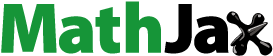
Abstract
Manufacturing of commercialized silicate is a highly polluting source in geopolymer production. To reduce these emissions, rice husk ash has been considered as an option for synthesizing alternative silicate. However, available research has been focused on the study of geopolymer pastes and mortars, but unknowns remain on its reliability to manufacture plain geopolymer concrete, motivating this research. Goals were synthesizing an unfiltered-alternative sodium silicate from rice husk ash at room conditions (21 °C − 65 ± 5%RH − atmospheric pressure) for manufacturing plain ambient-cured geopolymer concrete and assess its engineering properties. Results shown that the proposed concrete reached 21 MPa, 17959 MPa, 0.183, and 2.13 MPa for 28-day compressive strength, modulus of elasticity, Poisson’s ratio, and splitting tensile capacity, respectively. Results also portrayed that all these properties of the proposed concrete were comparable to those of geopolymer concrete with commercial silicate and traditional Portland-cement concrete. Its elasticity modulus was 44% higher than that of the geopolymer concrete with commercial silicate, which is considered as serviceability proxy. Based on the results, three equation models were developed to predict the engineering properties of the proposed concrete. Results demonstrate that the use of alternative silicate from rice husk ash provides an innovative-cheaper and eco-friendlier geopolymer concrete exhibiting suitable properties for structural applications.
Alternative sodium silicate from rice husk ash has not been assessed in geopolymer concrete
An alternative sodium silicate from rice husk ash was prepared at room temperature
Geopolymer concrete shows 44% higher modulus of elasticity with alternative silicate
Empirical models were developed to predict the engineering properties of the geopolymer concrete with alternative silicate
Geopolymer concrete with alternative silicate is reliable for structural applications
HIGHLIGHTS
1. Introduction
Geopolymers are a sustainable alternative for binder production in comparison to traditional cementitious systems. The reaction between aluminosilicate materials (precursors) and an alkaline activator solution with pH > 13 produces this synthetic material called ‘geopolymer’ (Davidovits, Citation1991). Sources of aluminosilicates can be natural such as kaolinitic clays, volcanic ash, metakaolin, etc., or industrial such as fly ash, blast furnace slag and red mud (Demir & Derun, Citation2019). As alkaline solution, the combination of sodium silicate (waterglass) and sodium hydroxide has been widely used. Being one-part of the alkaline solution, commercial sodium silicate aids to provide high mechanical strength to geopolymers, along with reduced permeability and a stable structure (Fernandez-Jimenez & Palomo, Citation2005). Nonetheless, its manufacture is cost-expensive and energy-intensive releasing considerable greenhouse gases to the atmosphere, being neither economical nor sustainable (Bajpai et al., Citation2020). This manufacture comprises melting sodium carbonate and quartz sand at high temperatures ranging between 1000 and 1500 °C (Liu & Ott, Citation2020), which derives in roughly 1.514 kg CO2 emissions per kg of silicate produced (Turner & Collins, Citation2013). In addition, this generates air pollution and land erosion due to the exploitation of mines (Novotny et al., Citation1991). Alternative sources of silica such as rice husk ash may help to reduce the environmental and economic impacts of sodium silicate manufacture, due to its low cost and high silica content for geopolymerization (>80%). Rice husk ash is an agricultural by-product that comes from burning rice husk at temperatures between 600 and 800 °C for power generation; nowadays its global production reaches 7.5 million tons annually (Mosaberpanah & Umar, Citation2020).
Rice husk ash has recently been studied for processing alternative silicate solutions in geopolymer production. This has been encouraged to reduce the high polluting emissions and costs derived by the manufacture of commercial sodium silicate, as well as for greener disposal of copious rice husk ash worldwide. Previous studies (Passuello et al., Citation2017; Bernal et al., Citation2012; Kamseu et al., Citation2017; Mejía et al., Citation2016; Tchakouté et al., Citation2016; Bernal et al., Citation2015; He et al., Citation2013; Rajan & Kathirvel, Citation2021; Villaquirán-Caicedo et al., Citation2017) synthesized geopolymer pastes and mortars by alternative silicate from rice husk ash focusing only on the microstructure, compressive and flexural strengths. However, fundamental engineering properties of these geopolymers on a concrete scale such as compressive strength evolution, tensile strength capacity, modulus of elasticity, and Poisson’s ratio have not yet been studied to the best knowledge of the authors; this has left open a void to further deepen into the performance of this alternative silicate when tailored for field applications. Paste, mortar and concrete behaviors are not directly comparable because of the different size and geometry of aggregates used in each one, i.e. current results reported in pastes without aggregate, and mortars with fine aggregate, will not be the same to those obtained from concrete having fine and coarse aggregates. In addition, its properties also cannot be fully predicted by knowing only the chemical composition or activity index of the rice husk ash. The state-of-the-art (Passuello et al., Citation2017; Bernal et al., Citation2012; Kamseu et al., Citation2017; Mejía et al., Citation2016; Tchakouté et al., Citation2016; Bernal et al., Citation2015; He et al., Citation2013; Rajan & Kathirvel, Citation2021; Villaquirán-Caicedo et al., Citation2017) shows that many of the alternative silicate solutions were prepared by mixing rice husk ash with aqueous hydroxides under processing conditions of high temperatures (100-200 °C), longer stirring durations (from one to 640 hours), and filtration processes, via fusion, hydrothermal/hydrothermobaric, reflux or thermochemical processes. Although these conditions greatly increase the dissolution of rice husk ash into the alternative silicate as well as the formation of more soluble silica capable to enhance the geopolymerization reactions (Kamseu et al., Citation2017), these could increase the embodied energy consumption, cost, the processing time, and the environmental impact of this initiative as well. Instead, the processing at room conditions of unfiltered-alternative silicate solutions using a high alkalinity environment could be an efficient solution in energy, monetary, duration, and environmental terms, without a considerable reduction of the overall geopolymer performance. These conditions also promote high dissolution of the rice husk particles, formation of silicate species that enhance the geopolymerization at room temperature (Kamseu et al., Citation2017; Rajan & Kathirvel, Citation2021), as well as the availability of unfiltered residues and undissolved rice husk particles acting as fillers to increase the geopolymer compactness and the interfacial reactions between solid particles during the hardening (Kamseu et al., Citation2017; Autef et al., Citation2012).
Given the growing interest in using alternative activators for geopolymer production, which is in line with current sustainable trends, this work studies the total replacement of commercial sodium silicate by an alternative sodium silicate from rice husk ash for manufacturing plain ambient-cured geopolymer concrete. To this end, two geopolymer concretes were produced by activating them with two alkaline solutions: (i) alkaline solution based on commercial sodium silicate, and (ii) alkaline solution based on alternative sodium silicate from rice husk ash. The latter was prepared under practical room conditions (21 °C, 65 ± 5% RH, atmospheric pressure), without filtration processes, and using a high alkalinity environment. Also, a traditional cement-based concrete was manufactured as a benchmark. All concretes were designed with a comparable nominal compressive strength of 25 MPa, tracked by means of 135 laboratory tests in fresh and hardened states. Their behaviors were compared in terms of the engineering properties workability, microstructure, compressive strength evolution, splitting tensile capacity, modulus of elasticity and Poisson’s ratio, from where conclusions were driven. This innovative study encourages one proper way to manage one copious agro-industrial waste such as rice husk ash which is underutilized and low stockpiled, being commonly dumped into landfills and water sources resisting natural degradation, which causes pollution and major disposal problems to the environment. Beyond this, it assesses the possibility of using an alternative sodium silicate from rice husk ash for manufacturing ambient-cured geopolymer concrete to be tailored in field applications.
The main novelties of this work are: (i) Assessing the behavior of plain ambient-cured geopolymer concrete based on a rice husk ash-derived activator and focus on the engineering properties of workability, compressive strength evolution, splitting tensile capacity, modulus of elasticity, and Poisson’s ratio. (ii) Developing a set of empirical models to predict with confidence the compressive strength evolution up to a 28-day age, the modulus of elasticity, and the splitting tensile capacity of the proposed concrete. (iii) Presenting behavioral values and trends for boosting the existing database about geopolymers from rice husk ash-derived activators. To the best knowledge of the authors, these features has not been studied in the current state of art and will be very useful to incorporate plain ambient-cured geopolymer concrete activated by alternative silicate from rice husk ash in field applications as well as to evaluate its reliability.
2. Experimental program
The experimental program comprised the evaluation of three types of concrete hereinafter labelled as (a) geopolymer concrete activated by commercial silicate-based solution (GC); (b) geopolymer concrete activated by alternative silicate from rice husk ash (GA); and (c) traditional cement concrete (TC) -the benchmark-.
2.1. Raw materials and alkaline solutions
As-received ASTM Class F fly ash (ASTM C 618-22, Citation2022) provided by the Termo-Paipa power plant (Paipa, Boyacá, Colombia) was grinded until reaching an average particle size of 10 μm and particle density of 2.25 g/cm3. Blast furnace slag provided by Acerías Paz del Río (Steel factory located in Nobsa, Boyacá, Colombia) was grinded to an average particle size of 12 μm and particle density of 2.85 g/cm3. Rice husk ash coming from the rice mill La Esmeralda (Jamundí, Valle del Cauca, Colombia) was obtained through open heat treatment at 700 °C in a spontaneous combustion kiln which had an original particle size of 125 μm, but was reduced by grinding to an average size of 12.5 μm and particle density of 2.10 g/cm3. Grinding of the materials was performed in a ball mill using 50 mm diameter steel balls, milling media to powder ratio of 10:1, and grinding time of 60 min at speed of 350 rpm (Hamidi et al., Citation2014). SEM images of grinded fly ash, slag, and rice husk ash are shown in . It is evident from the figure that after grinding the fly ash retains some spherical shape, the slag keeps angular forms, and the rice husk ash presents an irregular morphology and a rough surface, also exhibiting some agglomerations. The general-use cement (Type GU) complied with ASTM C1157-20 ASTM C 1157-20, ASTM C 1157-20, (ASTM C 1157-20 Citation2020) and had a particle density of 2.88 g/cm3 and an average size of 45 μm. River sand was chosen as fine aggregate with a maximum size of 4.75 mm and fineness modulus of 3.04, while fine grey gravel with a Nominal Maximum Size (NMS) of 12 mm was selected as coarse aggregate; granulometric curves and other aggregate physical properties are depicted in and . In general, the particle size distributions of the aggregates partially meet the requirements of the ASTM C33-18 gradation standard (ASTM C 33-18,18, Citation2018) for structural concrete purposes. Commercial sodium silicate (Na2SiO3) of industrial-type had 9.1% Na2O, 27.5% SiO2, and 63.4% H2O, with SiO2/Na2O ratio of 3.02. The sodium hydroxide (NaOH) was prepared under laboratory conditions by dissolving caustic soda flakes (98% purity) (Technical Data sheet Panreac PA-ACS-ISO, Citation2020) in distilled water to obtain a concentration of 16 M.
Figure 1. SEM micrographs for: (a) grinded fly ash, (b) grinded blast furnace slag, (c) grinded rice husk ash.
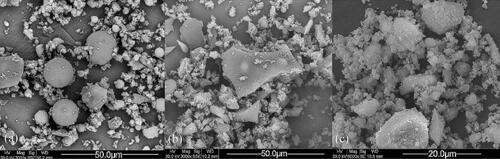
Table 1. Physical properties of fine and coarse aggregates.
presents the chemical characterization of the fly ash, slag, rice husk ash, and cement by X-ray fluorescence tests (XRF). Results showed that the fly ash had Fe2O3=7.3% (<10%), CaO = 1.3% (<8%), loss on ignition = 4.9% (<5%), and SiO2+Al2O3+Fe2O3=79% (>70%), which confirms a proper composition to guarantee cementitious properties in geopolymer (ASTM C 618-22, Citation2022; Fernández-Jiménez & Palomo, Citation2003). Slag had alkaline coefficients 1.3 ≤ CaO/SiO2=1.3 ≤ 1.4, 0.1 ≤ Al2O3/SiO2=0.4 ≤ 0.6, 1.0≤(CaO + MgO)/(SiO2+Al2O3)=1.0 ≤ 1.3, (CaO + MgO)/SiO2=1.4 (≥1.4), (CaO + MgO + Al2O3)/SiO2=1.7 (>1.0), SO3=0% (≤3%), and MgO = 1.4% (≤8%), indicators of its good hydraulic properties for geopolymerization (Pal et al., Citation2003). Finally, rice husk ash had SiO2=90.9% (>80%) which is ideal to assure high silica content in geopolymer (Mosaberpanah & Umar, Citation2020; Yaseri et al., Citation2019). shows that fly ash, slag and rice husk ash meet the allowable loss on ignition content (<6%) prescribed by ASTM C618-22 (ASTM C 618-22, Citation2022). GU cement contains the common oxides reported elsewhere (Neville, Citation2004).
Table 2. Chemical composition of raw materials.
The mineralogical characterization of fly ash, slag, rice husk ash, and cement by X-ray diffraction tests (XRD) is shown in and quantified in . The pattern obtained for the fly ash allowed to identify 38.1% crystalline content highlighted on the spectrum by multiple peaks, and a broad hump or diffused halo which reflected 61.9% amorphous content at 2θ ≈ 19°-30°. Two phases composing the crystalline content of the fly ash were observed: quartz (SiO2) and mullite (Al4SiO8). These are reported as the most common in the literature for fly ash and found in small percentages when compared to amorphous content (≈ 5-25 wt.%) (Velandia et al., Citation2016). The diffraction pattern of the slag indicated 37.3% crystalline content associated with phases gehlenite (Ca4Al4.12Si1.90O14) and magnesium oxide (MgO), as well as a diffused halo centered at 30° 2θ reflecting 62.7% amorphous content. The rice husk ash pattern exhibited 55.3% crystalline content linked to a unique cristobalite phase (SiO2), as well as a diffused halo centered at 22° 2θ reflecting 44.7% amorphous content. This depicts a low amorphous silica content in comparison to the desirable one for producing alternative activators, i.e. >80% (Alnahhal et al., Citation2021). Finally, the GU cement contains the common crystalline phases reported elsewhere (Neville, Citation2004).
Table 3. Mineralogical composition for raw materials.
Two alkaline solutions were produced in this study based on previous trials and literature results: (i) an alkaline solution based on commercial silicate, and (ii) an alkaline solution based on alternative silicate from rice husk ash. The former solution comprised 71.5 wt.% commercial sodium silicate plus 28.5 wt.% sodium hydroxide 16 M, having a sodium silicate to sodium hydroxide mass ratio of 2.5, liquid/solid ratio of 1.5, SiO2/Na2O molar ratio (silica modulus) of 1.0 and H2O/Na2O molar ratio of 10.6 (Hardjito & Rangan, Citation2005). The latter solution comprised 15 wt.% rice husk ash plus 85 wt.% sodium hydroxide 16 M, exhibiting a liquid/solid ratio of 0.85, SiO2/Na2O molar ratio (silica modulus) of 0.32 and H2O/Na2O molar ratio of 4.0. Although lower liquid/solid ratios close to 0.50 were used in the alternative silicate for geopolymer paste preparation reflecting higher rice husk ash amount (Bernal et al., Citation2012; Mejía et al., Citation2016), the high ratio of 0.85 was adopted in this study to attain proper workability of the geopolymer concrete mix and the mobilization of alkali ions during the mixing based on previous trials; workability in geopolymer concrete is more critical than in geopolymer paste due to the presence of coarse and fine aggregates in the batch. Moreover, the SiO2/Na2O ratio (silica modulus) of 0.32 selected for the alternative silicate was driven from Tchakouté et al. (Citation2016). Lastly, the high alkalinity environment of NaOH 16 M in both alkaline solutions was provided for both the crystalline and the amorphous contents into the raw materials to participate in the geopolymerization at room temperature (Kamseu et al., Citation2017; Rajan & Kathirvel, Citation2021; Autef et al., Citation2012).
The alkaline solution based on commercial silicate was premixed and stored 24 hours prior to the manufacture of the specimens. The alkaline solution based on alternative silicate from rice husk ash was processed under room conditions (21 °C, 65 ± 5% RH, atmospheric pressure), continuously stirring the rice husk ash and sodium hydroxide solution over 30 minutes to promote the dissolution of the husk particles, and then stored for a week prior to the manufacture of the specimens, without any filtration processes.
2.2. Concrete mixtures
All concretes (TC, GC and GA) were designed for a nominal compressive strength fixed to 25 MPa for comparison purposes. This implied a water/cement ratio of 0.45 for TC concrete, and liquid/solid ratios of 0.35 and 0.30 for GC and GA concretes, respectively. GC geopolymer concrete was activated with the alkaline solution based on commercial silicate, while GA was activated with the solution of alternative silicate from rice husk ash. Both GC and GA geopolymer concretes were based on the blended precursor 80 wt.% grinded fly ash and 20 wt.% slag; this combination was previously validated to prompt good mechanical performance in ambient-cured fly ash geopolymer concrete (Lee & Lee, Citation2013; Deb et al., Citation2014). These two also had comparable SiO2/Al2O3 molar ratios fixed to 5.5 as this parameter is the most relevant for achieving the required geopolymer performance. Such data make evident that even if the features of each activator and the geopolymer mix formulations differ (refer to Subsections 2.1 and 2.2), both the nominal compressive strength and the SiO2/Al2O3 molar ratio fixed equal for GC and GA geopolymer concretes enable their straightforward comparison. Proportions of the concrete mixtures are shown in , which were adjusted based on aggregate properties and previously reported results (Cardenas-Pulido et al., Citation2020; Hardjito et al., Citation2005).
Table 4. Proportions of concrete mixtures.
During the casting of geopolymer concretes, the aggregates and raw materials were dry-mixed for five minutes, followed by the addition of the alkaline solutions and ending with a 20-minute mixing process to increase the dissolution of the raw materials. This procedure was similar for the traditional cement concrete. Each fresh mixture was poured into 150 × 300-mm metallic cylinder molds, tamped and compacted properly by traditional methods, as per the guidelines of ASTM C192-19 (ASTM C 192-19 Citation2019). The specimens were demolded after 48 hours and cured at room temperature (21 °C, 65 ± 5% RH) until the day of the tests. shows the typical appearance of the casted specimens.
2.3. Test setup and instrumentation
In total 135 characterization tests were carried out on GC, GA, and TC concretes to determine and compare their engineering properties. The tests are described throughout the following sections.
2.3.1. Isothermal calorimetry
Per 2010 BS EN 196-9 (BS EN 196-9 Citation2010), the heat evolution of pastes from concrete mixtures was measured using a calorimeter to gather information about the ongoing hardening reactions. This procedure consisted of preparing fresh pastes at the same water/cement or liquid/solid ratios as their companion concretes and to cast them into expanded polyethylene recipients. These were then placed inside Dewar flasks and sealed. The temperature evolution of the samples was obtained from thermocouple measurements every 5 minutes for 72 hours.
2.3.2. X-ray diffraction
Mineralogical characterization of the raw materials and paste samples extracted from hardened concretes was accomplished by quantitative X-ray diffraction, employing a diffractometer with Cu-Kα monochromatic radiation wavelength of 1.5406 Å in a Bragg-Brentano geometry. The paste samples were obtained by scraping the surfaces of the hardened concretes, and the powders were finely ground using a ceramic mortar and pestle to a 75 μm particle size at fineness of 4500 cm2/g. A goniometer in θ/θ configuration was used in a scanning range 2θ between 15° and 120°, at a pitch and pitch time of 0.02° and 2 seconds, respectively. That range was selected based on main mineralogical information of rice husk ash-based geopolymers found there (Mejía et al., Citation2016; Tchakouté et al., Citation2016). Different crystalline phases of the samples were identified by diffraction peaks in the obtained patterns and compared with the COD-2016 database (Crystallography Open Database). An external standard method was also used to obtain the instrumental K-factor of the equipment through Rietveld refinement on a high crystallinity standard; 10 wt. % spike of rutile was used as the high crystallinity standard. The K-factor stored the crystallinity configuration of the internal standard and was then applied to the obtained patterns to determine the amorphous phases.
2.3.3. Workability
Slump, unit weight and air content tests were conducted to characterize the fresh state of the concrete mixtures according with standards ASTM C143-20 , (ASTM C 143-20 Citation2020) and ASTM C138-17, (Citation2017) Rheology tests on pastes from concrete mixtures were also performed under controlled rate mode (CR) to assess the yield stress and the plastic viscosity for each mix according to the Binghamian rheological model. The preparation of the pastes was the same as for the isothermal calorimetry test.
2.3.4. Mechanical tests
Compressive strength of concretes at different ages (3, 7, 14, 28 days) was measured using the 150 × 300 mm cylinder specimens, per standard ASTM C39-21 , (ASTM C39-21 Citation2021). The modulus of elasticity, Poisson’s ratio, and splitting tensile strength of concretes were also estimated from the cylinder specimens after 28-days days as per recommendations of ASTM C469-22 , (ASTM C469-22 Citation2022) and ASTM C496-17 ,(ASTM C 496-17 Citation2017), respectively.
2.3.5. SEM/EDS analysis
Scanning electron microscopy analysis (SEM) through a microscope at an accelerating voltage of 30 kV, allowed the inspection of microstructural features of the raw materials and paste samples extracted from hardened concretes after 28 days. The preparation of the paste samples was the same as for the X-ray diffraction test. In addition, energy-dispersive X-ray spectroscopy (EDS) was used to obtain semi-quantitative chemical analyses at different sampling spots.
To consider the variability of the experimental data, three replicas were made of each test for every type of concrete. Statistical parameters such as the arithmetic mean (X), the coefficient of variation (CV) and standard deviations showed in a graphical form were calculated to support trustfulness the results.
3. Results and discussion
Results of the tests performed on all the concretes are presented and analyzed in this section. To get a better understanding of the performance of the geopolymer concretes, their results are compared against those of traditional cement concrete and reference values from the literature.
3.1. Isothermal calorimetry
summarizes the temperature increase, cumulative heat, and heat flow evolution curves overtime for the pastes from concretes mixtures. confirms temperature increases of 1.75, 2.62 and 7.96 °C, while indicates cumulative heats of 88.6, 73.2 and 323.8 J/g for the TC, GC, and GA pastes, respectively. In addition, results in reveal, maximum heat flows of 0.58, 0.91 and 3.46 mW/g occurring in reaction times of 24.4, 7.8 and 2.8 h (outcomes are mentioned in the same order as before). It is clear from that the GA paste presented the highest temperature increase, cumulative heat and heat flow. This can be ascribed to the high amount of Na2O from the alternative silicate required to geopolymerize the GA paste at ambient curing, which in turn generated a high early exothermic reaction. The lower normalized molar ratios SiO2/Na2O and H2O/Na2O of the alternative silicate vs. the commercial solution (see Subsection 2.1) allow to prove the high amount of Na2O in the GA paste than GC paste as well as support its high heat release. Tong et al. (Citation2018) also observed that geopolymer pastes activated by rice husk ash-derived silicate exhibited higher cumulative heat and heat flow than pastes activated by commercial silicate. shows an early peak temperature of the GC and GA pastes which is related to the wetting and dissolution of the precursors, as well as complexation between initial dissolved silicate units and calcium and sodium ions in the activator (Bernal et al., Citation2011). Puligilla and Mondal argued that the occurrence of that first peak in geopolymers is also associated with the C-S-H gel precipitation from slag, which causes initiation and acceleration of the hardening during the first 60 to 80 minutes of reaction (Puligilla & Mondal, Citation2013). This suggests that the early stage of heat evolution in fly ash slag geopolymer is ascribed to the slag hydration, considering that fly ash geopolymerization is extremely slow at room temperature exhibiting a dissolution-precipitation reaction (Kumar et al., Citation2010; Winnefeld et al., Citation2010). However, the higher peak temperature for the GA paste compared to GC in cannot be attributed to its rapid hardening (referring to GA); in fact, replacement of commercial sodium silicate by alternative silicate generates slow release and low availability of silicate species in the geopolymer and the delay of its hardening. Instead, this peak temperature is justified by a higher dissolution of the raw materials because of the higher pH of the pore solution triggering high heat release (Ravikumar & Neithalath, Citation2012).
Figure 5. Calorimetric responses for pastes of concrete mixtures: (a) temperature increase vs. time, (b) cumulative heat vs. time, (c) heat flow vs. time (12 h), (d) heat flow vs. time (50 h).
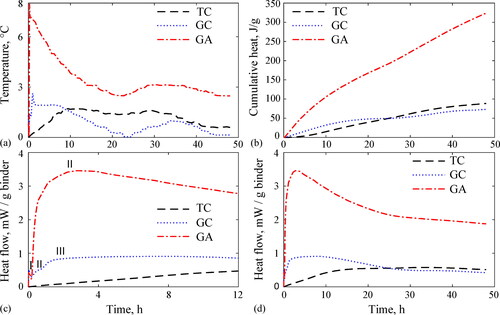
also shows that after the first peak, the temperature for the GC and GA pastes drops steadily until reaching a dormant period after 23 hours. This drop is associated with the induction of the pastes (Puligilla & Mondal, Citation2013). This means that newly formed reaction products grow rapidly and deposit on the surface of the unreacted slag particles, creating a barrier layer that limits the amount of alkali available for dissolution and the heat release of the reaction (Gao et al., Citation2015). Then, the continuous supply of alkalis penetrates through that barrier layer and the reaction proceeds. A second peak temperature of smaller magnitude occurs after approximately 35 hours for the GC and GA pastes (refer to ), which is highly influenced by the slag content in geopolymer systems (Puligilla & Mondal, Citation2013). This peak can be linked to the reaction acceleration and the formation of further cementing products in the GC paste, such as the calcium aluminosilicate hydrate (C-(A)-S-H) gel and the sodium aluminosilicate hydrate (N-A-S-H) i.e. geopolymer gel (Puligilla & Mondal, Citation2015). For the GA paste, this peak (of greater magnitude) may be mainly attributed to the high concentration of Na2O in the alternative silicate raising the reaction temperature (similar to the description of the first peak), rather than to the formation of cementing products. This conclusion was confirmed by the slow compressive strength evolution at early ages of the GA concrete when compared with that of the GC, ascribed to the slower release rate of silicates necessary for initial hardening reactions (see Section 3.4). It should be noted that the temperature curves in represent several ongoing overlapping reactions (Kumar et al., Citation2010; Winnefeld et al., Citation2010), and that the highest temperature peaks of the GA paste do not necessarily indicate increased amounts of reaction products linked to higher mechanical strengths (Winnefeld et al., Citation2010; Xu et al., Citation2014). Likewise, the early heat peak may be related to the physical progress of the reaction rather than to chemical progress (Gao et al., Citation2015). Accordingly, the gain of mechanical strength depends not only on the early dissolution stages but also on the subsequent reaction stages linked to the formation of the geopolymer gel (Kumar et al., Citation2007).
Concerning the heat flow, shows that the TC paste exhibits the typical behavior reported elsewhere, i.e. a main peak of the tricalcium silicate phase hydration (C3S) followed by a minor point of the tricalcium aluminate phase hydration (C3A) (Mindess et al., Citation2003). Nevertheless, these peaks are not clearly visible in given the high water/binder ratio of 0.45 of these particular samples. In addition, for none of the pastes was it possible to fully record the first heat peak generated from the immediate contact between the liquid and the solid materials as evidenced in . This was due to the time required for the external preparation of the pastes and their assembly in the calorimeter. However, a small part of that first peak for the GC and GA pastes were registered and labelled as peak I in . This figure also shows two additional peaks for the GC paste (labelled II and III), and only an additional one for GA (tagged as II). A greater number of heat peaks taking place in the GC paste could confirm its rapid hardening and an additional formation of cementing products at early ages when compared with the GA paste. Overall, the occurrence of the initial heat peaks (I and II) for the GC and GA pastes is similar, correlating well with the similar 28-day mechanical strength between these two concretes (see Section 3.4). This suggests that the reaction mechanisms of GC and GA geopolymers are similar, except for the slower reaction kinetics and maturation of the GA geopolymer at early ages (see Section 3.4) and its higher heat release. The latter should be addressed to avoid temperature-cracking issues.
3.2. X-ray diffraction
plots the X-ray diffraction patterns of the GC and GA pastes extracted from hardened concretes, while lists their mineralogical compositions. and prove that commercial and alternative silicate activators alter comparably the phase grouping of the precursors. GC paste evidenced crystalline phases of quartz, mullite, and gehlenite inherited from fly ash and slag, but they were attenuated due to their partial dissolution during the geopolymerization reactions (compare crystalline contents in and ). For the GC pattern, a calcium carbonate polymorph called calcite (CaCO3) was evidenced from the partial carbonation of the slag. In both GC and GA pastes, there is a slight change in the broad hump of the raw fly ash due to the geopolymerization reactions, which causes a movement from a centered position at roughly 23° 2θ to slightly greater 2θ angles (Provis et al., Citation2005). The presence of this particular hump between 20° and 40° centered on approximately 28° 2θ is distinctive of short-range order aluminosilicate and calcium gels formed in GC and GA pastes, i.e. amorphous material providing the mechanical strengths. Its extension is visually more prominent in the GC paste compared to the GA one, which indicates higher amorphous content as confirmed in (83% for GC vs. 69% for GA), and higher compressive strength as well (see Section 3.4). As more reactive silica is present in the silica source, there will be a broader hump in the geopolymer diffractograms indicating the increased formation of the geopolymer gel (Mejía et al., Citation2016; Velandia et al., Citation2016). It is worth mentioning that the amorphous content for GA paste in was calculated by excluding the natron and sodium carbonate beta contents from the total crystalline content since these are considered secondary products independent from geopolymerization reactions.
Table 5. Mineralogical composition for pastes from GC and GA concretes.
Regarding the diffraction pattern of the GA paste, indicates the presence of remnant crystalline phases of quartz, mullite, and cristobalite inherited from the raw materials, suggesting these phases were partially dissolved (compare crystalline contents in and ). However, these have little participation in the geopolymerization processes and act mainly as unreactive fillers in the microstructure (He et al., Citation2013). According to and , it can be stated from mixing rules that there was a 25% partial dissolution of the cristobalite from the raw rice husk ash equivalent to 15 wt.% out of the original phase (55.3 wt.%), remaining approximately 40 wt.% of undissolved cristobalite as filler in GA paste. Most of the amorphous content of rice husk ash was also converted to silicate species for the formation of amorphous aluminosilicate and calcium gels in GA paste according to mixing rules (compare amorphous contents in and ). The previous observation could indicate the good efficiency of the alternative silicate from rice husk ash in geopolymerization processes. On the other hand, also evidences newly crystalline phases in the GA pattern associated with sodium carbonates, mainly natron (Na2CO3·10H2O) and traces of beta-sodium carbonate (Na2CO3). These are indicative of efflorescence in the GA paste, caused by the slow release of silicate species from the alternative silicate at early ages, as well as by gradual geopolymerization of the precursors at room temperature. At early ages, the slow dissolution of rice husk ash does not provide enough silicate species to react with the aluminum and sodium from the alkaline solution; therefore, this type of geopolymers will be prone to efflorescence (Rajan & Kathirvel, Citation2021; Hajimohammadi & van Deventer, Citation2017). Natron compound is formed at room temperature (23 °C) and CO2 concentrations ranged between 0.03 and 0.04% (Bernal et al., Citation2012). These conditions coincide with the curing regime at room temperature of the GA concrete. In addition, natron grows inside the pores of the geopolymer and binds a large amount of water to its structure (five water molecules per Na+ cation) having a large molar volume (196.56 cm3/mol) (Bernal et al., Citation2012). This allows the natron to act as a filler product in the microstructure of the GA concrete, filling porosities and causing a reduction of the pore volume.
Efflorescence are secondary products formed by the chemical reaction between alkalis in geopolymer and atmospheric carbon dioxide (Allahverdi et al., Citation2017). These resulted in sodium carbonate salts in the form of whitish deposits, which migrated from the inside to the surface of the GA and GC concretes (even more for GA concrete as per ). The trend of geopolymers to the efflorescence formation is due to (i) high open porosity resulting in greater permeability (Škvára et al., Citation2009), (ii) excess alkali (Lloyd et al., Citation2010) and (iii) a weak adhesion between the alkalis and the geopolymer gel (Škvara et al., Citation2008). As previously reported, the role of sodium hydroxide during the alkaline activation is to generate high pH conditions for the dissolution of the raw materials by the hydroxide anions (OH–); once the geopolymer gel has been formed, the Na+ alkaline cations from sodium hydroxide remain bonded to the geopolymer gel and balance the Al– charges (Škvára et al., Citation2012). Škvára et al. (Citation2009) evaluated the susceptibility of geopolymers to efflorescence formation through nuclear magnetic resonance analysis (23Na NMR MAS), and found that the Na+ alkali cations are more bonded to the geopolymer gel in the form of Na(H2O)n+ complex rather than the direct bond of Na+ in Al at the Si-O-Al chain structure. They concluded that the bond of the Na+ alkaline cations in the Na(H2O)n+ complex is weaker than the direct one of Na+ ion, which helps to explain the ease in alkali leaching of the geopolymers and the efflorescence formation. For geopolymers cured at room temperature, the dissolution rates of the raw materials are limited, provoking alkali leaching and efflorescence formation as well (Temuujin et al., Citation2009). In fact, van Jaarsveld et al. (Citation1998) reported that almost the same amount of alkali hydroxide added during the geopolymer synthesis is leached from the hardened structure. Accordingly, natron and beta-sodium carbonate efflorescence in GA series can be mainly indicators of either slow geopolymerization rate or excess alkali, or even both (Temuujin & van Riessen, Citation2009).
3.3. Workability
3.3.1. Slump and rheology tests
shows the measured slump of the different concrete mixtures, and other values of geopolymer concrete mixes from reference studies (Hardjito, Citation2005; Nath & Sarker, Citation2014). On the one hand. the GC concrete exhibited the highest slump (250 mm), while GA and TC concretes registered 140 mm and 110 mm, respectively. Despite the larger values of GC and GA compared to the TC concrete, the formers had a sticky consistency; therefore, their flowability was reduced. The higher slump of the GC concrete in comparison to GA concrete is explained by the greater H2O/Na2O molar ratio of 10.10 for GC versus 4.32 for GA from the mix formulations. The unburnt carbon and residues of unfiltered-rice husk ash-based activator also lower the flowability of the GA concrete (Alnahhal et al., Citation2021). On the other hand, the flow sweep curves of pastes from concrete mixtures in reveal yield point and plastic viscosity values of 19.6 Pa–0.43 Pa·s, 16.8 Pa–8.48 Pa·s, and 140.1 Pa–12.52 Pa·s respectively for TC, GC and GA. GA viscosity values are similar to those reported by Alnahhal et al. (Citation2021) for geopolymer pastes activated from rice husk ash-derived activators. The yield point represents the shear stress required to break the rest state of the mixture and produce the initial flow, whereas the plastic viscosity denotes the properties of pumpability, placement, and finishing, and is the parameter that controls the flow after the yield point has been exceeded. Rheological properties of the pastes roughly connect with the concrete slump trends and visual observations in the casting phase, e.g. GA paste shows high plastic viscosity and yield stress, and consequently low slump.
Figure 7. Results of the concrete mixtures in the fresh state: (a) slump, (b) unit weight, (c) air content.
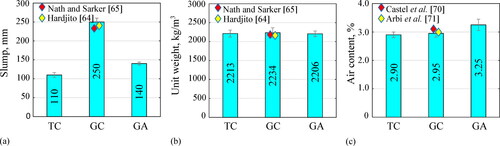
The workability results obtained for the GC and GA geopolymer concretes are consistent with those reported in the literature. Deb et al. (Citation2014) stated that silicate and hydroxide solutions are more viscous than water (up to 27 times more viscous (Alnahhal et al., Citation2021)), making geopolymer concretes more cohesive than traditional cement concretes; they also observed that the slump of fly ash geopolymer concrete decreased with the slag inclusion and with the reduction in the sodium silicate to sodium hydroxide ratio. Paya et al. (Citation1996) as well reported that a high fineness of the fly ash and slag reduces the workability of the geopolymer concrete. Hardjito and Rangan (Citation2005) suggested that the workability of geopolymer concrete is highly affected by the molarity of sodium hydroxide and the sodium silicate to sodium hydroxide ratio; similar results were reported by Rattanasak and Chindaprasirt (Rattanasak & Chindaprasirt, Citation2009). In this study, a high concentration of sodium hydroxide (16 M) was used to dissolve the raw materials at ambient curing, as performed by Hardjito and Rangan (Citation2005). Therefore, the high amount and molar concentration of sodium hydroxide plus the irregular geometry of the grinded precursors (see ) reduced the workability of the geopolymer concrete mixes. In the case of GA concrete, remnant undissolved rice husk ash particles in the alternative silicate could further affect this property because their high hygroscopic capacity is attributed to their unburnt carbon content (Hajimohammadi & van Deventer, Citation2017).
3.3.2. Unit weight and air content
show the unit weight and air content of all the concretes, as well as those reported elsewhere for fly ash slag geopolymer concretes (Hardjito, Citation2005; Nath & Sarker, Citation2014; Castel et al., Citation2016; Arbi et al., Citation2015). The variation of the unit weights among all is less than 3%, and is within the range of 2155 to 2560 kg/m3, as prescribed by ACI 318-19 for normal weight cement concrete (ACI 318-19, Citation2019). The unit weights of GC and GA with 20 wt.% slag are also consistent with those reported by Nath and Sarker (2323 to 2400 kg/m3) for fly ash geopolymer concrete having 15 wt.% slag (Nath & Sarker, Citation2017). In terms of the air content, GA presented the highest value (3.25%), followed by the GC (2.95%), and the TC (2.90%). Slightly higher values for GC and GA, than for TC concrete, are related to the greater viscosity of these fresh geopolymer concretes (Bondar, Citation2009).
3.4. Compressive strength
The 28-day compressive strength of the GC, GA and TC concretes are shown in , while the evolution of this parameter is depicted in . Overall, the highest strength was exhibited by TC concrete with 24.3 MPa, while GC and GA were 23.2 MPa and 21.0 MPa; strength variations between the GC and GA concretes with respect to TC concrete were only 4.4% and 13.4%, respectively (the difference between GC and GA concretes was only 9%). These similar values allow to reliably compare GC, GA and TC concretes in other engineering properties being the point of reference. Commercial sodium silicate enhances the mechanical strength of geopolymers, along with reduced permeability and a stable structure (Fernandez-Jimenez & Palomo, Citation2005). Nonetheless, the results in this study demonstrate that alternative sodium silicate from rice husk ash can be used instead of the commercial one for manufacturing ambient-cured geopolymer concrete, since both provide comparable 28-day compressive capacities. The 28-day compressive strength of the GA concrete is also higher than the 17 MPa lower bound prescribed by the ACI 318 Building Code (ACI 318-19, Citation2019), and hence is acceptable for structural practical applications. Results of this study match well with earlier research (Passuello et al., Citation2017; Bernal et al., Citation2012; Kamseu et al., Citation2017; Bernal et al., 2015), which identified that total replacement of commercial sodium silicate by alternative silicate from rice husk ash does not drastically reduce the compressive strength of geopolymer pastes and mortars, but rather provides comparable behaviors. The comparable 28-day compressive strength of the GA concrete with respect to the GC could be ascribed to: (i) a high release of silicate species at later ages from the alternative silicate capable of participating in the geopolymerization reaction (Hajimohammadi & van Deventer, Citation2017); (ii) presence of unfiltered residues and remanent undissolved rice husk ash particles in the alternative silicate that fill the porosities of the geopolymer concrete and cause a densified microstructure by packing (Kamseu et al., Citation2017); and (iii) slight filler effect of the natron and beta-sodium carbonate efflorescence formed (Zhang et al., Citation2014).
Table 6. Compressive strength of concretes at 28-day age, MPa.
The input oxide molar ratios of the GC and GA concretes are reported in to help explain the 28 day-compressive strength, considering that both the crystalline and amorphous contents of the raw materials may be involved in the geopolymerization under high alkalinity conditions like those of this study (Kamseu et al., Citation2017; Rajan & Kathirvel, Citation2021; Autef et al., Citation2012). These ratios are calculated as the quotients between sodium, aluminum, silicon, and calcium oxides present in the precursors and the alkaline activators. also shows suggested intervals of these ratios for which the mechanical geopolymer performance would be boosted (Kovalchuk et al., Citation2007; Davidovits & J, Citation2015; Talling & Brandstetr, Citation1989). From the table it is evident that: (i) the Na2O/Al2O3 molar ratios of the GC and GA concretes were greater than 1 and exceeded the recommended limit established by Kovalchuk et al. (Citation2007); consequently, as reported by the authors, charge imbalances between Na+ and Al3+ ions and Si-Al net negative charges may occur in the geopolymer skeleton causing efflorescence along with a lower mechanical strength (even more for the GA concrete); (ii) the Na2O/SiO2 molar ratio of the GC concrete was found to be within the interval proposed by Davidovits and J (Citation2015), but this interval was not fulfilled for the GA concrete, which could explain its lower compressive strength; (iii) the SiO2/Al2O3 ratios of the GC and GA concretes were within the Talling and Brandstetr interval (Talling & Brandstetr, Citation1989), but outside the intervals proposed by Davidovits and J (Citation2015) and Kovalchuk et al. (Citation2007). However, it was observed from previous trials that increasing the SiO2/Al2O3 molar ratio to 5.50 caused the formation of denser and more resistant microstructures of GC and GA concretes; and (iv) the CaO/SiO2 molar ratios of the GC and GA concretes were close to the interval proposed by Talling and Brandstetr (Talling & Brandstetr, Citation1989) promoting good mechanical strength in these concretes with calcium sources.
Table 7. Input oxide molar ratios (input atomic ratios) of the GC and GA geopolymer concretes.
demonstrates that the compressive strength evolution of the TC, GC concretes exhibited power-shaped curves. On the one hand, this plot confirms the rapid strength evolution of the TC concrete reaching 50% of its 28-day compressive strength at a 3-day age, when most of the calcium hydroxide was consumed for the calcium silicate hydrate formation (C-S-H gel); however, this growth dropped beyond 7 days. On the other hand, GC and GA concretes reached 30% and 11% of their 28-day compressive strengths at 3-day age. These findings confirm the slower compressive strength evolution of the GA concrete in comparison with the TC and GC concretes at early age. However, the evolution rate GA concrete rate became remarkable after 3 days, and exhibited an uprising slope until reaching a 28-day compressive strength comparable to TC and GC concretes. Further strength gain is still expected for the GC and GA concretes beyond 28 days as inferred from trends in .
The lower early-age compressive strength of the GA concrete could be ascribed to the slow-initial release rate of silicate species from the alternative silicate. Bernal et al. (Citation2015) argued that, at an initial phase, the activation mechanism of the raw materials is dominated by the different release rates from silica sources. The undissolved rice husk ash in the alternative silicate delays the availability of soluble SiO2 in the GA concrete reducing the early-age compressive strength since geopolymer mechanical performance depends on the amount of soluble Si atoms and siliceous species in the activator (clusters, colloidal structures, etc.) (Tchakouté et al., Citation2016). Kamseu et al. also suggested that the greater reactivity of the commercial silicate is related to their finer molecular silica aggregates compared to the coarser molecular compounds of the alternative silicate from rice husk ash (Kamseu et al., Citation2017). In the same way, Hajimohammadi and van Deventer (Hajimohammadi & van Deventer, Citation2017) found that rice husk ash geopolymers exhibited low compressive strength initially, but those became stronger over time as evidenced by current work. Several reasons for this behavior are that (i) rice husk ash has a low amorphous silica content (see Subsection 2.1) and releases it slowly over time (Alnahhal et al., Citation2021; Hajimohammadi & van Deventer, Citation2017), (ii) part of the crystalline silica from rice husk ash did not dissolve at early age to participate in the geopolymerization reaction (Mejía et al., Citation2016; Duan et al., Citation2015; Rajamma et al., Citation2012) and (iii) the unburnt carbon and insoluble residues of unfiltered-rice husk ash-based activator slow down the gel formation of the GA geopolymer (Alnahhal et al., Citation2021). However, as the geopolymerization proceeds and a significant amount of soluble silica takes part in the formation of the geopolymer gel at later ages, there will be a sufficient driving force or silica concentration gradient for the further silica dissolution from rice husk ash (Hajimohammadi & van Deventer, Citation2017). That implies that a greater amount of silica from rice husk ash dissolves at later ages, providing at this stage the high silica content required to enhance polycondensation and compressive strength growth (Hajimohammadi & van Deventer, Citation2017). The findings of the current study connect well with those of previous studies (Kamseu et al., Citation2017; Mejía et al., Citation2016; Tchakouté et al., Citation2016; Bernal et al., Citation2015Hajimohammadi and van Deventer, 2017; Alnahhal et al., Citation2021; Duan et al., Citation2015; Rajamma et al., Citation2012) and confirm the reliability of replacing the commercial sodium silicate by an alternative silicate from rice husk ash for manufacturing ambient-cured geopolymer concrete of acceptable compressive strength. These findings also suggest addressing the issue of the low early-age mechanical strength of the GA concrete by some reactive mineral addition or adjusting the SiO2/Na2O ratio (silica modulus) of the activator.
Based on the compressive strength results, the empirical model described by EquationEq. 1(1)
(1) is proposed to predict the compressive strength evolution up to a 28-day age, which is valid for GC and GA geopolymer concretes.
(1)
(1)
where
is the compressive strength at a specific age,
is the nominal concrete compressive strength at 28 days in MPa, and
is the age of concrete in days. After fitting EquationEq. 1
(1)
(1) to the collected data in by nonlinear regression, the constants
and
are obtained and listed in . A comparison of the proposed empirical model (EquationEq. 1
(1)
(1) ) with those presented by ACI 209R-08,08 (Citation2008) (EquationEq. 2
(2)
(2) ) and EN-1992.1.1, (Citation2004) (EquationEq. 3
(3)
(3) ) codes is shown in .
(2)
(2)
(3)
(3)
where
and
are constants depending on the type of concrete and the curing type used, respectively. For cement Type I and moist curing,
and
(ACI 209R-08,08, Citation2008). In the case of the Eurocode, the constant
depends on the type of cement and for the case of concrete with normal strength (class N cement)
(EN-1992.1.1, Citation2004). On the one hand, indicate that the models proposed by ACI 209R-08,08 (Citation2008) and EN-1992.1.1, (Citation2004) are not adequate for predicting the compressive strength evolution of GC and GA geopolymer concretes as they overestimate the strength before 28 days, and probably underestimate it beyond this time. On the other hand, the proposed model fits the experimental behaviors as shown in , with correlation coefficients (r) close to 1. Accordingly, the empirical model proposed by EquationEq. 1
(1)
(1) exhibits suitable method for predicting the compressive strength evolution of the GC and GA geopolymer concretes until 28-day age.
Figure 10. Comparison between experimental evolution of compressive strength and theoretical models for: (a) GC concrete, (b) GA concrete.
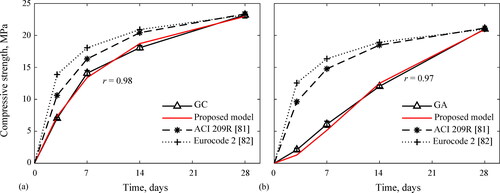
Table 8. Constants used in predicting the compressive strength evolution of geopolymer concretes.
3.5. Modulus of elasticity and poisson’s ratio
Results regarding the modulus of elasticity after 28-days are listed in . The value of TC concrete (22974 MPa) is 56% and 22% higher than that of GC (10107 MPa) and GA (17959 MPa), respectively. In addition, the value of GA concrete is 44% higher than that of the GC concrete. It is known that the modulus of elasticity of ambient-cured geopolymer concrete tends to be lower than that of cement-based concrete with similar compressive strengths (Nath & Sarker, Citation2017). Several studies (Fernandez-Jimenez et al., Citation2006; Pan et al., Citation2011; Noushini et al., Citation2016) reported that geopolymer concrete exhibit modulus of elasticity up to 50% lower than that of cement concrete, which is a concern from a mechanical point of view. This could be because N-A-S-H gels in fly ash geopolymers exhibit a lower modulus of elasticity than that of C-S-H gels in traditional cement composites (Pan et al., Citation2011). Hardjito and Rangan (Citation2005) also stated that lower curing temperatures provoke differences in crystallinity throughout the geopolymer microstructure which induces low stiffness. Lastly, fly ash slag geopolymer concrete having a small pore size experience high shrinkage and microcracks, which decrease the modulus of elasticity too (Olivia & Nikraz, Citation2012).
Table 9. Modulus of elasticity of concretes at 28-day age, MPa.
The modulus of elasticity of the GA concrete that is 44% higher than the GC concrete could be mainly credited to the filler effect of unfiltered residues and remnant undissolved rice husk ash particles into the alternative silicate which increase the axial stiffness of the GA concrete. It is well known that the elastic modulus of concrete depicts the slope of the linear-elastic branch into the compressive stress-strain relationship according to Hooke’s law; hence, it is a function not only of the concrete compressive strength but also of the concrete longitudinal strain capacity. Via filler effect, unfiltered residues and remnant undissolved rice husk ash particles from the alternative silicate greatly decrease the geopolymer deformability by increasing the microstructure confinement, but these have a lesser effect on modifying the geopolymer compressive strength (Cardenas-Pulido et al., Citation2020). Accordingly, a decreased longitudinal strain capacity of the GA concrete and subsequent gain of its axial stiffness due to fillers, let to explain the 44% higher modulus of elasticity of GA concrete than GC concrete at comparable 28-day compressive strengths. The reader should also keep in mind that strength and stiffness are completely distinct concrete properties indicating resistance to forces and resistance to deformations, respectively. To a lesser extent, the higher modulus of elasticity of the GA concrete could be credited to the filler effect of the natron and beta-sodium carbonate efflorescence formed in that concrete (Zhang et al., Citation2014). Olivia and Nikras (Olivia & Nikraz, Citation2012) argued that high silicate content can increase the elasticity of the geopolymer, which could also explain the lower modulus of elasticity of the GC concrete having a greater amount of reactive silicate species than the GA concrete. In summary, results in point out that the commercial sodium silicate can be replaced by alternative sodium silicate from rice husk ash to produce ambient-cured geopolymer concrete with an enhanced modulus of elasticity, whereas geopolymer concrete members with this mechanical enhancement could experience less deflection, creep, vibration, and fatigue from externally applied loads, improving serviceability.
There are several models to predict the modulus of elasticity of traditional cement concrete and the geopolymer concrete for different precursors and curing conditions as shown in Appendix A (Hardjito & Rangan, Citation2005; Lee & Lee, Citation2013; ACI 318-19, Citation2019; Nath & Sarker, Citation2017; EN-1992.1.1, Citation2004; Prachasaree et al., Citation2014; Diaz-Loya et al., Citation2011; Tempest, Citation2010; Islam et al., Citation2014; CEB-FIP model code, Citation1990; Singh et al., Citation2016; Thomas & Peethamparan, Citation2015; Yang et al., Citation2012). The calculation of this property using these models and the experimental results of this work are plotted in as a function of the square root of concrete compressive strength. It can be stated From that models for traditional cement concrete prescribed by ACI 318-19 Code (ACI 318-19, Citation2019), the European CEB-FIP Code (CEB-FIP model code, Citation1990), and Eurocode 2 (EN-1992.1.1, Citation2004), are not adequate and overestimate the modulus of elasticity of the GC and GA concretes. As shown in , the models for geopolymer concrete proposed by Hardjito and Rangan (Citation2005), i.e. and Singh et al. (Citation2016), i.e.
give reasonable predictions for GA concrete and match well with the modulus of elasticity
reported in for this concrete. It is worth noting that Hardjito and Rangan (Citation2005) tested fly ash geopolymer concrete with curing conditions ranging from room to high temperatures, and Singh et al. (Citation2016) tested fly ash slag geopolymer concrete with slag additions up to 33 wt.% cured at room temperature; these conditions agree with the manufacturing process of the GA concrete. For the case of GC concrete, the best-fit prediction is given by the Prachasaree et al. model (Prachasaree et al., Citation2014), i.e.
which agrees well with the modulus of elasticity
reported in for that concrete. In addition, shows that models for alkali-activated slag concretes overestimate the modulus of elasticity of the GC and GA concretes, because alkali-activated slag concretes are based on the C-S-H gels with higher stiffness than that of the C-S-H gels in fly ash slag geopolymer concretes.
Figure 11. Comparison between experimental and theoretical values of the modulus of elasticity for: (a) Portland cement concrete, (b) fly ash geopolymer concrete, (c) fly ash slag geopolymer concrete, (d) alkali-activated slag concrete.
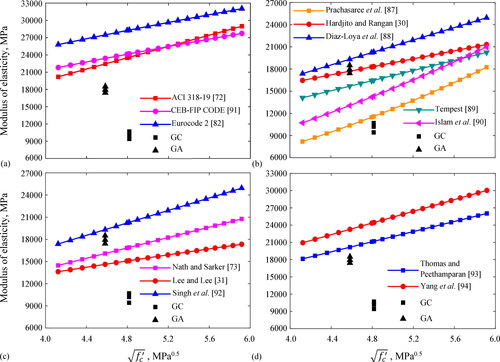
Results concerning Poisson’s ratios are listed in . GC and GA exhibited ratios 11% higher than the TC concrete; consequently, GC and GA concretes have slightly lesser transverse confinement of the microstructure than the traditional cement one, which matches with previous research (Olivia & Nikraz, Citation2012; Bondar et al., Citation2011). Singh et al. (Citation2016) found that Poisson’s ratio of fly ash slag geopolymer concrete is within a range of 0.19 to 0.24, in line with the ratios of the GC and GA reported in . In the absence of more experimental data, it is not possible to establish a clear correlation between the Poisson’s ratio and the compressive strength for the GA concrete. Pan et al. found that the Poisson’s ratio of the fly ash geopolymer concrete did not correlate well with its compressive strength (Pan et al., Citation2011), but future research is still needed on this topic for GA concrete. From the results in , the replacement of the commercial sodium silicate by an alternative sodium silicate from rice husk ash does not affect the Poisson’s ratio of the fly ash slag geopolymer concrete, and both activators produce comparable ratios.
Table 10. Poisson’s ratios of concretes at 28-day age.
3.6. Splitting tensile strength
Splitting tensile strength results after 28-days are shown in and plotted in . This capacity is obtained indirectly by applying several prediction models listed in Appendix B for traditional cement concrete and geopolymer concretes with different precursors and curing conditions (Hardjito & Rangan, Citation2005; Lee & Lee, Citation2013; ACI 318-19, Citation2019; EN-1992.1.1, Citation2004; Tempest, Citation2010; CEB-FIP model code, Citation1990; Thomas & Peethamparan, Citation2015; Yang et al., Citation2012; Albitar et al., Citation2015; Nguyen et al., Citation2016; Ryu et al., Citation2013; Neupane, Citation2016; Sofi et al., Citation2007; Ding et al., Citation2016) which are also plotted in as a function of concrete compressive strength. shows that GC and GA exhibited splitting tensile strengths up to 23% and 26% higher than that of TC concrete, respectively. Also, tensile failure of GC and GA is less brittle than that of the TC concrete (Cardenas-Pulido et al., Citation2020). Singh et al. (Citation2016) explained that interfacial transition zone (ITZ) between the paste and the aggregates improves the splitting and bonding strengths more for geopolymer concrete than for cement-based concrete. It is noteworthy from that the splitting tensile strengths of GA and GC concretes are comparable just exhibiting a slight difference of 3%, and that their splitting tensile strengths are close to 10% of their compressive strengths.
Figure 12. Comparison between experimental and theoretical values of splitting tensile capacity for: (a) Portland cement concrete, (b) fly ash geopolymer concrete, (c) fly ash slag geopolymer concrete, (d) alkali-activated slag concrete.
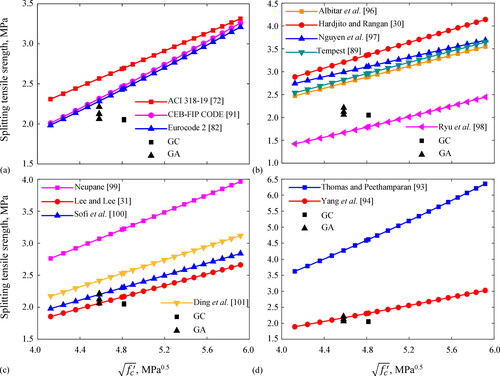
Table 11. Splitting tensile strength of concretes at 28-day age, MPa.
show that the models for cement-based concrete, fly ash geopolymer concrete, and alkali-activated slag concrete, are not adequate and overestimate the splitting tensile capacity of GC and GA concretes, most likely due to the calcium sources and the high curing temperatures that promote stronger microstructures in those concretes (Lee & Lee, Citation2013; Pan et al., Citation2011). demonstrates that the splitting capacity of the GC and GA concretes can be well predicted through the model for fly ash slag geopolymer concrete proposed by Lee and Lee (Lee & Lee, Citation2013), i.e. 0.45 The model matches well with capacities of 0.426
and 0.465
reported in for the GC and GA concretes, respectively.
A last point of discussion is that the splitting tensile capacity of the GA concrete was the highest among all the concretes. This is somehow contradictory to what has been stated regarding that all mechanical strengths of concrete are linked to the compressive strength. However, the highest tensile capacity of this concrete could be attributed to the presence of unfiltered residues and undissolved rice husk ash particles in the activator densifying the ITZ of the GA concrete as well as increasing the interfacial reactions to improve bonding. To a lesser extent, such increment is due to the filler effect of the efflorescence. This enhanced property could contribute to the rebar bonding and an improved shear resistance in ambient-cured geopolymer concrete members.
3.7. SEM/EDS analysis
shows the SEM micrographs for the three types of pastes after a 28-day age. show a compact microstructure characterized by a predominant phase of crosslinked, homogeneous and continuous C-S-H gel, with some microcracks. In these images, some calcium hydroxide crystals with shape of hexagonal plates (portlandite) and ettringite needles were observed, which are typical products of GU cement hydration. shows an elementary composition analysis by EDS carried out on the C-S-H gel of the TC paste (spot a in ), identifying Si/Al and Ca/Si atomic ratios of 2.07 and 5.59 respectively, which are typical values for cement binders. On the other hand, SEM micrographs of the GC paste shown in depict a continuous amorphous gel phase which is assumed to be composed by sodium aluminosilicate hydrate (N-A-S-H) and calcium aluminosilicate hydrate (C-(A)-S-H) gels, due to the geopolymerization of fly ash and slag respectively (J, 2015). Also, for the GC paste, spherical and irregular particles of unreacted or partially reacted fly ash and slag are observed embedded in the gel, acting as fillers in the microstructure. This indicates that considering the activation and curing conditions, the geopolymerization of the precursors in the GC paste was not fully achieved. Previous research (Somna et al., Citation2011) revealed that dissolution of fly ash at room temperature had not been completed before the final hardened structure was formed, which confirms the presence of unreacted or partially reacted precursors in the GC paste. shows the EDS analysis carried out on the continuous gel phase of the GC paste (spot b in ) which revealed Si/Al = 5.92, Ca/Si = 0.3 and Na/Al = 2.68 atomic ratios; notice that these differ from the input atomic ratios of the GC concrete in (Si/Al = 2.75, Ca/Si = 0.17 and Na/Al = 1.21). The largest difference between the Si/Al and Na/Al input ratios vs. the Si/Al and Na/Al measured proportions is because the input ratios consider that 22.7 wt.% Si, 25.7% Na and 7.9 wt.% Al are involved in the geopolymerization reactions, while the measured ones evidenced that 22.9 wt.% Si, 10.4% Na and 3.9 wt.% Al really took part in the reaction. This indicates either partial geopolymerization of precursors or alumina and sodium leaching from geopolymer concrete cured at room temperature (Chindaprasirt et al., Citation2009).
Figure 13. SEM micrographs of pastes from manufactured concretes: (a) TC (50 μm), (b) GC (50 μm), (c) GA (50 μm), (d) TC (10 μm), (e) GC (5 μm), (f) GA (2 μm).
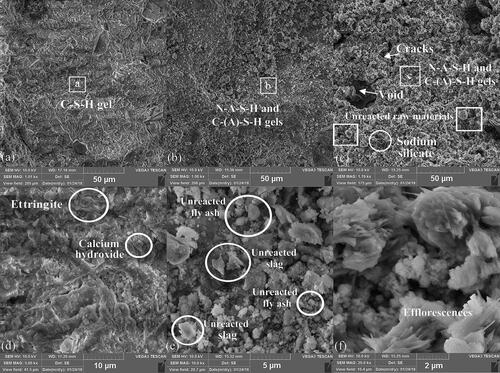
Figure 14. EDS analysis of pastes from manufactured concretes: (a) TC (spot a in GC (spot b in GA (spot c in ).
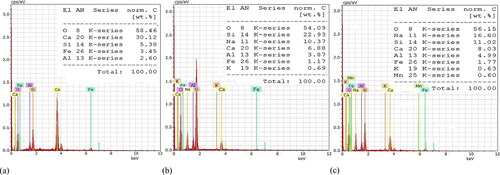
evidence the morphology of the GA paste with a continuous gel phase composed by the combination of N-A-S-H and C-(A)-S-H which provide the mechanical strength. Particles of the unreacted raw materials not connected to the networks but embedded in the gel were also identified in the Figures acting as fillers in the microstructure. It was observed in that the surface of the gel phase was coarser and rougher in comparison with the gel phase of the GC paste, indicating relatively lower maturity, compactness and degree of geopolymerization of the GA paste. This may be attributed to the slower release of silicate species from the alternative silicate (monomers and oligomers) required to participate in the geopolymerization and gel formation of the GA paste at room temperature, which correlates well with its slower compressive strength evolution. These findings confirm that the replacement of commercial sodium silicate by an alternative sodium silicate from rice husk ash slows down geopolymerization reactions, delaying the hardening process of the geopolymer concrete. presents the EDS analysis in the gel phase of the GA paste (spot c in ) revealing Si/Al = 2.21, Ca/Si = 0.73 and Na/Al = 3.37 atomic ratios. When a crosscheck comparison is performed against the input atomic ratios of for the GA concrete (Si/Al = 2.74, Ca/Si = 0.18 and Na/Al = 3.09), the difference between the Si/Al input and the measured ratio is because the former considers that 19 wt.% Si and 6.7 wt.% Al are involved in the geopolymerization, while the latter evidenced 11.1 wt.% Si and 5 wt.% Al participation. These results suggest that the real Si content involved in the geopolymerization of the GA concrete was 58% out of 100% nominal input Si value, and it approaches 69% total amorphous content of the GA concrete (). The Na/Al measured ratio of this gel correlates well with the Na/Al input one, meaning excess alkali for the GA concrete.
It can also be observed from that the GA paste microstructure had more porosity and some cracks, resulting mainly from the lower effectiveness of the alternative silicate, some shrinkage and water evaporation, and lower mix workability (see Section 3.3), i.e. difficulties in the mixing and tamping processes of the fresh GA concrete caused voids and trapped air bubbles remaining in the hardened state. Kamseu et al. (Citation2017) also reported higher cumulative pore volume and more porous microstructure of geopolymer pastes activated by rice husk ash-derived silicate linked to lower dissolution and polycondensation reactions. Tchakouté et al. (Citation2016) argued that the increased pore volume and voids may be attributed to amount of P2O5 available in the rice husk ash-based activators hindering the silica dissolution in geopolymer. Results of Kamseu et al. (Citation2017) and Tchakouté et al. (Citation2016) connect with SEM observations of the current study for GA paste. The morphology of the GA paste in exhibits acicular crystal blooms attributed to the presence of efflorescence, which correlates well with the high Na/Al ratio measured by the EDS technique on the GA paste, the XRD findings on the presence of natron and beta sodium carbonate, and previously reported data (Rajan & Kathirvel, Citation2021). These findings indicate that ambient-cured geopolymer concrete activated with alternative sodium silicate from rice husk ash will experience efflorescence formation. Finally, shows an evidence of silica conversion to silicate species from the rice husk ash-derived activator. Based on the SEM micrographs of the GA paste () it is difficult to clearly identify if the undissolved rice husk ash particles remain as fillers in the microstructure to check the activator effectiveness since efflorescence formation. However, considering the practical processing conditions of the alternative silicate and the curing conditions of the GA concrete, a large part of rice husk ash was converted to sodium silicate to participate in the geopolymerization reaction (see evidence in ), and the remaining undissolved or unreacted part is hypothesized to act together with the unfiltered residues as fillers of the microstructure providing mechanical capacity to this concrete. Overall, acceptable compressive strength, and outstanding improvements in the modulus of elasticity and splitting tensile capacity of the GA concrete were evidenced.
3.8. Strategies for increasing the effectiveness of the rice husk ash-derived activator, related costs, and environmental impacts
An in-depth review of recent literature was done by the authors in order to propose, in conjunction with their own criteria, some actions that could increase the effectiveness of the unfiltered-silicate from rice husk ash processed at room conditions which was used in this study. As well, literature review allowed to approach the costs and environmental impacts by using such activator in geopolymers. Strategies for increasing the quality and effectiveness of the rice husk ash-derived activator are: (i) Enhancing the dissolution of the rice husk ash into the activator. This can be achieved, on the one hand, increasing the fineness and amorphous content of the rice husk ash as well as reducing/removing/converting to soluble ions both its unburnt content or loss on ignition (K2O and Na2O metal residues, dust, other impurities) and burned organic matter (cellulose and lignin) (Alnahhal et al., Citation2021; Mendes et al., Citation2021; Tsen et al., Citation2019), having these important effects in increase its specific surface area, solubility, pure silica extraction, reactivity (activation energy and puzzolanity) and conversion rate to silicate, also benefitting the activator kinetics and accelerating geopolymerization reactions. These features can be reached through a purifying pretreatment (cleaning) of the rice husks prior to burning by soaking with deionized water, liquid ionic or alkaline solution, by thermal process, by mechanical grinding, or by leaching with mineral acids like HCl, HNO3, H2SO4, H3PO4 and organic ones like acetic, citric, oxalic (Zou & Yang, Citation2019; Bakar et al., Citation2015; Buás de Lima et al., Citation2011; Onojah et al., Citation2013; Tchakouté & Rüscher, Citation2017), also through managing closed calcination of the rice husks in laboratory or in an electric oven at controlled burning temperatures and times of 500-800 °C and 1-2 hours respectively, or by mechanical grinding, sieving, flotation, air/electrostatic/magnetic classification, or re-calcination (600 °C/6 hours) of the as-received rice husk ashes (Alnahhal et al., Citation2021; Mendes et al., Citation2021; Tsen et al., Citation2019). One the other hand, dry premixing rice husk ash and ground caustic soda flakes for 0.25 to 3 hours (prior to water addition) until achieving homogeneous consistency and an exothermic reaction that increases the precipitation of the Na+ ions on the surface of rice husk ash particles hydrolyzing them (Rajan & Kathirvel, Citation2021; Kaur et al., Citation2018), increasing the stirring time of the activator as high as 72 hours (Andreola et al., Citation2020), and allowing a resting period of the activator higher than a week (i.e. storage time prior to its use in geopolymer), also greatly assure dissolution of the rice husk ash particles and increase availability of silicate species into the activator with higher equilibrium over time as well (Tchakouté et al., Citation2016). (ii) Providing a higher amount of silicate species into the activator accelerates and enhances the geopolymerization (Rajan & Kathirvel, Citation2021), which can be achieved either by increasing the SiO2/Na2O molar ratio (silica modulus) of the activator up to 2.0, or by adding a reactive extra rich silica source to the activator (like nanosilica) that also helps to increase the release rate of silicates species from the rice husk ash (by catalytic effect) (Alnahhal et al., Citation2021; Mendes et al., Citation2021). (iii) Increasing the fresh mixing time higher than 20 minutes between the activator and the precursors could increase its effectiveness in the geopolymerization reactions. (iv) Lastly, ambient curing at ≥90%RH of the geopolymer specimens sealed by plastic film could decrease their cracking, efflorescence, and evaporation of water and oxides from the activator into the microstructure, favoring the geopolymerization reactions.
Regarding the costs and the environmental impacts, Tong et al. (Citation2018), Tchakouté et al. (Citation2016) and Abdulkareem et al. (Citation2021) stated that rice husk ash-derived activators reduces the price of the activation up to 55% compared to using commercial silicate, thereby reducing the cost of geopolymer about 22% (Mendes et al., Citation2021; Tchakouté et al., Citation2016). Several works assert that environmental impacts of geopolymers are greatly lowered by the use of rice husk ash-derived activators. According to Mellado et al. (Citation2014), rice husk ash-derived activators reduce geopolymer CO2 emissions by 50% compared to commercial silicate. Abdulkareem et al. (Citation2021) found that geopolymers activated with rice husk ash activators exhibited 62%, 61%, 76% and 56% lower greenhouse gases respectively in the categories of climate change, fossil depletion, terrestrial acidification, and photochemical ozone creation formation, compared to commercial silicate outcomes. Passuello et al. (Citation2017) also identified environmental impacts less than 60% in the categories of acidification potential, global warming potential, eutrophication potential, freshwater aquatic ecotoxicity, human toxicity potential, and marine aquatic ecotoxicity. Kamseu et al. (Citation2017) claimed that global warming potential from an unfiltered-rice husk ash activator processed at room conditions is less than 70% when compared to commercial silicate. Furthermore, Rajan and Kathirvel (Citation2021) reported 71% and 65% lower embodied energy consumption and CO2 emissions respectively by using rice husk ash activators. In spite of the related costs and environmental impacts of the GA concrete were not evaluated in the current work, cited research provide insights of the cheapness and eco-friendliness if rice husk ash-derived activators were used in the manufacture of ambient-cured geopolymer concrete of structural grade.
4. Conclusions
This study explored the potential use of an alternative silicate from rice husk for manufacturing plain ambient-cured geopolymer concrete and evaluating its engineering properties. To the best knowledge of the authors, these topics have not been investigated in the current state of art, hence will be very useful to incorporate geopolymer concrete from rice husk ash-derived activators in field applications. The alternative silicate was synthesized under room conditions (21 °C, 65 ± 5% RH, atmospheric pressure), without filtration processes, by constant stirring over 30 minutes throughout the preparation stage, and a final storage for one-week to promote the dissolution of the rice husk ash particles. Although higher temperatures, filtration processes, and longer stirring periods increase the dissolution and conversion to silicate of the rice husk ash into the activator, these conditions were not considered in this work since they could increase the costs, time processing, the embodied energy and the environmental impact of this initiative. Instead, a high alkalinity environment was the strategy towards a cost-effective technique in the preparation stage. Another set of strategies based on recent literature and the own criteria were also elucidated to increase the effectiveness of the silicate processed. Engineering properties of the proposed concrete were comprehensively assessed and compared against geopolymer concrete with commercial sodium silicate and traditional cement concrete. Based on the results the following can be concluded:
Ambient-cured geopolymer concrete with alternative silicate from rice husk ash exhibited a 28-day compressive strength of 21 MPa, comparable to those of the geopolymer concrete with commercial sodium silicate and the traditional cement concrete (differences less than 13%). This compressive strength is adequate for manufacturing structural concrete members since it exceeds the 17 MPa lower bound prescribed by the ACI 318 Building Code. However, the compressive strength evolution of the geopolymer concrete with the alternative silicate was slightly slower than that with commercial silicate. From the mechanical point of view, the alternative sodium silicate from rice husk ash is reliable and can fully replace the commercial sodium silicate, if the early strength of the ambient-cured geopolymer concrete is not the topic of interest.
Ambient-cured geopolymer concrete with alternative silicate from rice husk ash exhibited a modulus of elasticity of 17959 MPa which is 44% higher than that of geopolymer concrete with commercial sodium silicate. By such improvement, it is hypothesized that the alternative silicate could provoke geopolymer concrete members suffering less deflection from externally applied loads as well as having superior serviceability in terms of creep, vibration and fatigue. In addition, the splitting tensile capacity of 2.13 MPa and Poisson’s ratio of 0.183 are similar for both types of geopolymer concretes but higher than that for the traditional cement concrete. Consequently, the alternative silicate could effectively contribute to shear capacity and rebar bonding in geopolymer concrete members.
An empirical model to predict the compressive strength evolution until 28 days was proposed from 24 tested specimens, focused on ambient-cured fly ash slag geopolymer concrete, activated by either commercial sodium silicate or alternative sodium silicate from rice husk ash, having a 28-day compressive strength ranging between 20 MPa and 25 MPa, and having slag additions of up to 20 wt.%. Useful expressions from 9 tested specimens to compute the modulus of elasticity and splitting tensile capacity of ambient-cured geopolymer concrete with the alternative silicate were 3918
and 0.465
respectively. The proposed models show good fitting with the measured properties in the experimental tests.
Workability of geopolymer concrete with alternative silicate from rice husk ash is lower than that with commercial sodium silicate. Adjusting the H2O/Na2O ratio of the activator or the use of dispersing agents could improve its rheological behavior.
Amorphous silica and some of crystalline silica from alternative silicate based on rice husk ash participate in the geopolymerization of the ambient-cured geopolymer concrete. It was found that the real Si content involved in the geopolymerization was 58% out of 100% nominal input Si content, which approaches to 69% of the total amorphous content of this geopolymer concrete. Some of the undissolved rice husk ash residues can also fill the microstructure providing mechanical capacity to the geopolymer concrete.
Replacement of commercial sodium silicate by alternative sodium silicate from rice husk ash could significantly reduce the carbon footprint and the cost of conventional geopolymer concrete in accordance with previous literature, as well as contribute to a proper disposal of copious rice husk ash, being aligned with the current worldwide sustainability goals. Future research is pending on rheology improvement, enhancing early-age mechanical strength, decreasing the hydration heat, controlling the efflorescence phenomena, managing the long-term performance in terms of compressive strength evolution, microstructural maturity, and durability, as well as addressing the structural properties of this promising concrete for use in field applications. Efflorescence drawback could be solved by adjusting the chemical formulation of this concrete or including alumina additions to increase the fixation of the alkaline cations inside the geopolymer microstructure.
Author contributions
Jhon Cárdenas-Pulido and Fernando Ramirez conceived the experimental program, performed the experiments of workability, isothermal calorimetry, compressive strength and splitting tensile strength, and analyzed their data. Diego Velandia, Juan C. Reyes, and Julian Carrillo performed the experiments of modulus of elasticity, Poisson’s ratio, and XRD, and analyzed their data. Willian Aperador performed the SEM-EDS experiments and analyzed their data. All authors illustrated, wrote, and reviewed the manuscript.
Acknowledgements
The authors gratefully acknowledge the support given by the companies Planta Eléctrica Sochagota (Termopaipa IV), Acerías Paz del Río, and Argos S.A., for providing the raw materials required for the development of present work. The outstanding help of Christiam C. Ángel with the style editing and overall proofreading is highly appreciated. Julian Carrillo expresses his gratitude to the Universidad Militar Nueva Granada (UMNG, Colombia) for granting the research scholarship. This research did not receive any specific grant from funding agencies in the public, commercial, or not-for-profit sectors.
Disclosure statement
No potential conflict of interest was reported by the authors.
Data availability statement
Data available within the article or its supplementary materials.
References
- Demir, F., & Derun, E. M. (2019). A response surface methodology application to fly ash based geopolymer synthesized by alkali fusion method. Journal of Non-Crystalline Solids. 524, 119649. https://doi.org/10.1016/j.jnoncrysol.2019.119649
- Abdulkareem, M., Havukainen, J., Nuortila-Jokinen, J., & Horttanainen, M. (2021). Environmental and economic perspective of waste-derived activators on alkali-activated mortars. Journal of Cleaner Production, 280, 124651. https://doi.org/10.1016/j.jclepro.2020.124651
- ACI 209R-08. (2008). Prediction of creep, shrinkage, and temperature effects in concrete structures. In ACI Manual of Concrete. Practice Part 1: materials and general properties of concrete .
- ACI 318-19. (2019). Building code requirements for structural concrete and commentary. American Concrete Institute.
- Albitar, M., Visintin, P., Ali, M. M., & Drechsler, M. (2015). Assessing behaviour of fresh and hardened geopolymer concrete mixed with class-F fly ash. KSCE Journal of Civil Engineering, 19(5), 1445–1455. https://doi.org/10.1007/s12205-014-1254-z
- Allahverdi, A., Najafi Kani, E., & Shaverdi, B. (2017). Carbonation versus efflorescence in alkali-activated blast-furnace slag in relation with chemical composition of activator. International Journal of Civil Engineering, 15(4), 565–573. https://doi.org/10.1007/s40999-017-0225-4
- Alnahhal, M. F., Hamdan, A., Hajimohammadi, A., & Kim, T. (2021). Effect of rice husk ash-derived activator on the structural build-up of alkali activated materials. Cement and Concrete Research. 150, 106590. https://doi.org/10.1016/j.cemconres.2021.106590
- Alnahhal, M. F., Kim, T., & Hajimohammadi, A. (2021). Waste-derived activators for alkali-activated materials: A review. Cement and Concrete Composites. 118, 103980. https://doi.org/10.1016/j.cemconcomp.2021.103980
- Andreola, F., Barbieri, L., & Lancellotti, I. (2020). The environmental friendly route to obtain sodium silicate solution from rice husk ash: A comparative study with commercial silicates deflocculating agent. Waste and Biomass Valorization, 11(11), 6295–6305. https://doi.org/10.1007/s12649-019-00849-w
- Arbi, K., Nedeljkovic, M., Zuo, Y., Grünewald, S., Keulen, A., & Ye, G. (2015). Experimental study on workability of alkali activated fly ash and slag-based geopolymer concretes. In Icers (Eds.) Geopolymers: The route to eliminate waste and emissions in ceramic and cement manufacturing , ISBN. : 9781326377328 75–78,
- ASTM C 1157-20. (2020). Standard performance and specification for hydraulic cement (Vol. 04.01). American Society of Testing and Materials (ASTM).
- ASTM C 138-17. (2017). Standard test method for density (unit weight), yield, and air content (Gravimetric) of Concrete (Vol. 04.02). American Society of Testing and Materials (ASTM).
- ASTM C 143-20. (2020). Standard test method for slump of hydraulic-cement concrete (Vol. 04.02). American Society of Testing and Materials (ASTM).
- ASTM C 192-19. (2019). Standard practice for making and curing concrete test specimens in the laboratory (Vol. 04.02). American Society of Testing and Materials (ASTM).
- ASTM C 33-18. (2018). Standard specification for concrete aggregates (Vol. 04.02). American Society of Testing and Materials (ASTM).
- ASTM C 496-17. (2017). Standard test method for splitting tensile strength of cylindrical concrete specimens (Vol. 04.02). American Society of Testing and Materials (ASTM).
- ASTM C 618-22. (2022). Standard specification for coal fly ash and raw or calcined natural pozzolan for use as a mineral admixture in concrete (Vol. 04.02). American Society of Testing and Materials (ASTM).
- ASTM C39-21. (2021). Standard test method for compressive strength of cylindrical concrete specimens (Vol. 04.02). American Society of Testing and Materials (ASTM).
- ASTM C469-22. (2022). Standard test method for static modulus of elasticity and Poisson’s ratio of concrete in compression (Vol. 04.02). American Society of Testing and Materials (ASTM).
- Autef, A., Joussein, E., Gasgnier, G., & Rossignol, S. (2012). Role of the silica source on the geopolymerization rate. Journal of Non-Crystalline Solids, 358(21), 2886–2893. https://doi.org/10.1016/j.jnoncrysol.2012.07.015
- Bajpai, R., Choudhary, K., Srivastava, A., Sangwan, K. S., & Singh, M. (2020). Environmental impact assessment of fly ash and silica fume based geopolymer concrete. Journal of Cleaner Production, 254, 120147. https://doi.org/10.1016/j.jclepro.2020.120147
- Bakar, R. A., Yahya, R., & Gan, S. N. (2015). Production of high purity amorphous silica from rice husk. In Proceedings of the 5th International Conference on Recent Advances in Materials, Minerals and Environment (RAMM) & 2nd International Postgraduate Conference on Materials, Mineral and Polymer (MAMIP ). Universiti Sains Malaysia, Penang, Malaysia.
- Bernal, S. A., Provis, J. L., Brice, D. G., Kilcullen, A., Duxson, P., & van Deventer, J. S. J. (2012). Accelerated carbonation testing of alkali-activated binders significantly underestimates service life: The role of pore solution chemistry. Cement and Concrete Research, 42(10), 1317–1326. https://doi.org/10.1016/j.cemconres.2012.07.002
- Bernal, S. A., Provis, J. L., Rose, V., & Mejía de Gutierrez, R. (2011). Evolution of binder structure in sodium silicate-activated slag-metakaolin blends. Cement and Concrete Composites. 33(1), 46–54. https://doi.org/10.1016/j.cemconcomp.2010.09.004
- Bernal, S. A., Rodríguez, E. D., Mejía de Gutiérrez, R., & Provis, J. L. (2015). Performance at high temperature of alkali-activated slag pastes produced with silica fume and rice husk ash based activators. Materiales de Construcción, 65(318), e049-10. https://doi.org/10.3989/mc.2015.03114
- Bernal, S. A., Rodríguez, E. D., Mejía de Gutiérrez, R., Provis, J. L., & Delvasto, S. (2012). Activation of metakaolin/slag blended alkaline solutions based on chemically modified silica fume and rice husk ash. Waste and Biomass Valorization, 3(1), 99–108. https://doi.org/10.1007/s12649-011-9093-3
- Bondar, D. (2009). Alkali activation of iranian natural pozzolans for producing geopolymer cement and concrete [Ph.D thesis]. University of Sheffield.
- Bondar, D., Lynsdale, C. J., Milestone, N. B., Hassani, N., & Ramezanianpour, A. K. (2011). Engineering properties of alkali-activated natural pozzolan concrete. ACI Materials Journal. 108, 64–72.
- BS EN 196-9. 2010. Methods of testing cement. Part 8. Heat of hydration. Semi-adiabatic method.
- Buás de Lima, S. P., Pereira de Vasconcelos, R., Paiva, O. A., Cordeiro, G. C., Chaves, M. R., Filho, R. D. T., & Fairbairn, E. M. R. (2011). Production of silica gel from residual rice husk ash. Química Nova, 34(1), 71–75. https://doi.org/10.1590/S0100-40422011000100014
- Castel, A., Foster, S. J., Ng, T., Sanjayan, J. G., & Gilbert, R. I. (2016). Creep and drying shrinkage of a blended slag and low calcium fly ash geopolymer concrete. Materials and Structures, 49(5), 1619–1628. https://doi.org/10.1617/s11527-015-0599-1
- CEB-FIP model code. (1990). Comite Euro-International Du Beton p. 39.
- Chindaprasirt, P., Jaturapitakkul, C., Chalee, W., & Rattanasak, U. (2009). Comparative study on the characteristics of fly ash and bottom ash geopolymers. Waste Manage. (Oxford), 29(2), 539–543. https://doi.org/10.1016/j.wasman.2008.06.023
- Davidovits, J. (1991). Geopolymers: Inorganic polymeric new materials. Journal of Thermal Analysis. 37(8), 1633–1656. https://doi.org/10.1007/BF01912193
- Davidovits, J. (2015). Geopolymer chemistry and application (4th ed., p. 585). Institute Geopolymer.
- Deb, P. S., Nath, P., & Sarker, P. K. (2014). The effects of ground granulated blast-furnace slag blending with fly ash and activator content on the workability and strength properties of geopolymer concrete cured at ambient temperature. Materials and Design, 62, 32–39. https://doi.org/10.1016/j.matdes.2014.05.001
- Diaz-Loya, E. I., Allouche, F. N., & Vaidya, S. (2011). Mechanical properties of fly-ash based geopolymer concrete. ACI Materials Journal. 108, 300–306. https://doi.org/10.14359/51682495
- Ding, Y., Dai, J. G., & Shi, C. J. (2016). Mechanical properties of alkali-activated concrete: A state-of-the-art review, Construction and Building Materials, 127, 68–79. https://doi.org/10.1016/j.conbuildmat.2016.09.121
- Duan, P., Yan, C., Zhou, W., Luo, W., & Shen, C. (2015). An investigation of the microstructure and durability of a fluidized bed fly ash–metakaolin geopolymer after heat and acid exposure. Materials and Design. 74, 125–137. https://doi.org/10.1016/j.matdes.2015.03.009
- EN-1992.1.1. (2004). Eurocode 2, design of concrete structures – part 1-1: General rules and rules for buildings, european committee for standardization. Belgium.
- Fernandez-Jimenez, A. M., Palomo, A., & Lopez-Hombrados, C. (2006). Engineering properties of alkali activated fly ash concrete. ACI Materials Journal. 103, 106–112.
- Fernández-Jiménez, A., & Palomo, A. (2003). Characterisation of fly ashes, potential reactivity as alkaline cements. Fuel, 82(18), 2259–2265. https://doi.org/10.1016/S0016-2361(03)00194-7
- Fernandez-Jimenez, A., & Palomo, A. (2005). Composition and microstructure of alkali activated fly ash binder: Effect of the activator. Cement and Concrete Research, 35(10), 1984–1992. https://doi.org/10.1016/j.cemconres.2005.03.003
- Gao, X., Yu, Q. L., & Brouwers, H. J. H. (2015). Reaction kinetics, gel character and strength of ambient temperature cured alkali activated slag–fly ash blends. Construction and Building Materials. 80, 105–115. https://doi.org/10.1016/j.conbuildmat.2015.01.065
- Hajimohammadi, A., & van Deventer, J. S. J. (2017). Solid reactant-based geopolymers from rice hull ash and sodium aluminate. Waste and Biomass Valorization, 8(6), 2131–2140. https://doi.org/10.1007/s12649-016-9735-6
- Hamidi, R. M., Man, Z., Azizli, K. A., Ismail, L., & Nuruddin, M. F. (2014). Mechanical activation of fly ash by high energy planetary ball mill and the effects on physical and morphology properties. Applied Mechanics and Materials, 625, 38–41. https://doi.org/10.4028/www.scientific.net/AMM.625.38
- Hardjito, D. (2005). Studies on fly ash-based geopolymer concrete [PhD thesis]. Curtin University of Technology.
- Hardjito, D., & Rangan, B. V. 2005. Development and properties of low-calcium fly ash based geopolymer concrete . Research report GC-1 2005. Faculty of Engineering, Curtin University of Technology.
- Hardjito, D., Wallah, S. E., Sumajouw, D. M. J., & Rangan, B. V. (2005). Fly ash-based geopolymer concrete. Australian Journal of Structural Engineering. 6(1), 77–86. https://doi.org/10.1080/13287982.2005.11464946
- He, J., Jie, Y., Zhang, J., Yu, Y., & Zhang, G. (2013). Synthesis and characterization of red mud and rice husk ash-based geopolymer composites, Cement and Concrete Composites, 37, 108–118. https://doi.org/10.1016/j.cemconcomp.2012.11.010
- Islam, R., Montes, C., & Allouche, E. (2014). Correlation between chemical and phase composition of fly ash and mechanical properties of geopolymer concrete. International Journal of Environmental Engineering and Natural Resources, 1, 235–239.
- J., Cardenas-Pulido, J. C., Reyes, J., Carrillo, J., & F., Ramirez. (2020). Shear behavior of geopolymer concrete panels under diagonal tensile stresses. Engineering Structures. 212, 110518. https://doi.org/10.1016/j.engstruct.2020.110518
- Kamseu, E., Beleuk, A., Moungam, L. M., Cannio, M., Billong, N., Chaysuwan, D., Melo, U. C., & Leonelli, C. (2017). Substitution of sodium silicate with rice husk ash NaOH solution in metakaolin-based geopolymer cement concerning reduction in global warming. Journal of Cleaner Production, 142, 3050–3060. https://doi.org/10.1016/j.jclepro.2016.10.164
- Kaur, K., Singh, J., & Kaur, M. (2018). Compressive strength of rice husk ash based geopolymer: The effect of alkaline activator, Construction and Building Materials, 169, 188–192. https://doi.org/10.1016/j.conbuildmat.2018.02.200
- Kovalchuk, G., Fernandez-Jimenez, A., & Palomo, A. (2007). Alkali-activated fly ash: effect of thermal curing conditions on mechanical and microstructural development- Part II. Fuel, 86(3), 315–322. https://doi.org/10.1016/j.fuel.2006.07.010
- Kumar, S., Kumar, R., & Mehrotra, S. P. (2010). Influence of granulated blast furnace slag on the reaction, structure and properties of fly ash based geopolymer. Journal of Materials Science, 45(3), 607–615. https://doi.org/10.1007/s10853-009-3934-5
- Kumar, S., Kumar, R., Alex, T. C., Bandopadhyay, A., & Mehrotra, S. P. (2007). Influence of reactivity of fly ash on geopolymerisation, Advances in Applied Ceramics, 106(3), 120–127. https://doi.org/10.1179/174367607X159293
- Lee, N. K., & Lee, H. K. (2013). Setting and mechanical properties of alkali activated fly ash/slag concrete manufactured at room temperature, Construction and Building Materials, 47, 1201–1209. https://doi.org/10.1016/j.conbuildmat.2013.05.107
- Liu, S., & Ott, W. K. (2020). Sodium silicate applications in oil, gas & geothermal well operations. Journal of Petroleum Science abd Engineering, 195, 107693. https://doi.org/10.1016/j.petrol.2020.107693
- Lloyd, R. R., Provis, J. L., & Van Deventer, J. S. J. (2010). Pore solution composition and alkali diffusion in inorganic polymer cement. Cement and Concrete Research, 40(9), 1386–1392. https://doi.org/10.1016/j.cemconres.2010.04.008
- Mejía, J. M., Mejía De Gutiérrez, R., & Montes, C. (2016). Rice husk ash and spent diatomaceous earth as a source of silica to fabricate a geopolymeric binary binder. Journal of Cleaner Production, 118, 133–139. https://doi.org/10.1016/j.jclepro.2016.01.057
- Mellado, A., Catalán, C., Bouzón, N., Borrachero, M. V., Monzó, J. M., & Payá, J. (2014). Carbon footprint of geopolymeric mortar: study of the contribution of the alkaline activating solution and assessment of an alternative route. RSC Advances. 4(45), 23846–23852. https://doi.org/10.1039/C4RA03375B
- Mendes, B. C., Pedroti, L. G., Vieira, C. M. F., Marvila, M., Azevedo, A. R. G., Franco de Carvalho, J. M., & Ribeiro, J. C. L. (2021). Application of eco-friendly alternative activators in alkali-activated materials: A review. Journal of Building Engineering, 35, 102010. https://doi.org/10.1016/j.jobe.2020.102010
- Mindess, S., Young, J. F., & Darwin, D. (2003). Concrete (2nd ed., p. 644.). Person Education, Inc.
- Mosaberpanah, M. A., & Umar, S. A. (2020). Utilizing rice husk ash as supplement to cementitious materials on performance of ultra high performance concrete: – A review. Materials Today Sustainility, 7–8, 100030. https://doi.org/10.1016/j.mtsust.2019.100030
- Nath, P., & Sarker, P. K. (2014). Effect of GGBFS on setting, workability and early strength properties of fly ash geopolymer concrete cured in ambient condition. Construction and Building Materials. 66, 163–171. https://doi.org/10.1016/j.conbuildmat.2014.05.080
- Nath, P., & Sarker, P. K. (2017). Flexural strength and elastic modulus of ambient-cured blended low-calcium fly ash geopolymer concrete, Construction and Building Materials, 130, 22–31. https://doi.org/10.1016/j.conbuildmat.2016.11.034
- Neupane, K. (2016). Fly ash and GGBFS based powder-activated geopolymer binders: a viable sustainable alternative of Portland cement in concrete industry. Mechanics of Materials. 103, 110–122. https://doi.org/10.1016/j.mechmat.2016.09.012
- Neville, A. M. (2004). Properties of concrete (4th ed., p. 860). Wiley.
- Nguyen, K. T., Ahn, N., Lee, T. A., & Lee, K. (2016). Theoretical and experimental study on mechanical properties and flexural strength of fly ash geopolymer concrete, Construction and Building Materials, 106, 65–77. https://doi.org/10.1016/j.conbuildmat.2015.12.033
- Noushini, A., Babaee, M., & Castel, A. (2016). Suitability of heat-cured low-calcium fly ash based geopolymer concrete for precast applications. Magazine of Concrete Research, 68(4), 163–177. https://doi.org/10.1680/macr.15.00065
- Novotny, R., Hoff, A., & Schuertz, J. (1991). Process for hydrothermal production of sodium silicate solutions. United States Patent, 5,000, 933.
- Olivia, M., & Nikraz, H. (2012). Properties of fly ash geopolymer concrete designed by taguchi method. Matererials and Design, 36, 191–198. https://doi.org/10.1016/j.matdes.2011.10.036
- Onojah, A. D., Agbendeh, N. A., & Mbakaan, C. (2013). Rice husk ash refractory: The temperature dependent crystalline phase aspects. IJRRAS, 15, 246–248.
- Pal, S. C., Mukherjee, A., & Pathak, S. R. (2003). Investigation of hydraulic activity of ground granulated blast furnace slag in concrete. Cement and Concrete Research, 33(9), 1481–1486. https://doi.org/10.1016/S0008-8846(03)00062-0
- Pan, Z., Sanjayan, J. G., & Rangan, B. V. (2011). Fracture properties of geopolymer paste and concrete. Magazine of Concrete Research, 63(10), 763–771. https://doi.org/10.1680/macr.2011.63.10.763
- Passuello, A., Rodriguez, E. D., Hirt, E., Longhi, M., Bernal, S. A., Provis, J. L., & Kirchheim, A. P. (2017). Evaluation of the potential improvement in the environmental footprint of geopolymers using waste-derived activators. Journal of Cleaner Production, 166, 680–689. https://doi.org/10.1016/j.jclepro.2017.08.007
- Paya, J., Monzo, J., Borrachero, M., Peris-Mora, E., & González-López, E. (1996). Mechanical treatment of fly ashes part II: Particle morphologies in ground fly ashes (GFA) and workability of GFA-cement mortars. Cement and Concrete Research. 26(2), 225–235. https://doi.org/10.1016/0008-8846(95)00212-X
- Prachasaree, W., Limkatanyu, S., Hawa, A., & Samakrattakit, A. (2014). Development of equivalent stress block parameters for fly-ash-based geopolymer concrete. Arabian Journal for Science and Engineering, 39(12), 8549–8558. https://doi.org/10.1007/s13369-014-1447-2
- Provis, J. L., Lukey, G. C., & van Deventer, J. S. J. (2005). Do geopolymers actually contain nanocrystalline zeolites? A reexamination of existing results. Chemistry of Materials, 17(12), 3075–3085. https://doi.org/10.1021/cm050230i
- Puligilla, S., & Mondal, P. (2013). Role of slag in microstructural development and hardening of fly ash slag geopolymer. Cement and Concrete Research, 43, 70–80. https://doi.org/10.1016/j.cemconres.2012.10.004
- Puligilla, S., & Mondal, P. (2015). Co-existence of aluminosilicate and calcium silicate gel characterized through selective dissolution and FTIR spectral subtraction. Cement and Concrete Research. 70, 39–49. https://doi.org/10.1016/j.cemconres.2015.01.006
- Rajamma, R., Labrincha, J. A., & Ferreira, V. M. (2012). Alkali activation of biomass fly ash–metakaolin blends. Fuel, 98, 265–271. https://doi.org/10.1016/j.fuel.2012.04.006
- Rajan, H. S., & Kathirvel, P. (2021). Sustainable development of geopolymer binder using sodium silicate synthesized from agricultural waste. Journal of Cleaner Production, 286, 124959. https://doi.org/10.1016/j.jclepro.2020.124959
- Rattanasak, U., & Chindaprasirt, P. (2009). Influence of NaOH solution on the synthesis of fly ash geopolymer. Mining Engineering, 22, 1073–1078. https://doi.org/10.1016/j.mineng.2009.03.022
- Ravikumar, D., & Neithalath, N. (2012). Reaction kinetics in sodium silicate powder and liquid activated slag binders evaluated using isothermal calorimetry. Thermochimica Acta, 546, 32–43. https://doi.org/10.1016/j.tca.2012.07.010
- Ryu, G. S., Lee, Y. B., Koh, K. T., & Chung, Y. S. (2013). The mechanical properties of fly ash-based geopolymer concrete with alkaline activators, Construction and Building Materials, 47, 409–418. https://doi.org/10.1016/j.conbuildmat.2013.05.069
- Singh, B., Rahman, R. M., Paswan, R., & Battacharyya, S. K. (2016). Effect of activator concentration on the strength. ITZ and Drying Shrinkage of Fly Ash/Slag Geopolymer Concrete, Construction and Building Materials, 118, 171–179. https://doi.org/10.1016/j.conbuildmat.2016.05.008
- Škvára, F., Kopecký, L., Šmilauer, V., & Bittnar, Z. (2009). Material and structural characterization of alkali activated low-calcium brown coal fly ash. Journal of Hazardous Materials, 168(2-3), 711–720. https://doi.org/10.1016/j.jhazmat.2009.02.089
- Škvara, F., Pavlasova, S., Kopecký, L., Myškova, L., & Alberovska, L. (2008). High temperature properties of fly ash-based geopolymers. In Proceedings of the 3rd international symposium on nontraditional Cement and Concrete, Bílek and Keršner (pp. 741–750).
- Škvára, F., Šmilauer, V., Hlaváček, P., Kopecký, L., & Cílová, Z. (2012). A weak alkali bond in (N, K)–A–S–H gels: Evidence from leaching and modeling. Ceramics-Silikáty, 56, 374–382.
- Sofi, M., van Deventer, J. S. J., Mendis, P. A., & Lukey, G. C. (2007). Engineering properties of inorganic polymer concretes (IPCs). Cement and Concrete Research, 37(2), 251–257. https://doi.org/10.1016/j.cemconres.2006.10.008
- Somna, K., Jaturapitakkul, C., Kajitvichyanukul, P., & Chindaprasirt, P. (2011). NaOH activated ground fly ash geopolymer cured at ambient temperature. Fuel, 90(6), 2118–2124. https://doi.org/10.1016/j.fuel.2011.01.018
- Talling, B., & Brandstetr, J. (1989). Present state and future of alkali-activated slag concretes. In Proceedings of the Third International Conference on Fly Ash, Silica Fume, Slag, and Natural Pozzolans in Concrete. American Concrete Institute, Trondheim, Norway.
- Tchakouté, H. K., & Rüscher, C. H. (2017). Metakaolin-based geopolymer cements from commercial sodium waterglass and sodium waterglass from rice husk ash: A comparative study. In Developments in Strategic Ceramic Materials II, 1st (p. 296). John Wiley & Sons.
- Tchakouté, H. K., Rüscher, C. H., Kong, S., & Ranjbar, N. (2016). Synthesis of sodium waterglass from white rice husk ash as an activator to produce metakaolin-based geopolymer cements. Journal of Building Engineering, 6, 252–261. https://doi.org/10.1016/j.jobe.2016.04.007
- Tchakouté, H. K., Rüscher, C. H., Kong, S., Kamseu, E., & Leonelli, C. (2016). Comparison of metakaolin-based geopolymer cements from commercial sodium waterglass and sodium waterglass from rice husk ash. Journal of Sol-Gel Science and Technology, 78(3), 492–506. https://doi.org/10.1007/s10971-016-3983-6
- Technical Data sheet Panreac PA-ACS-ISO. (2020). PANREAC QUÍMICA S.L.U. España.
- Tempest, B. (2010). Engineering characterization of waste derived geopolymer cement concrete for structural applications [PhD thesis]. The University of North Carolina at Charlotte.
- Temuujin, J., & van Riessen, A. (2009). Effect of fly ash preliminary calcination on the properties of geopolymer. Journal of Hazardous Materials. 164(2-3), 634–639. https://doi.org/10.1016/j.jhazmat.2008.08.065
- Temuujin, J., van Riessen, A., & Williams, R. (2009). Influence of calcium compounds on the mechanical properties of fly ash geopolymer pastes. Journal of Hazardous Materials. 167(1–3), 82–88. https://doi.org/10.1016/j.jhazmat.2008.12.121
- Thomas, R. J., & Peethamparan, S. (2015). Alkali-activated concrete: Engineering properties and stress-strain behavior, Construction and Building Materials, 93, 49–56. https://doi.org/10.1016/j.conbuildmat.2015.04.039
- Tong, K. T., Vinai, R., & Soutsos, M. N. (2018). Use of Vietnamese rice husk ash for the production of sodium silicate as the activator for alkali-activated binders. Journal of Cleaner Production, 201, 272–286. https://doi.org/10.1016/j.jclepro.2018.08.025
- Tsen, T. J., Zeimaran, E., & Soutsos, M. (2019). Rice husk ash derived sodium silicate using hydrothermal and convection heating methods. In Proceedings of the AWAM International Conference on Civil Engineering 2019 - AICCE’19.
- Turner, L. K., & Collins, F. G. (2013). Carbon dioxide equivalent (CO2-e) emissions: a comparison between geopolymer and OPC cement concrete. Construction and Building Materials. 43, 125–130. https://doi.org/10.1016/j.conbuildmat.2013.01.023
- van Jaarsveld, J. S. G., van Deventer, J. S. J., & Lorenzen, L. (1998). Factors affecting the immobilization of metals in geopolymerized fly ash. Metallurgical and Materials Transactions B, 29(1), 283–291. https://doi.org/10.1007/s11663-998-0032-z
- Velandia, D. F., Lynsdale, C. J., Provis, J. L., Ramirez, F., & Gomez, A. C. (2016). Evaluation of activated high volume fly ash systems using Na2SO4, lime and quicklime in mortars with high loss on ignition fly ashes. Construction and Building Materials. 128, 248–255. https://doi.org/10.1016/j.conbuildmat.2016.10.076
- Villaquirán-Caicedo, M. A., Mejía de Gutierrez, R., & Gallego, N. C. (2017). A novel Mk-based geopolymer composite activated with rice husk ash and KOH: Performance at high temperature. Materiales de Construcción, 67(326), 117. https://doi.org/10.3989/mc.2017.02316
- Winnefeld, F., Leemann, A., Lucuk, M., Svoboda, P., & Neuroth, M. (2010). Assessment of phase formation in alkali activated low and high calcium fly ashes in building materials, Construction and Building Materials, 24(6), 1086–1093. https://doi.org/10.1016/j.conbuildmat.2009.11.007
- Xu, H., Gong, W. L., Syltebo, L., Izzo, K., Lutze, W., & Pegg, I. L. (2014). Effect of blast furnace slag grades on y ash based geopolymer waste forms. Fuel, 133, 332–340. https://doi.org/10.1016/j.fuel.2014.05.018
- Yang, K.-H., Cho, A.-R., & Song, J.-K. (2012). Effect of water–binder ratio on the mechanical properties of calcium hydroxide-based alkali-activated slag concrete. Construction and Building Materials. 29, 504–511. https://doi.org/10.1016/j.conbuildmat.2011.10.062
- Yaseri, S., Verki, V. M., & Mahdikhani, M. (2019). Utilization of high volume cement kiln dust and rice husk ash in the production of sustainable geopolymer. Journal of Cleaner Production, 230, 592–602. https://doi.org/10.1016/j.jclepro.2019.05.056
- Zhang, Z. H., Yang, T., & Wang, H. (2014). The effect of efflorescence on the mechanical properties of fly ash-based geopolymer binders. In Proceedings of the 23rd Australasian Conference on the Mechanics of Structures and Materials (ACMSM23) , S.T. Smith, Byron Bay, NSW (pp. 107–112).
- Zou, Y., & Yang, T. (2019). Chapter 9 – Rice husk, rice husk ash and their applications. In Rice bran and rice bran oil chemistry, processing and utilization (1st ed., p. 315). Academic Press.
Appendix A
Table A1. Existing models in the literature of modulus of elasticity for different types of concrete.
Appendix B
Table B1. Existing models in the literature of splitting tensile strength for different types of concrete.