ABSTRACT
A synergistic balance of strength and ductility was achieved in a prototypical fcc-based Al0.3CoCrFeNi complex concentrated alloy by incorporating hierarchical microstructural features into heterogeneous grain structure. Microstructural hierarchy was composed of different morphologies and size-scales of B2 precipitates and nano-twins that were incorporated in parent fcc matrix, which, additionally, was comprised of domains of fine and coarse grains. Strain partitioning between refined and coarse grains produced geometrically necessary dislocations during plastic deformation. This facilitated long-range back stresses during further deformation leading to simultaneous enhancement of strength and ductility. Furthermore, B2 precipitates complemented back stress and increased inherent matrix strength.
GRAPHICAL ABSTRACT
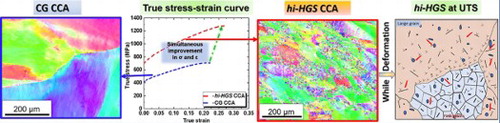
IMPACT STATEMENT
Architecting hierarchical microstructural features into a heterogeneous grain structured complex concentrated alloy avoided the classic strength-ductility trade-off paradigm.
The conflicting nature of strength and ductility has been a decades-long paradigm while choosing structural materials. The importance of high strength for structural application has led to the development of numerous strengthening mechanisms, such as solid solution strengthening, work hardening, and precipitation strengthening. Grain refinement has also been extensively utilized method for improving strength due to the fact that ultrafine-grained (UFG) and nano-crystalline (NC) materials typically exhibit higher strength as compared to coarse-grained (CG) materials [Citation1–3]. However, the poor strain hardening response of UFG and NC materials limits their ductility and, consequently, impairs their applicability for critical components [Citation4,Citation5]. Nevertheless, the past decade has witnessed the development of innovative approaches for manufacturing materials with considerably distinct microstructures consisting of hard and soft domains. Several studies on materials containing heterogeneous lamellar structures [Citation6], bimodal structures [Citation7], and gradient structures [Citation8] have pointed to an exciting phenomenon of strength-ductility harmony rather than the trade-off. Broadly, such materials are classified into a common category of heterogeneous materials and the microstructure is labeled as heterogeneous grain structure (HGS) [Citation9].
Alongside, inspirations drawn from nature have also guided efforts to solve the strength-ductility predicament by engineering microstructural hierarchy into structural materials [Citation10,Citation11]. Consequently, hierarchical microstructural features (features of different length scales) have been exploited to enhance superplastic properties in titanium [Citation12] and aluminum alloys [Citation13], in addition to the improved mechanical properties [Citation14,Citation15] in high-entropy alloys. Thus, such unconventional approaches have opened new avenues for microstructural modification to improve mechanical performance.
In this regard, a new class of materials known as complex concentrated alloys (CCAs) or more conventionally referred to as high-entropy alloys (HEAs), has generated tremendous interest in the scientific community [Citation16]. With their extensive compositional space, CCAs are being subjected to numerous investigations, ranging from cryogenic [Citation17] and refractory properties [Citation18] to magnetic and electrochemical properties [Citation19,Citation20]. Mechanical properties in CCAs originate from a combination of various strengthening mechanisms [Citation21]. Recent investigations focused on exploiting Hall-Petch strengthening and precipitation hardenability via cold-rolling and heat-treatment to improve strength [Citation22–24]. Also, the low stacking fault energy (SFE) of CCAs promotes the formation of twins during annealing and deformation processes [Citation16,Citation17]. Given the complex nature of physical metallurgy involved in CCAs, several metallurgical variables can be used to modify the microstructure for targeted properties.
Considering this context, we present a novel approach to combine the benefits of both hierarchical microstructural features and heterogeneous grain structure to achieve a simultaneous improvement in strength and ductility. The present study involves traditional cold-rolling and annealing of an Al0.3CoCrFeNi CCA to achieve a partially-recrystallized HGS with B2 precipitates of different sizes and morphologies. While the key objective of an HGS is to impart load or strain partitioning, the hierarchical features introduced in the microstructure complement the back stress and result in improved work-hardening rates, ductility, and delayed necking.
An Al0.3CoCrFeNi alloy containing 6.70%Al-23.15%Co-23.35%Cr-23.45Fe-23.35%Ni (at%) obtained from Sophisticated Alloys was subjected to a homogenization treatment at 1150°C for 1 h to achieve a single fcc phase. The homogenized sample was then cold-rolled to achieve a 30% and 50% reduction in the initial thickness. The homogenized and cold-rolled samples were subsequently annealed at 800°C for 50 h. Mini-tensile samples of gage length ∼5 mm and both width and thickness of ∼1 mm were quasi-statically tested using a custom-built computer controlled mini-tensile tester with an initial strain rate of 10−3 s−1. Loading-unloading-reloading (LUR) tensile tests were conducted on the mini-tensile tester with the same strain rate. Strain values were measured via digital image correlation (DIC). Three samples were tested for each condition for statistical accuracy. Scanning electron microscopy (SEM) was performed on FEI Nova NanoLab 200TM while transmission electron microscopy (TEM) was performed on FEI Tecnai F20-FEGTM operating at 200 kV.
The initial microstructures of the 30% and 50% cold-rolled and annealed (800°C for 50 h) specimens are compared in Figure . Figure (a) shows the macro-EBSD image of 30% cold-rolled and annealed Al0.3CoCrFeNi CCA. An enlarged view of the region shown in the blue box in Figure (a) is displayed in Figure (b). Twins from the prior cold-rolling step (indicated with blue colored Σ3 interface), and several B2 precipitates are clearly visible in the fcc matrix (phase map in Supplementary Figure S1(c)). Because of the large grain size (average size was approximately 160 μm, Supplementary Figure S1(e)), this microstructure will be referred to as CG (coarse-grained) CCA during further discussion. Figure (c) is a macro-EBSD view of 50% cold-rolled and annealed CCA. The microstructure is composed of domains of predominantly two different grain sizes (i) partially recrystallized grains (PRGs) of large size (i.e. remnant strain-relieved grains and have large size), and (ii) completely recrystallized grains (CRGs) of fine size (complete recrystallization after heat-treatment has led to the formation of new fine-scale grains) (Figure (c)). This strategy of deliberate partial recrystallization was previously employed to obtain HGS in titanium alloys [Citation6] and medium entropy alloy [Citation23]. Several annealing twins (Supplementary Figures S2(c) and (f)) can also be observed in the magnified view (Figure (d)) of completely recrystallized fine grains (grain size distribution information in Supplementary Figure S2(b) and (e)). The cold-rolling (50%) and subsequent annealing produce B2 precipitates of different morphology and distribution within the fcc matrix (Figure (e)). High-angle annular scanning TEM or HAADF-STEM (Figure (f)) shows B2 precipitates of divergent size scales and morphologies (globular and plate-like B2 precipitates are marked with red and green arrows, respectively). Our previous study provided a detailed orientation relationship (OR), i.e. Kurdjumov-Sachs, Nishiyama Wasserman and Pitch [Citation24], and suggested that such B2 alignments can restrict dislocation movements on the {111} planes of fcc [Citation24]. These B2 precipitates of different sizes (from ∼100 nm to ∼1–2 μm) and varying morphologies (plate and globular as shown in BSE (Figure (e)) and TEM image (Figure (f)), along with the remnant twins from prior cold-rolling in PRGs and annealing twins in CRGs, provide hierarchy in the microstructure. Additionally, these hierarchical microstructural features are blended into the heterogeneous grain structured fcc matrix. Henceforth, we will refer 50% cold-rolled and subsequently annealed microstructure as hi-HGS (hierarchical features infused heterogeneous grain structured) CCA.
Figure 1. EBSD micrographs of (a) CG-CCA and (b) magnified view of CG CCA. (c) hi-HGS CCA, and (d) magnified view of completely recrystallized fine grains. (e) BSE image of hi-HGS showing B2 precipitates and (f) TEM image showing B2 precipitates of plate shape (red arrow), globular shape (green arrows) and the diffraction pattern in the inset.
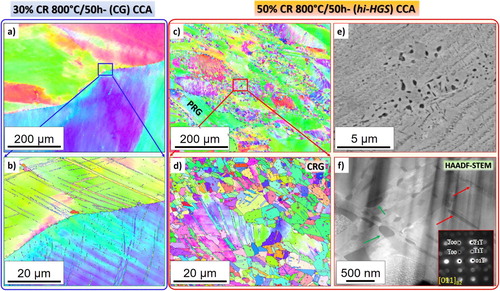
Next, we analyzed the mechanical response of hi-HGS CCA and CG CCA in the plastic regime through engineering and true stress–strain curves (Figure (a)) and summarized them in Table . Both CG and hi-HGS CCAs have B2 precipitates of divergent sizes and morphologies. These B2 precipitates block dislocation movement during the deformation process and the effectiveness towards strengthening depends on the size. (Supplementary Figure 3S(a)). A literature review on single phase CCA indicates that grain boundary strengthening (Hall-Petch effect) has only a small contribution of ∼ 110 MPa for CG CCA and ∼200 MPa for hi-HGS CCA, respectively [Citation22]. Also, the CG CCA contains twin boundaries (Figure (b)), which act as strong obstacles to dislocation movement and lead to an increase in the flow stress. In this study, a clear enhancement in the tensile properties of the hi-HGS can be observed with ∼ 75% increment in yield strength (YS) and ∼ 70% increment in ultimate tensile strength (UTS) values when compared to that of CG CCA. These improvements are due to the symbiotic interaction of heterogeneous grain structured fcc matrix with B2 precipitates, which we will explore in later sections.
Figure 2. (a) Engineering and true stress-strain curves at an initial strain rate of 10−3 s−1. (b) Work-hardening rate and true stress curves as a function of true strain.

Table 1. Tensile properties of hi-HGS and CG CCA in plastic regime.
Figure (b) presents a combined work hardening rate (Θ) and true stress curves as functions of true strain for both microstructures. In low SFE materials, stage A (continuous drop in Θ) generally represents dislocation slip-dominated plasticity while stage B (plateau type region) is characterized by twinning-mediated plasticity [Citation25]. Since both microstructures have low SFE [Citation24], we expect them to exhibit both stages of Θ. As B2 precipitates prune the matrix of aluminum, the deformation mechanism of soft fcc matrix becomes analogous to that of any single-phase CCA. Also, reduction in aluminum content lowers the SFE of the matrix and facilitates the formation of nano-twins during deformation [Citation24] (Supplementary Figure 3S(b)). In fact, these nano-twins provide an extra layer of hierarchy in the microstructure during the deformation process. By increasing obstacles to dislocation glide and leading to the so-called ‘dynamic Hall-Petch effect’, nano-twins result in higher work-hardening and ductility in later stages of deformation. However, the heterogeneity of the grain structure in the hi-HGS material imparts additional Θ when compared with CG CCA. Also, imperatively important is the observation that the hi-HGS shows nearly a 30% improvement in uniform elongation and plastic stability over CG CCA as indicated by Considère criterion (Θ = σ) in Figure (b). Hence, these enhanced properties of the hi-HGS can be attributed to the unique microstructure containing hierarchical B2 precipitates, deformation nano-twins, and heterogeneous grain structured fcc matrix.
To understand the observed high strength and strain hardening, loading-unloading-reloading (LUR) tests up to three cycles for both CG and hi-HGS CCAs were performed (Figure (a)). LUR curves for both microstructures exhibit a hysteresis loop, a phenomenon associated with the Bauschinger effect [Citation26]. With the LUR curve, the flow stress can be divided into back stress (σb) and effective stress (σf). During the deformation of plastically non-homogenous material, deformation gradients form with wavelengths proportional to the spacing between the hard phases [Citation28,Citation29]. These strain gradients are accommodated by geometrically necessary dislocations (GNDs) which lead to back-stress, a type of long-range stress crucial to achieve an excellent strength-ductility combination [Citation9,Citation23,Citation28]. Authors have applied the approach of Yang et al. [Citation8] for back stress (σb) calculation, given as:
where σu and σr are unloading yield point (UYP) and reloading yield point (RYP), respectively. It is also assumed that back stress remains constant during the elastic segment of unloading (while other parameters remain the same). The effective stress (σf), obtained by subtracting back stress from the flow-stress, is the stress required locally for dislocation movement and therefore is affected by the dislocation density [Citation8,Citation9,Citation27].
Figure 3. (a) Loading-unloading-reloading (LUR) curves of hi-HGS and CG CCAs, (b) measured hysteresis loop for hi-HGS and CG CCAs showing UYP and RYP, (c) back stress and effective stress values of hi-HGS and CG CCAs, and (d) comparison of back stress to YS ratio with literature data.
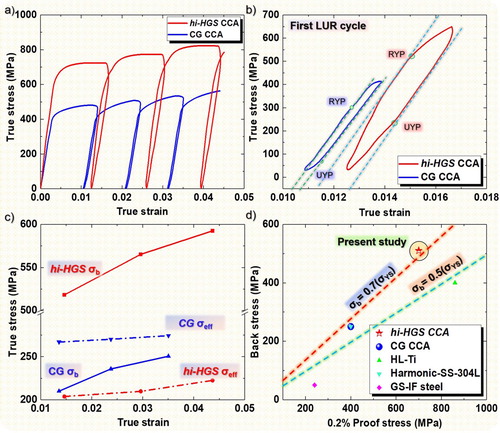
A larger width of the hysteresis loop and higher UYP for hi-HGS over CG CCA (Figure (b)) are unambiguous indications of strong back stress generation during deformation [Citation6,Citation23]. Values of σb and σf for both microstructures are plotted in Figure (c). It is evident that for hi-HGS, the influence of back stress during deformation is much higher than the effective stress. On the other hand, both back stress and effective stress contribute almost equally during CG CCA’s deformation. In hi-HGS, the fcc matrix is composed of domains of large and fine grains, which deform in a non-uniform way, resulting in gradients of plastic deformation and storage of GNDs [Citation28]. Increasing strain would activate more dislocation sources in softer grain domains and would lead to more dislocation pile-ups against the boundaries between the domains of large and fine grains. Since back stress strengthening is a result of GNDs pile-ups, the deformation process of hi-HGS would produce an excessively large number of GNDs and would result in the creation of long-range back stress. Additionally, coarse and fine fcc grains are synchronously infused with hierarchical B2 precipitates. Since these B2 precipitates act as hard phases, GNDs within the fcc matrix will also be produced to have a compatible deformation [Citation29]. According to Ashby [Citation29], the density of GNDs (ρg) depends on the size and morphology of the hard phases. Hence, the different shapes of B2 (plate and globular) precipitates in the hi-HGS CCA provide varying levels of ρg. Accordingly, these precipitates will create strain gradients and back stresses which will increase the inherent strength of the respective domains. In fact, a comparison of normalized back stress (ratio of back stress in first LUR to 0.2% proof stress) with other heterogeneous grain structured alloys reveals an extraordinary contribution of back stress strengthening in hi-HGS (Figure (d)). A recent study on a medium-entropy alloy also shows a very high contribution of back stress due to the dynamic evolution of corner twins into nano-grains, thus increasing the level of heterogeneity in the microstructure [Citation23].
Finally, we analyzed microstructural evolution during tensile deformation through Kernel average misorientation (KAM) images. KAM analysis quantifies the average misorientation around a measurement point which can be used to understand local lattice distortion and strain energy within the grain. To ensure a comprehensive analysis, all the EBSD parameters (such as magnification, step size of 80 nm, current, and voltage) for both microstructures were kept constant throughout the deformation study. The location of KAM analysis was also fixed with the help of fiduciary FIB markings on the sample. The misorientation values from zero to two degrees were examined and presented on a blue to red color scale. Figure (a–c) represent the KAM images obtained during various stages of deformation in hi-HGS CCA. The higher KAM values of coarse grains prior to loading are indicators of small amounts of residual stress remaining after the partial recrystallization. Also, the completely recrystallized fine grains show very little strain before loading (Figure (a)). Figure (b) presents the KAM micrograph of hi-HGS microstructure slightly below the yield point. The higher KAM values in coarse grains are clear evidence of strain partitioning in which the large grain carries higher amounts of strain before the overall yielding occurs. This strain partitioning creates strain gradients, which result in the pile-up of GNDs, a fact that can be substantiated by even higher KAM values close to the domain boundaries (the boundary between large grain and fine grains (Figure (b)). GNDs aid strain-hardening not only by creating long-range back stress, but also by acting as barriers to further slip. With increasing strain beyond the yield point, the fine grains and coarse grains will deform plastically as verified by Figure (c). In stark contrast, the CG CCA shows an almost uniform strain development during various stages of deformation (Figure (d–f)).
Figure 4. Microstructural evolution during deformation displayed via Kernel average misorientation (KAM) micrographs of hi-HGS (a) at zero stress, (b) just below yield point, and (c) at UTS. (d-f) Microstructural evolution of CG CCA during deformation.
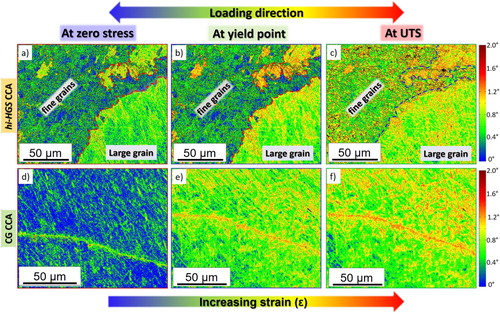
In summation, we successfully achieved an excellent strength-ductility combination by embedding hierarchical B2 precipitates into a heterogeneous grain structured complex concentrated alloy. The hi-HGS microstructure and overall stages of deformation are summarized in Figure . B2 precipitates of different morphologies have different orientation relationships with the fcc matrix. While the B2 precipitates raise matrix strength, the imposed heterogeneity in grain structure brings out additional long-range back stress with deformation. In addition, the matrix is susceptible to the formation of nano-twins during deformation which, in turn, increases work-hardening even further. Notably, traditional cold-rolling and subsequent annealing processes, which can be scaled easily for industrial production, were involved in obtaining this hi-HGS CCA. With their vast range of composition and intricate physical metallurgy, CCAs provide excellent opportunities to engineer the desired microstructure and create high-performance materials.
Supplementry_Information.docx
Download MS Word (1.9 MB)Acknowledgement
Authors acknowledge the support of National Science Foundation (NSF) grant 1435810 and Materials Research Facility (MRF) at University of North Texas (UNT).
Disclosure statement
No potential conflict of interest was reported by the authors.
ORCID
Tianhao Wang http://orcid.org/0000-0002-7151-2658
Rajiv S. Mishra http://orcid.org/0000-0002-1699-0614
Additional information
Funding
References
- Valiev RZ, Islamgaliev RK, Alexandrov IV. Bulk nanostructured materials from severe plastic deformation. Prog Mater Sci. 2000;45:103–189. doi: 10.1016/S0079-6425(99)00007-9
- Langdon TG. Twenty-five years of ultrafine-grained materials: achieving exceptional properties through grain refinement. Acta Mater. 2013;61:7035–7059. doi: 10.1016/j.actamat.2013.08.018
- Shukla S, Komarasamy M, Mishra RS. Grain size dependence of fatigue properties of friction stir processed ultrafine-grained Al-5024 alloy. Int J Fatigue. 2018;109:1–9. doi: 10.1016/j.ijfatigue.2017.12.007
- Wei Y, Li Y, Zhu L, et al. Evading the strength-ductility trade-off dilemma in steel through gradient hierarchical nanotwins. Nat Commun. 2014;5:3580. doi: 10.1038/ncomms4580
- Wu X, Yuan F, Yang M, et al. Nanodomained nickel unite nanocrystal strength with coarse-grain ductility. Sci Rep. 2015;5:11728. doi: 10.1038/srep11728
- Wu X, Yang M, Yuan F, et al. Heterogeneous lamella structure unites ultrafine-grain strength with coarse-grain ductility. Proc Natl Acad Sci. 2015;112:14501–14505. doi: 10.1073/pnas.1517193112
- Wang Y, Chen M, Zhou F, et al. High tensile ductility in a nanostructured metal. Nature. 2002;419:912–915. doi: 10.1038/nature01133
- Yang M, Pan Y, Yuan F, et al. Back stress strengthening and strain hardening in gradient structure. Mater Res Lett. 2016;4:145–151. doi: 10.1080/21663831.2016.1153004
- Wu X, Zhu Y. Heterogeneous materials: a new class of materials with unprecedented mechanical properties. Mater Res Lett. 2017;5:527–532. doi: 10.1080/21663831.2017.1343208
- Cao SC, Liu J, Zhu L, et al. Nature-inspired hierarchical steels. Sci Rep 2018;8:1–7. doi: 10.1038/s41598-017-17765-5
- Sankaran KK, Mishra RS. Metallurgy.and Design of Alloy. with Hierarchical Microstructure. Elsevier, 2017. Chapter 1, Introduction p. 1–19.
- Mishra RS, Stolyarov VV, Echer C, et al. Mechanical behavior and superplasticity of a severe plastic deformation processed nanocrystalline Ti–6Al–4V alloy. Mater Sci Eng A. 2001;298:44–50. doi: 10.1016/S0921-5093(00)01338-1
- Ma ZY, Liu FC, Mishra RS. Superplastic deformation mechanism of an ultrafine-grained aluminum alloy produced by friction stir processing. Acta Mater. 2010;58:4693–4704. doi: 10.1016/j.actamat.2010.05.003
- Shukla S, Wang T, Cotton S, et al. Hierarchical microstructure for improved fatigue properties in a eutectic high-entropy alloy. Scr Mater. 2018;156:105–109. doi: 10.1016/j.scriptamat.2018.07.022
- Zhu ZG, Nguyen QB, Ng FL, et al. Hierarchical microstructure and strengthening mechanisms of a CoCrFeNiMn high-entropy alloy additively manufactured by selective laser melting. Scr Mater. 2018;154:20–24. doi: 10.1016/j.scriptamat.2018.05.015
- Cantor B. Multicomponent and high-entropy alloys. Entropy. 2014;16:4749–4768. doi: 10.3390/e16094749
- Gludovatz B, Hohenwarter A, Catoor D, et al. A fracture-resistant high-entropy alloy for cryogenic applications. Science. 2014;345:1153–1158. doi: 10.1126/science.1254581
- Senkov ON, Isheim D, Seidman DN, et al. Development of a refractory high entropy superalloy. Entropy. 2016;18:102. doi: 10.3390/e18030102
- Kao YF, Chen SK, Chen TJ, et al. Electrical, magnetic, and Hall properties of AlxCoCrFeNi high-entropy alloys. J. Alloys Compd. 2011;509:1607–1614. doi: 10.1016/j.jallcom.2010.10.210
- Kumar N, Fusco M, Komarasamy M, et al. Understanding effect of 3.5 wt% NaCl on the corrosion of Al 0.1 CoCrFeNi high-entropy alloy. J Nucl Mater. 2017;495:154–163. doi: 10.1016/j.jnucmat.2017.08.015
- Miracle DB, Senkov ON. A critical review of high-entropy alloys and related concepts. Acta Mater. 2017;122:448–511. doi: 10.1016/j.actamat.2016.08.081
- Gwalani B, Soni V, Lee M, et al. Optimizing the coupled effects of Hall-Petch and precipitation strengthening in a Al0.3CoCrFeNi high entropy alloy. Mater Des. 2017;121:254–260. doi: 10.1016/j.matdes.2017.02.072
- Yang M, Yan D, Yuan F, et al. Dynamically reinforced heterogeneous grain structure prolongs ductility in a medium-entropy alloy with gigapascal yield strength. Proc Natl Acad Sci. 2018;115:7224–7229. doi: 10.1073/pnas.1807817115
- Choudhuri D, Shukla S, Green WB, et al. Crystallographically degenerate B2 precipitation in a plastically deformed fcc-based complex concentrated alloy. Mater Res Lett. 2018;6:171–177. doi: 10.1080/21663831.2018.1426649
- Tian YZ, Zhao LJ, Chen S, et al. Significant contribution of stacking faults to the strain hardening behavior of Cu-15%Al alloy with different grain sizes. Sci Rep. 2015;5:2–10.
- Xiang Y, Vlassak JJ. Bauschinger effect in thin metal films. Scr Mater. 2005;53:177–182. doi: 10.1016/j.scriptamat.2005.03.048
- Park HK, Ameyama K, Yoo J, et al. Additional hardening in harmonic structured materials by strain partitioning and back stress. Mater Res Lett. 2018;6:261–267. doi: 10.1080/21663831.2018.1439115
- Ma E, Zhu T. Towards strength–ductility synergy through the design of heterogeneous nanostructures in metals. Mater Today. 2017;20(6):323–331. doi: 10.1016/j.mattod.2017.02.003
- Ashby MF. The deformation of plastically non-homoge-neous materials. Philos Mag: J Theor Exp Appl Phys. 1970;21(170):399–424. doi: 10.1080/14786437008238426