ABSTRACT
The production of ballistic composites using polyethylene fibres from ultra-high molecular weight polyethylene (UHMWPE) and carbon fibres are gaining relevance. Although these materials have standard properties, they are very expensive and are not readily available. To develop a military helmet that will be less expensive and protect the safety of the personnel that leads to the development of polyester reinforced banana stem fibres (BSF) and cow horn particulate (CHp) composite. Polyester-15 wt BSF+4 wt% CHp was produced using a hand laying method. The composite was cured at 100°C for 6 h. The microstructure, strength, hardness values, and impact energy were determined using the standard method. Lower weight helmet that will not be too heavy and the same protect the safety of the personnel can be produced from this formulation. 94.66% enhancement in tensile strength and 174.79% of the impact energy were obtained. The values of the impact energy, hardness values, and strength obtained in this work are within the range for the production of military helmet.
1. Introduction
Every year many workers are killed or seriously injured in the military as a result of head injuries (Abdulrahim Citation2019). Wearing an appropriate safety helmet significantly reduces the risk of injury or even death. Nowadays, the production of ballistic composites using polyethylene fibres from ultra-high molecular weight polyethelene (UHMWPE) and carbon fibres (Bahadur, Gong, and Anderegg Citation1993; Kulkarni et al. Citation2013) are gaining relevance. Although these materials have standard properties, they are very expensive and are not readily available. Besides, they are non-biodegradable, hence a major environmental threat (Gogineni et al. Citation2012; Haneefa et al. Citation2008). Therefore, focus on the choice of reinforcement fibres is gradually shifting towards natural sources. Natural fibres have received notable attention over the years because they are low-cost and have very lightweight. Nonetheless, they suffer from low mechanical characteristics relative to their glass counterparts. To overcome this problem, hybrid natural fibres could be a potential solution (Palta, Fang, and Weggel Citation2018; Pamela Citation2007).
In recent years, development of military helmet using natural fibres composite materials has been giving great attention to reduce the heavyweight of steel helmet and protect the safety of the personnel. Natsa, Akindapo, and Garba (Citation2015) produced a military helmet using polymer reinforced with coir fibres. They obtained impact energy of 8.73 J/mm2 at 70% coir fibre addition. Murali et al. (Citation2014) developed epoxy composite using sisal/banana/jute particle as reinforcement for the production of helmet. They observed that the weight of the developed composite was lower than ABS plastic with higher impact energy. Rajasekar, Ashokkumar, and Narayanan (Citation2015) used Creo simulate 2.0 software to simulated the properties of polypropylene/natural fibres composite. Obele and Ishidi (Citation2015) produced a helmet using epoxy reinforced coir fibre. They obtained the optimum impact energy of 26.43 KJ/m2 and tensile strength of 23.68 N/mm2 at 30 wt% coir fibres composite. They established that the composite can be used in the production of an industrial safety helmet. Yahaya et al. (Citation2016) studied the ballistic impact properties of woven kenaf-aramid hybrid composites. They used hand laying method in the production of the composites. They observed increased the energy absorption (14.46% to 41.30%) and V50 (5.5% to 8.44%).
From the literature above it can be observed the there is little or no information on the hybridisation of polyester reinforced with cow horn particles and banana stem fibre composites for the production of a military helmet. Hence, this work will report for the first time the possibility of using waste banana stem fibres and cow horn particles for the production of the military helmet using tensile strength, flexural strength, hardness values and impact energy as criteria properties.
2. Materials and method
The unsaturated polyester resin of low viscosity of orthophthalic type (UP-973STV), methyl-ethyl-ketone peroxide (MEKP)(EPerox-P as initiator and cobalt octoate accelerator (Unidry Co 12), Acetic Acid used in this work were purchased in Tony Chemical shop Lagos Nigeria. The Banana stem fibre(BPF) used in this work was obtained in the Ilorin Kwara State Nigeria (). The BPF was cleaned and dried to removed dirt and other dead organic materials. The BSF was treated using a 5% NaOH solution with 2% acetic. After the chemical treatment, the treated BSF was dried for 24 h.
The cow horns were collected at an abattoir in Zaria, Kaduna State, Nigeria (). The horns were washed thoroughly and rinsed with tap water to remove the debris, sun dried for one month, after which it was grounded to powder form (75 um) using high speed vibrating ball mill. The ball milling machine contains fifty (50) tungsten ball of 10 mm diameter. The milling was done with ball to powder ratio of 5:2, speed of 300rpm and 2 hours. The cow horn particles were soaked in chloroform for 72 hours to remove the fat, after which it was sun dried and washed with de-ionised water to remove the colour as done by Jimoh et al. (Citation2014).
Before the production of the test samples, the experimental trial was conducted to know the optimum addition of CHp and BSF to the polyester. The results of the trial experiment have shown that 15 wt%BSF and 4 wt% CHp was the better condition. This composition was then used in the production of the test samples. The hybrid composite was produced using a hand lay-up method using 15 wt%BSF, 4 wt% CHp, and balance polyester. %2 cobalt naphthalene (as an accelerator) and 2% methyl-ethyl-ketone-peroxide (MEKP) as initiator were added to the mixture. The composite was cured in the open air for 24 hours before artificial curing in the oven set at 100°C for 6 hours holding time. shows the photograph of the test sample inside the mould. After curing the sample was cut to various dimensions for the test.
The elemental composition of the CHp was determined using X-Ray Fluorescence (XRF) analysis. The particles were formed into pellets in a pelletiser with hydraulic press (Carver Inc.). The pellets were then sealed into the chamber of the XRF (Amptek Inc.) and allowed to run for 1000 s at a voltage of 20 kV, and a current of 40 μA. The resulting spectrum then provides the elemental composition of the material.
The density was determined by ASTM D792 – 13. The transmission electron microscopy model (Jeol, JSM2010) was used to determine the particle size of the CHp. Siemens (D-500) diffractometer using Co-Kc radiation (Kc = 1.79026A) was used to determine the X-ray diffractometer patterns of the samples in question. Scanning electron microscope model: JEOLJSM840A was used to determine the morphology of the samples. The SEM/EDS of the composite samples was done as per ASTM E2809. The FTIR of the samples under investigation were analysed using Equinox 55FTIR machine. The spectrum was determined using 500–4000 cm−1.
The tensile test was conducted by ASTM D3039 / D3039M. (Citation2017) standards. A 10 mm/min cross-head speed and sample size of 177 mm×20 mm×5 mm were used. The flexural test was conducted by ASTM D2344 / D2344M. (Citation2016) standards using a three-point bend test. A 10 mm/min cross-head speed was used.
The hardness values of the composites were determined as per the ASTM D785 – 08. (Citation2015) standard. A hardness testing machine with a B-scale using a minor and major load of 10 and 100 kg receptivity was used for the hardness test. The impact energy of the composite was determined as per ASTM D256 – 10. (Citation2018) standard. A velocity of 3.36 m/s and a V-notched sample size of 10x 5x55mm were used. The ballistic of the flat composite was determined using the V50 ballistic resistance and bullet proofness in accordance with NIJ-0106.01 Type 11and MIL-H-44099A standards.
3. Results and discussion
Test was also conducted to find the elemental composition of the cow horn particulate (CHp). It is found that the major elements present are carbon (54.08%), oxygen (28.23%), nitrogen (10.23%) and molybdenum (6.23%) with a maximum carbon composition of 54.08 wt%. Other elements present in smaller amounts are iron, sodium, chlorine and calcium, respectively ().
Table 1. Composition of CHp
displays the TEM image of the CHp. It can be seen that the CHp image revealed that the particles are not round and they are irregular in shape. An average particle size obtained for the CHp using TEM was found to be 98.13 nm.
- displays the SEM/EDS images of the CHp and BSF. In it can be seen that the particles of the CHp are not too round, but they are solid. The result of the SEM is in line with the analysis of the TEM discussed above. The high percentage of carbon obtained in the EDS is in par with the composition of CHp discussed in .
From , one can observe that the structure of the BSF was cleaned without impurities and debris; these confirm that our chemical treatment used was able to remove all the impurities. This is in par with other fibre investigated by Atuanya, Ibhadode, and Igboanugo (Citation2011), Ariff, Jalil, and Bahar (Citation2014). The EDS shows a high percentage of carbon, the presence of high carbon obtained can be referred to the fact that the BSF contains high cellulose after chemical treatment
Density values of 0.95, 1.12 and 1.25 g/cm3 were obtained for the CHp, untreated and treated BPF respectively (). Comparatively from obtained results, it shows that CHp have the lower density among them. Also, it can be seen that the treated BPF have the higher density than the untreated BPF. This could be attributed to the treatment process which removed the lignin and hemicelluloses. Similar observation was observed in the work of Bledzki and Gassan (Citation1999).
Table 2. Density of CHp and BPF
Density values of 1.25 and 1.13 g/cm3 were obtained for the polyester and polyester-15 wt%BSF-CHp. The results show that the composite has a lower density than the polyester. The lower value of density obtained for the composite can be associated with the lower values of density of CHp (0.95 g/cm3) and BSF (1.12 g/cm3) which is lower than the density of polyester. It can be concluded lower weight helmet that will not be too heavy and the same protect the safety of the personnel can be produced from this formulation.
XRD pattern of the polyester and composite are displayed in . The addition of CHp and BPF in the polyester has a resulting nucleating effect. There was a great difference between the XRD patterns of the composite from that of the matrix. From the XRD pattern of the composite, additional low reflections are obtained. The addition of the reinforcement to the matrix changes the characteristic peak position and the reinforcement effect increases the bulk crystallinity.
FTIR help to give information on the functional group in the materials. The FTIR results obtained in this research are shown in and . The FTIR patterns of all the samples under investigation have a different shape. The higher band peak of 1020 cm–1 was obtained for the BSF. The band at 3753 cm–1 – 3278.91 cm–1 of the BSF can be referred to as hydroxyl groups, while the band at 1595.3–1319.5 cm–1 and 1040–1020 cm–1 refers to C–C, C = C, OH, CO, CHn, CH, and C–O – C. This band observed confirm that the BSF contains cellulose, hemicellulose, and lignin that are associated with natural fibres. This work is in par with the work of Pothan, Thomas, and Neelakantan (Citation1997)
Table 3. Major peaks in the FTIR analysis
FTIR bands of CHp become very prominent when the major components in its FTIR spectrum major component are hydroxyapatite and collagen (see ). The band of the CHp at 84.98 cm−1 and 10,287–1367.9 cm−1 refer to hydroxyapatite, while the band at 2165–3697.5 cm−1 associated with collagen and 1423.8 cm−1 can be referred to carbonate. These FTIR bands obtained are in par with the works of Arnold, Marshall, and Wood (Citation1990), Arthanarieswaran., Kumaravel, and Kathirselvam (Citation2014).
In it was observed that the polyester matrix and the developed composite, there spectrum are similar; however, there are small additional peaks in the composite. These additional peaks obtained in the composite can be attributed to the presence of CHp and BSF that alter the bands. In the polyester, the band at 3060 and 1106 cm−1are refer to the O–H, C = O group in the polymer. The stretching at C-H and bending C-H group of the polymer were obtained at 2922 and 2322.1 cm−1. The composite has the same bands obtained in the polymer with the presence of 3652.8 cm−1 which was obtained for CHp and BSF. Increases in the band of the composite than that of the polyester was one of the factors for the enhancement in properties of the composite. The results are in par with the work of Oksman et al. (Citation1998), Natsa, Akindapo, and Garba (Citation2015).
The stress-strain graph is shown in and . It can be observed that both graphs are similar in shape; however, the composite has higher modulus and strength than the polymer matrix. For example, an elastic modulus of 378.13 and 465.92 MPa was obtained for the polyester and the developed composite. The high modulus obtained for the composite was attributed to the fact that the reinforcement used was able to increase the stiffness of the polyester matrix. Tensile strength of 29.45 and 57.33 MPa were obtained for the polyester and the developed composite which corresponded to 94.66% enhancement of the polyester matrix after the addition of 15 wt%BSF and 4 wt%CHp. The high tensile strength obtained for the composite was attributed to the fact that the reinforcement used was able to strengthen and transfer the load to the matrix in question. This observation obtained was in par with the work of Nuhu et al., (Citation2015) and Natsa et al., (Citation2015).
Figure 8a. displays the fractured image of the polyester and the composite. The fracture surface of the polyester matrix revealed spherulites and linear boundaries, interlammeller amorphous surface associated with polyester matrix (). This chain of interlammeller amorphous surface was altering with the addition of CHp and BSF. High agglomeration and segregation of reinforcement were not observed in , the fibres were seen visible around with dense-pack CHp. These images obtained for the composite were the main reason for the higher impact energy and strength obtained for the composite. (a) SEM image of the polyester matrix. (b) SEM image of the developed composite
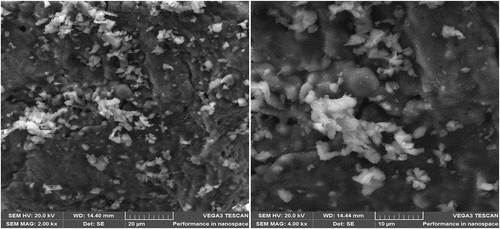
displays the hardness value and flexural strength of the developed composite and polyester. It can be observed that the hardness values and flexural strength increased with the addition of 15 wt%BSF and 4 wt%CHp. For example, a flexural strength of 46.71 and 75.23 MPa and hardness values of 10.5 and 15.6HRB were obtained for the polyester and polyester-15 wt%BSF-4 wt%CHp, respectively. The high flexural strength obtained is attributed to the BSF which helps to toughen the material under bending and enable the matrix to withstand gross deformation under bending load. It can be concluded that hybridisation using CHp and BSF can effectively be used in the enhancement of the hardness value and flexural strength of polyester for possible helmet production.
Impact energy value of 2.34 and 6.43 J/mm2 were obtained for the polyester and composite. A 174.79% increment in impact energy was obtained when compared with the polyester. The high level of impact energy obtained was attributed to the toughening and strengthening obtained from the BSF which help to increase the area under the stress-strain curve of the composite. However, the level of impact energy, strength and hardness values obtained in this work are within the ranges established by other scholars using natural fibres as displayed in and within the range of values for the production of a military helmet in accordance with military helmet (NIJ Standard Citation0106.01:1981), Helmets and PN-V-87001: (Citation1999) Light ballistic armour.
Table 4 Comparison with previous work
4. Conclusions
The work has established new reinforcement using CHp and BSF for the production of polyester composite for possible use in the production of a military helmet. From the discussion above the following can be the silent conclusion in this work.
New composite of polyester using CHp and BSF as reinforcement was successfully produced.
Lower weight helmet that will not be too heavy and the same protect the safety of the personnel can be produced from this formulation.
A 94.66% enhancement in tensile strength and 174.79% of the impact energy were obtained.
The values of the impact energy, hardness values, strength and ballistic resistance obtained in this work are within the range for the production of military helmet
Acknowledgments
The authors hereby appreciate and acknowledge the Department of Mechanical Engineering, Ahmadu Bello University Zaria Nigeria, for their support.
Disclosure statement
No potential conflict of interest was reported by the authors.
Additional information
Notes on contributors
M.Y Abdulrahim
M.Y Abdulrahim is a PhD student in the Department of Mechanical Engineering, Ahmadu Bello University Zaria. He obtained his Bachelors’ Degree in Mechanical Engineering in 2006 from the University of Ilorin, Nigeria. He also obtained a Masters’ Degree in Production Engineering in 2013 from the Nigerian Defence Academy, Kaduna, Nigeria. His research interests is in Advanced Materials, specifically in the area of converting “waste to wealth”.
D. S Yawas
D. S Yawas is a full professor in the Department of Mechanical Engineering, Ahmadu Bello University Zaria, Nigeria. His scientific activity is focused on Material Development, Mechanical designs, Rheological; Shear-thickening; Shear-thinning; Biodegradation; FTIR analysis.
R.A Mohammed
R.A Mohammed is a full professor in the Department of Metallurgy and Materials Engineering, Ahmadu Bello University Zaria, Nigeria. His research interests include Process Metallurgy, Iron and steel making, Thermodynamics of Metallurgy, Polymer and plastic Engineering. He is currently the Head of Metallurgy and Materials Engineering Department.
M.O Afolayan
M.O Afolayan is a Senior lecturer in the Department of Mechanical Engineering, Ahmadu Bello university Zaria. He holds a PhD in Mechanical Engineering. His specialty is Embedded systems, mechatronics and robotics with keen interest in using non-conventional materials for building device mechanical structure.
References
- Abdulrahim MY. 2019. Development of military anti-crash helmet shell from polyester resin reinforced banana pseudo stem fibre and cow horn particles hybrid composites, Ph.D. thesis ongoing Mechanical Engineering, Ahmadu Bello University Zaria Nigeria, ongoing.
- Ademoh, N. A., and O. C. Olanipekun. 2015. “Production of Motorcycle Anti-Crash Helmet Shell from Composite Reinforced with Male Flower Bunch Stalk Fibre of Elaeis Guineensis.” American Journal of Materials Engineering and Technology 3 (2): 27–34. 2015a.
- Ariff, T. F., M. E. Jalil, and R. Bahar. 2014. “Design Improvements in the Inner Shell of a Motorbike Helmet Using Coconut Fiber Composite.” Abstract of Emerging Trends in Scientific Research 2: 1–7.
- Arnold, W. S., I. H. Marshall, and J. Wood. 1990. “Optimum Design Considerations for Mechanically Fastened Composite Joints.” Composite Structures 16 (1–3): 85–101. doi:https://doi.org/10.1016/0263-8223(90)90068-P.
- Arthanarieswaran., V. P., A. Kumaravel, and M. Kathirselvam. 2014. “Evaluation of Mechanical Properties of Banana and Sisal Fiber Reinforced Epoxy Composites: Influence of Glass Fiber hybridization.” Materials and Design 4 (9): 194–202.
- ASTM D2344 / D2344M. 2016. Standard Test Method for Short-Beam Strength of Polymer Matrix Composite Materials and Their Laminates
- ASTM D256 – 10. 2018. Standard Test Methods for Determining the Izod Pendulum Impact Resistance of Plastics
- ASTM D3039 / D3039M. 2017. Standard Test Method for Tensile Properties of Polymer Matrix Composite Materials
- ASTM D785 – 08. 2015. Standard Test Method for Rockwell Hardness of Plastics and Electrical Insulating Materials
- ASTM E2809 - 2013. Standard Guide for Using Scanning Electron Microscopy/X-Ray Spectrometry in Forensic Paint Examinations
- Atuanya, C. U., A. O. A. Ibhadode, and A. C. C. Igboanugo. 2011. “Potential of Using Recycled Low-density Polyethylene in Wood Composites Board.” Tribology in Industry 33 (1): 11–17.
- Bahadur, S., D. Gong, and J. W. Anderegg. 1993. “Tribochemical Studies by XPS Analysis of Transfer Films of Nylon 11 and Its Composites Containing Copper Compounds.” Wear 165 (2): 205–212. doi:https://doi.org/10.1016/0043-1648(93)90336-K.
- Bledzki, A. K., and J. Gassan. 1999. “Composites Reinforced with Cellulose Based Fibres.” ProgPolym.Sci 24: 221–274.
- Gogineni, S., X. L. Gao, N. V. David, and J. Q. Zheng. 2012. “Ballistic Impact of Twaron CT709® Plain Weave Fabrics.” Mechanics of Advanced Materials and Structures 19 (6): 441–452. doi:https://doi.org/10.1080/15376494.2011.575532.
- Haneefa, A., P. Bindu, I. Aravind, and S. Thomas. 2008. “Studies on Tensile and Flexural Properties of Short Banana/glass Hybrid Fiber Reinforced Polystyrene Composites.” Journal of Composite Materials 42 (15): 1471–1489. doi:https://doi.org/10.1177/0021998308092194.
- Jimoh, O. T., T. B. Mercy, M. Musa, and O. F. Idowu. 2014. “Development of Low Cost Adsorbent from Cow Horn for the Biosorption of Mn (II), Ni (II) and Cd (II) Ion from Aqueous Solution.” Research Journal of Applied Sciences Engineering & Technology 7 (1): 9–17.
- Kulkarni, S. G., X. L. Gao, S. E. Horner, J. Q. Zheng, and N. V. David. 2013. “Ballistic Helmets–their Design, Materials, and Performance against Traumatic Brain Injury.” Composite Structures 101: 313–331. doi:https://doi.org/10.1016/j.compstruct.2013.02.014.
- Murali, B., D. Chandramohan, S. K. Nagoor Vali, and B. Mohan. 2014. “Fabrication of Industrial Safety Helmet by Using Hybrid Composite Materials.” Journal of Middle East Applied Science and Technology (JMEAST) 15: 584–587.
- Natsa, S., J. O. Akindapo, and D. K. Garba. 2015. “Development of a Military Helmet Using Coconut Fiber Reinforced Polymer Matrix Composite.” European Journal of Engineering and Technology 3: 7.
- NIJ 2008. “NIJ Standard −0101.06: Ballistic Resistance of Personal Body.”
- NIJ Standard 0106.01 1981 “Standard for ballistic helmets.”
- Obele, C., and E. Ishidi. 2015. “Mechanical Properties of Coir Fiber Reinforced Epoxy Resin Composites for Helmet Shell.” Industrial Engineering Letters 5: 7.
- Oksman, K., and C. Clemons. 1998. “Mechanical Properties and Morphology of Impact-modified Polypropylene-Wood Flour Composites.” Journal of Applied Polymer Science 67 (9): 1503–1513. doi:https://doi.org/10.1002/(SICI)1097-4628(19980228)67:9<1503::AID-APP1>3.0.CO;2-H.
- Palta, E., H. Fang, and D. C. Weggel. 2018. “Finite Element Analysis of the Advanced Combat Helmet under Various Ballistic Impacts.” International Journal of Impact Engineering 112: 125–143. doi:https://doi.org/10.1016/j.ijimpeng.2017.10.010.
- Pamela, W. 2007. “The Life of Composite Materials.” Pp.1–29.polyester Hybrid Composites, Comp. Sci. Technol. 63 1377. Polymer Matrix Composites Journal of Mechanical Engineering and Polystyrene Composites, Journal of Composite Materials 42: 1471–1489.
- PN-V-87001. 1999 Light Ballistic Armor. Bullet- and Fragment-proof Ballistic Helmets. General Requirements and Testing
- Pothan, L. A., S. Thomas, and A. Neelakantan. 1997. “Short Banana FibreReinforcedPolyester Composites: Mechanical, Failure and Aging Characteristics”.” Journal of Reinforced Plastics and Composites 16 (8): 744–765. doi:https://doi.org/10.1177/073168449701600806.
- Rajasekar, K., K. Ashokkumar, and L. Narayanan. 2015. “Design and Analysis of Industrial Safety Helmet Using Natural Fibers.” International Journal of Innovations in Engineering and Technology (IJIET) 5 (3): 31–37.
- Yahaya, R., S. M. Sapuan, M. Jawaid, Z. Leman, and E.S. Zainudin. (2016). Investigating ballistic impact properties of woven kenaf-aramid hybrid composites. Fibers and Polymers 17 (2): 275–281. doi:https://doi.org/10.1007/s12221-016-5678-6