Abstract
Considering the inherent advantages of eutectic alloys as high-temperature materials, eutectic high-entropy alloys provide a brand new research direction for developing materials to be used in high-temperature environments. Along this line of thinking, the solidification microstructure in a near-eutectic Al2CrCuFeNi2 alloy was studied. A unique sunflower-like eutectic colony structure was observed, where the Ni–Al-rich B2 phase formed as the primary phase with a spherical or ellipsoidal morphology, the Ni–Al-rich B2/Cr-rich A2 eutectics grew on the primary phase in a radial manner, and the primary B2 phase further decomposed into nearly cubic particles dispersed in the matrix at lower temperatures.
Introduction
Eutectic alloys are important in many aspects, including controllable near-equilibrium microstructures that can resist change up to the reaction temperature, high rupture strength, good high-temperature creep resistance, and sometimes interesting and unusual electrical, magnetic, and optical properties.[Citation1] Naturally, eutectic alloys are good candidate materials to be used in high-temperature environments. A representative example is the NiAl–Cr eutectic alloy, where NiAl has excellent oxidation resistance, high melting temperature, high thermal conductivity, and relatively low density, while Cr provides enhancements in both the toughness and the creep strength for the eutectic composite material.[Citation2,Citation3] It is also widely known that the addition of some minor elements, such as Mo, Fe, and W, can affect the microstructure and orientation of the NiAl and Cr phases.[Citation2]
High-entropy alloys (HEAs), or multicomponent alloys with equiatomic or close-to-equiatomic compositions, are newly emerging metallic materials that have great potential to be used in high-temperature environments.[Citation4–7] A distinctive feature of HEAs is the stabilization of the solid solution phases by the high configuration entropy at elevated temperatures,[Citation8] and the usually simple phase constitutions [Citation9,Citation10] even in such a highly concentrated multi-component alloy system. Two notes are raised here for clarification. First, solid solutions are not necessarily the sole alloying products in HEAs. Depending on the alloy compositions, intermetallic compounds can form, and the amorphous phase can also form.[Citation9–12] Second, the solid solutions in the cast HEAs are normally non-equilibrium phases. They are actually the first formed solid phases upon solidification, and are kept to the ambient temperature due to the sluggish diffusion of HEAs[Citation13,Citation14]: the time scale of the cooling process is relatively too short for the phase transformation toward its equilibrium state. It is also that this sluggish diffusion effect that leads to the exceptional high-temperature strength and structural stability of HEAs.[Citation7,Citation15] The eutectic HEAs seem to be an interesting idea for designing new high-temperature materials, if the advantages of both HEAs and the eutectics can be utilized. Previous work on eutectic HEAs has been sporadic,[Citation16–19] and a comparative study of eutectic HEAs to conventional eutectic high-temperature alloys is missing. Here, we used a recently developed near-eutectic Al2CrCuFeNi2 HEA [Citation20,Citation21] as an example, to compare its solidification structure with the NiAl–Cr eutectic alloys. The formation mechanism of the unique sunflower-like microstructure in Al2CrCuFeNi2 was given particular attention.
Experimental
The Al2CrCuFeNi2 alloy was prepared by arc-melting a mixture of constituent elements with purity higher than 99.9 wt% in a Ti-gettered high-purity argon atmosphere. Subscripts in the alloy compositions indicate the atomic portion of each individual element. The melting was repeated five times to improve the chemical homogeneity, and finally the molten alloy was drop-cast into a 10 mm diametered copper mold. The phase constitutions of the alloy were examined by the X-ray diffractometer (XRD) using the Co radiation (Bruker AXS D8 Discover). To facilitate the microstructure observation, the sample surfaces were sequentially polished down to the 0.3 μm grit alumina suspension furnish, and then electrochemically etched using the Cica-Reagent Electrolyte A (Kanto Chemical). The microstructures of the alloys were examined using the field emission scanning electron microscope (FE-SEM, Zeiss 1550 VP, equipped with an X-ray energy-dispersive spectrometer (EDS)). Transmission electron microscope (TEM) specimens were prepared by mechanical thinning followed by the twin-jet electrochemical polishing with the 10 vol% HClO4-90 vol% ethanol solution. The chemical composition was analyzed using the TEM-EDS (Philips CM20) method.
Results and discussion
The microstructure of the alloy is given in (a), where copious eutectic grains or colonies can be seen. According to Li and Kuribayashi [Citation22] when discussing the free solidification behavior of undercooled eutectics, a single eutectic colony shall be the basic unit rather than the bulk. This methodology was adopted here to study the eutectic structure. Essentially, each eutectic colony has a similar microstructure in that the lamellae grow on the spherical or ellipsoidal phase in a radial manner, and copious nearly cubic particles appear within the spherical or ellipsoidal phase. A typical microstructure of the eutectic colony is shown in (b). Interestingly, it resembles much the structure of a sunflower. The lamellae constitute the petals and inter-petals, the spherical phase as the disk floret and the particles form the seeds. This sunflower-like microstructure can basically represent the morphology of all the eutectic colonies, with the main differences among colonies being the size and shape of the disk-floret phase, and whether the collision of neighboring colonies would prevent the full development of an individual colony. For the eutectic colony shown in (b), the disk-floret phase has a diameter of ∼4 μm, the petals are ∼1.4 μm in length and ∼300 nm in width, with the spacing between petals ranging from ∼75 to ∼350 nm, and the seeds have an average size of 230 nm. Depending on the growth condition (for both the floret disk and the petals), these sizes vary among different eutectic colonies but these measurements give an idea of the magnitude.
Figure 1. (color online) (a) Secondary electron image of the etched Al2CrCuFeNi2 alloy and (b) the enlarged view of a typical sunflower-like microstructure. The inset in (a) gives the XRD pattern for the alloy.
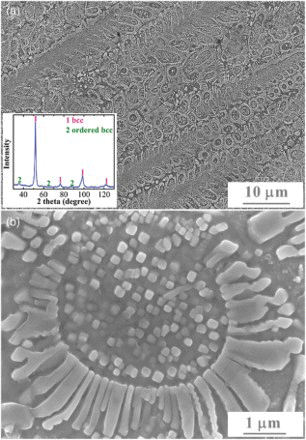
shows an SEM-EDS map for a typical eutectic colony, and it gives a glimpse of the elemental distribution for the eutectic structure. The petals and seeds are both enriched in Cr and Fe, while the inter-petals and the disk floret are both enriched in Ni and Al. Interestingly, the seeds form in a concentric region to the disk floret, which is highlighted in the secondary electron image. The preliminary chemical information indicates that the petals and seeds could be the same phase, the inter-petals and the disk floret also belong to the same phase. To confirm this conjecture, the chemical compositions were analyzed by TEM-EDS with a much improved spatial resolution (with the electron beam size of 40 nm), and the results are given in . Indeed, the inter-petals and the disk floret (matrix, excluding the seeds) have almost the exact chemical compositions. A more careful observation of their compositions suggests that they can be written in the form of (Ni, Fe, Cr)50(Al, Cu)50, or with the composition of a NiAl-type solid solution. The petals and seeds do not have the same compositions, but they are both enriched in Cr and Fe, and the enrichment is more significant in the petals. Considering that the XRD analysis only shows the existence of two phases in this alloy, bcc (A2) and ordered bcc (B2) phase, the above chemical analysis leads us to presume that the petals and seeds have the A2 structure, while the inter-petals and the disk-floret matrix have the B2 structure. This presumption is further supported by the selected area diffraction patterns (SADP). (a) shows the morphology of a eutectic colony under TEM, where the interface of the floret disk and the radially grown petals on the floret disk can be clearly observed. The SADPs for both the seeds and the petals, shown in Figures 3(b) and 3(c), confirm that they have the A2 structure.
Figure 2. (color online) SEM-EDS elemental map of a typical sunflower-like microstructure. The dash-dotted lines imposed on the image are drawn to guide the eyes.
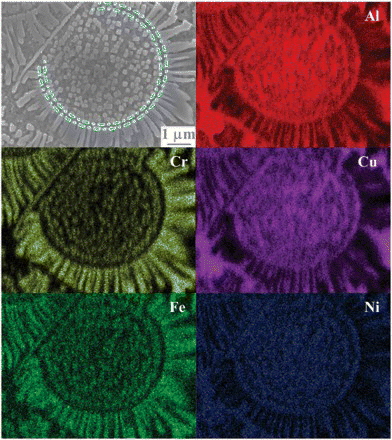
Figure 3. (color online) (a) TEM image showing the sunflower-like microstructure, with some sketch lines drawn to highlight the shape of the petals and seed particles. (b) and (c) are representative SADPs for the seed parties and petals.
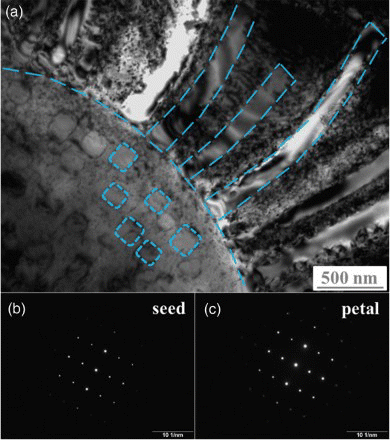
Table 1. TEM-EDS analysis for the sunflower-like structure.
Combining the XRD analysis, the microstructural features, the chemical composition, together with the structural characterization by TEM, we came up with the formation mechanism of the unique sunflower-like microstructure, shown in . During the solidification, the B2 phase with the composition of (Ni, Fe, Cr)50(Al, Cu)50 forms first from the liquid phase as the primary phase. The primary phase grows almost isotropically, not forming a dendritic structure. When reaching the eutectic temperature, the alternating B2 and A2 phases form the lamellae growing on the primary phase, and the growth direction of the lamellae is normal to the boundary of the primary phase, thus forming a radial pattern. A eutectic colony is then formulated and the growth of each eutectic colony stops when the solidification ends or it collides with neighboring colonies. The nearly cubic A2 phases form at a lower temperature, decomposing from the primary B2 phase, very possibly due to the occurrence of the spinodal decomposition. The separation of the Ni–Al-rich B2 phase (matrix) and the Cr–Fe-rich A2 phase (seeds) seems to lend support to this hypothesis. Spinodal decompositions forming the compositionally different A2 and B2 phases are frequently seen in HEAs,[Citation23,Citation24] and it is interesting to note that in the AlCoCrCuFeNi HEA, the products of the spinodal decomposition are also Ni–Al-rich B2 phase and Cr–Fe-rich A2 phase.[Citation24] The cubic form of the A2 phase, rather than the modulated plates as in References,[Citation23,Citation24] shall originate from the need to minimize the elastic strain energy.[Citation25] The nature of the confinement of the region where the spinodal decomposition occurs, for example to within the region circled by the dash-dotted lines in , is unclear but it could be related to the boundary effect, as the spinodal decomposition free region locates nicely along the phase boundary between the primary phase and the eutectics.
Figure 4. (color online) Sketch showing the proposed formation mechanism of the sunflower-like structure. Symbols used here: L for the liquid phase, α for the primary B2 phase and the B2 phase in the lamellae, β for the A2 phase in the lamellae, α′ and β′ for the B2 and A2 phase out of the spinodal decomposition, respectively, differentiating them with the B2 and A2 phase mentioned above.
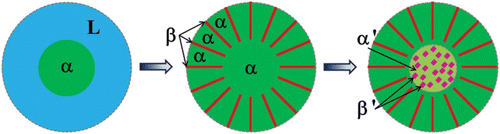
It is interesting to recognize that the sunflower-like microstructure formed in this near-eutectic Al2CrCuFeNi2 HEA bears much similarity to those formed in some hypo-eutectic NiAl–Cr alloys. For example, a similar structure was seen in an induction melt and drop-cast 33Ni–32Al–28Cr–3Mo–4Ti (at%) alloy,[Citation26] and the phase constitutions of the structural features are almost close to those in the HEA: NiAl phase forming the primary phase, alternating NiAl–Cr(Mo) eutectic lamellae grow on the primary NiAl phase in a radial manner, with the Cr(Mo) phase being the petals, and Cr(Mo) particles forming within the primary NiAl phase. However, the sizes of the structural features in the 33Ni–32Al–28Cr–3Mo–4Ti alloy are much coarser than those in the HEA. In the former, the petals are ∼50 μm in length and the seeds are about 1 μm. It is also worthy pointing out that in some hyper-eutectic NiAl–Cr alloy where the Cr(Mo) phase was the primary phase, NiAl halos were present surrounding the primary Cr(Mo) phase, and the eutectics then grew over the halos.[Citation2] According to the non-reciprocal nucleation principle,[Citation27] no Cr(Mo) halos would form on the primary NiAl phase, and this was experimentally confirmed.[Citation28] The point of mentioning this is to exclude the possibility of the halo formation in the current HEA, and to state that the spinodal decomposition-free region, as seen in , is not the halo. NiAl–Cr alloys are the generally recognized as a pseudo-binary eutectic system,[Citation29] the solidification behavior in the near-eutectic NiAl–Cr alloys is not surprising. However, the solidification of the Al2CrCuFeNi2 HEA also follows a pseudo-binary eutectic manner which is somewhat unexpected, considering such a highly concentrated alloy system and the high doping of elements other than Ni, Al and Cr (). This phenomenon can possibly be rationalized by two points: the enhanced solid solutioning by the high configuration entropy at elevated temperatures and the non-equilibrium nature of the achieved pseudo-binary eutectics in the HEA. The significance of knowing this structural similarity between the Al2CrCuFeNi2 HEA and NiAl–Cr alloys is that previous knowledge to optimize the mechanical properties of the latter can now be transplanted to the former, which would certainly simplify the alloy design for desirable eutectic HEAs.
The observation of sunflower-like eutectic microstructure is rather rare in the literature. To the best knowledge of the authors, the most similar structures are only seen in some NiAl–Cr(Mo) hypo-eutectic alloys,[Citation26,Citation30] which are also essentially equiatomic ternary alloys doped with small amounts of alloying elements such as Mo, Ti and rare-earth elements. To achieve the universal sunflower-like solidification microstructure as seen in (a), all the following four conditions need to be satisfied simultaneously: (1) the existence of copious nucleation sites for the primary phases;[Citation22] (2) the almost isotropic growth of the primary phase; (3) the eutectic lamellae growing normal to the phase boundary of the primary phase, hence forming a radial pattern; and (4) the primary phase decomposing to form copious discontinuous particles at lower temperatures. Certainly, it is highly demanding to obtain the perfect sunflower-like microstructure, in terms of the alloy compositions [Citation2,Citation21] and solidification conditions.[Citation2,Citation31–33] Whether the appearance of a sunflower-like structure bears any relation to the specific alloy compositions, or in another word whether such a unique structure can be achieved in other HEAs or multi-component alloy systems, for example, when the alloy compositions are not highly concentrated, or when the eutectics are no longer the NiAl-like B2 phase and Cr-rich A2 phase are interesting topics to be explored in the future.
Conclusions
In summary, the solidification micro-structure in a near-eutectic Al2CrCuFeNi2 HEA was studied, with a particular attention to the formation of the unique sunflower-like eutectic colony structure. During the solidification process, the Ni–Al-rich B2 phase formed as the primary phase with a spherical or ellipsoidal morphology, followed by the Ni–Al-rich B2/Cr-rich A2 eutectics growing on the primary phase in a radial manner, and finally the primary B2 phase decomposed at lower temperatures leading to the formation of copious nearly cubic particles, very possibly via the spinodal decomposition. The structural similarity to NiAl–Cr hypo-eutectics paves the way to further optimize the near-eutectic HEAs for high-temperature applications.
SG thanks the initiation funding from the Area of Advance Materials Science at Chalmers University of Technology. The research of CTL was supported by Hong Kong RGC Grant CityU/521411 at City University of Hong Kong, P. R. China.
REFERENCES
- Glicksman ME. Principles of solidification: an introduction to modern casting and crystal growth concepts. New York: Springer Verlag; 2010.
- Cline HE, Walter JL. The effect of alloy additions on the rod-plate transition in the eutectic NiAl–Cr. Metall Trans. 1970;1:2907–2917.
- Johnson DR, Chen XF, Oliver BF, Noebe RD, Whittenberger JD. Processing and mechanical properties of in-situ composites from the NiAl–Cr and the NiAl–(Cr,Mo) eutectic systems. Intermetallics. 1995;3:99–113. doi: 10.1016/0966-9795(95)92674-O
- Yeh JW, Chen YL, Lin SJ, Chen SK. High-entropy alloys—a new era of exploitation. Mater Sci Forum. 2007;560:1–9. doi: 10.4028/www.scientific.net/MSF.560.1
- Yeh JW, Chen SK, Lin SJ, Gan JY, Chin TS, Shun TT, Tsau CH, Chang SY. Nanostructured high-entropy alloys with multiple principal elements: novel alloy design concepts and outcomes. Adv Eng Mater. 2004;6:299–303. doi: 10.1002/adem.200300567
- Cantor B, Chang ITH, Knight P, Vincent AJB. Microstructural development in equiatomic multicomponent alloys. Mater Sci Eng A. 2004;375–377:213–218.
- Senkov ON, Wilks GB, Miracle DB, Chuang CP, Liaw PK. Refractory high-entropy alloys. Intermetallics. 2010;18:1758–1765. doi: 10.1016/j.intermet.2010.05.014
- Craievich PJ, Weinert M, Sanchez JM, Watson RE. Local stability of nonequilibrium phases. Phys Rev Lett. 1994;72:3076–3079. doi: 10.1103/PhysRevLett.72.3076
- Guo S, Hu Q, Ng C, Liu CT. More than entropy in high-entropy alloys: forming solid solutions or amorphous phase. Intermetallics. 2013;41:96–103. doi: 10.1016/j.intermet.2013.05.002
- Zhang Y, Zhou YJ, Lin JP, Chen GL, Liaw PK. Solid-solution phase formation rules for multi-component alloys. Adv Eng Mater. 2008;10:534–538. doi: 10.1002/adem.200700240
- Zhang Y, Yang X, Liaw PK. Alloy design and properties optimization of high-entropy alloys. JOM. 2012;64: 830–838. doi: 10.1007/s11837-012-0366-5
- Guo S, Liu CT. Phase stability in high entropy alloys: formation of solid-solution phase or amorphous phase. Prog Nat Sci Mater Int. 2011;21:433–446. doi: 10.1016/S1002-0071(12)60080-X
- Tsai KY, Tsai MH, Yeh JW. Sluggish diffusion in Co–Cr–Fe–Mn–Ni high-entropy alloys. Acta Mater. 2013;61:4887–4897. doi: 10.1016/j.actamat.2013.04.058
- Ng C, Guo S, Luan JH, Shi SQ, Liu CT. Entropy-driven phase stability and slow diffusion kinetics in Al0.5CoCrCuFeNi high entropy alloy. Intermetallics. 2012;31:165–172. doi: 10.1016/j.intermet.2012.07.001
- Hsu CY, Juan CC, Wang WR, Sheu TS, Yeh JW, Chen SK. On the superior hot hardness and softening resistance of AlCoCrxFeMo0.5Ni high-entropy alloys. Mater Sci Eng A. 2011;528:3581–3588. doi: 10.1016/j.msea.2011.01.072
- Li BS, Wang YR, Ren MX, Yang C, Fu HZ. Effects of Mn, Ti and V on the microstructure and properties of AlCrFeCoNiCu high entropy alloy. Mater Sci Eng A. 2008;498:482–486. doi: 10.1016/j.msea.2008.08.025
- Ma SG, Zhang Y. Effect of Nb addition on the microstructure and properties of AlCoCrFeNi high-entropy alloy. Mater Sci Eng A. 2012;532:480–486. doi: 10.1016/j.msea.2011.10.110
- Zhu JM, Fu HM, Zhang HF, Wang AM, Li H, Hu ZQ. Microstructures and compressive properties of multicomponent AlCoCrFeNiMox alloys. Mater Sci Eng A. 2010;527:6975–6979. doi: 10.1016/j.msea.2010.07.028
- Mishra AK, Samal S, Biswas K. Solidification behaviour of Ti–Cu–Fe–Co–Ni high entropy alloys. Trans Indian Inst Met. 2012;65:725–730. doi: 10.1007/s12666-012-0206-x
- Guo S, Ng C, Lu J, Liu CT. Effect of valence electron concentration on stability of fcc or bcc phase in high entropy alloys. J Appl Phys. 2011;109:103505. doi: 10.1063/1.3587228
- Guo S, Ng C, Liu CT. Anomalous solidification microstructures in Co-free AlxCrCuFeNi2 high-entropy alloys. J Alloy Compd. 2013;557:77–81. doi: 10.1016/j.jallcom.2013.01.007
- Li M, Kuribayashi K. Free solidification of undercooled eutectics. Mater Trans. 2006;47:2889–2897. doi: 10.2320/matertrans.47.2889
- Tong CJ, Chen YL, Chen SK, Yeh JW, Shun TT, Tsau CH, Lin SJ, Chang SY. Microstructure characterization of AlxCoCrCuFeNi high-entropy alloy system with multiprincipal elements. Metall Mater Trans A. 2005;36: 881–893. doi: 10.1007/s11661-005-0283-0
- Singh S, Wanderka N, Murty BS, Glatzel U, Banhart J. Decomposition in multi-component AlCoCrCuFeNi high-entropy alloy. Acta Mater. 2011;59:182–190. doi: 10.1016/j.actamat.2010.09.023
- Zhu JZ, Chen LQ, Shen J. Morphological evolution during phase separation and coarsening with strong inhomogeneous elasticity. Modell Simul Mater Sci Eng. 2001;9:499–511. doi: 10.1088/0965-0393/9/6/303
- Xiao X, Guo JT, Yu HP. Microstructure and mechanical properties of NiAl(Ti)–Cr(Mo) eutectic alloy. Acta Metall Sin. 2006;42:1031–1035.
- Sundquist BE, Mondolfo LF. Heterogeneous nucleation in the liquid-to-solid transformation in alloys. Trans Metall Soc AIME. 1961;221:157–164.
- Li HT, Guo JT, Huai KW, Ye HQ. Microstructure characterization and room temperature deformation of a rapidly solidified NiAl-based eutectic alloy containing trace Dy. J Crys Growth. 2006;290:258–265. doi: 10.1016/j.jcrysgro.2005.12.089
- Huang W, Chang YA. Thermodynamic properties of the Ni–Al–Cr system. Intermetallics. 1999;7:863–874. doi: 10.1016/S0966-9795(98)00138-1
- Xiao X, Guo JT, Yu HP. Microstructure and mechanical properties of an electromagnetic centrifugal casting NiAl eutectic alloy. Acta Metall Sin. 2005;41:507–510.
- Dahle AK, Nogita K, Zindel JW, McDonald SD, Hogan LM. Eutectic nucleation and growth in hypoeutectic Al–Si alloys at different strontium levels. Metall Mater Trans A. 2001;32:949–960. doi: 10.1007/s11661-001-0352-y
- Mullins WW, Sekerka RF. Morphological stability of a particle growing by diffusion or heat flow. J Appl Phys. 1963;34:323–329. doi: 10.1063/1.1702607
- Trivedi R. Morphological stability of a solid particle growing from a binary alloy melt. J Crys Growth. 1980;48: 93–99. doi: 10.1016/0022-0248(80)90197-9