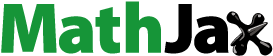
Abstract
Water mist is considered to be one of the most effective ways to suppress fire in coal mines. The structure of an atomization device for water mist was determined based on preliminary research. By regulating the working conditions, including air pressure and water flow volume, we obtained water mist with varying particle size distributions, which proved to be the most important factor for fire suppression. Particle size distribution, characterized by a V99 and V50, changed from 50 to 1600 µm during the experiment at a given air pressure (0.6–0.16 MPa) and water flow volume (0.6–1.0 m3/h). The particle size distribution along an axial line can be divided into a wavy flow zone and a fully atomizing zone. Based on the experiments, three types of particle size distributions, 98, 498 and 1013 µm, were used to test the fire-suppression characteristics of water mist in a simulated roadway with a self-built platform. The result showed that water mist could suppress fire rapidly and the highest temperature dropped from 205 to 10 °C within 30 s.
1. Introduction
Fire is a major disaster during coal-mine production and threatens miners’ safety (NFPA 2006; Ren et al. Citation2017; Cheng et al. Citation2017; Ren et al. Citation2016). On 15 March 2010, 25 miners from Dongxin Coal Mine in Xinmi, Henan, were killed by a cable fire in a roadway. On 6 July 2011, at Zaozhuang Prepared Coal Mine Co., Ltd, a wood and coal fire caused by a blowhole air compressor electrical fault killed 28 people (Liang Citation2010). Large volumes of toxic gas are produced by combustion, and because of the relatively small space, tunnel fires in coal mines especially endanger miners’ safety. Ventilation disorders that are caused by tunnel fires often result in a serious loss of property (Ray and Singh Citation2007).
As a new fire-extinguishing technology, water mist is used widely in the fire-protection industry because of its advantages of a high efficiency, a low-cost and personnel and equipment safety (Mawhinney and Richardson Citation1997, Citation1996; Mawhinney Citation1993, Citation1997; Mawhinney and Back Citation1998). Water mist for fire suppression and control has gradually become the focus of coal mine-safety researchers (Mawhinney and Dlugogorski Citation1994; Liu and Kim Citation2001; Jones and Nolan Citation1995). Yuan and Lazzara conducted fire-suppression experiments with water mist at the Pittsburgh Laboratory under the National Institute for Occupational Safety and Health (NIOSH) (Yuan and Lazzara Citation2004). Based on the experimental results, the fire-extinguishing mechanism of water mist is proposed to result from three aspects: fuel-surface cooling, flame cooling and oxygen isolation. Loomis and Mcpherson carried out a series of experiments on water mist in a simulated roadway built by Virginia Tech, and proved that water mist was effective at suppressing fire in fuel-rich combustion mines (Loomis and Mcpherson Citation1995). Since 2004, Ray and Singh at The Central Mining Research Institute in India have conducted a series of studies in this area, and have indicated that water mist, liquid nitrogen and high-stability nitrogen foam were three major technical means for fire suppression and control in coal mines (Ray and Singh Citation2005). The experiment that was conducted on a roadway simulation showed that water mist can reduce the downhole combustion intensity, the probability of reversing smoke and the amount of suspended particles in the combustion products and improve the visibility in fire areas (Ren et al. Citation2016).
Scholars have conducted research on and have explored the application of water-mist technology in the field of coal mine fires (Downie et al. Citation1995; Heskestad Citation2002; CMRI Citation2004; Kong et al. Citation2018; Ren et al. Citation2015). Although some achievements have been made, the following problems still exist. First, few studies exist on the mist-field and motion-diffusion characteristics of water mist, especially in ventilation tunnels. The atomization of water mist in the roadway and its movement diffusion affects the fire-extinguishing and cooling effect in fire areas. Therefore, it is necessary to carry out experimental research on the atomization effect and movement diffusion characteristics of water mist in the roadway. Second, compared with the application of water mist in other fields, most experimental studies on the application of this technology in coal mines have been completed based on numerical simulation, however, the results are unsupported by research trials.
Based on the problems above and using a small-scale simulated tunnel test bench and water-mist-generating device in the laboratory, experiments were carried out to study the particle size distribution (PSD) and fire-suppression characteristics of water mist under different ventilation conditions.
2. Mechanism for fire suppression of water mist
Water mist is converted into small particles with a large surface area through an atomizer nozzle. This mist can absorb the heat of the fire area rapidly, and achieve rapid fire extinguishing. Heat exchange between the water mist and the fire area includes heat conduction, heat radiation and heat convection, which are termed sensible heat exchange. Besides these three forms of heat exchange, water mist with its phase change, can absorb substantial heat to cool the fire area, which is termed latent heat exchange. The total heat exchange during fire suppression consists of a sensible heat exchange and latent heat exchange.
When droplets in the water mist contact the surrounding air, as a result of molecular motion in the droplet, the surrounding air forms a saturated boundary layer with the same temperature as the surface of the droplet. The temperature difference between the saturated air boundary layer and the ambient air results in heat conduction and material exchange.
If we assume a tiny droplet surface of dS, sensible heat exchange between the tiny surface and the surrounding air can be expressed as EquationEquation (1)(1)
(1) :
(1)
(1)
The latent heat exchange can be expressed as EquationEquations (2)(2)
(2) , Equation(3)
(3)
(3) and Equation(4)
(4)
(4) :
(2)
(2)
(3)
(3)
(4)
(4)
The total heat exchange between the droplet and the fire area can be expressed as EquationEquation (5)(5)
(5) :
(5)
(5)
EquationEquation (5)(5)
(5) suggests that more dispersed particles will have a larger specific surface area, and a faster heat transfer rate will result when the water quantity is constant.
Where is the Droplet surface, m2;
is Sensible heat exchange, J;
is the Heat-exchange coefficient W·m−2·K−1;
is the Air temperature, K;
is the Boundary layer temperature, K;
is the Latent heat exchange, J;
is the Unit latent heat at temperature Tb, J·kg−1;
is the Wet heat exchange volume;
is the Wet heat exchange coefficient, kg·m−2·s−1;
is the Moisture content, kg/kgdry air;
is the Moisture content of the air layer, kg/kgdry air;
is the Total heat exchange, J.
3. Experiment platforms
3.1. Testing systems for water-mist PSD
3.1.1. Testing systems and procedures
shows the self-built experimental testing system. Core components included a water-mist atomization device, an air compressor, a plunger pump and a laser particle-size analyzer (Winner318C, China University of Mining and technology). The air source was supplied by an air compressor that provides an air flow rate of 0–360 m3/h with an air pressure of 0–0.8 MPa. Instruments included an electromagnetic flowmeter, a vortex-shedding flowmeter and two pressure gauges (P1, P2). The laser particle-size analyzer could determine PSDs from 0 to 2000 µm.
lists the structural parameters of atomization device. When compressed air flows through the nozzle, the air velocity increases and the static pressure decreases. A maximum was reached at the nozzle throat. At the same time, water was pumped to the device through a water inlet with a high speed. Original water mist was generated during the collision of water and air.
Table 1. Structural parameters of the atomization device.
3.1.2. Experimental procedures
The specific experimental procedures were as follows:
The experimental system was established according to and every connection was sealed and stable. The laser particle-size analyzer was 1 m away from the water-mist outlet.
The air pressure P1 was maintained at 0.06 MPa before the water flow (Q) was changed 0.6–1.0 m3/h in each group with an increment of 0.1 m3/h by adjusting the valve.
The air pressure P1 was changed from 0.06 to 0.16 MPa in increments of 0.02 MPa. Step 2 was repeated to measure the water-mist distribution.
The laser particle-size analyzer was stabilized and the atomization device was moved axially with the distance between them (d) being 0–1.5 m. The PSD was determined at each point and at a given work condition for P1 = 0.1–0.12 MPa, Q = 0.7–0.8 m3/h.
3.2. Experimental setup to test the fire-suppression characteristics of the water mist
3.2.1. Test system
shows the setup of experiment for fire suppression in roadway. The main instruments were a scale, an oil container, temperature sensors and carbon monoxide transducer (GTH1000, China Coal Science and Industry Group Chongqing Research Institute CO. LTD). The self-built roadway was 3 m × 30 cm × 30 cm, and was covered with an insulating layer on three sides. Toughened glass at the front of the setup provided for observation. The room temperature was 15 °C.
3.2.2. Experimental procedure
The simulated roadway was stabilized and eight temperature sensors were fixed as shown in . The diameter of the oil container R was 6 cm and its height h was 4 cm. The oil depth d4 was 2cm. The tested heat-release rate was characterized by a mass combustion rate, and was 3 g·m−2·s−1, and its HRR was 1560W when the kerosene was completely burned.
The water-mist generating system was regulated under working conditions of P1 = 0.06 MPa, Q = 0.6–1.0 m3/h to obtain three PSDs with V99 = 98 µm, 498 µm and 1013 µm based on the former experiment.
The oil was burned and the temperatures was recorded every 5 s. The water-mist system was run at the given working conditions to produce a water mist with a PSD V99 = 98 µm, 498 µm and 1013 µm near 100 s.
4. Results and discussion
4.1. PSD under different working conditions
shows the change in PSD with Q for different P1. We used V50 and V99 to characterize the PSD, V50 refers to some particles with diameter less than certain particle, and that their whole volume takes 50% of all the particles’. The characteristics of V99 are the same with V50. For a given P1, V50 and V99 increased with an increase in Q. During atomization, the jet velocity increased with an increase in pressure. The water membrane broke into a filament or ribbon because of the inertial force. Intensive vibrations developed from the relative motion of the water membrane lower surface tension and the viscous force itself, which twisted and shortened the liquid membrane and converted the water to droplets.
Figure 3. Relationship between PSD and Q and P1.
Water mist with different working parameters is shown in .
4.2. PSD along axial line
As shown in , the distribution of jetting flow in an open space can be divided into three zones: (1) a jetting core zone, (2) a transition zone and (3) a fully developed zone.
(6)
(6)
Where Sn-length of jetting core zone, cm; r-radius of outlet, 0.01 m; β-turbulence coefficient, 0.08 for cylindrical tube.
It can be calculated from EquationEquation (6)(6)
(6) :
The PSD was obtained for the given working conditions: Q = 0.8 m3/h, P1 = 0.16 MPa (). V50 and V99 decreased with an increase in d. When d < Sn, the PSD was larger and decreased rapidly. Then PSD decreased slowly when Sn<d < 50 cm. When d > 50 cm, water was atomized completely and the particle size remained stable.
The PSD results indicate that water was atomized partly in an atomization device, and the rest of the water continues to atomize in an open space as a function of the air-splitting force ().The falling speed of the droplet was maintained at a large value near the centerline. It began to fall away from the centerline and became stable at the edge. This was because the droplets near the centerline had a greater momentum, after leaving the centerline, the interaction between droplet and air increased, and also the air resistance reduced the falling speed of the droplet. When the droplet reached the edge of the water mist field, the droplet was basically balanced by resistance and gravity, and the falling speed of the droplet tended to be stable.
4.3. Effect of water-mist particle size on fire suppression
Temperatures (Ti, i = 1, 2…8) along the simulated roadway were measured for different PSDs (V99 = 98, 498, and 1013 µm). We chose T1 and T5 to represent the test-point temperatures. T5 was located to the top right of the burning oil, and its temperature was the highest, which illustrates the suppression effect clearly. T1 represents the surrounding temperature. Other temperatures were changed in the range of [T1, T5].
showed the temperature changes of testing points over 140 s. Temperatures increased initially and dropped rapidly after water-mist addition. When first applied, the momentum of the water mist increased the disturbance to the flow field, which would increase the turbulent combustion velocity. Therefore, the flame cannot be effectively suppressed but strengthened, so the temperature rose at first. When the mist continued to move downwards and entered the high-temperature plume, it would be heated and evaporated to generate a large amount of water vapor absorbing a large amount of heat, which can effectively reduce the temperature.
5. Conclusions
The PSDs of water mist under different working conditions and the water-mists’ fire-suppression characteristics were investigated and measured. Conclusions are as follows: The water-mist particle size depends mainly on air pressure and water flow volume, which increases with an increase in water flow volume and air pressure. Under given working conditions, the PSD along the axial line consisted of two sectors: a wavy flow zone and a fully atomized zone. Water mist with various PSDs could suppress fire, but the detailed mechanism needs to be studied and validated.
Additional information
Funding
References
- Cheng W, Hu X, Xie J, Zhao Y. 2017. An intelligent gel designed to control the spontaneous combustion of coal: Fire prevention and extinguishing properties. Fuel. 210:826–835.
- CMRI. 2004. Studies on Simulation of Open Fires in a Mine Gallery under Varied Airflow for Suppression of Fire and Explosions in Underground Coal mines.116.
- Downie B, Polymeropoulos C, Gogos G. 1995. Interaction of a water mist with a buoyant methane diffusion flame. Fire Saf J. 24(4):359–381.
- Heskestad G. 2002. Scaling the interaction of water sprays and flames. Fire Saf J. 37, 37(6):535–548.
- Jones A, Nolan PF. 1995. Discussions on the use of fine water sprays or mists for fire suppression. J Loss Prev Process Ind. 8(1):17–22.
- Kong B, Li Z, Wang E, Lu W, Chen L, Qi G. 2018. An experimental study for characterization the process of coal oxidation and spontaneous combustion by electromagnetic radiation technique. Process Saf Environ Protect. 119:285–294.
- Liang CL. 2010. Cause analysis and preventive measures for several very large coal mine fire accidents. West China Technol. 09(13):18–19.
- Liu Z, Kim AK. 2001. A review of water mist fire suppression technology: Part II Application Studies. J Fire Protect Eng. 11(1):15–42.
- Loomis M, Mcpherson MJ. 1995. Application of water mist for the control of fuel rich fires in model coal mine entries. Proceedings of the 7th US Mine Ventilation Symposium; p. 225–230.
- Mawhinney JR. 1993. Design of water mist fire suppression systems for shipboard enclosures. Boras, Sweden: Swedish National Testing and Research Institute.
- Mawhinney JR. 1997. Fire protection water mist suppression systems, fire protection handbook. 18th ed. Quincy, MA: NFPA.
- Mawhinney JR, Back GG. 1998. Bridging the gap between theory & practice: practice: protecting flammable liquid hazards using water mist fire suppression systems, Fire Suppression and Detection Research Application Symposium, Orlando, Orlando, Florida.
- Mawhinney JR, Dlugogorski BZ. 1994. A closer look at the extinguishing properties of water mist, 4th International Association for Fire Safety Science (IAFSS) Conference, Ottawa, Canada; p. 13–17.
- Mawhinney JR, Richardson JK. 1996. A state-of-the-art review of water mist fire suppression research and development, Internal Report No.718, National Research Council Canada.
- Mawhinney JR, Richardson JK. 1997. A review of water mist fire suppression research and development, 1996. Fire Technol. 33(1):54–90.
- National Fire Protection Association. 2006. NFPA 750 Standard on water mist fire protection systems. 2006 Edition. Quincy, MA: An International Codes and Standards Organization. 7.
- Ray SK, Singh RP. 2007. Recent developments and practices to control fire in underground coal mines. Fire Technol. 43(4):285–300.
- Ray SK, Singh RP. 2005. Effects of water mist on open fire–a model study. Min Technol. 114(1):1–A12.
- Ren W, Shi J, Guo Q, Zhao Q, Bai L. 2017. The influence of dust particles on the stability of foam used as dust control in underground coal mines. Process Saf Environ Protect. 111:740–746.
- Ren W, Guo Q, Wang Z. 2016. Application of foam–gel technology for suppressing coal spontaneous combustion in coal mines. Nat Hazards. 84(2):1207–1218.
- Ren WX, Guo Q, et al. 2016. Design and application of device to add powdered gelling agent to pipeline system for fire prevention and suppression in coal mines. J Loss Prev Process Ind. 41:147–153.
- Ren XW, Wang FZ, Guo Q, Zuo ZB, Fang QS. 2015. Application of foam-gel technique to control co exposure generated during spontaneous combustion of coal in coal mines. J Occup Environ Hyg. 12(11):D239–D245.
- Yuan LM, Lazzara CP. 2004. The effects of ventilation and preburn time on water mist extinguishing of diesel fuel pool fires. J Fire Sci. 22(5):379–404.