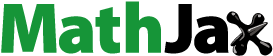
ABSTRACT
In this study, the laminar nanofluid flow in the microchannel with a discontinuous-boundary condition was investigated. Considering the slip condition, heat transfer and entropy generation were studied. Different layouts with the discontinuous-boundary condition (i.e. layouts A, B and C) were introduced and compared with the basic microchannel (microchannel with the continuous-boundary condition). Reynolds number and non-slip coefficient parameters on the effect of using discontinuous-boundary condition were discussed. The results revealed that the application of discontinuous-boundary condition affects the heat transfer as well as entropy generation so that the effects are more pronounced at higher Reynold number. By applying discontinuous-boundary condition, the heat transfer through the layouts of A, B and C was 34, 45 and 53% higher than the base microchannel. Simultaneously, the entropy generation through the layouts of A, B and C intensified by 31, 39 and 46%, respectively. The results proved that the applying slip condition has two positive effects as well as a negative effect. It enhanced the heat transfer and diminished the viscose entropy generation, but on the other hand, it intensified the thermal entropy generation.
1. Introduction
The investigations on the micro-scale devices (Xu et al., Citation2022) is fundamental in many industries such as aerospace (Weiß et al., Citation2019), electronics systems (Abo-Zahhad et al., Citation2019; Ma et al., Citation2019; Vajdi et al., Citation2020), photovoltaic–thermal systems (Ahmed & Radwan, Citation2017; Radwan et al., Citation2016), concentrator solar cells (Abo-Zahhad et al., Citation2020), etc. For the enhancement of the heat transfer on the micro-scale the microchannels are essential. Microchannels have a wide range of applications from microfluidics devices (Lai & Wong, Citation2021) to electronic devices for the quality of a better heat exchange. There are various methods to enhance the heat transfer including active methods such as magnetohydrodynamic (Jarray et al., Citation2020; Mehrez et al., Citation2015) and passive methods like adding nanoparticles to the base fluid (Li et al., Citation2021; Mehrez & El Cafsi, Citation2017, Citation2021a, Citation2021b; Sun et al., Citation2021). However, most methods result in a considerable pressure loss. Applying discontinuous-boundary conditions has been widely used in heat transfer cases (Bahrami et al., Citation2019; Ma et al., Citation2019; M. Mansour et al., Citation2018; Toghraie et al., Citation2019). Microchannels have a high surface-to-volume ratio and can be valuable in the cooling issue. The knowledge of material science has a vital role in industries(Kuskov et al., Citation2021; Torosyan et al., Citation2020) and shows by improving the thermal properties of the working fluid, the microchannels thermal performance can be enhanced (Huminic & Huminic, Citation2020). The thermal conductivity of nanoparticles is very high and many researchers have proven that adding nanoparticles to base fluids improves the thermal conductivity (Zahmatkesh et al., Citation2021).
By examining the second law of thermodynamic systems, the degree of deviation from the ideal state will be determined. The second law is examined from two perspectives of entropy (Chamkha et al., Citation2017; Mansour et al., Citation2019; Mehrez et al., Citation2015; Rashad et al., Citation2018; Rashad et al., Citation2019; Zamzari et al., Citation2015) or exergy balance equations (Tian et al., Citation2020). The entropy generation is concerned with the entropy balance equation (Mansour et al., Citation2019; Rashad et al., Citation2018; Rashad et al., Citation2019) while the exergy loss is obtained through solving the exergy balance equation (Abo-Zahhad et al., Citation2019; Abo-Zahhad et al., Citation2020) . Huminic and Huminic (Citation2020) presented a valuable study on the entropy-based second law analysis in which the viscous entropy generation
as well as thermal entropy generation
, are discussed comprehensively. Many studies have identified the effect of nanofluids on entropy production (Ishak et al., Citation2019; Shashikumar et al., Citation2018; Tayebi & Chamkha, Citation2019). Singh et al. (Citation2010) theoretically studied the entropy generation through the microchannel in the presence of
nanofluid (one of the first work in this field). The flow regime was considered laminar and turbulent. They established the correlations by which the ratio of entropy generation in the presence of nanofluids to the entropy generation in the presence of base fluid
can be determined. They proved that under the turbulent flow, incorporation of
into water diminished
. Ebrahimi et al. (Citation2016) investigated
through a rectangular cavity (with a 20 kW boundary condition at the left surface) to determine the effect of the presence of
and CuO nanoparticles. The results showed that the presence of both nanofluids reduced
. However, the decremental effect of adding CuO on
is greater than the decremental effect of the incorporation of
nanoparticles. In another study conducted by Heshmatian and Bahiraei (Citation2017), the effects of the presence of
nanoparticles in water have been investigated. The authors focused on the particle migration to determine
and
considering the Brownian diffusion using ANN. They found that as the nanoparticles size decreased,
intensified. By solving the energy and momentum equations, Yang et al. (Citation2015) determined the temperature as well as the velocity inside a trapezoidal cavity (nanofluid impregnated). They calculated the thermal and
considering the temperature gradients as well as the velocity gradients and found that
contribution to the viscous entropy production was about three times. Also, they observed that the zones with large
was located at the bottom side of the cavity. According to the results, as the Reynolds number (Re) decreased,
diminished while
amplified. The second law of analysis of a counter flow micro-heat exchanger was examined by Mohammadian et al. (Citation2014). The hot fluid (water) flows into the inner tube and the cold fluid
flows through the annular space. It was found that with increase in nanoparticle size and decrease in volume fraction,
diminished. In contrast, the thermal entropy generation intensified. As the thermal entropy generation contribution has a higher value than the viscous one, so
intensified with increase in particle size and decrease in volume fraction. The effect of hybrid nanofluid presence with non-Newtonian behavior on the thermal performance of a microchannel heat sink was investigated by Al-Rashed et al. (Citation2019). They examined the effects of adding CNT/Fe3O4 to the water on
. The simulation results revealed that by rising
to the critical number (
),
diminished. As
increases upon the critical value,
will rise. In the meantime, the use of numerical methods has been widely considered.
In this study, the laminar nanofluid flow in the microchannel with a discontinuous boundary condition was investigated. The major aim of this study is to boost the heat transfer without increasing pressure loss in the microchannel. To this goal, this study answers the question of whether heat transfer can be improved by applying discontinuous-boundary conditions? For this, we introduced three layouts to examine the effects of discontinuous-boundary conditions on heat transfer. Then, by examining the second law, the question is answered: what effect does the application of discontinuous-boundary conditions have on the entropy generation? It seems that owing to the presence of an adiabatic zone between the hot zones, the temperature gradients in hot zones intensify and therefore the heat transfer increases. The question then is answered that whether the heat transfer improvement made by applying discontinuous-boundary conditions is accompanied by more entropy generation or less?
2. Problem description
In this study, as shown in Figure , the microchannel walls were divided into two equal parts, with 25% of the walls subjected at constant temperature and the remaining 75% is adiabatic. The ratio of length to the height of the microchannel was considered 40. The main purpose of this study is to examine the hot-walls arrangement on HT as well as . Figure illustrates the different arrangements of the hot walls. Given the slip conditions, the Al2O3-water nanofluid enters the microchannel at a temperature of
. The nanofluid flow is assumed to be laminar and simulated within
of 5–100. Hot-wall temperatures are
. The thermophysical properties of nanofluid are reported in Table .
Table 1. Thermophysical properties of Al2O3-water (Jalali & Karimipour, Citation2019).
3. Governing equations
In many studies, researchers have used numerical methods to describe physical phenomena (Dinarvand et al., Citation2021; Huang et al., Citation2022; Mahdavi et al., Citation2021; Moradi et al., Citation2020; Razavi et al., Citation2019; Wang et al., Citation2021). In this paper, single-phase model is used for the nanofluid. The basic non-dimension equations for continuity, momentum and energy equation, in stationary and incompressible flow, can be written as follows(Dinarvand et al., Citation2021; Mahdavi et al., Citation2021; Razavi et al., Citation2019; Tayebi et al., Citation2021):
(1)
(1)
(2)
(2)
(3)
(3)
(4)
(4)
The dimensionless slip velocity is (Veera Krishna & Chamkha, Citation2021):
(5)
(5) where
is dimensionless slip coefficient. Also, the dimensionless parameters involved in Equations (1–4) are:
(6)
(6)
Boundary conditions:
(7)
(7)
The local and average Nusselt numbers are (Jalali & Karimipour, Citation2019):
(8)
(8)
(9)
(9) Entropy generation shows the value of irreversibility that is usually attributed to heat transfer and friction. Generally, in this study, the local entropy generation includes frictional and thermal that obtained as follows (Esfahani et al., Citation2017; Kefayati, Citation2015):
(10)
(10)
(11)
(11) and the dimensionless form of local entropy generations:
(12)
(12)
(13)
(13)
The normalized dimensionless entropy generations rate per unit depth are:
(14)
(14)
(15)
(15)
It is worth mentioning that to obtain nanofluid properties, the following equations are used. To solve the density, the specific heat capacity viscosity, and effective thermal conductivity(Brinkman, Citation1952; Jalali & Karimipour, Citation2019; Patel et al., Citation2006):
(16)
(16)
(17)
(17)
(18)
(18)
(19)
(19)
(20)
(20)
In Equation (20), c is an experimental constant and its value is 15000. Kf and Ks are the thermal conductivity of fluid and nanoparticles that are 0.613 and 40 W/mK, respectively.
The molecular area’s ratio of the base-liquid and that of solid nanoparticles is as follows where Pe, and j are defined as follows:
(21)
(21)
Pe is a constant parameter and describes as follows:
(22)
(22)
In Equation (22), j is associated with the impact of the Brownian motion and is obtained as follows: where Kb = J/K (the Boltzmann constant) and the molecular diameter of water and solid nanoparticles is df = 2 A° and ds = 40 nm, respectively
(23)
(23)
4. Grid study and validation
The finite volume method (FVM) with second-order discretization (to have more accurate) is utilized for continuity, momentum, and energy equations. In addition, coupling of the pressure and velocity is implemented by the SIMPLE algorithm. Grid study is performed using four networks with different grid numbers (Table ). The mean Nusselt number was used to examine the grid study. According to Table , for Network A, with the grid number of 7000, is 1.63. By doubling the number of meshes (Network B),
is increased by 17.79%. This figure for networks of C and D is 3.12% and 1%. Since the difference between the results of C and D networks is acceptable, hence network C is selected and utilized.
Table 2. Grid study.
For validation, the results of Raisi et al. (Citation2011). In their study, the nanofluid flow in a microchannel with a constant temperature boundary was investigated by considering the slip condition. The comparison between the present study and Raisi et al. (Citation2011) is shown in Figures and . In Figure , local Nusselt number is depicted along the microchannel walls and in Figure dimensionless slip velocity (as a function of vertical direction) at the microchannel outlet. As can be seen, the results are in good agreement with those of Raisi et al. (Citation2011). Therefore, the methods of solving the conservation equations are reliable.
5. Results
In the base microchannel, the constant temperature location on the wall remains constant. Whereas in other microchannels, constant temperature locations become smaller and smaller. It should be noted that in all microchannels, half of the upper wall is subjected to a constant temperature boundary condition . The other half of the wall is adiabatic. First, heat transfer through these microchannels investigate and then the thermal, viscose and
will analyze considering the slip condition and non-slip condition.
5.1. Nusselt number
Figure shows along the upper microchannel wall in four different layouts. Simulations were performed at
, and 0.02 vol.%. as well as
of 5, 20, 60 and 100. In all microchannels, the highest
occurs at the entrance of the zones which is subjected to constant temperature boundary conditions and then, gradually decreases along the microchannel. In insulated zones where the temperature gradient is zero,
is also zero. For layout b, the two discontinuity created in the local Nusselt diagram corresponds to the two zones with a constant temperature boundary condition. The constant temperature locations are well illustrated in Figure . In other layouts, there is discontinuity caused by the presence of high-temperature locations.
If the calculation of is performed, the mean value of Nu is obtained. The area under the curve for layout A is larger than that of the base case. This means that
for layout A is higher which is equivalent to more heat transfer in layout A than that of the base one.
From a physical point of view, in layout A, after the fluid passes through the first hot zone, the temperature of the fluid in the area close to the wall, increases. For the adiabatic zone, no extra thermal energy is added to the fluid molecules. Therefore, hot molecules have the opportunity to transfer energy to colder molecules through molecular collisions along with molecular diffusion. Therefore, in the adiabatic zones, the temperature distribution becomes more uniform and therefore the molecules near the upper wall become cooled. As the fluid approaches the second hot zone, these cold molecules can receive more heat from the hot wall because they have cooled in the previous zone (which was adiabatic). Therefore, as the number of hot zones increases, more heat is expected to transfer between the wall and the fluid.
Figure shows for four layouts at
, and 0.02 vol.%. As the
rises, the temperature gradient decreases and hence HT improves. On the other hand, since
is better for layout C, it can be concluded that applying a discontinuous-constant temperature boundary condition is better than the continuous one. The more the number of intermittent boundary conditions, the greater the impact on HT.
Figure shows of different layouts relative to the base microchannel. In this case, the base microchannel has a continuous-constant temperature boundary condition at
.
Based on the results, at ,
of layouts of A, B and C is improved by 10, 19 and 26% compared to the base microchannel. Therefore, applying a discontinuous boundary condition can improve HT up to 26%. This figure at
is 53%. The heat transfer in the microchannel with slip condition is higher than the non-slip microchannel. Because applying the slip condition reduces the temperature gradient along the wall and hence enhances HT.
The temperature distribution for the four layouts is shown in Figure . It is observed that at higher the Reynolds (b), a smaller percentage of the fluid molecules have undergone a temperature gradient, or, at higher Reynolds (state B), the temperature variations in the fluid are concentrated in the vicinity of the wall.
5.2. Entropy generation
In this section, the effects of ,
and the most important parameter of this study, namely applying discontinues-boundary conditions. As noted,
is caused by the velocity and temperature gradients. The velocity gradient is responsible for
while the temperature gradient leads to the thermal entropy generation. First,
is examined. Figure shows
for the four layouts. According to the results,
increases with increasing
. Any rise in
results in an increase in the velocity gradient in the microchannel which consequently raises the viscous entropy generation. More focus on Figure reveals that the using discontinuous-boundary condition (i.e. layouts of A, B and C) has no considerable effect on viscous entropy generation. Because
depends only on the velocity gradient. Changing the layout has no particular effect on the velocity gradient. As shown in Figure , applying discontinuous-boundary conditions only affects the temperature gradient.
Figure shows in terms of
. According to this figure, it can be seen that at
(microchannel with the non-slip condition)
is the highest. As
rises, the viscous entropy diminished. Because as
rises, the velocity gradient diminishes. Decreasing the velocity gradient results in a reduction in the viscosity-generation entropy term.
Figure shows the effect of the layouts on the thermal entropy generation. As shown in Figure , it is observed that the effect of applying discontinuous-boundary conditions at the higher is more noticeable. As
rises, the thermal boundary layer growth decreases. As the effect of applying discontinuous-boundary condition is more pronounced at higher
, it is therefore predicted that at higher
, the difference between the layouts of A, B and C are more.
It can be seen in Figure that
With increasing
,
amplify owing to the growth in the temperature gradients
Any growth in
improves HT (Figure ). Higher HT means a higher temperature gradient, which subsequently intensifies the thermal entropy generation.
Applying discontinuous-boundary conditions leads to HT improvement (Figure ). The more HT is due to the higher temperature gradient. On the other hand, a higher temperature gradient means a higher rate of thermal entropy generation.
Figure showed that the heat transfer for layouts A, B and C was higher than for the base case. Because the presence of adiabatic leads to the opportunity for warm molecules near the wall to transfer their energy to colder molecules. Therefore, the temperature in the adiabatic zone becomes uniform. This means that the temperature of the molecules close to the wall decreases. Thus, molecules close to the wall enter the next hot zones at lower temperatures. As the temperature difference in these areas increases, heat transfer intensifies. Although from the first law viewpoint, increasing the temperature difference is desirable (because it increases the heat transfer), but from the point of view of the second law, increasing the temperature difference is not very desirable. In other words, although the greater the temperature difference, the higher the heat transfer, but it should be noted that this heat transfer is accomplished with more irreversibility, which is not very desirable from the second law viewpoint. Therefore, in layouts A, B and C, heat transfer and entropy generation are higher than the base microchannel. Based on Figure , the microchannel with the continuous-boundary condition, if is increased from 0 to 0.1,
will increase up to 13%. The same is true in the layouts of A, B and C. Increasing
from 0 to 0.1 leads to an increase in
up to 31% (for layout A), 39% (for layout B) and 46% (for layout C).
The distribution of for each layout is shown in Figure . In the regions where the constant temperature boundary condition is applied, the concentration of
(zones marked in red) is high. Because in these zones, the temperature gradient is higher than in the other regions. On the other hand, at constant
(e.g. 200), it is observed that in the layout of C, where the most discontinuity in the boundary condition is present, there is a greater thermal entropy generation. Therefore, the arrangement of using discontinuity-boundary conditions can affect the thermal entropy generation.
Figure compares the distribution of at
and
. Note that the comparison is performed for layout B. In both Reynolds numbers, applying the slip condition causes the increase in a temperature gradient, hence
intensified. However, the effect of slip condition at higher
is more pronounced. On the other hand, the effect of
on
is illustrated in Figure . The results prove that there is the highest distribution of
along the microchannel walls, and as the
increases,
increases. Also, as
increases, the distribution of
in the microchannel center decreases.
6. Conclusion
In the current research four types of the microchannel with continuous-boundary conditions with equal heat sources’ area were examined using the finite volume method. Moreover, the microchannels were analyzed by the impacts of various parameters such as Re number, slip velocity on heat transfer, and entropy generation. The numerical results confirmed that the continuous-boundary conditions are highly beneficial to increasing the heat transfer which in comparison to the base microchannel HT boosted by 26%. Applying the slip condition changed the sensitivity of HT to the arrangement. At β* = 0.1, using discontinuous boundary conditions improved HT by 34, 45, and 53% for layouts A, B, and C, respectively. Based on the second law analysis main, It was found that applying discontinuous boundary conditions, did not affect the viscous entropy generation significantly although viscous entropy generation intensified with increasing Re while it reduced as β* increased. As for thermal entropy generations, since continuous-boundary conditions played a vital role in increasing the temperature gradient, it increased the thermal entropy generation as a result of the higher gradient. Furthermore, if β* increased from 0 to 0.1, intensified up to 13%. This figure was 31% (for layout A), 39% (for layout B), and 46% (for layout C).
Nomenclature
A | = | Area (m2) |
c | = | experimental constant |
= |
| |
d | = | Diameter (m) |
= | ||
= | ||
= | ||
j | = | impact of the Brownian motion |
Kb | = | Boltzmann constant J/K |
= | ||
= | ||
= | ||
= | ||
= | ||
= | ||
Pe | = | constant parameter |
= | ||
Re | = | |
= |
| |
= |
| |
= |
| |
= |
| |
= |
| |
= | ||
= | ||
= | ||
= | ||
= | ||
= | ||
= | ||
= |
Greek letters
= | Dimensionless slip coefficient | |
β | = | Slip coefficient (mm) |
= |
| |
µ | = |
|
= | ||
= | ||
= | ||
α | = |
Super and subscripts
ave | = | average |
c | = | cold |
f | = | fluid |
h | = | hot |
nf | = | nanofluid |
s | = | solid |
Disclosure statement
No potential conflict of interest was reported by the author(s).
References
- Abo-Zahhad, E. M., Ookawara, S., Esmail, M. F. C., El-Shazly, A. H., Elkady, M. F., & Radwan, A. (2020). Thermal management of high concentrator solar cell using new designs of stepwise varying width microchannel cooling scheme. Applied Thermal Engineering, 172, 115124. https://doi.org/10.1016/j.applthermaleng.2020.115124
- Abo-Zahhad, E. M., Ookawara, S., Radwan, A., El-Shazly, A. H., & Elkady, M. F. (2019). Numerical analyses of hybrid jet impingement/microchannel cooling device for thermal management of high concentrator triple-junction solar cell. Applied Energy, 253, 113538. https://doi.org/10.1016/j.apenergy.2019.113538
- Ahmed, M., & Radwan, A. (2017). Performance evaluation of new modified low-concentrator polycrystalline silicon photovoltaic/thermal systems. Energy Conversion and Management, 149, 593–607. https://doi.org/10.1016/j.enconman.2017.07.057
- Al-Rashed, A. A. A. A., Shahsavar, A., Entezari, S., Moghimi, M. A., Adio, S. A., & Nguyen, T. K. (2019). Numerical investigation of non-Newtonian water-CMC/CuO nanofluid flow in an offset strip-fin microchannel heat sink: Thermal performance and thermodynamic considerations. Applied Thermal Engineering, 155, 247–258. https://doi.org/10.1016/j.applthermaleng.2019.04.009
- Bahrami, A., Poshtiri, A. H., & Akbarpoor, A. M. (2019). Nusselt number correlations for forced convection in a microchannel including discrete heat sources. Journal of Thermophysics and Heat Transfer, 7(11), 1–12. https://doi.org/10.2514/1.T5814
- Brinkman, H. C. (1952). The viscosity of concentrated suspensions and solutions. The Journal of Chemical Physics, 20(4), 571–571. https://doi.org/10.1063/1.1700493
- Chamkha, A. J., Rashad, A. M., Mansour, M. A., Armaghani, T., & Ghalambaz, M. (2017). Effects of heat sink and source and entropy generation on MHD mixed convection of a Cu-water nanofluid in a lid-driven square porous enclosure with partial slip. Physics of Fluids, 29(5), 052001. https://doi.org/10.1063/1.4981911
- Dinarvand, M., Abolhasani, M., Hormozi, F., & Bahrami, Z. (2021). Cooling capacity of magnetic nanofluid in presence of magnetic field based on first and second laws of thermodynamics analysis. Energy Sources, Part A: Recovery, Utilization, and Environmental Effects, 1–17. https://doi.org/10.1080/15567036.2021.1872746
- Ebrahimi, A., Rikhtegar, F., Sabaghan, A., & Roohi, E. (2016). Heat transfer and entropy generation in a microchannel with longitudinal vortex generators using nanofluids. Energy, 101, 190–201. https://doi.org/10.1016/j.energy.2016.01.102
- Esfahani, J., Akbarzadeh, M., Rashidi, S., Rosen, M., & Ellahi, R. (2017). Influences of wavy wall and nanoparticles on entropy generation over heat exchanger plat. International Journal of Heat and Mass Transfer, 109, 1162–1171. https://doi.org/10.1016/j.ijheatmasstransfer.2017.03.006
- Heshmatian, S., & Bahiraei, M. (2017). Numerical investigation of entropy generation to predict irreversibilities in nanofluid flow within a microchannel: Effects of Brownian diffusion, shear rate and viscosity gradient. Chemical Engineering Science, 172, 52–65. https://doi.org/10.1016/j.ces.2017.06.024
- Huang, K., Su, B., Li, T., Ke, H., Lin, M., & Wang, Q. (2022). Numerical simulation of the mixing behaviour of hot and cold fluids in the rectangular T-junction with/without an impeller. Applied Thermal Engineering, 204, 117942. https://doi.org/10.1016/j.applthermaleng.2021.117942
- Huminic, G., & Huminic, A. (2020). Entropy generation of nanofluid and hybrid nanofluid flow in thermal systems: A review. Journal of Molecular Liquids, 302, 112533. https://doi.org/10.1016/j.molliq.2020.112533
- Ishak, M. S., Alsabery, A. I., Chamkha, A., & Hashim, I. (2019). Effect of finite wall thickness on entropy generation and natural convection in a nanofluid-filled partially heated square cavity. International Journal of Numerical Methods for Heat & Fluid Flow, 22(9), 122–139. https://doi.org/10.1108/HFF-06-2019-0505
- Jalali, E., & Karimipour, A. (2019). Simulation the effects of cross-flow injection on the slip velocity and temperature domain of a nanofluid flow inside a microchannel. International Journal of Numerical Methods for Heat & Fluid Flow, 29(5), 1546–1562. https://doi.org/10.1108/HFF-04-2018-0149
- Jarray, A., Mehrez, Z., & El Cafsi, A. (2020). Effect of magnetic field on the mixed convection $$Fe_3O_4/water $$ Fe 3 O 4/water ferrofluid flow in a horizontal porous channel. Pramana, 94(1), 1–12. https://doi.org/10.1007/s12043-020-02015-7
- Kefayati, G. R. (2015). FDLBM simulation of entropy generation due to natural convection in an enclosure filled with non-Newtonian nanofluid. Powder Technology, 273, 176–190. https://doi.org/10.1016/j.powtec.2014.12.042
- Kuskov, K. V., Abedi, M., Moskovskikh, D. O., Serhiienko, I., & Mukasyan, A. S. (2021). Comparison of conventional and flash spark plasma sintering of Cu–Cr pseudo-alloys: Kinetics, structure, properties. Metals, 11(1), 141. https://doi.org/10.3390/met11010141
- Lai, W.-F., & Wong, W.-T. (2021). Property-tuneable microgels fabricated by using flow-focusing microfluidic geometry for bioactive agent delivery. Pharmaceutics, 13(6), 787. https://doi.org/10.3390/pharmaceutics13060787
- Li, Y., Moradi, I., Kalantar, M., Babadi, E., Malekahmadi, O., & Mosavi, A. (2021). Synthesis of new dihybrid nanofluid of TiO2/MWCNT in water–ethylene glycol to improve mixture thermal performance: Preparation, characterization, and a novel correlation via ANN based on orthogonal distance regression algorithm. Journal of Thermal Analysis and Calorimetry, 144(6), 2587–2603. https://doi.org/10.1007/s10973-020-10392-9
- Ma, D. D., Xia, G. D., Zong, L. X., Jia, Y. T., Tang, Y. X., & Zhi, R. P. (2019a). Experimental investigation of flow boiling heat transfer performance in zigzag microchannel heat sink for electronic cooling devices. International Journal of Thermal Sciences, 145, 106003. https://doi.org/10.1016/j.ijthermalsci.2019.106003
- Ma, Y., Mohebbi, R., Rashidi, M., & Yang, Z. (2019b). MHD convective heat transfer of Ag-MgO/water hybrid nanofluid in a channel with active heaters and coolers. International Journal of Heat and Mass Transfer, 137, 714–726. https://doi.org/10.1016/j.ijheatmasstransfer.2019.03.169
- Mahdavi, M., Sharifpur, M., Aybar, H. S., Chamkha, A. J., & Meyer, J. P. (2021). Impact of micro-fins on a heated cylinder submerged in a nanofluid saturated medium. International Journal of Heat and Mass Transfer, 177, 121551. https://doi.org/10.1016/j.ijheatmasstransfer.2021.121551
- Mansour, M., Janiga, G., Nigam, K., Thévenin, D., & Zähringer, K. (2018). Numerical study of heat transfer and thermal homogenization in a helical reactor. Chemical Engineering Science, 177, 369–379. https://doi.org/10.1016/j.ces.2017.11.031
- Mansour, M. A., Armaghani, T., Chamkha, A. J., & Rashad, A. M. (2019). Entropy generation and nanofluid mixed convection in a C-shaped cavity with heat corner and inclined magnetic field. The European Physical Journal Special Topics, 228(12), 2619–2645. https://doi.org/10.1140/epjst/e2019-900050-3
- Mehrez, Z., Cafsi, A. E., Belghith, A., & Quéré, P. L. (2015a). Effect of heated wall position on heat transfer and entropy generation of Cu–water nanofluid flow in an open cavity. Canadian Journal of Physics, 93(12), 1615–1629. https://doi.org/10.1139/cjp-2014-0388
- Mehrez, Z., & El Cafsi, A. (2017). Thermodynamic analysis of $${{Al}}_{2}{O}_{3}$$–water nanofluid flow in an open cavity under pulsating inlet condition. International Journal of Applied and Computational Mathematics, 3(1), 489–510. https://doi.org/10.1007/s40819-017-0366-9
- Mehrez, Z., & El Cafsi, A. (2021a). Forced convection Fe3O4/water nanofluid flow through a horizontal channel under the influence of a non-uniform magnetic field. The European Physical Journal Plus, 136(4), 451. https://doi.org/10.1140/epjp/s13360-021-01410-2
- Mehrez, Z., & El Cafsi, A. (2021b). Heat exchange enhancement of ferrofluid flow into rectangular channel in the presence of a magnetic field. Applied Mathematics and Computation, 391, 125634. https://doi.org/10.1016/j.amc.2020.125634
- Mehrez, Z., El Cafsi, A., Belghith, A., & Le Quéré, P. (2015b). MHD effects on heat transfer and entropy generation of nanofluid flow in an open cavity. Journal of Magnetism and Magnetic Materials, 374, 214–224. https://doi.org/10.1016/j.jmmm.2014.08.010
- Mohammadian, S. K., Reza Seyf, H., & Zhang, Y. (2014). Performance augmentation and optimization of aluminum oxide-water nanofluid flow in a two-fluid microchannel heat exchanger. Journal of Heat Transfer, 136(2), 2. https://doi.org/10.1115/1.4025431
- Moradi, I., Karimipour, A., Afrand, M., Li, Z., & Bach, Q.-V. (2020). Three-dimensional numerical simulation of external fluid flow and heat transfer of a heat exchanger in a wind tunnel using porous media model. Journal of Thermal Analysis and Calorimetry, 141(5), 1647–1667. https://doi.org/10.1007/s10973-020-10184-1
- Patel, H. E., Anoop, K., Sundararajan, T., & Das, S. K. (2006). A micro-convection model for thermal conductivity of nanofluids. Paper presented at the International heat transfer conference 13, London, UK, 12 May 2006.
- Radwan, A., Ahmed, M., & Ookawara, S. (2016). Performance enhancement of concentrated photovoltaic systems using a microchannel heat sink with nanofluids. Energy Conversion and Management, 119, 289–303. https://doi.org/10.1016/j.enconman.2016.04.045
- Raisi, A., Ghasemi, B., & Aminossadati, S. (2011). A numerical study on the forced convection of laminar nanofluid in a microchannel with both slip and no-slip conditions. Numerical Heat Transfer, Part A: Applications, 59(2), 114–129. https://doi.org/10.1080/10407782.2011.540964
- Rashad, A. M., Armaghani, T., Chamkha, A. J., & Mansour, M. A. (2018). Entropy generation and MHD natural convection of a nanofluid in an inclined square porous cavity: Effects of a heat sink and source size and location. Chinese Journal of Physics, 56(1), 193–211. https://doi.org/10.1016/j.cjph.2017.11.026
- Rashad, A. M., Mansour, M. A., Armaghani, T., & Chamkha, A. J. (2019). MHD mixed convection and entropy generation of nanofluid in a lid-driven U-shaped cavity with internal heat and partial slip. Physics of Fluids, 31(4), 042006. https://doi.org/10.1063/1.5079789
- Razavi, S. E., Farhangmehr, V., & Babaie, Z. (2019). Numerical investigation of hemodynamic performance of a stent in the main branch of a coronary artery bifurcation. BioImpacts: Bi, 9(2), 97–103. https://doi.org/10.15171/bi.2019.13
- Shashikumar, N., Gireesha, B., Mahanthesh, B., Prasannakumara, B., & Chamkha, A. J. (2018). Entropy generation analysis of magneto-nanoliquids embedded with aluminium and titanium alloy nanoparticles in microchannel with partial slips and convective conditions. International Journal of Numerical Methods for Heat & Fluid Flow, 5(9), 38–45. https://doi.org/10.1108/HFF-06-2018-0301
- Singh, P. K., Anoop, K. B., Sundararajan, T., & Das, S. K. (2010). Entropy generation due to flow and heat transfer in nanofluids. International Journal of Heat and Mass Transfer, 53(21), 4757–4767. https://doi.org/10.1016/j.ijheatmasstransfer.2010.06.016
- Sun, L., Wang, G., Zhang, C., Jin, Q., & Song, Y. (2021). On the rheological properties of multi-walled carbon nano-polyvinylpyrrolidone/silicon-based shear thickening fluid. Nanotechnology Reviews, 10(1), 1339–1348. https://doi.org/10.1515/ntrev-2021-0087
- Tayebi, T., & Chamkha, A. J. (2019). Entropy generation analysis during MHD natural convection flow of hybrid nanofluid in a square cavity containing a corrugated conducting block. International Journal of Numerical Methods for Heat & Fluid Flow, 13(8), 66–76. https://doi.org/10.1108/HFF-04-2019-0350
- Tayebi, T., Dogonchi, A. S., Karimi, N., Ge-JiLe, H., Chamkha, A. J., & Elmasry, Y. (2021). Thermo-economic and entropy generation analyses of magnetic natural convective flow in a nanofluid-filled annular enclosure fitted with fins. Sustainable Energy Technologies and Assessments, 46, 101274. https://doi.org/10.1016/j.seta.2021.101274
- Tian, M.-W., Parikhani, T., Jermsittiparsert, K., & Ashraf, M. A. (2020). Exergoeconomic optimization of a new double-flash geothermal-based combined cooling and power (CCP) system at two different cooling temperatures assisted by boosters. Journal of Cleaner Production, 261.(4), 69–88. https://doi.org/10.1016/j.jclepro.2020.120921.
- Toghraie, D., Mashayekhi, R., Arasteh, H., Sheykhi, S., Niknejadi, M., & Chamkha, A. J. (2019). Two-phase investigation of water-Al2O3 nanofluid in a micro concentric annulus under non-uniform heat flux boundary conditions. International Journal of Numerical Methods for Heat & Fluid Flow, 9(8), 117–133. https://doi.org/10.1108/HFF-11-2018-0628
- Torosyan, K. S., Sedegov, A. S., Kuskov, K. V., Abedi, M., Arkhipov, D. I., Kiryukhantsev-Korneev, P. V., Vorotilo Stepan Moskovskikh Dmitry O., Mukasyan, A. S. (2020). Reactive, nonreactive, and flash spark plasma sintering of Al2O3/SiC composites—A comparative study. Journal of the American Ceramic Society, 103(1), 520–530. https://doi.org/10.1111/jace.16734
- Vajdi, M., Moghanlou, F. S., Niari, E. R., Asl, M. S., & Shokouhimehr, M. (2020). Heat transfer and pressure drop in a ZrB2 microchannel heat sink: A numerical approach. Ceramics International, 46(2), 1730–1735. https://doi.org/10.1016/j.ceramint.2019.09.146
- Veera Krishna, M., & Chamkha, A. J. (2021). Thermo-diffusion, Chemical reaction, Hall and ion slip effects on MHD rotating flow of micro-polar fluid past an infinite vertical porous surface. International Journal of Ambient Energy, 7(11), 1-29. https://doi.org/10.1080/01430750.2021.1946146
- Wang, Y., Wang, H., Zhou, B., & Fu, H. (2021). Multi-dimensional prediction method based on Bi-LSTMC for ship roll. Ocean Engineering, 242, 110106. https://doi.org/10.1016/j.oceaneng.2021.110106
- Weiß, A., Popp, T., Zinn, G., Preißinger, M., & Brüggemann, D. (2019). A micro-turbine-generator-construction-kit (MTG-c-kit) for small-scale waste heat recovery ORC-plants. Energy, 181, 51–55. https://doi.org/10.1016/j.energy.2019.05.135
- Xu, H., He, T., Zhong, N., Zhao, B., & Liu, Z. (2022). Transient thermomechanical analysis of micro cylindrical asperity sliding contact of SnSbCu alloy. Tribology International, 167, 107362. https://doi.org/10.1016/j.triboint.2021.107362
- Yang, Y.-T., Wang, Y.-H., & Huang, B.-Y. (2015). Numerical optimization for nanofluid flow in microchannels using entropy generation minimization. Numerical Heat Transfer, Part A: Applications, 67(5), 571–588. https://doi.org/10.1080/10407782.2014.937282
- Zahmatkesh, I., Sheremet, M., Yang, L., Heris, S. Z., Sharifpur, M., Meyer, J. P., Ghalambaz Mohammad Wongwises Somchai Jing Dengwei, Mahian, O. (2021). Effect of nanoparticle shape on the performance of thermal systems utilizing nanofluids: A critical review. Journal of Molecular Liquids, 321, 114430. https://doi.org/10.1016/j.molliq.2020.114430
- Zamzari, F., Mehrez, Z., Cafsi, A. E., Belghith, A., & Quéré, P. L. (2015). Entropy generation and mixed convection in a horizontal channel with an open cavity. International Journal of Exergy, 17(2), 219–239. https://doi.org/10.1504/IJEX.2015.069993