Abstract
The shape memory effect and nanoindentation response of various phases of sputtered NiTi shape memory thin films were investigated as a function of temperature. The phase transformation temperatures of NiTi films were observed to be sensitive to a compositional shift. The mechanical properties of NiTi thin films also presented a significant response to phase transformations. At the same load, the maximum indentation depth for austenite is smaller than for martensite, indicating that martensite is softer than austenite. A martensite thin film was converted to austenite via in situ heating nanoindentation and displayed the mechanical properties similar to the austenite film at room temperature. These results underscore the validity of elevated temperature nanoindentation methods as a means of interrogating the mechanical properties of materials that undergo thermally-induced phase transformations. The details of the load–displacement curves are also described.
1. Introduction
Nanoindentation has become widespread as a method to study the mechanical response of materials [Citation1], particularly the measurement of hardness [Citation2–4], elastic modulus [Citation2–4], hardening exponents [Citation5], creep parameters [Citation6], and residual stresses [Citation7]. Testing consists of recording the indentation load as a function of penetration depth of a sharp tip. Although the technique is common, the use of nanoindentation to study films that undergo phase transformations is quite limited. There have been a few reports on the use of nanoindentation to characterize the phase transformation behavior of silicon, which has been observed to display a pop-out feature on the unloading curve. It is believed that the material experiences an associated volume increase due to hydrostatic pressure and as a result undergoes a phase transformation [Citation8,Citation9]. By providing the critical pressure to trigger this structural transformation [Citation10] and by probing a small volume of material [Citation1,Citation2], nanoindentation enables these observations. What remains missing from the literature, however, is an examination of materials other than silicon that undergo phase transformations. This paper aims to look at shape memory thin films and apply elevated nanoindentation conditions to explore their mechanical properties.
Shape memory alloys (SMA) are a class of materials that undergo phase transformations triggered by heating [Citation11]. For several decades, NiTi-based shape memory thin films have attracted much attention due to their potential applications in micro- or nano-electromechanical systems (MEMS/NEMS) as sensor and actuation materials [Citation12–14]. They have the advantage over other actuation methods (such as piezoelectric or electrostatic methods), due to their high power-to-weight ratio, large recovery stress/strain, high damping capacity, good mechanical properties, and excellent chemical resistance and biocompatibility [Citation12,Citation15,Citation16]. These materials undergo a phase transformation from one crystallographic arrangement to another; a force or displacement accompanies this change. Along with the phase change, material properties (electrical, optical and mechanical) also change.
For MEMS applications, the mechanical properties of all the phases of NiTi-based shape memory thin films must be evaluated. Recently, there has been a spate of research efforts that have employed room-temperature nanoindentation to investigate the hardness and elastic modulus of NiTi-based materials, from sputtered polycrystalline thin films [Citation14,Citation17–26] to nanopillars [Citation27,Citation28], in a variety of geometries and test conditions [Citation29]. Analysis of the shape memory effect on the small scale has also been studied by coupling nanoindentation with atomic force microscopy (AFM) [Citation30]. Unfortunately, analysis of the high-temperature phase at the same composition as the low-temperature phase cannot be performed at ambient temperature. To test austenite (the high-temperature phase), researchers must modify the composition and employ the compositional sensitivity of these materials. The transformation temperatures of these materials have been found to increase 100°C for a 1% decrease in Ni content [Citation31]. An intentionally Ni-rich film can thus manifest the high-temperature phase at room temperature. However, the composition shift may change the resulting microstructure and produce precipitates [Citation32,Citation33] that may complicate the nanoindentation analysis. The present work endeavors to examine the mechanical properties of high- and low-temperature phases of the same composition by heating a sample during nanoindentation. Such work will explore the feasibility of elevated heating studies and illuminate the role of composition on the mechanical properties of austenite.
Nanoindentation studies at elevated temperatures will benefit researchers and MEMS designers by providing an understanding of the role of phase transformations on mechanical properties. Such heating studies have been successfully executed in the study of the deformation of metallic glasses [Citation34] and the Al–Ni–Si system [Citation35]. In the present study, the NiTi shape memory films are interrogated at elevated temperatures and compared with their room temperature counterparts to explore the properties of phases in both sets of conditions.
2. Experimental methods
Amorphous NiTi thin films were deposited onto 200 nm Si3N x -coated silicon wafers by dc magnetron sputtering at 3 mTorr of argon gas pressure at ambient temperature. Two 75 mm targets of a Ti50Ni50 alloy and pure Ti were co-sputtered to create a thin film nominally 1 μm thick. The base pressure of the chamber is about 2 × 10−7 Torr. The substrate platen was rotated at 30 rpm during deposition to obtain homogeneous films [Citation36]. The film compositions were determined using a calibrated JEOL JXA-8530F microprobe.
The films are deposited in an amorphous form and required a high-temperature crystallization step to produce films that undergo the shape memory effect. Crystallization of the two compositions was conducted at 440°C for 30 min under vacuum. Two compositions were deposited in the present study: Ti–48.3 at. % Ni (Sample A) and Ti–50.8 at. % Ni (Sample B). The former is a composition of room-temperature martensite; the latter is a room-temperature austenite.
A Shimadzu X-ray diffractometer operated at room temperature with a Cu Kα source with a 2θ scan between 35° and 50° was used to determine the phases present. The phase transformation was characterized using a wafer curvature system operating between 25 and 100°C, using 10 × 25 mm2 coupons. The key transformation temperatures of Sample A, which are associated with the start and finish temperatures of austenite and martensite phase formation, are A s, A f, M s, M f and are equal to 60, 70, 57, and 40°C, respectively. Conversely, Sample B (austenite) has a linear response [Citation37,Citation38]. These data show that different phases are present at room temperature.
Key to these studies is the analysis of the mechanical properties of NiTi films at room temperature and at elevated temperatures. Films were characterized using a CSM Instruments Ultra Nanoindentation Tester at room temperature and at 110°C (). The temperature was measured directly by a K-type thermocouple at the indented surface of the sample. This indentation system is capable of low-load measurements for extended times with minimal thermal drift due to its design which employs materials with extremely low coefficient of thermal expansion.
Figure 1. (a) The ultra nanoindentation tester with heated stage and cooling liquid circuit for high temperature measurements, and (b) a schematic drawing of the nanoindentation tester.
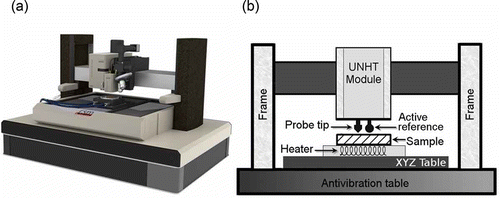
A Berkovich diamond indenter was used for the indentation experiments. At room temperature both loading and unloading times were set to 30 s, with a hold time at maximum load (Fmax ) of 5 s. At the elevated temperature of 110°C, the loading, unloading and hold times were set to 5 s to further minimize the eventual thermal drift. It is worth noting that the resulting mechanical properties for these different loading rates have been found to be comparable, with the only difference being the noise in the curves. The Fmax was set as 1000 μN, which corresponds to a maximum nanoindentation depth of less than 110 nm for all samples (following the rule of thumb to indent less than 10% of the thickness of the sample). The data were evaluated using the Oliver–Pharr method [Citation3], and the nanoindenter area function was calibrated using fused silica. Each sample was tested 10 times; the mean average value is presented.
3. Results and discussion
3.1. The effect of composition on NiTi phase transformations
The phase transformation temperatures of NiTi are compositionally sensitive [Citation31]. With greater Ni content, the phase transformation is suppressed. As such, the high-temperature phase of austenite can be present at room temperature if the composition is tailored accordingly. shows the X-ray diffraction patterns for the two compositions of NiTi films in this study. The Ti–48.3 at. % Ni film (Sample A) is a martensitic film at room temperature, and only the martensite diffraction peaks exist. No austenite is present, since the (110)A peak, which is associated with austenite (B2 structure), is absent. Austenite is present when higher temperatures are sustained. Yet a small change in stoichiometry can cause a film to be austenitic, as the results for the Ti–50.8 at. % Ni film (Sample B) show. XRD results, shown in , confirm the (110)A peak is dominant in comparison to the (002)M peak, indicating that the film is largely austenite but has a small amount of martensite present.
Figure 2. (a) The X-ray diffraction pattern of the sputtered Ti–48.3 at. % Ni and Ti–50.8 at. % Ni films at room temperature. (b) The phase transformation behaviors of sputtered Ti–48.3 at. % Ni and Ti–50.8 at. % Ni films, which were measured using wafer curvature between room temperature and 100°C.
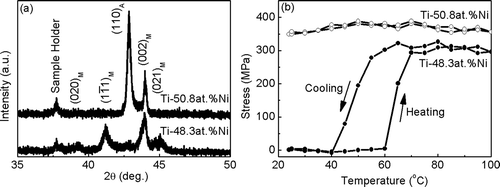
3.2. Shape memory effect
Shape memory thin films undergo a phase transformation from the low temperature crystalline phase of martensite (B19') to the high temperature phase of austenite (B2). We characterized the phase transformation behavior of our films using wafer curvature methods, which, in addition to differential scanning calorimetry (DSC), is a standard method to characterize the phase transformation behavior in NiTi-based shape memory films. Wafer curvature offers some advantages in that it is a non-destructive technique and has a greater resolution of transformation temperatures than DSC [Citation39].
Wafer curvature methods measure the film stress as a function of temperature [Citation40], by employing Stoney's equation [Citation41]. After deposition, the film can be considered to be clamped to the substrate surface and as a result of deposition has a residual stress [Citation37,Citation38]. This film stress is further increased when films undergo a phase transformation, which often accompanies a volumetric change in the film. As such, the film departs from that of other metals, which display a linear response, and displays a large jump in film stress ().
The phase transformation behaviors of the crystallized NiTi films between room temperature and 100°C are presented in . For the Ti–48.3 at. % Ni films (Sample A), the stress initially has a small decrease from room temperature to 60°C, which is attributed to the difference in coefficient of thermal expansion between the NiTi films of martensite and the Si substrate [Citation37,Citation38]. Above 60°C, the stress has a dramatic increase that ends at about 70°C; this change results from the transformation of martensite to austenite. With increased heating, the stress decreases again with temperature and presents a thermal expansion response of the austenite. When the heating cycle is reversed and cooling is applied, the stress decreases significantly at 60°C corresponding to the transformation from austenite to martensite, which is complete at 40°C. The different paths between the heating and cooling curves create the transformation hysteresis, which can be related to the response frequency of NiTi-based MEMS devices. Interestingly, as shows, the Ti–50.8 at. % Ni film (austenitic film, Sample B) does not present this hysteresis, and the heating and cooling curves overlap. The curve of measured stress for the Ti–50.8 at. % Ni film (Sample B) has a small positive slope in the temperature range of interest, which is contrary to the coefficient of thermal expansion difference between most metallic films and their substrates, which is commonly negative [Citation37,Citation38]. This positive slope indicates that the small amount of martensite remaining in this sample is transforming to austenite.
3.3. Nanoindentation response at room temperature
The phases that are present have different nanoindentation responses. As shown in , the dominant phase of Sample A (Ti–48.3 at. % Ni) is martensite at room temperature, whereas Sample B (Ti–50.8 at. % Ni) is largely austenite at room temperature. As shown in , the maximum indentation depth of Sample B is smaller than that of Sample A, indicating that the film will yield more under the same load. Accordingly, the Young's modulus and hardness for the martensite films were found to be smaller than that for the austenite films, consistent with those found in bulk materials [Citation42]. Using the Oliver–Pharr method [Citation3], the calculated Young's modulus and hardness of the martensite film (Sample A) are 73.7±4.2 and 2.5±0.3 GPa. The modulus and hardness for the austenite film (Sample B) are 80.1±2.1 and 4.4±0.1 GPa (). These results are comparable with those in the literature [Citation14].
Figure 3. The load–depth curves of sputtered NiTi films obtained using a Berkovich diamond indenter at room temperature.
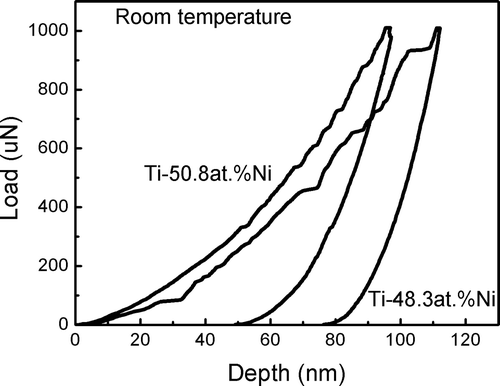
Table 1. The Young's modulus and hardness of NiTi shape memory thin films
An analysis of the energy dissipation ratio η during nanoindentation is instructive for determining the deformation mechanisms at play [Citation19]. During the nanoindentation process, a load vs. displacement curve is generated. The area under the loading and unloading curves is the total absorbed energy Wt and the recoverable energy Wre . The ratio η can be expressed as
The energy dissipation ratio in martensite is much larger than that in austenite, indicating that the deformation mechanisms are different. When the shape memory alloys are deformed as austenite, a superelasticity (or pseudoelasticity) behavior occurs; indicating that the specimen will return to the original shape once the loading is released [Citation11]. For martensite, twin reorientation occurs during deformation; as such returning to the original shape after the loading is released cannot occur. It can only do so after being heated above the austenite transformation temperature (the shape memory effect).
During nanoindentation of shape memory alloys, the deformation can be divided into three regions: in the farthest region from the point of indentation the lowest stress field exists and reversible elastic deformation occurs; in direct proximity to the indenter, the highest stress field exists and plastic deformation occurs; and between these regions, a mild stress field exists and the superelasticity or martensite twin reorientation occurs [Citation30]. When the indentation is in austenite, the superelasticity occurs in the intermediate region and it recovers during unloading, so a lower dissipation energy ratio is obtained. When martensite is indented, the martensite twin reorientation occurs in the intermediate region, so it cannot recover during unloading, and a higher dissipation energy ratio is observed. Additionally, the yield stress in austenite is much higher than that in its martensite counterpart [Citation42]. All these deformation mechanisms correlate to the lower energy dissipation ratio in austenite thin films.
3.4. Nanoindentation response at elevated temperatures
An investigation of the mechanical properties of martensite and austenite requires elevated temperatures to trigger the martensitic transformation within shape memory alloys. Sample A (Ti–48.3 at. % Ni) is martensite at room temperature and austenite at 110°C, as shows. To explore the load–depth response of the thermally-induced austenite phase, nanoindentation was performed at 110°C and the results were compared to the room-temperature austenite film.
The martensite phase is softer than austenite, as shown by the greater indentation depth at the same load as for the martensite sample. We find that the maximum indentation depth decreases when the room-temperature martensite film is heated to 110°C (and is austenite). As shown in , the maximum indentation depth at 1000 μN load decreases by 10% from approximately 110 nm at room temperature (martensite, Sample A) to about 100 nm at 110°C (austenite, heated Sample A). This high temperature value is reasonably close to that from austenite at room temperature (Sample B), at approximately 96 nm, suggesting the temperature that enables a phase transformation is obtainable.
Figure 4. A comparison of the load–depth curves of sputtered NiTi films at different temperatures using a Berkovich diamond indenter: (a) Ti–48.3 at. % Ni film at room temperature (martensite); (b) Ti–48.3 at. % Ni film at 110°C (austenite); (c) Ti–50.8 at. % Ni film at room temperature (austenite); (d) Ti–50.8 at. % Ni film at 110°C (austenite).
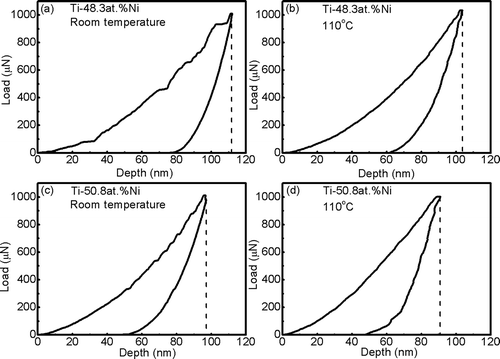
Further analysis of the load–depth curves provides us additional evidence that phase transformations have occurred and can be characterized with in situ heating. The calculated Young's modulus and hardness were determined using the Oliver–Pharr method [Citation3] (). The room temperature martensite film was found to have a Young's modulus of 73.7±4.2 GPa. The modulus of this sample increases with heating to a value of 89.0±2.1 GPa. For comparison, we conducted nanoindentation experiments to obtain the Young's modulus of the austenite film (Ti–50.8 at. % Ni/Sample B) at room temperature and 110°C, which were found to be 80.1±2.1 and 92.8±3.1 GPa, respectively. This observation of a small increase in value is consistent with the literature, whereby the transformation stress in austenite has been found to increase slightly with temperature [Citation43]. The small difference between these values for the room-temperature and heated austenite thin film may be due to the small amount of martensite remaining in the room temperature sample, as discussed in Section 3.1. Other factors might include, the role of surface roughness [Citation44] and experimental noise. Also, the NiTi shape memory alloys are very sensitive to the composition [Citation31]. Interestingly, the Young's modulus for the thermally activated austenite (89.0±2.1 GPa) and the room-temperature austenite (92.8±3.1 GPa) are nearly the same. All in all, these close values indicate the validity of these in situ heating methods to determine details of the mechanical properties of high temperature phases.
The increase in the value of the modulus proves the phase change has occurred and that it can be measured by in situ heating methods. Nanoindentation at elevated temperatures has been applied to a range of materials systems that do not undergo a phase transformation. Researchers have found that the maximum indentation depth increases with temperature in Al, Si and intermetallic phases like Al3Ni2, and Al7Cu4Ni. More importantly, the hardness and modulus were found to decrease with temperature in all phases, this correlates with the difference in deformation behaviors; which consists of dislocation generation and pile-up at room temperature; and creep and plastic flow at elevated temperatures [Citation35]. Contrary to these findings [Citation35], the modulus and hardness for the samples presented here increase with temperature for Sample A, indicating that the higher temperature phase is being measured. The calculated energy dissipation ratio from Sample A at 110°C is about 64.5±0.8%, which is very close to that of Sample B at room temperature, at 62.5±1.8%. These data show the capability of nanoindentation with heating as a means to explore the mechanical properties of the phases of NiTi thin films.
Lastly, it is worthy to note that the pop-in features on the loading curves, which is usually attributed to the onset of plastic deformation [Citation45–47], varies during nanoindentation as a function of phase transformations. At a critical stress level, an abrupt depth excursion occurs which is related to the dislocation formation in crystal specimens [Citation47] or shear band formation in amorphous ones [Citation45,Citation46]. Several studies have been conducted to explore the underlying mechanism of pop-in events, which include the Hertzian stress analysis [Citation45] and a quantitative analysis [Citation47]. As shows, the pop-in depth is much larger in martensite films, however pop-ins are nearly non-existent when nanoindentation is performed at 110°C (austenite) and the load–depth curves are smooth. Interestingly, the load–depth curve of austenite at 110°C is comparable with the austenite conducted at room temperature (Sample B). These data show that features of the high temperature phase can be measured with these means. Given the similarity of the high temperature curves for austenite and the room temperature curves for austenite, it seems that thermally-induced phases and chemically-modified phases are nearly the same for the temperature and composition conditions assessed in this work.
4. Summary
Nanoindentation with an in situ heating stage was employed to evaluate the mechanical properties of sputtered NiTi shape memory films. Using these methods, the following observations were made:
-
The transformation temperatures of sputtered NiTi films are sensitive to composition. After processing, the room temperature phase of the Ti–48.3 at. % Ni film is martensite, whereas the phase of Ti–50.8 at. % Ni film is austenite.
-
The martensite film is softer than the austenite film. At the same load, the maximum indentation depth of the martensite film is larger than that for the austenite film, indicating that the film will yield more under the same load. Accordingly, the Young's modulus and hardness values for the martensite films were found to be smaller than that for the austenite films.
-
When nanoindentation is conducted at an elevated temperature, at which the martensite transforms to austenite, the maximum indentation depth decreased and the sample behaved similarly to room-temperature austenite. These data confirm that phase transformations have a significant effect on the mechanical response of sputtered NiTi films and that heated testing is able to measure these changes.
-
The energy dissipation ratio, η, from the austenite film is smaller than that from the martensite film, implying the deformation mechanisms are different between them.
Acknowledgments
This work made possible by the National Science Foundation (Grant No. 0907090).
References
- Schuh , C.A. 2006 . Nanoindentation studies of materials , 32 – 40 . Mater : Today 9 .
- Bhushan , B. , ed. 1999 . Handbook of Micro/Nano Tribology , 433 Boca Raton, Florida : CRC Press .
- Oliver , W.C. and Pharr , G.M. 1992 . An improved technique for determining hardness and elastic-modulus using load and displacement sensing indentation experiments . J. Mater. Res. , 7 : 1564 – 1583 .
- Oliver , W.C. and Pharr , G.M. 2004 . Measurement of hardness and elastic modulus by instrumented indentation: advances in understanding and refinements to methodology . J. Mater. Res. , 19 : 3 – 20 .
- Dao , M. , Chollacoop , N. , Van Vliet , K.J. , Venkatesh , T.A. and Suresh , S. 2001 . Computational modeling of the forward and reverse problems in instrumented sharp indentation . Acta Mater , 49 : 3899 – 3918 .
- Storakers , B. and Larsson , P.L. 1994 . On Brinell and Boussinesq indentation of creeping solids . J. Mech. Phys. Solid , 42 : 307 – 332 .
- Suresh , S. and Giannakopoulos , A.E. 1998 . A new method for estimating residual stresses by instrumented sharp indentation . Acta Mater , 46 : 5755 – 5767 .
- Domnich , V. , Gogotsi , Y. and Dub , S. 2000 . Effect of phase transformations on the shape of the unloading curve in the nanoindentation of silicon . Appl. Phys. Lett. , 76 : 2214 – 2216 .
- Jang , J.I. , Lance , M.J. , Wen , S.Q. , Tsui , T.Y. and Pharr , G.M. 2005 . Indentation-induced phase transformations in silicon: influences of load, rate and indenter angle on the transformation behavior . Acta Mater. , 53 : 1759 – 1770 .
- Gridneva , I.V. , Milman , Y.V. and Trefilov , V.I. 1972 . Phase transition in diamond-structure crystals during hardness measurements . Phys. Status Solidi (a) , 14 : 177 – 182 .
- Otsuka , K. and Wayman , C.M. 1998 . Mechanism of shape memory effect and superelasticity, in Shape Memory Materials , Edited by: Otsuka , K. and Wayman , C.M. 27 – 49 . New York : Cambridge University Press .
- Miyazaki , S. and Ishida , A. 1999 . Martensitic transformation and shape memory behavior in sputter-deposited TiNi-base thin films . Mater. Sci. Eng. A , 275 : 106 – 133 .
- Otsuka , K. and Kakeshita , T. 2002 . Science and technology of shape-memory alloys: new developments . MRS Bull. , 27 : 91 – 100 .
- Fu , Y.Q. , Huang , W.M. , Du , H.J. , Huang , X. , Tan , J.P. and Gao , X.Y. 2001 . Characterization of TiNi shape-memory alloy thin films for MEMS applications . Surf. Coating Tech. , 145 : 107 – 112 .
- Van Humbeeck , J. 1999 . Non-medical applications of shape memory alloys . Mater. Sci. Eng. A , 273 : 134 – 148 .
- Otsuka , K. and Ren , X.B. 1999 . Recent developments in the research of shape memory alloys . Intermetallics , 7 : 511 – 528 .
- Birnbaum , A.J. , Chung , U.J. , Huang , X. , Im , J.S. , Ramirez , A.G. and Yao , Y.L. 2009 . Substrate temperature effects on laser crystallized NiTi thin films . J. Appl. Phys. , 105 : 073502-1 – 10 .
- Ishida , A. , Sato , M. and Miyazaki , S. 1999 . Mechanical properties of Ti–Ni shape memory thin films formed by sputtering . Mater. Sci. Eng. A , 275 : 754 – 757 .
- Liu , R. , Li , D.Y. , Xie , Y.S. , Llewellyn , R. and Hawthorne , H.M. 1999 . Indentation behavior of pseudoelastic TiNi alloy . Scripta Mater. , 41 : 691 – 696 .
- Moyne , S. , Poilane , C. , Kitamura , K. , Miyazaki , S. , Delobelle , P. and Lexcellent , C. 1999 . Analysis of the thermomechanical behavior of Ti-Ni shape memory alloy thin films by bulging and nanoindentation procedures . Mater. Sci. Eng. A , 273 : 727 – 732 .
- Ni , W.Y. and Grummon , D.S. 2001 . Nanoindentation and wear behavior of nickel-titanium alloys and thin films, in Surface Engineering 2001 – Fundamentals and Applications , Edited by: Meng , W.J. , Kumar , A. , Doll , G.L. , Cheng , Y.T. , Veprek , S. and Chung , Y.W. 53 – 58 . Warrendale : Materials Research Society .
- Tall , P.D. , Ndiaye , S. , Beye , A.C. , Zong , Z. , Soboyejo , W.O. , Lee , H.J. , Ramirez , A.G. and Rajan , K. 2007 . Nanoindentation of Ni–Ti thin films . Mater. Manuf. Process. , 22 : 175 – 179 .
- Huang , X. and Ramirez , A.G. 2009 . Structural relaxation and crystallization of NiTi thin film metallic glasses . Appl. Phys. Lett. , 95 : 121911
- Fei , X.L. , Zhang , Y.J. , Grummon , D.S. and Cheng , Y.T. 2009 . Indentation-induced two-way shape memory surfaces . J. Mater. Res. , 24 : 823 – 830 .
- Ni , W.Y. , Cheng , Y.T. and Grummon , D.S. 2004 . Microscopic shape memory and superelastic effects under complex loading conditions . Surf. Coating Tech. , 177 : 512 – 517 .
- Ni , W.Y. , Cheng , Y.T. , Lukitsch , M. , Weiner , A.M. , Lev , L.C. and Grummon , D.S. 2005 . Novel layered tribological coatings using a superelastic NiTi interlayer . Wear , 259 : 842 – 848 .
- Frick , C.P. , Orso , S. and Arzt , E. 2007 . Loss of pseudoelasticity in nickel-titanium sub-micron compression pillars . Acta Mater. , 55 : 3845 – 3855 .
- San Juan , J.M. , No , M.L. and Schuh , C.A. 2008 . Superelasticity and shape memory in micro- and nanometer-scale pillars . Adv. Mater , 20 : 272 – 278 .
- Amini , A. , He , Y. and Sun , Q.P. 2011 . Loading rate dependency of maximum nanoindentation depth in nano-grained NiTi shape memory alloy . Mater. Lett. , 65 : 464 – 466 .
- Shaw , G.A. , Stone , D.S. , Johnson , A.D. , Ellis , A.B. and Crone , W.C. 2003 . Shape memory effect in nanoindentation of nickel-titanium thin films . Appl. Phys. Lett. , 83 : 257 – 259 .
- Saburi , T. 1998 . Ti–Ni shape memory alloys, in Shape Memory Materials , Edited by: Otsuka , K. and Wayman , C.M. 49 – 96 . New York : Cambridge University Press .
- Kajiwara , S. , Kikuchi , T. , Ogawa , K. , Matsunaga , T. and Miyazaki , S. 1996 . Strengthening of Ti–Ni shape-memory films by coherent subnanometric plate precipitates . Phil. Mag. Lett. , 74 : 137 – 144 .
- Ramirez , A.G. , Huang , X. and Lee , H.-J. 2009 . Crystallization and microstructural development, in Thin Film Shape Memory Alloys: Fundamentals and Device Applications , Edited by: Miyazaki , S. , Fu , Y.Q. and Huang , W.M. 124 – 144 . New York : Cambridge University Press .
- Schuh , C.A. , Lund , A.C. and Nieh , T.G. 2004 . New regime of homogeneous flow in the deformation map of metallic glasses: elevated temperature nanoindentation experiments and mechanistic modeling . Acta Mater , 52 : 5879 – 5891 .
- Richter , A. , Chen , C.L. , Smith , R. , McGee , E. , Thomson , R.C. and Kenny , S.D. 2008 . Hot stage nanoindentation in multicomponent Al–Ni–Si alloys: experiment and simulation . Mater. Sci. Eng. A , 494 : 367 – 379 .
- Lee , H.J. and Ramirez , A.G. 2004 . Crystallization and phase transformations in amorphous NiTi thin films for microelectromechanical systems . Appl. Phys. Lett. , 85 : 1146 – 1148 .
- Grummon , D.S. and Zhang , J.P. 2001 . Stress in sputtered films of near-equiatomic TiNiX on (100) Si: intrinsic and extrinsic stresses and their modification by thermally activated mechanisms . Phys. Status Solidi (a) , 186 : 17 – 39 .
- Liu , Y. and Huang , X. 2004 . Substrate-induced stress and transformation characteristics of a deposited Ti–Ni–Cu thin film . Phil. Mag. , 84 : 1919 – 1936 .
- Huang , X. , Lee , H.-J. and Ramirez , A.G. 2008 . Incomplete martensitic transformations in NiTi thin films . Scr. Mater , 59 : 1067 – 1070 .
- Krulevitch , P. , Ramsey , P.B. , Makowiecki , D.M. , Lee , A.P. , Northrup , M.A. and Johnson , G.C. 1996 . Mixed-sputter deposition of Ni–Ti–Cu shape memory films . Thin Solid Film , 274 : 101 – 105 .
- Stoney , G.G. 1909 . The tension of metallic films deposited by electrolysis . Proc. Roy. Soc. Lond. Math. Phys. Sci. , 82 : 172 – 175 .
- Van Humbeeck , J. and Stalmans , R. 1998 . Characteristics of shape memory alloys, in Shape Memory Materials , Edited by: Otsuka , K. and Wayman , C.M. 149 – 183 . New York : Cambridge University Press .
- Ng , K.L. , Sun , Q.P. , Tomozawa , M. and Miyazak , S. 2010 . “ Wear behavior of NiTi thin film at micro-scale ” . In Int. J. Mod. Phys. B Vol. 24 , 85 – 93 .
- Goken , M. , Sakidja , R. , Nix , W.D. and Perepezko , J.H. 2001 . Microstructural mechanical properties and yield point effects in Mo alloys . Mater. Sci. Eng. A , 319 : 902 – 908 .
- Bei , H. , Lu , Z.P. and George , E.P. 2004 . Theoretical strength and the onset of plasticity in bulk metallic glasses investigated by nanoindentation with a spherical indenter . Phys. Rev. Lett. , 93 : 125504
- Schuh , C.A. , Argon , A.S. , Nieh , T.G. and Wadsworth , J. 2003 . The transition from localized to homogeneous plasticity during nanoindentation of an amorphous metal . Phil. Mag. , 83 : 2585 – 2597 .
- Schuh , C.A. , Mason , J.K. and Lund , A.C. 2005 . Quantitative insight into dislocation nucleation from high-temperature nanoindentation experiments . Nat. Mater , 4 : 617 – 621 .