Abstract
We present a high-resolution transmission electron microscopy study that gives evidence for cutting apart of DO22 Ni3Nb γ″ precipitates by dislocations emitted from nanoscale notches on free surfaces in Inconel® 725. This finding suggests that the surface morphology influences the rate of cutting apart of sub-surface precipitates in Ni-base alloys under mechanical loading.
Inconel® 725 is a Ni-base alloy with exceptional resistance to pitting, hydrogen embrittlement, and stress corrosion cracking in corrosive environments, such as those found in deep oil wells Citation1. Because it is age-hardened during heat treatment by precipitation of nanoscale Ni3M γ′ and γ″ phases (M=Al, Ti, Nb) rather than by cold work, alloy 725 also displays high strength along with excellent ductility and toughness Citation2–4. Coherency strains from γ′ and γ″ precipitates are thought to be the main strengthening mechanism in alloys such as Inconel® 718 Citation5 Citation6 and 725 Citation7. If these precipitates are destroyed, the mechanical properties of the alloy are degraded. For example, cyclic loading in Inconel® 718 gives rise to planar bands that have been cleared of precipitates Citation8–12. Slip along these bands is easier than in the virgin material and their formation is therefore believed to soften Ni-base alloys under cyclic loading and reduce fatigue life.
Planar slip bands are known to form by dislocation glide-assisted breakup of precipitates Citation9 and are thought to initiate from dislocation sources at grain boundaries Citation11. In this paper, we present evidence that nanoscale notches on free surfaces in alloy 725 also emit dislocations that cut apart γ″ precipitates, suggesting that surface morphology influences the rate of cutting apart of sub-surface precipitates in Ni-base alloys and may ultimately affect mechanical behaviors that depend on the integrity of these precipitates, such as the initiation of planar slip bands.
The Inconel® 725 used in this study was supplied by Special Metals Corp. Its chemical composition was measured by energy dispersive spectroscopy (EDS) in a transmission electron microscope (TEM) and the size of the grains was measured using electron backscatter diffraction (EBSD). To prepare TEM specimens, 3 mm diameter discs (for conventional TEM samples) or rectangular sheets of 11.5×2.5 mm2 (for straining samples) were cut out from 50 to 100 μm thick foils and electrochemically polished to electron transparency by twin jet thinning using a 7 vol.% perchloric acid in methanol electrolyte at −50°C with a current of ∼50 mA. We carried out a structural investigation in a JEOL 2010F TEM using a conventional double-tilt holder. The phase identification was carried out using selected area electron diffraction (SAED), electron energy loss spectroscopy, and EDS. In situ tensile straining was performed using a Gatan 654 single-tilt straining holder (Supplementary information, Figure S1) inside a JEOL 2011 TEM operated at 200 kV.
Alloy 725 has been studied much less extensively than alloy 718, so we first carried out a detailed microstructural investigation of alloy 725. Its composition is reported in . The EBSD-determined grain size was in the 30–80 μ m range (Supplementary information, Figure S2). The TEM analysis () shows that the fcc Ni-Cr solid solution γ matrix contains numerous bct (DO22) Ni3Nb γ″ particles. These particles are coherent with the γ matrix and typically ∼10 nm thick and 20–40 nm in diameter. A smaller number of coherent L12 Ni3(Al, Ti) γ′ particles were also found, often contiguous with γ″ precipitates. Reflections 1 or 2 in are actually composed of a point, which is a ⟨ 100⟩ reflection from all the γ′ precipitates, and a streak, which is a (002) reflection from one of the three sets of γ″ precipitates with differently oriented c-axes. A dark-field micrograph using one of these spots, therefore, shows all of the γ′ particles and only one of the three systems of γ″ particles. Thus, by imaging with different reflections, the γ′ and γ″ precipitates may be distinguished. The stress-free lattice parameters of γ, γ′, and γ″ are a γ=0.352 nm, a γ′=0.356 nm, and a γ″=0.362 nm and c γ″=0.741 nm, respectively Citation13. However, because all three phases are strained to coherency with each other, a γ≈ a γ′≈ a γ″≈ c γ″/2 in alloy 725. Additionally, 100–200 nm Nb-rich carbides were observed within grains and at grain boundaries (Supplementary information, Figure S3), where they appeared either as isolated particles or as continuous films, respectively. Finally, cuboidal 0.5–10 μ m Ti carbonitrides were also occasionally observed (Supplementary information, Figure S4).
Figure 1. (a) and (b) Dark-field images of Inconel® 725 sample using ‘1’ and ‘2’ diffraction points in the SAED pattern (c) respectively, revealing the distribution of γ″ and γ′ precipitates of specific orientations. The two γ″ precipitates indicated in (b) are parts of a single sandwich composite particle with γ′ in the middle, similar to the one shown in (e). (c) SAED pattern along the [001] zone axis, showing γ matrix as well as γ″ and γ′ superlattice reflections. (d) High-resolution TEM image of two γ″ particles oriented perpendicular to each other. (e) A composite γ″/γ′ precipitate with the sandwich morphology and (f) one with a ‘core-shell’ morphology.
![Figure 1. (a) and (b) Dark-field images of Inconel® 725 sample using ‘1’ and ‘2’ diffraction points in the SAED pattern (c) respectively, revealing the distribution of γ″ and γ′ precipitates of specific orientations. The two γ″ precipitates indicated in (b) are parts of a single sandwich composite particle with γ′ in the middle, similar to the one shown in (e). (c) SAED pattern along the [001] zone axis, showing γ matrix as well as γ″ and γ′ superlattice reflections. (d) High-resolution TEM image of two γ″ particles oriented perpendicular to each other. (e) A composite γ″/γ′ precipitate with the sandwich morphology and (f) one with a ‘core-shell’ morphology.](/cms/asset/bc46830e-4234-4067-9582-c5c0278d8aea/tmrl_a_775187_o_f0001g.gif)
Table 1. Composition of Inconel® 725 samples.
Dark-field images of the alloy 725 sample ( and ) acquired using superlattice reflections ‘1’ and ‘2’ shown in the SAED pattern in reveal uniform distributions of γ′ and γ″ precipitates. γ″ precipitates are typically shaped as oblate ellipsoids with the shortest principal axis aligned with [001] directions. In addition to isolated γ″ precipitates, such as those in , high-resolution TEM also revealed coherent composite γ′/γ″ precipitates. For example, in , γ′ is sandwiched between two γ″ layers with cube-on-cube orientation relationships between all components: (001)γ″//{100}γ//{100}γ′ and 100γ″//⟨ 100⟩γ//⟨ 100⟩γ′ Citation13. Similar precipitates have been observed in Inconel® 718 Citation13 Citation16. In another common γ′/γ″ morphology, shown in , cubic γ′ ‘cores’ with edge lengths 10–15 nm are coated with a ‘shell’ of γ″ on all six {100} faces. The extensive similarities in microstructure that we have observed in alloy 725 compared to that previously reported in alloy 718 suggest that similar mechanisms of mechanical deformation and environmental degradation are likely to be operative in both.
Next, we used in situ TEM tensile straining experiments to investigate crack propagation in alloy 725. When tensile loading is applied to the TEM samples, transgranular cracks originating from the edges of the electropolished hole propagate along {111} planes into the foil, as illustrated in . Some cracks were found to cross multiple grain boundaries and no crack was observed to propagate exclusively along grain boundaries, indicating that the boundaries in thin foils of alloy 725 are not intrinsically weak. Stereoscopic and contrast analysis showed that the opening mode of most of these cracks was either mode II (‘sliding’) or, more frequently, mode III (‘tearing’) Citation16 Citation17. Propagation of such cracks in fcc metal TEM foils is known to proceed by the emission of glide dislocations on conventional {111}⟨ 110⟩ slip systems from the crack tips: edge dislocations in mode II and screw dislocations in mode III Citation16. Therefore, these cracks may be viewed as sources of dislocations with known glide planes and Burgers vectors.
Figure 2. (a) TEM image showing a crack propagating in alloy 725 along {111} planes across two twin boundaries. (b) High-resolution TEM image of the crack surface indicated by a black square in (a) contains part of a γ″ precipitate. (c) A nanoscale surface notch with slip displacement of 20 nm along the (111) plane. (d) A γ″ precipitate ahead of the notch shown in (c) that has been cut into two halves along the same (111) plane forming the notch. The amorphous structures above the scale bar in (b) and below the arrow in (c) are organic contaminants.
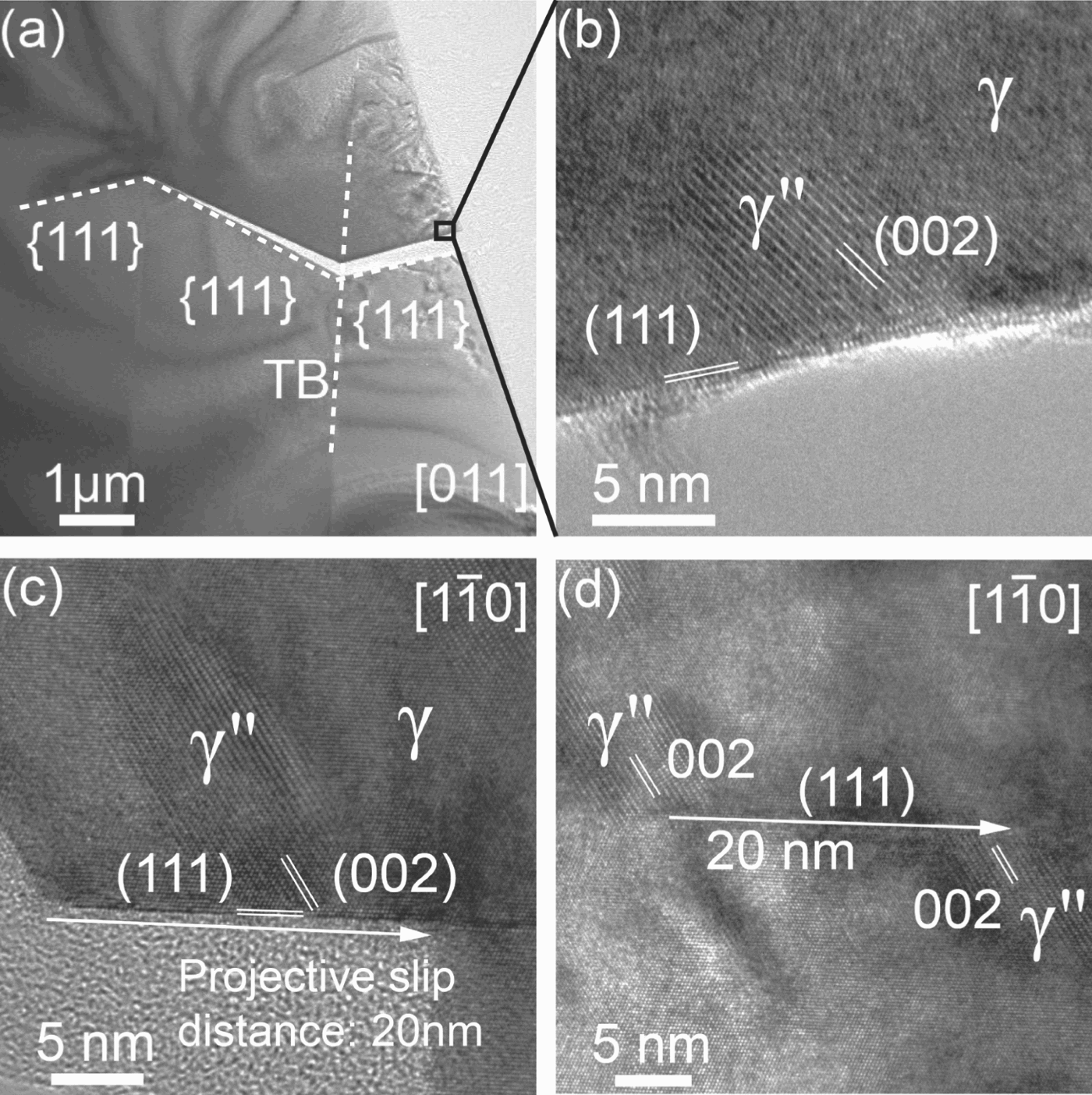
High-resolution examination of the region close to the crack surface (shown in and indicated by the black square in ) demonstrates that the crack surface is nearly atomically flat and lies on a {111} plane, as expected. We note that the amorphous structures observed on the surface (above the scale bar in and below the arrow in ) are organic contaminants, which may adsorb during sample transfer as well as during the TEM investigation itself. They do not reflect the structure of the sample or affect its mechanical properties. Interestingly, we frequently observed evidence of cutting through of γ″ precipitates by cracks (); however, these may in fact be cut by dislocations emitted from the crack tip or from surface notches well in advance of a crack propagating through them. Therefore, we focus on examining γ″ precipitates ahead of such surface notches.
shows a notch that grows by the emission of edge dislocations. The sliding displacement along the notch in the ⟨ 110⟩ projection is ∼20 nm, corresponding to ∼80 glide dislocation Burgers vectors. γ″ precipitates directly ahead of this notch were found to be cut into two parts: one lying above the {111} plane parallel to and aligned with the notch surface, and the other lying below it, as shown in . These matching parts of initially disc-shaped γ″ precipitates have identical crystallographic orientations and are displaced from each other by the notch size, i.e. ∼ 20 nm. These observations indicate that upper and lower halves of γ″ precipitates, such as those in , initially belonged to a single particle and were cut apart by dislocations emitted from the growing notch.
The fact that surface features such as nanoscale notches emit dislocations that cut apart γ″ precipitates suggests that surface morphology influences the rate at which sub-surface precipitates in Ni-base alloys are destroyed under mechanical loading. Thus, the state of free surfaces in alloys 718 and 725 may affect the evolution of sub-surface microstructure and, ultimately, mechanical behaviors that depend on the integrity of γ′ and γ″ precipitates, such as initiation of planar bands. Stress concentration factors between 2 and 4 have been found at the tips of isolated surface notches Citation18 and pits Citation19 Citation20 as well as for arrays of pits Citation21, supporting the view that dislocations are most likely to nucleate in their vicinity. Large pits have even been shown to nucleate cracks in steels Citation22.
A wide range of factors, especially mechanical contact with other solids, influence the state of free surfaces of engineering components. The surface morphology also depends on the chemistry of the operating environment. For example, in alloy 725, we find that selective etching of γ′ and γ″ precipitates in sour environments may contribute to the formation of nanoscale notches on free surfaces. To simulate conditions that might be encountered in sour environments, we immersed TEM foils of alloy 725 into 20 vol.% sulfuric acid in methanol. shows that all the γ′ and γ″ precipitates have been selectively etched, leaving behind nanoscale holes whose shapes, sizes, and distributions are the same as those of the precipitates. Most of the holes are, therefore, shaped as sections of oblate spheroids. The selective etching of the precipitates is further confirmed by the absence of corresponding superlattice reflections in the SAED pattern for the etched foil (, inset). In a bulk alloy 725 component, such holes would only intersect one surface (as opposed to two in the TEM foil) and would, therefore, form nanoscale surface pits.
Figure 3. Bright-field TEM image of alloy 725 etched in an acidic solution showing selective etching of γ″/γ′ precipitates. Inset: corresponding SAED shows only γ reflections.
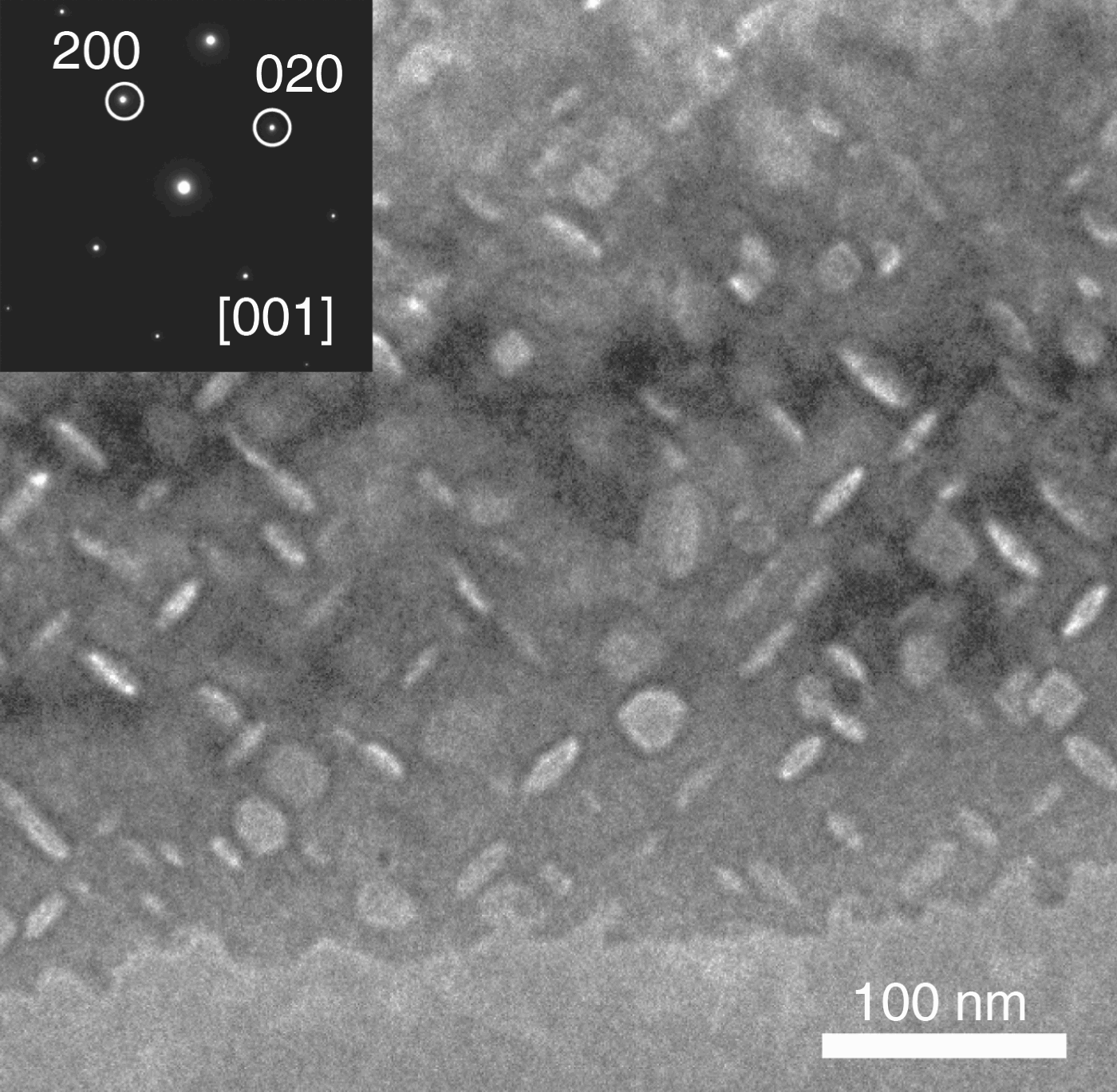
Khantha et al. Citation23 proposed a classification of DO22 compounds into two types: those that deform by twinning on {111} planes (e.g. Al3Ti or Ni3V), and those that deform by glide of ⟨ 110⟩ superdislocations on {111} planes (e.g. Al3V). Since we did see cutting apart of DO22 Ni3Nb precipitates and never found any evidence of twinning, our work suggest that the deformation of DO22 Ni3Nb is likely more akin to DO22 Al3V rather than Al3Ti or Ni3V. In planar slip band formation under cyclic loading, precipitates are thought to be repeatedly cut by dislocations into segments so small that they may no longer be detected in TEM and may even re-dissolve into the matrix. Some controversy remains as to whether dislocation cross-slip is Citation9 Citation24 or is not Citation8 essential to the breakup of the precipitates. The TEM results presented in suggest that cross slip is not necessary for cutting apart of γ″ precipitates by glide dislocations, at least at room temperature.
In summary, we presented tensile straining and high-resolution TEM evidence for the cutting apart of γ″ precipitates by glide dislocations emitted from nanoscale notches on free surfaces in Inconel® 725. This finding suggests that the state of free surfaces in alloy 725 may affect the evolution of sub-surface microstructure and, ultimately, mechanical behaviors that depend on the integrity of γ′ and γ″ precipitates. Selective dissolution of γ″ precipitates in acidic environments is one example of a process that may provide copious surface pits capable of emitting dislocations that cut apart sub-surface γ″ precipitates.
Supplementary online material
A more detailed information on experiments is available at http://dx.doi.org/10.1080/21663831.2013.775187
tmrl_a_775187_sm5124.pdf
Download PDF (4.7 MB)Acknowledgements
We are grateful to S. Shademan, A. Turnbull, and S. Lynch for useful discussions. This work was supported by the BP-MIT Materials and Corrosion Center. The authors acknowledge access to Shared Experimental Facilities provided by the MIT Center for Materials Science Engineering supported in part by MRSEC Program of National Science Foundation under award number DMR—0213282. J. P. H. acknowledges the Department of Energy Office of Science Graduate Fellowship Program (DOE SCGF), made possible in part by the American Recovery and Reinvestment Act of 2009, administered by ORISE-ORAU under contract no. DE-AC05-06OR23100.
References
- Sims , C T , Stoloff , N S and Hagel , W C . 1987 . Superalloys II , New York (NY) : Wiley .
- Durand-Charre , M . 1997 . The microstructure of superalloys , Amsterdam (NL) : Gordon and Breach Science Publishers .
- Sabol , G P and Stickler , R . 1969 . Microstructure of nickel-based superalloys . Phys Status Solidi. , 35 ( 1 ) : 11 – 52 . (doi:10.1002/pssb.19690350102)
- Reed , R C . 2006 . The superalloys: fundamentals and applications , New York (NY) : Cambridge University Press .
- Oblak , J M , Paulonis , D F and Duvall , D S . 1974 . Coherency strengthening in Ni base alloys hardened by DO22 gamma″ precipitates . Metall Trans. , 5 ( 1 ) : 143 – 153 .
- Chaturvedi , M C and Han , Y F . 1983 . Strengthening mechanisms in Inconel-718 superalloy . Met Sci. , 17 ( 3 ) : 145 – 149 . (doi:10.1179/030634583790421032)
- Don , X J , Zhang , M C and Mannan , S K . 2003 . Microstructures and the structure stability of Inconel 725, a new age-hardenable corrosion resistant superalloy . Acta Metall Sin. , 16 ( 2 ) : 145 – 150 .
- Xiao , L , Chen , D L and Chaturvedi , M C . 2008 . Cyclic deformation mechanisms of precipitation-hardened Inconel 718 superalloy . Mater Sci Eng A. , 483–484 ( SI ) : 369 – 372 .
- Sundararaman , M , Chen , W , Singh , V and Wahi , R P . 1990 . TEM investigation of gamma’ free bands in Nimonic PE16 under LCF loading at room temperature . Acta Metall Mater. , 38 ( 10 ) : 1813 – 1822 . (doi:10.1016/0956-7151(90)90293-P)
- Sundararaman , M , Chen , W and Wahi , R P . 1989 . Interpretation of fatigue softening at room temperature in a superalloy . Scripta Metall Mater. , 23 ( 10 ) : 1795 – 1800 .
- Worthem , D W , Robertson , I M , Leckie , F A , Socie , D F and Altstetter , C J . 1990 . Inhomogeneous deformation in Inconel 718 during monotonic and cyclic loadings . Metall Trans A. , 21 ( 12 ) : 3215 – 3220 . (doi:10.1007/BF02647316)
- Xiao , L , Chen , D L and Chaturvedi , M C . 2005 . Shearing of gamma″ precipitates and formation of planar slip bands in Inconel 718 during cyclic deformation . Scr Mater. , 52 ( 7 ) : 603 – 607 . (doi:10.1016/j.scriptamat.2004.11.023)
- Cozar , R and Pineau , A . 1973 . Morphology of y′ and y″ precipitates and thermal stability of Inconel 718 type alloys . Metall Trans. , 4 ( 1 ) : 47 – 59 . (doi:10.1007/BF02649604)
- Phillips , P J , McAllister , D , Gao , Y , Lv , D , Williams , RE A , Peterson , B , Wang , Y and Mills , M J . 2012 . Nano gamma′/gamma″ composite precipitates in alloy 718 . Appl Phys Lett. , 100 ( 21 ) : 211913 (doi:10.1063/1.4721456)
- Xie , X S , Dong , J X , Zhang , M C and Fu , S H . 2007 . High temperature structure stability study on Nb-containing nickel-base superalloys . Mater Sci Forum. , 546–549 : 1281 – 1288 . (doi:10.4028/www.scientific.net/MSF.546-549.1281)
- Ohr , S M . 1985 . An electron microscope study of crack tip deformation and its impact on the dislocation theory of fracture . Mater Sci Eng. , 72 ( 1 ) : 1 – 35 . (doi:10.1016/0025-5416(85)90064-3)
- Maurer , R . 1992 . In situ straining: crack development in thin foils of Ni3Al . J Mater Sci. , 27 ( 23 ) : 6279 – 6290 . (doi:10.1007/BF00576273)
- Li , Z H and Guo , W L. 2001 . Three-dimensional elastic stress fields ahead of blunt v-notches in finite thickness plates . Int J Fract. , 107 ( 1 ) : 53 – 71 . (doi:10.1023/A:1026586819885)
- Cerit , M . 2013 . Numerical investigation on torsional stress concentration factor at the semi elliptical corrosion pit . Corros Sci. , 67 : 225 – 232 . (doi:10.1016/j.corsci.2012.10.028)
- Cerit , M , Genel , K and Eksi , S . 2009 . Numerical investigation on stress concentration of corrosion pit . Eng Fail Anal. , 16 ( 7 ) : 2467 – 2472 . (doi:10.1016/j.engfailanal.2009.04.004)
- Lu , X P and Barber , J R . 1992 . Comninou M. Stress-concentration due to an array or hemispherical cavities at the surface of an elastic half-space . J Elast. , 28 ( 2 ) : 111 – 122 . (doi:10.1007/BF00041775)
- Horner , D A , Connolly , B J , Zhou , S , Crocker , L. and Turnbull , A . 2011 . Novel images of the evolution of stress corrosion cracks from corrosion pits . Corros Sci. , 53 ( 11 ) : 3466 – 3485 . (doi:10.1016/j.corsci.2011.05.050)
- Khantha , M , Vitek , V and Pope , D P . 1992 . An atomistic study of dislocations and their mobility in a model DO22 alloy . Mater Sci Eng A. , 152 ( 1–2 ) : 89 – 94 . (doi:10.1016/0921-5093(92)90051-2)
- Phillips , P J , Unocic , R R , Kovarik , L , Mourer , D , Wei , D and Mills , M J . 2010 . Low cycle fatigue of a Ni-based superalloy: non-planar deformation . Scr Mater. , 62 ( 10 ) : 790 – 793 . (doi:10.1016/j.scriptamat.2010.01.044)