ABSTRACT
By using a functional requirement analysis, through Design for Manufacture and Assembly and Design for Environment principles, this paper aims at showing a new design method to improve the overall assembly features and environmental sustainability of a packaging solution. This method provides to rank functional requirements according to three different design specifications and also to the number of relationships they have with each other. At the same time, a ranked order of importance for the packaging parts has been realised, considering the number of performed functions. The purpose of this method is to support the designers in focusing their attention on the most important packaging parts and, at the same time, giving them a clear idea of which are the most important functional requirements to be satisfied. This study has been focused on domestic household packaging, but the provided method can be extended to any particular packaging solution and its findings are still valid. According to the Design for Environmental perspective, the actual and the new resulting packaging solutions have been then compared through Life Cycle Assessment method. The results have shown the new packaging solution being able to cut down the environmental impacts, on average, of approximately 30%.
1 Introduction
Packaging plays a very significant role in product protection for delivery phases (Fadiji et al. Citation2019). In the manufacturing industry, commodity delivery concerns internal logistics and external logistics, extended to providers, material suppliers, and sales (McDonald Citation2016). A packaging system consists of three levels known as primary, secondary, and tertiary packaging. Primary packaging is the first package to protect the product. Secondary packaging is used to protect the primary packaging. Lastly, the tertiary level concerns the packaging system used for bulk handling in warehousing and transportation. Tertiary packaging affects the logistics efficiency in supply chains inducing different requirements on the handling equipment, vehicles, etc. (Jahre and Hatteland Citation2004). In the context of household appliances and electronic devices, the tertiary packaging concerns pallets with plastic films or roll containers. Even if the principal purpose of a packaging system is product protection, the marketing requirements can affect the packaging of consumer goods (Favier, Celhay, and Pantin-Sohier Citation2019). The manufacturing delocalisation and the worldwide market have increased exponentially the transportation of goods between customers, producers, and end-users (Meherishi, Narayana, and Ranjani Citation2019). The impacts of the packaging materials have gained importance in terms of cost and environmental issues due to the increasing demand for protective solutions in product delivery (Pålsson and Hellström Citation2016). The waste related to packaging is a relevant problem in several countries such as Europe where: ‘Packaging waste is a growing and important waste stream, which accounts for between 15% and 20% of total municipal solid waste in different countries’ (OECD Citation2011).
The most used materials for the packaging of electronics and household appliances are the corrugated paper board (Frank Citation2014), card, wood, and plastics such as Polyurethane (EPU), Polyethylene (EPE), Polypropylene (EPP), and expanded polystyrene (EPS). Roughly 80% of the volume of all paper packaging used in the United States is in the form of corrugated boxes (Leatherdale Citation2005). Corrugated and honeycomb paperboard materials have been widely used also for their cushioning property (Zhang et al. Citation2012). Considering the interior parts of the packaging, Expanded Polystyrene (EPS), Polyurethane (EPU), Polyethylene (EPE) and Polypropylene (EPP) are the most popular cushioning materials thanks to their lightweight and excellent cushioning capabilities. Despite their functionality, the widespread use of these polymeric materials with fossil origin is under investigation in the literature (Gong et al. Citation2020). Moreover, plastic production is responsible for a significant amount of waste related to several industrial sectors. In Europe, the Packaging and Packaging Waste (PPW) directive regulates the reduction of environmental impacts in this context. The initiative of the European Commission (EC) requires an environmental responsibility in packaging design through green policies. This regulation forces enterprises to study eco-sustainable solutions for packaging to reduce relative resource consumption and environmental impacts. Therefore, several scholars have been studying recyclable, lightweight, recycled, and renewable packaging solutions to achieve an environment-friendly improvement. As a solution, bio-based materials are proposed instead of petrochemical-based plastics for packaging (Curling et al. Citation2017; Shanmugam et al. Citation2019). However, the applications of bio-based and modelled pulp solutions are limited by the relative cost and investment of the production equipment and machines involved. Therefore, these solutions are used more frequently and suitable in the packaging of small-medium sized products.
Only in the past few years, the strategic role of packaging design has been recognised both in theory and in practice. As Betancur-Muñoz et al. (Citation2014) claimed in their study, the packaging design has been mostly focused in the accomplishment of some specific objectives: cost; space-saving; material reduction, and quality problems avoidance (Netake et al. Citation2019). This design approach does not consider that the packaging is also utilised to handle, transport, distribute and promote the product. Nowadays, the role of packaging in industrial management continues to rise due to increased logistic costs, improved packaging technology, and enhanced environmental regulation. Therefore, a great interest is now focused on improving product-packaging operations by minimising the volume of material used and rationalising the number and types of packaging operations.
An approach proposed by Lee and Lye (Citation2003), called ‘Design for manual Packaging (DFPkg)’, was based on Design for Assembly (DfA) guidelines, since the activities related with packaging could be considered as assembly activities seeing that all the packed pieces are part of a unique system. In general, DfA methods seek to guide the design process to facilitate and optimise the assembly reliability in order to improve the quality of the product and the environment of the assembly system (Molloy, Warman, and Tilley Citation1998). An evolution of the DfA technique is the Design for Manufacturing and Assembly (DfMA) technique. It has been first introduced by Boothroyd (Citation1994), who synthesised the concepts of Design for Manufacturing (DfM) and DfA, already well-known ‘Design For X’ (DfX) techniques used in several concurrent engineering applications, into a single design approach. He recognised the fact that manufacturing decisions have an impact on assembly and vice-versa. Therefore, one method could integrate the two design techniques to reduce cost, errors, and time to market (Annamalai et al., Citation2013; Bevilacqua, Ciarapica, and Giacchetta Citation2007). DfMA has also been applied to the packaging field. In particular, Betancur-Muñoz et al. (Citation2014) presented an integral approach for packaging design, complementing the guidelines proposed by Lee and Lye (Citation2003) in key contexts of the packaging lifecycle. As highlighted by Koblasa, Šírová, and Králíková (Citation2019), the limit of these techniques in packaging design is related to the lack of analysis of logistical requirements. Abdallah et al. (Citation2015) pointed out that the Design for Logistics (DfL) is a study focused on economical packaging to optimise the use of space, parallel/concurrent processes to shorten the lead time, and standardisation. Storage systems play an essential part in the logistic chain. In this context, DfMA processes should be analysed with Design for Logistics (DfL) requirements. Furthermore, as stated by Favi, Germani, and Mandolini (Citation2016), a step forward would be to include other interesting production aspects, such as environmental impacts, energy consumptions, and so on, in order to shift the overall production features early in the conceptual design phase.
This study aims at providing a useful methodology to designers and company managers who combine DfMA and DfE principles to design and optimise the packaging solutions of products. The innovative aspect of this research consists in the realisation of a practical and customisable design tool. The tool is able to simultaneously evaluate assembly features and environmental impacts of the designed packaging solution, this latter obtained by considering the most important functional requirements, design specifications, and components of the packaging solution itself. In doing so, this study follows the approach of Le Pochat, Bertoluci, and Froelich (Citation2007) who stated specific tools used in DfE methodology can be divided into two main categories: environmental assessment and environmental improvement tools. As environmental assessment tool, this study has used the Life Cycle Assessment (LCA) method, structured according to the ISO 14,040 directives (ISO 14040 Citation2006a; ISO 14044, Citation2006b), while, as a way to improve the environmental performance of a product solution, this study has used the Eco-design approach.
The paper has been organised as follows: after this introduction, Section 2 describes the scientific literature that has been reviewed. The first part (Section 2.1) deals with the Life Cycle Assessment method, and in particular with its use in scientific packaging studies. The second part (Section 2.2) with the Eco-design approach as a way to improve the environmental performance of a product. Section 3 explains the research approach and the general methodology itself; Section 4 shows the case study and the LCA analysis; Section 5 reports the outcomes of the case study; Section 6 reports the Discussion and conclusions of the study.
2 Literature review
The following section provides the background for the topic of this study. The first part is a review of the LCA literature in the packaging sector. It shows how it has evolved in time in different industrial fields (from the food and beverage to the pharmaceutical), with an attention to studies about recycling and reuse of product packaging. It ends with a focus on studies concerning the environmental impacts of delivery packages. The second part is a review of the DfE approach in product design stage, of its connection with LCA method and other traditional design tools, and of its measurable benefits for the companies (both economic and environmental).
2.1 Life cycle assessment for packaging solutions
Several studies in literature investigated the environmental impacts of the product packaging, through the use of LCA. The majority of these studies focused their attention on the packaging in food and beverage products, due to the necessity of the packaging to maintain food/beverage quality, safety assurance and preventing food/beverage waste through extending the product shelf life. Zabaniotou and Kassidi (Citation2003) applied the LCA for the comparison of two egg packages: one made of polystyrene and the other made of recycled paper. The results did not provide a clear-cut answer for defining the eco-friendlier product, but the goal was a preliminary approach to perform a comparative analysis. Bertoluci, Leroy, and Olsson (Citation2014) conducted two series of five Life Cycle Assessments (corresponding to the national situation of five European countries: France, Germany, Italy, Spain, Sweden) on three olive packaging solutions: doypacks, glass jars, and steel cans. The results highlighted the influence of national household waste collection rates and selected technologies for waste treatment (recycling and incineration) on the environmental performance of packaging design. The authors concluded that eco-design of packaging cannot be considered only in terms of the materials employed: the contribution of the consumers’ behaviour is also a determinant criterion in the design of food packaging. Battini et al. (Citation2016) performed a critical analysis of two fresh food packaging solutions, i.e. corrugated fibreboard boxes and re-usable plastic containers, from both an economic and an environmental perspective (using LCA). They proposed also two new packaging solutions and compared them with the existing solutions in different supply chain scenarios. Their results showed the packaging solutions being more or less convenient according to the specific supply chain scenario. Wikström, Williams, and Venkatesh (Citation2016) have analysed how user behaviour influences the environmental comparison of two different packages for minced meat: a lightweight tube and a tray. The direct and indirect environmental effects were evaluated and the results show that the tube is the superior environmental alternative when only the direct effects are considered. When indirect effects and user behaviour are included in the comparison, the tray is the better alternative due to higher recycling rates and, most importantly, less food waste during the process of emptying. Ingrao, Gigli, and Siracusa (Citation2017) performed an Attributional-LCA to identify environmental hotspots in the life-cycle of expanded Polylactic Acid (PLA) trays for fresh-food packaging. Their study highlighted that the highest environmental impacts come from the production and transport of the PLA granules. Gutierrez, Meleddu, and Piga (Citation2017) tried to identify improvements in food packaging solutions to minimise environmental externalities. The environmental impact of packaging and food losses and the balance between the two were examined concerning a cheesecake that is normally packaged in low-density polyethylene film and has a limited shelf life due to microbial growth. A shelf life extension was sought through the application of the well-established modified atmosphere packaging (MAP) technique. Results showed that the new packaging solution could considerably extend the shelf life of cheesecakes, reducing food waste and decreasing the overall environmental impact. Abejón et al. (Citation2020) assessed the environmental impacts of the distribution of fruit and vegetables using reusable plastic crates and single-use cardboard boxes. Their results showed that reusable plastic crates implied significant lower environmental impacts than the single-use cardboard boxes. Their work showed that plastic packaging should not be totally avoided or banned since, for certain applications, it can be the most environmentally friendly option.
Other studies focused their attention on recycling and reuse of the product packaging. Ross and Evans (Citation2003) examined whether a re-use and recycle strategy for a plastic-based packaging would also reduce the overall environmental burden. The LCA results demonstrated that recycle and reuse strategies for plastic-based products can yield significant environmental benefits. In 2013, Cleary (Citation2013) examined the impacts related to the wine and spirit packaging supply in the City of Toronto, Canada. He evaluated five alternative means of packaging, including the container, closures, capsules and labels: conventional single-use glass bottles; lightweight single-use glass bottles; refillable glass bottles (assuming 14 refills maximum); polyethylene terephthalate bottles; and aseptic cartons. The results of these LCA comparisons indicated that the net environmental burdens from each package life cycle broadly reflected the relative masses of the containers, except for the refillable glass bottles. Postacchini et al. (Citation2018) showed how the adoption of a packaging reuse policy, together with a logistical reorganisation of the supply chain, in a honey production case, can consistently reduce the environmental emissions of the whole supply chain. The results are dependent on the packaging reuse rate but they confirmed to be valid and consistent even in a worst-case scenario of a 10% reuse factor. The LCA results also proved that a logistical optimisation of a supply chain, by itself, does not lead to the best solution for the environment, in terms of polluting emissions.
The environmental impacts of packaging have also been studied for pharmaceutical products. Dhaliwal et al. (Citation2014) compared the environmental impacts of two packaging options for contrast media offered by GE Healthcare: +PLUSPAK™ polymer bottle and traditional glass bottle. This study indicated that the polymer bottle outperforms the glass bottle in all the considered environmental categories. The lower impacts of the polymer bottle for this packaging application can be attributed to lower material and manufacturing impacts, lower distribution impacts, and lower end-of-life disposal impacts. The results of this study suggested that using polymer rather than glass bottles provides a means by which to lower the environmental impact of contrast media packaging. Using LCA, Raju et al. (Citation2016) compared two packaging forms frequently used in the pharmaceutical industry. The study showed that the environmental performance of PVC blister packaging is better than that of aluminium blister packaging, as the PVC blister packaging performed better in nine out of the eleven considered impact categories. It has also been observed that the process of manufacturing of aluminium foils is a significant contributor to the overall environmental impact of aluminium blister packaging.
Some other studies investigated the environmental impacts of delivery packages. In 2004, Franklin Associates (Citation2004) prepared a report for the Oregon Department Of Environmental Quality (DEQ) and U.S. EPA Environmentally Preferable Purchasing Programme, in which 26 different packaging options were investigated to obtain a lifecycle inventory. The report inventoried inputs (energy, materials) and outputs (solid waste, atmospheric and waterborne emissions) but made no claims regarding the impacts of these inputs and outputs. Tan and Khoo (Citation2005) compared two different packaging materials such as Expanded polystyrene (EPS) and corrugated paperboard (CPB), in the context of a specific insert packaging solution. The LCA case study has been divided into two main parts. The first investigated the impact assessment of two different designs of both EPS and CPB. The second part presented various end-of-life scenarios. For the original designs, CPB displayed a higher total environmental load. In the redesigned comparison, the proposed EPS insert potentially generates about 70% lower environmental overall load, as compared to the original EPS insert. Yi et al. (Citation2017) used lifecycle assessment (LCA) approach to examine the environmental impacts and energy consumption of delivery packages used for express purposes, which mainly include corrugated boxes, plastic bags and tapes for binding and sealing purposes. The results showed that production and usage stage consume the most energy and create the most environmental impacts. One-layer box uses less materials and energy and thus can replace two-layer box to reduce environmental impacts. Finally, Su et al. (Citation2020) used the life cycle assessment method to conduct a quantitative analysis of the Green House Gases (GHGs) emissions of express delivery packaging materials in China. Their results indicated that the total CO2-eq from packaging materials’ overall life has increased from 0.3 metric tons (Mt) in 2007 to 13.2 ± 5% Mt in 2018. Their scenario-based analysis implied there are great opportunities to reduce packaging materials consumed and then mitigate their impact.
2.2 Design for environment and its measurable benefits
Design For Environment (DFE) or Eco-Design (De Grave and Olsen Citation2006), as defined in ISO 14,062 (ISO/TR 14,062, Citation2002), is a design approach aiming at reducing the environmental impacts of products and services throughout the whole life cycle, while assuring similar or improved services to the end customer (Vallet et al. Citation2013). Eco-design not only is considered to be an efficient environmental approach, but it is also said to carry several economic advantages for the firms adopting it. Plouffe et al. (Citation2011) investigated the economic outcome for companies marketing one or more eco-designed products. Their results showed that there are clear short-term benefits for the firm. Profitability over the long term, however, cannot be assessed, as fixed costs seem to be higher for eco-designed products compared to traditional products. In 2002, Holdway, Walker, and Hilton (Citation2002) suggested Eco-design as a way to overcome barriers to sustainable packaging and they outlined perspectives and processes that could help development teams to maximise results in this increasingly important aspect of design. Despite the progressive use of eco-design in the industrial world, taking into account environmental constraints remains problematical for small and medium-sized enterprises (SMEs). Le Pochat, Bertoluci, and Froelich (Citation2007) dealt with the issue of eco-design integration in a company’s organisation. They put forward a method to carry out the integration of eco-design in small and medium-sized enterprises, guiding change management in a company by establishing connections between the company’s ordinary preoccupations (strategy, design) and the environmental aspects. Bevilacqua, Ciarapica, and Giacchetta (Citation2007) discussed a methodology for integrating Design for Environment (DfE) and life cycle assessment (LCA) techniques both into new product development and into the process of redesigning a set of existing products. Later, Grande et al. (Citation2017) demonstrated that through the use of LCA is possible to improve a methodology for eco-design of materials (in particular metal-organic framework materials). In their study of 2015, Andriankaja et al. (Citation2015) proposed a holistic approach to ecodesign geared to operate within a Product Life cycle Management (PLM) system. A PLM system is a set of tools used to create and manage the product information through its whole life cycle. Within the mechanical design area, a PLM system is composed of the traditional design tools such as Computer-aided design (CAD), Computer-aided manufacturing (CAM), Computer-aided engineering (CAE), etc., and allows bidirectional informational flows between the embedded tools. The study aimed to foster sustainable design solutions for high-end structural parts used in the transport sector, especially in the automotive and aeronautic industries. In their work of 2016, Lacasa et al. (Citation2016) implemented a sustainable product development methodology to obtain an improved design of two different products: a solar tracker and an isothermal container. First, the main inputs and outputs associated with the production process of each product were obtained. Next, the quantification of the economic, environmental and social aspects was carried out by the use of suitable engineering metrics and indicators. Finally, sustainability strategies focused on the selection of low impact materials and the reduction of materials were applied in the product redesign process. In both cases, a lower environmental impact and higher company benefit have been achieved. Chun et al. (Citation2018) proposed a consumer-oriented eco-design index (CEDI) and a producer-oriented ecodesign index (PEDI) as a method to identify the target components of a product for ecodesign, using the water purifier case study. Their study tried to overcome the challenges on the tool related barriers that limit ecodesign implementation, such as allowance of multi-objective analysis, inclusion of life cycle perspective, and linkage with economic aspects. Cicconi (Citation2019) proposed an Eco-design tool able to promote a collaborative approach among all the different stakeholders (such as designers, manufacturers and suppliers) to support the product design stage in the creative industry. A collaborative platform tool has been described and the design workflow is based on the development of a Material Selection Tool, which reduces the gap between research, development, and innovation using a design-driven approach. Civancik-Uslu et al. (Citation2019) showed how to apply LCA and eco-design as a shortcut to environmentally improve a particular packaging in the context of the cosmetic industry (a cosmetic tube). To improve the environmental profile of this packaging, virgin petrochemicals have been partially replaced by mineral fillers or/and recycled plastics. They showed that a cosmetic tube with less environmental emissions can be obtained, while maintaining its technical feasibility and reducing the economic costs. Finally, Kamalakkannan and Kulatunga (Citation2021) proposed a parametric life cycle assessment (PLCA) approach to eco-design optimisation and decision-making at the early stage of design. Their suggested model reflected the characteristics of the environmental performance as an objective function at the early design stage. This could allow designers to optimise the design and to mitigate environmental impacts, without performing scenario analysis.
This study aims at showing a new design method to improve the overall assembly features and environmental sustainability of a packaging solution. It helps to fill the following research gap: to give the product designers a concrete method to spot and focus their attention on the most important packaging parts and, at the same time, give them a clear idea of which are the most important functional requirements to be satisfied. This study has been focused on domestic household packaging, but the provided method can be extended to any particular packaging solution and its findings be still valid.
3 Research approach
The research approach has been described with hypothesis, materials and methods. The Hypothesis section describes the limits of the analysed design approach for packaging. The Materials and Methods section deals with the methodological approach, describing in detail the phases for supporting the packaging design.
3.1 Hypothesis
The main hypothesis related to this study are:
The study has been focused on the packaging design for small-medium-sized household appliances. However, the approach can be extended to any particular packaging solution. As a case study, the redesign of packaging for cooker hoods has been proposed;
The interviewed experts and stakeholders, who have helped to formulate the proposed approach, are related to the industrial field of the household appliances;
The dimensions of the external box and the interior parts have been studied together. These dimensions are related to the product size to be analysed.
3.2 Materials and methods
This section describes the methodological approach that has been used to support the design activity of a packaging solution. describes the traditional lifecycle process for packaging from the design to the product delivery. The design phase of packaging consists of two levels: the design of the external box and the design of the interior. The complexity is related to the selection of the materials and their configurations in terms of thickness, shape, and layers. In this design workflow, the designers evaluate the level of the product protection that has to be performed by the packaging itself but, assembly properties and eco-sustainability of it are very rarely considered in this stage.
describes the approach proposed in this paper to support the design of a packaging solution. The approach is based on the definition of the basic functions (Fs) and the functional requirements (FRs) that a packaging must perform (see paragraph 3.2).
Functions and functional requirements of a specific product packaging should be discussed and formalised, when possible, by the product experts and the stakeholders or, in alternative and when available, derived by specific scientific literature. All the Fs and FRs considered in this paper have been established by a panel of experts and stakeholders and they referred to the case of a generic household appliance packaging. Indeed, while the list of functions could be considered valid for a large variety of product packaging (if not all), to fulfil a correct and detailed FRs list, it is essential to define and know what kind of product the packaging is for. On this basis, in this study, each component of the panel of experts has been selected among packaging designers, product managers and logistic managers that work in the household appliance field, according to the criteria of competence and area of expertise (Clayton Citation1997; Okoli and Pawlowski Citation2004; Mazzuto et al. Citation2018).
Once Fs and FRs are identified, each functional requirement is linked to the functions it performs, resulting in a Functions/Functional Requirements (F/FR) matrix. This matrix is the tool to identify and describe the relationships between the functional requirements and their performed functions. Functional requirements are then specifically evaluated in terms of three design specifications: Customer Perception, Strategic Value, and Lean Production. This evaluation involves external and internal actors in the packaging process, including a representation of end-users. Using the Analytic Hierarchy Process (AHP) approach, a single normalised Design Score (DS) is obtained for each FR, out of the single three design specification score (see paragraph 3.2.1). Then, a Pair Comparison Analysis is performed on the FRs to highlight the number of relationships among the FRs and rank them accordingly to the obtained Pair Comparison Score (PCS – see paragraph 3.2.1). For each FR, by multiplying the obtained DS and PCS, a final Combined score (CS) is produced (see section 3.2.2). The CS indicates the importance of the associated FR: the higher the CS, the more important is the associated FR.
In parallel with this FRs development process, the list of the parts of the packaging solution (the physical components of it) are analysed and singularly connected to the functions they have to perform. The result is a second ranked matrix (P/F matrix) that highlights the number of relationships between parts and functions (see section 3.2.3). The parts with the highest number of performed functions are the ones that need to be carefully redesigned first. On the other hand, parts with the fewest number of relationships are considered less important.
Having in mind which are the most important FRs that have to be fulfiled (the ones with the highest CS), the designers can focus their attention on the parts that have the highest impact on the packaging. Designers can now decide whether to change, add or delete a part, or change the part material, or searching for a different assembly configuration.
Finally, the redesign draft is validated using two analysis related to assembly properties and environmental sustainability. The assembly properties analysis estimates the average time of assembly in the production line while the environmental sustainability is analysed by means of the LCA tool. The results of these two analyses are important because they give feedback on the results achieved in the packaging design. Therefore, during the proposed design workflow, the packaging designers and the product managers can compare different solutions for achieving a final decision process. The final decision is based on the evaluation of the environmental and lean production gains.
3.2.1 Functions and functional requirements
The most important and most obvious function of the packaging is to protect the product during transportation. However, the packaging should have characteristics that add convenience in distribution, handling, stacking, display, sale, opening, reclosing, using, dispensing, reusing, recycling, ease of disposal, etc. As stated in the previous section, the methodological approach for defining Fs and FRs, in this study, has been referred to a generic household appliance packaging. This does not invalidate or affect the generality of the method itself, but it is necessary for a correct Fs and FRs development. As a result, seven basic functions have been defined. These basic functions are the following:
To Protect: one of the main functions of a packaging system is to protect its content, avoiding any damages during the delivery phase (breakage, leakage, etc.). Therefore, ‘to protect’ means that the package has to provide structural resistance to compression, accidental drop, and vibration;
To Contain: a packaging has to contain products and its accessories inside the same box avoiding limit conditions such as a too tight package or a loose and over-sized one;
To Preserve: the contents of a package have to avoid any spoilage related to environmental influences such as humidity, temperature, light, air, liquid, etc. This type of protection depends on the type of goods to be transported (i.e. foods, appliances, textiles, metal, etc.);
To Transport: the packaging has to provide a structure compliant with the transportation (lorry, containers, etc.);
To Communicate: each package has its labels to inform about its content (which can be a commodity or food), logistics data, tracking, transport details, use, brand, etc. Labels are also marketing tools and they can include barcodes and q-codes for a rapid access to information and codes;
To Assembly: this function concerns the manufacturing line where the parts of the packaging are assembled together with the product. The packaging process in a manufacturing line requires specific needs in order to reduce time and cost in production;
To Be Sustainable: current packaging has to provide functionalities such as recycling or reuse, and in general minimisation of the resources involved to reduce the overall environmental impacts;
After the definition of the list of functions, the same panel of experts and stakeholders has outlined a list of 20 functional requirements the packaging solution has to perform. reports each functional requirement (FR) with its description. Regarding all the functional requirements focused on avoiding damages, the entity of the loading conditions is defined with the customer, considering normative. As an example, the resistance force to vertical compression is a specification defined with the customer before the conceptual design. In general, the resistance check to any loading condition (such as compression force, vibration, etc.) needs of tests on physical prototypes.
Table 1. Functional Requirements list and description
As a second step, a Function/Functional Requirement (F/FR) table is defined to describe the relationships between each FR and functions (see the case study in section 4.1.1, ).
Table 2. FR/F matrix for the packaging of household appliances
3.2.2 Ranking the functional requirements
Once the relationships between each FR and the functions have been discovered, the FRs are assessed using three different design specifications: Customer Perception, Strategic Value, and Lean Production. These design specifications have been chosen to cover the needs of the different supply chain actors and stakeholders. The ‘Customer Perception’ is obtained through a customer survey and then used to assess the perception and the importance given by the customers to a certain FR. The ‘Strategic Value’ represents the benefit (or the added value) that the improvement of a specific FR could create for the supply chain. As an example, the employment of environmentally friendly materials is a feature that could create strategic value to the whole supply chain. The ‘Lean Production’ is more specific for the company and it describes how an FR is compliant with the general Lean Production thinking. Therefore, while the company experts and stakeholders have to be employed for the characterisation of the Strategic Value and Lean Production score, a panel of end-users (customers) must be employed for the analysis of the Customer Perception value. A scale from 1 to 5 has been proposed to score the single FRs for each design specification. The three different design specification scores are multiplied in order to obtain a single score for each FR. Then, a final normalised Design Score (DS), expressed in percentage, is obtained by dividing the related single score for the sum of all the scores (Total score). An Analytic Hierarchy Process (AHP) is then applied to rank the list of FRs according to their normalised Design Score. AHP is a multicriteria decision-making approach in which factors are arranged in a hierarchic structure (Saaty Citation1990). The results of this process are shown in practice in the case study section 4.1.1 (see ). As a next step, a Paired Comparison Analysis must be performed to describe the relationships between each FR, to determine if any of them has a connection with others. In paired comparisons, the alternatives depend on each other and a new alternative can affect the relative ranks of existing alternatives (Saaty Citation2016). This analysis is important to qualitatively evaluate how a change in a specific FR could affect other FRs and their number. in section 4.1.1 shows the results of this analysis in the considered case study.
Table 3. Results of the AHP with normalised Design Score for each FR
Table 4. Paired Comparison matrix of the functional requirements
3.2.3 Combining the scores
Having obtained both the normalised DS and the Paired Comparison Score (PCS – see ), for each single FR, the next step is to create a single index score that combines them together. The result is shown in of section 4.1.1. The Combined Score (CS) gives a more comprehensive understanding of the importance of each FR, because it takes into consideration both the three design specifications and the relationship among the FRs. gives the final indication on which are the most important FRs that have to be kept or improved (highest Combined Score) and which are the less important. Indeed, any design modification on these latter ones does not affect in a significant way the final packaging.
Table 5. Results of the number of total relationships per each FR analysed in Pair Comparison analysis and correlated Pair Comparison Score (PCS)
Table 6. Combined Score (CS) table
3.2.4 Parts/Functions analysis
When the design activity starts, the packaging designers collect the list of parts (components) of the packaging solution. Data and information such as geometry, material property, weight, sizing, and assembly time, are considered per each part which constitutes the packaging structure. The designers then define the relationships between each specific part and the functions it has to perform. The result is a second ranked matrix (P/F matrix) that highlights the number of relationships between parts and functions. The parts with the highest number of relationships are considered the most important parts for that packaging solution, because they perform multiple functions. These parts are the ones that need to be carefully redesigned first. On the other hand, parts with fewer numbers of relationships are considered less important. in section 4.1.1 shows this matrix for the analysed case study.
Table 7. Part/Functions matrix
4 Case study
The proposed approach has been applied and tested in the design of a packaging for a common vertical kitchen hood with a glass surface. The data have been provided by a kitchen-hoods large size manufacturing company located in Italy and the panel of experts and stakeholders has been selected within the company management and the company stakeholders.
4.1 The actual packaging
The test case is focused on the redesign of an already existing packaging described in . It consists of several items for cushioning and protect the contained commodity. In particular, 4 compressed cardboard corners are employed to improve the angular cushioning and resistance, 1 EPS base is used as a cushioning system for avoiding ruptures from drops, 1 corrugated fibreboard chimney protection is used to avoid contact between the steel chimney and the vertical glass of the product, and four internal air bags are included for improving the protection of the product. Finally, the commodity is packaged using a corrugated fibreboard box. The parts list of the actual packaging has been analysed in terms of materials, weight, and functions. In order to define a relationship between parts and FR, each part has been associated to one or more functions.
Figure 3. Internal packaging scheme of the analysed kitchen-hood: 1) external box; 2) EPS base; 3) chimney protection; 4) Internal air bags (four items per packaging); 5) Corner (four items per packaging); 6) kitchen-hood; 7) Chimney
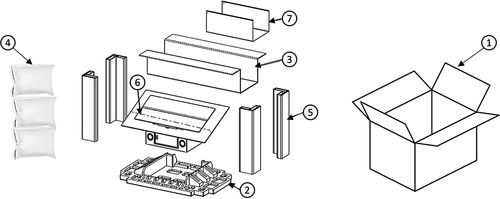
4.1.1 Functional analysis and functional requirements
shows the F/FR matrix for a kitchen-hood packaging, while shows the results of the AHP on the normalised Design Score (see section 3.2). A scale from 1 to 5 has been proposed to score the single FR for each design specification where: 1 = not at all important; 2 = slightly important; 3 = important; 4 = fairly important; 5 = very important.
Analysing , it is evident that the three most important Functional Requirements are FR 15, FR 3 and FR 20. This means that a moderate or low weight together with an adequate resistance to vertical compression and the use of environmentally friendly material are the most important requirements to satisfy when designing the new packaging solution.
shows the results of the Pair Comparison Analysis. As stated in section 3.2, this analysis is essential to assess how a change in a specific FR could affect other FRs. The number of total relationships per each FR is summarised in with the relative percentage Pair Comparison Score (PCS). This score is calculated as the number of relationships of a FR divided by the total number of relationships and then expressed in percentage.
Having calculated the normalised Design Score and the Pair Comparison Score of all the FRs, it has been possible to calculate the Combined Score (CS). reports the Combined Scores. These scores give the final indication on which are the most important FRs that have to be kept or improved.
Finally, reports the relationships between each packaging part and the highlighted functions, concerning the components of the actual packaging solution. For example, the external box performs a total of 6 functions: to protect, to contain, to transport, to assemble and to be sustainable.
From the analysis of , it is clear that some items are less important than others in terms of total relationships.
4.2 The redesigned packaging
According to the results of the previous section, the design of the new packaging solution has been focused on the first four components ranked in , i.e.: the external box, the EPS base, the chimney protection, and the internal air bags. In particular:
External box: the structure of the board box has been optimised to reduce the weight maintaining a similar level of Edge Compression Test (ECT value) per each carton board sheet. A wave-sheet has been removed from the composition of the corrugated fibreboard, passing from a double wall board to a single wall board. However, an increased use of kraft material has been considered per each layer of the corrugated fibreboard (outer and inner liner);
EPS base: a new base design has been developed to increase the cushioning aspects (see ). Not only that, it has been chosen to use a more dense EPS material (30 kg/m3 instead of the previous 27 kg/m3). Therefore, the new EPS base is more robust. Moreover and very importantly, with this new design the EPC base avoids the employment of other packaging parts such as the lateral corners and the internal air bags;
Chimney protection: being composed by a single wave corrugated fibreboard (E flute), this part was already optimised for assembly and it has not been redesigned;
Internal air bags: these parts have been removed due to the improved design of the new EPS base, which could provide an increased level of cushioning;
No design changes have been performed in parts such as plastic cover, external tape, internal tape, clips, and labels. Indeed, all these parts have already a very reduced mass weight in the packaging assembly and they also have a lower number of P/F relationships. describes the redesigned EPS base. The new design has aimed at reducing the number of internal packaging parts by increasing the thickness, the shape and the density of the EPS base. In this way, it has been possible to remove four corners and four internal air bags.
Analysing the improvements related to the redesigned EPS base, shows the difference between the first EPS base and the redesigned model. The height and length of the lateral protections have been increased as well as the lateral reinforcements. These lateral reinforcements have extended the contact with the corrugated fibreboard box. This feature has increased the commodity stability, avoiding the use of the lateral corners, though it has incremented the weight of the EPS base from 396 g to 531 g (approximately a 34% weight increase).
4.3 Life cycle assessment
Life Cycle Assessment has been used to quantify the environmental impacts of the packaging solutions. The LCA has been structured according to the ISO 14,040 directives (ISO 14040 Citation2006a,b). As functional unit, the packaging of a single kitchen hood has been chosen. The method ReCiPe 2016 in its ‘Midpoint Hierarchist’ version has been used to assess the impacts. In order to cover a range of significant environmental impacts, 12 ReCiPe characterisation categories have been chosen to consider: ‘Global warming’, ‘Stratospheric ozone depletion’, ‘Terrestrial acidification’, ‘Freshwater eutrophication’, ‘Marine eutrophication’, ‘Terrestrial ecotoxicity’, ‘Freshwater ecotoxicity’, ‘Marine ecotoxicity’, ‘Human carcinogenic toxicity’, ‘Land use’, ‘Fossil resource scarcity’ and ‘Water consumption’.
4.3.2 Description of the system and system boundaries
This study does not include the LCA of the kitchen hood manufacturing nor all the material transportations between the different production stages. shows the materials and processes that have been taken into the analysis.
4.3.3 Life Cycle Inventory of the actual and redesigned packaging
All the LCI inputs used in this study have been taken from the Ecoinvent database (version 3.5), except the ‘Electricity’ input. This has been borrowed from the European Life Cycle Database (ELCD). The following sections explain how each stage/process has been modelled. show the packaging items and their number in the ‘Actual Packaging’ configuration and the ‘Redesigned Packaging’ configuration.
Table 8. List of packaging items for the actual and the redesigned packaging solution
show a summary of the LCI inputs for each process/stage, with the relative consumption, for, respectively, the actual and the redesigned packaging configuration.
Table 9. LCI inputs for the actual packaging solution
Table 10. LCI inputs for the redesigned packaging solution
5 Results
shows the Life Cycle Assessment results. The ‘Redesigned Packaging’ has shown to be able to cut all the considered environmental emissions, approximately of 30% on average. It is a consistent cut when it comes to ‘Land use’ and ‘Terrestrial ecotoxicity’ (respectively, 68% and 37%), while the cut is fairly low on ‘Marine eutrophication’ and ‘Fossil resource scarcity’ (15% and 11%).
Table 11. Life Cycle Impact Assessment results
In order to give a better representation of the environmental savings of this Redesigned packaging, and show the normalised LCA results, considering an annual production of 60,000 pieces (which was the real market demand in 2019 for the considered kitchen-hood model). These results have a unit expressing an impact per person and year, also referred to as person equivalent.
Figure 7. Normalised LCA results, expressed in person equivalent, for an annual production of 60.000 pieces

Table 12. Normalised LCA results, expressed in person equivalent, for an annual production of 60.000 pieces
These results show the environmental categories that are the most affected by the packaging production, in particular: ‘Marine ecotoxicity’, ‘Freshwater ecotoxicity’, ‘Human carcinogenic toxicity’ and ‘Terrestrial ecotoxicity’. On the other hand, the environmental impact contributions of both the packaging solutions, for categories such as ‘Stratospheric ozone depletion’ and ‘Marine eutrophication’ have resulted to be negligible. The normalised results give a better understanding of the savings in terms of environmental emission that the Redesigned packaging could allow to reach. For example, with the Redesigned packaging, in a year, the emission of 4810 person equivalent could be saved in the ‘Marine ecotoxicity’ category, 2779 person equivalent in the ‘Freshwater ecotoxicity’ category, 1727 person equivalent in the ‘Human carcinogenic toxicity’ category, up to 2 person equivalent in the ‘Stratospheric ozone depletion’ category. From a ‘lean production’ point of view, the Redesigned packaging brought to save a 10% in assembly time, when compared to the Actual packaging. This is due to the minor number of items it is composed and therefore its minor assembly complexity.
6 Discussion and conclusion
Starting from identifying the functions, the functional requirements and the components of a packaging solution, this study has shown a feasible and helpful approach to improve the design of a packaging solution, in terms of assembly and sustainability. The proposed design approach aims at discovering which are the most important functional requirements to be satisfied for a packaging solution and, at the same time, which are the most important parts composing it. The first aim has been reached by ranking the FRs according to three different design specifications (Customer Perception, Strategic Value and Lean Production). Simultaneously, the FRs have been also ranked according to a Paired Comparison analysis, which highlights the relationships among the FRs. A final combined score for the FRs has been obtained by joining together the two previous single rank scores. The second aim has been reached by analysing the single parts and the functions they perform. This allows to rank the parts according to the number of performed functions and therefore to understand the single part importance. The importance is given by the fact that any change on them would affect greatly the whole packaging solution.
Once the two ranks have been obtained, the designers are able to focus their attention on the most important parts according to the most important FRs that have to be satisfied. This method considers a final evaluation stage, in which the new redesign solution is compared with the actual one, from a sustainability and assembly point of view. The results of these two comparisons have to be assessed by both the designers and the product managers, in order to approve the new design or discard it and start over the procedure.
The proposed design approach has been tested on the case of a kitchen hood packaging solution. In particular, Life Cycle Assessment method has been used to assess the impact of both the actual and the redesigned packaging solution, over 12 different environmental categories. By following this design approach, the Redesigned packaging has shown an environmental impact reduction in all the environmental categories (approximately 30% on average). At the same time, the Redesigned packaging has allowed to save time in the assembly line for approximately 10%.
It is important to underline that the general idea of this new design approach can be easily applied to any kind of packaging solution, not only household appliances. In order to do that, specific set of functional requirements have to be evaluated for each specific packaging application (households rather than food, rather than electronics, etc.), but the general procedure explained by this paper can be extended to any kind of packaging needs and requirements.
The proposed approach responds to the necessity to investigate specific properties in the packaging design such as assembly and eco-sustainability. Other properties can be investigated and added in the final evaluation stage of the designed packaging, according to the company goals. This method is indeed flexible and open to customisation. The two properties to be assessed in the final stage (assembly and eco-sustainability) have been chosen because, nowadays, they are important for all kind of packaging. Indeed, an easy assembly configuration can reduce time and money related to the product packaging with important benefits in terms of line efficiency. The easier the packaging assembly, the more compliant with the Just-In-Time (JIT) paradigm the solution. In general, the parts and materials used to assemble a packaging are bought in large quantity and stored in the warehouse as a current asset. Therefore, the reduction in terms of weight, volume, and quantity of parts allow to achieve important targets in terms of cost and time. On the other hand, sustainability also means to achieve a low-cost configuration within a reduction of resources. This study in particular, has shown how the cardboard reduction, replaced by a proper EPS design, has been able to ensure the same level of product protection, with a considerable reduction of the environmental impacts.
Disclosure statement
No potential conflict of interest was reported by the author(s).
Additional information
Notes on contributors
Leonardo Postacchini
Leonardo Postacchini Ph.D. in Sustainable Energy and Technology, he obtained his bachelor degree in Logistic and Production Engineering (summa cum laude), and then his master degree in Management Engineering (summa cum laude) both at Università Politecnica delle Marche (Ancona, Italy). He worked as project manager for photovoltaic plants and as process engineer for a wastewater treatment plant. In 2016 he started collaborating with the Università Politecnica delle Marche as a postdoctoral researcher, developing life cycle sustainability researches (Life Cycle Costing, Environmental Life Cycle Assessment and Social Life Cycle Assessment) on industrial and manufacturing processes and wastewater treatment technologies.
Paolo Cicconi
Paolo Cicconi obtained his bachelor’s degree in Mechanical Engineering from Università Politecnica delle Marche in November 2005 and a master's degree in Thermomechanical Engineering in December 2007. After graduating, he continued his studies in Engineering Design at Università Politecnica delle Marche, where in January 2011 he obtained a Ph.D. in Mechanical Engineering. From 2010 to 2018 he was a research fellow at the same University. He has been involved in several research activities in collaboration with various companies and research institutes in topics about engineering design and sustainability for the industry. His research interests are focused on design tools and methods. Since 2018 he is a contract professor of “Computer Graphics and BIM„ and “Design Tools for UAV„ at the Università degli Studi eCampus. Since 2019 he is a contract professor of “Mechanical Drawing” at Università degli Studi Roma Tre.
Filippo E. Ciarapica
Filippo E. Ciarapica Full professor in Industrial Plants at the School of Engineering of the Polytechnic University of Marche, graduated with distinction in 1999 in mechanical engineering at the University of Ancona. In 2003 he has got Ph. D. in Energy Management at the University of Ancona. From 2002 he has been giving courses of “Industrial Logistic” and “Industrial Facility Management” at the University Politecnica delle Marche, Ancona, Italy. He is author of more than 140 papers published on national and international proceedings and journals. His research topics mainly focus on industrial plants design, strategies for the integration of management standard (ISO 9000-Vision 2000, ISO 14000 and OHSAS 18001) and production systems, soft computing techniques in reliability analysis and maintenance activities planning, Life Cycle Assessment (LCA) in the development of a sustainable supply chain, and Logistics.
Michele Germani
Michele Germani is Full Professor of Tools and Methods for Industrial Engineering at the Polytechnic University of Marche and Director of the Department of Industrial Engineering and Mathematical Sciences. He is Rector Delegate for Third Mission - Technology Transfer. He is Past President of Hyperlean srl, a spin-off of the Polytechnic University of Marche. His main research topics are Design for X methods, tools and methods for Life Cycle Thinking, advanced virtual prototyping tools, and user-centered design for product and process. He is responsible for several European and National research projects.
Maurizio Bevilacqua
Maurizio Bevilacqua Full professor in Industrial System Engineering at the Università Politecnica delle Marche, Ancona, Italy (formerly Università di Ancona) graduated with distinction in 1986 in mechanical engineering at the University of Ancona. His research activity mainly deals with Life Cycle Assessment Project Management, Maintenance Management, Supply Chain Management, Environmental Analysis of Process Plants. He is author of several papers that have been published in several national and international journals (Project Management Journal, International Journal of Project Management, Journal of Cleaner Production, Journal of Sustainable Engineering, International Journal of Production Research Journal of Food Engineering, Production Planning & Control, Reliability Engineering and System Safety, Quality and Reliability Engineering International, International Journal of Quality and Reliability Management, Journal of Loss Prevention in the Process Industries, International Journal of Production Economics, Business Process Management, International Journal of Logistics, International Journal of Operations and Production Management, The Journal of Enterprise Information Management,) and also in conference proceedings.
References
- Abdallah, S. B., M. Aidi, A. Zouari, and A. Maalej. 2015. “Systems Engineering Used for Logistics Integration in Product Design.” Journal of Traffic and Logistics Engineering 3 (2): 185–188. doi:https://doi.org/10.12720/jtle.3.2.185-188.
- Abejón, R., A. Bala, I. Vázquez-Rowe, R. Aldaco, and P. Fullana-i-palmer. 2020. “When Plastic Packaging Should Be Preferred: Life Cycle Analysis of Packages for Fruit and Vegetable Distribution in the Spanish Peninsular Market.” Resources, Conservation and Recycling 155: 104666. doi:https://doi.org/10.1016/j.resconrec.2019.104666.
- Andriankaja, H., F. Vallet, J. Le Duigou, and B. Eynard. 2015. “A Method to Ecodesign Structural Parts in the Transport Sector Based on Product Life Cycle Management.” Journal of Cleaner Production 94: 165–176. doi:https://doi.org/10.1016/j.jclepro.2015.02.026.
- Annamalai, K., Naiju, C.D., Karthik, S., and M. Mohan-Prashanth. 2013. Early Cost Estimate of Product During Design Stage Using Design for Manufacturing and Assembly (DFMA) Principles. Advanced Materials Research 622–623: 540–544. doi:10.4028/www.scientific.net/amr.622–623
- Battini, D., M. Calzavara, A. Persona, and F. Sgarbossa. 2016. “Sustainable Packaging Development for Fresh Food Supply Chains.” Packaging Technology and Science 29 (1): 25–43. doi:https://doi.org/10.1002/pts.2185.
- Bertoluci, G., Y. Leroy, and A. Olsson. 2014. “Exploring the Environmental Impacts of Olive Packaging Solutions for the European Food Market.” Journal of Cleaner Production 64: 234–243. doi:https://doi.org/10.1016/j.jclepro.2013.09.029.
- Betancur-Muñoz, P., G. Osorio-Gómez, J. F. Martínez-Cadavid, and J. F. Duque-Lombana. 2014. “Integrating Design for Assembly Guidelines in Packaging Design with a Context-based Approach.” Procedia CIRP 21: 342–347. doi:https://doi.org/10.1016/j.procir.2014.03.173.
- Bevilacqua, M., F. E. Ciarapica, and G. Giacchetta. 2007. “Development of a Sustainable Product lifecycle in Manufacturing Firms: A Case Study.” International Journal of Production Research 45(18-19) (18–19): 4073–4098. doi:https://doi.org/10.1080/00207540701439941.
- Boothroyd, G. 1994. “Product Design for Manufacture and Assembly.” Computer-Aided Design 26 (7): 505–520. doi:https://doi.org/10.1016/0010-4485(94)90082-5.
- Chun, Y. Y., K. M. Lee, J. S. Lee, J. Y. Lee, M. H. Lee, N. Mishima, and K. Tahara. 2018. “Identifying Key Components of Products Based on Consumer-and Producer-oriented Ecodesign Indices considering Environmental Impacts, Costs, and Utility Value.” Journal of Cleaner Production 198: 1031–1043. doi:https://doi.org/10.1016/j.jclepro.2018.07.035.
- Cicconi, P. 2019. “Eco-design and Eco-materials: An Interactive and Collaborative Approach.” Sustainable Materials and Technologies e00135. doi:https://doi.org/10.1016/j.susmat.2019.e00135.
- Civancik-Uslu, D., R. Puig, S. Voigt, D. Walter, and P. Fullana-i-palmer. 2019. “Improving the Production Chain with LCA and Eco-design: Application to Cosmetic Packaging.” Resources, Conservation and Recycling 151: 104475. doi:https://doi.org/10.1016/j.resconrec.2019.104475.
- Clayton, M. J. 1997. “Delphi: A Technique to Harness Expert Opinion for Critical Decision‐making Tasks in Education.” Educational Psychology 17 (4): 373–386. doi:https://doi.org/10.1080/0144341970170401.
- Cleary, J. 2013. “Life Cycle Assessments of Wine and Spirit Packaging at the Product and the Municipal Scale: A Toronto, Canada Case Study.” Journal of Cleaner Production 44: 143–151. doi:https://doi.org/10.1016/j.jclepro.2013.01.009.
- Curling, S. F., N. Laflin, G. M. Davies, G. A. Ormondroyd, and R. M. Elias. 2017. “Feasibility of Using Straw in a Strong, Thin, Pulp Moulded Packaging Material.” Industrial Crops and Products 97: 395–400. doi:https://doi.org/10.1016/j.indcrop.2016.12.042.
- De Grave, A., and S. I. Olsen, 2006. Challenging the Sustainability of Micro Products Development. In 4M 2006-Second International Conference on Multi-Material Micro Manufacture, Grenoble, France, 285-288. https://doi.org/10.1016/b978-008045263-0/50064-7
- Dhaliwal, H., M. Browne, W. Flanagan, L. Laurin, and M. Hamilton. 2014. “A Life Cycle Assessment of Packaging Options for Contrast Media Delivery: Comparing Polymer Bottle Vs. Glass Bottle.” The International Journal of Life Cycle Assessment 19 (12): 1965–1973. doi:https://doi.org/10.1007/s11367-014-0795-1.
- Fadiji, T., C. J. Coetzee, T. M. Berry, and U. L. Opara. 2019. “Investigating the Role of Geometrical Configurations of Ventilated Fresh Produce Packaging to Improve the Mechanical strength–Experimental and Numerical Approaches.” Food Packaging and Shelf Life 20: 100312. doi:https://doi.org/10.1016/j.fpsl.2019.100312.
- Favi, C., M. Germani, and M. Mandolini. 2016. “Design for Manufacturing and Assembly Vs. Design to Cost: Toward a Multi-objective Approach for Decision-making Strategies during Conceptual Design of Complex Products.” Procedia CIRP 50: 275–280. doi:https://doi.org/10.1016/j.procir.2016.04.190.
- Favier, M., F. Celhay, and G. Pantin-Sohier. 2019. “Is Less More or a Bore? Package Design Simplicity and Brand Perception: An Application to Champagne.” Journal of Retailing and Consumer Services 46: 11–20. doi:https://doi.org/10.1016/j.jretconser.2018.09.013.
- Frank, B. 2014. “Corrugated Box Compression—a Literature Survey.” Packaging Technology and Science 27 (2): 105–128. doi:https://doi.org/10.1002/pts.2019.
- Franklin Associates, 2004. Life Cycle Inventory Of Packaging Options For Shipment Of Retail Mail-Order Soft Goods: Final Peer-Reviewed Report. Accessed on 23th March 2021: http://seeds4green.org/sites/default/files/LIFE%20CYCLE%20INVENTORY%20OF%20PACKAGING%20OPTIONS%20FOR%20SHIPMENT%20OF%20RETAIL%20MAIL-ORDER%20SOFT%20GOODS_1.pdf
- Gong, Y., E. Putnam, W. You, and C. Zhao. 2020. “Investigation into Circular Economy of Plastics: The Case of the UK Fast Moving Consumer Goods Industry.” Journal of Cleaner Production 244: 118941. doi:https://doi.org/10.1016/j.jclepro.2019.118941.
- Grande, C. A., R. Blom, A. Spjelkavik, V. Moreau, and J. Payet. 2017. “Life-cycle Assessment as a Tool for Eco-design of Metal-organic Frameworks (Mofs).” Sustainable Materials and Technologies 14: 11–18. doi:https://doi.org/10.1016/j.susmat.2017.10.002.
- Gutierrez, M. M., M. Meleddu, and A. Piga. 2017. “Food Losses, Shelf Life Extension and Environmental Impact of A Packaged Cheesecake: A Life Cycle Assessment.” Food Research International 91: 124–132. doi:https://doi.org/10.1016/j.foodres.2016.11.031.
- Holdway, R., D. Walker, and M. Hilton. 2002. “Eco‐design and Successful Packaging.” Design Management Journal (Former Series) 13 (4): 45–53. doi:https://doi.org/10.1111/j.1948-7169.2002.tb00330.x.
- Ingrao, C., M. Gigli, and V. Siracusa. 2017. “An Attributional Life Cycle Assessment Application Experience to Highlight Environmental Hotspots in the Production of Foamy Polylactic Acid Trays for Fresh-food Packaging Usage.” Journal of Cleaner Production 150: 93–103. doi:https://doi.org/10.1016/j.jclepro.2017.03.007.
- ISO 14040. 2006a. Environmental Management – Life Cycle Assessment – Principles and Framework. International Organization for Standardization.
- ISO 14044. 2006b. Environmental Management – Life Cycle Assessment – Requirements and Guidelines. International Organization for Standardization.
- ISO/TR 14062, 2002. Environmental Management–Integrating Environmental Aspects into Product Design and Development. https://www.iso.org/standard/33020.html
- Jahre, M., and C. J. Hatteland. 2004. “Packages and Physical Distribution.” International Journal of Physical Distribution & Logistics Management 34 (2): 123–139. doi:https://doi.org/10.1108/09600030410526923.
- Kamalakkannan, S., and A. K. Kulatunga. 2021. “Optimization of Eco-design Decisions Using a Parametric Life Cycle Assessment.” Sustainable Production and Consumption 27: 1297–1316. doi:https://doi.org/10.1016/j.spc.2021.03.006.
- Koblasa, F., E. Šírová, and R. Králíková. 2019. “The Use of Process Thinking in the Industrial Practice–Preliminary Survey.” Tehnicki Vjesnik 26 (3): 786–792. doi:https://doi.org/10.17559/tv-20150617135306.
- Lacasa, E., J. L. Santolaya, and A. Biedermann. 2016. “Obtaining Sustainable Production from the Product Design Analysis.” Journal of Cleaner Production 139: 706–716. doi:https://doi.org/10.1016/j.jclepro.2016.08.078.
- Le Pochat, S., G. Bertoluci, and D. Froelich. 2007. “Integrating Ecodesign by Conducting Changes in SMEs.” Journal of Cleaner Production 15 (7): 671–680. doi:https://doi.org/10.1016/j.jclepro.2006.01.004.
- Leatherdale, D. 2005. Cartons, Crates and Corrugated Board: Handbook of Paper and Wood Packaging Technology. Twede D, Selke S. DEStech Publications Inc., Lancaster, USA. ISBN: 1‐932078‐42‐8.
- Lee, S. G., and S. W. Lye. 2003. “Design for Manual Packaging.” International Journal of Physical Distribution & Logistics Management 33 (2): 163–189. doi:https://doi.org/10.1108/09600030310469162.
- Mazzuto, G., M. Bevilacqua, C. Stylios, and V. C. Georgopoulos, 2018. Aggregate Experts Knowledge in Fuzzy Cognitive Maps. In 2018 IEEE International Conference on Fuzzy Systems (FUZZ-IEEE), Rio de Janeiro, Brazil, 1–6. IEEE. https://doi.org/10.1109/fuzz-ieee.2018.8491656
- McDonald, C. M. 2016. “Integrating Packaging and Supply Chain Decisions: Selection of Economic Handling Unit Quantities.” International Journal of Production Economics 180: 208–221. doi:https://doi.org/10.1016/j.ijpe.2016.08.003.
- Meherishi, L., S. A. Narayana, and K. S. Ranjani. 2019. “Sustainable Packaging for Supply Chain Management in the Circular Economy: A Review.” Journal of Cleaner Production 237: 117582. doi:https://doi.org/10.1016/j.jclepro.2019.07.057.
- Molloy, O., E. A. Warman, and S. Tilley. 1998. Design for Manufacturing and Assembly: Concepts, Architectures and Implementation. US: Springer. doi:https://doi.org/10.1007/978-1-4615-5785-2_1.
- Netake, A., R. Mutha, A. Mishra, A. Sawant, P. Potdar, and N. Panaskar, 2019. Optimization of the Chest Geometry for the Storage and Transportation of Fruits and Vegetables. In Proceedings of International Conference on Intelligent Manufacturing and Automation, Tokyo, Japan, 253-263. https://doi.org/10.1007/978-981-13-2490-1_23
- OECD. 2011. “Invention and Transfer of Environmental Technologies.” In OECD Studies on Environmental Innovation. Paris: OECD Publishing. doi:https://doi.org/10.1787/9789264115620-en.
- Okoli, C., and S. D. Pawlowski. 2004. “The Delphi Method as a Research Tool: An Example, Design Considerations and Applications.” Information and Management 42 (1): 15–29. doi:https://doi.org/10.1016/j.im.2003.11.002.
- Pålsson, H., and D. Hellström. 2016. “Packaging Logistics in Supply Chain Practice–current State, Trade-offs and Improvement Potential.” International Journal of Logistics Research and Applications 19 (5): 351–368. doi:https://doi.org/10.1080/13675567.2015.1115472.
- Plouffe, S., P. Lanoie, C. Berneman, and M. F. Vernier. 2011. “Economic Benefits Tied to Ecodesign.” Journal of Cleaner Production 19 (6–7): 573–579. doi:https://doi.org/10.1016/j.jclepro.2010.12.003.
- Postacchini, L., G. Mazzuto, C. Paciarotti, and F. E. Ciarapica. 2018. “Reuse of Honey Jars for Healthier Bees: Developing a Sustainable Honey Jars Supply Chain through the Use of LCA.” Journal of Cleaner Production 177: 573–588. doi:https://doi.org/10.1016/j.jclepro.2017.12.240.
- Raju, G., P. Sarkar, E. Singla, H. Singh, and R. K. Sharma. 2016. “Comparison of Environmental Sustainability of Pharmaceutical Packaging.” Perspectives in Science 8: 683–685. doi:https://doi.org/10.1016/j.pisc.2016.06.058.
- Ross, S., and D. Evans. 2003. “The Environmental Effect of Reusing and Recycling a Plastic-based Packaging System.” Journal of Cleaner Production 11 (5): 561–571. doi:https://doi.org/10.1016/s0959-6526(02)00089-6.
- Saaty, T. L. 1990. “How to Make a Decision: The Analytic Hierarchy Process.” European Journal of Operational Research 48 (1): 9–26. doi:https://doi.org/10.1016/0377-2217(90)90057-I.
- Saaty, T. L. 2016. “The Analytic Hierarchy and Analytic Network Processes for the Measurement of Intangible Criteria and for Decision-making.” International Series in Operations Research & Management Science 363-419. doi:https://doi.org/10.1007/978-1-4939-3094-4_10.
- Shanmugam, K., H. Doosthosseini, S. Varanasi, G. Garnier, and W. Batchelor. 2019. “Nanocellulose Films as Air and Water Vapour Barriers: A Recyclable and Biodegradable Alternative to Polyolefin Packaging.” Sustainable Materials and Technologies 22: e00115. doi:https://doi.org/10.1016/j.susmat.2019.e00115.
- Su, Y., H. Duan, Z. Wang, G. Song, P. Kang, and D. Chen. 2020. “Characterizing the Environmental Impact of Packaging Materials for Express Delivery via Life Cycle Assessment.” Journal of Cleaner Production 274: 122961. doi:https://doi.org/10.1016/j.jclepro.2020.122961.
- Tan, R. B., and H. H. Khoo. 2005. “Life Cycle Assessment of EPS and CPB Inserts: Design Considerations and End of Life Scenarios.” Journal of Environmental Management 74 (3): 195–205. doi:https://doi.org/10.1016/j.jenvman.2004.09.003.
- Vallet, F., B. Eynard, D. Millet, S. G. Mahut, B. Tyl, and G. Bertoluci. 2013. “Using Eco-design Tools: An Overview of Experts’ Practices.” Design Studies 34 (3): 345–377. doi:https://doi.org/10.1016/j.destud.2012.10.001.
- Wikström, F., H. Williams, and G. Venkatesh. 2016. “The Influence of Packaging Attributes on Recycling and Food Waste Behavior – An Environmental Comparison of Two Packaging Alternatives.” Journal of Cleaner Production 137: 895–902. doi:https://doi.org/10.1016/j.jclepro.2016.07.097.
- Yi, Y., Z. Wang, R. Wennersten, and Q. Sun. 2017. “Life Cycle Assessment of Delivery Packages in China.” Energy Procedia 105: 3711–3719. doi:https://doi.org/10.1016/j.egypro.2017.03.860.
- Zabaniotou, A., and E. Kassidi. 2003. “Life Cycle Assessment Applied to Egg Packaging Made from Polystyrene and Recycled Paper.” Journal of Cleaner Production 11 (5): 549–559. doi:https://doi.org/10.1016/s0959-6526(02)00076-8.
- Zhang, G. Q., Y. F. Du, X. Z. Li, and X. X. Che. 2012. “Parametric Design and Multi-Objective Optimization of LCD Packaging Cushion Foams.” Applied Mechanics and Materials 200: 32–36. doi:10.4028/www.scientific.net/amm.200.32.