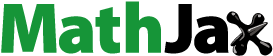
ABSTRACT
Reasons for recycling of waste include conservation of resources, reduction in the need for landfills, paying associated tipping fees and provision of low-cost raw materials for products. A high-speed weaving machine generates a high amount of selvedge wastes. In this study, stitch-bonded non-woven samples were developed by recycling woven fabric selvedge wastes. Selvedge wastes were collected from the weaving department and changed to fibre by using a fabric opener. The fibres are carded by a mechanical carding machine. Non-woven samples were developed, and sound absorption coefficients were measured by an impedance tube according to the ASTM E 1050 standard. The test result shows that the sound absorption coefficient increased with an increasing frequency level of 0 Hz, 500 Hz, 1000 Hz, 1500 Hz, 2000 Hz, 2500 Hz and 3000 Hz. The sound absorption property of all stitch-bonded samples was increased with increasing frequency. Similarly, the sound-absorbing property also increases with the increase in the thickness. The larger the density, the higher the number of fibres per unit area. Structures with less density and open pores absorb the sound with a low frequency of 500 Hz. Structures with high fibre density have better absorbency for frequency levels above 2000 Hz. The air permeability property of the developed sample decreases the sound-absorbing performance.
1. Introduction
The fast fashion cycle in the textile industry has led to a high level of consumption and waste generation. This can cause a negative environmental impact since the textile and clothing industry is one of the most polluting industries. Non-hazardous solid textile waste recycling is a viable alternative (Yalcin-Enis, Kucukali-Ozturk, and Sezgin Citation2019). Textile recycling is a process in which textile wastes, old clothing and other textiles are recovered for reuse or material recovery (Bartl and Marini Citation2008; Bhatia, Sharma, and Malhotra Citation2014). While recycling is not new to the textile industry, it is now a necessity brought on by increased fees at landfills and decreased availability of landfill space. Recycling was more than simply a trend or a new marketing campaign designed to make a profit as an economic necessity (Bartl, Citation2009; Pensupa et al. Citation2017).
The main reasons for textile waste recycling include conserving resources, reducing landfills, paying the associated tipping fees and provision of low-cost raw materials for products (Vasile and Van Langenhove Citation2004).
Fibre production is steadily growing and rapidly increasing. From an economical and an ecological point of view, the development of proper recycling technologies for this waste fraction is evident (Bhatia, Sharma, and Malhotra Citation2014).
Different textile companies are looking for applying waste materials. However, the responsibilities of recycling cannot be shouldered by individual companies or industries. A large number of companies are currently developing manufacturing processes using alternative materials for their products and seeking new markets. In order to create a sustainable society, it is necessary to develop effective utilisation of all sorts of wastes. With the significant production of waste fibrous materials, different companies are looking for applications where waste materials may represent an added-value material (Hawley Citation2006; Stanescu and Research Citation2021; Velosa et al. Citation2013).
The introduction of a shuttleless weaving technique launched a new era of high-speed weaving. Over the last 40 years, shuttleless looms have been dominant in most segments of woven fabric production (Gong, Chen, and Zhou Citation2018). Shuttleless looms are, however, unable to produce real selvedge, while a strong selvedge is created automatically at conventional shuttle looms since the inserted weftis practically endless, and this results in the formation of a strong and continuous selvedge. This shortcoming is due to the natural phenomena of this weaving technique and overcome by the formation of false selvedges. Whether it is real or false, a firm and strong selvedge is extremely important when producing woven fabrics and also in their subsequent treatment. Therefore, selvedge formation is essential and almost compulsory, and it is carried out on both sides of the cloth despite certain constraints. Shuttleless machines are, therefore, equipped with a false selvedge mechanism (Akdeniz, Özek, and Durusoy Citation2017; Mozafary and Payvandy Citation2019; Qureshi, Kumar, and Prakash Citation2021).
The formation of a false selvedge, on the other hand, generates wastes in the weft and warp yarns. The length of the presented weft yarn needs to be slightly greater than the width of woven cloth so as to result in certain wastes. The ideal way is to present just a long enough pick length with a minimum number of auxiliary warps to carry out any specific selvedge making operation. The length of this extra weft yarn may be 7–9 cm at each side, accounting to as much as 9–10% wastes (Qureshi, Kumar, and Prakash Citation2021).
The economic advantages and key technologies that need to be overcome of weaving waste selvage were analysed by researchers. It is considered that reasonable and efficient use of weaving waste selvage has better economic and social benefits (Fang et al. Citation2021). A study by Juras analysed the shuttleless weaving machines in terms of false selvedge. It reported that the selvedge wastes could be as much as 4–8% of total yarn consumption (Jurasz and Europe Citation2000).
Another work performed by Kovacevic makes comments about the effect of warp tension on selvedge fringes and fabric structure. Clear disruptions in cloth selvedge and fabric quality problems are observed when the warp tension is off the standard value. Lower warp tension makes selvedge fringes shorter than usual and also results in a wider fabric width. These conditions increase the warp breakages and stoppage period (Kovaceyic and Hadina Citation2001). New techniques and machine settings for reduction in selvedge waste are discussed in two other works (Legler Citation1999; Roy and Rahman Citation2014).
Undesirable and potentially hazardous noises are side effects of a wide range of modern engineering and other processes. With the continuing development of new technologies, particularly the trend towards faster and more powerful machinery, the environmental impact of noise is a matter of increasing concern, and considerable efforts are being made to finding effective means of noise abatement (Al-Mutairi, Al-Rukaibi, and Koushki Citation2009; Qiu Citation2016).
Noise can be considered as one of the serious environmental issues, which causes many problems, such as effects on health, communication, hearing loss, changes in human behaviour and sleep disturbances; few decades ago, industrial materials such as rock wool, glass wool and asbestoses have been introduced to reduce the noise level, especially in workplace (Crocker Citation2007; Dalton and Behm Citation2007; Rabinowitz Citation2000).
The new developments and durable non-wovens from recycled fibre materials were used in automotive interior applications. The multiple uses of recycled fibre products are presented to show how they are moving out of their traditional role as sound absorbers and into new applications and new markets (Cai et al. Citation2021; Wyerman Citation2010).
Non-wovens can be used in the automotive industry for a variety of purposes due to their following advantages: lightweight, sound efficiency, flexibility, versatility, easily tailored properties, mouldability (easiness to conform to irregular shapes), recyclability, and low process and materials costs, as well as attractive cost per performance ratio (Karthik and Rathinamoorthy Citation2017; Tejyan et al. Citation2019; Tejyan Citation2021).
Porous materials have been widely accepted as sound absorptive materials. Different papers review and describe that the sound absorption behaviour of porous materials can be affected by the physical properties of materials like fibre type, fibre size, material thickness, density, air flow resistance and porosity. The sound absorption property of different fibrous materials was experimentally tested. The relationship between the sound absorption, air flow resistance, material thickness, air gap and attachment film was studied. The higher air flow resistance always gives better sound absorption values, but for frequencies higher than 1000 Hz, the sound absorption has less values due to the difficulty in movements of sound waves through the materials (Seddeq et al. Citation2013; Taşcan Citation2016).
The objective of this study is to develop an efficient sound-absorbing textile material by recycling selvage textile wastes. The absorption properties of different materials were studied by different researchers, but not selvage textile waste materials. In this study, selvage waste textiles are used for developing a functional sound-absorbing material.
2. Materials and methods
2.1. Raw material
The cotton selvedge waste as shown in is the raw material from 100% cotton woven fabric-producing companies. These selvedge wastes are collected and segregated based on their counts of the yarn and are prepared for recycling to the next process in the recycling machine. The fabric opening machine having specification shown in recycles the waste and produces a textile fibre. The carding machine converts the produced fibre into a web structure with different areal densities. Finally, a stitching machine is used to produce a stitch-bonded non-woven sample.
Table 1. Selvedge opening machine specification.
2.2. Processing
2.3.1. Web formation
In the process of developing, non-woven web formation is the first step (Wu et al. Citation2022). In this study, the manufactured fibre from selvedge wastes was processed in the carding machine with process variables shown in for the formation of fibre web. Carding is the mechanical process in which the fibres are held by one surface, while the other surface combs the fibres causing individual fibre separation as shown in . The main objectives of carding are to begin the process of parallelisation, to separate small tufts into individual fibres and to deliver the fibres in the form of a web.
Table 2. Carding machine specification.
2.3.2. Non-woven bonding
The bonding process interlocks preferentially arranged fibre or film assemblies by mechanical, chemical, solvent and/or thermal means (Li et al. Citation2021). Stitch-bonding is a process by which fibre webs and/or yarns are bonded together by stitching with a continuous filament or staple yarn, creating a series of loops that hold the web together (Saad et al. Citation2018). Stitching machine specifications are shown in . Non-woven samples were produced with different areal densities of 310, 355, 405, 496, 680, 711, 750 and 797 GSM.
Table 3. Stitching machine specifications.
2.3.2.1. Stitching yarn
Polyester/cotton core spun sewing thread is used in this study with a count of 60 Tex. This thread is strong and has excellent sewability. Core spun threads have good elasticity and a high resistance to heat and shrinkage.
2.3.2.2. Stitch density
The stitch was applied in both directions with a constant stitch density of 10 stitches per inch (SPI).
2.3.2.3. Base fabrics
Plain structured woven base fabrics are used in this study to hold the web and improve the strength of the non-woven. The areal density of plain fabric is 200 GSM.
2.3. Testing methods
2.3.1. Methods of testing the physical property of non-wovens
This article presents the identification of factors that influence the sound absorption coefficient of porous materials used for absorption of the sound wave. To achieve this, researchers used three materials (glass wool, flexible polyurethane foam and rigid polyurethane foam) for which the sound absorption coefficient was determined using the impedance tube and analysed the influence of the thickness, density and structure of these materials on the sound absorption coefficient (Seddeq and Sciences Citation2009). The physical properties of non-wovens tested with their test equipment and the standard are listed in .
Table 4. Physical property tests.
2.3.1.1. Fabric thickness
Thickness is one of the important parameters affecting the sound absorption. If the acoustics impedance at the surface of the textile structures matches that of the medium, the sound is not reflected back to the medium, then the thicker the structure is, the larger its sound absorption will be. The latest MESDAN LAB thickness tester was employed, which has a maximum capacity of 10 mm and an accuracy of 0.01 mm. The average fabric thicknesses of the samples were calculated for all samples.
2.3.1.2. Areal density
The density of a material indicates the mass concentration of the material, which is measured as mass per unit volume. In the case of porous structures, the bulk density plays an important role in acoustic absorption. First, samples were prepared by cutting 5 cm by 5 cm and weighing by using electronic weighing balance, and the results were recorded in grams. Finally, the fabric areal densities were calculated by using Equationequation 1(1)
(1) . The average areal density of the produced samples was calculated as follows:
2.3.1.3. Air permeability
The airflow resistances of materials greatly influence the acoustic absorption of a porous material. The interlacement of threads in a woven structure or intermeshing of fibres in a non-woven structure provides a resistance to the passage of air, which is an intrinsic property of the textiles. The fast, simple and accurate FX 3300 Air Permeability Tester III was used in this study. The average air permeability of the prepared eight samples was calculated.
2.3.2. Impedance tube method for sound absorption
A sound source was mounted at one of the impedance tube ends, and the non-woven was placed at the other end. The schematic diagram of the impedance tube set-up is shown in . The sound source generates random sound, and the sound propagates as planar waves in the tube, hits the sample and gets absorbed. The standing wave interference pattern is observed due to the superimposition of forward and backward travelling waves inside the tube. The sound pressure at two fixed locations was measured by using a two-channel digital frequency analyser (Takahashi, Otsuru, and Tomiku Citation2005; Taşcan Citation2016). The impedance tube method determines the sound absorption coefficient of the non-woven samples by the ASTM E 1050 standard. The tube set-up with a diameter of 30 mm measures the parameter of sound in the frequency range from 0 Hz to 3000 Hz. In this article, the frequency level range was 0 Hz, 500 Hz, 1000 Hz, 1500 Hz, 2000 Hz, 2500 Hz and 3000 Hz.
A sound of particular decibel was created by the sound source, and the receipt decibels were measured by the decibel metre with and without the sample. The sound insulation by the fabric samples can be calculated using Equationequation 2(2)
(2) ,
where SRisthe sound reduction, dBwos is the sound level without the sample and dBws is the sound level with the sample.
The arithmetic average of sound absorption over seven frequencies, 0 Hz, 500 Hz, 1000 Hz, 1500 Hz, 2000 Hz, 2500 Hz and 3000 Hz, for the prepared eight samples was calculated by using Equationequation (3)(3)
(3) ,
The sound absorption coefficient of each specimen should be tested at least twice.
3. Results and discussion
The waste selvage was opened, the carded webs were stitched, and finally, the produced stitch-bonded non-woven is shown below. shows the production steps from selvedge waste to the final stitch-bonded non-woven samples.
3.1. Sound absorption coefficient of samples by the impedance tube test method
Depending on the types of materials and products, the measurement methods for sound absorption coefficient were varied. In this research, we used one of the most widely used methods to determine the acoustic properties of materials called the impedance tube method. The tube set-up has a diameter of 30 mm, and the frequency ranges from 0 Hz to 3000 Hz. The frequency levels are 0 Hz, 500 Hz, 1000 Hz, 1500 Hz, 2000 Hz, 2500 Hz and 3000 Hz. A sound of particular decibel was created by the sound source, and the receipt decibels were measured using the decibel metre with and without the sample. The sound absorption coefficients of the samples with different frequencies are shown in .
Table 5. Sound absorption coefficients of stitch-bonded non-wovens.
shows the sound absorption coefficient of non-woven samples with various frequency levels. From and , it can be observed that the increment in frequency increases the sound absorption coefficient in all samples. Similarly, the increment in thickness increases the sound-absorbing property of the samples.
The sound absorption coefficient value ranges from 0 to 1. If the sound absorption coefficient value is 0.5, this means that 50% of incident sound waves are absorbed. If the coefficient is zero, there is no incident sound wave absorption, and if the sound absorption value is 1, this means that 100% of incident sound wave is absorbed (Sakthivel Citation2021).
With the highest frequency level of 3000 Hz, the SAC values of Sample#1, Sample#2, Sample#3, Sample#4, Sample#5, Sample#6, Sample#7 and Sample#8 are 0.42, 0.53, 0.64, 0.76, 0.83, 0.87, 0.89 and 0.93, respectively. The maximum absorption of samples can be 93% of incident sound.
3.2. Physical property test results of non-woven samples
This article presented the identification of factors that influence the sound absorption coefficient of porous materials used for absorption of the sound wave. The sound absorption coefficient using the impedance tube was influenced by thickness, density and air permeability property of the materials (Hassan et al. Citation2021; Paul, Mishra, and Behera Citation2021). The test results for physical properties influencing the sound absorption efficiency of selvedge recycled stitch-bonded non-woven are given in .
Table 6. Physical properties of non-wovens samples.
3.3. Influence of the fabric thickness on sound absorption
From , we can understand that the thicknesses of samples have direct relationships with the sound absorption property of samples. The sound absorption increases with the thickness of the sample (Hassan et al. Citation2021). The absorption value increases with the low frequency level than with the high frequency level, because at low frequencies, there is a high increment of sound absorption. If the thickness of the material gets high, the sound absorption decreases as shown in . However, at higher frequencies, the thickness has an insignificant effect on sound absorption. shows that the thicker the material, the better the sound absorption values on the middle value of the thickness of the sample.
3.4. Influence of fabric areal density on sound absorption
shows that the sound absorption coefficient of the sample increases with increasing fabric areal density. The sound absorption property of samples has a direct relationship with the areal density (Hassan et al. Citation2021). With the higher fibre content and fibre friction, the absorption improved. The result revealed that less density of fibre with more open structures absorbs sound of low frequencies of about 500 Hz. Relatively dense structures have better absorption for frequencies above 2000 Hz.
3.5. Influence of fabric air permeability on sound absorption
shows that air permeability of samples decreases with increasing sound absorption of samples. The air permeability has an inverse relationship with sound absorption (Hassan et al. Citation2021). The result reveals that better sound absorption values were performed with the increasing airflow resistance. The high increase in air flow affects the sound absorption property of the sample. The variations of the sound absorption value of the samples were insignificant beyond a frequency of 2000 Hz.
4. Conclusion
Eight non-woven samples were produced from 100% cotton woven fabric selvedge waste, and the sound absorption property and influencing factors were tested based on their standards. The study revealed that the sound absorption coefficient of all samples increases with the increasing frequency level. The produced non-woven samples can efficiently absorb sound up to a maximum sound absorption coefficient of 0.93 at a frequency of 3000 Hz. The increment in thickness has a direct relationship with low frequency, but at the highest frequency, the absorption was insignificant. The absorption increased with fabric area density. Less dense samples are more effective at low frequency, and highly dense samples better absorbat a frequency level above 2000 Hz . High air permeability affects the sound absorbing performance of non-woven, and it was inversely proportional. Different textile companies are looking for applying alternative materials for their products and seeking new markets. In order to create a sustainable society, it is necessary to develop effective utilisation of all sorts of wastes.
Data availability
In this work, all the relevant data have been included; if you want additional data, you can communicate with the corresponding author.
Acknowledgments
We are grateful to the Ethiopian Institute of Textile and Fashion Design Technology and Wolkite University Textile Engineering Department, Ethiopia.
Disclosure statement
No potential conflict of interest was reported by the author(s).
Additional information
Notes on contributors
Temesggen Feleke Fera
Temesggen Feleke Fera received his BSc and MSc degree in Textile Engineering and Textile Manufacturing from the Ethiopian Institute of Textile and Fashion Technology, Ethiopia. He is currently a senior lecturer at the Department of Textile Engineering, Wolkite University (WKU), Ethiopia. His research interests include; Textile production, Textile waste recycling, Technical textiles, Textile composites, Waste management, Product development, and Additive manufacturing. The author is a reviewer for international journals and published research articles.
Yerdaw Zeleke
Yerdaw Zeleke is currently working in the Department of Textile Engineering, Wolkite University, Ethiopia. He completed his BSc and MSc degree in Textile Manufacturing and Textile Manufacturing from Ethiopian Institute of Textile and Fashion Technology, Ethiopia. His research interest includes; Textile Manufacturing, Composite materials, Functional composites, Textile Materials, Technical textiles, and Engineering materials. He participated on so many scientific conferences and presented papers. The author is a reviewer for international journals and published research articles.
Yohannes Girmay
Yohaness Girmay is an active academic staff in department of Fashion Design, Wolkite University, Ethiopia. He received his BSc and MSc degree from the Ethiopian Institute of Textile and Fashion Technology in Fashion Design and Fashion Technology. His research interest includes; Fashion Designing, Traditional Fabric modification, Product development, and design, and Influences on the fashion industry and future fashion. He is a reviewer, advisor, and published research articles.
References
- Akdeniz, R., H. Z. Özek, and G. J. T. Durusoy, Apparel. 2017. “A Study of Selvedge Waste Length in Rapier Weaving by Image Analysis Technique”. Textile and Apparel. 27(1): 22–26.
- Al-Mutairi, N., F. Al-Rukaibi, and P. J. Koushki. 2009. “Measurements and Model Calibration of Urban Traffic Noise Pollution.” American Journal of Environmental Sciences. 5 (5): 613.
- Bartl, A., and I. Marini 2008. “Recycling of Apparel”. na.
- Bartl, A. 2009. “Fiber Recycling: Potential for Saving Energy and Resources”. na.
- Bhatia, D., A. Sharma, and U. Malhotra. 2014. “Recycled Fibers: An Overview.” International Journal of Fiber and Textile Research 4 (4): 77–82.
- Cai, Z., M. A. Al Faruque, A. Kiziltas, D. Mielewski, and M. J. M. Naebe. 2021. “Sustainable Lightweight Insulation Materials from textile-based Waste for the Automobile Industry.” Materials (Basel, Switzerland) 14 (5): 1241. doi:10.3390/ma14051241.
- Crocker, M. J. 2007. Handbook of Noise and Vibration Control. John Wiley & Sons.
- Dalton, B. H., and D. Behm. 2007. “Effects of Noise and Music on Human and Task Performance: A Systematic Review.” Occupational ergonomics. 7 (3): 143–152.
- Fang, Y., Z. Lianying, Z. Chentian, X. Guofu, and C. J. Cao. 2021. “Discussion on Structure and Utilization Plan of Weaving Waste Selvage.” Cotton Textile Technology. 49 (592).
- Gong, X., X. Chen, and Y. Zhou. 2018. “Advanced Weaving Technologies for high-performance Fabrics.” In High-Performance Apparel, 75–112. Elsevier.
- Hassan, T., H. Jamshaid, R. Mishra, M. Q. Khan, M. Petru, M. Tichy, and M. J. T. Muller. 2021. “Factors Affecting Acoustic Properties of natural-fiber-based Materials and Composites: A Review.” Textiles. 1 (1): 55–85.
- Hawley, J. M. 2006. “Textile Recycling: A Systems Perspective.” In Recycling in Textiles. UK: Woodhead Publishing Limited.
- Jurasz, J. J. F., and T. Europe. 2000. “Assessment, Choice and Utilisation of Selvedge in non-classical Weaving.” Fibres & Textiles in Eastern Europe. 8 (2): 50–53.
- Karthik, T., and R. Rathinamoorthy. 2017. Nonwovens: Process, Structure, Properties and Applications. WPI Publishing.
- Kovaceyic, S., and J. J. T. Hadina. 2001. “The Impact of Warping Mistakes on Forming Fabric Selvedges.” Tekstil. 50 (4): 159–163.
- Legler, F. J. 1999. “New Technology to Reduce Yarn Wastage.” Sulzer Technical Review. 1 (99): 17.
- Li, J.-H., B.-C. Shiu, C.-W. Lou, J.-C. Hsieh, W.-H. Hsing, and J. Lin. 2021. “Mechanical Properties of needle-punched/thermally Treated non-woven Fabrics Produced from Recycled Materials.” The Journal of The Textile Institute. 112 (1): 23–29.
- Mozafary, V., and P. J. Payvandy, Polymers. 2019. “Online Control System Design for Selvedge Waste Length in Rapier Weaving Loom”. Journal of Textiles and Polymers. 7(2): 73–80.
- Paul, P., R. Mishra, and B. J. Behera. 2021. “Acoustic Behaviour of Textile Structures.” Textile Progress. 53 (1): 1–64.
- Pensupa, N., S.-Y. Leu, Y. Hu, C. Du, H. Liu, H. Jing,and C. T. Valorization. 2017. “Recent Trends in Sustainable Textile Waste Recycling Methods: Current Situation and Future Prospects.” 189–228.
- Qiu, X. 2016. “Principles of Sound Absorbers.” In Acoustic Textiles, 43–72. Springer.
- Qureshi, S. A., M. R. Kumar, and C. J. Prakash. 2021. “Design and Development of a Novel Mechanism for the Removal of False Selvedge and Minimization of Its Associated Yarn Wastage in Shuttleless Looms.” Autex Research Journal. 21 (4): 352–362.
- Rabinowitz, P. 2000. “Noise-induced Hearing Loss.” American Family Physician 61 (9): 2749–2756.
- Roy, A., and H. Rahman. 2014. Study on Selvedge Wastage in Rapier Loom. Daffodil International University.
- Saad, M., M. F. Nasr, H. A. Yassen, and G. J. Turky. 2018. “Electrical and Dielectric Properties of Stitched non-woven Engineered Fabrics Containing Activated Carbon Fiber.” Egyptian Journal of Chemistry. 61 (3): 559–568.
- Sakthivel, S. J. A. A. 2021. “Studies on Influence of Bonding Methods on Sound Absorption Characteristic of polyester/cotton Recycled Nonwoven Fabrics.” Applied Acoustics. 174: 107749.
- Seddeq, H. S., and A. Sciences. 2009. “Factors Influencing Acoustic Performance of Sound Absorptive Materials.” Australian Journal of Basic and Applied Sciences. 3 (4): 4610–4617.
- Seddeq, H. S., N. M. Aly, A. Marwa, and M. Elshakankery. 2013. “Investigation on Sound Absorption Properties for Recycled Fibrous Materials.” Journal of Industrial Textiles 43 (1): 56–73. doi:10.1177/1528083712446956.
- Stanescu, M. D., and P. Research. 2021. “State of the Art of post-consumer Textile Waste Upcycling to Reach the Zero Waste Milestone.” Environmental Science and Pollution Research International 28 (12): 14253–14270. doi:10.1007/s11356-021-12416-9.
- Takahashi, Y., T. Otsuru, and R. Tomiku. 2005. “In Situ Measurements of Surface Impedance and Absorption Coefficients of Porous Materials Using Two Microphones and Ambient Noise.” Applied Acoustics 66 (7): 845–865. doi:10.1016/j.apacoust.2004.11.004.
- Taşcan, M. 2016. “Acoustical Test Methods for Nonwoven Fabrics.” In Acoustic Textiles, 115–141. Springer.
- Tejyan, S., T. Singh, A. Patnaik, G. Fekete, and B. Gangil. 2019. “Physico-mechanical and Erosive Wear Analysis of Polyester fibre-based Nonwoven fabric-reinforced Polymer Composites.” Journal of Industrial Textiles. 49 (4): 447–464.
- Tejyan, S. 2021. “Effect of Erosive Parameters on Solid Particle Erosion of Cotton fiber–based Nonwoven mat/wooden Dust Reinforced Hybrid Polymer Composites.” Journal of Industrial Textiles. 15280837211064241.
- Vasile, S., and L. Van Langenhove. 2004. “Automotive Industry a High Potential Market for Nonwovens Sound Insulation.” Journal of Textile and Apparel, Technology and Management 3 (4): 1–5.
- Velosa, J., R. Fangueiro, N. Martins, M. Fernandes, and F. Soutinho. 2013. “Waste Fiber Reinforced Composite Materials: Production and Mechanical Properties”. Paper presented at the Materials Science Forum.
- Wu, X., H. Shao, J. Cheng, and D. J. F. Kang. Polymers, “Preparation of Non-woven Fabric Reinforced Poly (Vinylidene Fluoride) Composite Membranes for Water Treatment.” Fibers and Polymers. 1–9, 2022
- Wyerman, B. 2010. “New Frontiers for Fiber-Based Noise Control Solutions.” Sound and Vibration 44 (10): 14.
- Yalcin-Enis, I., M. Kucukali-Ozturk, and H. Sezgin. 2019. “Risks and Management of Textile Waste.” In Nanoscience and Biotechnology for Environmental Applications, 29–53. Springer.