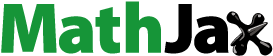
Abstract
Due to ever increasing use of telecommunication and electronic devices in offshore and stealth technology sectors, developing highly-efficient electromagnetic interference (EMI) shielding materials with good thermal resistance are urgently required. In this paper, the effect of MWCNTs incorporation on the mechanical, interlaminar bonding and EMI performance of MWCNT/CF/PEEK composites were firstly studied. The introduction of interlaminar MWCNTs did not affect the tensile strength and modulus significantly at low loadings whilst slight decrease in them was seen beyond a MWCNT content of 2.5 g/m2 due to the presence of CNT clusters. Improvement in the flexural strength and modulus as well as interlaminar bonding were achieved, reaching the peak values at an interlaminar MWCNT content of 1.5 g/m2. This is because the existence of inter-ply CNTs improves the stiffness and strength of the interlaminar region in shear when the material is subjected to bending moment. EMI shielding effectiveness of the laminates was markedly enhanced by 76% at an interlaminar CNT content as low as 2.5 g/m2 (equivalent to 0.53 wt.%). For the first time, this work has demonstrated the effectiveness and high efficiency of utilizing a multilayer structural design with the CNTs spray coated at the interlaminar region to improve the EMI shielding performance of CF/PEEK composites.
Graphical Abstract
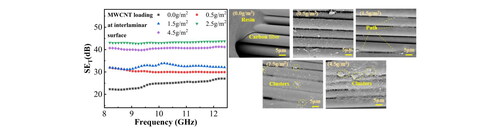
1. Introduction
The wide application of modern electronic and electrical appliances in telecommunication, automotive, medical, laboratory and stealth technology sectors has led to concerning electromagnetic interference (EMI) pollution [Citation1,Citation2], which not only deteriorates the proper functioning and durability of devices, but also tends to harm human health after prolonged exposure to EM wave radiation. Developing EMI shielding materials are of great importance in term of mitigating and suppressing EMI pollution.
The material shielding effectiveness is mainly dependent on electrical conductivity, dielectric properties and magnetic loss [Citation3,Citation4]. Main shielding mechanisms range from typical reflection shielding based on the Faraday cage principle [Citation5] observed in metal materials to absorption dominant mechanism seen in magnetic materials [Citation6] and foamed polymer composites [Citation7]. However, conventional metallic shielding materials such as steel, aluminum and copper suffer from high density, high processing cost, poor corrosion resistance and a lack of flexibility and integration. To tackle aforementioned limitations, conductive polymer nanocomposites utilizing carbon nanotube (CNT) [Citation3,Citation8,Citation9], graphene nanoplatelet (GNP) and its derivatives [Citation10], Mxene [Citation11,Citation12], metal nanoparticle/wire [Citation2] have emerged as promising EMI shielding materials thanks to their lower density, versatility and multifunctionality [Citation13].
Common strategies like multi-layered structures [Citation1,Citation14], multi-scale hybrids [Citation12,Citation15], the combined use of nanohybrid or nanocarbon architectures [Citation10,Citation16] have been employed to enhance EMI shielding effectiveness (EMI SE). For instance, Gupta et al. [Citation14] synthesized conductive polypyrrole (PPY) containing multilayer graphene anchored with titanium dioxide (TiO2) by in-situ polymerization. A maximum total SE of 53 dB were realized with 5 wt. % graphene and 5 wt. % TiO2 in the 12.4–18 GHz. Huynen et al. [Citation4] prepared hierarchical hybrid materials with superior EM absorption capabilities by inserting a CNT-filled polymer foam into a metallic honeycomb, and the peak absorption frequency was tunable by varying the shape of honeycomb unit cell. Chen et al. [Citation17] fabricated highly porous graphene aerogels enhanced phenolic resin by a hydrothermal synthesis followed by high-temperature annealing, leading to an excellent EMI SE of 35 dB at an aerogel content as low as 0.33 wt.%.
In terms of fabrication method for ‘CNT-based polymer nanocomposites’, melt blending [Citation18,Citation19] and solution compounding [Citation20,Citation21] are widely adopted. Common problems involve the use of toxic solvent and its subsequent elimination in the final product, the reduced processability due to the increased viscosity as a consequence of high CNT loading as well as potential filler breakage and polymer degradation if the mixing temperature and shear force is not properly optimized [Citation22]. Chemical vapor deposition [Citation23,Citation24], electrophoretic deposition [Citation25,Citation26] and in-situ polymerization [Citation14] could avoid some limitations above to achieve adequate dispersion locally yet with challenges for scale-up. Recently, spray coating has emerged as a simple, low-cost and effective approach to incorporate CNTs into polymer composites suitable for large-scale production. For example, Su et al. [Citation27] prepared unidirectional oxidized-CNTs/CF/PEEK composite using prepreg spraying method. It was observed that the interlaminar shear strength (ILSS), flexural strength and flexural modulus were improved by 35.8%, 25.4% and 23.7%, respectively, at an optimum CNT loading of 0.5 wt.%. Meanwhile the electrical conductivity was also continuously improved with increasing CNT content up to 1 wt.%. Zhang et al. [Citation28] also deposited CNTs on the carbon fiber epoxy prepreg by spraying coating. The mode I fracture toughness of the CNT/CF/epoxy composite was significantly improved by approximately 50% with 0.047 wt.% ultra-low CNT loading as a consequence of nano-bridging effect and highly deformed epoxy matrix. Gong et al. [Citation29] fabricated CNT/CFRP composites by dry spray deposition and the maximum ILSS of the composites was achieved at an interlaminar loading of 1.5 g/m2. Furthermore, Li et al. [Citation30] investigated the synergistic effect of the spray-coated hybrid CNT and GNP nanoparticles on the electrical conductivity and found the surface resistivity of CFRP laminate was reduced by four orders of magnitude (from 2–3 Ω/sq to 3 × 10−4 Ω/sq). However, most of aforementioned studies have either focused on mechanical and electrical properties of CF/PEEK nanocomposites or on EMI properties of modified general polymers like polypropylene (PP), polystyrene (PS), polymethylmethacrylate (PMMA), acrylonitrile butadiene styrene (ABS) [Citation7], which has restricted applications to a service temperature up to 150 °C as a consequence of their intrinsically low thermal stability. In case of more demanding operating situations like aerospace, offshore telecommunication for oil and drilling (which often involves flammable gasses and is likely to become explosive), the materials which can endure more severe operating temperature up to 250 °C and high pressure are desired.
In this study, thermoplastic polymer polyether ether ketone (PEEK) with good high temperature resistance up to 340 °C was selected aiming to develop EMI materials suitable for more demanding application. MWCNT/CF/PEEK composites with a multi-layered structure were fabricated with CNTs deposited on each individual layer by spray coating. The effects of CNTs on morphological, mechanical, interlaminar bonding, EMI SE of the composites were investigated in detail for the first time.
2. Materials and experimental
2.1. Materials
Multiwall carbon nanotubes (MWCNTs) with a diameter of 30 ∼ 50 nm and a length of 10 ∼ 30 μm were purchased from Xianfeng Nano Material Technology Ltd (China); Carbon fiber (T300) reinforced PEEK prepregs (satin-woven organosheet) with a resin content of 37%∼43% were supplied by Jiangsu Junhua Special Engineering Plastic Products Ltd (China); CNTs water dispersant (Product code: TNWDIS) was supplied by Chengdu Organic Chemistry Co. Ltd (China), which is a kind of non-ionic surfactant used to facilitate the dispersion of CNTs in deionized water. Zyvax® Flex-ZTM 5.0 mould release agent and Zyvax® sealer GPTM mould sealer (Chem Trend Ltd) were purchased from Shanchuan Composites Ltd (China).
2.2. Fabrication
shows the preparation process of multiscale hybrid MWCNT/CF/PEEK composites. 0.01 wt.% MWCNT dispersion was prepared as follows: 0.04 g CNTs water dispersant was added into 500 mL deionized water and heated in a water bath at 50 °C for 0.5 h. After the dispersant was dissolved, 0.05 g (0.01 wt.%) MWCNTs were added into the solution, followed by 50 min sonication in water bath to form a homogeneous dispersion for spray coating. The dispersion was evenly spray-coated on the surface of a 150 mm × 250 mm prepreg by a spray gun, followed by drying at 80 °C for 30 min. This process was repeated until the MWCNT content in each prepreg reached the predesigned value: 0.5 g/m2, 1.5 g/m2, 2.5 g/m2 and 4.5 g/m2, respectively. In order to ensure the consistency and repeatability, the spraying direction was kept perpendicular to prepreg with a distance of 10 cm between spraying nozzle and the prepreg.
The self-made mould was treated with mould sealing agent and release agent. In order to comply with EMI test and mechanical tests standards, unidirectional MWCNT/CF/PEEK samples containing 6 and 9 layers of prepregs were compression moulded separately using a hydraulic hot press according to the manufacturer’s recommended process parameters as shown in . In addition, the MWCNT/CF/PEEK samples without spray coating treatment were also fabricated for comparison purpose.
2.3. Characterizations
2.3.1. Morphology analysis
Scanning electron microscopy (SEM) was carried out using a Phenom Prox desktop SEM (Thermo Fisher Scientific Inc, USA) and field-emission SEM (TESCAN MIRA LMS, Czech Republic) to determine the MWCNTs distribution and dispersion state along the spray-treated prepreg and the interfacial morphology. For cryofracture morphological observation, the samples were immersed in liquid nitrogen for ten minutes prior to fracture, and then were coated with gold by ion sputtering instrument (SBC-12, Kyky. Technology. Co. Ltd, China) to avoid the accumulation of static charge before imaging.
2.3.2. Tensile and flexural test
Tensile tests were performed on a universal mechanical testing machine (Instron 5982, USA) according to GB/T1447. The test speed was 40 mm/min and the test samples were of size 180 mm × 20 mm × 1.7 mm.
Three-point bending tests were carried out on a universal mechanical testing machine (CMT5105, Shenzhen Sans Testing Machine Co. Ltd, China) according to GB/T1449. The test samples were of size 80 mm × 10 mm × 2.6 mm, with a span length of 50 mm. The tests were carried out at a speed of 1 mm/min.
2.3.3. Dynamic mechanical analysis
DMA test was performed on a Dynamic Mechanical Analyzer (242E Artemis, Netzsch, Germany) to investigate the bonding properties of MWCNT/CF/PEEK laminates using a three-point bending test mode. The flexural storage modulus G′, loss modulus G″ and loss factor Tanδ were obtained as a function of the temperature from 25 °C to 250 °C. The heating rate was 10 K/min and a sinusoidal force with a peak value of 6.55 N at the frequency of 1 Hz was applied. The sample size is 60 mm × 10 mm × 1.7 mm.
2.3.4. Electrical conductivity measurements
The resistance of CF/MWCNT/PEEK laminates with different interlaminar MWCNT contents (0.0 g/m2, 0.5 g/m2, 1.5 g/m2, 2.5 g/m2, 4.5 g/m2) were tested in the plane direction by using a B2912a (Keysight) source meter with silver paint applied to the sample edge along the sample width. The conductivity can be calculated from
(1)
(1)
where
is the sample resistance,
is the cross-sectional area through which the current flows during resistance measurement, and
is the length perpendicular to the cross-sectional area through which the current flows.
2.3.5. EMI shielding properties test
The EMI SE performance of the samples was characterized by a vector network analyzer (E5063A, USA) in X-band frequency of 8.2 GHz to 12.4 GHz. The sample size is 22.9 mm × 10.2 mm × 1.7 mm. The total shielding electromagnetic shielding effectiveness can be defined as the ratio of transmitted to incident energy in logarithmic scale [Citation31].
(2)
(2)
The SEm could be negligible when >15 dB, thus
(3)
(3)
Where and
are the power of incident and transmitted EM waves, respectively.
is absorption loss efficiency,
is reflection loss efficiency, and
is the multiple reflection loss efficiency.
3. Result and discussion
3.1. Morphology analysis
The fractography of the MWCNT/CF/PEEK laminates with various CNT contents (Figure S1 in SI) shows a good wettability between the fiber and PEEK matrix. ,a′) show the TEM diagrams of MWCNTs used in this study, with an approximate diameter of 40 nm. f′) show the SEM images of the prepreg surface with different MWCNT content. It can be seen that a relatively uniform MWCNT distribution was found in the sample with an interlaminar MWCNT content of 0.5 g/m2 (equivalent to 0.11 wt. %) (see and c′). It is noted that some CNTs also reached the CF surfaces due to uneven PEEK resin coverage on the as-received PEEK prepregs with presences of exposed CF yarns and visible voids. A homogenous network formed with MWCNTs bridging between fibers at a content of 1.5 g/m2 (see and d′). With continuous increase in MWCNT content to 2.5 g/m2, a few CNT clusters were observed in the network. Furthermore, compared with the former case, the network had a much better coverage on carbon fibers, leading to more interconnected conductive paths, as indicated in ,e′). When the content of MWCNT reached 4.5 g/m2 (equivalent to 0.96 wt. %), MWCNTs formed large amount of agglomeration, which is likely to has detrimental effect on the interlaminar and mechanical properties of the materials. Previous research results [Citation27] also showed a perfect conductive network was formed on a unidirectional CF/PEEK prepreg at a CNT content of 0.1 wt.% whilst the CNTs started to agglomerate at 1 wt.% loading, which is comparable to our results.
3.2. Tensile and flexural properties
shows the tensile properties of MWCNT/CF/PEEK laminates with various MWCNT content. The tensile strength of the CF/PEEK laminates without spraying coating treatment is approximately 754 MPa. Compared with CF/PEEK laminates, the introduction of MWCNTs between plies did not seem to affect the tensile strength and modulus at low loadings. Slight decrease in tensile strength and modulus was seen beyond a MWCNT content of 2.5 g/m2 due to the presence of the CNT clusters. shows flexural strength and flexural modulus of the laminates. In contrast, bending properties of MWCNT/CF/PEEK laminates show different trends with increasing CNT loading. The effect of CNT incorporation is more influential on flexural strength and flexural modulus, with a maximum increment of 28.6% and 24.6%, respectively, than on tensile strength and modulus, i.e. 4.1% and 5.4%, respectively. Compared to tensile loading, flexural loading consists of a combination of tensile/compressive stresses and shear stresses on planes perpendicular to load direction as well as between plies. The existence of CNTs improves the stiffness and strength of the interlaminar region in shear and thus flexural strength (see ).
3.3. Electrical conductivity of the composites
and show the electrical conductivity of MWCNT/CF/PEEK composites as a function of MWCNT loading and the correlation between CNT content expressed in terms of g/m2 and wt.%, respectively. The initial electrical conductivity of untreated CF/PEEK laminates is 6.46 S/cm due to the high carbon fiber content of the composite. With the addition of CNTs at an amount as low as 0.11 wt.% (equivalent to an interlaminar content of 0.5 g/m2), the conductivity of the laminate was improved by 29%, demonstrating the efficiency of spray coating technique. A continuous increase in conductivity from 8.34 S/cm to 10.87 S/cm was found until a slight drop was seen at a content of 4.5 g/m2 as a consequence of formation of multiple large-size CNT clusters as shown section 3.1 (see ′). The conductivity is in the similar range as observed by Rohini et al. [Citation32]. When the CNT content of the composite continues to increase, the conductivity level is relatively stable without significant change.
Figure 6. Electrical conductivity of MWCNT/CF/PEEK composites as a function of MWCNT content. Note: the solid triangle indicates the improvement in the conductivity compared to that of untreated CF/PEEK composites.
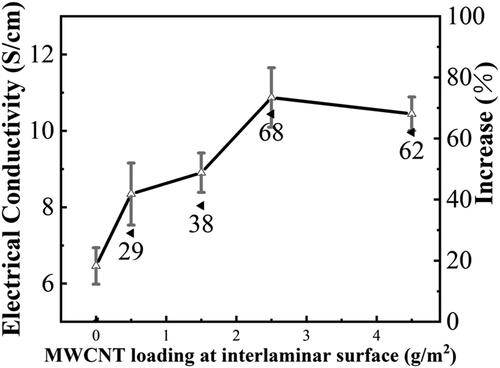
Table 1. Electrical conductivity of MWCNT/CF/PEEK composites as a function of MWCNT loading expressed in terms of g/m2 and wt.% at the interface.
3.4. EMI shielding properties
It is widely known that the shielding effectiveness of polymer nanocomposite is affected by conductivity, dispersion, aspect ratio and concentration of the conductive fillers used [Citation3]. The presence of a homogenous conductive network plays a key role in attenuating EM wave. shows the total shielding effectiveness SET of the laminates in the X-band. An optimum EMI performance of SET value being 43.19 dB was achieved at a CNT content of 2.5 g/m2, which is 76% enhancement than that of the CF/PEEK laminate samples (24.57 dB) thanks to the incorporation of fairly homogenous conductive MWCNTs network at the interlaminar region as observed by SEM (see ′) in spite of a small amount of CNT clusters. The presence of large-size CNT agglomerates led to a slight reduction in EMI properties for a CNT content of 4.5 g/m2. shows the absorption loss SEA, reflection loss SER and total shielding loss of the laminate samples. In each case, MWCNT/CF/PEEK laminates exhibit a much higher SEA value than SER, revealing absorption-dominated shielding characteristics. Similar trends in EMI properties and conductivity results with varying CNT contents were observed in our study, which are consistent with previous reported findings [Citation33].
Figure 7. (a) Total shielding effectiveness SET of MWCNT/CF/PEEK composites in the whole X-band; (b) Average SEA, SER and SET values of MWCNT/CF/PEEK laminates.
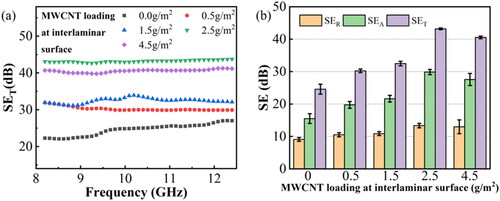
Further efforts were made to summarize the EMI SE study of PEEK-based nanocomposites in the literature. No work has been conducted on enhancing the EMI SE performance of the continuous carbon fiber reinforced PEEK composites using nanofillers so far. Although it is not ideal, we have to compare our results with nanofiller reinforced PEEK and other carbon fiber reinforced polymer nanocomposites instead, as listed in . It is noted specific SE should be interpreted with care as a result of the difference in materials structure. With the introduction of as low as 0.53 wt.%, an enhanced EMI performance of 43.2 dB was achieved, confirming the high efficiency and effectiveness of introducing CNT in the interlaminar region.
Table 2. EMI SE comparison of nanofiller reinforced polymer composites in X band.
3.5. Dynamic mechanical analysis
show the change in flexural storage modulus G′ and tanδ of the laminates as a function of testing temperature, respectively. In all cases, the G′ value of various MWCNT/CF/PEEK laminates is larger than that of untreated CF/PEEK laminates, confirming the reinforcing effect of MWCNTs in bending mode. The bonding of MWCNT/CF/PEEK laminates is positively correlated with the storage modulus G′ [Citation37,Citation38] and negatively correlated to the loss factor tan δ [Citation20,Citation39]. With increasing MWCNT content, the storage modulus gradually increases, reaching the peak value at a MWCNT content of 1.5 g/m2 whilst the tan δ follows the opposite trend, implying better interlaminar bonding properties as a consequence of interlocking effect imparted by the existence of MWCNTs between laminae, which also inhibits the chain segment movement of inter-ply molecules [Citation20]. However, with the continuous increase in MWCNT content beyond 1.5 g/m2, the storage modulus began to decrease. At this time, in spite of the existence of the interpenetrating network, the formation of MWCNT agglomerates/clusters (see ′ and f′) has led to unfavorable defects between each lamina which negatively affects the stress transfer and thus results in the reduction of G′. Additionally, no significant changes in Tg were observed which might be due to a small loading of MWCNTs introduced in this study. Similar finding in Tg has been reported in Chen et al.’s work [Citation39] using graphene oxide as the filler for PEEK matrix.
4. Conclusions
In this paper, MWCNT/CF/PEEK composites with a multilayer structure were prepared by hot pressing with CNT spray-coated in the interlaminar region. A homogenous conductive network with good MWCNT dispersion was observed at an interlaminar CNT content of 1.5 g/m2 (equivalent to 0.32 wt. %), at which optimum tensile and flexural strength were achieved. DMA results also indicated the best interlaminar bonding at this level. The CNT incorporation was found to contribute more to improving flexural properties than tensile properties. This is because the presence of interlaminar CNTs improves the stiffness and strength of inter-ply region in shear when the composites are subjected to bending moment. With further increase in CNT amount, the mechanical properties experienced a continuous drop resulting from the formation of a certain amount of CNT clusters, with bending properties still remaining above that of untreated CF/PEEK composites. EMI performance follows the same trend as conductivity variations in this study. A maximum of EMI shielding effectiveness of 43.2 dB was achieved at an interlaminar CNT content of 2.5 g/m2 (equivalent to a total CNT mass fraction as low as 0.53 wt.%), beyond which both conductivity and EMI properties started to decrease. For the first time, the effect of CNT incorporation on the EMI properties of continuous carbon fiber reinforced PEEK composites has been investigated, demonstrating the effectiveness and high efficiency of spray-coating of MWCNTs in the interlaminar region to improve the EMI performance.
Author contributions
Conceptualization, S.C., Y.T., H.L., M.R. and J.S.; methodology, S.C. and Y.T.; software, S.C.; validation, S.C.; formal analysis, S.C. and Y.T.; investigation, S.C.; resources, S.C., Y.T., H.L., M.R. and J.S.; data curation, S.C.; writing—original draft preparation, S.C. and Y.T.; writing—review and editing, Y.T., H.L., M.R. and J.S.; visualization, S.C.; supervision, Y.T., H.L., M.R. and J.S.; project administration, Y.T., H.L., M.R. and J.S.; funding acquisition, H.L., M.R. and J.S.
Supplemental Material
Download PDF (163.5 KB)Disclosure statement
No potential conflict of interest was reported by the authors.
Additional information
Funding
Notes on contributors
Shouyi Cao
Shouyi Cao received his MSc degree in Materials Science at Shanghai University (2022). During his study, he worked on the electromagnetic interference (EMI) shielding property of high-performance polymer matrix composites.
Yinping Tao
Yinping Tao, currently working as a lecturer in the Composite Materials Research Centre of Shanghai University. She has obtained her PhD degree from Queen Mary University of London (2018), working on the fatigue of carbon fibre reinforced composites. After that she continued her postdoc research in The University of Manchester and SET Europe Ltd to develop lightweight and acoustic plastics for automotive applications. She has both research and industrial R&D experience with an emphasis on elastomer, nanocomposites, fibre reinforced composites.
Hong Li
Hong Li, currently working as a professor in the Composite Materials Research Centre, Shanghai University. Her current research focuses on the development of high performance composite materials for severe environmental applications.
Musu Ren
Musu Ren, currently working as a professor in the Composite Materials Research Centre, Shanghai University. Her current research focuses on composite materials for aerospace applications.
Jinliang Sun
Jinliang Sun, has considerable expertise in the design and manufacturing of special textiles and their composite materials.
References
- Chung DDL, Eddib AA. Effect of fiber lay-up configuration on the electromagnetic interference shielding effectiveness of continuous carbon fiber polymer-matrix composite. Carbon. 2019;141:685–691. doi:10.1016/j.carbon.2018.09.081.
- Li J, Peng W-J, Fu Z-J, et al. Achieving high electrical conductivity and excellent electromagnetic interference shielding in poly(lactic acid)/silver nanocomposites by constructing large-area silver nanoplates in polymer matrix. Compos Part B: Eng. 2019;171:204–213. doi:https://doi.org/10.1016/j.compositesb.2019.05.003.
- Sharika T, Abraham J, Arif P M, et al. Excellent electromagnetic shield derived from MWCNT reinforced NR/PP blend nanocomposites with tailored microstructural properties. Compos Part B: Eng. 2019;173:106798. doi:https://doi.org/10.1016/j.compositesb.2019.05.009.
- Huynen I, Quiévy N, Bailly C, et al. Multifunctional hybrids for electromagnetic absorption. Acta Mater. 2011;59(8):3255–3266. doi:https://doi.org/10.1016/j.actamat.2011.01.065.
- Gupta S, Tai N-H. Carbon materials and their composites for electromagnetic interference shielding effectiveness in X-band. Carbon. 2019;152:159–187. doi:https://doi.org/10.1016/j.carbon.2019.06.002.doi:10.1016/j.carbon.2019.06.002.
- Shukla V. Review of electromagnetic interference shielding materials fabricated by iron ingredients. Nanoscale Adv. 2019;1(5):1640–1671.doi:https://doi.org/10.1039/c9na00108e.
- Abbasi H, Antunes M, Velasco JI. Recent advances in carbon-based polymer nanocomposites for electromagnetic interference shielding. Progress Mater Sci. 2019;103:319–373. doi:https://doi.org/10.1016/j.pmatsci.2019.02.003.
- Li H, Lu X, Yuan D, et al. Lightweight flexible carbon nanotube/polyaniline films with outstanding EMI shielding properties. J Mater Chem C. 2017;5(34):8694–8698. doi:https://doi.org/10.1039/c7tc02394d.
- Shajari S, Arjmand M, Pawar SP, et al. Synergistic effect of hybrid stainless steel fiber and carbon nanotube on mechanical properties and electromagnetic interference shielding of polypropylene nanocomposites. Compos Part B: Eng. 2019;165:662–670. doi:https://doi.org/10.1016/j.compositesb.2019.02.044.
- Zhang H, Zhang G, Tang M, et al. Synergistic effect of carbon nanotube and graphene nanoplates on the mechanical, electrical and electromagnetic interference shielding properties of polymer composites and polymer composite foams. Chem Eng J. 2018;353:381–393. doi:https://doi.org/10.1016/j.cej.2018.07.144.
- Qian K, Zhou Q, Wu H, et al. Carbonized cellulose microsphere@void@MXene composite films with egg-box structure for electromagnetic interference shielding. Compos Part A-Appl S. 2021;141:106229. doi:https://doi.org/10.1016/j.compositesa.2020.106229.
- Song P, Qiu H, Wang L, et al. Honeycomb structural rGO-MXene/epoxy nanocomposites for superior electromagnetic interference shielding performance. Sustain Mater Technol. 2020;24:e00153. doi:https://doi.org/10.1016/j.susmat.2020.e00153.
- Dong M, Zhang H, Tzounis L, et al. Multifunctional epoxy nanocomposites reinforced by two-dimensional materials: a review. Carbon. 2021;185:57–81. doi:https://doi.org/10.1016/j.carbon.2021.09.009.
- Gupta A, Varshney S, Goyal A, et al. Enhanced electromagnetic shielding behaviour of multilayer graphene anchored luminescent TiO2 in PPY matrix. Mater Lett. 2015;158:167–169. doi:https://doi.org/10.1016/j.matlet.2015.05.154.
- Li S, Li W, Nie J, et al. Synergistic effect of graphene nanoplate and carbonized loofah fiber on the electromagnetic shielding effectiveness of PEEK-based composites. Carbon. 2019;143:154–161. doi:https://doi.org/10.1016/j.carbon.2018.11.015.
- Jiang B, Luan J, Qin S, et al. Fabrication of very effective ferroferric oxide and multiwalled carbon nanotubes@polyetherimide/poly(ether ether ketone) electromagnetic interference shielding composites. Polym Compos. 2020;41(8):3135–3143. doi:https://doi.org/10.1002/pc.25604.
- Chen Y, Zhang H-B, Wang M, et al. Phenolic resin-enhanced three-dimensional graphene aerogels and their epoxy nanocomposites with high mechanical and electromagnetic interference shielding performances. Compos Sci Technol. 2017;152:254–262. doi:https://doi.org/10.1016/j.compscitech.2017.09.022.
- Na R, Liu J, Wang G, et al. Light weight and flexible poly(ether ether ketone) based composite film with excellent thermal stability and mechanical properties for wide-band electromagnetic interference shielding. RSC Adv. 2018;8(6):3296–3303.doi:https://doi.org/10.1039/C7RA11675F.
- Wang H, Wang G, Li W, et al. A material with high electromagnetic radiation shielding effectiveness fabricated using multi-walled carbon nanotubes wrapped with poly(ether sulfone) in a poly(ether ether ketone) matrix. J Mater Chem. 2012;22(39):21232–21237. doi:https://doi.org/10.1039/C2JM35129C.
- Su Y, Zhou F, Wei X, et al. Enhanced mechanical and electrical properties of carbon fiber/poly(ether ether ketone) laminates via inserting carbon nanotubes interleaves. J Appl Polym Sci. 2020;137(19):48658.doi:https://doi.org/10.1002/app.48658.
- Yang Y, Gupta MC, Dudley KL, et al. The fabrication and electrical properties of carbon nanofibre– polystyrene composites. Nanotechnology. 2004;15(11):1545–1548. doi:https://doi.org/10.1088/0957-4484/15/11/030.
- Papageorgiou DG, Kinloch IA, Young RJ. Mechanical properties of graphene and graphene-based nanocomposites. Progress Mater Sci. 2017;90:75–127. doi:https://doi.org/10.1016/j.pmatsci.2017.07.004.
- Kepple KL, Sanborn GP, Lacasse PA, et al. Improved fracture toughness of carbon fiber composite functionalized with multi walled carbon nanotubes. Carbon. 2008;46(15):2026–2033. doi:https://doi.org/10.1016/j.carbon.2008.08.010.
- Veedu VP, Cao A, Li X, et al. Multifunctional composites using reinforced laminae with carbon-nanotube forests. Nat Mater. 2006;5(6):457–462. doi:https://doi.org/10.1038/nmat1650.
- Yang K, Mei H, Han D, et al. Enhanced electromagnetic shielding property of C/SiC composites via electrophoretically-deposited CNTs onto SiC coating. Ceram Int. 2018;44(16):20187–20191. doi:https://doi.org/10.1016/j.ceramint.2018.08.001.
- Yang L, Zheng W, Zhang P, et al. MXene/CNTs films prepared by electrophoretic deposition for supercapacitor electrodes. J Electroanal Chem. 2018;830-831:1–6. doi:https://doi.org/10.1016/j.jelechem.2018.10.024.
- Su YN, Zhang SC, Zhang XH, et al. Preparation and properties of carbon nanotubes/carbon fiber/poly (ether ether ketone) multiscale composites. Compos Part A-Appl S. 2018;108:89–98. doi:https://doi.org/10.1016/j.compositesa.2018.02.030.
- Zhang H, Liu Y, Kuwata M, et al. Improved fracture toughness and integrated damage sensing capability by spray coated CNTs on carbon fibre prepreg. Compos Part A-Appl S. 2015;70:102–110. doi:https://doi.org/10.1016/j.compositesa.2014.11.029.
- Gong S, Zhu ZH, Arjmand M, et al. Effect of carbon nanotubes on electromagnetic interference shielding of carbon fiber reinforced polymer composites. Polym Compos. 2018;39(S2):E655–E663. doi:https://doi.org/10.1002/pc.24084.
- Li Y, Zhang H, Liu Y, et al. Synergistic effects of spray-coated hybrid carbon nanoparticles for enhanced electrical and thermal surface conductivity of CFRP laminates. Compos Part A-Appl S. 2018;105:9–18. doi:https://doi.org/10.1016/j.compositesa.2017.10.032.
- Lee S-H, Kang D, Oh I-K. Multilayered graphene-carbon nanotube-iron oxide three-dimensional heterostructure for flexible electromagnetic interference shielding film. Carbon. 2017;111:248–257. doi:https://doi.org/10.1016/j.carbon.2016.10.003.
- Rohini R, Verma K, Bose S. Interfacial architecture constructed using functionalized MWNT resulting in enhanced EMI shielding in epoxy/carbon fiber composites. ACS Omega. 2018;3(4):3974–3982. doi:https://doi.org/10.1021/acsomega.8b00218.
- Li S, Jin Y, Wang Z, et al. Preparation and characterisation of nickel-plated carbon fibre/polyether ether ketone composites with high electromagnetic shielding and high thermal conductivity. Colloid Polym Sci. 2019;297(7-8):967–977. doi:https://doi.org/10.1007/s00396-019-04522-5.
- Chauhan SS, Verma P, Malik RS, et al. Thermomechanically stable dielectric composites based on poly(ether ketone) and BaTiO3 with improved electromagnetic shielding properties in X-band. J Appl Polym Sci. 2018;135(26):46413. doi:https://doi.org/10.1002/app.46413.
- Yang YL, Gupta MC, Dudley KL, et al. A comparative study of EMI shielding properties of carbon nanofiber and multi-walled carbon nanotube filled polymer composites. J Nanosci Nanotechnol. 2005;5(6):927–931. doi:https://doi.org/10.1166/jnn.2005.115.
- Singh BP, Choudhary V, Saini P, et al. Designing of epoxy composites reinforced with carbon nanotubes grown carbon fiber fabric for improved electromagnetic interference shielding. AIP Adv. 2012;2(2):022151. doi:https://doi.org/10.1063/1.4730043.
- Afaghi-Khatibi A, Mai Y-W. Characterisation of fibre/matrix interfacial degradation under cyclic fatigue loading using dynamic mechanical analysis. Compos Part A-Appl S. 2002;33(11):1585–1592. doi:https://doi.org/10.1016/S1359-835X(02)00117-3.
- Keusch S, Haessler R. Influence of surface treatment of glass fibres on the dynamic mechanical properties of epoxy resin composites. Compos Part A-Appl S. 1999;30(8):997–1002. doi:https://doi.org/10.1016/s1359-835x(99)00007-x.
- Chen J, Wang K, Zhao Y. Enhanced interfacial interactions of carbon fiber reinforced PEEK composites by regulating PEI and graphene oxide complex sizing at the interface. Compos Sci Technol. 2018;154:175–186. doi:https://doi.org/10.1016/j.compscitech.2017.11.005.