ABSTRACT
The main aim of this paper is to improve the quality of recycled coarse concrete aggregates by using the carbonation technique. The aggregates are tested for physical properties and microstructural analysis. The concrete produced using these treated aggregates is tested for Non-destructive, Mechanical and Durability properties and the results are compared for control concrete, recycled aggregate concrete, and carbonated recycled aggregate concrete. A total of three mix combinations named NAC (using 100% natural coarse aggregate), RAC (using 100% recycled coarse aggregate) and CRAC (using 100% carbonated recycled coarse aggregate) were prepared using w/c ratio of 0.48. It has been found that by using the carbonated recycled concrete aggregates (CRCA), RAC’s non-destructive, mechanical and durability properties can be improved because of the method of carbonation. The compressive strength of the 100% RAC shows a decrement of 24.52% as compared to the 100% NAC. Whereas the compressive strength of the 100% CRAC shows an increase of 21.05% as compared to the 100% RAC, but it shows a decrement of 8.63% as compared to the 100% NAC. It not only refines the properties of RCA but also reduces the greenhouse effect which is originated by CO2 emissions.
Introduction
Concrete has been the most commonly used and leading construction material all around the world for a period of more than a century, due to its durability, satisfactory compressive strength, versatility, availability, and cost-effectiveness. However, it is not an environmentally friendly material, because it utilises large amounts of natural aggregates and also after the demolition of buildings, it is disposed of in the landfills and occupies large space of the land. In the past years, due to faster growth in urbanisation and industrialisation, the demand for concrete has increased manifold. It is estimated that 1 m3 per capita of concrete is produced annually around the world. The concrete industry is using large amounts of natural resources, as a result of which, it has become a challenge to fulfil the increasing demands of the industry. Also, the utility of old structures is decreasing, so these structures are demolished to make a way for modern construction. Structures are demolished because of many reasons like natural disasters, world-war damages, and new construction for improved economic gains. It is estimated that every year worldwide over 1 billion tonnes of concrete wastes and construction & demolition wastes (C&DW) are generated.
USA is one of the biggest producers in the world for C&DW, generating more than 500 million tonnes annually. In Europe, France is the biggest producer of C&DW around 246 million tonnes until 2012. In Asia, China is the largest producer of C&DW estimating around 1 billion tonnes until 2012. Also, India generates around 530 million tonnes of C&DW which makes it the second-largest producer of C&DW in the world. Many countries such as the USA, Germany, U K and Japan have successfully utilised the C&DW nearly around 90%; however, in India, fewer efforts are reported about the recycling of demolition wastes.
Due to the continuous population growth, house building activities, construction of infrastructure, industrial development, very large amounts of C&DW has been generated and hence, now it needs for recycling this waste. The construction industry is the main user of natural resources and worldwide aggregate production becomes almost doubled from 21 billion tonnes in the year 2007 to 40 billion tonnes in the year 2014. Countries like China, India, Gulf States, Indonesia, Russia, Mexico, Turkey, Brazil, Thailand, Malaysia have recorded the strongest increases in demand for recycling this waste. (Asgari et al. Citation2017). Also, large amounts of natural aggregates are produced for construction applications every year resulting in the large-scale depletion of natural resources.
To reduce the energy and raw material consumption is a major issue for the world at present. Thus, recycling waste concrete has been gaining good attention in the construction industry over the past few years. Coarse aggregates are one of those materials that can be recycled from the demolished structures. Using the recycled coarse aggregates in concrete mixes because of awareness of society for the protection of natural resources & for the effective use of concrete waste materials. In eastern & western countries like Korea and Japan, there is increasing emphasis on the usage of coarse-recycled aggregates for the production of new concrete. As sources of natural aggregate are not inexhaustible; therefore, it is crucial to create awareness regarding the potential usage of recycled coarse aggregates for the production of concrete in India. But in India, there is relatively less awareness regarding the potential usage of such aggregates and concrete waste is still dumped on landfill sites which occupy the large land area.
There may be many types of recycled aggregates like Recycled Concrete Aggregate (RCA), Reclaimed Asphalt Pavement (RAP), Recycled Concrete & Masonry (RCM), Reclaimed Asphalt Aggregate (RAA), Glass Cullet Scrap Tyres and Used Foundry Sand, etc. Recycled aggregates can be obtained from the existing concrete, and therefore known as recycled concrete aggregates (RCA). In the recycled aggregate, the volume of adhered mortar generally varies from 25% to 60% depends on the size of aggregate. Hence, if the attached cement mortar can be improved; then, it will increase the applications of RCA.
Various methods like mechanical grinding (Nagataki et al. Citation2004; Quattrone, Angulo, and John Citation2014), heat and rubbing methods (Akbarnezhad et al. Citation2011; Nagataki et al. Citation2004), pre-soaking in acid (Tam, Tam, and Le Citation2007), ultrasonic cleaning (Katz Citation2004) or dipping the aggregates in mineral admixture solution (Li, Quan, and Qin Citation2010; Shayan and Xu Citation2003) have been adopted in order to ameliorate the quality of recycled concrete aggregate. A lot of studies have investigated the properties of different types of recycled aggregate concretes. Thomas, Thaickavil, and Wilson (Citation2018) reported that with an increase in RCA replacement % with natural coarse aggregates, a decrease in the compressive strength of concrete mixes was observed. When 25% of the RCA were replaced with natural aggregates, it shows a 1.5–5% reduction in the compressive strength of concrete. When 100% of the RCA were replaced with natural aggregates, it shows an 11–19% reduction in the compressive strength of produced concrete. On increasing the w/c ratio, the splitting tensile strength decreases and increases when the cement content of the mix increases. Poon et al. (Citation2004) examined the influence on hardened and fresh concrete properties, of moisture states of recycled and natural aggregates. He also observed that using the air-dried (AD) aggregates and using recycled aggregates not more than 50% should be optimum for making the normal strength recycled aggregate concrete. It was observed that with an increase in RCA replacement % with natural coarse aggregates, the capillary absorption of concrete mixes increases. Ozbakkaloglu, Gholampour, and Xie (Citation2017) observed that mix prepared by Normal mixing approach (NMA) has less compressive strength up to 6% than mix prepared by Two-stage mixing approach (TSMA), due to improvement in a bond of aggregate to mortar by TSMA. It has also been reported when a specific w.b ratios are considered, with the increase in the recycled aggregate replacement ratio, the compressive strength for RAC is found to decrease. Rahal (Citation2007) investigated that for recycled aggregate concrete, the compressive strength was more than 80% as compared to the concrete with natural aggregates, when aggregate’s relative water absorption was below 1.8%, whereas for recycled aggregate concrete, the compressive strength was dropped significantly around 40% as compared to the concrete with natural aggregates when aggregate’s relative water absorption was above 5.5%. Tangchirapat et al. (Citation2008) investigated the concretes made by incorporating coarse recycled aggregate as 100% replacement of coarse aggregate and replacing sand at 0%, 50% and 100% by recycled fine aggregate along with ground rice husk-bark ash. It was observed that lower compressive strength values are obtained due to the high amount of coarse and fine recycled aggregate usage in concrete. Andreu and Miren (Citation2014) analysed the properties for the high performance recycled aggregate concrete and he concluded that an increase in recycled aggregates content decreases the resistance to chloride-ion penetration. Surya, VVL, and Lakshmy (Citation2013) studied the concrete mixes with five different types without and with class F Fly ash. As compared to normal concrete, recycled aggregate concrete shows better compressive strength which is shown by 100%-recycled aggregate concrete. Dilbas, Şimşek, and Çakır (Citation2014) investigated the compressive strength of recycled aggregate concrete by using silica fume, the usage of silica fume in concrete mixtures has a very marginal increasing effect. Kou, Poon, and Wan (Citation2012) and Lima et al. (Citation2013) used commercially recycled aggregates and replaced them with natural aggregates at 100%, 50%, 25% and 0% in concrete mixes. A reduction of 12.2% in compressive strength at 28 days was observed for the 100%-recycled aggregate concrete as compared to the natural aggregate concrete. Also, better chloride-ion penetration resistance was observed when the better quality of recycled aggregates and fly ash were used in concrete mixes.
In the recent past use of accelerated carbonation to enhance the properties of attached mortar-recycled aggregates has been investigated by a few researchers (Kou, Zhan, and Poon Citation2014; Thiery et al. Citation2013; Zhang et al. Citation2015). The basic concept is the reaction of CO2 and mainly Portlandite in cement mortar (Morandeau, Thiery, and Dangla Citation2014). It has been shown in the past studies that if concrete undergoes a full carbonation process it could absorb or take up to 50% of the CO2. One of the products of carbonation, i.e., CaCO3 densifies the whole structure of concrete by getting precipitated within in the pore space of the system. Bertos et al. (Citation2004) and Zhang et al. (Citation2015) found that the solid volume is found to increase by 11.8% to about 23% on getting carbonated depending upon the carbonation products. Previous studies have also shown that carbonated RCA exhibited such properties like a decrease in water absorption increase in density and an increase in crushing value (Zhan et al. Citation2014). Xuan, Zhan, and Poon (Citation2016) studied the compressive strength behaviour of various concrete mixes at 28 days, that were prepared by using various types of coarse aggregates named natural (N), the non-carbonated old type of RCA (ORCA), a non-carbonated new type of RCA (NRCA), carbonated ORCA at 5 bar pressure level, carbonated NRCA at 0.1 bar pressure level and carbonated NRCA at 5 bar pressure level, using w/c ratio of 0.55, superplasticizer to maintain slump in 150–200 mm range. As reported previously (Tam, Butera, and Le Citation2016; Xuan, Zhan, and Poon Citation2016; Zhang et al. Citation2015), an accelerated carbonation technique can improve the properties of RA by precarbonating them and further, in turn, improving the properties of RAC. In real life scenario, carbonation of concrete occurs at atmospheric conditions with Co2 concentration of 0.03% to 0.06%; however, this process, in general, takes around 100 years to complete the carbonation (Pade and Guimaraes Citation2007). Zhao et al. (Citation2018) studied the influence of accelerated carbonation on the properties of RCA. Original concrete was manufactured and crushed by a jaw crusher in the laboratory. The different fractions of laboratory-produced RCA were stored in an accelerated carbonation room. The mass loss, density, porosity and water absorption of the RCA were tested before and after carbonation. Industrial RCA was also studied for comparison with the laboratory-produced RCA. The results clearly showed that, after accelerated carbonation, the density of the RCA increased due to the transformation of portlandite into calcite. Park et al. (Citation2020) accelerated the carbonation of recycled aggregate by sparging with supercritical carbon dioxide (scCO2) to reduce the amount of time needed for carbonation, which is necessary for the pH neutralisation of recycled aggregate. The water absorption and porosity of the RCA decreased after carbonation. Alternatively, accelerated carbonation techniques can be tried to fasten the process of carbonation and in turn, improve the properties of RCA. So far, very limited information is available in this regard which could help in ascertaining the properties of RAC using RAC in the literature. Thus, the main aim of this study was to study the changes in properties of carbonated RAC as compared to uncarbonated RAC. Taking into consideration that carbonation, in general, has a tendency to improve the strength of unreinforced cement paste/concrete mix, this method is of significant interest. Even though the improvement in strength properties of RAC using carbonated RAC is available in the literature, the durability aspects and microstructural studies are still not available.
Research significance
The recycled concrete aggregates (coarse), generally have weak mechanical properties due to cracks formed during its crushing process and also contain attached cement mortar having a large number of pores which makes it less durable than natural aggregates. Therefore, the main objective of this study is to improve the quality of recycled concrete aggregates (coarse) by using the ‘Carbonation’ technique and after making the concrete by using these treated aggregates, then compare the Mechanical & Durability properties of the normal concrete, recycled aggregate concrete and carbonated recycled aggregate concrete.
Materials and methods
Cement
Cement conforming to requirements of I.S. Citation8112 (1989) the Ordinary Portland cement (OPC) of grade-43 was used in the study. The Physical properties of cement are given in .
Table 1. Physical properties of cement used
Fine aggregate
The natural sand that is used in this research work is obtained from nearby sources and also conformed to I.S. 383 (Citation1970) (grading zone II) specifications. For fine aggregate, the physical properties are presented in .
Table 2. Physical properties of fine aggregate
Natural Coarse Aggregate (NCA)
Aggregates having a maximum size of 10 mm & 20 mm, that are available from nearby sources are used in this research work. For natural coarse aggregate for a maximum size of 10 mm fineness modulus (FM) was 6.218 and for a maximum size of 20 mm FM was 6.970.
Recycled Coarse Aggregate (RCA)
Large quantities of tested specimens of concrete-like beams, cylinders and cubes, etc., of different sizes were placed outside of the concrete lab. These specimens were used to make the recycled coarse aggregates (RCA) in the lab. Firstly, the unreinforced specimens were broken down into small pieces manually as shown in . Then, the broken pieces were crushed by putting them in a jaw crusher. These crushed concrete pieces, depending on their size, were separated into two fractions as shown in .
The fraction that passes through 20 mm sieve and then retained on 10 mm sieve was classified as RCA20-10 mm and the other fraction that passes through 10 mm sieve and then retained on 4.75 mm sieve was classified as RCA10-4.75 mm. The fraction that passes from the 4.75 mm sieve was rejected. RCA’s of two different sizes was mixed in suitable amounts while making the RCA concrete so that for the combined RCA concrete, the gradation curve was identical to that of NCA. FM for RCA 20–10 mm was 5.9 and for RCA 10–4.75 mm was 6.934. shows the grain size distribution of Natural and Recycled Coarse Aggregate.
Residual mortar test
Also, the residual mortar (or mortar content test) is done on the recycled coarse aggregates to determine the amount of mortar attached to the recycled coarse aggregates. For this test, three plastic bathing mugs are used. In each mug, a total of 400 g of recycled coarse aggregates (60% of 20 mm size and 40% of 10 mm size) is placed. The previously mixed solution made with half a quantity of water and half quantity of HCL acid was used. Aggregates were dipped in this solution placed in three mugs for about 48 h. Also, the aggregates were stirred after 24 h with a wooden stick. After 48 h, the aggregates were removed and washed with clean water. Then, the aggregates were placed in the oven for drying about 24 h. Finally, the weights of dried samples are noted and the mortar content present on recycled coarse aggregates is calculated. The mortar content was found to be approximately 44%.
Carbonated Recycled Coarse Aggregate (CRCA)
For the preparation of carbonated recycled coarse aggregates (CRCA), an airtight steel-cubical carbonation chamber along with a CO2 cylinder was used. shows the setup used for the carbonation curing of recycled coarse aggregates (RCA) in this study. The carbonation chamber was connected to the CO2 cylinder having a concentration of 99% of the industrial-grade CO2 gas.
Recycled coarse aggregates (RCA) of a maximum size of 10 mm & 20 mm both were treated with CO2 gas in the carbonation chamber to prepare Carbonated Recycled Coarse Aggregate (CRCA) of both sizes. To facilitate the carbonation process and to reduce free water content in aggregates, firstly the recycled coarse aggregates (RCA) were dried in ambient conditions (temperature 25 ± 3°C and RH 40–70%) for about 6 h.
Then, before the injection of CO2 gas in the chamber, it was vacuumed to −0.46 bar (−350 mmHg) by using a vacuum motor. Then, the CO2 gas in the cylinder was heated for about 5 min by using a heater attached to the cylinder. Then, at a pressure level of 2.76 Bar (40 psi), the CO2 gas having a concentration of 99% was injected into the chamber. With the help of pressure gauges, at the curing chamber and at the CO2 cylinder, the pressure was maintained for about 48 h in the carbonation chamber, the RCAs were carbonated in this study. To absorb the water evaporated from aggregates, at the bottom of the carbonation chamber, enough amount of silica gel was placed. Until enough quantities of CRCA were obtained, the above steps was repeated. shows the carbonated recycled coarse aggregates of 10 and 20 mm maximum size. shows the comparison of the physical properties of NA, RCA, CRA. It is visible that carbonation tends to improve the properties of RCA. To determine the reason microstructural analysis was conducted which is discussed in the subsequent section.
Table 3. Physical properties of Natural, Recycled and Carbonated Recycled coarse aggregates
Mix proportions
Design of the concrete mix proportion was done carefully by following the authorised guidelines of IS. 10262 (Citation2009). A total of three mix combinations named NAC (using 100% natural coarse aggregate), RAC (using 100% recycled coarse aggregate) and CRAC (using 100% carbonated recycled coarse aggregate) were prepared by keeping the cement, fine aggregate and water content constant in all mixes. Potable water is normally considered adequate. In this research, tap water is used for curing, mixing and testing purposes. The various concrete mix proportions are presented in . The desired workability for the concrete mixes was kept at a 90–100 mm slump. Recycled aggregates and carbonated recycled aggregates were firstly pre-soaked for 24 h to compensate for the recycled aggregate’s additional water requirement and sun-dried before use in the concrete mixes. The mix design requirement is represented in .
Table 4. Mix Design Requirements
Table 5. Concrete Mix Proportions
Firstly, the samples were casted and kept in the moulds for about 24 h for hardening of concrete; then, the hardened concrete samples were removed from the moulds and immediately placed in the curing tank. All types of samples were allowed to remain in the curing tank for 28 days and then the required testing of specimens was done.
The tests conducted and specifications adopted are given in .
Table 6. Tests performed and codes followed
Microstructure analysis
Powdered broken samples were tested for Scanning electron microscopic (SEM) and X-Ray diffraction (XRD) analysis. Powdered XRD analysis was performed in Sophisticated Analytical Instruments (SAI) Labs of Thapar Institute of Engineering and Technology, the diffraction angle was varied from 10° to 80° with 2θ = 0.020°. Match software containing crystallography open database with an extension for cement-based materials was used to identify the peak phases of XRD.
Results and discussion
Microstructure analysis
Broken concrete pieces from the compressive strength test were used to take SEM images using secondary electron mode in order to analyse their microstructure. In the SEM image from non-carbonated aggregate ()) a clear formation of C-S-H gel is visible as compared to the carbonated aggregate in which CaCO3 is also found with the existing C-S-H gel, whereas the images for carbonated aggregate ()) show the formation of CaCO3 along with the C-S-H gel. The observation in SEM images are in coherence with results of compressive strength. CaCO3 is formed due to the carbonation reaction which further causes the densification of the mix by producing a micro aggregate effect. Thus, when the uncarbonated sample is compared to carbonated sample lesser voids are visible in the carbonated sample; thus, indicated towards a decrease in porosity of the mix. This happened because Ca (OH)2 gets converted into CaCO3, thus clogging the pores. A similar reaction of observed with the cement mortar attached to the aggregate where Ca(OH)2 and C-S-H gel react with CO2 to form CaCO3 during carbonation thus improving the interfacial transition zone (ITZ). Thus, very clearly shows that improvement in the strength of RCA can be done by accelerated carbonation technique.
Similar results are found in the XRD pattern obtained from the carbonated specimen, exhibiting strong peaks of calcium carbonate (calcite), which further strengthens the evidence of carbonation reaction and carbon uptake. XRD pattern of the carbonated sample also shows reduced peaks of CH (portlandite) in ) as compared to ) which shows the XRD for an uncarbonated aggregate sample. It can be concluded from the results of XRD and SEM that hydration is not affected by the carbonation reaction. In . P – Portlandite, Q – Quartz/Silica, C3A – Tricalcium Aluminate, C – CSH gel and C2S – Dicalcium Silicate.
Non-destructive properties
Ultrasonic pulse velocity
For each type of concrete mix, three concrete cubes of size 150 × 150 × 150 mm were cast and 28 days curing of specimens was done for determining the UPV values of various concrete mixes including 100% NAC, 100% RAC and 100% CRAC. The UPV values of various concrete mixes at 28 days in the form of a bar graph, the data is presented in .
From , it is observed that at the 28 days, the UPV value of the 100% RAC shows a decrease of 10.02% as compared to the 100% NAC. This decrease in UPV value may be due to the poor quality of aggregates and the formation of microcracks in the concrete transition zone of RCAs during its crushing process. Also, as compared to NAs, the RCAs had high porosity and low density.
In these results for all types of concrete mix, the UPV values exceeded 4500 m/s and hence the quality of these concretes can be graded as excellent as per IS 13,311 (Part 1): 1992. It is also observed that the UPV value of RAC increases when using the carbonated RCAs. At 28 days, the UPV value of the 100% CRAC shows an increase of 6.38% as compared to the 100% RAC, but it shows a decrease of 4.27% as compared to the 100% NAC. After the carbonation of RCAs, the porosity and water absorption of concrete becomes low, which results in fewer pore spaces and hence results in the good transmission of ultrasonic waves
Rebound hammer
For each type of concrete mix, three concrete cubes of size 150 × 150 × 150 mm were cast and 28 days curing of specimens was done for determining the compressive strength by rebound hammer test of various concrete mixes including 100% NAC, 100% RAC and 100% CRAC. The compressive strength by rebound hammer test of various concrete mixes at 28 days in the form of a bar chart, the data is presented in .
Figure 9. Comparison of rebound hammer and experimental compressive strengths for all types of mix at 28 days
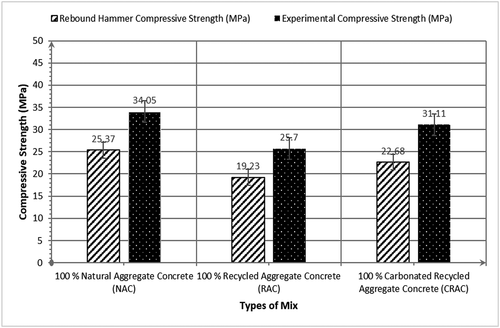
From , it is observed that at the 28 days, the compressive strength by rebound hammer test of all-concrete mixes shows a decrement as compared to the experimental compressive strengths. This behaviour has shown may be due to the reason that in the rebound hammer test, a point load is applied to the specimen as compared to the uniform loading acts in the CTM for calculating the experimental compressive strength.
Mechanical properties
Compressive strength
For each type of concrete mix, three concrete cubes of size 150 × 150 × 150 mm were cast and 28 days curing of specimens was done for determining the compressive strength of various concrete mixes including 100% NAC, 100% RAC and 100% CRAC. The compressive strength of various concrete mixes at 28 days in the form of a bar chart, the data is presented in .
From , it is observed that at 28 days, the compressive strength of the 100% RAC shows a decrease of 24.52% as compared to the 100% NAC. This decrease in compressive strength may be due to the poor quality of aggregates and the formation of microcracks in the RCAs during its crushing process. Also, a weak layer of hardened cement paste remains on the surface of RCAs which has high water absorption, so no enough residual water remains in the concrete mix to complete the reactions with cement when using the dry RCAs and also, this old-adhered mortar weakens the interfacial transition zone (ITZ) in RAC and hence, results in a decrease in its compressive strength.
In these results, it is also observed that the compressive strength of RAC increases when using the carbonated RCAs. At 28 days, the compressive strength of the 100% CRAC shows an increase of 21.05% as compared to the 100% RAC, but it shows a decrease of 8.63% as compared to the 100% NAC. Thomas, Thaickavil, and Wilson (Citation2018) observed that when 100% of the RCA were replaced with natural aggregates, it shows 11–19% reduction in compressive strength of concrete. Ozbakkaloglu, Gholampour, and Xie (Citation2017) observed that for a given w/b ratio, as the recycled aggregate replacement ratio increases, the compressive strength for RAC decreases. Xuan et al. reported a reduction of 26.3% in the compressive strength for concrete made by using 100% non-carbonated NRCAs as compared to 100% natural aggregate concrete, but no noticeable reduction was found in compressive strength for replacement % up to 30%. An increase of 22.6% in the compressive strength was observed for concrete made by using 100% carbonated NRCAs at 5 bar pressure level as compared to the concrete made by using 100% non-carbonated NRCAs. When the natural aggregates were replaced with carbonated NRCAs up to 60%, an insignificant reduction was observed in the compressive strength as compared to control concrete. Therefore, it was found that by treating RCAs with carbonation, the compressive strength of RAC increases and RCAs at higher % can also be used in concrete.
It is found that when the carbonation process is used to treat RCAs, the compressive strength of RAC increases, and it also allows the usage of RCAs at a higher percentage in new concrete. In attached cement mortar, the two cement hydration products present C-S-H gel and Ca(OH)2 reacts with CO2 to form CaCO3 during carbonation of RCAs, this CaCO3 precipitates in pore space of attached cement mortar; hence, it densified the RCAs and also, an interfacial transition zone (ITZ) is improved by carbonation of RCAs. Therefore, after carbonation, RCAs water absorption becomes low and hence enough residual water remains in the concrete mix to complete the reactions with cement which results in an increase in its compressive strength.
Flexural strength test
For each type of concrete mix, three concrete beams of size 700 × 150 × 150 mm were casted and 28 days curing of specimens was done for determining the flexural strength of various concrete mixes including 100% NAC, 100% RAC and 100% CRAC. The flexural strength of various concrete mixes at 28 days is presented in .
From , it is observed that at the 28 days, the flexural strength of the 100% RAC shows a decrease of 32.96% as compared to the 100% NAC. This decrease in flexural strength may be due to the poor quality of aggregates and the formation of microcracks in the RCAs during its crushing process. Also, due to the attached cement mortar presence on the surface of RCA, the surface texture of RCA becomes rough. With an increase in RCA’s quantity in concrete, the strength of aggregate-mortar ITZs decreases, therefore it reduces the RAC’s flexural strength.
In these results, it is also observed that the flexural strength of RAC increases when using the carbonated RCAs. At 28 days, the flexural strength of the 100% CRAC shows an increase of 30.32% as compared to the 100% RAC, but it shows a decrease of 12.63% as compared to the 100% NAC. A similar trend is followed for Flexural strength as compared to compressive strength. Thomas, Thaickavil, and Wilson (Citation2018) observed that when 100% of The RCA were replaced with natural aggregates, it shows 7–17% reduction in flexural strength of concrete. In a mix, having 450 kg/m3 of cement, 0.5 w/c ratio and 100% RCA replacement with natural aggregates shows a maximum reduction in flexural strength (13%). With the increase in w/c ratio, the flexural strength decreases and increases when the cement content of mix increases. Ozbakkaloglu, Gholampour, and Xie (Citation2017) observe that flexural strength for all mixes decreases with an increase in the RCA% due to decrease in aggregate-mortar ITZs strength with increasing RCA% in concrete. Xuan et al. (2015) reported an increase of 28.7% in flexural strength for concrete made by using 100% carbonated NRCAs as compared to the concrete made by using 100% non-carbonated NRCAs. When the natural aggregates were replaced with carbonated RCAs up to 60%, an insignificant reduction was observed in the flexural strength as compared to control concrete. Also, on properties of concrete, there was a lesser influence of carbonation pressure. Also, on an increase in flexural strength of concrete made by using carbonated ORCAs, there was a lesser influence of carbonation pressure.
Split tensile strength
For each type of concrete mix, three concrete cylinders of dia. 100 mm and height 200 mm were cast and 28 days curing of specimens was done for determining the split tensile strength of various concrete mixes including 100% NAC, 100% RAC and 100% CRAC. The split tensile strength of various concrete mixes at 28 days in the form of a bar graph, the data is presented in .
From , it is observed that at the 28 days, the split tensile strength of the 100% RAC shows a decrease of 23.67% as compared to the 100% NAC. This decrease in split tensile strength may be due to the poor quality of aggregates and the formation of microcracks in the RCAs during its crushing process. Also, due to porous mortar presence on the surface of RCA, therefore at the surface of aggregate the water absorption increases. With an increase in RCA's quantity in concrete, the strength of aggregate-mortar ITZs decreases, therefore it reduces the RAC’s split tensile strength.
In these results, it is also observed that the split tensile strength of RAC increases when using the carbonated RCAs. At 28 days, the split tensile strength of the 100% CRAC shows an increase of 16.73% as compared to the 100% RAC, but it shows a decrease of 10.90% as compared to the 100% NAC. Interfacial transition zone (ITZ) is improved by the carbonation of RCAs, which results in an increase in its split tensile strength. Thomas, Thaickavil, and Wilson (Citation2018) observed that when 100% of the RCA were replaced with natural aggregates, it shows 7–19% reduction in splitting tensile strength of concrete. In a mix, having 450 kg/m3 of cement, 0.5 w/c ratio and 100%. Ozbakkaloglu, Gholampour, and Xie (Citation2017) observed that split tensile strength for all mixes decreases with an increase in the RCA% due to decrease in aggregate-mortar ITZs strength with increasing RCA% in concrete. Xuan et al. (2015) reported an increase of 28.7% in flexural strength for concrete made by using 100% carbonated NRCAs as compared to the concrete made by using 100% non-carbonated NRCAs. When the natural aggregates were replaced with carbonated RCAs up to 60%, an insignificant reduction was observed in the flexural strength as compared to control concrete. Also, on properties of concrete, there was a lesser influence of carbonation pressure. Also, on the increase in flexural strength of concrete made by using carbonated ORCAs, there was a lesser influence of carbonation pressure. RCA replacement with natural aggregates shows a maximum reduction in splitting tensile strength (28%). With the increase in w/c ratio, the splitting tensile strength decreases and increases when the cement content of mix increases
Durability properties
Rapid chloride permeability test
For each type of concrete mix, the concrete cylinder of dia. 100 mm and height 200 mm was cast and 28 days curing of specimens was done for determining the rapid chloride permeability of various concrete mixes including 100% NAC, 100% RAC and 100% CRAC. It was cut into slices of dia. 100 mm and height 50 mm to prepare samples for this test. The rapid chloride permeability of various concrete mixes at 28 days in the form of a bar graph, the data is presented in .
From , it is observed that at the 28 days, the chloride-ion penetration of the 100% RAC shows an increase of 27.97% as compared to the 100% NAC. This increase in chloride-ion penetration may be due to the formation of microcracks at the aggregate-paste interface of RCAs during its crushing process. Also, due to porous mortar presence on the surface of RCA, therefore at the surface of aggregate the water absorption increases.
In these results, it is also observed that the chloride-ion penetration of RAC decreases when using the carbonated RCAs. At 28 days, the chloride-ion penetration of the 100% CRAC shows a decrease of 14.26% as compared to the 100% RAC, but it shows an increase of 9.72% as compared to the 100% NAC. The precipitation of CaCO3 in pore space of attached cement mortar, hence densifying the RCAs decreases its water absorption which results in a decrease in the chloride-ion penetration. Thomas, Thaickavil, and Wilson (Citation2018) observed that when 100% of the RCA were replaced with natural aggregates, it shows 15–40% increase in chloride permeability of concrete. For a w/c ratio of 0.4, 16–24% increase in chloride permeability was observed when RCA % in the mix was extended from 25% to 100%. Kou, Poon, and Wan (Citation2012) observed that when in concrete-recycled aggregates were incorporated, a reduction was shown in the chloride-ion penetration resistance. Xuan et al. reported A reduction of 36.4% in chloride penetration was observed for concrete made by using 100% carbonated NRCAs as compared to the concrete made by using non-carbonated NRCAs at 56 days. But, as compared to the normal concrete made by using only NAs, this value was still approximately 1.5 times more. An increase in resistance to chloride-ion penetration and a reduction of 15.4% were found in total charge passed when concrete made by using carbonated ORCAs. Also, better chloride-ion penetration resistance was observed when the better quality of recycled aggregates was used in concrete mixes.
Water absorption
For each type of concrete mix, three concrete cubes of size 150 × 150 × 150 mm were cast and 28 days curing of specimens was done for determining the water absorption of various concrete mixes including 100% NAC, 100% RAC and 100% CRAC. The water absorption of various concrete mixes at 28 days in the form of a bar graph, the data is presented in .
From , it is observed that at the 28 days, the water absorption of the 100% RAC shows an increase of 60.09% as compared to the 100% NAC. This increase in water absorption may be due to the poor quality of aggregates and the formation of microcracks at the aggregate-paste interface of RCAs during its crushing process. Also, due to porous mortar presence on the surface of RCA, therefore at the surface of aggregate the water absorption increases. Thomas, Thaickavil, and Wilson (Citation2018) observed that when 100% of the RCA were replaced with natural aggregates, it shows maximum 40% increase in water absorption of concrete for the mix having 450 kg/m3 of cement and 0.5 w/c ratio. For a w/c ratio of 0.4, 13–19% increase in water absorption was observed when RCA % in the mix was extended from 25% to 100%. Xuan et al. (2017) reported a reduction of 10.5% was found in water absorption of RAC when carbonation pressure is increased from 0.1 to 5 bars of NRCA's. A reduction of 9.4% in water absorption of RAC was found when using concrete made with 100% ORCAs, also it was less as compared to the RAC made by using 100%-carbonated ORCAs. For RAC, an increase in water absorption was found when NAs was replaced from 0% to 100% by RCAs in normal concrete. A decrease was observed in water absorption of RAC when carbonation of RCAs was done.
In these results, it is also observed that the water absorption of RAC decreases when using the carbonated RCAs. At 28 days, the water absorption of the 100% CRAC shows a decrease of 20.77% as compared to the 100% RAC, but it shows an increase of 26.83% as compared to the 100% NAC. The same reason for chloride-ion penetration could be cited to decrease water absorption.
Water permeability
For each type of concrete mix, three concrete cubes of size 150 × 150 × 150 mm were casted and 28 days curing of specimens was done for determining the water permeability of various concrete mixes including 100% NAC, 100% RAC and 100% CRAC. The depth of penetration of water of various concrete mixes at 28 days in the form of a bar graph, the data is presented in .
From , it is observed that at the 28 days, the depth of penetration of water of the 100% RAC shows the maximum value of 85.0 mm as compared to the 100% CRAC and 100% NAC which shows the depth of penetration of water of 53.5 mm and 28.0 mm, respectively. This increase in depth of penetration of water of 100% RAC may be due to the poor quality of aggregates and the formation of microcracks at the aggregate-paste interface of RCAs during its crushing process. Also, due to weak and porous mortar presence on the surface of RCA, the porosity of RAC increases which further increases its depth of penetration of water.
In these results, it is also observed that the depth of penetration of water of RAC decreases when using the carbonated RCAs. At 28 days, the depth of penetration of water of the 100% CRAC decreases as compared to the 100% RAC by 31.5 mm, but it shows an increase of 25.5 mm as compared to the 100% NAC.
Sorptivity
For each type of concrete mix, the concrete cylinder of dia. 100 mm and height 200 mm was casted and 28 days curing of specimens was done for determining the sorptivity of various concrete mixes including 100% NAC, 100% RAC and 100% CRAC. It was cut into slices of dia. 100 mm and height 50 mm to prepare samples for this test. The sorptivity of various concrete mixes at 28 days is shown in .
From , it is observed that at the 28 days, the sorptivity of the 100% RAC shows the maximum value as compared to the 100% CRAC and 100% NAC. This increase in sorptivity of 100% RAC may be due to the poor quality of aggregates and the formation of microcracks at the aggregate-paste interface of RCAs during its crushing process. Also, due to weak and porous mortar presence on the surface of RCA, the porosity of RAC increases which further increases its sorptivity.
In these results, it is also observed that the sorptivity of RAC decreases when using the carbonated RCAs. At 28 days, the sorptivity of the 100% CRAC decreases as compared to the 100% RAC, but it shows an increase as compared to the 100% NAC.
Conclusions
General
In this study to improve the quality of RCAs, an accelerated carbonation technique had been investigated. In this chapter, the main conclusions are drawn from the results of various non-destructive properties (Ultrasonic pulse velocity, Rebound hammer), mechanical properties (Compressive strength, Flexural strength, Split tensile strength), and durability properties (Rapid chloride permeability, Water absorption, Water permeability, Sorptivity) of various concrete mixes including 100% NAC, 100% RAC and 100% CRAC are discussed.
Main conclusions of the study
The UPV value of the 100% CRAC shows an increase of 6.38% as compared to the 100% RAC, but it shows a decrement of 4.27% as compared to the 100% NAC and the compressive strength by rebound hammer test of all-concrete mixes shows a decrement as compared to the experimental compressive strengths.
The compressive strength of the 100% RAC shows a decrement of 24.52% as compared to the 100% NAC whereas, the compressive strength of the 100% CRAC shows an increase of 21.05% as compared to the 100% RAC, but it shows a decrement of 8.63% as compared to the 100% NAC at 288 days.
The flexural strength of the 100% RAC shows a decrement of 32.96% as compared to the 100% NAC whereas for 100% CRAC it shows an increase of 30.32% as compared to the 100% RAC, but it shows a decrement of 12.63% as compared to the 100% NAC at 28 days. Almost a similar trend was observed for Split Tensile Strength.
The chloride-ion penetration of the 100% RAC shows an increase of 27.97% as compared to the 100% NAC whereas for the 100% CRAC its shows a decrement of 14.26% as compared to the 100% RAC, but it shows an increase of 9.72% as compared to the 100% NAC at the end of 28 days.
Water absorption and Water Penetration show an increasing trend for Recycled aggregates as compared to RAC, whereas much better results were observed when comparing CRAC to RAC.
The sorptivity of the 100% RAC shows the maximum value as compared to the 100% CRAC and 100% NAC. At the 28 days, the sorptivity of the 100% CRAC shows decrement as compared to the 100% RAC, but it shows an increase as compared to the 100% NAC.
Disclosure statement
On behalf of all authors, the corresponding author states that there is no conflict of interest.
Additional information
Notes on contributors
Manpreet Singh
Dr. Manpreet Singh is an Assistant Professor in Civil Engineering Department, Thapar Institute of Engineering and Technology. His research interests include Sustainable Materials, Concrete and Pavement Materials.
A.B Danie Roy
Dr A.B. Danie Roy is an Assistant Professor in Civil Engineering Department, Thapar Institute of Engineering and Technology. His research interests include Reinforced Concrete, High Strength Concrete, Fibre Reinforced Concrete, High Temperature Testing of Concrete elements and Structural evaluation and retrofitting.
Shakeel Waseem
Dr. Shakeel Ahmad Waseem is an Assistant Professor in Civil Engineering Department in National Institute of Technology Srinagar. His research interests include Sustainable Concrete; Durability of Concrete; Structural Behaviour of Reinforced Concrete. Development and Testing of Indigenous Ultra High Performance Concrete.
Harsimranjit Singh
Mr. Harsimranjit Singh is Post Graduate Student in in Civil Engineering Department, Thapar Institute of Engineering and Technology.
References
- Akbarnezhad, A., K. C. G. Ong, M. H. Zhang, C. T. Tam, and T. W. J. Foo. 2011. “Microwave-assisted Beneficiation of Recycled Concrete Aggregates.” Construction and Building Materials 25 (8): 3469–3479. doi:https://doi.org/10.1016/j.conbuildmat.2011.03.038.
- Andreu, G., and E. Miren. 2014. “Experimental Analysis of Properties of High Performance Recycled Aggregate Concrete.” Construction and Building Materials 52: 227–235. doi:https://doi.org/10.1016/j.conbuildmat.2013.11.054.
- Asgari, A., T. Ghorbanian, N. Yousefi, D. Dadashzadeh, F. Khalili, A. Bagheri, and A. H. Mahvi. 2017. “Quality and Quantity of Construction and Demolition Waste in Tehran.” Journal of Environmental Health Science & Engineering 15 (1): 14. doi:https://doi.org/10.1186/s40201-017-0276-0.
- ASTM. 2012. “ASTM C1202: Standard Test Method for Electrical Indication of Concrete’s Ability to Resist Chloride Ion Penetration.” ASTM International West Conshohocken, PA, USA.
- ASTM, C. 2004. “1585-04. Standard Test Method for Measurement of Rate of Absorption of Water by Hydraulic-cement Concretes.” ASTM International.
- ASTM, C. 2006. “642, Standard Test Method for Density, Absorption, and Voids in Hardened Concrete.” Annual Book of ASTM Standards 4: 2.
- Bertos, M. F., S. Simons, C. D. Hills, and P. J. Carey. 2004. “A Review of Accelerated Carbonation Technology in the Treatment of Cement-based Materials and Sequestration of CO2.” Journal of Hazardous Materials 112 (3): 193–205. doi:https://doi.org/10.1016/j.jhazmat.2004.04.019.
- Dilbas, H., M. Şimşek, and Ö. Çakır. 2014. “An Investigation on Mechanical and Physical Properties of Recycled Aggregate Concrete (RAC) with and without Silica Fume.” Construction and Building Materials 61: 50–59. doi:https://doi.org/10.1016/j.conbuildmat.2014.02.057.
- I.S. 383. 1970. “Specification for Coarse and Fine Aggregates from Natural Sources for Concrete.” New Delhi: Bureau of Indian Standards.
- I.S. 516. 1959. “Indian Standard Methods of Tests for Strength of Concrete.” Bureau of Indian Standards.
- I.S. 5816. 1999. “Splitting Tensile Strength of Concrete–method of Test.” New Delhi: Bureau of Indian Standards.
- I.S. 8112. 1989. “43 Grade Ordinary Portland Cement–Specification.” New Delhi: Bureau of Indian Standards.
- IS. 10262. 2009. “Indian Standard Code for Concrete Mix Proportioning Guidelines (First Revision).” New Delhi: Bureau of Indian Standards .
- Katz, A. 2004. “Treatments for the Improvement of Recycled Aggregate.” Journal of Materials in Civil Engineering 16 (6): 597–603. doi:https://doi.org/10.1061/(ASCE)0899-1561(2004)16:6(597).
- Kou, S.-C., C.-S. Poon, and H.-W. Wan. 2012. “Properties of Concrete Prepared with Low-grade Recycled Aggregates.” Construction and Building Materials 36: 881–889. doi:https://doi.org/10.1016/j.conbuildmat.2012.06.060.
- Kou, S.-C., B. Zhan, and C.-S. Poon. 2014. “Use of a CO2 Curing Step to Improve the Properties of Concrete Prepared with Recycled Aggregates.” Cement and Concrete Composites 45: 22–28. doi:https://doi.org/10.1016/j.cemconcomp.2013.09.008.
- Li, Q. Y., H. Z. Quan, and Y. Qin. 2010. Performance and Application Technology of Recycled Concrete, 167–168. Beijing, China: China Building Materials Press.
- Lima, C., A. Caggiano, C. Faella, E. Martinelli, M. Pepe, and R. Realfonzo. 2013. “Physical Properties and Mechanical Behaviour of Concrete Made with Recycled Aggregates and Fly Ash.” Construction and Building Materials 47: 547–559. doi:https://doi.org/10.1016/j.conbuildmat.2013.04.051.
- Morandeau, A., M. Thiery, and P. Dangla. 2014. “Investigation of the Carbonation Mechanism of CH and CSH in Terms of Kinetics, Microstructure Changes and Moisture Properties.” Cement and Concrete Research 56: 153–170. doi:https://doi.org/10.1016/j.cemconres.2013.11.015.
- Nagataki, S., A. Gokce, T. Saeki, and M. Hisada. 2004. “Assessment of Recycling Process Induced Damage Sensitivity of Recycled Concrete Aggregates.” Cement and Concrete Research 34 (6): 965–971. doi:https://doi.org/10.1016/j.cemconres.2003.11.008.
- Ozbakkaloglu, T., A. Gholampour, and T. Xie. 2017. “Mechanical and Durability Properties of Recycled Aggregate Concrete: Effect of Recycled Aggregate Properties and Content.” Journal of Materials in Civil Engineering 30 (2): 4017275. doi:https://doi.org/10.1061/(ASCE)MT.1943-5533.0002142.
- Pade, C., and M. Guimaraes. 2007. “The CO2 Uptake of Concrete in a 100 Year Perspective.” Cement and Concrete Research 37 (9): 1348–1356. doi:https://doi.org/10.1016/j.cemconres.2007.06.009.
- Park, J., J. Lee, C.-W. Chung, S. Wang, and M. Lee. 2020. “Accelerated Carbonation of Recycled Aggregates Using the Pressurized Supercritical Carbon Dioxide Sparging Process.” Minerals 10 (6): 486. doi:https://doi.org/10.3390/min10060486.
- Poon, C. S., Z. H. Shui, L. Lam, H. Fok, and S. C. Kou. 2004. “Influence of Moisture States of Natural and Recycled Aggregates on the Slump and Compressive Strength of Concrete.” Cement and Concrete Research 34 (1): 31–36. doi:https://doi.org/10.1016/S0008-8846(03)00186-8.
- Quattrone, M., S. C. Angulo, and V. M. John. 2014. “Energy and CO2 from High Performance Recycled Aggregate Production.” Resources, Conservation and Recycling 90: 21–33. doi:https://doi.org/10.1016/j.resconrec.2014.06.003.
- Rahal, K. 2007. “Mechanical Properties of Concrete with Recycled Coarse Aggregate.” Building and Environment 42 (1): 407–415. doi:https://doi.org/10.1016/j.buildenv.2005.07.033.
- Shayan, A., and A. Xu. 2003. “Performance and Properties of Structural Concrete Made with Recycled Concrete Aggregate.” Materials Journal 100 (5): 371–380.
- Surya, M., K. R. VVL, and P. Lakshmy. 2013. “Recycled Aggregate Concrete for Transportation Infrastructure.” Procedia-Social and Behavioral Sciences 104: 1158–1167. doi:https://doi.org/10.1016/j.sbspro.2013.11.212.
- Tam, V. W. Y., A. Butera, and K. N. Le. 2016. “Carbon-conditioned Recycled Aggregate in Concrete Production.” Journal of Cleaner Production 133: 672–680. doi:https://doi.org/10.1016/j.jclepro.2016.06.007.
- Tam, V. W. Y., C. M. Tam, and K. N. Le. 2007. “Removal of Cement Mortar Remains from Recycled Aggregate Using Pre-soaking Approaches.” Resources, Conservation and Recycling 50 (1): 82–101. doi:https://doi.org/10.1016/j.resconrec.2006.05.012.
- Tangchirapat, W., R. Buranasing, C. Jaturapitakkul, and P. Chindaprasirt. 2008. “Influence of Rice Husk–bark Ash on Mechanical Properties of Concrete Containing High Amount of Recycled Aggregates.” Construction and Building Materials 22 (8): 1812–1819. doi:https://doi.org/10.1016/j.conbuildmat.2007.05.004.
- Thiery, M., P. Dangla, P. Belin, G. Habert, and N. Roussel. 2013. “Carbonation Kinetics of a Bed of Recycled Concrete Aggregates: A Laboratory Study on Model Materials.” Cement and Concrete Research 46: 50–65. doi:https://doi.org/10.1016/j.cemconres.2013.01.005.
- Thomas, J., N. N. Thaickavil, and P. M. Wilson. 2018. “Strength and Durability of Concrete Containing Recycled Concrete Aggregates.” Journal of Building Engineering 19: 349–365. doi:https://doi.org/10.1016/j.jobe.2018.05.007.
- Xuan, D., B. Zhan, and C. S. Poon. 2016. “Assessment of Mechanical Properties of Concrete Incorporating Carbonated Recycled Concrete Aggregates.” Cement and Concrete Composites 65: 67–74. doi:https://doi.org/10.1016/j.cemconcomp.2015.10.018.
- Zhan, B., C. S. Poon, Q. Liu, S. Kou, and C. Shi. 2014. “Experimental Study on CO2 Curing for Enhancement of Recycled Aggregate Properties.” Construction and Building Materials 67: 3–7. doi:https://doi.org/10.1016/j.conbuildmat.2013.09.008.
- Zhang, J., C. Shi, Y. Li, X. Pan, C.-S. Poon, and Z. Xie. 2015. “Performance Enhancement of Recycled Concrete Aggregates through Carbonation.” Journal of Materials in Civil Engineering 27 (11): 4015029. doi:https://doi.org/10.1061/(ASCE)MT.1943-5533.0001296.
- Zhao, Z., S. Remond, D. Damidot, L. Courard, and F. Michel. 2018. “Improving the Properties of Recycled Concrete Aggregates by Accelerated Carbonation.” Proceedings of the Institution of Civil Engineers - Construction Materials 171 (3): 3, 126–132. doi:https://doi.org/10.1680/jcoma.17.00015.