ABSTRACT
An Al0.1CoCrFeNi high-entropy alloy (HEA) with a face-centered cubic structure in the as-cast and the recrystallized states is investigated. The mean grain size of the as-cast HEA is 14 times larger than that of the recrystallized HEA. The tension tests reveal that deformation twinning is the main mechanism dominating the plastic deformation of two HEAs. With a decrease in the grain size, twin spacing increases, and twin thickness decreases, which results in a low twinning activity. The twinning activity of the recrystallized HEA is strongly inhibited by grain refinement, which degrades the promotion of twinning on the strain-hardening ability and the tensile ductility.
GRAPHICAL ABSTRACT
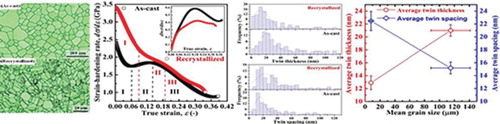
IMPACT STATEMENT
Grain refinement on strain hardening and twinning in a high-entropy alloy (HEA) is investigated, which is associated with the nanotwin substructure. Grain refinement decreases the twin thickness, and increases the twin spacing.
Simultaneously alloying many principal elements (usually ≥ 5) in an equimolar or near-equimolar composition is accepted as a radical alloy-design paradigm to form alloys [Citation1–12]. These multicomponent alloys are termed as high-entropy alloys (HEAs) due to their high configurational entropy of random solid solution states [Citation1,Citation3,Citation6]. What fascinate us is that HEAs have many superior mechanical and physical properties, such as ultrahigh fracture toughness comparable to the cryogenic steels [Citation13], excellent high strength [Citation3–5,Citation14,Citation15], significant resistance to fatigue, corrosion, and oxidation [Citation7–9,Citation16–19], outstanding high-temperature strength [Citation18–21], superconductivity [Citation22], etc. Such remarkable performances of HEAs are explained in general by four core effects, called high-entropy, sluggish diffusion, severe lattice distortion and cocktail effect [Citation3–5,Citation14].
Inspired by the good properties, there is an increasing interest to understand the correlation between the deformation behavior and the microstructures of HEAs [Citation1–13,Citation23–29]. Deformation twins, as a part of a deformed substructure, were observed in some HEAs [Citation13,Citation23–30]. As twinning depends strongly on the stacking fault energy (SFE), temperature, and strain rate [Citation31], the twin-HEAs were regarded to have a low SFE range [Citation32,Citation33]. Moreover, these HEAs showed very active twinning at cryogenic temperatures, high strain rates, or cycle loading, but very low even no twinning activity at ambient temperature or quasi-static loading [Citation8,Citation13,Citation23–29]. Not only SFE and temperature but also grain size have a strong influence on deformation twinning [Citation24,Citation25,Citation29,Citation30,Citation34–37]. Although a previous study has found that coarse-grained HEAs rather than fine-grained one contain nano-twinning [Citation29], the correlation between the grain size, the deformation twinning behavior, and the strain-hardening behavior has not been well elucidated.
In the present study, an Al0.1CoCrFeNi HEA with two different mean grain sizes is chosen. The effect of grain refinement on the strain-hardening behavior of the HEA, in particular its role on the twinning and twin substructure, is discussed.
Ingots (85 × 10 × 2 mm3) of the Al0.1CoCrFeNi alloy were prepared by arc melting a mixture of pure elements (purity ≥ 99.99%) under argon atmosphere and, then, suction casting into a water-cooled Cu mold. Cold rolling along the length direction was performed to reduce the thickness (2 mm) to be 0.75 mm. The rolled sheets subsequently were annealed for 1 h at 1073 K to obtain fully recrystallized and homogenized microstructures. The X-ray diffraction (XRD) measurements were conducted in a Gigaku D\max-2550 diffractometer with Cu-Kα radiation. Backscattered-electron imaging of the microstructure was conducted in a 7500F JEOL scanning-electron microscope (SEM). Electron-backscattering-diffraction (EBSD) tests were performed in a CamScan Apollo 300 SEM equipped with a HKL-Technology EBSD system. Tension tests at a strain rate of 1 × 10−3 s−1 were performed at an MTS CMT 5205 machine. The dog bone-shaped specimens with gauge geometry of 38 × 2 × 1.9 mm for the as-cast HEA, and ×0.45 mm for the recrystallized HEA, respectively, were fabricated. After fracture, the HEA were observed in a JEM-2010F transmission electron microscope (TEM) operated at 200 kV. The TEM samples were cut from the area close to the fracture surface, and then ground down to 30 µm in thickness, then, twin-jet polishing in a 5% (vol%) perchloric acid alcohol solution at a temperature of 243 K was performed to generate an electron-transparent region on the TEM samples.
The XRD patterns ((a)) show only single-phase face-centered cubic (fcc) peaks, revealing a single-phase fcc solid solution in both as-cast and recrystallized HEAs. The single-phase fcc structure is further confirmed by the EBSD images ((b,c)), and both EBSD-phase images exhibit the equiaxed grain structures in the as-cast and the recrystallized HEAs. Many grains contain the annealing twins in the recrystallized HEA. The average grain sizes, , measured from the EBSD images ((b,c)), are 114.9 ± 26.2 µm for the as-cast HEA, and 7.9 ± 0.2 µm for the recrystallized HEA (annealing twin boundaries (TBs) were not counted), indicating that the grain refinement was achieved by cold rolling followed by homogenization annealing. The statistical result of the grain-boundary misorientation distribution from the EBSD image of the as-cast HEA illustrates that the high-angle grain boundaries, that is, the grain-boundary angle ≥ 15°, have the maximum percentage (∼78%) ((d)). For the recrystallized HEA, a half of recrystallized grain boundaries are the annealing TBs, that is, the grain-boundary angle being ∑3 = 60°
((e)).
Figure 1. (a) XRD patterns of the Al0.1CoCrFeNi HEA in as-cast and recrystallized states; EBSD-phase map of (b) the as-cast HEA, (c) the recrystallized HEA; and the statistical result of the grain-boundary misorientation distribution of (d) the as-cast, and (e) the recrystallized HEAs.
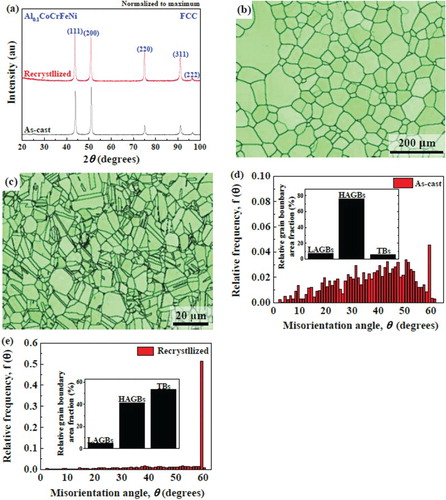
From the tension stress–strain curves ((a)), the yield strengths of the as-cast and recrystallized HEAs are noted to be 199 and 366 MPa, respectively. A strong increase (up to 84%) in the yield strength of the recrystallized HEA upon refining the grain size from 114.9 ± 26.2 (coarse-grained) to 7.9 ± 0.2 µm (fine-grained) is found. The ultimate strength and the global elongation of the as-cast and the recrystallized HEAs are 531, 715 MPa and 60%, 46%, respectively, which indicates significant strain-hardening behaviors in both curves.
Figure 2. (a) Tensile true stress–strain curves of the as-cast and recrystallized HEAs at room temperature, (b) corresponding plots of strain-hardening rate versus true strain, and the inset illustrates the instantaneous strain-hardening exponent versus true strain of two HEAs; the lateral surface morphology image of fractured samples of (c) the as-cast, and (d) the recrystallized HEAs.
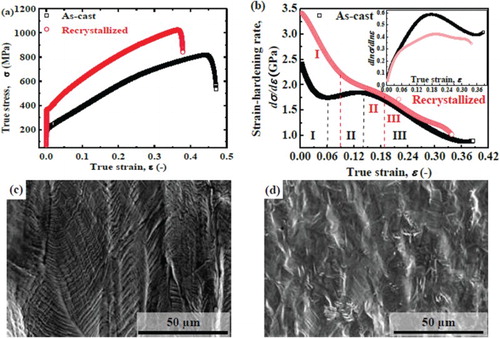
According to stress–strain curves, the strain-hardening rates (dσ/dε) versus true strain curves are plotted in (b), which can be classified into three regions. In region I, the strain-hardening rates of the as-cast and the recrystallized HEAs decrease lineally from 2.4 to 1.75 GPa, and from 3.5 to 2.2 GPa, respectively. With an increase in the strain, the strain-hardening rate of the as-cast HEA gradually increases to the peak value of 1.85 GPa at the strain of 0.14, while the decreasing rate (the slope) of the strain-hardening rate is reduced in the range from 0.09 to 0.19 for the recrystallized HEA in region II. The increase in the strain-hardening rate in region II is unique and rarely reported among HEAs [Citation25,Citation29,Citation30], but is very popular in TWIP steels [Citation34,Citation38]. In region III, the strain-hardening rate progressively decreases with further increasing strain for both two HEAs. To further characterize the strain-hardening behavior, the instantaneous strain-hardening exponent, n (n = d ln σ/d ln ε) as a function of strain, is calculated in the inset of (b). It is obvious that the n value varies with the strain for both HEAs. At early stages of deformation (below the strain of 0.06), the n value of the as-cast HEA is almost the same as that of the recrystallized HEA. After the strain of 0.06, the n value of the as-cast HEA is always larger than that of the recrystallized HEA.
(c,d) shows the SEM images of the lateral surface of the as-cast and recrystallized HEAs after tension fracture, respectively, exhibiting strong plastic distortions of the grains and numerous slip bands inside the grains. Compared to those in the recrystallized HEA, more slip bands are presented inside the grains, and a higher height of the slipping ledge is observed in the as-cast HEA. Some slip bands intersected intensively with each other in the as-cast HEA ((c)).
The deformation-induced microstructural evolution of the as-cast HEAs is characterized by TEM in . A bright-field (BF) image of the as-cast HEA ((a)), and a corresponding selected area diffraction (SAED) pattern (i.e. the image along Z = [011]) (the inset of (a)), confirm the single-phase fcc structure of the as-cast HEA. (b) shows the DF image of the fractured microstructure of the as-cast HEA, in which some narrow deformation twins (marked by the yellow rings in (b)) with a width of tens of nanometer are observed. The twin substructure is further characterized by the corresponding SAED pattern (i.e. the image along Z = [110]), (the inset of (b)). (c,d) reveals the single-phase fcc structure of the recrystallized HEA. Some large and wide annealing twins with a width of nearly 500 nm can be found in the grains ((c)). After tension, some nanotwins bundles (marked by the yellow rings in (d)) with one side near the grain boundary can be observed, which can be directly evidenced by the corresponding SAED pattern (the inset of (d)).
Figure 3. Representative TEM micrographs of the microstructure evolution of the as-cast and the recrystallized Al0.1CoCrFeNi HEA subjected to tension deformation: (a) BF image, inset of selected-area diffraction pattern of the microstructure without tension deformation, (b) dark-field image, inset of selected-area diffraction pattern of the tension-fractured substructure of the as-cast HEA, (c) BF image, inset of selected-area diffraction pattern of the microstructure without tension deformation, and (d) dark-field image, inset of selected-area diffraction pattern of the tension-fractured substructure of the recrystallized HEA.
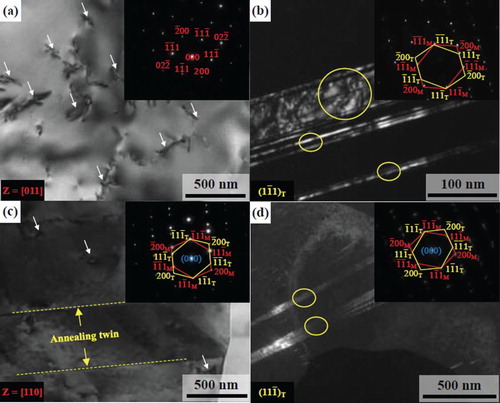
shows the statistical measurements of twins in the as-cast and the recrystallized HEAs. Twin thickness and twin spacing are two important values that characterize the twinning behavior in HEAs. (a) representatively shows the DF image of the twin structures in the fractured as-cast HEA. Twin thickness is the spacing between two deformation TBs, and twin spacing is the spacing between two neighboring deformation twins [Citation39,Citation40], which are shown in (a). For multiple twin lamellae adjoined with each other, the twin thickness means the spacing between the two boundaries of one lamellae, as shown in (a). The statistical measurements of twin thicknesses in the as-cast and the recrystallized HEAs are 21 and 13 nm, respectively ((b)). The average spacing between adjacent twins are 15 and 23 nm for the as-cast and the recrystallized HEAs, respectively ((c)). The statistical results suggest that the thickness of deformation twins decreases, and the spacing remarkably increases with reducing in the grain size ((d)).
Figure 4. (a) Substructures of the fractured as-cast HEA. The rectangle highlights the untwined portions inside TBs; (b) the twin thickness, (c) twin spacing distributions of tension-fractured samples of the as-cast and recrystallized HEAs measured from numerous TEM images, and (d) the calculated average values of twin thickness and twin spacing versus mean grain size of the current Al0.1CoCrFeNi HEA.
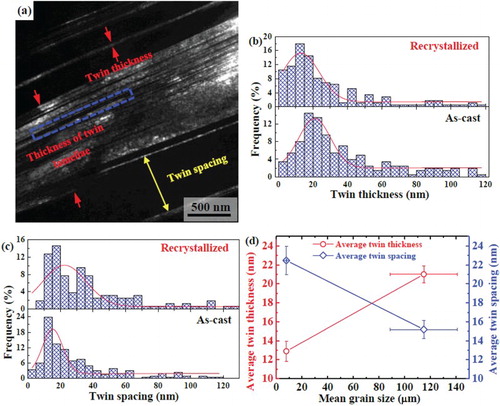
The results of the present study demonstrate that the Al0.1CoCrFeNi HEA presents a stable single fcc solid solution and high tensile ductility at room temperature. A strong grain refinement strengthening is achieved when the grain size is decreased from 114.9 ± 26.2 µm of the as-cast state to 7.9 ± 0.2 µm of the recrystallized state. Both the as-cast and the recrystallized HEAs show the high strain-hardening ability and ductility, which is microscopically and intrinsically attributed to the twinning mechanism. The deformation twins in HEAs, including CoCrFeMnNi and CrFeMnNi18 alloys, have been observed at 77 K or high strain-rate deformation [Citation13,Citation23–25,Citation27]. Moreover, CoCrFeMnNi-0.5C [Citation28], and Fe40Mn40Co10Cr10 [Citation30] alloys undergo twinning by alloying elements to reduce SFE. Our results indicate that mechanically twinning in the Al0.1CoCrFeNi HEA is more active than the above CoCrFeMnNi alloys during tension deformation.
Both the as-cast and recrystallized Al0.1CoCrFeNi HEA exhibit a remarkably high strain hardening. The strain-hardening behavior in region I ((b)) is characterized by a decreasing strain-hardening rate that is similar to the behavior of fcc metals with high SFE [Citation29,Citation38,Citation41], and also agrees with that of low SFE HEAs [Citation25,Citation29,Citation30]. Therefore, the strain-hardening mechanism in region I ((b)) is attributed to the dislocation-control plasticity, including the prevalence of dynamic recovery processes, such as cross-slip and annihilation of screw dislocations of opposite signs [Citation29,Citation36,Citation38,Citation41]. For the recrystallized HEA, the grain refinement reduces the dislocation mean free path, and a larger value of the strain-hardening rate than that of the as-cast HEA during the whole plastic regime is observed in (b) [Citation34,Citation37,Citation41]. In region II, the strain-hardening rate of the as-cast HEA increases, and the decreasing rate of the strain-hardening rate of the recrystallized HEA decreases, which is believed to be associated with the effect of deformation twinning [Citation25,Citation29,Citation37,Citation38,Citation41]. The twin boundary acts as a strong obstacle to prohibit the dislocation motion, which serves as an efficient site for the dislocation accumulation similar to grain boundaries [Citation25,Citation29,Citation30,Citation35,Citation38,Citation41]. With further straining, in region III, the strain-hardening rate decreases, which is possibly attributed to a slip-dominated plasticity, indicating the reduced capability for trapping more dislocations into the refined microstructure [Citation29,Citation38,Citation41].
The as-cast HEA exhibits a higher instantaneous n value than that of the recrystallized HEA when the strain value is above 0.06 (the inset of (b)). A high n value means a strong strain-hardening ability to postpone necking, which causes the as-cast HEA behave with better ductility [Citation25,Citation41]. Furthermore, in region II of the plastic deformation, the strain-hardening rate of the as-cast HEA increases approximately by 0.15 GPa, while the value of the recrystallized HEA decreases. Such an increase of the strain-hardening rate in region II surely contributes to the more rapid growth of the n value of the as-cast HEA, then, leading to better ductility [Citation38,Citation41].
The opposite trends of the strain-hardening rates in region II for the as-cast and the recrystallized HEAs are inherently induced by the nanotwin substructure. According to the dislocation theory of strain hardening, the strain-hardening rate, θ, can formally be written as [Citation41]
(1)
where α is a constant related to thermal activation, μ is the shear modulus, ρ is the statistical stored dislocation density, and Λ is the dislocation-free path. The TBs, as well as the grain boundaries, are the main microstructural obstacles for the gliding dislocations, which can be possibly written as [Citation41–44]
(2)
where d is the mean grain size, t is the average twin spacing, k is a constant, and the third term on the right-hand side is proportional to the forest dislocation spacing. As compared with the case in the as-cast HEA, the larger twin spacing of the recrystallized HEA means the coarser refinement of the dislocation-free path, and the weaker promotion of the strain-hardening rate caused by deformation twins [Citation34,Citation41–44]. When glide dislocations encounter nanoTBs, pile-up, and stress concentrate, then the dislocations can propagate through the twins if dislocation dissociation reactions occur [Citation45–48]. Such a dissociation can improve the dislocation accumulation capability and, thus, enhance the strain-hardening ability. In the present study, the larger the twin thickness of the as-cast HEA, the lower external stress for the glide dislocations is needed to cross the nanotwins boundaries. Hence, it is easy for glide dislocations of the as-cast HEA to dissociate to transmit across the nanotwin bundles, which significantly increases the dislocation accumulation capability [Citation47,Citation48]. Therefore, a weak effect of twinning on the improvement of strain hardening occurs in the fine-grained structure of the recrystallized HEA.
The smaller twin spacing and larger twin thickness illustrates that twinning in the as-cast HEA is more activated than in the recrystallized HEA [Citation31,Citation34,Citation36,Citation38]. The grain size is well known as the sensitively intrinsic variable of mechanically twinning [Citation31]. For polycrystalline materials, the yield strength, σ, and grain size, d, always follow the Hall–Petch behavior, (where σ0 and k are size-independent constants, a is an exponent typically between 0.5 and 1). k is the Hall–Petch slope, whose value for the twinning-mediated plasticity is much larger (up to 10 times) than that for dislocation-glide plasticity [Citation35,Citation36], no matter dislocation glide or twinning is regarded as the major deformation mechanism [Citation29,Citation31,Citation35,Citation36,Citation38,Citation48]. According to the Hall–Petch behavior, a decrease in the average grain size results in a higher twin nucleation stress, which could hardly be achieved by strain hardening. Thus, it is hard to deform by twinning in the recrystallized HEA. Therefore, the relatively low twinning activity of the recrystallized HEA in the current study is due to the grain refinement, as reported in TWIP steels, brasses, stainless steels, etc. [Citation29,Citation31,Citation34,Citation37,Citation49].
A strong effect of grain refinement on the strain-hardening and twinning behavior in the Al0.1CoCrFeNi HEA is investigated, which is ascribed to the nanotwin substructure formed upon straining. Grain refinement of the recrystallized HEA results in a higher strength than the as-cast HEA, decreases the twin thickness and increases the twin spacing. This trend causes the strain-hardening rate of the recrystallized HEA to be decreased and that of the as-cast increased with increasing strain in the strain ranged from 0.09 to 0.19 and 0.06 to 0.14, respectively, which leads to the lower tensile ductility of the recrystallized HEA.
Disclosure statement
No potential conflict of interest was reported by the authors.
Additional information
Funding
References
- Yeh JW, Chen SK, Lin SJ, et al. Nanostructured high entropy alloys design with multiple principle elements: novel alloy design concepts and outcomes. Adv Eng Mater. 2004;6:299–303. doi: 10.1002/adem.200300567
- Cantor B, Chang ITH, Knight P, et al. Microstructural development in equiatomic multicomponent alloys. Mater Sci Eng A. 2004;375–377:213–218. doi: 10.1016/j.msea.2003.10.257
- Zhang Y, Zuo TT, Tang Z, et al. Microstructures and properties of high-entropy alloys. Prog Mater Sci. 2014;61:1–93. doi: 10.1016/j.pmatsci.2013.10.001
- Lu ZP, Wang H, Chen MW, et al. An assessment on the future development of high-entropy alloys: summary from a recent workshop. Intermetallics. 2015;66:67–76. doi: 10.1016/j.intermet.2015.06.021
- Ye YF, Wang Q, Lu J, et al. High-entropy alloy: challenges and prospects. Mater Today. 2015;19:349–362. doi: 10.1016/j.mattod.2015.11.026
- Zhang Y, Zhou YJ, Lin JP, et al. Solid-solution phase formation rules for multi-component alloys. Adv Eng Mater. 2008;10:534–538. doi: 10.1002/adem.200700240
- Hemphill MA, Yuan T, Wang GY, et al. Fatigue behavior of Al0.5CoCrCuFeNi high entropy alloys. Acta Mater. 2012;60:5723–5734. doi: 10.1016/j.actamat.2012.06.046
- Tang Z, Yuan T, Tsai CW, et al. Fatigue behavior of a wrought Al0.5CoCrCuFeNi two-phase high-entropy alloy. Acta Mater. 2015;99:247–258. doi: 10.1016/j.actamat.2015.07.004
- Mohsen SF, Li DY, Zhang Y, et al. Fracture toughness and fatigue crack growth behavior of as-cast high-entropy alloys. JOM. 2015;67:2288–2295. doi: 10.1007/s11837-015-1563-9
- Santodonato LJ, Zhang Y, Feygenson M, et al. Deviation from high-entropy configurations in the atomic distributions of a multi-principal-element alloy. Nat Commun. 2015;6:5964. doi: 10.1038/ncomms6964
- Zhang Y, Yang X, Liaw PK. Alloy design and properties optimization of high-entropy alloys. JOM. 2012;64:830–838. doi: 10.1007/s11837-012-0366-5
- Gao MC, Yeh JW, Liaw PK, et al. High-entropy alloys: fundamentals and applications. Cham: Springer International; 2016.
- Gludovatz B, Hohenwarter A, Catoor D, et al. A fracture-resistant high-entropy alloy for cryogenic applications. Science. 2014;345:1153–1158. doi: 10.1126/science.1254581
- Tsai KY, Tsai MH, Yeh JW. Sluggish diffusion in Co–Cr–Fe–Mn–Ni high-entropy alloys. Acta Mater. 2013;61:4887–4897. doi: 10.1016/j.actamat.2013.04.058
- Youssef KM, Zaddach AJ, Niu CN, et al. A novel low-density, high-hardness, high-entropy alloy with close-packed single-phase nanocrystalline structures. Mater Res Lett. 2015;3:95–99. doi: 10.1080/21663831.2014.985855
- Lee CP, Chen YY, Hsu CY, et al. The effect of boron on the corrosion resistance of the high entropy alloys Al0.5CoCrCuFeNiBx. J Electrochem Soc. 2007;154(8):C424–C430. doi: 10.1149/1.2744133
- Chuang MH, Tsai MH, Wang WR, et al. Microstructure and wear behavior of AlxCo1.5CrFeNi1.5Tiy high-entropy alloys. Acta Mater. 2011;59:6308–6317. doi: 10.1016/j.actamat.2011.06.041
- Senkov ON, Wilks GB, Miracle DB, et al. Refractory high-entropy alloy. Intermetallics. 2010;18:1758–1765. doi: 10.1016/j.intermet.2010.05.014
- Senkov ON, Wilks GB, Scott JM, et al. Mechanical properties of Nb25Mo25Ta25W25 and V20Nb20Mo20Ta20W20 refractory high entropy alloys. Intermetallics. 2011;19:698–706. doi: 10.1016/j.intermet.2011.01.004
- Senkov ON, Senkova SV, Woodward C, et al. Low-density, refractory multi-principal element alloys of the Cr–Nb–Ti–V–Zr system: microstructure and phase analysis. Acta Mater. 2013;61:1545–1557. doi: 10.1016/j.actamat.2012.11.032
- Zou Y, Ma H, Spolenak R. Ultrastrong ductile and stable high-entropy alloys at small scales. Nat Commun. 2015;6:8748. doi: 10.1038/ncomms9748
- Koželj P, Vrtnik S, Jelen A, et al. Discovery of a superconducting high-entropy alloy. Phy Rev Lett. 2014;113:107001. doi: 10.1103/PhysRevLett.113.107001
- Stepanov N, Tikhonovsky M, Yurchenko N, et al. Effect of cryo-deformation on structure and properties of CoCrFeNiMn high-entropy alloy. Intermetallics. 2015;59:8–17. doi: 10.1016/j.intermet.2014.12.004
- Schuh B, Mendez-Martin F, Völker B, et al. Mechanical properties, microstructure and thermal stability of a nanocrystalline CoCrFeMnNi high-entropy alloy after severe plastic deformation. Acta Mater. 2015;96:258–268. doi: 10.1016/j.actamat.2015.06.025
- Otto F, Dlouhy A, Somsen C, et al. The influences of temperature and microstructure on the tensile properties of a CoCrFeMnNi high-entropy alloy. Acta Mater. 2013;61:5743–5755. doi: 10.1016/j.actamat.2013.06.018
- Zhang ZJ, Mao MM, Wang JW, et al. Nanoscale origins of the damage tolerance of the high-entropy alloy CrMnFeCoNi. Nat Commun. 2015;6:10143. doi: 10.1038/ncomms10143
- Wu Z, Bei H. Microstructures and mechanical properties of compositionally complex Co-free FeNiMnCr18 FCC solid solution alloy. Mater Sci Eng A. 2015;640:217–224. doi: 10.1016/j.msea.2015.05.097
- Wu Z, Parish CM, Bei H. Nano-twin mediated plasticity in carbon-containing FeNiCoCrMn high entropy alloys. J Alloys Compd. 2015;647:815–822. doi: 10.1016/j.jallcom.2015.05.224
- Komarasamy M, Kumar N, Tang Z, et al. Effect of microstructure on the deformation mechanism of friction stir-processed Al0.1 CoCrFeNi high entropy alloy. Mater Res Lett. 2015;3:30–34. doi: 10.1080/21663831.2014.958586
- Deng Y, Tasan CC, Pradeep KG, et al. Design of a twinning-induced plasticity high entropy alloy. Acta Mater. 2015;94:124–133. doi: 10.1016/j.actamat.2015.04.014
- Christian JW, Mahajan S. Deformation twinning. Prog Mater Sci. 1995;39:1–157. doi: 10.1016/0079-6425(94)00007-7
- Zaddach AJ, Niu C, Koch CC, et al. Mechanical properties and stacking fault energies of NiFeCrCoMn high-entropy alloy. JOM. 2013;65:1780–1789. doi: 10.1007/s11837-013-0771-4
- Huang S, Li W, Lu S, et al. Temperature dependent stacking fault energy of FeCrCoNiMn high entropy alloy. Scr Mater. 2015;108:44–47. doi: 10.1016/j.scriptamat.2015.05.041
- Gutierrez-Urrutia I, Raabe D. Grain size effect on strain hardening in twinning-induced plasticity steels. Scr Mater. 2012;66:992–996. doi: 10.1016/j.scriptamat.2012.01.037
- Yu Q, Shan ZW, Li J, et al. Strong crystal size effect on deformation twinning. Nature. 2010;463:335–338. doi: 10.1038/nature08692
- Gutierrez-Urrutia I, Zaefferer S, Raabe D. The effect of grain size and grain orientation on deformation twinning in a Fe–22 wt.% Mn–0.6 wt.% C TWIP steel. Mater Sci Eng A. 2010;527:3552–3560. doi: 10.1016/j.msea.2010.02.041
- El-Danaf E, Kalidindi SR, Doherty RD. Influence of grain size and stacking-fault energy on deformation twinning in fcc metals. Metall Mater Trans A. 1999;30:1223–1233. doi: 10.1007/s11661-999-0272-9
- Gutierrez-Urrutia I, Raabe D. Dislocation and twin substructure evolution during strain hardening of an Fe–22 wt.% Mn–0.6 wt.% C TWIP steel observed by electron channeling contrast imaging. Acta Mater. 2011;59:6449–6462. doi: 10.1016/j.actamat.2011.07.009
- Zhang X, Wang H, Chen X H, et al. High-strength sputter-deposited Cu foils with preferred orientation of nanoscale growth twins. Appl Phys Lett. 2006;88:173116. doi: 10.1063/1.2198482
- Lu L, Chen X, Huang X, et al. Revealing the maximum strength in nanotwinned copper. Science. 2009;323:607–610. doi: 10.1126/science.1167641
- Kocks UF, Mecking H. Physics and phenomenology of strain hardening: the FCC case. Prog Mater Sci. 2003;48:171–273. doi: 10.1016/S0079-6425(02)00003-8
- Estrin Y, Necking H. A unified phenomenological description of work hardening and creep based on one-parameter models. Acta Metall. 1984;32:57–70.
- Bouaziz O, Guelton N. Modelling of TWIP effect on work-hardening. Mater Sci Eng A. 2001;319-321:246–249. doi: 10.1016/S0921-5093(00)02019-0
- Bouaziz O, Allain S, Scott C. Effect of grain and twin boundaries on the hardening mechanisms of twinning-induced plasticity steels. Scr Mater. 2008;58:484–487. doi: 10.1016/j.scriptamat.2007.10.050
- Mahajan S, Chin GY. Twin-slip, twin-twin and slip-twin interactions in Co–8 wt.% Fe alloy single crystals. Acta Metall. 1973;21:173–179.
- Mahajan S, Chin GY. The interaction of twins with existing substructure and twins in cobalt-iron alloys. Acta Metall. 1974;22:1113–1119. doi: 10.1016/0001-6160(74)90066-2
- Lu L, Shen YF, Chen XH, et al. Ultrahigh strength and high electrical conductivity in copper. Science. 2004;304:422–426. doi: 10.1126/science.1092905
- Shen YF, Lu L, Lu QH, et al. Tensile properties of copper with nano-scale twins. Scr Mater. 2005;52:989–994. doi: 10.1016/j.scriptamat.2005.01.033
- Ueji R, Tsuchida N, Terada D, et al. Tensile properties and twinning behavior of high manganese austenitic steel with fine-grained structure. Scr Mater. 2008;59:963–966. doi: 10.1016/j.scriptamat.2008.06.050