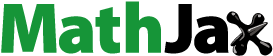
ABSTRACT
Self-healing materials span diverse application fields, including flexible electronics, soft robotics, and energy devices. However, conventional self-healing materials pose a challenge in achieving the delicate balance between flexibility and electrical conductivity. Moreover, they also suffer from prolonged healing times, incomplete healing, and high manufacturing costs. Liquid metals possess excellent self-healing capabilities owing to their unique combination of fluidic and metallic properties, high surface tension, and reversible solid-liquid phase change at room temperature, offering an intriguing material option for addressing the challenges associated with flexibility and electrical conductivity. In this review article, we comprehensively examine the domain of self-healing liquid metals from the standpoint of typical mechanisms underlying self-healing processes, as well as practical strategies employed for achieving such rejuvenation. Additionally, we explore representative applications that showcase the potential of these materials while aiming to provide a valuable reference for advancing and enhancing the field of self-healing materials. Future prospect along this direction is made.
KEYWORDS:
1. Introduction
Recently, the practical value of flexible electronic devices has been prominently highlighted alongside their emerging development requirements across various industries, including consumer electronics, biomedicine, clean energy, sports, and environmental sectors [Citation1–3]. These devices exhibit exceptional stability under severe test conditions, such as stretching, bending, rolling, twisting, wrinkling, or rubbing. This surpasses the capabilities of conventional rigid electronic devices composed of rigid inorganic materials [Citation4,Citation5]. However, although such remarkable features showcase diversified application potentials [Citation6–9], they also impose high demands on the durability of the materials used in device fabrication. Therefore, self-healing materials are beginning to make inroads into the field of flexible devices.
Self-healing materials belong to intelligent materials that possess the remarkable capability to fully or partially restore functionality upon encountering damage, drawing inspiration from the inherent self-healing ability observed in living organisms. Presently, self-healing materials encompass a diverse range of types, including polymers or their composites [Citation10–12], metals [Citation13–17], ceramics [Citation18–20], concrete [Citation21–25], etc. Despite the practical success achieved by these self-healing materials, they still encounter several challenges such as a relatively sluggish healing rate, difficulties in achieving full recovery, and high preparation costs. Moreover, most existing self-healing materials lack the conductivity required by flexible electronic devices, whereas conductive metallic self-healing materials fail to provide adequate flexibility. Consequently, discovering novel self-healing materials and improving existing ones remains a crucial focus of ongoing research.
Against this backdrop, self-healing liquid metals (LMs) have emerged as an appealing choice. Their unique combination of fluidic and metallic properties renders them highly suitable for applications that require both flexibility and electrical conductivity. Among the developed LM material systems, gallium-based (Ga-based) and bismuth-based (Bi-based) LMs own unparalleled advantages in terms of their fluidity, stretchability, and malleability under ambient conditions. For instance, pure Ga exhibits a high boiling point and maintains its liquid state from nearly ambient temperature (with a melting point at 29.7 °C) up to approximately 2403°C. As such, they are widely used for functional restorations in the fields of flexible electronics, soft robotics, self-healing batteries, and so on. Metals such as francium (Fr), cesium (Cs), sodium (Na), potassium (K), rubidium (Rb), and mercury (Hg) are also classified as LMs. However, certain limitations restrict their widespread application in specific areas. For example, the radioactivity of Fr and Cs poses concerns, while Na, K, and Rb exhibit extreme instability, and Hg is known for its toxicity. Notably, the self-healing advantages of LM primarily stem from their fluidity and high electrical conductivity, which render them superior to other self-healing materials in the realm of flexible electronics. However, this does not imply that LMs are universally optimal for all scenarios. The usability of LM may be constrained by their melting points (see in Section 2 Fundamental self-healing mechanisms and practical strategies) due to the solidification and loss of fluidity at low temperatures. This significantly restricts their self-healing performance, allowing only specific self-healing strategies in a few low-temperature applications (see Section 2.2 Volume expansion enabled self-healing for details). This highlights the concept of complementarity: while LMs excel in certain applications, other self-healing materials may be better suited for different purposes.
Table 1. Typical LMs with self-healing capabilities and their physical properties.
Considering the adaptability and safety of LMs, this review mainly focuses on the representative Ga-based LMs and Bi-based alloys. The LM possesses excellent self-healing capabilities within the realm of flexible electronic devices due to their distinctive physicochemical properties as well as the modulation and application of these properties. Here, we comprehensively review the self-healing LMs from the perspective of typical self-healing mechanisms, practical self-healing strategies, and representative applications. The subsequent sections are structured as follows: Section 2 provides a concise overview of the capabilities of typical LM materials while proposing three self-healing mechanisms, and evaluates dynamic external field stimulation and composites comprising LM materials as highly effective self-healing strategies; Section 3 demonstrates the typical applications of current self-healing LM materials; Section 4 sheds light on their challenges and prospects for future advancements.
2. Fundamental self-healing mechanisms and practical strategies
The unique self-healing capabilities of LMs arise from their distinct physical and chemical properties. Currently, three fundamental mechanisms have been developed to achieve the self-healing capabilities of LMs based on their unique properties (), namely droplet coalescence (), volume expansion (), and chemical crosslinking (). In the following section, we provide a detailed introduction to each of these mechanisms along with their underlying practical self-healing strategies. The typical LMs that feature self-healing capabilities are showcased in , which is arranged in ascending order of melting point of LMs.
Figure 1. Three fundamental self-healing mechanisms for LMs. A. Droplet coalescence mechanism. Oscillating coalescence of two identical LM droplets in a NaOH solution. Reproduced with permission from ref [Citation30]. Copyright 2015, science china press. B. Volume expansion mechanism. (a) Schematic of the conductivity self-healing induced by volume expansion of LMs; (b) the distance between two LM droplets decreases due to their volume expansion. Reproduced with permission from ref [Citation31]. Copyright 2019, royal society of chemistry. C. Various binding of LM and its derivatives to chemical groups in polymers: (a) –OH [Citation32]; (b) –NH2 [Citation33]; (c) polysulfide loops (R–sn–R) and thiol terminal groups (R–SH) [Citation34]; (d) –COOH [Citation35]; (e) polyphenol [Citation36].
![Figure 1. Three fundamental self-healing mechanisms for LMs. A. Droplet coalescence mechanism. Oscillating coalescence of two identical LM droplets in a NaOH solution. Reproduced with permission from ref [Citation30]. Copyright 2015, science china press. B. Volume expansion mechanism. (a) Schematic of the conductivity self-healing induced by volume expansion of LMs; (b) the distance between two LM droplets decreases due to their volume expansion. Reproduced with permission from ref [Citation31]. Copyright 2019, royal society of chemistry. C. Various binding of LM and its derivatives to chemical groups in polymers: (a) –OH [Citation32]; (b) –NH2 [Citation33]; (c) polysulfide loops (R–sn–R) and thiol terminal groups (R–SH) [Citation34]; (d) –COOH [Citation35]; (e) polyphenol [Citation36].](/cms/asset/92492eb7-8fcf-4674-9863-054ef66f982b/tsnm_a_2385349_f0001_c.jpg)
2.1. Droplet coalescence enabled self-healing
2.1.1. Droplet coalescence
LM droplets can be used to form conductive paths by mutual contact. However, when external stimuli damage the conductive path, the misalignment of the LM droplets prevents them from making contact with each other and thus inhibits current transfer. Droplet coalescence serves as a fundamental, convenient and efficient mechanism for the self-healing of LMs, facilitating their natural migration without requiring external intervention once merging is initiated. depicts the droplet coalescence process of LMs. As the distance between two droplets approaches the atomic scale, the liquid film on the surface of the droplets begins to break down and coalesce, forming a growing liquid bridge. It is evident that periodic oscillations occur between the droplets in both the x and y directions. The free oscillation period T can be described by Equation (1), where it is related to droplet density ρ, diameter d, surface tension σ [Citation37]:
Furthermore, the influence of viscous dissipation on the oscillation period is typically determined through curve fitting [Citation38]. As the oscillation period decreases, there is a corresponding increase in droplet coalescence rate. According to EquationEquation (1)(1)
(1) , a higher surface tension and a smaller droplet size can facilitate the coalescence effect. Experimental evidence [Citation39] has disclosed that droplet coalescence is primarily governed by surface tension. As shown in , the surface tension of typical LM surpasses that of water by many times. For instance, Ga demonstrates a surface tension of 0.707 N/m, approximately ten times greater than that of water. The large surface tension exhibited by LMs endows them with remarkable coalescing capabilities, thereby enabling their self-healing potential through droplet coalescence.
Apart from surface tension, many other factors influence the process of droplet coalescence, including viscous forces, geometric parameters [Citation30], surface charge [Citation40,Citation41], temperature [Citation42], and surface wettability [Citation43]. Additionally, the location of the droplet also influences the behavior of droplet coalescence [Citation44]. In a novel approach, Li et al. [Citation44] employed molecular dynamics simulation to investigate the coalescence of nano-droplets on a graphene nanoribbon-decorated stripe substrate. Based on this study, they devised a stripe surface with gradient intervals, thereby effectively controlling the coalescence behavior.
Notably, the droplet coalescence mechanism of LM may be restrained by the surficial oxide layer. Unlike conventional droplets, the LMs oxidize rapidly and spontaneously when they are exposed to a certain concentration of oxygen, forming an oxide layer that is capable of adsorbing foreign matters (e.g. water, organic molecules, particulate matter, etc.), which may restrain the droplet coalescence [Citation45]. Consequently, it is necessary to isolate LM from oxygen to mitigate the effects of the oxide layer. However, preventing oxidation of LMs poses challenges as they only exhibit liquid behavior when maintained at an oxygen concentration of 1 part per million (ppm) [Citation46]. In practical trials, to further improve the adaptability of droplet coalescence-enabled self-healing, the droplet coalescence mechanism is usually triggered by mechanical stimulation or applying external fields, to achieve the healing on demand. For instance, mechanical stimulation can disrupt the surface oxide layer, while electric fields, magnetic fields, or acoustic fields can intelligently manipulate dispersed LM droplets and facilitate their coalescence for restoring functionality as needed. The following part of this subsection describes the specific methods.
2.1.2. Contact stimulation induced droplet coalescence
The efficacy of contact stimulation in inducing coalescence for LMs has been empirically demonstrated by mechanical stimulation. When the device sustains damage such as punctures, tears or cuts, the LMs can effectively reconnect through droplet coalescence triggered by mechanical stimulation, thereby achieving functional healing.
Generally, mechanical stimulation can effectively address various sizes of LMs ranging from micro-/nanoparticles to macro-droplets. Tutika et al. [Citation47] fabricated reconfigurable and recyclable soft electronics with self-healing composites, which are composed of elastomer matrix and discrete micron-sized LM droplets with a diameter of 27.8 ± 7.7 μm. By using an embossing technique, they achieve conductive LM networks on demand (). Kramer’s team [Citation48] introduced the ‘mechanical sintering’ strategy, applying pressure to rupture the oxide layer of LM nanoparticles and then release the LM. The local coalescence of LM nanoparticles triggered by mechanical stress is demonstrated in . With certain localized regions experiencing sufficient stress, a continuous liquid phase is formed (see top right detail in ) and the electrical property of LM nanoparticle film changes from non-conductive to conductive, while other regions endure lower levels of stress, maintaining the intact LM nanoparticles (see bottom right detail in ).
Figure 2. Cases of mechanical stimulation induced droplet coalescence for self-healing of LMs. A. Schematic to illustrate the embossing process of discrete insulated LM microdroplets in elastomer matrix to form a connected conductive network. Reproduced with permission from ref [Citation47]. Copyright 2021, nature publishing group. B. SEM image to display local mechanical sintering of LM (EGaIn) nanoparticles. Detailed views highlight the formation of liquid EGaIn during pressing (top-right) and intact nanoparticles (bottom-right). Reproduced with permission from ref [Citation48]. Copyright 2015, Wiley-Blackwell. C. Schematic diagram of disconnection and reconnection of a basic electronic circuit using self-healing wire, where EGaIn is injected into microchannels fabricated with self-healing polymers. Reproduced with permission from ref [Citation49]. Copyright 2013, Wiley-Blackwell. D. Schematic diagram of self-healing LM line patterned on paper substrate. Reproduced with permission from ref [Citation50]. Copyright 2018, Wiley-Blackwell. E. Schematic detailing the self-healing flexible conductive LM/ITO film using a synergistic mechanism of mechanical stimulation and the spontaneous capillary-induced core suction of LM droplets. Reproduced with permission from ref [Citation6]. Copyright 2019, MDPI (Basel, Switzerland). F. Schematic illustrating a self-healing multilayer electrical circuit, where the LM flows are released from microcapsules to the damaged area upon encountering a crack. Reproduced with permission from ref [Citation51]. Copyright 2012, Wiley-Blackwell. G. Schematic diagram depicting an autonomously electrically self-healing LM – elastomer composite. Inset: equivalent electrical circuit schematic. Reproduced with permission from ref [Citation52]. Copyright 2018, Springer nature.
![Figure 2. Cases of mechanical stimulation induced droplet coalescence for self-healing of LMs. A. Schematic to illustrate the embossing process of discrete insulated LM microdroplets in elastomer matrix to form a connected conductive network. Reproduced with permission from ref [Citation47]. Copyright 2021, nature publishing group. B. SEM image to display local mechanical sintering of LM (EGaIn) nanoparticles. Detailed views highlight the formation of liquid EGaIn during pressing (top-right) and intact nanoparticles (bottom-right). Reproduced with permission from ref [Citation48]. Copyright 2015, Wiley-Blackwell. C. Schematic diagram of disconnection and reconnection of a basic electronic circuit using self-healing wire, where EGaIn is injected into microchannels fabricated with self-healing polymers. Reproduced with permission from ref [Citation49]. Copyright 2013, Wiley-Blackwell. D. Schematic diagram of self-healing LM line patterned on paper substrate. Reproduced with permission from ref [Citation50]. Copyright 2018, Wiley-Blackwell. E. Schematic detailing the self-healing flexible conductive LM/ITO film using a synergistic mechanism of mechanical stimulation and the spontaneous capillary-induced core suction of LM droplets. Reproduced with permission from ref [Citation6]. Copyright 2019, MDPI (Basel, Switzerland). F. Schematic illustrating a self-healing multilayer electrical circuit, where the LM flows are released from microcapsules to the damaged area upon encountering a crack. Reproduced with permission from ref [Citation51]. Copyright 2012, Wiley-Blackwell. G. Schematic diagram depicting an autonomously electrically self-healing LM – elastomer composite. Inset: equivalent electrical circuit schematic. Reproduced with permission from ref [Citation52]. Copyright 2018, Springer nature.](/cms/asset/ee6caeb4-ec28-4107-88aa-96bc9b14ca09/tsnm_a_2385349_f0002_c.jpg)
Undoubtedly, mechanical sintering is an efficient repair strategy due to its simplistic structural design suitability for selectively repairing damage. Palleau et al. [Citation49] successfully fabricated self-healing wires by injecting EGaIn into microchannels composed of self-healing polymers (). When the wire is pulled off, the LM rapidly forms an oxide layer at the broken cross-section, effectively preventing LM leakage. By squeezing the disconnected wires together, the oxide layer can be destroyed, facilitating the coalescence of LM droplets and restoration of conductivity. For the circumstance, where the LMs are patterned as self-healing circuits in soft substrates, such as paper [Citation50], polydimethylsiloxane (PDMS) [Citation53], and hydrogel [Citation32], the disconnected circuit can also be restored through the application of pressure on the LM, inducing mechanical sintering for droplet coalescence (). However, achieving precise alignment of wire interfaces poses challenges for miniature circuits. Synergistic with mechanical stimulation, the layer structured composite LM/ITO film effectively restores conductivity by the spontaneous capillary-induced core suction of LM droplets into cracks or defects in ITO film, thereby repairing their conductivity [Citation6], as shown in .
In addition to addressing the circuits of filling, patterning, and coating LMs, mechanical stimulation also offers a versatile approach for tackling diverse configurations of LM circuits encompassing encapsulated LMs and embedded LMs, thereby facilitating timely and on-demand self-healing processes. In this scenario, LMs are encapsulated in shells such as reaction products of urea and formaldehyde [Citation51], Ga2O3 shells [Citation54], nanosilver shells [Citation55], fatty acid shells [Citation56], etc. When external stresses cause the shell to rupture, the released LMs fill the cracked damage and restore the electrical conductivity (). Such an approach may achieve a rapid self-healing response; however, long-term stability cannot be guaranteed due to the limited quantity of microcapsules. Additionally, Markvicka et al. [Citation52] introduced a material structure comprising LM particles (LMPs) suspended in a soft elastomer. The LMPs near damaged sites exhibit a tendency to bind with neighboring particles (), facilitating reconfiguration of conductive traces that enable uninterrupted transmission of electrical signals even when the traces are mechanically damaged. Notably, in order to achieve this self-repairing functionality, it is necessary to maintain a relatively high volume fraction of the LM (typically ≥50%), which also implies a higher consumption of LM. This aspect somewhat restricts their potential applications. Moreover, if two wires are in close proximity, the self-repair process may lead to a short circuit.
2.1.3. Remote stimulation-induced droplet coalescence
Implementing the droplet coalescence through mechanical stimulation to achieve self-healing of LM is simple and efficient. However, in complex scenarios where conducting contact stimulation is challenging, remote self-healing would be a preferable alternative that can be achieved through the utilization of external fields, such as magnetic field, thermal field, acoustic field, and electric field.
Magnetic Field. The LM itself is not magnetic, but the introduction of magnetic particles such as Ni [Citation57,Citation58], Fe [Citation59], and carbon steel [Citation60] into the LMs enables flow control under a magnetic field. As shown in Ma et al. [Citation57] successfully manipulated the surface deformation and movement of Ni-doped LM droplets by applying a magnetic field. Based on these characteristics, the self-healing principle relying on a magnetic field can be summarized as follows: guiding the flow of LM in each region using a magnetic field (), thereby facilitating the re-aggregation of damaged areas for electrical self-healing. The LM droplet coalescence triggered by magnetic fields offers several advantages: (1) The magnetically doped LM can respond rapidly to the magnetic field and enable self-healing of the LM within a short duration of 10 s [Citation59]. (2) This non-contact self-healing mechanism is suitable for diverse complex applications and can be performed remotely. (3) The magnetic field features high efficiency, enabling precise manipulation over small-sized LMs and facilitating more application scenarios [Citation59].
Figure 3. Four remote stimulation induced droplet coalescence for self-healing of LMs. A. Magnetic field induced self-healing: (a) photographs depicting contact angle before and after applying magnetic field and obliquity tests with magnetic field) of LM on paper; (b) schematic illustrating the healing mechanism of Fe-EGaIn electronics facilitated via magnetic field. (a) and (b) reproduced with permission from ref [Citation57]. And ref [Citation59], respectively. Copyright 2019, Wiley-VCH Verlag. B. Thermal field induced self-healing: photographs depicting the heat-triggered self-healing for LM-elastomer composite. Reproduced with permission from ref [Citation61]. Copyright 2016, Wiley-Blackwell. C. Acoustic field induced self-healing: schematic demonstrating the synthesis of highly conductive LM nanoparticles network in acoustic field. Reproduced with permission from ref [Citation62]. Copyright 2022, American association for the advancement of science. D. Electric field induced self-healing: In-plane self-healing capability of LM electrodes induced by electrostatic attraction forces at boundaries. Reproduced with permission from ref [Citation63]. Copyright 2013, American Institute of Physics.
![Figure 3. Four remote stimulation induced droplet coalescence for self-healing of LMs. A. Magnetic field induced self-healing: (a) photographs depicting contact angle before and after applying magnetic field and obliquity tests with magnetic field) of LM on paper; (b) schematic illustrating the healing mechanism of Fe-EGaIn electronics facilitated via magnetic field. (a) and (b) reproduced with permission from ref [Citation57]. And ref [Citation59], respectively. Copyright 2019, Wiley-VCH Verlag. B. Thermal field induced self-healing: photographs depicting the heat-triggered self-healing for LM-elastomer composite. Reproduced with permission from ref [Citation61]. Copyright 2016, Wiley-Blackwell. C. Acoustic field induced self-healing: schematic demonstrating the synthesis of highly conductive LM nanoparticles network in acoustic field. Reproduced with permission from ref [Citation62]. Copyright 2022, American association for the advancement of science. D. Electric field induced self-healing: In-plane self-healing capability of LM electrodes induced by electrostatic attraction forces at boundaries. Reproduced with permission from ref [Citation63]. Copyright 2013, American Institute of Physics.](/cms/asset/0746d6b3-79da-47b5-8509-a6f2e1319c91/tsnm_a_2385349_f0003_c.jpg)
Currently, the magnetic field-induced droplet coalescence relies on several factors. For instance, the movement path and rate of the magnetic LM droplet are directly determined by the strength and orientation of the magnetic field. Another crucial factor lies in the distribution and content of the magnetic particles within the LM, which not only determines how sensitive a droplet is to changes in magnetic fields but also affects its response speed. These various factors pose challenges in achieving precise control over the motion and direction of LM droplets. Firstly, it is difficult to realize precise control of magnetic field in complex environments with multiple electromagnetic interferences. Secondly, it is essential to consider the material’s magnetic stability and potential degradation to ensure the long-term efficacy and reliability of the system. Besides, more attention should be paid to the environmental factors such as the medium and temperature variations, which can affect the surface tension and viscosity of the LM, thereby influencing its movement. Furthermore, the interaction between the LM and magnetic particles should be strong enough to drive the droplet while avoiding breakage or unwanted chemical reactions. In general, the interaction between LM and magnetic particles is typically achieved through two distinct mechanisms: physical adhesion and metallic bonding. The former is achieved through a variety of methods, including mechanical stirring of LM and magnetic particles [Citation64,Citation65], rolling the oxidized LM on a bed of magnetic particles [Citation66,Citation67]. It should be noted that none of these methods produced intermetallic compounds. However, the LM can also facilitate the formation of intermetallic compounds with magnetic particles. For instance, Cui et al. [Citation68] prepared FeGa3 in direct contact with EGaInSn on a Fe substrate to enhance the interface wetting between LM and Fe, which is beneficial for magnetic field control and self-healing. The underlying mechanism can be attributed to the formation of an intermetallic compound, namely FeGa3, which is deposited on the surface of the Fe substrate. This results in the formation of a robust metal bond interaction with Ga atoms, thereby conferring excellent wettability [Citation69].
Overall, achieving precise control over LM droplets via magnetic field necessitates considering the magnetic field precision, particle interactions, magnetic degradation and environmental adaptations. Additionally, employing a digitally-controlled moving platform may offer an accurate means for manipulating magnets, thereby enhancing controllability over both path and speed during drop motion.
Thermal Field. The LMs can undergo a reversible solid-liquid phase change at room temperature. By providing a proper thermal field, they can easily transform a solid state into a fluid state that demonstrates capability in infiltrating cracks, voids, or other structural damages. Once the system heals the damage, the LMs can recrystallize with themselves to achieve self-healing for cracks. For instance, Van Meerbeek et al. [Citation61] employed the heat-triggered self-healing of eutectic Sn – Bi – In (Field’s metal) to repair damaged foam composites (). They cut the metal – elastomer-foam composite in half and rejoined them by only melting and refreezing Field’s metal. Although the elastomer foam does not rebound, the self-healed composite has an elastic modulus that is very close to that of a virgin sample. However, the effectiveness of such a self-healing strategy may be hindered by the heat transfer process with the environment, necessitating prolonged exposure to a thermal field for complete heating and cooling to ensure successful repair of the damaged area. Consequently, this leads to high energy consumption and low healing speed. Therefore, developing this strategy requires precise thermal control as well as intelligent structural design.
Acoustic Field. The acoustic field can promote the generation of smaller LM droplets on the surface of large LM droplets, and manipulate their movement, thereby enabling LM self-healing. However, when employing LM droplets in suspension within a carrier fluid, coalescence is often hindered by the presence of an oxide skin [Citation70], leading to suboptimal conductivity in fabricated structures. To address this issue, it is customary to break the oxide skin and reunite the droplets to establish functional conductive pathways [Citation71]. Lee et al. [Citation62] employed an acoustic field operating at a 20 kHz ultrasound frequency to integrate individual LM micro-droplets within a polymer matrix (). This approach induced the shedding of nano-sized droplets from the micro-droplets, forming a coherent interlinked chain structure that established robust electrical pathways without fusion or the necessity to remove oxide skins. Furthermore, even under mechanical strain, the configuration of microdroplet-nanodroplet exhibited remarkable resilience with maintained conductive properties and good self-healing properties. Utilizing an acoustic field for achieving self-healing of LM circuits can tackle the difficulties associated with manufacturing conductive circuits using LM polymers. Nevertheless, these composites encounter further obstacles during fabrication [Citation62,Citation72]. For instance, the sonication and stirring mixing process used to produce Ga LM micro-droplets in the carrier fluid often lacks precise control over droplet size which directly affects the electrical and mechanical properties of the composite.
Electric Field. The conductivity of LM enables self-healing via an electric field [Citation63], as depicted in . When LM electrode (a) is positively charged at 3.5 kV, the boundaries of LM electrode (b) will correspondingly acquire a negative charge, resulting in opposite charge distributions that induce mutual attraction between the boundaries. At the narrow end of these boundaries where charges converge and the distances are short, the attractive forces intensify, prompting LM to breach its thin layer of oxidation and merge. Once merged, they establish an electrical connection and form a new layer of oxidation to sustain this connection.
2.2. Volume expansion enabled self-healing
2.2.1. Volume expansion
The reversible phase transition of LM at room temperature enables a feasible and controllable self-healing mechanism by leveraging solely the volume changes during the melting-recrystallization process (). As depicted in , the distance between the LM droplets decreases after freezing, indicating expansion of LMs. Essentially, volumetric expansion enables LM to infiltrate the cracked areas, promoting reconnection and functional restoration [Citation31]. The volume expansion of LM during the phase transition can be calculated by the Equation (2):
where, VL and VS denote the volume of LM in the liquid and solid state, respectively; ρL and ρS represent the density in the liquid and solid state, respectively. The calculations demonstrate that gallium and bismuth are the sole metals exhibiting negative volume expansion, with specific values of − 3.05% and − 3.08%, respectively. This abnormal expansion is primarily attributed to the relatively diminutive interatomic distances of both gallium and bismuth in their liquid states. When these elements transition from a liquid state to a solid state, their interatomic arrangement becomes looser, resulting in volume expansion. By utilizing the volume expansion mechanism, it becomes feasible to create self-healing conductive paths using Ga-based and Bi-based LM droplets.
2.2.2. Phase transition induced reversible self-healing
In contrast to the self-healing process involving thermal field discussed in Section 2.1.3 Remote stimulation-induced droplet coalescence, where LM droplets irreversibly aggregate, the self-healing mechanism of LM droplets introduced in this section during solidification is characterized by reversibility. Specifically, as LMs cool and solidify, they expand in volume and come into contact with each other, creating conductive pathways without merging. Upon heating, these LMs contract and separate, disrupting the conductive pathways. Thus, the volume expansion during the self-healing process exhibits distinct reversible behavior.
Based on the reversible phase transition of gallium-based LMs, the present group successfully realized a reversible electrical transition between insulator and conductor in the LM-polymer composite by primarily leveraging their abnormal expanding behavior after freezing [Citation73], as depicted in . When the LM-polymer composite is frozen, the polymer changes into a rigid state while the LM droplets expand and connect with adjacent ones () [Citation74], thereby forming conductive paths. As a result, the LM-polymer composite exhibits conductivity with resistivity spanning more than 109 times), and then it recovers an insulated state after warming. Importantly, no structural damage or electrical degradation has been observed even after 100 cycles at extreme-low temperatures, since the solidified LM droplets would not merge.
Based on the above work, Chen et al. [Citation31] further developed a generalized way to make temperature tunable conductor-insulator transition with gallium-based and bismuth-based LM composites through freezing and thawing these LM droplets dispersed in dimethicone. Specifically, the solidified LM composites are in a conductive state at low temperatures, melting at high temperatures and transitioning to an insulating state. As demonstrated in , the resistance of LM composites decreases sharply at 229 K and finally reaches 1.29 × 10−5 Ω/m, followed by constant conductivity until reaching 180 K. Notably, such a reversible transition process demands low temperature and precise control, typically more than 60 K lower than room temperature, which may restrict its applicability. However, it presents promising potential in some specific scenarios, such as exploration of the polar regions on Earth or outer space.
To take advantage of the volume expansion properties of Ga-based and Bi-based LMs, the melting points of LMs can be determined, which represent the critical temperatures triggering volume expansion [Citation31]. As shown in , the melting points of both Ga-based and Bi-based LMs typically exceed 0°C (273.15 K). However, the liquid-solid transition temperature of LM micro-/nano-droplets becomes very low, due to that the nucleation sites for crystal formation reduce as well, rendering nucleation more arduous and resulting in an escalation of subcooling magnitude. illustrates the results obtained from differential scanning calorimeter (DSC) tests, revealing an exothermic peak at 227 K that signifies the transition of liquid LM nanoparticles into a solid phase during cooling. Notably, the diverse composition and abundant components of LMs will result in variations in their phase transition behavior and volume changes, thereby offering a wide range of material choices for self-healing processes based on volume expansion mechanisms.
Figure 4. Phase transition induced reversible self-healing. A. Insulation and conduction transition of a LM-polymer composite triggered by the phase change of LM droplets and the rigidity change of polymer. Reproduced with permission from ref [Citation73]. Copyright 2019, Wiley-Blackwell. B. Schematic of solidified LM droplets expanding and connecting with adjacent ones. Reproduced with permission from ref [Citation74]. Copyright 2020, Elsevier BV. C. Temperature tunable conductor-insulator transition of a LM-polymer composite. D. Differential scanning calorimeter tests reveal an exothermic peak at 227 K that signifies the transition of liquid LM nanoparticles. C and D were produced with permission from ref [Citation31]. Copyright 2019, royal society of Chemistry.
![Figure 4. Phase transition induced reversible self-healing. A. Insulation and conduction transition of a LM-polymer composite triggered by the phase change of LM droplets and the rigidity change of polymer. Reproduced with permission from ref [Citation73]. Copyright 2019, Wiley-Blackwell. B. Schematic of solidified LM droplets expanding and connecting with adjacent ones. Reproduced with permission from ref [Citation74]. Copyright 2020, Elsevier BV. C. Temperature tunable conductor-insulator transition of a LM-polymer composite. D. Differential scanning calorimeter tests reveal an exothermic peak at 227 K that signifies the transition of liquid LM nanoparticles. C and D were produced with permission from ref [Citation31]. Copyright 2019, royal society of Chemistry.](/cms/asset/d4a91de9-3503-43b0-99ed-e421c82ad330/tsnm_a_2385349_f0004_c.jpg)
2.3. Chemical crosslinking enabled self-healing
2.3.1. Chemical crosslinking
The aforementioned two self-healing mechanisms primarily rely on physical mechanisms, and some scholars also employ the chemical crosslinking to achieve the self-healing of LM-based composites [Citation75]. As mentioned before, LMs possess high reactivity and readily undergo chemical reactions with various substances. For instance, the Ga-based LMs can easily react with O2 and H+ to form the Ga oxide (Ga2O3) and ionic Ga3+ compounds [Citation32,Citation76]. Moreover, the Ga-based LMs and their derivatives can bind with different chemical groups, such as -OH, -NH2, -S-, -COOH, and polyphenol [Citation33,Citation36,Citation77–79]. Consequently, incorporating LMs into the polymer composite enhances the intricacy of reversible bonds within the network, thereby increasing the connection strength and enabling healing for composites. The chemical crosslinking mechanism is illustrated in , where LM plays a pivotal role in bonding diverse composites. Such a strategy further improves the adaptability and functionalization applications for self-healing LMs, endowing them with exceptional mechanical properties, significant electrical conductivity, and excellent self-healing ability.
2.3.2. Bonds in composites
In clinical medicine, sutures are frequently utilized to prevent wound eversion and secondary rupture, thereby facilitating improved repair outcomes and wound aesthetics () [Citation82]. Similarly, upon the LM composites sustain damage or cracks, LM and its derivatives can serve as sutures to bind the chemical groups presented in the polymer matrix [Citation80]. By leveraging its fluidity, LM drives bonding at the crack site, promoting crack polymerization and effectively stitching the cracks together, thus facilitating self-healing of the composites. Consequently, it is imperative to investigate methods for enhancing the affinity between LM and its composite materials.
Figure 5. Chemical crosslinking enabled self-healing in LM composites. A. Schematic of chemical crosslinking serving as sutures to achieve wound self-healing in LM composites. Reproduced with permission from ref [Citation80]. Copyright 2022, Elsevier. B. Self-healing scheme for LM-embedded sulfur polymer materials. Reproduced with permission from ref [Citation34]. Copyright 2019, Wiley-VCH Verlag. C. Design strategy (a) and self-healing mechanism (b) of supramolecular PAA – LM/rGO hydrogels. Reproduced with permission from ref [Citation35]. Copyright 2021, royal society of chemistry. D. Formation and reversible self-healing of PVA-LMPs hydrogel. Reproduced with permission from ref [Citation81]. Copyright 2019, American chemical society. E. Scheme illustrating the self-healing mechanism of magnetic PVA/EGaInSn–Ni hydrogel. Reproduced with permission from ref [Citation58]. Copyright 2023, Springer Singapore.
![Figure 5. Chemical crosslinking enabled self-healing in LM composites. A. Schematic of chemical crosslinking serving as sutures to achieve wound self-healing in LM composites. Reproduced with permission from ref [Citation80]. Copyright 2022, Elsevier. B. Self-healing scheme for LM-embedded sulfur polymer materials. Reproduced with permission from ref [Citation34]. Copyright 2019, Wiley-VCH Verlag. C. Design strategy (a) and self-healing mechanism (b) of supramolecular PAA – LM/rGO hydrogels. Reproduced with permission from ref [Citation35]. Copyright 2021, royal society of chemistry. D. Formation and reversible self-healing of PVA-LMPs hydrogel. Reproduced with permission from ref [Citation81]. Copyright 2019, American chemical society. E. Scheme illustrating the self-healing mechanism of magnetic PVA/EGaInSn–Ni hydrogel. Reproduced with permission from ref [Citation58]. Copyright 2023, Springer Singapore.](/cms/asset/1a2e7784-bf6b-4e7c-b255-360e8921ad74/tsnm_a_2385349_f0005_c.jpg)
The self-healing property, as depicted in , is partially attributed to the dynamic bonding between the LM and the sulfur polymer through -S-metal- bonds. Unlike previous studies that utilized solid metal nanoparticles [Citation83,Citation84], this work employs LM which offers greater fluidity for easier redistribution and reconnection to form conductive pathways during self-healing. This eliminates the need for tightly controlled concentrations of electrically conductive materials dependent on their state of dispersion and interaction with substrate material. Xu et al. [Citation85] employed sonication-assisted EGaIn to induce the polymerization of acrylic acid (AA), resulting in the formation of moldable and self-healing hydrogels via Ga3+ crosslinking. Zhang et al. [Citation35] successfully fabricated supramolecular poly (acrylic acid)-LM/reduced graphene oxide (PAA-LM/rGO) hydrogels with remarkable properties including self-healing, multisensory capabilities, and high stretchability (). In addition to AA, self-healing hydrogels can be generated through the sonication-induced polymerization of tannic acid (TA) [Citation86], or other materials in combination with EGaIn. As illustrated in , Liao et al. [Citation81] dispersed EGaIn’s LMPs into a borate-modified polyvinyl alcohol (PVA) polymer network to fabricate PVA-LMPS Hydrogel, which possesses the capability of self-healing and dissolvability for the development of skin sensors. Xin et al. [Citation34] achieved self-healing without the need for intricate structural designs by integrating LM with sulfur polymers. Previously, pure sulfur polymers required high-temperature annealing to achieve complete healing. This new combination successfully enables room-temperature self-healing within 24 h.
As shown in , Zhao et al. [Citation58] mixed EGaInSn suspension with Ni particles, PVA, and sodium tetraborate to produce PVA/EGaInSn-Ni composite. Borate molecules act as crosslinking agents through forming rich hydrogen bonds with PVA. Additionally, a thin oxide skin forms on the surface of Ga-based LM, resulting in secondary crosslinking with the PVA chain. The as-prepared PVA/EGaInSn-Ni hydrogel exhibits excellent self-healing ability, which is derived from abundant hydrogen bond sites. One of the key factors contributing to the self-healing properties of as-prepared hydrogels is the abundant molecular cross-linking sites facilitated by hydrogen bonding between the hydroxyl group of PVA chains and the metal oxide layer on LM surfaces, thereby enabling rapid repair following interconnection. In addition, the fluidity of the LM further promotes the cross-linking of the PVA hydrogels and enhances their self-healing capabilities.
Self-healing through chemical crosslinking holds considerable promise. The key role of chemical crosslinking in self-healing LM composites has been highlighted: by integrating LM with a polymer matrix containing different functional groups, a network structure capable of repairing itself after damage is formed. Building on relevant research findings in chemical crosslinking, LM can explore additional strategies to achieve more efficient and stable self-healing behavior.
Application of Molecular Dynamics Simulation [Citation87]: Molecular dynamics simulations can uncover the dynamic cross-linking mechanisms between LM and the polymer matrix, which are essential for the self-healing process. These simulations enable the optimization of cross-linking density and polymer chain fluidity, thereby improving the self-healing efficiency and mechanical properties of the material. Biologically Inspired Structural Design [Citation88]: Inspired by the structure of vascular smooth muscle, LM microdroplets can be engineered with a core-shell configuration. These droplets form a hierarchical structure within the composite material through chemical crosslinking, analogous to biological tissue. This design significantly enhances the fracture toughness and crack propagation resistance of the material. Multifunctional Optimization of Self-Healing Materials [Citation89]: Incorporating a self-creasing structure in polyaniline (PANI)-based hydrogels enhances mechanical properties and self-healing through chemical crosslinking, achieving high ductility and stability. These strategies can optimize liquid metal composites for improved self-healing efficiency and durability in dynamic environments, especially where high electrical or thermal conductivity is needed. Supramolecular Interface Assembly [Citation90]: The supramolecular assembly of layered structures enables room-temperature self-healing in soft composite materials, imparting high fracture toughness and exceptional resistance to crack propagation. By incorporating a specifically oriented reinforcement phase into the polymer matrix, this approach significantly enhances mechanical strength and durability, while maintaining efficient self-healing capabilities and favorable thermal conductivity. Applied to LM composites, careful regulation of the LM-polymer interface interaction enhances self-healing properties, offering valuable insights for advancing liquid metal composites in intelligent response and thermal management applications. Underwater self-healing achievement [Citation91]: To sustain material self-healing and mechanical stability in underwater or high-humidity environments, researchers devised a self-healing polymer with a water-resistant network structure using a targeted chemical cross-linking mechanism. This research not only advances understanding of LM self-healing mechanisms but also introduces new design principles and potential applications for developing robust LM self-healing materials capable of functioning reliably in harsh conditions.
The comparison of seven self-healing strategies for LMs is presented in , focusing on their response speed, degree of recovery, triggering condition, cycle life, process complexity, adaptability to the environment, and repair scope.
Table 2. Comparison of self-healing strategies for liquid metals.
3. Representative applications
3.1. Wearable device
LM self-healing materials demonstrate distinctive advantages in the domain of wearable devices, exhibiting a superior self-healing capacity in comparison to conventional materials. This capacity enables the LM to autonomously respond to damage, flow and fill cracks without the necessity for external repair, markedly enhancing the durability and reliability of the equipment. Furthermore, LM exhibits high conductivity and flexibility, enabling it to adapt to the body’s natural movement and shape changes while maintaining circuit integrity, a challenging feat to achieve with traditional hard or rigid materials. The combination of these self-healing properties with LM’s inherent electrical and thermal characteristics positions it as an ideal material for next-generation wearable devices. This has led to innovative applications in the field of wearable electronics, where LM’s ability to conform to the body and maintain functionality under dynamic conditions is particularly beneficial.
For instance, Guo et al. [Citation92] prepared a large area Cu-Ag-EGaIn circuit by heat transfer method, and printed a 12-lead ECG circuit on a knitted T-shirt for cardiac activity monitoring (, top-left). Tang et al. [Citation93] printed LM on sports T-shirts as interconnects to make highly integrated smart wearables (, top-right). These smart wearables are equipped with an electrophysiological sensor for electrocardiogram (ECG) detection, an electrochemical sensor for potassium ion detection, a strain sensor for motion detection, and a heating module for maintaining a constant body temperature.
Figure 6. Examples of LM wearable devices with self-healing functions. A. Clothes with integrated multiple sensors (top). Textile fibers containing LM (bottom). Top left image: reproduced with permission from ref [Citation92]. Copyright 2022, American Chemical Society. Top right image: reproduced with permission from ref [Citation93]. Copyright 2019, American Chemical Society. Bottom image: reproduced with permission from ref [Citation94]. Copyright 2023, Elsevier BV. B. LM-based exoskeleton fixator for joint protection. Reproduced with permission from ref [Citation95]. Copyright 2023, Wiley-VCH Verlag. C. Schematic of real-time EEG recording during sleep state. Reproduced with permission from ref [Citation96]. Copyright 2022, American Chemical Society. D. Images of a glove equipped with LM capacitive sensor network and EMG signal acquisition using LM electronic tattoo on the forearm. Reproduced with permission from ref [Citation97]. Copyright 2018, American Chemical Society. E. Palisade shape stretchable LM@PDMS heater for thermotherapy at knee. Reproduced with permission from ref [Citation98]. Copyright 2019, Wiley-Blackwell.
![Figure 6. Examples of LM wearable devices with self-healing functions. A. Clothes with integrated multiple sensors (top). Textile fibers containing LM (bottom). Top left image: reproduced with permission from ref [Citation92]. Copyright 2022, American Chemical Society. Top right image: reproduced with permission from ref [Citation93]. Copyright 2019, American Chemical Society. Bottom image: reproduced with permission from ref [Citation94]. Copyright 2023, Elsevier BV. B. LM-based exoskeleton fixator for joint protection. Reproduced with permission from ref [Citation95]. Copyright 2023, Wiley-VCH Verlag. C. Schematic of real-time EEG recording during sleep state. Reproduced with permission from ref [Citation96]. Copyright 2022, American Chemical Society. D. Images of a glove equipped with LM capacitive sensor network and EMG signal acquisition using LM electronic tattoo on the forearm. Reproduced with permission from ref [Citation97]. Copyright 2018, American Chemical Society. E. Palisade shape stretchable LM@PDMS heater for thermotherapy at knee. Reproduced with permission from ref [Citation98]. Copyright 2019, Wiley-Blackwell.](/cms/asset/65c93471-e0af-44a5-84e1-10e0d05a1545/tsnm_a_2385349_f0006_c.jpg)
In addition to printing LM on fabric, the LM can also be embedded in the fabric. As shown in , bottom, the LM-based double helix cored yarn proposed by Fu et al. [Citation94] can be mass-produced by simple friction-cored spinning for human motion monitoring, energy harvesting, and thermal management. Due to the stable double helix structure and layered structure, yarns and fabrics show the combined advantages of flexibility, air permeability and washable capabilities. Beyond the double helix structure, LM demonstrates versatility and self-healing capabilities in fabric sensors through various forms [Citation99]. As a coating [Citation100], LM particles are dipped and dried to form a conductive layer on fibers. In fiber form [Citation101], ultra-stretched fibers with high permeability and electrical stability are produced by combining electrospinning technology with LM. When used in fiber pads [Citation102], LM forms an elastic mesh structure on electrospun fiber pads, providing high conductivity and biocompatibility. These forms offer high electrical conductivity, self-healing ability, antibacterial properties, high permeability, and adaptability to dynamic deformation. However, they also present challenges such as oxidation, high costs, moisture sensitivity, and the need for additional packaging to enhance stability and durability.
Moreover, the wearable devices based on self-healing LMs also demonstrate significant potential in clinical applications. The LM-based exoskeleton fixators that are adaptable to all body parts, including feet, ankles, knees, waist, shoulder, head, and neck, have been successfully used in patients for various bone injury repair and bone support () [Citation95]. When the exoskeleton fixator is knocked and damaged, the internal LM can be heated to flow to heal the cracks, and the strength of the fixator can be restored after cooling down.
Furthermore, the self-healing LMs have been developed as multifunctional electronic skin (e-skin) to achieve the accurate recording of weak electroencephalogram (EEG) signal. As shown in , Li et al. [Citation96] reported a LM electrode, called kirigami structured LM paper (KLP), that is self-supporting, conductor exposed, stretchable, ultra-thin, and recyclable for multi-functional e-skin. When the electrode is damaged, it can be repaired easily by mechanical stimulation with external pressure. With its capability to function as an e-skin and acquire high-quality electrophysiological signals, the self-healing LM electrodes is anticipated to evolve into a versatile e-skin for healthcare monitoring and intelligent control. In addition to ECG and EEG monitoring, the self-healing LMs can also be used for EMG acquisition. The electronic tattoo [Citation97] utilizing Ag-In-Ga LM, as depicted in , exhibits high electrical conductivity and consistency over 3D surfaces. This tattoo can be easily placed on the human forearm via water printing the purpose of collecting EMG signals and then control a robotic hand prosthesis. Importantly, the self-healing of LMs improve the durability and adaptability between the device and the biological interface, thereby facilitating the acquisition of high-quality physiological information under dynamic conditions.
Besides applications in monitoring physiological signal, the self-healing LMs have also received attention as flexible heaters for wearable hyperthermia. Wang et al. [Citation98] reported a high-performance electrically driven heater using LM and PDMS conductive composite material, which was patterned into a sinusoidal structure using direct ink writing printing technology (). Generally, the wearable heaters require both high stretchability and stability to achieve thermal therapy of joints or muscles during dynamic exercise. The self-healing properties exhibited by LMs precisely offer the desired assurance for this purpose.
Despite the numerous advantages of LM self-healing materials, several challenges hinder their broader application. A primary issue is the relatively high cost, which may limit their market adoption. Furthermore, LM’s susceptibility to oxidation necessitates additional protective measures to preserve performance, thereby increasing manufacturing complexity and expenses. The inherent weight and volume of LM also pose concerns, as they may exceed those of lightweight alternatives, potentially impacting the comfort and user acceptance of wearable devices. Addressing these challenges is essential for the successful integration and commercial viability of LM self-healing technologies.
3.2. Self-healing battery
Lithium-ion batteries (LIBs) stand as one of the predominant offerings within the contemporary energy storage market. LIBs are usually composed of cathode, anode, electrolyte, diaphragm and packaging materials. Among these components, the electrode materials are extremely vulnerable to wear and tear, significantly affecting the life of the battery. There are three primary reasons for electrode damage: (1) During the cycling process of battery charging and discharging, the embedding/de-embedding of ions on the electrode induces volumetric expansion/contraction of the electrode. This uneven stress distribution on the electrode material leads to mechanical damage such as particle cracking, detachment, or structural loosening, ultimately resulting in mechanical and electrical failures of the battery; (2) In battery systems, extended charge and discharge cycles tend to promote the formation of dendrites on lithium metal negative electrodes. This phenomenon adversely affects the coulombic efficiency and cycle life of the battery, ultimately leading to a decline in cycle capacity; (3) In flexible devices where the battery utilizes flexible electrodes, mechanical stresses such as buckling, stretching, or compression may destruct of the electrode structure. These mechanical stresses may arise from various factors including physical battery operation and thermal expansion caused by temperature changes.
One of the principal operational scenarios for batteries is at room temperature. In comparison to traditional electrode materials, LM demonstrates exceptional mobility at this temperature, enabling the electrode to self-heal and effectively address the formation of cracks and voids during the battery cycling process. This intrinsic self-healing capability significantly enhances the cycle life of energy storage devices. Additionally, the incorporation of LM electrode material results in the formation of a liquid-liquid interface with the electrolyte, which plays a crucial role in suppressing dendrite formation. Furthermore, LM’s inherent high conductivity makes it an optimal candidate for battery electrodes. The following sections will explore specific application scenarios that highlight the unique advantages of LM as an electrode material.
Conventional liquid batteries typically operate at elevated temperatures due to the high melting point of electrode materials [Citation103], which may impose limitations on their widespread adoption. For instance, the liquid Li/Bi battery operates at 550°C [Citation104], while the Li/Sb-Sn liquid battery reaches temperatures as high as 500°C [Citation105]. Current research endeavors primarily focus on developing room temperature LM batteries. As shown in , Wu et al. [Citation106] utilized liquid Ga-Sn alloy at room temperature as a negative electrode, harnessing its fluidity and surface tension to mend crack damage during the cycle, exhibiting a theoretical specific capacity of approximately 795 mA·h/g (in comparison to graphite with a capacity of around 372 mA·h/g). The battery underwent 4000 cycles at 4000 mA/g within the voltage range of 0.01 ~ 2.50 V, demonstrating a specific capacity of 400 mAh/g. The cycle life surpasses that of most reported metal cathode materials. In addition, the eutectic gallium-indium-tin (EGaInSn) [Citation110] is also developed as a self-healing anode for LIBs, exhibiting promising anode performance with a capacity retention of 77% after 500 cycles. These reports suggest the successful application of room-temperature self-healing LM electrodes in large-scale LIBs with high energy density.
Figure 7. Application of LM in self-healing battery electrodes. A. Synthesis procedure of a room-temperature self-healing anode for lithium-ion batteries with Ga-sn LM alloy stabilizing in a reduced graphene oxide/carbon nanotube skeleton. Reproduced with permission from ref [Citation106]. Copyright 2017, royal society of chemistry. B. Schemes of spontaneous repairing LM/Si anode for lithium-ion battery. (a) Charge-discharge process of the LM/Si anode (left); (b) STEM image (right-top) and element mappings of LM/Si anodes before (right-middle) and after (right-bottom) discharge. Reproduced with permission from ref [Citation107]. Copyright 2018, Elsevier BV. C. Carbonization steps and electrochemical processes of self-healing LM nanoparticles encapsulated in hollow carbon fibers as a free-standing anode for lithium-ion batteries. Reproduced with permission from ref [Citation108]. Copyright 2019, Elsevier BV. D. Hollow Ga2O3@N-CQD as a self-healing anode for lithium-ion batteries. Reproduced with permission from ref [Citation109]. Copyright 2020, American Chemical society.
![Figure 7. Application of LM in self-healing battery electrodes. A. Synthesis procedure of a room-temperature self-healing anode for lithium-ion batteries with Ga-sn LM alloy stabilizing in a reduced graphene oxide/carbon nanotube skeleton. Reproduced with permission from ref [Citation106]. Copyright 2017, royal society of chemistry. B. Schemes of spontaneous repairing LM/Si anode for lithium-ion battery. (a) Charge-discharge process of the LM/Si anode (left); (b) STEM image (right-top) and element mappings of LM/Si anodes before (right-middle) and after (right-bottom) discharge. Reproduced with permission from ref [Citation107]. Copyright 2018, Elsevier BV. C. Carbonization steps and electrochemical processes of self-healing LM nanoparticles encapsulated in hollow carbon fibers as a free-standing anode for lithium-ion batteries. Reproduced with permission from ref [Citation108]. Copyright 2019, Elsevier BV. D. Hollow Ga2O3@N-CQD as a self-healing anode for lithium-ion batteries. Reproduced with permission from ref [Citation109]. Copyright 2020, American Chemical society.](/cms/asset/03978ee3-887b-4ec0-b33d-8a295b9e8eec/tsnm_a_2385349_f0007_c.jpg)
Apart from serving as an anode for LIB electrodes, the self-healing LMs also demonstrate great potential in enhancing other electrode materials. Among various anode materials, Si possesses the highest theoretical capacity of 4200 mA·h/g) (lithiated to Li4.4Si). However, Si-based electrodes often suffer from poor capacity retention due to significant volume changes, leading to material pulverization, loss of electrical contact with electrodes, continuous solid electrolyte interface growth, and electrolyte consumption [Citation111]. LM can function as a buffer, liquefying to heal fractures caused by Si’s volume expansion/contraction. Simultaneously, Si can serve as an ideal reinforcement to compensate for the LM’s capacity deficiency and enhance the battery’s energy density. As illustrated in , Han et al. [Citation107] devised a LM-mediated self-healing Si anode for a LIB, where the LM enables the contact between Si and the conducting-network throughout its repeated electrochemical reactions. Consequently, the LIB exhibits a high-capacity utilization (2300 mA·h/g at 500 mA/g), long-term stability (968 mA·h/g after 1500 charge-discharge cycles at 8 A/g with 81.3% retention), high rate capability (360 mA·h/g at 20 A/g, equivalence of 55 C, or full charge/discharge in 65 s), and an extra-ordinarily high initial coulombic efficiency (95.92%). Moreover, the nanosized self-healing LM particles were incorporated within carbon shells through coaxial electrospinning and carbonization () [Citation108]. The resulting free-standing anode exhibited a capacity of 552 mA·h/g after undergoing 1500 cycles at 1 A/g. This remarkable electrochemical performance can be attributed to the unique core-shell structure and well-designed void spaces, effectively mitigating volume changes of the LMNPs during lithiation/delithiation processes. Notably, the Ga-based LM nanoparticles tend to aggregate during charge/discharge due to their low surface energy, which may have an impact on the cycling stability of the battery. To address this issue, Guo et al. [Citation109] developed hollow Ga2O3@nitrogen-doped carbon quantum dot nanospheres (H-Ga2O3@N-CQDs) as LIB anodes (). This material takes advantage of Ga’s self-healing property and the hollow core-shell framework, delivering a specific capacity of 700.5 mA·h/g after 500 cycles at 0.5 A/g.
Overall, the effectiveness of utilizing Ga-based LMs as self-healing electrodes in LIBs has been extensively demonstrated, owing to their advantageous characteristics including low melting point, ideal fluidity, and high conductivity. However, the practical application of Ga-based anode materials encounters several challenges under certain harsh conditions. The liquid advantage of LMs will be limited for applications where the environmental temperature falls below their melting point. Currently, Ga-based and Bi-based LMs maintain a melting point above 0°C (), while other types with lower melting points are limited due to instability and poor safety performance. Therefore, further efforts should be dedicated to developing Ga-based and bismuth-based LMs with even lower melting points. Additionally, the high density and relatively low capacity exhibited by LMs constrain their potential for lightweight. Consequently, more studies should be conducted to mitigate these challenges.
3.3. Soft robotics
The field of soft robotics is advancing along two principal directions. On one hand, elastomer materials with low Young’s modulus [Citation112–114], such as silicone rubber, have been extensively researched and employed in various applications due to their advantageous properties, including ease of deformation and the ability to be cast into complex shapes. These materials are typically actuated by hydraulic or air pressure [Citation115–117] and often draw design inspiration from biological structures in nature, such as the human finger [Citation118], tentacles [Citation119], and arthropods [Citation120]. On the other hand, smart materials, including shape memory alloys [Citation121], smart polymers [Citation122], and hydrogels [Citation123,Citation124], are capable of responding to external stimuli such as magnetic fields, electric fields [Citation125], temperature [Citation126], and light [Citation127,Citation128]. This responsiveness provides a more diverse range of actuation strategies and functions for soft robotics, broadening their application potential and functionality.
LM represents an emerging class of soft robotic materials with several distinctive advantages [Citation129,Citation130]. These include a low melting point, low viscosity, high electrical conductivity, and high thermal conductivity. These properties enable LM to transition between solid and liquid states, achieving a wide range of Young’s modulus. This ability to transform between different polymorphic states, coupled with intelligent responses to external stimuli, provides soft robots with greater flexibility and precise control. This versatility makes LMs an attractive option for enhancing the functionality and performance of soft robotic systems.
The character of the T-1000 humanoid robot in the film of Terminator 2 offered a futuristic portrayal of self-healing and self-transformable LM soft robotics. In the pursuit of imitating such capabilities, researchers have continuously endeavored to explore self-healing LMs in soft robotics, such as preparing stiffness tunable LM robots [Citation95–98]. Furthermore, to advance the development of LM soft robots, the self-healing LMs have been utilized to manufacture the functional components, thereby enhancing the electromechanical stability and mitigating the risk of electrical failure when subjected to tearing, puncture, or other mechanical damage [Citation52]. According to the composition of the robot, functional components incorporating self-healing LMs include:
Circuit components. LMs, such as Ga-based alloys, are employed in the development of self-healing circuits. When encountering damage, the LM can flow to the affected area and reform a conductive path, thereby effectively restoring functionality. This inherent self-healing capability is crucial for ensuring continuous operation of soft robots in intricate environments. Markvicka’s team [Citation52] embedded Ga-based LM droplets in a soft silicone elastomer (LM embedded elastomer, LMEE) to create the control circuit for the soft robotic (, left). This circuit possesses excellent stretchability and ductility, seamlessly integrating with soft robots. Moreover, it owns self-healing capabilities, ensuring uninterrupted robot operation even if the conductive path is cut, torn, punctured, or material is removed, thus guaranteeing circuit integrity and continuous robot functionality (, right).
Figure 8. Self-healing design using LMs in soft robotics. A. Structure of the soft robotic with autonomously self-healing soft electronics (left); the soft robot encountering puncture damage from a hole punch traverses smooth terrain without altering its gait, requiring no manual intervention or external energy sources to continue moving (right). Reproduced with permission from ref [Citation52]. Copyright 2018, Springer Nature. B. The activation of the self-healing LMPA substrate results in a bending shape of VSEDA. Reproduced with permission from ref [Citation131]. Copyright 2015, IEEE/RSJ. C. (a) Object grasping analysis: resistance changes during hand movements and sequential pressure application (top). Sensor positions on the index finger, thumb, and palm (bottom); (b) assembly of layers, LM injection, and formation of electrical contacts with Ag NW sticker. (a) Reproduced with permission from ref [Citation132]. Copyright 2016, RSC. (b) Reproduced with permission from ref [Citation133]. Copyright 2015, Wiley-VCH Verlag. D. Representative photos depict LMESP-50% composite bone specimens during self-healing tests. After being cut in half, the specimens were left to self-heal under ambient conditions. The images below offer detailed views of the cut samples. Reproduced with permission from ref [Citation34]. Copyright 2019, Wiley-VCH.
![Figure 8. Self-healing design using LMs in soft robotics. A. Structure of the soft robotic with autonomously self-healing soft electronics (left); the soft robot encountering puncture damage from a hole punch traverses smooth terrain without altering its gait, requiring no manual intervention or external energy sources to continue moving (right). Reproduced with permission from ref [Citation52]. Copyright 2018, Springer Nature. B. The activation of the self-healing LMPA substrate results in a bending shape of VSEDA. Reproduced with permission from ref [Citation131]. Copyright 2015, IEEE/RSJ. C. (a) Object grasping analysis: resistance changes during hand movements and sequential pressure application (top). Sensor positions on the index finger, thumb, and palm (bottom); (b) assembly of layers, LM injection, and formation of electrical contacts with Ag NW sticker. (a) Reproduced with permission from ref [Citation132]. Copyright 2016, RSC. (b) Reproduced with permission from ref [Citation133]. Copyright 2015, Wiley-VCH Verlag. D. Representative photos depict LMESP-50% composite bone specimens during self-healing tests. After being cut in half, the specimens were left to self-heal under ambient conditions. The images below offer detailed views of the cut samples. Reproduced with permission from ref [Citation34]. Copyright 2019, Wiley-VCH.](/cms/asset/f69913d1-d544-4099-b572-149eb00a9bcd/tsnm_a_2385349_f0008_c.jpg)
Actuators. The LM droplets can be incorporated into soft materials for crafting self-healing dielectric elastomer actuators (DEAs) for soft robots [Citation134,Citation135]. When the actuator is damaged, the LM droplets can flow and fill the cracks, thereby restoring both the shape and functionality of the actuator. Shintake’s team [Citation131] introduced a variable stiffness DEA (VSDEA) to fabricate electrically controllable soft robots, in which the self-healing LM enables adjustable stiffness between soft and rigid states through Joule heating, while the DEA generates bending actuation ().
Electronic skin. To replicate the softness of human skin, robotics often use silicone to cover their bodies and sensors. Although this provides a human-like appearance, it reduces sensor effectiveness. Conversely, LM e-skin offers a superior solution. LM e-skin is flexible, stretchable, and meets all the sensing requirements for robotics, including the detection of mechanical force [Citation132,Citation136–140], temperature [Citation133,Citation141], motion [Citation142–144], light [Citation145] and gas composition [Citation146–150]. As showcased in , the high conductivity and fluidity of LM allow it to be embedded in a deformable polymer substrate, serving as an electrical interconnect for tactile sensors [Citation132] and temperature sensors [Citation133] in e-skin. This approach boasts a simple manufacturing process and a high fill factor for active devices. However, there are several challenges: (1) LM has a high material cost; (2) LM is prone to oxidation, which reduces their conductivity and fluidity, necessitating strict environmental controls; (3) Compared to other conductive materials, LM requires proper fixing and packaging to prevent leakage and accidental contact with other components.
Structural materials. The self-healing LMs are also utilized in the development of structural materials for the casing or support structures of soft robots. Following mechanical damage, the LM can flow and fill the damaged area, thus preserving the structural integrity of the robotic. Xin et al. [Citation34] employed liquid-metal-embedded sulfur polymer (LMESP) as a bone material, and showcased the remarkable self-healing capability under mild conditions (). This is facilitated by dynamic bonds between polysulfide rings/sulfhydryl groups and LMs.
Overall, the aforementioned applications collectively demonstrate the substantial potential of LM self-healing technology within the realm of soft robotics, particularly in enhancing the reliability, longevity, and versatility of robots. As research progresses, it is anticipated that the self-healing LMs will assume an increasingly pivotal role in the design and production of soft robots.
4. Discussion and outlook
The potential of self-healing LMs to revolutionize various industries is evident, yet the path to widespread adoption is lined with challenges that must be meticulously addressed. The unique combination of fluidity and metallic properties positions LMs as promising candidates for applications in flexible electronics, soft robotics, and energy storage. However, realizing their full potential requires overcoming several key hurdles and exploring new research directions.
4.1. Key challenges
Trigger Mechanisms. The implementation of effective and reliable trigger mechanisms is crucial for facilitating the self-healing process. Identifying suitable triggers capable of responding to specific damages, as well as developing responsive systems that activate the self-healing mechanisms at the appropriate time and under optimal conditions, pose challenges in this field. Currently, researchers are increasingly shifting their focus from single-physical field stimulation to multi-physical field stimulations, leveraging the inherent advantages offered by multiple physical fields. However, a notable challenge arises due to the lack of coordinated triggering mechanisms for self-healing across multiple physical fields.
Long-Term Stability. Ensuring the enduring stability of self-healing properties stands as a pivotal prerequisite for their practical application. Investigating the long-term durability of self-healing LMs across extended periods presents a formidable challenge, necessitating scrutiny of factors encompassing fatigue, recurrent healing cycles, and diverse environmental conditions. This multifaceted endeavor demands comprehensive research efforts aimed at elucidating the mechanisms governing the sustained efficacy of self-healing LM over time.
Integration into Existing Systems. Integrating self-healing LMs into existing systems and technologies while maintaining overall performance integrity poses a significant challenge. Adapting LM to diverse applications like electronics, robotics, and structural materials requires careful consideration of system compatibility and seamless integration. Tailored approaches and interdisciplinary collaboration are essential to optimize performance and leverage LM’s healing capabilities effectively.
Cost-Effectiveness.Ensuring cost-effectiveness is critical in the development and implementation of self-healing LMs. Establishing efficient manufacturing processes and evaluating implementation costs against benefits are key. Techniques like additive manufacturing and scalability are important for reducing waste and meeting growing demand. By prioritizing cost-effectiveness, stakeholders can promote widespread adoption of self-healing LMs, leading to significant economic benefits.
External Field Considerations: At the experimental level, the self-healing induced by external fields such as electric, magnetic and acoustic fields offers precise control of the LM healing process. However, this introduces several complex factors, including the precise regulation of electric field strength and distribution, management of thermal effects and electromagnetic interference in magnetic field applications, optimization of energy transfer efficiency and dielectric dissipation in sound fields, and the influence of environmental factors like temperature and humidity on self-healing efficiency. Additionally, experimental design must incorporate safety measures, such as protection against strong electromagnetic and acoustic fields and the evaluation and maintenance of specialized equipment.
4.2. Future exploration
Multi-physical Field Synergy. In addressing complex application needs, studying collaborative self-healing mechanisms across various physical domains is vital for enhancing the speed and efficiency of self-healing processes. This interdisciplinary approach integrates insights from materials science, chemistry, physics, and engineering to optimize performance. Overall, this comprehensive approach promises significant advancements in self-healing materials for complex applications.
Theoretical Calculation. Currently, there is a paucity of computational studies on the self-healing mechanism of LM. The rules of the self-healing mechanism are predominantly derived from experimental observation or calculation under simplified conditions, and the comprehension of complex mechanisms remains incomplete. However, the integration of deep learning with molecular dynamics and first-principles calculations offers a promising avenue for the calculation of self-healing mechanisms, thereby providing theoretical guidance for the development of self-healing flexible devices.
Intelligent Responsive Systems. Developing self-healing materials capable of intelligently responding to environmental changes and damage involves integrating sensors and feedback mechanisms. These technologies enable the materials to detect changes and initiate self-repair processes promptly, enhancing resilience and adaptability across various applications.
Innovative Material Design. Creating new self-healing LMs involves formulating materials with lower melting points, higher capacities, and improved environmental stability. These advancements aim to broaden their applications and enhance resilience against damage, thereby extending their functional lifespan.
Exploration of Application Scenarios. Expanding liquid metals (LMs) to extreme environments like deep-sea and space involves adapting them for challenging conditions. LMs resistant to extreme temperatures, pressures, and corrosive elements could revolutionize underwater exploration and space applications, offering solutions for propulsion, thermal management, and structural components. Through innovative research, LMs hold big promise for advancing scientific discovery and technology in extreme environments.
4.3. Conclusion
Despite the challenges, the future of self-healing LMs is bright and filled with opportunity. Through interdisciplinary research and innovative technological development, LMs are poised to play a significant role in future technological innovations, offering profound implications for society. Future research should focus on resolving current scientific and technical issues while actively seeking new areas of application to facilitate the commercialization and large-scale production of self-healing LMs. Additionally, considerations regarding environmental impact, safety, international collaboration, and policy support are pivotal to propelling the advancement of self-healing LMs. By taking a comprehensive approach that includes these factors, one can better utilize the potential of self-healing LMs to effect positive change in society.
Acknowledgments
This work was partially supported by NSFC Grant No. 91748206; the China Postdoctoral Science Foundation of China under grant 2023M731888; Frontier Project of the Chinese Academy of Sciences.
Disclosure statement
No potential conflict of interest was reported by the author(s).
Additional information
Funding
References
- Collias D, Beisel CL. CRISPR technologies and the search for the PAM-free nuclease. Nat Commun. 2021;12(1):555. doi: 10.1038/s41467-020-20633-y
- Sivaraman G, Guo J, Ward L, et al. Automated development of molten salt machine learning potentials: application to LiCl. J Phys Chem Lett. 2021;12(17):4278–4285. doi: 10.1021/acs.jpclett.1c00901
- Dubal DP, Chodankar NR, Kim DH, et al. Towards flexible solid-state supercapacitors for smart and wearable electronics. Chem Soc Rev. 2018;47(6):2065–2129. doi: 10.1039/C7CS00505A
- Lu G, Ni E, Jiang Y, et al. Room‐temperature liquid metals for flexible electronic devices. Small. 2024;20(9):2304147. doi: 10.1002/smll.202304147
- Kothandaraman RK, Jiang Y, Feurer T, et al. Near-infrared-transparent perovskite solar cells and perovskite-based tandem photovoltaics. Small Methods. 2020;4(10):2000395. doi: 10.1002/smtd.202000395
- Niu R, Jin M, Cao J, et al. Self-healing flexible conductive film by repairing defects via flowable liquid metal droplets. Micromachines. 2019;10(2):113. doi: 10.3390/mi10020113
- Chelfouh N, Rousselot S, Coquil G, et al. Using pectin for energy storage devices. Meet Abstr. 2023;243(5):891–891. doi: 10.1149/MA2023-015891mtgabs
- Abdallah MS, Aboona BE, Adam J, et al. Global Λ -hyperon polarization in Au + Au collisions at s NN = 3 GeV. Phys Rev C. 2021;104(6):L061901. doi: 10.1103/PhysRevC.104.L061901
- Chen TY, Shao SC, Hsu CK, et al. Incidence of acute kidney injury in COVID-19 infection: a systematic review and meta-analysis. Crit Care. 2020;24(1):346. doi: 10.1186/s13054-020-03009-y
- Hager MD, Greil P, Leyens C, et al. Self-healing materials. Adv Mater. 2010;22(47):5424–5430. doi: 10.1002/adma.201003036
- Bekas DG, Tsirka K, Baltzis D, et al. Self-healing materials: a review of advances in materials, evaluation, characterization and monitoring techniques. Compos Part B: Eng. 2016;87:92–119. doi: 10.1016/j.compositesb.2015.09.057
- Blaiszik BJ, Kramer SLB, Olugebefola SC, et al. Self-healing polymers and composites. Annu Rev Mater Res. 2010;40(1):179–211. doi: 10.1146/annurev-matsci-070909-104532
- Kilicli V, Yan X, Salowitz N, et al. Recent advancements in self-healing metallic materials and self-healing metal matrix composites. JOM. 2018;70(6):846–854. doi: 10.1007/s11837-018-2835-y
- Van Dijk N, Van der Zwaag S. Self-healing phenomena in metals. Adv Mater Interface. 2018;5(17):1800226. doi: 10.1002/admi.201800226
- Rohatgi PK. Al-shape memory alloy self-healing metal matrix composite. Mater Sci Eng: A. 2014;619:73–76. doi: 10.1016/j.msea.2014.09.050
- Ferguson JB, Schultz BF, Rohatgi PK. Self-healing metals and metal matrix composites. JOM. 2014;66(6):866–871. doi: 10.1007/s11837-014-0912-4
- Alaneme KK, Bodunrin MO. Self-healing using metallic material systems – a review. Appl Mater Today. 2017;6:9–15. doi: 10.1016/j.apmt.2016.11.002
- Huang J, Guo L, Zhong L. Synergistic healing mechanism of self-healing ceramics coating. Ceram Int. 2022;48(5):6520–6527. doi: 10.1016/j.ceramint.2021.11.198
- Greil P. Self-healing engineering ceramics with oxidation-induced crack repair. Adv Eng Mater. 2020;22(9):1901121. doi: 10.1002/adem.201901121
- Madhan M, Prabhakaran G. Self-healing ability of structural ceramics – a reviewPONNAMBALAM. In: Ponnambalam SG, Parkkinen J, Ramanathan K, editors. Trends in intelligent robotics, automation, and manufacturing: Vol. 330. Berlin, Heidelberg: Springer; 2012. p. 466–474.
- De Belie N, Gruyaert E, Al-Tabbaa A, et al. A review of self-healing concrete for damage management of structures. Adv Mater Inter. 2018;5(17):1800074. doi: 10.1002/admi.201800074
- Vijay K, Murmu M, Deo SV. Bacteria based self healing concrete – a review. Construct And Building Mater. 2017;152:1008–1014. doi: 10.1016/j.conbuildmat.2017.07.040
- Seifan M, Samani AK, Berenjian A. Bioconcrete: next generation of self-healing concrete. Appl Microbiol Biotechnol. 2016;100(6):2591–2602. doi: 10.1007/s00253-016-7316-z
- Wiktor V, Jonkers HM. Quantification of crack-healing in novel bacteria-based self-healing concrete. Cem And Concr Compos. 2011;33(7):763–770. doi: 10.1016/j.cemconcomp.2011.03.012
- Jonkers HM. Self healing concrete: a biological approach. Dordrecht: Springer Netherlands; 2007.
- Wang X, Guo R, Liu J. Liquid metal based soft robotics: materials, designs, and applications. Adv Mater Technol. 2019;4(2):1800549. doi: 10.1002/admt.201800549
- Gao JY, Chen S, Liu TY, et al. Additive manufacture of low melting point metal porous materials: capabilities, potential applications and challenges. Mater Today. 2021;49:201–230. doi: 10.1016/j.mattod.2021.03.019
- Hao Y, Gao J, Lv Y, et al. Low melting point alloys enabled stiffness tunable advanced materials. Adv Funct Mater. 2022;32(25):2201942. doi: 10.1002/adfm.202201942
- Zhu L, Wang B, Handschuh-Wang S, et al. Liquid metal–based soft microfluidics. Small. 2020;16(9):1903841. doi: 10.1002/smll.201903841
- Yuan B, He Z, Fang W, et al. Liquid metal spring: oscillating coalescence and ejection of contacting liquid metal droplets. Sci Bull. 2015;60(6):648–653. doi: 10.1007/s11434-015-0751-x
- Chen S, Wang HZ, Sun XY, et al. Generalized way to make temperature tunable conductor–insulator transition liquid metal composites in a diverse range. Mater Horiz. 2019;6(9):1854–1861. doi: 10.1039/C9MH00650H
- Park JE, Kang HS, Koo M, et al. Autonomous surface reconciliation of a liquid-metal conductor micropatterned on a deformable hydrogel. Adv Mater. 2020;32(37). doi: 10.1002/adma.202002178
- Yuk H, Lu B, Zhao X. Hydrogel bioelectronics. Chem Soc Rev. 2019;48(6):1642–1667. doi: 10.1039/C8CS00595H
- Xin Y, Peng H, Xu J, et al. Ultrauniform embedded liquid metal in sulfur polymers for recyclable, conductive, and self-healable materials. Adv Funct Mater. 2019;29(17):1808989. doi: 10.1002/adfm.201808989
- Zhang Z, Tang L, Chen C, et al. Liquid metal-created macroporous composite hydrogels with self-healing ability and multiple sensations as artificial flexible sensors. J Mater Chem A. 2021;9(2):875–883. doi: 10.1039/D0TA09730F
- Andersen A, Krogsgaard M, Birkedal H. Mussel-inspired self-healing double-cross-linked hydrogels by controlled combination of metal coordination and covalent cross-linking. Biomacromolecules. 2018;19(5):1402–1409. doi: 10.1021/acs.biomac.7b01249
- Rayleigh L. On the instability of jets. Proc Lond Math Soc. 1878;1-10(1):4–13. doi: 10.1112/plms/s1-10.1.4
- Antar BN, Ethridge EC, Maxwell D. Viscosity measurement using drop coalescence in microgravity. Microgravity Sci Technol. 2003;14(1):9–19. doi: 10.1007/BF02873332
- Aarts DGAL, Lekkerkerker HNW, Guo H, et al. Hydrodynamics of droplet coalescence. Phys Rev Lett. 2005;95(16):164503. doi: 10.1103/PhysRevLett.95.164503
- Wang BB, Wang XD, Wang TH, et al. Electrocoalescence behavior of two identical droplets with various droplet radii. Appl Therm Eng. 2017;111:1464–1469. doi: 10.1016/j.applthermaleng.2016.05.088
- Wang BB, Wang XD, Yan WM, et al. Molecular dynamics simulations on coalescence and non-coalescence of conducting droplets. Langmuir. 2015;31(27):7457–7462. doi: 10.1021/acs.langmuir.5b01574
- Li T, Li M, Zhang L, et al. Molecular dynamics study of the temperature-dependent coalescence of liquid nanodrops: implications for microfluidics. ACS Appl Nano Mater. 2019;2(12):7978–7988. doi: 10.1021/acsanm.9b02018
- Li T, Li J, Lin H, et al. Control of wettability transition and coalescence dynamics of droplets on the surface via mechanical vibration: a molecular simulation exploration. Appl Surf Sci. 2019;473:393–400. doi: 10.1016/j.apsusc.2018.12.171
- Li T, Xia Y, Zhang L, et al. Effects of stripy surfaces with intervals on the coalescence dynamics of nano-droplets: insights from molecular dynamics simulations. Appl Surf Sci. 2019;481:951–959. doi: 10.1016/j.apsusc.2019.03.120
- Cademartiri L, Thuo MM, Nijhuis CA, et al. Electrical resistance of Ag TS –S(CH 2)n−1CH3//Ga2O3/EGaIn tunneling junctions. J Phys Chem C. 2012;116(20):10848–10860. doi: 10.1021/jp212501s
- Liu T, Sen P, Kim CJ. Characterization of nontoxic liquid-metal alloy galinstan for applications in microdevices. J Microelectromech Syst. 2012;21(2):443–450. doi: 10.1109/JMEMS.2011.2174421
- Tutika R, Haque ABMT, Bartlett MD. Self-healing liquid metal composite for reconfigurable and recyclable soft electronics. Commun Mater. 2021;2(1):1–8. doi: 10.1038/s43246-021-00169-4
- Boley JW, White EL, Kramer RK. Mechanically sintered gallium–indium nanoparticles. Adv Mater. 2015;27(14):2355–2360. doi: 10.1002/adma.201404790
- Palleau E, Reece S, Desai SC, et al. Self-healing stretchable wires for reconfigurable circuit wiring and 3D microfluidics. Adv Mater. 2013;25(11):1589–1592. doi: 10.1002/adma.201203921
- Guo R, Tang J, Dong S, et al. One-step liquid metal transfer printing: toward fabrication of flexible electronics on wide range of substrates. Adv Mater Technol. 2018;3(12):1800265. doi: 10.1002/admt.201800265
- Blaiszik BJ, Kramer SLB, Grady ME, et al. Autonomic restoration of electrical conductivity. Adv Mater. 2012;24(3):398–401. doi: 10.1002/adma.201102888
- Markvicka EJ, Bartlett MD, Huang X, et al. An autonomously electrically self-healing liquid metal–elastomer composite for robust soft-matter robotics and electronics. Nat Mater. 2018;17(7):618–624. doi: 10.1038/s41563-018-0084-7
- Li G, Wu X, Lee DW. A galinstan-based inkjet printing system for highly stretchable electronics with self-healing capability. Lab Chip. 2016;16(8):1366–1373. doi: 10.1039/C6LC00046K
- Wang J, Cai G, Li S, et al. Printable superelastic conductors with extreme stretchability and robust cycling endurance enabled by liquid-metal particles. Adv Mater. 2018;30(16):1706157. doi: 10.1002/adma.201706157
- Zheng R, Peng Z, Fu Y, et al. A novel conductive core–shell particle based on liquid metal for fabricating real-time self-repairing flexible circuits. Adv Funct Mater. 2020;30(15). doi: 10.1002/adfm.201910524
- Li Y, Fang T, Zhang J, et al. Ultrasensitive and ultrastretchable electrically self-healing conductors. Proc Natl Acad Sci USA. 2023;120(23):e2300953120. doi: 10.1073/pnas.2300953120
- Ma B, Xu C, Chi J, et al. A versatile approach for direct patterning of liquid metal using magnetic field. Adv Funct Mater. 2019;29(28):1901370. doi: 10.1002/adfm.201901370
- Zhao B, Bai Z, Lv H, et al. Self-healing liquid metal magnetic hydrogels for smart feedback sensors and high-performance electromagnetic shielding. Nano-Micro Lett. 2023;15(1):79. doi: 10.1007/s40820-023-01043-3
- Guo R, Sun X, Yuan B, et al. Magnetic liquid metal (fe-EGaIn) based multifunctional electronics for remote self-healing materials, degradable electronics, and thermal transfer printing. Adv Sci. 2019;6(20):1901478. doi: 10.1002/advs.201901478
- Liu H, Li M, Li Y, et al. Magnetic steering of liquid metal mobiles. Soft Matter. 2018;14(17):3236–3245. doi: 10.1039/C8SM00056E
- Van Meerbeek IM, Mac Murray BC, Kim JW, et al. Morphing metal and elastomer bicontinuous foams for reversible stiffness, shape memory, and self-healing soft machines. Adv Mater. 2016;28(14):2801–2806. doi: 10.1002/adma.201505991
- Lee W, Kim H, Kang I, et al. Universal assembly of liquid metal particles in polymers enables elastic printed circuit board. Science. 2022;378(6620):637–641. doi: 10.1126/science.abo6631
- Liu Y, Gao M, Mei S, et al. Ultra-compliant liquid metal electrodes with in-plane self-healing capability for dielectric elastomer actuators. Appl Phys Lett. 2013;103(6):064101. doi: 10.1063/1.4817977
- Dodbiba G, Ono K, Park HS, et al. FeNbVB alloy particles suspended in liquid gallium: investigating the magnetic properties of the mr suspension. Int J Mod Phys B. 2011;25(7):947–955. doi: 10.1142/S0217979211058444
- Chang H, Guo R, Sun Z, et al. Direct writing and repairable paper flexible electronics using nickel–liquid metal ink. Adv Mater Interface. 2018;5(20):1800571. doi: 10.1002/admi.201800571
- Kim D, Lee JB. Magnetic-field-induced liquid metal droplet manipulation. J Korean Phys Soc. 2015;66(2):282–286. doi: 10.3938/jkps.66.282
- Jeon J, Lee JB, Chung SK, et al. On-demand magnetic manipulation of liquid metal in microfluidic channels for electrical switching applications. Lab on a chip. Lab Chip. 2017;17(1):128–133. doi: 10.1039/C6LC01255H
- Cui Y, Liang F, Xu S, et al. Interfacial wetting behaviors of liquid Ga alloys/FeGa3 based on metallic bond interaction. Colloids And Surfaces A: Physicochem And Eng Aspects. 2019;569:102–109. doi: 10.1016/j.colsurfa.2019.01.079
- Wang H, Chen S, Li H, et al. A liquid gripper based on phase transitional metallic ferrofluid. Adv Funct Mater. 2021;31(32):2100274. doi: 10.1002/adfm.202100274
- Sivan V, Tang SY, O’Mullane AP, et al. Liquid metal marbles. Adv Funct Mater. 2013;23(2):144–152. doi: 10.1002/adfm.201200837
- Kazem N, Hellebrekers T, Majidi C. Soft multifunctional composites and emulsions with liquid metals. Adv Mater. 2017;29(27):1605985. doi: 10.1002/adma.201605985
- Qiao R, Tang SY. Connecting liquid metals with sound. Science. 2022;378(6620):594–595. doi: 10.1126/science.ade1813
- Wang H, Yao Y, He Z, et al. A highly stretchable liquid metal polymer as reversible transitional insulator and conductor. Adv Mater. 2019;31(23):1901337. doi: 10.1002/adma.201901337
- Zhang M, Zhang P, Zhang C, et al. Porous and anisotropic liquid metal composites with tunable reflection ratio for low-temperature electromagnetic interference shielding. Appl Mater Today. 2020;19:100612. doi: 10.1016/j.apmt.2020.100612
- Ikura R, Park J, Osaki M, et al. Design of self-healing and self-restoring materials utilizing reversible and movable crosslinks. NPG Asia Mater. 2022;14(1):1–17. doi: 10.1038/s41427-021-00349-1
- Wang H, Yuan B, Liang S, et al. PLUS-M: a porous liquid-metal enabled ubiquitous soft material. Mater Horiz. 2018;5(2):222–229. doi: 10.1039/C7MH00989E
- Lu HF, Nie ZZ, Bisoyi HK, et al. An ultrahigh fatigue resistant liquid crystal elastomer-based material enabled by liquid metal. Sci China Mater. 2022;65(6):1679–1686.
- Zhang Y, Xie L, Chai B, et al. A highly attenuated mumps virus strain of genotype F generated by passaging in vero cells. Virol Sin. 2021;36(2):337–340. doi: 10.1007/s12250-020-00292-5
- Choi YY, Ho DH, Cho JH. Self-healable hydrogel–liquid metal composite platform enabled by a 3D printed stamp for a multimodular sensor system. ACS Appl Mater Interfaces. 2020;12(8):9824–9832. doi: 10.1021/acsami.9b22676
- Wang X, Zhao M, Zhang L, et al. Liquid metal bionic instant self-healing flexible electronics with full recyclability and high reliability. Chem Eng J. 2022;431:133965. doi: 10.1016/j.cej.2021.133965
- Liao M, Liao H, Ye J, et al. Polyvinyl alcohol-stabilized liquid metal hydrogel for wearable transient epidermal sensors. ACS Appl Mater Interfaces. 2019;11(50):47358–47364. doi: 10.1021/acsami.9b16675
- Martin P. Wound healing–aiming for perfect skin Regeneration. Science. 1997;276(5309):75–81. doi: 10.1126/science.276.5309.75
- Martin R, Rekondo A, de LAR, et al. Dynamic sulfur chemistry as a key tool in the design of self-healing polymers. Smart Mater And Struct. 2016;25(8):084017. doi: 10.1088/0964-1726/25/8/084017
- Martín R, Rekondo A, Echeberria J, et al. Room temperature self-healing power of silicone elastomers having silver nanoparticles as crosslinkers. Chem Commun. 2012;48(66):8255–8257. doi: 10.1039/c2cc32030d
- Xu J, Wang Z, You J, et al. Polymerization of moldable self-healing hydrogel with liquid metal nanodroplets for flexible strain-sensing devices. Chem Eng J. 2020;392:123788. doi: 10.1016/j.cej.2019.123788
- Xu Y, Rothe R, Voigt D, et al. Convergent synthesis of diversified reversible network leads to liquid metal-containing conductive hydrogel adhesives. Nat Commun. 2021;12(1):2407. doi: 10.1038/s41467-021-22675-2
- Liu T, Li C, Yao H, et al. Extremely strengthening fatigue resistance, elastic restorability and thermodynamic stability of a soft transparent self-healing network based on a dynamic molecular confinement-induced bioinspired nanostructure. Mater Horiz. 2023;10(8):2968–2979. doi: 10.1039/D3MH00358B
- Sun F, Liu L, Liu T, et al. Vascular smooth muscle-inspired architecture enables soft yet tough self-healing materials for durable capacitive strain-sensor. Nat Commun. 2023;14(1):130. doi: 10.1038/s41467-023-35810-y
- Song H, Wang Y, Fei Q, et al. Cryopolymerization-enabled self-wrinkled polyaniline-based hydrogels for highly stretchable all-in-one supercapacitors. Exploration. 2022;2(4):20220006. doi: 10.1002/EXP.20220006
- Xu J, Li Y, Liu T, et al. Room-temperature self-healing soft composite network with unprecedented crack propagation resistance enabled by a supramolecular assembled lamellar structure. Adv Mater. 2023;35(26):2300937. doi: 10.1002/adma.202300937
- Yao H, Liu T, Jia Y, et al. Water-insensitive self-healing materials: from network structure design to advanced soft electronics. Adv Funct Mater. 2023;33(48):2307455. doi: 10.1002/adfm.202307455
- Guo R, Li T, Wu Z, et al. Thermal transfer-enabled rapid printing of liquid metal circuits on multiple substrates. ACS Appl Mater Interfaces. 2022;14(32):37028–37038. doi: 10.1021/acsami.2c08743
- Tang L, Mou L, Zhang W, et al. Large-scale fabrication of highly elastic conductors on a broad range of surfaces. ACS Appl Mater Interfaces. 2019;11(7):7138–7147. doi: 10.1021/acsami.8b20460
- Fu C, Tang W, Miao Y, et al. Large-scalable fabrication of liquid metal-based double helix core-spun yarns for capacitive sensing, energy harvesting, and thermal management. Nano Energy. 2023;106:108078. doi: 10.1016/j.nanoen.2022.108078
- Gao S, Yang Y, Falchevskaya AS, et al. Phase transition liquid metal enabled emerging biomedical technologies and applications. Adv Sci. 2023:2306692. doi: 10.1002/advs.202306692
- Li X, Zhu P, Zhang S, et al. A self-supporting, conductor-exposing, stretchable, ultrathin, and recyclable kirigami-structured liquid metal paper for multifunctional E-skin. ACS Nano. 2022;16(4):5909–5919. doi: 10.1021/acsnano.1c11096
- Lopes PA, Paisana H, De Almeida AT, et al. Hydroprinted electronics: ultrathin stretchable Ag–in–Ga E-skin for bioelectronics and human–machine interaction. ACS Appl Mater Interfaces. 2018;10(45):38760–38768. doi: 10.1021/acsami.8b13257
- Wang Y, Yu Z, Mao G, et al. Printable liquid-metal@PDMS stretchable heater with high stretchability and dynamic stability for wearable thermotherapy. Adv Mater Technol. 2019;4(2):1800435. doi: 10.1002/admt.201800435
- Chen G, Wang H, Guo R, et al. Superelastic EGaIn composite fibers sustaining 500% tensile strain with superior electrical conductivity for wearable electronics. ACS Appl Mater Interfaces. 2020;12(5):6112–6118. doi: 10.1021/acsami.9b23083
- Yang J, Nithyanandam P, Kanetkar S, et al. Liquid metal coated textiles with autonomous electrical healing and antibacterial properties. Adv Mater Technol. 2023;8(14):2202183. doi: 10.1002/admt.202202183
- Li H, Qu R, Ma Z, et al. Permeable and patternable super-stretchable liquid metal fiber for constructing high-integration-density multifunctional electronic fibers. Adv Funct Mater. 2023:2308120. doi: 10.1002/adfm.202308120
- Ma Z, Huang Q, Xu Q, et al. Permeable superelastic liquid-metal fibre mat enables biocompatible and monolithic stretchable electronics. Nat Mater. 2021;20(6):859–868. doi: 10.1038/s41563-020-00902-3
- Cheng Y, Wang C, Kang F, et al. Self-healable lithium-ion batteries: a review. Nanomaterials. 2022;12(20):3656. doi: 10.3390/nano12203656
- Ning X, Phadke S, Chung B, et al. Self-healing Li–bi liquid metal battery for grid-scale energy storage. J Power Sources. 2015;275:370–376. doi: 10.1016/j.jpowsour.2014.10.173
- Li H, Wang K, Cheng S, et al. High performance liquid metal battery with environmentally friendly antimony–tin positive electrode. ACS Appl Mater & Interface. 2016;8(20):12830–12835. doi: 10.1021/acsami.6b02576
- Wu Y, Huang L, Huang X, et al. A room-temperature liquid metal-based self-healing anode for lithium-ion batteries with an ultra-long cycle life. Energy Environ Sci. 2017;10(8):1854–1861. doi: 10.1039/C7EE01798G
- Han B, Yang Y, Shi X, et al. Spontaneous repairing liquid metal/si nanocomposite as a smart conductive-additive-free anode for lithium-ion battery. Nano Energy. 2018;50:359–366. doi: 10.1016/j.nanoen.2018.05.044
- Zhu J, Wu Y, Huang X, et al. Self-healing liquid metal nanoparticles encapsulated in hollow carbon fibers as a free-standing anode for lithium-ion batteries. Nano Energy. 2019;62:883–889. doi: 10.1016/j.nanoen.2019.06.023
- Guo J, Gao F, Li D, et al. Novel strategy of constructing hollow Ga 2 O 3 @N-CQDs as a self-healing anode material for lithium-ion batteries. ACS Sustain Chem Eng. 2020;8(36):13692–13700. doi: 10.1021/acssuschemeng.0c03756
- Kidanu WG, Hur J, Kim IT. Gallium-indium-tin eutectic as a self-healing room-temperature liquid metal anode for high-capacity lithium-ion batteries. Materials. 2022;15(1):168. doi: 10.3390/ma15010168
- Wu H, Cui Y. Designing nanostructured si anodes for high energy lithium ion batteries. Nano Today. 2012;7(5):414–429. doi: 10.1016/j.nantod.2012.08.004
- Marchese AD, Katzschmann RK, Rus D. A recipe for soft fluidic elastomer robots. Soft Robot. 2015;2(1):7–25. doi: 10.1089/soro.2014.0022
- Anderson IA, Gisby TA, McKay TG, et al. Multi-functional dielectric elastomer artificial muscles for soft and smart machines. J Appl Phys. 2012;112(4):041101. doi: 10.1063/1.4740023
- Marchese AD, Onal CD, Rus D. Autonomous soft robotic fish capable of escape maneuvers using fluidic elastomer actuators. Soft Robot. 2014;1(1):75–87. doi: 10.1089/soro.2013.0009
- Cho B, Kim MS, Kim SW, et al. Design of a compact embedded hydraulic power unit for bipedal robots. IEEE Robot Autom Lett. 2021;6(2):3631–3638. doi: 10.1109/LRA.2021.3061390
- Moghadam AAA, Alaie S, Deb Nath S, et al. Laser cutting as a rapid method for fabricating thin soft pneumatic actuators and robots. Soft Robot. 2018;5(4):443–451. doi: 10.1089/soro.2017.0069
- Terryn S, Brancart J, Lefeber D, et al. Self-healing soft pneumatic robots. Sci Robot. 2017;2(9):eaan4268. doi: 10.1126/scirobotics.aan4268
- Mosadegh B, Polygerinos P, Keplinger C, et al. Pneumatic networks for soft robotics that actuate rapidly. Adv Funct Mater. 2014;24(15):2163–2170. doi: 10.1002/adfm.201303288
- Wehner M, Truby RL, Fitzgerald DJ, et al. An integrated design and fabrication strategy for entirely soft, autonomous robots. Nature. 2016;536(7617):451–455. doi: 10.1038/nature19100
- Nemiroski A, Shevchenko YY, Stokes AA, et al. Arthrobots. Soft Robot. 2017;4(3):183–190. doi: 10.1089/soro.2016.0043
- Huang X, Kumar K, Jawed MK, et al. Highly dynamic shape memory alloy actuator for fast moving soft robots. Adv Mater Technol. 2019;4(4):1800540. doi: 10.1002/admt.201800540
- Shen Q, Trabia S, Stalbaum T, et al. A multiple-shape memory polymer-metal composite actuator capable of programmable control, creating complex 3D motion of bending, twisting, and oscillation. Sci Rep. 2016;6(1):24462. doi: 10.1038/srep24462
- Buwalda SJ, Boere KW, Dijkstra PJ, et al. Hydrogels in a historical perspective: from simple networks to smart materials. J Control Release. 2014;190:254–273. doi: 10.1016/j.jconrel.2014.03.052
- Taylor DL, in het Panhuis M. In het Panhuis M. Self-healing hydrogels. Adv Mater. 2016;28(41):9060–9093. doi: 10.1002/adma.201601613
- Acome E, Mitchell SK, Morrissey TG, et al. Hydraulically amplified self-healing electrostatic actuators with muscle-like performance. Science. 2018;359(6371):61–65. doi: 10.1126/science.aao6139
- Yuan C, Roach DJ, Dunn CK, et al. 3D printed reversible shape changing soft actuators assisted by liquid crystal elastomers. Soft Matter. 2017;13(33):5558–5568. doi: 10.1039/C7SM00759K
- Zeng H, Wani OM, Wasylczyk P, et al. Light-driven, caterpillar-inspired miniature inching robot. Macromol Rapid Commun. 2018;39(1):1700224. doi: 10.1002/marc.201700224
- Wani OM, Zeng H, Priimagi A. A light-driven artificial flytrap. Nat Commun. 2017;8(1):15546. doi: 10.1038/ncomms15546
- Ren L, Xu X, Du Y, et al. Liquid metals and their hybrids as stimulus–responsive smart materials. Mater Today. 2020;34:92–114. doi: 10.1016/j.mattod.2019.10.007
- Yu Y, Miyako E. Recent advances in liquid metal manipulation toward soft robotics and biotechnologies. Chem – A Eur J. 2018;24(38):9456–9462. doi: 10.1002/chem.201800605
- Shintake J, Schubert B, Rosset S, et al. Variable stiffness actuator for soft robotics using dielectric elastomer and low-melting-point alloy. In: IEEE/RSJ International Conference on Intelligent Robots and Systems (IROS); Hamburg, Germany. IEEE; 2015. p. 1097–1102.
- Hong SY, Lee YH, Park H, et al. Wearable tactile sensor based on flexible microfluidics. Lab Chip. 2016;16(17):3244–3250. doi: 10.1039/C6LC00579A
- Y HS, H LY, Park H, et al. Stretchable active matrix temperature sensor array of polyaniline nanofibers for electronic skin. Adv Mater. 2016;28(5):930–935. doi: 10.1002/adma.201504659
- Gu GY, Zhu J, Zhu LM, et al. A survey on dielectric elastomer actuators for soft robots. Bioinspir Biomim. 2017;12(1):011003. doi: 10.1088/1748-3190/12/1/011003
- Hines L, Petersen K, Lum GZ, et al. Soft actuators for small-scale robotics. Adv Mater. 2017;29(13):1603483. doi: 10.1002/adma.201603483
- Jeong YR, Kim J, Xie Z, et al. A skin-attachable, stretchable integrated system based on liquid GaInSn for wireless human motion monitoring with multi-site sensing capabilities. NPG Asia Mater. 2017;9(10):e443–e443. doi: 10.1038/am.2017.189
- Mengüç Y, Park YL, Pei H, et al. Wearable soft sensing suit for human gait measurement. The Int J Robot Res. 2014;33(14):1748–1764. doi: 10.1177/0278364914543793
- Yeo JC, Kenry YJ, Loh KP, et al. Triple-state liquid-based microfluidic tactile sensor with high flexibility, durability, and sensitivity. ACS Sens. 2016;1(5):543–551. doi: 10.1021/acssensors.6b00115
- Gu KM, Alrowais H, Brand O. 3D-integrated and multifunctional all-soft physical microsystems based on liquid metal for electronic skin applications. Adv Elect Mater. 2018;4(2):1700434. doi: 10.1002/aelm.201700434
- Kim K, Choi J, Jeong Y, et al. Highly sensitive and wearable liquid metal-based pressure sensor for health monitoring applications: integration of a 3D-printed microbump array with the microchannel. Adv Healthc Mater. 2019;8(22):1900978. doi: 10.1002/adhm.201900978
- Li H, Yang Y, Liu J. Printable tiny thermocouple by liquid metal gallium and its matching metal. Appl Phys Lett. 2012;101(7):073511. doi: 10.1063/1.4746397
- Varga M, Ladd C, Ma S, et al. On-skin liquid metal inertial sensor. Lab on a chip. Lab Chip. 2017;17(19):3272–3278. doi: 10.1039/C7LC00735C
- Babatain W, Buttner U, El-Atab N, et al. Graphene and liquid metal integrated multifunctional wearable platform for monitoring motion and human–machine interfacing. ACS Nano. 2022;16(12):20305–20317. doi: 10.1021/acsnano.2c06180
- Babatain W, El‐atab N, Hussain MM. Graphene coated liquid metal droplet-enabled dual-axis integrated accelerometer. Adv Mater Technol. 2023;8(1):2201094. doi: 10.1002/admt.202201094
- Yun J, Lim Y, Lee H, et al. A patterned graphene/ZnO UV sensor driven by integrated asymmetric micro-supercapacitors on a liquid metal patterned foldable paper. Adv Funct Mater. 2017;27(30):1700135. doi: 10.1002/adfm.201700135
- Wei Z, Akbari MK, Hai Z, et al. Ultra-thin sub-10 nm Ga2O3-WO3 heterostructures developed by atomic layer deposition for sensitive and selective C2H5OH detection on ppm level. Sensors And Actuators B: Chem. 2019;287:147–156. doi: 10.1016/j.snb.2019.02.046
- Shafiei M, Hoshyargar F, Motta N, et al. Utilizing p-type native oxide on liquid metal microdroplets for low temperature gas sensing. Mater & Des. 2017;122:288–295. doi: 10.1016/j.matdes.2017.03.017
- Idrus-Saidi SA, Tang J, Yang J, et al. Liquid metal-based route for synthesizing and tuning gas-sensing elements. ACS Sens. 2020;5(4):1177–1189. doi: 10.1021/acssensors.0c00233
- Schwebel T, Fleischer M, Meixner H, et al. CO-sensor for domestic use based on high temperature stable Ga2O3 thin films. Sensors And Actuators B: Chem. 1998;49(1):46–51. doi: 10.1016/S0925-4005(97)00334-1
- Gu KM, Alrowais H, Kim C, et al. All-soft, battery-free, and wireless chemical sensing platform based on liquid metal for liquid- and gas-phase VOC detection. Lab Chip. 2017;17(13):2323–2329. doi: 10.1039/C7LC00390K