ABSTRACT
Engineering transport properties of thermoelectric (TE) materials leads to incessantly breakthroughs in the zT values. Nevertheless, modular design holds a key factor to advance the TE technology. Herein, we discuss the structures of TE module and illustrate the inter-diffusions across the interface of constituent layers. For Bi2Te3-based module, soldering is the primary bonding method, giving rise to the investigations on the selections of solder, diffusion barrier layer and electrode. For mid-temperature PbTe-based TE module, hot-pressing or spark plasma sintering are alternative bonding approaches; the inter-diffusions between the diffusion barrier layer, electrode and TE substrate are addressed as well.
GRAPHICAL ABSTRACT
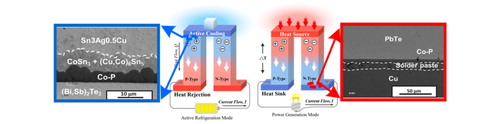
1. Introduction
In cope with the increasing energy demand, thermoelectric technology has attracted growing attentions, due to its capability in converting waste heat into useable electricity via the Seebeck effect [Citation1]. The conversion efficiency of a thermoelectric (TE) material is guided by a dimensionless figure-of-merit (zT = S2σ/κ), whereas the S refers to the Seebeck coefficient, σ is the electrical conductivity, T is the absolute temperature and κ is the thermal conductivity that comprises two contributors from the traveling phonons (κL) and the transporting electrons (κe), respectively. Strategies for zT enhancement have been enormously reported in the past decade, including the maximization of S thorough the band structure engineering [Citation2], the reduction of κ via the nanostructuring [Citation3] while maintaining high σ by increasing the carrier mobility. Accordingly, improving the electronic transport (i.e. power factor PF = S2σ) is one of the approaches, as the combinational effects of the convergence of heavy valence/conduction band [Citation2], quantum effect [Citation4,Citation5], etc.
The TE technology specializes in converting the waste heat below 800 K through Seebeck effect, so-called the thermoelectric generator (TEG). For the waste heat higher than 800 K, the thermal stability of TE material might be degraded. Peltier cooler (or referring as thermoelectric cooler, TEC) is a solid state heat pump used in various industrial applications, which provides cooling for lasers, diodes, refrigerators and automobiles or acts as temperature stabilizer for equipment and chips [Citation6]. Figure S1(a) and S1(b) show the schematic illustrations for the TEG and TEC, respectively. In this review paper, we discuss the state of art TE materials for TEC and TEG applications, and place great emphasis on the interfacial reactions between the TE materials, solders and diffusion barrier layers.
2. Low-temperature Bi2Te3-based modules
2.1 Bi2Te3-based materials
Since 1960s, the Bi2Te3-based materials have been the most well-established TE cooler, which reached zT > 1 in p-type (BixSb1−xTe3) [Citation7-11] and zT > 0.6 for n-type (Bi2(TexSe1−x)3) [Citation12-14]. The Bi2Te3 is a narrow-bandgap layered semiconductor with a trigonal unit cell, in which the van der Waal bonding between neighboring tellurium atoms in adjacent quintuple layers of Te(1)–Bi–Te(2)–Bi–Te(1), which makes it cleave easily along the trigonal axis. Such layered structure results in the highly anisotropic transportation of free electrons and phonons. e.g. σ is approximately four times greater perpendicular to the trigonal axis than in the parallel orientation, κ is about two times greater perpendicular to the trigonal axis than that parallel to it, and S is nearly isotropic [Citation12]. Therefore, the maximum zT occurs in the parallel orientation. Approaches for tuning the inter-related thermoelectric parameters of Bi2Te3-based materials including alloying or doping, to optimize power factor and/or to reduce thermal conductivity. For example, alloying equal mole of Sb and Se into Bi2Te3 makes κL reduce from 0.7 to 0.47 (W/mK) at 400 K [Citation11]. By additional Ag doping, an enhanced S and reduced κL ∼ 0.29 (W/mK) can be achieved in BiSbTe1.5Se1.5 [Citation11]
Nanostructuring has been considered as an effective way to reduce κL, as a result of enhancing phonon scattering at grain boundary, and to improve the thermoelectric performance and mechanical strength in various material systems. To reach a high bulk density and high thermoelectric performance, various methods such as spark plasma sintering (SPS) [Citation8], ball-milling following by hot-pressing [Citation9] or mechanical alloying (MA) [Citation10], are conducted to sinter Bi2Te3 powders into bulks, and are subsequently assembled together with their electrical interconnects into thermoelectric modules.
2.2 Solders in Bi2Te3-based modules
Solder is commonly used as a metallurgical junction between Cu electrodes and thermoelectric materials for low-temperature TE modules. Sn [Citation15, Citation16] and Sn-based alloys, such as Sn–Bi [Citation17-19], Sn–Cu [Citation20], Sn–Ag [Citation21], Sn–Sb [Citation22] and Sn–Ag–Cu [Citation23] are promising solders for Bi2Te3 modules. Several studies have depicted the interfacial reaction and the resultant microstructures at the junction between solders and Te substrate. For example, the interfacial reaction between pure Sn and pure Te leads to a very unique cruciform pattern [Citation15, Citation18] (Figure S2(a)), owing to the fast reaction-limit growth of SnTe IMC. In the Sn/Te couple, the Te acts as the dominant diffusion species, while the Sn also diffuses across the reaction region, to react with Te and form the duplex structure [Citation15]. The similar cruciform pattern (Figure S2(b)) can be observed in Sn–Bi/Te [Citation18]. As known, the SnTe forms mainly at the interface between Sn-based solder and Te-based TE substrate, and it is weak in mechanical strength and likely deteriorating the reliability of the thermoelectric module. That directs the selection of solders towards to the alloys which could be self-diffusion barriers. In addition to the SnTe IMC, the interfacial reactions bwteen Sn–Cu, Sn–Ag or Sn–Sb solders and Te substrate result in the formation of multiple reaction layers, such as the CuTe IMC in Sn–Cu/Te [Citation20], Ag2Te IMC in Sn–Ag/Te [Citation21], or SnSb IMC in Sn–Sb/Te [Citation22], respectively.
The above-mentioned IMCs creates extra interfaces, increases the contact resistance and possibly degrades the thermoelectric performance. A metal-based diffusion barrier is typically added, between the solder and TE substrate, to inhibit the formation of IMCs while ensuring good electrical contact [Citation23–26]. The barrier layer also creates extra interfaces and possibly form new IMCs with either the TE substrate or the solders. Sputtering and electroless-plating are the two common methods for depositing the diffusion barrier layers. The interfacial reaction between the barrier metals, solders and TE substrate will be discussed.
2.3 Diffusion barrier in Bi2Te3-based modules
A layer of Ni could be an effective diffusion barrier for Bi2Te3-based modules [Citation27-31]. The NiTe IMC is commonly observed. However, the bonding strength between the Ni layer (electroless-plated or sputtered) and Bi2Te3 substrate is less than 10 MPa, which fail to meet the requirement for practical application. Another promising candidate for diffusion barrier is Co, owing to the slow inter-diffusion between Co and Te [Citation32, Citation33]. After aging, only the CoTe2 grows slowly at the interface of Co/TE substrate.
(a)–(c) summarize the inter-diffusion between p-type (Bi,Sb)2Te3 and the SAC305 (Sn3Ag0.5Cu) solder, with ((b) and (c)) or without ((a)) the incorporation of diffusion barrier layer. As shown, the incorporation of various diffusion barriers, such as Ni–P ((b)) and Co–P ((c), not only alter the type of IMCs, but prohibit the inter-diffuion between the (Bi,Sb)2Te3 and SAC305. The IMCs transform from the SnTe ((a)) to (Cu,Ni)6Sn5 ((b)) or CoSn3+ (Cu,Co)6Sn5 ((c)), with thickness less than 5 µm.
Figure 1. SAC305 reflow on (Bi,Sb)2Te3 substrate at 250°C (a) without diffusion barrier for 30 min (b) with Ni–P (c) with Co–P diffusion barrier and aging at 150°C for 15 days.
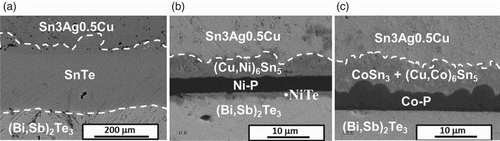
In addition to the metal Ni and Co, metallic thin films, including Pd, Pt, binary Ni-7 at% V and ternary Ta–Si–N, are effective diffusion barriers for Bi2Te3-based modules [Citation34]. Among them, the ternary Ta–Si–N (100 nm in thickness) successfully prevents the out-diffusion of constituent elements in Bi2Te3,, and acts as effective diffusion barrier layer [Citation34].
3. Mid-temperature PbTe-based modules
3.1 PbTe-based materials
Since 1950s, the PbTe has been unitilized in TEG [Citation35-40]. The Sb-doped PbTe shows n-type semiconducting with a peak zT of 0.62 at 723 K [Citation35], while the addition of Ag in PbTe leads to a degenerate p-type PbTe due to the formation of interstitial Ag [Citation39]. Moreover, composites comprising nanosized Ag2Te precipitates and Ag-doped PbTe matrix exhibit exceptionally high zT (zT > 1.3 at T > 725 K), owing to the combined effects of carrier concentration optimization and phonon scattering [Citation37].
3.2 Bonding in PbTe-based modules
Hot-pressing or SPS are major bonding methods to fabricate the PbTe-based TE modules. Both methods require high operation temperature and may induce severe inter-diffusion. Alternatively, a solid–liquid inter-diffusion provides a low-temperature bonding, through the incorporation of low-melting-point interlayers, such as the Sn or In [Citation41-43]. Those interlayers (Sn or In) are consumed by the metal layers (such as Ag), resulting in the high-melting-point IMCs (such as Ag3Sn and Ag3In), which might enhance the bonding strength.
Various metals or alloys are selected for the electrodes, while the diffusion barrier layer or interlayer are inserted in between the TE substrate (e.g. PbTe) and the electrodes, to prevent the severe inter-diffusion. (a)–(d) interpret the inter-diffusion of n-type PbTe/Cu and n-type PbTe/Ni couples [Citation43], where the diffusion barrier layer (e.g. Co–P) is introduced or not. After aging (650°C for 60 min), the formation of IMCs and interfacial irregularity in (a) and (c) (i.e. free of diffusion barrier) reveal the joint failure, in contrast to flat interface as introducing the Co-P diffusion barrier layer ((b) and (d)). Moreover, the mismatch in coefficient of thermal expansion (CTE) between the TE substrate, diffusion barrier layer and electrode is likely to induce the joint failures. Table S1 collects the CTE of the electrodes, the diffusion barrier layer/interlayer, the IMCs formed between the electrodes and PbTe substrate and the bonding methods.
Figure 2. n-type PbTe bonded on Cu [Citation43] (a) without (b) with Co–P diffusion barrier. n-PbTe bonded on Ni (c) without (d) with Co–P diffusion barrier, at 650°C for 60 min.
![Figure 2. n-type PbTe bonded on Cu [Citation43] (a) without (b) with Co–P diffusion barrier. n-PbTe bonded on Ni (c) without (d) with Co–P diffusion barrier, at 650°C for 60 min.](/cms/asset/0fb4ea9d-e3e2-424e-88e3-2b0791422f5b/tmrl_a_1436092_f0002_b.gif)
Fe is an ideal electrode for the n-type PbTe [Citation44]. As for p-type (Na-doped) PbTe, an interlayer (SnTe) is typically introduced between the PbTe and Fe electrode, to form a completely graded solid solution. Instead, an interlayer of Ni with CTE of 13.4 × 10−6/K should be inserted to minimize the CTE mismatch between PbTe (19.8 × 10−6/K) and Fe (11.7 × 10−6/K), in order to reduce thermal stress during the thermal cycling. Further investigations upon the interfacial reactions between PbTe and Ni is therefore of interests [Citation45, Citation46]. In the beginning of aging (600°C), the β2 phase (Ni3±xTe2) precipitates out from the PbTe nearing PbTe/Ni interfaces, and grows as a continuous layer with increasing aging time. Attentions needs to be drawn that the β2 acts as a self-diffusion barrier layer. As elevating the temperature to 650°C, a ternary Ni5Pb2Te3 forms between the PbTe and Ni layer.
Mo is another candidate for metal electrode, and the corresponding diffusion barrier is of NiFeMo layer (82Ni–15Fe–3Mo (wt%) [Citation47]). While bonding, the liquid Pb forms inside the PbTe, and penetrates into NiFeMo film, which leads to the joint failure. As switching to Nb electrode, two reaction products, which are of Nb3Te4 and Pb, are observed at the interface of Nb/PbTe [Citation48]. However, the large mismatch in CTE between Nb (7.3 × 10−6/K) and PbTe (19.8 × 10−6/K) limits the use of Nb in the PbTe-based modules.
For temperature lower than 400°C, Ag and Cu could be ideal electrodes, owing to the similarity in CTE (see Table S1). As bonding (400°C), both Ag and Cu atoms diffuse into PbTe, and form Ag2Te and Cu2Te IMC, respectively [Citation49, Citation50]. An increase in bonding temperature (∼550°C) leads to the formation of liquid Pb that induces voids and cracks. Nevertheless, both Ag and Cu are not suitable in bonding p-type (Pb0.6Sn0.4)Te, due to the fact that the Ag or Cu reacts with Sn to form Ag4Sn and Cu3Sn, respectively, and thus depletes the Sn in (Pb0.6Sn0.4)Te.
In addition to the pure metals, the eutectic Ag–Ge is a promising electrode [Citation51]. With the incorporation of Co or Ni diffusion barrier layer, a sandwich-like couple of PbTe/(Co,Ni)/Ag–Ge depicts a prototype for TEG. The inter-diffusion of the reaction couple is thereupon of interest. After aging at 400°C, the interface of PbTe/Co remains free of IMCs, while that of Co/Ag–Ge shows two IMCs, which are of the β-Co5Ge3 and CoGe, respectively. The inter-diffusion upon the Ni/Ag–Ge is even more severe; multiple IMCs (ε-Ni5Ge3 and Ag) are formed, reflecting that both Ni and Ge are fast diffusion species. Consequently, Co acts as an much more appropriate diffusion barrier layer as compared to Ni, in the bonding of PbTe and Ag–Ge.
5. Conclusions
The interfacial reactions between the electrode, the solder and the TE materials, are of great importance for a reliable module that can undergo a long-term operation with a constantly high performance at elevated temperature. In this review, the solders and diffusion barriers used for state-of-the-art Bi2Te3 and PbTe-based TE modules are discussed. The maximum/average zTs in various TE materials are still on the rise, showing an upward tendency at presen as well as in the future. Against this backdrop, progressive advances in bonding techniques are essential to develope the next-generation TEG and TEC.
Disclosure statement
No potential conflict of interest was reported by the authors.
Additional information
Funding
References
- Goldsmid HJ. Applications of thermoelectricity. London (UK): Methuen & Co. Ltd.; 1960.
- Tang Y, Gibbs ZM, Agapito LA, et al. Convergence of multi-valley bands as the electronic origin of high thermoelectric performance in CoSb3 skutterudites. Nat Mater. 2015;14:1223–1228.
- Zhang SN, Zhu TJ, Yang SH, et al. Improved thermoelectric properties of AgSbTe2 based compounds with nanoscale Ag2Te in situ precipitates. J Alloys Compd. 2010;499:215–220.
- Hicks LD, Dresselhaus MS. Effect of quantum-well structures on the thermoelectric figure of merit. Phys Rev B. 1993;47:12727–12731.
- Paul B, Kumar A, Banerji VP. Embedded Ag-rich nanodots in PbTe: enhancement of thermoelectric properties through energy filtering of the carriers. J Appl Phys. 2010;108:064322–064325.
- Zhao L, Tan G, Hao S, et al. Ultrahigh power factor and thermoelectric performance in hole-doped single-crystal SnSe. Science. 2016;351:141–144.
- He W, Zhang G, Zhang X, et al. Recent development and application of thermoelectric generator and cooler. Appl Energy. 2015;143:1–25.
- Jeon H, Ha H, Hyun D, et al. Electrical and thermoelectrical properties of undoped Bi2Te3-Sb2Te3 and Bi2Te3-Sb2Te3-Sb2Se3 single crystals. J Phys Chem Solids. 1991;52(4):579–585.
- Bulat LP, Drabkin IA, Karatayev V, et al. Structure and transport properties of bulk nanothermoelectrics based on BixSb2-xTe3 fabricated by SPS method. J Electron Mater. 2013;42:2110–2113.
- Poudel B, Hao Q, Ma Y, et al. High-thermoelectric performance of nanostructured bismuth antimony telluride bulk alloys. Science. 2008;320:634–638.
- Li H, Jing H, Han Y, et al. Microstructure and transport properties of copper-doped p-type BiSbTe alloy prepared by mechanical alloying and subsequent spark plasma sintering. J Alloy Compd. 2013;576:369–374.
- Son JH, Oh MW, Kim BS, et al. Effect of ball milling time on the thermoelectric properties of p-type (Bi,Sb)2Te3. J Alloy Compd. 2013;566: 168–174.
- Fan Z, Wang H, Wu Y, et al. Thermoelectric high-entropy alloys with low lattice thermal conductivity. RSC Adv. 2016;6:52164–52170.
- Yan X, Poudel B, Ma Y, et al. Experimental studies on anisotropic thermoelectric properties and structures of n-type Bi2Te2.7Se0.3. Nano Lett. 2010;10:3373–3378.
- Chen SW, Wu HJ, Wu CY, et al. Reaction evolution and alternating layer formation in Sn/(Bi0.25Sb0.75)2Te3 and Sn/Sb2Te3 couples. J Alloys Compd. 2013;553:106–112.
- Chen SW, Chiu CN. Unusual cruciform pattern interfacial reactions in Sn/Te couples. Scr Mater. 2007;56:97–99.
- Ma C, Swalin R. Self-diffusion in liquid Tin. J Chem Phys. 1962;36:3014–3018.
- Chen SW, Wu CY, Wu HJ, et al. Interfacial reactions in Sn/Bi2Te3, Sn/Bi2 Se3 and Sn/Bi2 (Te1− xSex)3 couples. J Alloys Compd. 2014;611:313–318.
- Chiu CN, Wang CH, Chen SW. Interfacial reactions in the Sn-Bi/Te couples. J Electron Mater 2008;37:40–44.
- Ellis W, Nachtrieb N. Anomalous self-diffusion in solid bismuth: the trapping mechanism. J Appl Phys. 1969;40:472–476.
- Liao CN, Lee CH. Suppression of vigorous liquid Sn/Te reactions by Sn-Cu solder alloys. J Mater Res. 2008; 23: 3303–3308.
- Liao CN, Huang YC. Effect of Ag addition in Sn on growth of SnTe compound during reaction between molten solder and tellurium. J Mater Res. 2010; 25(20): 391–395.
- Lee CH, Chen WT, Liao CN. Effect of antimony on vigorous interfacial reaction of Sn-Sb/Te couples. J Alloys Compd. 2011;509:5142–5146.
- Zhang H, Jing H, Han Y, et al. Interfacial reaction between n- and p-type thermoelectric materials and SAC305 solders. J Alloys Compd. 2013;576:424–431.
- Ko CY, Wu AT. Evaluation of diffusion barrier between pure Sn and Te. J Electron Mater. 2012;41:3320–3324.
- Lin TY, Liao CN, Wu AT. Evaluation of diffusion barrier between lead-free solder systems and thermoelectric materials. J Electron Mater. 2012;41:153–158.
- Lin WP, Wesolowski DE, Lee CC. Barrier/bonding layers on bismuth telluride (Bi2Te3) for high temperature thermoelectric modules. J Mater Sci Mater Electron. 2011;22:1313–1320.
- Lan Y, Wang D, Chen G, et al. Diffusion of nickel and tin in p-type (Bi, Sb)2Te3 and n-type Bi2(Te, Se)3 thermoelectric materials. Appl Phys Lett. 2008;92:101910.
- Iyore O, Lee T, Gupta R, et al. Interface characterization of nickel contacts to bulk bismuth tellurium selenide. Surf Interface Anal. 2009;41:440–444.
- Lin CF, Hau NY, Huang YT, et al. Synergetic effect of Bi2Te3 alloys and electrodeposition of Ni for interfacial reactions at solder/Ni/Bi2Te3 joints. J Alloys Compd. 2017;708:220–230.
- Wada H, Takahashi K, Nishizaka T. Electroless nickel plating to Bi-Te sintered alloy and its properties. J Mater Sci Lett. 1990;9:810–812.
- Liu W, Wang H, Wang L, et al. Understanding of the contact of nanostructured thermoelectric n-type Bi2Te2.7Se0.3 legs for power generation applications. J Mater Chem A. 2013;1:13093–13100.
- Gupta R, Iyore O, Xiong K, et al. Interface characterization of cobalt contacts on bismuth selenium telluride for thermoelectric devices. Electrochem Solid State Lett. 2009; 12: H395–H397.
- Li S, Yang D, Tan Q, et al. Evaluation of electroplated Co-P film as diffusion barrier between In-48Sn solder and SiC-dispersed Bi2Te3 thermoelectric material. J Electron Mater. 2015; 44: 2007.
- Ravich Y, Efimova BA, Smirnov TA. Semiconducting lead chalcogenide, Ed. Stil'bans LS. New York (NY): Plenum Press; 1970.
- Pei Y, Heinz NA, LaLonde A, et al. Combination of large nanostructures and complex band structure for high performance thermoelectric lead telluride. Energy Environ Sci. 2011;4:3640–3645.
- Lu P, Wang X, Lu M. Largely enhanced thermoelectric properties of the binary-phased PbTe-Sb2Te3 nanocomposites. J Mater Res. 2012;27:734–739.
- Pei Y, May AF, Snyder GJ. Self-tuning the carrier concentration of PbTe/Ag2Te composites with excess Ag for high thermoelectric performance. Adv Energy Mater. 2011;1:291.
- Ahn K, Li C, Uher C, et al. Improvement in the thermoelectric figure of merit by La/Ag cosubstitution in PbTe. Chem Mater. 2009;21:1361–1367.
- Dow HS, Oh MW, Kim BS, et al. Effect of Ag or Sb addition on the thermoelectric properties of PbTe. J Appl Phys. 2010;108:113709.
- Strauss AJ. Effect of Pb- and Te-saturation on carrier concentrations in impurity-doped PbTe. J Electron Mater. 1973;2:553–569.
- Chuang TH, Lin HJ, Chuang CH, et al. Solid liquid interdiffusion bonding of (Pb, Sn) Te thermoelectric modules with Cu electrodes using a thin-film Sn interlayer. J Electron Mater. 2014;43(12):4610–4618.
- Hsieh HC, Wang CH, Lin WC, et al. Electroless Co-P diffusion barrier for n-PbTe thermoelectric material. J Alloy Compd. 2017;728:1023–1029.
- Weinstein M, Mlavsky AI. Bonding of lead telluride to pure iron electrodes. Rev Sci Instrum. 1962;33(10):1119–1120.
- Xia H, Drymiotis F, Chen CL, et al. Bonding and interfacial reaction between Ni foil and n-type PbTe thermoelectric materials for thermoelectric module applications. J Mater Sci. 2014; 49(4): 1716–1723.
- Ferreres XR, Yamini S, Nancarrow M, et al. One-step bonding of Ni electrode to n-type PbTe – A step towards fabrication of thermoelectric generators. Mater Des. 2016;107:90–97.
- Xia H, Drymiotis F, Chen CL, et al. Bonding and high-temperature reliability of NiFeMo alloy/n-type PbTe joints for thermoelectric module applications. J Mater Sci. 2015;50(7):2700–2708.
- Xia H, Chen CL, Drymiotis F, et al. Interfacial reaction between Nb foil and n-type PbTe thermoelectric materials during thermoelectric contact fabrication. J Electron Mater. 2014; 43(11): 4064–4069.
- Li CC, Drymiotis F, Liao LL, et al. Silver as a highly effective bonding layer for lead telluride thermoelectric modules assembled by rapid hot-pressing. Energy Convers Manag. 2015; 98: 134–137.
- Li CC, Drymiotis F, Liao LL, et al. Interfacial reactions between PbTe-based thermoelectric materials and Cu and Ag bonding materials. J Mater Chem C. 2015; 3(40): 10590–10596.
- Chen SW, Wang JC, Chen LC. Interfacial reactions at the joints of PbTe thermoelectric modules using Ag-Ge braze. Intermetallics. 2017;83:55–63.