ABSTRACT
Sustainable development favours integration between different sectors to facilitate effective utilisation of natural resources. In this regard, the objective of this work was to investigate the use, in the building industry, of the following two components derived from cow milk that is unfit for human consumption: a biodegradable release agent composed of milk fat and used soybean oil; and cementitious mortar composed of a biodegradable admixture of protein complexes (whey and κ-casein). Scanning electron microscopy and Raman spectroscopy analyses were performed to examine the morphology and chemical structure/curing process of the materials, respectively. Finally, the results were used to demonstrate that the products obtained from milk waste are viable for use in cementitious compounds. It was observed that the bio-release agent aided the demoulding process of the specimens in both moulds and did not decrease the compressive strength of the specimens. As regards the biopolymer, an increase in the compressive strength of the samples was observed at all ages, thus indicating a positive effect compared with that of commercial plasticisers in the 90-day samples.
1. Introduction
The building industry relies on specific methodologies to assess the development of sustainable enterprises to achieve the goals of the 2030 Agenda for Sustainable Development, linked to industry, innovation and, infrastructure (Barbosa and Almeida Citation2017; Oliveira, Burattino Melhado, and Vittorino Citation2015). Brazil is currently the third largest producer of bovine milk, and in 2019, approximately 34.4 billion L of milk was produced (Projeções do Agronegócio: Brasil Citation2018/19 a 2028/29 projeções de longo prazo 2019). Approximately 0.5% – 4% of the milk produced is considered as waste milk by the dairy industry because it is unfit for human consumption. Therefore, the waste milk is discarded in accordance with the National Environmental Policy (Omil et al. Citation2003; Silva, Siqueira, and Nogueira Citation2018).
Studies have demonstrated the possibility of using different types of proteins to improve the properties of concrete (Biswas et al. Citation2010; Panesar Citation2013; Remadnia et al. Citation2009; F. Zhang et al. Citation2019). In particular, a recent study has demonstrated the possibility of using protein complexes (whey and κ-casein) as cooperators in the hydration process of Portland cement for the production of concrete with exceptional properties (de Souza et al. Citation2019), allowing utilisation of approximately 20.0% of the total milk waste. Notably, the aforementioned technology and innovation processes aided the relationship between the dairy industry and construction industry. This promoted the utilisation of material based on a circular and efficient economy to overcome old practices that diverge from the concept of sustainable development (Salmenperä et al. Citation2020).
The construction industry is accessible to novel technological alternatives that ensure adequate results such as reuse of industrial waste for construction (Costa and Ribeiro Citation2020; Kabirifar et al. Citation2020; Soares Filho et al. Citation2020; Tayeh et al. Citation2019). In this scenario, while constructing pieces (structural or non-structural) using Portland cement, moulds (e.g. wood and metal) have been used to fabricate the models that fulfill the projects that constitute the entire construction process of an enterprise (Ahmed and Lim Citation2021; Mo et al. Citation2020; Prasara-A and Gheewala Citation2017).
In practice, it has been observed that the appearance of the components of Portland cement is highly linked to the curing conditions and the concrete-mould contact. Release agents prevent natural adhesion between the mould and the cementitious compound. As this covering over the mould decreases the friction between the faces (cementitious product/ mould), selecting an adequate release agent reduces the maintenance and operational costs of the final products (Izarra et al. Citation2019; León-Martínez et al. Citation2016; Shah Mohammadi et al. Citation2017; W. Zhang et al. Citation2020).
In this context, this study aimed to develop and test a biodegradable release agent. Further, its effect on the curing of Portland cement added with a biopolymer admixture was examined and compared with that on the curing of cement with a commercial plasticiser admixture. Therefore, an experimental procedure was developed to evaluate the quality of mortars produced with the proposed materials. The results were compared with reference mixtures (without the biodegradable materials), and the possibility of using these waste products in the building industry was verified.
The importance of this study lies in the potential integration of building and dairy sectors owing to the development of sustainable products using the admixture (biopolymer) and biodegradable release agent. This study is expected to provide the basis for future studies in this direction with emphasis on sustainable development.
2. Materials and methods
2.1. Cement
Portland cement type V, with high early resistance, was used in this investigation; shows the characterisation of the cement.
Table 1. Characterisation of portland cement type V
2.2. Aggregate
River sand was used as the aggregate and it had the following physical characteristics: maximum diameter of 2.40 mm, specific mass within the range of 1.46–2.62 kg/dm3, fineness modulus of 2.52, powdered material content of 1.33%, and organic impurity < 300 ppm.
Plasticiser:
The following two types of plasticisers were used: (1) an aqueous solution of the biopolymer (protein complex of whey and κ-casein) obtained from skimmed cow milk which was unfit for human consumption, according to the procedure described in the literature (Dias de Souza et al. Citation2019) and (2) commercial (plasticiser type), composed of adhesives based on natural resins. The first plasticiser had 5.118 ± 0.026% of total solids suspended in water to form the mixture.
2.4. Moulds
Wooden (plywood sheets) and metallic moulds were used. The metallic moulds were cylindrical in shape with a diameter of 5 cm and a height of 10 cm, and the wooden moulds had a cubic shape with an edge of 5 cm.
2.5. Release agent
The two following types of release agents were used: (1) commercial compound based on liquid wax and organic fat, usually used in the Brazilian building industry to prevent adherence and facilitate the removal of moulds without damaging the cement mixture; and (2) bio-release agent composed of 50% used soy oil and 50% unsafe milk fat. The fat was obtained using the following procedure: 1 L of unsafe milk was added in a beaker, and it was heated and stirred until boiling. The unsafe milk in the beaker was allowed to cool and settle down at 30 °C. It was observed that a liquid phase (cream) was formed in the upper part of the milk. The mixture was transferred to a separatory funnel and allowed to settle for 2 h for phase separation. The upper phase was collected, cooled to 15 °C and beaten for 30 min to form fat globules, which were separated from the formed serum through filtration.
Finally, the bio-release agent was obtained by heating at 50 °C for 10 min; the fat extracted from the milk and the soybean oil were used in the same mass proportion.
2.6. Mortar
A mortar ratio of 1:6:0.9 (cement: sand:water/cement factor; proportion in weight), which is usually used in the engineering works in the southeastern region of Brazil, was used. Notably, 2 mL of commercial admixture was used in the mixture, as recommended by the manufacturer. As for the biopolymer additive, 168 g was added in relation to the total cement mass, that is, 168 g for each kilogram of cement.
2.7. Mechanical properties
The compressive strength, absorption by immersion, and capillary absorption were verified in accordance with the Brazilian standards as shown in (BrazilianAssociationofTechnicalStandards Citation2012, Citation2009, Citation2019).
Table 2. Summary of the tests performed in the study
The capillary water absorption test determines the amount of water that can be absorbed owing to capillary action rise in the specimen. The specimens were placed in an oven and weighed until a constant mass was obtained. Subsequently, a marking was carried out at a height of 5 mm from its base and they were taken to a container with water at the height of the marking made. Mass measurements were performed at 10, 90, 180, 360, 2880, and 4320 min after exposure to water slides. At 4320 min, the specimens were broken by diametrical compression and the height of water rise in their interior was measured with a ruler.
The water absorption test by immersion represents the maximum capacity of the mortar to absorb water. In this test, the specimens were placed in a container filled with water for 1/3 of its height for 4 h. Subsequently, the container was filled with water up to two-thirds the height of the specimen and left to rest for the same period. Finally, the specimen was submerged in water and was allowed to rest for another 64 h. The absorptive capacity was determined through the mass of the specimen after 24 h, 48 h, and 72 h of immersion, being made with its dry surface.
For the compressive strength test, after moulding, the specimens, still in the moulds, were placed in a humid chamber for 24 h. After this period, the specimens were removed from the moulds and left in the humid chamber inside the curing tank, where they remained until the resistance test was performed (7, 21, and 90 days).
During the test, the faces of the test piece were levelled to ensure a uniform distribution of load. Next, the specimens were placed in an electronic hydraulic press (Conteco Company, model 5 T I4214). A continuous load without shocks was applied, with a loading speed of 0.5 MPa/s, and the load was measured when the specimen approached rupture.
With regard to the nomenclature adopted for the specimens, presents an illustrative scheme where, for example, the sequence ‘B1Z’ corresponds to mortar specimens (1:6:0.9) in which the bio release agent was used, in metallic moulds, with the biopolymer admixture (168 g) in the mixture.
2.8. Microstructural analysis
A microstructural analysis of the solids on the surface of the samples was performed to observe the fragments of residual release agent on the surface, using scanning electron microscopy (SEM) with a voltage of 20 kV, Mag 500x and 20 μn.
2.9 Raman spectroscopy
Raman spectroscopy was used to evaluate the hydration reactions of the cement mortar with the use of the commercial admixture and the biopolymer admixture. The measurements were performed using a Bruker RFS 100 spectrometer excited with a Nd+3/YAG laser operating at 1.064 nm, equipped with an InGaAs detector, cooled with liquid nitrogen. The spectra were acquired at a resolution of 4 cm−1. An average of 256 scans were collected with a laser power of 40 mW.
3. Results and discussion
, and show the results obtained in this study. It should be noted that the coefficient of variation (CV) of the samples was calculated for the results presented in each property evaluated to ensure that only results with a CV ≤ 25% are accepted as adequate. Therefore, it was observed from the results that the release agent used (B or D) does not interfere in the development of the compressive strength of the specimen test studied. However, there is an effect of the type of admixture (Y or Z), and the biodegradable admixture contributes in a favourable way. The utilisation of the bio-release agent (B) in mortars where commercial admixture is used was comparatively effective in the case of the metallic moulds (B1Y and D1Y), as well as when it is associated with the use of biopolymer (B1Z and D1Z), enhancing the effect of the sustainable admixture.
Table 3. Test results using the bio release agent (B)
Table 4. Test results using commercial release agent (D)
The specimens formed in wooden moulds had a higher level of absorption by capillarity (B2X, B2Y, B2Z, D2X, D2Y and D2Z), possibly due to the loss of water to the environment through the material that constitutes the mould, which allowed the formation of pores in the specimen test (W. Zhang et al. Citation2020), as illustrated in .
The use of commercial plasticiser admixture (B1Y, D1Y, B2Y and D2Y) tends to increase the capillary action and the number of pores in the specimen test, directly affecting the transport of moisture between the capillary pores (Wesołowska and Kaczmarek Citation2016);
shows irregularly agglomerated surfaces with fibrous spots in the vicinity (Kontoleontos et al. Citation2012), where the C-S-H formation occurs. The ‘close’ structure of the ettringite (thin and elongated in the shape of a needle) found in the vicinity of the pores was used as a hydration product to fill the voids, being a C-S-H gel (Li et al. Citation2004).
Figure 3. SEM images after 90 days of age (a) specimen: B2Z; (b) specimen: B2Y; (c) specimen: D2Z and (d) specimen: D2Y
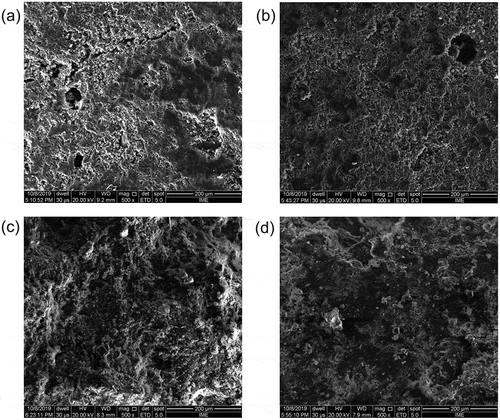
show the Raman spectrum of the specimen test. It was observed that after 7 days of age, the formation of a pronounced shoulder approximately 710 cm−1, in the spectrum of all specimen tests was verified, which was related to the decrease in the band intensity at 650 cm−1 due to the hydration process of the C3S component of Portland cement (Bonen, Johnson, and Sarkar Citation1994; Dias de Souza et al. Citation2019; Martinez-Ramirez, Frías, and Domingo Citation2006). This process can also be observed by the increase in the intensity of the bands at 1119 and 1024 cm−1, associated with the C2S component. At 90 days of age, the presence of the bands at 465 cm−1 (in all samples) was verified, which was attributed to the deformation of the tetrahedral SiO4, referring to the occurrence of the hydration process and the formation of C-S-H bonds (Kirkpatrick et al. Citation1997). Further, the bands at 1084 cm−1 (only in samples BZ and DZ) are attributed to the formation of calcium carbonate (in its polymorphic form of valerite) due to the reaction between the calcium hydroxide and the atmospheric carbon dioxide (Bensted Citation1977).
Figure 4. Raman spectra of the samples without admixture: (a) 0 days of age; (b) 7 days of age; (c) 21 days of age and (d) 90 days of age
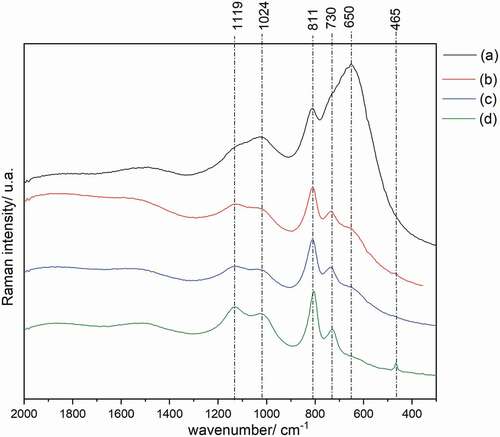
Figure 5. Raman spectra of the samples with the addition of the biopolymer admixture: (a) 0 days of age; (b) 7 days of age; (c) 21 days of age and (d) 90 days of age
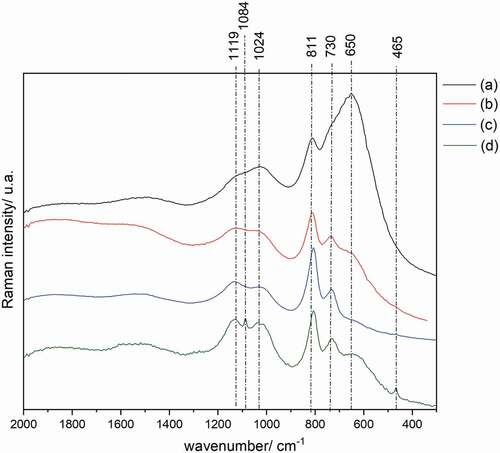
Figure 6. Raman spectra of the samples with commercial admixture: (a) 0 days of age; (b) 7 days of age; (c) 21 days of age and (d) 90 days of age
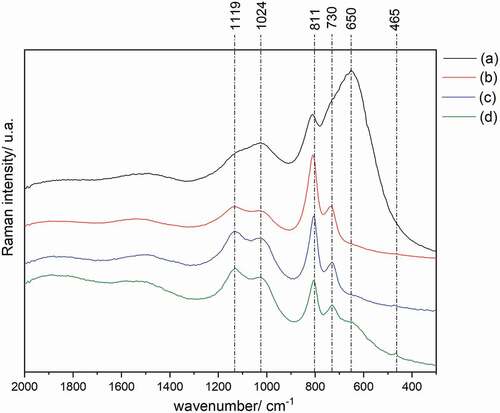
The hydration of the cement is relatively slow; this involves the hydration of calcium silicates, precipitation of the C-S-H (Ca2SiO4.H2O) gel and portlandite (Ca(OH)2). The composition and structure of the C-S-H gel vary with time, with a gradual decrease in the Ca/Si ratio and an increase in the length of the silicate chain (Martinez-Ramirez, Frías, and Domingo Citation2006). As reported previously, the ratio of the areas between the bands 811 (A811) and 650 cm−1 (A650) may be an indicator of the formation of C-S-H and of the degree of curing of the Portland cement CPV-ARI. Therefore, when the A811/A650 ratio presents a value greater than 1.0, it is obtained the formation of the C-S-H gel and, consequently, the degree of hydration of the cement (Kirkpatrick et al. Citation1997). In this sense, shows the ratio of these bands over time for the specimen without admixture, with biopolymer admixture, and with commercial admixture. It was possible to verify during analysis that at 7 days of age, the specimen with the commercial admixture and with the biopolymer admixture reached a ratio greater than 1.0, while the specimen without admixture does not reach this ratio. This indicated that the commercial admixture and the biopolymer admixture aid in the initial hydration of the cement. However, the action of the commercial admixture is comparatively intense than that of the biopolymer, given that the area ratio was significantly higher. At 21 days of age, the ratio of the areas of the specimen with commercial admixture declined, while that of the other specimen continued to increase. Finally, at 90 days of age, the ratio of the specimen with the biopolymer admixture and commercial admixture decreased, while that of the specimen without admixture continued to increase. This behaviour indicated that the commercial admixture has a greater action at the beginning of the hydration process, while the biopolymer contributes to the hydration of the cement in a slower manner.
5. Conclusions
It was observed that the bio-release agent acted as a facilitator in the demoulding process of the specimens, especially in metallic moulds, and it did not affect the compressive strength of the tested specimens. Both plasticiser additives visually affected the plasticity of the samples, in relation to the compressive strength in the first ages. Additionally, both plasticisers caused an increase in strength compared with that of the non-additive sample, and the samples with biopolymer at the age of 90 days showed better performance. However, it was observed that there is a reduction in the performance of the biopolymer when wooden moulds were used. A similar performance reduction was observed when commercial plasticiser was used in metallic moulds. This phenomenon might be affected by the absorption capacity of the surface of the mould material.
Furthermore, the presence of pores in the microstructure of the compounds with biopolymer additive was observed, which was not associated with greater water absorption. In the microscopic analysis, a longer cure was found for the compounds added with the biopolymer mixture and with the presence of the bio release agent, which presents a well-formed structure with fibrous stains and without the presence of residues of the bio-release agent.
A new application of these materials in civil construction was also analysed, evaluating their physicochemical, macro and microstructural properties and comparing their use in metallic and wooden moulds. Additivated concrete exhibited superior performance in terms of resistance and water absorption compared with that of common concrete; this contributes to the reduction of material consumption and the durability of the system.
The utilisation of biopolymers and bio-release agents adds economic value to a material that would previously be discarded and reduces the volume of disposal. The proposed biomaterials can be used for civil construction, creating an opportunity for the sector to reduce the environmental impact caused by the inadequate disposal of waste by using fewer polluting materials and generating a circular economy chain.
Acknowledgments
National Council for Scientific and Technological Development – CNPq/Brazil, Coordination of Superior Level Staff Improvement – CAPES/ Brazil, The Foundation for Research of the State of Minas Gerais – FAPEMIG/ Brazil and Federal University of Juiz de Fora – UFJF/ Brazil.
Disclosure statement
No potential conflict of interest was reported by the author(s).
Additional information
Notes on contributors
Clarissa Sousa
Clarissa Dias de Sousa: Civil Engineering from the Federal University of Juiz de Fora (2011). Specialist in Geotechnics and Earth Works (2017) and Sustainability in Construction (2018). Master's Degree in Built Environment from the Federal University of Juiz de Fora (2019) and Doctoral Student in Material Sciences by the Military Institute of Engineering, with professional experience in tunnel excavations, design in concrete structures and hydraulic installations, new technologies and innovation.
Nelson Luis Souza
Nelson Luis Gonçalves Dias de Souza: Adjunct Professor of Physical Chemistry at the Exact Sciences and Biotechnologies collegiate of the Federal University of Tocantis, Campus-Gurupi. Member of the Graduate Program in Chemistry (UFT). Bachelor and Degree in Chemistry from the Federal University of Juiz de Fora (UFJF). Doctor in Chemistry (emphasis in Physical Chemistry) from UFJF. He has experience in the characterization of materials through the use of vibrational (Raman and Infrared) and thermal techniques and their applications in controlled drug delivery matrices. Greater focus on the study of supramolecular interactions existing in organic and coordination polymers and the decomposition process of organic polymers.
Vicente Rosse
Vicente Junio de Olivera Rosse: Graduated in Civil Engineering from the Federal University of Juiz de Fora. He has experience in Civil Engineering, with an emphasis on Civil Engineering, working mainly on the following topics: thermography, degree of degradation, watertightness, pathological manifestations. and nanosilica.
Pedro Henrique da Silveira
Pedro Henrique Poubel Mendonça da Silveira: Master in Materials Science from the Military Institute of Engineering (2020), Bachelor in Mechanical Engineering from the University Center Anhanguera de Niterói (2017). Currently taking a PhD course in Materials Science at the Military Institute of Engineering, working in the research line of ceramic materials, with emphasis on the processing and characterization of advanced ceramic materials based on alumina.
Maria Teresa Barbosa
Maria Teresa Gomes Barbosa: Graduated in Engineering from the Federal University of Juiz de Fora (1990), Master's in Engineering from the Federal University of Rio Grande do Sul (1993) and Ph.D. in Civil Engineering from the Federal University of Rio de Janeiro (2002). She is currently a full professor at UFJF, reviewer of indexed periodicals (American Concrete Institute, Built Environment, Engineering Study and Research, among others), ad hoc consultant at FACEPE, evaluator of a higher education institution at the Ministry of Education and Culture. She has experience in the Civil Engineering area, with an emphasis on Construction Materials and Components, working mainly on the following topics: pathology, steel-concrete adhesion, new materials, always seeking integration with the built environment and its sustainability.
References
- Ahmed, W., and C. W. Lim. 2021. “Production of Sustainable and Structural Fiber Reinforced Recycled Aggregate Concrete with Improved Fracture Properties: A Review.” Journal of Cleaner Production 279: 123832. doi:https://doi.org/10.1016/j.jclepro.2020.123832.
- Barbosa, M. T. G., and M. Almeida. 2017. “Developing the Methodology for Determining the Relative Weight of Dimensions Employed in Sustainable Building Assessment Tools for Brazil.” Ecological Indicators 73: 46–51. doi:https://doi.org/10.1016/j.ecolind.2016.09.017.
- Bensted, J. 1977. “Raman Spectral Studies of Carbonation Phenomena.” Cement and Concrete Research 7 (2): 161–164. doi:https://doi.org/10.1016/0008-8846(77)90026-6.
- Biswas, M., S. Majumdar, T. Chowdhury, B. Chattopadhyay, S. Mandal, U. Halder, and S. Yamasaki. 2010. “Bioremediase a Unique Protein from a Novel Bacterium BKH1, Ushering a New Hope in Concrete Technology.” Enzyme and Microbial Technology 46 (7): 581–587. doi:https://doi.org/10.1016/j.enzmictec.2010.03.005.
- Bonen, D., T. J. Johnson, and S. L. Sarkar. 1994. “Characterization of Principal Clinker Minerals by FT-Raman Microspectroscopy.” Cement and Concrete Research 24 (5): 959–965. doi:https://doi.org/10.1016/0008-8846(94)90016-7.
- Brazilian Association of Technical Standards. 2009. NBR 9778: Mortar and Concrete – Determination of Water Absorption of Immersion. ABNT, Brazil.
- Brazilian Association of Technical Standards. 2012. NBR 9779: Mortar and Concrete – Determination of Capillary Absorption. ABNT, Brazil.
- Brazilian Association of Technical Standards. 2019. NBR 7215: Cement Portland – Determination of Compressive Strength. ABNT, Brazil.
- Costa, F. N., and D. V. Ribeiro. 2020. “Reduction in CO2 Emissions during Production of Cement, with Partial Replacement of Traditional Raw Materials by Civil Construction Waste (CCW).” Journal of Cleaner Production 276: 123302. doi:https://doi.org/10.1016/j.jclepro.2020.123302.
- de Souza, D., C. Gonçalves, N. L. Dias de Souza, M. T. Gomes Barbosa, R. Stephani, and L. F. Cappa de Oliveira. 2019. “Investigation the Sustainable Additive Influence, Obtained from Milk Protein, in the Chemical and Physical Properties of Portland Cement.” Composites Part B: Engineering 175: 107148. doi:https://doi.org/10.1016/j.compositesb.2019.107148.
- Izarra, I., J. Cubillo, A. Serrano, J. F. Rodriguez, and M. Carmona. 2019. “A Hydrophobic Release Agent Containing SiO2-CH3 Submicron-sized Particles for Waterproofing Mortar Structures.” Construction and Building Materials 199: 30–39. doi:https://doi.org/10.1016/j.conbuildmat.2018.12.018.
- Kabirifar, K., M. Mojtahedi, C. Wang, and V. W. Y. Tam. 2020. “Construction and Demolition Waste Management Contributing Factors Coupled with Reduce, Reuse, and Recycle Strategies for Effective Waste Management: A Review.” Journal of Cleaner Production 263: 121265. doi:https://doi.org/10.1016/j.jclepro.2020.121265.
- Kirkpatrick, R. J., J. L. Yarger, P. F. McMillan, Y. Ping, and X. Cong. 1997. “Raman Spectroscopy of C-S-H, Tobermorite, and Jennite.” Advanced Cement Based Materials 5 (3): 93–99. doi:https://doi.org/10.1016/S1065-7355(97)00001-1.
- Kontoleontos, F., P. E. Tsakiridis, A. Marinos, V. Kaloidas, and M. Katsioti. 2012. “Influence of Colloidal Nanosilica on Ultrafine Cement Hydration: Physicochemical and Microstructural Characterization.” Construction and Building Materials 35: 347–360. doi:https://doi.org/10.1016/j.conbuildmat.2012.04.022.
- León-Martínez, F. M., E. F. Abad-Zarate, L. Lagunez-Rivera, and P. F. D. J. Cano-Barrita. 2016. “Laboratory and Field Performance of Biodegradable Release Agents for Hydraulic Concrete.” Materials and Structures 49 (7): 2731–2748. doi:https://doi.org/10.1617/s11527-015-0681-8.
- Li, H., H.-G. Xiao, J. Yuan, and J. Ou. 2004. “Microstructure of Cement Mortar with Nano-particles.” Composites Part B: Engineering 35 (2): 185–189. doi:https://doi.org/10.1016/S1359-8368(03)00052-0.
- Martinez-Ramirez, S., M. Frías, and C. Domingo. 2006. “Micro-Raman Spectroscopy in White Portland Cement Hydration: Long-term Study at Room Temperature.” Journal of Raman Spectroscopy 37 (5): 555–561. doi:https://doi.org/10.1002/jrs.1428.
- Mo, K. H., B. S. Thomas, S. P. Yap, F. Abutaha, and C. G. Tan. 2020. “Viability of Agricultural Wastes as Substitute of Natural Aggregate in Concrete: A Review on the Durability-related Properties.” Journal of Cleaner Production 275: 123062. doi:https://doi.org/10.1016/j.jclepro.2020.123062.
- Oliveira, L. A., S. Burattino Melhado, and F. Vittorino. 2015. “Selection of Building Technology Based on Sustainability Requirements – Brazilian Context.” Architectural Engineering and Design Management 11 (5): 390–404. doi:https://doi.org/10.1080/17452007.2014.942249.
- Omil, F., J. M. Garrido, B. Arrojo, and R. Méndez. 2003. “Anaerobic Filter Reactor Performance for the Treatment of Complex Dairy Wastewater at Industrial Scale.” Water Research 37 (17): 4099–4108. doi:https://doi.org/10.1016/S0043-1354(03)00346-4.
- Panesar, D. K. 2013. “Cellular Concrete Properties and the Effect of Synthetic and Protein Foaming Agents.” Construction and Building Materials 44: 575–584. doi:https://doi.org/10.1016/j.conbuildmat.2013.03.024.
- Prasara-A, J., and S. H. Gheewala. 2017. “Sustainable Utilization of Rice Husk Ash from Power Plants: A Review.” Journal of Cleaner Production 167: 1020–1028. doi:https://doi.org/10.1016/j.jclepro.2016.11.042.
- Projeções do Agronegócio: Brasil 2018/19 a 2028/29 projeções de longo prazo. 2019. Ministério Da Agricultura. Pecuária e Abastecimento 10th ed, MAPA, Brazil.
- Remadnia, A., R. M. Dheilly, B. Laidoudi, and M. Quéneudec. 2009. “Use of Animal Proteins as Foaming Agent in Cementitious Concrete Composites Manufactured with Recycled PET Aggregates.” Construction and Building Materials 23 (10): 3118–3123. doi:https://doi.org/10.1016/j.conbuildmat.2009.06.027.
- Salmenperä, H., K. Pitkänen, P. Kautto, and L. Saikku. 2020. “Critical Factors for Enhancing the Circular Economy in Waste Management.” Journal of Cleaner Production 124339. doi:https://doi.org/10.1016/j.jclepro.2020.124339.
- Shah Mohammadi, M., M. Ghani, M. Komeili, B. Crawford, and A. S. Milani. 2017. “The Effect of Manufacturing Parameters on the Surface Roughness of Glass Fibre Reinforced Polymer Moulds.” Composites Part B: Engineering 125: 39–48. doi:https://doi.org/10.1016/j.compositesb.2017.05.028.
- Silva, R. R., E. Q. Siqueira, and I. S. Nogueira. 2018. “Impactos Ambientais De Efluentes De Laticínios Em Curso D Água Na Bacia Do Rio Pomba.” Engenharia Sanitaria E Ambiental 23 (2): 217–228. doi:https://doi.org/10.1590/s1413-41522018138062.
- Soares Filho, J. E., J. C. Aurich, F. J. P. Sousa, R. M. Nascimento, C. A. Paskocimas, and A. H. A. Silva. 2020. “Polishing Performance of Eco-friendly Porcelain Stoneware Tiles Reusing Bricks and Roof Tiles Wastes.” Journal of Cleaner Production 256: 120362. doi:https://doi.org/10.1016/j.jclepro.2020.120362.
- Tayeh, B. A., M. W. Hasaniyah, A. M. Zeyad, and M. O. Yusuf. 2019. “Properties of Concrete Containing Recycled Seashells as Cement Partial Replacement: A Review.” Journal of Cleaner Production 237: 117723. doi:https://doi.org/10.1016/j.jclepro.2019.117723.
- Wesołowska, M., and A. Kaczmarek. 2016. “The Effect of Modifications on Humidity Parameters of Cement Mortar.” Journal of Materials Science 865: 178–182. www.scientific.net/MSF.865.178.
- Zhang, F., C. Chen, R. Hou, J. Li, Y. Cao, S. Dong, … J. Pan. 2019. “Investigation and Application of Mussel Adhesive Protein Nanocomposite Film-forming Inhibitor for Reinforced Concrete Engineering.” Corrosion Science 153: 333–340. doi:https://doi.org/10.1016/j.corsci.2019.03.023.
- Zhang, W., Q. Zheng, A. Ashour, and B. Han. 2020. “Self-healing Cement Concrete Composites for Resilient Infrastructures: A Review.” Composites Part B: Engineering 189: 107892. doi:https://doi.org/10.1016/j.compositesb.2020.107892.