ABSTRACT
In the construction field, supplementary cementitious materials (SCMs) have brought about a technological revolution in the manufacturing of concrete as a partial replacement or addition to conventional binder mass. Keeping this in mind, this paper aims to summarise and discuss the reported findings on the mechanical and durability properties of alccofine-1203 based concretes. It is also aimed to give a better understanding of the behaviour and effect of alccofine-1203 as an SCM in various types of concretes. The alccofine-1203 has ultra-fine particles with a unique chemical composition that improves the hydration process and pozzolanic reaction. Therefore, its incorporation in concrete has resulted in good workability, reduction in segregation, reduction in heat of hydration, and reduction in permeability to concrete, and increased the rate of hydration process and improved the pozzolanic reaction to achieve high strength to concrete at the early curing stage. The presence of calcium (CaO) and silica (SiO2) in alccofine-1203 improved the mechanical and durability properties of concrete better than the other SCMs. From the literature review, the optimum dosage of alccofine-1203 is obtained between 8% to 12%, and at these percentages, the improvement in mechanical and durability properties of the concrete is highest.
1. Introduction
Cement production is one of the major causes of environmental pollution due to the release of large amounts of carbon dioxide into the atmosphere from cement production plants. There is a need to limit the use of cement in concrete manufacturing due to a number of issues such as emissions of toxic gases during the cement manufacturing process, continuous depletion of raw materials for cement production, and the rising cost of cement production (Sivakumar et al. Citation2015). The reduction in consumption of large quantity of cement in the manufacturing of concrete can be achieved by use of supplementary cementitious materials (SCMs) as a partial or full replacement to cement.
The use of SCMs is indeed a revolutionary step in the field of civil engineering. Due to the pozzolanic properties of SCMs, the combination of SCMs with cement can produce various strengths and durable concretes. Thus, using SCMs as an alternative or partial replacement to cement can reduce the use of cement in concrete manufacturing and reduce environmental pollution. There are different types of SCMs such as fly ash, ground granulated blast furnace slag (GGBS), silica fume, pond ash, limestone fines, rice husk ash, metakaolin, etc … (Reddy and Meena Citation2018). The SCMs are obtained by processing discharged waste materials from factories and industries. Otherwise, dumping of all these waste materials into the environment is also a cause of environmental problems and the spread of diseases. All the waste materials are reusable in the construction field after suitable changes are made to them so that these waste materials are converted into useful SCMs (Kumar et al. Citation2016). Recycling waste materials from industries and factories have economic, technical, and environmental benefits. Globally, the application of SCMs-based concretes is increasing widely due to its eco-friendly nature, good performance, and energy-conserving reasons (Kumar et al. Citation2016). So far, SCMs have been playing a major role in the development of sustainable concrete and will continue to do so in the future. The SCMs were used either as mineral admixture or partial replacement to cement in the production of sustainable concrete (Reddy and Meena Citation2018) (Kumar et al. Citation2016). The use of SCMs in the development of concrete will reduce the use of consumption of cement and leads to a reduction in the emission of carbon dioxide from the cement production plants and limiting the excavation of raw materials used in the manufacture of cement, and also provide a solution for safe disposal of industrial waste.
Recent advancements in SCMs have led to the development of a new micro-mineral SCM called Alccofine by Ambuja Cements Pvt Ltd, one of India’s major cement manufacturing plants (Sharma, Sharma, and Goyal Citation2016). Based on different calcium content, there are three types of alccofine such as alccofine-1101, alccofine-1203, and alccofine-1206 are commercially available in the market. Among these three, alccofine-1101 is a high calcium silicate content material that is primarily used for grouting and soil stabilisation purposes (Gupta, Sharma, and Sharma Citation2015). Alccofine-1203 is a low calcium silicate content material that is used as SCM to replace silica fume in the manufacturing of high-strength concrete (HSC) and high-performance concrete (HPC). Similarly, alccofine-1206 is also a low calcium silicate content material used in the manufacturing of various types of concretes (Kumar et al. Citation2016). Conforming to ASTM C 989–99 standards, the physical and chemical properties of alccofine-1203 are shown in .
Table 1. Physical and chemical properties of Alccofine-1203 (Sharma, Sharma, and Goyal Citation2016)
Alccofine-1203 is an eco-friendly and low calcium silicate-based microfine material that consists of a high amount of glass content with high reactivity. Alccofine-1203 is a highly processed material obtained from GGBS, the waste material generated from the iron ore industries in India. Alccofine-1203 is a fine powder. Due to the controlled granulation process, alccofine-1203 contains ultra-fine particles with a fineness of 12,000 cm2/gm with a unique chemistry (Ansari et al. Citation2015; Parveen et al. Citation2018; Jindal et al. Citation2017b; Soni, Kulkarni, and Parekh Citation2013; Pawar and Saoji Citation2013b; IS 9103 Citation1999; Parveen, Singhal, and Jindal Citation2017a). The use of alccofine-1203 in the development of concrete not only increases the compressive strength of concrete but also improves the flowability and workability of the concrete (Rajesh Kumar, Samanta, and Singha Roy Citation2015). Particles of alccofine-1203 material are much finer than other binding materials such as cement, GGBS, silica, fly ash, etc. Therefore, the voids that occurred between the cement particles can be filled by the incorporation of alccofine-1203, shown in . To show the morphology, shape, and size of the ultra-fine particles of alccofine-1203, (Sagar and Sivakumar Citation2020) presented a scanning electron microscope (SEM) image of alccofine-1203 as shown in . The SEM image revealed that the particles of alccofine-1203 are highly fine with glassy surface characteristics and have irregular in shape with sharp edges. The comparison of chemical compositions of alccofine-1203 with cement and other SCMs are presented in . The presence of CaO (Lime) makes alccofine-1203 performance superior to all other mineral admixtures (Gupta, Sharma, and Sharma Citation2015). X-ray diffraction (XRD) analysis of alccofine-1203 is presented in , which has the peak intensity of calcite composition and followed by the trace of Gehlenite, Quartz, and Akermanite (Sagar and Sivakumar Citation2021). The XRD pattern of alcofine-1203 is almost shown the amorphous characteristic because of high glass content (Saxena, Kumar, and Singh Citation2018). The use of pozzolanic materials like Fly ash alone cannot gain desired strength or performance in the early age of concrete. The addition of performance accelerating agents like silica fume, alccofine, metakaolin enhance the performance of high fly ash volume concrete and in geopolymer concrete (GPC), etc. (Suthar Sunil and Shah Citation2013).
Table 2. Chemical compositions of cement, alccofine-1203 and other SCMs (Sagar and Sivakumar Citation2021)(Gautham Kishore and Ramadoss Citation2020)(Srinivasreddy and Balamurugan Citation2019)(Parveen, Singhal and Jindal Citation2017b)
Figure 2. SEM image of alccofine-1203 (Sagar and Sivakumar Citation2020)
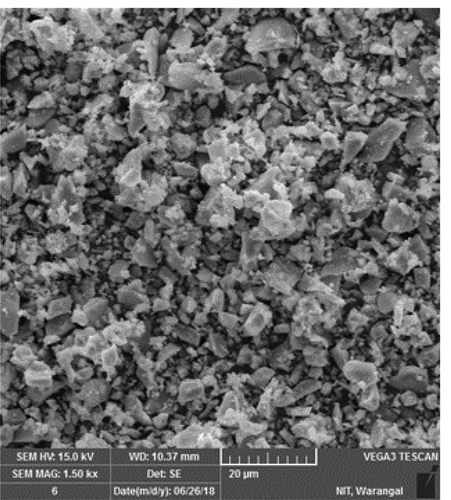
Figure 3. XRD analysis of alccofine-1203 (Sagar and Sivakumar Citation2021)
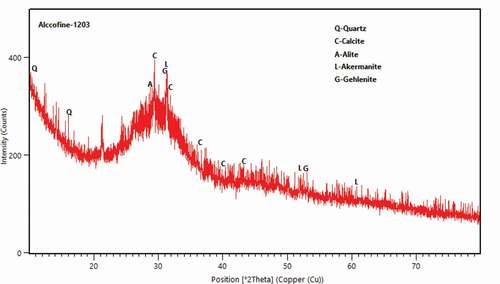
In recent years, the use of alccofine-1203 has been increasing in the development of different types of concrete because of its well particle packing of ultrafine particles and unique chemical composition. Therefore, this study aims to present a comprehensive review of the effect of alccofine-1203 on workability, strength properties, and durability properties of different types of concrete developed by using alccofine-1203 as a partial replacement to cement or other SCM. In addition, this study also aims to find the optimum percentage of alccofine-1203 based on mechanical and durability properties to be used in the development of various types of concrete in the future.
1.2. Selections of papers
A comprehensive literature review has been conducted based on the recent publications that investigated the addition or partial replacement of cement with alccofine-1203 in combination with other SCMs such as Fly Ash and GGBS. Such review is an important basis for further discussion on the potentials and limitations of the alccofine-1203 in the application of construction of concrete structures. The selection of papers was based on keywords: Alccofine, Alccofine-1203, and Alccofine-1203-based concrete from the sources like Web of Science, Science Direct, Scopus, Techno press, Tylor and Francis, Springer link, Google scholar, etc. This review was conducted with limited papers obtained from the above mentioned sources.
2. Literature review
Before using newly developed cementitious material in the construction of concrete structures, it is important to study the mechanical and durability properties of the concrete manufactured using it. Since alccofine-1203 is a new SCM for the construction industry, it is important and necessary to study the mechanical properties and durability performances of alccofine-1203-oriented concretes before its safe application in the construction of concrete structures. Because the analysis and design of concrete structures are highly influenced by the mechanical properties of the concrete, and the performance and service life of the concrete structures are influenced by the concrete resistance against chemical attacks. Keeping this in view, recent studies have been chosen to present a comprehensive review of the mechanical and durability properties of different types of alccofine-1203-based concretes.
2.1. Mechanical properties
The efficiency of alccofine-1203 in the development of self-compacting concrete (SCC) was investigated by few researchers. Pawar and Saoji (Citation2013a) attributed self-compatibility characteristics to the concrete by increasing the number of fine particles in the binder mass with the addition of 0%, 5%, 10% and 15% volume percentages of alccofine-1203 while keeping the cement, fly ash, and coarse and fine aggregates proportions constant. The test results of alccofine-1203-based SCC were compared with the normal SCC and found that incorporating alccofine-1203 has improved the fresh and hardened properties of the SCC significantly compared to normal SCC. From test results, it was determined that the SCC with 10% alccofine-1203 exhibited superior workability and compressive strength than SCC with 0%, 5%, and 15% addition of alccofine-1203. Kavitha and Felix Kala (Citation2016) developed SCC by partial replacement of cement using alccofine-1203 and GGBS. In this investigation, authors examined the effect of 5%, 10%, 15% and 20% alccofine-1203 replacement levels with a combination of 30% GGBS on workability properties and compressive, flexural and split tensile strengths of SCC. It was reported that the replacement of cement using alccofine-1203 with a combination of GGBS improved the workability and strength properties of SCC. The incorporation of alccofine-1203 improved the workability properties of SCC due to high fineness and glassy surface characteristics with low calcium silicate chemical composition of alccofine-1203. Kavitha and Felix Kala (Citation2016) found that the EFNARC (European Federation of National Associations Representing for Concrete) recommendations can be followed to produce the alccofine-1203 and GGBS-based SCC as its workability results satisfying the EFNARC specifications. From test results, it was concluded that the highest compressive and split tensile strengths to SCC are attributed by replacing cement with 10% alccofine-1203 and 30% GGBS than the other replacement levels of alccofine-1203. Kavyateja, Guru Jawahar, and Sashidhar (Citation2020) investigated the mechanical properties of SCC, developed by partial replacement of cement using 25% fly ash with 0%, 5% 10% and 15% alccofine-1203 combinations. The developed mixes were designated as NM, SCC0, SCC1 SSC2, and SCC3 concerning the alccofine-1203 replacement percentages. From , it was reported that at 3, 7, 28, and 90 days, the specimens of SCC2 (65% cement + 25% fly ash + 10% alccofine-1203) have shown the highest compressive and split tensile strengths and modulus of rupture than the control mix (NM) specimens and other alccofine-1203 incorporated mix specimens. Based on this, it was concluded that 25% fly ash and 10% alccofine-1203 is an optimum percentage to partially replace cement to achieve SCC with superior strength properties.
Figure 4. Change in strength properties of SCC with the incorporation of alccofine-1203 and fly ash (Kavyateja, Guru Jawahar, and Sashidhar Citation2020)
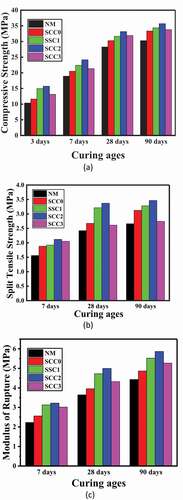
In another study, the effect of the addition of steel fibres on workability and compressive, flexural, and split tensile strength properties of alccofine-1203 and fly ash-based steel fibre reinforced SCC was investigated by Khating, Supekar, and Mehetre (Citation2018). Initially, SCC was developed by replacing 30% cement with fly ash then, steel fibre-reinforced SCC developed by adding 1% steel fibres and partial replacement of remaining 70% cement with 5%, 10%, 15%, 20% and 25% alccofine-1203. It was reported from the fresh properties of steel fibre-reinforced SCC that incorporating ultra-fine particles of alccofine-1203 imparted good flowability and good self-compacting characteristics to the steel fibre-reinforced SCC and also satisfied the EFNARC specifications given for the development of SCC. From , it was found that the mix with 15% alccofine-1203 exhibited the highest compressive, flexural and split tensile strengths than the other mixes.
Table 3. Strength results of SCC at 28 days test (Khating, Supekar, and Mehetre Citation2018)
Sanjeev Kumar et al. (Citation2019) investigated to enhance the strength properties of lightweight aggregate concrete using alccofine-1203. In this study, the authors attempted to obtain the strength decreased to the lightweight concrete due to partial replacement of coarse aggregates with coconut shells by using partial replacement of cement with alccofine-1203. Cement replaced with 6%, 8%, 10% and 12% of alccofine-1203. It was concluded that compared to coarse aggregate based control mix, the concrete mix with 8% alccofine-1203 has 18% lowest density and it is least among all the developed mixes. The 28 days test results showed that the partial replacement of coarse aggregates with coconut shells reduced the compressive strength of concrete from 44.8MPa to 35.49MPa, and by replacing cement with 8% alccofine-1203, the compressive strength of lightweight concrete increased to 42.41MPa. Balamuralikrishnan and Saravanan (Citation2021) used 0%, 5%, 10%, 15% and 20% of alccofine-1203 to replace cement to investigate the effect of alccofine-1203 on the compressive strength of cement mortar. As shown in , by replacing 10% cement with alccofine-1203, the mortar specimen has shown the highest compressive strength in all stages of curing, and specifically, at 28 days, it has attained a compressive strength of 53.12MPa, whereas the specimen with 100% cement attained only 44.74 MPa.
Figure 5. Compressive strength of alccofine-1203 incorporated mortar cubes (Balamuralikrishnan and Saravanan Citation2021)
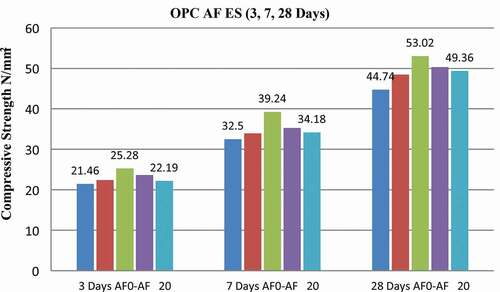
Soni, Kulkarni, and Parekh (Citation2013) conducted an experimental investigation to optimise the percentage of fly ash and alccofine-1203 to partially replace the cement for high-performance concrete (HPC) development. It was determined that replacing cement with 16% fly ash and 8% alccofine-1203 led to the development of HPC with improved properties. Suthar, Shah, and Patel (Citation2013) compared the test results of alccofine-1203-based HPC with silica fume-based HPC. It was found that the alccofine-1203-based HPC mixes have shown higher compressive and flexural strengths than the silica fume-based mixes in all stages of curing. Based on compressive and flexural strength results, Suthar, Shah, and Patel (Citation2013) reported that the replacement of cement with 8% alccofine-1203 and 20% fly ash has exhibited higher compressive and flexural strengths compared to the same percentages of cement replacement with silica fume and fly ash. This is due to the particle packing of binder mass has increased with the incorporation of ultra-fine particles of alccofine-1203, which led to the gain of high strength to concrete in the early stages of curing. The presence of lime (CaO) enhances and provides the secondary hydrated C-S-H gel products that result in gaining high strengths at early ages of curing and also result in low heat generation in the hydration process (Soni, Kulkarni, and Parekh Citation2013)(Gupta, Sharma, and Sharma Citation2015).
Gautham Kishore and Ramadoss (Citation2020) stated that alccofine-1203 can be considered as SCM in the development of ultra-HPC. The mechanical properties of ultra-HSC improved with the presence of alccofine-1203 compared to the silica fume-based ultra-HSC. At 28 days test, alccofine-1203 and GGBS-based ultra-HSC yielded compressive strength of 136.67 MPa, the flexural strength of 31.88 MPa, and split tensile strength of 15.20 MPa whereas silica fume and GGBS-based ultra-HSC yielded compressive strength of 119.31 MPa, the flexural strength of 27.82MPa and split tensile strength of 13.26 MPa. According to Upadhyay and Jamnu (Citation2014), the highest compressive strength of HPC attained at replacement of cement with 10% of alccofine-1203 and 30% of fly ash. Based on the addition of alccofine-1203, the maximum strength of concrete was achieved at an early age and increased the self-compatibility characteristics such as passing and filling ability and segregation resistance. In the development of HSC and HPC, the usage of alccofine-1203 has significant effects on the water to binder ratio such as lowering the water demand as it acts as a high range water reducer without loss of concrete workability to increase compressive strength on concrete (Suthar Sunil and Shah Citation2013). The alccofine-1203 has well particle packing, therefore its incorporation resulted in improved rheology and good flow ability to concrete (Soni, Kulkarni, and Parekh Citation2013) and the voids present between cement particles can be minimised by ultra-fine particles of alccofine-1203 thereby, upon hydration of cement and pozzolanic reaction of alccofine-1203 leads to the development of dense core matrix structure. The cost of alccofine-1203 is less than the ordinary Portland cement (OPC); hence it is economical to use in the development of HSC (Upadhyay and Jamnu Citation2014). Based on the literature review conducted on alccofine-1203-based HPC, Boobalan et al. (Citation2021) concluded that incorporation of alccofine-1203 has caused concrete to attain high strength at an early stage and improved the workability, strength properties and durability characteristics of concrete. The presence of CaO in alccofine-1203 leads to the formation of additional C-S-H gel to attribute higher strength to concrete at an early age. As alccofine-1203 is low calcium silicate-based material, its incorporation in concrete development enhances the pH value to protect against corrosion and improves durability characteristics.
Sagar and Sivakumar (Citation2021) investigated the mechanical and microstructural behaviour of HSC developed by partial replacement of cement with various percentages of alccofine-1203 and 20% fly ash. The increase in alccofine-1203 percentages slightly increased the consistency of mixes but decreased the initial and final setting times. From , it was reported that due to the good particle packing and unique chemical composition of ultra-fine particles of alccofine-1203, its incorporation in the development of concrete improved the flowability of the concrete smoothly without bleeding and segregation. As presented in , the replacement of 30% cement (20% fly ash and 10% alccofine-1203) has shown the highest compressive strength of 80.33 MPa, flexural strength of 6.22 MPa, and split tensile strength of 5.81 MPa at 28 days test compared to mixes with 0%, 4%, 6%, 8%, 12% and 14% alccofine-1203. The decrease in compressive strength noticed in case of mixes with 12% and 14% alccofine due to the unsoundness of binder caused by an increase of free lime (CaO), alumina (Al2O3) and magnesia (MgO), which upon hydration process resulted in the excessive expansion and micro-cracks in the concrete and showed lower resistance against compression load.
Table 4. Compressive strength, flexural strength and split tensile strength test results at 28 days (Sagar and Sivakumar Citation2021)
Figure 6. Influence of alccofine-1203 on workability of HSC (Sagar and Sivakumar Citation2021)
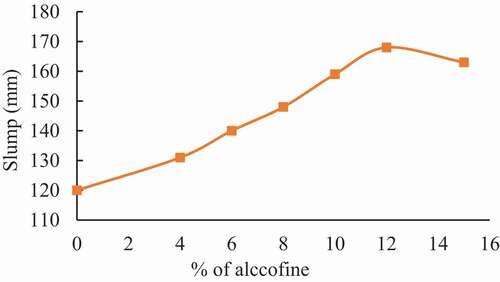
According to Vimal Arokiaraj and Elangovan (Citation2019), with increasing percentage of steel fibre (1%, 2%, 3%, 4%, and 5%) addition, the compressive strength of steel fibre-reinforced concrete increased by replacing 10% of cement with alccofine-1203.
Magdum and Karjinni (Citation2016) investigated the compressive and flexural strength of hybrid fibre reinforced HSC. The highest compressive and flexural strengths were obtained by adding 1.5% of hybrid fibres (80% steel fibres + 20% polypropylene fibre) and by partial replacement of cement with 7.5% of alccofine-1203. The effect of alccofine-1203 on the rapid strength gain property of HSC was investigated by Srinivas, Ponraj Sankar, and Kumara Swamy (Citation2021). From the control mix, 0%, 5%, 10% and 15% of cement replaced with alccofine-1203. The developed mixes are tested for mechanical properties at 1, 2, 7 and 28 days. All the alccofine-1203 based mixes had superior quick setting property than the concrete without alccofine-1203. From the results presented in , it was noticed that with the incorporation of alccofine-1203, there was a great increase in compressive, flexural and split tensile strengths at an early age curing. At 10% alccofine-1203, the highest compressive, flexural and split tensile strengths are obtained in all stages of curing.
Figure 7. Compressive, flexural and split tensile strength of alccofine-1203 incorporated HSC cubes (Srinivas, Ponraj Sankar, and Kumara Swamy Citation2021)
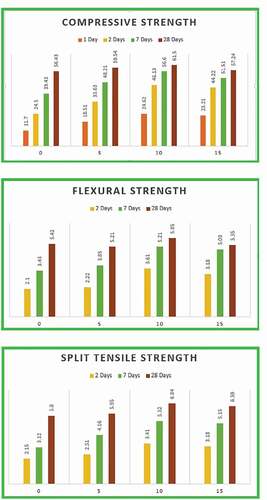
Kaviya et al. (Citation2017) determined that 15% incorporation of alccofine-1203 as partial replacement to cement led to the development of HSC and stated that due to the low cost of alccofine-1203 the development of HSC is more economical. Sharma, Sharma, and Goyal (Citation2016) investigated to optimise the percentage of alccofine-1203 in the development of HSC by replacing cement with 0%, 5%, 10%, 15% and 20% alccofine-1203. At 15% replacement level, the mix obtained the highest compressive, flexural and split tensile strengths. Based on these results, Sharma, Sharma, and Goyal (Citation2016) proposed that the replacement of cement with 15% alccofine-1203 is an optimum dosage for the development of HSC. And further, Sharma, Sharma, and Goyal (Citation2016) also reported the effective utilisation of alccofine-1203 and waste-foundry slag in the development of HSC. The natural fine aggregates were replaced with 0%, 10%, 20%, 30%, 40%, 45% and 50% foundry slagand Portland Pozzolana cement (PPC) replaced with 15% alccofine-1203. It was concluded that the highest compressive, flexural and split tensile strengths was obtained at 45% replacement of fine aggregates with foundry slag and 15% cement replacement with alccofine-1203. The experimental and analytical investigation on the mechanical properties and uniaxial stress-strain behaviour of the alccofine-1203-based HSC were carried out by Sagar and Sivakumar (Citation2020). In this study, 0%, 4%, 6%, 8%, 10%, 12% and 14% alccofine-1203 with a combination of 20% fly ash used to partially replace the cement for the development of HSC. The experimental stress-strain curves for all percentages of alccofine-1203 were presented in . From experimental results, it was determined that the highest compressive, flexural and split tensile strengths were obtained at 10% alccofine-1203. From the analytical study on stress-strain curves, it was found that the stress-strain curve obtained to the mix having 10% alccofine-1203 has shown higher Young’s modulus and higher energy absorption capacity than the stress-strain curves obtained to the mixes having other percentages of alccofine-1203. It was also reported that replacing cement with alccofine-1203 beyond 10% exhibited a negative effect on investigated parameters.
Figure 8. Compressive stress-strain behaviour of alccofine-1203 incorporated HSC (Sagar and Sivakumar Citation2020)
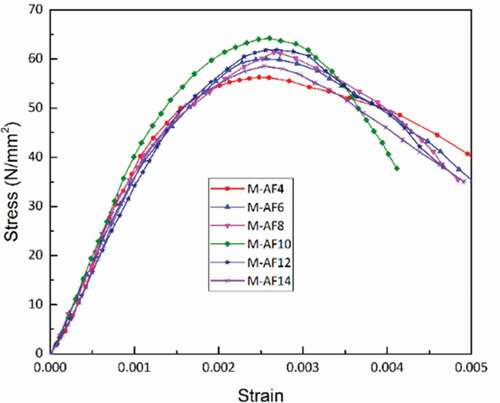
Saurav and Gupta (Citation2014) compared the cube and cylindrical compressive strength results of alccofine-1203-based HSC. In this investigation, cement replaced with 0%, 3%, 5%, 7%, 10%, 13%, 15% and 18% alccofine-1203. It was found that the replacement of cement with alccofine-1203 effectively increased the compressive strength of concrete up to 10%, and slightly increased for 13% and decreased for 15% and 18% replacements. The highest cube and cylindrical compressive strength were obtained at 13% replacement. The cylindrical specimens showed lower compressive strengths than the cube specimens. From the investigation on HSC, Rajesh Kumar, Samanta, and Singha Roy (Citation2015) reported that replacement of cement with 10% alccofine-1203 has led to the development of the highest compressive and flexural strengths at 7 and 28 days than the replacement of cement with 0%, 5%, 15% and 20% alccofine-1203. The compressive and flexural strength results of HSC reported by Rajesh Kumar, Samanta, and Singha Roy (Citation2015) are presented in .
Table 5. Compressive and flexural strengths of HSC with alccofine-1203 (Rajesh Kumar, Samanta, and Singha Roy Citation2015)
Gupta, Sharma, and Sharma (Citation2015) presented a literature survey on alccofine-1203-based concretes. It was concluded that alccofine-1203 used as SCM in the manufacturing of concrete as a partial replacement to cement due to its ultra-fine particles and calcium content. The use of alccofine-1203 improved the workability of concrete and can be retained for a sufficient duration. Alccofine-1203 reduces the heat of hydration and improves the strength of concrete at early and later ages. The ultra-fine particles of alccofine-1203 result in smooth texture to concrete members. The production cost of alccofine-1203-based HSC is lower than that of OPC-based HSC due to the lower price of alccofine-1203. The efficiency of alccofine-1203 as a cementing material in the manufacturing of concrete was examined by Gayathri, Ravichandran, and Saravanan (Citation2016). It was concluded that 15% replacement to cement yielded higher strength than the 5%, 10% and 20% replacements. From the investigation on green concrete, Narasimha Reddy and Ahmed Naqash (Citation2019) also determined that 20% replacement of cement with alccofine-1203 has achieved early strength to the concrete. Reddy and Meena (Citation2017a) stated that replacement of cement with alccofine-1203 in combination with fly ash has resulted in the development of eco-friendly concrete having better and superior properties than only cement-based concrete. It was determined that replacement of cement with 15% fly ash and 10% alccofine-1203 shown higher compressive, flexural, and split tensile strengths than the other alccofine-1203-based mixes and control mix. In another investigation, Narender Reddy and Meena (Citation2017b) studied the change in behaviour of fresh properties of concrete developed by partial replacement of cement with alccofine-1203 in combination with GGBS. It was reported that due to replacement of cement with alccofine-1203 and GGBS has decreased the setting time of concrete and shown better workability than the control mix. Further, Reddy and Meena (Citation2018) also evaluated the compressive strength property of ternary-blended concrete developed by using alccofine-1203 and GGBS as partial replacement to cement. Initially, the influence of partial replacement of cement with GGBS on compressive strength of concrete was investigated and concluded that among 0%, 10%, 20%, 30% and 40%, the 20% replacement of cement with GGBS (mix M2) increased the compressive strength of concrete highest than the other GGBS percentages as shown in ). Then, to evaluate the effect of alccofine-1203 on strength properties, 8%, 10%, 12% and 14% of alccofine-1203 are used to partially replace 80% of the remaining cement. It was concluded that the combination of alccofine-1203 and GGBS reduced the compressive strength of ternary-blended concrete compared to GGBS and cement-based concrete. As shown in ), as the percentage of alccofine-1203 increased, there was a great reduction in compressive strength due to the incompatible nature of GGBS and alccofine material. Hence, Narender and Meena achieved the highest compressive strength to ternary-blended concrete at a combination of 72%–20%–8% (mix M5 in )) of cement, GGBS and alccofine, respectively.
Figure 9. Change in compressive strength (a) replacement of cement with GGBS; (b) replacement of cement with alccofine-1203 and 20% GGBS (Reddy and Meena Citation2018)
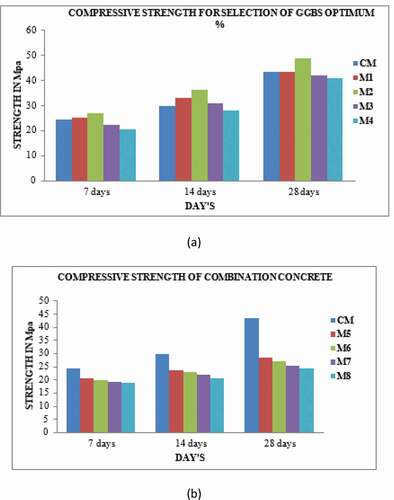
Sagar and Sivakumar (Citation2021) presented SEM analysis on alccofine-1203-based HSC binder paste. From , it was concluded that the formed portlandite and stratlingite crystals upon reaction with silica (SiO2) present in alccofine-1203 and fly ash leads to the development of additional honeycomb structure called C-S-H (calcium silicates hydrated) gel upon hydration process and pozzolanic reaction to impart high strength to concrete in early stages of curing period.
Figure 10. SEM of HSC paste incorporated with 10% alccofine-1203 (Sagar and Sivakumar Citation2021)
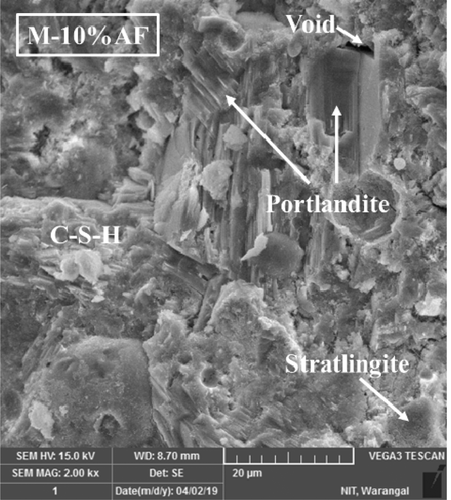
Jindal et al. (Citation2017c) developed geopolymer concrete (GPC) by partial replacement of low calcium fly ash with 0%, 5% and 10% alccofine-1203. The developed mixes were cured in ambient and heat curing conditions for 3-, 7- and 28-day strength tests. From test results, it was concluded that the compressive, flexural and split tensile strengths of GPC cured in both curing conditions were increased with the incorporation of alccofine-1203. Compared to ambient cured GPC, the heat-cured GPC attained higher strengths because the alccofine-1203 enhanced the geopolymerization process significantly in high temperature curing conditions than normal ambient temperature curing conditions. However, the ambient cured GPC has also obtained the required compressive strength for purpose of general constructions. From the compressive strength results of oven-cured GPC, Jindal et al. (Citation2017a) concluded that the specimens of mix replacing 10% fly ash with alccofine-1203 showed higher resistance to compressive loads than specimens of mixes replaced with 0% and 5%. To strengthen this, Jindal et al. (Citation2017a) also studied the microstructural characteristics using XRD studies on GPC manufactured with and without alccofine-1203. From , it was reported that during the polymerization process of GPC, the amorphous materials are converted into crystalline materials, and this transformation is even greater in the case of alccofine-1203 incorporated GPC, so does the GPC with 10% alccofine-1203 has exhibited higher compressive strength than normal GPC. It was reported that the GPC manufactured by incorporating alccofine-1203 is suitable for general constructions and for pre-cast plain and reinforced concrete members due to its early strength gaining property.
Figure 11. XRD analysis on GPC with and without alccofines-1203 (Jindal et al. Citation2017a)
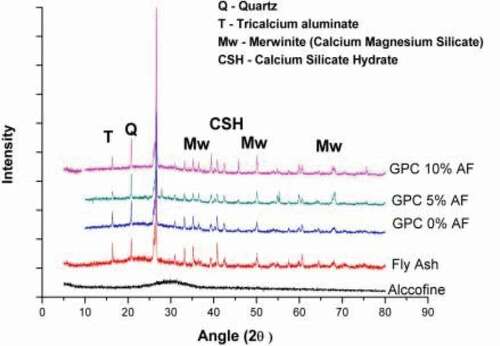
Srinivasreddy and Balamurugan (Citation2019) reported the setting time, consistency and compressive strength behaviour of the ternary blended GPC manufactured using fly ash, GGBS and alccofine-1023, and replaced 100% fine aggregate with msand. In this study, Srinivasreddy and Balamurugan (Citation2019) investigated two types of ternary-blended GPC. In type-1, GGBS content kept constant and replaced fly ash with alccofine-1203 by 10%, 20% and 30% to the weight of fly ash and given mix designation as Mix-2, Mix-3 and Mix-4. In type-2, fly ash content kept constant and replaced GGBS with alccofine-1203 by 10%, 20%, and 30% by the weight of GGBS and given mix designation as Mix-5, Mix-6 and Mix-7. Mix-1 represents the control mix having 50% fly ash and 50% GGBS. From , it was concluded that the consistency of fly ash replaced with alccofine-1203 GPC mixes has increased gradually with an increase in alccofine-1203 replacement levels, and the consistency of GGBS replaced with alccofine-1203 GPC mixes has decreased gradually with an increase in alccofine-1203 replacement levels. The replacement of fly ash or GGBS with alccofine-1203 has increased the setting time of both fly ash and GBBS-based GPC. From , compared to the control mix, by partial replacement of fly ash with alccofine-1203, the compressive strength of GPC increased significantly at 7 and 28 days but partial replacement of GGBS with alccofine-1203 significantly decreased the compressive strength of GPC at 7 and 28 days compared to fly ash–based GPC. Based on results obtained in this study, Srinivasreddy and Balamurugan (Citation2019) concluded that manufacturing concrete using fly ash, GGBS and alccofine-1203 lead to 100% replacement of OPC and effective utilisation of industrial waste products into beneficial materials.
Figure 12. Consistency of alccofine-1203 incorporated geopolymer paste mixes (Srinivasreddy and Balamurugan Citation2019)
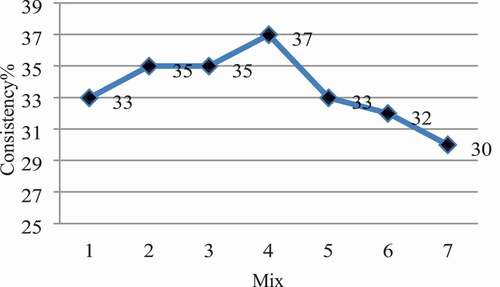
Figure 13. Consistency of ternary blended GPC mixes (Srinivasreddy and Balamurugan Citation2019)
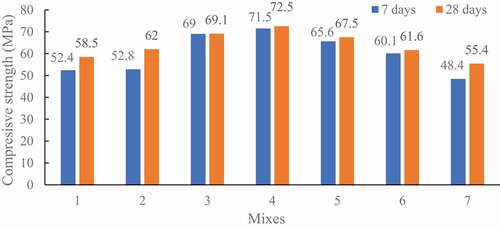
Parveen, Singhal and Jindal (Citation2017b) developed GPC using high silica rice husk ash and alccofine-1203. The developed concrete mixes are cured in ambient and heat conditions. Based on the results obtained, it was reported that alccofine-1203 is effectively increased the compressive and split tensile strengths of GPC in heat-curing conditions than in the ambient curing conditions. The presences of alccofine-1203 enhance the polymerization process in heat curing conditions to improve the early age strength properties of the concrete. The effect of alccofine-1203 on characteristics of pond fly ash and alccofine-1203-based geopolymer mortar in microwave oven curing conditions and hot air oven curing conditions was investigated by Saxena, Kumar, and Singh (Citation2018). From test results, it was concluded that the compressive strength obtained to geopolymer mortar cured in the microwave for an hour was comparable to the compressive strength obtained to geopolymer mortar cured in a hot air oven at 80 °C for 12 hours, as shown in . The increase in compressive strength of geopolymer mortar is because the presence of alccofine-1203 increased the compactness and nano-structural geopolymer formation that improved the compressive strength of the mortar. The incorporation of alccofine-1203 increased the compressive strength of pond fly ash-based geopolymer mortar effectively similarly to silica fume and also offered a higher resistance to sulphuric acid in the durability test.
Figure 14. Compressive strength under different curing conditions including microwave heating (Saxena, Kumar, and Singh Citation2018)
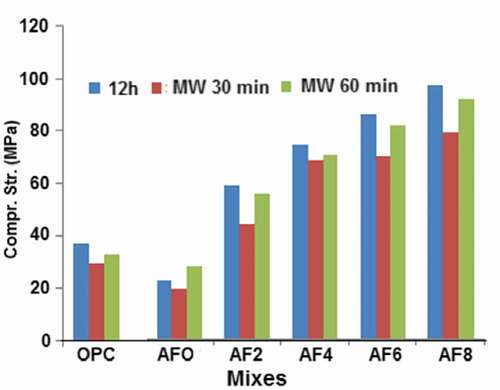
Parveen et al. (Citation2018) studied the mechanical and microstructural properties of fly ash and alccofine-1203-based GPC cured in ambient conditions. The microstructural and phase composition properties of GPC were examined by using SEM and XRD analysis. It was concluded that the compressive, flexural and split tensile strengths of GPC were obtained similarly to the conventional concrete. The GPC exhibited better microstructural and strength properties because the incorporated alccofine-1203 enhanced the polymerization process of GPC, which resulted in fewer micro-cracks and pores and formation of denser matrix as shown in to attributed higher strength to concrete.
Figure 15. SEM image of GPC prepared with 8 molarity solution (Parveen et al. Citation2018)
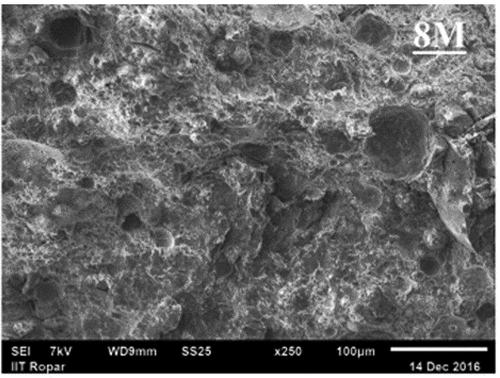
2.2. Durability properties
Research on the durability properties of newly developed concrete is important and is essential for its safe application as a construction material. Parmar et al. (Citation2014) carried out an investigation to study the durability characteristics of HPC manufactured by partial replacement of cement using alccofine-1203 and fly ash and compared these test results with test results of HPC manufactured by partial replacement of cement using silica fume and fly ash. Rapid chloride permeability test, sorptivity test, accelerated corrosion test, chloride attack test, seawater test, sulphate attack test and alkali attack test were performed to evaluate the durability characteristics of HPC. It was noticed from sorptivity test results that the rate of capillarity of alccofine-1203 and fly ash-based HPC is less than silica fume and fly ash-based HPC. Under accelerated corrosion test, silica fume and fly ash-based HPC effected significantly than the alccofine-1203 and fly ash-based HPC. Under the rapid chloride permeability test, though silica fume-based HPC has good resistance to chloride ion permeability, silica fume-based HPC specimens have high coulomb passing rate than the alccofine-1203-based HPC due to denser core structure formation in alccofine-1203 based HPC specimens. It was concluded that under the alkali attack test, sulphate attack test and seawater attack test, the loss of strength and weight to alccofine-1203-based specimens is minimal compared to the silica fume-based specimens. The presence of CaO in alccofine-1203 leads to the formation of secondary C-S-H gel product that reduces the permeability of concrete to a great extent, thus improves the durability charecteristics of concrete (Patel and Patel Citation2013; Soni, Kulkarni, and Parekh Citation2013).
Sharma, Sharma, and Goyal (Citation2016) performed a carbonation test and rapid chloride permeability test to investigate the durability characteristics of HSC manufactured using waste foundry slag and alccofine-1203. It was concluded that at 15% replacement of PPC with alccofine-1203, the pH value of concrete slightly increased with the increase in replacement levels of fine aggregates using foundry slag, but the alkalinity test results showed that concrete was safe enough from the carbonation effect and decreased the probabilities of corrosion. It was concluded from rapid chloride permeability test results that as shown in , among all different percentages, the concrete mix with 45% replacement of fine aggregates with foundry slag and 15% PPC with alccofine-1203 yielded high resistance to permeability of concrete.
Figure 16. Coulombs passed through the alccofine-1203 incorporated HSC with various foundry slag content (Sharma, Sharma, and Goyal Citation2016)
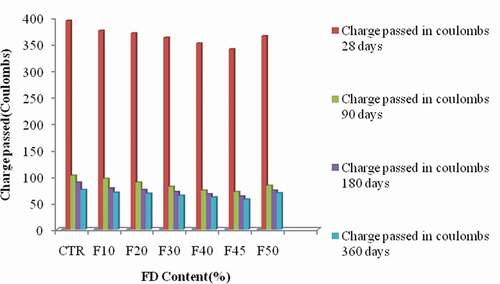
Gayathri, Ravichandran, and Saravanan (Citation2016) investigated the durability characteristics of concrete developed by replacing cement with 5%, 10%, 15% and 20% of alccofine-1203. Rapid chloride permeability test, sulphate attack test, chloride attack test and acid attack test were performed. From , it was concluded that the concrete mix with 15% alccofine-1203 had the lowest coulombs passing value, highest resistance to acid penetration and low weight and strength loss than the control mix and other alccofine-1203 based mixes.
Figure 17. Durability characteristics of alccofine-1203 incorporated concrete (Gayathri, Ravichandran, and Saravanan Citation2016)
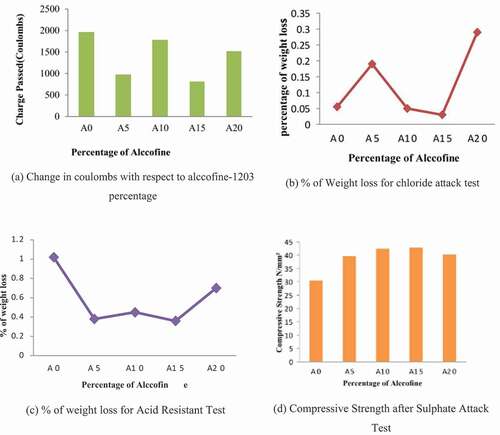
The water absorption and porosity of alccofine-1203 based HSC was reported by Sagar and Sivakumar (Citation2020). It was concluded as shown in , the specimen with 10% alccofine-1203 and 20% fly ash has the lowest water absorption capacity due to the formation of a dense matrix with low pore concentration compared to specimens with 0%, 4%, 6%, 8%, 12% and 14% alccofine-1203, and 20% fly ash.
Figure 18. Influence of alccofine-1203 on water absorption and porosity of HSC (Sagar and Sivakumar Citation2021)
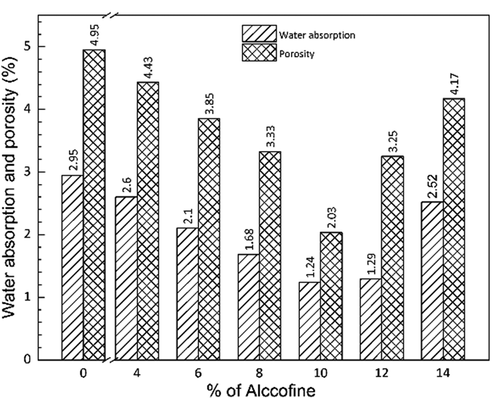
Kavyateja, Jawahar, and Sashidhara (Citation2020) reported the durability properties of SCC manufactured with alccofine-1203 and fly ash. It was determined that at replacement of cement with 25% fly ash and 10% alccofine-1203 has shown the highest resistance against alkali attack test, chloride permeability test, electrical resistivity test and rapid chloride penetration test. The effect of alccofine-1203 and GGBS addition on durability performance of concrete was investigated by Balamuralikrishnan and Saravanan (Citation2019). It was found that among various percentage replacement of cement with alccofine-1203 and GGBS, the specimens with 40% replacement of cement with 10% alccofine-1203 and 30% GGBS have shown highest resistance to acid attack, chloride attack, sulphate attack and had lowest pass of coulombs than the base mix and mixes with various other replacement levels of alccofine-1203 and GGBS. From , it was found that compared to the control mix specimen, the specimens of 60% cement, 10% alccofine-1203 and 30% GGBS have shown the lowest strength loss and weight loss than the other specimens with various cement, alccofine-1203 and GGBS content.
Table 6. Durability results of concrete mixes at 28 days (Balamuralikrishnan and Saravanan Citation2019)
The durability performance of alccofine-1203-based microsteel fibre-reinforced concrete was investigated by Sumathi, Gowdham, and Saravana Raja Mohan (Citation2018). To develop alccofine-1203-based steel fibre-reinforced concrete, 10% of cement was replaced with alccofine-1203 and incorporated with 1%, 2% and 3% microsteel fibres. The developed mixes are tested for water absorption, sorptivity, acid attack and sulphate attack. Based on test results, it was concluded that the mix with 10% alccofine-1203 and 2% microsteel fibre has shown the lowest water absorption capacity, lowest weight loss and strength after acid and sulphate chemical attacks compared to the control mix specimens. The sorptivity results showed that the mixes with 3% microsteel fibres have the highest sorptivity coefficient indicating the high water absorption, and mix with alccofine-1203 and 0% microsteel fibres have the lowest sorptivity coefficient indicating the lowest water absorption capacity of concrete. Sivakumar et al. (Citation2015) reported that 10% replacement of cement with alccofine-1203 reduced the permeability of concrete significantly. Therefore, there was a great reduction in permeability of chloride infiltration into concrete, thereby shown high resistance to chloride attack. The effect of alccofine-1203 on durability characteristics of hybrid fibre-reinforced concrete was studied by Magdum and Karjinni (Citation2017). In this study, four types of concrete mixes were developed for the investigation, such as plain concrete, alccofine concrete with 7.5% alccofine-1203, hybrid fibre-reinforced concrete with 1.5% hybrid fibres (20% polypropylene fibres and 80% steel fibres), and alccofine-1203-based hybrid fibre-reinforced concrete (7.5% alccofine-1203 and 1.5% hybrid fibres). The developed concrete was tested for water absorption test, acid attack test and fire attack test. After an acid attack, the compressive strength of alccofine-1203-based hybrid fibre-reinforced concrete has shown 39% higher compressive strength compared to plain concrete. The concrete with 7.5% alccofine-1203 shown the lowest water penetration capacity of 22% lower than the plain concrete. To study the chloride permeability effect on alccofine-1203 incorporated concrete, Thangapandi et al. (Citation2020) replaced the cement with 10%, 12%, 14% and 16% alccofine-1203. It was concluded that as shown in , concrete with 12% alccofine-1203 shows the lowest coulombs, indicating the highest resistance to chloride attack compared to the mixes with 0%, 10%, 14% and 16% alccofine-1203.
Figure 19. RCPT results of alccofine-1203 incorporated concrete (Thangapandi et al. Citation2020)
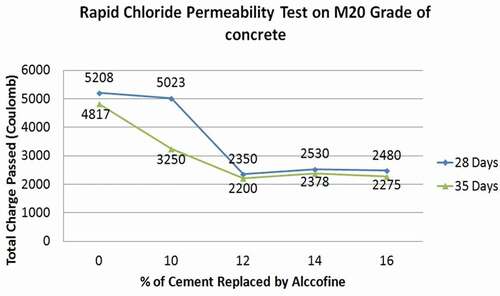
3. Discussion on literature summary
Based on literature analysis, it is clear that to date, most of the research on concrete members incorporated with alccofine-1203 as a partial replacement or as a mineral additive has mainly focused on the evaluation of mechanical properties to propose optimum dosage of alccofine-1203, and very few studies have reported the durability performance of alccofine-1203-based concretes. Alccofine-1203 is a micromineral material used to develop different types of concretes such as HSC, HPC, SCC, fly ash and alccofine-1203-based GPC, GGBS and alccofine-1203-based GPC, pond and ash alccofine-1203-based GPC, rice husk ash and alccofine-1203-based GPC, standard strength concretes by partial replacement to cement with alccofine-1203, etc. It was observed that in most of these concrete members, performances were found to be similar in behaviour concerning their strengths, and they exhibited good resistance to chemicals in the durability test. In most of the research, mechanical and durability properties were investigated and reported according to India Standard code specifications. As the production plant of alccofine micromineral additive material is in India, all the investigations were carried out in India. In all the investigations, the researchers investigated to find the optimum dosage of alccofine-1203 to be used with and without the combination of other SCMs to partial and full replacement to cement. Due to its exceptional chemical composition, alccofine-1203 can be used as a replacement for silica fume in the manufacture of concrete. On comparing the mechanical properties of alccofine-1203-based HSC and HPC with silica fume-based HSC and HPC, alccofine-1203-based concretes had better strength and durability performance than silica fume-based concretes.
The proposed optimum dosage of alccofine-1203 as a replacement to cement or SCM is differed from one concrete type to other. Some studies determined that 10% replacement of cement with alccofine-1203 is an optimum dosage to achieve the highest strength properties and durability properties to concrete and concluded that above 10% replacement gradually decreased the strength properties of concrete, but some studies determined that at 12%, 13% and 15% replacement to cement obtained highest strength properties to concrete. From the above literature review, it is clear that between 8% to 12% of alccofine-1203 as a partial replacement or as an additive to binder mass in concrete provided better mechanical properties and durability performance of concrete. The combination of alccofine-1203 and fly ash as partial or full preplacement to cement leads to the development of sustainable and eco-friendly concrete. In literature, some investigations reported that a combination of GGBS and alccofine increased the rheological and mechanical properties of SCC, whereas few studies found that the combination of alccofine-1203 with GGBS reduced the compressive strength of ternary-blended concrete than conventional concrete and in another study by replacing cement with alccofine-1203 and GGBS combination developed the ultra-HSC. There is a need to study the effect of alccofine-1203 in combination with GGBS on the mechanical properties of concrete compared to GGBS-based and standard cement-based concrete. In terms of durability behaviour of concrete, while alccofine-1203-based concrete members exhibited better and enhanced resistance than other conventional and silica fume-based concrete members, there was a lowering of the cost of construction, as alccofine is less expensive than silica fume.
Finally, based on the literature review presented above, it can be concluded that alccofine-1203 can be used as an SCM in the development of various types of concrete as a partial replacement to cement or other SCMs.
4. Scope for future research
Microstructural studies on alccoifne-1203 incorporated concrete need to study more.
The effect of alccofine-1203 on mechanical and durability properties of various types of concretes at elevated temperatures can be studied.
There was no investigation on the effect of alccofine-1203 on the mechanical strength and durability of recycled aggregate concrete.
To find the optimum combination of alccofine-1203 and GBBS, more investigations on mechanical and durability properties of alccofine- and GGBS-based concrete are required.
The flexural and shear performance of alccofine-1203 based concrete members can be investigated.
The effect of alccofine-1203 on various types of fibre reinforced concrete can be studied.
5. Conclusions
The efficiency of alccofine-1203 in the development of various types of concrete and its effect on mechanical and durability properties has been reviewed and summarised in the present study. The following conclusion can be drawn for the application of alccofine-1203 in the concrete making based on the literature review presented:
Alccofine-1203 is a low calcium silicate-based ultra-fine material with exceptional chemical composition. Due to this, there is no detrimental effect of using alccofine-1203 as SCM for partial replacement to cement or other SCMs in the development of various types of concretes.
The optimum dosage of alccofine-1203 is varied between 8% to 12%, at these percentages, alccofine-1203 improved the workability, mechanical and durability properties of the concrete at the highest.
The use of ultra-fine particles of alccofine-1203 can fill the voids between cement particles and reduces the permeability of concrete. The unique chemical composition and glassy surface characteristics of alccofine-1203 particles improve the workability of concrete and reduce segregation and bleeding by lowering the water demand.
The presence of a good amount of calcium (CaO) and silica (SiO2) in alccofine-1203 increases the rate of hydration process and improves the pozzolanic reaction to ensure the formation of additional hydrated C-S-H gel, this results in the development of dense core matrix structure of concrete to attribute higher strength to concrete at early stages of curing.
The concrete containing the optimum amount of alccofine-1203 has shown the highest resistance to chloride attack, sulphate attack, carbonation and alkaline attacks due to the formation of a dense core matrix, which reduced the deep penetration and diffusion of chemicals into the concrete.
The cost of alccofine-1203 is less than the OPC. Therefore, the use of alccofine-1203 as a partial or full replacement to cement with a combination of other SCMs in the development of concrete will be economically viable.
Disclosure statement
No potential conflict of interest was reported by the author(s).
Additional information
Notes on contributors
Bhanavath Sagar
Bhanavath Sagar is a Ph.D. student in the structural engineering division, department of civil engineering, National Institute of Technology Warangal, India. He is working under the supervision of Dr. M.V.N. Sivakumar.
M V N Sivakumar
Dr. M.V.N. Sivakumar is an Assistant Professor in the structural engineering division, department of civil engineering, National Institute of Technology Warangal, India.
References
- Ansari, U. S., I. M. Chaudhri, N. P. Ghuge, and R. R. Phatangre. 2015. “High Performance Concrete with Partial Replacement of Cement by Alccofine & Fly Ash.” Indian Research Transaction 5 (2): 19–23.
- Balamuralikrishnan, R., and J. Saravanan. 2019. “Effect of Alccofine and GGBS Addition on the Durability of Concrete.” Civil Engineering Journal 5 (6): 1273–1288. doi:https://doi.org/10.28991/cej-2019-03091331.
- Balamuralikrishnan, R., and J. Saravanan. 2021. “Effect of Addition of Alccofine on the Compressive Strength of Cement Mortar Cubes.” Emerging Science Journal 5 (2): 155–170. doi:https://doi.org/10.28991/esj-2021-01265.
- Boobalan, S. C., V. A. Srivatsav, A. M. T. Nisath, A. P. Babu, V. Gayathri, et al. 2021. “A Comprehensive Review on Strength Properties for Making Alccofine Based High Performance Concrete.” Materials Today: Proceedings 45: 4810–4812. doi:https://doi.org/10.1016/j.matpr.2021.01.278.
- Gautham Kishore, R. G., and P. Ramadoss. 2020. “Performance Evaluation of Ultra-High Performance Concrete Designed with Alccofine.” Innovative Infrastructure Solutions 6 (1): 1–11. doi:https://doi.org/10.1007/s41062-020-00375-y.
- Gayathri, K., K. Ravichandran, and J. Saravanan. 2016. “Durability and Cementing Efficiency of Alccofine in Concretes.” International Journal of Engineering Research & Technology 5 (05): 460–468.
- Gupta, S., S. Sharma, and E. D. Sharma. 2015. “A Review on Alccofine : A Supplementary Cementitous Material.” International Journal of Modern Trends in Engineering and Research 2 (8): 114–119.
- IS 9103. 1999. Concrete Admixture-Specifications. New Delhi, India: Bureau of Indian Standards.
- Jangra, P., D. Singhal, and B. B. Jindal. 2017a. “Preparation of Geopolymer Concrete (GPC) Using High-Silica Rice Husk Ash (RHA) Incorporating Alccofine.” Advanced Science, Engineering and Medicine 9 (5): 370–376. doi:https://doi.org/10.1166/asem.2017.1993.
- Jindal, B. B., D. Singhal, S.K. Sharma, D. K. Ashish, Parveen, et al. 2017a. “Improving Compressive Strength of Low Calcium Fly Ash Geopolymer Concrete with Alccofine.” Advances in Concrete Construction 5 (1): 17–29. DOI:https://doi.org/10.12989/acc.2017.5.1.17.
- Jindal, B. B., D. Singhal, S. K. Sharma, and Parveen. 2017b. “Prediction of Mechanical Properties of Alccofine Activated Low Calcium Fly Ash Based Geopolymer Concrete.” ARPN Journal of Engineering and Applied Sciences 12 (9): 683–688.
- Jindal, B. B., D. S. Praveen, and A. Goyal. 2017c. “Predicting Relationship between Mechanical Properties of Low Calcium Fly Ash-Based Geopolymer Concrete.” Transactions of the Indian Ceramic Society 76 (4): 258–265. https://doi.org/https://doi.org/10.1080/0371750X.2017.1412837
- Kavitha, S., and T. Felix Kala. 2016. “Evaluation of Strength Behavior of Self-Compacting Concrete Using Alccofine and GGBS as Partial Replacement of Cement.” Indian Journal of Science and Technology 9 (22): 1–5. doi:https://doi.org/10.17485/ijst/2016/v9i22/93276.
- Kaviya, B., K. Rohith, S. Kindo, J. M. Kumar, P. Divya, et al. 2017. “Experimental Study on Partial Replacement of Cement Using Alccofine.” International Journal of Pure and Applied Mathematics 116 (13): 399–405. http://www.ijpam.eu.
- Kavyateja, B. V., J. Guru Jawahar, and C. Sashidhar. 2020. “Effectiveness of Alccofine and Fly Ash on Mechanical Properties of Ternary Blended Self Compacting Concrete.” In Materials Today: Proceedings, 73–79. Elsevier. doi:https://doi.org/10.1016/j.matpr.2020.03.152.
- Kavyateja, B. V., J. G. Jawahar, and C. Sashidhara. 2020. “Durability Performance of Self Compacting Concrete Incorporating Alccofine and Fly Ash.” International Journal of Engineering, Transactions B: Applications 33 (8): 1522–1528.
- Khating, A., G. S. Supekar, and S. M. Mehetre. 2018. “Alccofine and Steel in Self-Compacting Concrete.” International Journal of Advance Engineering and Research Development 5 (04): 504–508.
- Kumar, A., O. Parihar, R. Chaudhary, and S. P. Singh. 2016. “Use of Alccofine 1206 to Achieve High Performance Durable Concrete.” SSRG International Journal of Civil Engineering (SSRG-IJCE) 3 (5): 181–185.
- Magdum, M. M., and V. V. Karjinni. 2016. “Open Access Influence of Mineral Admixture (Alccofine-1203) on the Properties of Hybrid Fiber Reinforced Concrete.” American Journal of Engineering Research 10: 72–75.
- Magdum, M. M., and V. V. Karjinni. 2017. “Effect of Mineral Admixture (Alccofine-1203) on Durability of Hybrid Fiber Reinforced Concrete.” Indian Journal of Science and Technology 10 (29): 1–4. doi:https://doi.org/10.17485/ijst/2017/v10i29/117016.
- Narasimha Reddy, P., and J. Ahmed Naqash. 2019. “Effect of Alccofine on Mechanical and Durability Index Properties of Green Concrete.” International Journal of Engineering, Transactions B: Applications 32 (6): 813–819.
- Narender Reddy, A., and T. Meena. 2017b. “Study on Compressive Strength of Concrete Incorporating Alccofine and Ground Granulated Blast Furnace Slag (GGBS).” In International Conference on Materials, Manufacturing and Modelling, 1–11, Vellore, India.
- Parmar, A., D. M. Patel, D. Chaudhari, and H. Raol. 2014. “Effect of Alccofine and Fly Ash Addition on the Durability of High Performance Concrete.” International Journal of Engineering Research & Technology 3 (1): 1600–1605.
- Parveen, D. Singhal, M. T. Junaid, B. B. Jindal, A. Mehta, et al. 2018. “Mechanical and Microstructural Properties of Fly Ash Based Geopolymer Concrete Incorporating Alccofine at Ambient Curing.” Construction and Building Materials 180: 298–307. doi:https://doi.org/10.1016/j.conbuildmat.2018.05.286.
- Parveen, D. S., and B. B. Jindal. 2017b. “Experimental Study on Geopolymer Concrete Prepared Using High-Silica RHA Incorporating Alccofine.” Advances in Concrete Construction 5 (August): 345–358. doi: https://doi.org/10.12989/acc.2017.5.4.345
- Patel, P. J., and H. S. Patel. 2013. “Effect on Compressive and Flexural Strength of High-Performance Concrete Incorporating Alccofine and Fly Ash.” International Journal of Civil, Structural, Environmental and Infrastructure Engineering Research and Development (IJCSEIERD) 3 (2): 109–114.
- Pawar, M. S., and A. C. Saoji. 2013a. “Performance of Self Compacting Concrete By Using Alccofine.” International Journal of Engineering Research and Applications 3 (4): 190–192.
- Pawar, M. S., and A. C. Saoji. 2013b. “Effect of Alccofine on Self Compacting Concrete.” The International Journal Of Engineering And Science 2 (6): 5–9.
- Rajesh Kumar, S., A. K. Samanta, and D. K. Singha Roy. 2015. “An Experimental Study on the Mechanical Properties of Alccofine Based High Grade Concrete.” International Journal of Multidisciplinary Research and Development 2 (10): 218–224.
- Reddy, A. N., and T. Meena. 2017a. “An Experimental Investigation on Mechanical Behaviour of Eco-Friendly Concrete.” In 14th International Conference on Science, Engineering the Technology, IOP Conference Series: Materials Science and Engineering, Vellore, India. doi:https://doi.org/10.1088/1757-899X/263/3/032010.
- Reddy, A. N., and T. Meena. 2018. “A Study on Compressive Behavior of Ternary Blended Concrete Incorporating Alccofine.” In International Conference on Materials Manufacturing and Modelling 2017, Materials Today: Proceedings, 11356–11363. Elsevier. doi:https://doi.org/10.1016/j.matpr.2018.02.102.
- Sagar, B., and M. V. N. Sivakumar. 2020. “An Experimental and Analytical Study on Alccofine Based High Strength Concrete.” International Journal of Engineering 33 (4): 530–538.
- Sagar, B., and M. V. N. Sivakumar. 2021. “An Experimental and Analytical Study on Alccofine Based High Strength Concrete.” International Journal of Engineering 33 (4): 530–538.
- Sanjeev Kumar, L. J., P. Bhuvaneshwari, M. Eswar, and K. Aditya Subramanian. 2019. “Strength Characteristics of Alccofine Based Light Weight Concrete.” International Journal of Advanced Research in Engineering and Technology 10 (1): 268–275. doi:https://doi.org/10.34218/IJARET.10.1.2019.027.
- Saurav, and A. K. Gupta. 2014. “Experimental Study of Strength Relationship of Concrete Cube and Concrete Cylinder Using Ultrafine Slag Alccofine.” International Journal of Scientific & Engineering Research 5 (5): 102–107.
- Saxena, S. K., M. Kumar, and N. B. Singh. 2018. “Effect of Alccofine Powder on the Properties of Pond Fly Ash Based Geopolymer Mortar under Different Conditions.” Environmental Technology and Innovation 9: 232–242. doi:https://doi.org/10.1016/j.eti.2017.12.010.
- Sharma, D., S. Sharma, and A. Goyal. 2016. “Utilization of Waste Foundry Slag and Alccofine for Developing High Strength Concrete.” International Journal of Electrochemical Science 7 (March): 1–10.
- Sharma, D., S. Sharma, and A. Goyal. 2016. “Utilization of Waste Foundry Slag and Alccofine for Developing High Strength Concrete.” International Journal of Electrochemical Science 7 (March): 1–10.
- Sivakumar, D., T. Hemalatha, N. S. Sri, T. Shobana, C. Soundarya, et al. 2015. “Durability and Mechanical Characterization of Concrete Using Alccofines.” International Journal of Applied Engineering Research 10 (53): 178–182.
- Soni, D., S. Kulkarni, and V. Parekh. 2013. “Experimental Study on High-Performance Concrete, with Mixing of Alccofine and Flyash.” Indian Journal of Research 3 (4): 84–86.
- Srinivas, K., L. Ponraj Sankar, and C. Kumara Swamy. 2021. “Experimental Investigation on Rapid Strength Gain by Adding Alccofine in High Strength Concrete.” In Materials Today: Proceedings, 925–929. Elsevier . doi:https://doi.org/10.1016/j.matpr.2021.01.068.
- Srinivasreddy, K., and S. Balamurugan. 2019. “Effect of Alccofine 1203 on Setting Times and Strength of Ternary Blended Geopolymer Mixes with Msand Cured at Ambient Temperature.” Revista Romana De Materiale/ Romanian Journal of Materials 49 (4): 527–534.
- Sumathi, A., K. Gowdham, and K. Saravana Raja Mohan. 2018. “Strength and Durability Studies on Alccofine Concrete with Micro Steel Fibres.” Revista Româna De Materiale/Romanian Journal of Materials 48 (1): 58–63.
- Suthar, S., B. K. Shah, and P. J. Patel. 2013. “Study on Effect of Alccofine & Fly Ash Addition on the Mechanical Properties of High Performance Concrete.” Study on Effect of Alccofine & Fly Ash Addition on the Mechanical Properties of High Performance Concrete 1 (3): 464–467.
- Suthar Sunil, B., and B. K. Shah. 2013. “Study on Strength Development of High Strength Concrete Containing Alccofine and Fly-Ash.” Indian Journal of Research 2 (3): 102–104.
- Thangapandi, K., R. Gobinath, R. Anuradha, P. Sarla, S. Shrihari, J. S. Jeevarethinam, T. A. K. Mueenudeen, N. Archana, J. T. Walter, et al. 2020. “Experimental Investigations on Chloride Permeability and Strength Properties of Concrete Using Alccofine.” In International Conference on Recent Advancements in Engineering and Management, IOP Conference Series: Materials Science and Engineering. Warangal, India. doi:https://doi.org/10.1088/1757-899X/981/3/032085
- Upadhyay, S. P., and M. A. Jamnu. 2014. “Effect on Compressive Strength of High Performance Concrete Incorporating Alccofine and Fly Ash.” Journal of International Academic Research for Multidisciplinary 2 (2): 125–130.
- Vimal Arokiaraj, G., and G. Elangovan. 2019. “Improving Strength Properties of Fiber Reinforced Concrete with Alccofine.” International Journal of Innovative Technology and Exploring Engineering 8 (12): 1500–1505.