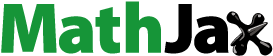
ABSTRACT
A novel bioflocculant CBF with high flocculating activity, produced by mixed culture of Rhizobium radiobacter F2 and Bacillus sphaericus F6 from soil, was investigated with regard to its production and flocculation performance in Al(III) removal. The most preferred carbon source, nitrogen source and C/N ratio (w/w) for strains F2 and F6 to produce CBF were glucose, urea and 20, respectively. The optimal inoculum size for CBF production was 10 % (v/v). The optimal initial pH, culture temperature and shaking speed were 7–8, 30°C and 140 r/min for 24 h, respectively, under which the flocculating activity of the bioflocculant reached 98.52 %. According to literature review, flocculant dosage, coagulant aid dosage, pH, hydraulic condition of coagulation and sedimentation time are considered as influencing parameters for CBF flocculation performance in Al(III) removal by L16(45) orthogonal design. The optimal conditions for Al(III) removal obtained through analysis and verification experiments were as follows: CBF, 28 mg/L; coagulant aid, 1.5 mL/L; initial pH, 8.0; and hydraulic conditions of coagulation: stir speed, 160 r/min; stir time, 40 s; and sedimentation time, 30 min. Under the optimal conditions, the removal efficiency of Al(III) was 92.95 %. Overall, these findings indicate that bioflocculant CBF offers an effective alternative method of decreasing Al(III) during drinking water treatment.
Introduction
Flocculants are useful agents in the aggregation of colloids, cells and suspended solids and are commonly used for drinking water production, waste water treatment, fermentation processes and food production.Citation1 Many chemical flocculants, including aluminum sulfate (AS), ferric chloride and polyacrylamide are widely used, although their use may incur some environmental and health problems.Citation2 Bioflocculants, extracellular biopolymeric substances secreted by bacteria, fungi, algae and yeast, are biodegradable and nontoxic flocculants.Citation3 The study of bioflocculants has attracted considerable scientific and biotechnological attention over the years because of their biodegradability, harmlessness and lack of secondary pollution.Citation3-5 Bioflocculants have a great potential for industrial applications,Citation6-8 however, low flocculating capability and large dosage requirement have been a major problem in bioflocculant development for actual wastewater treatment.
Bioflocculants have been used in a wide range of applications, such as wastewater treatment, drinking water treatment and downstream processes in biotechnology.Citation3,9-11 During drinking water treatment, flocculation precipitation is the main method used due to its low cost and established process. Many chemical flocculants, including polyaluminum chloride (PAC) and AS, are widely used for drinking water treatment because of their high flocculating performance and low cost. However, aluminum can cause health problems, including Alzheimer disease and Parkinson disease.Citation12-16 The identification of a safer and less-expensive flocculant, as a substitute for chemical flocculants in drinking water purification industry, is necessary and urgent. Given these concerns, bioflocculants are attractive alternative to existing synthetic flocculants, such as PAC and AS. Although so many studies about bioflocculants have been done For drinking water treatment, low flocculating capability and the low yields are still the major problems in limiting bioflocculants development for practical application of drinking water treatmentCitation10,11,17 Consequently, increasing yields in producing bioflocculants and improving the flocculating performance of the biofloccualnts have become recent hot topics in this field.Citation17
The compound bioflocculant CBF shows an excellent flocculating activity against solid particles and metal aqueous solution.Citation18 In this study, CBF was used in all experiments. A series of experiments was performed to investigate CBF production and its flocculation performance in aluminum removal, turbidity removal from surface water.
Materials and methods
Strains
Bioflocculant-producing strains F2 and F6 were originally screened from soil by State Key Laboratory of Urban Water Resource and Environment, Harbin Institute of Technology of China. F2 and F6 were identified as R. radiobacter and B. sphaericus, respectively.Citation19
The stock culture was maintained at 4°C on slant medium (per liter) that consisted of 3 g of beef extract, 10 g of peptone, 5 g of NaCl and 20 g of agar and subcultured every 30 days.
Culture media
Production medium (per liter) was composed of 10 g of glucose, 2 g of KH2PO4, 5 g of K2HPO4, 0.2 g of MgSO4·7H2O, 0.1 g of NaCl, 0.5 g of urea and 0.5 g of yeast extract. Initial pH was adjusted to 7.2–7.5. All media solutions were prepared with distilled water and sterilised at 115°C for 30 min.
Bioflocculant production
A set of 250 mL flasks containing 100 mL of production medium were was for fermentation. The F2 and F6 strains were separately inoculated from stock cultures into the production media and incubated at 30°C on a shaker at 140 r/min for 24 h. In the fermentation experiments, 6.6 mL of F2 broth and 3.3 mL of F6 broth were inoculated into a flask containing 100 mL production medium together and incubated under the same conditions. The compound bioflocculant used in the study was extracted from fermentation broth of one batch under the same conditions. The fermentation broth obtained was centrifuged (4000 g, 30 min) to separate the cells. The cell-free culture supernatant was the liquid bioflocculant, which was used for the analysis of flocculating activity and in experiments of removal of Al(III) during drinking water treatment. All experiments were performed in triplicate for the mean calculation.
Assay of flocculating activity
Flocculating activity was evaluated by measuring the turbidity of kaolin suspension based on the method reported by Kurane et al.Citation6 About 1.5 mL of 10% (w/v) CaCl2 and CBF solution were added into 1.0 L of kaolin suspension (5 g/L), and then pH was adjusted to 7.5 by adding NaOH. The solution was first stirred at 140 r/min for 40 s and then 40 r/min for 160 s. After 20 min settlement, samples were carefully withdrawn from the upper layer for optical density determination at the wave length of 550 nm using a 721 UV-Vis spectrophotometer. A control solution was prepared by replacing CBF solution with distilled water. The flocculating activity was expressed as follows:(1)
(1) where A is the optical density of control experiment at 550 nm and B is the optical density of the sample experiment at 550 nm.
Each of the experiments was repeated 3 times, and the arithmetic average values were obtained. All the chemicals used in this study were of analytical grade without further purification.
Source water flocculation experiments
Source water with low temperature (1.4–3.3°C) was collected from the Harbin water supply company (Harbin, China), whose source water came from the Songhua River. The turbidity and Al(III) of the raw water were 16.32 NTU and 0.4993 mg/L, respectively. A 1000 mL of raw water sample and 10%(w/v) CaCl2 solution were mixed in a 1000 mL beaker. The flocculant was then added to the raw water, and the mixture was vigorously stirred at 200 r/min for 0.5 min and slowly stirred at 60 r/min for 2 min. The mixture was then allowed to stand for 20 min, and the supernatant was removed for analysis. The measurements of turbidity and Al(III) were determined according to the standard methods issued by the China National Environmental Protection Agency, and the removal efficiency was calculated as follows:(2)
(2) where C0 is the initial value and C is the value after the flocculation treatment.
Orthogonal test of removal of turbidity and Al(III)
Based on the obtained preliminary optimum condition, CBF dosage, coagulant aid dosage, pH, hydraulic conditions and sedimentation time were considered as influencing parameters, and the concrete parameter of hydraulic conditions are shown in . The design of experiment is shown in .
Table 1. Hydraulic conditions for flocculation.
Table 2. Design form of the orthogonal test L16(45).
Results and discussion
CBF production
The bioflocculant production is affected by many factors, such as the constituents of the culture medium and culture conditions.Citation2,20-22 The effects of the key factors, including culture time, carbon source, nitrogen source, C/N ratio, metal ions and ionic strength, initial pH of the production medium, culture temperature, inoculum size and shaking speed on the flocculating activity of CBF, were investigated to identify the optimal culture conditions for the CBF production.
Time course of the production of CBF
shows how the bioflocculant production varies with the growth curve of strains F2 and F6. The flocculating activity reached 93.7% at the early stationary phase (at 24 h) and then flocculating activity slightly increased in stationary phase from 24 h to 48 h. The flocculating activity reached its maximum flocculating activity (94.7%) at the middle stage of the stationary phase (at 48 h), which is higher than 94.3% of Serratia ficaria SF-1Citation23 and 87.2% of Aspergillus flavus IH-7.Citation2 The bioflocculant was produced by biosynthesis during its growth. The pH of the fermentation broth smoothly decreased from 7.5 to 6.2 during the logarithm and stationary phases, followed by no evident variation until the end. The reciprocal change of pH and flocculating activity confirmed the production of organic acids in the bioflocculant production.Citation24,25 To obtain the cost-optimal bioflocculant with high flocculating activity, culture time of 24 h was chosen in the following studies.
Effects of carbon source, nitrogen source and C/N ratio on CBF production
The effects of carbon source, nitrogen source and the C/N ratio on CBF production were investigated. shows the flocculating activity (in a kaolin suspension) after 24 h cultivation with various carbon sources (sucrose, fructose, lactose, mannitol and low molecular weight organic matter) replacing glucose at the same concentration. Sucrose, glucose and lactose were favorable carbon sources for CBF production. In the experiments of effect of low molecular weight organic matter on CBF production, n-butanoic acid was more favorable than other low molecular weight organic matters; however, its flocculating activity was still lower than that of other 5 carbon sources. Results showed that low molecular weight organic matters were not suitable for CBF production. Considering the high CBF production and the cost of the culture medium, glucose was chosen as the sole carbon source in the following study.
Table 3. Effects of constituents of the culture medium on CBF production.
The effect of nitrogen sources was investigated in the same medium after 24 h cultivation (). Strains F2 and F6 were able to use organic nitrogen (peptone, yeast extract and urea) and inorganic nitrogen effectively (ammonium sulfate and sodium nitrate) as nitrogen sources. Urea was the preferred and cost-effective nitrogen source, and thus used for the following experiments. Many reported strains could effectively use organic nitrogen sources or organic nitrogen combined with inorganic nitrogen sources to produce bioflocculants.Citation22,23,26 For example, peptone (organic nitrogen source) and sodium nitrate (inorganic nitrogen source) provide the best nitrogen source to Aspergillus parasiticus for bioflocculant production, whereas with (NH4)2SO4, no flocculant is produced.Citation26 Compared with inorganic sources, urea and yeast extract are more favorable for bioflocculant production by S. ficaria S-14, but a complex nitrogen source that consists of beef extract and urea is better than solely inorganic or organic nitrogen source.Citation23 Bacillus licheniformis X14 can effectively use ammonium chloride as a nitrogen source.Citation16
At a fixed urea concentration of 0.5 g/L, a rapid increase on CBF production was observed when the C/N ratio increased up to 20/1 (), but a further increase in the C/N ratio caused a decrease on CBF production. Flocculating activity in C/N ratio of 30/1 was 96.6 ± 0.71%, which was a little lower than that in C/N ratio of 20/1 (P > 0.05). C/N ratio of 20/1 was relatively economical compared with C/N ratio of 30/1 for the production medium. Thus, C/N ratio of 20/1 was chosen for the next experiments.
Considering the high CBF production and cost of the culture medium, the most preferred carbon source, nitrogen source and C/N ratio were glucose, urea and 20/1, respectively. The use of 10 g/L glucose and 0.50 g/L urea in the production medium was evidently more economical than using 10 g/L glucose, 0.5 g/L urea and 0.5 g/L yeast extract in the initial culture media.
Effects of metal ions and ionic strength on CBF production
Bioflocculant production is influenced by metal ions present in the culture medium. The flocculant production of Proteus mirabilis TJ-1 was stimulated in the presence of Ca2+, Mg2+ and Fe3+, but inhibited by Al3+.Citation22 Ca2+ ions enhanced both the cell growth and the flocculant production of Paecilomyces sp., but Fe2+ and Cu2+ inhibited the cell growth.Citation27 For B. licheniformis X14, some cations, such as Na+, Fe2+, Ca2+ and Mg2+, did not affect ZS-7 production, whereas cations, such as Cu2+ inhibited the cell growth.Citation16 For strains F2 and F6, some cations, such as Na+, K+, Ca2+ and Mg2+, could be assimilated as a micronutrient by the strains and be propitious to their growth and CBF production, whereas cations, such as Fe3+, inhibited the cell growth (). Mg2+ was the most favorable metal ion and used in the following studies. We also investigated the influence of ionic strength. K2HPO4 and KH2PO4 were used as buffers to stabilize pH of the production medium during fermentation with optimal concentrations of 5 and 2 g/L, respectively.
Effect of the initial pH on CBF production
The effect of the initial pH of the culture medium on CBF production was investigated (). Over the pH range of 6–9, the lowest flocculating activity was 85.36%. The optimal pH for the CBF production ranged from 7 to 8, which should save the amount of acid and alkaline solutions required to adjust pH. When the initial pH was 7.5, the flocculating activity of CBF reached a peak (97.43%). This pH value was chosen as the initial pH in the following studies. Higher pH (above 7) appeared to be more favorable for CBF production. The initial pH of the culture medium determines the electric charge of the cells and the redox potential that can affect nutrient absorption and enzymatic reaction.Citation3 For different strains, their requirement for the initial pH varied greatly. Alkaline pH, especially pH 9.5, effectively stimulates the flocculant production of Rhodococcus erythropolis.Citation28 pH 7.0, which is a neutral pH and can save large numbers of acid and alkali used to adjust pH, is the optimum for TJ-F1 production.Citation22 The optimal pH for the ZS-7 bioflocculant production ranges from 6.5 to 9.0.Citation16
Effect of temperature, inoculum size and shaking speed on CBF production
The effect of temperature, inoculum size and shaking speed on CBF production was examined (details not shown). When the culture temperature was 30°C, the flocculating activity of CBF reached 97.53% which was maximal flocculating activity in the experiments. When the temperature was over 30°C, the flocculating activity of CBF gradually decreased. The optimal temperature for CBF production was 30°C, which was used for the following studies. The metabolism of microorganisms is directly related to culture temperature.Citation22,29 Maximum enzymatic activation can only be obtained at an optimum temperature.Citation22
The flocculating rate of CBF obtained from the culture media inoculated with 3%–15% (v/v) was investigated. The flocculating activity initially increased with inoculum size. At the inoculum size of 10%, the maximum flocculating activity of 97.81% was obtained. However, any further increase in inoculum size did not result in any higher flocculating activity. A small inoculum prolongs the stagnant phase, whereas a large inoculum makes niche of strains overlap excessively and inhibits the bioflocculant production.Citation3 As a result, an inoculum size of 10% was used for all subsequent cultures.
The effect of shaking speed on CBF production was also investigated. The optimum shaking speed was 140 r/min, and flocculating activity was 98.52%. Either higher or lower shaking speed than the optimum caused a decrease in the flocculating activity. The shaking speed of 140 r/min was used in the following studies. The shaking speed determines the dissolved oxygen concentration, which can also affect nutrient absorption and enzymatic reaction.Citation3 The optimum shaking speed for strains F2 and F6 was 140 r/min, which is different from the speed listed in various reports.Citation1,22 This difference may be attributed to the different oxygen demands of microorganisms.
Impact factors on removal efficiency of Al(III) by CBF during drinking water treatment
In this study, source water with low temperature was used to evaluate the flocculating activity of CBF. Sixteen sets of experiments were conducted according to the orthogonal design table L16 (45), and the experimental results are shown in .
Table 4. L16(45) orthogonal tests and results on the removal efficiency of turbidity and Al(III).
According to mean value analysis, optimum flocculation condition was the combination of A3B3C3D1E4, which was CBF dosage of 20 mg/L, coagulant aid dosage of 1.5 mL, pH 8.0, hydraulic condition of I and sedimentation time of 40 min (). Under this condition, the turbidity removal efficiency of 89.05% was obtained. By comparing the range, the influencing factors on the turbidity removal efficiency followed the order C>D>E>B>A. That is to say, turbidity removal efficiency was affected mostly by pH, followed by hydraulic condition, sedimentation time, coagulant aid dosage and CBF dosage. This result is due to the dissociation of flocculant, which occurs within a certain pH range. Proper pH value could increase the dissociation degree, lead to a higher charge density of flocculant, benefit the spread of flocculant molecules and facilitate the bridging action of bioflocculant. Thus, pH value plays a critical role.Citation30
shows experimental results of the removal efficiency of CBF on Al(III). The range analysis results suggest that the removal efficiency of Al(III) was influenced by the following factors in descending order: C>D>E>B>A. Al(III) removal efficiency was affected mostly by pH, followed by hydraulic condition, sedimentation time, coagulant aid dosage and CBF dosage. The removal efficiency order of Al(III) is the same as that of turbidity. This result indicates that not only the functional groups of CBF, –OH, –NH, C = O and C–O, among others, absorbed Al(III), but also the colloidal particles in water. Colloidal particles and Al(III) were removed from water simultaneously, and the colloidal particles with Al(III) integrated a whole group under van der Waals force, charge neutralisation and stronger bridging ability, finally precipitating from water by gravity.Citation31 The optimal factor combination for removal efficiency of Al(III) of drinking water from the result above was A4B3C3D1E3, which was CBF dosage of 28 mg/L, coagulant aid dosage of 1.5 mL, pH 8.0, hydraulic condition of I and sedimentation time of 30 min. Under this condition, the removal efficiency of the turbidity was 92.95%. The results of the treatment at the optimal condition of A4B3C3D1E3 showed a significant improvement in the water quality. The high removal efficiency of the CBF on Al (III) was due to the high molecular weight of CBF, which contains abundant chemical groups with chelating ability with metals.Citation18
Conclusions
The bioflocculant CBF produced by mixed culture of R. radiobacter F2 and B. sphaericus F6 possesses high molecular weight. In this study, the most preferred carbon source, nitrogen source and C/N ratio for strains F2 and F6 were glucose, urea and 20/1, respectively. CBF production could be stimulated by Na+, K+, Ca2+ and Mg2+. K2HPO4 and KH2PO4 were used as buffers to stabilize pH of the production medium during fermentation with optimal concentrations of 5 and 2 g/L, respectively. The optimal conditions for CBF production for 24 h were inoculum size of 10% (v/v), initial pH of 7.5, culture temperature of 30°C and shaking speed of 140 r/min, under which the flocculating activity of CBF reached 98.52 %. The CBF showed good flocculating performance and industrial potential for drinking water treatment with low temperature. The maximum removal efficiency of Al(III) was 92.95 %.
The results show that CBF is a potential bioflocculant in drinking water treatment. Present studies further prove that CBF could be used as a potential alternative for Al(III) removal of source water. Considering its excellent flocculating activity and harmlessness toward humans and the environment, CBF is expected to be a potential replacement of conventional synthetic flocculants and widely applied in water treatment and downstream processing of food and fermentation industries.
Disclosure of potential conflicts of interest
No potential conflicts of interest were disclosed.
Notes on contributors
The experimental work was conducted by Lixin Li, Fang Ma and Huimin Zuo. The manuscript was written by Lixin Li and Huimin Zuo. Data analysis was performed by Lixin Li and Fang Ma. All authors approved the final version of the article, including the authorship list.
Acknowledgements
The EssayStar Company for their English language editing and the suggestions from the anonymous reviewers are highly appreciated.
Funding
This work was supported Sponsored by the National Science Foundation of China (Grant No. 51478140 & 51408200), the State Key Laboratory of Urban Water Resource and Environment (Harbin Institute of Technology)(Grant No. 2015DX06), the Natural Science Foundation of Heilongjiang Province (No. E201461), the Special Fund for Science and Technology Innovation Talents of Harbin (Grant No. 2015RQQXJ015) and the Promising Youngsters Training Program of Heilongjiang University of Science and Technology (Grant No. Q20120201).
References
- Shih IL, Van YT, Yeh LC, Lin HG, Chang YN. Production of a biopolymer flocculant from Bacillus licheniformis and its flocculation properties. Bioresour Technol 2001; 78:267–72; PMID:11341686; http://dx.doi.org/10.1016/S0960-8524(01)00027-X
- Ahmad HRA, Azni I, Norhafizah A, Rosfarizan M. Production and characterization of a bioflocculant produced by Aspergillus flavus. Bioresour Technol 2013; 127:489–93; PMID:23159465; http://dx.doi.org/10.1016/j.biortech.2012.09.016
- Salehizadeh H, Shojaosadati SA. Extracellular biopolymeric flocculants: recent trends and biotechnological importance. Biotechnol. Adv 2001; 19:371–85; PMID:14538073; http://dx.doi.org/10.1016/S0734-9750(01)00071-4
- He N, Li Y, Chen J, Li QB. Recent investigations and applications of bioflocculant. Microbiol 2005; 32:104–8
- Salehizadeh H, Shojaosadati SA. Removal of metal ions from aqueous solution by polysaccharide produced from Bacillus firmus. Water Res 2003; 37:4231–5; PMID:12946905; http://dx.doi.org/10.1016/S0043-1354(03)00418-4
- Kurane R, Hatamochi K, Kakuno T, Kiyohara M, Hirano M, Taniguchi Y. Production of a bioflocculant by Rhodococcus erythropolis S-l grown on alcohols. Biosci Biotech Bioch 1994; 58:428–9; http://dx.doi.org/10.1271/bbb.58.428
- Lee SH, Lee SO, Jang IL, Lee TH. Microbial flocculant from Arcuadendron sp. TS-49. Biotechnol Lett 1995; 17:95–100; http://dx.doi.org/10.1007/BF00134203
- Lian B, Chen Y, Zhao J, Teng HH, Zhu LJ, Yuan S. Microbial flocculation by Bacillus mucilaginosus: applications and mechanisms. Bioresource Technol 2008; 99:4825–31; PMID:17967531; http://dx.doi.org/10.1016/j.biortech.2007.09.045
- Zhuang XL, Wang YP, Li QB, Yan S, He N. The production of bioflocculants by Bacillus licheniformis using molasses and its application in the sugarcane industry, biotechnol. Bioproc E 2012; 17:1041–7; http://dx.doi.org/10.1007/s12257-012-0213-0
- Giri SS, Harshiny M, Sen SS, Sukumaran V, Park SC. Production and characterization of a thermostable bioflocculant from Bacillus subtilis F9, isolated from wastewater sludge. Ecotox Environ Safe 2015; 121:45–50; PMID:26091955; http://dx.doi.org/10.1016/j.ecoenv.2015.06.010
- Feng P, Wang SM, Zhou LX. Isolation, identification of a bioflocculant producing bacterium and its application in drinking water purification. Acta Scientiae Circumstantiae 2009; 29:1666–71
- Arezoo C. The potential role of aluminium in Alzheimer’s disease. Nephrol Dial Transpl 2002; 17:17–20
- Nayak P. Aluminum: impacts and disease. Environ Res 2002; 89:101–15; PMID:12123643; http://dx.doi.org/10.1006/enrs.2002.4352
- Berthon G. Aluminum speciation In relation to aluminium bioavailablility metabolism and toxieity. Coordin Chem Rev 2002; 228:319–41; PMID:9756695; http://dx.doi.org/10.1016/S0010-8545(02)00021-8
- Meng L, Yang JX, Ma F, Pang CL, Jin C. Influence factors in treatment of low temperature and low turbidity water by compound bioflocculant. J Harbin Inst Technol 2009; 41:42–5
- Li Z, Zhong S, Lei HY, Chen RW, Yu Q, Li HL. Production of a novel bioflocculant by Bacillus licheniformis X14 and its application to low temperature drinking water treatment. Bioresour Technol 2009; 100:3650–6; PMID:19303286; http://dx.doi.org/10.1016/j.biortech.2009.02.029
- Huang X, Sun SL, Gao BY, Yue QY, Wang Y, Li Q. Coagulation behavior and floc properties of compound bioflocculant-polyaluminum chloride dual-coagulants and polymeric aluminum in low temperature surface water treatment. J Environ Sci-China 2015; 30:215–22; PMID:25872730; http://dx.doi.org/10.1016/j.jes.2014.07.033
- Wang LL, Ma F, Qu YY, Sun DZ, Li A, Guo JB, Yu B. Characterization of a compound bioflocculant produced by mixed culture of Rhizobium radiobacter F2 and Bacillus sphaeicus F6. World J Microb Biot 2011; 27:2559–65; http://dx.doi.org/10.1007/s11274-011-0726-2
- Ma F, Liu JL, Li SG, Yang JX, Zhang LQ, Wu B, Zhu YB. Development of complex microbial flocculant. Chinese Water Wastewater 2003; 19:1–4
- He N, Li Y, Chen J. Production of a novel polygalacturonic acid bioflocculant REA-11 by Corynebacterium glutamicum. Bioresour Technol 2004; 94:99–105; PMID:15081493; http://dx.doi.org/10.1016/j.biortech.2003.11.013
- Nakata K, Kurane R. Production of an extracellular polysaccharide bioflocculant by Klebsiella pneumoniae. Biosci Biotechnol Biochem 1999; 63:2064–8; PMID:10664839; http://dx.doi.org/10.1271/bbb.63.2064
- Xia SQ, Zhang ZQ, Wang XJ, Yang AM, Chen L, Zhao JF, Leonard D, Renault NJ. Production and characterization of a bioflocculant by Proteus mirabilis TJ-1. Bioresour Technol 2008; 99:6520–7; PMID:18155905; http://dx.doi.org/10.1016/j.biortech.2007.11.031
- Gong WX, Wang SG, Sun XF, Liu XW, Yue QY, Gao BY. Bioflocculant production by culture of Serratia ficaria and its application in wastewater treatment. Bioresour Technol 2008; 99:4668–74; PMID:18024024; http://dx.doi.org/10.1016/j.biortech.2007.09.077
- Deng SB, Bai RB, Hu XM, Luo Q. Characteristics of a bioflocculant produced by Bacillus mucilaginosus and its use in starch wastewater treatment. Appl Microbiol Biotechnol 2003; 60:588–93; PMID:12536261; http://dx.doi.org/10.1007/s00253-002-1159-5
- Lu WY, Zhang T, Zhang DY, Li CH, Wen JP, Du LX. A novel bioflocculant produced by Enterobacter aerogenes and its use in defecating the trona suspension. Biochem Eng J 2005; 27:1–7; http://dx.doi.org/10.1016/j.bej.2005.04.026
- Deng SB, Yu G., Ting YP. Production of a bioflocculant by Aspergillus parasiticus and its application in dye removal. Colloids and Surfaces B: Biointerfaces 2005; 44:179–86; PMID:16084070; http://dx.doi.org/10.1016/j.colsurfb.2005.06.011
- Takagi K, Kadowaki K. Poly galactosamine produced by a microorganism. Chitin Nat Technol 1985; 3:121–8
- Kurane R, Toeda K, Takeda K, Suzuki T. Culture condition for production of microbial flocculant by Rhodococcus erythropolis. Agric Biol Chem 1986; 50:2309–13; http://dx.doi.org/10.1271/bbb1961.50.2309
- Zhang ZQ, Lin B, Xia SQ, Wang XJ, Yang AM. Production and application of a bioflocculant by multiple-microorganism consortia using brewery wastewater as carbon source. J Environ Sci 2007; 19:660–6
- Wang LL, Wang LF, Ren XM, Ye XD, Li WW, Yuan SJ, Sun M, Sheng GP, Yu HQ, Wang XK. pH dependence of structure and surface properties of microbial EPS. Environ Sci Technol 2012; 46:737–44; PMID:22191521; http://dx.doi.org/10.1021/es203540w
- Xing J, Yang JX, Li A, Ma F, Liu KX, Wu D, Wei W. Removal efficiency and mechanism of sulfamethoxazole in aqueous solution by bioflocculant MFX. J Anal Methods Chem 2013; 2013:1–8; PMID:23476893; http://dx.doi.org/10.1155/2013/568614