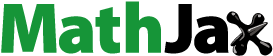
ABSTRACT
Nano particles contribute as a partial substitute in the production of eco-friendly building materials. This research presents a quantitative assessment of the sustainability effect of partially replacing cement in the green concrete mix with two types of nano-waste particles. The assessment is achieved using two weighing criteria developed by a Sustainable Decision Support System (SDSS) model. This assesses the alternatives using scoring systems based on both the Life Cycle Assessment (LCA) technique and Multi-Criteria decision analysis method. Ten sustainable aspects comprising four sustainability features: environmental, social, economic, and technological are incorporated within the model. The study investigates the partial substitution of cement by carbon nano tubes (CNT) and rice husk ash (RHA) in the concrete mix as compared to the control mix. The concrete mix with RHA showed the best sustainability results for all factors. This was attributed to the negligible RHA’s life cycle indexes as an agricultural residue of a natural material. Substituting 5% of the cement content in the mix by RHA partially contributed to minimising the carbon emissions and energy consumed during the cement manufacturing phase. CNT is expensive and its production consumes high amount of energy thus contributed negatively to the final evaluation result although its substitution proportion was minimal.
1. Introduction
1.1. Development of nanotechnology
Nanoscience is the science of studying, controlling, and re-engineering of particles at the atomic and molecular level. The size of the particles is the main reason for using this science as the material’s properties are highly altered under a Nano scale. Nanoparticles can be in the form of a powder, fibre, crystal, or pipe. It can be used as it is or can be deployed to reach the desired characteristics. (Bakhoum et al. Citation2017; Hernández-Moreno and de la Torre Citation2017; Sabihuddin Citation2014; Singh, Kalra, and Saxena Citation2017)
Moreover, the aim of nano particles is to manipulate the chemical alignment of the original material to achieve new tasks that cannot be attained in its macroscopic form. To ascertain this outcome, two approaches are industrialised: the top to bottom technique- also known as contemporary method- which is the reduction of large particles into nano-sized ones without enforcing any changes on their atomic level, and the bottom-up approach- also referred to as molecular nanotechnology – where the materials are created from atoms or molecules through a procedure of self-assembly. The last process is used to produce most of nanomaterials used in concrete such as: nano silica, nano alumina, and nano clay. It includes more indirect uses like synthesis and chemical preparation. The properties of the particles such as size and shape are easily designed and regulated using chemical processes. The choice between those two approaches depends on practicality, cost, and proficiency of nano conduct. (Hanus and Harris Citation2013; Norhasri, Hamidah, and Fadzil Citation2017)
1.2. Some nanotechnology applications in construction
Nanotechnology allows developing construction materials with enhanced or new properties. Most nanoparticles added to cement and concrete either accelerates the hardening process, seal the concrete surface, or improve the concrete properties. illustrates the increase in strength that some nanoparticles can cause when added to the concrete mix. Multi-Walled Carbon Nano Tubes (MWCNTs) highly affect the flexural strength, whereas Nano ferrous oxide significantly increases the compressive strength in the concrete mix. (Gammampila et al. Citation2010)
Figure 1. Effect of some nanoparticles on the strength of concrete (Gammampila et al. Citation2010)
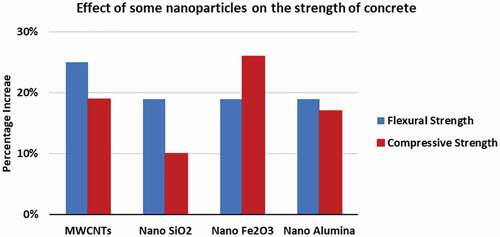
Nanotech Concrete helps in analysing, adjusting, and controlling the hydration in cement-based building materials to enhance the general performance in relative to the mass. As a result, better chemical, mechanical and physical properties are obtained with less materials and resources. In addition, higher durability can be achieved by modifying the calcium-silicate-hydrate (CSH) structure occurring during the cement hydration. The main cement hydration product (CSH) combines aggregates together and increase the strength and other macroscopic engineering properties of cement-based materials (CBMS). The size of the basic structural unit of (CSH) is in the nanometre scale. The nanomaterials act as a superb filler in the cement- based materials and improve the cement hydration process. Du et al. (Citation2019) presented several studies on the effect of adding nano silica to the concrete as a supplementary cementitious material (SCM) to form additional CSH. The small-sized gel of CSH generated due to the pozzolanic reaction of nano silica contributed to the densification of the microstructure and thus improved the concrete frost resistance.
Other physical and mechanical properties of CBMS such as: creep, permeability, porousness, and elasticity are enhanced. Mohamed (Citation2015) reported that the addition of nanomaterials to the CBMS produce nanocomposites with unique properties, for example, more carbon dioxide absorption. Cement composites reinforced with nanomaterials, such as carbon nano tubes (CNT), nano-SiO2 and nano-MgO, exhibit lower autogenous shrinkage compared to those without nanomaterials. These nanomaterials also delays and reduces the rebars onset active corrosion rates due to the reduced porosity of the matrix. (Du et al. Citation2019; Rong, Zhao, and Wang Citation2020)
In steel structures, the main weakness of steel is the fatigue that leads to structural failure caused by cyclic loading. Bridges and towers are two examples of these structures. Some manufactured steel is improved by adding copper nanoparticles. This resulted in reduction of surface unevenness which decreased the steel stress and fatigue cracking. (Bakhoum et al. Citation2017; Elvin Citation2007; Mohamed Citation2015; Sabihuddin Citation2014)
Nano particles are added to coatings of glass/windows, work surfaces, buildings, and structures. It provides various advantages, such as: protective, anti-corrosion, self-cleaning, thermal control, energy saving, anti-reflection, easy to clean, antibacterial, durable, and anti-graffiti. The coating used in self-cleaning windows uses TiO2 particles that react with ultraviolet rays (from the sun) to break down organic dirt in a ‘photocatalytic’ process. (Ganesh Citation2012)
Another type of commonly used nano particles in construction is Carbon nanotubes. According to Saifuddin, Raziah, and Junizah (Citation2013), Carbon nanotubes (CNT) are cylindrical allotropes that have a nanostructure. Its volume and size are smaller than other nanoparticles used in construction. Its diameter to length ratio is 1:132,000,000. There are two types of CNT: single-walled CNT (SWCNT) and multi-walled CNT (MWCNT). The inclusion of carbon nanotubes as fillers in the cement-based materials enhance some mechanical as well as physical properties of the material. The addition of carbon nanotubes by small amounts (1% by weight) improves the compressive strength and durability of cementitious composites. Furthermore, using carbon nanotubes as reinforcement in the cement improves flexure strength and toughness. This aids in reducing the cement content in concrete without compromising its mechanical properties. (Singh, Kalra, and Saxena Citation2017; Vidivelli and Ashwini Citation2018)
Regarding the dispersion of carbon nanoparticles in cement-based materials, (Du et al. Citation2019; Rocha and Ludvig Citation2018) recommended that the optimal dosage of CNT to be incorporated in the cement matrix was 0.05% by weight, beyond which aggregation of CNT may occur, resulting in a decrease in the mechanical properties of cement paste. In addition, Irshidat, Al-Nuaimi, and Rabie (Citation2021) investigated the influence of CNT on the thermal characteristics of post-heated cementitious composites aiming to predict the ability of concrete structures to survive after exposure to fire. The tested batches used 0.05% of CNT by weight of cement. The presence of CNT positively affected the hydration process in unheated and heated mortar up to 200 ◦C and significantly enhanced the compressive strength of heated mortar specimens for all studied temperatures.
1.3. Nanotechnology and sustainability
This context is intended to demonstrate the nano particle applications affecting cement-based building materials as being widely used in the construction industry thus having the greatest influence on the sustainable aspect of construction. During the manufacturing process of construction materials, nanotechnology is claimed to reduce the negative environmental impact and save energy.
The production of new nano binders that reduces the cement content and consequently the cost by almost 50 % is reported by Elvin (Citation2007); Hernández-Moreno and Solache de la Torre (Citation2017).
Several researches were undertaken to investigate the effect of Rice Husk Ash (RHA) on the compressive strength of the green concrete produced. Givi et al. (Citation2010) claimed that RHA exists in two sizes with average particle size of 5 micron (ultra-fine particles) and 95 microns. The research investigated the result of replacing cement by different proportions of both types of RHA with an aim to study the effect of finesse of particles on the concrete mix. The ultimate strength of concrete was gained at 10% of cement replacement by ultra-fine rice husk ash particles.
Similarly, Bansal and Antil (Citation2015) studied the compressive strength of M30 and M60 grade concrete at different ages after replacement of cement by rice husk ash (RHA). Both concrete mixes showed 3 to 10% increase in compressive strength at 10% rice husk ash replacement level. Gopi and Sruthi (Citation2017) concluded that the optimum strength of M20 grade concrete is obtained at the level of 5 % of ordinary Portland Cement replaced by RHA.
Ahmad Shah, Rao, and Gupta (Citation2019) presented a more advanced research on partially replacing cement in the M20 grade concrete with rice husk ash and wastepaper sludge collected from paper mills. The replacement of cement by RHA up to 4% showed comparatively equal compressive strength to that of the control mix. The benefit of replacing cement by RHA does not only enhance the mechanical and physical properties of concrete, but its advantage is extended to sustainability gain. Replacement of cement by RHA produces green concrete with a lower consumption of cement, thus reducing the CO2 emissions during the production of cement besides diminishing the environmental and disposal problems of the rice husk.
Another type of industrial waste produced from the manufacturing process of ornamental stones is marble and granite waste. Bakhoum et al. (Citation2017) conducted a study on the use of nano-granite waste particles as a replacement of cement and fine aggregate in mortar production. Sustainability indicators were used to assess the environmental, social, and economic impact of both types of mortar. The results showed that 10% of the natural resources consumption was saved. Also, CO2 releases were reduced by 5%. Furthermore, from the economic point of view a reduction of 6.5% of the cost was reached.
In the same sustainability context, Kırgız (Citation2018) presented the physical properties of green cement composite reinforced by graphite nano-engineered particles suspension (GNPS). Sustainability, stiffness, hydraulic lateral formwork pressure, and strength gained at early age were examined. Findings of numerous tests covering the optical atomic absorbance spectra, the initial and final stiffness of time, the flow, and the early age compressive strength of green composite concept, were discussed. In all tests, the usability of GNPS as an innovative original nano-engineered-suspension for infrastructure renewal material and for manufacturing of green cement composite concept was highly effective.
Adedeji, Ibiyeye, and Adedeji (Citation2018) studied the influence of the plastering materials on the thermal performance of three strawbale building units. Laterite mortal with nanoparticle clay screeding and cement-sand mortal were evaluated in this study as compared to normal laterite mortal. The thermal conductance, thermal resistance and thermal transmittance of the building units were evaluated according to ASTM C1045-90 standard specifications. The thermal resistivity of the laterite plastered wall was greater than that of cement-sand mortal. Clay screeding was of slight influence on the thermal performance of the straw bale wall.
This research aims to investigate the sustainable effect of partially substituting cement in the concrete mix with two types of waste particles, one from an agricultural origin and the other from an industrial basis.
2. Methodology
Two types of nano waste particles, rice husk ash (RHA) and carbon nanotubes (CNT) were chosen to be a step towards evaluating wastes from agricultural and industrial origins. The two wastes are specifically chosen to evaluate their sustainability effect on concrete as partial replacement of cement. The cement contained in the control mix (1st mix) represented 20% of the mix content. Carbon nanotubes (CNT) replaced 0.1% of the cement content in the second mix, while rice husk ash (RHA) replaced 5% of the cement content in the third mix.
A software for evaluating the sustainability of the nano waste materials was investigated. The Sustainable Decision Support System (SDSS) model was selected due to its simplicity, and its high sensitivity to scoring systems based on both the life cycle assessment (LCA) technique and Multi-Criteria Decision analysis Methods (MCDM).
The used Sustainable Decision Support System (SDSS) model is a computer-based system that supports the sustainable evaluation of structural materials. This evaluation depends on a developed sustainable scoring system; a life cycle assessment (LCA) of the three phases of materials: manufacturing, construction, and demolition; a Multi-Criteria Decision analysis Method (AHP, TOPSIS and Entropy); Four sustainability aspects: environmental, social, economic, and technological; as well as using ten sustainable factors divided into two sets. The first set includes factors regarding the design of the structural elements among which are: Climate Change, Pollution, Energy Consumption, Resources and waste and Cost. Whereas the second set includes factors concerning the general characteristics of the materials such as: Recyclability, Local Economic Development, Health and Safety, Human Satisfaction, and Practicability. (Bakhoum and Brown Citation2015)
In order to measure these aspects, the SDSS model used some indicators such as:
Embodied carbon dioxide for measuring the global warming for climate change.
Disability-Adjusted Life Years (DALYs) and Acidification Index for measuring air pollution and acidification for pollution.
Embodied energy for measuring Energy Consumption.
Raw material consumption and weight of residual waste for measuring Resource & waste.
Recycled contents for measuring Recyclability.
Material cost for measuring Cost
Local content and contribution to employment for measuring Local Economic Development.
Environmental quality against ozone depletion and safety against accidents for measuring Health and Safety
Appropriateness for culture and Level of noise & vibration for measuring the Human Satisfaction.
Degree of off-site manufacture and Renewability of resources for measuring Practicability.
Finally, technical, environmental and economic information about the nano-waste alternatives under study were collected and fed into the model.
The study conducted used two criteria of assessment. Both assessments used the same alternatives, data inputs, and quantities. The first assessment used the default system weight for all sustainability factors included. The second assessment used equal weights for the factors. These two methods of weighing the factors were undertaken to test its sustainability effect on the final evaluation results of the different materials.
In general, the three phases of material’s life cycle are manufacturing, construction, and demolition. In this study, the life cycle inventory data for the control mix and the other two alternatives were considered only for the manufacturing phase (phase 1) in the SDSS model as the main difference between the three materials would greatly affect the sustainability aspects in this phase.
During the manufacturing phase, carbon nanotubes consume energy and result into emissions and release of waste. Despite that its characteristics, even with small amounts (0.1%) as replacement of cement, would significantly improve the concrete mechanical properties. To the contrary, rice husk ash consumes zero energy and doesn’t release emissions as it is produced from a natural raw residue, yet its use as a replacement for cement in the concrete mix reduce the strength of concrete unless it is used in proportions ranging between 3–10%.
3. Data collection
According to the inputs demanded by the model, a life cycle assessment (LCA) of carbon nanotubes has been obtained from ‘Environmental Assessment of Single-Walled Carbon Nanotube Processes’. The LCA of CNT using High-pressure carbon monoxide (HiPco) process has been chosen among the three-different processes of CNT manufacturing investigated in (Healy, Dahlben, and Isaacs Citation2008) as it has the least negative environmental impact. This fact contributes to this research’s aim to investigate the sustainability effect of replacing cement; the most conventional expensive material; in the concrete mix with nano waste particles.
Besides, the LCA of rice husk ash (RHA) as a pozzolanic material blended with Portland cement to produce green concrete was obtained from previous studies to serve the inputs in the SDSS model (Garas, Bakhoum, and Allam Citation2015; Zerbino, Giaccio, and Isaia Citation2011). LCA data of cement and aggregate were collected from both studies conducted by Bakhoum et al. (Citation2017) and Healy, Dahlben, and Isaacs (Citation2008).
presents the data required in the Life Cycle Inventory (LCI) of each component inserted in the model. The table includes CO2, SOx, NOx, particulates, embodied energy, raw material consumption and solid waste for all used materials. Nevertheless, rice husk ash is considered of zero CO2, SOx, and NOx emissions. Also, there is neither release of particulates and solid wastes nor energy and raw material consumption as illustrated. Rice husk ash as an agricultural waste has no energy consumption in its natural state, and the energy used during its incineration process was negligible.
Table 1. LCA of Components Compiled in the Studies (Bakhoum et al. Citation2017; Garas, Bakhoum, and Allam Citation2015; Healy, Dahlben, and Isaacs Citation2008; Zerbino, Giaccio, and Isaia Citation2011)
The cost of cement and aggregate are according to the current local price of the market in Egypt. The price of carbon nanotubes was obtained from local suppliers, whereas RHA was of zero-cost as it is a disposed waste that contributed to land pollution.
The SDSS model uses Air pollution and Acidification to measure the pollution. Air pollution is measured by Disability-Adjusted Life Years (DALYs) as a common metric criterion. Air pollutants index can be calculated as follows:
mi = mass (in grams) of inventory flow i, and CPi = microDALYs per gram of inventory flow i. (CPi = 0.002, 0.046, and 0.014 for NOx, Particulates and SOx respectively.)
Acidification index is measured as follows:
mi = mass (in grams) of inventory flow i, and APi = Acidification Potentials (APi = 1, and 0.7 for SO2 and NOx respectively).
The SDSS can consider the sustainable scores of structural materials using the actual LCI data of materials, which is automatically compiled to a score by the system. The system converts the real material LCI value into a percentage value to be measurable by the scale. The process includes the following calculation steps:
-Calculate the life cycle inventory step value (T) that presents 1% of the percentage score in the SDSS scale. It can be calculated as follows:
Where, M: Maximum LCI value in the scale
N: Minimum LCI value in the scale
-Calculate the percentage sustainable score (P)
Where, L: life cycle inventory number
-Calculate the Score (S) as follows:
The SDSS integrate the scoring system into a Multi-Attribute Decision Making (MADM) approach that utilises the theories of decision-making – Analytical Hierarchy Process (AHP), Technique for Order Preference by Similarity to the Ideal Solution (TOPSIS), and Entropy theory – to rank and select the structural materials based on the identified sustainability criteria over their total life.
4. Results and analysis
The results of evaluating the 3 concrete mixes according to the different weighing criteria of the sustainability factors is presented.
4.1. Assessment using system default weights of factors
This assessment was carried out using system’s default weight as designed for all the ten sustainability factors during the three life cycle phases of any material. presents the general sustainability weights of all factors. Climate change, pollution, energy consumption, and cost were the factors of greatest weight in phase 1(the manufacturing phase). Whereas recyclability had the greatest relative weight during the demolition phase and practicability was the most dominant during the construction phase.
4.1.1. Sustainability ranks and scores of each material
The SDSS model assessed each of the three materials using the score given to each of the ten sustainability factors according to the life cycle assessment (LCA) input of each material’s components during the manufacturing phase only. In the relative score of RHA concrete mix in general exceeds the scores of the control concrete mix and CNT concrete mix by 0.01 and 0.081, respectively.
demonstrates a detailed comparison of each material solely for the ten-sustainability factors. Although CNT replaced some of the cement content, its sustainability scores are almost similar to those of the control mix due to the small replacement proportion of 0.1% of the cement content, resulting in nearly no effect on the score outcome. The energy consumption sustainability score was the least for the mix containing CNT. This is a result of the high amount of energy consumed by CNT manufacturing according to its life cycle assessment. The RHA concrete mix energy score surpasses those of control concrete mix and concrete-CNT by 0.03, and 3.63, respectively. This is attributed to the fact that RHA is assumed to consume zero energy and its addition in the concrete mix decreased the cement content and accordingly its energy consumption. In addition, control concrete mix score is higher than that of the concrete-CNT mix by 3.6. This is a result of the high amount of energy consumed by CNT manufacturing according to its life cycle assessment.
4.2. Assessment using equal weights of factors
This assessment was carried out using equal weights for the ten sustainability factors. The SDSS model assessed each of the three materials according to the life cycle assessment (LCA) input of each material’s components. demonstrates the overall score of each of the three materials according to the 2nd type of assessment. The score of concrete-RHA mix exceeds the scores of the control concrete mix and the concrete-CNT mix by 0.007 and 0.051, respectively. Comparing between the two types of assessment based on the weights given to the ten sustainability factors, the results demonstrated that the CNT concrete mix is the least sustainable among all mixes. The concrete mix with RHA was the most sustainable among all mixes especially for the 1st set of factors.
5. Conclusions
The research presented a quantitative assessment of the sustainability effect of partially replacing cement in the green concrete mix with two types of nano-waste particles. It is intended to be a step towards sustainable construction by making decisions for evaluation and selection of nanomaterials in green concrete mixes based on sustainable/environmental criteria. The main benefits are the reduction of cement consumption and its consumed energy, as well as improving the quality of environment by reducing air pollution, acidification, and solid waste
The different assessment weighing techniques of the sustainability factors for the three mixes did not show substantial variance in the resulting scores for the same manufacturing phase. However, the concrete mix with RHA showed the best sustainability results for all factors. This is because RHA’s life cycle categories were zero as being an agricultural residue of a natural material. Substituting 5% of the cement content in the mix by RHA partially contributed to minimising the carbon emissions and energy consumed during the cement manufacturing phase. Whereas, CNT is expensive, and its production consumes high amount of energy thus contributed negatively to the final evaluation result although its substitution proportion was minimal. It is recommended to undertake more studies on the Life Cycle assessment of nano- waste particles of natural origin that would replace the cement content in the concrete mix with optimum proportions to enhance its sustainability without significantly affecting its mechanical properties.
Disclosure statement
No potential conflict of interest was reported by the author(s).
Additional information
Funding
Notes on contributors
Gihan Garas
Dr. Gihan Garas is a Professor of Civil Engineering/Construction Management researcher at the National Research Centre. Also Dr Garas acts as a Professor of Construction Management at the British University in Egypt. Dr. Garas is engaged in teaching and supervising the graduation projects at the Construction Management Department.
Alaa Mohamed Sayed
Dr Emad Bakhoum is an Associate Professor at the National Research Centre. He is recently acting as a tutor and supervisor of the Construction and Engineering Management Department at The Nile University.
Emad Shaker Hana Bakhoum
Eng. Alaa Mohamed is a Teaching Assistant at the British University in Egypt.
References
- Adedeji, A. A., A. Ibiyeye, and A. M. Adedeji. 2018. “Effect of Temperature on Strawbale Wall Rendered with Laterite and Clay Nanoparticle.” MATEC Web of Conferences 165: 22008. doi:https://doi.org/10.1051/matecconf/201816522008.
- Ahmad Shah, I., H. Rao, and V. Gupta. 2019. “An Experimental Research On Partially Replacement Of Cement In M20 Conrete With rice husk ash And Waste Paper Sudge.” International Journal of Engineering Sciences & Research Technology 8 (1): 100–110.
- Bakhoum, E. S., and D. C. Brown. 2015. “An Automated Decision Support System for Sustainable Selection of Structural Materials.” International Journal of Sustainable Engineering 8 (2): 80–92. doi:https://doi.org/10.1080/19397038.2014.906513.
- Bakhoum, E. S., G. L. Garas, M. E. Allam, and H. Ezz. 2017. “The Role of Nano-technology in Sustainable Construction: A Case Study of Using Nano Granite Waste Particles in Cement Mortar.” Engineering Journal 21 (4): 217–227. doi:https://doi.org/10.4186/ej.2017.21.4.217.
- Bansal, S., and Y. Antil. 2015. “Effect of Rice Husk on Compressive Strength of Concrete.” International Journal on Emerging Technologies 6 (1): 144.
- Du, S., J. Wu, O. AlShareedah, and X. Shi. 2019. “Nanotechnology in Cement-based Materials: A Review of Durability, Modeling, and Advanced Characterization.” Nanomaterials 9 (9): 1213. doi:https://doi.org/10.3390/nano9091213.
- Elvin, G. 2007. “Building Green with Nanotechnology.” In 2007 NSTI Nanotechnology Conference and Trade Show - NSTI Nanotech 2007, Technical Proceedings, vol. 4, 683–686. Santa Clara May 20, 2007.
- Gammampila, R., P. Mendis, T. Ngo, L. Aye, A. S. Jayalath, and R. A. M. Rupasinghe. 2010. Application of Nanomaterials in the Sustainable Built Environment. International Conference on Sustainable Built Environment (ICSBE-2010), Kandy, 13-14 December 2010
- Ganesh, V. K. 2012. “Nanotechnology in Civil Engineering.” European Scientific Journal 8 (27): 96–109.
- Garas, G., E. Bakhoum, and M. Allam. 2015. “Rice Straw-cementitious Bricks: Analytical Study on Mechanical Properties and Sustainability Measures.” ARPN Journal of Engineering and Applied Sciences 10 (18): 7959–7968.
- Givi, A. N., S. A. Rashid, F. N. A. Aziz, and M. A. M. Salleh. 2010. “Assessment of the Effects of rice husk ash Particle Size on Strength, Water Permeability and Workability of Binary Blended Concrete.” Construction and Building Materials 24 (11): 2145–2150. doi:https://doi.org/10.1016/j.conbuildmat.2010.04.045.
- Gopi, N., and P. Sruthi. 2017. “An Experimental Study on the Strength of Concrete with Partial Replacement of Cement by rice husk ash.” In International Conference on Emerging Trends in Engineering, Science and Sustainable Technology (ICETSST-2017), 9–12, Erode, India.
- Hanus, M. J., and A. T. Harris. 2013. “Nanotechnology Innovations for the Construction Industry.” Progress in Materials Science 58 (7): 1056–1102.
- Healy, M. L., L. J. Dahlben, and J. A. Isaacs. 2008. “Environmental Assessment of Single‐walled Carbon Nanotube Processes.” Journal of Industrial Ecology 12 (3): 376–393. doi:https://doi.org/10.1111/j.1530-9290.2008.00058.x.
- Hernández-Moreno, S., and S. C. S. de la Torre. 2017. “Nano-technological Products in Architecture and Construction.” Holos 2: 35–51. doi:https://doi.org/10.15628/holos.2017.5497.
- Hernández-Moreno, S., and S. C. Solache de la Torre. 2017. “Nano-Technological Products in Architecture and Construction.” Holos 2: 34. doi:https://doi.org/10.15628/holos.2017.5497.
- Irshidat, M. R., N. Al-Nuaimi, and M. Rabie. 2021. “Influence of Carbon Nanotubes on Phase Composition, Thermal and Post-Heating Behavior of Cementitious Composites.” Molecules 26 (4): 850. doi:https://doi.org/10.3390/molecules26040850.
- Kırgız, M. S. 2018. “Green Cement Composite Concept Reinforced by Graphite Nano-engineered Particle Suspension for Infrastructure Renewal Material.” Composites Part B: Engineering 154: 423–429. doi:https://doi.org/10.1016/j.compositesb.2018.09.012.
- Mohamed, A. S. Y. 2015. “Nano-Innovation in Construction, A New Era of Sustainability.” In International Conference on Environment and Civil Engineering, Vol. April, 97–100–108. Pattaya-Thailand.
- Norhasri, M. S. M., M. S. Hamidah, and A. M. Fadzil. 2017. “Applications of Using Nano Material in Concrete: A Review.” Construction and Building Materials 133: 91–97. doi:https://doi.org/10.1016/j.conbuildmat.2016.12.005.
- Rocha, V. V., and P. Ludvig. 2018. “Nanocomposites Prepared by a Dispersion of CNTs on Cement Particles.” Architecture, Civil Engineering, Environment 11: 73–77.
- Rong, Z., M. Zhao, and Y. Wang. 2020. “Effects of Modified Nano-SiO2 Particles on Properties of High-Performance Cement-Based Composites.” Materials 13 (3): 646. doi:https://doi.org/10.3390/ma13030646.
- Sabihuddin, S. 2014. “Application of Nanotechnology in Civil Infrastructure.” Journal of Engineering Research and Applications 4(3) (version1). www.Ijera.Com.
- Saifuddin, N., A. Z. Raziah, and A. R. Junizah. 2013. “Carbon Nanotubes: A Review on Structure and Their Interaction with Proteins.” Journal of Chemistry 2013: 1–18.
- Singh, N. B., M. Kalra, and S. K. Saxena. 2017. “Nanoscience of Cement and Concrete.” Materials Today: Proceedings 4 (4): 5478–5487.
- Vidivelli, B., and B. Ashwini. 2018. “A Study on Carbon Nanotube (CNT) in Concrete.” International Research Journal of Engineering and Technology (IRJET) 5 (7): 481–489.
- Zerbino, R., G. Giaccio, and G. C. Isaia. 2011. “Concrete Incorporating Rice-husk ash without Processing.” Construction and Building Materials 25 (1): 371–378. doi:https://doi.org/10.1016/j.conbuildmat.2010.06.016.