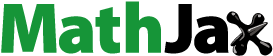
Abstract
The extremely serious effects of the marine environment pollution due to oil spill, oil slick and toxic heavy metals on the human, ecosystem, and society are clearly seen. Findings of absorbent materials with high absorption capacity and high usage efficiency are being much interested by several researchers. In this work, four samples of absorbent material fabricated after adding, respectively, 5%, 25% of rice straw mass percentage along with 0.5 and 3 mm of rice straw size, four oil types including crude oil, fuel oil (FO), diesel oil (DO), kerosene, and a solution containing toxic heavy metals such as Cd2+, Pb2+, Hg2+ are used for the experimental purposes related to the evaluation of the oil absorption capacity (OAC) and toxic heavy metal, and the oil removal efficiency (ORE) during 120–150 min. As a result, the as-used sample with 25% of rice straw mass and 0.5 mm of rice straw size shows the highest absorption capacity. In addition, the influence of capillary pressure on the OAC and ORE is analysed, the assistance of Scanning Electron Microscope (SEM) for observation of porous structure of rice straw, pristine PU, and the as-fabricated absorbent are also conducted and presented in this study.
Introduction
Nowadays, several researchers, managers and policy makers in maritime field, as well as ocean shipping companies are paying much attention to the issues related to not only the sustainable development in maritime transportation through the application of advanced technologies in energy management for dynamic-propulsion system (Hoang Citation2018c; Kuroshi and Ölçer Citation2018) along with the use of alternative fuels and renewable energy for marine engines (Hoang Citation2018b; Hoang and Le Citation2018), but also the satisfaction of strategies and more and more strict regulations for the marine environment protection and maritime safety (Le and Hoang Citation2017; Yuan et al. Citation2017; Pham et al. Citation2018). Facts showed that several cases regarding the pollution of maritime environment have left extremely serious consequences, and oil spill incidents have been considered as the most severe ones because oil spills prevent the dissolution of oxygen into the water resulting in killing marine creatures and aquatic ecosystems, damaging marine biodiversity considerably and coral ecosystems, and others (Goncharov Citation2009; Zilakos et al. Citation2018). As reported in the literature, industrial development, petroleum transportation, oil industry, oil-refining processes, shipwrecks, maritime accidents, maritime operation, and forethought of people are considered as the primary reasons causing the above-mentioned oil spills. Oily contaminants originated from oil spills may be found with various forms such as lubricants, heavy or light hydrocarbons (like grease, crude oil, fuel oil, diesel oil, tars, gasoline, kerosene, and jet fuel) (Zhou et al. Citation2017). Therefore, the in-situ oil spill removal and the elimination of other pollutants are very important purposes aiming at preventing oil spill from spreading and widening on the seawater surface and reducing their disastrous and negative influences on the marine ecosystem (Hoang and Chau Citation2018). Normally, oil spill may cause the negative effects on the environment through one or more following mechanisms (Ma and Chen Citation2013):
Physical smothering causing the unpredictable influence on physiological functions
Chemical toxicity rising to lethal impacts or impairing functions of the cell
Ecological changes causing the takeover of opportunistic species
Other indirect/direct effects on the social economy and human
For oil spill incidents, their nature and duration of the effects are affected by several factors such as oil spill quality and types, the location of the spilled oil, weather conditions, to name just a few (Shadizadeh et al. Citation2014). The selection of suitable techniques for oil spill cleanup with high effectiveness and insignificant effects on the marine environment is extremely necessary. Nowadays, there are several ever-developing techniques to satisfy the strategies of oil spill recovery and removal the fastest, the most economically and efficiently (Hoang, Bui, et al. Citation2018). Advanced techniques and methods may be divided into four main ones, they are physical methods (booms, or skimmers, or adsorbent materials), chemical methods (dispersants or solidifiers), thermal or in-situ burning methods, and bioremediation methods (Hoang Citation2018a). The above methods are used different techniques based on the principles like filtration (micro-, ultra-), osmosis, gravity-based separation, biological in order to treat and recover oil spill (Sayyad Amin et al. Citation2015; Mondal et al. Citation2016). However, physical methods are considered as safe and efficient ones to remove the polluted components because they can recover them with high efficiency, take short time, and affect the marine creatures minimally (Fu and Wang Citation2011; Wang et al. Citation2012). Besides the pollution of marine environment related to oil spills, the appearance of heavy metals in seawater from many different sources such as the soil, the wastewater, maritime operation, oil-rig explosion, harbour is also considered as the serious effect on the human health due to the accumulation of toxic heavy metals such as Cd, Fe, Pb, As, Hg into the food chain (Worthington et al. Citation2017; Lundquist et al. Citation2018). Generally, applied technologies based on chemical precipitates, gelatinisation, electrochemical methods, the ion-exchanger methods, nano-/micro-adsorbents, membrane filtration are used to reduce the heavy metal concentrations in the seawater (Worthington et al. Citation2018). Really, facts showed that there were not many good methods for meeting the criteria of efficiency and low cost. Several studies on the treatment of toxic heavy metals aiming at looking for the new natural and non-toxic absorbents with high adsorption capacity for either spilled oil or toxic heavy metals. Feng et al. (Citation2011) suggested the orange peel-based absorbent, the seaweed was found by Lee and Chang (Lee and Chang Citation2011), biochar was also considered using as a new absorbent by Kilic et al. (Citation2013). In addition, the peanut shell suggested by Witek-Krowiak et al. (Citation2011), coconut fibre and husk suggested by Deng et al. (Citation2013), activated carbon proposed by (Raj and Joy Citation2015) were thought to be considerable absorbents in oil spill and heavy metals cleanup. In recent year, the development of synthetic material-based sorbents in the strategy of improving the adsorption capacity of spilled oil and heavy metals has been much paid attention to. One of the synthetic polymer-based materials used commonly for absorption of the oil spill is polyurethane (PU) which shows featured properties such as open-cell, high porosity causing low density, pore size and connectivity (Shi et al. Citation2014). In the study of Li et al. (Citation2013), PU-based sorbents was detected with higher oil absorption capacity (OAC) after being added appropriate ingredients than other. For another study of, the higher portion of the absorbed oil spill in case of using modified PU foams by changing the monomer ratio, duration of the polymerisation, or initiator concentration than that of pristine PU foams was indicated (Zhang et al. Citation2017). Regarding natural ingredients used to combine with pristine PU, cloisite 20A nanoclay was chosen to add into pristine PU foams at 3% weight in the study of Nikkhah et al. (Nikkhah et al. Citation2015), as a consequence, the mass of absorbed oil increased by 16%; meanwhile, oil removal efficiency increased up 56% compared to the case of using pristine PU. Besides, many natural absorption materials with very low cost and low density may be used to blend with pristine PU to not only increase the pore size, the OAC, the floatability on the seawater surface, but also reduce the cost significantly. Such natural materials may include bagasse, cotton, husk, paper, sawdust, rice straw, e sponges and peat (Rengasamy et al. Citation2011; Kenes et al. Citation2012; Pham and Dickerson Citation2014).
In this study, a new absorbent based on pristine PU foam and rice straw available in Vietnam was fabricated. The absorption capacity of oil and heavy metal concentration was evaluated and determined for the as-used sorbent material aiming at orientating the production process and application of the as-fabricated sorbent material to the purposes of recovery and treatment of oil spill and heavy metal, the contribution of the marine environment protection.
Materials and methods
Materials
Rice straw and pristine polyurethane
A great potential of materials originated from biomass in Vietnam is a clear fact because Vietnam is one of the top countries in rice exports in the world with around 7.8 million hectares of cultivation, thus, rice straw and husk are considered as the extremely cornucopia material sources. Besides, bagasse is also available in Vietnam because the area for planting the cane tree in Vietnam is around 0.3 million hectares. The properties of rice straw, husk and bagasse are given in .
Table 1. Properties of rice straw, husk, and bagasse.
Normally, these above-mentioned biomass sources including rice straw, husk, and bagasse are usually used as a combustive material for daily lives of farmers living in the rural area, a small number of those are annealed to rot before using as compost. However, rice straw, husk, and bagasse are light and porous materials, therefore, their utilisation and application for the other useful works should be conducted. The SEM of rice straw, husk, and bagasse are presented in Figure .
From Figure and Table , it can be seen that the porous level of rice straw (Figure (c)) is higher than that of husk (Figure (b)) and bagasse (Figure (a)). In addition, the density is rice straw is lower than that of husk and bagasse, Due to this reason, rice straw was used in this study to fabricate a new sorbent for experimental purposes related to the evaluation of the OAC. The as-used rice straw was collected from rice variety based on Oryza sativa HYT100, which has been being popularly planted in Vietnam.
Regarding polyurethane (PU), it is known along with ultra-light and highly-porous properties, very low density (around 45–40 kg/m3) and open-cell that allow the oil to be absorbed into its internal structure that is shown through its SEM in Figure .
However, due to the contain of Di-/poly-functional hydroxyl (–OH) (so-called polyol, (R′−(OH)n) compounds (component B) or amino-based compounds (component A (including di-/poly-functional isocya-nates, R−(N = C=O)n), the PU uptake for either oil or water was indicated (Hoang et al. Citation2018). The PU uptake for either oil or water is indicated. Besides, the oleophilic/hydrophobic properties due to the addition with some hydrophobic monomers (such as Lauryl methacrylate, Butyl Methacrylate, Styrene), cross-linker component (such as Divinylbenzene), the initiator (Benzoyl peroxide), and the solvent (Toluene) are reported. The ratio of monomer and the polymerisation time are the factors to evaluate the OAC of PU and they are studied and mentioned in this work.
Absorbent synthetic
By experiment, the ratio of component A and component B for production of pristine PU in this work was determined with 150:60. For the preparation of new absorbent based on rice straw and pristine PU, a 5% and 25% mass of rice straw was added into component-A after being cut and selected a good sieve which helped to collect the rice straw with the length meeting the requirements. Before using rice straw for fabricating the new absorbent, rice straw was pre-processed by NaOH (at 10–20%), at around 130–160°C during 3–5 h. After that, the mixture containing component A and pre-processed rice straw was mixed by a stirrer during 2–3 min before pouring component B. The new absorbent based on PU and rice straw was cut into pieces with dimension appropriate to the experiment requirements after the polymerisation process finished. In this study, the length values of rice straw were, respectively, 0.5 and 3 mm, thus, there were four samples used to evaluate the results for the above-mentioned experimental purposes. Four samples were 5% mass of rice straw with 0.5 mm of rice straw length (S1), 25% mass of rice straw with 0.5 mm of rice straw length (S2), 5% mass of rice straw with 3 mm of rice straw length (S3), 25% mass of rice straw with 3 mm of rice straw length (S4). The as-fabricated samples were taken the photo as Figure and SEM taken by JSM-7000F were shown in Figure . After fabricating this new absorbent, they were carefully weighed to measure the density which was given in Table .
Table 2. Density of absorbent based on PU and rice straw.
Oil samples for experiments
For these purposes in this work, four oil samples including crude oil, fuel oil (FO), diesel oil (DO), and kerosene with some key physical properties were given in Table . The ASTM F726-99 standard was used to monitor and measure the value of OAC. The reason of selection of the above-mentioned oil samples was that those oil samples are the petroleum refinery products and are transported by the sea route the most.
Table 3. Physical properties of oil samples.
Methods
To determine the OAC for four samples S1, S2, S3, and S4, they were cut with appropriate dimension (2 × 2 × 2 for this work) before being immersed into the glass that contained 100 ml of pure water and 50 ml of the oil sample. All experiments shown in Figure were carried out in the laboratory under ambient pressure and temperature without external forces.
Each sample was immersed into the glass containing oil and water during 15, 30, 60, 90, 120, and 150 min (with duration error ± 30s). After the above duration, the sample was taken out the glass and was weighed to measure the oil and water that was absorbed. The OAC for each sample was determined after the sample was completely dried to drain under vacuum. After weighing the weight of the sample before (Wo) and after (Wt) conducting the experiment, the weight of uptake water (Wu), the OAC for each sample was calculated by the following equation (Hoang et al. Citation2018):
(1)
(1)
The OAC (g/g) for each sample was considered as the mass of absorbed oil compared to the mass of ass-used absorbent. To get the accuracy results, each experiment was conducted under three times to get the average value, and the result with three decimals was used in this experiment. If any results deviated over 15% from the arithmetic mean in the two-time measurement, that data was rejected and the test was repeated. Oil removal efficiency (ORE) of the absorbent was evaluated through the ratio of the weight of adsorbed oil (Woil) compared to the total weight of as-used absorbent (Wt), ORE is calculated as followed:
(2)
(2)
Regarding the measurement of the absorption capacity for heavy metal concentrations, a 50 ml solution including Cd2+, Pb2+, Hg2+ with 100 mg/l of concentration was poured into a glass containing 100 ml of water. After that, each absorbent sample, which was accurately weighed to the milligram, was immersed into the above glass. The ICP-OES method (Inductively Coupled Plasma – Optical Emission Spectrophotometer, WLY-100-15000) was used to determine the absorbed heavy metal concentration Qe (mg/g) after duration 10, 20, 40 and 60 min, Qe (mg/g) was calculated by the following equation (Hoang et al. Citation2018):
(3)
(3)
where Co (mg/l) – the concentration of initial metal ion; Ce (mg/l) – the concentration of metal ion after experiment; V (l) – the volume of solution.
Results and discussion
Capillary pressure (Δp)
As reported in the literature, the volumetric absorption coefficient was considered as a factor evaluating the mass/volume of absorbed oil as well as the porosity of absorbent. Thus, the maximum volume of absorbed oil may be equal to the porosity volume. In fact, VAC is calculated through the ratio of volumetric absorption (voil/vo) which is the rate of absorbed oil volume to the volume of the as-used absorbent. It is evident that the maximal volumetric absorption capacity (voil/vo)max is thought to correlate with the porosity percentage of absorbent directly, the porosity percentage is also a factor characterising the OAC of absorbent when it allows the oil to be filled and trapped inside its porous structure. The increase of filling and trapping, retaining absorbed spilled oil into the porosity of absorbent is the mechanism to improve the OAC. However, when the oil was pushed and trapped into the porous pores of the absorbent, the key factor such as the capillary pressure (ΔP) is used to determine the retaining capacity of the absorbent. Normally, ΔP is inversely proportional to the pore diameter, but it is proportional to spilled oil surface tension and contact angle (θ) between oil particles and the surface of the absorbent. ΔP was suggested by Zhu et al. (Citation2013) with Equation (4), and the contact angle (θ) is illustrated in Figure .
(4)
(4)
where σoil – the oil surface tension (N/m), θ – contact angle between oil particles and the surface of absorbent, d – the pore diameter (μm).
From Figure and Equation (4), it can be seen the dependence of absorbed oil mass on either the contact angle (θ) or spilled oil surface tension and the pore diameter (Hubbe et al. Citation2013). The increase in the values of ΔP results in the increase of OAC, this is similar to that the decrease of the pore diameter along with the increase in the spilled oil surface tension also leads to the retention of absorbed oil in the pore, thus, the OAC increases. The relationship between ΔP and the pore diameter (d) for each spilled oil type is plotted in Figure (a–d).
Figure (a–d) shows that crude oil is easily absorbed with the same contact angle and pore diameter of the absorbent. Meanwhile, kerosene with low surface tension is thought to be difficultly absorbed due to the decrease of ΔP. Normally, the OAC increases in the proportional relationship to the pore diameter. The big OAC may occur while the pore diameter is larger than 1000μm. This result may be because of ΔP value in each pore of absorbent with a large diameter is small enough to continue filling and trapping high-surface tension spilled oils into the porous structure and absorbed oil is transferred to the inside porous pores. After that, spilled oil is retained in those porous pores before being recovered and extracted by other mechanical devices. In addition, surface tension also plays an important role in the OAC through its effects on ΔP. In this study, a finding for four samples of absorbent related to the OAC was indicated that kerosene with the lowest surface tension (σ = 0.225 N/m) showed the lowest OAC for four samples of absorbent; meanwhile, the crude oil with the highest surface tension (σ = 0.317 N/m) showed the highest OAC for the four samples of absorbent. Achieved results from this study are similar to those from the published work of Hokkanen et al. (Citation2016).
Oil absorption capacity
Effect of rice straw mass and size on OAC of as-fabricated absorbent
As presented in the previous section, four samples S1, S2, S3, and S4 were fabricated based on the percentage of rice straw mass and the size of rice straw. In this section, the OAC values for the above samples were evaluated during 150 min. Figure (a) showed the OAC of four samples S1, S2, S3, and S4; meanwhile, Figure (b) showed the water uptake of four samples S1, S2, S3 and S4 at room temperature in comparison with pristine PU and rice straw.
It can be clearly seen from Figure that there were differences in OAC and water uptake of the as-used samples. Figure (a) showed that the OAC of S2 sample was much higher than that of S1 in the case of 0.5 mm of rice straw size. This difference may be because the porous pores in S2 were much more than that in S1 as increased the mass percentage of rice straw. The increase in porous pore resulted in the suitability for high-viscosity liquid. Consequently, absorption capacity for crude oil of S1 and S2 samples were higher than that for FO, DO, and kerosene. After 150 min of the experiment, the absorbed crude oil mass for S1 was 4.942 g/g, and it was higher than a case of using FO, DO and kerosene was 7.20%, 16.91%, and 27.47%, respectively. The absorbed crude oil mass for S1 was 7.71% and 130.39% higher compared to pristine PU and rice straw. The absorbed FO, DO, and kerosene mass for S1 were also found with higher than those of pristine PU and rice straw. For S2 sample, the absorbed crude oil mass was around three times higher than that of S1, corresponding to 14.921 g/g. The similar increases in absorbed FO, DO, and kerosene mass for S2 compared to S1 were clearly observed in Figure (a). However, the absorbed FO, DO, and kerosene mass for S2 were 7.58%, 24.21%, and 41.20%, respectively, lower than the absorbed crude oil mass. Especially, the OAC of four oil samples for S2 was just above 3 times higher than that for pristine PU and from seven to eight times higher than that for rice straw. Besides, the reflection from the results of water uptake based on Figure (b) in the experiments of the OAC evaluation (such as EX1 for the evaluation of crude OAC, EX2 for the evaluation of fuel OAC, EX3 for the evaluation of diesel OAC, EX4 for the evaluation of kerosene absorption capacity) was appropriate to the achieved results from Figure (a). It is evident that the water uptake mass was inversely proportional to the mass of absorbed oil. The highest mass of water uptake for S1 was 7.572 g/g in the EX4; meanwhile, the lowest mass of water uptake for S1 was 5.814 g/g in the EX1. For S2 sample, the highest mass of water uptake was only 2.814 g/g in the EX4, and the lowest mass of water uptake was 2.228 g/g in the EX1.
In the case of 3 mm of rice straw size, the obtained results showed the contrary trend related to the OAC and water uptake mass compared to the case of 0.5 mm of rice straw size. This meant that the OAC increased when the mass percentage of rice straw was decreased. The S3 sample with (5% of rice straw mass) showed the higher OAC than S4 sample (25% of rice straw mass). The above results may be explained due to the increase in pore diameter resulting in a decrease of oil retention. However, the water retention in PU structure may increase due to the low viscosity of water, and it is thus easily absorbed. Based on the obtained results from Figure , the highest absorbed crude oil for S3 was 11.758 g/g. The OAC of S3 for kerosene was the lowest, corresponding to 5.074 g/g. Meanwhile, for S4, the absorbed crude oil was only 4.716 g/g, and the absorbed kerosene was only 3.486 g/g. The highest mass of water uptake for S3 was 2.428 g/g and for S4 was 6.239 g/g the EX4. Although the OAC for S1 and S4 were much lower than those of S2 and S3, they were still higher than those of pristine PU and rice straw. These results were appropriate to ΔP values of four oil samples shown in Figure . Regarding the oil removal efficiency (ORE) suggested in Equation (2), the ORE for S1, S2, S3, and S4 samples was given in Table .
Table 4. Oil removal efficiency (ORE) of as-fabricated absorbent samples
As presented, ORE was used to evaluate the OAC compared to the water uptake capacity. It can be clearly seen in Table that S2 and S3 samples showed the higher ORE than that of other cases. Although the OAC of S1 and S4 were higher than those of PU and rice straw, the water uptake mass was found with higher values leading to the decrease of the ORE. For S2, the ORE in the case of crude oil was the highest, corresponding to 87%, thus, it showed only 13% of water uptake. ORE is considered as an extremely important factor to evaluate the floating characteristic of oil absorption materials. Based on the values of ORE, S1 and S2 may be suitable absorbent materials for strategies of marine protection from oil spill incidents.
Effect of time on the ORE
Oil removal efficiency (ORE) is considered as a key factor to evaluate the OAC of each absorbent material. Normally, absorbent material should have high ORE that characterises high OAC. As reported in the previous section, the OAC of samples S2 and S3 showed the highest value. In this section, the effects of time on the ORE of samples of the as-used S2 and S3 samples were investigated. The ORE of S2 and S3 samples were plotted in Figure .
It can be clearly seen from Figure that the ORE of samples tended to be proportional to the increase of time. The ORE of S2 and S3 in the first 15 min reached the highest values. The ORE values for S2 sample in case of using crude oil, fuel oil, diesel oil, and kerosene for experiments were 56.5%, 53.6%, 50.7%, and 47.8%, respectively. However, the ORE values for S3 tended to reduce in comparison with S2 sample, the ORE values for S3 sample in case of using crude oil, fuel oil, diesel oil, and kerosene for experiments were 54.2%, 51.0%, 39.6%, and 34.7%, respectively. These results may be explained because the volume of porous pore in the absorbent structure in the first minutes was the highest. After the first 15 min, the absorbed oil and water increased leading to the reduction of porous pore and the increase of the drawback pressure, as a result, the OAC decreased in the next period. After 120 min of experiments, the equilibrium tendency and saturated phenomenon in the absorbent structure seemed to occur due to the penetration of oil into the micro-pores/porosities. Although the ORE for two samples S2 and S3 also increased, the increasing level was very small. Compared to first 15 min, the ORE for S2 after 120 min of experiment increased only 28.6%, and for S3 increased 30.0%. This increase was seen lower after 150 min, corresponding to 1.9% for S2 and 2.2% for S3. This meant that the absorbed oil in 105 min (from first 15 min to the period of 120 min) increased only 0.3% per a minute compared to 3.8% per a minute for S2 and 3.6% a minute for S3 in the first 15 min. The similar results related to the OAC and ORE of PU-based absorbent materials were presented in the published works (Hoang et al. Citation2018)(Sayyad Amin et al. Citation2015). In addition, the as-fabricated absorbent on the basis of rice straw (a by-product of agriculture) and pristine PU showed higher OAC and ORE compared to the other natural absorbent materials such as Azolla plant (Zeiger et al. Citation2016), vegetable fibres (Wu et al. Citation2014), palm fruit bunch fibre (Izani et al. Citation2013), or treated rice husk (Wang et al. Citation2015).
The absorption capacity of toxic heavy metals
Based on the rice straw SEM (Figure ) and SEM of pristine PU (Figure ), it can be clearly seen that there are many nodules on the groove-structure surface of rice straw and many porous pores in the internal structure of PU. These structures increase not only the OAC and toxic heavy metal ions due to the porous structure, but also the retention capacity of the above components because of the roughness on the surface of rice straw. As reported in the above section, the S2 and S3 samples showed the highest OAC and ORE, therefore, the study on the absorption capacity of toxic heavy metal ions including Cd2+, Pb2+, Hg2+ is evaluated for S2 and S3 samples in this section. The dependence of the absorbed metal ion concentrations for S2 and S3 samples on the time is shown in Figure .
It can be clearly seen from Figure that the absorbed toxic heavy metal concentrations Cd2+, Pb2+, Hg2+ increased rapidly in the first 60 min, however, this increase was insignificantly after the first 60 min. For Cd2+, it is considered as a toxic metal affecting strongly the bone. In the first 60 min, the absorbed Cd2+ concentration was 93.1 mg/g for S3 sample (Figure (b)) and 212.9 mg/g for S2 sample (Figure (a)). However, the Cd2+ concentration increased by only 8.2 mg/g for S3 and 9.6 mg/g for S2 after the following 60 min. Additionally, Lead (Pb) is also a very toxic chemical element affecting the human and animal health as well as the environment seriously. Based on Figure (a), after the first 60 min, the absorbed Pb2+ concentration for S2 sample was 221.8 mg/g, this Pb2+ concentration for S3 sample was only 102.1 mg/g. It is similar to Cd2+ concentration, the increase of absorbed Pb2+ concentration at the period of 90 and 120 min was infinitesimal, corresponding to around 0.3%. The Hg2+ concentration absorbed was found the highest in this experiment. The highest absorbed Hg2+ concentration for S2 was 241.1 mg/g after 120 min, this value was 87.78% higher than that of S3 sample. Up to now, Mercury (Hg) is always considered as the extremely toxic element, the concerns related to the appearance of Hg in the environment due to the maritime operation or mining operation was mentioned in the references (Esdaile and Chalker Citation2018). The absorption capacity of heavy metal of S2 was higher than that of S3 may be because the absorbent material based on 25% of the rice straw mass percentage and 0.5 mm of rice straw size showed the appropriate porosity and roughness to imbibe and retain the heavy metal in their structure. The achieved results showed that this new absorbent material can be used to absorb either spilled oil or toxic heavy metal in some industries and maritime field to protect the environment from oil spill and toxic heavy metal.
Conclusions
In this experimental study, the new absorbent material was fabricated based on polyurethane (PU) and by-product agriculture such as rice straw. The obtained results showed that the as-fabricated absorbent with 25% of rice straw mass percentage and 0.5 mm of rice straw size had the highest OAC, ORE as well as the absorption capacity of toxic heavy metal. The minimal time for the as-used sample to get the stable equilibrium in the experiment of the OAC and ORE determination was 120 min; meanwhile, the minimal time in the experiment of heavy metal absorption was 60 min. As a result, the mass of absorbed oil after 120 min of treatment increased significantly, corresponding to 14.921 g/g for crude oil, 13.870 g/g for fuel oil, 12.012 g/g for diesel oil and 10.567 g/g for kerosene. For toxic heavy metal, the absorption capacity of the above-mentioned sample also showed the highest value. The highest Cd2+, Pb2+, and Hg2+ concentrations after the stable equilibrium occurred were, respectively, 212.9, 221.8, and 231.2 mg/g. Based on the OAC and ORE of the above-mentioned new absorbent material, a small-to-medium scale may be applied to the strategies of oil spill recovery and treatment. The as-fabricated absorbent material originated from available endless biomass resources and PU can bring many benefits related to not only the strategies of the marine environment protection, but also the eco-technical/socioeconomic development.
Disclosure statement
No potential conflict of interest was reported by the authors.
References
- Deng PY, Liu W, Zeng BQ, Qiu YK, Li LS. 2013. Sorption of heavy metals from aqueous solution by dehydrated powders of aquatic plants. Int J Environ Sci Technol. 10(3):559–566. doi: 10.1007/s13762-013-0186-3
- Esdaile LJ, Chalker JM. 2018. The mercury problem in artisanal and small-scale gold mining. Chem Eur J. 24(27):6905–6916. doi: 10.1002/chem.201704840
- Feng N, Guo X, Liang S, Zhu Y, Liu J. 2011. Biosorption of heavy metals from aqueous solutions by chemically modified orange peel. J Hazard Mater. 185(1):49–54. doi: 10.1016/j.jhazmat.2010.08.114
- Fu F, Wang Q. 2011. Removal of heavy metal ions from wastewaters: a review. J Environ Manag. 92(3):407–418. doi: 10.1016/j.jenvman.2010.11.011
- Goncharov VK. 2009. Simulation of oil drops dynamics in seawater environment. J Mar Eng Technol. 8(3):21–28. doi: 10.1080/20464177.2009.11020224
- Hoang AT. 2018a. A report of the oil spill recovery and treatment technologies to reduce the marine environment pollution. Int J E-Navig Marit Econ. 9:35–49.
- Hoang AT. 2018b. Prediction of the density and viscosity of biodiesel and the influence of biodiesel properties on a diesel engine fuel supply system. J Mar Eng Technol. doi:10.1080/20464177.2018.1532734.
- Hoang AT. 2018c. Waste heat recovery from diesel engines based on organic Rankine cycle. Appl Energy. 231:138–166. doi: 10.1016/j.apenergy.2018.09.022
- Hoang AT, Bui XL, Pham XD. 2018. A novel investigation of oil and heavy metal adsorption capacity from as-fabricated adsorbent based on agricultural by-product and porous polymer. Energy Sources A. 40(8):929–939. doi: 10.1080/15567036.2018.1466008
- Hoang AT, Chau MQ. 2018. A mini review of using oleophilic skimmers for oil spill recovery. J Mech Eng Res Dev. 41(2):92–96.
- Hoang AT, Le AT. 2018. A review on deposit formation in the injector of diesel engines running on biodiesel. Energy Sources A. doi:10.1080/15567036.2018.1520342.
- Hoang AT, Le VV, Al-Tawaha ARMS, Nguyen DN, Al-Tawaha ARMS, Noor MM, Pham VV. 2018. An absorption capacity investigation of new absorbent based on polyurethane foams and rice straw for Oil spill cleanup. Pet Sci Technol. 36(5):361–370. doi: 10.1080/10916466.2018.1425722
- Hokkanen S, Bhatnagar A, Sillanpää M. 2016. A review on modification methods to cellulose-based adsorbents to improve adsorption capacity. Water Res. 91:156–173. doi: 10.1016/j.watres.2016.01.008
- Hubbe MA, Rojas OJ, Fingas M, Gupta BS. 2013. Cellulosic substrates for removal of pollutants from aqueous systems: a review. 3. spilled Oil and emulsified organic liquids. BioResources. 8(2):3038–3097.
- Izani MAN, Paridah MT, Anwar UMK, Mohd Nor MY, H’ng PS. 2013. Effects of fiber treatment on morphology, tensile and thermogravimetric analysis of oil palm empty fruit bunches fibers. Compos B Eng. 45(1):1251–1257. doi: 10.1016/j.compositesb.2012.07.027
- Kenes K, Yerdos O, Zulkhair M, Yerlan D. 2012. Study on the effectiveness of thermally treated rice husks for petroleum adsorption. J Non-Cryst Solids. 358(22):2964–2969. doi: 10.1016/j.jnoncrysol.2012.07.017
- Kılıc M, Kırbıyık C, Çepelioğullar Ö, Pütün AE. 2013. Adsorption of heavy metal ions from aqueous solutions by bio-char, a by-product of pyrolysis. Appl Surf Sci. 283:856–862. doi: 10.1016/j.apsusc.2013.07.033
- Kuroshi L, Ölçer AI. 2018. A modified AD-TRIZ hybrid approach to regulation-based design and performance improvement of ballast water management system. J Mar Eng Technol. doi:10.1080/20464177.2018.1507444.
- Le VV, Hoang AT. 2017. Marine pollution and remedies of Vietnamese government. Int J Recent Eng Res Dev. 2(4):51–55.
- Lee Y-C, Chang S-P. 2011. The biosorption of heavy metals from aqueous solution by spirogyra and cladophora filamentous macroalgae. Bioresour Technol. 102(9):5297–5304. doi: 10.1016/j.biortech.2010.12.103
- Li H, Liu L, Yang F. 2013. Oleophilic polyurethane foams for oil spill cleanup. Proc Environ Sci. 18:528–533. doi: 10.1016/j.proenv.2013.04.071
- Lundquist NA, Worthington MJH, Adamson N, Gibson CT, Johnston MR, Ellis AV, Chalker JM. 2018. Polysulfides made from re-purposed waste are sustainable materials for removing iron from water. RSC Adv. 8(3):1232–1236. doi: 10.1039/C7RA11999B
- Ma L, Chen G. 2013. Method for oil spill monitoring by polarimetric SAR. Environ Forensics. 14(4):294–300. doi: 10.1080/15275922.2013.843615
- Mondal DK, Mondal C, Roy S. 2016. Catalytic wet air oxidation of aqueous solution of phenol in a fixed bed reactor over Ru catalysts supported on ceria promoted MCM-41. RSC Adv. 6(115):114383–114395. doi: 10.1039/C6RA22080K
- Nikkhah AA, Zilouei H, Asadinezhad A, Keshavarz A. 2015. Removal of Oil from water using polyurethane foam modified with nanoclay. Chem Eng J. 262:278–285. doi: 10.1016/j.cej.2014.09.077
- Pham MT, Hoang AT, Le AT, Al-Tawaha ARMS, Dong VH, Le VV. 2018. Measurement and prediction of the density and viscosity of biodiesel blends. Int J Technol. 9(5):1015–1026. doi: 10.14716/ijtech.v9i5.1950
- Pham VH, Dickerson JH. 2014. Superhydrophobic silanized melamine sponges as high efficiency Oil absorbent materials. ACS Appl Mater Interfaces. 6(16):14181–14188. doi: 10.1021/am503503m
- Raj KG, Joy PA. 2015. Coconut shell based activated carbon–iron oxide magnetic nanocomposite for fast and efficient removal of Oil spills. J Environ Chem Eng. 3(3):2068–2075. doi: 10.1016/j.jece.2015.04.028
- Rengasamy RS, Das D, Praba Karan C. 2011. Study of oil sorption behavior of filled and structured fiber assemblies made from polypropylene, kapok and milkweed fibers. J Hazard Mater. 186(1):526–532. doi: 10.1016/j.jhazmat.2010.11.031
- Sayyad Amin J, Abkenar MV, Zendehboudi S. 2015. Natural sorbent for oil spill cleanup from water surface: environmental implication. Ind Eng Chem Res. 54(43):10615–10621. doi: 10.1021/acs.iecr.5b01715
- Shadizadeh SR, Khodashenas A, Abtahi SM, Roayaei E. 2014. Experimental investigation of oil spill cleanup using cholan as a natural oil absorber. Energy Sources Part A. 36(9):982–992. doi: 10.1080/15567036.2010.549924
- Shi H, Shi D, Yin L, Yang Z, Luan S, Gao J, Zha J, Yin J, Li RK. 2014. Ultrasonication assisted preparation of carbonaceous nanoparticles modified polyurethane foam with good conductivity and high Oil absorption properties. Nanoscale. 6(22):13748–13753. doi: 10.1039/C4NR04360J
- Wang J, Zheng Y, Wang A. 2012. Superhydrophobic kapok fiber Oil-absorbent: preparation and high Oil absorbency. Chem Eng J. 213:1–7. doi: 10.1016/j.cej.2012.09.116
- Wang Z, Barford JP, Hui CW, McKay G. 2015. Kinetic and equilibrium studies of hydrophilic and hydrophobic rice husk cellulosic fibers used as oil spill sorbents. Chem Eng J. 281: Elsevier:961–969. doi: 10.1016/j.cej.2015.07.002
- Witek-Krowiak A, Szafran RG, Modelski S. 2011. Biosorption of heavy metals from aqueous solutions onto peanut shell as a Low-cost biosorbent. Desalination. 265(1):126–134. doi: 10.1016/j.desal.2010.07.042
- Worthington MJH, Kucera RL, Albuquerque IS, Gibson CT, Sibley A, Slattery AD, Campbell JA, Alboaiji SF, Muller KA, Young J. 2017. Laying waste to mercury: inexpensive sorbents made from sulfur and recycled cooking oils. Chem Eur J. 23(64):16219–16230. doi: 10.1002/chem.201702871
- Worthington MJH, Shearer CJ, Esdaile LJ, Campbell JA, Gibson CT, Legg SK, Yin Y, Lundquist NA, Gascooke JR, Albuquerque IS. 2018. Sustainable polysulfides for oil spill remediation: repurposing industrial waste for environmental benefit. Adv Sust Syst. 2(6). doi:10.1002/adsu.201870034.
- Wu Z-Y, Li C, Liang H-W, Zhang Y-N, Wang X, Chen J-F, Yu S-H. 2014. Carbon nanofiber aerogels for emergent cleanup of oil spillage and chemical leakage under harsh conditions. Scientific Reports 4. Nature Publishing Group.
- Yuan Y, Li Z, Malekian R, Yan X. 2017. Analysis of the operational ship energy efficiency considering navigation environmental impacts. J Mar Eng Technol. 16(3):150–159. doi: 10.1080/20464177.2017.1307716
- Zeiger C, Isabelle C, da Silva R, Mail M, Kavalenka MN, Barthlott W, Hölscher H. 2016. Microstructures of superhydrophobic plant leaves-inspiration for efficient oil spill cleanup materials. Bioinspir Biomim. 11(5). doi:10.1088/1748-3190/11/5/056003.
- Zhang T, Kong L, Dai Y, Yue X, Rong J, Qiu F, Pan J. 2017. Enhanced oils and organic solvents absorption by polyurethane foams composites modified with MnO2 nanowires. Chem Eng J. 309:7–14. doi: 10.1016/j.cej.2016.08.085
- Zhou Y, Gu X, Zhang R, Chen L, Lu J. 2017. Microbial degradation of diesel oil and heavy oil in the presence of modified clay. Energy Sources Part A. 39(3):326–331. doi: 10.1080/15567036.2014.960956
- Zhu Q, Chu Y, Wang Z, Chen N, Lin L, Liu F, Pan Q. 2013. Robust superhydrophobic polyurethane sponge as a highly reusable oil-absorption material. J Mater Chem A. 1(17):5386–5393. doi: 10.1039/c3ta00125c
- Zilakos I, Chatzidouros E, Tsouvalis N. 2018. An innovative ship salvage concept and its effect on the hull structural response. J Mar Eng Technol. doi:10.1080/20464177.2018.1508629.