Abstract
With the rapid development of artificial intelligence and ever-increasing demand for electronic devices, constructing high-performance flexible pressure sensors is urgently needed. In this study, a novel flexible pressure sensor with superhigh sensitivity and ultrawide detection range is tactfully designed and prepared based on wrinkle-structured MXene film. Due to the unique wrinkle structure, the prepared pressure sensor exhibits outstanding performance including high sensitivity of nearly 860 kPa−1, wide detection range (0.5 Pa ‒ 30 kPa), short response/recover time (40/53 ms) and high stability (11600 cycles). A multi-scale working mechanism is proposed to explain the sensing process. Interestingly, the prepared sensor can easily detect the smallest movement of a millet (2.4 mg) in real time. Based on these advantages, the prepared pressure sensor is expected to show significant potentials in future physiological detection and precision instrument monitoring systems.
Graphical Abstract
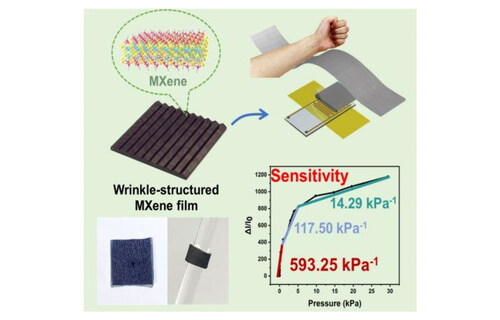
1. Introduction
In recent years, the rapid advancement of flexible electronics has brought a high demand for pressure sensors that can be used in the field of information collection and information conversion [Citation1]. However, due to the requirement of flexibility, the performance of sensitivity and pressure range of the sensors will always be unsatisfactory. Even for traditional pressure sensors, it is hard to simultaneously realize high sensitivity and wide pressure range. Constructing flexible pressure sensors with high sensitivity and a wide pressure range remains a big challenge. For pressure sensors, the sensing components are the key part of sensing. Therefore, it is necessary to improve the performance of these components to meet the high requirements of sensing. To date, the most used method to achieve target requirements of pressure sensing devices is a rational combination of material selection and structural design [Citation2].
Nowadays, a large number of conductive nano-materials have been used as pressure sensors’ sensitive components. According to their material morphology, these materials can be divided into: zero-dimensional (0 D) materials (e.g. metal nanoparticles [Citation3–5], graphene nanocrystals [Citation6], one-dimensional (1 D) materials (e.g. metal nanowires [Citation7], polymer nanofibers, nanorods [Citation8–10], carbon nanotubes [Citation11–14], two-dimensional (2 D) materials (e.g. graphene and its derivatives [Citation15–18], MXene [Citation19] and multi-dimensional conductive composite materials [Citation20–24]. Among them, MXene, a series of 2 D transition metal carbides and nitrides, has drawing ever-increasing attention in recent years due to its excellent electrical conductivity, abundant hydrophilic groups, and tunable systesis [Citation25]. Under the action of external force, the distance between the sheets of MXene will largely change, which is the basic working mechanism for MXene-based pressure sensors [Citation26]. By integrating MXene into other materials, flexible, stretchable, highly sensitive pressure sensors have been fabricated [Citation27–29].
By combining and integrating multiple sensing components together into a single device can promote device performance to some extent, although the complexity of manufacturing and inspection processes will inevitably increased. Moreover, it is often difficult to reach the performance limits of a single substance component when multiple substances are mixed. The introduction of specific microstructures onto the surface of a single sensing material in order to achieve both a high sensitivity and wide detection range seems an interesting strategy attracted lots of interests recently [Citation30, Citation31]. So far, the main structure-molding strategies include the template method and substrate shrinkage method. For the template method, the micro-structure of fabrics [Citation21, Citation32, Citation33], nanofiber membranes [Citation9] or bionic components are selected as templates [Citation34, Citation35], to produce the conductive materials which have the micro-structure of those. In the substrates shrinkage method, the substrates are prestretched either through [Citation36, Citation37] are prestretched either through the effects of temperature [Citation19] and solvent [Citation38] and the substrate will shrink according to various factors. Hence, the obtained microstructure morphology can be controlled by tuning the corresponding shrinkage factors. For example, Jia et al. fabricated a graphene-based pressure sensor with skin-like continuous-gradient wrinkles by deformations via a pre-stretched elastomer [Citation39]. Compared to the template transfer method, the substrate shrinkage method offers a tunable strategy for the microstructural design of the sensitive components. Therefore, this method is more conducive to meet the high requirements of flexible pressure sensors in different working conditions circumstances.
In the present work, we developed a simple and universal strategy to fabricate a high-performance flexible pressure sensor based on a pristine wrinkle-structured MXene film. The wrinkle-structured MXene film was prepared by depositing the single-layer MXene sheets on a pre-stretched substrate. This simple preparation strategy makes it possible for pure MXene to be used in flexible electronic devices for large-scale preparation. Benefiting from the unique wrinkle structure, the prepared pressure sensor exhibits outstanding performance including high sensitivity of nearly 860 kPa−1, wide detection range (0.5 Pa ‒ 30 kPa), short response/recover time (40/53 ms) and high stability (11 600 cycles). Moreover, the obtained flexible sensor is easy to attach to the surface of objects for real-time monitoring of object motion and human health. Based on its excellent performances, the prepared flexible wrinkle-structured MXene film-based pressure sensor is expected to show great potentials in future human function monitoring, artificial intelligence devices, soft robots, instrumentation vibration monitoring and so on.
2. Experimental section
2.1. Synthesis of MXene dispersion
MXene (Ti3C2Tx) nanosheets were synthesized by the wet chemical method. Briefly, 1.9 g LiF (Aladdin, 99.9%) was first added to 40 mL of 9 M HCl (Beijing Chemical Works, 36–38%), then magnetically stirred in an ice bath for 5 min. Subsequently, 1.85 g of Ti3AlC2 phase powder (Ningbo Jinlei Technology Corporation, 200 mesh, 95%) was gradually added to the above solution within 15 min in the ice bath. The MAX phase was etched at 38 °C for 24 h. Finally, the reacted product was washed 6–7 times by centrifugation (3500 rpm) until the supernatant in centrifuge tube was acquired with pH ≥ 6. The washed clay-like multilayer Ti3C2 precipitated product was placed in a flask, and deionized water was added and shaken by hand for 10 min. Then the dispersion was frozen at −6 °C and thawed at room temperature, this process was repeated 5 times. The thawed dispersion was shaken by hand for 30 min and sonicated in a low temperature water bath for 1 h, subsequently by centrifuging at 3500 rpm for 1 h. Lastly, the dark green stable solution was obtained as an MXene dispersion. The concentration of Ti3C2Tx dispersion, which is 14.7 mg mL−1, was measured by filtering a certain volume of the solution and then weighing the obtained MXene film.
2.2. Preparation of wrinkle-structured MXene film
Commercial VHB tape (3 M Company, 3 M 4910), a highly stretchable double-sided adhesive acrylic tape, was firstly cut into pieces with appropriate size, and pre-stretched and fixed at different strains (50%, 100%, and 200%) by metal frame (3 cm × 12 cm). Then, MXene film was obtained by dropping the 3.5 mg mL−1 MXene nanosheets dispersion (5 mL) onto the surface of the VHB tape. After releasing the pre-stretched VHB, an MXene film with a wrinkle structure was obtained.
2.3. Assembling of wrinkle-structured MXene film-based pressure sensor
The wrinkle-structured MXene-based pressure sensor was assembled by attaching the MXene film to an interdigital electrode. Specifically, the as-prepared wrinkle-structured MXene film was cut to a suitable size as a sensing electrode and placed on the interdigital electrode. The two electrodes were fixed with a flexible PE film. A flexible PI tape was applied as a substrate to prevent additional short circuits. The medical non-woven tape was used to fix each part of the entire sensor, and it was also used to attach the sensor to the human body for physiological signal detection.
2.4. Characterization and measurement
The contact angle of the VHB substrate and different solutions were measured by Dataphysics OCA40. The shape, structure, and constituent of the MXene were studied by transmission electron microscope (TEM, FEI Tecnai F30), x-ray powder diffraction (XRD, UItima IV with Cu Kα-radiation), x-ray photoelectron spectroscopy (XPS, Thermo ESCALAB 250XI), confocal microscopic Raman spectrometer (Renishaw inVia-Reflex, 514 nm, 100 − 1000 cm−1). The thickness of the MXene was measured by atomic force microscope (AFM, BRUKER Dimension Edge). The morphology and structure of the pristine MXene film and wrinkle-structured MXene film were measured by scanning electron microscope (SEM, Hitachi microscope S-4800, acceleration voltage of 20 kV). To test the sensing performance of the wrinkle-structured MXene film-based pressure sensor under loading, a test system containing a stepper motor (used to test cyclic stability), an electrochemical workstation (CHI660E) was employed. The applied voltage was 1 V during the measurements.
3. Results and discussion
3.1. Preparation and characterization of wrinkle-structured MXene film
The preparation process of the wrinkle-structured MXene film-based pressure sensor is divided into three parts, as shown in . First, MXene dispersion was prepared by wet-chemical etching method [Citation40]. In Detail, multilayer-Ti3C2 dispersion was synthesized by etching the precursor MAX phases (Ti3AlC2) in HCl-LiF etchant, which could add abundant surface functionalities and etch off the Al element layer from the precursor materials. The MXene dispersion was obtained by delaminating the multilayer-Ti3C2 dispersion after the etching process followed by hand-shaking, freezing-thawing and ultrasonication [Citation41, Citation42], as displayed in . Then the wrinkle-structured MXene film was fabricated by depositing the MXene dispersion onto a pre-stretched 3 M Very High Bond (VHB) elastomeric double-sided adhesive tape. Herein, it should be pointed out that VHB substrate is a hydrophobic material, of which MXene dispersion cannot be directly attached to the substrate (). However, the addition of ethanol solution could promote the compatibility of the MXene dispersion with the VHB substrate. The MXene dispersion was dropped and deposited evenly on the pre-stretched substrate with a certain stretch ratio. After drying at room temperature, the pre-stretched state was released. Because of the difference in Young’s modulus of MXene and VHB, a continuous wrinkle microstructure was formed on the surface of the MXene film. The structural process is schematically displayed in f.
Figure 1. Schematic diagram showing the preparation of wrinkle-structured MXene film-based pressure sensor. (a-c) The preparation process of MXene dispersion. (d-f) The preparation process of wrinkle-structured MXene film. (g) Schematic diagram of flexible ultrasensitive pressure sensors based on the wrinkle-structured MXene film. (h) Photograph of the MXene film with a wrinkle microstructure. (i) The bending of the wrinkle-structured MXene film from glass rod (surrounds 360o). (j) Photograph of flexible ultrasensitive pressure sensors.
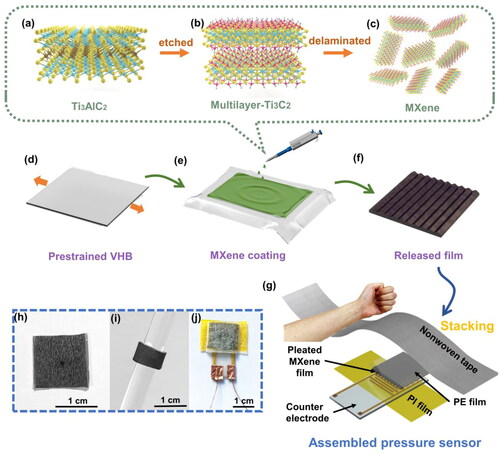
illustrates the assembly process of the wrinkle-structured MXene film-based pressure sensor. The pressure sensor possessed a typical sandwich structure, in which the wrinkle-structured MXene film was combined with a counter electrode, and flexible transparent polyethylene (PE) film and insulating polyimide (PI) tape were wrapped on the pleated film and electrode respectively. Finally, the pressure sensor was attached to a nonwoven tape for sensing detection, in which the wrinkle-structured MXene film is applied as the pressure ‐sensitive component. ,i present the photos of the film. It could be observed that the surface of the MXene film has a continuous stripe pattern. Besides, the film shows good flexibility and can be easily attached to the surface of a glass rod and wound at 360°.
A digital photo of the obtained wrinkle-structured MXene film-based pressure sensor is shown in .
illustrates the characterizations of the MXene dispersion and flexible MXene films. As shown in , the prepared MXene dispersion has a typical Tyndall effect, revealing that the dispersion is a colloidal solution. TEM image shows that the sliced layer size of the prepared MXene nanosheets is about 3.69 μm (). Besides, the thickness of the MXene nanosheets is approx. 1.8 nm according to AFM image (). presents the digital image and cross-sectional SEM image of the self-supporting film obtained by vacuum filtration of the MXene dispersion. The SEM image shows that the MXene self-supporting film is formed by layer-to-layer stacking of the MXene nanosheets, demonstrating that the etching and delamination process of MXene has a high degree of completion.
Figure 2. The characterizations of MXene dispersion and flexible MXene films. (a) Digital photograph of MXene dispersions. (b) TEM and (c) AFM images of MXene nanosheet. (d) Digital photo and cross-sectional SEM image of MXene filtration film. (e) SEM image of MXene film with wrinkle microstructure. (f,g) SEM image of the amplified top area of wrinkle microstructure.
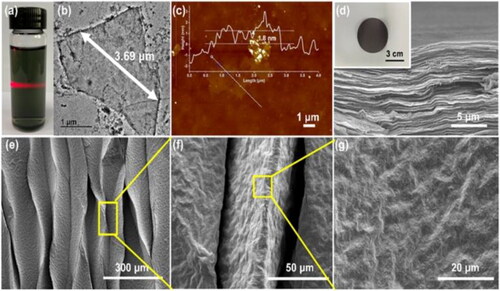
The successful fabrication of MXene was also confirmed by XRD, XPS and Raman data, as illustrated in . Compared with the XRD patterns of MAX phase and multilayer Ti3C2 etched for 24 h, the film of delaminated MXene only has an obvious (002) characteristic peak at 6.52°, demonstrating the good degree of delamination of MXene [Citation43]. XPS spectrum in shows that Ti, C, O and F elements are present in the obtained MXene. The undetected Al element also indicates that the Al from Ti3AlC2 were completely etched and washed away. The MXene nanosheet was further explored through Raman spectroscopy (). The adsorption peaks at ≈201 cm−1 and 724 cm−1 were attributed to the Ti − C and C − C vibrations of the oxygen‐terminated Ti3C2TX MXene, respectively. The peaks at 392 cm−1 and 574 cm−1 are assigned to the vibrations of O atoms (Eg and A1g, respectively) [Citation44]. According to the above results ( and ), it can be concluded that MXene is successfully obtained.
Since the features of MXene nanosheet is large and thin, it can fully reduce the surface cracks that may occur due to the small and thick nano-layer. As shown in , the wrinkle-structured MXene film has an obvious regular striped structure. The result is consistent with the graph of the wrinkle-structured MXene film (). The wrinkle-structured MXene film is continuous and stable, providing a good foundation for the sensor. ,g shows the amplified morphology of wrinkle structure at the tip area. The wrinkle-structured film has an obvious micro-bulge structure, which is caused by the character of the MXene nanosheet [Citation41]. The smooth micro-bulge secondary structure also endows the sensing layer with high sensitivity. According to the SEM images in ,g, it could be observed that no obvious cracks are present in the prepared wrinkle-structured MXene film, which guaranteed stability and a long working life of the resulting sensor.
According to the cross-sectional SEM images of the MXene film (), we can see that the surface structure is also undulating and serrated. Moreover, it can be seen that the cross-sectional structure of the MXene film attached to the VHB substrate () is similar to the structure of the MXene film from as obtained by vacuum filtration (). It indicates that depositing the MXene on the VHB substrate does not cause damage to the internal stacked structure of the MXene sheets. Moreover, elemental mapping analyses reveal that Ti, C, O, and F elements were evenly distributed in each layer of the pleated MXene film (). Consequently, in the process of preparing wrinkle-structured MXene film, MXene is uniformly deposited on the surface of the VHB substrate and the MXene substance itself is not damaged.
Figure 3. Evaluation of the electromechanical performances of the wrinkle-structured MXene film-based pressure sensor. (a) I–V curves of the pressure sensor under different applied pressures. (b-c) Plot of I–T curve at different pressures applied on the pressure sensor: (b) low pressure (0.49‒196 Pa), (c) high pressure (294 Pa‒9.8 kPa). (d) Detection performance under ultralow pressure of 4.9 Pa. The corresponding (e) response time and (f) recovery time of the pressure sensor. (g-h) Test of the repeatability performance of 11600 cycles under a pressure of 343 Pa.
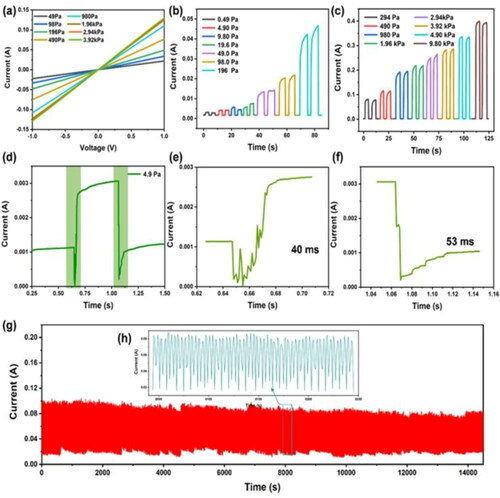
3.2. Pressure-sensing performance of the wrinkle-structured MXene film-based pressure sensor
The electromechanical performances of the wrinkle-structured MXene film-based pressure sensor were investigated. To evaluate the film’s characteristics in terms of pressure detection, we measured voltammetry characteristics of the sensor at different pressures, as shown in . The current-voltage (I–V) curves of the flexible sensor under different pressures (49 Pa ‒ 3.92 kPa) all exhibit a linear relationship, and the greater the pressure, the steeper slope of the curve. presents the real-time current response of the flexible sensor at the pressure range of 0.49 Pa to 9.8 kPa. Even in the low-pressure range, the output electrical signal of the sensor changes apparently (). Moreover, as the pressure increases, the sensor shows output different electrical signals of which their value increases accordingly, indicating that the sensor can distinguish a wide range of pressures. Moreover, the current intensity of the sensor remains unchanged under a certain pressure, demonstrating its stability and repeatability under different pressures. The above results demonstrate that the sensor can act as piezoresistive device.
To further evaluate the sensor’s ability to respond to a demanding working environment in practical applications, we measured the accurate sensing performance of sensor under an ultralow pressure of ∼5 Pa. In , obvious current could be detected, suggesting that the prepared sensor can detect an extremely low pressure of 5 Pa. Besides, the response and recovery time of the sensor when outside pressure was loaded and released was also recorded (). The corresponding time was 40 ms and 53 ms, respectively. The unique wrinkle structure of the MXene film provides the sensor with a fast response and recovery time. In addition, durability is another important parameter to evaluate device performance of pressure sensors. displays the sensor’s cycling stability and service life. It is shown that the sensor can maintain a relatively stable electrical signal output even after 11600 cycles. The result indicates that the sensor can maintain a high cycle stability during continuous operation and working conditions for an extended period of time.
3.3. Working mechanism of the pressure sensor
Sensitivity is an important parameter to evaluate the device performance of a pressure sensor, which is also an important basis for a sensing mechanism analysis. The sensitivity calculated by the ratio of current change to pressure change is represented as ‘S = δ(ΔI/I0)/δP’. Where ΔI is the change between the current under with and without loading, I0 is the current without loading, and P is the pressure applied on the sensor. show the sensitivity curves of the sensor, in which different sensitivity is observed under different applied pressure. In detail, the sensitivity can reach up to 860 kPa−1 under ultralow pressure stage of 0.5 Pa ‒ 0.5 kPa (Stage 1, ). Besides, the sensitivity begins to decrease to ∼130 kPa−1 when the applied pressure is in the range of 0.5 kPa ‒ 5 kPa (Stage 2, ). When the pressure continued to increase and reached to high pressure range of 5 kPa ‒ 30 kPa, the sensitivity is 15 kPa−1 (Stage 3, ). To the best of our knowledge, the high sensitivity (up to nearly 860 kPa−1) and large detection pressure range (0.5 Pa ‒ 30 kPa) of the present sensor is superior to most previously reported flexible MXene‐based pressure sensors [Citation21, Citation27–29, Citation33, Citation35, Citation45–49], as shown in and Table S1. AgNWs/MXene Aerogel [Citation27], Hollow MXene Sphere/rGO Aerogel [Citation29] and other materials are compared the sensitivity of my sensor. Obviously, our sensor has a wider detection range and has an ultra-high sensitivity in the micropressure range. Generally, when external pressure is applied to pressure sensors, the conductive material will deform and the contact area between the conductive material and counter electrode will increase [Citation15]. Consequently, more current pathways will be formed and a clear output signal by the sensor will be observed. As we know, MXene is a typical 2 D conductive nanomaterial, and its nanosheets are easily to stack together. When pressure is applied, deformation of the MXene nanosheets occurs and the gaps between the nanosheets decrease. Moreover, as the intensity of pressure continues to increase, the conductive nanosheets will begin to stack, thus forming a conductive percolation network, which will also increase the current [Citation26, Citation50].
Figure 4. Ultrasensitive device performance and working mechanism of the wrinkle-structured MXene film pressure sensor. Performance of the sensitivity in the pressure range of (a) 0.49 Pa‒0.49 kPa, (b) 0.49 kPa‒4.9 kPa and (c) 4.9 kPa‒29.4 kPa. Cross-sectional SEM images of the wrinkle-structured MXene film: (d) the continuous serrated structure, (e) the appearance of air gaps from the tip structure. (f) Model of MXene nanosheets used to derive the mechanism of the sensor under low pressure. (g) A single wrinkle model used to derive the mechanism of the sensor under high pressure.
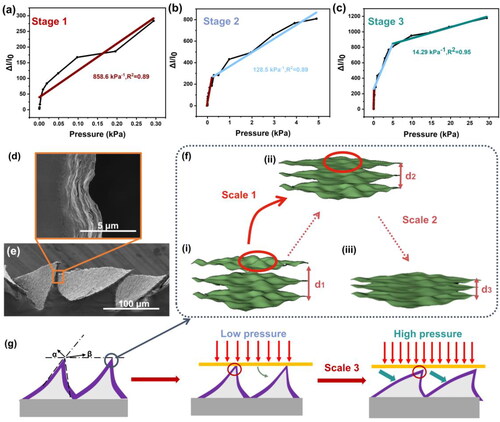
It is seen that the MXene sheets are stacked regularly layer-to-layer in the wrinkle-structured MXene film (), which will be used to analyze the working mechanism from a micromechanical perspective. Besides, the cross-sectional SEM image of the wrinkled MXene-VHB film () shows a regular serrated structure, which can provide more deformation space for the assembled sensor to adapt to large strains and compose the sensing mechanism of a macro perspective. According to the SEM data, we propose a simple model to explain the sensitivity characteristic of the wrinkle-structured MXene film-based pressure sensor, which is mainly attributed to a multi-scale mechanism ().
The Scale 1 sensing process originates from the microstructure change of the single MXene layer under applied pressure. When an ultra-low pressure is applied to the sensor, the micro-bulge structure of MXene film (as shown in ) will become the first pressure point. As the pressure increases, the dome-like structure is gradually compressed into a flat structure, leading to an increase of contact area between the sensing layer and the counter electrode, which in turn causes an increase of the electron flow path and the relative current (i,ii)). The Scale 2 sensing process takes place between the MXene nanosheets. When an external outside pressure is applied on the sensor, the layer gap between the MXene nanosheets will decrease. The gap between the layers is reduced, so that charge transfer between the MXene nano-sheets is increased (d1>d2>d3), thereby increasing the current flowing through the conductive layer, meaning that the output signal by the sensor is increased (i–iii)). Scale 3 is the macro-level sensing mechanism of the wrinkle structure on the MXene film surface. As the applied pressure on the sensor continues to increase, the gap between the MXene nanosheets is further reduced, until the MXene film is in full contact with the counter electrode.
On the other hand, as presented in , the cross-section structure of the wrinkle-structured film looks like some regular obtuse triangles. The force analysis shows that when a vertical downward pressure is applied, since f1 > f2, the film will actually receive a force F in the right direction (). This force can cause the triangle structure to topple over to one side, thus the contact area between the wrinkle-structured MXene film and the counter electrode will be increased. Meanwhile, the charge flow through the conductive layer will be further magnified, which is reflected by the signal value in real time. As a consequence, the sensor shows the highest sensitivity under ultralow pressure (). When the pressure continues to increase, the contact area between the MXene film and the interdigital counter gradually increases. The value of the signal decreases compared with the previous stage, so the sensitivity decreases accordingly (). Finally, the maximum limit of the sensor is reached when the MXene film is in full contact with the counter electrode (). The sensing process corresponds to the measured sensitivity change curves. In addition, by controlling the pre-stretching ratio, the structural distribution density of the wrinkle-structured MXene film can be easily changed. As shown in , when the pre-stretching ratio is 50%, 100%, and 200% respectively, the width of the microstructure trends to decrease, and the wrinkle structure accumulated on the film of the same area becomes denser. To further explore the influence of this structure on the sensing mechanism of the sensor, we assembled the sensor with the pleated film under different pre-stretching ratio and recorded the sensitivity curves (). When the pre-stretching ratio is 50%, the sensitivity is around 525 kPa−1. Interestingly, the sensitivity can reach up to 860 kPa−1, when the pre-stretching ratio is 100%. Meanwhile, a sensitivity of around 528 kPa−1 is obtained under the pre-stretch ratio of 200%. On the basic of the above results, it can be seen that the sensitivity of the sensor is closely related to the wrinkle structure. Within limits, the higher degree of pleated structure, the higher the sensitivity of the sensor. However, the sensitivity will decrease after the threshold of the pre-stretching ratio is reached. Besides, it should be pointed out that compared with a 100% pre-stretching ratio, the wrinkle-structured MXene film with 200% pre-stretching shows a higher sensitivity of ∼220 kPa−1 in the low pressure range ( vs. ). The reform, it is foreseeable that for different working conditions, the sensing properties of the wrinkle-structured MXene film-based pressure sensor can be adjusted by controlling the pre-stretching ratio of the VHB tape. It demonstrates the flexibility and simplicity of this strategy in adjusting the sensing performance of the wrinkle-structured MXene film.
Figure 6. The SEM image of the wrinkle-structured MXene film with different pre-stretching ratio. (a-b) 50%, (c-d) 100%, (e-f) 200%.
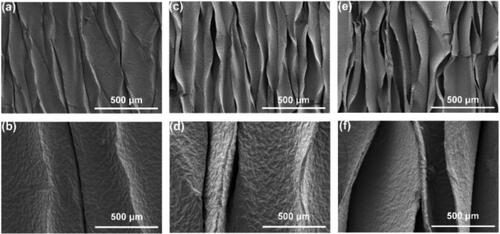
Figure 7. Performance of sensitivity in different pressure range of the wrinkle-structured MXene film with different pre-stretching ratio. (a-c) The wrinkle-structured film with 50% pre-stretching ratio: (a) the pressure range of 0.49 Pa‒0.49 kPa, (b) the pressure range of 0.49‒4.9 kPa, (c) the pressure range of 4.9‒29.4 kPa. (d-f) The wrinkle-structured film with 200% pre-stretching ratio:(d) the pressure range of 0.49 Pa‒0.49 kPa, (e) the pressure range of 0.49‒4.9 kPa, (f) the pressure range of 4.9‒29.4 kPa.
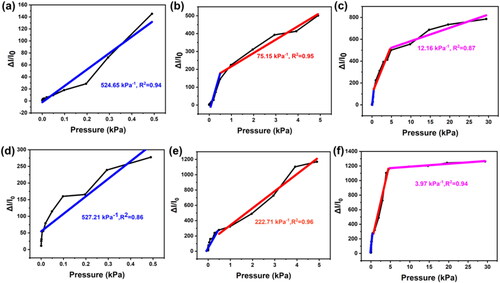
3.4. Applications of the wrinkle-structured MXene film-based pressure sensor
In view of the special surface microstructure and sensing characteristics of the prepared wrinkle-structured MXene film, we further explored its potentials for detecting special objects. As shown in , the prepared flexible pressure sensor can sensitively detect the stress signals of different small objects in daily life. The investigated objects include millet (2.4 mg), black rice (22.0 mg), red bean (141.4 mg), kidney beans (404.1 mg), small orange (49.9 g), and larger orange (276.1 g). The different output signals indicate that the sensor can be used to accurately detect different objects. According to the signals in , it is found that relatively stable electrical signals were detected even when tiny objects were placed on the sensor, the heavier the object, the more obvious the output signals. Interestingly, the output signal exhibited an arc shape when the surface of the object is smooth (), which was caused by the unstable contact of the investigated objects with the sensor. It indicates that the pressure sensor possesses the ability of detecting dynamic motion of the object, which shows potential in precision micro-instrument vibration monitoring.
Figure 8. Applications of the wrinkle-structured MXene film-based flexible pressure sensor for detecting various object motions, including small objects’ signals of (a) millet, (b) black rice, (c) red bean, (d) kidney bean and large objects’ signals of (e) small orange, (f) orange.
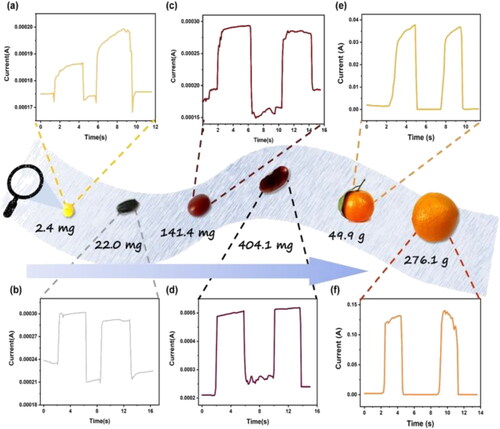
In addition, the sensing characteristics of the wrinkle-structured MXene film-based sensor enables it to be also used in medical devices such as a wearable sensor to detect human physical signs and health. To further investigate this, we attached the prepared pressure sensors to the human body for real-time monitoring of the movements of vocal cords, throat, carotid artery and cervical vertebra, as shown in . According to the degree of motion, the output sensing signals can be divided into small motion signals and large motion signals. For example, the sensor could detect the tiny vocal cords vibrating when a person makes a sound of ‘a’ (), indicating that the pressure sensors have potential in voice recognition and human-computer interaction. Meanwhile, by attaching the sensor to carotid artery, real-time monitoring of pulse fluctuation could also be realized (). As shown in , the periodic variation of pulse vibration can be clearly distinguished by the sensor. The pulse cycle was 0.8 s, demonstrating that the participants’ heart rate was 75 beats per minute (in the normal range). Significantly, the output results display that the carotid artery may vibrates in a large amplitude every four cycles. Based on this, the sensors are applicable to physiological signs record and disease diagnosis. Moreover, the sensor can also clearly recognize large motions of the human body. presents the recorded signals of a swallowing process when the sensor was pasted to the throat. This feature shows that the sensor can be potentially used for emotional state reconnaissance and monitoring devices such as lie detectors. Furthermore, the as-prepared flexible sensors can also detect the cervical activity (). The above results powerfully demonstrate that the prepared wrinkle-structured MXene film-based flexible pressure sensor can efficiently monitor human motions in real-time, which may hold significant potential for applications in the field of flexible wearable smart sensors.
4. Conclusions
In summary, we have established a simple, efficient and low-cost method to prepare a flexible wrinkle-structured MXene film and developed a novel MXene-based flexible pressure sensor. The study demonstrated that different levels of pre-stretching of the VHB substrate will produce corrugated structures with different sizes and densities, which significantly affect the sensitivity of the flexible pressure sensor. When the elastic VHB substrate is pre-stretched to 100%, the wrinkle-structured MXene film-based pressure sensor exhibited a high sensitivity (near to 860 kPa−1), a wide pressure range (0.5 Pa ‒ 30 kPa), a short response/recovery time (40/53 ms) and good cycle stability (11 600 cycles). The sensor has the advantages of great flexibility, high sensitivity, wide detection range, simple preparation process, and cost-effectiveness. Based on these merits, the prepared pressure sensor shows great potential in the fields of small object recognition and dynamic monitoring, biometric sign analysis and monitoring etc.
Author contributions
Yuhuan Lv, Lizhen Min: Bibliographic search, data curation, and draft manuscript preparation. Yuhuan Lv and Lizhen Min contributed equally to this work. Fengxiao Niu, Xiangyang Chen, Yong Liu: Supervision. Biao Zhao, Kai Pan: Draft revision. The manuscript was written through contributions of all authors.
Ethical statement
Informed consent was obtained from the volunteer who participated in the experiments with the pressure sensor used to detect various human motions.
Supplemental Material
Download MS Word (935.4 KB)Disclosure statement
No potential conflict of interest was reported by the authors.
Additional information
Funding
Notes on contributors
Yuhuan Lv
Yuhuan Lv is a doctoral candidate at Beijing University of Chemical Technology. Her scientific interests include the creation of two-dimensional conductive films and their use in flexible piezoresistive sensors.
Lizhen Min
Lizhen Min, a master's student, received her diploma from the Beijing University of Chemical Technology. Her scientific interests include the synthesis of MXene, a highly conductive polymer, and its use in flexible piezoresistive sensors.
Fengxiao Niu
Fengxiao Niu, a master's student, received his diploma from Beijing University of Chemical Technology. His scientific interests include the development of highly conductive aerogels and their use in flexible piezoresistive sensors.
Xiangyang Chen
Xiangyang Chen is a doctoral student at Beijing University of Chemical Technology. His research interests are the preparation of highly conductive nanomaterial MXene and its application.
Biao Zhao
Biao Zhao, Ph.D. candidate at Beijing University of Chemical Technology, graduated from Beijing University of Chemical Technology. Biao Zhao is associate professor at Beijing University of Chemical Technology. His research interests include circularly polarized light-emitting materials and devices, chiral polymer and bio-based polymer.
Yong Liu
Yong Liu, associate researcher, PhD supervisor, and head of polymer nanocomposites laboratory at Beijing University of Chemical Technology. He is mainly engaged in the research of polymer and nanocomposite materials preparation and application.
Kai Pan
Kai Pan, researcher, PhD supervisor at Beijing University of Chemical Technology. His research areas are new nylon resin preparation and its composites, electrostatic spinning nanofiber (membrane) preparation and functionalization, and high-performance composites.
References
- Koo JH, Kim DC, Shim HJ, et al. Flexible and stretchable smart display: materials, fabrication, device design, and system integration. Adv Funct Mater. 2018;28(35):1801834.
- Kang H, Zhao CL, Huang JR, et al. Fingerprint-Inspired conducting hierarchical wrinkles for energy-harvesting e-skin. Adv Funct Mater. 2019;29(43):1903580. 10,
- Chan YT, Skreta M, McPhee H, et al. Solution-processed wrinkled electrodes enable the development of stretchable electrochemical biosensors. Analyst. 2018;144(1):172–179.
- Kim J, Chou EF, Le J, et al. Soft wearable pressure sensors for beat-to-beat blood pressure monitoring. Adv Healthcare Mater. 2019;8(13):1900109. 9,
- Gao NW, Zhang XY, Liao SL, et al. Polymer swelling induced conductive wrinkles for an ultrasensitive pressure sensor. ACS Macro Lett. 2016;5(7):823–827.
- Xue PD, Chen C, Diao DF. Ultra-sensitive flexible strain sensor based on graphene nanocrystallite carbon film with wrinkle structures. Carbon. 2019;147:227–235.
- Fan HW, Li KR, Li Q, et al. Prepolymerization-assisted fabrication of an ultrathin immobilized layer to realize a semi-embedded wrinkled AgNW network for a smart electrothermal chromatic display and actuator. J Mater Chem C. 2017;5(37):9778–9785.
- Wei Y, Chen S, Yuan X, et al. Multiscale wrinkled microstructures for piezoresistive fibers. Adv Funct Mater. 2016;26(28):5078–5085.
- Liu W, Liu N, Yue Y, et al. Piezoresistive pressure sensor based on synergistical innerconnect polyvinyl alcohol nanowires/wrinkled graphene film. Small. 2018;14(15):1704149.
- Qin Z, Yin YY, Zhang WZ, et al. Wearable and stretchable triboelectric nanogenerator based on crumpled nanofibrous membranes. ACS Appl Mater Interfaces. 2019;11(13):12452–12459.
- Jung J, Lee KM, Baeck SH, et al. Piezoresistive behavior of a stretchable carbon nanotube-interlayered poly(dimethylsiloxane) sheet with a wrinkled structure. RSC Adv. 2015;5(89):73162–73168.
- Lipomi DJ, Vosgueritchian M, Tee BCK, et al. Skin-like pressure and strain sensors based on transparent elastic films of carbon nanotubes. Nat Nanotechnol. 2011;6(12):788–792.
- Park SJ, Kim J, Chu M, et al. Highly flexible wrinkled carbon nanotube thin film strain sensor to monitor human movement. Adv Mater Technol. 2016;1(5):1600053.
- Zhang CJ, Li H, Huang AM, et al. Rational design of a flexible CNTs@PDMS film patterned by bio-inspired templates as a strain sensor and supercapacitor. Small. 2019;15(18):1805493. 8,
- Jia J, Huang GT, Deng JP, et al. Skin-inspired flexible and high-sensitivity pressure sensors based on rGO films with continuous-gradient wrinkles. Nanoscale. 2019;11(10):4258–4266.
- Wang MT, Qiu YY, Jia J, et al. Wavelength-gradient graphene films for pressure-sensitive sensors. Adv Mater Technol. 2019;4(1):1800363.
- Yin FX, Yang JZ, Ji PG, et al. Bioinspired pretextured reduced graphene oxide patterns with multiscale topographies for high-performance mechanosensors. ACS Appl Mater Interfaces. 2019;11(20):18645–18653.
- Chang TH, Tian Y, Li CS, et al. Stretchable graphene pressure sensors with Shar-Pei-like hierarchical wrinkles for collision-aware surgical robotics. ACS Appl Mater Interfaces. 2019;11(10):10226–10236.
- Chang TH, Zhang TR, Yang HT, et al. Controlled crumpling of two-dimensional titanium carbide (MXene) for highly stretchable, bendable, efficient supercapacitors. Acs Nano. 2018;12(8):8048–8059.
- Bae GY, Han JT, Lee G, et al. Pressure/temperature sensing bimodal electronic skin with stimulus discriminability and linear sensitivity. Adv Mater. 2018;30(43):1803388. 8,
- Li TK, Chen LL, Yang X, et al. A flexible pressure sensor based on an MXene-textile network structure. J Mater Chem C. 2019;7(4):1022–1027.
- Sahoo BN, Woo J, Algadi H, et al. Superhydrophobic, transparent, and stretchable 3D hierarchical wrinkled film-based sensors for wearable applications. Adv Mater Technol. 2019;4(10):1900230.
- Hui N, Chai FL, Lin PP, et al. Electrodeposited conducting polyaniline nanowire arrays aligned on carbon nanotubes network for high performance supercapacitors and sensors. Electrochim Acta. 2016;199:234–241.
- Shi XL, Liu SR, Sun Y, et al. Lowering internal friction of 0D-1D-2D ternary nanocomposite-based strain sensor by fullerene to boost the sensing performance. Adv Funct Mater. 2018;28(22):1800850.
- Huang WC, Hu LP, Tang YF, et al. Recent advances in functional 2D MXene-based nanostructures for next-generation devices. Adv Funct Mater. 2020;30(49):2005223. 32,
- Ma YN, Liu NS, Li LY, et al. A highly flexible and sensitive piezoresistive sensor based on MXene with greatly changed interlayer distances. Nat Commun. 2017;8(1):1207.
- Bi LL, Yang ZL, Chen LJ, et al. Compressible AgNWs/Ti(3)C(2)T(x)MXene aerogel-based highly sensitive piezoresistive pressure sensor as versatile electronic skins. J Mater Chem A. 2020;8(38):20030–20036.
- Fu X, Wang L, Zhao L, et al. Controlled assembly of MXene nanosheets as an electrode and active layer for high-performance electronic skin. Adv Funct Mater. 2021;31(17):2010533.
- Zhu M, Yue Y, Cheng YF, et al. Hollow MXene sphere/reduced graphene aerogel composites for piezoresistive sensor with ultra-high sensitivity. Adv Electron Mater. 2020;6(2):1901064. 9,
- Hu XY, Dou YY, Li JJ, et al. Buckled structures: Fabrication and applications in wearable electronics. Small. 2019;15(32):1804805. 26,
- Ruth SRA, Feig VR, Tran H, et al. Microengineering pressure sensor active layers for improved performance. Adv Funct Mater. 2020;30(38):2003491. 31,
- Liu M, Pu X, Jiang C, et al. Large-area all-textile pressure sensors for monitoring human motion and physiological signals. Adv Mater. 2017;29(41):1703700.
- Liu R, Li JM, Li M, et al. MXene-coated air-permeable pressure-sensing fabric for smart wear. ACS Appl Mater Interfaces. 2020;12(41):46446–46454.
- Yang Y, Luo C, Jia J, et al. A wrinkled Ag/CNTs-PDMS composite film for a high-performance flexible sensor and its applications in human-body single monitoring. Nanomaterials. 2019;9(6):850.
- Cheng YF, Ma YA, Li LY, et al. Bioinspired microspines for a high-performance spray Ti3C2Tx MXene-based piezoresistive sensor. Acs Nano. 2020;14(2):2145–2155.
- Liu Q, Chen J, Li Y, et al. High-performance strain sensors with Fish-Scale-like graphene-sensing layers for full-range detection of human motions. ACS Nano. 2016;10(8):7901–7906.
- Tai Y, Bera TK, Yang Z, et al. Leveraging a temperature-tunable, scale-like microstructure to produce multimodal, supersensitive sensors. Nanoscale. 2017;9(23):7888–7894.
- Chen W, Gui X, Liang B, et al. Structural engineering for high sensitivity, ultrathin pressure sensors based on wrinkled graphene and anodic aluminum oxide membrane. ACS Appl Mater Interfaces. 2017;9(28):24111–24117.
- Yan S, Zhang GZ, Jiang HY, et al. Highly stretchable room-temperature self-healing conductors based on wrinkled graphene films for flexible electronics. ACS Appl Mater Interfaces. 2019;11(11):10736–10744.
- Alhabeb M, Maleski K, Anasori B, et al. Guidelines for synthesis and processing of two-dimensional titanium carbide (Ti3C2TX MXene). Chem Mater. 2017;29(18):7633–7644.
- Huang XW, Wu PY. A facile, high-yield, and freeze-and-Thaw-assisted approach to fabricate MXene with plentiful wrinkles and its application in on-chip micro-supercapacitors. Adv Funct Mater. 2020;30(12):1910048. 11,
- Ma RZ, Sasaki T. Two-dimensional oxide and hydroxide nanosheets: controllable high-quality exfoliation, molecular assembly, and exploration of functionality. Acc Chem Res. 2015;48(1):136–143.
- Lipatov A, Alhabeb M, Lukatskaya MR, et al. Effect of synthesis on quality, electronic properties and environmental stability of individual monolayer Ti3C2 MXene flakes. Adv Electron Mater. 2016;2(12):1600255. 9,
- Sarycheva A, Makaryan T, Maleski K, et al. Two-dimensional titanium carbide (MXene) as surface-enhanced raman scattering substrate. J Phys Chem C. 2017;121(36):19983–19988.
- Gao YY, Yan C, Huang HC, et al. Microchannel-confined MXene based flexible piezoresistive multifunctional micro-force sensor. Adv Funct Mater. 2020;30(11):1909603. 8,
- Jiang D, Zhang J, Qin S, et al. Superelastic Ti3C2Tx MXene-based hybrid aerogels for compression-resilient devices. ACS Nano. 2021;15(3):5000–5010.
- Wang DY, Wang LL, Lou Z, et al. Biomimetic, biocompatible and robust silk Fibroin-MXene film with stable 3D cross-link structure for flexible pressure sensors. Nano Energy. 2020;78, 8:105252.
- Wang L, Zhang MY, Yang B, et al. Highly compressible, thermally stable, light-weight, and robust aramid nanofibers/Ti3AlC2 MXene composite aerogel for sensitive pressure sensor. Acs Nano. 2020;14(8):10633–10647.
- Zhuo H, Hu YJ, Chen ZH, et al. A carbon aerogel with super mechanical and sensing performances for wearable piezoresistive sensors. J Mater Chem A. 2019;7(14):8092–8100.
- Wu SY, Peng SH, Han ZJ, et al. Ultrasensitive and stretchable strain sensors based on mazelike vertical graphene network. ACS Appl Mater Interfaces. 2018;10(42):36312–36322.