Abstract
Poly(methyl methacrylate) (PMMA) nanocomposites containing nanoclay with and without compatibilizer (PMMA-g-MA) were prepared by melt blending followed by compression molding in order to investigate the rheological and flammability properties of developed nanocomposites. The rheological measurements at various temperatures and frequencies were performed using rheometer with parallel-plate geometry. The frequency sweep result revealed that storage modulus improved with the addition of nanoclay at lower frequency and gradually changed from liquid-like behavior to solid-like behavior due to the formation of percolating network structure. For all the samples, complex viscosity decreased as the temperature increased. Similarly, dynamic mechanical investigations exhibited a significant enhancement in storage modulus at lower temperature due to reinforcing effect of nanoclay. The flammability test also demonstrated that rate of burning was reduced by 37% with the addition of nanoclay.
Graphical Abstract
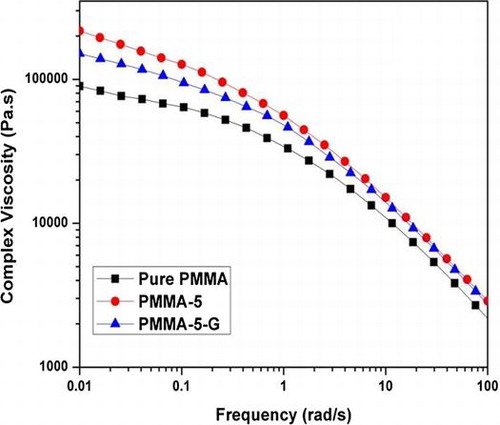
Introduction
In recent days, polymer nanocomposites are attaining considerable interest owing to its improved mechanical property, increased heat resistance, decreased gas permeability, and flammability retardancy over the matrix polymers.Citation1–4 Various fillers such as inorganic nanotubes, expandable graphite, metal oxide nanoparticles, cellulose nanowhiskers, polyhedral oligomeric silsesquioxanes (POSS), and clay have been used to achieve a significant improved performance.Citation5–7 Poly (methyl methacrylate) is an amorphous thermoplastic with excellent optical clarity, hard, good ultraviolet stability, and outstanding weathering properties. One of its limitations is its thermal instability at higher temperature due to which its use is severely restricted. Pristine-layered silicates generally contain hydrated Na+ or K+ ions and only miscible with polyethylene oxide and polyvinyl alcohol (PVA).Citation8 The interaction of these pristine particles with nonpolar polymers is unfavorable. To overcome this, the hydrated Na+ ions content of the MMT clay must be converted to organophilic one by ion-exchange reactions with cationic surfactants, which results in organically modified clay. The addition of layered type of nanofillers including montmorillonite (MMT)Citation9 and layered double hydroxide (LDH)Citation10 in the polymer matrices usually yielded either intercalated or exfoliated structures depending upon the interaction between nanofiller and polymer.Citation11 Different methods have been employed for the preparation of polymer–clay nanocomposites, which include solution blending, melt blending, and in situ polymerization. Among these methods, melt blending has been proved to be most adoptable technique to prepare polymer nanocomposites as it is widely accepted as an industrial process. This process generally produces the intercalation or exfoliation of layered silicate nanocomposites. The other advantages are no usage of solvent and contrary to other synthesis routes, enable a continuous processing. This melt blending method is generally suitable for samples with 1–10 wt% of nanofiller loading.Citation12 When the nanofiller content is greater than 10 wt%, the viscosity of polymer increases drastically and mixing becomes more difficult. Consequently, the properties of the nanocomposite reduce significantly.
Rheometry is a useful tool for analyzing the melt rheological behavior of polymer nanocomposites. Several studies have been carried out on the basis of frequency dependent to understand the rheological behavior.Citation13–17 However, according to our best knowledge, very limited work was reported in the open literatureCitation18 on the rheological properties of the polymer nanocomposites with the variation in temperature. The frequency-dependent analysis usually provides complex viscosity, storage, and loss moduli data, which are useful to ascertain the processing conditions. On the other hand, the temperature-dependent analysis exhibits up to what extent polymer material is stable for processing. Therefore, it is beneficial where one can understand both types of rheological study. The incorporation of nanofillers in a molten polymer brings a significant change in the viscoelastic properties. It was also observed that modifier concentration, critical mixing time, and long-chain branching influenced the viscoelastic property of PP nanocomposites.Citation19–21 Lim and ParkCitation22 noticed that the presence of randomly oriented anisotropic stacks of silicate layers was responsible for the enhancement of storage and loss modulus in intercalated structure. In another study,Citation23 it was found that percolation threshold depended upon both concentration and alignment of carbon nanotubes. Chrissopoulou and AnastasiadisCitation24 reported that polyolefin/layered silicate nanocomposites demonstrated solid-like rheological behavior with an increase in clay content. Abdel-Goad et al.Citation25 stated that dynamic moduli and melt viscosity of different polymer nanocomposites were increased with the addition of expanded graphite. Chopra et al.Citation26 stated that 14% maleic anhydride in styrene-co-maleic anhydride provided higher miscibility over other compositions. Song et al.Citation27 pointed out that graphene-based nanocomposite displayed higher storage modulus and complex viscosity as compared to nanoclay and CNT’s. Ray and co-workersCitation28 reported that PLA/C18 MMT clay nanocomposites exhibited increased material properties in both solid state and melt state as compared to neat polymer. He et al.Citation29 reported that nylon 11 nanocomposites demonstrated better storage modulus and viscosity at 2% clay loading over 5% loading. The relaxation behavior of polymer chains is altered when they are tethered or in close proximity of silicate layers in intercalated structure (Krishnamoorti et al.Citation30).
As discussed above, the influence of different temperatures on the rheological properties of nanocomposites is scarce in the literature. Therefore, in this work, the influence of nanoclay and compatibilizer on the rheological behavior of PMMA nanocomposites as a function of temperature and frequency is investigated. The dynamic mechanical analysis and flammability retardancy of nanocomposites are also examined.
Experimental
Materials
PMMA (IG 840) polymer used in this study was a commercial product from LG Polymers, South Korea. The melt flow index (MFI at 230°C and 3.8 kg load) and specific gravity of PMMA were 5.8 g/10 min and 1.18, respectively. Nanoclay (Nanomer 1.31 PS, MMT clay surface modified with 15–35% octadecylamine and 0.5–5 wt% aminopropyl triethoxysilane) was purchased from Sigma-Aldrich, USA. Methanol was procured from Merck India Ltd. Benzoyl peroxide and maleic anhydride were supplied by Loba Chemie Pvt. Ltd. Xylene was obtained from Rankem, RFCL Limited, India. All the materials were used as such without further purification.
Preparation of PMMA nanocomposites
Firstly, compatibilizer, maleic anhydride (MA) grafted PMMA (PMMA-g-MA), was synthesized according to the procedure reported elsewhere.Citation31 Before melt intercalation, PMMA pellets and nanoclay were dried in a vacuum oven at 80 and 65°C, respectively, for 12 h. PMMA nanocomposites containing 5 wt% nanoclay (with and without compatibilizer) were prepared by melt intercalation technique in a single screw extruder (Make: Neoplast Engineering Pvt. Ltd., Ahmedabad, India; Model : SSE = 25; L/D = 25). The processing temperature was maintained at 150, 200, 210, 220, and 210°C for the feed zone, the metering zone, the compression zone, the adaptor zone, and the die head, respectively. In typical experiment, 90 wt% of PMMA, 5 wt% nanoclay, and 5 wt% PMMA-g-MA were fed into the extruder and the obtained extrudate was quenched in water at room temperature. The extrusion process was repeated twice for better dispersion of nanoclay in polymer matrix. Subsequently, the extrudate was cut into pellets and then oven-dried before being compression molded (Make: Saumya Technocrates, Ahmedabad, India; Model: HYPR-25T semi-automatic compression molding machine). The temperature was maintained at 220 and 200°C for lower and upper plate, respectively, to make specimens for rheological testing. The nanocomposite prepared with 5 wt% nanoclay and 5 wt.% PMMA-g-MA is denoted as PMMA-5-G, while the nanocomposite prepared with 5 wt% nanoclay (without PMMA-g-MA) is referred as PMMA-5. The composition of the nanocomposites is listed in Table .
Table 1 Composition table for PMMA and its nanocomposites
Measurements
Dynamic mechanical properties of the composites were determined on a TA Instrument (Q-800) New Castle, DE, USA. The temperature dependence frequency was taken as 1 Hz in the temperature range of 25–150°C with a heating rate of 3 C/min. The optical test for nanocomposite samples was performed according to ASTM D 1003 on spherical haze-meter instrument. The PMMA nanocomposite specimen with dimension of 125 × 12.7 × 3.2 mm was employed for flammability test in accordance with ASTM D 635 method. The gauge length was maintained constant (25 mm). The samples were kept horizontally to perform test, and average rate of burning was mentioned in mm/min.
The rheological properties of pure PMMA and PMMA/nanoclay nanocomposites were measured by Anton Paar MCR 101 in an oscillation mode with parallel-plate geometry using 25-mm-diameter disk at 200°C. Samples with 1 mm thickness were prepared by compression molding at 220 C and 40 kg/cm2 pressure. Rheological measurements were also made at various temperatures ranging from 160 to 200 C, in order to investigate the temperature dependence of the rheological properties.
Results and discussion
Dynamic mechanical analysis
The investigation of storage modulus (E′), loss modulus (E″), and tan δ by DMA are very beneficial in determining the performance of a sample under stress at various temperatures. The storage modulus (E′) and tan δ versus temperature for PMMA and its nanocomposites measured from 25 to 150°C are illustrated in Fig. a and b. For all the samples, a decrease in storage modulus (E’) is observed as the temperature increases. It is seen that at above 70°C, the storage modulus decreases sharply with an increase in the temperature. This indicates that the material undergoes a glass/rubber transition state. It is also noticed that the incorporation of nanoclay into the polymer matrix leads to a considerable increase in the storage modulus of PMMA nanocomposites over pure PMMA. This improvement is in agreement with the modulus data obtained from the static mechanical test, as discussed in our earlier publication.Citation32 The raise in the storage modulus is due to reinforcing effect of nanoclay and interfacial interaction between clay and polymer that restricts the mobility of polymer chains at polymer–clay interface and high modulus of clay.
The effect of PMMA-g-MA and nanoclay on the damping factor (tan δ) for the PMMA nanocomposites is displayed in Fig. b. The tan δ graph exhibits the presence of a single glass transition peak around 120°C. According to Chow et al.Citation33, the Tg is associated with the breakage of hydrogen bonds between the polymer chains that induces long-range segmental motion in amorphous region. A hump is appeared in the PMMA-5-G sample, which is related to those segmental anhydride groups that do not contribute in hydrogen bonding. It is observed from the figure that for PMMA-5, tan δ peak shifts toward higher transition temperature due to restricted segmental motions of PMMA in the clay–polymer interface. The compatibilizer, PMMA-g-MA, provides enhanced interfacial bonding between clay and polymer; as a result, further increase in Tg is observed for PMMA-5-G sample that is confirmed by the rightward shift of tan δ peak.
Rheological properties
At fixed temperature (200°C)
Rheological analysis of polymer composites is an efficient method to predict the processing behavior and microstructure of composites (distribution and concentration of filler as well as adhesion between filler and polymer matrix). Many polymer composites showed transition in rheological behavior from liquid-like to pseudo-solid-like or solid-like with increasing filler concentration.Citation28,30 This transition concentration is called the rheological percolation threshold. The frequency dependence of the storage modulus (G′) and loss modulus (G″) versus frequency (ω) measured at 200 C for PMMA and its nanocomposites are shown in (Fig. a and b). The frequency dependence of storage modulus (G’) for the PMMA nanocomposites containing nanoclay demonstrates the normal response of a conventional thermoplastic polymer with a liquid-like behavior at lowest frequency i.e. below 0.1. It is clear from the graph (Fig. a) that pure PMMA along with PMMA-5 and PMMA-5-G shows similar trend at lower frequency region; however, the modulus of nanocomposite samples is higher compared to pure PMMA. As the frequency increases, the storage modulus is also enhanced and is less dependent on the frequency. This entire phenomenon indicates the behavior from a liquid-like to a solid-like viscoelastic i.e. rheological percolation threshold and the formation of nanoclay–polymer chain network. The appearance of rheological percolation threshold of PMMA-5 can be attributed to the formation of continuous network of nanoclay and polymer chains. However, in the case of PMMA-5-G sample, formation of interfacial bond between the anhydride groups of PMMA-g-MA and amino groups in nanoclay can entangle with polymer chains of matrix to form a continuous polymer–nanofiller network. From the loss modulus graph (Fig. b), it is observed that at lower frequency, PMMA nanocomposites show higher loss modulus with respect to pure PMMA. This indicates that nanoclay has pronounced effect on it. At higher frequency, it is noticed that long-time relaxation for all the samples have perturbed and network formation takes place due to polymer–filler and filler–filler interaction. It is also noticed that the direction of clay platelets also aligned toward shear direction; therefore, all the compositions demonstrate similar trend at higher angular frequency as nanoclay and PMMA-g-MA have less effect. Similar type of results is also reported by Zhang et al.Citation34 for graphene-based PMMA composites.
Figure 2 (a) Storage modulus and (b) loss modulus of pure PMMA, PMMA-5, and PMMA-5-G nanocomposites at 200°C
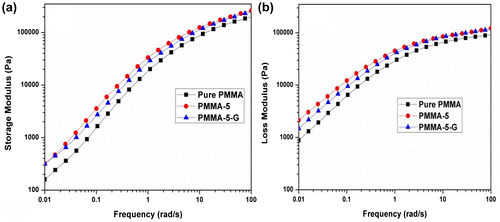
The complex viscosity of the polymer melts can be easily understood by the shear thinning phenomenon. This states that polymer melts are non-Newtonian fluids and their viscosity decreases with an increase in shear rate and this behavior is considered the most important property in polymer processing. The complex viscosity versus frequency (ω) of pure PMMA, PMMA-5, and PMMA-5-G analyzed at 200°C is displayed in Fig. a. The graph shows that PMMA nanocomposites (PMMA-5 and PMMA-5-G) have a higher viscosity at lower frequency in comparison with pure PMMA. At lower frequency, the entanglement of polymer chains hinders shear flow, and therefore, viscosity is high. As the frequency increases, the chains begin to orient in the flow direction and disentangle from one another, the viscosity reduces. Finally, the molecules become fully oriented in the flow direction at very high frequency. At this point, stable entanglements are no longer possible and the viscosity reaches a low level that is again independent of shear strain rate.
Figure 3 (a) Complex viscosity and (b) tan δ of pure PMMA, PMMA-5, and PMMA-5-G nanocomposites at 200°C
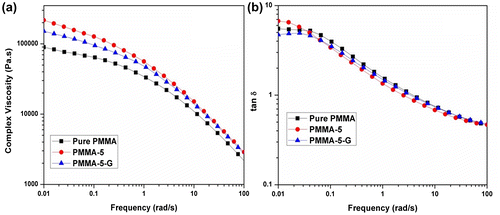
The tan δ of PMMA and its nanocomposites is shown in Fig. b. The ratio of loss modulus to storage modulus is defined as tan δ. The plot shows a slight increase in tan δ and then a major drop as the frequency increases. The physical entanglements of polymer chains with the addition of nanoclay particles cause the formation of some network structures among the nanoclay particles and polymer chains and also among nanoclay particles themselves. The rigid structure of nanoclay particles inhibits the viscous behavior and facilitates the transition from viscous to elastic behavior. Once the network is formed, no further change in loss factor is observed with an increase in frequency. The decrease in loss factor values in the high-frequency region is attributed to the partial orientation of polymer chains and nanoclays as result of deformation. Majid et al.Citation35 also found similar type of reduction in the damping factor for PP/ZnO nanocomposites.
In order to predict the storage modulus, one of the simplest equations for the reinforcement of a material due to an inclusion was given by EinsteinCitation36
(1)
where G is the storage modulus, subscripts c and m represent composite and matrix, respectively. Vf is the volume fraction of the nanoparticles inclusions.
Another equation proposed by Einstein was
(2)
where the terms are same as discussed above. A modification of Einstein’s equation was done by GuthCitation37 and the proposed equation was
(3)
Generally, rigid fillers decrease the damping as expressed by mechanical loss factor (tan δ) to an extent predicted by a rule of mixtureCitation38
(4)
In the case of rigid inclusions, the first term can be ignored and the equation becomesCitation39(5)
where the subscripts c and m denote composite and matrix, Vm is the volume fraction of the matrix. This equation must have some stiffness parameters because it is assumed that the matrix in the presence of fillers offers a stiffness equivalent to the minimum elastic modulus of the composite; then, above equation was modified asCitation40
(6)
where G is the storage modulus of the material.
The graphs of experimental and theoretical storage moduli values at 200°C for PMMA and its nanocomposites are shown in Fig. a. The storage modulus evaluated using Einstein equations (Equation1(1) ) and (Equation2
(2) ) shows more deviation from the experimental values. This can be attributed to the fact that nanoclay particles do not have good compatibility with matrix; however, the nanofiller particles could compensate due to increase in the surface area at the interface region. The storage modulus predicted using Guth model equation (Equation3
(3) ) has better agreement with experimental value of PMMA-5 nanocomposite, while the Einstein [equation (Equation2
(2) )] is deviated most. Karamipour et al.Citation41 have obtained similar results for PP/CaCO3 nanocomposites.
Figure 4 Plots of experimental and theoretical storage modulus (a) and loss factor (b) of pure PMMA, PMMA-5, and PMMA-5-G nanocomposites at 200°C
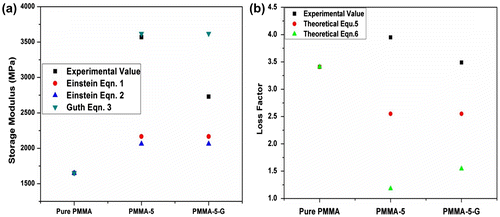
The experimental and theoretical loss factor (tan δ) values of all the samples are presented in Fig. b. It can be observed from the graph that loss factor obtained using both the equations (equations Equation5(6) and Equation6
(5) ) shows deviation from the experimental value. The deviations shown by the models from the experimental data may be due to the fact that localized constraints are insisted by nanoclay on deformed PMMA matrix, which is ignored by both equations. Moreover, the influence of the presence of nanoclay on thermal property of PMMA has not been considered by these equations. Similar findings were also noticed by Nielsen and Landel.Citation38
At different temperature (160–200 C)
Fig. a and b displays the storage modulus and loss modulus against different temperatures (160–200°C). The plot demonstrates that nanoclay and compatibilizer have marked effect on the storage modulus of PMMA nanocomposites. At lower temperature, the polymer chains are very close to each other; thus, it is assumed that the polymer chains are fully relaxed. As the temperature increases, the storage modulus of PMMA-5 also enhances up to 170°C, while for pure PMMA, it is around 165°C. However, in the case of PMMA-5-G, formation of interfacial bond between the anhydride groups of PMMA-g-MA and hydroxyl groups present in the nanoclay leads to the high storage modulus in comparison with PMMA-5. The entanglement of nanoclay with polymer chains of matrix to form a continuous polymer–nanofiller network results in higher storage modulus. At higher temperature, the polymer chains start moving apart from each other, which result in the reduction of moduli. Loss modulus has also similar reasons what we have discussed for storage modulus. Kashiwagi et al.Citation18 have observed similar findings with polystyrene nanocomposites containing Cloisite and carbon nanotubes as filler.
The complex viscosity of PMMA and its nanocomposites measured at various temperatures is depicted in Fig. . The trend of complex viscosity with temperature is also similar to moduli. It is clear from the graph that with the addition of nanoclay and compatibilizer (PMMA-g-MA), both nanocomposites exhibit appreciable enhancement in complex viscosity in comparison with pure PMMA. As the temperature increases, the polymer chains started separating from each other, and therefore, viscosity reduces. It is also noticed from the Figure that for PMMA-5-G, compatibilizing agent, i.e. PMMA-g-MA, improves the bonding between the polymer matrix and nanoclay, which results in higher complex viscosity than PMMA-5 as well as pure PMMA.
Optical test
The optical test was carried out in order to study transmission of light through the sample. The effect of nanoclay and compatibilizer, PMMA-g-MA, on the transmittance of PMMA nanocomposites was studied, and results are reported in Table . It is found that pure PMMA shows the transmittance around 67.3%. The PMMA-5 nanocomposite exhibits 35% lower transmittance of light with respect to pure PMMA. This clearly indicates that addition of nanoclay in the PMMA matrix hinders the transmittance of light. In addition, staged layers of nanoclay may also occur, which reduces the emission of light. However, with PMMA-5-G nanocomposite, the compatibilizer (PMMA-g-MA) improves the bonding between nanoclay and polymer matrix that results in better dispersion of clay particles. As a result, the transparency is more as compared to PMMA-5 sample.
Table 2 Optical clarity and rate of burning of pure PMMA, PMMA-5, and PMMA-5-G nanocomposites
Flammability test
The horizontal flammability analysis was performed to characterize the rate of burning of PMMA with the addition of organically modified nanoclay, and the results are presented in Table . The pure PMMA demonstrates a rate of burning of 65 mm/min with melting and dripping characteristics. However, in the PMMA nanocomposite samples, the rate of burning is decreased considerably demonstrating that nanoclay acts as a barrier in protecting the polymer matrix. The PMMA-5 nanocomposite shows lowest rate of burning (41 mm/min) in comparison with PMMA-5-G as well as pure PMMA, which is probably due to the formation of silica-rich char that inhibits the out dispersion of the volatile decomposition products. This reduction is often observed in intercalated or partly exfoliated clay platelets in polymer/nanoclay systems.Citation42 The PMMA-5-G nanocomposite also displays almost similar rate of burning as PMMA-5 sample suggesting that compatibilizer has no effect on the flammability. It is apparent that in this work, PMMA-5 nanocomposite sample displays around 37% reduction in the burning rate when compared to pure PMMA sample. In the work of Mohanty et al.Citation40, PMMA/B109 nanocomposite exhibited about 36% reduction in the burning rate over neat PMMA.
Zhu et al.Citation43 reported that development of char acts as barrier to degradation products and as a heat insulation layer, a catalytic charring action of the strongly acidic proton sites created in the silicate by the thermal degradation of the organic modifier, and radical trapping by paramagnetic iron within the clay. The intercalation of PMMA matrix into clay galleries results in decreased rate of burning. The other mechanism proposed by Zannetti et al.Citation44 indicates that the clay serves as a char promoter by slowing down the degradation and providing a transient protective barrier to the nanocomposites.
Conclusions
The influence of compatibilizer (PMMA-g-MA) and clay on the rheological properties of PMMA/clay nanocomposites, including storage and loss moduli, and complex viscosity was investigated. It was found that storage and loss modulus increased as the frequency increases and it was less dependent at higher frequency for a fixed temperature. The complex viscosity of different PMMA nanocomposites (with and without compatibilizer) decreased under varied frequency at 200°C. However, for different temperature range analysis (160–200 C), the polymer chains started separating from each other with an increase in the temperature and polymer–nanoclay network no more exists; therefore, both the moduli and complex viscosity reduced. It was also observed that the rheological properties of PMMA-5-G nanocomposite are better with respect to other samples at different temperatures. The optical clarity of PMMA-5-G nanocomposite was 7% higher as compared to PMMA-5 nanocomposite. From the flammability analysis, it was confirmed that PMMA-5 nanocomposite has ~37% higher fire retardancy in comparison with pure PMMA.
Disclosure statement
No potential conflict of interest was reported by the authors.
References
- P. B. Messersmith and E. P. Giannelis: Synthesis and barrier properties of poly(1-caprolactone)-layered silicate nanocomposites, J. Polym. Sci. Part A: Polym. Chem., 1995, 33, 1047–1057.
- P. C. LeBaron, Z. Wang and T. J. Pinnavaia: Polymer-layered silicate nanocomposites: An overview, Appl. Clay. Sci., 1999, 15, 11–29.
- J. W. Gilman: Flammability and thermal stability studies of polymer-layered silicate (clay) nanocomposites, Appl. Clay. Sci., 1999, 15, 31–49.
- J. Ma, Z. Qi and Y. Hu: Synthesis and characterization of polypropylene/clay nanocomposite, J. Appl. Polym. Sci., 2001, 82, 3611–3617.
- P. Kwizera, M. S. Dresselhaus and D. R. Uhlmann: The microstructure of intercalated graphite fibres, Carbon, 1982, 20, 387–394.
- M. Joshi, B. S. Butola, G. Simon and N. Kukaleva: Rheological and viscoelastic behavior of HDPE/Octamethyl-POSS nanocomposites, Macromolecules, 2006, 39, 1839–1849.
- W. Zhang, J. Suhr and N. Koratkar: Carbon/nanotubes/polycarbonate composites as multifunctional strain sensors, J. Nanosci. Nanotechnol., 2006, 6, 960–964.
- K. E. Strawhecker and E. Manias: Structure and properties of poly(vinyl alcohol)/Na+montmorillonite nanocomposite, Chem. Mater., 2000, 12, 2943–2949.
- K. R. Ratinac, R. G. Gilbert, L. Ye, A. S. Jones and S. P. Ringer: The effects of processing and organoclay properties on the structure of poly(methyl methacrylate)-clay nanocomposites, Polymer, 2006, 47, 6337–6361.
- S. V. Krishna and G. Pugazhenthi: Structural and thermal properties of polystyrene (PS)/Co-Al layered double hydroxide (LDH) nanocomposites prepared via solvent blending: Effect of LDH loading, J. Exp. Nanosci., 2013, 8, 19–31.
- A. B. Morgan and J. W. Gilman: Characterization of polymer-layered silicate (clay) nanocomposites by transmission electron microscopy and X-ray diffraction: A comparative study, J. Appl. Polym. Sci., 2003, 87, 1329–1338.
- S. V. Krishna and G. Pugazhenthi: Influence of processing conditions on the properties of polystyrene (PS)/organomontmorillonite (OMMT) nanocomposites prepared via solvent blending method, Int. J. Polymer. Mater., 2011, 60, 144–162.
- A. A. Tager, V. D. Krasyuk, V. Y. Dreval, A. I. Suvorova, L. K. Sidorova and M. S. Kotov: Dielectric and rheological properties of solutions of polymethylmethylacrylate in good and poor solvents, Polym. Sci. USSR, 1973, 15, 1961–1968.
- N. Moussaif and R. Jérôme: Compatibilization of immiscible polymer blends (PV/PVDF) by the addition of a third polymer (PMMA): Analysis of phase morphology and mechanical properties, Polymer, 1990, 40, 3919–3932.
- D. F. Farrar and J. Rose: Rheological properties of PMMA bone cements during curing, Biomaterials, 2001, 22, 3005–3013.
- S. Ahmad and S. A. Agnihotry: Nanocomposite electrolytes with fumed silica in poly(methyl methacrylate): Thermal, rheological and conductivity studies, J. Power Sources, 2005, 140, 151–156.
- M. Kogan, C. J. Dibble, R. E. Rogers and M. J. Solomon: Viscous solvent colloidal system for direct visualization of suspension structure, dynamics and rheology, J. Colloid Interface Sci., 2008, 318, 252–263.
- T. Kashiwagi, M. Mu, K. Winey, B. Cipriano, S. R. Raghavan, S. Pack, M. Rafailovich, Y. Yang, J. Shields, R. Harris and J. Douglas: Relation between the viscoelastic and flammability properties of polymer nanocomposites, Polymer, 2008, 49, 4358–4368.
- C. C. Teng, C. C. M. Ma, Y. W. Huang, S. M. Yuen, C. C. Weng, C. H. Chen and S. F. Su: Effect of MWCNT content on rheological and dynamic mechanical properties of multiwalled carbon nanotubes/polypropylene composites, Composites Part A, 2008, 39, 1869–1875.
- S. Li, M. Xiao, D. Wei, H. Xiao, F. Hu and A. Zheng: The melt grafting and rheological characterization of long chain branching polypropylene, Polymer, 2009, 50, 6121–6128.
- I. Ivanov, S. Muke, N. Kao and S. N. Bhattacharya: Morphological and rheological study of polypropylene blends with a commercial modifier based on hydrogenated oligo (cyclopentadiene), Polymer, 2011, 42, 9809–9817.
- Y. T. Lim and O. O. Park: Phase morphology and rheological behavior of polymer/layered silicate nanocomposites, Rheol. Acta, 2001, 40, 220–229.
- M. Moniruzzaman and K. I. Winey: Polymer nanocomposites containing carbon nanotubes, Macromolecules, 2006, 39, 5194–5205.
- K. Chrissopoulou and S. H. Anastasiadis: Polymer/layered silicate nanocomposites with functional compatibilizers, Eur. Polym. J., 2011, 47, 600–613.
- M. Abdel-Goad, P. Potschke, D. Zhou, J. E. Marck and G. Heinrich: Preparation and rheological characterization of polymer nanocomposites based on expanded graphite, J. Macromol. Sci., Pure Appl. Chem., 2007, 44, 591–598.
- D. Chopra, M. Kontopoulou, D. Vlassopoulos and S. G. Hatzikiriakos: Effect of maleic anhydride content on the rheology and phase behaviour of poly(styrene-co-maleic anhydride)/poly(methyl methacrylate) blends, Rheol. Acta, 2002, 41, 10–24.
- P. Song, Y. Yu, T. Zhang, S. Fu, Z. Fang and Q. Wu: Permeability, viscoelasticity, and flammability performances and their relationship to polymer nanocomposites, Ind. Eng. Chem. Res., 2012, 51, 7255–7263.
- S. S. Ray, P. Maiti, M. Okamoto, K. Yamada and K. Ueda: New polylactide/layered silicate nanocomposites. 1. Preparation, characterization, and properties, Macromolecules, 2002, 35, 3104–3110.
- X. He, J. Yang, L. Zhu, B. Wang, G. Sun, P. Lv, I. Y. Phang and T. Liu: Morphology and melt rheology of nylon11/clay nanocomposites, J. Appl. Polym. Sci., 2006, 102, 542–549.
- R. Krishnamoorti, R. A. Vaia and E. P. Giannelis: Structure and dynamics of polymer-layered silicate nanocomposites, Chem. Mater., 1996, 8, 1728–1734.
- K. Kakati, G. Pugazhenthi and P. K. Iyer: Effect of organomodified Ni-Al layered double hydroxide (OLDH) on the properties of polypropylene (PP)/LDH nanocomposites, Int. J. Polym. Mater., 2012, 61, 931–948.
- M. Kumar, V. Kumar, P. Upadhaya and G. Pugazhenthi: Fabrication of poly(methyl methacrylate) (PMMA) nanocomposites with modified nanoclay by melt intercalation, Compos. Interfaces, 2014, 21, 819–832.
- W. S. Chow, A. A. Bakar, Z. A. M. Ishak, J. K. Kocsis and U. S. Ishaiku: Effect of maleic anhydride-grafted ethylene-propylene rubber on the mechanical, rheological and morphological properties of organoclay reinforced polyamide 6/polypropylene nanocomposites, Eur. Polym. J., 2005, 41, 687–696.
- H. B. Zhang, W. G. Zheng, Q. Yan, Z. G. Jiang and Z. Z. Yu: The effect of surface chemistry of graphene on rheological and electrical properties of polymethylmethacrylate composites, Carbon, 2012, 50, 5117–5125.
- M. Majid, E. D. Hassan, A. Davoud and M. Saman: A study on the effect of nano-ZnO on rheological and dynamic mechanical properties of polypropylene: Experiments and models, Composites Part B, 2011, 42, 2038–2046.
- A. Einstein: ‘A investigation on the theory of brownian movement’, 1st edn, 1956, New York, NY, Dover.
- E. Guth: Theory of filler reinforcement, J. Appl. Phys., 1945, 16, 20–25.
- L. E. Nielsen and F. L. Landel: ‘Mechanical properties of polymers and composites’, 2nd edn, 1993, New York, NY, Marck Dekker.
- L. T. Drzal, M. J. Rich and P. F. Lioyd: Adhesion of graphite fibers to epoxy matrices: I The role of fiber surface treatment, Adhesion, 1983, 16, 133–140.
- C. M. Tung and P. J. Dynes: Morphological characterization of polyetheretherketone-carbon fiber composites, J. Appl. Polym. Sci., 1987, 33, 505–516.
- S. Karamipour, H. Ebadi-Dehaghani, D. Ashouri and S. Mousavian: Effect of nano CaCO3 on rheological and dynamic mechanical properties of polypropylene: Experiments and models, Polym. Test., 2010, 30, 110–117.
- S. Mohanty and S. K. Nayak: Effect of organo-modified silicates on the properties of poly(methyl methyacryalte) nanocomposites, J. Thermoplast. Compos. Mater., 2010, 23, 623–645.
- J. Zhu, F. M. Uhl, A. B. Morgan and C. A. Wilkie: Studies on the mechanism by which the formation of nanocomposites enhances thermal stability, Chem. Mater., 2001, 13, 4649–4654.
- M. Zannetti, G. Canuino, P. Reichert and R. Mulhaupt: Thermal behaviour of poly (propylene) layered silicate nanocomposites, Macromol. Rapid Commun., 2001, 22, 176–180.