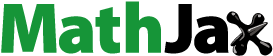
ABSTRACT
Design Thinking is a user-centred framework that captures unmet needs of users and generates ideas for sustainable solutions. Quality Function Deployment is a tool that translates the voice of customers into engineering attributes required for product and process design. Both concepts are globally adopted in various fields including but not limited to; manufacturing industries, business and service sectors, education, research, health care and social innovation. This study aims to propose a methodological framework that combine principles from user-driven ideation and customer-focused product/process design for the development of a sustainable solution in the context of small-scale agricultural community. The framework is validated with a case study at a learning community centre in Thailand. The machine was built with functions that allowed it to shred plants and mix the fertiliser simultaneously which was well accepted and sustainably used in the community. A policy recommendation based on this study is when working with community-based problems, the designers should immerse themselves with the community to completely understand the problem and solution context. A co-creation between the designers and the community users is encouraged to obtain impactful solutions. Local resources and accessible technology should be taken into account to reassure an effective and sustainable solution.
1. Introduction
Food security, sustainable food products and healthy lifestyles are some of the rising trends within global consumption. This is an area Thailand excels at, with its natural advantages and rich environmental resources, making agriculture one of the largest industries in Thailand (Agricultural in Thailand, Citation2023). In order to sustain this industry, it is important that the younger generation of farmers are retained, to continue to pursue their farming careers, as well as educating the new generation on the basics of agriculture and its importance (Jansuwan, Zander, and Ustaoglu Citation2022).
Banerjee and Puneka (Citation2020) stated that the lack of appropriate agricultural machinery and labour shortages led to higher farming costs and decisions to quit farming careers. This led to an increase of migration to cities and caused burden on the infrastructure. Although using agricultural machines produce higher outputs at the cost of less time and labour, the high selling price is a factor that affects the farmer’s buying decision (Mbosso et al. Citation2015). A wrong purchasing decision from a lack of knowledge led to an under-utilisation of the agricultural machinery. Therefore, the design and development of smaller, more affordable machinery is in high demand especially for small scale and low-to-medium income agricultural communities (Karthigayan et al. Citation2021; Matharu, Mulla, and Nadaf Citation2021; Pare and Aman Citation2019).
There are literatures in a field of a small-scale agricultural machinery design and development. Shahadan et al. (Citation2022) developed a semi-automatic organic fertiliser processing machine for small and medium industries that can be operated with one worker, with decreased cycle time and increased outputs. Pawar et al. (Citation2017) designed and fabricated a low cost, small-scale and low power consumption liquid fertiliser making machine that reduced the labour intensive method for villagers in Indonesia. Ambade et al. (Citation2022) developed food waste shredding machines for making organic fertilisers. These machines are all engineering-centric, focusing solely on the efficiency or success in executing its function. Challenges found within community-based farms include the lack of economic and cultural understanding, as well as the mismatch between the designer’s solutions and the real needs of the community (Nieusma and Riley Citation2010). The previously mentioned machines may be highly efficient; they are designed by engineers. As stated by Nieusma and Riley (Citation2010) that engineers focus too heavily on technology, they are lack consideration for users’ needs and involvement. This may deter said users from using engineering-centric machines due to the intimidation and uncertainty users may feel, with no clear understanding of how the machine operates or how it can be maintained. The machine may not necessarily provide a proper solution to the specific problems the user hopes to fix, leading to the machine being left unused.
Kristian (Citation2014a) suggested an application of the Design Thinking concept where the designers immerse themselves into the ecosystem of the community. Thus, they gained an understanding of the local’s lifestyle, culture, knowledge and skills, and were able to develop appropriate solutions. Burra et al. (Citation2003) mentioned that a collaboration with the community leads to more impactful solutions. Design Thinking (DT) is an integrative human-centric approach to create ideas and solutions that regard feasible technology and business viability (Brown Citation2008; Mueller-Roterberg Citation2018). Design thinking serves as a tool that enables and promotes innovation and social transformation. Soh and Kristian (Citation2014) shared ideas on a transnational social innovation programme amongst ASEAN institutions. The programme implemented DT concepts to discover the unmet needs of the community. The ideas and solutions were then developed and co-created with the community stakeholders (Soh Citation2011; Soh and Kristian Citation2014). As suggested by Mattson and Wood (Citation2014), an immersion of the designer in the local community allow them to fully understand the problem and solution context. The local community can continue developing the final concept by using available and sustainable local resources and technology (Brown and Wyatt Citation2010; Kristian Citation2014b).
Gherardini et al. (Citation2017) proposed a user-centred design methodological framework and implemented successfully with small and medium enterprises in Italy. In addition, they implemented Quality Function Deployment (QFD), a method that translates the customer voice into technical requirements. By involving users throughout the design phases, they found that the design of injection-moulded housing and the related interfaces of a biomedical electronic device were achieved with a reduction of uncertainty and development time. QFD is applied globally in many manufacturing industries and service sectors including government, banking, health care, education and research (Chan and Wu Citation2002). García-León et al. (Citation2021) implemented QFD to translate the customer requirements into detailed requirements for designing a low-cost, eco-friendly, versatile, high performance and practical cocoa pulping machine in Colombia. The machine benefited farmers by reducing cutting-pulping time, improving resource efficiency while obtaining high quality products.
Although there are several researches on DT and QFD and their applications in various fields, limited studies have worked on integrating both DT and QFD especially in agricultural machinery design and development. The insight needs of the users from DT can be translated systematically with QFD to identify technical attributes. This study aims to propose a methodological framework that combine principles from user-driven ideation (DT) and customer-focused product/process design (QFD) for the development of a sustainable solution in the context of small-scale, low-and-middle income agricultural communities in developing countries considering available and sustainable local resources and technology.
2. Methodological framework
A DT-QFD methodological framework for agricultural machinery design and development is proposed as displayed in .
Figure 1. A proposed DT-QFD methodological framework.
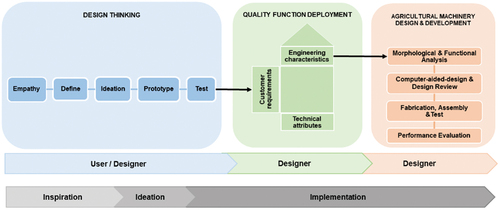
2.1. Phase 1: generate solutions using DT concept
displays the DT concept which includes 5 steps. The Empathy step aims to fully understand the community stakeholders. The designer immerses themselves by living with the community and observing lifestyles and cultures by participating in activities, as well as engaging with the villagers by interviewing them on the agricultural processes. The Define step aims to gain a clear point of view from the community stakeholders. This is performed by transcribing qualitative data from the empathy stage, clustering data, finding insights and the deeper needs of the community. A Need statement is generated to reflect the issues the community faces. The Ideation step intends to generate a large number of possible solutions using a brainstorming technique. The brainstorming process encourages the building of ideas as a collective to generate wild and innovative solutions. A decision matrix is applied to evaluate, combine and shape a final concept.
Figure 2. Design Thinking process.
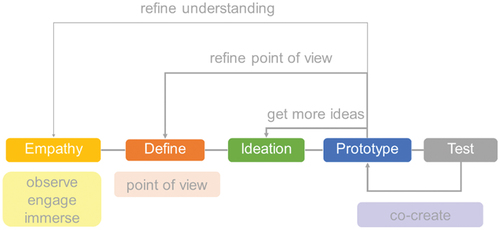
Prototypes were widely used to transfer ideas into concepts which serves as a medium to share and test with the real users (Kelley and Kelley Citation2013; Kleinsmann, Valkenburg, and Sluijs Citation2017). There are several types of prototypes, such as, a story board, user journey, role play, etc. Coulentianos et al. (Citation2020) found that physical prototypes enhanced stakeholder engagement in the real use environment and developed long-term relationships with community partners. The physical prototypes are built based on the final concept. The test step is carried out by presenting the findings from the DT process and proposing solutions. The prototypes are presented as a medium that allowed the stakeholders to visualise the solution in its real use environment, leading to discussions and feedback to the designers. This also stimulates the stakeholders to co-create the solutions for the best fit with the community. This step is a key process that generates a deeper understanding of the unmet needs (Ramos et al. Citation2016) and collaboration amongst all stakeholders (Duarte, Lulham, and Kaldor Citation2011; Luotola et al. Citation2017).
2.2. Phase 2: determine technical requirements with QFD technique
There are several methods that are applied to translate user needs into product requirements; namely, an Axiomatic design, a Function-Behavior-Structure framework, a Kansei Engineering technique, a Product Attribute Function Deployment, and a Quality Function Deployment. Among these existing methods, the QFD technique is widely used and mostly applied with the small to medium enterprises due to its ease of use (Gherardini, Renzi, and Leali Citation2017). Cristiano et al. (Citation2001) surveyed more than 400 companies and found that QFD provides a comprehensive, systematic approach to ensure that new products meet or exceed customer expectations. QFD is a customer-oriented process that the voice of customer carefully analysed in the development process. It is a common method for designers and engineers and encourages a cross-functional team to work closely with the customer. It can support sustainable product-service systems conceptual design and extend to different context of use (Sousa-Zomer and Miguel Citation2017). Sengazani Murugesan et al. (Citation2020) found that QFD offers cost, time and quality improvement in sustainable design. QFD translates the customer requirements into technical characteristics for each stage of product development and production (Sullivan Citation1986). The Akao model is a well-known application of QFD that creates a template called a House of Quality (Akao Citation1990). The customer requirements are translated into technical characteristics. The relationships between customer needs and technical attributes are systematically deployed in order to develop the product, process or quality plan that answers to the voice of the customer. There are 6 steps in applying QFD as shown in .
Figure 3. Qualify Function Deployment (QFD) or House of Quality (HoQ) template.
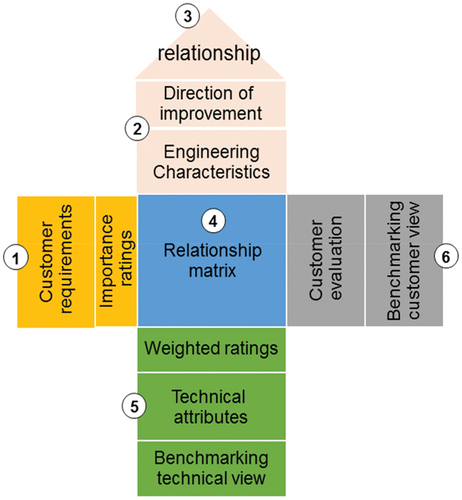
Step 1 determines what the customer requirements are. The output from the DT process was used to define the customer requirements. The list of customer requirements was documented as a survey and asked the students at the school to fill out the survey form. A Likert-scale rating score of 1 to 5 was used, where 5 means the most important and 1 means the least important. The average score was calculated and put into the HoQ template based on the importance ratings.
Step 2 identifies engineering characteristics that directly respond to and satisfies the customer requirements. The direction of improvement for each engineering characteristic is given by using the symbols of an upward arrow (↑), a downward arrow (↑) and a circle (〇). The upward arrow means that the engineering characteristic can be improved by increasing the technical attribute target value. On the other hand, the downward arrow represents a decrease of that technical specification as a direction of improvement.
Step 3 indicates the strength of the relationships between the different engineering characteristics. There are three types of symbols to be used; ⊙ for a strong relationship, 〇 for a moderate relationship and for a weak relationship.
Step 4 evaluates each of the customer requirements against the engineering characteristics. The relationship matrix is formed to evaluate how well the engineering design responds to the voice of the customer. The three symbols from step 3 are also used in this step.
Step 5 identifies the technical attributes and specification target value based on the engineering characteristics. The weighted ratings are calculated by assigning scores (⊙ = 5, 〇 = 3, • = 1) to each entry in the relationship matrix and multiplying by the customer’s importance rating. Then, the percentage of each weighted rating is calculated. The highest value/percentage represents the most critical engineering characteristic and technical attribute when developing the product. The technical attributes are identified with specification target values, followed by technical view benchmarking against competitors’ designs
Step 6 benchmarks the own design with other designs, with consideration to the customer’s view. Three abbreviations are used for this step; G = good, F = fair and P = poor.
2.3. Phase 3: machinery design and development
The output from QFD is transferred as part of input information to generate a design for the agricultural machinery design. This stage involves multiple steps as shown in . Morphological analysis is a popular method for measuring plant characteristics such as length, width, and ratios (Chuanromanee, James, and Ryan Citation2019). Morphological analysis on parts of plants are performed to identify the appropriate size of the machinery parts.
Figure 4. Machine design and development process.
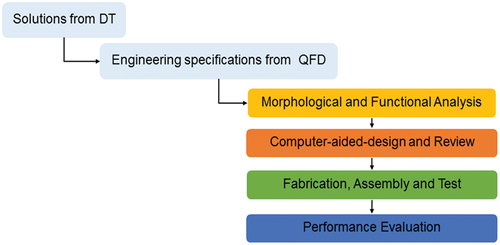
Functional analysis is a basic tool for designers to create conceptual designs and its elements. Functional analysis is widely used to define a product’s functional requirements and list its necessary physical components. A functional tree represents a product that considers functional views from the top level into lower level functions (Viola et al. Citation2012). The functional analysis was carried out based on the availability of the community’s resources and technology.
The 3D CAD software is widely used to generate 2-dimensional and 3-dimensional machinery parts, sub-assemblies and the final product. A design review is carried out to list all purchasing materials and parts for the next step. The machine parts are then fabricated and assembled into a final machine. The evaluation of machine performance is performed to evaluate its efficiency.
3. A case study
3.1. Participating community
Agricultural learning centres and school programmes play a significant role in cultivating positive attitudes towards agricultural careers. Within school farms, the students learn about the process of seedling, planting and harvesting their own organic produce. Additionally, the crops from the school farms can be used as ingredients to supply the school canteen. The students can then apply what they have learned to their daily life, allowing them to understand the benefits and values of agriculture (Saduak et al. Citation2016). Agricultural learning centres are part of self-sufficient community learning centres under the Thai national education policy. The community learning centres focus on developing occupational skills and increasing knowledge of agricultural practices (UNESCO Office Bangkok and Regional Bureau for Education in Asia and the Pacific Citation2008).
An agriculture learning centre at Bo Ngern community is located inside Soontharomattaprachasun School, Ladlumkaew district, Pathum Thani province. The school is one of the leading academic schools in regards to sufficiency economy philosophy which is attributed to the late King Bhumibol Adulyadej (King Rama IX the Great). To educate and motivate young students towards organic farming, the school provides an organic fertiliser club as an extracurricular activity. The students who join the club are 12–16 years old and mostly come from farming families. The club runs every school day in the afternoon. The organic fertiliser making process is shown in . The students collect water hyacinths and banana sheaths around the school area, manually chopping them into small pieces. The next step is to mix fertiliser ingredients including; chopped water hyacinths, chopped banana sheaths, fallen leaves, cow manure, rice husk, rice husk ashes and enzyme water. All ingredients are mixed manually with shovels and left for decomposition. The fertiliser is used by the school farm and is also put on sale for the villagers in the community.
Figure 5. The organic fertiliser making process at the school agricultural learning center.
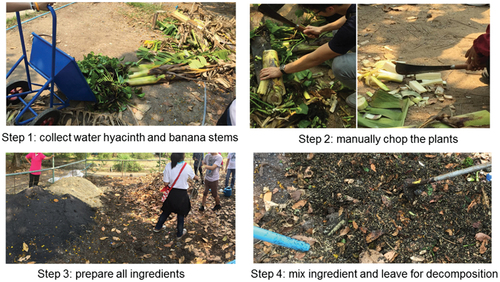
3.2. Outcomes of DT process
The engagement and immersion with the community allowed the designers to fully understand the students’ difficulties when making the organic fertiliser. shows snapshots of the interviewing and data clustering at the school agricultural learning centre. The Empathy study found that the preparation of the organic fertiliser’s ingredients required a lot of manpower and strength. The water hyacinths and banana sheaths were difficult to chop manually with hand tools. The students found this lengthy process very tedious and the smell of the fertiliser was unpleasant. The ingredients required a lot of time and effort to be well mixed. It was found that the user’s pain points were the heavy workload, time consuming process and inconvenient location of raw materials.
Figure 6. Interviewing and data clustering activities at the learning center.
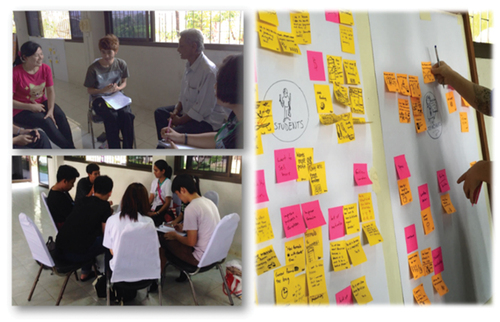
The main users of this study were the school students who participate in the organic fertiliser club as part of their extracurricular activities. Joining the club made them proud as contributors to the school. The Define stage indicated their insights and deep needs were motivation and an efficient process. They needed better tools and facilities to motivate and inspire them to continue to join the club and make more organic fertilisers.
The Ideation stage resulted in generating a large amount of ideas. Ideas were grouped, re-arranged, combined and categorised. A decision matrix was carried out by evaluating their impacts on solving the problem and their feasibilities for real application. The group then voted on the best ideas to develop the final concepts. shows the result from the ideation stage.
Figure 7. Outcome from the ideation stage.
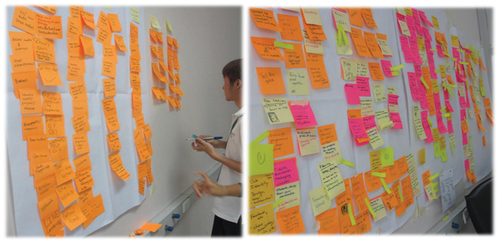
The final concepts were a plant cutting machine and an organic fertiliser mixing machine. The physical prototypes were made from recycled materials. A half-day meeting with the community was arranged where the DT findings and prototypes of proposed solutions were presented to the users. After the presentation, the users gave feedback on the ideas and recommended what needed to be improved. This co-creation between the users and the designers led to an improved version of prototypes as shown in . In addition, the user suggested combining two separated machines into one multi-function fertiliser making machine.
3.3. QFD results
3.3.1. Determine customer requirements and importance ratings
The data retrieved from the in-depth interview and the output from the DT were converted into a customer requirements questionnaire. The survey was conducted by asking 10 representatives from the school club to fill out the form. Average scores were then calculated. The maximum score was 5.0 which meant the most important. displays the list of customer requirements and their ratings. The results show that the top requirements with high scores were that the machine can chop both water hyacinths and banana sheaths (4.7), easily operated (4.6), does not require electricity (4.5) and inexpensive (4.5).
Table 1. Customer requirements and importance ratings.
3.3.2. Determine engineering characteristics and direction of improvement
The customer requirements were translated into engineering characteristics. This step determined how well the customer needs were met. displays the engineering characteristics and the direction of improvement. Sharp cutting blades are needed to answer the ‘chop water hyacinth and banana sheath’ requirement. This required a direction in improvement towards increasing the sharpness of the blades. An easily operated machine is determined by the amount of steps required to run the machine. The direction for improvement was to minimise the number of steps. A gasoline engine was selected to respond to the ‘does not require electricity’ requirement. The cost to develop a machine responded to the ‘inexpensive’ requirement where the direction of improvement was to minimise the costs.
Table 2. Engineering characteristics and direction of improvement.
3.3.3. Determine the relationships between the engineering characteristics
The relationships between the engineering characteristics were identified using three symbols (⊙ = strong, 〇 = moderate, and = weak) by the researchers as shown in . The number of machine elements had a strong relationship with the cost of the machine and a moderate relationship with the machine dimension. More machine parts make the cost to develop the machine higher and enlarges the machine dimension. The sharp cutting blades, the cutting system and number of blades had strong relationships with each other. Sharp blades resulted in a lower number of blades and an efficient cutting system. The mixing bin had a strong correlation with the mixing system and a moderate relationship with the machine dimension. Cover parts had weak relationships with the cutting system and the machine dimension. For the safety purposes, the feeding system needed to be covered.
3.3.4. Determine a relationship matrix between customer requirements and engineering characteristics
The relationship matrix was formed to evaluate how well the engineering attributes meet the customer needs using three symbols (⊙ = strong, 〇 = moderate, and = weak) as shown in . The number of steps to operate the machine answered to 2 customer requirements; easily operated (strong) and can feed the plant continuously (moderate). The sharp cutting blades responded to 3 customer requirements; can chop both water hyacinths and banana sheaths (strong), can chop plants into small pieces (moderate) and safe to operate (moderate). Other relationships can be explained similarly.
3.3.5. Identify weighted ratings, technical attributes and technical-viewed benchmarking
The weighted ratings are calculated as shown in . The sharp cutting blades got the highest values of 13.2% followed by a machine dimension (12.5%) and a number of blades (10.9%). These results represented the most critical engineering characteristics to consider when designing the machine. Next, the technical attributes are identified with target specification values. For example, 6-step was set to be the number of steps to operate the machine; (1) check the readiness of the machine, (2) turn on gasoline engine, (3) feed the plants to the feeding hopper, (4) put fertiliser ingredients in the mixing box and (5) take the fertiliser out, (6) turn off the engine.
The benchmarking with regards to the technical view is carried out to evaluate the own design with other similar designs available in the market. Machine A, a water hyacinth chopper developed by Kassanuk and Phasinam (Citation2019); and machine B, a water hyacinth shredding machine developed by Tapananont et al. (Citation1999); were used as the name of competitors in this analysis. Our machine had the most competitive advantage due to its multifunction design that both chops the plants and mixes the fertiliser. On the other hand, machine A and B were solely plant cutters without a fertiliser mixing function.
3.3.6. Evaluate and benchmark based on customer requirement
also displays the evaluation of the own design (our machine) and benchmark with other available machines with regards to the customer requirements. Three abbreviations are used for this step (G = good, F = fair, P = poor). The result showed that our machine can compete with other machines in terms of responding to the needs of customers. The complete HoQ (as shown in ) displays results from 6-step of QFD analysis.
3.4. Morphological analysis
A Morphological analysis on water hyacinths and banana sheaths was performed to design the cutting blade and the dimension of that machine’s elements. Water hyacinths are a free-floating invasive aquatic plant. It has negative impacts on the ecosystem. The plant has spongy inflated leafstalks (Dersseh et al. Citation2019). The shape is like a cylinder, the bottom width larger than the top width. The leaf is oval-shaped, waxy and thick. Banana trees are a large plant with tight-packed leaf sheaths and large leaves (Daniells Citation2003). In order to design the way the cutting blades penetrate, water hyacinth leafstalks and banana sheaths were harvested to measure the length, and the width at the top and bottom. shows the harvested leafstalks and sheaths. exhibits the average length and width of the sample plants.
Figure 10. Water hyacinth leafstalks and banana sheaths harvested for morphological analysis.
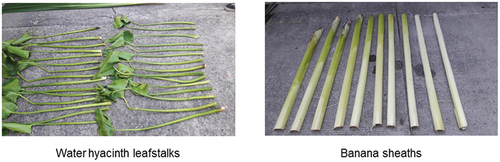
Table 3. Water hyacinth and banana sheath dimension.
3.5. Functional analysis
To obtain a community-based sustainable solution, functional analysis was carried out based on the availability of the community’s resources and technology. Therefore, advanced and complex parts were not included in the analysis. exhibits the functional tree from the functional analysis. The objective was to design a multi-function fertiliser mixing machine.
Figure 11. Functional tree analysis for winning concepts.
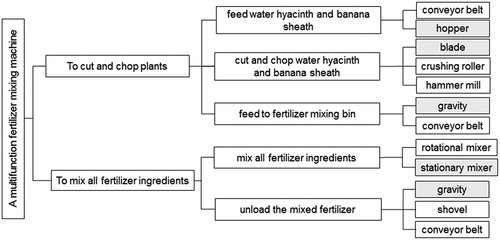
A top level represents two main functions; to cut and chop plants, and to mix all fertiliser ingredients. In order to cut and chop plants, the next functions involved with feeding water hyacinth and banana sheath in, cut and chop the plants, and feed them to the fertiliser mixing bin. The lowest level represented the alternatives that served such function. For example, to feed the plants into the machine, conveyor belt and hopper were good candidates. Alternatives were discussed, the more favourable choice based on the customer needs were selected (highlighted in grey).
3.6. Computer-aided design and a design review
The SolidWork 2018 was used to draw each machinery part, sub-assemblies and a finished machine in 2-dimensional and 3-dimensional views. exhibits the CAD drawings of the design details. The multi-function fertiliser mixing machine is powered by a 4-stroke, pull-start, 5.5 horse power gasoline engine. For the cutting system, the pulley drove the blade spindle shaft to rotate.
Figure 12. CAD drawings of parts, sub-assemblies and a machine.
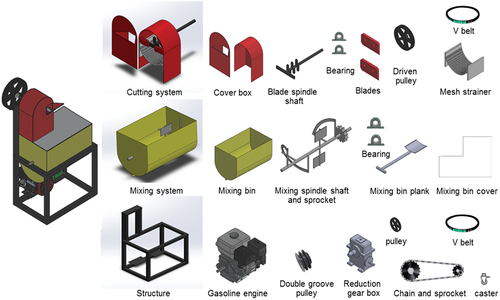
Figure 13. CAD drawing of the multi-function machine and its details.
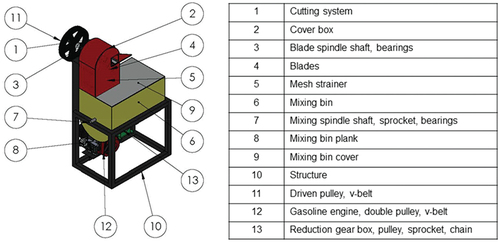
The water hyacinth or banana sheath was fed manually by the operator through the hopper. Two cutting blades cut and chop the plants. The fine-chopped plants go through the mesh strainer into the mixing bin. For the mixing system, the engine transfers the energy through pulley, v-belt, and a reduction gear box that is connected to the sprocket. The bottom sprocket drives the upper sprocket with a chain. The operator then opens the bin cover to load the fertiliser ingredients. For the mixing system, the mixing spindle shaft rotates and mixes all the fertiliser ingredients. After the ingredients are well mixed, the operator presses the off button to turn-off the engine. The operator opens the mixing bin plank at the bottom to unload the mixed fertiliser. The steel structure supports all parts of the machine.
3.7. Fabrication and assembly
Materials and parts to fabricate the machine are all available locally. The fabrication, assembly and test took place at the RMUTT machine shop. The finished machine is shown in . shows the materials, parts and components list.
Figure 14. The finished product – a multi-function fertiliser mixing machine.
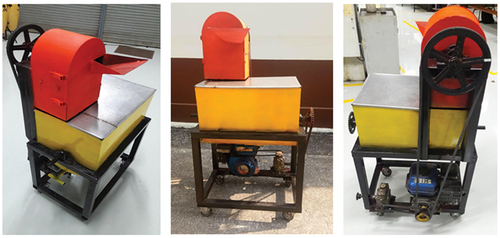
Table 4. Materials list.
3.8. Performance evaluation
exhibits the cut and chopped water hyacinths and banana sheaths. To evaluate the machine performance, two experiments were conducted. The first experiment tested the cutting and chopping function. One kilogram of the plants were fed in the machine with a rotational speed of 550, 750 and 950 revolutions per minute (rpm). Three sets of each setting were carried out. The chopped plants were weighed and the percentage of efficiency was calculated using Equationequation (1)(1)
(1) . The average output and %efficiency is shown in . The results concluded that a rotational speed of 950 rpm yields the highest efficiency for chopping water hyacinths and banana sheaths.
Figure 15. Chopped water hyacinth and banana sheath.
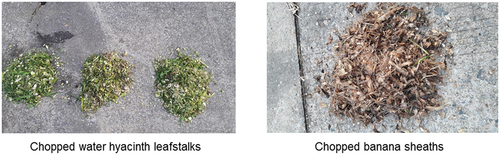
Table 5. The cutting system efficiency.
The second experiment was to test the fertiliser mixing function. One kilogram of all ingredients were fed in the mixing bin. Then, the machine was set at a rotational speed of 550, 750 and 950 rpm. The total time required to mix all the ingredients together was measured in seconds. Each setting was tested 3 times and the average mixing time was calculated as shown in . The results showed that at 950 rpm, the fertilisers were well mixed at 18 seconds for water hyacinths and 17 seconds for banana sheaths.
Table 6. The mixing system performance.
4. Discussion
The DT process started with the empathy study which encouraged the designers to realise the problem context. At the school learning centre, it was found that the preparation of the organic fertiliser’s ingredients required a lot of manpower and strength. The users’ pain points were the heavy workload, time consuming process and inconvenient location of raw materials. These findings were similar to a process of converting cassava roots into crackers in Polengan village, Indonesia (Kristian Citation2014b). To make local crackers, the villagers manually squeeze cassava to obtain juice. The squeezing process was found to be labour intensive and tedious. García-León et al. (Citation2021) also found that the manual work of cocoa pod opening required skilled operators and long processing time. Consistent with the work of Mbosso et al. (Citation2015) regarding the adoption of the agricultural technology. The small-scale farmers need agricultural machinery to relieve the labour-intensive work and increase their incomes. However, purchasing prices and perceived characteristics of the machine such as complexity, installation space, fuel consumption and maintainability were the main factors associated with the decision. As stated by Burra et al. (Citation2003), the users know what the problems are and which ones are their preferable solutions. Thus, the co-creation between the users and the designers lead to a desirable solution. In this case, the solution was a multi-function fertiliser making machine. This idea of replacing laborious work with an equipment is also found in Kristian (Citation2014b) in which the squeezer was created to allow the villager to work with less time and efforts.
QFD provides customers with a better design which leads to a total satisfaction with the final concept. The results of QFD analysis were consistent with other literatures to several degrees. Firstly, the customer requirements, the school learning centre put high weights in a well-function, easily operated, does not require electricity and inexpensive fertiliser mixing machine. Similar to the requirements of Columbian villagers, they requested that feeding, cutting and separation systems of the cocoa pulping machine should be well-function, following by a suitable power source, easy to operate, and accessible financially (García-León et al. Citation2021). The Indian farmers in Nagpur requested the shredding machine to be operated easily and safely, makes good quality fertilisers and does not require large space to instal (Ambade et al. Citation2022). Other Indian farmers in Maharashtra requested for a portable, less power consumption, need less space to instal, low cost, and affordable organic fertiliser making machine (Pawar et al. Citation2017). Secondly, the translated engineering characteristics from voices of customers were consistent with the analysis of García-León et al. (Citation2021); for example, numbers of steps to operate the machine were used to respond to ‘easy to operate’, the equipment cost was used in accordance with ‘accessible financially’. Thirdly, the technical attributes according to engineering characteristics, we found similarities with other literatures with regards to the small-scale agricultural machinery. Our machine and others were affordable in terms of design and development cost. Parts and machine elements were simple and available in local markets such as hopper, cutting blades, chain drives, gear housing, shafts, bearings, pulley, and belts (Ambade et al. Citation2022; Bhad et al. Citation2018; García-León et al. Citation2021)
The functional analysis of the multi-function fertiliser making machine was in line with the analysis of the cocoa pulping machine (García-León et al. Citation2021) in terms of feeding plants into the machines and cutting plants. However, the winning concepts were different. A conveyor belt and a hopper were the alternatives for a feeder design on both machines. The cocoa pulping machine winning concept was the gears and chains, while the fertiliser mixing machine winning concept was a hopper. Similarly, the water hyacinth chopper (Kassanuk and Phasinam Citation2019), the water hyacinth shredding machine (Tapananont et al. Citation1999), the waste food shredder machine (Ambade et al. Citation2022), and the organic compost fertiliser processing machine (Shahadan et al. Citation2022), a hopper was chosen as a plant feeder as well. For the cutting function, there were cutting disc, blade, crushing roller and hammer mill as alternatives. The cocoa pulping machine designer chose the cutting disc, while the designer of the multi-function fertiliser making machine selected cutting blades. The reason was the differences in shape, size and weight of the cocoa pods, water hyacinths and banana sheaths. Water hyacinths and banana sheaths are long, slim and light weight, a manual feed in the hopper and cutting blades were well-served the purpose of the function.
The 6.5 horse power, gasoline engine water hyacinth chopper developed by Kassanuk and Phasinam (Citation2019) was used to benchmark the cutting system efficiency. It was previously mentioned as Machine A in QFD analysis part. Their machine efficiency was 96.46% at a revolution speed of 2,000 rpm. Our machine yields a competitive efficiency at 93% at a lower revolution speed of 950 rpm. In term of fuel consumption, our machine uses 625 ml/hour while Machine A consumes 772 ml/hour of gasoline. In term of output, machine A and our machine can produce a fine chopped plants with less than 4 mm in length. It is the recommended length for making an organic fertiliser from water hyacinth (Suttiwattana and Wongkaew Citation2009). Other machines equip with a single function to either cut, chop or shred the plants; however, our machine responds to the deep needs of the users for a multi-function for chopping the plants and mixing the fertiliser. The machine was delivered and tested in the actual setting which is an important principal suggested by George and Shams (Citation2007). Being maintainable with local resources, the machine was well accepted by the school agricultural learning centre as they continue using it until the present day.
5. Conclusion
This paper presents an integration of Design Thinking (DT) framework and Quality Function Deployment (QFD) to generate a sustainable solution for a small-scale, low-to-medium machinery design and development for an agricultural-based community. The user-centred approach allowed the design team to fully understand the deeper needs and pain points the community were facing. This DT methodology is in accordance with the ‘Design for Localization’ by Butchers et al. (Citation2020). In order to create a sustainable and robust solutions, the designers should understand the local environment and technical capabilities. With in-depth understanding of the users’ needs. The solutions were generated insightfully. The co-creation process encouraged the users’ involvement in deciding which solution worked best for them.
The complete HoQ exhibited various dimensions to develop the product. Using QFD, the customer needs were transformed into engineering characteristics. The technical weight rating allowed the designer to focus on the critical engineering attributes. The available local resources were taken into consideration when performing QFD analysis. The technical-view and the customer-view benchmarking assured that the product’s design is comparable to other competitive designs.
Integrating DT with QFD to design a sustainable solution in this study has supported ‘Design for Developing World’ principles proposed by Mattson and Wood (Citation2014). Firstly, the designers developed empathy through the understanding the local context. The co-design between the users and the designers have resulted in impactful solutions and encouraged the ownership of the local people. Secondly, when using the QFD, the designer took the local resource and technical availability into considerations. Adapting the technology to meet local contexts allowed an effective and acceptable solution. Thirdly, the machine was tested in the actual setting and proved that it met the users’ needs and maintainable by local resources.
The case study has validated the proposed methodological framework that brought about sustainable solutions. The empathy study revealed that the students at the school agricultural centre needed a better way to make organic fertilisers more efficiently. Although there are plant cutting and fertiliser mixing machines available in the market, they are usually sold separately at individual prices. The machines are impractical due to their expensive prices, high power consumption and large land space requirements. They were satisfied with the physical machine prototypes and suggested combining them into a multi-function fertiliser mixing machine. The co-creation generated a desired solution which was a small-scale, inexpensive, multi-function machine that is well-designed to fit the users. The insight data and the winning concept idea from DT provided valuable customer inputs to the QFD process. The multi-function fertiliser mixing machine was designed based on available local resources and technology; using a gasoline engine to drive both cutting and mixing systems simultaneously. The cutting system efficiency was 93% for water hyacinth and 93.75% for banana sheath. The mixing system performance was 18 seconds for water hyacinth and 17 seconds for banana sheath when making the fertiliser. Both cutting and mixing systems worked best at 950 rpm. The multi-function agricultural machine was designed, fabricated, assembled, tested and evaluated based on its performance. It was delivered and tested the actual use at the community. The machine met the community expectations. It was affordable, easy to use, easy to maintain and the fertiliser making process became more efficient. The students were pleased with the machine and continue to use it in their afterschool farming club.
Acknowledgments
The authors would like to acknowledge the collaboration with Singapore Polytechnic on a transnational social innovation programme (Learning Express). We acknowledge students, instructors and staff of Soontharomattaprachasun School, RMUTT and Singapore Polytechnic for their participation in the DT process. We acknowledge the support from the Department of Agricultural Engineering and Department of Industrial Engineering, Faculty of Engineering, RMUTT.
Disclosure statement
All authors certify that they have no affiliations with or involvement in any organisation or entity with any financial interest or non-financial interest in the subject matter or materials discussed in this manuscript.
Data availability statement
All data generated or analysed during this study are included in this published article.
Additional information
Funding
Notes on contributors
Sanidda Tiewtoy
Sanidda Tiewtoy is an Assistant Professor at the Agricultural Engineering Department, Faculty of Engineering, Rajamangala University of Technology Thanyaburi (RMUTT) Thailand. She received a DEng in Water Engineering Management, Asain Institute of Technology. Her research expertise is irrigation engineering and water management.
Weerasak Moocharoen
Weerasak Moocharoen is a lecturer at Agricultural Engineering Department, Faculty of Engineering, Rajamangala University of Technology Thanyaburi (RMUTT) Thailand. His research is agricultural machinery and power system.
Natha Kuptasthien
Natha Kuptasthien is an Associate Professor at the Industrial Engineering Department, Faculty of Engineering, Rajamangala University of Technology Thanyaburi (RMUTT) Thailand. She received MS and PhD in Engineering Management from University of Missouri-Rolla, USA. Her research areas are Production and Operation Management and Engineering Education.
References
- Agriculture in Thailand – statistics & facts. (2023). Available online: https://www.statista.com/topics/5730/agriculture-in-thailand/#topicOverview. Accessed April 9, 2023)
- Akao, Y. 1990. Quality Function Deployment: Integrating Customer Requirements into Product Design. translated by G.H. Mazur eds. Cambridge, M.A: Productivity Press.
- Ambade, V., P. Pardhi, A. Kuttarmare, D. Mule, V. Bind, A. Kelekar, and A. Ingale. 2022. “Fabrication of Waste Food Shredder Machine for Generation of Organic Fertilizers.” International Journal of Advances Engineering and Management 4 (5): 195–197.
- Banerjee, S., and R. M. Puneka. 2020. “A Sustainability-Oriented Design Approach for Agricultural Machinery and Its Associated Service Ecosystem Development.” Journal of Cleaner Production 264:121642. https://doi.org/10.1016/j.jclepro.2020.121642.
- Bhad, V. J., A. S. Gaikwad, H. B. Jagtap, N. S. Koshti, and B. D. Nikam. 2018. “Modern multipurpose plant cutting machine.” International Journal of Advance Research and Innovative Ideas in Education 4 (1): 419–424. DUI: 16.0415/IJARIIE-7329.
- Brown, T. 2008. “Design Thinking.” Harvard Business Review 86 (6): 84–92, 141.
- Brown, T., and J. Wyatt. 2010. “Design Thinking for Social Innovation.” Development Outreach 12 (1): 29–43. https://doi.org/10.1596/1020-797X_12_1_29.
- Burra, S., S. Patel, and T. Kerr. 2003. “Community-Designed, Built and Managed Toilet Blocks in Indian Cities.” Environment and Urbanization 15 (2): 11–32. https://doi.org/10.1177/095624780301500202.
- Butchers, J., J. Cox, S. Williamson, J. Booker, and B. Gautam. 2020. “Design for Localisation: A Case Study in the Development and Implementation of a Low Head Propeller Turbine in Nepal.” Development Engineering 5:100051. https://doi.org/10.1016/j.deveng.2020.100051.
- Chan, L. K., and M. L. Wu. 2002. “Quality Function Deployment: A Literature Review.” European Journal of Operational Research 143 (3): 463–497. https://doi.org/10.1016/S0377-2217(02)00178-9.
- Chuanromanee, T. S., I. James, and G. L. Ryan. 2019. “Morphological Analysis of Size and Shape (MASS): An Integrative Software Program for Morphometric Analyses of Leaves.” Applications in Plant Sciences 7 (9): e11288. https://doi.org/10.1002/aps3.11288.
- Coulentianos, M. J., I. Rodriguez-Calero, S. R. Daly, and K. H. Sienko. 2020. “Global Health Front-End Medical Device Design: The Use of Prototypes to Engage Stakeholders.” Development Engineering 5:100055. https://doi.org/10.1016/j.deveng.2020.100055.
- Cristiano, J. J., J. K. Liker, and C. C. I. White. 2001. “Key Factors in the Successful Application of Quality Function Deployment (QFD.” IEEE Transactions on Engineering Management 48 (1): 81–95. https://doi.org/10.1109/17.913168. Feb 2001.
- Daniells, J. W. 2003. Bananas and Plantains. Editors Benjamin Caballero. Second. Academic Press 372–378 Encyclopedia of Food Sciences and Nutritionhttps://doi.org/10.1016/B0-12-227055-X/00080-8
- Dersseh, M. G., A. M. Melesse, S. A. Tilahun, M. Abate, and D. C. Dagnew. 2019. “Chapter 19 - Water Hyacinth: Review of Its Impacts on Hydrology and Ecosystem Services—Lessons for Management of Lake Tana”. In Extreme Hydrology and Climate Variability, In edited by A. M. Melesse, W. Abtew, and G. Senay, 237–251.https://doi.org/10.1016/B978-0-12-815998-9.00019-1.
- Duarte, O. C., R. Lulham, and L. Kaldor. 2011. “Co-Designing Out Crime.” CoDesign 7 (3–4): 155–168. https://doi.org/10.1080/15710882.2011.630476.
- García-León, R. A., W. Jaimes-Gonzalez, L. D. Becerra, E. Flo´rez-Solano, M. Cabellos-Martı´nez, and D. Meneses-Torres. 2021. “Application of the QFD Method to the Design of a Cocoa Pulping Machine.” International Journal of System Assurance Engineering & Management 12 (6): 1199–1220. https://doi.org/10.1007/s13198-021-01416-0.
- George, C., and A. Shams. 2007. “The Challenge of Including Customer Satisfaction into the Assessment Criteria of Overseas Service-Learning Projects.” International Journal for Service Learning in Engineering, Humanitarian Engineering and Social Entrepreneurship 2 (2). https://doi.org/10.24908/ijsle.v2i2.2092.
- Gherardini, F., C. Renzi, and F. Leali. 2017. “A Systematic User-Centred Framework for Engineering Product Design in Small- and Medium-Sized Enterprises (SMEs).” International Journal of Advanced Manufacturing Technology 91 (5–8): 1723–1746. https://doi.org/10.1007/s00170-016-9857-9.
- Jansuwan, P., K. K. Zander, and E. Ustaoglu. 2022. “Multifunctional Farming as Successful Pathway for the Next Generation of Thai Farmers.” PLoS One 17 (4): e0267351. https://doi.org/10.1371/journal.pone.0267351.
- Karthigayan, G., C. Z. Zulkiflib, S. T. Xinhuic, and N. H. Nurdinii. 2021. “Economical Smart Composting Machine to Manage Food Waste, Alleviate Environmental Degradation and Combat Climate Change on Penang Hill.” International Journal of Innovation, Creativity & Change 9 (11): 12–27. https://www.ijicc.net/images/vol9iss11/91111_Gunasegaran_2019_E_R.pdf.
- Kassanuk, T., and K. Phasinam.2019. “Design and Construction of Water Hyacinth Chopper.” RMUTI Journal Science and Technology 13 (3): 57–68. September – December (in Thai). Accessed November 10, 2022 https://ph01.tci-thaijo.org/index.php/rmutijo/article/download/218122/165407/.
- Kelley, T., and D. Kelley. 2013. Creative Confidence, Unleashing the Creative Potential within Us. New York: Crown Business.
- Kleinsmann, M., R. Valkenburg, and J. Sluijs. 2017. “Capturing the Value of Design Thinking in Different Innovation Practices.” International Journal of Design 11 (2): 25–40. http://ijdesign.org/index.php/IJDesign/article/view/2771/780.
- Kristian, N. 2014a. Social Innovation in South East Asia. The chemical engineer magazine, issue 874, April 2014, 26-27.
- Kristian, N. 2014b. Work in Progress – Using Transnational Education Program to Inculcate Social Innovation and Sustainability Mindset. Proceedings of the 2nd International Conference on Sustainable Innovation, Yogyakarta, Indonesia. https://doi.org/10.13140/RG.2.1.2521.5840
- Luotola, H., M. Hellström, M. Gustafsson, and O. Peminova-Harikoski. 2017. “Embracing Uncertainty in Value-Based Selling by Means of Design Thinking.” Industrial Marketing Management 65:59–75. https://doi.org/10.1016/j.indmarman.2017.05.004.
- Matharu, S. S., I. A. Mulla, and R. Nadaf. 2021. “Design and Development of Organic Waste Compost Machine.” International Journal of Innovation Engineering Research and Technology 7 (4): 1–5. Retrieved from. https://repo.ijiert.org/index.php/ijiert/article/view/2095.
- Mattson, C., and A. E. Wood. 2014. “Nine Principles for Design for the Developing World as Derived from the Engineering Literature.” Journal of Mechanical Design 136 (12): 121403. https://doi.org/10.1115/1.4027984.
- Mbosso, C., A. Degrander, G. B. Villamor, P. V. Damme, Z. Tchoundjeu, and S. Tsafack. 2015. “Factors Affecting the Adoption of Agricultural Innovation: The Case of a Ricinodendron Heudelotii Kernel Extraction Machine in Southern Cameroon.” Agroforestry Systems 89 (5): 799–811. https://doi.org/10.1007/s10457-015-9813-y.
- Mueller-Roterberg, C. 2018. Handbook of Design Thinking. Accessed August 18, 2020, from https://www.researchgate.net/publication/329310644_Handbook_of_Design_Thinking.
- Nieusma, D., and D. Riley. 2010. “Designs on Development: Engineering, Globalization, and Social Justice.” Engineering Studies 2 (1): 29–59. https://doi.org/10.1080/19378621003604748.
- Pare, M., and M. Aman. 2019. “Design of Organic Compost Machine.” International Research Journal of Engineering & Technology 6 (12): 532–6. Retrieved from. https://www.irjet.net/archives/V6/i12/IRJET-V6I1264.pdf.
- Pawar, P., A. Mahajan, S. Pwar, V. Pawar, S. S. Pachpor, and M. S. Bachhav. 2017. “Design & Fabrication of Organic Fertilizer Manufacturing Machine.” International Research Journal of Engineering & Technology 4 (2): 1348–1350. Retrieved from. https://www.irjet.net/archives/V4/i2/IRJET-V4I2264.pdf.
- Ramos, A. K., N. Trinidad, A. Correa, and R. Rivera. 2016. “Partnering for Health with Nebraska’s Latina Immigrant Community Using Design Thinking Process.” Progress in Community Health Partnerships: Research, Education, & Action 10 (2): 311–318. https://doi.org/10.1353/cpr.2016.0022.
- Saduak, W., A. Saduak, N. Pourpan, and P. Poungsuk. 2016. “Need for Developing a School Agricultural Learning Center Model of Students at Praibuengwittayakom School, Praibueng District, Srisaket Province, Thailand.” International Journal of Agricultural Technology 12 (7.2): 1971–1981.
- Sengazani Murugesan, V., A. H. Sequeira, S. K. Jauhar, and V. Kumar. 2020. “Sustainable Postal Service Design: Integrating Quality Function Deployment from the Customers Perspective.” International Journal of System Assurance Engineering & Management 11 (2): 494–505. https://doi.org/10.1007/s13198-019-00906-6.
- Shahadan, N. H., I. Taman, S. H. Hasim, and H. Jambari 2022. Organic Compost Fertilizer Processing Machine for Small and Medium Industries. Proceedings of the 4th International Applied Sciences Engineering, Information and Technology, Johor, Malaysia.
- Soh, K. F. 2011. An Observational Study of Infusing Design Thinking into the CDIO Framework. Proceedings of the 7th CDIO International Conference, Lyngby, Denmark. Accessed August 30, 2022, from http://cdio.org/knowledge-library/documents/observational-study-infusing-design-thinking-cdio-framework.
- Soh, K. F., and N. Kristian 2014. Promoting Sustainable and Social Responsible Mindset Through a Transnational Programme Using the CDIO Framework. Proceedings of the 10th International CDIO Conference, Barcelona, Spain. Accessed April 18, 2022, from http://www.cdio.org/node/6089.
- Sousa-Zomer, T. T., and P. A. C. Miguel. 2017. “A QFD-Based Approach to Support Sustainable Product-Service Systems Conceptual Design.” International Journal of Advanced Manufacturing Technology 88 (1–4): 701–717. https://doi.org/10.1007/s00170-016-8809-8.
- Sullivan, L. P. 1986. Quality Function Deployment. Milwaukee: Quality Progress.
- Suttiwattana, P., and D. Wongkaew. 2009. “Development of Water Hyacinth Cutting Machine from Prototype with Community Participation.” Rajamangala University Technology Tawan-Ok Research Journal 2 (1): 1–8.
- Tapananont, P. 1999. Prototype of Water Hyacinth Shredding Machine. Thailand Institute of Scientific and Technological Research (In Thai) Res. Proj. No. 40-14. Accessed November 15, 2022, from https://opac.tistr.or.th/cgi-bin/koha/opac-ISBDdetail.pl?biblionumber=13890.
- UNESCO Office Bangkok and Regional Bureau for Education in Asia and the Pacific. (2008). Community Learning Centres: Country Report from Asia, 84–89.
- Viola, N., S. Corpino, M. Fioriti, and F. Stesi. 2012. Functional Analysis in Systems Engineering: Methodology and Applications, Systems Engineering: Practice and Theory. edited by B. Cogan. InTech. https://doi.org/10.5772/34556.