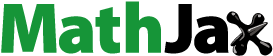
Abstract
Considerable amounts of noncommercial materials generated from thinning treatments remain unattended on the site because the value of small-sized timber is lower than overall thinning operation costs in South Korea. In addition, thinning operations with conventional and mechanized harvesting systems often cause severe physical damage to residual trees. In this study, therefore, we compared and analyzed the harvesting productivity, cost, and residual stand damage between single-tree selection thinning (SST) and mechanized line thinning (MLT) systems on conifer plantation forests. For conventional SST, ground skidding (uphill/downhill) was performed using a tractor winch after manual felling and bucking. The MLT consisted of mechanized felling, downhill shovel logging, and processing with a small-scale grapple-saw for the fourth double row (MLT1) and the third row (MLT2) thinning section. The MLT system was more productive and cost-effective in performing thinning treatment and collecting thinning materials than SST. The MLT1 and MLT2 costs were 81.4% and 70.6% lower than the SST cost ($77.6/m3), respectively. The residual stand damages of the SST (3.4%) were lower than those of MLT1 (4.8%) and MLT2 (21.2%); however, there was no significant difference in residual stand damages between two thinning systems (p > 0.05). Therefore, forest managers should consider the use of MLT system to reduce thinning costs and efficiently produce thinning materials for their thinning operations. However, operators still need to be careful felling and extracting operations to reduce the residual stand damages for thinning treatments.
Introduction
Forest ecosystems offer various environmental benefits, such as maintaining water resources, reducing global warming, and enhancing biodiversity (Behjou Citation2014). Sustainable forest management is needed to maintain the various functions of forest ecosystems, promote the efficient production of forest resources, and reduce negative impacts on the forest environment (Higman et al. Citation2005; Klenner et al. Citation2009; Karlsson et al. Citation2013; Schweier et al. Citation2019). Thinning treatments in forest management can positively affect tree growth (Boncina et al. Citation2007) and increase the value of timber in a final harvesting operation (Emmingham and Elwood Citation2010; Nikooy et al. Citation2020). Furthermore, woody biomass collection from thinning operations can be used to generate electrical power (Karlsson et al. Citation2013), reduce forest fire hazard, prevent insect and disease outbreaks, and improve overall forest health (NIFoS, Citation2019).
A successful reforestation project after the Korean War in South Korea resulted in the increase of forest growing stocks from 23.1 m3/ha in 1981 to 161.4 m3/ha in 2019 (KFS Citation2020). However, ∼74.5% of all forests are under forty-year-old plantations and growing under high density conditions (e.g. 1082 trees/ha) (Korea Statistical Information Service Citation2020). In overstocked dense stand with small-diameter trees, competition for light, water, and nutrients gradually intensifies as they grow, resulting in reduced tree growth and mortality. In addition, these stands generally increase the hazard of forest wildfires. Therefore, forest thinning programs can be implemented to produce high-quality and large trees at final harvesting operation, improve forest health, and reduce forest fire hazards. The Korea Forest Service designated 2.34 million ha of Commercial Forest Promotion Complexes nationwide as of 2018 (0.66 million ha for national forests and 1.68 million ha for private forests) to increase the domestic timber supply and obtain other forest management objectives such as activating the local economy and sustainable wood supply (KFS Citation2018).
For thinning treatments, ground-based harvesting system is cost-effective to treat the overstocked dense stand (Proto et al. Citation2018). The most common ground-based harvesting system has been accompanied by conventional mechanized harvesting system including chainsaw and farm tractors equipped with winches (Stankić et al. Citation2012; Borz et al. Citation2013; Proto et al. Citation2018; Jeong et al. Citation2019), although the harvesting productivity and its cost are strongly correlated with the mechanization level (Borz et al. Citation2013; Spinelli et al. Citation2014). Over the last decade, numerous studies on ground-based harvesting system using fully mechanization (e.g. harvester, forwarder, and skidder) were conducted (Sirén and Aaltio Citation2003; Vitorelo et al. Citation2011; Spinelli et al. Citation2014; Mederski et al. Citation2018; Proto et al. Citation2018; She et al. Citation2018; Cabral et al. Citation2020; Miyajima et al. Citation2020). Thinning costs of conventional mechanized harvesting system (Kim and Park Citation2010; Cho et al. Citation2016; Jeong et al. Citation2019) tend to be higher (e.g. $50./m3, include felling, delimbing, and extraction operation) than that of fully mechanized harvesting system (e.g. $16.6–$18.8/m3) (Spinelli and Magagnotti Citation2010a; Mederski et al. Citation2018).
In thinning operations, there is very important for how to fell and extract small-diameter trees selected from thinning prescription because of their low market values compared to high thinning treatment costs (Sirén and Aaltio Citation2003; Kärhä et al. Citation2004; Spinelli and Magagnotti Citation2010a; Mederski et al. Citation2018; Proto et al. Citation2020). Several past studies were conducted to solve the high thinning treatment cost problems including the efficient production of noncommercial thinning material (Spinelli and Magagnotti Citation2010a; Karlsson et al. Citation2013; Shizuoka Prefecture Citation2020). The selection of appropriate thinning methods could be applicable as a solution for reducing thinning costs. The mechanized line thinning (MLT) system that is often applied to reduce thinning treatment costs and to enhance thinning materials’ production, has shown to be 20% more productive than the single-tree selection thinning (SST) system (Shizuoka Prefecture Citation2020). Furthermore, reduced machine moving time in systematic thinning operations (e.g. corridors, lines, rows and strip thinning) significantly improve harvesting productivity and increase wood production (Karlsson et al. Citation2013).
Machine selection could be the other solution for reducing thinning operation costs (Sirén and Aaltio Citation2003; Kärhä et al. Citation2004; Spinelli and Magagnotti Citation2010b; Mederski et al. Citation2018). This has led to the development of dedicated thinning harvesters which can achieve the same productivity as larger units, but at a lower operating cost (Kärhä et al. Citation2004; Spinelli and Magagnotti Citation2010b). Past studies reported that the use of small sized harvesters (60–118 hp, 30–37 cm of felling capacity) was more cost-effective than the use of medium/large sized harvesters (107–127 hp, 45–60 cm of felling capacity) for thinning operations (Iwaoka et al. Citation1999; Kärhä et al. Citation2004; Spinelli and Magagnotti Citation2010a; Kalēja and Zimelis Citation2019). These results were contributed by the difference of machine costs (purchase price, fuel consumption, etc.) according to different machine sizes. The use of small sized harvesters enabled the reduction of 16–20% in overall thinning operation costs compared to the use of medium/large sized harvests, while there had similar machine productivities (small sized harvester: 13–16 m3/PMH; Productive Machine Hour, medium/large sized harvester: 14–15 m3/PMH) regardless of different machine sizes (Iwaoka et al. Citation1999; Kärhä et al. Citation2004; Kalēja and Zimelis Citation2019). In these reasons, therefore, forest managers could be often considering the use of small sized machine for thinning treatments and it’s also depends on the terrain slope, soil disturbance and fertility. A small-scale grapple-saw (53 hp, 35 cm of felling capacity) is also often applied for thinning operation in South Korea. This machine was developed with a 5-ton excavator base and a grapple-saw head and mainly used for the production of small diameter trees or pulp woods. In addition, the number of 5-ton excavator was extensively used for felling, extracting, and loading in shovel logging in South Korea and machine costs was also relatively cheaper than other small harvesters (Lee et al. Citation2019). Therefore, the low-cost excavator-based grapple-saw could be more efficient than a high-cost small harvester for thinning operation.
Although the main goal of thinning activity is to enhance the growth of residual trees, severe stand damage, such as scaring and gauging, of residual trees often occurs through contact with thinning machinery and falling trees. Therefore, in thinning operations, the residual stand damage needs to be minimized because the wound on the tree stem can cause various problems including insect reproduction, decay fungi infection, and a decline in wind resistance (Reisinger and Pope, Citation1991; Smith et al. Citation1994; Froese and Han Citation2006; Hokkaido Prefectural Research Organization, Citation2020). The frequency and degree of stand damage for residual trees are typically influenced by thinning density, prescription, and thinning method (Han et al. Citation2000; Behjou and Mollabashi Citation2012; Behjou Citation2014; Sirén et al. Citation2015; Tavankar et al. Citation2015; Citation2017; Grzywiński et al. Citation2019; Han et al. Citation2019; Picchio et al. Citation2019a, Citation2019b; Gifu Forest Research Institute, Citation2020; Picchio et al. Citation2020). Thinning systems and equipment applied for thinning treatments highly affect residual stand damage. Residual stand damage reported in a previous study was 5.5% lower in the MLT system (44.5% of residual trees) than in the SST system (50% of residual trees) because trees did not exist on the lines when using the MLT system (Gifu Forest Research Institute, Citation2020). In an SST system using cable yarding, 7.4% and 6.9% of residual trees in felling and yarding operations, respectively, were damaged (Han et al. Citation2019). However, economic analyses of thinning operation costs and the degree of residual stand damage for different thinning systems in South Korea were not performed, and only the thinning productivity, cost, and residual stand damage for the SST systems were evaluated (Han et al. Citation2008; Kim and Park Citation2010; Cho et al. Citation2016; Han et al. Citation2019).
Therefore, this study aimed to evaluate the economic feasibility and impacts on residual trees on the mechanized line thinning systems using a small-scale grapple-saw. The specific objectives of this study were to: (1) compare harvesting productivity and cost including thinning treatments and thinning material collection, and (2) analyze residual stand damage characteristics between the SST system using manual felling and the MLT system using a small-scale grapple-saw.
Materials and methods
Study area
This study was conducted on the Manchurian fir (Abies holophylla) stand of the experimental forest of the National Institute of Forest Science (NIFoS, 37°45′01.85″ N and 127°11′42.47″ E) in Namyangju, Gyeonggi-do, South Korea. The total thinning treatment area was 0.82 ha, which was divided into the SST (0.45 ha) and the MLT (0.37 ha) systems. The study site parameters are outlined in , and the site location is shown in .
Table 1. Description of the study site.
Description of SST and MLT systems
A total of 255 m of designated skidding road was constructed on the study site for SST and MLT operations (). The average skidding trails were 48.9 m, 68.5 m, and 53.2 m in SST, MLT1, and MLT2, respectively.
The SST system is one of the most used thinning systems in South Korea. In the SST system, manual felling using a chainsaw (MS261 STIHL, Waiblingen, Germany) was conducted using the directional felling method to reduce the overlapping of the fallen trees. Then, ground skidding of fallen whole-trees was performed using a tractor equipped with a winch (EGV 65 A TAJFUN, Planina pri Sevnici, Slovenia) and two workers (one operator and one choker setter).
In addition, processing was conducted using a 5-ton excavator-based wood grapple loader (DX55MT-5K DOOSAN Infracore, Incheon, South Korea) and two chainsaws with three workers; a loader operator held one-side of a whole-tree and then lifted it up to help two chainsaw workers delimb and buck the tree (). In the MLT system, fourth double row thinning (MLT1) was mainly applied on the entire thinning stand; however, only one third row thinning (MLT2) was used in the end of the thinning stand. It was because the boundary of this study site was not sufficient to set the additional fourth double row of thinning line. The width of corridor lines in MLT1 and MLT2 were 5.4 m and 3.6 m, respectively. Thinning operations including felling, shovel logging, and processing were performed with a 5-ton excavator-based grapple-saw (GS350 OAK, Cheonan, South Korea, ). In South Korea, small-diameter trees are usually supplied to pulp mills (KFS, Citation2020); therefore, a specific log length was not applied in this study. Hence, an excavator-based grapple-saw without a device measuring log length should be more cost-effective than other mechanized machines, such as a harvester, in thinning with short extraction distance (<70 m). The specifications of the equipment used for SST and MLT are listed in .
Table 2. Descriptions of SST and MLT systems.
Table 3. SST and MLT machine specifications.
Data collection
Before thinning treatments, the diameter at breast height (DBH, cm) and height (m) were measured for all trees on the thinning stand, and only thinning trees were marked to evaluate thinning productivity and cost using the time and motion study method with a stopwatch (Han et al. Citation2008; Cho et al. Citation2015; Choi et al. Citation2018).
To calculate the machine cost, the machine purchase price, durable years, annual operation time, oil consumption, oil price, repair and maintenance cost, interest rate, and labor cost were obtained. Furthermore, to compare and analyze the residual stand damages between SST and MLT systems, the type, shape, and position of the residual stand damages were classified as shown in (Smith et al. Citation1994; Grzywiński et al. Citation2019; Han et al. Citation2019). The residual stand damages with a width >10.16 cm were investigated (Behjou Citation2014). Han et al. (Citation2000) reported that damages with a width of ≤10.16 cm were naturally cured for needle-leaf trees. In addition, the height (m), length (cm), and width (cm) were measured using a measuring rod and ruler. Residual stand damages occurring >5 m was photographed (Smith et al. Citation1994; Han et al. Citation2019).
Table 4. Classification of residual stand damage.
Analysis
Thinning productivity and cost
The thinning system operation times were divided into delay-free cycle time and delay time to calculate the machine utilization (%). Delays were consisting of operational (e.g. waiting for wood to process, hang-up, and re-choking), mechanical (e.g. fueling, maintenance, and repairing machines), personal (e.g. breaks, and personal time) types (Vitorelo et al. Citation2011). The productivity (m3/SMH; Scheduled Machine Hour) was analyzed using the total cycle time including the delay and volume (m3/trees) (Cho et al. Citation2019).
The thinning cost ($/m3) was calculated using the machine cost ($/SMH) and productivity (m3/SMH), as shown in Equationequation (1)(1)
(1) :
(1)
(1)
The machine cost ($/SMH) was calculated using the depreciation, interest, repair and maintenance expenses, fuel price, and labor costs using the Kuratorium für Waldarbeit und Forsttechnik e.V. (KWF) method (Germany) as shown in (Woo et al. Citation1997; Brinker et al. Citation2002; Cho et al. Citation2015; Choi et al. Citation2018; NIFoS, 2018). In this method, depreciation is calculated with considering the annual operating time of machines and also used by the straight-line approach. Furthermore, the harvesting costs for MLT1 and MLT2 systems were compared based on the SST system cost.
Table 5. Cost factors and assumptions used for machine cost calculation using the KWF method.
Residual stand damage
To compare the residual stand damage characteristics of each thinning system, statistical analysis was performed with the height (m), length (cm), and width (cm) of residual stand damages using IBM SPSS Statistics 23.0 (IBM Inc., Armonk, New York, USA). Before analyzing the residual stand damage characteristics of thinning systems, a Shapiro-Wilk normality test was performed using the residual stand damage height, length, and width. The results showed that the residual stand damage height, length, and width of SST, MLT1, and MLT2 did not follow the normal distribution within 95% significance level, except for the height of SST (Froese and Han Citation2006; Spinelli et al. Citation2010; Behjou Citation2014; Han et al. Citation2019; Picchio et al. Citation2019a). Therefore, a Kruskal-Wallis test was performed to analyze the statistical differences in the residual stand damages of thinning systems.
The residual stand damage areas (cm2) of square, narrow rectangular, and wide rectangular areas were calculated by the length and width, and irregular shapes were calculated using Media Cybernetics Image-Pro Plus 6.2 (Media Cybernetics Inc., 1700 Rockville Pike, Suite 240, Rockville, USA). In addition, frequency analysis was performed for the residual stand damage shapes, positions, and heights (m) for thinning systems.
Results and discussion
Thinning productivity and cost
The productivity of the MLT system was greater than that of the SST system. These results were mainly contributed by the lower machine utilization of felling (76.5%) and extracting (47.0%) activities in the SST system.
In the felling operation, a lower SST system productivity (2.0 m3/SMH) was observed due to searching and directional felling among residual trees, compared to that of the MLT system (10.9–11.2 m3/SMH) (). In the SST system, the choking activity for the directional felling was applied to prevent fallen trees from being overlapped and hung-up with residual trees. However, this choking activity increased the felling cycle time with additional activities such as set-up and displacement of the choker setter, reducing felling productivity.
Table 6. Productivity and cost of SST and MLT systems.
The greatest difference in the productivities of the SST and the MLT systems was found during extraction. The extracting productivity was 2.0 m3/SMH in the SST system and 6.1–18.5 m3/SMH in the MLT system (). The low productivity in the SST system was caused by longer operational delay including the moving, set-up, and displacement times of the tractor and pulleys, reducing hang-up problems among residual trees which was previously reported by Jeong et al. (Citation2019). On the other hand, the MLT system had a high machine utilization rate (92.4–94.2%) because there were no residual trees on the corridors disturbing the shovel logging performance.
In our study, the SST system was processed using a conventional processing method, including an excavator-based wood grapple and chainsaw, while the mechanized grapple-saw was solely used in the MLT system. The productivity of mechanized processing (8.1–9.9 m3/SMH) was higher than that of the conventional processing (5.5 m3/SMH) (). The lower productivity of the SST system was a result of the conventional processing performances which were divided into two phases for a processing tree. First, a processing tree was lifted using an excavator-based wood grapple; then, two chainsaws were used to limb and buck the tree.
The system productivities of MLT1 and MTL2 were compared to evaluate the influence of two different line thinning methods. The extracting productivity of MLT1 (18.5 m3/SMH) after applying the fourth double row thinning method was approximately 3.0 times higher than MLT2 (6.1 m3/SMH) after applying the third row thinning method (). During extraction, the influence of corridor width between the remaining rows on was previously demonstrated by Hokkaido Prefectural Research Organization (Citation2020). The productivity in wide areas (20.3 m3/h) were approximately 1.5 times higher than that in narrow areas (13.9 m3/h) for the MLT system using a harvester. Therefore, it is important to secure enough working spaces to enhance the extracting productivity of the MLT system.
SST system cost was $77.6/m3. This result was more expensive than previous study ($51/m3) which was conducted with chainsaw and grapple skidder (Proto et al. Citation2020) (). Proto et al. (Citation2020) reported that wood extraction cost with the grapple skidder was cheaper than farm tractor equipped with a winch. This indicate that it is important to select the machine in SST system for reducing cost.
MLT1 and MLT2 systems cost were $14.8/m3 and $22.8/m3, respectively (). The wide corridor of MLT1 reduced the thinning cost (35%) by offering a sufficient working space for felling and extracting operations compared to the narrow corridor of MLT2 (). MLT1 system cost was cheaper than that of the harvester-forwarder system ($18.6/m3) reported by Spinelli and Magagnotti (Citation2010a). In our study, there was no need for bucking to specific lengths for pulp production so small-scale grapple-saw was more cost-effective than harvester. However, depend on the markets demanded precise log lengths, the harvester would be more preferable than the small-scale grapple-saw.
MLT1 and MLT2 systems cost showed 81.4% and 70.6%, respectively, lower than the SST system ($77.6/m3) (). The MLT system is more cost-effective than the SST system because only one machine and operator were used for felling, extracting, and processing in the MLT system.
The influence of machine size on thinning cost was previously reported by Iwaoka et al. (Citation1999). They determined that there was no significant difference in operation time (small harvester: 45.0 sec./cycle, large harvester: 41.5 sec./cycle) according to the size of machines and suggested that small-sized machines were more competitive in thinning operations due to the low machine cost. Our results revealed that the cost of felling and processing operations using a small-scale grapple-saw ($11.5/m3) was 53.8% cheaper than that of a small harvester (Vimek 404 T5, $24.9/m3) which was demonstrated by Mederski et al. (Citation2018) as shown in . The productivity of a small-scale grapple-saw (6.0 m3/PMH at DBH 18 cm) was 1.4 times higher than a small harvester (4.3 m3/PMH at DBH 13 cm) because of piece-volume-law. We also found that the small-scale grapple-saw (price: $65,152), initially developed for harvesting of small-sized trees, was more cost-effective in the thinning operation compared to a small harvester, owing to its high price ($273,164) ().
Table 7. Productivity and cost of felling and processing operations using a small-scale grapple-saw and small harvester.
Residual stand damage
The result of the Kruskal-Wallis H test for the residual stand damages of thinning systems showed that all variables such as the residual stand damage height, length, and width had no statistically significant differences (p > 0.05) (). Therefore, the residual stand damages of the SST system, the MLT1 and MLT2 systems did not have statistically significant differences. Thus, the damage characteristics of each thinning system were analyzed, including the residual stand damage rate, type, position, height, and area.
Table 8. Kruskal-Wallis H test of residual stand damage between SST and MLT systems.
The residual stand damage rate (%) of MLT2 (21.2% of total residual trees) was higher than that of MLT1 (4.8% of total residual trees) because of a narrow operation space. Therefore, MLT requires a sufficient operation space. The residual stand damage rate (%) of MLT1 was similar to the result of a previous study on MLT (5.5% of total residual trees) in Japan, whereas that of SST (3.4% of total residual trees) was lower than that reported in a previous study (50.0% of total residual trees) () (Gifu Forest Research Institute, Citation2020). The residual stand damage rate of SST was lower than that of MLT because the latter was the initial step and had low experience for thinning operation. On the other hand, SST system has been widely applied by the national units of forest craft workers in South Korea. In addition, shovel logging operation using small-scale grapple-saw in MTL caused higher residual stand damage due to frequent rotation and movement of machines and whole trees in narrow tree spaces compared to ground skidding operation using tractor attached winch in SST.
The damage area of residual stands was high in MLT1 (667.9 cm2/tree) and MLT2 (644.5 cm2/tree) () because residual stand damages were generated in large areas due to the grapple arm during felling and bunching operations. Sirén et al. (Citation2015) also reported that felling operation using a harvester generated residual stand damages mostly by the harvester boom. MLT2 requires long-term monitoring for residual stand growth because the gouge area was large at 413.7 cm2/tree ().
Table 9. Description of residual stand damage by SST and MLT systems.
Most residual stand damages were scars, reflecting 68.7–90.9% of damages in SST, MLT1, and MLT2 systems. This was similar to those reported in previous studies: 67.2–89.6% by Froese and Han (Citation2006), 89.8–95.0% by Behjou (Citation2014), and 67.5–98.5% by Picchio et al. (Citation2019a). The ratio of gouge damages was the highest in MLT2 at 31.3%, which was performed in narrow operation spaces ().
Figure 4. Percentage of total stand damages as related to (a) type, (b) location, (c) height, and (d) shape for SST and MLT systems.
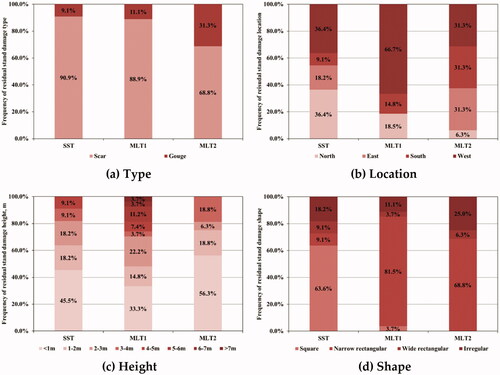
The residual stand damage positions of the SST system using a tractor winch were mostly north and west at 72.8%, and the damage positions of MLT1 and MLT2 using an excavator-based grapple-saw were mostly east and west at 66.7% and 62.6%, respectively (). Previous studies demonstrated that the closer to the skidding road and corridor, the more the residual stand damages occurred (Smith et al. Citation1994; Bembenek et al. Citation2013a,Citation2013b; Allman et al. Citation2016), which was similar to MLT systems in this study.
Kellogg et al. (Citation1986) reported the residual stand damage height ratio of <2.1 m was 82%, and Froese and Han (Citation2006) and Han et al. (Citation2019) reported that the ratio of <3.0 m was approximately 80%. In this study, the residual stand damage to trees with heights of <3 m was 70.4–81.8% for the SST, MLT1, and MLT2 systems (). Therefore, we suggest operators must be cautious (e.g. limiting machine activity and crane zone) to minimize residual stand damages.
The shapes of residual stand damages were mostly square and narrow rectangles in 72.7–85.2% of trees for the SST, MLT1 and MLT2 systems (). In all the thinning systems, the proportion of wide rectangular area was <9.1%. Regarding the wide rectangular shape of residual stand damage, previous studies reported that the width of the residual stand damage was more important than the length. When the width was >10.16 cm, it decayed the residual stand and reduced the volume (Wallis and Morrison Citation1975; Han et al. Citation2000). Hence, long-term monitoring of the residual stand growth is required in the future.
To minimize residual stand damages, detailed harvesting plans, including the use of existing skidding road; skidding road placement, considering the machine capacity and wide operation spaces (Han et al. Citation2000; Sirén et al. Citation2015; Tavankar et al. Citation2017; Picchio et al. Citation2020) and operator still need to be careful felling and extracting operations (Reisinger and Pope Citation1991; Smith et al. Citation1994).
Conclusions
In South Korea, approximately 77% of trees were not collected in all forest thinning programs in 2018 because of the high costs involved. Thus, low-cost thinning systems need to be introduced in place of the conventional SST systems. Furthermore, after thinning operations, the growth and value of residual stands should be studied simultaneously. Therefore, this study compared the productivity and cost between SST and MLT systems and analyzed the residual stand damage characteristics after thinning operations.
When the MLT system was applied, the productivity improved compared to the conventional SST system, enabling low-cost thinning operation. The MLT system using a small-scale grapple-saw with a wide operation space was the most economical. We did not find statistically significant differences in the residual stand damages between the conventional SST and MLT systems. It is believed that to minimize the residual stand damage, comprehensive tree harvesting plans and operator still need to be careful felling and extracting operations. In our study, we suggest that forest managers should consider the use of MLT system to reduce thinning costs and efficiently produce thinning materials for their thinning operations. However, forest managers should also take account of the ecological effects (e.g. soil fertility, biodiversity, and etc.) for their thinning treatments.
Disclosure statement
No potential conflict of interest was reported by the author(s).
Correction Statement
This article has been corrected with minor changes. These changes do not impact the academic content of the article.
Additional information
Funding
References
- Allman M, Allmanová Z, Jankovský M, Ferenčík M, Messingerová V. 2016. Damage of the remaining stands caused by various types of logging technology. Acta Univ Agric Silvic Mendelianae Brun. 64(2):379–385.
- Behjou FK. 2014. Effects of wheeled cable skidding on residual trees in selective logging in Caspian forests. Small-Scale For. 13(3):367–376. doi:https://doi.org/10.1007/s11842-013-9259-x.
- Behjou FK, Mollabashi OG. 2012. Selective logging and damage to unharvested trees in a Hyrcanian forest of Iran. BioResources. 7(4):867–874. doi:https://doi.org/10.15376/biores.7.4.4867-4874.
- Bembenek M, Giefing DF, Karaszewski Z, Mederski PS, Szczepańska, Alvarez A. 2013a. Tree damage in lowland spruce stands caused by early thinnings. Sylwan. 157:747–753.
- Bembenek M, Giefing DF, Karaszewski Z, Mederski PS, Szczepańska Alvarez A. 2013b. Tree damage in lowland spruce stands because of late thinning. Sylwan. 157:892–898.
- Boncina A, Kadunc A, Robic D. 2007. Effects of selective thinning on growth and development of beech (Fagus sylvatica L.) forest stands in south-eastern Slovenia. Ann for Sci. 64(1):47–57. doi:https://doi.org/10.1051/forest:2006087.
- Borz SA, Dinulică F, Bîrda M, Ignea G, Ciobanu VD, Popa B. 2013. Time consumption and productivity of skidding Silver fir (Abies alba Mill.) round wood in reduced accessibility conditions: a case study in windthrow salvage logging form Romanian Carpathians. Ann for Res. 56(2):363–375.
- Brinker RW, Kinard J, Rummer B, Lanford B. 2002. Machine rates for selected forest harvesting machines. Circular 296 (Revised). Auburn (AL): Alabama Agricultural Experimental Station; p. 32.
- Cabral OMJV, Lopes EDS, Rodrigues CK. 2020. Impact of distance between strip roads on productivity and costs of a forwarder in commercial thinning of Pinus Taeda stands. Croat J for Eng. 41(2):1–7. doi:https://doi.org/10.5552/crojfe.2020.592.
- Cho KH, Cho MJ, Han HS, Han SK, Cha DS. 2015. Harvesting cost of tree-length thinning in a Larix leptolepis stands. J Korean for Soc. 104(2):221–229.
- Cho MJ, Cho KH, Jeong EJ, Lee J, Choi BK, Han SK, Cha DS. 2016. Harvesting cost and productive of tree-length thinning in a Pinus densiflora stand using the tower yarder (HAM300). J Environ Sci. 32(2):189–195. doi:https://doi.org/10.7747/JFES.2016.32.2.189.
- Cho MJ, Choi YS, Paik SH, Mun HS, Cha DS, Han SK, Oh JH. 2019. Comparison of productivity and cost between two integrated harvesting systems in South Korea. Forests 10(9). doi:https://doi.org/10.3390/f10090763.
- Choi YS, Cho MJ, Mun HS, Kim DH, Cha DS, Han SK, Oh JH. 2018. Analysis on yarding productivity and cost of tower-yarder based on excavator using radio-controlled double clamp carriage. J Korean for Soc. 107:266–277.
- Construction Association of Korea. 2019. Report of the first half year on the actual condition of construction industry wage in the second half of 2019. Seoul (Korea): Construction Association of Korea; p. 9–10.
- Emmingham WH, Elwood NE. 2010. Thinning an important timber management tool. Corvallis (OR): Pacific Northwest Extension Publication.
- Froese K, Han HS. 2006. Residual stand damage from cut-to-length thinning of a mixed conifer stand in Northern Idaho. West J Appl For. 21(3):142–148. doi:https://doi.org/10.5849/wjaf.12-026.
- Gifu Forest Research Institute. 2020. Efficient work with row thinning. http://www.forest.rd.pref.gifu.lg.jp/rd/rinsan/0005gr.html
- Grzywiński W, Turowski R, Naskrent B, Jelonek T, Tomczak A. 2019. The effect of season of the year on the frequency and degree of damage during commercial thinning in black alder stands in Poland. Forests. 10(8):668. doi:https://doi.org/10.3390/f10080668.
- Han SK, Cho MJ, Baek SA, Yun JU, Cha DS. 2019. The characteristics of residual stand damages caused by skyline thinning operations in mixed conifer stands in South Korea. J for Environ Sci. 35(3):197–204. doi:https://doi.org/10.7747/JFES.2019.35.3.197.
- Han WS, Han HS, Kim YS, Shin MY. 2008. The yarding productivity and cost of cable yarding operation by yarder attached on tractor – using the Chuncheon tower-yarder. J Korean for Soc. 97:641–649.
- Han HS, Kellogg LD, Filip GM, Brown TD. 2000. Scar closure and future timber value losses from thinning damage in Western Oregon. For Prod J. 50(1):36–42.
- Higman S, Mayers J, Bass S, Judd N, Bassbaum R. 2005. The sustainable forestry handbook: a practical guide for tropical forest managers on implementing new standards. London: Earthscan.
- Hokkaido Prefectural Research Organization. 2020. Development of low-cost production system suitable for gentle slopes. https://www.hro.or.jp/list/forest/research/fri/kanko/nempo/h23/02_1keiei.pdf
- Iwaoka M, Aruga K, Sakurai R, Cho KH, Sakai H, Kobayashi H. 1999. Performance of small harvester head in a thinning operation. J for Res. 4(3):195–200.
- Jeong EJ, Cho MJ, Park JM, Cho KH, Yoo YM, Cha DS. 2019. The productivity and cost of yarding operations using a tractor-attached winch in Pinus densiflora stands. J Korean for Soc. 108:574–581.
- Kalēja S, Zimelis A. 2019. Comparison of costs in pre-commercial thinning using medium-sized and small-sized harvesters. In: Rural development 2019: research and innovation for bioeconomy (RD2019): proceedings of the 9th international scientific conference, Agriculture Academy of Vytautas Magnus University, Salaspils (Latvia). p. 253–259.doi:https://doi.org/10.15544/RD.2019.055.
- Kärhä K, Rönkkö E, Gumse SI. 2004. Productivity and cutting costs of thinning harvesters. Int J for Eng. 15(2):43–56.
- Karlsson L, Bergsten U, Ulvcrona T, Elfving B. 2013. Long-term effects on growth and yield of corridor thinning in young Pinus sylvestris stands. Scand J for Res. 28(1):28–37. doi:https://doi.org/10.1080/02827581.2012.702222.
- Kellogg LD, Oslen ED, Hargrave MA. 1986. Skyline thinning a western Hemlock-Sitka spruce stand: harvesting costs and stand damage. Corvallis (OR): Forest Research Lab College of Forestry Oregon State University; p. 21.
- Kim JH, Park SJ. 2010. An analysis of the yarding productivity and cost in forest tending operation. J Korean for Soc. 99(4):625–632.
- Klenner W, Arsenault A, Brockerhoff EG, Vyse A. 2009. Biodiversity in forest ecosystems and landscapes: a conference to discuss future directions in biodiversity management for sustainable forestry. For Ecol Manage. 258:51–64. doi:https://doi.org/10.1016/j.foreco.2009.10.037.
- Korea Forest Service. 2012. Forestry mechanization promotion. Daejeon (Korea): Korea Forest Service; p. 24.
- Korea Forest Service. 2018. Forest resource creation and management, enforcement decree Article 44-2. In Designated as economic forest development area. Daejeon, Korea: Korea Forest Service.
- Korea Forest Service. 2020. Statistical yearbook of forestry. Daejeon (Korea): Korea Forest Service; p. 190–191.
- Korea Forest Service. 2021. Domestic timber supply by use in 2020. https://www.forest.go.kr.
- Korea National Oil Corporation. 2020. Oil price database in July 2019. http://www.knoc.co.kr.
- Korea Statistical Information Service. 2020. National forest resources survey. http://kosis.kr
- Lee EJ, Han SK, Im SJ. 2019. Performance analysis of log extraction by a small shovel operation in steep forests of South Korea. Forests. 10(7):585. doi:https://doi.org/10.3390/f10070585.
- Mederski P, Venanzi R, Bembenek M, Karaszewski Z, Rosińska M, Pilarek Z, Luchenti I, Surus M. 2018. Designing thinning operations in 2nd age class pine stands – economic and environmental implications. Forests. 9(6):335. doi:https://doi.org/10.3390/f9060335.
- Ministry of Government Legislation. 2018. Commodity management act, decree Article 16-2. Sejong (Korea): Ministry of Government Legislation.
- Miyajima RH, Fenner PT, Batistela GC, Simões D. 2020. Technical-economic analysis of grapple saw: a stochastic approach. Croat J Eng. 41(2):219–229. doi:https://doi.org/10.5552/crojfe.2020.681.
- Miyata ES. 1980. Determining fixed and operating costs of logging equipment. St. Paul (MN): U.S. Department of Agriculture Forest Service.
- National Institute of Forest Science. 2018. Tree volume·biomass and harvesting table. Seoul (Korea): National Institute of Forest Science. ISBN 979-11-6019-231-5.
- National Institute of Forest Science. 2019. International symposium on forest operations technology for forest sector circular economy. NIFoS. 833:254.
- Nikooy M, Tavankar F, Naghdi R, Ghorbani A, Jourgholami M, Picchio R. 2020. Soil impacts and residual stand damage from thinning operations. Int J for Eng. 31(2):126–137. doi:https://doi.org/10.1080/14942119.2020.1744954.
- Picchio R, Mederski PS, Tavankar F. 2020. How and how much, do harvesting activities affect forest soil, regeneration and stands? Curr Forestry Rep. 6(2):115–128. doi:https://doi.org/10.1080/14942119.2020.1744954.
- Picchio R, Tavankar F, Bonyad A, Mederski PS, Venanzi R, Nikooy M. 2019a. Detailed analysis of residual stand damage due to winching on steep terrains. Small-Scale For. 18:255-277. doi:https://doi.org/10.1007/s11842-019-09417-5.
- Picchio R, Tavankar F, Nikooy M, Pignatti G, Venanzi R, Lo Monaco A. 2019b. Morphology, growth and architecture response of beech (Fagus orientalis Lipsky) and Maple tree (Acer velutinum Boiss.) seedlings to soil compaction stress caused by mechanized logging operations. Forests. 10(9):771. doi:https://doi.org/10.3390/f10090771.
- Proto AR, Bernardini V, Cataldo MF, Zimbalatti G. 2020. Whole tree system evaluation of thinning a pine plantation in southern Italy. Ann Sil Res. 45(1):44–52. doi:https://doi.org/10.12899/asr-1849.
- Proto AR, Macri G, Visser R, Russo D, Zimbalatti G. 2018. Comparison of timber extraction productivity between winch and grapple skidding: a case study in Southern Italian forests. Forests. 9(2):61. doi:https://doi.org/10.3390/f9020061.
- Proto AR, Sperandio G, Costa C, Maesano M, Antonucci F, Macri G, Mugnozza GS, Zimbalatti G. 2020. A three-step neural network artificial intelligence modeling approach for time, productivity and costs prediction: a cast study in Italian forestry in southern Italy. Croat J Eng. 41(1):15. doi:https://doi.org/10.5552/crojfe.2020.611.
- Reisinger TW, Pope PE. 1991. Impact of timber harvesting on residual trees in a central hardwood forest in Indiana. USA: USDA Forest Service. General Technical Report. NE-148.
- Schweier J, Magagnotti N, Labelle ER, Athanassiadis D. 2019. Sustainability impact assessment of forest operations: a review. Curr Forestry Rep. 5(3):101–113.
- She J, Chung WD, Kim D. 2018. Discrete-event simulation of ground-based timber harvesting operations. Forests. 9(11):683. doi:https://doi.org/10.3390/f9110683.
- Shizuoka Prefecture 2020. Column productivity of thinning. https://www.pref.shizuoka.jp/sangyou/sa-850/18a.pdf.
- Sirén M, Hyvönen J, Surakka H. 2015. Tree damage in mechanized uneven-aged selection cuttings. Croat J Eng. 36:33–42.
- Sirén M, Aaltio H. 2003. Productivity and costs of thinning harvesters and harvester-forwarders. Int J for Eng. 14(1):39–48.
- Smith HC, Miller GW, Schuler TM. 1994. Closure of logging wounds after 10 years. USA: USDA Forest Service. Research Papper. NE-692.
- Spinelli R, Lombardini C, Magagnotti N. 2014. The effect of mechanization level and harvesting system on the thinning cost of Mediterranean softwood plantations. Silva Fenn. 48(1):1–15. doi:https://doi.org/10.14214/sf.1003.
- Spinelli R, Magagnotti N. 2010a. Comparison of two harvesting systems for the production of forest biomass from the thinning of Picea abies plantations. Scand J for Res. 25(1):69–77. doi:https://doi.org/10.1080/02827580903505194.
- Spinelli R, Magagnotti N. 2010b. Performance and cost of a new mini-forwarder for use in thinning operations. J for Res. 15(6):358–364. doi:https://doi.org/10.1007/s10310-010-0193-x.
- Spinelli R, Magagnotti N, Nati C. 2010. Benchmarking the impact of traditional small-scale logging systems used in Mediterranean forestry. For Ecol Manage. 260(11):1997–2001. doi:https://doi.org/10.1016/j.foreco.2010.08.048.
- Stankić I, Poršinsky T, Tomašić Ž, Tonković I, Frntić M. 2012. Productivity models for operational planning of timber forwarding in Croat. Croat J Eng. 33:61–78.
- Tavankar F, Bonyad A, Marchi E, Venanzi R, Picchio R. 2015. Effect of logging wounds on diameter growth of beech (Fagus orientalis Lipsky) trees following selection cutting in Caspian forests of Iran. N Z J Sci. 45:1–7. doi:https://doi.org/10.1186/s40490-015-0052-9.
- Tavankar F, Nikooy M, Picchio R, Bonyad A, Venanzi R. 2017. Effect of logging wounds on Caucasian Alder trees (Alnus subcordata C.A. Mey.) in Iranian Caspian forests. Croat J Eng. 38:73–82.
- Vitorelo B, Han HS, Elliot W. 2011. Productivity and cost of integrated harvesting for fuel reduction thinning in mixed-conifer forest. For Prod J. 61(8):664–674. doi:10.13073.0015-7473-61.8.664.
- Wallis GW, Morrison DJ. 1975. Root rot and stem decay following commercial thinning in western hemlock and guidelines for reducing losses. For Chron. 51(5):203–207.
- Woo BM, Koh DH, Kim JS, Oh KC, Kwon TH, Ma HS, Kim JW, Lee HH, Kim NC. 1997. Forest engineering, 332–334. Seoul (Korea): Gwangilmunhwasa.