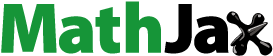
ABSTRACT
Along with the living environment, organisms have evolved structures that adapt to specific environments and have better mechanical properties. Bioinspired materials learn from nature and improve their mechanical properties by imitating the structure of living organisms. Based on the 4D printed shape memory polymer and the bioinspired design method, this research proposes a soft and hard phase hybrid bioinspired metamaterial with shape memory effect and programmable mechanical properties. Compared with traditional nacre-like materials, bioinspired materials have adjustable characteristics of mechanical properties, impact resistance, and low-frequency vibration isolation. First, based on the constitutive relation of SMP (Shape memory polymer) material and its numerical simulation, an intelligent bioinspired metamaterial is designed. Subsequently, the mechanical properties and vibration isolation behavior and adjustability performance of multi-scale bioinspired metamaterials are explained by experiments. Finally, the adjustable functional mechanism of the deformation and vibration isolation of the bioinspired metamaterial is described. The research of these bioinspired metamaterials has broad application prospects in the fields of impact protection and low-frequency vibration absorption.
Graphical abstract
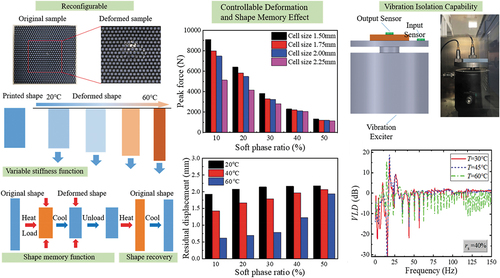
1. Introduction
Mechanical metamaterials are materials and structures designed artificially, which are usually periodic or aperiodic [Citation1]. They have mechanical properties or functions that even natural materials do not have [Citation2,Citation3]. By manually designing the internal microstructure, different deformation characteristics can be generated under the excitation of external physical fields. For example, the negative Poisson’s ratio, compression torsion coupling, negative compression, and negative stiffness characteristics of the response stress field [Citation4]; negative thermal expansion characteristics in response to temperature field [Citation5] and thus extensively applied in military, aerospace [Citation6], medical, and other fields [Citation7], such as flexible robots [Citation8], aviation structural devices [Citation9,Citation10], mechanical damping devices [Citation11,Citation12], mechanical invisibility cloaks [Citation13], etc. Imitating nature is the source of innovative scientific research. By simulating and imitating the typical structural characteristics of biological systems, transferring the unique functions of organisms to technical systems is a critical way to create new materials and structures [Citation14–16].
The bioinspired design method brings new possibilities to the development of the properties of the metamaterial [Citation17]. Recently, many research groups have successfully imitated the microstructure configuration of organisms such as bones, pearls [Citation18], and fish [Citation19,Citation20] to developed high-performance and multifunctional materials and structures [Citation21,Citation22]. For instance, Yin et al. [Citation23] drew lessons from the rare collagen fiber double helix structure in shark scales to design and manufacture a new composite material. The composite material has multistage delamination under bending and impact loads, which effectively prevents crack propagation and prolongs failure displacement, providing a new idea for designing the next-generation toughened composites. Barthelat et al. [Citation24] described and characterized the structure of the nacre on multiple scales, observed and quantified it, and found that the lamella had a wavy interlaced surface. The tensile and shear tests of the sample show that the nacre can withstand large inelastic strains and exhibit strain hardening.
Due to the extraordinary mechanical properties of shell structures, bioinspired design has broad application prospects [Citation14]. Research by Gu et al. [Citation25] shows that the fracture toughness is 1000 times harder than that of its mineral phase and ten times harder than the nacre. Subsequently, they prepared a multi-layered shell-like material structure. The experimental results show that compared with a single-level layered structure, the multi-level layered structure performs better in resisting impact loading. These nacre-like design methods, which significantly improve the mechanical properties, have broad prospects in developing bioinspired materials [Citation26]. LT et al. [Citation27] found that shells have a cross-layered microstructure, which is layered according to different geometric proportions and is a model of shell glued. The mineral content in the shell is high, but the mechanical properties are excellent. They studied the fracture properties of shells and found that their micro-periodical structure can guide the deflection and bending of cracks, and limit crack propagation and local deformation, thereby improving the toughness, strength, and hardness. These observations of the shell fracture mechanism led them to prepare a layered synthetic material with high toughness, high strength, and high hardness.
At present, bioinspired metamaterials have great application potential in aerospace industries due to their unique material order and geometric configuration, outstanding impact resistance [Citation28], highlighted energy absorption, and vibration reduction and isolation functions [Citation29,Citation30]. However, existing bioinspired metamaterials also have the following shortcomings: (1) Currently, most of the bioinspired metamaterials use traditional materials as the base material, and it is difficult to change the shape of the structure once molded [Citation31]; that means, it is impossible to realize the automatic adjustment of the structural mechanical properties; (2) Some of the bioinspired metamaterials cannot achieve shape recovery after deformation; (3) Research on the low-frequency vibration isolation function of bioinspired metamaterials is limited.
Shape memory polymer (SMP), a typical representative of materials with functional changes in mechanical properties and shape, refers to a type of intelligent polymer that can return to its original shape under high-temperature conditions. It has adjustable stiffness, shape memory effect, and high-temperature recovery characteristics [Citation32]. Through the combination of SMP and 3D printing technology [Citation33,Citation34], the use of SMP’s shape memory function [Citation35] for 3D printing formed 4D printing technology came into being [Citation11]. It adds the dimension of time to the base of 3D printing. 4D printed objects are no longer static and stable, and their morphology and properties may change dynamically over time [Citation36]. 4D printing technology brings new challenges and opportunities to the design and realization of heterogeneous bioinspired metamaterials. Combining the geometrically optimized configuration of shell bioinspired metamaterials with the characteristics of SMP materials can bring more application prospects [Citation37]. Hu et al. [Citation38] proposed to control the propagation of elastic waves/sound waves through metamaterials and designed SMP metamaterials with mechanical reconstruction and self-healing capabilities. The configuration and geometric parameters of the metamaterial are controlled by temperature changes so that the metamaterial can realize mechanical programming and response recovery, and the bandgap of the metamaterial can be significantly adjusted by changing the external temperature. By implanting SMP into the bioinspired metamaterial, an innovative configuration of SMP heterogeneous (multi-material) bioinspired metamaterial is designed and obtained, which can make the metamaterial sense external temperature changes and drive the structure to adjust stiffness, energy absorption, and insulation. The automatic adjustment of vibration and the automatic restoration of shape realize the controllable changes of the structural mechanics function in time and space dimensions and meet the application requirements of different occasions [Citation39].
Based on the 4D printing shape memory polymer and the bioinspired design method, this research proposes a soft and hard phase hybrid bioinspired metamaterial with a shape memory effect and adjustable mechanical properties. Compared with traditional nacre-like materials, it has adjustable mechanical properties, impact resistance, and low-frequency vibration isolation characteristics. First, based on the constitutive relation of SMP material and its numerical simulation, an intelligent bioinspired metamaterial is designed. Subsequently, the adjustable mechanical properties of multi-scale bioinspired metamaterials are explained through experiments and numerical calculations. Finally, the adjustable functional mechanism of the deformation and vibration isolation of the bioinspired metamaterial is described. The research of these bioinspired metamaterials can have broad application prospects in the fields of impact protection and low-frequency vibration isolation.
2. Specimen and material
2.1. Design concept
In nature, shells have been widely concerned due to their high toughness and strength. Recent research [Citation40] has shown that the nacre of shells is composed of inorganic and organic substances stacked in soft and hard alternately, presenting a cross-scale configuration of mixed and staggered soft and hard (see ). Just inspired by the shell microstructures, a multi-scale nacre-like metamaterial was proposed in the present study as illustrated in . The sublayers are alternatively arranged with a ply angle of [0°/90°]2s as schematically shown in . Note that in each sublayer, the specific dimensions of hard and soft phase materials are denoted as a and b, respectively. Correspondingly, the soft phase ratio is equal to
.
Figure 1. Design and fabrication of the nacre-like metamaterial. (a) Microscopic SEM of the shell; (b) arrangement of soft and hard materials in each sublayer of the nacre-like metamaterial; (c) stacking angle of the nacre-like metamaterial with different sublayers. (d) Multi-material printing technology to fabricate the nacre-like metamaterial; (e) 3D-printed nacre-like metamaterial samples with different soft phase ratios.
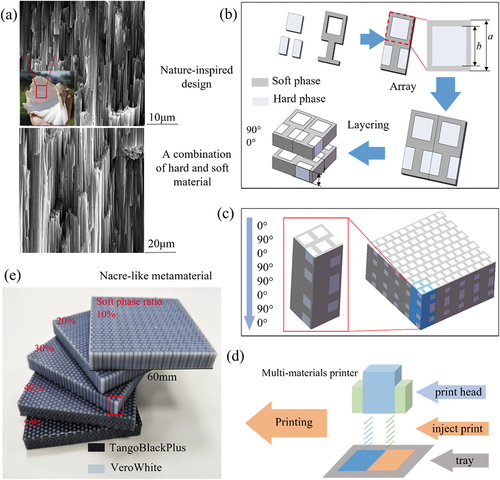
2.2. Samples
The development of multi-material printing technology has made it possible to prepare materials with particularly complex geometric structures. This work adopted multi-material 3D printing technology (Objet 350, Stratasys, U.S.A) to prepare the nacre-like metamaterials with dimensions of 60 mm × 60 mm. The basic flow of the 3D printing process is depicted in . The printer has a print precision of 16 ~ 30 μm in the thickness direction and 20 ~ 50 μm in the in-plane directions. In the multi-materials print model, the soft phase material is selected to be TangoBlackPlus. In particular, the hard phase is a VeroWhite, polymer, which has a shape memory function and variable stiffness function. Five soft phase ratios of 10%, 20%, 30%, 40%, and 50% were considered.
2.3. Material properties
In this study, the adopted soft phase material is TangoBlackPlus with a density of 1150 kg/m3, while the hard phase material is VeroWhite, with 1180 kg/m3 in mass density. To characterize the mechanical properties of these two materials, quasi-static uniaxial tensile tests were conducted on a universal testing machine at a displacement rate of 1 mm/min, in accordance with the ASTM. Standard dog-bone samples were cut from soft and hard material plates, as shown in . The obtained stress-strain curves are shown in , respectively. The peak stress of soft material and hard material is about 0.3 MPa and 35.1 MPa, respectively.
The hard phase is a shape memory polymer named VeroWhite, which has shape memory and variable stiffness functions. The printing strip is heated, then loaded, and then quickly cooled down and unloaded. The strip remains in an elongated and deformed state. When it is heated, the strip automatically returns from the deformed state to its original shape. The reason for the stiffness of shape memory polymers is that as the temperature increases, the activity of polymer chains in the polymer increases, and its elastic modulus decreases. Through dynamic mechanical analysis, the elastic modulus of VeroWhite varies with temperature. Therefore, under the same tensile force, the higher the temperature, the greater the deformation.
3. Adjustable indentation performance
3.1. Indentation tests
In the experiment, the diameter of the indenter is 12 mm, and the specimen size is 60 mm × 60 mm × 8 mm. There is a sensor on the indenter, and the influence of the cell size on the material properties is compared by measuring the reaction force of the indenter. The specimen is pressed into a depth of 3 mm and lifted. The experimental process is shown in .
3.2. Effect of cell size
By changing the cell size, the mechanical properties of the bioinspired metamaterials can be adjusted. Experiments were carried out at room temperature. As shown in , indentation tests were performed on bioinspired metamaterials with different cell sizes. The cell sizes are 1.50 mm, 1.75 mm, 2.00 mm, and 2.25 mm, respectively, and the experimental results after compression are shown in , respectively. It can be seen from that the cell size and the proportion of soft and hard phases have a significant impact on the peak pressure. shows the comparison of the peak pressure of the metamaterial compression experiment with different cell sizes under different soft-hard phase ratios. It can be seen from that when the soft phase ratio is low, the cell size has an important effect on the indenter reaction force. As the cell size increases, the indenter reaction force gradually decreases. When it is lower, the size of the soft phase mainly affects the indenter reaction force level. When the size of the cell increases, the soft size also increases. When the size of the indenter is constant, the larger the size of the cell, the less the number of compressed cells, and the larger the size of the compressed soft phase, so the indenter reaction force is smaller. As the cell size decreases, the number of cells within the same volume decreases, and the volume of the soft phase decreases relatively, so the indenter reaction force gradually increases. With the increase of the soft phase ratio, the influence of the cell size on the indenter reaction force becomes smaller and smaller. When the soft phase ratio is 50%, the indenter reaction force under different cell sizes is basically the same. By comprehensively comparing the compression tests of each cell size, it can be found that when the proportion of soft phase is less than 30%, the bearing capacity of the overall structure is greatly affected by the proportion of soft phase. Changing the proportion of soft phase will significantly reduce the peak pressure. An increase of 10% of the proportion of soft phase can reduce the pressure head reaction by about 3kN, with a reduction of 30%. When the proportion of soft phase tends to more than 30%, the overall bearing capacity tends to decrease linearly. This shows that the proportion of soft phase is 30%, which is the critical point of the change of the overall bearing capacity. When the proportion of soft phase is higher than 30%, the overall bearing capacity is reduced by the influence of the proportion of soft phase. An important relationship is that the larger the proportion of soft phase, the smaller the reaction force of the indenter. This is because the increase of the proportion of soft phase reduces the overall strength of the bionic material and makes it easier to deform. According to the experiment, an increase of 40% in soft ratio can reduce the overall peak pressure by about 85%. After the experiment, the soft and hard materials overlapped obviously in the part of the contact head, and the larger extrusion happened between different layers. Due to the different angle between different layers, the deformation of soft-hard interface is not continuous, and the deformation of each layer is relatively independent. Because VeroWhite is a hyperelastic material and TangoBlackPlus is a soft material, a hysteresis curve appears during the unloading process after loading. This is mainly due to the energy dissipation in the material, so the loading curve and the unloading curve cannot coincide. When a certain bearing pressure is given, different unit cell sizes can be selected according to these results to meet the performance requirements of the response. By changing the size of the unit cell, the indenter reaction force can be adjusted from 500 N to 1000 N.
3.3. Effect of temperature
Temperature also has a significant effect on the soft and hard phase bioinspired metamaterials. The purpose of adjusting the mechanical properties of metamaterials can be achieved by changing the temperature. As shown in , compression tests were performed on bioinspired metamaterials with different soft phase ratio. The experiment was measured under the conditions of 20°C, 40°C, and 60°C, respectively. The results are shown in . It can be seen from that the lower the proportion of the soft phase of the material at the same temperature, the greater the indenter reaction force as the force required to compress the hard material with the same displacement at the same temperature is greater. When the proportion of soft phase tends to more than 30%, the overall bearing capacity tends to decrease linearly. Under the condition of 40°C, the change range of the reaction force of the indenter is 400N to 1800N, which is because the elastic modulus of the hard phase material changes sharply with the temperature. The change of the elastic modulus of the hard phase material with the temperature is shown in . At 20°C, the elastic modulus of the hard phase material is 960 MPa, when the temperature is 40°C, the elastic modulus becomes 700MPa, when the temperature rises to 60°C, the elastic modulus is about 100MPa, and the change range can reach 10 times. After slowly raising the indenter, noticeable indentation can still be seen, which indicates that there is a residual strain in the bioinspired material. This is because the hard phase material is a viscoelastic material, which shows linear elasticity before the glass transition temperature. The elastic modulus decreases gradually with the increase of temperature, and the bearing capacity decreases gradually. When the temperature exceeds the glass transition temperature, the material becomes viscous material, basically losing its bearing capacity and having greater flexibility. At 40°C, the peak pressure decreases by about 200N with each 10% increase in the proportion of soft phase, and the overall change tends to be linear. Under the condition of 60°C, the ratio of soft and hard phases has an obvious influence on the reaction force of the indenter, and the variation range is from 100N to 1400N. When the proportion of soft phase increases from 10% to 20%, the peak pressure decreases by 1000N, and the bearing capacity of the whole structure suddenly decreases. This shows that hard phase materials also lose their bearing capacity due to their variable stiffness characteristics at high temperatures. It can be seen from that the smaller the proportion of soft phase, the greater the impact of temperature on the overall peak pressure. This is because the elastic modulus of hard phase materials is significantly affected by temperature, so the higher the proportion of hard phase, the greater the impact of temperature on the overall bearing capacity. When the proportion of soft phase is 50%, the peak pressure changes little, and the overall structural bearing capacity is poor.
Figure 6. Preparation and adjustment principle a-shaped memory polymer: (a) VeroWhite DMA curve; (b) 3D printing variable material; (c) variable stiffness function; (d) shape memory function.
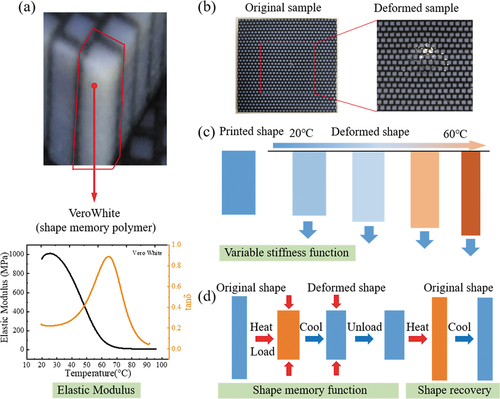
Figure 7. Force-displacement curves of at different temperatures: (a) 20°C; (b) 40°C; (c) 60°C; (d) peak pressure temperature curve.
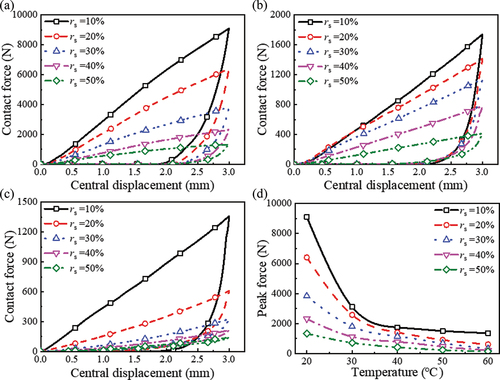
It can be seen from that at the room temperature of 20°C, the depth of the residual depression is 2 mm, and the overall recovery is only 1 mm, which is basically independent of the proportion of soft phase, which indicates that the shape memory material is not active at low temperature, and the shape memory effect is not obvious at lower temperature. However, in contrast, as the temperature rises to 40°C, the depth of residual depression decreases to 1.5 mm-2 mm, and the overall shape recovery reaches 50%. When the temperature rises to 60°C, the depth of the residual depression decreases to 0.5 mm-2 mm, indicating that when the temperature is 60°C, the overall shape recovers 2.5 mm, and the shape recovers to 83% of the original state. This is mainly because the temperature increases the activity of the molecular chain in the shape memory polymer, which makes the structure have a certain degree of shape memory effect after the indenter is lifted. When the proportion of soft phase is 10%, the shape memory effect at different temperatures is significantly different, because the hard phase material VeroWhite is a shape memory material with temperature-sensitive characteristics. Therefore, when the proportion of hard phase is high, the shape memory effect is obvious. As the proportion of soft phase increases, the proportion of hard phase decreases, and the overall shape memory effect decreases. However, by adding shape memory materials to it, it can be achieved that when the model is compressed and deformed, the deformed state of the bioinspired model can be restored to its original shape after heating.
3.4. Numerical simulation and validation
To further study the mechanical behavior of the bioinspired metamaterial under local compression, a model with a cell size of 2 mm and a soft phase ratio of 50% was used as a typical example for finite element simulation, and the model size was set to 32 mm × 32 mm × 8 mm. The simulation is carried out by the finite element analysis software ABAQUS. The metamaterials were meshed with four-node linear tetrahedron elements (C3D4). There are 31,030 nodes and 169,994 elements. First, as shown in , the model is imported, and the soft and hard phases are assembled in the assembly step, then they are merged into one entity, and the geometric boundary of the interface part is selected and kept, thus, the soft and hard phase materials can be endowed with material properties, respectively, in the attribute steps. The staggered distribution of soft and hard phase materials gives the two materials corresponding mechanical parameters. Then set the analysis step to 0.05 s, define the contact type as general contact and the contact attribute as hard contact. Set the boundary condition of the soft and hard phase materials to be fixed on the ground. The bioinspired metamaterials with adjustable soft and hard phases are modeled by Solidworks software and meshed in Hypermesh.
It can be seen from that the stress is mainly concentrated in the hard phase area in the bioinspired metamaterial, while the soft phase area is less loaded. The high-stress distribution of a single material model should be concentrated in the lower part of the indenter, and the farther away from the indenter, the smaller the stress. cuts along different cross-sections, it can be seen that the hard phase material plays the main supporting role, and the deformation is small after compression. In contrast, the soft phase material has a larger deformation and serves as a buffer. It makes the deformation range smaller, and the deformation variable is also smaller. According to the experimental data and simulation data under the same conditions, the force-displacement curve is obtained, and the finite element results are compared with the experimental results in . The results have good consistency, which indicates that the finite element results are reliable.
4. Vibration isolation performance
4.1. Vibration isolation tests
With the rapid development of automobile and aviation industries, the industry has higher and higher requirements for the vibration isolation performance of materials. The reduction of vibration and noise is an important goal for material performance optimization. This paper studies the vibration isolation performance of the bioinspired metamaterial with adjustable soft and hard phases through a self-made vibration and noise test system, as shown in .
Figure 12. Vibration isolation testing device and load input. (a) and (b) Vibration test bench; (c) amplitude time curve.
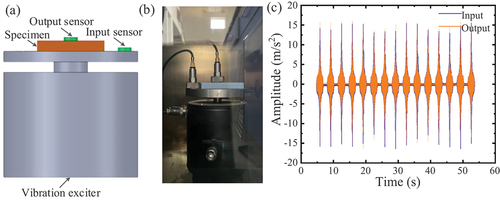
As shown in , the metamaterial is placed on the vibrating table, while the vibration exciter is located under the metamaterial to generate the vibration load. After the load generated by the exciter is transferred to the metamaterial, the acceleration amplitude (aoutput) can be measured by the output sensor on the top. An input sensor is connected to the vibration table to measure the acceleration amplitude of the input signal (ainput). Both the input and output signals will be recorded and transmitted to the computer. As shown in , the input and output vibration amplitude changes with time and frequency at 30°C. Calculate the vibration level difference (VLD) to characterize the pros and cons of the metamaterial’s vibration isolation performance.
4.2. Evaluation of vibration isolation performance
It can be observed from that the VLD of 0–25 Hz is negative for the metamaterial whose soft phase accounts for 20% under the condition of 30°C. That is to say, within this vibration frequency, the amplitude of the vibration acceleration is significantly reduced after the metamaterial is vibration-isolated. It shows that this metamaterial has excellent vibration isolation performance at low frequencies. When the frequency increased to 25 Hz, the VLD increases as the frequency increases, and reaches a resonance peak around 30 Hz, and then gradually decreases. In contrast, at 30 degree Celsius, the metamaterial with 40% of the soft phase has a negative VLD at 0–24 Hz, which has a better vibration isolation effect. At the same time, the resonance peak is reached at 25 Hz, and then after a slight fluctuation, it begins to decrease to a negative value at 40 Hz and continues to 75 Hz. This shows that the metamaterial whose soft phase accounts for 40% is very effective in low-frequency vibration isolation. It can be seen from that the vibration isolation effect of the metamaterial with a soft phase ratio of 40% is also different at different temperatures. As the temperature rises, the vibration isolation effect gradually increases. This also shows that metamaterials can achieve temperature-adjustable vibration isolation effects. During use, we can adjust the temperature according to the desired vibration isolation strength to achieve adjustable vibration isolation effects.
Figure 13. Vibration isolation experiment results: (a) soft phase accounted for 20% and 40% at 30°C VLD frequency curve; (b) soft phase accounted for 40% VLD frequency curve at different temperatures.
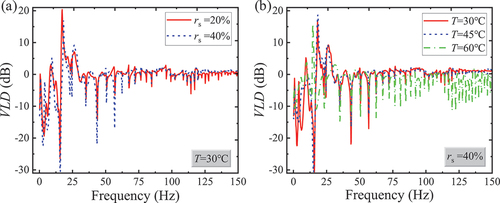
In comparison, the traditional vibration isolation material VLD increases as the frequency increases. After reaching the resonance frequency, it decreases to a negative value, which means that there is no low-frequency vibration isolation effect. For example, if a spring wants to achieve low-frequency vibration isolation, it needs to change its stiffness and damping properties. However, metamaterials can achieve VLD with a negative value in the low-frequency region before resonance, which means that the vibration isolation effect can be achieved before and after resonance, and there is no need to change any inherent characteristics such as strength and damping. The metamaterials that combine intelligent and bioinspired soft and hard materials will have broad development prospects in the automotive and aviation industries.
5. Conclusions
In this research, we designed an intelligent bioinspired metamaterial based on 4D printing. The corresponding mechanical properties, mechanical behaviors, and vibration isolation capabilities are studied. Main conclusions of this research are summarized as follows:
4D printed bioinspired metamaterials have the functions of shape memory and shape automatic recovery, which can be automatically recovered by changing the temperature after being deformed under pressure. After changing the temperature, it can change its own stiffness to realize adjustable stiffness. When the temperature changes by 30 degrees, the modulus changes by more than 40 times.
Cell size has different effects on the properties of bioinspired metamaterials. In the case of the same soft and hard ratio, the smaller the cell size, the greater the indenter reaction force that compresses the same distance. By changing the cell size and the ratio of soft and hard, the compression reaction force can be adjusted between 2kN and 5kN. It is of great significance for the design of equipment for manufacturing different bearing capacities.
The mechanical properties of the bioinspired metamaterial can be adjustable by changing the temperature. Under the condition of compressing the same distance, the lower the proportion of the soft phase of the material at the same temperature, the greater the indenter reaction force; the higher the temperature under the same condition of the proportion of the soft phase, the smaller the indenter reaction force. The indenter reaction force can be adjusted between 2kN and 5kN by controlling the temperature, and the shape recovery can be up to 80% by changing the temperature after compression.
The bioinspired metamaterial can realize the VLD with a negative value in the low-frequency region before resonance, which means that the vibration isolation effect can be achieved before and after resonance, and it has excellent low-frequency vibration isolation ability and does not need to change any inherent characteristics such as strength and damping. In addition, the vibration isolation performance of the bioinspired metamaterials can also be adjusted by changing the temperature and the soft phase ratio to achieve temperature-driven intelligent adjustment.
Acknowledgments
The authors would like to thank the support from National Natural Science Foundation of China under Grant No. 52225108, 12202065, and 52171290.
Disclosure statement
No potential conflict of interest was reported by the authors.
Data availability statement
Data will be made available on request.
Additional information
Funding
References
- Yu X, Zhou J, Liang H, et al. Mechanical metamaterials associated with stiffness, rigidity and compressibility: a brief review. Pro Mater Sci. 2018;94:114–173.
- Duan S, Wen W, Fang D. A predictive micropolar continuum model for a novel three-dimensional chiral lattice with size effect and tension-twist coupling behavior. J Mech Phys Solids. 2018;121:23–46.
- Coulais C, Teomy E, de Reus K, et al. Combinatorial design of textured mechanical metamaterials. Nature. 2016;535(7613):529–532. DOI:10.1038/nature18960
- Fu M, Liu F, Hu L. A novel category of 3D chiral material with negative Poisson’s ratio. Compos Sci Technol. 2018;160:111–118.
- K DK, Attard D, Caruana-Gauci R, et al. Unimode metamaterials exhibiting negative linear compressibility and negative thermal expansion. Smart Mater Struct. 2016;25(2):025009. DOI:10.1088/0964-1726/25/2/025009
- Cao X, Huang Z, He C, et al. In-situ synchrotron X-ray tomography investigation of the imperfect smooth-shell cylinder structure. Compos Struct. 2021;267:267.
- Mizzi L, M ME, Titov K, et al. Mechanical metamaterials with star-shaped pores exhibiting negative and zero Poisson’s ratio. Mater Design. 2018;146:28–37.
- Yu J. State-of-art of compliant mechanisms and their applications. J Mech Eng. 2015;51(13):53.
- Rossiter J, Takashima K, Scarpa F, et al. Shape memory polymer hexachiral auxetic structures with tunable stiffness. Smart Mater Struct. 2014;23(4):045007. DOI:10.1088/0964-1726/23/4/045007
- Gong X, Huang J, Scarpa F, et al. Zero Poisson’s ratio cellular structure for two-dimensional morphing applications. Compos Struct. 2015;134:384–392.
- Liu K, Han L, Hu W, et al. 4D printed zero Poisson’s ratio metamaterial with switching function of mechanical and vibration isolation performance. Mater Design. 2020;196:196.
- Bodaghi M, Liao WH. 4D printed tunable mechanical metamaterials with shape memory operations. Smart Mater Struct. 2019;28(4):045019.
- Shelby RAJE, Smith DR, Schultz S. Experimental verification of a negative index of refraction. Science. 2001;292(5514):77–79.
- Van LT, Ghazlan A, Ngo T, et al. A comprehensive review of selected biological armor systems – from structure-function to bio-mimetic techniques. Composite Structures. 2019;225:225.
- Studart AR. Towards high-performance bioinspired composites. Adv Mater. 2012;24(37):5024–5044.
- G WU, Bai H, Saiz E, et al. Bioinspired structural materials. Nat Mater. 2015;14(1):23–36. DOI:10.1038/nmat4089
- Ghazlan A, Ngo T, Tan P, et al. Inspiration from Nature’s body armours – a review of biological and bioinspired composites. Composites. 2021;205:205.
- A F-JE, Shen L, Guiamatsia I, et al. A numerical study of bioinspired nacre-like composite plates under blast loading. Compos Struct. 2015;126:329–336.
- Zhu D, Szewciw L, Vernerey F, et al. Puncture resistance of the scaled skin from striped bass: collective mechanisms and inspiration for new flexible armor designs. J Mech Behav Biomed Mater. 2013;24:30–40.
- Yang W, H CI, Gludovatz B, et al. Natural flexible dermal armor. Adv Mater. 2013;25(1):31–48. DOI:10.1002/adma.201202713
- Ha NS, Lu G. A review of recent research on bio-inspired structures and materials for energy absorption applications. Composites. 2020;181:181.
- Wang Y, Naleway SE, Wang B. Biological and bioinspired materials: structure leading to functional and mechanical performance. Bioact Mater. 2020;5(4):745–757.
- Yin S, Yang R, Huang Y, et al. Toughening mechanism of coelacanth-fish-inspired double-helicoidal composites. Compos Sci Technol. 2021;205:205.
- Barthelat F, Tang H, Zavattieri P, et al. On the mechanics of mother-of-pearl: a key feature in the material hierarchical structure. J Mech Phys Solids. 2007;55(2):306–337. DOI:10.1016/j.jmps.2006.07.007
- Gu GX, Takaffoli M, Buehler MJ. Hierarchically enhanced impact resistance of bioinspired composites. Adv Mater. 2017;29(28):1700060.
- Greco F, Leonetti L, De Maio U, et al. Macro- and micro-instabilities in incompressible bioinspired composite materials with nacre-like microstructure. Compos Struct. 2021;269:269.
- Kuhn-Spearing LT, Kessler, H., Chateau, E., Ballarini, R., Heuer, A. H., & Spearing, S. M. Fracture mechanisms of the Strombus gigas conch shell: implications for the design of brittle laminates. J Mater Sci. 1996;31(24):6583–6594. DOI:10.1007/BF00356266
- Yamamoto N, Gdoutos E, Toda R, et al. Thin films with ultra-low thermal expansion. Adv Mater. 2014;26(19):3076–3080. DOI:10.1002/adma.201304997
- Zhang Q, Guo D, Hu G. Tailored mechanical metamaterials with programmable quasi‐zero‐stiffness features for full‐band vibration isolation. Adv Funct Mater. 2021;31(33):2101428.
- Alshaqaq M, Erturk A. Graded multifunctional piezoelectric metastructures for wideband vibration attenuation and energy harvesting. Smart Mater Struct. 2021;30(1):015029.
- Cao X, Jiang Y, Zhao T, et al. Compression experiment and numerical evaluation on mechanical responses of the lattice structures with stochastic geometric defects originated from additive-manufacturing. Composites Part B: Engineering, 2020, 194.
- Zhao W, Liu L, Zhang F, et al. Shape memory polymers and their composites in biomedical applications. Mater Sci Eng C Mater Biol Appl. 2019;97:864–883.
- Wang Z, Yuan X, Yang J, et al. 3D-printed flexible, Ag-coated PNN-PZT ceramic-polymer grid-composite for electromechanical energy conversion. Nano Energy. 2020;73:73.
- Hamidi A, Tadesse Y. Single step 3D printing of bioinspired structures via metal reinforced thermoplastic and highly stretchable elastomer. Compos Struct. 2019;210:250–261.
- Wei Y-L, Yang Q-S, Ma L-H, et al. Design and analysis of 2D/3D negative hydration expansion metamaterial driven by hydrogel. Mater Design. 2020;196:196.
- Zhen D, Yuan, Chao C, et al. Direct 4D printing via active composite materials. Sci Adv. 2017;3(4).
- Wu W, Geng L, Niu Y, et al. Compression twist deformation of novel tetrachiral architected cylindrical tube inspired by towel gourd tendrils. Extreme Mech Lett. 2018;20:104–111.
- Hu W, Ren Z, Wan Z, et al. Deformation behavior and band gap switching function of 4D printed multi-stable metamaterials. Mater Design. 2021;200:200.
- Cui H, Hensleigh R, Yao D, et al. Three-dimensional printing of piezoelectric materials with designed anisotropy and directional response. Nat Mater. 2019;18(3):234–241. DOI:10.1038/s41563-018-0268-1
- P SA, Marciniak S, O’Dea A, et al. Modern, archaeological, and paleontological DNA analysis of a human-harvested marine gastropod (Strombus pugilis) from Caribbean panama. Mol Ecol Resour. 2021;21(5):1517–1528. DOI:10.1111/1755-0998.13361