ABSTRACT
In this work, dissimilar welding of Incoloy alloy 825 and AISI 316 stainless steel tubes is experimentally investigated using gas metal arc welding process. For this purpose, different filler metals such as stainless steel 308, stainless steel 309, stainless steel 316 and Inconel 82 are employed for joining of Incoloy alloy 825 and AISI 316 stainless steel tubes. The results show that during tensile tests, fracture occurred in all weldments in the heat-affected zone (HAZ) of stainless steel 316. Also, it is concluded that dissimilar welds produced by stainless steel 309 filler metal have the maximum tensile strength while the lowest strength is obtained with Inconel 82 filler metal. The results of average hardness prove that the dissimilar joint with filler metal say stainless steel 309 and filler metal say Inconel 82 have maximum and minimum values of average hardness in the weld metal, respectively. The results show a considerable unmixed zone (UMZ) in the form of laminar layers between filler 82 weld metal and the Incoloy 825 base metal along the welding line. In addition, considerable UMZ is seen in the interface of the weld metal/AISI 316 base metal, but more grain growth occurred in the AISI 316 HAZ due to the temperature increase during various welding passes. It is indicated that there is a very narrow UMZ between the 309 weld metal and Incoloy 825 base metal; however, no considerable UMZs can be observed in the AISI 316 base metal.
1. Introduction
Incoloy alloy 825 is a nickel-iron-chromium alloy with additions of molybdenum, copper, and titanium. Its chemical composition is presented in Table . The chemical composition of Incoloy alloy 825 provides exceptional resistance to many corrosive environments. Due to its resistance to corrosion, Incoloy 825 can be used in many industrial applications such as chemical processing, pollution control, acid production, pickling operations. Bimetallic joints of Inconel alloys (such as Incoloy 825) and austenitic stainless steel AISI 316 find their applications in aerospace industries. This is due to high strength and good corrosion resistance in both room and high-temperature conditions. In recent years, a lot of researches have been reported in different areas of welding process such as advanced welding processes (Moradi et al. Citation2014, Citation2016, Citation2018), tube welding process (Krolczyk et al. Citation2015; Palanivel et al. Citation2017; Stütz et al. Citation2018; Tavassolimanesh and Alavi Nia Citation2018; Yazdian et al. Citation2018) and inspection methods of welded joints (Krolczyk et al. Citation2016). In recent years, a lot of researches have been reported on dissimilar welding process. However, few papers reported on dissimilar welding process of Inconel alloy sheet to stainless steel alloy sheet in comparison with other dissimilar welded joints. In the following, some of those papers are explained. In Citation2018, Dev et al. studied the microstructure and mechanical properties of dissimilar welds of Inconel 718 and sulphur-rich martensitic stainless steel (AISI 416). Two Nb-free consumables namely ERNiCrMo-4, ERNiCu-7 and a duplex filler ER2553 were used to join these dissimilar combinations. It was endorsed from the studies that the welds obtained from these fillers were free from deleterious Laves phase. Irrespective of fillers, the tensile failures were experienced at the base metal side of AISI 416. In Citation2018, Zhang et al. examined the microstructure and mechanical performance of a tungsten inert gas (TIG) welded joint between a novel heat-resistant austenitic steel and Inconel 617. Microhardness profiles of the joint were obtained and the backing passes were found to produce the highest microhardness values, which was caused by the grain refinement effect. Ductile failure with slipping separation occurred in those joints ruptured after tensile tests at both room temperature and 923 K. In Citation2017, Hejripour and Aidun investigated the dissimilar welding between martensitic stainless steel type AISI 410 and Inconel 718 using cold wire gas tungsten arc welding (GTAW). They used two types of consumables namely 718-410 and 82-410. In both weldments, the microstructure investigation showed fully austenitic weldments with the formation of secondary phases. Secondary phases were present in the heat-affected zone (HAZ) of 718, and an unmixed melted zone was observed on the 410 interface. In Citation2017, Wang et al. investigated the oxidation mechanism on the dissimilar welds between 316 stainless steels/Inconel 182 in high-temperature and high-pressure water. The results indicated that there were different types of duplex-structural oxide layers on both sides of the fusion boundary. In the external oxide layer, spinel oxide appeared on 316 SS side, while a component of flaky and spinel oxides deposited on Inconel 182 side. In Citation2017, Ramkumar et al. studied the structural property, mechanical relationships and corrosion behaviour of Inconel 718 and SS316L dissimilar joints by TIG welding without using activated flux. The studies proved that a complete penetration could be achieved in multi-pass. It was indicated from the notch tensile studies that the notch strength ratio was better than unity, which established that the weldments were ductile in all circumstances. The corrosion studies were carried out in the NaCl solution and it was found that Inconel 718 and SS316L dissimilar joint possess less corrosion resistance than similar SS316L weldment. In Citation2017, Kangazian et al. studied the effect of the filler metal type, welding process and the welding pass number on the corrosion behaviour of Incoloy 825 Ni-based alloy to SAF 2507 super-duplex stainless steel weld zones. The results detailed the formation of some secondary phases in the weld metals. The welds employing Ni-based filler wires revealed the highest general corrosion resistance, while super-duplex stainless steel weld metals displayed the best pitting corrosion behaviour. In Citation2016, Shah Hosseini et al. studied the microstructural evolutions and weldability of the Inconel 617/310 austenitic stainless steel dissimilar welds. Three types of filler materials including Inconel 82, Inconel 617 and 310 austenitic stainless steel were used to fabricate dissimilar joints using the GTAW process. Microstructural observations showed distinct cracks in the weldment produced by 310 austenitic stainless steel filler metal. The results of varestraint weldability test showed that the joints produced by Inconel 617 and 310 stainless steel filler metals exhibited the highest and lowest resistance to solidification cracking, respectively. In Citation2016, Ramkumar et al. investigated the effect of fillers on the microstructure and tensile strength of dissimilar joints of Inconel 625 and UNS S32205 by pulsed current GTAW employing ERNiCrMo-10 and ERNiCrMo-14 fillers. This study attested that tensile failure occurred in the fusion zone of the dissimilar joints for both the cases in the as-welded un-peened condition. Double shot laser shock peening (DLSP) was performed on the fusion zone of these pulsed current gas tungsten arc welds on the cap and root regions of the weldments. The results demonstrated that after subjecting to double-sided DLSP, the fusion zones were subjected to compressive residual stresses. In Citation2016, Zhou et al. investigated the sulphide stress cracking (SSC) behaviour of the dissimilar metal welded joint of X60 pipeline steel and Inconel 625 alloy in H2S environment using constant load testing, weight loss testing and finite element analysis. The dissimilar welded joint showed high SSC susceptibility, and the asymmetric stress concentration after corrosion was the prerequisite for crack initiation. In Citation2015, Wang et al. studied the microstructures and microhardness at fusion boundary of a weld joint in a 316 stainless steel/Inconel 182 dissimilar weldment. The results showed that there were two alternately distributed typical fusion boundaries, a narrow random boundary with a clear sharp interface and an epitaxial fusion one. Microhardness was continuously decreased across the random fusion boundary from the side of Inconel 182 to 316SS, but a hardening phenomenon appeared in the epitaxial fusion boundary zone because of its fine cellular microstructure. In Citation2015, Sayiram and Arivazhagan studied the microstructural of dissimilar welds between Incoloy 800H and 321 stainless steel has been discussed. Their results revealed precipitates of Ti (C, N) in the austenitic matrix along the grain boundaries of the base metals. Migration of grain boundaries in the Inconel 82 weld metal was very extensive when compared to Inconel 617 weldment. In Citation2015, Chen et al. investigated GTAW of Ti3Al-based alloy and nickel-based superalloy. The microstructure evolution, mechanical properties and fracture behaviours of the joints were investigated. Their results showed that the gradient structure remarkably decreased the formation tendency of brittle phases within the joints compared with single filler alloy and thus improved the joint strength effectively. In Citation2014, Mortezaie and Shamanian determined the relationship between the microstructure of the welds and the resultant mechanical and corrosion properties in a dissimilar welding between Inconel 718 nickel-based superalloy and 310S austenitic stainless steel using GTAW process. For this purpose, three filler metals including Inconel 625, Inconel 82 and 310 stainless steel were used. Microstructural observations showed that weld microstructures for all filler metals were fully austenitic. In tension tests, welds produced by Inconel 625 and 310 filler metals displayed the highest and the lowest ultimate tensile strength, respectively. The results of Charpy impact tests indicated that the maximum fracture energy was related to Inconel 82 weld metal. In Citation2014, Shakil et al. investigated the electron beam welding of dissimilar Inconel 625 and SS304L alloys. The welded joint was found homogeneous, well-bonded and defect-free. The development of different microstructures in the fusion zone was attributed to the localised cooling effects during solidification. Few micro-cracks along with dendrites splitting were observed in the vicinity of end crater that was mainly due to the segregation of S element. In Citation2014, Ramkumar et al. compared the mechanical properties of the dissimilar combinations of Inconel 625 and AISI 304 obtained from continuous current GTAW and pulsed current GTAW techniques using ERNiCrMo-3 filler. The studies showed that the pulsed current GTAW resulted in the lower segregation effects at the weld zone and the minimisation of precipitation of chromium carbides at the HAZ. In Citation2014, Mithilesh et al. investigated the weldability, metallurgical and mechanical properties of the dissimilar joints of Inconel 625 and AISI 304. Dissimilar joints were obtained by GTAW process employing ERNiCrMo-3. Their results showed that the tensile fracture occurred at the parent metal of AISI 304 in all the trials. In Citation2009, Naffakh et al. investigated the bimetallic combinations of Inconel 657 and austenitic stainless steel 310 using Inconel 82, Inconel A, Inconel 617 and 310 SS filler wires. It was observed from the studies that these joints exhibited lower tensile strengths and showed brittle fracture which was reasoned due to the segregation of Mo. Similarly, the researchers addressed the typical problem of hot cracking associated with the dissimilar welding. In Citation2007, Jeng et al. investigated the microstructure of the Alloy 690 and SUS 304L stainless steel dissimilar joints obtained by GTAW techniques employing different filler metals. The authors observed the precipitation of Cr-carbides at the inter-dendritic regions due to the multi-pass welding. It was found that the Cr content near the grain boundary decreased as a result of Cr-carbide precipitates. Further, the Cr depletion caused by the Cr-carbide precipitation along the grain boundary results in the reduction of corrosion resistance. As mentioned above, all references have been focused on dissimilar welding process of Inconel sheets to stainless steel sheets. It should be noted that based on authors knowledge there is not any report of dissimilar welding process on Incoloy alloy tubes to stainless steel alloy tubes. Meanwhile, dissimilar welded joints of Incoloy tubes to stainless steel tubes have wide applications in oil and gas industries. Hence, in this work, dissimilar welding of Incoloy alloy 825 and AISI 316 stainless steel tubes is experimentally investigated using gas metal arc welding (GMAW) process. For this purpose, different filler metals such as stainless steel 308, stainless steel 309, stainless steel 316 and Inconel 82 are employed for joining of Incoloy alloy 825 and AISI 316 stainless steel tubes by GTAW process. After welding process, metallurgical and mechanical studies are conducted to determine the microstructure and mechanical properties of dissimilar welded tabular joints. It should be mentioned that GTAW process can be employed successfully for joining of nickel-based superalloys and stainless steels which have some advantages such as low cost in comparison with the laser beam welding process. So, in this research, the GTAW process has been chosen in order to joining Incoloy 825 to AISI 316 austenitic stainless steel.
Table 1. Chemical compositions of the base metal and filler materials (wt.%).
2. Materials and methods
Incoloy alloy 825 and stainless steel 316 tubes are used for dissimilar welding in this research. The tubes have an outer diameter of 100 mm, wall thickness of 9 mm and length of 200 mm.
Tubes are machined to create a single V-groove butt joint configuration with a 70° groove angle. The root face and the root opening are 1 and 2 mm, respectively. To perform the dissimilar welding; four filler metals Inconel 82, stainless steel 308, stainless steel 309 and stainless steel 316 are employed. The chemical compositions of the base and filler materials are given in Table . The chemical compositions of the base metals were determined by optical spectroscopy method. Welding procedure was performed in four passes by the automatic GMAW process with direct current electrode negative. The welding parameters and the heat input in each welding pass are given in Table .
Table 2. The GTAW welding parameters used in this study; the heat input was taken as 0.7 EI/V, where E is welding voltage, I is current and V is welding speed.
After welding, a series of tests are conducted to determine the properties and microstructure. The microstructure of different regions including base and weld metals and HAZs are metallographically characterised. For this purpose, transverse sections of the welds are investigated after etching in marble solution (10 g CuSO4 + 50 ml H2O + 50 ml HCl). In order to determine the tensile strength of the base and weld metals, the tensile test was performed with a nominal loading rate of 1.0 mm min−1 on a Kpruf universal testing machine. Tensile test specimens were prepared from the transverse section of the welds. The microhardness measurements are carried out using Koopa Vickers hardness machine under a 300 g load. In Figure , the dissimilar welded Incoloy alloy 825 and stainless steel 316 tubes, prepared specimens for tensile, hardness and metallography tests are shown.
3. Results and discussion
3.1. The results of mechanical tests
The results of tensile tests for dissimilar welded joints are shown in Table along with the properties of the two base metals. During the transverse tensile tests, fracture occurred in all weldments in the HAZ of stainless steel 316. As will be noted in Section 3.2, the occurrence of grain growth in the HAZ of stainless steel 316 base metal has caused fracture to occur in these zones. It should be mentioned that unlike the conventional tensile specimens, failure processes are more complicated in welded specimens, particularly in dissimilar welding which contains different zones with different properties, and behaviour of one zone can have an effect on its adjacent zones. Results obtained from tensile tests on the weldments indicate that dissimilar welds produced by stainless steel 309 filler metal have the maximum tensile strength. Moreover, the results prove that the Inconel 82 filler metal has the lowest strength. The results of average hardness for dissimilar welded joints are presented in Table . As it is seen in Table , dissimilar joint with filler metal say stainless steel 309 and filler metal say Inconel 82 have maximum and minimum values of average hardness in the weld metal, respectively.
Table 3. Tensile strength and fracture position of dissimilar welded joints with different filler metals.
Table 4. The average hardness of weld metal for dissimilar welded joints with different filler metals.
3.2. Microstructural results
As it was seen in the results of mechanical tests, the filler metal 309 provided the best mechanical properties for dissimilar welds of Incoloy alloy 825 and AISI 316 stainless steel tubes. Also, the worst mechanical properties were obtained with filler metal Inconel 82. Therefore, in this section, only the microstructural results of these two filler metals will be studied.
3.2.1. Base metal microstructures
The microstructure of the AISI 316 austenitic stainless steel base metal is shown in Figure . The microstructure consists of fine equiaxed grains of austenite. Annealing twins can be observed in the austenitic matrix. There does not appear to be any delta ferrite or carbide precipitates in the microstructure due to a proper annealing treatment after cold rolling. The fully austenitic structure improves toughness and corrosion properties especially at high temperatures, but encourages the sensitivity to solidification cracking (Zhang et al. Citation2018). The Incoloy 825 alloy was supplied in the form of a solution-treated and water-quenched plate. The typical metallographic features of the alloy in the as-delivered condition are shown in Figure . The microstructure consisted of an austenitic matrix with some inter- and intra-granular precipitates. Incoloy 825 contains about 20% chromium, 3% molybdenum, 1% titanium and 0.05% carbon and hence tends to form alloying carbide during high-temperature exposure. It has been shown that these precipitates are mainly Cr23C6, Mo6C and TiC or a combination of them. Shah Hosseini et al. (Citation2016) have been reported that the majority of these precipitates are Mo-rich particles. It has been reported that Mo-rich precipitates have not any damaging effects on solidification cracking resistivity. Water quenching from the solution annealing temperature is effective in preventing the formation of M23C6 carbides during cooling in order to help avoid intergranular attack in certain environments. However, it should be noted that when water quenched, the HAZ may be subject to carbide formation if repair welding becomes necessary.
Figure 2. Light optical micrograph of AISI 316 austenitic stainless steel base metal in two different magnifications: (a) 50 µm and (b) 20 µm.
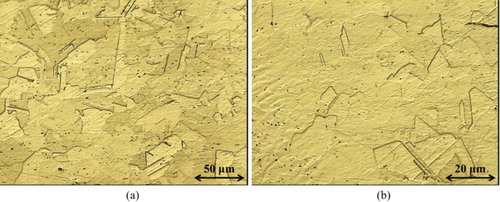
Figure 3. Light optical micrograph of Incoloy 825 base metal in three different magnifications: (a) 200 µm, (b) 100 µm and (c) 50 µm.
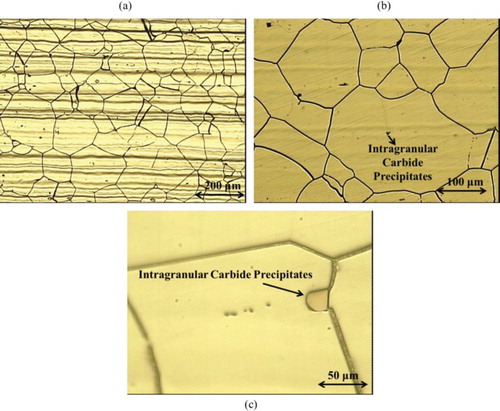
Cold work can be applied to these alloys to increase base metal strength, but this is not normal, especially in applications that require welding. The HAZ in alloys strengthened by cold work will undergo recrystallisation resulting in local softening of the structure (Hejripour and Aidun Citation2017).
3.2.2. Microstructure of HAZs and interfaces
The HAZ microstructure of Incoloy 825 is shown in Figure . It can be seen that no significant grain growth has occurred in this area. The interface between filler 82 weld metal and Incoloy 825 base metal is displayed in Figure . There is a considerable unmixed zone (UMZ) in the form of laminar layers between filler 82 and the base metal along the welding line. When the melting range of filler materials is similar to or higher than that of the base metal, only a small fraction of the base metal can be melted and no dilution occurs in the re-solidification stage; therefore, an UMZ is formed between two regions. Note that the addition of Mo in nickel-based alloys results in a significant increase in the pitting resistance of the base metal but that the weld metal response is not as large. This is primarily due to the partitioning of Mo during solidification. A similar trend was seen in the interface of the weld metal/AISI 316 base metal, but more grain growth occurred in the AISI 316 HAZ due to the temperature increase during various welding passes. Although the base metals are now immune from pitting attack, the narrow UMZ is subject to local pitting.
Figure 4. Optical micrograph of HAZ microstructure of Incoloy 825 in two different magnifications: (a) 50 µm and (b) 20 µm.
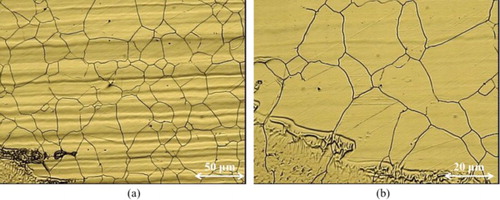
The microstructure of HAZ in the AISI 316 side is shown in Figure . It can be seen that almost significant grain growth has occurred in the HAZ of AISI 316 base metal. In addition, it can be observed annealing twins are formed more effectively and no delta ferrite phase has been formed that in this area.
Figure 6. Optical micrograph of HAZ microstructure of AISI 316 stainless steel in two different magnifications: (a) 200 µm and (b) 100 µm.
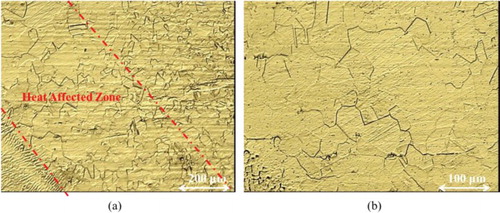
The interfacial regions of the filler 82 weld metal and the base metal of AISI 316 are shown in Figure . There is an UMZ between the weld metal and AISI 316 base metal similar to that observed for filler 82.
The weld metal interfaces for the 309 filler metal with the AISI 316 and Incoloy 825 base metals are shown in Figure (a,b), respectively. There is a very narrow UMZ between the weld metal and Incoloy 825 base metal similar to that observed for filler 82; however, no considerable UMZs can be observed in the AISI 316 base metal showing more dilution. It can be attributed to the similarity of filler (309) and base metal (AISI 316) from the viewpoint of the melting temperature and chemical composition.
Figure 8. Interfaces between the filler 309 weld metal and the AISI 316 base metal (a) and between the filler 309 weld metal and the Incoloy 825 base metal (b).
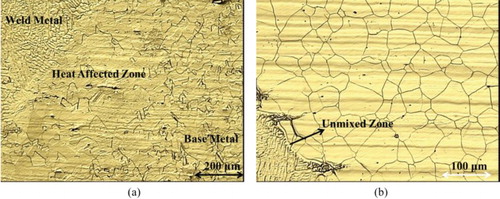
The microstructure of filler 82 weld metal is shown in Figure (a,b). The weld metal is fully austenitic. The solidification grain boundaries, solidification subgrain boundaries and migrated grain boundaries are distinct in the figure. The solidification subgrains represent the finest structure that can be resolved through the optical microscope. These subgrains are normally present as cells or dendrites. These boundaries are evident in the microstructure because their composition is different from that of the bulk microstructure. There is virtually no crystallographic misorientation across the solidification subgrain boundaries, and these boundaries are characterised as ‘low-angle’ boundaries (Wang et al. Citation2017).
Figure 9. Optical micrographs of filler 82 welding metal microstructure in two different magnifications: (a) 200 µm and (b) 50 µm.
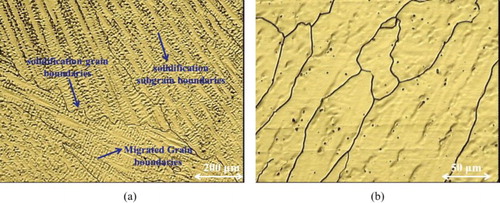
The solidification grain boundary results from the intersection of packets, or groups, of subgrains. Thus, solidification grain boundaries are the direct result of competitive growth that occurs along the trailing edge of the weld pool. Because each of these packets of subgrains has a different growth direction and orientation, their intersection results in a boundary with high angular misorientation. These are often called ‘high angle’ grain boundaries (Wang et al. Citation2017).
The solidification grain boundary that forms at the end of solidification has both a compositional and crystallographic component. In some situations, it is possible for the crystallographic component of the solidification grain boundary to migrate away from the compositional component. This new boundary that carries with it the high-angle misorientation of the ‘parent’ solidification grain boundary is called a migrated grain boundary (Wang et al. Citation2017).
Figure shows the solidification microstructure of the 309 weld metal near the fusion line consisting of columnar dendrites. This morphology in this area is due to the high G (temperature gradient) to R (solidification rate) ratio and hence low constitutional undercooling (Zhang et al. Citation2018). Under conditions of low solidification rates (low R), steep temperature gradients (high G), or both, plane front solidification can occur. In most practical cases, the plane front breaks down into other modes described by either cellular or dendritic morphologies. In other words, the ratio G/R decreases from the fusion line toward the centreline. This suggests that the solidification mode may change from planar to cellular, columnar dendritic across the fusion zone. The solidification mode that is most stable is dictated by the combined effect of composition, temperature gradient, and solidification rate.
Figure 10. The microstructure of 309 weld metal near the fusion line in two different magnifications: (a) 100 µm and (b) 50 µm.
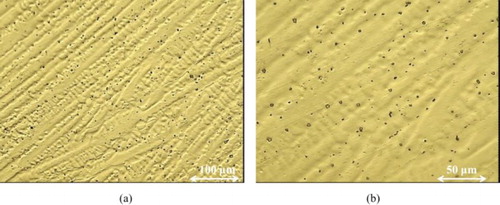
Further investigations showed that inter-dendritic delta ferrite (dark parts) is distributed in the microstructure of weld centre (Figure (a,b)). Elmer et al. reported that a decrease in cooling rate led to an increase in the delta ferrite proportion (Elmer et al. Citation1989). The mean cooling rate in the present study was partially low; it is even lower in the centre of the welding pool. This would result in reduction of alloying elements segregation (Elmer et al. Citation1989). It should be noted that the presence of delta ferrite phase in microstructure could have a two-fold effect. This type of microstructure (AF mode) shows an improved resistance to solidification cracking. However, upon exposure to elevated temperatures, delta ferrite can be transformed to a brittle σ phase impairing the mechanical properties of the welds (Kangazian et al. Citation2017).
4. Conclusion
In this work, dissimilar welding of Incoloy alloy 825 and stainless steel 316 was experimentally investigated using GMAW process. For this purpose, different filler metals such as stainless steel 308, stainless steel 309, stainless steel 316 and Inconel 82 were employed for joining of Incoloy alloy 825 and stainless steel 316. After welding, metallurgical and mechanical tests were conducted to determine the microstructure and mechanical properties of dissimilar welded joints. The following results were obtained from this research:
During tensile tests, fracture occurred in all weldments in the HAZ of stainless steel 316. The reason is that occurrence of grain growth in the HAZ of stainless steel 316 base metal has caused fracture to occur in these zones.
The results of tensile tests showed that dissimilar welds produced by stainless steel 309 filler metal have the maximum tensile strength (566 MPa). Also, the Inconel 82 filler metal has the lowest strength (429 MPa).
The results of average hardness proved that the dissimilar joint with filler metal say stainless steel 309 and filler metal say Inconel 82 had maximum (192 Vickers) and minimum values (150 Vickers) of average hardness in the weld metal, respectively.
A considerable UMZ in the form of laminar layers was observed between filler 82 weld metal and the Incoloy 825 base metal along the welding line. When the melting range of filler materials is similar to or higher than that of the base metal, only a small fraction of the base metal can be melted and no dilution occurs in the re-solidification stage.
A similar trend (considerable UMZ) was seen in the interface of the weld metal/AISI 316 base metal, but more grain growth occurred in the AISI 316 HAZ due to the temperature increase during various welding passes.
A very narrow UMZ between the 309 weld metal and Incoloy 825 base metal was observed; however, no considerable UMZs can be observed in the AISI 316 base metal showing more dilution.
Disclosure statement
No potential conflict of interest was reported by the authors.
ORCID
Mehdi Safari https://orcid.org/0000-0002-6753-677X
Hossein Mostaan http://orcid.org/0000-0003-3890-5502
References
- Chen BQ, Xiong HP, Sun BB, Du BR, Wei ZW, Chen B. 2015. Dissimilar joining of Ti3Al-based alloy to Ni-based superalloy by arc welding technology using gradient filler alloys. Mater Des. 87:732–741. doi: 10.1016/j.matdes.2015.07.168
- Dev S, Ramkumar KD, Arivazhagan N, Rajendran R. 2018. Investigations on the microstructure and mechanical properties of dissimilar welds of Inconel 718 and sulphur rich martensitic stainless steel, AISI 416. J Manuf Process. 32:685–698. doi: 10.1016/j.jmapro.2018.03.035
- Elmer JW, Allen SM, Eagar TW. 1989. Microstructural development during solidification of stainless steel alloys. Metall Mater Trans A. 20:2117–2131. doi: 10.1007/BF02650298
- Hejripour F, Aidun DK. 2017. Consumable selection for arc welding between stainless steel 410 and Inconel 718. J Mater Process Technol. 245:287–299. doi: 10.1016/j.jmatprotec.2017.02.013
- Jeng SL, Lee HT, Weirich TE, Rebach WP. 2007. Microstructual study of the dissimilar joints of alloy 690 and SUS 304L stainless steel. Mater Trans. 48:481–489. doi: 10.2320/matertrans.48.481
- Kangazian J, Shamanian M, Ashrafi A. 2017. Dissimilar welding between SAF 2507 stainless steel and Incoloy 825 Ni-based alloy: the role of microstructure on corrosion behavior of the weld metals. J Manuf Process. 29:376–388. doi: 10.1016/j.jmapro.2017.08.012
- Krolczyk GM, Nieslony P, Krolczyk JB, Samardzic I, Legutko S, Hloch S, Barrans S, Maruda RW. 2015. Influence of argon pollution on the weld surface morphology. Measurement. 70:203–213. doi: 10.1016/j.measurement.2015.04.001
- Krolczyk JB, Gapinski B, Krolczyk GM, Samardzic I, Maruda RW, Soucek K, Legutko S, Nieslony P, Javadi Y, Stas L. 2016. Topographic inspection as a method of weld joint diagnostic. Tehn Vjes – Tech Gazette. 23:301–306.
- Mithilesh P, Varun D, Reddy ARG, Ramkumar KD, Arivazhagan N, Narayanan S. 2014. Investigations on dissimilar weldments of Inconel 625 and AISI 304. Procedia Eng. 75:66–70. doi: 10.1016/j.proeng.2013.11.013
- Moradi M, Ghoreishi M, Khorram A. 2018. Process and outcome comparison between laser, tungsten inert gas (TIG) and laser-TIG hybrid welding. J Lasers Eng. 39:379–391.
- Moradi M, Ghoreishi M, Rahmani A. 2016. Numerical and experimental study of geometrical dimensions on laser-TIG hybrid welding of stainless steel 1.4418. J Mod Proc Manuf Prod. 5:21–31.
- Moradi M, Salimi N, Ghoreishi M, Abdollahi H, Shamsborhan M, Frostevarg J, Ilar T, Kaplan AFH. 2014. Parameter dependencies in laser hybrid arc welding by design of experiments and by a mass balance. J Laser Appl. 26: 022004 (1–9). doi: 10.2351/1.4866675
- Mortezaie A, Shamanian M. 2014. An assessment of micro-structure, mechanical properties and corrosion resistance of dissimilar welds between Inconel 718 and 310S austenitic stainless steel. Int J Press Vessels Pip. 116:37–46. doi: 10.1016/j.ijpvp.2014.01.002
- Naffakh H, Shamanian M, Ashrafizadeh F. 2009. Dissimilar welding of AISI 310 austenitic stainless steel to nickel-based alloy Inconel 657. J Mater Process Technol. 209:3628–3639. doi: 10.1016/j.jmatprotec.2008.08.019
- Palanivel R, Dinaharan I, Laubscher RF. 2017. Microstructure evolution and mechanical characterization of Nd:YAG laser beam welded titanium tubes. Mater Charact. 134:225–235. doi: 10.1016/j.matchar.2017.10.025
- Ramkumar KD, Kumar PSG, Krishna VR, Chandrasekhar A, Dev S, Abraham WS, Prabhakaran S, Kalainathan S, Sridhar R. 2016. Influence of laser peening on the tensile strength and impact toughness of dissimilar welds of Inconel 625 and UNS S32205. Mater Sci Eng A. 676:88–99. doi: 10.1016/j.msea.2016.08.104
- Ramkumar KD, Mithilesh P, Varun D, Reddy ARG, Arivazhagan N, Narayanan S, Kumar KG. 2014. Characterization of microstructure and mechanical properties of Inconel 625 and AISI 304 dissimilar weldments. ISIJ Int. 54:900–908. doi: 10.2355/isijinternational.54.900
- Ramkumar T, Selvakumar M, Narayanasamy P, Begam AA, Mathavan P, Raj AA. 2017. Studies on the structural property, mechanical relationships and corrosion behaviour of Inconel 718 and SS 316L dissimilar joints by TIG welding without using activated flux. J Manuf Process. 30:290–298. doi: 10.1016/j.jmapro.2017.09.028
- Sayiram G, Arivazhagan N. 2015. Microstructural characterization of dissimilar welds between Incoloy 800H and 321 Austenitic stainless steel. Mater Charact. 102:180–188. doi: 10.1016/j.matchar.2015.03.006
- Shah Hosseini H, Shamanian M, Kermanpur A. 2016. Micro-structural and weldability analysis of Inconel 617/AISI 310 stainless steel dissimilar welds. Int J Press Vessels Pip. 144:18–24. doi: 10.1016/j.ijpvp.2016.05.004
- Shakil M, Ahmad M, Tariq NH, Hasan BA, Akhter JI, Ahmed E, Mehmood M, Choudhry MA, Iqbal M. 2014. Microstructure and hardness studies of electron beam welded Inconel 625 and stainless steel 304L. Vacuum. 110:121–126. doi: 10.1016/j.vacuum.2014.08.016
- Stütz M, Pixner F, Wagner J, Reheis N, Raiser E, Kestler H, Enzinger N. 2018. Rotary friction welding of molybdenum components. Int J Refract Met Hard Mater. 73:79–84. doi: 10.1016/j.ijrmhm.2018.02.004
- Tavassolimanesh A, Alavi Nia A. 2018. Investigating the properties of bimetallic aluminum-clad copper tubes produced by friction stir welding. J Alloys Compd. 751:299–306. doi: 10.1016/j.jallcom.2018.04.117
- Wang W, Cao X, Lu Y, Ding X, Shoji T. 2017. TEM study on oxide mechanism of the dissimilar welds between 316 stainless steels/Inconel 182 in high temperature and high pressure water. Mater Charact. 131:339–347. doi: 10.1016/j.matchar.2017.07.004
- Wang W, Lu Y, Ding X, Shoji T. 2015. Microstructures and microhardness at fusion boundary of 316 stainless steel/Inconel 182 dissimilar welding. Mater Charact. 107:255–261. doi: 10.1016/j.matchar.2015.07.018
- Yazdian N, Mohammadpour M, Kong F, Kovacevic R. 2018. Hybrid laser/arc girth welding of 304L stainless steel tubes, part 1 – pore mitigation, thermal analysis and mechanical properties. Int J Press Vessel Pip. 163:75–93. doi: 10.1016/j.ijpvp.2018.05.003
- Zhang Y, Jing H, Xu L, Han Y, Zhao L, Xiao B. 2018. Microstructure and mechanical performance of welded joint between a novel heat-resistant steel and Inconel 617 weld metal. Mater Charact. 139:279–292. doi: 10.1016/j.matchar.2018.03.012
- Zhou C, Huang Q, Guo Q, Zheng J, Chen X, Zhu J, Zhang L. 2016. Sulphide stress cracking behaviour of the dissimilar metal welded joint of X60 pipeline steel and Inconel 625 alloy. Corros Sci. 110:242–252. doi: 10.1016/j.corsci.2016.04.044