ABSTRACT
The aim of this research is to determine if the polyesterification of sorbitol and citric acid in wood has a future potential as a wood modification process. Pine wood was impregnated with an aqueous solution containing citric acid and sorbitol and was thereafter cured at 103 or 140°C for 18 hours. The dimensional stability and leaching resistance were studied for both modification temperatures. The leachates from the modified wood samples were analysed by HPLC and the susceptibility to decay and staining fungi were studied. Impregnated samples cured at 140°C showed a permanent (leach-resistant) increased dimensional change, but samples treated at 103°C were not stable to leaching. Treated samples cured at 103 and 140°C showed significant resistance to white-rot (Trametes versicolor) and brown-rot decay (Postia placenta) after a leaching procedure. Furthermore, samples cured at 103 and 140°C (leached and unleached) were significantly less susceptible to blue-stain fungi than the untreated controls.
Introduction
The uses of wood as a material in the building industry are continuously increasing in the European countries (http://ec.europa.eu/eurostat).
Most native European wood species have low inherent durability, and for applications where high durability is needed, these wood species require additional protection to meet the requirements for product lifetime. One way to protect wood is to treat it with biocides to prevent microbiological degradation in outdoor situations. Environmentally motivated legislation is making the use of biocides less attractive from a commercial perspective and promotes the search for new low-cost wood modification technologies (Hill Citation2006). Apart from imparting decay resistance, wood modification can also confer additional advantages on wood, such as improved dimensional stability.
Ideally, in order to limit capital expenditure, a low-cost wood modification technology should be water based and use thermal curing. This research has concentrated on the potentials for esterification of citric acid and sorbitol in an aqueous-based modification process. Citric acid and sorbitol are both low priced and readily available feedstock chemicals, an essential pre-requisite for a commercial modification process. Citric acid is mostly produced by microbial fermentation using Aspergillus niger (Show et al. Citation2015). Traditionally sorbitol is industrially manufactured from starch by enzymatic hydrolysis of starch to dextrose and catalytic hydrogenation of dextrose to sorbitol (Young and O’Sullivan Citation2011). Sorbitol can also be produced from cellulose in biomass as presented by Romero et al. (Citation2016). In order to improve dimensional stabilisation and decay resistance, it is necessary that the reagents are capable of penetrating the cell wall and that once polymerisation takes place within the cell wall the bulking agent should not be leachable by water (Hill Citation2011). The reaction of sorbitol with citric acid is potentially of interest from a wood modification perspective. Doll et al. (Citation2006) note that sorbitol has been used to synthesise polyesters. They reacted citric acid with sorbitol in melt conditions in a vacuum oven, with reaction temperatures of 110 and 150°C for 2 or 4 hours. Evidence for polymerisation was found at both reaction temperatures, although the reaction was considerably faster at 150°C. The reaction mechanism () was considered to proceed via the uncatalyzed dehydration of the citric acid (A) to form a cyclic anhydride intermediate (B) which reacted with the sorbitol (C) to form an ester (D), further dehydration can lead to the formation of another cyclic anhydride intermediate (E) or an anhydrosorbitol ring (F), which can then undergo further polymerisation reactions. Centonella and Razor (Citation1972) showed that polyesters of sorbitol and citric acid could be prepared from aqueous solution by heating between 130 and 150°C and removing the water from the reaction mixture.
Limited research has been performed on the utilisation of sorbitol for wood modification. Bateson (Citation1938, Citation1939) conducted experiments on using sorbitol for dimensional stabilisation of the wooden matrix. In this case, the sorbitol was used as a consolidant only and was not reacted with the wood or with other reagents. A published patent by Kiljunen et al. (Citation2011) mentions wood modification using a combination of sorbitol with citric acid (along with other combinations of water-soluble reagents), with some experimental details. The reaction involved a combination of aqueous solutions of 5% citric acid and 10% of an alcohol (wt/wt) plus the addition of 2% sodium hypophosphite as a catalyst. Samples were vacuum-impregnated at 10 mbar and then left for one week to allow for diffusion of the reagents into the cell wall, then air dried for 24 hours, followed by heating in an oven at 120°C for 24 hours. There was a reported reduction in Weight Percent Gain (WPG) from 18 to 9% after leaching of the sorbitol-citric acid treated wood.
However, work has been performed on the modification of wood using polyesterification reaction reagents other than sorbitol. The research group of Marion Noël at Bern University of Applied Sciences describes among others the use of glycolic and lactic acids and polybutylenesuccinate (PBS) and polybutylene adipate esters as a wood modification agent. They have looked into impregnation behaviour, mechanical properties and hydrophobicity of modified beech, maple and radiata pine samples (Noël et al. Citation2014; Noël, Grigsby, Vitkeviciute, et al. Citation2015; Noël, Grigsby, Volkmer Citation2015). Their impregnation procedure was either performed with melt polymerisation, room temperature impregnation or the solution was pre-heated with no addition of water and they reached a weight uptake of ca 150% (Noël, Volkmer, Pichelin Citation2015).
Several studies have targeted the use of citric acid and glycerol for wood protection. Essoua et al. (Citation2016) treated samples of Pinus strobus and Pinus contorta with citric acid and glycerol and cured the samples at temperatures of 180°C. L’Hostis et al. (Citation2017) treated Fagus sylvatica with citric acid and glycerol and cured at temperatures ranging from 100 to 160°C. Both studies prove among other properties a better protection against fungal decay and improved mechanical properties. Berube et al. (Citation2018) modified wood with glycerol and citric acid and found that the use of acid catalysts resulted in higher levels of polymerisation. Citric acid has been reacted with wood in order to produce a material that is able to remove metal ions from solution (Low et al. Citation2004; McSweeny et al. Citation2006). A combination of sucrose and citric acid has been used as an adhesive for particleboard production (Umemura et al. Citation2013, Citation2015; Widyorini et al. Citation2016) and citric acid has been used as an adhesive for wood flour based mouldings (Umemura et al. Citation2012). Citric acid has also been used as a wood modification method to improve the water resistance of the end grain of butt joints in wood welding (Amirou et al. Citation2017) and as a wood modification agent for solid wood where it acts as a cell wall crosslinking agent (Vukusic et al. Citation2006; Ou et al. Citation2016).
The aim of this research is to determine if the polyesterification of sorbitol and citric acid in wood has a future potential as wood protection agents, by investigating the following properties:
stability of the reacted chemical
dimensional stability of the treated wood
decay resistance
resistance to blue-stain fungi
Material and methods
Chemicals
Powdered citric acid (VWR Chemicals, CAS 77-92-9) and D-Sorbitol (VWR Chemicals, CAS 50-70-4) were used in a 3:1 molar ratio to achieve complete esterification of the citric acid. These solids were dissolved in deionised water during stirring at 20°C together with 8 g of water to each 10 g of solids. The liquid solution exhibited a pH of 2 and a density of 1.284 g cm−3.
Wood samples and treatment
The samples for the various test were produced from pine sapwood (Pinus sylvestris), and the data on sample dimensions, replicates, uptake and WPG are in accordance to . Pine wood is the predominant wood species used for wood modification processes intended for outdoor use in northern Europe, hence Norwegian grown pine was chosen for this experiment.
Table 1. Wood properties before and after impregnation and leaching.
All wood samples, except for the untreated controls, were impregnated with the solution performing a 30 min pre-vacuum of 40 mbar followed by 1 hour of 8 bars of pressure. The samples were then cured for 18 hours at a temperature of 103 or 140°C. Then the samples were acclimatised at 20°C and 65% RH until stable weight. The level of treatment was calculated as WPG, which is the percentage difference between the dry weight before and after treatment. WPG is calculated as follows:where Mm is the oven-dry mass of the modified and the Mu is the oven-dry mass of the unmodified wood.
Stability of the reacted chemical
For the fungal testing (see below), the samples were leached according to EN 84 (European Standard Citation1997a) over a period of 363 hours. In addition to the first water change after a vacuum period of 20 min, 10 water changes were performed. Before each water change 20 mL of leachate was pipetted out and stored in the dark at a temperature of 4°C. The water samples were collected after 2, 22, 47, 73, 99, 167, 196, 242, 270, 336 and 363 hours.
The leachate was analysed on an Agilent 1260 Infinity II Quaternary LC equipped with aminex HPX-87 h column (300 × 7.8 mm). As an eluant, 5 mM sulphuric acid was used with a flowrate of 0.60 mL min−1 at a temperature of 50°C. The detector used for these analyses was a refractive index detector (RI 830). For reference standards, citric acid dissolved in water and sorbitol dissolved in water were used. The concentrations are displayed in .
Table 2. HPLC standards used in this experiment.
Water soaking and dimensional stability
For the soaking test, 15 samples of each of the treatments; cured at 103°C, cured at 140°C and untreated, were placed in a water bath for 12 days. Each treatment was placed in a separate container with 1.5 L of water. The samples were weighted down to prevent floating. The containers were stored in a dark place at room temperature. The water was changed once at day 9. After the water soaking the samples were acclimatised to a stable weight at a temperature of 20°C and 65% relative humidity before and after the soaking procedure. The weight of the samples was taken before and after soaking on a Mettler Toledo scale ME303 with an accuracy of 1 mg. The dimensions of all samples were measured in all three directions before and after leaching with a MITOTOYO Absolute 543-460B with an accuracy of 0.001 mm. The measuring point was marked to ensure measurement on the same spot each time.
Fungal test; modified EN113
Wood samples were exposed to brown-rot fungi Postia placenta and white-rot fungi Trametes versicolor. The samples were leached according to EN 84 (European Standard Citation1997a) (the steps are described above) and exposed to fungi according to a modified version of EN 113 (European Standard Citation1997b). The modifications to EN 113 were that the sample size was smaller and the exposure time was 8 weeks instead of 16. The samples were sterilised in an autoclave for 20 min at 120°C before they were placed on petri dishes with malt agar. The petri dishes were incubated in a climate chamber at 70 ± 5% RH and 22 ± 2°C. The short exposure to 120°C was considered not to affect the samples.
The dry mass was recorded before and after the fungi test. The correction value, which is the mean percentage loss in mass of the treated test specimen that was not exposed to fungal decay, was subtracted from the sample that was exposed to fungal decay. This was done for each curing temperature as defined in the EN 113 (European Standard Citation1997b) standard.
Blue-stain fungi test
This test was performed was a modified version of EN 15457 (European Standard Citation2014). The test specimens had a dimension of 6.5 × 25 × 50 mm. Before the test, half of the samples went through a leaching procedure according to EN 84 (European Standard Citation1997a). Following the leaching procedure, the samples were dried at room temperature for 16 hours and then at 103°C for 18 hours. The samples were conditioned at 65% RH and 20°C until stable weight was achieved, before the samples were autoclaved for 20 min at 120°C to sterilise the samples. The short exposure to 120°C was considered not to affect the samples. The samples were then placed on agar plates containing 1.25% malt agar. A plastic mesh was placed between the agar and the specimens in order to avoid that the specimens were in direct contact with the agar. Three different spore suspensions were made from (1) Aureobasidium pullulans (de Bary) Arnaud, strain BAM 9, with about 13 × 104 spores per mL, (2) Sydowia polyspora, strain BAM 31, with about 8.24 × 104 spores per mL and (3) a mixed culture consisting of A. pullulans BAM 9, Cladosporium cladosporioides DSM 62121, Ulocladium atrum DSM 63068 and Sydowia polyspora BAM 31, with about 19.25 × 104 spores per mL. The spore suspensions were made from well-sporulating cultures on agar plates. Five milliliter sterile water was added to each plate, and with a Drigalski spatula the spores were loosened from the mycelium before the suspensions were mixed into a batch. The mixed culture spore suspensions contained equal volume suspensions from all test fungi. Inoculation with spore suspensions onto the specimens was performed in sterile conditions. The spore suspensions were applied on to the upper face of the specimens. The agar plates were incubated at room temperature for a period for 57 days. The samples were evaluated on day 3, 7, 14, 21, 36, 43, 50 and 57 for mould growth coverage according to BS 3900-G6 (British Standard Citation1969) rating from 0 = no mould growth to 5 = more than 70% growth on the surface of the replicates. Hence, the rating of mould growth is not continuous but an ordinal one. When presenting the result of the blue-stain fungi test we have showed the mean response value and the standard deviation values. This is done even though the response variable is ordinal categorical, just to give an overview of the results.
Results and discussion
Chemicals
The aqueous solution of sorbitol and citric acid is a stable transparent solution that can be stored. The solution proved to be easy to handle and easy to impregnate. After impregnation and curing, the treated samples exhibited a light brown colour. shows the WPG's before and after leaching for treatments; cured at 103 and 140°C. For all the three tests in this publication, the WPGs were higher in the samples cured at 103°C than the samples cured at 140°C. During the polyestrification process, water is released during the curing process (Doll et al. Citation2006). The higher WPG in the samples cured at 103°C could therefore be explained by an uncompleted chemical reaction. In comparison with the study of L’Hostis et al. (Citation2017), we achieved much higher solution uptake and WPG. They used citric acid, glycerol and water in a 34/10/56 g ratio to impregnate beech wood. L’Hostis et al. (Citation2017) used beech which is more difficult to treat in radial and tangential directions (Larnøy et al. Citation2005) and this could explain the lower WPG in the study of L’Hostis et al. (Citation2017).
Polyols have several functional groups. In our case sorbitol has six alcoholic hydroxyl groups which means six potential reaction sites on one molecule, whereas citric acid has three acidic and one alcoholic hydroxyl group. There have not been many publications examining the reaction mechanism of sorbitol and citric acid or the reaction between these reagents and the wood cell wall. Disregarding the existence of the cell walls in the first step and only focusing on the reaction between the two monomers Doll et al. (Citation2006) have proposed two different mechanisms for the initial steps of the polyesterification reaction. According to them, citric acid undergoes an intramolecular anhydride formation to result in a ring. This is followed by a nucleophilic addition of a terminal hydroxyl group to one of the carbonyl groups including ring opening of the anhydride. In the second step either the bonded sorbitol molecule or the citric acid part can undergo ring formation again to be followed by another nucleophic addition of the next hydroxyl group (sorbitol) to a carbonyl group (citric acid).
The release of a water molecule with each addition step of a functional group belonging to sorbitol explains further weight loss due to the curing process. The differences between varying curing temperatures and the results from leaching tests lead us to assume that the higher curing temperature causes higher conversion rates of accessible functional groups to yield a much denser crosslinked network in the cell wall that prevents leaching of chemicals from the wooden samples. This explanation is in harmony with Doll’s (Citation2006) result that the reaction of the two monomers occurs faster at 150°C than at 110°C.
Stability of the reacted chemical
In and , the leachate of citric acid and sorbitol are displayed as g L−1 over leaching time. The leachate from the untreated samples did not give any response in the HPLC for the targeted peaks. The results from the leachate from the samples cured at 103 and 140°C in and show very low leaching from the samples treated at 140°C.
For the samples treated at 103°C the leaching of citric acid and sorbitol is substantial. After only a short period, they leach considerably, and the highest peaks are displayed at 22 hours. The concentration in the leachate thereafter decreases with time until it stabilised around 200–300 hours.
In the chromatograms of the leaching water from samples cured at 103°C, a large unidentified peak with the shortest retention time (5.6 min) in the HPLC trace was only observed with the wood samples cured at 103°C and is presumably related to incomplete polymerisation of the reactants. Further work is under way to identify the molecular species associated with these peaks and to elucidate the reaction pathway.
Dimensional stability
From the soaking tests presented in and , it is evident that the samples cured at 140°C did not significantly change weight or dimensions after soaking. The samples cured at 140°C showed a permanent increased in dimension. Although this is strong evidence that the bulking chemicals have ended up in the cell wall, these results do not indicate whether or not the chemical is bonded to the cell wall (Rowell Citation1983). The samples cured at 103°C showed large changes before and after soaking. Dimensional stability of the sample was determined using the bulking coefficient (BC), defined as follows:where Vu is the volume of the unmodified wood sample; Vm is the volume of the modified wood sample. Before soaking, the samples cured at 103°C had a BC of 13.62% and the samples cured at 140°C had a BC of 12.20%. After leaching, the samples cured at 103°C had a BC of 5.89% and the samples cured at 140°C had a BC of 11.10%.
Similar to the dimensional change, the weights after soaking are stable for the samples cured at 140°C and for the untreated samples. The samples cured at 103°C shows significant mass loss after leaching. The WPG of the samples is shown in . These results are comparable to the work by L’Hostis et al. (Citation2017). They impregnated beech samples with citric acid, glycerol and water and cured to 103,120,140 and 160°C. They measured a high leaching rate by weight for the samples cured at 103°C and no leaching at the temperature of 140°C. L’Hostis et al. (Citation2017) showed that even after 72 hours of curing, the beech wood samples treated with citric acid and glycerol at 100°C had a leaching rate of 17%, indicating that this process needed a higher temperature for complete chemical reaction.
Fungi test; modified EN113
Both sets of treated samples, cured at 103 and 140°C, showed significantly lower mass loss due to decay compared to untreated samples. In almost no decay is evident in the treated samples. The corrected mass loss data showed a higher variation between the samples cured at 103°C than between the samples cured at 140°C. The unexposed samples for the correction values showed high mass losses for the samples cured at 103°C, and therefore some samples showed negative mass losses. This concurs with the work of Essoua et al. (Citation2016), who also reported negative mass loss. They impregnated with citric acid, glycerol and water and cured at 180°C for 20 min. Their theory was that ‘the mass gain was a result of the liberation of sorption water (hydroxyl groups) from the wood or polymer structure because of fungal action’. This could imply that the first 18 hours of curing was not sufficient, and further chemical reactions occur during the drying in the fungi trials. In the samples cured at 140°C, there were almost no variation in the data, and low mass loss in the correction samples, implying a complete reaction after 18 hours at 140°C. The results from the fungal trials concur with the findings of L’Hostis et al. (Citation2017). Even though the samples cured at 103°C had a much higher loss in WPG due to leaching in our study, the residual WPG was nonetheless sufficient to maintain a good protection from the fungal decay. Further research should investigate the threshold needed for fungal protection.
Blue-stain fungi test
Both unleached and leached samples cured at 103 and 140°C performed in a similar manner and had significantly less surface growth of A. pullulans, S. polyspora and the fungal mix than untreated samples at all evaluations times and . The results show that both treatments, particularly samples treated at 140°C, resist growth of blue-stain fungi also after a leaching procedure. Leached samples treated at 140°C had no indication of growth of A. pullulans during the test period, and had less growth of S. polyspora and fungal mix than samples cured at 103°C.
Figure 7. Blue stain coverage evaluated after (British Standard Citation1969). Unleached treated and untreated pine samples after 57 days of incubation.
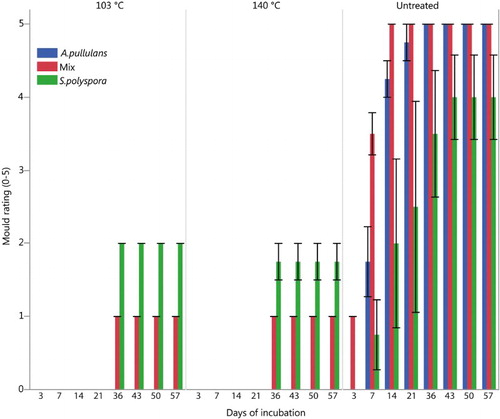
Figure 8. Blue stain coverage evaluated after (British Standard Citation1969). Leached treated and untreated pine samples after 57 days of incubation.
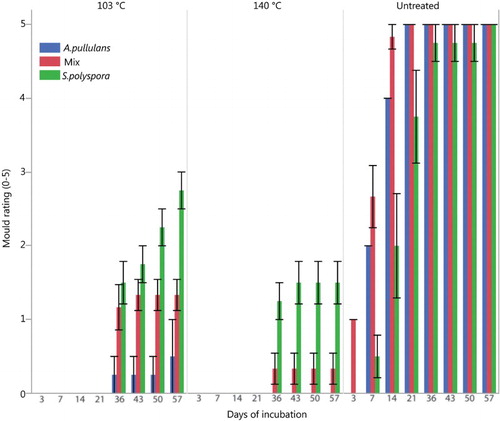
Generally, most fungi grow over the pH range 3–7 (Zabel and Morrell Citation1992). The liquid solution that was used to impregnate the wood samples had a pH of 2, and although the pH of the surface of the treated samples was not determined, the low pH could be part of the explanation for the limited fungal growth. The mode-of-action for this limited growth will be has to be further studied future trials.
Conclusions
The polyesterification of sorbitol and citric acid in wood has through this study proven to be a product with enhanced properties such as increased dimensional stability, increased durability against decay fungi and less susceptibility to blue-stain fungi. From this research, it has been proven that curing at 103°C is not enough to fixate the chemicals in the wood. By way of contrast, the fixation is very good at 140°C. Further studies should look to how long a curing time and how high a temperature is needed. The chemicals used in the process are affordable, nontoxic and easy to handle. The wood achieves a high WPG with a standard impregnation, and the concentration of the impregnation solution can probably be reduced in further trials and process optimisation. From the fungal trials in this study, the concentration of chemicals is more than enough to achieve protection. Further studies should look to the concentration threshold and possible addition of catalysts. The end product has the potential to be resistant to fungal degradation in above ground applications.
Acknowledgements
The authors would like to thank Sigrun Kolstad, Eva Grodås and Monica Fongen for their laboratory work.
Disclosure statement
No potential conflict of interest was reported by the authors.
ORCID
E. Larnøy http://orcid.org/0000-0002-8724-4010
References
- Amirou S, Pizzi A, Delmotte L. 2017. Citric acid as waterproofing additive in butt joints linear wood welding. Eur J Wood Wood Prod. 75:651–654. doi: 10.1007/s00107-017-1167-x
- Bateson BA. 1938. Sorbitol in wood treatment. Chem Trade J. 104:26–27.
- Bateson BA. 1939. Sorbitol in wood treatment. Chem Trade J. 105:93–94.
- Berube MA, Schorr D, Ball RJ. 2018. Determination of in situ parameters of citric acid-glycerol based polymers for wood impregnation. J Polym Environ. 26:970–979. doi: 10.1007/s10924-017-1011-8
- British Standard. 1969. Methods of test for paints. Assessment of resistance to fungal growth Standard No. BS 3900-G6:1989.
- Centolella AP, Razor BG. 1972. Polyesters of citric acid and sorbitol. US Patent No. 3661955.
- Doll KM, Shogren RL, Willett JL, Swift G. 2006. Solvent-free polymerization of citric acid and D-sorbitol. J Polym Sci A Polym Chem. 44:4259–4267. doi: 10.1002/pola.21535
- Essoua Essoua GG, Blanchet P, Landry R, Beauregard R. 2016. Pine wood treated with a citric acid and glycerolmixture: biomaterial performance improved by a bio-byproduct. Bioresources. 11:3049–3072. doi: 10.15376/biores.11.2.3049-3072
- European Standard. 1997a. Wood preservatives. Accelerated ageing of treated wood prior to biological testing. Leaching procedure Standard No. EN 84:1997.
- European Standard. 1997b. Wood preservatives. Test method for determining the protective effectiveness against wood destroying basidiomycetes. Determination of the toxic values Standard No. EN 113:1997.
- European Standard. 2014. Paints and varnishes. Laboratory method for testing the efficacy of film preservatives in a coating against fungi. Standard No. EN 15457:2014.
- Hill CAS. 2006. Wood modification – chemical, thermal and other processes. Chicester: John Wiley & Sons.
- Hill CAS. 2011. Wood modification. Bioresources. 6(2):918–919.
- http://ec.europa.eu/eurostat. http://ec.europa.eu/eurostat/statistics-explained/index.php/Wood_products_-production_and_trade
- Kiljunen S, Koski A, Kuntitu M. 2011. Impregnation of chemicals into wood. World Patent No. WO2011/042609 A1.
- Larnøy E, Militz H, Eikenes M. 2005. Uptake of chitosan based impregnation solutions with varying viscosities in four different European wood species. Holz Roh Werkst. 63:456–462. doi: 10.1007/s00107-005-0014-7
- L’Hostis C, Thévenon M, Fredon E, Gérardin P. 2017. Improvement of beech wood properties by in situ formation of polyesters of citric and tartaric acid in combination with glycerol. Holzforschung. 72(4):291–299. doi: 10.1515/hf-2017-0081
- Low KS, Lee CK, Mak SM. 2004. Sorption of copper and lead by citric acid modified wood. Wood Sci Technol. 38:629–640. doi: 10.1007/s00226-003-0201-9
- McSweeny JD, Rowell RM, Min S-H. 2006. Effect of citric acid modification of aspen wood on sorption of copper ion. J Nat Fib. 3:43–58. doi: 10.1300/J395v03n01_05
- Noël M, Grigsby WJ, Vitkeviciute I, Volkmer T. 2015a. Modifying wood with bio-polyesters: analysis and performance. Int Wood Prod J. 6(1):14–20. doi: 10.1179/2042645314Y.0000000086
- Noël M, Grigsby WJ, Volkmer T. 2014. Investigating the viscoelastic properties and mechanical performance of wood modified by biopolyester treatments. J Renew Mater. 2(4):291–305. doi: 10.7569/JRM.2014.634118
- Noël M, Grigsby WJ, Volkmer T. 2015. Evaluating the extent of bio-polyester polymerization in solid wood by thermogravimetric analysis. J Wood Chem Techno. 35(5):325–336. doi: 10.1080/02773813.2014.962154
- Noël M, Volkmer T, Pichelin F. 2015. Bio-modification of wood: improvement of wood and wood surface properties by chemical modifications with 100% bio-based treatments. Bern Univ Appl Sci. Final report from the State Secretariat for Education and Research SER International Cooperation/COST Competence center Hallwylstrasse 4, CH-3003 Bern. Report no: E.001119-10-62FE-01-FB-01. https://pdb.bfh.ch/pdbwebinterface/download.aspx?imgId=da6bc295-aa9f-41f8-83fd-2bdd9cc93145
- Ou R, Wang Q, Wolcott P, Sui S, Xie Y. 2016. Rheological behaviour and mechanical properties of wood flour/high density polyethylene blends: effects of esterification of wood with citric acid. Polym Comp. 37:553–560. doi: 10.1002/pc.23212
- Romero A, Esther E, Sastre Á, Nieto-Márquez A. 2016. Conversion of biomass into sorbitol: cellulose hydrolysis on MCM-48 and d-Glucose hydrogenation on Ru/MCM-48. Micropor Mesopor Mater. 224:1–8. doi: 10.1016/j.micromeso.2015.11.013
- Rowell RM. 1983. Chemical modification of wood: a review. Oxford: Commonwealth Forestry Bureau. Vol. 6, p. 363–382.
- Show PL, Oladele KO, Siew QY, Aziz Zakry FA, Lan JCW, Ling TC. 2015. Overview of citric acid production from Aspergillus niger. Front Life Sci. 8(3):271–283. doi: 10.1080/21553769.2015.1033653
- Umemura K, Sugihara O, Kawai S. 2013. Investigation of a new natural adhesive composed of citric acid and sucrose for particleboard. J Wood Sci. 59:203–208. doi: 10.1007/s10086-013-1326-6
- Umemura K, Sugihara O, Kawai S. 2015. Investigation of a new natural adhesive composed of citric acid and sucrose for particleboard II: effects of board density and pressing temperature. J Wood Sci. 61:40–44. doi: 10.1007/s10086-014-1437-8
- Umemura K, Ueda T, Kawai S. 2012. Effect of moulding temperature on the physical properties of wood-based moulding bonded with citric acid. For Prod J. 62:63–68.
- Vukusic SB, Katovic D, Schramm C. 2006. Polycarboxylic acids as non-formaldehyde anti-swelling agents for wood. Holzforschung. 60:439–444.
- Widyorini R, Nugraha PA, Rahman MZA, Prayitno TA. 2016. Bonding ability of a new adhesive composed of citric acid-sucrose for particleboard. Bioresources. 11:4526–4535. doi: 10.15376/biores.11.2.4526-4535
- Young NWG, O’Sullivan GR. 2011. The influence of ingredients on product stability and shelf life. In Food and Beverage Stability and Shelf Life, Woodhead Publishing Series in Food Science, Technology and Nutrition. Cambridge: Woodhead Publishing; p. 132–183.
- Zabel RA, Morrell JJ. 1992. Wood microbiology: decay and its prevention. London: Academic Press.