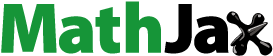
ABSTRACT
Ionogels is a kind of hybrid materials composed of ionic liquids (ILs) and solid polymer network matrix, has been extensively investigated in the most recent decade. Due to the excellent mechanical properties and ionic conductivity, their promising applications in flexible stress and strain sensors have been proposed and explosively developed. In this review, we briefly summarize research progresses on ionogel based flexible stress and strain sensors (IFSSs) from five aspects, including material synthesis, device fabrication, working principles, characteristics and performances, and potential applications. Some outlooks and perspectives are also proposed at the end of review. The review is expected to provide reference and new insights into the research of IFSS.
Graphical abstract
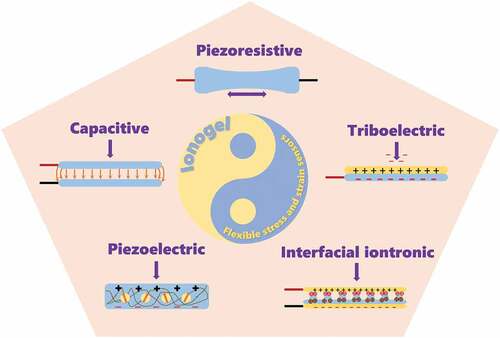
1. Introduction
The demand for real-time social communication, internet information and health monitoring has promoted the rise and development of wearable electronic devices. For wearable devices, the constant pursuit of lightweight and portability always stimulate the research interests to develop flexible electronic components. In recent years, flexible electronics are accelerating into the commercial stage and beginning to enter people’s daily lives. For instance, foldable or rollable screens enable the smart phone with large display area portable, some of which even could be worn as a wristlet. Among different portable and wearable electronics, sensor is an important constituent part for converting physical quantities into electrical signals. Typically, flexible sensors that can sense stress and strain have been a research hotspot for their promising applications in soft robots [Citation1], virtual reality interaction [Citation2], human motion detection and healthy monitoring [Citation3,Citation4] and medical prosthesis [Citation5]. As the name suggests, stress sensors can convert force exert on itself into an electrical signal. Normally, when an object is subjected to pressure, deformation also occurs, and deformation degree is depended on mechanical properties such as hardness and elastic modulus of the material. As stress sensors, their deformation degree is far less than the magnitude of the force exerted, i.e. their electrical characteristics (resistance, capacitance, etc.) are more sensitive to stress or pressure instead of strain or deformation [Citation6–8]. Conversely, strain sensors are more responsive to their deformation, and are flexible devices with excellent deformation ability and elastic recovery ability [Citation9–12]. Some flexible sensors sensitive to both stress and strain can detect pressure and strain, respectively [Citation13–16].
As main parts of flexible stress/strain sensors, the active materials and/or conductive materials should have both flexibility and stress/strain responsiveness. Incorporation of conducting micro/nano fillers with various structures (i.e. particle, tube, fiber, sheet, and layer) [Citation17–19] into elastomer or polymer matrix is a traditional method to prepare stress/strain-responsive material. Conductive passages among the conductive fillers will change when elastomer composites are deformed under an external stress and strain, which will be reflected in the overall resistance change of the composites. The sensitivity and hysteresis of these sensors are usually related to mechanical properties of the elastomers themselves. Furthermore, the opaque fillers seldom meet the need of transparency for sensors. Conductive hydrogels, as a kind of flexible composites made from a three-dimensional (3D) network of cross-linked hydrophilic polymers, conductive polymer/fillers and water, show their unique advantages in bioelectronics, drug delivery and tissue engineering because of their high transparency, conductivity, stretchability, and biocompatibility [Citation20]. Thanks to the high stretchability and mechanically toughness of hydrogel composites, some flexible sensors possess strain sensing which could be used for human motion detection [Citation21]. Adopting special polymer network structure and fillers, hydrogel based flexible strain sensors even obtain recyclability [Citation22]. However, there has some disadvantages that cannot be overcome at present, such as easiness of evaporation, narrow work temperature range, etc.
The emergence of ionogel opens up another pathway for intelligent flexible electronic sensors. It is a type of hybrid material, whose polymer network is formed in ionic liquid (IL). ILs are compounds completely composed of ions with melting point below 100°C, and most of them have the nonvolatility under ambient conditions, and air and water stability [Citation23,Citation24], which aqueous ionic solution in hydrogels do not possess. The chemical structures of common used ILs in ionogel based flexible stress and strain sensor (IFSS) are listed in . The term ‘ionic gel’ normally covers another gel materials which contain aqueous salt solution as ionic conductor [Citation25–27]. Here, ‘ionogels’ involve only those contain ILs as conductors in this review. Ionogel entraps IL into its polymer network matrix, so it inherits the excellent properties of ILs (including ionic conductivity, high thermal stability, wide electrochemical window, etc.) and solid state network structure (including elasticity, flexibility, stretchability and transparency) at the same time. These merits contribute to their potential applications in the field of flexible supercapacitors [Citation28], electrochromic devices [Citation29], catalysis [Citation30,Citation31], and sensing [Citation32–34].
Table 1. The ions of common used ILs in IFSS
This review paper mainly summarizes the progresses of ionogel based flexible stress/strain sensors (IFSSs) in recent years. The preparation of ionogel, the manufacturing process, the characteristics and properties, the working principles of ionogel based flexible sensors and their applications are presented. In the last part of the review, some outlooks and problems in the practical application of ionogel based sensors are also described, which might promote their performance improvement and practical applications.
2. Preparation of IFSS
2.1 Synthesis of Ionogel in IFSS
Ionogel is the main constituent material of IFSS. There have been a lot of review literatures discuss the synthesis routes of ionogels and their classification [Citation35–38]. For high porosity and specific surface area, ionogel electrolytes used in batteries have porous matrices, which are often based on nanoparticles. These ionogel electrolytes are mainly prepared by sol-gel, impregnation and covalent grafting, where IL is entrapped into the pores of matrix through IL hydrolysis and condensation reaction, impregnated into the nanoporous matrix or covalently tethering cation to a variety of inorganic nanoparticles [Citation39]. While ionogels used in sensors usually adopt polymer matrix out of condition for flexible, robust and integrated molding devices. The synthesis of ionogel in IFSS and their typical features are summarized in . Although there are various methods for synthesizing ionogel, photopolymerization is the most popular synthetic method, attributed to their cost-effectiveness, simplicity, controllability and potential in 3D printing technologies. In 2019, Nie’s group used butyl acrylate (BA) as the polymer monomer, 2-hydroxy-2-methylpropiophenone (1173) as a photoinitiator, 1,6-bis(acryloyloxy)hexane (HDDA) as a crosslinking agent, and bis(trifluoromethylsulfonyl imide ([BMIM]TFSI) as an IL to synthesize a transparent, stretchable, stable, and self-adhesive ionogel through one-pot photopolymerization ()) [Citation40]. By means of this simple method, they also polymerized acrylic acid (AA) units in the ILs by UV irradiation with the introduction of a poly(ethylene glycol) diacrylate (PEGDA) cross-linker [Citation41]. Chen et al. synthesized an ionogel by photopolymerization of the same monomer and crosslinker in the IL 1-ethy-l-3-methylimidazolium ethylsulfate ([C2mim][EtSO4]) ()) [Citation42]. Sun et al. synthesized an ionogel containing the IL [1-ethyl-3-methylimidazolium dicyanamide ([EMIM][DCA])) through in situ one-step photopolymerization of 3-dimethyl (methacryloyloxyethyl) ammonium propane sulfonate (DMAPS) and AA [Citation43]. Thermal polymerization is another frequently used method, which is commonly achieved by thermal initiator ammonium persulfate (APS). Wang’s group in situ synthesized an air-stable, highly conductive, and semitransparent ionogel by dissolving N,N’-methylene bis(acrylamide) (NNMBA) and APS in 1-vinyl-3-ethylimidazolium dicynamide ([VEIM][DCA]) and heating the solution at 80°C ()) [Citation44]. They also thermally polymerized the mixture solution of [VEIM][DCA] ILs/ APS/ silicon dioxide (SiO2) on flexible substrate to prepare an ionogel for flexible high-sensitive pressure sensor [Citation45,Citation46]. One-pot thermal polymerization method can also be adopted to synthesize poly(methyl methacrylate-co-butylmethacrylate) /poly(vinylidene fluoride-co-hexafluoropropylene) (P(MMA-co-BMA)/PVDF-HFP) double-network (DN) ionogel ()) [Citation47]. Zhang et al. integrated metal coordination bonds in a loosely cross-linked network of ionogel [Citation48]. They utilized Fe3O4 nanoparticles (NPs) coated with poly(acrylic acid) (PAA) polymer, PEGDA cross-linker, APS and [C2mim][EtSO4] IL to synthesize a super-stretchable ionogel ()).
Figure 1. Free radical polymerization of ionogel. (a) The one-pot photopolymerization of ionogel based on BA, HDDA and [BMIM]TFSI through 1173 photoinitiator [Citation40]. (b) The photopolymerization of ionogel based on AA, PEGDA and [C2mim][EtSO4] [Citation42]. (c) The thermal polymerization of NNMBA [Citation44]. (d) The one-pot thermal polymerization of DN ionogel [Citation47]. (e) Integrating metal coordination bonds in a loosely cross-linked network of ionogel during thermal polymerization [Citation48]
![Figure 1. Free radical polymerization of ionogel. (a) The one-pot photopolymerization of ionogel based on BA, HDDA and [BMIM]TFSI through 1173 photoinitiator [Citation40]. (b) The photopolymerization of ionogel based on AA, PEGDA and [C2mim][EtSO4] [Citation42]. (c) The thermal polymerization of NNMBA [Citation44]. (d) The one-pot thermal polymerization of DN ionogel [Citation47]. (e) Integrating metal coordination bonds in a loosely cross-linked network of ionogel during thermal polymerization [Citation48]](/cms/asset/3ef4353a-cb7a-4b81-b3e6-12e68b8c8aa7/tsnm_a_1958085_f0001_c.jpg)
Table 2. Synthesis and materials of ionogel for flexible stress and strain sensors
Except free radical polymerization, some ionogels for sensors are prepared through electrostatic interactions, hydrogen bond interactions, π–π bond interactions and a thiol-ene click reaction. ) schemes that 1-ethyl-3-methylimidazolium dicyanamide ([EMIm][DCA]) IL is locked into poly(2-acrylamido-2-methyl-1-propanesulfonic acid) (PAMPS)-based double network through the electrostatic interactions between the negatively charged polymer network and [EMIm][DCA] [Citation57]. Owing to hydrogen bonds provided by the H protons in the imidazolium ring of [BMIm]BF4, Xiang et al. displaced the dimethylacetamide (DMAc) in polyimide organogels by [BMIm]BF4 to form polyimide ionogels ())[Citation54]. Cao et al. prepared transparent, mechanically robust, ultrastable ionogels and high ionic conductive ionogel by locking ILs into the poly(ethyl acrylate) (PEA)-based elastomer network through hydrogen bonding between [NTf2] anion and methyl or methylene groups on the polymer molecular chain ()) [Citation61]. With the help of π–π interactions between the imidazolium ring of [BMIM]+ cation and the graphene oxide nanoplatelets, Crump et al. mixed graphene oxide, [BMIM]BF4 and hydrazine to synthesize conductive ionogel [Citation53]. Ren et al. synthesized a double network click ionogel in a one-pot reaction scheme through mixing two solution [Citation63], one solution containing PEGDA, pentaerythritol tetraacrylate (PETA) as cross-linker for covalent network and anionic benzene tetracarboxylic acid (BTCA) as cross-linker for the ionic bond network, and another containing poly(1-butyl-3-vinyl imidazolium fluoborate) (PIL-BF4) and triethylamine (TEA) as a catalyst for the thiol-ene click reaction and 1,2-ethanedithiol (ED) ()).
Figure 2. Other synthesis methods of ionogel. (a) Locking ILs in DN network through electrostatic interactions [Citation57]. (b) Forming polyimide ionogels by solution displacement attributed to hydrogen bonding [Citation54]. (c) Locking ILs into the elastomer network through hydrogen bonding [Citation61]. (d) The thiol-ene click reaction for preparing DN click ionogel [Citation63]
![Figure 2. Other synthesis methods of ionogel. (a) Locking ILs in DN network through electrostatic interactions [Citation57]. (b) Forming polyimide ionogels by solution displacement attributed to hydrogen bonding [Citation54]. (c) Locking ILs into the elastomer network through hydrogen bonding [Citation61]. (d) The thiol-ene click reaction for preparing DN click ionogel [Citation63]](/cms/asset/4aaed8c8-59a0-4ac9-8da0-e3d01e5383f9/tsnm_a_1958085_f0002_c.jpg)
In terms of material selection, [EMIM]BF4 is the most used IL for its affordable price, relative high ionic conductivity (4.09 mS/cm), low melting point (−81°C) and high decomposition temperature (403°C). To obtain high conductivity of finished ionogel device, [EMIm][DCA] is often adopted due to its very high ionic conductivity of 2.8 S/m at 25°C. For polymer network design and synthesis, covalent bonded networks in situ formed in ILs, such as photopolymerization, thermal polymerization usually endow mechanical robust ionogel. Physical cross-linking polymer networks through hydrogen bonding, π–π interactions, etc. could achieve self-healable ionogel. In addition, the compatibility between block monomers and ILs and the ILs content also should be considered, which influence the mechanical properties and conductivity.
2.2 Manufacturing and Structure of IFSS
The forming process of ionogel and device structure design of present IFSS have summarized in . As seen from the table, solution cast is the easiest forming process to synthesis ionogel material ()). Hence, most of IFSS are thin film structure originated from the solution-casted synthesis process of ionogel [Citation40,Citation41,Citation44,Citation46–48,Citation54,Citation56,Citation57,Citation60,Citation61]. As a stretchable strain sensor, simple film is the optimum device structure. But for special purpose of structural design and application, different processing or forming methods need to be applied. 3D printing has been a popular prototyping and manufacturing technology because of its advanced precision, high efficiency and high controllability. Especially it is the most effective way for forming complex architectures. Typically, the precursor solution of ionogel is put into dedicated 3D printer with UV exposure device, and the ionogel sensors with different shapes will be obtained after chemical cross-linking under the UV radiation [Citation49]. The circular tube-like IFSS can be worn on finger to detect its bending, which is more convenient than those pasted on finger by adhesive tape ()). In ), Wong et al. 3D-printed an IFSS with hourglass auxetic structure, which had more robust mechanical strength, lighter mass, more sensitive response to strain and larger elongation [Citation50]. It is impossible to achieve integrated forming with encapsulating material and volume production of IFSS by solution cast, and artificial tailoring and assembling. By means of 3D printing, Crump et al. manufactured a batch of stretchable strain sensors encapsulated by (polydimethylsiloxane) PDMS through one process ()) [Citation53].
Figure 3. Solution casting and 3D printing molding process of IFSS. (a) Solution casting during synthesizing ionogel [Citation41]. (b) 3D printing manufactured complex architectures [Citation49]. (c) 3D printed hourglass auxetic structure [Citation50]. (d) Volume production of IFSS by 3D printing [Citation53]
![Figure 3. Solution casting and 3D printing molding process of IFSS. (a) Solution casting during synthesizing ionogel [Citation41]. (b) 3D printing manufactured complex architectures [Citation49]. (c) 3D printed hourglass auxetic structure [Citation50]. (d) Volume production of IFSS by 3D printing [Citation53]](/cms/asset/dfffd40f-3feb-488f-b995-f0870f83244d/tsnm_a_1958085_f0003_c.jpg)
Table 3. The principle, forming process of ionogel and device structures of IFSS
Another common structure of IFSS is sandwich-like structure, which needs hand-assembling. Such structure is often designed for three purposes. One is to protect ionogel itself from external interference. The sensor is often encapsulated by flexible material, such as Eco-flex or silicone rubber elastomer to be protected from the electronic signal interference of human skin, which is usually applied as wearable sensor ()) [Citation45]. If conductive ionogel is used as flexible electrode of sensor, it should be covered with a protecting layer. This structure is commonly used in two type IFSS. One is capacitive-type sensor, which has an elastomer spacer sandwiched between two ionogel electrodes ()) [Citation51,Citation55]. Another is interfacial iontronic type sensor, which has a conductive layer to contact with ionogel electroyte layer to form elastic electrolytic-electronic interface. To obtain the high unit area capacitance (UAC), coarse or patterned surface of ionogel layer or conductive layer need to be manufactured. These micro-nano texture prepared by spin coating ionogel or conductive elastomer precursor on template with surface texture, such as leaf [Citation65], sandpaper [Citation66] and lithography mold [Citation75]. Ionogel fiber mats inherently have large specific surface area prepared through electrospinning, which is also an effective means to manufacture interfacial iontronic type sensor [Citation67,Citation76]. Ionogel film can also be used as soft electrodes of triboelectric principle-based stress sensors, where the ionogel layer is often stacked with a dielectric layer ()) [Citation43,Citation63] or contacted directly with a dielectric layer to generate charges ())[Citation48].
Figure 4. IFSS with sandwich-like structures. (a) IFSS with EcoFlex shell [Citation45]. (b) Ionogel as the electrode of capacitive type sensor [Citation55]. (c) Single-electrode mode TENG IFSS prepared by stacking ionogel and PDMS dielectric layer [Citation43]. (d) Contact-separation mode TENG IFSS working by contacting ionogel with patterned PDMS dielectric layer [Citation58]. (e) Paper-based IFSS prepared by direct-writing ionogel precursor solution on paper [Citation52]
![Figure 4. IFSS with sandwich-like structures. (a) IFSS with EcoFlex shell [Citation45]. (b) Ionogel as the electrode of capacitive type sensor [Citation55]. (c) Single-electrode mode TENG IFSS prepared by stacking ionogel and PDMS dielectric layer [Citation43]. (d) Contact-separation mode TENG IFSS working by contacting ionogel with patterned PDMS dielectric layer [Citation58]. (e) Paper-based IFSS prepared by direct-writing ionogel precursor solution on paper [Citation52]](/cms/asset/a7d0d665-c026-42aa-8e0f-41ad75fc4b3f/tsnm_a_1958085_f0004_c.jpg)
Paper-based devices have advantages of low-cost, simple manufacturing and environmentally-friendly, and attract a lot of research interests in recent years. Liu et al. directly write the ionogel precursor solution as an conductive path on the paper ()) [Citation52]. Through the novel design, they made two pressure sensors with different sensing principles, piezoresistive and triboelectric. All-paper based IFSS has another major merit: various structure designs. They could be tailored into different kirigami structures or folded into fancy origami structures [Citation72,Citation73,Citation74].
Actually, it can be found in the that the forming process of ionogel is highly relevant to device structure. For example, simple stretchable strain sensor could be mainly made by solution casting ionogel film; Manufacturing process of paper-based IFSS need to write the liquid ionogel precursor on paper followed by curing treatment, then be sandwiched with other components; Spin coating ionogel on template facilitate the micro structure of IFSS. Furthermore, the device structure is depended on sensing principles of IFSS, while the choice of principle is closely related to sensing function to be achieved.
3. Working principles of IFSS
In the consideration of correlation, the principles of IFSS are also summarized in the . The sensing principles of IFSS could be classified into 5 types: resistive, capacitive, interfacial iontronic, piezoelectric and triboelectric. They are suitable for different sensing functions as shown in , and discussed separately.
3.1. Resistive type
Resistive-type sensors mainly depend on the deformation of their active materials that can response to external stress or strain. With simple structure and assembly, most of IFSS adopt piezoresistive principle ()). Only by connecting leads with ionogel film and amperemeter, the current flow through ionogel can response to its strain according to the Equations (1) and (2):
Figure 5. Working principles of IFSS. (a) Piezoresistive-type IFSS [Citation44]. (b) IFSS based on piezoionic and piezoelectric mechanism [Citation62]. (c) The interfacial iontronic pressure sensor based EDL mechanism [Citation65]. (d) Single-electrode TENG principle [Citation63]. (e) Contact-separation TENG principle [Citation58]
![Figure 5. Working principles of IFSS. (a) Piezoresistive-type IFSS [Citation44]. (b) IFSS based on piezoionic and piezoelectric mechanism [Citation62]. (c) The interfacial iontronic pressure sensor based EDL mechanism [Citation65]. (d) Single-electrode TENG principle [Citation63]. (e) Contact-separation TENG principle [Citation58]](/cms/asset/3212056c-7ab3-41f1-9ef9-ac127f1c51bf/tsnm_a_1958085_f0005_c.jpg)
The resistance R of active material is related to its shape (length L, cross-sectional area A) and intrinsic characteristics, resistivity ρ. Equation (2) is derived through substitution of Ohm’s law, where the current I will change with the deformation (L and A) of ionogel when constant voltage is applied on its ends. Resistive principle could be adopted to achieve both stress/pressure and strain sensing, and as far as we know, tensile strain sensors are almost based on resistive principle. To obtain large elongation ratio, the polymer matrix and chemical composition of ionogel in tensile strain sensors should be considered and designed for robust mechanical properties.
3.2. Capacitive type
As mentioned above, conductive ionogel film can be used as the electrode of sensors. When a dielectric layer is sandwiched between two ionogel films, a simple parallel-plate capacitor will be obtained ()) [Citation51,Citation55]. According to the Equation (3):
when the sensor deforms under an external force, the distance d between two ionogel parallel plates will be changed, thus generating the variation of capacitance C. As a stress sensor, its active area S between two plates usually remains unchanged. k is dielectric constant of interlayer material. The flexible sensor based on capacitive principle involve two opposite electrodes, so cannot suffer large deformation, and only applies to pressure sensing.
3.3. Interfacial iontronic type
Interfacial iontronic sensor is a kind of new emerging type of IFSS in recent years, which mainly realize pressure and tactile sensing. They are different from traditional flexible electrostatic capacitive sensors mentioned in the above section. Interfacial iontronic sensors mainly utilize the supercapacitive nature of the electrical double layer (EDL) that occurs at the electrolytic-electronic interface [Citation77]. The EDL capacitance of the sensor is dependent on the interfacial contact area between the ionogel layer and the counter electrode. When the ionogel contacts with the electrode, ions in the asperities of the ionogel layer and electrons on the electrode attract each other and accumulate, which forms an ultrahigh specific capacitance at micro/nano scale. With the load increases, the number of the asperities contacted with electrode increases, i.e. the EDL area increases. So the capacitance of the sensor can be regarded as the sum of numerous EDL capacitance [Citation65,Citation78] ()). EDL effect based sensors usually have ultrahigh pressure sensitivity, high noise immunity, high pressure resolution, high spatial definition, and optical transparency. Similarly, interfacial iontronic sensor needs contact electrode to form electrolytic-electronic interface, so has layered assembly structure which cannot support stretchable deformation, and normally, strong mechanical properties like stretchable strain sensors are not required for its flexible components.
3.4. Piezoelectric type
Up to now, very few study has fabricated IFSS with the piezoelectric principle. The incorporation of piezoelectric components into ionogel matrix forms piezoelectric composites. After polarization, the dipole moment vector of piezoelectric components can be orientated. When the composite is subjected to an impulse compress stress, the dipole moments of deformed piezoelectric nanoparticles change and generate piezoelectric potential to realize a sensitive sensing. Villa et al. prepared a novel ionogel/BaTiO3 nanocomposite by UV photo-cross-linking reaction [Citation62]. The nanocomposite had a polymer interpenetrating network (IPN) composed of polyvinylpyrolidone (PVP), a random copolymer of (hydroxyethyl) methacrylate (HEMA) and acrylonitrile (AN) (poly-HEMA-co-AN) and piezoelectric BaTiO3 nanoparticles with chemically modified hydrophilic surface. The polarized sensor can achieve a low frequency and directional discriminative pressure sensing by combining piezoionic and piezoelectric activity, generating electric charge due to a redistribution of the mobile ions across the polymer matrix and to the presence of the polarized BaTiO3 nanoparticles, respectively ()). For piezoelectric type sensors, the piezoelectric particles in composites play an important role in sensing pressure. However, ionogel as conductive matrix, its corporation with piezoelectric particles will be a challenge for polarization of the composites. Besides, the piezoelectric effect in conductive ionogel matrix is still not entirely clear. The separate structure design of ionogel and flexible piezoelectric component in sensor may be better than ionogel/piezoelectric particles composites to achieve piezoelectric type ionogel sensor.
3.5 Triboelectric type
Triboelectric nanogenerator (TENG) is proposed by Wang’s group at 2012 [Citation79,Citation80,Citation81]. After nearly a decade of research and development, TENG is penetrating into different fields, such as energy harvesting, health monitoring, biomedical sensing and wearable electronics. TENG based flexible sensors allure a lot of attention by virtue of two main advantages: 1. Wide materials selection and flexibility achieved easily by polymer structure; 2. Self-powering without external energy supply [Citation82,Citation83]. IFSS based on TENG mechanism usually adopt two typical structural types: single-electrode and contact-separation. Single-electrode TENG mode IFSS has simple structure, and it generates current signals by contacting its dielectric layer with external object such as human finger [Citation43,Citation63]. When the external object approaching the dielectric surface material of the sensor, due to their different electronegativity, electrostatic charges will be induced in dielectric layer, and meanwhile, electrons flow between the ionogel electrode and earth terminal for reaching a potential balance ()). For contact-separation TENG mode IFSS, the contact-separation process occurs inside the sensor, in which two different dielectric layer and spacer between them are needed [Citation43,Citation52,Citation58]. It has the similar principle with single-electrode mode, but electrons flow between two ionogel electrodes ()). Dielectric and conductive layers are two necessary components of triboelectric type sensor. The sensor works through triboelectrification between two dielectric objects in contact-separation motion, which is structurally difficult to perform large deformation. Those stretchable TENG mode IFSS only perform normal pressure sensing at tensile state or detect bending strain through contact-separation at the bend [Citation43,Citation63].
4. Properties and performances
By contrasting and summarizing the principles, structures and functions of ionogel based sensors, it can be found that flexible ionogel based sensors just performs two sensing functions: tensile strain and stress (pressure), according to five mechanisms. Although they have some similar performance characteristics, such as gauge factor (GF, i.e. sensitivity) and response time, they cannot be compared together because of the difference of two types of ionogel based sensors on function and working modes. Bsesides, they both have their own performance characteristics. Therefore, their main performances are summarized separately in .
Table 4. The major characteristic parameters of ionogel based tensile strain sensors
Table 5. The major characteristic parameters of ionogel based pressure sensors
4.1. Stretchablility
Generally, stretchable strain sensors can be characterized by the properties including the properties of ionogel materials and the sensing performances. For stretchable strain sensors, the elongation of ionogel is used to characterize tensile property of the sensor, which is the ratio of the maximum length in tension state to the natural length, while the tensile strength is the tensile stress at the maximum tensile length. Low tensile strength is not conducive to resist large defamation. The elongation and tensile strength are mainly related to the polymer network, IL content and their compatibility. ) shows an ionogel with ultrahigh stretchability of higher than 5000% at a tensile strength of 1.75 MPa. The polymer double network was synthesized by two-step photopolymerization of ethyl acrylate (EA) monomer, and then the ionogel was yielded by incorporating [C2mim][NTf2] IL into the network through hydrogen bonding [Citation61].
Figure 6. The characteristics and properties of IFSS. (a) The transmittance of ionogel in visible light range [Citation61]. (b) The maximum elongation of ionogel [Citation61]. (c) The temperature sensibility of IFSS [Citation59]. (d) IFSS may have different GF in different elongation ranges [Citation48]. (e) The GF of capacitive IFSS [Citation55]. (f) The GF of triboelectric-type IFSS [Citation52]. (g) The resistance change of IFSS has a good linear relationship with strain [Citation41]. (h) An resistance IFSS with 80 ms responsive time [Citation59]. (i) High stability with 10,000 cycles of duration [Citation60]. (j) Self-healable ionogel [Citation56]. (k) An IFSS that can work in the temperature range of −60 ~ 250 °C [Citation49]
![Figure 6. The characteristics and properties of IFSS. (a) The transmittance of ionogel in visible light range [Citation61]. (b) The maximum elongation of ionogel [Citation61]. (c) The temperature sensibility of IFSS [Citation59]. (d) IFSS may have different GF in different elongation ranges [Citation48]. (e) The GF of capacitive IFSS [Citation55]. (f) The GF of triboelectric-type IFSS [Citation52]. (g) The resistance change of IFSS has a good linear relationship with strain [Citation41]. (h) An resistance IFSS with 80 ms responsive time [Citation59]. (i) High stability with 10,000 cycles of duration [Citation60]. (j) Self-healable ionogel [Citation56]. (k) An IFSS that can work in the temperature range of −60 ~ 250 °C [Citation49]](/cms/asset/81510917-98a7-4730-8af2-37c6cdd1c9d7/tsnm_a_1958085_f0006_c.jpg)
4.2. Transparency
Most of the ionogels have excellent transmittance in the visible light range ()) [Citation40,Citation41,Citation49,Citation50,Citation57,Citation61], while some have colors or are opacity because of doped colored fillers or ionogel components [Citation48,Citation62]. Therefore, the IFSS with thin film or stripe structure (mostly tensile strain IFSS) are usually transparent, which is attributed to their main component, transparent ionogel. For those with complex assembled structures (sandwiched, paper-based, patterned or fiberous), they usually have poor transparency because of the opaque electrode components [Citation65], micro-nano structure [Citation67,Citation71], or surface texture [Citation64,Citation66,Citation75].
4.3. Conductivity
Conductivity is an important parameter of ionogel to judge its electrical property. It depends heavily on the conductivity of IL locked in the polymer network. Li’s group and Liu’s group immobilized [EMIm][DCA] in poly(vinyl alcohol)-poly(vinylpyrrolidone) (PVA-PVP) complexes and PAMPS-based double networks, respectively. Owing to the high conductivity (28 mS/cm) of [EMIm][DCA] at room temperature, the corresponding ionolgels reached a high conductivity of 19.7 and 19 mS/cm, respectively [Citation56,Citation57]. However, the ionic conductivity of IL, as well ionogel, was affected by ambient temperature. The Vogel-Fulcher-Tammann (VFT) EquationEquation (4)(4)
(4) descripts the conductive behavior of the ionogel [Citation84,Citation85]:
where A is a pre-exponential factor related to the number of ion carriers, B is the activation energy of ion transport, and T0 is the idealized glass transition temperature of the ionogel, which is lower than the glass transition temperature of the ionogel by 20–50 K.
With the conductivity-temperature dependence relationship, the ionogel can realize sensing of temperature. The bimodal sensor based on ionogel prepared by Sun et al. can detect temperature changes over the range of 10 to 90°C by a 95.4% resistance variation ()) [Citation59]. Without influence by volatilization, thermal stability of ionogel materials is usually better than hydrogel and they also possess a wider operating temperature.
4.4. Sensitivity and linearity
Performance metrics of traditional sensors can also be applied to IFSS as sensing devices. Sensitivity is the key parameter to judge their response to external stimulations. For piezoresistive IFSS, the gauge factor (GF) is the slope of the fitted ΔR/R0 to the external strain or stress, where R0 is the resistance of IFSS at its original state, ΔR is the variation of resistance when IFSS is subjected to strain or stress, and strain is the elongation ratio ()). Similarly, GF of capacitive and interfacial iontronic IFSS is the ratio of the fitted ΔC/C0 to stress ()). Iontronic pressure sensors emerged in the last decade have much larger sensitivity than traditional capacitive sensors, and have become a promising pressure sensing solution [Citation77]. It is worth noting that GF may not be a constant in the whole working range. In another words, the slopes of the fitted ΔR/R0 to strain or stress are different in different strain /stress scope ()). For triboelectric IFSS, their GF is the ratio of triboelectric outputs (voltage or current) to stress ()).
Linearity represents the linear relationship of ΔR/R0 to strain /stress ()). The good linear response can significantly facilitate the calibration process, and improve signal accuracy and reliability, which is essential in practical applications of strain sensors. Generally, capacitive sensors have good linearity, while resistive sensors sometime have nonlinearity due to non-uniform morphology during deformation.
4.5. Response time
Response time is the time required from exerting /release external stimulation to generate /reset electric signals, which reflects the response speed of the sensor. The shorter is the response time, the faster sensor gives electrical feedback. For stretchable strain ionogel based sensor, 80 ms interval can be observed from 1.0 to 1.4 of ΔR/R0 for the agarose /PHEA /[EMIM]Cl DN IFSS ()) [Citation59]. Comparing with 2, it can be found that the response time of most pressure sensors are lower than tensile strain sensors, which could be attributed to the tiny elastic deformation during sensing external pressure. Furthermore, owing to the high UAC and EDL effect, iontronic pressure sensors with subtle structure design can reach ultralow response time [Citation67,Citation71], which is significantly lower than traditional piezoresistive pressure sensor’s [Citation44,Citation46]
4.6. Hysteresis
Through conducting loading and unloading pressure cycles, the hysteresis behavior of the sensor can be investigated, which reflected the ability of IFSS to detect strain quantitatively and the independence of strain history. The hysteresis phenomenon is mainly attributed to viscoelastic nature of ionogel [Citation86,Citation87]. The degree of hysteresis (DH) is calculated as the Equation (5) [Citation88]:
where ALoading and AUnloading are the area of loading and unloading curves, respectively. The lower DH value, the lesser hysteresis in the response to strain [Citation88].
In addition, durability and temperature tolerance determine the service life and operating temperature range of IFSS, respectively. These parameters are mainly related to properties of ionogel materials. The ionogel based ionic skins produced by Li et al. demonstrated ultra-durable sensing properties over 10,000 uninterrupted strain cycles and retained its original sensing properties even after 200 days of open storage ()) [Citation60].
Self-healing ionogel has the ability to repair mechanical damage independently, and may be an option to increase the service life of IFSS ()). Generally, their self-healing ability is benefited from the reversible hydrogen bonds in the polymeric network [Citation56,Citation60] or the reversible coordination bonds and ionic bonds among incorporated nanoparticles and polymer chain [Citation48].
4.7. Temperature tolerance
As mentioned above, although resistance is affected by ambient temperature, IFSS have wider operating temperature window than hydrogel-based sensors because of the non-volatility of ionogel. For instance, Wang et al. utilized poly(ionic liquid) (PIL) as the ionic conductive network and hyper branched polymer as macro-cross-linkers to 3D print ionogel, which could work at an extreme low temperature (−60°C) and a high temperature (250°C) ()) [Citation49]. Owing to this merit, IFSS can work at high temperature environment where hydrogel-based sensors are complete failure, and low temperature environment where hydrogel-based sensors become brittle because of the frozen water inside.
4.8. Working range
The working range decide the top and bottom sensing limitation of a sensor. Tensile strain sensors normally can work in their maximum elongation ratio, though have different sensitivity values at different tensile ratio [Citation40,Citation55,Citation56,Citation60]. For pressure sensors, working range is an important characteristic. The top limitation of working range represents how much load can be responded, while the bottom limitation of working range reflects the minimum load can be detected by the sensor. Owing to sensitively changing EDL capacitances at the interfacial contact areas, ionogel based iontronic sensors have low limitation of detection. Hence, micro-nano structure design and construction is key to iontronic pressure sensors.
Because of the differences on sensing modes between the ionogel based tensile strain sensors and pressure sensors, the development progress of their main performance indictors cannot be discussed generally together. Ionogel based tensile strain sensors are emerging flexible sensors in the last five years. Maximum strain as the indictor of their stretchability has been improved from 157% (Ref. [Citation57]) at 2017 to 5000% (Ref. [Citation61]) at 2020 ()). With a few exceptions, most of ionogel based tensile train sensors have a maximum sensitivity of less than 3. Altogether, comprehensive performances (maximum strain and sensitivity) of ionogel based tensile strain sensors are basically improving ()) in recent years. One of the major advantages of ionogel based sensors over aqueous ionic gel based sensors is wider working temperature window. After several years of development, ionoge based tensile strain sensors already can operating well from the low temperature of −60°C to high temperature of 250°C ()). Interfacial iontronic pressure sensors were developed for the last decade. Their sensing components are ionic materials, and solid ionogels are just one of them. Although their sensitivities can be measured in different ways, in the same measure method, the sensitivity still presents a trend of constant improvement ()). The sensitivity increased from 9.55 kPa−1 in 2017 (Ref. [Citation66]) to 131.5 kPa−1 in 2019 (Ref. [Citation64]) and increased from 3.1 nF/kPa in 2015 (Ref. [Citation71]) to around 100 nF/kPa in 2017 (Ref. [Citation67]) and 2018 (Ref. [Citation51]). The response time of ionogel based iontronic pressure sensors have reduced to millisecond level, while the response time of piezoresistive pressure sensor is still higher than iontronic pressure sensor’s [Citation44,Citation46] ()). Their lower limitation of detection are as low as a tenth of Pascal and upper limitation can reach to 750 kPa ()). Wide detection range is conducive to their practical applications.
Figure 7. The development progress of (a) maximum strain, sensitivity (sensitivity is not provided in Ref. [Citation50,Citation57]) and (b) temperature tolerance on ionogel based tensile strain sensors; and the development progress of (c) sensitivity, response time (response time is not provided in Ref. [Citation51,Citation69]) and (d) working range on ionogel based pressure sensors in recent years
![Figure 7. The development progress of (a) maximum strain, sensitivity (sensitivity is not provided in Ref. [Citation50,Citation57]) and (b) temperature tolerance on ionogel based tensile strain sensors; and the development progress of (c) sensitivity, response time (response time is not provided in Ref. [Citation51,Citation69]) and (d) working range on ionogel based pressure sensors in recent years](/cms/asset/a8bf59ff-0e8a-4912-8e81-2cd65360c078/tsnm_a_1958085_f0007_c.jpg)
5. Applications
5.1. Motion moniroring
Possessing stress and strain detecting function, IFSS can be applied in various fields. Human motion monitoring plays an important role in patient’s motor function restoration. 3D printed tube-like IFSS can be put on human finger to detect its bending movements ()) [Citation49]. It also can be printed into simple stripe shape and fixed on different body parts, such as wrist and elbow, to detect their movements ()) [Citation49]. Sensitive IFSS even can precisely monitor the bending angle of wrist, which is a promising application in evaluating patient’s recovery situation ()) [Citation45].
Figure 8. The IFSS can monitoring human limb movements, such as (a) finger bending, (b) wrist flexing, (c) elbow bending [Citation49] and (d) subtle wrist bending [Citation45]
![Figure 8. The IFSS can monitoring human limb movements, such as (a) finger bending, (b) wrist flexing, (c) elbow bending [Citation49] and (d) subtle wrist bending [Citation45]](/cms/asset/f13fc3c3-1228-4c3f-b5b1-57b976717e78/tsnm_a_1958085_f0008_c.jpg)
5.2. Human-machine interface
If IFSS is integrated with signal acquisition and analysis processing system to fabricate a wearable smart glove, it will be a potential product in motion capture and virtual reality interaction. For example, Wang et al. prepared an IFSS array connected with signal processing system, which can wirelessly control an unmanned aerial vehicle (UAV) ()) [Citation45]. Combining IFSS array with commercially available integrated circuit components consolidated on a flexible printed circuit board (PCB), V. Amoli et al. fabricate a wearable aerial drone microcontroller (WADM), capable of controlling a drone’s number of rotations and even its direction simultaneously and/or selectively during its flight ()) [Citation69]. Pan’s group design and fabricate a smart glove with a numbers of all-fabric ionogel based sensing units, which can detect the pressure on the palm when grabbing an object ()) [Citation67].
Figure 9. (a) Controlling an UVA by eyes blinking through an IFSS [Citation45]; (b) A smart wristband integrated IFSS array with circuit components consolidated on a flexible printed circuit board (PCB) can control the drone flight [Citation69]; (c) A smart glove can sensing distribution of pressure [Citation67]
![Figure 9. (a) Controlling an UVA by eyes blinking through an IFSS [Citation45]; (b) A smart wristband integrated IFSS array with circuit components consolidated on a flexible printed circuit board (PCB) can control the drone flight [Citation69]; (c) A smart glove can sensing distribution of pressure [Citation67]](/cms/asset/257bff83-03bc-450d-8480-d573cf0a1248/tsnm_a_1958085_f0009_c.jpg)
5.3. Real-time health monitoring
With the advent of the Internet of Things, considering more concern on human health in daily life, real-time health monitoring is becoming a great demand. IFSS can meet such requirements by virtue of their sensitive detection of breathing [Citation55], swallowing [Citation47], voice [Citation45], human pulse [Citation52,Citation59], and eye movements [Citation45,Citation64](). Compared with traditional sensors, IFSS have high sensitivity and fit the human skin better, and much more convenient to use than traditional non-flexible sensing device. Besides, compared with complicated circuit design and components integration of traditional sensors, manufacturing process of IFSS is relatively simple.
Figure 10. IFSS can real-time sensing physiological characteristics, such as (a) breathing [Citation55], (b) swallowing [Citation47], (c) speaking [Citation45], (d) pulse beating [Citation52] and (e) eye movements [Citation64], for monitoring human health situation
![Figure 10. IFSS can real-time sensing physiological characteristics, such as (a) breathing [Citation55], (b) swallowing [Citation47], (c) speaking [Citation45], (d) pulse beating [Citation52] and (e) eye movements [Citation64], for monitoring human health situation](/cms/asset/f81747d5-fd21-4409-b5ef-58877a60214e/tsnm_a_1958085_f0010_c.jpg)
5.4. E-skins and soft robotics
E-skins and soft robotics are also potential application fields of IFSS. E-skins can help robots have similar tactile sensing function as human skin [Citation52]. IFSS also can be integrated into soft robotic fingers for somatosensitive manipulation, which can perform the grasp action while sensing the grasping force [Citation89]. Ionogel nanocomposites with the properties of low frequency and directional discriminative pressure sensing have a huge potential in development of smart soft control panel [Citation62].
6. Summary and outlook
In this review, we present the recent progresses in the field of employing ionogels as active components in flexible stress and strain sensors. The current development of IFSSs is discussed, from the aspects of material synthesis, device fabrication, characteristics and performances, working principles and potential applications, which can be summarized as follows: (1) photoradical polymerization and thermal polymerization are the most commonly used synthetic methods for ionogels in IFSS, while hydrogen-bonding interactions are usually adopted to prepare self-healing ionogel. (2) Most of IFSS are ionogel films themselves, formed by solution casting. But 3D printing is being favored by more and more researchers. (3) Lots of applications demonstrates huge potential of IFSS in the fields of wearable electronics, motion monitoring, biosensing, soft robotics and intelligent interaction. However, there are some aspects that need further research and development: (1) Improvement of material properties. Ionogels vary considerably in properties and characteristics, and it needs further improvement and standardized synthesis for real product applications. Ionogel is still in a very early stage and its material properties involve many indictors. Utilizing the high-throughput experimentation and materials genome, it may accelerate the constitution design and formula optimizing. (2) Structure design of devices. The performance of device is a comprehensive result of material properties and structural design. The monotonous film structure design of IFSS will be improved in the future. There have been some reports on subtle structure designed IFSS through electrospinning, direct-writing and micro-nano machining technologies. Various manufacturing methods will provide the possibility for the design of various complex structures. (3) Applications in micro-nano devices. IFSS also need to adapt to the trend toward miniaturization, which is conducive to be integrated with other electric components. The standardized synthesis of materials and precision machining of devices is a prerequisites. The promising standardized manufacture of ionogel based sensing devices might be 3D printing, which is also suitable for manufacturing tiny devices. By virtue of photopolymerization, some ionogels might be able to be prepared and formed during photolithography manufacturing process so that can be integrated into micro-nano devices directly. Furthermore, it’s worth noting that the research about the application of interfacial iontronic principle in micro-nano electronics have been conducted. (4) System integration. Current applications of IFSS are just demonstrated as single sensing components, i.e. there are lack of closed-loop application of smart system from sensing to feedback. As a crossed research field, electronic circuit design, data acquisition and processing, computer programming and software development will be of great benefit to the application of IFSS in commercial product.
In summary, as a new research direction in recent years, IFSS are attracting increasing attentions and extensive efforts are devoted from researchers. Although there are some aspects to be improved and intensively studied, we have reason to believe that IFSS will be an important part of future wearable and flexible electronics.
Acknowledgments
We acknowledge the support from the grants of the National Natural Science Foundation of China (Grant Nos: 52005482, 51975562, and 82072065), the National Key R&D project from Minister of Science and Technology, China (2016YFA0202703), and the National Youth Talent Support Program.
Disclosure statement
No potential conflict of interest was reported by the author(s).
Additional information
Funding
References
- Lu N, Kim D-H. Flexible and stretchable electronics paving the way for soft robotics. Soft Robot. 2013; 1:53–62.
- Song K, Kim SH, Jin S, et al. Pneumatic actuator and flexible piezoelectric sensor for soft virtual reality glove system. Sci Rep. 2019; 9:1–8.
- Li H, Zhang J, Chen J, et al. A supersensitive, multidimensional flexible strain gauge sensor based on Ag/PDMS for human activities monitoring. Sci Rep. 2020; 10:1–9.
- Shan G, Li X, Huang W. AI-enabled wearable and flexible electronics for assessing full personal exposures. The Innovation. 2020; 1:100031.
- Kim J, Lee M, Shim HJ, et al. Stretchable silicon nanoribbon electronics for skin prosthesis. Nat Commun. 2014; 5:1–11.
- Nakamitsu M, Oyama K, Imai H, et al. Ultrahigh-sensitive compression-stress sensor using integrated stimuli-responsive materials. Adv Mater. 2021; 33:2008755.
- Lee S, Reuveny A, Reeder J, et al. A transparent bending-insensitive pressure sensor. Nat Nanotechnol. 2016; 11:472–478.
- Tao L-Q, Zhang K-N, Tian H, et al. Graphene-paper pressure sensor for detecting human motions. ACS Nano. 2017; 11:8790–8795.
- Oh J, Yang JC, Kim J-O, et al. Pressure insensitive strain sensor with facile solution-based process for tactile sensing applications. ACS Nano. 2018; 12:7546–7553.
- Jia Y, Sun R, Pan Y, et al. Flexible and thin multifunctional waterborne polyurethane/Ag film for high-efficiency electromagnetic interference shielding, electro-thermal and strain sensing performances. Composites Part B. 2021; 210:108668.
- Wang X, Liu X, Schubert DW. Highly sensitive ultrathin flexible thermoplastic polyurethane/carbon black fibrous film strain sensor with adjustable scaffold networks. Nano-Micro Lett. 2021; 13:64.
- Xiang S, Zheng F, Chen S, et al. Self-healable, recyclable, and ultrastrong adhesive ionogel for multifunctional strain sensor. ACS Appl Mater Interfaces. 2021; 13:20653–20661.
- Boutry CM, Kaizawa Y, Schroeder BC, et al. A stretchable and biodegradable strain and pressure sensor for orthopaedic application. Nat Electron. 2018; 1:314–321.
- Chhetry A, Sharma S, Yoon H, et al. Enhanced sensitivity of capacitive pressure and strain sensor based on CaCu3Ti4O12 wrapped hybrid sponge for wearable applications. Adv Funct Mater. 2020; 30:1910020.
- Agaoglu S, Diep P, Martini M, et al. Ultra-sensitive microfluidic wearable strain sensor for intraocular pressure monitoring. Lab Chip. 2018; 18:3471–3483.
- Li C, Zhang D, Deng C, et al. High performance strain sensor based on buckypaper for full-range detection of human motions. Nanoscale. 2018; 10:14966–14975.
- Kim SY, Choo Y, Bilodeau RA, et al. Sustainable manufacturing of sensors onto soft systems using self-coagulating conductive pickering emulsions. Sci Robot. 2020; 5:eaay3604.
- Chen K, Gao W, Emaminejad S, et al. Printed carbon nanotube electronics and sensor systems. Adv Mater. 2016; 28:4397–4414.
- Ma Y, Liu N, Li L, et al. A highly flexible and sensitive piezoresistive sensor based on mxene with greatly changed interlayer distances. Nat Commun. 2017; 8:1–8.
- Guo CF, Ding L. Integration of soft electronics and biotissues. The Innovation. 2021; 2:100074.
- Sun X, Qin Z, Ye L, et al. Carbon nanotubes reinforced hydrogel as flexible strain sensor with high stretchability and mechanically toughness. Chem Eng J. 2020; 382:122832.
- Lai J, Zhou H, Wang M, et al. Recyclable, stretchable and conductive double network hydrogels towards flexible strain sensors. J Mater Chem C. 2018; 6:13316–13324.
- Lei Z, Chen B, Koo Y-M, et al. Introduction: Ionic liquids. Chem Rev. 2017; 117:6633–6635.
- Singh SK, Savoy AW. Ionic liquids synthesis and applications: An overview. J Mol Liq. 2020; 297:112038.
- Wang H, Wang Z, Yang J, et al. Ionic gels and their applications in stretchable electronics. Macromol Rapid Commun. 2018; 39:1800246.
- Zhang X, Sheng N, Wang L, et al. Supramolecular nanofibrillar hydrogels as highly stretchable, elastic and sensitive ionic sensors. Mater Horiz. 2019; 6:326–333.
- Jin S, Qiu J, Sun M, et al. Strain-sensitive performance of a tough and ink-writable polyacrylic acid ionic gel crosslinked by carboxymethyl cellulose. Macromol Rapid Commun. 2019; 40:1900329.
- Shi M, Yang C, Yan C, et al. Boosting ion dynamics through superwettable leaf-like film based on porous gC3N4 nanosheets for ionogel supercapacitors. NPG Asia Mater. 2019; 11:1–11.
- Sydam R, Ojha M, Deepa M. Ionic additive in an ionogel for a large area long lived high contrast electrochromic device. Sol Energy Mater Sol Cells. 2021; 220:110835.
- Vittoz P-Fo, El Siblani H, Bruma A, et al. Insight in the alginate Pd-ionogels—application to the tsuji–trost reaction. ACS Sustainable Chem Eng. 2018; 6:5192–5197.
- Craythorne SJ, Anderson K, Lorenzini F, et al. The co‐entrapment of a homogeneous catalyst and an ionic liquid by a sol–gel method: Recyclable ionogel hydrogenation catalysts. Chem - Eur J. 2009; 15:7094–7100.
- Ma J, Yan B. Multi-component hybrid soft ionogels for photoluminescence tuning and sensing organic solvent vapors. J Colloid Interface Sci. 2018; 513:133–140.
- Khodagholy D, Curto VF, Fraser KJ, et al. Organic electrochemical transistor incorporating an ionogel as a solid state electrolyte for lactate sensing. J Mater Chem. 2012; 22:4440–4443.
- Netto MMO, Gonçalves WB, Li RWC, et al. Biopolymer based ionogels as active layers in low-cost gas sensors for electronic noses. Sens Actuat B- Chem. 2020; 315:128025.
- Kavanagh A, Byrne R, Diamond D, et al. Stimuli responsive ionogels for sensing applications—an overview. Membranes. 2012; 2:16–39.
- Zhang L, Jiang D, Dong T, et al. Overview of ionogels in flexible electronics. Chem Rec. 2020; 20:948–967.
- Vioux A, Viau L, Volland S, et al. Use of ionic liquids in sol-gel; ionogels and applications. C R Chim. 2010; 13:242–255.
- Le Bideau J, Viau L, Vioux A. Ionogels, ionic liquid based hybrid materials. Chem Soc Rev. 2011; 40:907–925.
- Chen N, Zhang H, Li L, et al. Ionogel electrolytes for high-performance lithium batteries: A review. Adv Energy Mater. 2018; 8:1702675.
- Sun J, Yuan Y, Lu G, et al. A transparent, stretchable, stable, self-adhesive ionogel-based strain sensor for human motion monitoring. J Mater Chem C. 2019; 7:11244–11250.
- Sun J, Li R, Lu G, et al. A facile strategy for fabricating multifunctional ionogel based electronic skin. J Mater Chem C. 2020; 8:8368–8373.
- Chen B, Lu JJ, Yang CH, et al. Highly stretchable and transparent ionogels as nonvolatile conductors for dielectric elastomer transducers. ACS Appl Mater Interfaces. 2014; 6:7840–7845.
- Sun L, Chen S, Guo Y, et al. Ionogel-based, highly stretchable, transparent, durable triboelectric nanogenerators for energy harvesting and motion sensing over a wide temperature range. Nano Energy. 2019; 63:103847.
- Zhang S, Wang F, Peng H, et al. Flexible highly sensitive pressure sensor based on ionic liquid gel film. ACS omega. 2018; 3:3014–3021.
- Wang J, Xu J, Chen T, et al. Wearable human-machine interface based on the self-healing strain sensors array for control interface of unmanned aerial vehicle. Sens Actuat A-Phys. 2021; 321:112583.
- Zhang Y, Wang F, Chen T, et al.: Flexible high-sensitive pressure sensor based on ionogels and its application in monitoring the human motions. 2019 IEEE 14th International Conference on Nano/Micro Engineered and Molecular Systems (NEMS), 2019, pp. 362–365.
- Lan J, Li Y, Yan B, et al. Transparent stretchable dual-network ionogel with temperature tolerance for high-performance flexible strain sensors. ACS Appl Mater Interfaces. 2020; 12:37597–37606.
- Zhang LM, He Y, Cheng S, et al. Self‐healing, adhesive, and highly stretchable ionogel as a strain sensor for extremely large deformation. Small. 2019; 15:1804651.
- Wang Z, Zhang J, Liu J, et al. 3D printable, highly stretchable, superior stable ionogels based on poly (ionic liquid) with hyperbranched polymers as macro-cross-linkers for high-performance strain sensors. ACS Appl Mater Interfaces. 2021; 13:5614–5624.
- Wong J, Gong AT, Defnet PA, et al. 3D printing ionogel auxetic frameworks for stretchable sensors. Adv Mater Technol. 2019; 4:1900452.
- He B, Zhou Y, Wang Z, et al. A multi-layered touch-pressure sensing ionogel material suitable for sensing integrated actuations of soft robots. Sens Actuat A-Phys. 2018; 272:341–348.
- Liu H, Zhao G, Wu M, et al. Ionogel infiltrated paper as flexible electrode for wearable all-paper based sensors in active and passive modes. Nano Energy. 2019; 66:104161.
- Crump MR, Gong AT, Chai D, et al. Monolithic 3D printing of embeddable and highly stretchable strain sensors using conductive ionogels. Nanotechnology. 2019; 30:364002.
- Xiang S, Chen S, Yao M, et al. Strain sensor based on a flexible polyimide ionogel for application in high-and low-temperature environments. J Mater Chem C. 2019; 7:9625–9632.
- Lai J, Zhou H, Jin Z, et al. Highly stretchable, fatigue-resistant, electrically conductive, and temperature-tolerant ionogels for high-performance flexible sensors. ACS Appl Mater Interfaces. 2019; 11:26412–26420.
- Weng D, Xu F, Li X, et al. Polymeric complex-based transparent and healable ionogels with high mechanical strength and ionic conductivity as reliable strain sensors. ACS Appl Mater Interfaces. 2020.
- Ding Y, Zhang J, Chang L, et al. Preparation of high‐performance ionogels with excellent transparency, good mechanical strength, and high conductivity. Adv Mater. 2017; 29:1704253.
- Zhao G, Zhang Y, Shi N, et al. Transparent and stretchable triboelectric nanogenerator for self-powered tactile sensing. Nano Energy. 2019; 59:302–310.
- Sun J, Lu G, Zhou J, et al. Robust physically linked double-network ionogel as a flexible bimodal sensor. ACS Appl Mater Interfaces. 2020; 12:14272–14279.
- Li T, Wang Y, Li S, et al. Mechanically robust, elastic, and healable ionogels for highly sensitive ultra‐durable ionic skins. Adv Mater. 2020; 32:2002706.
- Cao Z, Liu H, Jiang L. Transparent, mechanically robust, and ultrastable ionogels enabled by hydrogen bonding between elastomers and ionic liquids. Mater Horiz. 2020; 7:912–918.
- Villa SM, Mazzola VM, Santaniello T, et al. Soft piezoionic/piezoelectric nanocomposites based on ionogel/BaTiO3 nanoparticles for low frequency and directional discriminative pressure sensing. ACS Macro Lett. 2019; 8:414–420.
- Ren Y, Guo J, Liu Z, et al. Ionic liquid–based click-ionogels. Sci Adv. 2019; 5:eaax0648.
- Chhetry A, Kim J, Yoon H, et al. Ultrasensitive interfacial capacitive pressure sensor based on a randomly distributed microstructured iontronic film for wearable applications. ACS Appl Mater Interfaces. 2019; 11:3438–3449.
- Qiu Z, Wan Y, Zhou W, et al. Ionic skin with biomimetic dielectric layer templated from calathea zebrine leaf. Adv Funct Mater. 2018; 28:1802343.
- Yoon SG, Park BJ, Chang ST. Highly sensitive piezocapacitive sensor for detecting static and dynamic pressure using ion-gel thin films and conductive elastomeric composites. ACS Appl Mater Interfaces. 2017; 9:36206–36219.
- Li R, Si Y, Zhu Z, et al. Supercapacitive iontronic nanofabric sensing. Adv Mater. 2017; 29:1700253.
- Choi D, Jang S, Kim JS, et al. A highly sensitive tactile sensor using a pyramid-plug structure for detecting pressure, shear force, and torsion. Adv Mater Technol. 2019; 4:1800284.
- Amoli V, Kim JS, Jee E, et al. A bioinspired hydrogen bond-triggered ultrasensitive ionic mechanoreceptor skin. Nat Commun. 2019; 10:4019.
- Jin ML, Park S, Lee Y, et al. An ultrasensitive, visco-poroelastic artificial mechanotransducer skin inspired by piezo2 protein in mammalian merkel cells. Adv Mater. 2017; 29:1605973.
- Nie B, Li R, Cao J, et al. Flexible transparent iontronic film for interfacial capacitive pressure sensing. Adv Mater. 2015; 27:6055–6062.
- Zhang Y, Sezen S, Ahmadi M, et al. Paper-based supercapacitive mechanical sensors. Sci Rep. 2018; 8:16284.
- Li S, Pan N, Zhu Z, et al. All-in-one iontronic sensing paper. Adv Funct Mater. 2019; 29:1807343.
- Li S, Chu J, Li B, et al. Handwriting iontronic pressure sensing origami. ACS Appl Mater Interfaces. 2019; 11:46157–46164.
- Cho SH, Lee SW, Yu S, et al. Micropatterned pyramidal ionic gels for sensing broad-range pressures with high sensitivity. ACS Appl Mater Interfaces. 2017; 9:10128–10135.
- Reza MS, Ayag KR, Yoo MK, et al. Electrospun spandex nanofiber webs with ionic liquid for highly sensitive, low hysteresis piezocapacitive sensor. Fibers Polym. 2019; 20:337–347.
- Chang Y, Wang L, Li R, et al. First decade of interfacial iontronic sensing: From droplet sensors to artificial skins. Adv Mater. 2021; 33:2003464.
- Lu P, Wang L, Zhu P, et al. Iontronic pressure sensor with high sensitivity and linear response over a wide pressure range based on soft micropillared electrodes. Sci Bull. 2021.
- Fan F-R, Tian Z-Q, Lin Wang Z. Flexible triboelectric generator. Nano Energy. 2012; 1:328–334.
- Zhu G, Pan C, Guo W, et al. Triboelectric-generator-driven pulse electrodeposition for micropatterning. Nano Lett. 2012; 12:4960–4965.
- Wang S, Lin L, Wang ZL. Nanoscale triboelectric-effect-enabled energy conversion for sustainably powering portable electronics. Nano Lett. 2012; 12:6339–6346.
- Zhang C, Dai K, Liu D, et al. Ultralow quiescent power-consumption wake-up technology based on the bionic triboelectric nanogenerator. Adv Sci. 2020; 7:2000254.
- Li Q, Dai K, Zhang W, et al. Triboelectric nanogenerator-based wearable electronic devices and systems: Toward informatization and intelligence. Digit Signal Process. 2021; 113:103038.
- Wu F, Chen N, Chen R, et al. Self‐regulative nanogelator solid electrolyte: A new option to improve the safety of lithium battery. Adv Sci. 2016; 3:1500306.
- Wu F, Chen N, Chen R, et al. “Liquid-in-solid” and “solid-in-liquid” electrolytes with high rate capacity and long cycling life for lithium-ion batteries. Chem Mater. 2016; 28:848–856.
- Lin Y, Dong X, Liu S, et al. Graphene–elastomer composites with segregated nanostructured network for liquid and strain sensing application. ACS Appl Mater Interfaces. 2016; 8:24143–24151.
- Amjadi M, Turan M, Clementson CP, et al. Parallel microcracks-based ultrasensitive and highly stretchable strain sensors. ACS Appl Mater Interfaces. 2016; 8:5618–5626.
- Choi DY, Kim MH, Oh YS, et al. Highly stretchable, hysteresis-free ionic liquid-based strain sensor for precise human motion monitoring. ACS Appl Mater Interfaces. 2017; 9:1770–1780.
- Truby RL, Katzschmann RK, Lewis JA, et al.: Soft robotic fingers with embedded ionogel sensors and discrete actuation modes for somatosensitive manipulation. 2019 2nd IEEE International Conference on Soft Robotics (RoboSoft), 2019, pp. 322–329.