of the surface area) was observed on the bricks without POFA (). In contrast, no efflorescence was found on the bricks incorporating POFA. CaO is considered the primary cause of efflorescence on the bricks (Kazmi et al. Citation2016a; Netinger et al. Citation2014). The chemical analysis showed that the clay used in the brick mixes has a 9.97% CaO content, whereas the POFA has a content of 5.65%. In addition, the presence of Fe2O3 in the bricks would have also contributed to the formation of efflorescence. Furthermore, the clay used in the mixes has a slightly higher amount of Fe2O3 (7.83%) than the POFA (6.13%). Therefore, by replacing clay with POFA, and hence decreasing the relative quantities of CaO and Fe2O3 in the bricks, the resistance of the bricks to efflorescence was improved. Similar results have been reported is previous studies (Riaz, Khitab, and Ahmed Citation2019; Kazmi et al. Citation2016a). These observations indicate that the occurrence of efflorescence on bricks can be minimised by incorporating POFA.
4.3.2 Sulphate resistance
The results of the sulphate resistance tests are shown in . It can be observed that in all cases, the compressive strength of the test bricks decreased and the weight increased due to sulphate attack. For instance, the control bricks (without POFA) showed a 21.47% reduction in compressive strength after the sulphate test compared with a 22.31–32.21% reduction for the POFA bricks, depending on the mix. This is attributed to the pressures produced by salt crystallisation within pores, which results in internal micro-crack formation and a corresponding decrease in compressive strength.
Furthermore, the average weight gain of the control bricks was 9.54% compared with 12.89–23.12% for the POFA bricks. The partial in-filling of pores by salt crystals likely explains the observed increases in weight. Previous studies (Riaz, Khitab, and Ahmed Citation2019; Kazmi et al. Citation2016a; Faria, Gurgel, and Holanda Citation2012) reported similar results with respect to reductions in the compressive strength and increase in the weight of bricks during the sulphate resistance test. Even though cracks were not observed on the surface of the test specimen after the sulphate test, the appearance of the test specimens changed from reddish to dark colour (). This indicates that the POFA bricks resistance when subjected to sulphate attack was poor. Therefore, the use of bricks with POFA should be avoided in severe sulphate environments.
4.4. Microstructure
shows the SEM images for the control brick (0% POFA) and with 15% POFA content. Both specimens showed a porous microstructure; however, the addition of POFA resulted in a more visibly porous structure compared with the control brick. These results are in agreement with the density, strength, water absorption, and sulphate test results.
4.5. Relationships among properties
A linear regression analysis was performed to determine the effect of the physical properties of bricks, namely density, water absorption, and IRA on the compressive strength and sulphate resistance of bricks containing-POFA.
shows the correlation between the physical properties of bricks. All the physical properties showed strong relationship with an R2 value of >0.85. This was expected owing to the increase in the porosity of bricks, as the addition of POFA reduced the density of the bricks, increasing the water absorption and IRA values.
The relationships between the compressive strength and the physical properties of bricks are shown in . As discussed in Section 4.2.2, the porous structure of bricks is enhanced when clay is replaced with POFA. Thus, the compressive strength has a direct relationship with density, with an R2 value of 0.82. Furthermore, the inverse relationship between the compressive strength, water absorption, and IRA indicates that the strength of bricks deteriorated with the increase in porosity (Lawanwadeekul et al. Citation2020).
The strength loss and weight gain of bricks after sulphate test was significantly influenced by the physical properties, with an R2 value of >0.90 (). The higher porosity of the bricks facilitated easy access of sulphate ions into the material, thereby decreasing the compressive strength and increasing the weight gain. The results of the linear regression performed in this study demonstrated that the physical properties of bricks directly correlated with their compressive strength and sulphate resistance.
Figure 13. Linear relationship between pairs of physical properties: (a) density and water absorption; (b) density and initial rate absorption; (c) water absorption and initial rate absorption
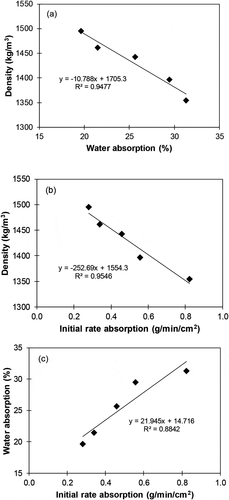
5. Conclusions
Fired clay bricks incorporating POFA as a replacement for clay by up to 20% by weight were manufactured in a local brick kiln and their properties were compared with those of conventionally produced bricks in Indonesia. The following conclusions can be drawn based on the test results:
The density of bricks decreased as more clay was replaced with POFA. This is related to an increase in porosity, resulting in lighter bricks. With a 20% POFA replacement, the brick density was reduced by up to 10.43%. Lighter bricks are more easily handled and also reduce the dead load of the structures they are made from.
Higher porosities resulting from the replacement of clay with POFA caused an increase in the water absorption capacity of the brick specimens. Specimens with 5% POFA had a water absorption of 21.47%, which is suitable for use in regions requiring moderate weathering resistance.
The IRA tests for all the bricks yielded values higher than 0.15 g/min/cm2, indicating that these bricks should be wetted before use in masonry structures.
The compressive strength of bricks decreased with an increase in the POFA content; replacement of clay with 5% POFA achieved a compressive strength of 7.22 N/mm2, which satisfies the requirements for conventional bricks (> 5 N/mm2) as specified by the EN 771–2 and BS 3921:1985.
Replacing up to 15% of clay with POFA achieved a flexural strength higher than 0.65 N/mm2, which is the minimum value required for conventional bricks as specified by the ASTM C67.
The brick specimens containing POFA had greater resistance to the formation of efflorescence than conventional bricks; however, their resistance was poor when subjected to sulphate attack. Therefore, the used of bricks with POFA should be avoided in severe sulphate environments.
The SEM observations indicated that the addition of POFA to bricks resulted in a more porous structure than the conventional bricks, which explains many of the observed differences in their mechanical properties.
Linear regression analysis results indicated that the physical properties of bricks strongly correlated with the mechanical and durability properties investigated in this study.
Overall, the replacement of clay with up to 5% POFA in brick production can produce a more sustainable building material. The use of POFA in large-scale brick production is not only useful for reducing the environmental impacts associated with the disposal of this waste material but also for conserving limited clay deposits.
Acknowledgements
The authors would like to thank Muhammad Hidayat, ST and Cynthia Lestari for their assistance during the experiment. We also thank the anonymous reviewers for providing constructive comments to improve the quality this paper.
Disclosure statement
No potential conflict of interest was reported by the authors.
Additional information
Notes on contributors
Abdul Rachman Djamaluddin
Abdul Rachman Djamaluddin is an Associated Professor at Department of Civil Engineering, Faculty of Engineering, Universitas Hasanuddin, Makassar, Indonesia. He received Doctoral degree from Universitas Hasanuddin, Indonesia in 2015. His area of expertise are geotechnical & geo-environmental engineering and sustainable construction materials.
Muhammad Akbar Caronge
Muhammad Akbar Caronge is Lecturer at Department of Civil Engineering, Faculty of Engineering, Universitas Hasanuddin, Makassar, Indonesia. He received Doctoral degree from Kyushu University, Japan in 2015. His area of expertise are concrete materials technology, concrete durability, corrosion and corrosion prevention technique of steel bars in concrete.
M. W. Tjaronge
M. W. Tjaronge is a Professor and currently the Head of Department of Civil of Engineering, Faculty of Engineering, Universitas Hasanuddin, Makassar, Indonesia. He received Doctoral degree from Nagoya Institute Technology, Japan in 2002. His research interests are concrete materials technology, porous concrete and asphalt, seawater concrete and geopolymer concrete.
Rita Irmawaty
Rita Irmawaty is an Associated Professor at Department of Civil Engineering, Faculty of Engineering, Universitas Hasanuddin, Makassar, Indonesia. She received Doctoral degree from Kyushu University, Japan in 2013. Her area of expertise are concrete materials technology, concrete durability and long-term performance of concrete.
References
- Abbas, S., M. A. Saleem, S. M. S. Kazmi, and M. J. Munir. 2017. “Production of Sustainable Clay Bricks Using Waste Fly Ash: Mechanical and Durability Properties.” Journal of Building Engineering 14: 7–14. doi:https://doi.org/10.1016/j.jobe.2017.09.008.
- Andreloa, F., I. Lancellotti, T. Manfredini, F. Bondioli, and L. Barbieri. 2018. “Rice Husk Ash (RHA) Recycling in Brick Manufacture: Effect on Physical and Microstructural Properties.” Waste and Biomass Valorization 9 (12): 2529–2539. doi:https://doi.org/10.1007/s12649-018-0343-5.
- Aouba, L., C. Bories, M. Coutand, B. Perrin, and H. Lemercier. 2016. “Properties of fired Clay Bricks with Incorporated Biomasses: Cases of Olive Stone flour and Wheat Straw Residues.” Construction and Building Materials 102: 7–13. doi:https://doi.org/10.1016/j.conbuildmat.2015.10.040.
- ASTM Standard C1012. 2018. Standard Test Method for Length Change of Hydraulic-Cement Mortars Exposed to a Sulfate Solution. Philadelphia, PA: ASTM International.
- ASTM Standard C62. 2013. Standard Specification for Building Brick (Solid Masonry Units Made from Clay or Shale). Philadelphia, PA: ASTM International.
- ASTM Standard C67. 2003. Standard Test Methods for Sampling and Testing Brick and Structural Clay Tile. Philadelphia, PA: ASTM International.
- Bilgin, N., H. A. Yeprem, S. Arslan, A. Bilgin, E. Gunay, and M. Marsoglu. 2012. “Use of Waste Marble Powder in Brick Industry.” Construction and Building Materials 29: 449–457. doi:https://doi.org/10.1016/j.conbuildmat.2011.10.011.
- BS Standard BS3921. 1985. Specifications for Clay Brick. United Kingdom: British Standard.
- Christy, C., and D. Tensing. 2011. “Greener Building Material with fly Ash.” Asian Journal of Civil Engineering (Building and Housing) 12 (1): 87–105.
- De Silva, G. H. M. J. S., and B. V. A. Perera. 2018. “Effect of Waste Rice Husk Ash (RHA) on Structural, Thermal and Acoustic Properties of Fired Clay Bricks.” Journal of Building Engineering 18: 252–259. doi:https://doi.org/10.1016/j.jobe.2018.03.019.
- De Silva, G. H. M. J. S., and E. Hansamali. 2019. “Eco-friendly Fired Clay Bricks Incorporated with Porcelain Ceramic Sludge.” Construction and Building Materials 228. https://www.sciencedirect.com/science/article/abs/pii/S0950061819321725
- DIN Standard 105–100. 2012. “Clay Masonry Units with Specific Properties.”
- Djangang, C. N., E. Kamseu, A. Elimbi, G. L. Lecomte, and P. Blanchart. 2014. “Net-shape Clay Ceramics with Glass Waste Additive.” Materials Sciences and Applications 5: 592–602. doi:https://doi.org/10.4236/msa.2014.58061.
- Elhusna, and A. S. Wahyuni (2016). “The Compressive Strength and the Absorption of the Clay Brick with the Rice Husk Ash and the Palm Oil Fuel Ash.” Proceeding of International Conference on Engineering and Science for Research and Development (ICESReD), Palembang, Indonesia 19–23.
- Eliche-Quesada, D., M. A. Felipe-Sesé, J. A. López-Pérez, and A. Infantes-Molina. 2017. “Characterization and Evaluation of Rice Husk Ash and Wood Ash in Sustainable Clay Matrix Bricks.” Ceramics International 43: 463–475. doi:https://doi.org/10.1016/j.ceramint.2016.09.181.
- EN Standard 771–2. 2011. “Specifications for Mansonry Units-Part 2: Calcium Silicate Mansory Units.” European Standard.
- Faria, K. C. P., R. F. Gurgel, and J. N. F. Holanda. 2012. “Recycling of Sugarcane Bagasse Ash Waste in the Production of Clay Bricks.” Journal of Environmental Management 101: 7–12. doi:https://doi.org/10.1016/j.jenvman.2012.01.032.
- Gatto, M., M. Wollni, and M. Qaim. 2015. “Oil Palm Boom and Land-use Dynamics in Indonesia: The Role of Policies and Socioeconomic Factors.” Land Use Policy 46: 292–303. doi:https://doi.org/10.1016/j.landusepol.2015.03.001.
- Gorhan, G., and O. Simsek. 2013. “Porous Clay Bricks Manufactured with Rice Husks.” Construction and Building Materials 40: 390–396. doi:https://doi.org/10.1016/j.conbuildmat.2012.09.110.
- Kadir, A. A., and N. A. Sarani. 2020. “Utilization of Palm Oil Fuel Ash in Brick Manufacturing for Lightweight Fired Clay Brick Production.” International Journal of Sustainable Construction Engineering and Technology 11 (1): 136–150.
- Kadir, A. A., N. A. M. Zahari, and N. A. Mardi. 2013. “Utilization of Palm Oil Waste into Fired Clay Brick.” Advances in Environmental Biology 7 (12): 3826–3834.
- Kazmi, S. M. S., S. Abbas, M. A. Saleem, M. J. Munir, and A. Khitab. 2016a. “Manufacturing of Sustainable Clay Bricks: Utilization of Waste Sugarcane Bagasse and Rice Husk Ashes.” Construction and Building Materials 120: 29–41. doi:https://doi.org/10.1016/j.conbuildmat.2016.05.084.
- Kazmi, S. M. S., S. Abbas, M. J. Munir, and A. Khitab. 2016b. “Exploratory Study on the Effect of Waste Rice Husk and Sugarcane Bagasse Ashes in Burnt Clay Bricks.” Journal of Building Engineering 7 372–378. doi:https://doi.org/10.1016/j.jobe.2016.08.001.
- Kazmi, S. M. S., S. Abbas, M. L. Nehdi, M. A. Saleem, and M. J. Munir. 2017. “Feasibility of Using Waste Glass Sludge in Production of Eco-friendly Clay Bricks.” Journal of Materials in Civil Engineering 29 (8): 04017056. doi:https://doi.org/10.1061/(ASCE)MT.1943-5533.0001928.
- Lawanwadeekul, S., T. Otsuru, R. Tomiku, and H. Nishiguchi. 2020. “Thermal-acoustic Clay Brick Production with Added Charcoal for Use in Thailand.” Construction and Building Materials 225: 119376. doi:https://doi.org/10.1016/j.conbuildmat.2020.119376.
- Leiva, C., C. Arenas, B. Alonso-farinas, L. F. Vilches, B. Paceno, and M. Rodriguez-galan. 2016. “Characteristics of fired Bricks with Co-combustion fly Ashes.” Journal of Building Engineering 5: 114–118. doi:https://doi.org/10.1016/j.jobe.2015.12.001.
- Lingling, X., G. Wei, W. Tao, and Y. Nanru. 2005. “Study on Fired Bricks with Replacing Clay by Fly Ash in High Volume Ratio.” Construction and Building Materials 19 (3): 243–247. doi:https://doi.org/10.1016/j.conbuildmat.2004.05.017.
- Mohajerani, A., A. Ukwatta, T. Jeffrey-Bailey, M. Swaney, M. Ahmed, G. Rodwell, S. Bartolo, N. Eshtiaghi, and S. Setunge. 2019. “A Proposal for Recycling the World’s Unused Stockpiles of Treated Wastewater Sludge (Bio-solids) in Fired-clay Bricks.” Buildings 9 (1): 14. doi:https://doi.org/10.3390/buildings9010014.
- Munir, M. J., S. Abbas, M. L. Nehdi, S. M. S. Kazmi, and A. Khatib. 2018. “Development of Eco-friendly Fired Clay Bricks Incorporating Recycled Marble Powder.” Journal of Materials in Civil Engineering 30 (5): 04018069. doi:https://doi.org/10.1061/(ASCE)MT.1943-5533.0002259.
- Murari, A., I. Singh, N. Agarwal, and A. Kumar. 2015. “Stabilization of Local Soil with Bagasse Ash.” SSRG International Journal of Civil Engineering 2(1): 37–39.
- Mushtaq, F., T. A. T. Abdullah, R. Mat, and F. N. Ani. 2015. “Optimization and Characterization of Bio-oil Produced by Microwave Assisted Pyrolysis of Oil Palm Shell Waste Biomass with Microwave Absorber.” Bioresource Technology 190: 442–450. doi:https://doi.org/10.1016/j.biortech.2015.02.055.
- Musthafa, A. M., K. Janaki, and G. Velraj. 2010. “Microscopy, Porosimetry and Chemical Analysis to Estimate the firing Temperature of Some Archaeological Pottery Shreds from India.” Microchemical Journal 95 (2): 311–314. doi:https://doi.org/10.1016/j.microc.2010.01.006.
- Netinger, I., M. Vracevic, J. Ranogajec, and S. Vucetic. 2014. “Evaluation of Brick Resistance to Freeze Thaw Cycles according to Indirect Procedures.” Gradevinar 66 (3): 197–209.
- Riaz, M. H., A. Khitab, and S. Ahmed. 2019. “Evaluation of Sustainable Clay Bricks Incorporating Brick Kiln Dust.” Journal of Building Engineering 24: 100725. doi:https://doi.org/10.1016/j.jobe.2019.02.017.
- Rukijkanpanich, J., and N. Thongchai. 2019. “Burned Brick Production from Residues of Quarry Process in Thailand.” Journal of Building Engineering 25: 100811. doi:https://doi.org/10.1016/j.jobe.2019.100811.
- Sata, V., C. Jaturapitakkul, and K. Kiattikomol. 2004. “Utilization of Palm Oil Fuel Ash in High-strength Concrete.” Journal of Materials in Civil Engineering 16 (6): 632–628. doi:https://doi.org/10.1061/(ASCE)0899-1561(2004)16:6(623).
- Sutas, J., A. Mana, and L. Pitak. 2012. “Effect of Rice Husk and Rice Husk Ash to Properties of Bricks.” Procedia Engineering 32: 1061–1067. doi:https://doi.org/10.1016/j.proeng.2012.02.055.
- Tay, J. H., and K. Y. Show. 1995. “Use of Ash Derived from Oil-palm Waste Incineration as a Cement Replacement Material.” Resources, Conservation and Recycling 13 (1): 27–36. doi:https://doi.org/10.1016/0921-3449(94)00012-T.
- Thomas, B. S., S. Kumar, and H. S. Arel. 2017. “Sustainable Concrete Containing Palm Oil Fuel Ash as A Supplementary Cementitious Material – A Review.” Renewable and Sustainable Energy Reviews 80: 550–561. doi:https://doi.org/10.1016/j.rser.2017.05.128.
- Ugwu, E. I., and A. Dickson. 2014. “Analysis of the Effect of Blending Nigeria Pure Clay with Rice Husk: A Case Study of Ekulu Clay in Enugu State.” American Journal of Materials Engineering and Technology 2 (3): 34–37.
- Umar, M. S., P. Jennings, and T. Urmee. 2013. “Strengthening the Palm Oil Biomass Renewable Energy Industry in Malaysia.” Renewable Energy 60: 107–115. doi:https://doi.org/10.1016/j.renene.2013.04.010.
- Velasco, P., M. Ortiz, M. Giro, and L. Velasco. 2014. “Fired Clay Bricks Manufactured by Adding Wastes as Sustainable Construction Material – A Review.” Construction and Building Materials 63: 97–107. doi:https://doi.org/10.1016/j.conbuildmat.2014.03.045.