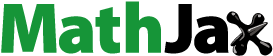
ABSTRACT
About one-fifth of coal ash produced by the thermal power plants are the bottom ash, and the rest is fly ash. During the past few decades, studies are made to use either of them as the partial replacement of sand in concrete manufacturing. The present study examines the behaviour of concrete manufactured by the complete replacement of natural sand with an optimum mixture of these ashes. The effect of fly ash and bottom ash mixture is ascertained through workability, strength tests, and resistance to acid attacks. It is observed that the mixture containing 50% fly ash and 50% bottom ash mix as fine aggregate has nearly the same compressive strength, 10% more split tensile strength, and higher flexural strength than the control concrete, yet, has 12.15% less density than the control concrete. The water absorption value and volume of pore space was found to be more for concrete containing the fly ash and bottom ash mixture. However, such concrete performed better in resisting sulphuric acid and sulphate attacks. All these conclusions suggested that the mixture containing 50% fly ash and 50% bottom ash may be used as a suitable replacement for natural sand in concrete in moderate environments.
1.0 Introduction
Thermal power plants produce enormous quantities of coal ash. About one-fifth of this ash content is bottom ash, and the rest is fly ash. Bottom ash has a granular structure due to which it is sometimes used as a replacement of sand in concrete. On the other hand, during the past few years, fly ash has been widely used in concrete as a replacement for cement. It is understood that, due to low calcium content in fly ash, the replacement of cement with it decreases initial strength development. Therefore, to limit such detrimental effect generally up to 30% of cement replacement is made. Since the amount of cement used in building and general construction works is about 20% of concrete volume, the overall use of fly ash in the concrete industry is much less. In contrast, the quantity of fine aggregate, which acts as inert filler within a concrete mix, is about 50–100% more than cement content. For that reason, if the purpose is to achieve the maximum usage of waste materials like coal ash; the full replacement of fine aggregate can be a better option. Further, fly ash is a pozzolanic material and contributes to strength development that can be an additional benefit.
Few studies are available in the literature on partial replacement of sand by fly ash. It is observed that the compressive strength (Siddique Citation2003a), and long-term corrosion resistance (Maslehuddinet al. Citation1989) of concrete has increased with an increase in the replacement level. But a high replacement level significantly decreases the workability and abrasion resistance (Siddique Citation2003b) of the resulting concrete. Due to that, the maximum replacement level was limited to 50% of fine aggregate volume. However, Bilir et al. (Citation2015) suggested that in mortar preparation fly ash can replace up to 60%-70% of sand without causing significant degradation of its properties. Further, it is demonstrated by Lieberman et al. (Citation2016) that the presence of aluminate and silicate anions at the surface of the fly ash results in the fixation of substandard quarry sand used in concrete.
On the other hand, several studies are available on the replacement of sand with bottom ash. The bottom ash has a porous structure and with water absorption capacity more than natural sand. As a result, the addition of bottom ash in the concrete mix increases its water demand. Hence, the increase in the percentage of bottom ash in concrete decreases its workability (Bai, Darcy, and Basheer Citation2005; Gafoori and Bucholc Citation1996; Chun et al. Citation2008; Singh and Siddique, Citation2014a). Aramraks (Citation2006) reported that about 25%-50% extra water is required for obtaining workability similar to the control mix in concrete containing bottom ash as fine aggregate. However, Kou and Poon (Citation2009) observed that the workability of concrete increases when coal bottom ash is used in the saturated surface dry condition.
Simultaneously, the unit weight of coal bottom ash is significantly less than that of natural sand. Due to this, Andrade et al. (Citation2007) observed a 25% reduction in concrete weight by replacing sand with bottom ash. It is revealed from the literature that replacement of sand in limited quantity by bottom ash increases compressive, flexural, and split tensile strength properties of concrete (Kurama and Kaya Citation2008; Arumugam et al. Citation2011; Hashemi et al. Citation2018). Kim and Lee (Citation2011) used coal bottom ash as fine aggregate for developing high-strength light-weight concrete. However, the addition of bottom ash above a limit decreases strength development at an early age (Andrade, Rocha, and Cheriaf Citation2007). Singh and Siddique (Citation2014b; Citation2015) from the microstructural analysis revealed that after 28 days, the bottom ash begins showing pozzolanic activities. As a result, the concrete containing bottom ash shows an increased strength gain rate at a later age than the control concrete (Aggarwal, Aggarwal, and Gupta Citation2007; Singh and Siddique,Citation2014b; Singh and Siddique Citation2015). Therefore, Singh and Siddique (Citation2015) reported that at 90 days, the compressive strength of control concrete and strength of concrete containing high volumes of coal bottom ash as fine aggregate are comparable. It is also been reported that using the bottom ash as fine aggregate improves resistance to sulphate and sulphuric acid attacks (Siddique Citation2014b). Additionally, the porous structure of bottom ash increases the thermal insulation properties of the mortar (Torkittikul Citation2017). However, the resistance to abrasion and wear and tear decreases (Siddique Citation2013).
A few researches are also made on the simultaneous use of coal bottom ash as replacement for sand and fly ash as replacement for cement, respectively. Rafieizonooz (Citation2016) reported that the experimental mix containing 75% bottom ash and 20% fly ash shows improvements in compressive, flexural, and split tensile strength properties and drying shrinkage of concrete. Besides, the resistance to sulphate and sulphuric acid improved from the control concrete (Rafieizonooz Citation2017).
Previous studies have indicated that bottom ash could be used as a fine aggregate in concrete. However, the use of a high volume of bottom ash in concrete negatively affects the early-age strength development, which is undesirable. On the contrary, the outcomes of the research available on concrete containing fly ash as fine aggregate suggest that it improves strength properties of concrete up to 50% replacement level. In this case, the workability reduces. Therefore, a possibility is there to utilise fly ash and bottom ash mixture in an optimum ratio to completely replace natural sand in concrete, while attaining better workability, strength, and durability properties. The present research explores this aspect through several experimental investigations to study the behaviour of concrete produced using fly ash and bottom ash mixture proportioned in different ratios as fine aggregate.
2.0 Experimental programme
2.1 Materials
Ordinary Portland cement (OPC) of 43 grade confirming IS: 8112 (Citation1989) was used in this study. The specific gravity and compressive strength were found to be 3.15 and 48.3 N/mm2, respectively. Crushed granite stones of the nominal size of 10 mm and 20 mm were used as coarse aggregate. Natural sand obtained from the Mahanadi river bed in Odisha was used as fine aggregates for the preparation of the control mix. provides different properties measured for coarse aggregates and sand.
Table 1. Properties of coarse and sand used in this study
Coal fly ash and bottom ash were collected from the captive power generation plant of the Hindalco industry located at Hirakud in Odisha. The chemical compositions of these ashes are collected from the source industry and provided in .
Table 2. Chemical composition of bottom ash and fly ash used in the study
Particle size analysis revealed that 97% by mass of fly ash passed through 90-micron sieve, while 99.92% passed through 150-micron sieve. Similarly, shows the particle size distribution curve of bottom ash and natural sand confirming zone III used in concrete manufacturing. It was observed that about 32% of the bottom ash is finer than 90 µm, a size corresponding to 97% of the mass of fly ash. Therefore, the bottom ash was sieved to remove particles of size less than 90 µm before using it in concrete manufacturing. The specific gravity, water absorption, moisture content, loose and compacted densities, and fineness modulus of the fly ash and the sieved bottom ash used for concrete manufacturing are presented in . Fly ash being finer than bottom ash contains more interparticle void space resulting reduction in loose density. Furthermore, smaller particle size in fly ash results in more surface area and hence more friction. As a result upon tapping, the flow of particles becomes more difficult and thus results in less compacted density for fly ash. Hence, the loose density and compacted density of fly ash are low compared with the bottom ash.
Table 3. Physical properties of fly ash and bottom ash used in concrete manufacturing
Polycarboxylic ether polymer-based superplasticizer named Auramix 300 was used for obtaining desired and uniform workability for the concrete mixes. The PH and specific gravity of the superplasticizer were found to be 5.76 and 1.06, respectively.
2.2 Concrete mix proportioning
Control concrete mix (CC01) of grade M25 was prepared according to provisions of IS: 10262 (Citation2009) using OPC 43-grade cement, coarse aggregate and natural sand as the fine aggregate. The water–cement ratio is fixed at 0.50. The workability of the concrete mix was assessed through the slump cone test according to IS: 1199 (Citation1959). The superplasticizer is added to the concrete mix to obtain a target slump value of 80 ± 05 mm.
This is followed by the preparation of five coal-ash-based concrete mixes keeping the quantities of cement, coarse aggregate, and superplasticizer constant. The fine aggregate was entirely replaced by varying percentages of fly ash and bottom ash mixture. In the concrete codes, the water requirement is represented in the water–cement ratio form. However, both fly ash and bottom ash are porous and have a particle size finer than the natural sand. In the present case, it is observed that 97% of fly ash passes through the 90-micron IS sieve. As a result, they require additional water to maintain a similar degree of workability. Hence, in this study, the water requirement is measured in the water-fines ratio form where the fines represent the weight of cement and the weight of particle size below 90µ contained in the fly ash. Although about 32% of bottom ash is also passing through the 90 µ sieve, they have been removed before its use in concrete manufacturing. Therefore, the fine contained in the bottom ash is excluded from the calculation of the water-fine ratio. represents different concrete mixes considered in the present study and the water requirement to achieve the target slump value of 80 ± 05 mm.
Table 4. Concrete mixes prepared for the study and their slump values
2.3 Study of strength properties for hardened concrete
The compressive strength, split tensile strength, and flexural strength properties of hardened concrete were evaluated according to relevant Indian codes. Cube specimens of 150 mm size and cylindrical specimens of diameter 150 mm and height 300 mm were prepared and tested under a 2000 KN capacity compression testing machine for assessment of compressive and split tensile strength, respectively. Additionally, beam specimens of 100 mm × 100 mm × 500 mm size were prepared for the assessment of the flexural strength and tested under a 100 KN capacity flexure testing machine. Nine test specimens were prepared for each mix designations so that each experiment can be conducted on three specimens after 7-day, 28-day, and 90-day. The average values for these three specimens were noted for evaluation.
2.4 Study of density, water absorption and volume of voids in hardened concrete
The effect of fly ash and bottom ash mixture as a complete replacement of natural sand on density, water absorption, and volume of voids for hardened concrete is determined according to ASTM C642-13 (Citation2013). These tests were performed on concrete cubes containing the optimum ratio of fly ash and bottom ash mixture, which provided the maximum compressive strength. These results were then compared with concrete control specimens. These tests were conducted on 100 mm concrete cubes after 28 days of curing.
2.5 Study of resistance to sulphuric acid and sulphate attacks
The resistance of concrete specimens to external acid and sulphate attacks was evaluated according to ASTM C267-01 (Citation2006). The tests were conducted on concrete cubes containing the optimum ratio of fly ash and bottom ash mixture, which provided maximum compressive strength, and the results were compared with concrete control specimens. Concrete specimens of size 100 mm × 100 mm × 100 mm cubes were cast and cured for 28 days. After that, to study the resistance to sulphuric acid, the specimens were immersed in 3% sulphuric acid solutions after 28 days of water curing. The changes in weight, appearance, and compressive strength of the specimen at the end of 7, 14 and 28 days of immersion in sulphuric acid solution were measured for determining the effect. Similarly, the resistance to sulphate attack was determined by immersing the 28-days water cured specimens in 10% magnesium sulphate solution and then measuring the changes in weight, appearance, and compressive strength of the specimen after 28, 56, and 84 days of immersion.
3.0 Results and discussions
3.1 Effects on water requirement
Fly ash and bottom ash have high water absorbing capacity. Therefore, extra water was added to obtain the slump within the desired range. As shown in , the concrete mixture containing 100% bottom ash displayed a slump value of 85 mm for 225.7 litres of water. In comparison, control concrete requires 197 litres of water to provide the same slump value. The change in water requirement with the variation of fly ash and bottom ash is shown in . Further, with the increase of fly ash content in the concrete mixture, the water requirement also increases linearly for maintaining a constant slump. In the mathematical form, the water requirement for concrete containing fly ash and bottom ash mixtures can be expressed in the form given below.
where represents the water requirement in control concrete, F and B represent the weight of fly ash and bottom ash, respectively. It can be observed from the figure that, for C4F0B specimens where sand is completely replaced by fly ash as fine aggregate, 290.7 litres of water were required to obtain a slump value of 76 mm. Concrete mix designations C2F2B where 50% fly ash and 50% bottom ash mixture is used as fine aggregate showed a slump value of 78 mm for 248.3 litres of water.
The irregular shape and rough texture of bottom ash particles (Singh and Siddique Citation2015) increase friction and decrease flow characteristics. Due to this, additional water is needed to maintain constant workability. In comparison, the spherical fly ash particles when used in saturated surface dry condition improve flow characteristics due to the increased ball-bearing effect (Siddique Citation2003a). But when used in dry condition, both bottom ash and fly ash absorb some of the water to fill the pores. Further, because of the smaller particle size, fly ash needs additional water to lubricate larger surface areas. Therefore, the addition of fly ash shows a net increase in water requirement to maintain the same state of workability.
3.2 Effects on strength properties
3.2.1 Effect on compressive strength
The compressive strength of control concrete specimens and specimens containing various proportions of fly ash and bottom ash mixture as fine aggregate are presented in . It can be observed from the figure that the compressive strength development pattern of concrete containing bottom ash and fly ash mixer as fine aggregate is similar to that of control concrete. Yet it can be seen from the figure that the strength of concrete specimens containing coal bottom ash and fly ash mixture as fine aggregate showed a continuous and significant increase in compressive strength after 28 days. After 7 days, the control concrete gained 69.6% of its 28-day compressive strength. In comparison, after 7 days, the concrete containing bottom ash and fly ash mixtures as fine aggregate attained 70.14% to 97% of the compressive strength gained by control concrete during the same period. In absolute term after 28 days, the control concrete mix gained compressive strength of 32.1 N/mm2, whereas, after 28 days, concrete specimens containing bottom ash and fly ash mixtures as fine aggregate attained 21.6–31.8 N/mm2 compressive strength.
The rate of strength gain after the first 28 days slowed down for the control concrete. It is evident from the fact that at the end of 90 days, the control concrete gained an additional 11.5% strength over the 28 days compressive strength. In comparison, concrete containing fly ash and bottom ash mixture as fine aggregate has gained an additional 16% to 28.7% strength between 28 days to 90 days. It can be noted from the figure that the concrete containing more fly ash gained higher additional strength during this prolonged curing period than the concrete containing more bottom ash. This is due to pozzolanic reaction of the fly ash.
The replacement of natural sand by fly ash and bottom ash mixture reduces the early age strength gain of concrete. This is mainly because both bottom ash and fly ash are weaker materials than natural sand. Moreover, these are more porous and absorb water from the surrounding concrete paste, thus providing a weaker transition zone. Additionally, during the initial curing ages, the pozzolanic action is less prominent due to the unavailability of Ca(OH)2. Due to this, additional strength cannot develop. However, during 28 to 90 days, sufficient Ca(OH)2 has been released due to hydration of OPC and thus accelerating the pozzolanic action. Hence, during this period, the concrete mixture containing fly ash and bottom ash mixture as fine aggregate could gain more compressive strength than the control concrete mixture.
Out of the five mix designations containing fly ash and bottom ash mixture as fine aggregate, the mix designation C2F2B showed the best result at 28 days. Although the mix designation C1F3B containing 75% of bottom ash and 25% of fly ash showed good results at the end of 07 days and comparable results with control concrete at the end of 28 days, the fly ash utilisation in the case of C1F3B is less than C2F2B. Considering this, the concrete mix designation C2F2B is the best option for fine aggregate replacement as it provides maximum compressive strength and simultaneously consumes maximum fly ash.
The bottom ash lowers the alkalinity of the pore solution and thus delays the hydration process (Singh and Siddique Citation2015). Although bottom ash is a pozzolanic material, owing to its larger particle size it exhibits pozzolanic activities only at a later date. It is evident from the fact that despite a reduction in strength at 7 days and 28 days, there is a net gain in strength at 90 days for C0F4F over CC01. In comparison, fly ash has a smaller particle size and hence shows an early pozzolanic reaction. As a result, the concrete mix attains a higher compressive strength when the combination of bottom ash and fly ash particles is used. On the other hand, the pozzolanic reaction is dependent on the quantity of Ca(OH)2 liberated during the hydration which in turn is limited by the cement quantity. As a result, there is an optimum level of fly ash that takes part in the pozzolanic reaction and the leftover remains inert in the matrix. Due to these reasons, the C2F2B mix shows the highest compressive strength.
3.2.2 Effect on split tensile strength
The splitting tensile strengths of concrete containing fly ash and bottom ash mixture as fine aggregate are given in . It may be observed from the figure that the inclusion of coal fly ash and bottom ash as fine aggregate in concrete improves the splitting tensile strength of concrete at all curing ages except C4F0B. It is observed from the results that, at an early curing age of 7 days, the concrete mix designations C0F4B, C1F3B, C2F2B, C3F1B, and C4F0B were achieved 79.4%, 80.93%, 80.82%, 82.64% and 91.67% of their respective 28-day splitting tensile strength. In comparison, the control mix has achieved 82.8% of its 28-day, splitting tensile strength. Similarly, at 90 days, the split tensile strength achieved by concrete designations C0F4B, C1F3B, C2F2B, C3F1B, and C4F0B are 118.5, 114.3, 113.8 118.5 and 109.21% of their respective 28-day splitting tensile strength. In comparison to this, the split tensile strength at 90 days for control concrete is 115.4% of its 28-day split-tensile strength. Therefore, it may be concluded that the concrete containing fly ash and bottom ash mix mixture as fine aggregate replacement gains split-tensile strength similar to control concrete.
Further, it is observed from the figure that, at the end of 28 days the split tensile strength of concrete containing fly ash and bottom ash mixture as fine aggregate surpasses the split tensile strength of control concrete by 4.3%, 8.6%, 14.06% and 3.5%, respectively, for C0F4B, C1F3B, C2F2B, and C3F1B mix designations. Similarly, at the end of 90 days, the strength of control concrete was surpassed by 5.3%, 0.66%, 9.2% and 4.30%, respectively, for the above mix designations. Therefore, in all the above cases, the concrete mix designation C2F2B provides the maximum splitting tensile strength. Hence, the results showed that the compressive strength of concrete containing fly ash and bottom ash mixture had achieved improved compressive strength at a faster rate than the splitting tensile strength.
3.2.3 Effect on flexural strength
The flexural strength of the beam made with concrete containing bottom ash and fly ash mixture as fine aggregate is evaluated and presented in . It is noticed from the figure that, at the end of 7 days, concrete mixtures C0F4B, C1F3B, C2F2B, C3F1B, and C4F0B achieved 94.08%, 95.72%, 101.98%, 91.77% and 84.21% of flexural strength of CC01. Similarly, at the end of 90 days of the curing period, concrete mixtures C0F4B, C1F3B, C2F2B, C3F1B, and C4F0B gained 14.92%, 13.28%, 11.38%, 10.72% and 14.97% over their respective 28 days flexural strengths . The control concrete, in comparison, has gained an additional 12.53% of flexural strength over its 28-day flexural strength.
Therefore, it may be concluded that the concrete containing fly ash and bottom ash mixture as fine aggregate show a similar trend in strength gain as that of control concrete. Yet, the concrete mix designation C2F2B, containing 50% of fly ash and 50% bottom ash mixture as fine aggregate, showed optimum flexural strength at the end of the 7, 28 and 90 days curing period. As from the earlier studies, it was seen that this mix designation performed better in compressive strength and split tensile strength test also and utilises a maximum quantity of fly ash, and hence it was considered for durability assessment.
3.3 Effect on density, water absorption and volume of voids hardened concrete
The density of concrete, the water absorption value, and the volume of voids are related to each other. The presence of pores reduces the density and provides a vent for the permeation of fluids. The effects of incorporating ash and bottom ash mixture in concrete as fine aggregate on these parameters are provided in . It can be observed from the table that the density of concrete C2F2B containing 50% fly ash and 50% bottom ash mixture is 12.15% less than the control concrete. This is because the density of fly ash and bottom ash is significantly less than the natural river sand. The lower density of C2F2B concrete helps to reduce the dead weight and seismic weight in the structure. This, in turn, reduces member size and support requirements, thus ensuring further reduction in dead load. However, both fly ash and bottom ash are porous due to which, for the C2F2B concrete the water absorption capacity and the volume of void space are 6.85% and 12.53%, respectively, which is more than the control concrete. Hence, further study is required to establish the performance of present concrete against the snow or frost action and other aggressive environments.
Table 5. Comparison of density, water absorption and volume of voids for control concrete and concrete containing fly ash and bottom ash mixture as fine aggregate
3.4 Resistance to sulphuric acid and sulphate attacks
3.4.1 Effect on resistance against sulphuric acid
Sulphuric acid attacks calcium hydroxide produced during cement hydration and produces gypsum. This gypsum then reacts with tri-calcium aluminate hydrate to form ettringites and ultimately leading to cracking and spalling in concrete. The effect of fly ash and bottom ash mixture on resistance to sulphuric acid is evaluated for C2F2B concrete and then compared with control concrete. The resistance to sulphuric acid is evaluated based on mass loss, loss in compressive strength, and the change in the appearance of concrete. The appearance of specimens at the end of 3, 7, 14, and 28 days of immersion in sulphuric acid solution are provided in and . It is seen from these figures that the CC01 on immersion in 3% sulphuric acid solution showed excess scaling and loss of materials while the effect is minimal on C2F2B concrete. Due to the excessive scaling and loss of materials, the surface of the control concrete specimens becomes highly uneven with exposed aggregate. Therefore, they are plastered with a thin mortar layer before conducting the compressive strength test. provides the mass loss and compressive strength of specimens after immersion of the concrete specimens in 3% sulphuric acid solutions.
Table 6. Effect of sulphuric acid on CC01 and C2F2B concrete
It is observed from that, after 7 days of immersion in 3% sulphuric acid solution, mass loss of control concrete CC01 is 5.04%. In comparison, the mass loss of the C2F2B specimen is 0.12%, which is only 2.4% of the mass loss observed in control concrete CC01. Similarly, at the end of 14 and 28 days, the mass loss in C2F2B is 3.8% and 7.6% of mass loss in CC01, respectively. Simultaneously, the compressive strength of CC01 is reduced by 36.63% after 7 days of immersion. In comparison, the reduction in the compressive strength of C2B2F is 6.67%. Similarly, after 14 days, the strength loss in C2B2F is 14.39% compared to 45.72% of CC01, and after 28 days, the strength of C2F2B was decreased by 24.45% compared to 50.10% of CC01. Therefore, it can be concluded from the above that the concrete containing fly ash and bottom ash mixture as fine aggregate provided better resistance to acid attack.
3.4.2 Effect on resistance against sulphate solution
The sulphate attack results in mass, strength loss, expansion, and scaling in concrete. Mass and strength loss occurs due to the attack of sulphate on hydrated cement paste, converting it into gypsum and leaving behind the cohesionless granular particles. Further, the reaction of sulphate to the hydrated aluminate phase results in the formation of ettringites causing expansion in concrete (Prasad, Jain, and Ahuja Citation2006). The sulphate attack is a slow process and does not dominate during the initial periods (Venkatanarayanan, and Rangaraju Citation2013). provides the mass loss and the compressive strength of concrete specimens after immersion in 10% magnesium sulphate solutions. It can be observed from the table that the mass loss after 84 days of immersion in magnesium sulphate solution is found to be 0.11% in the case of C2B2F, which is less than the control concrete. However, the strength of concrete is found to increase after immersion in a magnesium sulphate solution. It is observed that after the immersion of 84 days in the solution, the increase in compressive strength of C2B2F concrete is found to be 16.98% over the 28 days strength. In comparison, the control concrete CC01 gained 10.59% strength during the same period.
Table 7. Effect of magnesium sulphate solution on CC01 and C2F2B concrete
Some white patches of deposition were observed on the surface of the specimens after 84 days of immersion as shown in . As stated earlier, the magnesium sulphate solution produces both gypsum and ettringite. But the formation of ettringite is a slow process and associated with the cracking, spalling and softening of concrete specimens. It can be seen from that both CC01 and C2F2B gained strength during the test duration. Further, no visible crack or spalling could be observed on the surface. It is mainly due to insufficient exposure not long enough for the formation of ettringites (Amin et al. Citation2008). As the result, these white depositions are mostly gypsum.
4.0 Conclusions
Properties of concrete containing fly ash and bottom ash mixture as fine aggregate are evaluated through a series of experimental investigations. Water demand to maintain suitable workability, compressive strength, split tensile strength, and flexural strength properties of hardened concrete were evaluated to suggest an appropriate ratio of fly ash and bottom ash mix. Further, the effect of fly ash and bottom ash mixture on density, water absorption, and volume of voids, resistance to sulphuric acid, and sulphate attacks were evaluated. From the results, the following conclusions were drawn:
Fly ash and bottom ash, when used as fine aggregate, reduces the early age compressive strength development. However, both fly ash and bottom ash being pozzolanic material increases the strength development of the later ages. It is observed that the compressive strength of C2F2B incorporating 50% fly ash and 50% bottom ash mix as fine aggregate has strength nearly equal to the compressive strength of control concrete at the end of 28 days.
It is observed that the splitting tensile strength for C2F2B concrete is nearly 10% more than the control concrete. The flexural strength of the C2F2B mix designation is slightly more than the control concrete.
The density of C2F2B concrete is 12.15% less than the control concrete, which is useful in building lightweight structures. However, the water absorption value and volume of pore space is greater compared to the control concrete. This may cause a problem for construction in regions affected by snow or frost action.
The concrete containing fly ash and bottom ash mixture as fine aggregate performed better against sulphuric acid and sulphate attacks. After 28-day immersion in sulphuric acid, the mass loss for CF2B concrete is 0.85%. In comparison, the mass loss is 11.16% for control concrete CC01. Similarly, C2F2B concrete loses 50% less compressive strength than the CC01 after 28 days of immersion in a 3% sulphuric acid solution. Also, in a 10% magnesium sulphate solution, the concrete containing C2B2F performed better than the control concrete.
Therefore, the conclusions of all these tests suggest that the mixture containing 50% fly ash and 50% bottom ash may be used as a suitable replacement for natural sand in concrete in moderate environments without affecting the strength. However, further studies are needed to establish its durability under extreme exposure conditions.
Disclosure statement
No potential conflict of interest was reported by the authors.
Additional information
Notes on contributors
Bharadwaj Nanda
Bharadwaj Nanda is currently working as an Assistant Professor in the Department of Civil Engineering at the Veer Surendra Sai University of Technology, Burla, India. He holds a PhD degree in structural engineering. His research interests include sustainable concrete making materials, structural damage assessment, and retrofitting. He has published more than 40 papers in international journals of repute and conference proceedings. He has also handled several sponsored research and industrial consultancy projects and guided several research scholars.
Sudipta Rout
Sudipta Rout holds a master degree in structural engineering from Veer Surendra Sai University of Technology, Burla, India. His areas of research include sustainable concrete and optimum design of structural systems.
References
- Aggarwal, P., Y. Aggarwal, and S. M. Gupta. 2007. “Effect of Bottom Ash as Replacement of Fine Aggregates in Concrete.” Asian Journal of Civil Engineering (Building andHousing) 8 (1): 49–62.
- Amin, M. M., S. B. Jamaludin, F. C. Pa, and K. K. Chuen. 2008. “Effects of Magnesium Sulfate Attack on Ordinary Portland Cement (OPC) Mortars.” Portugaliae Electrochimica Acta 26 (2): 235–242. doi:https://doi.org/10.4152/pea.200802235.
- Andrade, L., J. C. Rocha, and M. Cheriaf. 2007. “Evaluation of Concrete Incorporating Bottom Ash as a Natural Aggregates Replacement.” Waste Management 27 (9): 1190–1199. doi:https://doi.org/10.1016/j.wasman.2006.07.020.
- Aramraks, T., 2006. Experimental Study of Concrete Mix with Bottom Ash as Fine Aggregate in Thailand. In Symposium on infrastructure development and the environment, 7-8 December 2006, University of the Philippines, Diliman, Philippines, (pp. 1–5).
- Arumugam, K., R. Ilangovan, and J. D. Manohar. 2011. “A Study on Characterization and Use of Pond Ash as Fine Aggregate in Concrete.” International Journal of Civil and Structural Engineering 2 (2): 466.
- ASTM C267-01. 2006. Standard Test Methods for Chemical Resistance of Mortars, Grouts, and Monolithic Surfacings and PolymerConcretes. ASTM International, WestConshohocken, USA.
- ASTM C642-13, Standard Test Method for Density, Absorption, and Voids in Hardened Concrete. ASTM International, WestConshohocken, USA, 2013.
- Bai, Y., F. Darcy, and P. A. M. Basheer. 2005. “Strength and Drying Shrinkage Properties of Concrete Containing Furnace Bottom Ash as Fine Aggregate.” Construction and Building Materials 19 (9): 691–697. doi:https://doi.org/10.1016/j.conbuildmat.2005.02.021.
- Bilir, T., O. Gencel, and I. B. Topcu. 2015. “Properties of Mortars with Fly Ash as Fine Aggregate.” Construction and Building Materials 93: 782–789. doi:https://doi.org/10.1016/j.conbuildmat.2015.05.095.
- Chun, L. B., K. J. Sung, K. T. Sang, and S. T. Chae, 2008. A Study on the Fundamental Properties of Concrete Incorporating Pond-ash in Korea. In: Proceedings of the 3rd international conference of the Asian Concrete Federation & Vietnam Concrete Association (ACF/ VCA) on the sustainable concrete technology and structures sustainable concrete technology and structures in local climate and environmental conditions. Vietnam; 11–13 November 2008 p. 401–408..
- Ghafoori, N., and J. Bucholc. 1996. “Investigation of Lignite-based Bottom Ash for Structural Concrete.” Journal of Materials in Civil Engineering 8 (3): 128–137. doi:https://doi.org/10.1061/(ASCE)0899-1561(1996)8:3(128).
- Hashemi, S. S. G., H. B. Mahmud, J. N. Y. Djobo, C. G. Tan, B. C. Ang, and N. Ranjbar. 2018. “Microstructural Characterization and Mechanical Properties of Bottom Ash Mortar.” Journal of Cleaner Production 170: 797–804. doi:https://doi.org/10.1016/j.jclepro.2017.09.191.
- IS: 1199. 1959. Indian Standard Methods of Sampling and Analysis of Concrete. Bureau of Indian Standards, New Delhi, India
- IS: 8112. 1989. Specification for 43 grade ordinary Portland cement. Bureau of Indian Standards, New Delhi, India.
- IS: 10262. 2009. Recommended Guidelines for Concrete Mix Design. Bureau of Indian Standards, New Delhi, India
- Kim, H. K., and H. K. Lee. 2011. “Use of Power Plant Bottom Ash as Fine and Coarse Aggregates in High-strength Concrete.” Construction and Building Materials 25 (2): 1115–1122. doi:https://doi.org/10.1016/j.conbuildmat.2010.06.065.
- Kou, S. C., and C. S. Poon. 2009. “Properties of Concrete Prepared with Crushed Fine Stone, Furnace Bottom Ash and Fine Recycled Aggregate as Fine Aggregates.” Construction and Building Materials 23 (8): 2877–2886.
- Kurama, H., and M. Kaya. 2008. “Usage of Coal Combustion Bottom Ash in Concrete Mixture.” Construction and Building Materials 22 (9): 1922–1928. doi:https://doi.org/10.1016/j.conbuildmat.2007.07.008.
- Lieberman, R. N., X. Querol, N. Moreno, Y. Mastai, and H. Cohen. 2016. “Physical and Chemical Changes in Coal Fly Ash during Acidic or Neutral Wastes Treatment, and Its’ Effect on the Fixation Process.” Fuel 184: 69–80. doi:https://doi.org/10.1016/j.fuel.2016.06.107.
- Maslehuddin, M., A. I. Al-Mana, M. Shamim, and H. Saricimen. 1989. “Effect of Sand Replacement on the Early-Age Strength Gain and Long-Term Corrosion-Resisting Characteristics of Fly Ash Concrete.” Materials Journal 86 (1): 58–62.
- Prasad, J., D. K. Jain, and A. K. Ahuja. 2006. “Factors Influencing the Sulphate Resistance of Cement Concrete and Mortar.” Asian Journal of Civil Engineering (Building and Housing) 7 (3): 259–268.
- Rafieizonooz, M., J. Mirza, M. R. Salim, M. W. Hussin, and E. Khankhaje. 2016. “Investigation of Coal Bottom Ash and Fly Ash in Concrete as Replacement for Sand and Cement.” Construction and Building Materials 116: 15–24. doi:https://doi.org/10.1016/j.conbuildmat.2016.04.080.
- Rafieizonooz, M., M. R. Salim, M. H. Hussin, J. Mirza, S. M. Yunus, and E. Khankhaje. 2017. “Workability, Compressive Strength and Leachability of Coal Ash Concrete.” Chemical Engineering Transactions 56: 439–444.
- Siddique, R. 2003a. “Effect of Fine Aggregate Replacement with Class F Fly Ash on the Mechanical Properties of Concrete.” Cement and Concrete Research 33 (4): 539–547. doi:https://doi.org/10.1016/S0008-8846(02)01000-1.
- Siddique, R. 2003b. “Effect of Fine Aggregate Replacement with Class F Fly Ash on the Abrasion Resistance of Concrete.” Cement and Concrete Research 33 (11): 1877–1881. doi:https://doi.org/10.1016/S0008-8846(03)00212-6.
- Siddique, R. 2013. “Compressive Strength, Water Absorption, Sorptivity, Abrasion Resistance and Permeability of Self-compacting Concrete Containing Coal Bottom Ash.” Construction and Building Materials 47: 1444–1450. doi:https://doi.org/10.1016/j.conbuildmat.2013.06.081.
- Singh, M., and R. Siddique. 2014a. “Strength Properties and Micro-structural Properties of Concrete Containing Coal Bottom Ash as Partial Replacement of Fine Aggregate.” Construction and Building Materials 50: 246–256. doi:https://doi.org/10.1016/j.conbuildmat.2013.09.026.
- Singh, M., and R. Siddique. 2014b. “Compressive Strength, Drying Shrinkage and Chemical Resistance of Concrete Incorporating Coal Bottom Ash as Partial or Total Replacement of Sand.” Construction and Building Materials 68: 39–48. doi:https://doi.org/10.1016/j.conbuildmat.2014.06.034.
- Singh, M., and R. Siddique. 2015. “Properties of Concrete Containing High Volumes of Coal Bottom Ash as Fine Aggregate.” Journal of Cleaner Production 91: 269–278. doi:https://doi.org/10.1016/j.jclepro.2014.12.026.
- Torkittikul, P., Nochaiya, T., Wongkeo, W. and Chaipanich, A., 2017. Utilization of coal bottom ash to improve thermal insulation of construction material. Journal of material cycles and waste management 19(1): 305–317. doi:https://doi.org/10.1007/s10163-015-0419–2
- Venkatanarayanan, H. K., and P. R. Rangaraju. 2013. “Evaluation of Sulfate Resistance of Portland Cement Mortars Containing Low-carbon Rice Husk Ash.” Journal of Materials in Civil Engineering 26 (4): 582–592. doi:https://doi.org/10.1061/(ASCE)MT.1943-5533.0000868.