ABSTRACT
In the present work, the uniaxial compressive mechanical proper\ties of ultrafine grained (UFG) aluminum produced by equal channel angular pressing method were investigated experimentally over a wide temperatures ranging from 77 to 473 K under both quasi-static and dynamic loading conditions. Based on the experimental results, the strain rate, temperature sensitivity, and the apparent activation volume were estimated. The coupling effects of both experimental temperature and applied strain rate on thermal-activated plastic deformation behavior were also investigated. Based on the thermal activation theory, the rate-controlling mechanisms for the UFG aluminum under both quasi-static and dynamic loading conditions were discussed.
1. Introduction
Over hundreds of years, engineers are searching for lightweight and strong materials which were driven by both commercial and defense applications. In 1950s, based on their experimental work carried out on steels, Hall and Petch published a series of papers independently which showed that the strength of metals correspond to grain size and thus a relationship could be established between the two [Citation1,Citation2]. This relationship, known as the Hall–Petch equation, has led to suggestions of ultrafine-grained/nanocrystalline (UFG/NC) metals as candidates for high-hardness materials [Citation3–Citation5]. In the past 30 years, a large number of literatures relating to the fabrication, microstructural character as well as their physical properties of these unusual solids were published. Systematic reviews of research progress in this area can also be found in the works by Valiev and Meyers [Citation3,Citation4].
It should be noted that as the plastic deformation resistances or flow stresses of metals and alloys depend on the microstructure of the material as well as the strain rate and temperature associated with the loading, investigations on the strain rate and temperature sensitivity (TS) of mechanical properties of UFG materials are of great importance for extending our understanding about UFG/NC metals [Citation3,Citation5]. It is generally observed that for metals with face-centered cubic (FCC) crystal structure, the strain rate sensitivity (SRS) increases with reduction in grain size while the body-centered cubic metals show the opposite trend [Citation6]. The variation of SRS with grain size is believed to be correlated with the change in rate-controlling mechanisms. In case of coarse grained (CG) metals, the forest dislocation cutting is the major mechanism for determining the SRS of flow stress [Citation7]. While for UFG/NC metals, grain boundary (GB)-related processes, for example, dislocation–GB interactions and GB sliding/shearing, are supposed to dominate the plastic deformation process, especially at very low strain rates and relatively high temperatures [Citation3,Citation5,Citation8]. Therefore, large SRS values are expected to be displayed in UFG/NC metals with FCC crystal structure [Citation9–Citation18]. The corresponding thermal activation volumes are also found to be the order of 1–10b3 (b is dislocation Burger’s vector), that is, up to a two-order decrease compared to undeformed CG metals (~1000b3) [Citation3,Citation12,Citation19,Citation20]. It should be pointed out that such high SRS values were usually obtained at very low strain rates, for example, 10−6–10−4/s. At normal strain rates, the SRS of UFG/NC metals rarely showed such strong dependence on experimental temperature [Citation9,Citation14]. Besides the enhanced SRS, limited experimental evidences also show that stronger dependence of flow stress and the SRS of UFG/NC metals with FCC crystal structure on experimental temperature can be achieved as the grain size of FCC metals is refined into UFG/NC regime [Citation21–Citation24]. The reduction in thermal activation volume due to the grain refinement is supposed to still be the reason for the enhanced sensitivity of temperature [Citation14,Citation20,Citation21,Citation25–Citation27].
One thing worth mentioning is that since UFG materials fabricated by severe plastic deformation method possess unstable microstructure with a high density of dislocations and non-equilibrium grain boundaries, an important issue when UFG materials are tested at elevated temperatures is preheating-induced microstructural change. Any significant microstructural change is likely to influence the experimental results or lead to unexpected conclusions ( in [Citation28]). Long plastic deformation stage with remarkable strain hardening up to the strain of 0.4 was even observed as the UFG-Cu was compressed at temperatures above its recrystallization temperature (488 K). As the authors suggested that the remarkable strain hardening was a phenomenon of microstructural instability, which has happened at the early stage of compressive deformation, and become more violent with increasing temperature up to recrystallization [Citation28], therefore, although great efforts have been made to understand the strain rate and temperature-coupling effects on the mechanical behavior of UFG/NC metals [Citation22], there remain many issues need further investigation.
For fully understanding of mechanical behavior of ultrafine grained (UFG) metals as well as their rate controlling deformation mechanism, the high purity aluminum was processed via equal channel angular pressing (ECAP) method with 8 passes processing to achieve UFG microstructure. Since the mechanical behavior and plastic deformation mechanism change as the microstructure of the ECAPed-Al varies with the pass number, in a previous work [Citation29], the SRS and deformation kinetics of the ECAPed-Al with different passes (0, 1, 2, 4, and 8 passes) were investigated experimentally over a wide range of strain rate at room temperature. Based on thermal activation theory, the apparent activation volumes of ECAPed-Al over both quasi-static and dynamic strain rate range were determined, respectively, and the deformation mechanism was suggested to change as the pass number increases and depends on the applied strain rate. Therefore, in the present work, the thermal-activated plastic uniaxial compressive deformation of UFG aluminum (UFG-Al, the same with 8 passes ECAPed-Al) were investigated over a wide range of temperatures and strain rates. The strain rate and TS, as well as thermal activation volume, are determined at quasi-static and dynamic strain rates, respectively. The rate-controlling plastic deformation mechanisms were also discussed.
2. Material preparation and experimental procedure
2.1. Material preparation
The raw material used for producing UFG-Al was a commercially available aluminum with a purity of greater than 99.99 containing in wt%. Before ECAP processing, the as-received material was annealed at 773 K for 1 h under inert atmosphere, leading to an initial grain size of ~1 mm. Then, the ECAP method was employed using a hydraulic machine at a speed of ~3 mm/s at room temperature to produce UFG-Al. The ECAP die used in this work has the geometry of an inner corner angle of Φ = 120° and an outer angle of ψ = 20° (). Theoretically, these values of Φ and ψ can lead to an imposed equivalent plastic strain of ~0.635 per passage [Citation30,Citation31]. The ECAP specimens were 10 mm in diameter and 80 mm in length. To achieve UFG microstructure, each specimen was pressed 8 passes using route Bc.
Microstructure of UFG-Al was examined using a Tecnai G2 F20 transmission electron microscope (TEM) operating at 200 kV. The TEM micrograph of UFG-Al is shown in where a homogenous structure characterized by sharp grain boundaries and a larger misorientation angle can be observed. The average grain size was measured to be 1 μm. Dalla Torre et al. [Citation32] referred to the observed sharp boundaries as equilibrium grain boundaries, which are more likely to be in an equilibrium state than cell-wall boundaries.
2.2. Mechanical testing
Quasi-static compressive experiments were performed using an electronic universal testing machine with a maximum load capacity of 10 kN. The split Hopkinson pressure bar (SHPB) was employed in high strain rate experiments [Citation33]. The specimens for both quasi-static and dynamic compressive tests were taken from the center part of the ECAPed rods and machined to cylinders with dimension of Φ4 × 4 mm. The loading direction was parallel to the ECAPed rod axis. During the tests, the strain rates were controlled from 10−3 to 103/s.
The lowest experimental temperature was 77 K which was achieved by immersing the specimen and grips or loading bars into liquid nitrogen. As mentioned before, since UFG materials fabricated by severe plastic deformation possess unstable microstructure, in case of high-temperature experiments, microstructure (in particular the grain size) may be changed significantly due to heating of specimens [Citation3]. Thus, the highest experimental temperature should be chosen to avoid any unexpected influence due to the microstructural change during the heating process. Although the best way to evaluate such changes is through TEM, a substantial amount of information can also be obtained through the combination of micro-hardness tests and microstructural observations [Citation34]. In this work, by combining the micro-hardness measurement and microstructural observation on short-time annealed UFG-Al, the highest testing temperature was determined to avoid any possibly significant microstructural change due to the heating process. This method is similar to Cottrell–Stokes-type experiments [Citation35]. For more detail of the determination of the highest experimental temperature, please refer to [Citation34]. shows the EBSD micrographs (a and b) and grain size distribution (c and d) of UFG-Al before and after heat treatment. It can be seen that although the fraction of grains with grain size larger than 1 μm increases slightly after heat treatment, the average grain size keeps almost unchanged, indicating remarkable grain coarsing does not occur during heat treatment at 473 K for 5 min. That is, it is reasonable to choose 473 K as the highest temperature since if the UFG-Al specimen is heated at 473 K, there will be no remarkable microstructure change before the compressive load is applied. Therefore, during compressive experiments, the elevated experimental temperatures were selected as 293, 373, and 473 K, respectively.
Figure 3. EBSD micrograph (a and b) and grain size distribution (c and d) of UFG-Al before and after heat treatment.
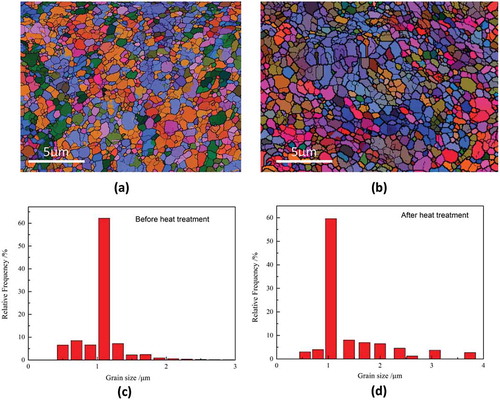
The high strain rate experiments were performed using the SHPB, as shown in . The primary components of the classic SHPB system are two long elastic bars: the incident and transmission bars. A short specimen is sandwiched between the two bars. When a projectile launched from a gas gun impacts the free end of the incident bar, a compressive pulse is generated and travels along the incident bar towards the specimen. Due to the mismatch of wave impedance between the specimen and loading bars, while reaching the bar/specimen interface, part of the stress pulse is reflected, and part of it is transmitted into the transmission bar. According to the one-dimensional elastic stress-wave theory, the dynamic strain, stress, and strain rate of tested specimen can be calculated, respectively. It should also be noted that in classic SHPB experiments, the incident and transmission bars must be in close touch with the specimen. In case of high-temperature experiments, if the loading bars are heated with the specimen, a strong temperature gradient within the bars will be generated, which will cause the gradient of both the elastic modulus and longitudinal elastic wave velocity within the loading bars. Therefore, adjustment is necessary during the post-processing of the experimental data. However, such technique has limitations since the temperature gradient is hard to be directly measured or estimated. To overcome this limitation and improve the high temperature experimental capability of SHPB, a synchronically assembled heating system (see ) was designed to be incorporated into the conventional SHPB apparatus. This technique enables us to preheat the specimen with the incident and transmission bars kept away from the heating zone of the furnace. After the desired specimen temperature has been achieved, the bars are brought into close contact with the specimen automatically (for more details, see [Citation36]).
Figure 4. High-temperature SHPB set-up with a synchronically assembled heating system [Citation36]. 1, inlet valve; 2, magnetic outlet valve; 3, main air chamber; 4, air chamber; 5, strike; 6, incident bar; 7, transmission bar; 8, plunger; 9, heating furnace; 10, air pipe; 11, electrical wire; 12, time relay; 13, switch; 14, sample; 15, sleeve; and 16, thermocouple.
![Figure 4. High-temperature SHPB set-up with a synchronically assembled heating system [Citation36]. 1, inlet valve; 2, magnetic outlet valve; 3, main air chamber; 4, air chamber; 5, strike; 6, incident bar; 7, transmission bar; 8, plunger; 9, heating furnace; 10, air pipe; 11, electrical wire; 12, time relay; 13, switch; 14, sample; 15, sleeve; and 16, thermocouple.](/cms/asset/6252b248-26c6-41e3-a5c6-1f7efde1cb66/tsnm_a_1300201_f0004_c.jpg)
3. Experimental results
3.1. Stress versus strain response
The true stress versus true strain curves of UFG-Al tested at elevated temperatures and strain rates are shown in (a–f). For comparison, the experimental results for CG-Al are also shown in (g,f). It can be seen that the UFG-Al displays higher strength as the grain size is reduced into ultrafine grain regime, which can be fully explained via the classic Hall–Petch relationship, that is, (where σy is the 0.2% proof stress, σ0 and kH−P are constants). If substituting σ0 = 11 MPa and kH−P = 115 MPa · μm1/2 [Citation37] into the Hall–Petch relationship, it gives a 0.2% proof stress of 126 MPa, which is in good agreement with the experimental value of the present UFG-Al deformed at the strain rate 0.001/s and room temperature. However, although high-yield strength is achieved, remarkable strain hardening is only observed at the early stage of plastic deformation of UFG-Al when it is compressed under quasi-static-loading condition.
Figure 5. True stress vs. strain curves for UFG-Al at the strain rate of (a) 0.001/s, (b) 0.01/s, (c) 0.1/s, (d) 1000/s, (e) 3000/s, and (f) 5000/s at elevated temperatures. For comparison, the true stress vs. strain curves for CG-Al tested at the strain rates (g) 0.001/s and (h) 3000/s at elevated temperatures are also shown.
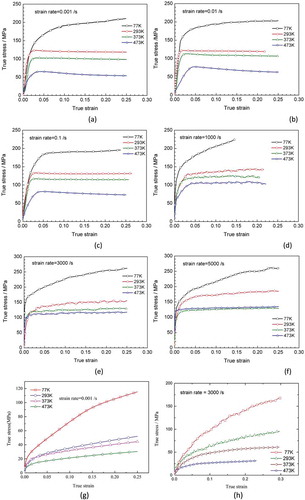
To qualify the strain-hardening capacity, the strain-hardening rate (defined as dσ/dε, where σ and ε are true stress and true strain, respectively) versus true strain curves are plotted at elevated temperatures. shows the typical strain-hardening rate for UFG-Al at quasi-static (strain rate 0.001/s) and dynamic (strain rate 3000/s) loading rates at different temperatures. The inset in ) is the same plot for conventional coarse-grained Al at 0.001/s. Typically, the conventional CG Al shows apparent strain-hardening behavior. Although the enhanced dynamic recovery of dislocations at high temperatures leads to a reduction in the strain-hardening capacity, positive strain-hardening rate still exists for CG-Al even at 473 K. Such a response is normally observed in FCC metals with coarse grains [Citation38,Citation39]. However, for UFG material, high strain-hardening rate is only observed at the early stage of plastic deformation. Even in this stage, the strain-hardening rate decreases sharply with strain. It has been estimated that the dislocation density for the UFG-Al fabricated by SPD methods is on the order of 1014 m−2 which is close to saturation [Citation29]. At the beginning of plastic deformation, a large number of dislocations generating from dislocation sources subsequently interact with grain or sub-grain boundaries, causing high strain-hardening rate. However, the enhanced dynamic recovery process due to extremely high dislocation density makes the balance between generation and annihilation of dislocations quickly [Citation3,Citation40–Citation42]. Therefore, a steady-state, long deformation stage is achieved while remarkable strain hardening is only observed when the UFG-Al was compressed at 77 K. However, as the experimental temperature increases to 293 K and above, slight strain softening occurs when compressed at 0.001/s. It should be noted that in our experiments, no shear band was observed on the surfaces of post-deformed UFG-Al specimens. Thus, the localized deformation can be ruled out for the observed post-yielding strain softening. In this work, such mechanisms as dynamic recovery, dynamic recrystallization, or stress-driven grain growth which can be enhanced at elevated temperatures are supposed to be responsible for the reduction in the strain-hardening rate as well as the strain softening at high temperatures in UFG/NC metals [Citation43–Citation45]. Similar behaviors were also observed in high energy ball-milling Al and Cu, UFG cryomilled Al 5083, and ECAPed UFG-Cu [Citation21,Citation34,Citation46]. One thing worth mentioning is that in the present work, although remarkable strain hardening is observed at temperatures of 373 and 473 K as the UFG-Al was compressed quasi-statically, the strain-hardening capacity vanishes after the true strain exceeds no more than 0.05. However, in the previous work by Yu et al. [Citation28], the remarkable strain hardening extends to the true strain ~0.4. Moreover, since the thermal instability test has shown that no remarkable microstructure change before the compressive load is applied if the UFG-Al specimen is heated at 473 K, the experimental results in the present work are believed to be obtained without the instability of the microstructure.
Figure 6. Strain-hardening rate for UFG-Al at (a) quasi-static (strain rate 0.001/s) and (b) dynamic (strain rate 3000/s) loading rates. The inset in (a) is the same plot for conventional coarse-grained Al at quasi-static loading rate (strain rate 0.001/s).
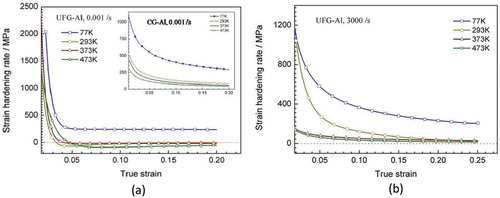
In case of compressed dynamically, strain-hardening capacity is regained at all experimental temperature. Even though remarkable strain-hardening behavior is only achieved when UFG-Al is compressed dynamically at extremely low temperature (77 K) (shown in ), it is believed that the suppression of dislocation dynamic recovery under the combined condition of low temperature and dynamic loading is the main reason for the renaissance of strain-hardening capacity of UFU-Al [Citation47]. The fact that UFG materials can regain the ability to strain hardening at cryogenic temperature and high strain rate has also been employed as a strategy to achieve larger uniform tensile deformation by Wang [Citation41,Citation42,Citation48].
3.2. Temperature and strain rate sensitivities
Since plastic deformation of metals under an applied stress is a well-known thermally activated process, which always depends on both strain rate and temperature, investigations on the sensitivity of UFG materials to strain rate and temperature are necessary to extending our understanding about these unusual solids. Usually, the TS of flow stress is defined as
It should be pointed out that since the flow stress of metals usually decrease with temperature, Equation (1) gives a negative value of TS factor which indicates the reduction in flow stress with increasing temperature. In the present work, to quantify the influence of experimental temperature on the flow stress, the TS factor at fixed strain 0.05, 0.10, 0.15, and 0.20 and different strain rates were determined approximately based on the experimental results. For the convenience of comparison, only the absolute value of TS factor was shown in , and experimental data on CG Cu at the strain rates of 0.001 and 3000/s are presented as well. It can be seen from that the TS of UFG-Al does increase remarkably as the grain size is refined into nano-regime, no matter the material is compressed under quasi-static or dynamic loading condition. Similar trends were also observed in UFG-Cu, NC-Ni [Citation14,Citation21,Citation49].
Figure 7. Temperature sensitivity factor for CG-Al and UFG-Al at different strain rates and fixed strains of 0.05, 0.10, 0.15, and 0.20.
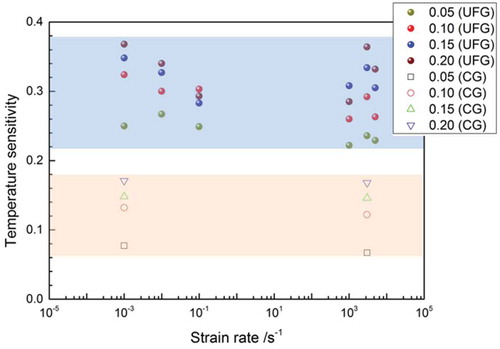
The dependence of flow stress on applied strain rate is usually described quantitatively by a coefficient named SRS factor m, which can be expressed as
Although the value of m is a function of applied strain, it’s impractical to estimate the SRS at every strain level. In practice, it is often given in the form of values at certain fixed strains. Meanwhile, m as defined in Equation (2) should be measured for a fixed microstructural state of the material. Thus, strain rate jump or stress relaxation tests are normally employed to determine its value [Citation14,Citation15,Citation17]. Occasionally, the values of SRS were also determined approximately by using log–log flow stress versus strain rate plots at a certain strain from which m was derived as the slope of a linear regression fit [Citation6,Citation13]. In the present work, SRS values at elevated temperatures were determined using the latter method.
shows the SRS factors at different temperatures for UFG-Al (squares) and CG-Al (triangles), respectively. For comparison, the quasi-static m values derived by May et al. [Citation15] on both UFG-Al (hollow circles) and CG-Al (hollow triangles) as well as dynamic values on CG-Al (hollow stars) by Chiddister et al. [Citation39] are also plotted in . Obviously, SRS of the UFG-Al is strongly enhanced comparing with its CG counterpart. Actually, the fact that the SRS increases with the reduction in grain size has been observed for several metals with FCC crystal structure [Citation6,Citation15]. Moreover, an obvious increase of SRS with increasing temperature is observed for both UFG and CG Al under whatever quasi-static or dynamic loading condition. Similar phenomenon was observed by Khan et al. [Citation50] in UFG-Al6061 processed using ECAP method. It should be pointed out that as m is defined in logarithmic term, such an evolution of m can lead to an obvious strength jump upon strain rate change. One thing also worth mentioning is that for UFG-Al developed by May et al. [Citation15], the SRS shows much higher values as well as higher sensitivity to testing temperature if compared with the present UFG-Al, that is, more than 10-fold increase with temperature increasing from 298 to 473 K. The reason that for the present UFG-Al, the SRS values and its sensitivity to temperature at quasi-static strain rates are much lower than those in May’s work [Citation15] might be attributed to the larger grain size as well as higher applied strain rates employed in this work.
4. Discussions
Since plastic deformation of metals is thermal-activated process in which thermal fluctuation can assist the applied stress in surmounting obstacles to plastic flow, an effective method for studying the physical mechanism of plastic deformation of crystals is thermal-activation analysis. According to the thermal activation theory, the shear strain rate, , can be given by an Arrhenius-type equation as [Citation51]
where the is a pre-exponential constant or characteristic strain rate at a given microstructure. k and T are the Boltzmann constant and absolute temperature, respectively. ∆G is the activation energy and is usually a strong function of the thermal-activated shear stress component τ* as
where ∆F is the activation energy needed to be provided by thermal activation alone (in the absence of any applied stress). V* is thermal activation volume. For the thermal activated shear stress component τ*, it can be expressed as τ* = τ − τa where τ is the applied shear stress and τa is the athermal internal stress stemming from long-range obstacles. If substituting Equation (4) into Equation (3) and replacing τ* with τ–τa, the relationship between applied shear stress with shear strain rate and temperature can be rewritten as [Citation52]
With the von Mises yield criterion, the shear stress can be related to normal stress by a factor . Similarly, for the shear and longitudinal strain rates,
. If substituting above relations into Equation (5), we will have
where is the athermal component of total stress in normal form,
reference longitudinal strain rate, and
applied longitudinal strain rate. By taking partial differential with respect to
, one obtains
Recalling that the SRS can be estimated as Equation (2), the apparent activation volume can then be estimated by
shows the apparent activation volumes as a function of temperature in which b = 2.86 × 10−10 m is the Burger’s vector of aluminum. For comparison, the values derived from May’s work [Citation15] are also included in this figure. The inset in is the same plot for conventional coarse-grained Al at quasi-static and dynamic loading rates which were derived from experimental results of May’s [Citation15] and Chiddister’s [Citation39] published works, respectively. If compared with its CG counterpart, the apparent activation volumes for UFG-Al are at least one order of magnitude lower (noted that at room temperature V* for CG-Al is even close to two orders higher than that of UFG-Al). Since it was proposed by Wei [Citation6] that at a fixed temperature, SRS is flow stress and activation volume dependent, and compared to its CG counterpart, there is a remarkable reduction in activation volume while the enhancement in flow stress is limited, it is not surprising to observe an obvious enhancement in SRS.
Figure 9. Normalized apparent activation volume (V*/b3) vs. T for the present UFG-Al at quasi-static (blue circles) and dynamic loading rates (wine triangles) as well as UFG-Al by May et al. [Citation15] deformed under static loading condition (triangles). The inset is the same plot for conventional coarse-grained Al at quasi-static (red circles) and dynamic loading rates (green squares) respectively (static data from May et al. [Citation15] and dynamic data from Chiddister et al. [Citation39]).
![Figure 9. Normalized apparent activation volume (V*/b3) vs. T for the present UFG-Al at quasi-static (blue circles) and dynamic loading rates (wine triangles) as well as UFG-Al by May et al. [Citation15] deformed under static loading condition (triangles). The inset is the same plot for conventional coarse-grained Al at quasi-static (red circles) and dynamic loading rates (green squares) respectively (static data from May et al. [Citation15] and dynamic data from Chiddister et al. [Citation39]).](/cms/asset/2185134d-1b33-452c-a605-f2a4fd5a2d20/tsnm_a_1300201_f0009_c.jpg)
As mentioned before, although the quasi-static SRS at 293 K (m = 0.016) for present UFG-Al is comparable with that determined by May et al. (m = 0.014 at 298 K), much higher SRS values were achieved in May’s UFG-Al when compressed at high temperatures. Such high values are believed to be mainly due to the very low applied strain rates. As the authors claimed in their work that deformation mechanisms correlated to grain boundaries or diffusive process should be the dominant rate-controlling processes in their UFG-Al [Citation15]. It has been proved by many researchers that such kinds of GB deformation often lead to unusually high SRS values [Citation3,Citation14,Citation53–Citation55].
Similarly, the dependence of TS on grain size can also be related to variation in activation volume. Based on the thermal activated theory, the TS factor can be expressed in the following form [Citation10,Citation34]
Equation (9) does indicate that at fixed strain rate, the TS depends on the evolution of activation volume. For UFG materials with FCC crystal structure, the activation volume has been proven to decrease with a reduction in grain size. Therefore, the smaller the grain size, the higher the TS of flow stresses is expected. This conclusion is in good agreement with the experimental data. Since the pre-exponential strain rate, , is of the order of 106–108/s [Citation56] which is several orders of magnitude higher than that in the present tests, values of TS is expected to be negative according to Equation (9). This indicates the reduction in flow stress with increasing temperature.
We all know that fully annealed metals with FCC structure usually have a large activation volume, that is, ~102–103b3, and the dominant rate-controlling process is the intersection of moving dislocations cutting through forest dislocations [Citation57]. In case that the grain size is reduced to ultrafine level (below 1 μm but above 100 nm) or nano-grain regime (grain size below 100 nm), GB-related processes, such as Coble creep [Citation58–Citation61], GB sliding/shear mediated by GB diffusion [Citation11,Citation56], and dislocation–boundary interactions [Citation14,Citation25,Citation32], have been proposed to be the possible rate-controlling mechanisms. Among these mechanisms, we note that the Coble creep can be ruled out first based on the SRS and activation volume values obtained experimentally. When such mechanism dominates, the plastic deformation should occur at a relatively low stress and a high homologous temperature, which makes it possible that the exponential stress activation term is small and the exponential becomes approximately linear in stress [Citation14]. At the same time, the expected SRS when Coble creep operates is usually much higher, that is, m = 0.1–0.3, while the corresponding activation volume, which is on the order of atom volume (= 1b3). These are inconsistent with our findings i.e. V* in the range of 70–150b3 and quasi-static SRS 0.013–0.058 for current UFG-Al [Citation3,Citation15,Citation54,Citation62]. Similarly, the grain-boundary shear could also be ruled out since it bears the same order of activation volume with Coble creep [Citation56,Citation63]. More importantly, recent analysis presented evidence that such diffusion-assisted GB processes are more likely operate at very low rates and high temperatures, especially in metals with grain size below tens of nanometers [Citation3,Citation14,Citation64,Citation65]. That is the grain size of current UFG-Al seems not small enough to activate these diffusion-assisted GB processes. Therefore, the Coble creep and GB sliding/shear are not the prominent deformation mode for current UFG-Al compressed at ordinary and high strain rates.
Dislocation motion often plays important roles in plastic deformation of metals and alloys. In coarse-grained metals, the plastic deformation at relatively low temperature is usually mediated by the nucleation and motion of dislocations. However, when the average grain size of materials is below some critical value, that is, tens of nanometers, dislocation sources and pile-ups are not expected to exist within the individual grains because of the limited grain size. In such case, the GB diffusion-mediated mechanisms are believed to dominate the plastic deformation. But even though the dislocation motions still play a role in plastic deformation [Citation66–Citation70]. For example, in situ TEM experiments on NC nickel films with an average grain size of about 10 nm show that although GB-mediated processes have become a prominent deformation mode, trapped lattice dislocations are observed in individual grains following deformation [Citation66]. In such tiny grains, grain boundaries are more likely acting as the source of dislocations. For metals with larger grain size (above the critical value associated with GB diffusion), the plastic deformation is believed to be dominated by dislocation–GB interactions [Citation10,Citation14,Citation71]. There are three likely scenarios associated with the interaction of dislocations with grain boundaries: punching of a mobile dislocation through a dense bundle of GB dislocations, the emission of dislocations from grain boundaries, and the de-pinning of a propagating dislocation that is pinned by grain boundaries [Citation14]. In the case of CG materials, these unusual activated processes are insignificant during plastic deformation but their contributions increase with decreasing grain size, possibly become dominant in UFG or NC materials. In the present work, the dislocation–GB interaction mechanism might be practical since the UFG-Al possesses such microstructural feature as equiaxed grains with the grain size close to 1 μm.
Theoretically, the activation volume associated with the thermal-activated plastic deformation can be calculated through the following equation [6]:
where ξ is the distance swept out by the gliding dislocation during one activation event which equals to b approximately, and l* is the length of dislocation segment involved in the thermal activation process. In the case of the dislocation–GB interactions, the length of dislocation segment involved in the thermal-activation process can be expressed as l* ≈ χd [Citation6,Citation10]. Therefore, the activation volume can be estimated by
where d is the average grain size, and χ (0 < χ ≤ 1) is a proportionality factor denoting the interactions of dislocation with grain boundaries, which is related to the grain size d and can be expressed as [Citation25,Citation64]
where m0 is the SRS exponent of CG counterpart; η = kH–P/(3 Mαμb1/2), which can be roughly estimated from the slope of Hall–Petch relationship (kH–P), Taylor orientation coefficient (M = 3.05), dislocation interaction constant (α = 0.5), and the shear modulus (26 GPa for bulk Al). Taking kH–P = 115 MPa · μm1/2, m0 = 0.0048 and m = 0.0162, χ can be calculated to be 0.124 at room temperature. Substituting this value and an average grain size d = 1 μm into Equation (11), the estimated activation volume is 420b3 which is larger than that of experimentally estimated value for the present UFG-Al (~150b3). Based on these parameters, it is physically to point out that at least in the present UFG-Al, dislocation–GB interactions might not play a dominant role in plastic deformation. Another possible explanation for that such dislocation–GB interaction processes are not applicable may be the grain size in the present UFG-Al that is still too large to activate any of three likely scenarios associated with the interaction of dislocations with grain boundaries.
After ruling out such unusual processes, that is, Coble creep, GB sliding/shear, and dislocation–GB interactions, as the dominant rate-controlling mechanism, let’s take a look at the possibility of conventional forest dislocation intersection. When such mechanism operates, l* is supposed to equal the square root of dislocation density ρ, that is, l* ≈ ρ−1/2 [Citation6,Citation10] and therefor the activation volume can be estimated from
According to Equation (13), to achieve the activation volume value, that is, ~150b3 under quasi-static loading, the corresponding dislocation density should be ~3.6 × 1014 m−2. This value is a little higher but still comparable with the results reported in literatures for ECAPed UFG-Al [Citation72,Citation73]. Actually, there are many studies which did show that in UFG metals developed by severely plastic deformation method, dislocations may concentrate in the vicinity of grain boundaries or in the so-called GB affect zone, while the interior of the grains are usually very low in the density of dislocations [Citation4,Citation20,Citation24,Citation74–Citation76]. The fact that the high density of dislocations is not observed under TEM might be due to the relaxation in very thin TEM samples near free surfaces [Citation14]. Thus, during plastic deformation, moving dislocations may travel almost unimpeded through the lattice of the interior of the grains but slow down and spend most of time on fighting against the forest dislocations near/at grain boundaries and therefore enable the rate-controlling mechanism to be medicated by dislocations intersection near/at grain boundaries [Citation3,Citation10,Citation56,Citation77]. Therefore, one possibility for the larger value of estimated dislocation density in the presence UFG-Al compared to results reported in literatures might be that the locally high density of dislocations arranging near/at the submicron grain boundaries [Citation56,Citation78,Citation79].
One thing also worth mentioning is that under quasi-static loading, the activation volumes are an order higher than those under dynamic loading. This is an indication of variation in thermal-activated deformation mechanism when the applied strain rate is increased from quasi-static to dynamic regime. Conventionally, for CG FCC metals with high purity, in case of high strain rate deformation (e.g. the strain rate above 103/s), viscous drag becomes the important obstacles to moving dislocations. In contrast to the forest dislocation intersection process where the time taken by moving dislocations to travel between the barriers is negligible compared with that spending at the obstacles, when the viscous drag operates the free traveling time between successive arrests becomes of the same order as the waiting time. In this case, the flow stress becomes dependent on the drag exerted by the lattice vibrations or the conduction electrons, and smaller values of activation volumes are expected [Citation80]. Meanwhile, the velocity of dislocation in this case is proposed to be a linear function of stress. Therefore, a linear relationship between flow stress and strain rate can be expected [Citation80,Citation81]
where τB is back stress corresponding to the stress required to overcome the forest dislocation barriers to the dislocation motion and α is the slope of the stress–strain rate curve above the back stress.
For the present UFG-Al specimens, it’s possible that the viscous drag process plays an important role since the dislocation activations have been proved to be still the main carrier of plastic deformation. To verify this deduction, the strain rate versus flow stress curves for UFG-Al are plotted (shown in ). Apparently, the linear relationship between stress and strain rate does prevail at high strain rate without any deviation. This suggests that some regarding viscous drag force which is proportional to the dislocation velocity is acting on the dislocations.
Figure 10. The linear dependence of flow stress at 10% strain on strain rate dependence at high-strain rates for UFG-Al deformed at elevated temperatures.
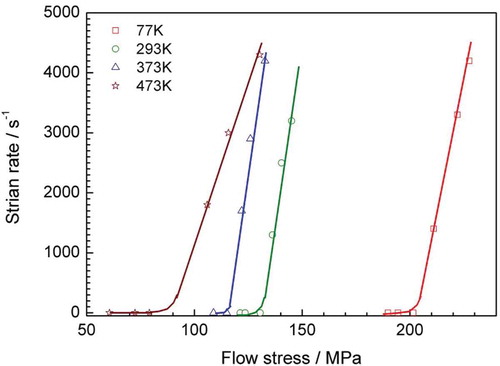
The above deduction indicates that the viscous drag does play an important role in dynamically plastic deformation in the present UFG-Al at high strain rates. Actually, analytic works by Borodin et al. [Citation82] and Weinberger et al. [Citation83] also suggested that the viscous effect is even a dominant factor during high strain rate deformation even in NC materials. In such case, the boundary viscosity acts as the viscous source for plastic deformation.
5. Summary and concluding remarks
In the present work, we have carried out uniaxial compressive experiments on UFG-Al fabricated by the ECAP method over a wide range of temperatures and strain rates. Compared with their conventional CG counterparts, the flow stress obtained at a fixed strain depends more strongly on both temperature and strain rate associated with the loading. Meanwhile, the SRS factors determined at dynamic strain rates are much larger than those determined at quasi-static strain rates. With increasing temperatures, the SRS for UFG-Al increases as well. The values of thermal activation volume obtained at elevated temperatures are much smaller than those for the CG FCC materials. This is in good consistent with the stronger temperature and strain rate dependence observed experimentally. Based on analysis of experimentally determined parameters, such mechanisms as Coble creep, GB sliding/shear, and the interaction of dislocations with grain boundaries are ruled out as the rate-controlling mechanism accommodating the plastic flow. Instead, the thermally activated cutting of forest dislocations in the lattice which is known as the rate-controlling mechanism in CG FCC metals is proposed to be still applicable in the present UFG-Al with the grain size 1 μm. However, such process is more likely to occur in the higher dislocation–density structure adjacent to the grain boundaries. The facts that much higher values of SRS as well as lower apparent activation volumes at dynamic strain rates compared to quasi-static strain rates indicate that some regarding viscous drag force appears to be an additional activated process in action, with a higher activation barrier, when the applied strain rate enters the dynamic regime.
Acknowledgments
This work was performed under the financial support from the National Science Foundation of China (grant No. 11522220). T. Suo would also like to thank Dr. P. Eswar, C. Q. Chen, and Y. Zhang (The Johns Hopkins University, USA) for useful discussions. We also thank Ms. LF Li (North Western Polytechnical University) for her help in TEM observations.
Disclosure statement
No potential conflict of interest was reported by the authors.
Additional information
Funding
Notes on contributors
Jin Su
Jin Su, PhD, is at School of Aeronautics, Northwestern Polytechnical University, Xi’an, China. His research interest includes dynamic response of advanced materials.
Zhong-bin Tang
Zhong-bin Tang, PhD, is at School of Aeronautics, Northwestern Polytechnical University, Xi’an, China. His research interest includes solid mechanics.
Cun-xian Wang
Cun-xian Wang, PhD, is at School of Aeronautics, Northwestern Polytechnical University, Xi’an, China. His research interest includes solid mechanics and composites.
Tian Ye
Tian Ye, Master, School of Aeronautics, is at Northwestern Polytechnical University, Xi’an, China. His research interest includes dynamic response of advanced materials.
Tao Suo
Tao Suo, PhD, is at School of Aeronautics, Northwestern Polytechnical University, Xi’an, China. His research interest includes solid mechanics and advanced materials.
Yu-long Li
Yu-long Li, PhD, is at School of Aeronautics, Northwestern Polytechnical University, Xi’an, China. His research interest includes impact dynamics and advanced materials.
References
- E.O. Hall, The deformation and ageing of mild steel: III discussion of results, Proc. Phys. Society. Section B 64 (1951), pp. 747–753. doi:10.1088/0370-1301/64/9/303
- N.J. Petch, The cleavage of polycrystals, J. Iron. Steel. Inst. 174 (1953), pp. 25.
- M.A. Meyers, A. Mishra, and D.J. Benson, Mechanical properties of nanocrystalline materials, Prog. Mater. Sci. 51 (2006), pp. 427–556. doi:10.1016/j.pmatsci.2005.08.003
- R.Z. Valiev, R.K. Islamgaliev, and I.V. Alexandrov, Bulk nanostructured materials from severe plastic deformation, Prog. Mater. Sci. 45 (2000), pp. 103–189. doi:10.1016/S0079-6425(99)00007-9
- J.C.M. Li, Mechanical Properties of Nanocrystalline Materials, Pan Stanford Publishing, New York, 2011.
- Q. Wei, Strain rate effects in the ultrafine grain and nanocrystalline regimes-influence on some constitutive responses, J. Mater. Sci. 42 (2007), pp. 1709–1727. doi:10.1007/s10853-006-0700-9
- M.A. Meyers, Dynamic Behavior of Materials, Wiley, New York, 1994.
- G. Saada and T. Kruml, Deformation mechanisms of nanograined metallic polycrystals, Acta. Mater. 59 (2011), pp. 2565–2574. doi:10.1016/j.actamat.2010.12.035
- T. Suo, Y. Li, K. Xie, F. Zhao, K. Zhang, and Q. Deng, Experimental investigation on strain rate sensitivity of ultra-fine grained copper at elevated temperatures, Mech. Mater. 43 (2011), pp. 111–118. doi:10.1016/j.mechmat.2011.02.002
- G. Malygin, Analysis of the strain-rate sensitivity of flow stresses in nanocrystalline FCC and BCC metals, Phys. Solid State 49 (2007), pp. 2266–2273. doi:10.1134/S1063783407120098
- H. Conrad and K. Jung, On the strain rate sensitivity of the flow stress of ultrafine-grained Cu processed by equal channel angular extrusion (ECAE), Scripta. Mater. 53 (2005), pp. 581–584. doi:10.1016/j.scriptamat.2005.04.030
- Q. Wei, S. Cheng, K.T. Ramesh, and E. Ma, Effect of nanocrystalline and ultrafine grain sizes on the strain rate sensitivity and activation volume: Fcc versus bcc metals, Mater. Sci. Eng. A 381 (2004), pp. 71–79. doi:10.1016/j.msea.2004.03.064
- G.T. Gray III, T.C. Lowe, C.M. Cady, R.Z. Valiev, and I.V. Aleksandrov, Influence of strain rate & temperature on the mechanical response of ultrafine-grained Cu, Ni, and Al-4Cu-0.5Zr, Nanostruct Mater 9 (1997), pp. 477–480. doi:10.1016/S0965-9773(97)00104-9
- Y.M. Wang, A.V. Hamza, and E. Ma, Temperature-dependent strain rate sensitivity and activation volume of nanocrystalline Ni, ActaMater. 54 (2006), pp. 2715–2726.
- J. May, H.W. Höppel, and M. Göken, Strain rate sensitivity of ultrafine-grained aluminium processed by severe plastic deformation, Scripta. Mater. 53 (2005), pp. 189–194. doi:10.1016/j.scriptamat.2005.03.043
- K. Gholamreza, K.M. Javad, and N. Ali, Microstructure and hot deformation behavior of AlMg6 alloy produced by equal-channel angular pressing, Mater. Sci. Eng. A5 42 (2012), pp. 15–20.
- C. Langlois, S. Guérin, M. Sennour, M.J. Hÿtch, C. Duhamel, and Y. Champion, Thermo-mechanical behaviour of nanostructured copper, J. Alloy. Compd 434-435 (2007), pp. 279–282. doi:10.1016/j.jallcom.2006.08.300
- Y.J. Li, W. Blum, and F. Breutinger, Does nanocrystalline Cu deform by Coble creep near room temperature?, Mater. Sci. Eng. A 387-389 (2004), pp. 585–589. doi:10.1016/j.msea.2003.11.086
- Y.M. Wang, A.V. Hamza, and E. Ma, Activation volume and density of mobile dislocations in plastically deforming nanocrystalline Ni, Appl. Phys. Lett. 86 (2005), pp. 1–3.
- P. Barai and G.J. Weng, Mechanics of very fine-grained nanocrystalline materials with contributions from grain interior, GB zone, and grain-boundary sliding, Int. J. Plasticity 25 (2009), pp. 2410–2434. doi:10.1016/j.ijplas.2009.04.001
- T. Suo, Y. Li, K. Xie, F. Zhao, K. Zhang, and Y. Liu, The effect of temperature on mechanical behavior of ultrafine-grained copper by equal channel angular pressing, Mater. Sci. Eng. A 527 (2010), pp. 5766–5772. doi:10.1016/j.msea.2010.05.046
- B. Farrokh and A.S. Khan, Grain size, strain rate, and temperature dependence of flow stress in ultra-fine grained and nanocrystalline Cu and Al: Synthesis, experiment, and constitutive modeling, Int. J. Plasticity 25 (2009), pp. 715–732. doi:10.1016/j.ijplas.2008.08.001
- Q.W. Jiang, L. Xiao, and X.W. Li, A comparison of temperature-dependent compressive deformation features of ultrafine-grained Ti and Cu Produced by ECAP, Mater. Sci. Forum 682 (2011), pp. 41–45. doi:10.4028/www.scientific.net/MSF.682.41
- J. Li and G.J. Weng, A secant-viscosity composite model for the strain-rate sensitivity of nanocrystalline materials, Int. J. Plasticity 23 (2007), pp. 2115–2133. doi:10.1016/j.ijplas.2007.03.016
- G.A. Malygin, Plasticity and strength of micro- and nanocrystalline materials, Phys. Solid. State. 49 (2007), pp. 1013–1033. doi:10.1134/S1063783407060017
- T. Kunimine, N. Takata, N. Tsuji, T. Fujii, M. Kato, and S. Onaka, Temperature and strain rate dependence of flow stress in severely deformed Copper by accumulative roll bonding, Mater. Trans. 50 (2009), pp. 64–69. doi:10.2320/matertrans.MD200809
- D.H. Shin, D.Y. Hwang, Y.J. Oh, and K.T. Park, High-strain-rate superplastic behavior of equal-channel angular-pressed 5083 Al-0.2 Wt Pct Sc, Metall. Mater. Trans. A-Phy. Metall. Mater. Sci. 35 (2004), pp. 825–837. doi:10.1007/s11661-004-0009-8
- Z.Y. Yu, Q.W. Jiang, and X.W. Li, Temperature-dependent deformation and damage behaviour of ultrafine-grained copper under uniaxial compression, Physica. Status. Solidi. A-Applications Mater. Sci. 205 (2008), pp. 2417–2421. doi:10.1002/pssa.200824003
- T. Suo, Y.Z. Chen, Y.L. Li, C.X. Wang, and X.L. Fan, Strain rate sensitivity and deformation kinetics of ECAPed aluminium over a wide range of strain rates, Mater. Sci. Eng. A 560 (2013), pp. 545–551. doi:10.1016/j.msea.2012.09.100
- T. Suo, Y. Li, Y. Guo, and Y. Liu, The simulation of deformation distribution during ECAP using 3D finite element method, Mater. Sci. Eng. A 432 (2006), pp. 269–274. doi:10.1016/j.msea.2006.06.035
- Y. Iwahashi, J. Wang, Z. Horita, M. Nemoto, and T.G. Langdon, Principle of equal-channel angular pressing for the processing of ultra-fine grained materials, Scripta. Mater. 35 (1996), pp. 143–146. doi:10.1016/1359-6462(96)00107-8
- F. Dalla Torre, R. Lapovok, J. Sandlin, P.F. Thomson, C.H.J. Davies, and E.V. Pereloma, Microstructures and properties of copper processed by equal channel angular extrusion for 1–16 passes, ActaMater. 52 (2004), pp. 4819–4832.
- H. Kolsky, An investigation of the mechanical properties of materials at very high rates of loading. proceedings of the physical society, Proc. Phys. Soc. B62 (1949), pp. 676–700. doi:10.1088/0370-1301/62/11/302
- T. Suo, Y.L. Li, F. Zhao, X.L. Fan, and W.G. Guo, Compressive behavior and rate-controlling mechanisms of ultrafine grained copper over wide temperature and strain rate ranges, Mech. Mater. 61 (2013), pp. 1–10. doi:10.1016/j.mechmat.2013.02.003
- E. Huskins, B. Cao, B. Li, and K. Ramesh, Temperature-dependent mechanical response of an UFG aluminum alloy at high rates, Exp.Mech 52 (2012), pp. 185–194. doi:10.1007/s11340-011-9565-1
- Y.L. Li, Y.Z. Guo, H.T. Hu, and Q. Wei, A critical assessment of high-temperature dynamic mechanical testing of metals, Int. J. Impact. Eng 36 (2009), pp. 177–184. doi:10.1016/j.ijimpeng.2008.05.004
- H. Hasegawa, S. Komura, A. Utsunomiya, Z. Horita, M. Furukawa, M. Nemoto, and T.G. Langdon, Thermal stability of ultrafine-grained aluminum in the presence of Mg and Zr additions Mater, Mater. Sci. Eng. A 265 (1999), pp. 188–196. doi:10.1016/S0921-5093(98)01136-8
- S. Nemat-Nasser and Y. Li, Flow stress of f.c.c. polycrystals with application to OFHC Cu, Acta. Mater. 46 (1998), pp. 565–577. doi:10.1016/S1359-6454(97)00230-9
- J. Chiddister and L. Malvern, Compression-impact testing of aluminum at elevated temperatures, Exp. Mech 3 (1963), pp. 81–90. doi:10.1007/BF02325890
- Y.M. Wang and E. Ma, Strain hardening, strain rate sensitivity, and ductility of nanostructured metals, Mater. Sci. Eng. A 375-377 (2004), pp. 46–52. doi:10.1016/j.msea.2003.10.214
- Y.M. Wang and E. Ma, On the origin of ultrahigh cryogenic strength of nanocrystalline metals, Appl. Phys. Lett 85 (2004), pp. 2750–2752. doi:10.1063/1.1799238
- Y.M. Wang and E. Ma, Three strategies to achieve uniform tensile deformation in a nanostructured metal, Acta. Mater. 52 (2004), pp. 1699–1709. doi:10.1016/j.actamat.2003.12.022
- Y.J. Li, X.H. Zeng, and W. Blum, Transition from strengthening to softening by grain boundaries in ultrafine-grained Cu, Acta. Mater. 52 (2004), pp. 5009–5018. doi:10.1016/j.actamat.2004.07.003
- S. Billard, J.P. Fondère, B. Bacroix, and G.F. Dirras, Macroscopic and microscopic aspects of the deformation and fracture mechanisms of ultrafine-grained aluminum processed by hot isostatic pressing, Acta. Mater. 54 (2006), pp. 411–421. doi:10.1016/j.actamat.2005.09.012
- S. Hariprasad, S.M.L. Sastry, and K.L. Jerina, Deformation behavior of a rapidly solidified fine grained Al-8.5%Fe-1.2%V-1.7%Si alloy, Acta. Mater. 44 (1996), pp. 383–389. doi:10.1016/1359-6454(95)00160-1
- D. Witkin, B.Q. Han, and E.J. Lavernia, Mechanical Behavior of Ultrafine-Grained Cryomilled Al 5083 at Elevated Temperature, J. Mater Eng. Perform 14 (2005), pp. 519–527. doi:10.1361/105994905X56232
- Y. Estrin, Dislocation-density-related constitutive modeling, in Unified constitutive laws of plastic deformation, in A.S. Krausz and K. Krausz, eds., Academic Press, New York, 1996, pp. 69–106.
- Y.M. Wang, E. Ma, R.Z. Valiev, and Y.T. Zhu, Tough nanostructured metals at cryogenic temperatures, Advanced Mater. 16 (2004), pp. 328–331. doi:10.1002/(ISSN)1521-4095
- Z. Huang, L.Y. Gu, and J.R. Weertman, Temperature dependence of hardness of nanocrystalleve copper in low-temperature range, Scr. Mater. 37 (1997), pp. 1071–1075. doi:10.1016/S1359-6462(97)00209-1
- A.S. Khan and C.S. Meredith, Thermo-mechanical response of Al 6061 with and without equal channel angular pressing (ECAP), Int. J. Plasticity 26 (2010), pp. 189–203. doi:10.1016/j.ijplas.2009.07.002
- U.F. Kocks, A.S. Argon, and M.F. Ashby, Thermodynamics and kinetics of slip, Prog. Mater. Sci. 19 (1975), pp. 1–281.
- D. Carillard and J.L. Martin, Thermally Activated Mechanisms in Crystal Plasticity, Pergamon, Oxford, 2003. PERGAMON MATERIALS SERIES.
- N. Wang, Z. Wang, K.T. Aust, and U. Erb, Room temperature creep behavior of nanocrystalline nickel produced by an electrodeposition technique, Mater. Sci. Eng. A237 (1997), pp. 150–158.
- H. Tanimoto, S. Sakai, and H. Mizubayashi, Mechanical property of high density nanocrystalline gold prepared by gas deposition method, Nanostruct. Mater. 12 (1999), pp. 751–756. doi:10.1016/S0965-9773(99)00230-5
- B. Cai, Q.P. Kong, P. Cui, L. Lu, and K. Lu, Creep behavior of cold-rolled nanocrystalline pure copper, Scr. Mater. 45 (2001), pp. 1407–1413. doi:10.1016/S1359-6462(01)01177-0
- H. Conrad and D. Yang, Plastic deformation kinetics of electrodeposited Cu foil at low and intermediate homologous temperatures, J. Electron. Mater. 31 (2002), pp. 304–312. doi:10.1007/s11664-002-0148-x
- Z. Jiang, H. Zhang, C. Gu, Q. Jiang, and J. Lian, Deformation mechanism transition caused by strain rate in a pulse electric brush-plated nanocrystalline Cu, J. Appl. Phys. 104 (2008), pp. 53505. doi:10.1063/1.2973200
- N.Q. Chinh, P. Szommer, Z. Horita, and T.G. Langdon, Experimental evidence for grain-boundary sliding in ultrafine-grained aluminum processed by severe plastic deformation, Advanced Mater. 18 (2006), pp. 34–39. doi:10.1002/(ISSN)1521-4095
- Z.H. Jiang, H.Z. Zhang, C.D. Gu, Q. Jiang, and J.S. Lian, Deformation mechanism transition caused by strain rate in a pulse electric brush-plated nanocrystalline Cu, J. Appl. Phys 104 (2008), pp. 053505. doi:10.1063/1.2973200
- Y.R. Kolobov, G.P. Grabovetskaya, K.V. Ivanov, and M.B. Ivanov, Grain boundary diffusion and mechanisms of creep of nanostructured metals, Interface Sci. 10 (2002), pp. 31–36. doi:10.1023/A:1015128928158
- C. Duhamel, Y. Brechet, and Y. Champion, Activation volume and deviation from Cottrell-Stokes law at small grain size, Int. J. Of Plasticity 26 (2010), pp. 747–757. doi:10.1016/j.ijplas.2009.10.003
- N.Q. Chinh, P. Szommer, T. Csanádi, and T.G. Langdon, Flow processes at low temperatures in ultrafine-grained aluminum, Mater. Sci. Eng. A 434 (2006), pp. 326–334. doi:10.1016/j.msea.2006.07.014
- H. Conrad and J. Narayan, On the grain size softening in nanocrystalline materials, Scr. Mater. 42 (2000), pp. 1025–1030. doi:10.1016/S1359-6462(00)00320-1
- X.F. Zhang, T. Fujita, D. Pan, J.S. Yu, T. Sakurai, and M.W. Chen, Influences of grain size and grain boundary segregation on mechanical behavior of nanocrystalline Ni, Mater. Sci. Eng. A 527 (2010), pp. 2297–2304. doi:10.1016/j.msea.2009.12.005
- Y.M. Wang, R.T. Ott, T. van Buuren, T.M. Willey, M.M. Biener, and A.V. Hamza, Controlling factors in tensile deformation of nanocrystalline cobalt and nickel, Phys. Rev. B 85 (2012), pp. 120.
- Z.W. Shan, E.A. Stach, J.M.K. Wiezorek, J.A. Knapp, D.M. Follstaedt, and S.X. Mao, Grain boundary-mediated plasticity in nanocrystalline nickel, Science 305 (2004), pp. 654–657. doi:10.1126/science.1098741
- K.J. Hemker, Understanding how nanocrystalline metals deform, Science 304 (2004), pp. 221–223. doi:10.1126/science.1097058
- H. Van Swygenhoven, Polycrystalline materials - Grain boundaries and dislocations, Science 296 (2002), pp. 66–67. doi:10.1126/science.1071040
- Z.W. Shan, J.M.K. Wiezorek, E.A. Stach, D.M. Follstaedt, J.A. Knapp, and S.X. Mao, Dislocation dynamics in nanocrystalline nickel, Phys. Rev. Lett. 98(2007). doi:10.1103/PhysRevLett.98.095502
- C.R. Weinberger, A.T. Jennings, K. Kang, and J.R. Greer, Atomistic simulations and continuum modeling of dislocation nucleation and strength in gold nanowires, J. Mech. Phys. Solids 60 (2012), pp. 84–103. doi:10.1016/j.jmps.2011.09.010
- L. Capolungo, M. Cherkaoui, and J. Qu, On the elastic-viscoplastic behavior of nanocrystalline materials, Int. J. Of Plasticity 23 (2007), pp. 561–591. doi:10.1016/j.ijplas.2006.05.003
- X.G. Qiao, N. Gao, and M.J. Starink, A model of grain refinement and strengthening of Al alloys due to cold severe plastic deformation, Philos. Mag. 92 (2012), pp. 446–470. doi:10.1080/14786435.2011.616865
- J. Gubicza, N.Q. Chinh, G. Krallics, I. Schiller, and T. Ungar, Microstructure of ultrafine-grained fcc metals produced by severe plastic deformation, Curr. Appl. Phys. 6 (2006), pp. 194–199. doi:10.1016/j.cap.2005.07.039
- M.A. Meyers, D.J. Benson, O. Vohringer, B.K. Kad, Q. Xue, and H.H. Fu, Constitutive description of dynamic deformation: Physically-based mechanisms, Mater. Sci. Eng. Struct. Mater. Prop. Microstruct. Process 322 (2002), pp. 194–216. doi:10.1016/S0921-5093(01)01131-5
- P.L. Sun, E.K. Cerreta, G.T. Gray, and J.F. Bingert, The effect of grain size, strain rate, and temperature on the mechanical behavior of commercial purity aluminum, Metall. Mater. Trans. A 37 (2006), pp. 2983–2994. doi:10.1007/s11661-006-0180-1
- L.L. Zhu and J. Lu, Modelling the plastic deformation of nanostructured metals with bimodal grain size distribution, Int. J. Of Plasticity 30-31 (2012), pp. 166–184. doi:10.1016/j.ijplas.2011.10.003
- Y.T. Zhu and T.G. Langdon, Influence of grain size on deformation mechanisms: An extension to nanocrystalline materials, Mater. Sci. Eng. Struct. Mater. Prop. Microstruct. Process 409 (2005), pp. 234–242. doi:10.1016/j.msea.2005.05.111
- N. Hansen and B. Ralph, The strain and grain-size dependence of the flow-stress of Copper, Acta. Metallurgica. 30 (1982), pp. 411–417. doi:10.1016/0001-6160(82)90221-8
- M.R. Staker and D.L. Holt, Dislocation cell size and dislocation density in copper deformed at temperatures between 25 and 700 degrees C, Acta. Metallurgica. 20 (1972), pp. 569–579. doi:10.1016/0001-6160(72)90012-0
- A. Kumar and R.G. Kumble, Viscous drag on dislocations at high strain rates in Copper, J. Appl. Phys 40 (1969), pp. 3475–3480. doi:10.1063/1.1658222
- A. Kumar, F.E. Hauser, and J.E. Dorn, Viscous drag on dislocations in aluminum at high strain rates, Acta. Metallurgica. 16 (1968), pp. 1189–1197. doi:10.1016/0001-6160(68)90054-0
- E.N. Borodin and A.E. Mayer, Yield strength of nanocrystalline materials under high-rate plastic deformation, Phys. Solid. State. 54 (2012), pp. 808–815. doi:10.1134/S1063783412040038
- C.R. Weinberger, Dislocation drag at the nanoscale, Acta. Mater. 58 (2010), pp. 6535–6541. doi:10.1016/j.actamat.2010.08.017