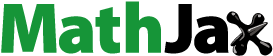
Abstract
In this work, Ni-W/diamond composite alloy coatings were successfully fabricated on low carbon steel by using direct current (DC) electrodeposition. The Ni-W molar ratio was varied in the range of 0.22–2 in the plating bath. The effect of variation of Ni-W molar on the microstructure, mechanical properties and tribology of Ni-W/diamond composite coatings was analyzed. The obtained results show that the W content and deposition rate of the Ni-W alloy tends to decrease from 19.02 at. % to 2.1 at. % and 34.86 µm/h to 11.98 µm/h, respectively as the Ni-W molar ratio is increased from 0.22 to 2. The hardness results reveal that the highest microhardness of 1346 Hv was reported for the sample fabricated with 0.75 Ni-W molar ratio. Furthermore, the wear rate of the Ni-W/diamond coatings tends to show a significant reduction as the Ni-W molar ratio is increased from 0.22 to 0.75.
1. Introduction
Electrodeposition of Ni-based alloy coatings has been researched extensively and the Ni-alloy tends to exhibit enhanced microstructure, mechanical and tribological properties as compared to pure Ni coatings [Citation1–4]. Several equipment used in machining tools, boiler, automobile and allied industries are exposed to damage by wear and corrosion. The materials used in the aforesaid industries should offer a high value of inherent and uniform hardness and corrosion resistance [Citation5–7] to avoid failures while in operation. Various techniques of surface finishing such as electroplating, electroless deposition, dip coating, etc. have been used by researchers to render mechanical strength, protection and toughness to the base materials (alloy or metals) by means of a sustainable metal alloy composite coating with enhanced properties. Moreover, the hardness and other mechanical properties of various metals is quite limited in contrast to the diversified demands of the flourishing machining/tools industries that need better performance coatings citing increase in production and consumer demands. Tool steel is known to exhibit hardness of around 450–500 Hv.
Fabrication of Ni- based alloys such as Ni-W [Citation8–12], Ni-Co [Citation13–16], Ni-Fe [Citation17–20], Ni-TiN [Citation21–23], Ni-B [Citation24–27], Ni-P [Citation28–31] renders the alloys with better morphology, mechanical and chemical characteristics like hardness, wear resistance, self-lubrication, and corrosion resistance as compared to metal deposits. Electrodeposited composite coatings based on Ni alloys (such as Ni-W), have been used as a viable alternative to hard chrome coatings. As opposed to the Ni alloy, the various particles co-deposited with the Ni-based alloy during the electro-deposition process tend to reinforce the abrasion resistance, and as a result, they show promise as a substitute for the various mechanical characteristics displayed by the hard chrome coatings [Citation32–39].
Owing to their high hardness values, excellent wear resistance capabilities, and enhanced corrosion resistance compared to the base metal or alloy, ceramic particle reinforced Ni-W composite coatings typically exhibit wide range of industrial and engineering applications [Citation38,Citation40–44]. The composite ceramic particles co-deposited on the base matrix render mechanical strength to the base metal or alloy matrix. The enhancement of the mechanical and tribological properties of the deposits can be attributed to the co-deposition of ceramic particles on metal/metal alloy matrix and it depends upon the extent of incorporation and distribution of such particles on the base metal/alloy matrix. Contemporary researchers have used various ceramics to fabricate composite coatings. The results reported by contemporary as well as previous works on Ni-based alloy systems demonstrate that the hardness for the as-plated Ni-W alloy varies roughly from 450 to 750 Hv [Citation45], while the hardness of Ni- based alloy coatings (such as Ni-W) can be enhanced by the incorporation of certain particles, such as Al2O3 [Citation46–49], boron [Citation50–53], tungsten carbide [Citation33,Citation54,Citation55], silicon carbide [Citation56–59] and BN [Citation60–62] to a considerable extent. Diamond is one such material that has of late been used to fabricate Ni-W alloy-based composite deposits [Citation63–65].
Several contemporary as well as past researchers have been trying to obtain the high concentration and uniform distribution of ceramic particles such as diamond, boron co-deposited on an electrodeposited Ni-W alloy matrix [Citation51,Citation65–67]. They have in part succeeded to a fair extent to obtain a high particle content and distribution of the aforesaid ceramic particles on the base matrix. However, there lies a significant gap in the various surface and mechanical properties exhibited by the composite deposits and the individual properties of the ceramic particles that is used for the fabrication of such deposits. The ceramic particles tend to render enhancement of the mechanical properties of the alloy/metal matrix but the level of enhancement doesn’t stack up to the level of the hardness or tribological properties that the aforesaid (diamond, boron) ceramic particles individually are endowed with. Therefore, there is a scope of further enhancement of the aforesaid properties exhibited by various composites coatings including Ni-W/diamond (NWD) composite deposits by means of obtaining an optimal set of operating conditions or by undertaking experimental variations. Various new ideas for such modifications can be instituted on the Ni-W/diamond composite coatings system towards that end. This could be achieved by undertaking and investigating various modifications on the system and a thorough investigation of the effect of each such variation on the overall properties of the deposits. Variation of Ni-W molar ratio is one such example of modification in operating conditions of deposits in order to render enhanced mechanical properties to the as deposited Ni-W/diamond composite coatings.
Variation of Ni-W molar ratio (during fabrication of Ni-W/diamond composite coatings) can be applied on electrodeposited Ni-W/diamond composite coatings to further enhance the surface, mechanical and tribological properties of the obtained coatings. Liu et al. reviewed the impact of Si/Al molar ratio on the strength behavior of geopolymer derived from various industrial waste [Citation68]. They stated that the optimal Si/Al molar ratio can provide a reliable estimation for the Alkali-activated material (AAM) production. Their work validates the feasibility of using the optimal Si/Al molar ratio to formulate AAM which in turn leads to maintaining stable performances of the AAM. Wang et al. studied the properties of branched polyethyleneimine derivative as a cross-linker for low molar ratio urea-formaldehyde resins [Citation69]. They report that the low molar-ratio UF resin has become a significant adhesive for bonding wood-based panels as it tends to address formaldehyde release problems that had been faced by the industry. Xu et al. analyzed the impact of carbon source and Fe-Ti molar ratio in Fe–Ti–C system on the microstructure and mechanical properties of TiC/Fe composites [Citation70]. The authors reported to have fabricated TiC/Fe composites using hot pressing and combustion synthesis in the Fe-Ti-C system with various carbon sources and variations in molar ratios. They reported that TiC particle size decreased as Fe content increased, and that the shape of the particles changed from spherical to cubic, which can reduce stress concentration between ceramic particles and matrix. This study sheds light on the impact of the the molar ratio of the Fe-Ti-C system and the carbon source on the properties of TiC/Fe composites in useful for enhancing the mechanical properties and microstructure of the deposits. Zhang et al. investigated the impact of crystallization time, batch molar ratios of Al2O3/SiO2 and Na2O/SiO2 on particulate properties of sodalite crystals prepared under room-temperature conditions [Citation71]. They also investigated the effects of crystallization time, batch molar ratios of Al2O3/SiO2 and Na2O/SiO2 on the final crystalline products. They reported that the instance of a high Al2O3/SiO2 molar ratio resulted in the formation of smaller, individual sodalite nanocrystals, which led to the formation of larger, steadily congregated agglomerates. Serhal et al. studied the impact of Co/Fe molar ratio on hydrotalcite catalysts prepared with or without microwave [Citation72]. The authors used the traditional hydrotalcite route to fabricate two series of mixed cobalt-iron oxides namely CoxFe2-HT (without microwave irradiations) and CoxFe2-MW (with microwave irradiation). The authors reported that a higher molar ratio of Co2+ to Fe3+ improves catalytic activity, according to the light-off curves of CoxFe2-HT500 materials. The best catalytic performance was demonstrated by Co6Fe2-HT500, with a Co3+/Fe3+ ratio of 3. Zhang et al. studied the effect of SiO2/Na2O molar ratio on mechanical properties and durability of metakaolin-fly ash blend alkali-activated sustainable mortar incorporating manufactured sand [Citation73]. The authors used different SiO2/Na2O molar ratios and 100% MS to analyze the mechanical performance and durability of alkali-activated sustainable mortar. They reported that, the molar ratio of SiO2/Na2O significantly affects the durability and mechanical performance of MKF3A2MS while, a molar ratio of 1:2, MKF3A2MS had the best mechanical characteristics and durability. Jiang et al. investigated the influence of Si/Zr molar ratio on the sintering and crystallization behavior of zircon ceramics [Citation74]. The findings showed that zircon formation efficiency increased from 1 to 1.2 with increasing Si/Zr molar ratio, but decreased upon increasing Si/Zr molar ratio from 1.2 to 1.3. The authors also reported that the increase in Si/Zr molar ratio leads to an enhancement in grain growth, density and compactness. Tang et al. studied the impact of variations of Si/Al molar ratios on the mechanical and microstructural properties of phosphate-based geopolymers based on the sol-gel method by utilizing the Al2O3-nSiO2 powder made by the sol-gel method to synthesize phosphorus-based geopolymers with various Si/Al molar ratios [Citation75]. They studied the influence of the variations of the Si/Al molar ratios on the synthesis procedure and geopolymer properties and reported an increase in Flexural strength with increasing Si/Al molar ratios which was reported to have peaked at an Si/Al ratio of 2.5 before declining. Deghani et al. investigated the influence of initial SiO2/Al2O3 molar ratio and slag on fly ash-based ambient cured geopolymer properties [Citation76]. This study examines the initial SiO2/Al2O3 molar ratio and the replacement of fly ash with ground granulated blast furnace slag (GGBFS) impact on the characteristics of fly ash-based geopolymers. The geopolymer mixtures created in this study are user-friendly (SiO2/Na2O larger than 1.4) and suitable for making self-compacting geopolymer concrete at room temperature. Results revealed that by increasing the SiO2/Al2O3 ratio, a trend of increasing-decreasing compressive strength was seen. When the SiO2/Al2O3 ratio was 3.37 (Si/Al = 1.68), the highest compressive strength was attained. Kim et al. studied the influence of variation in viscosity of aluminosilicate melts with MgO/CaO molar ratio and the influence of five-fold coordinated aluminum [Citation77]. The authors state that for the CaO-MgO-SiO2 (CMS) and CaO-MgO-Al2O3-SiO2 (CMAS) systems, viscosity variations with increasing MgO/CaO molar ratios have been reported; however, the viscosity variation was not clearly correlated with the change in the melt structure. The authors further report that the aluminosilicate melts’ viscosity is decreased by the formation of Al [Citation5]. Im et al. conducted a research aimed at getting an insight on the mechanical properties of hierarchical porous calcium-silicate-hydrate pastes according to the Ca/Si molar ratio using in-situ synchrotron X-ray scattering and nanoindentation test [Citation78]. The authors investigated mechanical properties of artificial C–S–H pastes with Ca/Si ratios of 0.6–1.2 and the experimental results supported the deformation behavior of the C–S–H paste with various Ca/Si ratios under external loading. The results and inferences of the aforesaid contemporary authors is in sync with the motivation of the current work where we intend to enhance the microstructure, mechanical and tribological properties of the Ni-W/diamond composite deposits along with a possible enhancement in the uniformity of distribution of the co-deposited composite particles on the base matrix in the coatings by varying the Ni-W molar ratio in the plating bath.
These references from the literature clearly establish the role of molar ratio of metal alloy and alloys-based composite coatings in influencing the various mechanical properties, stability tribology, durability of metal and metal alloy-based deposits. There have also been several works by contemporary and past researchers in the Ni-W alloy system. Cheng et al. studied the impact of La2O3 nanoparticle reinforcement on the mechanical and corrosion properties of Ni-W/La2O3 composite coatings [Citation40]. They reported that the hardness value of Ni-W/La2O3 composite coating increased by 38.61% for the samples fabricated with 4 g/L La2O3 concentration while the friction coefficient and corrosion rate decreased by 46.57% and 81.54%, respectively. Xie et al. investigated the microstructure and mechanical properties of Ni-based superalloy joints using amorphous Ni-W-B alloys with high W concentration. brazing filler metal [Citation79]. They reported that the tensile strength of the joints is as high as that of the base superalloy with the reported values of up to 860 MPa at room temperature and 139 MPa at 1253 K. Liu et al. fabricated Ni-W-SiC nanocomposite thin films using pulse current electrodeposition and studied the impact of SiC Nanoparticle content on the properties of the deposited films [Citation80]. They reported that the crystalline sizes decreased as the SiC NPs’ level was changed up to 9 g/L. They also reported an increase in microhardness from 490.2 HV to 881.5 HV with the addition of SiC nanoparticles. The corrosion resistance was also reported to have increased by a factor of more than 5 for the film deposited at 9 g/L concentration of SiC as compared to the films deposited without any SiC. Bathini et al. fabricated composition modulated Ni-W multilayer coatings by pulse current electrodeposition and used reverse pulse current to control the coating thickness [Citation81]. They reported that the multilayer coatings exhibited a significant reduction in the residual stresses while retaining high hardness. They also reported that a low residual stress and effective thermal diffusion through the soft layers resulted in a significantly enhanced wear resistance for the Ni-W multilayer coating fabricated with λ ⁓0.1 µm. Liu et al. studied the impact of zirconium phenylphosphonate reinforcement Ni–W on the wear resistance corrosion resistance of the Ni-W/phenylphosphonate composite coatings [Citation42]. They reported a significant enhancement on the wear and corrosion resistance of the Ni–W/ZrPP composite coating upon the addition of ZrPP in the Ni-W base matrix. The authors also reported that the enhancement in wear resistance was due to the increase in the tight structure of the composite coating and the formation of the friction transfer film.
Diamond is used as a viable reinforcement material used to enhance the microstructure, mechanical and tribological properties of Ni based metal alloy coatings. The effect of the use of diamond reinforcement on the hardness and tribology of Ni deposits as well as Ni based metal alloy coatings as reported by several previous as well as contemporary researchers have been tabulated in for greater clarity on the role of diamond co-deposition on several Ni-based metal and alloy coatings. However, the impact of variation of Ni-W molar ratio on the microstructure, tribology and mechanical properties of Ni-W/diamond composite coatings is still not reported.
Table 1. Effect of diamond reinforcement on Ni-based alloys.
In this work, Ni-W/diamond (Ni-W/diamond) composite coatings were fabricated by varying the Ni-W molar ratio in the plating bath used to fabricate the NWD composite coatings. The Ni-W molar ratio was varied in the range of 0.22–2. This paper aims to analyze and establish the effects of variation of Ni-W molar ratio on the hardness, wear resistance, and microstructure of electrodeposited Ni-W/diamond composite coatings.
2. Experimental procedure
Ni-W/diamond composite coatings were electrodeposited in an ammonia-citrate plating bath. The plating bath volume was 200 ml. The plating bath constituents, Ni-W molar ratio variations and electrodeposition parameters are reported in . The substrate used for the process was a 3 × 2 cm2 commercial low carbon steel, and the deposited area was fixed to 2 × 2 cm2. Diamond particles with an average particle size of 0.9 μm were used during the electrodeposition process. The diamond particles loading was fixed at 10 g/L for all the samples. Diamond particles were dispersed in the plating bath by means of a magnetic stirrer which was set at rpm 200 throughout the deposition process. Diamond particles were incorporated in the Ni-W alloy matrix by means of co-deposition as a composite particle into the alloy matrix to generate Ni-W/Diamond composite coatings. A schematic diagram for the co-deposition of the diamond particles has been shown in . The NWD samples were fabricated with varying Ni-W molar ratio (in the range of 0.22–2) in the plating bath.
Table 2. Plating bath constituents and electrodeposition parameters.
2.1. Sample preparation
Commercial grade low carbon steel was used as substrate for the deposition process. The cathodic set up was an acrylic holder with the substrate attached at the lower edge of the holder. A platinum mesh was used as an anode. The dimensions of the cathodic acrylic holder and the anodic platinum mesh were the same of 12 cm x6 cm with the same size of both cathode and anode being immersed in the electrolytic solution of the plating bath. There was approximately 3.5 cm spacing between the two electrodes. The steel substrate was covered with insulating tape and fixed to the acrylic holder to enable only the desired surface to be used for deposition to be exposed to the electrolytic solution in the plating bath. The dimensions of the surface used for the electroplating of the soft iron substrate were 2 cm × 2 cm. All chemicals used in the experiment were laboratory grade. Before electrodeposition, the plating bath with suspended diamond particles was stirred at 300 rpm for 30 min and then sonicated for another 30 min to make the diamond particles well-dispersed in the electrolyte solution.
The steel plate substrate was polished by a sand paper of various grades (P400, P600, P800, P1200) for 3 min each to obtain smooth surfaces for the deposition process. Subsequently, the substrate was degreased by alkaline sodium hydroxide solution at 60 °C for 10 min, soaked in 14% hydrochloric acid at room temperature for another 10 min, and then rinsed in distilled water. The purpose of soaking the steel plate in 14% HCL was to render the surface suitable for the plating procedure by ensuring that no rust or impurities remained on the surface. During the electroplating process, the electrolyte temperature was controlled at 75 °C [Citation65,Citation66] and the electrolyte was stirred at 150 rpm by a magnetic stirrer.
The samples were cut into 1 × 2 cm2 pieces for cross-sectional study using a low-speed saw and mounted in tiny molds filled with epoxy resins. The samples were ground and polished by a Buehler Ecomet 250 automated grinder/polisher.
2.2. Characterization
2.2.1. XRD analysis
The phase of the Ni-W/B composite coatings was studied by X-ray diffraction (Bruker AXS), with a Cu target, Kα, at a scan rate of 0.2°/min and a scanning angle in the range of 10–100°. Scherrer’s equation [Citation82,Citation83] was used to calculate the grain size of the samples before and after heat treatment. Scherrer’s equation can be represented by the following formula:
(1)
(1)
In EquationEquation (1)(1)
(1) , D is the grain size, λ is the X-ray wavelength (1.5418 Å), β is the corrected peak width at half maximum intensity (FWHM) and θ is the Bragg angle.
2.2.2. SEM analysis
The samples were characterized and investigated in terms of morphology and microstructure by Horiba scanning electron microscope (SEM) with energy dispersive X-ray spectroscopy (EDS) capability embedded into it.
2.2.3. Cross-section preparation
Certain samples were cut into 1 × 2 cm2 pieces for cross-sectional study using a low-speed saw and mounted in tiny molds filled with epoxy resins. The samples were ground and polished by a Buehler Ecomet 250 automated grinder/polisher.
2.2.4. Hardness
The microhardness of the NWB deposits were coating on the surface using Mitutoyo hardness tester with a Vickers’s diamond indenter under a load of 100 g (0.98 N) at seven different locations of the coating. The dwell time for each indentation was 15 s. The Vickers hardness can be calculated in accordance with the formula:
(2)
(2)
In Equation (2), Hv is the hardness in Vickers’s and L. is the applied load and d is the diagonal of the indentation.
The average value of the five measurements (except the maximum and minimum values) has been reported as the hardness of the obtained composite coating.
2.2.5. Surface roughness
Surface roughness was measured using a Taylor Hobson Taylsurf ® PGI Novus surface profilometer. It is a contact profilometer that is utilized as an advanced system for surface finish, contour, 3D, and diameter measurement, providing special advantages for both design and production. The instrument’s design features a class-leading 20 mm gauge range with 0.2 nm resolution, the ability to measure diameter, included angle, in both normal and inverted directions, with the same speed and accuracy, and surface finish (roughness, form, waviness).
2.2.6. Wear
The tribological property of the deposits was investigated by a means of a wear resistance test. The wear test was conducted at an air humidity of 55 ± 5 RH% and a temperature of 25–30 °C using a ball-on-disc tribometer with the sample placed horizontally on a turntable. Zirconium dioxide ball was used as a counter-material under a load of 10 N and 300 m sliding distance. The hardness of the zirconium dioxide ball was ∼1300 Hv. The rotation per minute of the tribometer was fixed at 300 rpm for all the samples. The wear volume was calculated using Archad’s equation [Citation84]. The volume of coating material debris removed during wear is directly proportional to the applied normal load and the wear track distance and inversely proportional to the hardness of the sample under consideration. The wear rate was calculated using the equation below:
(3)
(3)
where Ki is the specific wear rate coefficient, Wvi is the wear volume, L is the applied normal load during the wear test and D is the sliding distance during the wear test.
Before each test, both the sample and the ball counter face were ultrasonically cleaned in acetone for 10 min, and dried by hot air. The anti-wear performance of the films was estimated from the weight loss of the specimens The tests were performed by applying a load of 10 N to a zirconium dioxide ball of diameter 6 mm, speed of 300 rpm, track radius of 5.0 mm for a total sliding distance of 800 m.
3. Results and discussion
and show the surface and cross-section SEM images for the N-W/diamond composite coatings with 10 g/L diamond and 0.15 A/cm2 current density for different Ni-W molar ratios ranging from 0.22 to 2. From all SEM images in and the corresponding cross-section SEM images in , it can be demonstrated that a significant amount of diamond particles appear to be co-deposited all over the coating layer. The diamond particles appear to be uniformly co-deposited into the matrix for the samples fabricated at almost all variations of Ni-W molar ratio as observed in . Das et al. have also reported that the optimal diamond incorporation and distribution on Ni-W base matrix is observed when the Ni-W/diamond composite coatings are fabricated with diamond particle loading of 10 g/L [Citation85]. exhibits the SEM micrograph for the Ni-W/diamond coating fabricated with Ni-W molar ratio of 0.22 and 0.42, respectively. It can be clearly observed that the surface is smooth and no microcracks seem to appear on the surface with fair incorporation of diamond particles in the base Ni-W matrix. However, as the Ni-W molar ratio is increased to 0.5 (), 0.75 () and 1 (), the density of diamond particles appears to get enhanced progressively with increasing Ni-W molar ratio. Upon increasing the Ni-W molar ratio, more amount of NiSO4.6H2O(source of Ni2+ ions) is added to the plating bath as compared to the Na 2WO4.2H2O which is fixed at 53 g/L (source of W6+ ions) as seen in . This leads to an increase in the number of Ni2+ ions in the plating bath as compared to the number of W6+ ions, which in turn translates to an enhanced Ni content in the coatings. Therefore, the increase in Ni-W molar ratio leads to a reduction in W content of the deposits. The increase in the Nickel ions concentration in the plating bath tends to induce an increase in co-deposition of the diamond particles in the base matrix [Citation63,Citation64]. Upon further increasing the Ni-W molar ratio to 2() it appears that the uniformity of diamond incorporation is reduced as compared to the coatings fabricated with lower values of Ni-W molar ratio. This could be because of the formation of a different phase due to significantly higher Ni-W molar ratio which inhibits the co-deposition of diamond particles.
Figure 2. SEM Image for different Ni:W ratio in Ni-W/diamond composite coatings fabricated at 75 °C, 0.15 A/cm2 current density,10 g/L diamond concentration and 8.9 pH (a) 0.22 (b) 0.35 (c) 0.42 (d) 0.75 (e) 1 (f) 2.
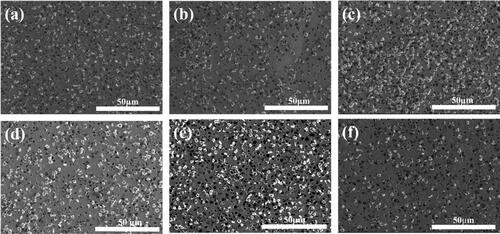
Figure 3. Cross-sectional SEM Image for different Ni:W ratio in Ni-W/diamond composite coatings fabricated at 75 °C, 0.15 A/cm2 current density,10 g/L diamond concentration and 8.9 pH (a) 0.22 (b) 0.35 (c) 0.42 (d) 0.75 (e) 1 (f) 2.
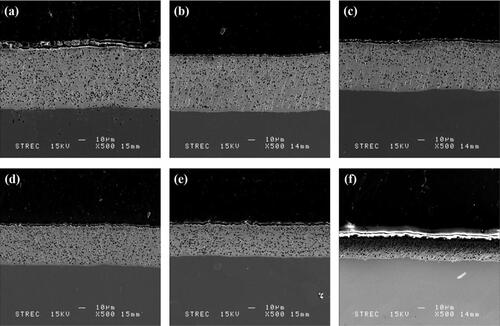
Table 3. Ni and W content in the Ni-W base matrix of the NWD coatings as per the EDS results.
The cross-section SEM images for the Ni-W/diamond coatings fabricated with various molar ratio () also suggests that the diamond incorporation and density tends to get enhanced as the Ni-W molar ratio is increased from 0.22 () to 1 (). Also, the Ni-W/diamond samples fabricated with Ni-W molar ratio of 0.75 and 1 () appears to have a comparatively more uniform and consistent incorporation and distribution of diamond particles throughout the base Ni-W matrix as compared to the samples fabricated with Ni-W molar ratio of 2 (). The coating thickness also appears to decline progressively for the NWD samples fabricated with Ni-W molar ratio of 0.75 (, 1 () and 2 () as compared to the NWD samples fabricated with lower values of Ni-W molar ratio. This is also corroborated by a progressive decline of almost two-fold in the deposition rate of the NWD coatings () as the Ni-W molar ratio is increased from 0.75 to 2 which in turn directly affects the coating thickness thereby, explaining it’s apparent decline in the cross-sectional SEM image.
Figure 4. Deposition rate for different Ni:W ratio in Ni-W/diamond composite coatings fabricated at 75 °C, 0.15 A/cm2 current density,10 g/L diamond concentration and 8.9 pH.
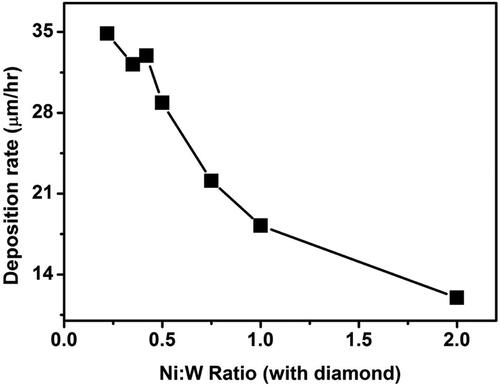
shows the variation of deposition rate of NWD coatings as the Ni-W molar ratio is increased from 0.22 to 2. The deposition rates as obtained were 34.86 µm/h, 32.18 µm/h, 32.94 µm/h, 28.87 µm/h, 22.11 µm/h, 18.23 µm/h, 11.98 µm/h for the NWD samples fabricated with Ni-W ratio of 0.22, 0.35, 0.42, 0.5, 0.75, 1 and 2, respectively. It can be observed that as the Ni-W ratio is increased from 0.22 to 2 the deposition rate tends to decline significantly. This can also be corroborated with the cross-section SEM images of the deposits as the sample fabricated with Ni-W molar ratio of 1 ()) and 2 () appears to be significantly less thick than the sample fabricated with lower Ni-W molar ratios (). This could be due to the reduced W content in the Ni-W base alloy which in turn acts as a base matrix for the deposition of diamond particles. When the Ni-W molar ratio is increased beyond 0.75 in the plating bath, the W content in the electrolyte decreases significantly which in turn leads to reduced tungsten content in the Ni-W alloy matrix thereby, directly affecting the coating thickness and in turn the deposition rate of the coatings.
shows the XRD pattern of Ni-W/diamond coatings for the samples fabricated with Ni-W molar ratio ranging from 0.22 to 2. The peaks for the NWD samples appear to be wider than the pure Ni-W peaks [Citation86]. This is caused due to the co-deposition of diamond particles into the Ni-W matrix causing a reduction in the grain size of Ni-W. The XRD pattern of the Ni-W/diamond samples without heat treatment exhibits a single broad peak at an approximate 2θ angle of 44°, which suggests a face-centered cubic structure corresponding to the (111) plane of Ni. However, as the Ni-W molar ratio is increased gradually increased beyond 0.75, minor peaks appeared at 51.8° and 76.4°, namely, Ni4W (200) and Ni4W (220) peaks, respectively. The Ni (111) peak tended to become less sharp and wider due to reduction in crystallization as the Ni-W molar ratio is increased beyond 0.75. It can also be seen that the intensity of the Ni (111) peak tends to increase as the Ni-W molar ratio is increased up to 2. The emergence of significant Ni4W (200) and Ni4W (220) peaks at Ni-W molar ratio beyond 0.75 suggests that the Ni-W/diamond coatings undergoes a phase transformation at higher Ni-W molar ratio. This could be due to the gradual decline in W content of the Ni-W coatings at higher values of Ni-W molar ratio which in turn leads to phase transformation compared to samples fabricated with lower values of Ni-W molar ratio. The crystalline size of the coatings can be calculated from the width of the Ni (111) peaks, which also exhibits a progressive increase as the Ni-W molar ratio is increased from 0.22 to 2 (), and the peaks tend to be wider. The dispersion of diamond particles in the Ni-W matrix results in strengthening of the Ni-W matrix, which in turn restricts further grain growth at the boundaries for the as-deposited coatings.
Figure 5. XRD Patterns for different Ni:W ratio in Ni-W/diamond composite coatings fabricated at 75 °C, 0.15 A/cm2 current density,10 g/L diamond concentration and 8.9 pH.
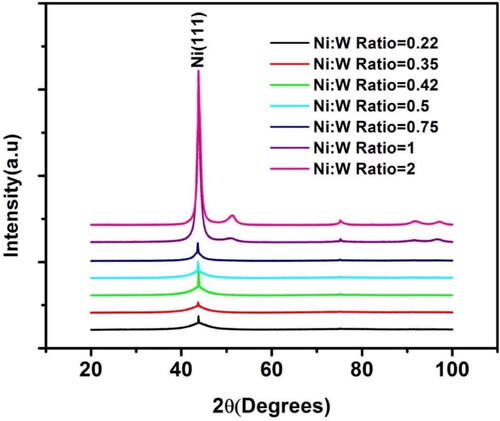
shows the high-resolution SEM micrographs for different Ni:W ratio in Ni-W/diamond composite coatings fabricated at 75 °C, 0.15 A/cm2 current density,10 g/L diamond concentration and 8.9 pH (a) 0.22 (b) 0.35 (c) 0.42 (d) 0.75 (e) 1 (f) 2. It can be observed that the introduction of diamond into the base Ni-W matrix also leads to an enhancement in the number of nucleation sites on the substrate, which undermines crystal growth for the coatings [Citation86,Citation87]. The grain size tends to increase slightly (in the range of 1.5 nm) as the Ni-W molar ratio is increased from 0.22 to 0.75 (). However, a sudden nearly threefold increase in grain size is observed as the Ni-W molar ratio is increased from 0.75 to 1, and the grain size of the Ni-W/diamond deposits prepared with Ni-W molar ratio 1 is approximately 8.55 nm. The co-deposition and incorporation of diamond particles into the base Ni-W matrix tends to inhibit grain growth thereby, rendering the grain size to be slightly lower than the samples where the level of diamond incorporation is relatively lower (). However, the grain size tends to vary in the range of 6.5 nm. The apparent increase in grain size is also evident in the high-resolution SEM images as the Ni-W molar ratio is increased from 0.75 () to 1 () as the grain boundaries appear to be conspicuous for the NWD samples fabricated with Ni-W molar ratio 1 as compared to the NWD samples fabricated with lower values of Ni-W molar ratio. This could be because the grain growth tends to undermine the strengthening effect of the co-deposited diamond particles in the Ni-W matrix while the W content in the plating bath is reduced upon increasing the Ni-W molar ratio.
Figure 6. High resolution (5000x) SEM image for different Ni:W ratio in Ni-W/diamond composite coatings fabricated at 75 °C, 0.15 A/cm2 current density,10 g/L diamond concentration and 8.9 pH (a) 0.22 (b) 0.35 (c) 0.42 (d) 0.75 (e) 1 (f) 2.
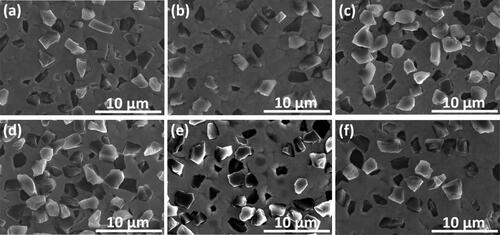
Figure 7. Hardness values for different Ni:W ratio in Ni-W/diamond composite coatings fabricated at 75 °C, 0.15 A/cm2 current density,10 g/L diamond concentration and 8.9 pH.
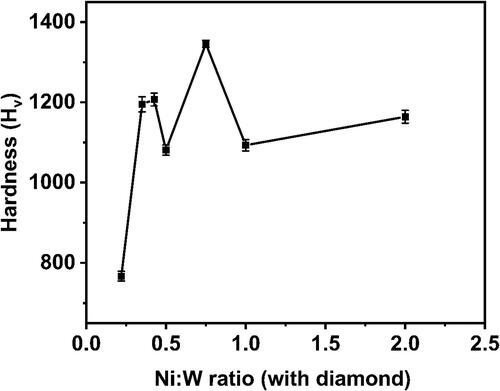
show the comparison of the Hardness, W content and grain size on the Ni-W/diamond composite coatings as the Ni-W molar ratio is varied from 0.22 to 2, respectively. The hardness values are 767 ± 12, 1195 ± 19, 1207 ± 16, 1081 ± 21, 1346 ± 9, 1093 ± 14, 1164 ± 16 for the NWD samples fabricated with Ni-W molar ratio 0.22, 0.35, 0.42, 0.5, 0.75, 1, 2, respectively. The W content was 19.02 at. %, 19.93 at. %, 18.3 at. %, 16.18 at. %, 9.77 at. %, 5.04 at. % and 2.1 at. % for the NWD samples fabricated with Ni-W molar ratio 0.22, 0.35, 0.42, 0.5, 0.75, 1, 2, respectively. The grain size was reported to be 1.9 nm, 2 nm, 2.3 nm, 2.25 nm, 3.4 nm, 8.55 nm and 5.24 nm for the NWD samples fabricated with Ni-W molar ratio 0.22, 0.35, 0.42, 0.5, 0.75, 1, 2, respectively.
Figure 8. W content for different Ni:W ratio in Ni-W/diamond composite coatings fabricated at 75 °C, 0.15 A/cm2 current density,10 g/L diamond concentration and 8.9 pH.
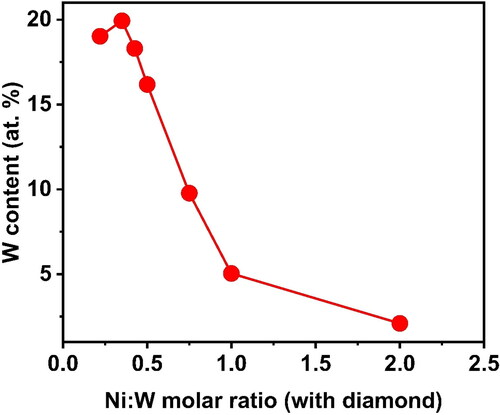
Figure 9. Grain size comparison for different Ni:W ratio in Ni-W/diamond composite coatings fabricated at 75 °C, 0.15 A/cm2 current density,10 g/L diamond concentration and 8.9 pH.
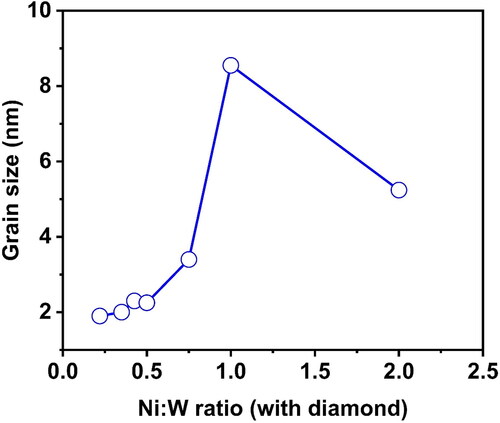
There was a negligible variation in the grain size in the range of 1.5 nm for the samples fabricated with Ni-W molar ratio of 0.22 to 0.75 (). However, there was a sudden enhancement observed in grain size as the Ni-W molar ratio was increased to 1. This could be due to the reduction in W content in the plating bath (upon increasing Ni-W molar ratio) which in turn leads to the decrease in W content in the Ni-W alloy deposits. This in turn tends to enhance the grain growth of Ni-W alloy samples with significantly lesser W content due to lesser inhibition in grain growth. The hardness and the grain size exhibit a gradual increasing trend till the Ni-W molar ratio of 0.75 ( and ).
The co-deposition of diamond particles results in the enhancement of the hardness value of the Ni-W/diamond deposits compared to the hardness values usually associated with Ni-W alloy deposits [Citation88]. This is due to the dispersion and incorporation of diamond particles into the base Ni-W matrix, which in turn tends to strengthen the matrix and inhibits the plastic deformation of the matrix by virtue of uniform incorporation of diamond particles throughout the matrix [Citation89,Citation90]. The increase in hardness of the deposits upon increase in the Ni-W molar ratio in the plating bath is possibly due to the consolidation of the base matrix by means of slight enhancement in the incorporation of the co-deposited diamond particles. Also, the base matrix is reinforced by the co-deposited diamond particles as the W content in the deposits tend to decline almost by a factor of 0.5 as the Ni-W molar ratio is increased from 0.22 to 0.75. When the Ni-W molar ratio is increased to 1, the hardness reports a significant decline in the value of almost 250 Hv (), while the corresponding grain size () is also increased by almost a factor of 2.5. There is also a drastic reduction of W content of the deposits as the Ni-W molar ratio is increased ().
This is due to the possible phase transformations that might have occurred in the samples fabricated at higher Ni-W molar ratio which is evident by the XRD results as shown in leading to a slightly reduced incorporation and compactness of co-deposited diamond particles at the grain boundaries in the base Ni-W matrix. Also, the reduced W content () in deposits tends to enhance the grain growth of the base alloy matrix which in turn results in increase of the grain size () significantly at Ni-W molar ratio of 1. The results reveal that a significant influence of Ni-W molar ratio on the hardness, W content and grain size of the Ni-W/diamond deposits.
exhibits the Ni and W content in the Ni-W base matrix as reported by the EDS element mapping and shows the NiSO4.6H2O and Na2WO4.2H2O content in the plating bath for the various Ni-W molar ratio along with the corresponding Ni and W content in the Ni-W base alloy matrix of the coatings. It can be observed from that as the Ni-W molar ratio is increased the Ni content of the Ni-W alloy matrix reports an increment in value while the W content in the coatings tends to get reduced. This is due to the increase in abundance of the Ni2+ ions in the plating bath due to the increase in the amount of nickel sulphate hexahydrate which acts as a nickel source as compared to the W6+ ions which are derived from the Sodium tungstate dihydrate whose amount is kept constant at 53 g/L in the plating bath.
Figure 10. EDS element mapping Graph for the Ni-W base matrix for the Ni-W/diamond composite coatings fabricated at various Ni-W molar ratios (a) 0.22 (b) 0.35 (c) 0.5 (d) 0.75 (e) 1 (f) 2.
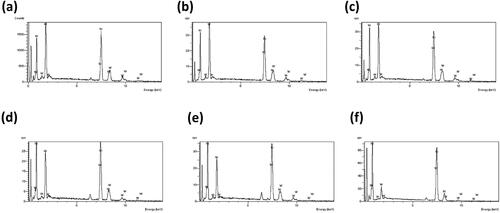
shows the effect of the variation of Ni-W molar ratio on the hardness of Ni-W alloy and Ni-W/diamond composite coatings. It can be clearly observed that the Ni-W samples fabricated with diamond reinforcement report a higher value of hardness for all the samples fabricated with various Ni-W molar ratio. This clearly establishes the effect of diamond reinforcement in the Ni-W alloy matrix on the hardness of the Ni-W/diamond composite coatings [Citation85,Citation87,Citation91]. The enhancement in the hardness value of the Ni-W/diamond coatings tends to increase as the Ni-W molar ratio is increased into the plating bath and the maximum hardness of 1346 Hv (at Ni-W molar ratio 0.75) is almost 550 points higher than the hardness of the corresponding Ni-W samples fabricated without diamond with the same Ni-W molar ratio. This can be directly attributed to the reinforcement of the Ni-W base alloy with diamond particles.
Table 4. Effect of the variation of Ni-W molar ratio on the hardness of Ni-W alloy and Ni-W/diamond composite coatings.
shows the effect of the variation of Ni-W molar ratio on the surface roughness of the Ni-W/diamond composite coatings as the Ni-W molar ratio is increased from 0.22 to 2. The surface roughness was reported to be 1.73 μm, 1.49 μm, 1.13 μm, 1.05 μm, 0.94 μm, 0.87 μm, 0.72 μm for the NWD samples fabricated with Ni-W molar ratio 0.22, 0.35, 0.42, 0.5, 0.75, 1 and 2, respectively. It can be observed that the roughness tends to decline as the Ni-W molar ratio in increased. Upon increasing the Ni-W molar ratio the W content of the deposits undergo a significant decline which in turn leads to more compact grain growth and render the surface of the Ni-W alloy matrix smoother. The reduction in surface roughness could also be due to the enhanced incorporation of diamond particles and the grain refinement of the Ni-W alloy due to the co-deposition of diamond particles at the grain boundaries, thereby inhibiting crystalline irregularities, grain growth and enhancing hardness and yield strength (wear resistance) of the samples which is evident by the declining wear rate of the NWD deposits () as the Ni-W molar ratio is increased till 0.75 [Citation92].
Figure 11. Effect of the variation in Ni-W molar ratio on the surface roughness of Ni-W/diamond composite coatings fabricated at 75 °C, 0.15 A/cm2 current density,10 g/L diamond concentration and 8.9 pH.
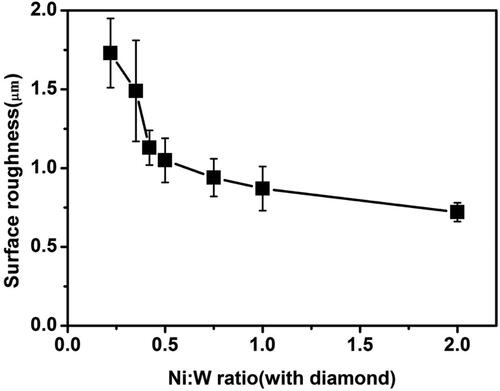
shows the impact of Ni-W molar ratio on the friction co-efficient of the Ni-W/diamond composite coatings. The NWD samples fabricated with Ni-W molar ratio 0.22 exhibits the lowest value of friction co-efficient and also exhibit the maximum range of variation in the friction co-efficient values. The variation in the friction co-efficient also is relatively lower for the NWD samples reporting low wear rate as in case of NWD sample fabricated with Ni-W molar ratio 0.75. The friction co-efficient of the NWD samples fabricated with Ni-W molar ratio 0.22 varied from 0.25 to almost 0.75, whereas the variation was within the range of 0.4 to 0.68 for the NWD sample fabricated with Ni-W molar ratio 0.75. The variation in friction co-efficient was also lower for the NWD samples fabricated with Ni-W molar ratio of 0.42 which is corroborated by the wear rate results which is almost similar for the NWD samples fabricated with Ni-W molar ratio of 0.42 and 0.75. The samples fabricated with Ni-W molar ratio of 0.42 and 0.75 show enhancement in mechanical properties with the hardness and wear rate reported as 1207 Hv, 0.0148 mg/mm2 and 1346 Hv and 0.0125 mg/mm2, respectively. These two aforesaid properties contribute to the relatively lower variations in the values of friction co-efficient as compared to NWD samples fabricated with 0.22 Ni-W molar ratio. Due to its high hardness and low average kinetic friction coefficient, Ni-W/diamond composite coatings fabricated at 0.75 Ni-W molar ratio have shown a significantly enhanced wear resistance performance compared to other ratios of Ni-W for the fabrication of NWD coatings. The highest values of friction co-efficient is recorded for the 0.75 molar ratio Ni-W/diamond samples which is corroborated by a significantly enhanced hardness () and wear resistance () as compared to the other NWD coatings fabricated with various Ni-W molar ratios [Citation93,Citation94].
Figure 12. Effect of the variation in Ni-W molar ratio on the friction co-efficient of Ni-W/diamond composite coatings fabricated at 75 °C, 0.15 A/cm2 current density,10 g/L diamond concentration and 8.9 pH.
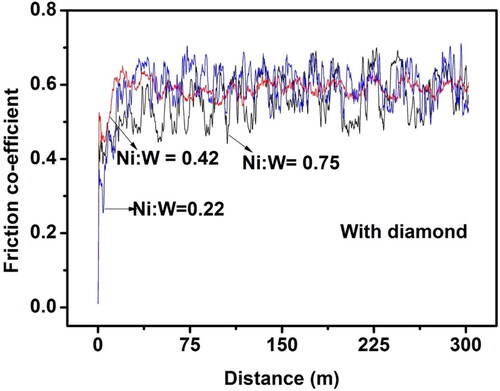
Figure 13. Effect of the variation in Ni-W molar ratio on the wear rate of Ni-W/diamond composite coatings fabricated at 75 °C, 0.15 A/cm2 current density,10 g/L diamond concentration and 8.9 pH.
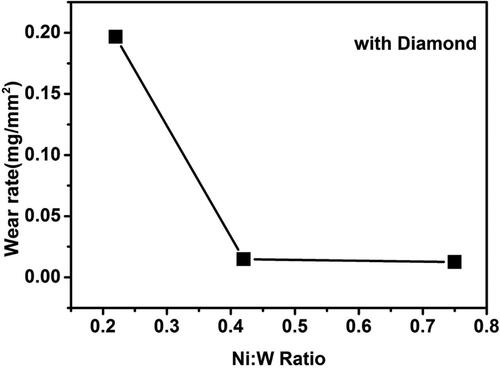
shows the effect of the variation of Ni-W molar ratio on the wear rate of the Ni-W/diamond composite deposits. The wear rate was reported to be 0.1966 mg/mm2, 0.0148 mg/mm2 and 0.0125 mg/mm2 for the samples fabricated with Ni-W molar ratio of 0.22, 0.42 and 0.75, respectively. The wear rate decreases continuously as the Ni-W molar ratio increases from 0.22 to 0.75. This observation is in agreement with the surface roughness data () which suggests that the NWD coating surfaces tend to get smoother as the Ni-W molar ratio is increased. Therefore, it is difficult for the counter material (zirconia ball) with comparable hardness (∼1300 Hv) to impact and remove the coating material at the surface, thereby reducing the wear debris and in turn the wear volume of the deposits which directly results in the reduction of the wear rate [Citation95]. The decline in the W content () of the NWD deposits as the Ni-W molar ratio is increased also tends to enhance the uniformity of incorporation of diamond particles as is evident from the cross-sectional SEM images (). This in turn enhances the compactness and strength of the surface of the deposits, thereby making it difficult for the counter material to cause wear damage on the surface of the coatings. This results in significantly lower wear rate for the NWD samples fabricated with Ni-W molar ratio of 0.75.
4. Conclusions
Ni-W/diamond composite coatings with enhanced mechanical and tribological properties can be fabricated by varying the Ni-W ratio in the plating bath. SEM results demonstrate that the diamond particles can be uniformly co-deposited in the Ni-W matrix. Upon variations in molar ratio results, new phases can be formed, especially Ni-W molar ratio of 1 and 2, which can be determined by XRD results. The hardness of the coatings tends to get enhanced as the Ni-W molar ratio is increased to 0.75 beyond which it exhibits a slight decline in value. This could be due to an increase in uniformity and distribution of co-deposited diamond particles as the Ni-W molar ratio is increased which renders reinforcement to the base Ni-W alloy matrix. It is evident from that the diamond incorporation into the base Ni-W matrix tends to enhance the hardness of the NWD coatings as compared to the lower values of hardness reported for the Ni-W alloy coatings fabricated with the same Ni-W molar ratios as the NWD coatings but without diamond co-deposition. The W content of the coatings reports a successive decline in value as the Ni-W molar ratio is increased from 0.22 to 2. There is a decline in the W content of the deposits nearly by a factor of 10 for the samples fabricated with Ni-W molar ratio of 2. This is due to the decline in the W in the plating bath at higher Ni-W molar ratio which results in lesser W to be deposited with Ni to form Ni-W alloy. The grain size of the coatings varies slightly in the range of 1.5 nm as the Ni-W ratio is increased from 0.22 to 0.75. However, as the Ni-W molar ratio is increased to 1, the grain size reports a nearly 3-fold increase in value. This is due to the decline in uniformity of incorporation of diamond particles in the deposits which promote grain growth by limiting the inhibiting impact of the co-deposited diamond particles on the grain growth. The wear rate reports a significant decline in the value as the Ni-W molar ratio is increased from 0.22 to 0.75. The wear rate for the NWD samples fabricated with 0.75 Ni-W molar ratio is nearly 15 times lesser than that of the NWD samples fabricated with 0.22 Ni-W molar ratio. This is due to the enhancement in the uniformity and incorporation of co-deposited diamond particles (as seen in ) which render strength and reinforcement to the base Ni-W matrix, thereby, making it difficult for the counter material to inflict wear damage on the surface of the NWD deposits. The effects of the variation of Ni-W molar ratio on the hardness and tribology of the Ni-W/diamond composite coatings as discussed above, clearly establish the role of the Ni-W molar ratio on the enhancement of the aforesaid properties of the NWD coatings.
Acknowledgments
M.K. would like to acknowledge the support received from ECPRL at the Faculty of Physics, Chulalongkorn University and also the Energy Storage Lab at the Metallurgical and Material Science Research Institute, Chulalongkorn University.
Disclosure statement
No potential conflict of interest was reported by the authors.
Additional information
Funding
Notes on contributors
Malay Kumar Das
Malay Kumar Das obtained his PhD from Chulalongkorn University, Thailand. He is working as a Postdoctoral Researcher at the Department of Physics, Chulalongkorn University, Thailand. His research focuses on superhard materials and tribology of metals based alloy and composite materials.
Jiaqian Qin
Dr. Jiaqian Qin obtained his PhD in physics from Sichuan University in 2010, and subsequently worked as JSPS Post doctoral Researcher at Ehime University, Japan and faculty member at Chulalongkorn University, Thailand. His research activities are mainly on Energy conversion and storage including Nano catalysts, supercapacitors and batteries. He has authored more than 100 papers in scientific journals and 30 patents. He is the editor board member of Advanced Powder Materials, Scientific Reports and Journal of Metal, Materials and Minerals.
Thiti Bovornratanaraks
Thiti Bovornratanaraks obtained his PhD at University of Edinburgh, UK. He currently works as an Associate Professor at the Department of Physics, Chulalongkorn University. His research activitiesare mainly in Condensed Matter Physics, Materials Science and Solid State Physics. His current interest is “Energy Materials under Extreme Conditions”.
References
- Kim J-H, Lim J-H, Lee W-T, et al. Microstructures and mechanical behavior of Ti-(38 + x)Ni-12Cu (at%) (x = 0 ∼ 3) alloys. J Alloys Compd. 2023;938:168664. doi: 10.1016/j.jallcom.2022.168664.
- Zhou A, Liu X-B, Wang Q, et al. Investigation of nano-tribological behaviors and deformation mechanisms of Cu-Ni alloy by molecular dynamics simulation. Tribol Int. 2023;180:108258. doi: 10.1016/j.triboint.2023.108258.
- Yang Z, Zhang M, Fan L, et al. Towards high mechanical performance Al–Cu–Mg–Fe–Ni alloy: influence of composition, solution treatment and aged process on microstructural evolution and mechanical properties. J Mater Res Technol. 2023;23:2054–2064. doi: 10.1016/j.jmrt.2023.01.166.
- Dai C, Wang J, Pan Y, et al. Tailoring the microstructural characteristic and improving the corrosion rate of Mg-Gd-Ni alloy by heat treatment with different volume fraction of LPSO phase. Corros Sci. 2023;210:110806. doi: 10.1016/j.corsci.2022.110806.
- Li C, Xia F, Yao L, et al. Investigation of the mechanical properties and corrosion behaviors of Ni-BN-TiC layers constructed via laser cladding technique. Ceram Int. 2023;49(4):6671–6677. doi: 10.1016/j.ceramint.2022.10.104.
- Li C, Xia F, Ma C, et al. Research on the corrosion behavior of Ni-SiC nanocoating prepared using a jet electrodeposition technique. J of Materi Eng and Perform. 2021;30(8):6336–6344. doi: 10.1007/s11665-021-05891-1.
- Ma C, Wu F, Ning Y, et al. Effect of heat treatment on structures and corrosion characteristics of electroless Ni–P–SiC nanocomposite coatings. Ceram Int. 2014;40(7):9279–9284. doi: 10.1016/j.ceramint.2014.01.150.
- Park J-H, Hagio T, Ichino R. Improvement in the corrosion resistance of electrodeposited Ni-W alloy by MWCNT co-deposition and prevention of metal-carbon interfacial corrosion by carbide formation. J Alloys Compd. 2023;939:168788. doi: 10.1016/j.jallcom.2023.168788.
- Hou Z, Nie Z, Liu Z, et al. Enhanced mechanical properties of a Ni–W–Al alloy in the as-cast state. Materials Science and Engineering: a. 2023;866:144686. doi: 10.1016/j.msea.2023.144686.
- Ye M-C, Ding T-T, Zhou H, et al. Nucleation and growth mechanism of electrodeposited Ni − W alloy. Trans Nonferrous Met Soc China. 2021;31(6):1842–1852. doi: 10.1016/S1003-6326(21)65621-2.
- Zhong Q, Wei K, Yue X, et al. Powder densification behavior and microstructure formation mechanism of W-Ni alloy processed by selective laser melting. J Alloys Compd. 2022;908:164609. doi: 10.1016/j.jallcom.2022.164609.
- Ramaprakash M, Deepika Y, Balamurugan C, et al. Pulse electrodeposition of nano-crystalline Ni-W alloy and the influence of tungsten composition on structure, microhardness and corrosion properties. J Alloys Compd. 2021;866:158987. doi: 10.1016/j.jallcom.2021.158987.
- Hu J, Zhu Z, Zhu D, et al. Synthesis mechanism of Ni–Co alloy uniting ultrahigh strength with tensile ductility via abrasive-assisted electroforming. Materials Science and Engineering: a. 2022;861:144375. doi: 10.1016/j.msea.2022.144375.
- Matsumoto K, Tachikawa Y, Lyth SM, et al. Performance and durability of Ni–Co alloy cermet anodes for solid oxide fuel cells. Int J Hydrogen Energy. 2022;47(68):29441–29455. doi: 10.1016/j.ijhydene.2022.06.268.
- Man T, Hu C, Lu H, et al. Effect of annealing temperature on microstructure and hardness of Ni-Co alloy coating. Mater Today Commun. 2022;31:103244. doi: 10.1016/j.mtcomm.2022.103244.
- Kada SR, Vaucorbeil A D, Fabijanic D, et al. Work hardening and the scratch resistance of Ni–Co alloys using a rapid prototyping approach. Wear. 2022;510–511:204493. doi: 10.1016/j.wear.2022.204493.
- Li Y, Cai X, Zhang G, et al. Optimization of electrodeposition nanocrytalline Ni-Fe alloy coatings for the replacement of ni coatings. J Alloys Compd. 2022;903:163761. doi: 10.1016/j.jallcom.2022.163761.
- Zhang Z, Tang P, Wen H, et al. Bicontinuous nanoporous Ni-Fe alloy as a highly active catalyst for hydrazine electrooxidation. J Alloys Compd. 2022;906:164370. doi: 10.1016/j.jallcom.2022.164370.
- Xu W, Qiu R, Mao X, et al. One-step fabrication of amorphous Ni-Fe phosphated alloys as efficient bifunctional electrocatalysts for overall water splitting. J Non-Cryst Solids. 2022;587:121598. doi: 10.1016/j.jnoncrysol.2022.121598.
- Zhu M, Yi H, Lu J, et al. Corrosion of ni–fe based alloy in chloride molten salts for concentrating solar power containing aluminum as corrosion inhibitor. Sol Energy Mater Sol Cells. 2022;241:111737. doi: 10.1016/j.solmat.2022.111737.
- Xia F, Li C, Ma C, et al. Effect of pulse current density on microstructure and wear property of Ni-TiN nanocoatings deposited via pulse electrodeposition. Appl Surf Sci. 2021;538:148139. doi: 10.1016/j.apsusc.2020.148139.
- Li Q, Xia F, Liu G, et al. Microstructure and properties of jet pulse electrodeposited Ni-TiN nanocoatings. J of Materi Eng and Perform. 2022;31(11):8823–8829. doi: 10.1007/s11665-022-06909-y.
- Liu T. Synthesis and wear characterization of ultrasonic electrodeposited Ni-TiN thin coatings. Int J Electrochem Sci. 2021;16(1):151028. doi: 10.20964/2021.01.50.
- Karahan İH, Aminifazl A, Golden TD. Effect of TMAB concentration on structural, mechanical and corrosion properties of electrodeposited Ni–B alloys. J Indian Chem Soc. 2022;99(6):100467. doi: 10.1016/j.jics.2022.100467.
- Zhang Y, Shen X. Facile fabrication of robust superhydrophobic coating for enhanced corrosion protection on AZ91 magnesium alloy by electroless Ni-B/GO plating. Surf Coat Technol. 2023;455:129213. doi: 10.1016/j.surfcoat.2022.129213.
- Xu J, Zhang T. On the eutectic transition of undercooled hypoeutectic Ni-B alloy in the differing heat extraction process. Mater Lett X. 2022;13:100128. doi: 10.1016/j.mlblux.2022.100128.
- Venkatakrishnan PG, Karthik V. Structural, morphological and mechanical properties of electroless Ni-B based alloy coatings. Mater Today Proc. 2020;27:2360–2363. doi: 10.1016/j.matpr.2019.09.129.
- Yi P, Qiu H, Wu Y, et al. Drilling fluid adhesion resistance of electroless plating nickel phosphorus (Ni-P) alloy coating deposited on laser-textured surface of bit waterways. Tribol Int. 2023;178:108081. doi: 10.1016/j.triboint.2022.108081.
- Liu C, Yin Y, Li C, et al. Preparation and properties of Ni-P/Bi self-lubricating composite coating on copper alloys. Surf Coat Technol. 2022;443:128617. doi: 10.1016/j.surfcoat.2022.128617.
- Roy S, Mishra BM, Bose GK. Characterization of Ni-P based poly-alloy and composite coatings involving nanoindentation and nanoscratch tests. Mater Today Commun. 2021;29:102991. doi: 10.1016/j.mtcomm.2021.102991.
- Naderi J, Sarhan AAD. Measure and evaluate the hardness of the electrodeposited nickel-phosphorous (Ni-P) thin film coating on carbon steel alloy for automotive applications. Measurement. 2019;139:490–497. doi: 10.1016/j.measurement.2019.03.027.
- Saxena A, Saxena KK, Jain VK, et al. A review of reinforcements and process parameters for powder metallurgy-processed metal matrix composites. Mater Today Proc. 2023. In press. doi: 10.1016/j.matpr.2023.02.227.
- Ren A, Kang M, Fu X. Corrosion behaviour of ni/WC-MoS2 composite coatings prepared by jet electrodeposition with different MoS2 doping concentrations. Appl Surf Sci. 2023;613:155905. doi: 10.1016/j.apsusc.2022.155905.
- Ren A, Kang M, Fu X. Tribological behaviour of ni/WC–MoS2 composite coatings prepared by jet electrodeposition with different nano-MoS2 doping concentrations. Eng Fail Anal. 2023;143:106934. doi: 10.1016/j.engfailanal.2022.106934.
- Wang Q, Luo S, Wang S, et al. Wear, erosion and corrosion resistance of HVOF-sprayed WC and Cr3C2 based coatings for electrolytic hard chrome replacement. Int J Refract Met Hard Mater. 2019;81:242–252. doi: 10.1016/j.ijrmhm.2019.03.010.
- Srivastava M, Anandan C, Grips VKW. Ni–Mo–Co ternary alloy as a replacement for hard chrome. Appl Surf Sci. 2013;285:167–174. doi: 10.1016/j.apsusc.2013.08.025.
- Liu T. Effect of SiC concentration on microstructure and properties of Ni-Co/SiC nanocomposites fabricated by pulse electrodeposition. Int J Electrochem Sci. 2020;15:12103–12121. doi: 10.20964/2020.12.25.
- Liu H, Wang H, Yu W, et al. Effect of TiN concentration on microstructure and properties of ni/W–TiN composites obtained by pulse current electrodeposition. Ceram Int. 2021;47(17):24331–24339. doi: 10.1016/j.ceramint.2021.05.145.
- Xia F, Li Q, Ma C, et al. Preparation and wear properties of ni/TiN–SiC nanocoatings obtained by pulse current electrodeposition. Ceram Int. 2020;46(6):7961–7969. doi: 10.1016/j.ceramint.2019.12.017.
- Cheng X, He Y, Song R, et al. Study of mechanical character and corrosion properties of La2O3 nanoparticle reinforced Ni-W composite coatings. Colloids Surf, A. 2022;652:129799. doi: 10.1016/j.colsurfa.2022.129799.
- Li M-Y, Wang Z-X, Zhang B, et al. Enhancing fatigue resistance of nanocrystalline Ni/Ni-W laminated composites. Scr Mater. 2023;222:114995. doi: 10.1016/j.scriptamat.2022.114995.
- Liu B, Yan S, He Y, et al. Study on wear resistance and corrosion resistance of zirconium phenylphosphonate reinforced Ni–W composite coating. Appl Surf Sci. 2022;603:154483. doi: 10.1016/j.apsusc.2022.154483.
- Zhong J, Zhang S, He Y, et al. Preparation, corrosion resistance and mechanical properties of electroless Ni-W-P-eGO composite coatings. Colloids Surf A. 2022;651:129704. doi: 10.1016/j.colsurfa.2022.129704.
- Bin Humam S, Gyawali G, Amanov A, et al. Microstructure, interface, and nanostructured surface modifications to improve mechanical and tribological performance of electrodeposited Ni-W-TaC composite coating. Surf Coat Technol. 2021;419:127293. doi: 10.1016/j.surfcoat.2021.127293.
- Figuet D, Billard A, Savall C, et al. A comparison between the microstructure and the functional properties of NiW coatings produced by magnetron sputtering and electrodeposition. Mater Chem Phys. 2022;276:125332. doi: 10.1016/j.matchemphys.2021.125332.
- Moradi M J, Moradi G, Heydarinasab A, et al. Preparation and optimization of Ni-Co/Al2O3-ZrO2 films as catalytic coating on microchannels reactor for methane dry reforming. Mater Today Commun. 2023;34:105226. doi: 10.1016/j.mtcomm.2022.105226.
- Rezayat M, Yazdi MS, Zandi MD, et al. Tribological and corrosion performance of electrodeposited Ni–Fe/Al2O3 coating. Res Surf Interf. 2022;9:100083. doi: 10.1016/j.rsurfi.2022.100083.
- Pandiyarajan S, Manickaraj SSM, Liao A-H, et al. Recovery of Al2O3 from hazardous al waste as a reinforcement particle for high-performance Ni/Al2O3 corrosion resistance coating via ultrasonic-aided supercritical-CO2 electrodeposition. Chemosphere. 2023;313:137626. doi: 10.1016/j.chemosphere.2022.137626.
- Sadri E, Bakhshi SR, Heidari M, et al. Mechanical properties and tribological behaviors of ni (5Al)-Al2O3-MoS2-Ag composite coatings at various temperatures. Surf Coat Technol. 2023;456:129251. doi: 10.1016/j.surfcoat.2023.129251.
- Yan L, Yan S, He Y, et al. Preparation, corrosion resistance and mechanical properties of electroless Ni-B/α-ZrP composite coatings. Colloids Surf A. 2022;654:130132. doi: 10.1016/j.colsurfa.2022.130132.
- Song J, He Y, Li H, et al. Preparation of pulse electrodeposited Ni-B/ZrC composite coatings and investigation of their mechanical properties and corrosion resistance. Surf Coat Technol. 2022;447:128845. doi: 10.1016/j.surfcoat.2022.128845.
- Wang J, Xiang C, Sui Q, et al. Facile preparation of ni(OH)2-B/S composite with an embroidered spherical nanosheet structure for high-performance supercapacitors. J Storage Mater. 2022;50:104616. doi: 10.1016/j.est.2022.104616.
- Zhang Y, Zhang S, He Y, et al. Mechanical properties and corrosion resistance of pulse electrodeposited Ni-B/B4C composite coatings. Surf Coat Technol. 2021;421:127458. doi: 10.1016/j.surfcoat.2021.127458.
- Wang Q, Li Q, Zhang L, et al. Microstructure and properties of Ni-WC gradient composite coating prepared by laser cladding. Ceram Int. 2022;48(6):7905–7917. doi: 10.1016/j.ceramint.2021.11.338.
- Yang R, Tian Y, Huang N, et al. Effects of CeO2 addition on microstructure and cavitation erosion resistance of laser-processed Ni-WC composites. Mater Lett. 2022;311:131583. doi: 10.1016/j.matlet.2021.131583.
- Zhang H, Wang J, Chen S, et al. Ni–SiC composite coatings with improved wear and corrosion resistance synthesized via ultrasonic electrodeposition. Ceram Int. 2021;47(7):9437–9446. doi: 10.1016/j.ceramint.2020.12.076.
- Wasekar NP, O'Mullane AP, Sayeed MA, et al. Influence of SiC reinforcement content and heat treatment on the corrosion behavior of pulsed electrodeposited Ni-W alloy metal matrix composite. Materialia. 2022;22:101390. doi: 10.1016/j.mtla.2022.101390.
- Huang P-C, Hou K-H, Hong J-J, et al. Study of fabrication and wear properties of Ni–SiC composite coatings on A356 aluminum alloy. Wear. 2021;477:203772. doi: 10.1016/j.wear.2021.203772.
- Nemane V, Chatterjee S. Evaluation of microstructural, mechanical, and tribological characteristics of Ni-B-W-SiC electroless composite coatings involving multi-pass scratch test. Mater Charact. 2021;180:111414. doi: 10.1016/j.matchar.2021.111414.
- Wani SM, Ahmad B, Saleem SS. Nano-mechanical and nano-tribological characterization of Ni-Co-BN nano-composite coating for bearing applications. Tribol Int. 2023;180:108281. doi: 10.1016/j.triboint.2023.108281.
- Corthay S, Kutzhanov MK, Narzulloev UU, et al. Ni/h-BN composites with high strength and ductility. Mater Lett. 2022;308:131285. doi: 10.1016/j.matlet.2021.131285.
- Huang P-C, Chou C-C, Wang H-T, et al. Tribocorrosion study of electrodeposited NiW alloy/BN(h) composited coatings for piston rings. Surf Coat Technol. 2022;436:128289. doi: 10.1016/j.surfcoat.2022.128289.
- Hong Q, Wang D, Yin S. The microstructure, wear and electrochemical properties of electrodeposited ni-diamond composite coatings: effect of diamond concentration. Mater Today Commun. 2023;34:105476. doi: 10.1016/j.mtcomm.2023.105476.
- Qu S, Zheng K, Gao J, et al. Diamond particles-reinforced ni-based composite coating on Ti6Al4V alloy: microstructure, mechanical, dynamic impact and dry-sliding tribological properties. Surf Coat Technol. 2023;458:129307. doi: 10.1016/j.surfcoat.2023.129307.
- Hou, K-H, Sheu, H-H, Ger, M-D, et al., Preparation and wear resistance of electrodeposited ni–W/diamond composite coatings. Appl Surf Sci. 2014. 308:372–379. doi: 10.1016/j.apsusc.2014.04.175.
- Wang H-T, Sheu H-H, Ger M-D, et al. The effect of heat treatment on the microstructure and mechanical properties of electrodeposited nanocrystalline Ni–W/diamond composite coatings. Surf Coat Technol. 2014;259:268–273. doi: 10.1016/j.surfcoat.2014.03.064.
- Harachai K, Kothanam N, Qin J, et al. Hardness and tribological properties of co-electrodeposited Ni-W-B/B coatings. Surf Coat Technol. 2020;402:126313. doi: 10.1016/j.surfcoat.2020.126313.
- Liu J, Doh J-H, Dinh HL, et al. Effect of si/al molar ratio on the strength behavior of geopolymer derived from various industrial waste: a current state of the art review. Constr Build Mater. 2022;329:127134. doi: 10.1016/j.conbuildmat.2022.127134.
- Wang H, Wang H, Liao J, et al. Technological properties of a branched polyethyleneimine derivative as a cross-linker for low molar ratio urea-formaldehyde resins. Polym Test. 2023;118:107914. doi: 10.1016/j.polymertesting.2022.107914.
- Xu Z-B, Kou S-Q, Yang H-Y, et al. The effect of carbon source and molar ratio in Fe–Ti–C system on the microstructure and mechanical properties of in situ TiC/Fe composites. Ceram Int. 2022;48(20):30418–30429. doi: 10.1016/j.ceramint.2022.06.319.
- Zhang X, Wang K, Huang H, et al. Influences of crystallization time, batch molar ratios Al2O3/SiO2 and Na2O/SiO2 on particulate properties of sodalite crystals prepared under room-temperature conditions. Adv Powder Technol. 2023;34(2):103957. doi: 10.1016/j.apt.2023.103957.
- Serhal CA, El Khawaja R, Labaki M, et al. Influence of co/fe molar ratio on hydrotalcite catalysts prepared with or without microwave. J Solid State Chem. 2022;309:122943. doi: 10.1016/j.jssc.2022.122943.
- Zhang P, Kang L, Zheng Y, et al. Influence of SiO2/Na2O molar ratio on mechanical properties and durability of metakaolin-fly ash blend alkali-activated sustainable mortar incorporating manufactured sand. J Mater Res Technol. 2022;18:3553–3563. doi: 10.1016/j.jmrt.2022.04.041.
- Jiang Z, Xiong T, Bai Z, et al. Effect of si/zr molar ratio on the sintering and crystallization behavior of zircon ceramics. J Eur Ceram Soc. 2020;40(13):4605–4612. doi: 10.1016/j.jeurceramsoc.2020.05.043.
- Tang J, Ji X, Liu X, et al. Mechanical and microstructural properties of phosphate-based geopolymers with varying si/al molar ratios based on the sol-gel method. Mater Lett. 2022;308:131178. doi: 10.1016/j.matlet.2021.131178.
- Dehghani A, Aslani F, Ghaebi Panah N. Effects of initial SiO2/Al2O3 molar ratio and slag on fly ash-based ambient cured geopolymer properties. Constr Build Mater. 2021;293:123527. doi: 10.1016/j.conbuildmat.2021.123527.
- Kim K-H, Sukenaga S, Tashiro M, et al. Variation in viscosity of aluminosilicate melts with MgO/CaO molar ratio: influence of five-fold coordinated aluminum. J Non-Cryst Solids. 2022;587:121600. doi: 10.1016/j.jnoncrysol.2022.121600.
- Im S, Jee H, Suh H, et al. Insight on the mechanical properties of hierarchical porous calcium-silicate-hydrate pastes according to the Ca/Si molar ratio using in-situ synchrotron X-ray scattering and nanoindentation test. Constr Build Mater. 2023;365:130034. doi: 10.1016/j.conbuildmat.2022.130034.
- Xie C, Deng K, Teng J, et al. Microstructural evolution and mechanical properties of Ni-based superalloy joints brazed using a ternary Ni-W-B amorphous brazing filler metal. J Alloys Compd. 2023;960:170663. doi: 10.1016/j.jallcom.2023.170663.
- Liu T, Li H, Xiao Z. Effect of SiC nanoparticle content on the properties of Ni-W-SiC nanocomposite thin films deposited by pulse current electrodeposition. Int J Electrochem Sci. 2023;18(5):100130. doi: 10.1016/j.ijoes.2023.100130.
- Bathini L, Prasad MJNV, Wasekar NP. Compositionally modulated Ni-W multilayer coatings: a facile approach to enhance the tribological performance. Tribol Int. 2023;179:108145. doi: 10.1016/j.triboint.2022.108145.
- Zenou VY, Bakardjieva S. Microstructural analysis of undoped and moderately Sc-doped TiO2 anatase nanoparticles using Scherrer equation and debye function analysis. Mater Charact. 2018;144:287–296. doi: 10.1016/j.matchar.2018.07.022.
- Lim DJ, Marks NA, Rowles MR. Universal scherrer equation for graphene fragments. Carbon. 2020;162:475–480. doi: 10.1016/j.carbon.2020.02.064.
- Liu B, Bruni S, Lewis R. Numerical calculation of wear in rolling contact based on the archard equation: effect of contact parameters and consideration of uncertainties. Wear. 2022;490–491:204188. doi: 10.1016/j.wear.2021.204188.
- Das MK, Li R, Qin J, et al. Effect of electrodeposition conditions on structure and mechanical properties of Ni-W/diamond composite coatings. Surf Coat Technol. 2017;309:337–343. doi: 10.1016/j.surfcoat.2016.11.074.
- Yuan Z, Li B, Miao Y, et al. Synthesis and protective properties of Ni-W alloy strengthened by incorporation of diamond particles. J Alloys Compd. 2021;883:160831. doi: 10.1016/j.jallcom.2021.160831.
- Zhang X, Qin J, Das MK, et al. Co-electrodeposition of hard Ni-W/diamond nanocomposite coatings. Sci Rep. 2016;6(1):22285. doi: 10.1038/srep22285.
- Quiroga Argañaraz MP, Gassa LM, Zelaya E, et al. Chapter 4 – Synthesis, characterization and applications of nanostructured Ni-W alloys with good corrosion resistance and high hardness. In: Hussain CM, editor. Handbook of nanomaterials for manufacturing applications. Amsterdam: Elsevier; 2020. p. 79–110.
- Liu JH, Yan JX, Liu YD, et al. Impact of annealing temperature on the microstructure, microhardness, tribological properties and corrosion resistance of ni–mo/diamond composites. Appl Surf Sci. 2021;541:148367. doi: 10.1016/j.apsusc.2020.148367.
- Rossetti M, Mathiyalagan S, Björklund S, et al. Advanced diamond-reinforced metal matrix composite (DMMC) coatings via HVAF process: effect of particle size and nozzle characteristics on tribological properties. Ceram Int. 2023;49(11):17838–17850. doi: 10.1016/j.ceramint.2023.02.150.
- Zhang X, Qin J, Perasinjaroen T, et al. Preparation and hardness of pulse electrodeposited ni–W–diamond composite coatings. Surf Coat Technol. 2015;276:228–232. doi: 10.1016/j.surfcoat.2015.06.073.
- Cheng M, Jiao L, Yan P, et al. Prediction and evaluation of surface roughness with hybrid kernel extreme learning machine and monitored tool wear. J Manuf Processes. 2022;84:1541–1556. doi: 10.1016/j.jmapro.2022.10.072.
- Shang X, Yu K, Zuo X, et al. Low wear braking material with high friction coefficient. Tribol Int. 2022;173:107608. doi: 10.1016/j.triboint.2022.107608.
- Ghatrehsamani S, Akbarzadeh S, Khonsari MM. Experimentally verified prediction of friction coefficient and wear rate during running-in dry contact. Tribol Int. 2022;170:107508. doi: 10.1016/j.triboint.2022.107508.
- Buj-Corral I, Sender P, Luis-Pérez CJ. Multi-objective optimization of tool wear, surface roughness, and material removal rate in finishing honing processes using adaptive neural fuzzy inference systems. Tribol Int. 2023;182:108354. doi: 10.1016/j.triboint.2023.108354.