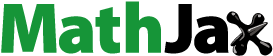
ABSTRACT
Since soon a huge amount of the spent lithium-ion batteries (LIBs) will end up in landfills, their recycling would be essential in reducing potential environmental issues and covering the raised lithium demands. Therefore, recycling LIBs has turned into a hot research topic. While essential developments in our understanding of recycling LIBs have been achieved, a fully optimised flowsheet design, to some extent, remained the in-house know-how of manufacturing plants. Pretreatment (physical separation), as an initial step, unquestionably affects the performance of the entire recycling process of the spent LIBs. Nevertheless, surprisingly no detail was provided through investigations for each step of the physical separation processes applied for recycling spent LIBs based on the published reports. To tackle these issues, this work analyzed approximately all the possible pretreatment processes involved in the safe recycling of LIBs. Detailed assessments of these investigations indicated that several critical points did not consider or reported through original and reviewed research for recycling LIBs. The process optimisation, metallurgical responses of various pretreatment steps, particle size limitation of different pretreatment methods, magnetic, specific gravity, and surface properties of cathode and anode materials, and several other essential variables did not consider or reported through various investigations. Addressing these gaps will pave the way for the design and operation of the recycling LIBs flowsheet.
1. Introduction
In the life cycle assessment (LCA) of lithium-ion batteries (LIBs), various aspects must be considered, including the extraction of raw materials, production, transportation, utilisation, and disposal at the end of the battery's life. Recycling is one of the indispensable factors for the LCA of LIBs. Since the demand for electric vehicles (Evs), cell phones, and other portable devices is markedly increased, the life-cycle thinking of rechargeable batteries would now be undoubtedly necessary [Citation1–3]. However, the recycling of LIBs as the most substantial energy storage devices (rechargeable batteries) needs to be updated. Besides the Li demand, which grows parallel to the rising number of Evs and hybrid electronic vehicles (Hevs) (), the toxicity of the spent LIBs may cause environmental issues that would emerge from the LCA of LIBs and their recycling [Citation1, Citation4].
Figure 1. Relationship between Li demand and various electric vehicle productions [Citation5].
![Figure 1. Relationship between Li demand and various electric vehicle productions [Citation5].](/cms/asset/49589ad4-318a-4806-a22f-84cdcbe23bbd/tetr_a_2248559_f0001_oc.jpg)
For recycling the spent LIBs, it would be crucial to know their structures. Two electrodes mainly construct batteries joined by an electrolyte [Citation6]. Generally, a LIB consists of an anode, a cathode, current collectors, and a separator of Li salts and organic solvents () [Citation7]. LIBs use the Li compound (LiCoO2, LiFePO4, LiMn2O4, LiNiMnCoO2, or LiNiCoAlO2) as the positive electrode and usually graphite as the negative one. Common components in LIBs are the cathode, anode, electrolyte separator, and casing. Li-ion batteries typically contain Li (5–7%), Co (5–20%), Ni (5–10%), 5–10% other base metals (e.g. Cu, Fe, Al), 15% organic compounds, and 7% plastic components [Citation8]. In 2020, the United States Geological Survey (USGS) had been released that about %71 of the produced Li was used for LIB productions, which showed an increase of around 209% compared to 2010. The global Li consumption in 2020 was about 56,000 tonnes [Citation9]. Besides Li, graphite, Ni, and Co are other elements in the LIB structures listed as strategic and critical raw materials by the European Union () [Citation10]. These aspects have enhanced the importance of developing optimised processes for recycling the spent LIBs.
Figure 2. Schematic of the main components of a LIB cell [Citation7].
![Figure 2. Schematic of the main components of a LIB cell [Citation7].](/cms/asset/4417261e-c426-425f-86aa-e59fe280eb14/tetr_a_2248559_f0002_oc.jpg)
Figure 3. EU 2020 critical raw material list [Citation10].
![Figure 3. EU 2020 critical raw material list [Citation10].](/cms/asset/f98d0646-7a9a-49a2-b132-a7f7c7b700b4/tetr_a_2248559_f0003_oc.jpg)
In general, the recycling processes of spent batteries can be divided into two stages: pretreatment and metal extraction [Citation3]. Pretreatment combines various physical separation methods (size reduction, gravity separation, magnetic separation, and froth flotation), which is essential for beneficiation recycling [Citation11]. The products of the pretreatment circuit would be fed to different metallurgical processes (pyrometallurgy or hydrometallurgy) to recover the specific elements from separated parts (metal extraction). In other words, the performance of the pretreatment circuit would affect the overall recycling process efficiency, and optimising each part of the pretreatment flowsheet would minimise the losses of valuable elements in the tailing stream [Citation12, Citation13].
Some researchers have reviewed and examined the published processes for pretreating and recycling LIBs [Citation7, Citation13–24]. However, they mainly presented the general pretreatment story and did not assess the materials and methods of the published original articles based on the processes and flowsheets’ detailed technical and metallurgical points of view. Using unknown terms such as ‘flotation grinding’ is another drawback of those published review articles. In other words, the existing errors within published original articles were rarely highlighted. While in terms of original research articles published about recycling LIBs, several misconceptions, miscalculations, and ambiguous information could be observed, such as the lack of proper comparison between various process conditions (variables) or different separation methods or the absence of reporting main process conditions. For instance, since the feed size is crucial for selecting pretreatment methods, reporting size factors (particle size distribution, d80, etc.) would be the minimum information about feed property for selecting an efficient process. However, it was missed through many documented investigations in this area. Moreover, many published articles did not consider the efficiency of their process flowsheets. They only focused on one separation unit, such as flotation, although other physical methods were used to prepare their flotation feed. To fill these gaps and enhance the process flowsheet assessment, this systematic study provided an extensive overview of various pretreatment methods employed to recycle the spent LIBs and compared them. The main objective is to highlight the most potential metallurgical conditions and practices for different stages of a pretreatment flowsheet and suggest a general flowsheet for such an assessment.
2. Preprocess
Several steps must be considered in recycling LIB before the metal extraction process (hydro or pyrometallurgical processes), called the pretreatment stages. Generally, these stages can be divided into the following sections: discharging, dismantling, crushing, grinding, size classification, and different separation methods.
2.1. Electrical discharge
During the spent LIBs dismantling, their anode and the cathode parts with the remaining electrical capacity could come into contact, leading to a short-circuit current flow and causing an explosion. Thus, the electrical discharging step should be implemented before any recycling processes for safety purposes. In other words, dismantling reduces the electrical charge and reduces fire risk [Citation25]. Although collecting the electrical charge (as an option) can be suggested to reduce the recycling capital cost [Citation26], such a system potentially would be challenging to operate on an industrial scale and won’t be feasible (the recycling plants would be received LIB with different sizes, shapes, and structure which stored in various conditions; therefore, collecting their charges will be costly, and not economically). Thus, the discharging pretreatment is mostly conducted through a thermal or cryogenic process or performed in a salt solution (brine).
Thermal discharging has been considered for recycling LIB with high Ni and Co concentrations since it is easy to operate [Citation27]. Through this process, the LIB would be heated up 100–150 °C for 1 h [Citation28–31] or 400 °C for 17–20 min [Citation32, Citation33] to discharge LIBs before any pretreatment steps. Thermal discharging is irreversible and can damage the electrolyte and release hazardous gas; thus, it is impractical for an industrial-scale discharging process [Citation34]. Using liquid nitrogen to solidify the electrolyte and lower the reactivity of the active components, known as cryogenic discharging, is a safe procedure; however, this method has moderate energy consumption. Injecting oxygen and nitrogen leads to a lower formation of reactive lithium carbonate [Citation35]. It is always performed before cryogenic grinding (known as freezer milling). Although this technique reduces the possible explosion through the LIB disassembling section, its scaling up also would be limited since it requires considerable energy to maintain low temperatures [Citation36, Citation37].
Self-discharging based on immersing in salt solution (brine) is the most recommended and doable process for scaling up [Citation38, Citation39]. Different electrolyte solutions (NaCl, KCl, NaNO3, NaSO4, MnSO4, MgSO4, FeSO4, and ZnSO4) have been explored for this purpose, and NaCl indicated the highest effectiveness for LIB discharging ()[Citation40–42]. Li et al. (2016b) examined different NaCl concentrations (0–20 wt %) for LIB self-discharge and concluded that the 10 wt% NaCl solution had the highest efficiency. They reported that the LiPF6 in the electrolyte might react with water at high NaCl concentrations, form HF, and cause various technical issues [Citation39]. Thus, 5–10 wt% NaCl solution is generally recommended for brine discharging. The process could be time-consuming, and different conditioning times from 5 min to 48 h for self-discharging were considered without reporting any restriction for the remaining charge [Citation33, Citation43–47]. However, a sharp decrease of the residual voltage to 0.5 V was monitored for 10 min in the presence of 5 wt% NaCl, while the complete discharge occurred after 70 min conditioning [Citation48]. It was reported that the discharging step might be unnecessary on an industrial scale for shredding LIBs. However, if the LIBs are shredded without discharging, it is important to perform the process under a well-ventilated system to collect the gases released. Avoiding the discharging step is also a viable option for industrial-scale operations.
Table 1. Brine discharging with various salt solutions.
2.2. Dismantling
After the discharging step, plastics, metal shells, electrolytes, separators, and partial adhesives can be dismantled, which increases the separation efficiency in the next stages of battery recycling [Citation53]. This process could be manual on the laboratory scale, while it mainly occurs after crushing [Citation54, Citation55].
2.2.1. Crushing and size classification
The dismantling material will be subjected to crushing and liberation. Particle size reduction for liberating various parts of the LIBs from each other could be performed by using different comminution circuits. Crushing (which would also be considered a mechanical force) has been used to separate active materials from the current collectors (Al-Cu foils) and other parts. The most examined crushers reported are granulators, shredders, cutting mills, or impact crushers. Since the rotation rate in the granulator crushers is high and their gear blades are fine, the static friction between materials and blades generates a centripetal force. This force holds the material inside the machine. However, the centripetal force decreases by continuing the size reduction process, and fine particles may jump out. Thus, several investigations mainly used shredder and impact with a lower rotation speed [Citation27].
The crushing could be one or several steps. For example, the Recupyl process accomplishes the first crushing step with a low-speed rotary mill, and the second crushing step is implemented with a high-speed impact mill [Citation56, Citation57]. The second crusher could markedly enhance the black mass yield (even by a 15% increase). In contrast, it may also increase the impurities of other fractions like Al-Cu foils in the black mass [Citation58]. Thus, the crushing time needs careful control [Citation47]. The same procedure was reported in other investigations, indicating that two crushing steps could reduce the losses to around 4% during upcoming separation processes [Citation59–61]. Granata et al. (Citation2012) compared the two-step crushing performance of a two-blade rotor crusher versus a combination of a two-blade rotor crusher followed by a hammer crushing. They reported that the latter could maximise the recovery of the electrode powders [Citation62].
Wet and inert gas are typical comminution environments for pretreating the spent LIBs. Different media and grinding conditions are mainly employed to minimise the oxidation of cathode materials (to limit potential chemical interactions and hazardous gas production). The wet process is a low-cost operation mainly used after self-discharging by salt solution. In the wet crushing, water fed into an inlet of the crusher caused the particles to form a slurry that carried the broken particles through a sieve plate. This method enriched each component in the spent LIBs into fine fractions due to the scouring action of the water flow, which may cause the losses of fine products [Citation62]. The wet comminution environment is efficient for simultaneous electrolyte separation; however, it requires effluent cleaning due to the emission of HF gas (Eqs.1) and if the wet comminution environment (water) in the explosion contains calcium ion, fluorine ion can be precipitated as (Eqs.2). It should be noted that HF is typically produced only in lithium iron phosphate batteries (LFP) [Citation25]. The dry process is mainly conducted in a two-stage process. The spent LIBs were first chopped into pieces using a shear crusher (shredder), and the products were subjected to an impact crusher. The dry crushing method could selectively enable the LiCoO2 and graphite electrode materials to be liberated from the Al-Cu foils without over-crushing the other components [Citation63].
(1)
(1)
(2)
(2) Cryogenic grinding (freezer milling) is the act of cooling materials (dry ice, liquid carbon dioxide, liquid nitrogen, and the mixture of CO2 and argon) and then cutting freeze samples into smaller pieces. This process was invented since thermoplastic materials are challenging to crush at ambient temperatures (softened, adhere in lumpy masses, and might clog screens) [Citation35, Citation57, Citation64–66]. Through this process, the crusher is sealed, and the cooling material is inserted to fill it [Citation35, Citation58]. An inert gas environment consumes more resources; thus, it is mostly out of interest, and wet processing is still the first environment chosen based on discharging and downstream processes [Citation27].
After crushing, the electrode materials would be separated from the other components (plastics, metal casing, copper/aluminum current collectors) [Citation67]. This process mostly occurs by sieving (screening), which could be operated with an automatic screening system [Citation29]. Through the process, the coarse particles (including the metallic shell, organic membrane, copper/aluminum foils, and other plastics) are screened and separated from the fine ones (including graphite and the LiCoO2 fine particles, mainly called black-mass). The positive electrodes are mostly structured in layers; thus, they are cut into coarse sheets. The battery ‘black mass’ would be sorted as fine powders [Citation43, Citation54, Citation68, Citation69]. Based on the type of LIB batteries (laptops, EV, etc.), the size of screens (coarse and fine classification) and the number of fractions could be varied (). Shin et al. (Citation2005) reported that an efficient comminution circuit (crushing followed by screening) could almost remove the whole Al-Cu foils from the electrode powder. An efficient screening could reduce the required hydrometallurgical steps to extract valuable metals from the leach liquor [Citation70].
Table 2. Various crushing conditions and different size classifications for treating spent LIB.
‘It was documented that agitation (no technical information was presented) and ultrasonication (with an ultrasonic frequency and electric power of 40 Hz and 100 W, respectively) could not divide the electrode materials from the Al-Cu foils [Citation71].’ Air-classification and pneumatic systems have been recently used to separate metallic shells and organic materials after crushing [Citation52, Citation58]. However, magnetic (for steel materials) or eddy current (for Al-Cu) are mostly used for removing metallic parts of the crushed samples [Citation35, Citation43, Citation56, Citation57, Citation66, Citation72–76].
2.2.2. Thermal treatment (pyrolysis)
Through the dismantling step, heat treatment might be used to decompose and remove organic compounds and their bonds from other parts, such as Polyvinylidene Fluoride (PVDF), from the surfaces of the cathode powder [Citation68, Citation82]. Thermal dismantling could be done in an electric or muffle furnace [Citation68, Citation83]. Zhong et al. (Citation2019) reported that approximately 99.91% of organic electrolytes in spent LIBs could be recovered by low-temperature volatilisation. It was documented that the separation efficiency of the LIB recycling process would be low without thermal treatment. For example, the efficiency of mechanical force for LiFePO4 separation from the Al-Cu foils would not be sufficient without thermal treatment. Since thermal treatment could be done for varied purposes, various size fractions would be subjected to thermal conditioning, and the process may be wisely considered [Citation49]. Unfortunately, several documented investigations did not report the particle size fractions considered for their thermal treatments (). Lee & Rhee. (2022) initially treated LIB samples for 0.5 h at 100–150 oC. Then the samples were disassembled by a shredder, and crushed particles were treated for 1 h at 300–500 oC. In the next stage, carbon and binders burned at 500–900 oC (0.5–2 h) after separating the liberated current collectors from electrode materials, and LiCoO2 resulted [Citation83]. The pyrolytic gas mainly contains light alkenes. Pyrolytic tar mostly has aromatic long-chain alkenes and light alcohols that can be reused as a fuel for pyrolysis, reducing energy consumption and removing environmental pollution [Citation49]. However, this treatment method may release poisonous gases into the environment generated during the thermal reactions of the binder and additives. After pyrolysis, the organic materials (including electrolytes and binders) were evaporated or decomposed to low molecular weight products (liquids or gases). At the same time, the inorganic components (mainly metal oxides) remained as solid residues. In general, to recover organic materials during pyrolysis, the pyrolysis gases are typically passed through a series of condensers and scrubbers to separate and capture the different components. The organic gases can be condensed and collected as a liquid, which can be further processed to extract valuable organic compounds [Citation44, Citation49, Citation84].
Table 3. Thermal treatment conditions for recycling spent LIBs (All experiments were conducted on the laboratory scale).
3. Physical and chemical separation
Several separation steps can be considered for processing various size fractions of the ground LIBs. Therefore, varied flowsheets have been suggested based on separation beneficiation methods (magnetic separation, eddy current, electrostatic, gravity separation, and froth flotation) and the spent LIB types.
3.1. Magnetic separation
Magnetic separation based on spent LIB types could be used in different steps. After vibration screening, magnetic separation has been frequently utilised in the LIB recycling process to remove Fe-containing components like steel casing fragments (steel coating) and Al-Cu electrodes from the other parts [Citation33, Citation35, Citation43, Citation44, Citation57, Citation70, Citation105]. In other words, the cathode, which comprised the active components (lithium manganese oxide, nickel manganese cobalt oxide, and lithium cobalt oxide) and the Al-Cu current collector, could be recovered from the anode, the steel casings, and the plastic packaging [Citation18]. Li et al. (Citation2016) used wet magnetic separation for processing a mixture of virgin cathode materials and could receive over 90% recoveries for each fraction [Citation13]. Bertuol et al. (Citation2006) added one more step of magnetic separation for releasing the strong magnetic material (metallic cases and screen) from weak magnetic material (a powder containing the material from positive and negative electrodes) [Citation59]. Qiu et al. (Citation2021) suggested an efficient and environmentally-friendly fluid-magnetic separation method to recover nickel and cobalt magnetic metals from vacuum reduction products of the spent LIBs. The total recovery rate of the corresponding magnetic metal particles was 98.26%, including 97.91% for nickel and 99.21% for cobalt. These magnetic metal recovery rates were two times higher than the conventional magnetic separation [Citation106].
Although magnetic separation has always been reported for recycling the spent LIB, few investigations have optimised this process or provided detail about recovery, grade, separation efficiency, magnetic intensity, feed rate, process environment (wet or dry), and type of magnet (). Improving this beneficiation step's efficiency was not considered the main focus of the published studies [Citation107, Citation108]. Nevertheless, by recycling the spent LIB in the industrial-scale process, a magnetic separator removes the iron flakes from the powder on the conveyer belt [Citation56, Citation74, Citation109]. For such a purpose, the Recupyl process, which is a high induction magnetic separator, generally would be used for removing the steel components in the coarse fractions [Citation57]. The nonmagnetic product of the process can be fed into an eddy current. The non-conductive parts (plastic film like PVC, etc.), also the conductive particles (Al-Cu foils) are by air table separated into lighter and heavier fractions [Citation25, Citation110].
Table 4. Magnetic separation conditions for recycling the spent LIB.
3.2. Eddy current
Al-Cu foils have proper electroconductivity and generate a high intensity in an alternating magnetic field [Citation34]. Thus, eddy current and electrostatic methods can be adapted for the separation of Al-Cu foils from nonferrous metals and non-metals (>1 mm) [Citation33, Citation43, Citation44, Citation62]. Yamaji et al. (Citation2011) investigated an eddy current to recover Al-Cu foils (−4.8+1.0 mm) at a belt speed of 0.78 m/s. A process for finer-size particles at a lower belt speed is necessary to increase separation efficiency. However, electrostatic separation was also reported for finer-size fractions [Citation25]. Zhang et al. (Citation2014) used the electrostatic separation method for particles in the size range of 0.075–2 mm [Citation77]. In general, few investigations have reported details about the intensity and process conditions when using eddy current or electrostatic separation methods ().
Table 5. Eddy current and electrostatic separation conditions for recycling the spent LIB (All experiments were conducted on a laboratory scale).
3.3. Gravity separation
Various gravity-based separation methods have been introduced for recycling the spent LIBs (). Gravity separations methods can be conducted in different process steps for separating the non-conductive (plastic film like PVC, etc.) and the conductive particles (Al-Cu foils) by classifying them into lighter and heavier fractions [Citation25]. Air and densiometric tables, pneumatic separators, and heavy media have frequently been considered for processing coarse fragments of the spent LIB batteries (mainly larger than 0.25 mm) [Citation35, Citation57, Citation68, Citation77, Citation100, Citation113]. After crushing, the first air-classification can recover the heavy components of the LIB modules, such as the casing materials, the electric conductors, and the steel screws. For different dense materials with the same particle sizes, the zigzag-sifting would be enabled a separation via the density by a cascade of the cross-flow sifting. The second air-classification via the zigzag sifter can also remove the non-valuable materials from the current collector foil fragments [Citation18, Citation58]. Zhu et al. (Citation2021) introduced a novel pilot-scale pneumatic separator for recycling the flaky Al-Cu particles with a size range of 0.25–2 mm by airflow rates set to 70–110 m3/h. They indicated that the minimum suspension velocities declined with particle size (for smaller particles), and the separation could be done at a relatively low airflow rate [Citation52]. Other gravity separation methods include air-based separation methods such as heavy liquid (using a heavy organic liquid such as tribromomethane or diiodomethane), and external centrifuge fields like a Falcon and Knelson [Citation105, Citation114–116] can also be utilised for processing materials even below 0.5 mm. Gravity separation would be feasible since graphite density is different from LiCoO2. However, the separation efficiency of all these methods would be decreased by reducing the feed particle size under the same operating parameter [Citation114]. Unfortunately, process optimisation, recovery, grade, the specific gravity of each fraction, and the efficiency of the gravity separation process were mainly not reported in the original published document ().
Table 6. Various gravity separation methods were used for recycling the spent LIB (All experiments were conducted on a laboratory scale).
3.4. Froth flotation
3.4.1. Particle size
Froth flotation has been mostly examined to separate graphite as a hydrophobic part of the spent LIBs from the hydrophilic parts (mainly LiCoO2). In the mineral processing plants (the main host of beneficiation processes), conventional flotation separation has been practically introduced for a limited size range (−25+150 µm). However, based on the hydrophobicity levels of different LIB parts, flotation could be recommended to separate a wider size range from millimetre to micron [Citation73]. After crushing, Sloop et al. (Citation2020) used flotation to recover plastics and foils from the black mass. In the next step, they also considered flotation for graphite recovery (−45μm). In general, a significant positive correlation exists between particle size and flotation separation efficiency; unfortunately, this fact was ignored in many documented investigations, and particle size distribution or d80 of flotation feeds is mostly not measured or present in the published documents.
3.4.2. Reagents
Besides particle size, several factors such as reagents (collectors, depressants, frothers, activators) and different pretreatment methods can remarkably change flotation separation efficiency. Since flotation has mostly been examined for graphite separation from LiCoO2, kerosene and n-dodecane were the most recommended collectors used in various investigations (). Sadly, no details were provided for the flotation separation of other parts, and only it was mentioned that the xanthate family could be used to separate pure Cu from Al foils [Citation117]. Generally, exploring the effect of different reagents and their dosage optimizations has not been the main core of reported flotation tests in the reported studies, which caused several contradictions. Zhan et al. (Citation2018) indicated that the flotation by using kerosene as the collector could improve the process recovery compared to a collectorless process [Citation113]. In contrast, Zhao & Zhong. (Citation2020) illustrated that the highest LiFePO4 recovery was achieved through a collectorless flotation process [Citation32]. Kim et al. (Citation2004) explored the effect of kerosene dosages (0–3200 g/t) on the flotation separation of graphite from LiCoO2 and showed that increasing the collector dosage may negligibly affect the process recovery [Citation100]. By exploring different published investigations, the average amount of collector that has been used varies mainly between 200 and 300 g/t (). Methyl Isobutyl Carbinol (MIBC) is the most popular frother used in several studies, mainly 100–150 g/t (). Zhao & Zhong. (Citation2020) examined different MIBC concentrations (5–25 g/t) and indicated that by increasing to 10 g/t, the graphite recovery was increased initially, and then after, it decreased. They offered different MIBC dosages for rougher and scavenger flotation steps (10 and 5 g/t, respectively) [Citation32]. The application of depressants through the process was limited to starch, amylum, sodium humate (NaA), and Na2SO3 [Citation32, Citation49]. Zhao & Zhong. (Citation2020) indicated that the optimal depressant for the reverse flotation of LiFePO4 is amylum (optimal dosage 100 g/t) [Citation32]. Conditioning time for various reagents is mainly missed to report; however, it was mostly between 2–5 min [Citation29, Citation46, Citation52, Citation118, Citation119]. Exploring surface properties of particles by using different analytical instruments (XPS ‘X-ray photoelectron spectroscopy’, TOF-SIMS ‘Time-of-Flight Secondary Ion Mass Spectrometry’, FTIR ‘Fourier-transform infrared spectroscopy’, Zeta potential measurement, etc.) would help to understand better various effective factors such as iso-electric points, and adsorption mechanisms through the process. This information could remarkably improve reagent selection and flotation separation efficiency.
Table 7. Various LIBs flotation conditions for processing black mass and their representative results (All experiments were conducted on a laboratory scale).
3.4.3. Pulp and hydrodynamic conditions
Pulp chemistry and hydrodynamic conditions (such as impeller speed and airflow rate) are other factors that drastically impact the flotation performance; however, they did not deeply examine for the flotation investigation of the spent LIBs. In many cases, the pH of the process was not documented or optimised through the process (). Zhao & Zhong (Citation2020) indicated that in the presence of kerosene and MIBC, by increasing the pH from 2 to 6, the grade and recovery of LiFePO4 decreased. While after that, the separation efficiency had been started to increase to pH 10, which hit its maximum. They reported the low flotation efficiency in acidic conditions might be due to the disappearance of the hydrophilic layer on the LiFePO4 surface. But in alkaline environments, hydrophilicity on the surface increased, which led to higher recovery. It should be noted part of the carbon will be absorbed by the ferric hydroxide flocculate when the alkalinity is too strong. This phenomenon would decrease the hydrophilicity of the surface of LiFePO4 after pH 10 [Citation32]. Various investigations documented that the examined pH for N-butyl xanthate was 2, and for Kerosene and N-dodecane was 9 or 10. On the other hand, the airflow rate and the impeller speed varied in different conditions (no optimisation was reported). The solid percentage has been reported at approximately 40 g/l in all published works; therefore, the effect of various solid percentages also needs to be addressed. In a rare study, Kim et al. (Citation2004) showed that the flotation efficiency would decrease by increasing the solid percentage to over 10% [Citation100].
3.4.4. Flotation preprocess
All mentioned pretreatment methods may change particle properties (size and surface), directly affecting the flotation performance. During the fabrication of the electrode material and the charge/discharge process, a layer of organic impurity composite is attached to the surface of LiCoO2 and graphite. This layer must be removed to facilitate their separations by flotation. In other words, separating particles with the same surface properties by flotation and without any preprocess is difficult. Therefore, before flotation, a heat treatment (pyrolysis) or smooth grinding can be carried out to remove the organic binders that attach to the surface of the active materials [Citation47, Citation51, Citation52, Citation80, Citation91, Citation100, Citation122]. By removing the outer organic compounds layer, the enrichment ratio in flotation could increase from 1.16 to 3.24 [Citation77].
In general, pyrolysis can improve liberation efficiency and shorten the crushing time [Citation44]. Different factors can be considered for optimising the pyrolysis process, such as temperature () and pyrolysis time [Citation33, Citation43]. As pyrolysis temperature rises, residual oils are removed, and the wetting difference between cathode and anode materials increases. In other words, as the pyrolysis temperature increases, the difference in contact angle between the anode and cathode materials increases [Citation44]. Zhan et al. (Citation2020) reported the initial increase in the surface hydrophobicity of the aged anode due to increasing the pyrolysis temperature might be attributed to removing hydrophilic layers on surfaces [Citation80].
Table 8. Products of Froth Flotation with and without Pyrolysis treatment at different temperatures [Citation80] (experiments were conducted on a laboratory scale).
Nevertheless, the PVDF binder decomposed and decreased its generated surface hydrophobicity at high temperatures (more than 450 oC). In other words, the surface hydrophobicity of the cathode composite materials decreases monotonically when the process temperature increases. However, suppose the pyrolysis time is getting longer than the optimal time. In that case, the sintering phenomenon of pyrolytic carbon may occur, which causes the cathode material to overflow and reduce flotation recovery [Citation43, Citation51].
After the pyrolysis, some pyrolysis residues may remain on the surface of particles, potentially changing the hydrophilicity of materials. Zhang et al. (Citation2018) reported that after pyrolysis at 500 °C, some residual pyrolysis products stocked on the surface of pyrolytic electrode particles, reducing the flotation recovery. Therefore ultrasonic has been employed to remove them. Pyrolysis-ultrasonic-assisted flotation could improve the LiCoO2 flotation grade from 67.25 to 93.89%, while the recovery increased from 74.62 to 96.88% [Citation46].
As mentioned, besides size reduction, grinding can also be used to remove the binder on the surface of the electrode material, and its final products could be subjected to flotation separation. Compared to pyrolysis, the main advantages of grinding for removing adhesives are its lower pollution and required investment. It should be pointed out that over-grinding may lead to ultrafine particle production and decrease the process efficiency [Citation29, Citation115, Citation120]. Since the conventional mechanical grinding process might be ineffective for removing hard organic binders (such as PVDF), the cryogenic grinding process was also recommended at low temperatures in a chamber cooled by liquid nitrogen [Citation29]. This process can change spherical graphite to a scaly layered structure, expose new surfaces, and improve separation efficiency [Citation29, Citation120]. Yu et al. (Citation2020) compared the contact angles of single-electrode grinding (graphite or LiCoO2) and grinding their mixture. They concluded that short-term low-speed grinding treatment could effectively increase the wettability difference between LiCoO2 and graphite [Citation115]. Zhang et al. (Citation2020) used wet milling (ball mill) to remove pyrolysis residues on the surface of pyrolytic cathode materials. They could improve flotation metallurgical responses (grade from 94.72 to 94.97% and recovery from 83.75 to 91.35%) [Citation44].
Fenton consisted of FeSO4 (0.1 mol/L) and H2O2 (0.1 mol/L) solutions and deionised water, which also can be used to remove the organic film layer after crushing and screening and prevent the prevention of toxic gases during its thermal removal. It was reported that surface modification by Fenton can improve the recovery of LiCoO2 from 5 to 60% through its reverse flotation. The formation of an inorganic compound layer (Fe(OH)3) on the surface of LiCoO2 in an alkali solution enhanced its hydrophilic properties [Citation50, Citation119]. The optimal recommended Fenton mixture for such removal could be a 1:120 the ratio at a 75:1 liquid – solid ratio [Citation50].
4. Flowsheets
Some investigations have presented a complete flowsheet for recycling the spent LIB batteries [Citation25, Citation33, Citation43, Citation52, Citation58, Citation68, Citation100, Citation110, Citation113, Citation123]. Gratz et al. (Citation2014) proposed a process that involves crushing the material using two steps (shearing and impact crushing) followed by discharging. The discharged material is then classified into three fractions based on size. The fraction above 2 mm mainly contains an aluminum shell, which can be processed using an airflow system. The fraction between 2 and 0.5 mm contains a large amount of Al-Cu and can be processed using electrostatic separation. The fraction between 0.5 and 0.075 mm, which contains a mix of graphite and LiCO2, may require further grinding before being subjected to flotation separation (). However, it should be noted that the efficacy of the proposed process has not been evaluated in terms of process efficiency, grade or recovery of valuable elements. [Citation105].
Figure 4. A simplified flowsheet for processing the spent LIB batteries [Citation105].
![Figure 4. A simplified flowsheet for processing the spent LIB batteries [Citation105].](/cms/asset/e4482660-1577-4f8f-a45c-4e5e48053121/tetr_a_2248559_f0004_oc.jpg)
According to Zhu et al. (Citation2021), the recycling process for spent LIBs involves a two-step crushing process followed by pneumatic separation. After that, the material is fed to a hammer mill and subjected to size classification through sieving with a mesh size of 0.25 mm. Fine particles are then subjected to a heat treatment at 500 °C for two hours to decompose the organic binders. The cathode and anode materials are separated through flotation, as recommended in their study [Citation52]. Similarly, Zhang et al. (Citation2019) suggested a similar circuit with magnetic and eddy current separation techniques for removing metallic shells from steel and aluminum shells. Part of the cathode and anode could be directly crushed and sieved in the next step, while another part should be treated using pyrolysis. Although different flowsheets could be proposed for recycling various spent LIBs, these studies lacked metallurgical response evaluations (grade and recovery) for all the process flowsheets. The investigations mainly focused on the recovery or grade of a specific element using a particular separation method without considering the entire process flowsheet's efficiency. As a result, the other pre or post-processing steps were not optimised or documented correctly [Citation33].
5. Summary
Efficiently recycling Lithium-ion batteries (LIBs) requires a stepwise process that mechanically separates materials based on their liberation size and composition. These separations are known as pretreatment stages and are critical for successful recycling. To reduce fire risk, electrical discharging should be performed at the initial stage of pretreatment using a 5–10 wt.% NaCl solution. The discharged material can then be crushed and size classified in the next stage using shredders, granulators, or impact crushers. Two shredding stages are recommended, and the resulting material should be screened (1 mm) into coarse and fine particles, including active materials, current collectors, and other pieces. Pyrolysis can further improve liberation efficiency and reduce crushing time.
After the screening, magnetic separation can separate cathode materials and the Al-Cu current collector from the anode part. The nonmagnetic product can be fed into an eddy current, and the non-conductive components (e.g. PVC) and conductive particles (e.g. Al-Cu foils) can be separated into lighter, heavier fractions using an air table. The coarse size goes through magnetic separation to remove Fe components, and eddy current separations remove metallic shells. Froth flotation can then be used to separate graphite, a hydrophobic component of spent LIBs, from hydrophilic components (mainly LiCoO2), operating at pH 9–10 when using kerosene or N-dodecane as a collector and MIBC as a frother. Before surface treatment by regrinding, pyrolysis can remove organic materials (binders) and liberate them from the surface of all materials. This process improves flotation efficiency by separating ionic parts from graphite. The optimal pyrolysis treatment can be conducted at 500°C for 1 h. Flotation can also be used to separate Cu from Al foils. These steps can serve as a general flowsheet for recycling spent LIBs, but for each LIB type, the process's steps must be optimised by considering different conditions, and all critical variables should be highlighted ().
6. Future investigations
The current investigation's main focus for recycling LiBs is the second stage of the process (stages 1. Pre-treatment, 2. Extraction), while pre-treatment would have a fundamental effect on the upstream processes and need substantial improvement. Through LiB investigations, several fundamental points must be considered: reporting particle size parameters (PSD, d80, etc.), considering unit separator limitations and optimising all enrichment stages, and calculating metallurgical responses (grade, recovery, separation efficiency, etc.) for the whole process (not only for one unit operation).
Numerous variables have to be measured and assessed through the LiB recycling pre-treatment stage that needs to be addressed for potential future investigations. Exploring the effect of various particle size ranges on different separation units, the influence of varied magnetic intensity and roll speed during the magnetic separation, and testing varied feed rate, feeding methods, excitation frequency, and splitter setting if eddy current was recommended for the flowsheet. Various enhanced gravity separators, such as Falcon and Knelson, can be examined for the process. Examining various flotation hydrodynamic parameters (impeller tip speed, air flow rate, etc.) and different flotation reagents (collectors, depressants, frothers, etc.). Flotation separation also requires basic surface studies, such as assessing the effects of pyrolysis on the surface properties of anode and cathode materials (zeta potential measurement, contact angle, surface chemistry analyses, etc.). Moreover, several assisting methods can be examined for improving the efficiency of pre-treatment steps, such as using grinding aids, considering ultrasonic pre-treatment, or implementing nanobubbles during the flotation separation.
Disclosure statement
No potential conflict of interest was reported by the author(s).
Data availability statement
All data used during the study appears in the submitted article.
Additional information
Funding
Notes on contributors

Gholamreza Khodadadmahmoudi
Gholamreza Khodadadmahmoudi (MS.c) He is a graduate student in mineral processing engineering at the University of Teheran with an interdisciplinary research background in extractive metallurgy, hydrometallurgy, bio-hydrometallurgy, froth flotation, material cycle, recycling, and waste management. His primary research goal is to put a curb on the environmental impact of mineral/metal processing industries and establish more sustainable routes.
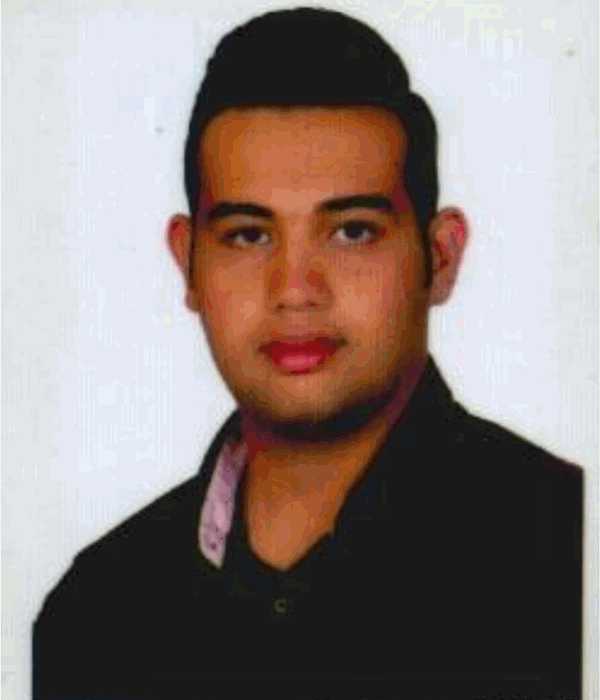
Kourosh Javdan Tabar
Kourosh Javdan Tabar (MS.c) Graduate student. His research work is mineral processing. He has worked on some projects and papers in the field of recycling using environmental methods.
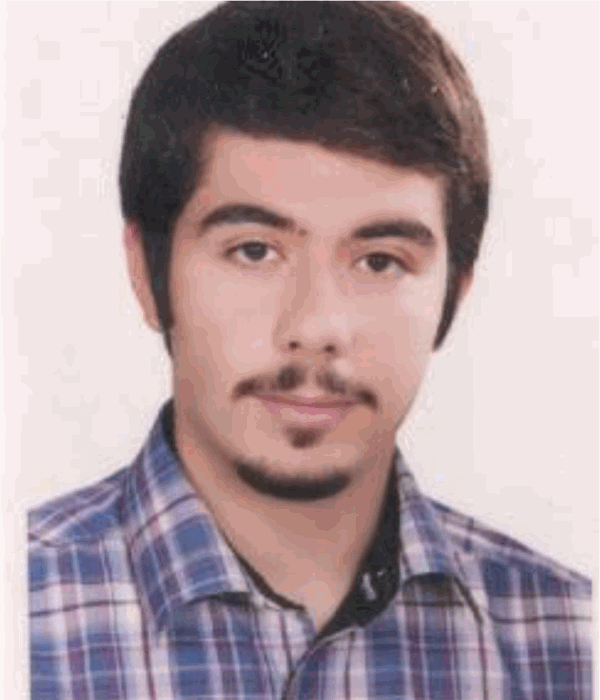
Amir Hesam Homayouni
Amir Hesam Homayouni (MS.c) Graduate student. His research work is mineral processing. He has worked on some projects and papers in the field of recycling using environmental methods.
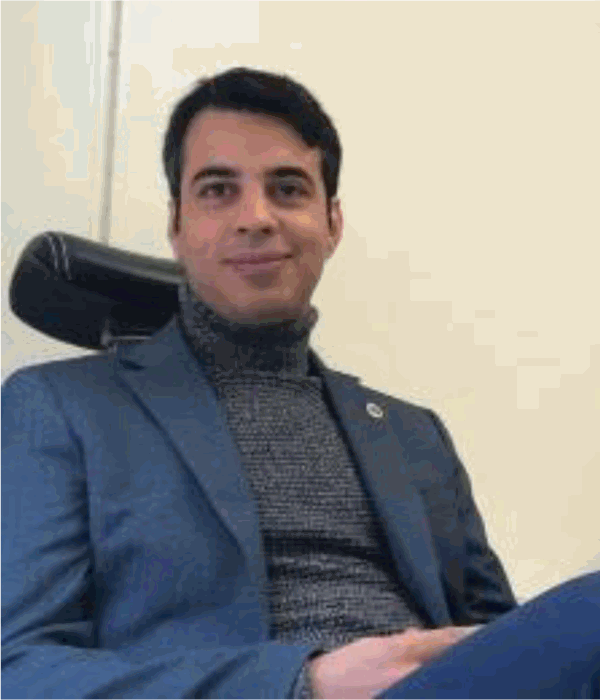
Saeed Chehreh Chelgani
Saeed Chehreh Chelgani As a mineral processor (associate professor), he is working at the Lulea University of Technology. Throughout collaborative works in mineral separation and metal extraction (industry and academia), he has gained a lot of experience in R&D, industrial teamwork, and management. He has received the most prestigious awards in Canada and other countries (OGS, NSERC, Outstanding researcher & reviewer). He is an editorial board member of some well-known journals within his research area.
References
- Hendrickson TP, Kavvada O, Shah N, et al. Life-cycle implications and supply chain logistics of electric vehicle battery recycling in California. Environ Res Lett. 2015;10:014011.
- Melin HE. The lithium-ion battery end-of-life market–a baseline study. World Economic Forum; 2018.
- Meireles N. (2020). Separation of anode from cathode material from End of Life Li-ion batteries (LIBs).
- Xu J, Thomas H, Francis RW, et al. A review of processes and technologies for the recycling of lithium-ion secondary batteries. J Power Sources. 2008;177:512–527.
- Zeng X, Li J, Ren Y. Prediction of various discarded lithium batteries in China. Boston, Ma, USA, Publisher; 2012.
- Pal P, Ghosh A. Dynamics and relaxation of charge carriers in poly (methylmethacrylate)-based polymer electrolytes embedded with ionic liquid. Physical Review E. 2015;92:062603.
- Latini D, Vaccari M, Lagnoni M, et al. A comprehensive review and classification of unit operations with assessment of outputs quality in lithium-ion battery recycling. J Power Sources. 2022;546:231979.
- Shao G, Hanaor DA, Wang J, et al. Polymer-derived SiOC integrated with a graphene aerogel as a highly stable Li-ion battery anode. ACS Appl Mater Interfaces. 2020;12:46045–46056.
- Summaries MC. Mineral commodity summaries; USGS unnumbered series. Reston (VA): US Geological Survey; 2021:200.
- Raw Materials Information System. https://rmis.jrc.ec.europa.eu/?page = crm-list-2020-e294f62022.
- Velázquez-Martínez O, Valio J, Santasalo-Aarnio A, et al. A critical review of lithium-ion battery recycling processes from a circular economy perspective. Batteries. 2019;5:68.
- Harper G, Sommerville R, Kendrick E, et al. Recycling lithium-ion batteries from electric vehicles. Nature. 2019;575:75–86.
- Sommerville R, Shaw-Stewart J, Goodship V, et al. A review of physical processes used in the safe recycling of lithium ion batteries. Sustainable Mater Technol. 2020: e00197.
- Yao Y, Zhu M, Zhao Z, et al. Hydrometallurgical processes for recycling spent lithium-ion batteries: a critical review. ACS Sustain Chem Eng. 2018;6:13611–13627.
- Asadi Dalini E, Karimi G, Zandevakili S, et al. A review on environmental, economic and hydrometallurgical processes of recycling spent lithium-ion batteries. Miner Process Extr Metall Rev. 2021;42:451–472.
- Chagnes A, Pospiech B. A brief review on hydrometallurgical technologies for recycling spent lithium-ion batteries. J Chem Technol Biotechnol. 2013;88:1191–1199.
- Gu F, Guo J, Yao X, et al. An investigation of the current status of recycling spent lithium-ion batteries from consumer electronics in China. J Cleaner Prod. 2017;161:765–780.
- Kim S, Bang J, Yoo J, et al. A comprehensive review on the pretreatment process in lithium-ion battery recycling. J Cleaner Prod. 2021;294:126329.
- Liu C, Lin J, Cao H, et al. Recycling of spent lithium-ion batteries in view of lithium recovery: a critical review. J Cleaner Prod. 2019;228:801–813.
- Lv W, Wang Z, Cao H, et al. A critical review and analysis on the recycling of spent lithium-ion batteries. ACS Sustain Chem Eng. 2018;6:1504–1521.
- Makuza B, Tian Q, Guo X, et al. Pyrometallurgical options for recycling spent lithium-ion batteries: a comprehensive review. J Power Sources. 2021;491:229622.
- Yu D, Huang Z, Makuza B, et al. Pretreatment options for the recycling of spent lithium-ion batteries: a comprehensive review. Miner Eng. 2021;173:107218.
- Zheng X, Zhu Z, Lin X, et al. A mini-review on metal recycling from spent lithium ion batteries. Engineering. 2018;4:361–370.
- Pinegar H, Smith YR. Recycling of end-of-life lithium-ion batteries, part II: laboratory-scale research developments in mechanical, thermal, and leaching treatments. J Sustainable Metall. 2020;6:142–160.
- Yamaji Y, Dodbiba G, Matsuo S, et al. A novel flow sheet for processing of used lithium-ion batteries for recycling. Resour Process. 2011;58:9–13.
- Sonoc A, Jeswiet J, Soo VK. Opportunities to improve recycling of automotive lithium ion batteries. Procedia cIRP. 2015;29:752–757.
- Hu Q, Xu L. An overview on lithium-ion batteries recycling processes. Arau, Malaysia, Publisher; 2021.
- Lisbona D, Snee T. A review of hazards associated with primary lithium and lithium-ion batteries. Process Saf Environ Prot. 2011;89:434–442.
- Liu J, Wang H, Hu T, et al. Recovery of LiCoO2 and graphite from spent lithium-ion batteries by cryogenic grinding and froth flotation. Miner Eng. 2020;148:106223.
- Granata G, Moscardini E, Pagnanelli F, et al. Product recovery from Li-ion battery wastes coming from an industrial pre-treatment plant: lab scale tests and process simulations. J Power Sources. 2012;206:393–401.
- Feng X, Sun J, Ouyang M, et al. Characterization of penetration induced thermal runaway propagation process within a large format lithium ion battery module. J Power Sources. 2015;275:261–273.
- Zhao C, Zhong X. Reverse flotation process for the recovery of pyrolytic LiFePO4. Colloids Surf A. 2020;596:124741.
- Zhang G, Du Z, He Y, et al. A sustainable process for the recovery of anode and cathode materials derived from spent lithium-ion batteries. Sustainability. 2019;11:2363.
- Bi H, Zhu H, Zu L, et al. A new model of trajectory in eddy current separation for recovering spent lithium iron phosphate batteries. Waste Manage. 2019;100:1–9.
- Tedjar F, Foudraz J-C. (2010). Method for the mixed recycling of lithium-based anode batteries and cells. Google Patents.
- Dorella G, Mansur MB. A study of the separation of cobalt from spent Li-ion battery residues. J Power Sources. 2007;170:210–215.
- Richa K, Babbitt CW, Gaustad G, et al. A future perspective on lithium-ion battery waste flows from electric vehicles. Resour Conserv Recycl. 2014;83:63–76.
- Wang X, Gaustad G, Babbitt CW. Targeting high value metals in lithium-ion battery recycling via shredding and size-based separation. Waste Manage. 2016;51:204–213.
- Li J, Wang G, Xu Z. Generation and detection of metal ions and volatile organic compounds (VOCs) emissions from the pretreatment processes for recycling spent lithium-ion batteries. Waste Manage. 2016;52:221–227.
- Ojanen S, Lundström M, Santasalo-Aarnio A, et al. Challenging the concept of electrochemical discharge using salt solutions for lithium-ion batteries recycling. Waste Manage. 2018;76:242–249.
- Xiao J, Guo J, Zhan L, et al. A cleaner approach to the discharge process of spent lithium ion batteries in different solutions. J Cleaner Prod. 2020;255:120064.
- Yao LP, Zeng Q, Qi T, et al. An environmentally friendly discharge technology to pretreat spent lithium-ion batteries. J Cleaner Prod. 2020;245:118820.
- Zhang G, He Y, Wang H, et al. Application of mechanical crushing combined with pyrolysis-enhanced flotation technology to recover graphite and LiCoO2 from spent lithium-ion batteries. J Cleaner Prod. 2019;231:1418–1427.
- Zhang G, He Y, Wang H, et al. Removal of organics by pyrolysis for enhancing liberation and flotation behavior of electrode materials derived from spent lithium-ion batteries. ACS Sustain Chem Eng. 2020;8:2205–2214.
- Zhang T, He Y, Wang F, et al. Surface analysis of cobalt-enriched crushed products of spent lithium-ion batteries by X-ray photoelectron spectroscopy. Sep Purif Technol. 2014;138:21–27.
- Zhang G, He Y, Feng Y, et al. Pyrolysis-ultrasonic-assisted flotation technology for recovering graphite and LiCoO2 from spent lithium-ion batteries. ACS Sustain Chem Eng. 2018;6:10896–10904.
- Zhang G, He Y, Feng Y, et al. Enhancement in liberation of electrode materials derived from spent lithium-ion battery by pyrolysis. J Cleaner Prod. 2018;199:62–68.
- Li J, Wang G, Xu Z. Environmentally-friendly oxygen-free roasting/wet magnetic separation technology for in situ recycling cobalt, lithium carbonate and graphite from spent LiCoO2/graphite lithium batteries. J Hazard Mater. 2016;302:97–104.
- Zhong X, Liu W, Han J, et al. Pyrolysis and physical separation for the recovery of spent LiFePO4 batteries. Waste Manage. 2019;89:83–93.
- He Y, Zhang T, Wang F, et al. Recovery of LiCoO2 and graphite from spent lithium-ion batteries by fenton reagent-assisted flotation. J Cleaner Prod. 2017;143:319–325.
- Wang F, Zhang T, He Y, et al. Recovery of valuable materials from spent lithium-ion batteries by mechanical separation and thermal treatment. J Cleaner Prod. 2018;185:646–652.
- Zhu X, Zhang C, Feng P, et al. A novel pulsated pneumatic separation with variable-diameter structure and its application in the recycling spent lithium-ion batteries. Waste Manage. 2021;131:20–30.
- Zhang X, Li L, Fan E, et al. Toward sustainable and systematic recycling of spent rechargeable batteries. Chem Soc Rev. 2018;47:7239–7302.
- Nan J, Han D, Zuo X. Recovery of metal values from spent lithium-ion batteries with chemical deposition and solvent extraction. J Power Sources. 2005;152:278–284.
- Tanii T, Tsuzuki S, Honmura S, et al. (2003). Method for crushing cell. Google Patents.
- Pudas J, Erkkila A, Viljamaa J. (2015). Battery recycling method. Google Patents.
- Pinegar H, Smith YR. Recycling of end-of-life lithium ion batteries, part I: commercial processes. J Sustainable Metall. 2019;5:402–416.
- Diekmann J, Hanisch C, Froböse L, et al. Ecological recycling of lithium-ion batteries from electric vehicles with focus on mechanical processes. J Electrochem Soc. 2016;164:A6184.
- Bertuol DA, Bernardes AM, Tenório JAS. Spent NiMH batteries: characterization and metal recovery through mechanical processing. J Power Sources. 2006;160:1465–1470.
- Contestabile M, Panero S, Scrosati B. A laboratory-scale lithium-ion battery recycling process. J Power Sources. 2001;92:65–69.
- Kaneko A, Kitazume N, Okada C. (1995). Method of recovering reusable metals from nickel-hydrogen rechargeable battery. Google Patents.
- Granata G, Pagnanelli F, Moscardini E, et al. Simultaneous recycling of nickel metal hydride, lithium ion and primary lithium batteries: accomplishment of European guidelines by optimizing mechanical pre-treatment and solvent extraction operations. J Power Sources. 2012;212:205–211.
- Zhang T, He Y, Ge L, et al. Characteristics of wet and dry crushing methods in the recycling process of spent lithium-ion batteries. J Power Sources. 2013;240:766–771.
- Castillo S, Ansart F, Laberty-Robert C, et al. Advances in the recovering of spent lithium battery compounds. J Power Sources. 2002;112:247–254.
- Zenger T, Krebs A, Van Deutekom HJH. (2010). Method of and apparatus for dismantling and storage of objects comprising alkali metals, such as alkali metal containing batteries. Google Patents.
- Pinegar H, Smith YR. End-of-life lithium-ion battery component mechanical liberation and separation. JOM. 2019;71:4447–4456.
- Sloop S, Crandon L, Allen M, et al. A direct recycling case study from a lithium-ion battery recall. Sustainable Mater Technol. 2020;25:e00152.
- Wu Z, Zhu H, Bi H, et al. Recycling of electrode materials from spent lithium-ion power batteries via thermal and mechanical treatments. Waste Manag Res. 2021;39:607–619.
- Ebin B, Petranikova M, Ekberg C. Physical separation, mechanical enrichment and recycling-oriented characterization of spent NiMH batteries. J Mater Cycles Waste Manage. 2018: 20), doi:10.1007/s10163-018-0751-4.
- Shin SM, Kim NH, Sohn JS, et al. Development of a metal recovery process from Li-ion battery wastes. Hydrometallurgy. 2005;79:172–181.
- Li J, Shi P, Wang Z, et al. A combined recovery process of metals in spent lithium-ion batteries. Chemosphere. 2009;77:1132–1136.
- Shin H, Zhan R, Dhindsa KS, et al. Electrochemical performance of recycled cathode active materials using froth flotation-based separation process. J Electrochem Soc. 2020;167:020504.
- Marinos D, Mishra B. An approach to processing of lithium-ion batteries for the zero-waste recovery of materials. J Sustainable Metall. 2015;1:263–274.
- Vieceli N, Nogueira CA, Guimarães C, et al. Hydrometallurgical recycling of lithium-ion batteries by reductive leaching with sodium metabisulphite. Waste Manage. 2018;71:350–361.
- Al-Thyabat S, Nakamura T, Shibata E, et al. Adaptation of minerals processing operations for lithium-ion (LiBs) and nickel metal hydride (NiMH) batteries recycling: critical review. Miner Eng. 2013;45:4–17.
- Peng C, Liu F, Aji AT, et al. Extraction of Li and Co from industrially produced Li-ion battery waste–using the reductive power of waste itself. Waste Manage. 2019;95:604–611.
- Zhang T, He Y, Wang F, et al. Chemical and process mineralogical characterizations of spent lithium-ion batteries: an approach by multi-analytical techniques. Waste Manage. 2014;34:1051–1058.
- Wuschke L, Jäckel H-G, Leißner T, et al. Crushing of large Li-ion battery cells. Waste Manage. 2019;85:317–326.
- Wang J, Chen M, Chen H, et al. Leaching study of spent Li-ion batteries. Proc Environ Sci. 2012;16:443–450.
- Zhan R, Yang Z, Bloom I, et al. Significance of a solid electrolyte interphase on separation of anode and cathode materials from spent Li-Ion batteries by froth flotation. ACS Sustain Chem Eng. 2020;9:531–540.
- Xiao J, Li J, Xu Z. Novel approach for in situ recovery of lithium carbonate from spent lithium ion batteries using vacuum metallurgy. Environ Sci Technol. 2017;51:11960–6.
- Golmohammadzadeh R, Rashchi F, Vahidi E. Recovery of lithium and cobalt from spent lithium-ion batteries using organic acids: process optimization and kinetic aspects. Waste Manage. 2017;64:244–254.
- Lee CK, Rhee K-I. Preparation of LiCoO2 from spent lithium-ion batteries. J Power Sources. 2002;109:17–21.
- Sun L, Qiu K. Vacuum pyrolysis and hydrometallurgical process for the recovery of valuable metals from spent lithium-ion batteries. J Hazard Mater. 2011;194:378–384.
- Xiao J, Li J, Xu Z. Recycling metals from lithium ion battery by mechanical separation and vacuum metallurgy. J Hazard Mater. 2017;338:124–131.
- Yang L, Xi G, Xi Y. Recovery of Co, Mn, Ni, and Li from spent lithium ion batteries for the preparation of LiNixCoyMnzO2 cathode materials. Ceram Int. 2015;41:11498–11503.
- Natarajan S, Boricha AB, Bajaj HC. Recovery of value-added products from cathode and anode material of spent lithium-ion batteries. Waste Manage. 2018;77:455–465.
- Hanisch C, Loellhoeffel T, Diekmann J, et al. Recycling of lithium-ion batteries: a novel method to separate coating and foil of electrodes. J Cleaner Prod. 2015;108:301–311.
- Li L, Ge J, Wu F, et al. Recovery of cobalt and lithium from spent lithium ion batteries using organic citric acid as leachant. J Hazard Mater. 2010;176:288–293.
- Chen X, Luo C, Zhang J, et al. Sustainable recovery of metals from spent lithium-ion batteries: a green process. ACS Sustain Chem Eng. 2015;3:3104–3113.
- Smith WN, Swoffer S. (2014). Process for recovering and regenerating lithium cathode material from lithium-ion batteries. Google Patents.
- Meng Q, Zhang Y, Dong P. Use of glucose as reductant to recover Co from spent lithium ions batteries. Waste Manage. 2017;64:214–218.
- Yang Y, Huang G, Xu S, et al. Thermal treatment process for the recovery of valuable metals from spent lithium-ion batteries. Hydrometallurgy. 2016;165:390–396.
- Lu M, Zhang H, Wang B, et al. The re-synthesis of LiCoO2 from spent lithium ion batteries separated by vacuum-assisted heat-treating method. Int J Electrochem Sci. 2013;8:8201–8209.
- Zheng R, Zhao L, Wang W, et al. Optimized Li and Fe recovery from spent lithium-ion batteries via a solution-precipitation method. RSC Adv. 2016;6:43613–43625.
- Liu Y-J, Hu Q-Y, Li X-H, et al. Recycle and synthesis of LiCoO2 from incisors bound of Li-ion batteries. Trans Nonferrous Met Soc China. 2006;16:956–959.
- Chen L, Tang X, Zhang Y, et al. Process for the recovery of cobalt oxalate from spent lithium-ion batteries. Hydrometallurgy. 2011;108:80–86.
- Liu W, Zhong X, Han J, et al. Kinetic study and pyrolysis behaviors of spent LiFePO4 batteries. ACS Sustain Chem Eng. 2018;7:1289–1299.
- Barik S, Prabaharan G, Kumar L. Leaching and separation of Co and Mn from electrode materials of spent lithium-ion batteries using hydrochloric acid: laboratory and pilot scale study. J Cleaner Prod. 2017;147:37–43.
- Kim Y, Matsuda M, Shibayama A, et al. Recovery of LiCoO2 from wasted lithium ion batteries by using mineral processing technology. Resour Process. 2004;51:3–7.
- Widijatmoko SD, Gu F, Wang Z, et al. Selective liberation in dry milled spent lithium-ion batteries. Sustainable Mater Technol. 2020;23:e00134.
- Kim HS, Shin EJ. Re-synthesis and electrochemical characteristics of LiFePO 4 cathode materials recycled from scrap electrodes. Bull Korean Chem Soc. 2013;34:851–855.
- Bahgat M, Farghaly F, Basir SA, et al. Synthesis, characterization and magnetic properties of microcrystalline lithium cobalt ferrite from spent lithium-ion batteries. J Mater Process Technol. 2007;183:117–121.
- Song D, Wang X, Zhou E, et al. Recovery and heat treatment of the Li (Ni1/3Co1/3Mn1/3) O2 cathode scrap material for lithium ion battery. J Power Sources. 2013;232:348–352.
- Gratz E, Sa Q, Apelian D, et al. A closed loop process for recycling spent lithium ion batteries. J Power Sources. 2014;262:255–262.
- Qiu R, Huang Z, Zheng J, et al. Energy models and the process of fluid-magnetic separation for recovering cobalt micro-particles from vacuum reduction products of spent lithium ion batteries. J Cleaner Prod. 2021;279:123230.
- Kang J, Senanayake G, Sohn J, et al. Recovery of cobalt sulfate from spent lithium ion batteries by reductive leaching and solvent extraction with cyanex 272. Hydrometallurgy. 2010;100:168–171.
- Kang J, Sohn J, Chang H, et al. Preparation of cobalt oxide from concentrated cathode material of spent lithium ion batteries by hydrometallurgical method. Adv Powder Technol. 2010;21:175–179.
- Ruffino B, Zanetti M, Marini P. A mechanical pre-treatment process for the valorization of useful fractions from spent batteries. Resour Conserv Recycl. 2011;55:309–315.
- Ruismäki R, Rinne T, Dańczak A, et al. Integrating flotation and pyrometallurgy for recovering graphite and valuable metals from battery scrap. Metals (Basel). 2020;10:680.
- Widijatmoko SD, Fu G, Wang Z, et al. Recovering lithium cobalt oxide, aluminium, and copper from spent lithium-ion battery via attrition scrubbing. J Cleaner Prod. 2020;260:120869.
- Silveira A, Santana M, Tanabe E, et al. Recovery of valuable materials from spent lithium ion batteries using electrostatic separation. Int J Miner Process. 2017;169:91–98.
- Zhan R, Oldenburg Z, Pan L. Recovery of active cathode materials from lithium-ion batteries using froth flotation. Sustainable Mater Technol. 2018;17:e00062.
- Zhu X-N, Tao Y-J, He Y-Q, et al. Pre-concentration of graphite and LiCoO2 in spent lithium-ion batteries using enhanced gravity concentrator. Phys Chem Prob Miner Process. 2018;2:54.
- Yu J, He Y, Qu L, et al. Exploring the critical role of grinding modification on the flotation recovery of electrode materials from spent lithium ion batteries. J Cleaner Prod. 2020;274:123066.
- Zhang Y, He Y, Zhang T, et al. Application of falcon centrifuge in the recycling of electrode materials from spent lithium ion batteries. J Cleaner Prod. 2018;202:736–747.
- Saneie R, Abdollahi H, Ghassa S, et al. Recovery of copper and aluminum from spent lithium-Ion batteries by froth flotation: a sustainable approach. J Sustainable Metall. 2022;8:386–397.
- Vanderbruggen A, Sygusch J, Rudolph M, et al. A contribution to understanding the flotation behavior of lithium metal oxides and spheroidized graphite for lithium-ion battery recycling. Colloids Surf A. 2021;626:127111.
- Yu J, He Y, Li H, et al. Effect of the secondary product of semi-solid phase fenton on the flotability of electrode material from spent lithium-ion battery. Powder Technol. 2017;315:139–146.
- Yu J, He Y, Ge Z, et al. A promising physical method for recovery of LiCoO2 and graphite from spent lithium-ion batteries: grinding flotation. Sep Purif Technol. 2018;190:45–52.
- Huang Y, Han G, Liu J, et al. A stepwise recovery of metals from hybrid cathodes of spent Li-ion batteries with leaching-flotation-precipitation process. J Power Sources. 2016;325:555–564.
- Zhang G, Ding L, Yuan X, et al. Recycling of electrode materials from spent lithium-ion battery by pyrolysis-assisted flotation. J Environ Chem Eng. 2021;9:106777.
- Bae H, Kim Y. Technologies of lithium recycling from waste lithium ion batteries: a review. Mater Adv. 2021;2:3234–3250.