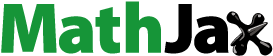
ABSTRACT
Lattice structure can realize excellent multifunctional characteristics because of its huge design space, and the cellular configuration directly affects the lattice structural performance and lightweight. A novel energy-absorbing multifunctional lattice structure with phononic bandgap is presented by topology and parameter optimization in this paper. First, the two-dimensional (2D) cellular configuration is lightweight designed by using independent continuous mapping (ICM) topology optimization method. The 2D cell is reconstructed by geometric parameters and rotated into a three-dimensional (3D) cell by using chiral shape to achieve bandgap. Subsequently, the surrogated model with energy absorption as the object and first-order natural frequency as the constraint is established to optimize a parametric 3D cell based on the Response Surface Methodology (RSM). Finally, the lattice structures are assembled with dodecagonal staggered arrangements to avoid the deformation interference among the adjacent cells. In addition, the lattice structural energy absorption and bandgap characteristics are analyzed and discussed. Compared to Kelvin lattice structure, the optimal lattice structure shows significant improvement in energy absorption efficiency. Besides, the proposed design also performs well in damping characteristics of the high-frequency and wide-bandgap. The lattice structural optimization design framework has great meaning to achieve the equipment structural lightweight and multi-function in the aerospace field.
GRAPHICAL ABSTRACT
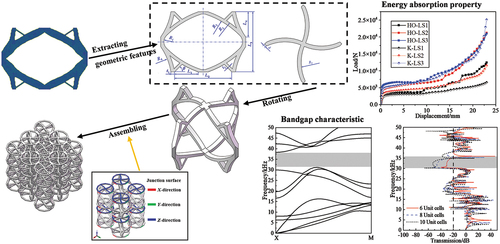
1. Introduction
Lattice structures have been widely used in the aerospace [Citation1], biomedical [Citation2–4] and other fields because of their high ratio of strength, high energy absorption, or vibration isolation. Therefore, extensive research has been conducted on the configuration design and property evaluation of lattice structures. Cellular configuration design is very important because the performance of the lattice structure is closely related to the geometric features of a cell. The traditional cellular configurations studied are mainly focused on body-centered cubic [Citation5], face-centered cubic [Citation6] and their combined deformed structures [Citation7,Citation8]. Furthermore, configurations with certain mechanical properties, such as negative Poisson’s ratio [Citation9,Citation10], compression and torsion [Citation11,Citation12], multi-stable switching [Citation13], and negative thermal expansion [Citation14,Citation15], have been designed owing to the high designability of lattice structures. However, it is necessary to design multifunctional lattice structures to ensure efficient and stable work of the mechanical system, with the diversification of engineering requirements. The design of multifunctional lattice structures has difficulties of interdisciplinary comparing with the single performance lattice structure, such as huge amount of calculation, high complexity of model establishment and solution, prominent coupling effect, etc. Hence, a systematic structural design method is needed to be developed to achieve multifunctional lattice structure.
The methods for designing lattice structures are summarized into three types, including bionic design inspired by nature, empirical design based on the deformation principle and structural optimization design using algorithms. Bionic design is an imitation of structures with specific properties and rules in nature, such that the resulting structures can reproduce these properties [Citation16–18]. Empirical design establishes a relationship between the structural geometric parameters and the required property during structural deformation by using the mechanical equilibrium equation, and the lattice structural property can be adjusted with the help of the established relationship [Citation19–22]. Structural optimization design involves the setting of objectives and constraints based on the optimization method and calculates the design variables iteratively by using an optimization algorithm until an optimal solution meeting the constraints is realized [Citation23–27]. Many studies have been conducted on artificially designed lattice structures based on the principle of functional structure deformation. However, few studies have been focused on designing lattice structures using a systematic structural optimization design method. Structural optimization design is classified as topology, shape, and parameter optimization. A configuration with the optimal material distribution is generated by topology optimization in the conceptual design stage [Citation28–30]. The mechanical properties can be further improved by detailed design of geometry shape and parameters optimization. Topology optimization has higher design freedom, more innovative configurations, and greater economic benefits. Therefore, the topology optimization is key to an innovative lattice structural design.
In recent decades, the research of topology optimization methods has attracted many scholars, the typical methods of continuum topology optimization are the homogenization method [Citation31], evolutionary structure optimization method [Citation32], SIMP method [Citation33,Citation34], phase field method [Citation35], level set method [Citation36–38], moving deformable component method [Citation39], and independent continuous mapping (ICM) method [Citation40,Citation41]. Homogenization theory [Citation42,Citation43] is a common analysis method to study periodic structures. The homogenization theory generally takes the flexibility as the optimization goal, introduces the hollow cell microstructure, and takes the unit cell size as the design variable. In addition, the homogenization method determines the existence of the microstructure by the change of the cell size in the optimization process, and allows the existence of the intermediate size unit cell, so that the topology optimization model and the size optimization model are unified and continuous. However, the sensitivity calculation becomes complicated due to the existence of density and orientation variables in the optimization model. It is still difficult to establish a topology optimization model based on the homogenization theory with the object of energy absorption and phononic bandgap. And the checkerboard phenomenon is easy to appear in the process of solving the optimization model, which affects structural continuity. Hence, the cellular configuration of the lattice structure is explored via the ICM method in this work. Generally, the optimization model of the ICM method is established with the goal of lightweight structure and the constraint of mechanical performance. The independent continuous topological variables are introduced to indicate the existence or absence of material and used to approximate discrete topological variables. A filtering function is implemented to recognize the relation between the topological variables and structural mechanical performances. Then, the topology optimization model is solved via the dual sequential quadratic programming algorithm to reduce the complexity of finite element calculation [Citation44].
The research studies on energy-absorbing lattice structures are relatively comprehensive, in terms of both configuration and material. In terms of configuration, in addition to the body-centered cubic structures [Citation45], there also exist ring [Citation46], Kelvin [Citation47], diamond [Citation48] and bionic lattice structures [Citation49,Citation50]. Many scholars have also analyzed the energy absorption performance of gradient lattice structures [Citation51–53]. The development of additive manufacturing has played a role in promoting further research on lattice structures, thus facilitating the application of a variety of materials to the study of lattice structures, such as aluminum alloys [Citation54], cobalt-chromium alloys [Citation55], steel [Citation56] and other metals, resins [Citation57] and other polymer materials, and fiber-reinforced composite materials [Citation58]. Recently, the bandgap analysis of lattice structures combined with phononic crystals has received significant attention and has become the research hotspot, which has important meanings to study the structural performance of vibration isolation, noise reduction, and wave absorption. The bandgap characteristic reflects the vibrational damping property of the structure, which prevents the propagation of elastic waves in a certain frequency domain. According to the boundary, lattice structures with phononic bandgap are divided into one-dimensional [Citation59], two-dimensional [Citation60,Citation61] and three-dimensional structures [Citation62]. Recently, the chiral structure [Citation63,Citation64] has been proven to not only have negative Poisson’s ratio, but also the potential to achieve band gaps due to their asymmetry. In addition, lattice structures with bandgap and other functions are designed, such as negative thermal expansion lattice structure with bandgap [Citation65] and multi-stable lattice structure with bandgap [Citation66].
Recently, scholars begin to pay attention to the study of multifunctional lattice structures with phonon bandgap and energy absorption. Jiang et al. [Citation67] added elastic strut connections to the face-centered cube frame, which realized the bandgap function of the energy-absorbing lattice structure. Zhang et al. [Citation68] designed a layered lattice structure with vibration isolation and energy absorption based on the idea of layered design. However, at present, there is no systematic optimization method to design this multifunctional lattice structure. Directly using topology optimization to obtain the final structure is the most ideal design form. However, the combination of these two properties exists in interdisciplinary problems of mechanics and acoustics in lattice structural design, which is mainly manifested in the establishment of the model and the coupling effect. The mechanical problem is to analyze the energy absorption capacity of the structure under large deformation, and the acoustic problem is to investigate the propagation characteristics of elastic waves in the structure. Hence, it is still difficult to characterize these two properties simultaneously. In addition, how to apply boundary conditions to the base structure to analyze the two properties also needs further consideration. In this study, the multifunction of the lattice structure is realized by step-by-step design. This design strategy simplifies the complex problem of two performance coupling, which also avoids the large amount of calculation and iterative non-convergence in the design process. A topology optimization model with displacement constraints is established based on the ICM method and solved to obtain a lightweight conceptual structure. The bandgap is realized by combining chiral rotation deformation and geometric parameters with better performance and is obtained by parameter optimization. The results of two performance analyses show that the design method is feasible.
This paper is composed of four sections as follows. The process of lattice structure design is described in section 2, including topology optimization, parameter optimization, and arrangement design. In section 3, the compression process of the lattice structure is analyzed, and the energy absorption capacity of two kinds of lattice structures composed of Hybrid Optimization-Cell and Kelvin cell are compared. In section 4, the phononic bandgap characteristics of lattice structures are analyzed via numerical simulations and the influence of cellular parameters on the bandgap frequency and width is discussed. Conclusions are provided in Section 5.
2. Lattice structure design
A novel structural design framework combining topology optimization and parameter optimization is proposed to design an energy absorption lattice structure with damping performance. The design process is divided into three steps, including topology optimization design, parameter optimization design, and assemble design of the cells.
2.1 Topology optimization design
The cellular configuration with energy absorption is explored by the ICM method. The design domain of the cell is a rectangle with the sizes of 14 mm × 10 mm, as shown in . Aluminum alloy is a selected material with an elastic modulus of 72.4 GPa, a density of 2800 kg/m3, and Poisson’s ratio of 0.33. Symmetrical fixed constraints are applied to the midpoints on the two vertical edges of the rectangle, and a vertical downward point load F = 1000 N is imposed at the midpoints and 1/7 side lengths from the end points on the two horizontal edges. The design domain is divided into 14,000 shell elements. The structural volume is considered as the objective and two horizontal edge midpoints of the base structure are set as the displacement constraints of key nodes. The topology optimization model is established as follows:
where is the topological variable vector,
the design variable space, and
the volume of the topological configuration, respectively;
the key nodal displacements,
the upper bound of the constraint value, and
the number of displacement constraints of key nodes, respectively;
the number of topological variables, and
the lower bound of the topological variables, respectively.
In order to obtain the standard quadratic programming model of EquationEquation (1)(1)
(1) , the explicit relationship between the objective and topology variables is established by the second-order Taylor expansion and the explicit function of constraints is obtained via the first-order Taylor expansion. Then, the standardized model is solved via using the dual sequence quadratic programming algorithm [Citation40].
The iterative history of topology configuration and its structural volume ratio are presented in . The topology optimization converges after 69 iteration steps. The structural volume ratio decreases rapidly at the beginning of the iteration, but the rate of decrease begins to slowdown when the iteration reaches step 10. After iteration to step 36, the volume ratio is almost unchanged, and the final value is 0.384. A highly lightweight configuration is obtained by topology optimization.
shows the design process of the lattice structure. A smooth topological configuration is presented in . A parametric two-dimensional (2D) cell is obtained via reconstructing a geometric model of the topological configuration, as illustrated in . The 2D cell is then rotated into a three-dimensional (3D) cell with reference to the chiral structure shown in to design the cell with phononic bandgap. lists the geometric parameters of the 2D cell and its chiral structure. The conceptual design of a 3D cell named Topology Optimization-Cell (TO-C) is displayed in , and the thickness of the 3D cell is determined by the chiral structure parameter δ. In addition, the parameters of TO-C are further optimized, which is described in section 2.2. The lattice structure is assembled by cells in a dodecagonal staggered layout, which is chosen in section 2.3.
Figure 2. Lattice structure design process. (a) Design domain of topology optimization; (b) Topology optimization configuration; (c) Parameterized two-dimensional cell; (d) Chiral structure; (e) Conceptual design of three-dimensional cell (Topology Optimization-Cell); (f) Detail design of three-dimensional (Hybrid Optimization-Cell); (g) Lattice structure assembled by cells.
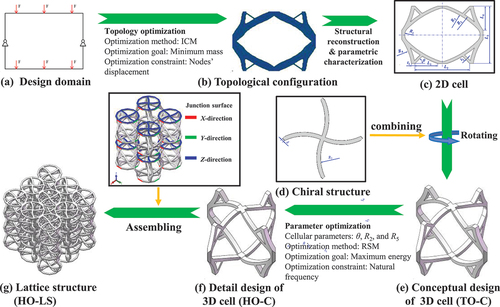
Table 1. Geometric parameters of the 2D cell and chiral structure.
2.2 Parameter optimization design
The above parameterized 2D lattice structure cell is constructed via a topology optimization method and a series of deformation designs. Parameter optimization is carried out to obtain a 3D cell with better mechanical properties.
The lattice structure material is aluminum alloy 2014-T4 and the material properties are as follows: Young’s modulus of 72.4 GPa, density of 2800 kg/m3, Poisson’s ratio of 0.33, yield stress of 290 MPa, ultimate strength of 470 MPa and elongation of 10%. The constitutive model of the material is an ideal elastic-plastic model. The stress–strain relationship is linear elastic when the stress is less than the yield stress. The material yield occurs when the stress is equal to the yield stress, and the stress value remains with the increase of strain. Quasi-static compression and vibration modal analysis of the cell are implemented by the numerical simulation to study the energy absorption and frequency characteristic of TO-C. shows the quasi-static compression performance, vibration mode, and parameter effects of TO-C. From the load–displacement curve illustrated in , the compression process includes three stages: elastic, platform, and dense stage. The displacement from 0 mm to approximately 0.9 mm occurs in the elastic stage. The load increases rapidly with the increase of displacement in this stage, and with the further compression, the rising trend of load becomes slower due to the bending of the main support rod. The displacement values from 0.9 mm to approximately 4.0 mm are in the platform stage and basically maintain a height as the displacement value increases. It begins to enter the dense stage after the displacement reaches 4.0 mm, and the load increases rapidly again as the displacement increases. A fixed constraint is imposed on the bottom of the cell, and a vibration modal analysis is performed. The vibrational mode is shown in and the cellular first-order natural frequency value is 7323.6 Hz.
Figure 3. Quasi-static compression history, vibration mode and parameters effects of TO-C. (a) Quasi-static compression load–displacement curve of cell. (b) Vibration mode. (c) Variation curve of energy absorption and first-order natural frequency with θ. (d) Variation curve of energy absorption and first-order natural frequency with R2. (e) Variation curve of energy absorption and first-order natural frequency with R5.
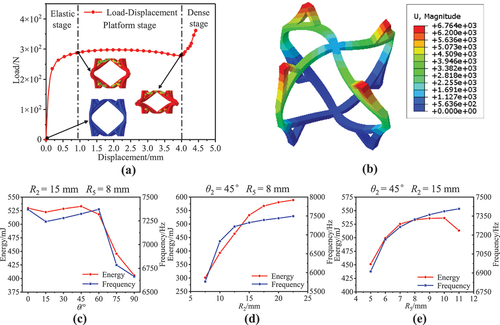
presents the effects of cellular parameters θ, R2, and R5 on the compressed energy absorption and first-order natural frequency, respectively. θ ranges from 0° to 90° with the spacing of 15°; R2 ranges from 7.5 mm to 22.5 mm with a spacing of 2.5 mm; R5 ranges from 5 mm to 11 mm with a spacing of 1 mm. It is found that the cellular energy absorption surges with the increase in R2, increases at first with the increase in R5, and begins to decrease after R5 reaches the value of 10 mm. The change of energy absorption as θ is complex: it decreases when the value of θ is less than 15°, increases between 15° and 45°, and decreases rapidly when the value of θ is greater than 45°. The variation in the first-order natural frequency with θ is like that in energy absorption and increases with the increase in R2 and R5. In addition, the influence of θ on the two properties is less than that of the other two parameters.
When the frequency of the external load is consistent with the natural frequency, structural resonance will be induced. This situation can be avoided by increasing the cell structural natural frequency. And then, the parameters of the cell are optimized by using the response surface methodology (RSM), which is an optimization method of fitting the functional relationship between influencing factors and response values via using multiple regression equations [Citation69,Citation70]. The parameter optimization model is established by taking the maximum energy absorption as the objective, first-order natural frequency as the constraint:
where x is the design variable vector, the design variable space, and
the function of the energy absorption with respect to cellular geometric parameters, respectively.
is the number of design variables,
the function of the first-order natural frequency with respect to cellular geometric parameters, and
the first-order natural frequency constraint value, respectively.
and
are the lower and upper bounds of the design variables, respectively. The number of design variables
is three, including the TO-C geometric parameters θ, R2, and R5.
Before function fitting, a certain amount of sample data needs to be prepared. Twenty sample points are randomly selected by the super-Latin cube method. The first-order natural frequency and energy absorption responses of the sample points are obtained via numerical simulations. The 20 sample points and the response values of the energy absorption and first-order natural frequency are shown in .
Table 2. Sample points and response values.
Based on the data in , the response polynomial relationship between the first-order natural frequency and absorbed energy with respect to the three parameters is obtained as follows:
The complex correlation coefficient and revised complex correlation coefficient
are introduced to evaluate the accuracy of the fitting formula. The closer these two values are to 1, the better the fitting accuracy [Citation71].
and
of the first-order natural frequency fitting formula are 0.991 and 0.975, respectively. Furthermore,
and
of the energy absorption fitting formula are 0.986 and 0.961, respectively. Therefore, the response surface fitting formulas of the first-order natural frequency and energy absorption satisfy the accuracy requirements.
The surrogated model is solved by using the Non-linear Programming by the Quadratic Lagrangian (NLPQL) algorithm. The algorithm solution settings are given as follows: the initial values of the TO-C geometric parameters θ, L2, and R2 are [45°, 15, 8], and the first-order natural frequency constraint value is 7700 Hz. The convergent accuracy of the optimization solution is set to 1 × 10−6.
After 75 iterations, the optimal parameter combination [50.72°, 21.52, 9.79] is obtained. The cell designed through topology optimization and parameter optimization is called the Hybrid Optimization-Cell (HO-C), as shown in . presents parameter changes of TO-C and HO-C. The energy absorption increases from 533.073 mJ to 596.114 mJ with a growth rate 11.8%. The first-order natural frequency raises from 5.1% from 7323.6 Hz to 7700 Hz with a growth rate 5.1%. In addition, the natural frequency of the cell is related to its phononic bandgap. The influence is analyzed in detail in section 4.1.
Table 3. Comparison of TO-C and HO-C.
To verify the accuracy of the parameter optimization structure, the 3D cell is reconstructed and simulated using the optimized parameters. The numerical analysis results of the frequency and absorbed energy absorption are 7517.5 Hz and 595.312 mJ, with errors of 2.37% and 0.13%, respectively.
2.3 Assemble design
The lattice structural mechanical properties are not only closely related to the cells, but also affected by the interaction among them. The deformation of the cell structure along the cross direction is large during the compression process, and a suitable arrangement could ensure the normal deformation of the lattice structure during the compression process. The arranged lattice structures are named the Topology Optimization-Lattice Structure (TO-LS) and the Hybrid Optimization-Lattice Structure (HO-LS), HO-LS as shown in .
shows three arrangements of lattice structures formed by cells. presents the TO-LS assembled by a direct linear periodic arrangement, where the red arrow indicates the direction of the large deformation of the cell. It is evident from that the transverse deformation of the four adjacent cells is concentrated in one position, which results in stress concentration of the lattice structure. The lattice structure is assembled in an octagonal staggered arrangement to avoid large deformation of adjacent cells in the same direction, as shown in . Although this arrangement prevents the direct influence of adjacent cells, as compression progresses, geometric interference occurs in the transverse deformation of diagonal cells, as indicated by the black circle in . Assembling cells using these two arrangements destroys the programmability of lattice structures.
Figure 4. Arrangements. (a) Linear arrangement. (b) Octagonal staggered arrangement. (c) Dodecagonal staggered arrangement. (d) the compressive deformation stress cloud diagram with linear arrangement. (e) the compressive deformation stress cloud diagram with octagonal staggered arrangement. (f) the compressive deformation stress cloud diagram with dodecagonal staggered arrangement.
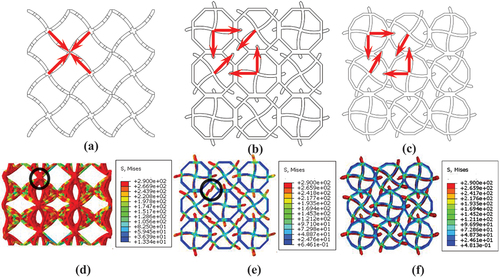
The final choice of dodecagon staggered arrangement to make cell and lattice structure satisfy certain law of energy absorption, as shown in . illustrates top view of the compressive deformation stress cloud diagram and it shows that the compression deformation of each cell is no longer affected by the adjacent cells. The energy absorption performance of the single-layer lattice structure is analyzed by numerical simulations to verify the lattice structural programmability in this arrangement. When the compression ratio of the single-layer lattice structure is 20%, the energy absorption is 4890.19 mJ. Theoretically, there is a multiple relationship between the lattice structural energy absorption and cellular energy absorption, and the coefficient is the number of the cells, which is 9. Hence, the energy absorption theoretical value of the single-layer lattice structure is 4797.657 mJ, which is basically consistent with the value of numerical simulation.
3. Energy absorption property
In this section, the energy absorption property of a 3 × 3 × 3 lattice structure is discussed in the process of quasi-static compression. The deformation of the lattice structure is first analyzed by compression stress cloud diagram. Then, the optimal lattice structures are compared with Kelvin lattice structure (K-LS) [Citation72] in the energy absorption capacity because Kelvin lattice structure has high compressive strain rate and long-stage interval of energy absorption platform.
3.1 Compression performance
The mechanical properties of HO-LS with the dodecagonal staggered arrangement are studied. presents the front and top views of the stress cloud diagram, with a compression ratio of 10%, 20%, 30%, and 40%, respectively. From the top views, it can be found that the lattice structural stress distribution is relatively even when it is compressed, and the lattice structure layers flip slightly when the strain reaches 30%. The front views presented in show that the deformation of each layer is almost identical during quasi-static compression.
Table 4. Top and front views of the HO-LS compression stress cloud diagram.
3.2 Comparison of energy absorption
The compression-energy absorption performances of HO-LS and K-LS with different volume ratios are compared. HO-LS with different volume ratios is obtained by changing the parameter δ of HO-C. The δ values of 0.5 mm, 0.7 mm, and 0.9 mm are selected here, and the corresponding lattice structures are presented in . And K-LS with the same volume ratio as HO-LS is established, as shown in .
Figure 5. Compression properties of HO-LS and K-LS with different volume ratios. (a) HO-LS. (b) K-LS. (c) Compression load–displacement curve of HO-LS and K-LS. (d) Compression energy absorption curve of HO-LS and K-LS.
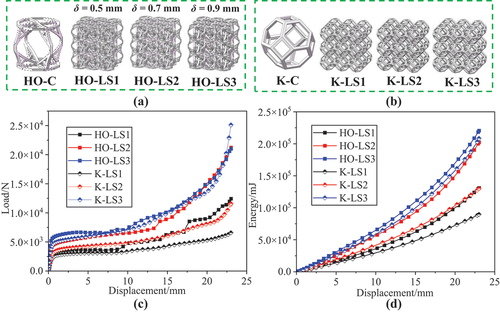
The mechanical properties of lattice structures under quasi-static compression of up to 80% are analyzed without considering failure, and the compression performance is characterized by load – displacement curves and energy–displacement curves.
It can be found from the load–displacement curves in that both HO-LS and KO-LS with different volume ratios have a long compression platform stage. In this stage, the height of the platform increases but the length of the platform becomes shorter with the increase in the volume ratio. The lattice structures enter the dense stage when the amount of their structural compression is approximately 30%. The rods inside the cell are toppled with the increase in displacement at this stage. Hence, the load–displacement curves show oscillation phenomenon. The energy–displacement curves are shown in , where the linear part corresponds to the platform stage and the rapidly growing part corresponds to the dense stage.
In addition, the load–displacement curves show that the stiffness of HO-LS is usually greater than that of K-LS with the same volume ratio. The energydisplacement curves are more intuitive to compare the energy absorption properties of the two lattice structures, and it is obvious that the HO-LS has higher energy absorption efficiency. The results indicate that the presented lattice structural optimization design framework is effective in achieving a lattice structure with excellent energy absorption performance.
4. Bandgap property
The damping performance is evaluated using bandgap and transmission characteristics of the elastic wave propagation in the structure. The phononic bandgap properties of the designed lattice structure are verified by the energy band structure and transmission characteristic curve. In addition, the influence of cellular geometric parameters on the frequency and width is analyzed and discussed.
4.1. Bandgap and transmission analysis
Bandgap is a range of frequencies in which the propagation of elastic waves is inhibited [Citation67]. A simplified triangular Brillouin region is presented in . The designed lattice structure is anisotropic, and there are two main directions: longitudinal (loading direction) and transverse. The setting of the chiral structure by rotational deformation is used to realize the bandgap in the loading direction. Therefore, the lattice structure designed is anisotropic, and only the bandgap characteristic in the X-M direction is studied. shows the bandgap properties of two lattice structures (TO-LS and HO-LS). As shown in , TO-C has an apparent X-M bandgap between 31 kHz and 38 kHz, while HO-C has an X-M bandgap between 33 kHz and 41 kHz. HO-C has higher bandgap frequency and wider bandwidth than TO-C.
Figure 6. The region of Bloch wave vector transmission and a model of analyzing transmission characteristic (a) Illustration of the Brillouin region. (b) the beam consisting of the six cells (excited by simple harmonics at one end).
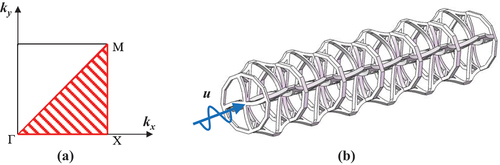
Figure 7. Bandgap and transmission characteristic. (a) X-M energy band structure diagram of TO-C. (b) Transmission characteristic curve of TO-Beam. (c) X-M energy band structure diagram of HO-C. (d) Transmission characteristic curve of HO-Beam.
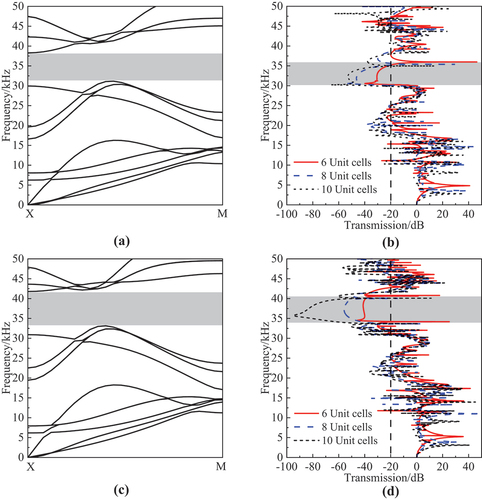
The transmission characteristic curve of the beam comprising six, eight, and ten cells along the X-M direction are analyzed to further characterize the damping property of the lattice structure in the bandgap frequency range. The beam with six cells is presented in . A simple harmonic wave excitation is applied at one end of the beam, and the displacement frequency response function is obtained via finite-element calculations with different excitation frequencies:
where is the transmission of the structure,
the displacements of the input under excitation, and
the displacement of the output under excitation, respectively. The transmission characteristic curves are illustrated by scanning the
in the frequency range of the energy band structure diagrams, which is illustrated in . The broadband damping region almost completely matches the bandgap of the energy band structure diagram on considering an attenuation of −20 dB as the standard. In addition, it can be found that with the increase in the number of cells, the smaller the transmission value is, the more obvious the damping capacity is.
4.2. Parametric analysis
The comparison of the cell structural bandgap before and after the parameter optimization in 4.1 also indicates that the cell geometric parameters have an effect on the bandgap. The bandgap influence of the cellular parameters is analyzed in this section. The selected parameters are δ, θ, R2, and R5. The range of δ is from 0.3 mm to 0.9 mm with an interval of 0.2 mm. The values of the other three parameters and corresponding rules are the same as those of section 2.2. shows the influence of the cellular geometric parameters on the bandgap frequency and bandgap width.
Figure 8. Variation of bandgap frequency and bandwidth with cellular geometric parameters. (a) Bandgap frequency of TO-C varying with θ. (b) Bandgap width of TO-C varying with θ. (c) Bandgap frequency of TO-C varying with R2. (d) Bandgap width of TO-C varying with R2. (e) Bandgap frequency of TO-C varying with R5. (f) Bandgap width of TO-C varying with R5.
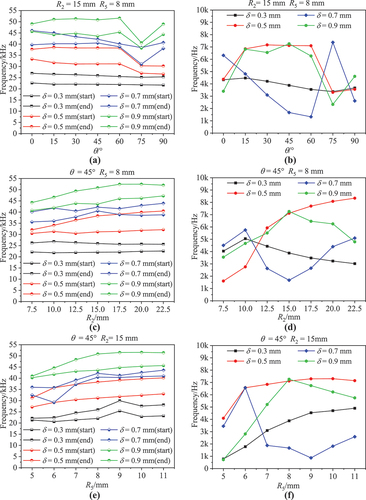
presents the influence of θ on the bandgap frequency. It is observed that a smaller value of θ has a little effect on the bandgap frequency. However, when the value of θ is 75°, the bandgap frequency exhibits an obvious downward mutation. presents the effect of R2 on the bandgap frequency. It can be observed that the bandgap frequency grows with R2. Similarly, the bandgap frequency also increases with R5, as shown in . From the three images, it is apparent that the bandgap frequency increases significantly with δ. However, when δ is 0.7 mm, the bandgap frequency curve of TO-C is oscillatory. The abrupt change in the bandgap frequency occurs because the specific parameter values of the cell structure could affect other parameters.
The width of the bandgap is determined by the bandgap start and end frequencies. Therefore, an abrupt change in the bandgap frequency causes a sudden change in the influence of the bandgap width parameters. present the effects of three parameters on the bandgap width of TO-C. It is observed that the bandgap width of TO-C for the same δ value is similarly affected by the three parameters. In addition, it is surprising that the bandgap frequency of the lattice structure is abrupt when the parameter value increases to a certain value.
5. Conclusions
This article proposes a lattice structural optimization design framework. A lattice structure with excellent energy absorption and phononic bandgap is designed by combining topology optimization, chiral rotation deformation, and parameter optimization. The design process of the lattice structure is described systematically, and its energy absorption and bandgap properties are analyzed. The main conclusions are as follows:
By assembling HO-C cells into a lattice structure in a dodecagonal-staggered arrangement, the energy-absorbing programmability can be guaranteed because the geometric interference among cells can be avoided when the lattice structure is compressed.
By comparing the energy absorption performance of HO-LS and K-LS with different volume ratios, the method combined with topology and parameter optimization is effective and feasible in designing a lattice with a good energy absorption characteristic. In addition, the platform height of load–displacement curves increases and the platform length decreases with the increase in the structure volume ratio.
Both HO-LS and K-LS show that the lattices designed by rotation deformation with reference to the chiral structure usually possess damping characteristics of high-frequency and wide-bandgap. The frequency range of the phononic bandgap can be adjusted by changing the geometric parameters of the cell.
This study provides a systematic method for the exploration of lightweight multifunctional lattice structure in the aerospace field. In addition, the phononic bandgap involves the frequency value and the width, which is more complicated than the natural frequency in the cell optimization design. The authors will further explore the parallel optimization design of the energy-absorbing lattice structure by adding bandgap properties to the optimization elements.
Acknowledgments
This research was supported by the National Natural Science Foundation of China (11872080, 12202008) and the Natural Science Foundation of Beijing, China (3192005).
Disclosure statement
The authors declare that they have no known competing financial interests or personal relationships that could have appeared to influence the work reported in this paper.
Additional information
Funding
References
- Wang C, Zhu J, Wu M, et al. Multi-scale design and optimization for solid-lattice hybrid structures and their application to aerospace vehicle components. Chin J Aeronaut. 2021;34(5):386–398.
- Sufiiarov VS, Orlov AV, Borisov EV, et al. Design and mechanical properties simulation of graded lattice structures for additive manufacturing endoprostheses, Mech Adv Mater Struc. 2021;28(16):1656–1662.
- Feng J, Liu B, Lin Z, et al. Isotropic octet-truss lattice structure design and anisotropy control strategies for implant application. Mater Design. 2021;203:109595.
- Jam A, du Plessis A, Lora C, et al. Manufacturability of lattice structures fabricated by laser powder bed fusion: a novel biomedical application of the beta Ti-21S alloy. Addit Manuf. 2022;50:102556.
- Cao X, Jiang Y, Zhao T, et al. Compression experiment and numerical evaluation on mechanical responses of the lattice structures with stochastic geometric defects originated from additive-manufacturing. Compos B Eng. 2020;194:108030.
- Wang P, Yang F, Li P, et al. Design and additive manufacturing of a modified face-centered cubic lattice with enhanced energy absorption capability. Exter Mech Lett. 2021;47:101358.
- Chang C, Wu W, Zhang H, et al. Mechanical characteristics of superimposed 316l lattice structures under static and dynamic loading. Adv Eng Mater. 2021;23(7):2001536.
- Sun ZP, Guo YB, Shim VPW. Characterisation and modeling of additively-manufactured polymeric hybrid lattice structures for energy absorption. Int J Mech Sci. 2021;191:106101.
- Qin H, Yang D. Vibration reduction design method of metamaterials with negative Poisson’s ratio. J Mater Sci. 2019;54(22):14038–14054.
- Yao Y, Ni Y, He LH. Rutile-mimic 3D metamaterials with simultaneously negative Poisson’s ratio and negative compressibility. Mater Design. 2021;200:109440.
- Fernandez Corbaton I, Rockstuhl C, Ziemke P, et al. New twists of 3d chiral metamaterials. Adv Mater. 2019;31(26):1807742.
- Frenzel T, Kadic M, Wegener M. Three-dimensional mechanical metamaterials with a twist. Science. 2017;358(6366):1072–1074.
- Yang H, Ma L. 1D to 3D multi-stable architected materials with zero Poisson’s ratio and controllable thermal expansion. Mater Design. 2020;188:108430.
- Yu H, Wu W, Zhang J, et al. Drastic tailorable thermal expansion chiral planar and cylindrical shell structures explored with finite element simulation. Compos Struct. 2019;210:327–338.
- Li Y, Wan Y, Shen Y, et al. Experimental demonstration of lightweight lattice metamaterials with controllable low thermal expansion. Thin Wall Struct. 2021;159:107112.
- Kumar A, Collini L, Daurel A, et al. Design and additive manufacturing of closed cells from supportless lattice structure. Addit Manuf. 2020;33:101168.
- Nazir A, Ali M, Jeng J. Investigation of compression and buckling properties of a novel surface-based lattice structure manufactured using multi jet fusion technology. Materials. 2021;14(10):2599.
- Zhang Z, Zhang L, Song B, et al. Bamboo-inspired, simulation-guided design and 3D printing of light-weight and high-strength mechanical metamaterials. Appl Mater Today. 2022;26:101268.
- Li S, Hu M, Xiao L, et al. Compressive properties and collapse behavior of additively-manufactured layered-hybrid lattice structures under static and dynamic loadings. Thin Wall Struct. 2020;157:107153.
- Bahrami Babamiri B, Askari H, Hazeli K. Deformation mechanisms and post-yielding behavior of additively manufactured lattice structures. Mater Design. 2020;188:108443.
- Guo M, Yang H, Ma L. Design and characterization of 3D AuxHex lattice structures. Int J Mech Sci. 2020;181:105700.
- Fleisch M, Thalhamer A, Meier G, et al. Functional mechanical metamaterial with independently tunable stiffness in the three spatial directions. Mater Today Aav. 2021;11:100155.
- Dong H, Zhao S, Wei P, et al. Systematic design and realization of double-negative acoustic metamaterials by topology optimization. Acta Mater. 2019;172:102–120.
- Zheng Y, Wang Y, Lu X, et al. Evolutionary topology optimization for mechanical metamaterials with auxetic property. Int J Mech Sci. 2020;179:105638.
- Deng H, Hinnebusch S, To AC. Topology optimization design of stretchable metamaterials with Bézier skeleton explicit density (BSED) representation algorithm. Comput Method Appl M. 2020;366:113093.
- Li Z, Luo Z, Zhang L, et al. Topological design of pentamode lattice metamaterials using a ground structure method. Mater Design. 2021;202:109523.
- Jia J, Da D, Hu J, et al. Crashworthiness design of periodic cellular structures using topology optimization. Compos Struct. 2021;271:114164.
- Bendsøe MP, Sigmund O. Material interpolation schemes in topology optimization. Arch Appl Mech. 1999;69(9–10):635–654.
- Zhang W, Sun S. Scale‐related topology optimization of cellular materials and structures. Int J Numer Meth Eng. 2006;68(9):993–1011.
- Li S, Yuan S, Zhu J, et al. Additive manufacturing-driven design optimization-Building direction and structural topology. Addit Manuf. 2020;36:101406.
- Noguchi Y, Yamada T. Topology optimization of acoustic metasurfaces by using a two-scale homogenization method. Appl Math Model. 2021;98:465–497.
- Xia L, Xia Q, Huang X, et al. Bi-directional evolutionary structural optimization on advanced structures and materials: a comprehensive review. Arch Comput Method E. 2018;25(2):437–478.
- Montemurro M, Bertolino G, Roiné T. A general multi-scale topology optimisation method for lightweight lattice structures obtained through additive manufacturing technology. Compos Struct. 2021;258:113360.
- Zhou M, Rozvany GIN. The COC algorithm, Part II: topological, geometrical and generalized shape optimization. Comput Method Appl M. 1991;89(1):309–336.
- Takezawa A, Nishiwaki S, Kitamura M. Shape and topology optimization based on the phase field method and sensitivity analysis. J Comput Phys. 2010;229(7):2697–2718.
- Wang L, Li Z, Ni B, et al. Non-probabilistic reliability-based topology optimization (NRBTO) scheme for continuum structures based on the parameterized level-set method and interval mathematics. Comput Method Appl M. 2021;373:113477.
- Wang MY, Wang X, Guo D. A level set method for structural topology optimization. Comput Method Appl M. 2003;192(1–2):227–246.
- Liu H, Zong H, Tian Y, et al. A novel subdomain level set method for structural topology optimization and its application in graded cellular structure design. Struct Multidiscip O. 2019;60(6):2221–2247.
- Guo X, Zhang W, Zhong W. Doing topology optimization explicitly and geometrically — a new moving morphable components based framework. J Appl Mech. 2014;81(8). DOI:10.1115/1.4027609
- Ye H, Dai Z, Wang W, et al. ICM method for topology optimization of multimaterial continuum structure with displacement constraint. Acta Mech Sinica-Prc. 2019;35(3):552–562.
- Ye H, Yuan B, Li J, et al. Geometrically nonlinear topology optimization of continuum structures based on an independent continuous mapping method. Acta Mech Solida Sin. 2021;34(5):658–672.
- Andreassen E, Andreasen CS. How to determine composite material properties using numerical homogenization. Comp Mater Sci. 2014;83:488–495.
- Sha W, Xiao M, Zhang J, et al. Robustly printable freeform thermal metamaterials. Nat Commun. 2021;12(1):7228.
- Wang W, Ye H, Sui Y. Lightweight topology optimization with buckling and frequency constraints using the independent continuous mapping method. Acta Mech Solida Sin. 2019;32(3):310–325.
- Zhao M, Ji B, Zhang DZ, et al. Design and mechanical performances of a novel functionally graded sheet-based lattice structure. Addit Manuf. 2022;52:102676.
- Wang P, Yang F, Ru D, et al. Additive-manufactured hierarchical multi-circular lattice structures for energy absorption application. Mater Design. 2021;210:110116.
- Arshad AB, Nazir A, Jeng J. The effect of fillets and crossbars on mechanical properties of lattice structures fabricated using additive manufacturing. Int J Adv Manuf Technol. 2020;111(3–4):931–943.
- Jin N, Wang F, Wang Y, et al. Failure and energy absorption characteristics of four lattice structures under dynamic loading. Mater Design. 2019;169:107655.
- Yu Z, Xin R, Xu Z, et al. Shock-resistant and energy-absorbing properties of bionic niti lattice structure manufactured by SLM. J Bionic Eng. 2022;19(6):1684–1698.
- Ashok D, Raju Bahubalendruni MVA, Johnney Mertens A, et al. A novel nature inspired 3D open lattice structure for specific energy absorption. P I Mech Eng E-J Pro. 2022;236(6):2434–2440.
- Niknam H, Akbarzadeh AH. Graded lattice structures: simultaneous enhancement in stiffness and energy absorption. Mater Design. 2020;196:109129.
- Plocher J, Panesar A. Effect of density and unit cell size grading on the stiffness and energy absorption of short fibre-reinforced functionally graded lattice structures. Addit Manuf. 2020;33:101171.
- Zhang J, Song B, Yang L, et al. Microstructure evolution and mechanical properties of TiB/Ti6Al4V gradient-material lattice structure fabricated by laser powder bed fusion. Compos B Eng. 2020;202:108417.
- Zhang C, Banerjee A, Hoe A, et al. Design for laser powder bed additive manufacturing of AlSi12 periodic mesoscale lattice structures. Int J Adv Manuf Technol. 2021;113(11–12):3599–3612.
- Liverani E, Fortunato A. Stiffness prediction and deformation analysis of Cobalt-Chromium lattice structures: from periodic to functionally graded structures produced by additive manufacturing. J Manuf Process. 2021;68:104–114.
- Cao X, Xiao D, Li Y, et al. Dynamic compressive behavior of a modified additively manufactured rhombic dodecahedron 316L stainless steel lattice structure. Thin Wall Struct. 2020;148:106586.
- Park J, Park K. Compressive behavior of soft lattice structures and their application to functional compliance control. Addit Manuf. 2020;33:101148.
- Wen J, Zeng Y, Wu C, et al. Silk lattice structures from unidirectional silk fiber–reinforced composites for breaking energy absorption. Adv Eng Mater. 2020;22(3):1900921.
- Chen Y, Wu B, Li J, et al. Low-frequency tunable topological interface states in soft phononic crystal cylinders. Int J Mech Sci. 2021;191:106098.
- Li Y, Wang Y, Yao S. Multipolar resonance and bandgap formation mechanism of star-shaped lattice structure. Int J Mech Sci. 2021;193:106163.
- Zhang Y, Fan X, Li J, et al. Low-frequency vibration insulation performance of the pyramidal lattice sandwich metamaterial beam. Compos Struct. 2021;278:114719.
- An X, Lai C, He W, et al. Three-dimensional meta-truss lattice composite structures with vibration isolation performance. Exter Mech Lett. 2019;33:100577.
- Wei Y, Yang Q, Tao R. SMP-based chiral auxetic mechanical metamaterial with tunable bandgap function. Int J Mech Sci. 2021;195:106267.
- An X, Lai C, He W, et al. Three-dimensional chiral meta-plate lattice structures for broad band vibration suppression and sound absorption. Compos Part B-Eng. 2021;224:109232.
- Zhang X, Ye H, Wei N, et al. Design optimization of multifunctional metamaterials with tunable thermal expansion and phononic bandgap. Mater Design. 2021;209:109990.
- Wang J, Liu X, Yang Q, et al. A novel programmable composite metamaterial with tunable Poisson’s ratio and bandgap based on multi-stable switching. Compos Sci Technol. 2022;219:109245.
- Jiang W, Yin G, Xie L, et al. Multifunctional 3D lattice metamaterials for vibration mitigation and energy absorption. Int J Mech Sci. 2022;233:107678.
- Zhang L, Bai Z, Chen Y. Dual-functional hierarchical mechanical metamaterial for vibration insulation and energy absorption. Eng Struct. 2022;271:114916.
- Hou S, Dong D, Ren L, et al. Multivariable crashworthiness optimization of vehicle body by unreplicated saturated factorial design. Struct Multidiscip O. 2012;46(6):891–905.
- Zhang Y, Ye H, Li B, et al. Mechanical behavior of composite bistable shell structure and surrogate-based optimal design. Struct Multidiscip O. 2021;64(1):303–320.
- Ye H, Zhang Y, Yang Q, et al. Quasi-static analysis and multi-objective optimization for tape spring hinge. Struct Multidiscip O. 2019;60(6):2417–2430.
- Weeks JS, Ravichandran G. High strain-rate compression behavior of polymeric rod and plate Kelvin lattice structures. Mech Mater. 2022;166:104216.