ABSTRACT
The fracture behavior of ultrafine WC–Co cemented carbide was demonstrated by in situ tensile tests in a transmission electron microscope. Using two kinds of cemented carbide samples with and without previously introduced microcracks, the process from deformation till fracture was studied. Particularly, the development and interaction of dislocations within Co and WC, as well as the alternation of dislocation motion between the two phases, was demonstrated, and the features of crack propagation in cemented carbide were disclosed. The finding of the dislocation characteristics and its correlation with the fracture behavior proposed the mechanisms of the ultrahigh fracture strength of the cemented carbide.
GRAPHICAL ABSTRACT
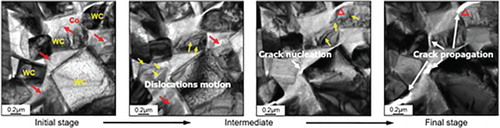
IMPACT STATEMENT
The fracture behavior of ultrafine WC–Co cemented carbide was for the first time directly observed by in situ TEM tensile tests. The correlation of dislocation motion and fracture mechanisms was proposed.
WC–Co cemented carbides have been widely used in industries, such as cutting tools and wear-resistant parts, due to their high hardness, excellent wear resistance and good fracture strength. To obtain a long lifetime and high machining precision of the end mill, printed circuit board drill and cutting blade made of cemented carbide, understanding of the fracture mechanism of the cemented carbide materials is of prime importance.[Citation1–3] Some researchers have attempted to investigate the fracture behavior of the WC–Co cemented carbide materials.[Citation4–6] However, as a typical ceramic material, the WC–Co cemented carbides usually exhibit brittle characteristic in the fracture behavior, which is very difficult to investigate the details of failure and demonstrate the fracture mechanism.[Citation7]
To disclose unambiguously the fracture characteristics of the cemented carbides, recently, we carried out in situ tensile tests in the transmission electron microscope (TEM) for the cemented carbide material, which was prepared by sinter-HIP densification of the WC–Co composite powder synthesized by in situ reactions.[Citation8] The mechanical properties of the prepared WC–12Co bulk material were firstly measured. The hardness was obtained by the Vickers hardness tester with a load of 30 kg. The fracture toughness (KIC) was determined by measuring the crack length then calculating with the equation KIC = 0.0028(HP/L)1/2, where H is the indentation hardness, P is the indentation load and L is the total crack length.[Citation9] The transverse rupture strength (TRS) was measured by the three-point bending method with the dimensions of the specimen as 20 × 6.5 × 5.25 mm according to the standard of ISO3327:2009. At least five specimens were prepared for the measurements of each property. The measured mechanical properties of the WC–12Co bulk material are given in Table , which shows that the cemented carbide sample has excellent combined mechanical properties, especially the fracture toughness and strength. The high fracture strength makes the sample available to carry out the in situ tensile tests to study the fracture behavior of the cemented carbide material.
Table 1. Mechanical properties of the prepared WC-12Co bulk sample.
The thin film of the cemented carbide material used for the in situ tensile tests was sampled by the focused ion beam (HELIOS NANOLAB 600i) with a voltage of 30 kV. Then, the film was repaired under a voltage of 2–5 kV to ensure the damage layer less than 5 nm at the surface of the film. The axial tensile tests were performed on two kinds of cemented carbide films, with and without previously introduced microcracks. As described in the literature,[Citation10] the pulling force is provided by the bimetallic plates, which were arranged to bend slowly in opposite directions under heating (from room temperature to <100°C), actuating the uniaxial pulling of the sample at an estimated strain rate of about 10−4 s−1. The in situ observation was made using JEOL 2010 TEM, and the details were analyzed by the high-resolution TEM (HRTEM, JEM-2100F) operated at 200 kV.
Figure (a) shows the TEM microstructure of the cemented carbide film without introducing microcrack before the tensile test. It can be seen in Figure (b) that there are some dislocations in the WC grain, as indicated by the arrows, which may be generated by the thermal stress or milling of the WC–Co powder before sintering.[Citation11,Citation12] These dislocations are mainly pinned with each other and hard to be triggered.
Figure 1. In situ TEM observations of fracture behavior of WC–Co cemented carbide: (a)–(i) follows the time sequence of the tensile test. Dislocations in Co and WC are indicated by red and yellow arrows, respectively.
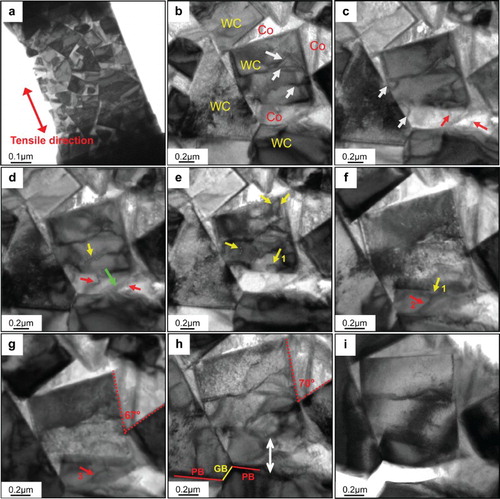
At the beginning of the tensile process, the stress was prone to be generated and concentrated at the regions near the grain triple junctions, as indicated by the arrows in Figure (c). Then, some dislocations were observed to move from the center of Co to the boundary. The dislocations within the Co binder phase are relatively more active, leading to a higher density, as marked by the thick green arrow in Figure (d). With loading and increase in the piled up dislocations, the Co binder was gradually strengthened by work hardening. As a result, further motion of dislocations is hindered in the Co binder, and stress concentration may occur at the WC/Co boundary. Subsequently, some dislocations were triggered in the neighboring WC grain. In the literature, the slip systems containing the basal and prismatic planes of the WC crystal were confirmed,[Citation13,Citation14] which contribute to the plastic deformation of WC grains. Moreover, the pyramidal planes {2–1–12} are possible to contain dislocations with Burger’s vector as b = 1/3[−2113], which may further lead to stacking faults by cross-slipping to {10–10} prism and {1211}/{10–11} pyramidal planes.[Citation11] As shown in Figure (e,f), the dislocations in the WC grain are active, and the motion direction of the dislocation marked as ‘1’ is from inside the WC grain to the WC/Co phase boundary (PB), and then the dislocation crosses the interface and slip in the binder phase. The dislocation ‘1’ combined with dislocation ‘2’, which was generated in the Co binder, and then merged into dislocation ‘3’. Generally, there are several orientation relationship with coherent or semi-coherent interfaces between WC and Co phases, for example, (0001)WC//{111}Co, (0001)WC//{100}Co and (0001)WC//{10–10}Co,[Citation8,Citation15,Citation16] which is favorable to obtain high toughness and high fracture strength of the cemented carbides. In the slip systems of WC and Co phases, there are also some corresponding atomic planes with small angle orientation difference (less than 10o) at certain coherent WC/Co interfaces, such as (10–11)WC and (001)Co planes at the (0001)WC//(111)Co interface. In these planes, the resolving shear stress is high enough to activate the dislocations in the slip system of Co, and thus penetration of the dislocation at specific interfaces is possible. The above all contribute to inhibit the nucleation of cracks in the cemented carbide. At the final fracture stage, as shown in Figure (g–i), the crack nucleated at the WC and Co grain boundaries (GB), and then propagated along the GB, partial WC/Co PB and region of stress concentration in Co, as indicated by the arrows in Figure (h,i). At the same time, large deformation occurred in the microstructure.
For the whole tensile process, the mechanical behavior of the sample can be described as the following procedures. At the early stage, in an elastic process the microstructure has little change. Then with loading, the dislocations existing in the Co phase are triggered to coordinate local stress concentration. With the increase in loading when the work hardening occurs in the Co phase, the dislocations in WC grains are gradually involved in the slipping. Apparent plastic deformation occurs in the Co phase before crack nucleation. The crack propagates in the order of preference as: in the Co binder, then along the WC/WC GB and WC/Co PB (see movie in supplementary material).
To make clear how the dislocations influence the crack propagation, we performed the in situ TEM observation of the tensile test of the cemented carbide film sample containing cracks. As shown in Figure (a,b), there are two small cracks in the sample. Generally, for a brittle material, the crack grows very fast under the external load.[Citation17,Citation18] However, for the present cemented carbide sample with high toughness and fracture strength, the characteristics of ductile fracture are observed. In Figure (c), at the early stage of the tensile test, it was found that the crack propagation is impeded by the dislocations that are very active in the Co binder (marked by thick arrows) and also the dislocations in the WC grain (marked by thin arrow), which are close to the tip of the crack. It suggests that the slip system in the WC grain is activated by the stress concentration near the crack tip, and hence the crack growth rate is decreased due to the reduction of the driving force.[Citation19] The crack propagates little with the width of the tip maintaining as about 20 nm, which can be attributed to the initiation of dislocations in the WC grains (Figure (d–f)). Consequently, the crack propagation along the WC/Co boundary and within WC grains can be weakened. However, once the work hardening occurs in the Co binder and motion of dislocations in WC is stagnated, cracks may nucleate at some position due to the stress accumulation, as marked by the thick arrow in Figure (g). It is also found that the dislocations piled up in the WC grain, which led to crack propagation. The path of crack propagation is observed along the WC GB, partial PB and in the Co phase (Figure (h,i)). From comparison of Figure (h,i), as indicated by the angles, the crack tip opens before propagation, which is a typical characteristic of the toughness property of the material. It can be seen that the dislocations motion, wherever it occurs in Co or WC grains, can coordinate effectively the local stress concentration and hence hinder the crack nucleation and propagation. Therefore, a high toughness against rapid fracture can be achieved in the cemented carbide in spite of its ceramic intrinsic property.
Figure 2. In situ TEM observations of crack propagation in the WC–Co cemented carbide sample containing microcracks: (a)–(i) follows the time sequence of the tensile test.
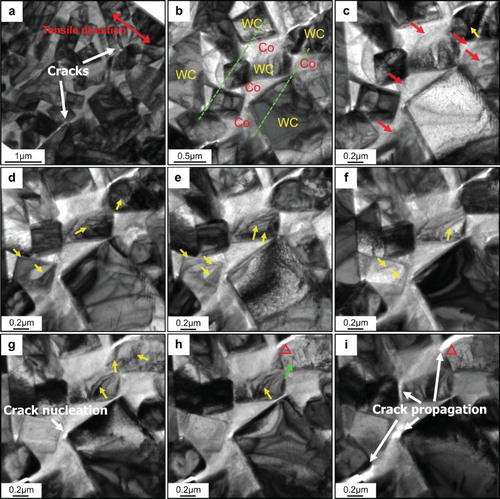
For the cemented carbide material with the submicron-scale microstructure, the plastic deformation of the Co binder still plays a significant role in impeding cleavage fracture of the sample. As shown in Figure (a–c), obvious plastic deformation occurs in the Co binder. The deformation stacking faults and piled-up dislocations in the Co phases are potential positions of fracture, as seen in Figure (d). Due to slip of {111}Co, as caused by continuous loading, the work hardening in Co-fcc is often induced by the stacking faults, which may lead to a martensitic phase transformation from Co-fcc to Co-hcp,[Citation20] which decrease the toughness of the Co binder.
Figure 3. Plastic deformation of the Co binder phase in the WC–Co cemented carbide: (a–c) follows the time sequence of the tensile test, (d) is the HRTEM analysis of the deformed Co phase.

In summary, the fracture behavior of the WC–Co cemented carbide with submicron microstructure was investigated by in situ tensile tests in TEM. The microstructure evolution during loading is revealed, and the fracture mechanisms are proposed. At the early tensile stage, the cemented carbide is at an elastic state. With the increase in stress, the slip system of dislocations initiates at first in the Co binder, and then the dislocation motion starts. With the increase in dislocation density, the work hardening occurs in the Co binder. Alternatively, the dislocations are activated in the WC grains. The alternative motion of dislocations hinders the nucleation and propagation of cracks in the cemented carbide. Therefore, the cooperation of the Co binder and WC grains facilitates to release local stress hence increase the fracture strength of the cemented carbide. For the cemented carbide containing microcracks, coordination of dislocations in WC and Co closed to the crack tip is effective to inhibit crack propagation. Particularly, the Co binder plays a significant role in the coordination of stress concentration through local plastic deformation, thus the cemented carbide is protected from cleavage fracture.
supplementary_material.mp4
Download MP4 Video (9.2 MB)Disclosure statement
No potential conflict of interest was reported by the authors.
Additional information
Funding
References
- Fang ZZ. Correlation of transverse rupture strength of WC–Co with hardness. Int J Refract Met Hard Mater. 2005;23:119–127. doi: 10.1016/j.ijrmhm.2004.11.005
- Gille G, Szesny B, Dreyer K, et al. Submicron and ultrafine grained hardmetals for microdrills and metal cutting inserts. Int J Refract Met Hard Mater. 2002;20:3–22. doi: 10.1016/S0263-4368(01)00066-X
- Zheng LJ, Wang CY, Fu LY, Yang LP, Qu YP, Song YX. Wear mechanisms of micro-drills during dry high speed drilling of PCB. J Mater Process Technol. 2012;212:1989–1997. doi: 10.1016/j.jmatprotec.2012.05.004
- Sarin VK, Johannesson T. On the deformation of WC–Co cemented carbides. The Metals Society. 1975;9:472–476. doi: 10.1179/030634575790444531
- Lay S. HRTEM investigation of dislocation interactions in WC. Int J Refract Met Hard Mater. 2013;41:416–421. doi: 10.1016/j.ijrmhm.2013.05.017
- Torres Y, Bermejo R, Gotor FJ, Chicardi E, Llanes L. Analysis on the mechanical strength of WC–Co cemented carbides under uniaxial and biaxial bending. Mater Des. 2014;55:851–856. doi: 10.1016/j.matdes.2013.10.051
- Namazu T, Morikaku T, Akamine H, Fujii T, Kuroda K, Takami Y. Mechanical reliability of FIB-fabricated WC–Co cemented carbide nanowires evaluated by MEMS tensile testing. Eng Fract Mech. 2015;150:126–134. doi: 10.1016/j.engfracmech.2015.07.007
- Liu XW, Song XY, Wang HB, Liu XM, Wang XL, Guo GS. Preparation and mechanisms of cemented carbides with ultrahigh fracture strength. J Appl Cryst. 2015;48:1254–1263. doi: 10.1107/S1600576715012832
- Shetty DK, Wright IG, Mincer PN, Clauer AH. Indentation fracture of WC–Co cermets. J Mater Sci. 1985;20:1873–1882. doi: 10.1007/BF00555296
- Wang LH, Han XD, Liu P, Yue YH, Zhang Z, Ma E. In situ observation of dislocation behavior in nanometer grains. Phys Rev Lett. 2010;105:135501–135504. doi: 10.1103/PhysRevLett.105.135501
- Gottschall RJ, Williams WS, Ward ID. Microstructural study of hot-deformed cemented carbides. Philos Mag. 1980;41(1):1–7. doi: 10.1080/01418618008241826
- Bock A, Zeiler B. Production and characterization of ultrafine WC powders. Int J Refract Met Hard Mater. 2002;20:23–30. doi: 10.1016/S0263-4368(01)00067-1
- Bolton JD, Redington M. Plastic deformation mechanisms in tungsten carbide. J Mater Sci. 1980;15:3150–3156. doi: 10.1007/BF00550388
- Csanádi T, Bľanda M, Chinh NQ, Hvizdoš P, Duszaa J. Orientation-dependent hardness and nanoindentation-induced deformation mechanisms of WC crystals. Acta Mater. 2015;83:397–407. doi: 10.1016/j.actamat.2014.09.048
- Song XY, Gao Y, Liu XM, Wei CB, Wang HB, Xu WW. Effect of interfacial characteristics on toughness of nanocrystalline cemented carbides. Acta Mater. 2013;61:2154–2162. doi: 10.1016/j.actamat.2012.12.036
- Wei CB, Song XY, Fu J, et al. Simultaneously high fracture toughness and transverse rupture strength in ultrafine cemented carbide. Cryst Eng Commun. 2013;15:3305–3307. doi: 10.1039/c3ce40211h
- Li AH, Zhao J, Wang D, Gao XL, Tang HW. Three-point bending fatigue behavior of WC–Co cemented carbides. Mater Des. 2013;45:271–278. doi: 10.1016/j.matdes.2012.08.075
- Taheri SM, Richart MN, Wolff C, Molinari JF. Dynamic crack propagation in a heterogeneous ceramic microstructure, insights from a cohesive model. Acta Mater. 2015;88:136–146. doi: 10.1016/j.actamat.2015.01.003
- Rice JR. Dislocation nucleation from a crack tip: an analysis based on the Peierls concept. J Mech Phys Solid. 1992;40(2):239–271. doi: 10.1016/S0022-5096(05)80012-2
- Vasel CH, Krawitz AD, Drake EF, Kenik EA. Binder deformation in WC-(Co, Ni) cemented carbide composites. Metall Mater Trans A. 1985;16:2309–2317. doi: 10.1007/BF02670431