ABSTRACT
Proper assessments of the role of various natural fibres in green composites are very significant to predict their behaviour in different conditions leading to optimise the use of green composites in more functional green products. This work has systematically investigated the effect of various lignocellulosic fibre types, fibre contents, and fibre intrinsic mechanical characteristics on the energy absorption capability and the corresponding rupture stress behaviour of low-density polyethylene-based composites. This was carried out to reveal more reliable behaviour trends during the impact process. The intrinsic mechanical properties of Mediterranean lemon, olive, and fig leaf fibres were considered including the tensile strength, density, modulus of elasticity, elongation to break, and the interfacial shear between the fibre and the matrix. The roles of the individual intrinsic mechanical properties of fibres were illustrated while comparing their effects at both energy absorptions and impact rupture stresses of the composites at various fibre loading. Results have revealed that olive fibres was capable of enhancing the energy absorbed as well as the impact ruptures stress. The elongation to break property was also found among the critical intrinsic mechanical characteristics in enhancing the energy absorption during impact. Non-linear trends were revealed for both the energy absorption and impact rupture stress of the green composites.
1. Introduction
Green composites have emerged as a potential eco-friendly and cost-effective option to synthetic fibre reinforced composite materials. The increasing attention and awareness of societies towards the environment have raised the demand of long-term sustainable applications substantially, and developing better techniques and methods for optimal exploitation of the available natural resources (Sanjay et al. Citation2018; Dayo et al. Citation2020; AL‐Oqla Citation2021; Thakur and Thakur Citation2014; Sapuan et al. Citation2013; Sapuan and Mujtaba Citation2009). Many industries were pushed towards using composites from natural resources to replace the conventional composites already used in their designs. This interest was developed due to the numerous attractive properties of such composites including massive availability, low cost, low density, high specific properties, biodegradability, and renewability (Gholampour and Ozbakkaloglu Citation2020; Robledo-Ortíz et al. Citation2020; Das, Chaudhary, and Mishra Citation2021; AL-Oqla and Sapuan Citation2020; AL-Oqla and Hayajneh Citation2020). As a result, green fibre reinforced polymeric composites are now involved in wide varieties of applications such as packaging, electronic devices, mobile phones, laptops, toys, medical applications, etc. As per the trend of many research centres worldwide, lignocellulosic materials are increasingly used as fillers in polymer composites. They are completely safe during preparation, production, and recycling. Their properties can be adjusted to meet the required needs (Das, Chaudhary, and Mishra Citation2021; Zuccarello, Militello, and Bongiorno Citation2021; Mahesh, Joladarashi, and Kulkarni Citation2021; AL-Oqla Citation2020a, Citation2020b; AL-Oqla and Salit Citation2017a). However, the production of such composites with excellent properties (on the macroscopic level) is challenging and is not a simple task. One of these challenges is the insufficient adhesion between the lignocellulosic fillers and the polymer matrix. A solution to this issue may be found using physical or chemical modifications of the composite constituents (Di Mauro et al. Citation2021; Ilyas et al. Citation2019; Fares, AL-Oqla, and Hayajneh Citation2019; El-Shekeil, AL-Oqla, and Sapuan Citation2020; AL-Oqla, Sapuan, and Fares Citation2018).
Therefore, developing proper evaluations and assessments of the role of various natural fibres in green composites is very important to predict their behaviour in different conditions, leading to optimise the use of green composites in more functional green products based on their overall reliable characteristics (AL-Oqla et al. Citation2015a, Citation2014a, Citation2014b). However, green bio-composites have limited applications in sustainable products due to the lack of proper reliable databases capable of assessing their mechanical performance for establishing more integrated sustainable industrial manufacturing systems (AL-Oqla, Hayajneh, and Fares Citation2019; AL-Oqla and El-Shekeil Citation2019; Alaaeddin et al. Citation2019a, Citation2019b; AL-Oqla and Sapuan Citation2018; AL-Oqla and Salit Citation2017b).
On the other hand, investigating the impact behaviour of green composites is more realistic simulation of the crash environment and conditions as it takes into account the stress rate sensitivity of such green materials (AL-Oqla Citation2020b; Jacob et al. Citation2002, Citation2005). It was noted that only little systematic studies had been reported in the literature regarding the effects of the green fibre content and their intrinsic mechanical properties in polymeric matrices on the energy absorption behaviour of composites (Mahesh, Joladarashi, and Kulkarni Citation2021; AL-Oqla Citation2020b; Supian et al. Citation2018; Anyakora Citation2013; Sari et al. Citation2020; Sun et al. Citation2009; Monteiro et al. Citation2019; Luo et al. Citation2021; Mache, Deb, and Gupta Citation2020). It was also noted that an increase in the green fibre content might not always be necessary to improve the energy absorbed during impact (Jacob et al. Citation2002; Sun et al. Citation2009; Monteiro et al. Citation2019; Luo et al. Citation2021; Alkbir et al. Citation2014, Citation2016). This is due to the fact that as the fibre content increases, the volume of the matrix between the fibres decreases, resulting in reducing the interfacial strength of the composite. Moreover, different green fibre types have different intrinsic mechanical characteristics that make the interfacial bonding of such green fibres with the polymeric matrix dramatically change. This resulted in various energy absorption capability trends of such green composites during impact (Živković et al. Citation2017; Liu et al. Citation2017; San Ha and Lu Citation2020). The strain energy-absorbing capabilities of the fibres as well as the geometrical configuration of the green composites are also important to the impact resistance of green composites due to the constituents debonding and fibres pull outs (Sarikaya, Çallioğlu, and Demirel Citation2019). Therefore, it is essential for the bio-composites to possess high levels of impact strength for certain applications. However, bio-composites are usually not as likely according to various design criteria concerning the impact behaviour. Moreover, lignocellulosic fibres may negatively affect the polymer capability of absorbing energy during impact as they may enhance internal gaps and inclusions inside the matrix. Hence, bio-composites usually suffer from their resistance to the impact loads, and composites with higher impact resistance are more desired for several applications (AL-Oqla et al. Citation2016a).
Accordingly, the aim of this work was to systematically investigate the effect of various lignocellulosic fibre types, fibre contents, and fibres intrinsic mechanical characteristics on the absorption capability and their corresponding rupture stress behaviour of low-density polyethylene-based matrix to reveal more reliable behaviour trends of such various composites during the impact process. This in order would enhance developing more reliable light weight bio-products for crash resistance applications like that of automotive industry, safety equipment and green armour design.
2. Materials and methods
Low-density polyethylene was provided from Saudi Arabian multinational chemical manufacturing company (SABIC®). Its density was 919 kg/m3. Its properties according to ISO 527–2 standard were as: stress at break 7 MPa, tensile modulus 165 MPa, strain at break 150%, and stress at yield 8 MPa. All of lemon leaf fibres, fig leaf fibres and olive leaf fibres were collected from Jordan, Amman city. Fibres were tested for their mechanical properties and densities. Densities of the considered fibres were determined according to ASTM D 1895 standard. Mechanical tensile strength, tensile modulus and elongating to break (%) were also determined according to the ASTM D 3822–01 standard and tabulated in . Fibres of each type were then cleaned with distilled water and air dried for 24 h. They were then cut into length of 3–5 mm and mixed with polyethylene in a double screw hot mixture with different fibre loadings of 10 wt.%, 20 wt.%, 30 wt.% and 40 wt.% for each fibre type. The fibres were utilised without any chemical treatment. The output mixtures were then utilised to make plates of composites under hot press machine, and then cut to prepare the impact test samples for each fibre/PE composites. The utilised fibre types, samples of the produced composites as well as prepared samples for investigations are demonstrated in .
Table 1. Characteristics of the utilised natural fibre
The impact test measures the applied work on the tested specimen, which in turn accumulates the energy until it fractures; if the composite absorbs a slight amount of energy, and then it is considered brittle, while the ductile composite absorbs a significant amount of energy before fracturing. The materials maximum rupture stress while impact loading is being applied can demonstrate the green composite suitability for various applications when it is employed in conditions with sudden impact like that of automotive applications. Charpy standard test was utilised to investigate the energy in (J) absorbed by the composites as well as the rupture stress at failure. The specimens were prepared as (50x20x3) mm. Specimens were tested according to ASTM D 256. The pendulum arm swing, initiates a plastic deformation of the plastic zone around the hit. The amount of work required to create a fracture equals the amount of cohesive energy that has to be conquered to separate the reinforcement and the matrix on both sides. On contrary, while the brittle materials endure lower plastic deformation before and during the fracture, which means small impact energy is needed for breaking of the bonds; the ductile materials endure higher plastic deformation, and a high amount of energy is required to break the bonds.
3. Results and discussions
The impact test indicates the applied work on the tested specimen that accumulates as energy absorbed by the materials until its fracture. On the other hand, investigating the impact behaviour of green composites is more accurate to illustrate their crash resistance behaviours in a more representative environment and conditions taking into account the stress rate sensitivity of such green materials. demonstrates the amount of energy absorbed in joules of low-density polyethylene/lemon fibres comparable to the neat polymer matrix. It can be seen that the amount of energy absorbed in such type of composites enhanced by increasing lemon fibre content. It is obvious that reinforcing the low-density polyethylene with only 10 wt. % has dramatically reduced the polymer matrix impact resistance of about 37% of the original matrix capability of energy absorption. However, reinforcing the polymer with more lemon fibres was capable of enhancing the composite energy absorption gradually until reached its maximum at 40 wt.% fibre content due to the better stress transfer between the polymer and the matrix in one hand, and the more energy required to pull out more fibres from the matrix on the other. Moreover, the intrinsic mechanical properties of lemon were reasonable to enhance the energy absorption of the composites as its tensile strength and tensile modulus were 3.9 MPa and 0.201 GPa respectively, and the shear strengths between the lemon fibre and the LDPE was 3.3 MPa (AL-Oqla, Hayajneh, and Fares Citation2019) (). Thus, more interfacial strength was achieved with fibre loading that makes an enhancement of the amount of energy absorption of the green composites. This was with agreement with the literature as different green fibres and their mechanical characteristics would affect the stress transfer with the polymeric matrix and can dramatically change the energy absorption capability trends of such green composites during impact (Živković et al. Citation2017; Liu et al. Citation2017; San Ha and Lu Citation2020). The regression trend of such energy absorption enhancement with fibre content was developed as illustrated in to demonstrate the trend in the absorbed energy enhancement of PE/lemon fibres. The parabolic trend was capable of explaining more that 94% of the composites and indicating that the enhancement of lemon fibres for the polyethylene matrix energy absorption was a nonlinear trend manner. Such investigations have to be performed to reveal the effect of particular fibre content on the green composite impact resistance.
Moreover, the rupture stress of low-density polyethylene/lemon fibre composites with fibre content is illustrated in . The materials maximum rupture stress while impact loading is being applied can demonstrate the green composite suitability for various applications. It can be demonstrated that reinforcing the polyethylene with 10 wt. % lemon fibres would reduce the rupture stress in the composite comparable with the matrix itself. This is due to the fact that such low fibre content has increased the stress concentrations inside the matrix resulted in reducing the maximum rupture stress under impact conditions (AL-Oqla and El-Shekeil Citation2019; AL-Oqla and Sapuan Citation2018). However, enhancing the matrix with more lemon fibre content was not capable of developing the maximum rupture stress of the composites as the intrinsic mechanical properties of the lemon fibres (tensile strength and tensile modulus for lemon fibres were 3.9 MPa and 0.201 GPa respectively as mentioned in ) were not capable of enhancing the rupture stress of the composites despite higher fibre content were utilised. Also, the nonlinear trend of enhancing the rupture stress on the lemon/PE composites was capable of explaining about 80% of the studies composites. That is, the interfacial strength of the composite strongly depends on the intrinsic mechanical characteristics of the green fibres and the stress transfer efficiency strongly depends on this interfacial bonding. This demonstrates why increasing fibre contents have led to enhancing the rupture stress during impact conditions (stress increased with fibre content) however, they were not better than that of the original matrix.
On the other hand, the energy absorption of the fig /PE composites with fibre contents is illustrated in . It was noticed that not all fibre contents were capable of enhancing the amount of energy absorbed during impact for the fig/PE composites. Also, the energy absorption was not increased with fibre contents as the trend seen in case of lemon/PE composites. It is demonstrated here that the 30 wt.% fig reinforcement case was the best in enhancing the composite energy absorption in impact, while the case of 40 wt.% was the worst. This is due to the fact that the intrinsic mechanical properties of the fig fibre were much lower than that of lemon, and the interfacial shear strength of fig/PE was only 1.8 MPa comparable to 3.3 MPa for the lemon/PE (). This in order have made the increase in fig fibre loading to 40 wt. % a cause to reduce the interfacial bonding between fibres and the polymer; leading to reduce the amount of energy absorbed by the composite. That is, as the fibre content increases, the volume of the matrix between the fibres decreases resulting in decreasing the interfacial strength of the composite (AL-Oqla and Sapuan Citation2018; AL-Oqla, Sapuan, and Jawaid Citation2016b; El-Shekeil et al. Citation2014). The regression trend of such energy absorption behaviour with fibre content was also developed to demonstrate the trend of the energy enhancement of fig fibre/PE composites. The nonlinear cubic trend was capable of explaining more that 93% of the composites indicating that the strain energy absorbing capabilities of the fibres as well as the geometrical configuration of the green composites are also important to the impact resistance of green composites (AL-Oqla Citation2020b; AL-Oqla et al. Citation2014b; Sarikaya, Çallioğlu, and Demirel Citation2019; AL-Oqla Citation2021; Sapuan, Haniffah, and AL-Oqla Citation2016). This obviously demonstrates the importance of various fibre intrinsic mechanical properties on the green composite impact resistance.
The effect of fibre content on the rupture stress of fig/PE composites is furthermore demonstrated in . It can be revealed that no linear relation occurred between the fibre content and the rupture stresses of fig/PE composites. On the contrary, fibre loading may enhance the rupture stress in some cases but destroy it in others. That is; the impact rupture stresses of the composites were reduced after 10 wt.%, then enhanced to the best value at 30 wt.% then reduced again in case of 40 wt.% fibre content. However, all cases the impact rupture stress were lower than that of the original matrix one. This trend of rupture stress was different from that observed in case of lemon fibres (in lemon, increased after 10 wt.% fibre content , but in fig was fluctuated) as fig fibres have lower mechanical intrinsic characteristics than lemon as mentioned in . The lower mechanical tensile strength and modulus of fig fibres have made the reinforcement efficiency lower than that of lemon cases. That is; for fig, the stress has been reduced in case of 20 wt.% fibre loading than that of 10 wt.% due to the higher stress concentrations inside the matrix as the fibre loading was not capable of enhancing the rapture stress inside the composite due to the lower intrinsic mechanical characteristics of the fig fibre. However, increasing the fibre content to 30 wt.% enhanced the impact stress rupture as this particular fibre content has increased the stress transfer efficiency inside the matrix and compensated the low mechanical characteristics of fig fibre (Sapuan et al. Citation2013; AL-Oqla Citation2020a; Shah et al. Citation2014; Sorrentino et al. Citation2015). Further increasing of fibre content to 40 wt.% however had decreased the impact rupture stress as no proper interfacial bonding with polymer occurred and thus, more stress concentrations were occurred. That is, as the fibre content increases, the volume of the matrix between the fibres decreases resulting in decreasing the interfacial strength of the composite, leading to lower stress transfer efficiency inside the composite. Also, a nonlinear cubic behaviour trend was capable of explaining more than 90% of the considered composites, revealing the importance of the intrinsic mechanical characteristics in enhancing the rupture stress of the green composites.
Moreover, the effect of olive fibres in reinforcing the polyethylene matrix was almost different from that of both fig and lemon fibres. The energy absorption of the olive/PE composites with fibre contents is illustrated in . It can be clearly noticed that the effect of fibre loading on enhancing the amount of energy absorbed during impact was much better than other fibre types as it was increased from 10 wt.% to 30 wt.% and all values were more than that of the original matrix polymer. The energy absorbed at 30 wt.% fibre content case was enhanced about 75% than that of the polymer matrix. This enhancement in energy absorption was mainly due to the intrinsic mechanical properties of olive fibres, as its tensile strength, modulus and shear strength with PE matrix were reasonably high in one hand, and the elongation to break was also high, which enables the matrix to behave as freely as possible as a ductile material on the other (AL-Oqla Citation2020b; Alkbir et al. Citation2014; AL-Oqla Citation2021, Citation2017). That is, the high relative ductility of the olive fibres was capable of limiting the brittleness of the composite (not dramatically changing the behaviour of the matrix to be a brittle one), leading to better energy absorption during impact due to the higher ductility. That is, the intrinsic mechanical characteristics of olives (the higher ductility, high tensile strength and high relative interfacial shearing with polymer) had enhanced the olive capability to develop better energy absorption of the matrix. On the other hand, increasing the fibre loading to 40 wt.% have reduced the interfacial bonding inside the composites due to the lower volume of polymer between the fibres. Also a nonlinear trend has been revealed to explain more than 97% of the considered composites. It was shown that a nonlinear behaviour trend of enhancing the energy absorption was occurred because olive fibre has better strain than that of lemon and fig types with reasonable mechanical properties, so that the behaviour of the composite has demonstrated more ductility that enabled better energy absorption during impact comparable to the other fibre-based composites.
Furthermore, the rupture stress behaviour of olive/PE composites is shown in . It can be demonstrated that the rupture stress was not similar to the energy absorbed behaviour. Here, some fibre loading cases have destroyed the rupture stress like that of 10 wt.% and 40 wt.%, due to the low modulus of elasticity of olive fibre, while the case of 30 wt.% had improved the rupture stress of about 41% comparable to the polymer matrix. That is the 30 wt.% fibre case was the best due the good interfacial shearing stress with the polyethylene (see ) and required enough fibre content to compensate the relative low modulus of elasticity to enhance the rupture stress. That is as more fibre content to 30 wt.% have increased, better interfacial bonding between the fibres and the polymer has been occurred, leading to improve the stress transfer efficiency inside the matrix. However, as fibres were extra loaded inside the matrix to 40 wt.%, less volume of polymer was found in contact with the fibres, resulting in lower interfacial bonding and more stress concentrations, which have reduced the rupture stress of the composite.
Besides, the role of the individual intrinsic mechanical properties of the lignocellulosic fibres can be illustrated while comparing their effects at both energy absorptions and impact rupture stresses of the PE/fibres at every fibre loading as demonstrated in and respectively. It can be noticed that olive fibre was the best in enhancing the polyethylene-based composite energy absorptions during impact for almost all fibre loadings except that of 40 wt.% case, which was in favour of lemon fibre. This demonstrates that olive fibre, which has reasonable mechanical characteristics as well as good interfacial bonding with the polyethylene matrix, had developed the amount of energy absorbed during the impact conditions. However, the lemon fibre type was capable of enhancing the energy absorption of the composites as fibre loading enhanced due to the best interfacial bonding with the PE matrix (El-Shekeil, AL-Oqla, and Sapuan Citation2020; El-Sabbagh Citation2014). But the enhancement of lemon was lower than that of olive due to its much lower ductility comparable to olive fibre. Moreover, fig fibre was capable of enhancing the energy absorption of the composites more than what lemon did for all of 10 wt.%, 20 wt.% and 30 wt.% due to its better strain to brake property comparable to lemon fibres. However, its interfacial bonding with the matrix as well as its intrinsic mechanical properties were much lower than that of olives and thus, its enhancement for the energy absorbed was much lower than that of olive.
Figure 8. Comparison for the energy absorption of different fibrebased composites with various fibre contents
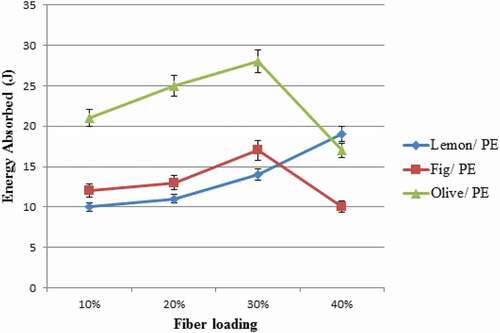
Figure 9. Comparison of impact rupture stress of different fibre-based composites with various fibre contents
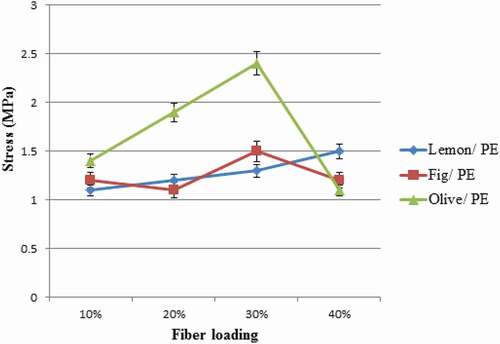
The sharp drop of energy absorbed for both of olive/PE and fig/PE bio-composites at 40 wt.% fibre content comparable to the lemon/ PE ones in is justified based on the mechanical intrinsic properties of the fibres. That is, enhancing the matrix with more lemon fibre content was capable of developing more energy absorption in the composite as the intrinsic mechanical properties of the lemon fibres (tensile strength and interfacial shear strength with LDPE were 3.9 MPa and 3.3MPa respectively as mentioned in ) they were better than those of both olives (3.4 MPa and 2.4 MPa) and Fig (1.2 MPa and 1.8MPa) thus, sharp drop of energy absorbed was found for both olive/PE and fig/PE bio-composites when fibre content was increased, but it was enhanced for the lemon/PE composite case. This demonstrates that both olive and fig fibres, which have reasonable mechanical characteristics as well as good interfacial bonding with the polyethylene matrix, had developed some amount of energy absorption during the impact conditions. However, lemon fibre type was capable of dramatically enhancing the energy absorption of the composites as fibre loading enhanced due to the best interfacial bonding with the PE matrix among other fibres as seen in .
In addition, the effect of the intrinsic natural fibre mechanical properties on the impact rupture stress can be revealed to be in favour of olive fibre except the case of 40 wt.% fibre content. That is, the stress transfer that was developed inside the olive based composites for all of 10 wt.%, 20 wt.% and 30 wt.% were better than that of other fibre types. This is due the fact that olive fibre has reasonable mechanical properties as well as desired elongation to break property that did not limit the ductility behaviour of the composites. However, lemon fibre-based composites was not capable of enhancing the impact rupture stress comparable to the matrix as its intrinsic elongation to break was much lower than that of olive fibre type (AL‐Oqla Citation2021; AL-Oqla et al. Citation2014a, Citation2015b, Citation2015c; Bhatti et al. Citation2020). But, its good tensile strength and tensile modulus have made the trend of enhancing the impact rupture stress with fibre content steadily. Fig fibres on the other hand were neither capable of enhancing the impact rupture stress better than the matrix, nor steadily enhanced that with fibre content. This was due to its lower tensile strength and modulus, in one hand, and its lower interfacial bonding with the matrix on the other. But because of its relative higher elongation to break property comparable to lemon, and its lower density have made it reasonable to enhance the impact rupture stress at 30 wt.% case more than lemon fibre did. That is, its better elongation to break had made its composites less brittleness and its lower density have made more fibres inside the polymer comparable to lemon fibres that made some more reasonable interfacial bonding comparable to lemon, resulting in enhancing the impact rupture stress.
4 Conclusions
The impact behaviour of low-density polyethylene/green fibre was revealed considering the effect of several lignocellulosic fibres types, contents, and intrinsic mechanical characteristics. Both energy absorption capability and corresponding rupture stress behaviour were discussed considering the intrinsic mechanical characteristics of Jordanian lignocellulosic fibres. Reliable behaviour trends of such various composites during the impact process were developed. The intrinsic natural fibre mechanical properties effects on the impact rupture stress were revealed to be in favour of olive fibre. Olive/PE composites have shown better stress transfer for all of 10 wt.%, 20 wt.% and 30 wt.% cases rather than lemon and fig-based composites. Olive fibre was found to have reasonable mechanical properties as well as desired elongation to break property that did not limit the ductility behaviour of the composites. However, lemon fibre-based composites was not able to enhance the impact rupture stress comparable to the matrix as its intrinsic elongation to break was much lower than that of olive fibre type. A nonlinear trend for the enhancement of energy absorption with fibre content in case of olive fibre-based composites was revealed to explain more than 97% of the considered composites. Both the interfacial shearing strength of the PE/ lignocellulosic fibres and their elongation to break intrinsic properties were found to be of paramount importance characteristics for the green composites to enhance their desired impact behaviour. This in order would enhance developing more reliable light weight bio-products for crash resistance applications like that of automotive industry, safety equipment and green armour design.
Disclosure statement
No potential conflict of interest was reported by the author(s).
Additional information
Notes on contributors
Faris M. AL-Oqla
Dr. Faris M. AL-Oqla, Associate Professor of Mechanical Engineering in the Mechanical Engineering Department at The Hashemite University (HU), Jordan. He has been involved in dozens of research projects funded by various institutions and his research has been recognized worldwide especially in the area of bio-composites, biomaterials, Nano and sustainable materials. Dr. AL-Oqla has been listed in the World's Top 2% Scientists published by Stanford University, Elsevier and SciTech Strategies, 2020. Dr. AL-Oqla contribution to his research field is revealed by his publications. To date he has authored more than 100 publications including 25 chapters in book, an authored book published in Elsevier 2017, and one edited book in Elsevier 2020. Dr. AL-Oqla has established novel tools, techniques and methodologies to evaluate biomaterials (including Moisture Content Criterion (MCC), Combined Multi-criteria Evaluation Stage Technique, as well as others) that can be implemented in natural fiber composite selection to expand the sustainable design possibilities, as well as supporting the cleaner production needs for the near future.
References
- Alaaeddin, M., S. Sapuan, M. Zuhri, E. Zainudin, and F. M. AL-Oqla. 2019a. “Development of Photovoltaic Module with Fabricated and Evaluated Novel Backsheet-Based Biocomposite Materials.” Materials 12: 3007. doi:https://doi.org/10.3390/ma12183007.
- Alaaeddin, M., S. Sapuan, M. Zuhri, E. Zainudin, and F. M. AL-Oqla. 2019b. “Lightweight and Durable PVDF–SSPF Composites for Photovoltaics Backsheet Applications: Thermal, Optical and Technical Properties.” Materials 12: 2104. doi:https://doi.org/10.3390/ma12132104.
- Alkbir, M., S. Sapuan, A. Nuraini, and M. Ishak. 2014. “Effect of Geometry on Crashworthiness Parameters of Natural Kenaf Fibre Reinforced Composite Hexagonal Tubes.” Materials & Design 60: 85–93. doi:https://doi.org/10.1016/j.matdes.2014.02.031.
- Alkbir, M. F. A., M. R. Ishak, N. B. A. Aziz, and M. R. Ishak. 2016. “Lateral Crushing Properties of Non-woven Kenaf (Mat)-reinforced Epoxy Composite Hexagonal Tubes.” International Journal of Precision Engineering and Manufacturing 17: 965–972. doi:https://doi.org/10.1007/s12541-016-0118-5.
- AL-Oqla, F. M. 2017. “Investigating the Mechanical Performance Deterioration of Mediterranean Cellulosic Cypress and Pine/polyethylene Composites.” Cellulose 24: 2523–2530. doi:https://doi.org/10.1007/s10570-017-1280-3.
- AL-Oqla, F. M. 2020a. Evaluation and Comparison of Date Palm Fibers with Other Common Natural Fibers, Date Palm Fiber Composites, 267–286. Singapore: Springer.
- AL-Oqla, F. M. 2020b. “Flexural Characteristics and Impact Rupture Stress Investigations of Sustainable Green Olive Leaves Bio-composite Materials.” Journal of Polymers and the Environment 29 (3): 892–899.
- AL-Oqla, F. M. 2021. “Performance Trends and Deteriorations of Lignocellulosic Grape Fiber/polyethylene Biocomposites under Harsh Environment for Enhanced Sustainable Bio-materials.” Cellulose 28 (4): 2203–2213.
- AL‐Oqla, F. M. 2021. “Introduction to Biobased Composites.” Biobased Composites: Processing, Characterization, Properties, and Applications, 1–11. New Jersey, USA: Wiley.
- AL-Oqla, F. M., and M. S. Salit. 2017a. Material Selection of Natural Fiber Composites Using the Analytical Hierarchy Process, Materials Selection for Natural Fiber Composites, 169–234. Elsevier Cambridge, USA: Woodhead Publishing.
- AL-Oqla, F. M., and M. S. Salit. 2017b. Material Selection of Natural Fiber Composites Using Other Methods, Materials Selection for Natural Fiber Composites, 235–272. Elsevier Cambridge, USA: Woodhead Publishing.
- AL-Oqla, F. M., M. S. Sapuan, M. R. Ishak, and A. A. Nuraini. 2015b. “Decision Making Model for Optimal Reinforcement Condition of Natural Fiber Composites.” Fibers and Polymers 16: 153–163. doi:https://doi.org/10.1007/s12221-015-0153-3.
- AL-Oqla, F. M., M. S. Sapuan, M. R. Ishak, and A. A. Nuraini. 2015c. “Selecting Natural Fibers for Bio-based Materials with Conflicting Criteria.” American Journal of Applied Sciences 12: 64–71. doi:https://doi.org/10.3844/ajassp.2015.64.71.
- AL-Oqla, F. M., M. S. Sapuan, M. R. Ishak, and N. A. Aziz. 2014a. “Combined Multi-criteria Evaluation Stage Technique as an Agro Waste Evaluation Indicator for Polymeric Composites: Date Palm Fibers as a Case Study.” BioResources 9: 4608–4621. doi:https://doi.org/10.15376/biores.9.3.4608-4621.
- AL-Oqla, F. M., and M. T. Hayajneh. 2020. “A Hierarchy Weighting Preferences Model to Optimise Green Composite Characteristics for Better Sustainable Bio-products.” International Journal of Sustainable Engineering 1–6. doi:https://doi.org/10.1080/19397038.2020.1822951.
- AL-Oqla, F. M., M. T. Hayajneh, and O. Fares. 2019. “Investigating the Mechanical Thermal and Polymer Interfacial Characteristics of Jordanian Lignocellulosic Fibers to Demonstrate Their Capabilities for Sustainable Green Materials.” Journal of Cleaner Production 241: 118256. doi:https://doi.org/10.1016/j.jclepro.2019.118256.
- AL-Oqla, F. M., O. Y. Alothman, M. Jawaid, S. Sapuan, and M. Es-Saheb. 2014b. Processing and Properties of Date Palm Fibers and Its Composites, Biomass Bioenergy, 1–25. Cham, Switzerland: Springer.
- AL-Oqla, F. M., and S. Sapuan. 2018. “Investigating the Inherent Characteristic/performance Deterioration Interactions of Natural Fibers in Bio-composites for Better Utilization of Resources.” Journal of Polymers and the Environment 26: 1290–1296. doi:https://doi.org/10.1007/s10924-017-1028-z.
- AL-Oqla, F. M., and S. Sapuan. 2020. Advanced Processing, Properties, and Applications of Starch and Other Bio-Based Polymers. Cambridge, USA: Elsevier.
- AL-Oqla, F. M., S. Sapuan, M. Ishak, and A. Nuraini. 2015a. “Predicting the Potential of Agro Waste Fibers for Sustainable Automotive Industry Using a Decision Making Model.” Computers and Electronics in Agriculture 113: 116–127. doi:https://doi.org/10.1016/j.compag.2015.01.011.
- AL-Oqla, F. M., S. Sapuan, and M. Jawaid. 2016b. “Integrated Mechanical-Economic–Environmental Quality of Performance for Natural Fibers for Polymeric-Based Composite Materials.” J. Nat. Fibers 13: 651–659.
- AL-Oqla, F. M., S. Sapuan, M. R. Ishak, and A. Nuraini. 2016a. “A Decision-making Model for Selecting the Most Appropriate Natural fiber–Polypropylene-based Composites for Automotive Applications.” Journal of Composite Materials 50: 543–556. doi:https://doi.org/10.1177/0021998315577233.
- AL-Oqla, F. M., S. Sapuan, and O. Fares. 2018. Electrical–Based Applications of Natural Fiber Vinyl Polymer Composites, Natural Fibre Reinforced Vinyl Ester and Vinyl Polymer Composites, 349–367. Cambridge, USA: Elsevier.
- AL-Oqla, F. M., and Y. El-Shekeil. 2019. “Investigating and Predicting the Performance Deteriorations and Trends of Polyurethane Bio-composites for More Realistic Sustainable Design Possibilities.” Journal of Cleaner Production 222: 865–870. doi:https://doi.org/10.1016/j.jclepro.2019.03.042.
- Anyakora, A. N. 2013. “Investigation of Impact Strength Properties of Oil and Date Palm Frond Fiber Reinforced Polyester Composites.” International Journal of Current Engineering and Technology 3: 493–497.
- Bhatti, H. N., Z. Mahmood, A. Kausar, S. M. Yakout, O. H. Shair, and M. Iqbal. 2020. “Biocomposites of Polypyrrole, Polyaniline and Sodium Alginate with Cellulosic Biomass: Adsorption-desorption, Kinetics and Thermodynamic Studies for the Removal of 2, 4-dichlorophenol.” International Journal of Biological Macromolecules 153: 146–157. doi:https://doi.org/10.1016/j.ijbiomac.2020.02.306.
- Das, P. P., V. Chaudhary, and S. Mishra. 2021. Emerging Trends in Green Polymer Based Composite Materials: Properties, Fabrication and Applications, Graphene Based Biopolymer Nanocomposites, 1–24. Singapore: Springer.
- Dayo, A. Q., A. A. Babar, Q. R. Qin, S. Kiran, J. Wang, A. H. Shah, A. Zegaoui, H. A. Ghouti, and W. B. Liu. 2020. “Effects of Accelerated Weathering on the Mechanical Properties of Hemp Fibre/polybenzoxazine Based Green Composites.” Composites Part A: Applied Science and Manufacturing 128: 105653. doi:https://doi.org/10.1016/j.compositesa.2019.105653.
- Di Mauro, C., A. Genua, M. Rymarczyk, C. Dobbels, S. Malburet, A. Graillot, and A. Mija. 2021. “Chemical and Mechanical Reprocessed Resins and Bio-composites Based on Five Epoxidized Vegetable Oils Thermosets Reinforced with Flax Fibers or PLA Woven.” Composites Science and Technology 205: 108678. doi:https://doi.org/10.1016/j.compscitech.2021.108678.
- El-Sabbagh, A. 2014. “Effect of Coupling Agent on Natural Fibre in Natural Fibre/polypropylene Composites on Mechanical and Thermal Behaviour.” Composites Part B: Engineering 57: 126–135. doi:https://doi.org/10.1016/j.compositesb.2013.09.047.
- El-Shekeil, Y., F. AL-Oqla, and S. Sapuan. 2020. “Performance Tendency and Morphological Investigations of Lignocellulosic Tea/polyurethane Bio-composite Materials.” Polymer Bulletin 77, 3907–3920. doi: https://doi.org/10.1007/s00289-019-02947-0
- El-Shekeil, Y., S. Sapuan, M. Jawaid, and O. M. Al-Shuja’a. 2014. “Influence of Fiber Content on Mechanical, Morphological and Thermal Properties of Kenaf Fibers Reinforced Poly (Vinyl Chloride)/thermoplastic Polyurethane Poly-blend Composites.” Materials & Design 58: 130–135. doi:https://doi.org/10.1016/j.matdes.2014.01.047.
- Fares, O., F. M. AL-Oqla, and M. T. Hayajneh. 2019. “Dielectric Relaxation of Mediterranean Lignocellulosic Fibers for Sustainable Functional Biomaterials.” Materials Chemistry and Physics 229: 174–182. doi:https://doi.org/10.1016/j.matchemphys.2019.02.095.
- Gholampour, A., and T. Ozbakkaloglu. 2020. “A Review of Natural Fiber Composites: Properties, Modification and Processing Techniques, Characterization, Applications.” Journal of Materials Science 55: 829–892.
- Ilyas, R. A., S. M. Sapuan, R. Ibrahim, H. Abral, M. Ishak, E. Zainudin, M. Asrofi, M. S. N. Atikah, M. R. M. Huzaifah, and A. M. Radzi. 2019. “Sugar Palm (Arenga Pinnata (Wurmb.) Merr) Cellulosic Fibre Hierarchy: A Comprehensive Approach from Macro to Nano Scale.” Journal of Materials Research and Technology 8 (3): 2753–2766. doi:https://doi.org/10.1016/j.jmrt.2019.04.011.
- Jacob, G. C., J. F. Fellers, S. Simunovic, and J. M. Starbuck. 2002. “Energy Absorption in Polymer Composites for Automotive Crashworthiness.” Journal of Composite Materials 36 (7): 813–850. doi:https://doi.org/10.1177/0021998302036007164.
- Jacob, G. C., J. M. Starbuck, J. F. Fellers, and S. Simunovic. 2005. “Effect of Fiber Volume Fraction, Fiber Length and Fiber Tow Size on the Energy Absorption of Chopped Carbon Fiber–polymer Composites.” Polymer Composites 26: 293–305. doi:https://doi.org/10.1002/pc.20100.
- Liu, T., S. Hou, X. Nguyen, and X. Han. 2017. “Energy Absorption Characteristics of Sandwich Structures with Composite Sheets and Bio Coconut Core.” Composites Part B: Engineering 114: 328–338. doi:https://doi.org/10.1016/j.compositesb.2017.01.035.
- Luo, H., D. Zhang, Z. He, X. Li, and Z. Li. 2021. “Experimental Investigation of the Quasi-static and Dynamic Axial Crushing Behavior of Carbon/glass Epoxy Hybrid Composite Tubes.” Materials Today Communications 26: 101941. doi:https://doi.org/10.1016/j.mtcomm.2020.101941.
- Mache, A., A. Deb, and N. Gupta. 2020. “An Experimental Study on Performance of Jute‐polyester Composite Tubes under Axial and Transverse Impact Loading.” Polymer Composites 41: 1796–1812. doi:https://doi.org/10.1002/pc.25498.
- Mahesh, V., S. Joladarashi, and S. M. Kulkarni. 2021. “Damage Mechanics and Energy Absorption Capabilities of Natural Fiber Reinforced Elastomeric Based Bio Composite for Sacrificial Structural Applications.” Defence Technology 17: 161–176. doi:https://doi.org/10.1016/j.dt.2020.02.013.
- Monteiro, S. N., J. W. Drelich, H. A. C. Lopera, L. F. C. Nascimento, F. S. da Luz, L. C. Da Silva, J. L. dos Santos, F. da Costa Garcia Filho, F. S. de Assis, and É. P. Lima. 2019. “Natural Fibers Reinforced Polymer Composites Applied in Ballistic Multilayered Armor for Personal Protection—an Overview.” Green Materials Engineering 33–47. Springer, Cham.
- Robledo-Ortíz, J. R., M. E. González-López, D. Rodrigue, J. F. Gutiérrez-Ruiz, F. Prezas-Lara, and A. A. Pérez-Fonseca. 2020. “Improving the Compatibility and Mechanical Properties of Natural Fibers/green Polyethylene Biocomposites Produced by Rotational Molding.” Journal of Polymers and the Environment 28: 1040–1049. doi:https://doi.org/10.1007/s10924-020-01667-1.
- San Ha, N., and G. Lu. 2020. “A Review of Recent Research on Bio-inspired Structures and Materials for Energy Absorption Applications.” Compo. Part B: Eng 181: 107496.
- Sanjay, M., P. Madhu, M. Jawaid, P. Senthamaraikannan, S. Senthil, and S. Pradeep. 2018. “Characterization and Properties of Natural Fiber Polymer Composites: A Comprehensive Review.” Journal of Cleaner Production 172: 566–581. doi:https://doi.org/10.1016/j.jclepro.2017.10.101.
- Sapuan, S., F.-L. Pua, Y. El-Shekeil, and F. M. AL-Oqla. 2013. “Mechanical Properties of Soil Buried Kenaf Fibre Reinforced Thermoplastic Polyurethane Composites.” . Materials & Design 50: 467–470. doi:https://doi.org/10.1016/j.matdes.2013.03.013.
- Sapuan, S., and I. M. Mujtaba. 2009. Composite Materials Technology: Neural Network Applications. Boca Raton, USA: CRC Press.
- Sapuan, S., W. Haniffah, and F. M. AL-Oqla. 2016. “Effects of Reinforcing Elements on the Performance of Laser Transmission Welding Process in Polymer Composites: A Systematic Review.” International Journal of Performability Engineering 12: 553.
- Sari, N. H., J. Fajrin, S. Fudholi, and A. Fudholi. 2020. “Characterisation of Swellability and Compressive and Impact Strength Properties of Corn Husk Fibre Composites.” Composites Communications 18: 49–54. doi:https://doi.org/10.1016/j.coco.2020.01.009.
- Sarikaya, E., H. Çallioğlu, and H. Demirel. 2019. “Production of Epoxy Composites Reinforced by Different Natural Fibers and Their Mechanical Properties.” Composites Part B: Engineering 167: 461–466. doi:https://doi.org/10.1016/j.compositesb.2019.03.020.
- Shah, D. U., P. J. Schubel, M. J. Clifford, and P. Licence. 2014. “Mechanical Property Characterization of Aligned Plant Yarn Reinforced Thermoset Matrix Composites Manufactured via Vacuum Infusion.” Polymer-Plastics Technology and Engineering 53 (3): 239–253. doi:https://doi.org/10.1080/03602559.2013.843710.
- Sorrentino, L., G. Simeoli, S. Iannace, and P. Russo. 2015. “Mechanical Performance Optimization through Interface Strength Gradation in PP/glass Fibre Reinforced Composites.” Composites Part B: Engineering 76: 201–208. doi:https://doi.org/10.1016/j.compositesb.2015.02.026.
- Sun, L., R. F. Gibson, F. Gordaninejad, and J. Suhr. 2009. “Energy Absorption Capability of Nanocomposites: A Review.” Composites Sci. Technol 69: 2392–2409.
- Supian, A., S. Sapuan, M. Zuhri, E. Zainudin, and H. H. Ya. 2018. “Hybrid Reinforced Thermoset Polymer Composite in Energy Absorption Tube Application: A Review.” Defence Technology 14 (4): 291–305. doi:https://doi.org/10.1016/j.dt.2018.04.004.
- Thakur, V. K., and M. K. Thakur. 2014. “Processing and Characterization of Natural Cellulose Fibers/thermoset Polymer Composites.” Carbohydrate Polymers 109: 102–117. doi:https://doi.org/10.1016/j.carbpol.2014.03.039.
- Živković, I., C. Fragassa, A. Pavlović, and T. Brugo. 2017. “Influence of Moisture Absorption on the Impact Properties of Flax, Basalt and Hybrid Flax/basalt Fiber Reinforced Green Composites.” Composites Part B: Engineering 111: 148–164. doi:https://doi.org/10.1016/j.compositesb.2016.12.018.
- Zuccarello, B., C. Militello, and F. Bongiorno. 2021. “Influence of the Anisotropy of Sisal Fibers on the Mechanical Properties of High Performance Unidirectional Biocomposite Lamina and Micromechanical Models.” Composites Part A: Applied Science and Manufacturing 143: 106320. doi:https://doi.org/10.1016/j.compositesa.2021.106320.